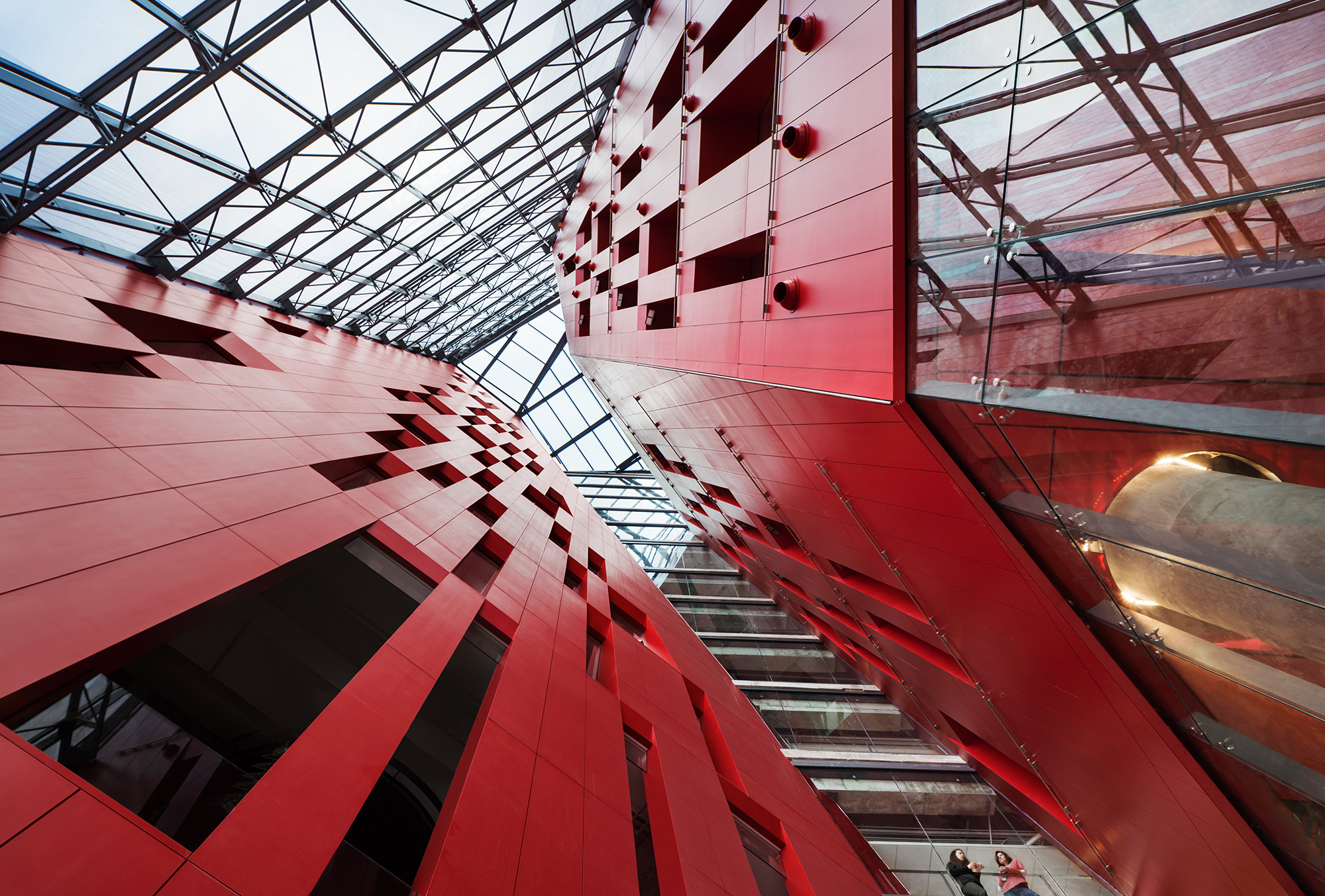
Photo by Stephane Brugger; courtesy of Guardian Glass
Îlot Balmoral in Montreal features a red glass atrium that appears to slice diagonally through the otherwise rectangular structure. The large glass facade brings ample natural light into the core of the building.
Design teams sourcing products for new construction or retrofits are increasingly taking into consideration how glass products embody the principles of stewardship. This article will explore how architects and designers can expand their knowledge of stewardship to source materials associated with responsible manufacturing and ethical standards. Specifically, the article will define the two categories of stewardship: Environmental, Social and Governance (ESG) Stewardship and Product Stewardship. Operational carbon and embodied carbon will be defined and discussed as measurable, reportable units that design teams can use to calculate the total carbon of their product. This discussion will also provide insight into methods for reducing embodied carbon in the glass manufacturing process. Finally, the article will explore other parameters that impact ESG and illustrate how architects can engage with manufacturers to ensure that the glass products they are specifying contribute to a project’s stewardship goals.
STEWARDSHIP AS A PHILOSOPHY
Our modern era has become increasingly interconnected. Actions on one side of the planet could impact populations across the globe. This has prompted more focus on stewardship, defined as the careful and responsible management of the resources entrusted to one’s care. It’s common to think of stewardship within an environmental framework. In industry, stewardship also includes social responsibility, which includes safety and governance. From a practical standpoint, our future depends on taking this responsibility seriously. In terms of the environment, everyone can strive to practice good stewardship. By combining the efforts of both individuals and industry, however, the impact can be exponential.
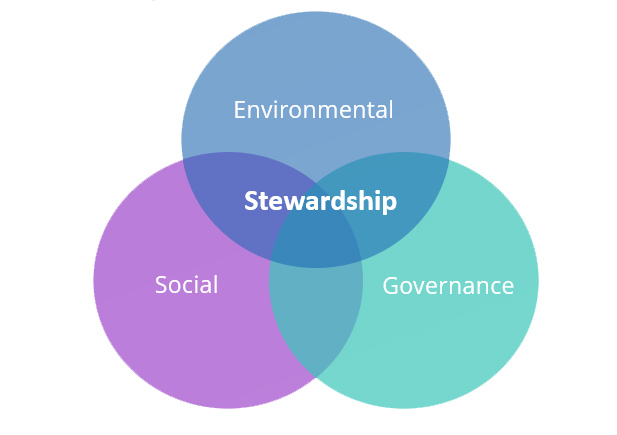
Graphic courtesy of Guardian Glass
Environmental, Social, and Governance (ESG) Stewardship covers the responsible management of our resources in a manner that respects the rights of others, including the right to life, property, and equal treatment under the law. Each pillar has unique stewardship parameters.
Stewardship in the Built Environment
Two different categories of stewardship that apply to the construction sector are Environmental, Social, and Governance Stewardship and Product Stewardship.
Environmental, Social, and Governance (ESG) Stewardship covers the responsible management of our resources in a manner that respects the rights of others, including the right to life, property, and equal treatment under the law. Each pillar has unique stewardship parameters.
Environmental Stewardship encompasses consuming fewer resources, minimizing waste, and constantly innovating to improve manufacturing processes and performance, which benefits customers, employees, investors, communities, and the planet. Environmental Stewardship priorities might include investing in innovative technologies, improving energy efficiency, and reducing air emissions and water consumption.
Social Stewardship incorporates priorities such as the health and safety of employees and the community; inclusive environments; meaningful, rewarding careers; and community outreach. Together, these priorities empower employees to contribute, self-actualize, and create value while supporting the communities in which they live and work.
Governance is found in a company’s management framework and is based on a deep appreciation for the dignity of every individual involved with the company while applying a shared vision, values, compliance standards, and oversight.
The second category of stewardship is Product Stewardship. This refers to the responsible management of the health, safety, and environmental aspects of raw materials and finished products both throughout their life cycles–including end-of-life–and across the value chain.
Float Glass Plays a Role in Stewardship
Float glass plays a vital role in construction and design, as it has a noticeable impact on the final space. Glass and selected coatings can help dictate the natural light available and temperature control through solar energy. Glass provides protection as a physical barrier blocking wind, rain, and other exterior threats. It can also offer protection from other thermal elements like temperature extremes when the right low-E coating and configuration are presented. Float glass does more than protect the physical space, it helps promote health and wellness in the emotional space of occupants as well. Glass connects interior and exterior spaces, which can be important to people inside the building–who can enjoy big views or be immersed in natural surroundings–and to passersby, whose experience could be influenced by the degree of glass reflection. The growth of glass in design is on the rise. According to U.S. Glass Metal & Glazing, the use of commercial float glass increased by 14% between 2022 and 2023 in all applicable subsectors, including hotel, office, and others. The institutional use of glass and glazing grew by 9% over this same period, led by the healthcare and educational building sectors.1 As glass continues to play a big role in modern design, it will become an increasingly useful and important opportunity for designers and builders to practice good stewardship.
OPERATIONAL AND EMBODIED CARBON
According to the World Green Building Council, buildings are responsible for approximately 39% of global energy-related carbon emissions.2
In the building sector, that can be broken down into two categories. One is the energy used to construct a building, called embodied carbon, which includes everything from the extraction and transportation of raw materials to the production, transportation, assembly, and installation of building materials.
Embodied carbon accounts for 11% of that 39% carbon emissions. The other category is the energy used by a building when functioning for its intended purpose, called operational carbon, which accounts for the remaining 28%. There are opportunities to reduce greenhouse gas emissions in both categories.
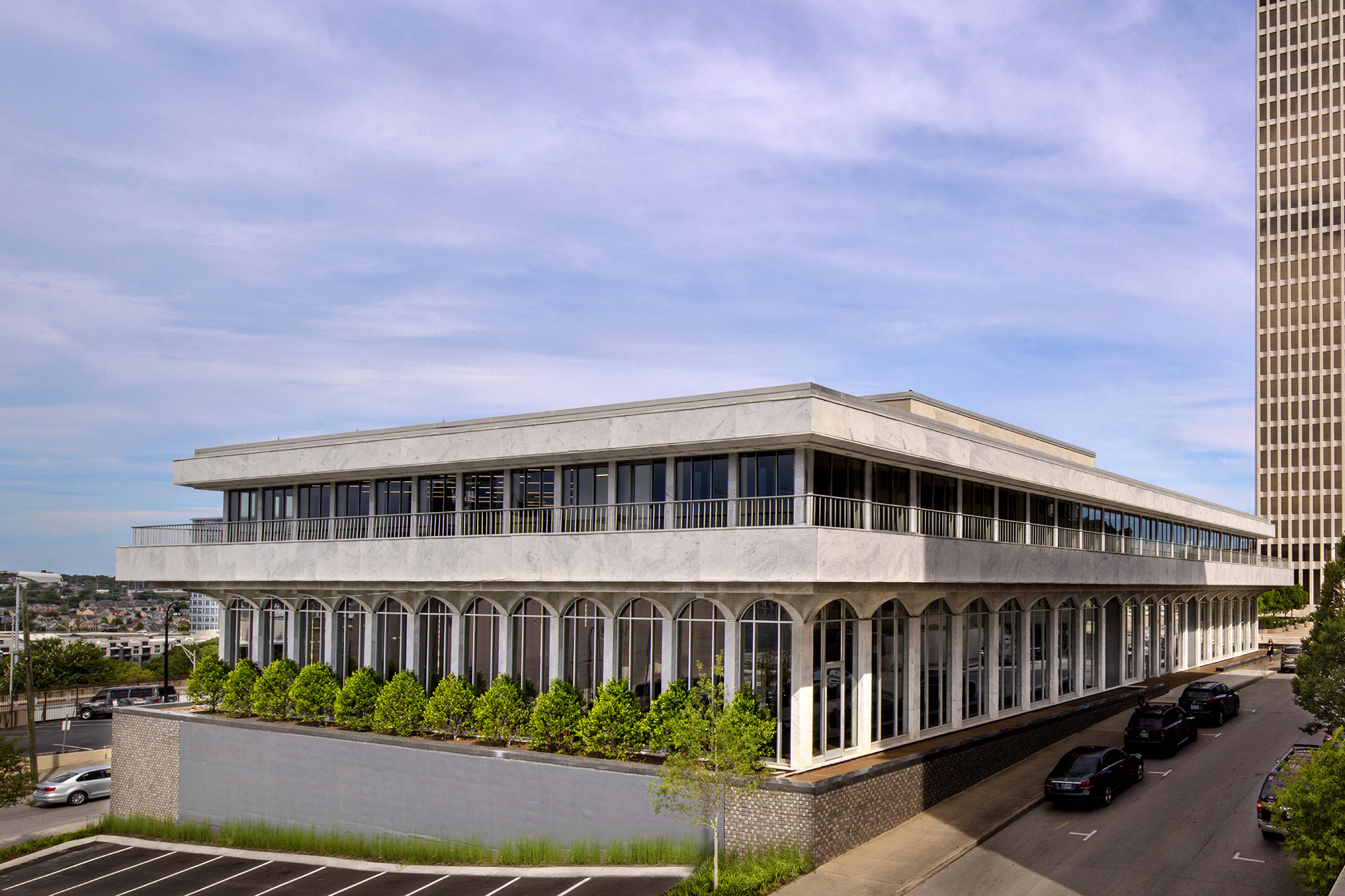
Photo by Eric Laignel; courtesy of Guardian Glass
The 225 Polk retrofit project in Nashville replaced the original glass with high-performance glazing to help improve energy efficiency as well as comfort for occupants by reducing solar heat gain.
Introduction to Carbon Dioxide
Carbon dioxide is one of several gases in the atmosphere called greenhouse gases (GHG)—that trap heat and contribute to some of the Earth’s temperature increases. Other GHGs include methane, nitrous oxide, and fluorinated gases. But carbon dioxide accounts for more than 79% of all GHG emissions emitted by the U.S. in 2021, according to the Environmental Protection Agency.3
Activities that emit carbon dioxide include burning solid waste, trees, and other biological materials, and burning fossil fuels including coal, natural gas, and oil. It’s also a byproduct of some chemical processes, including cement production. Carbon dioxide is naturally removed from the atmosphere when it’s absorbed by plants through photosynthesis.
Governments at all levels are starting to set goals and develop policies designed to reduce greenhouse gas emissions associated with the built environment. For example, Local Law 97 in New York City sets energy efficiency and greenhouse gas emissions limits on most buildings over 25,000 square feet.
At the state level, the Buy Clean California Act and the Buy Clean Colorado Act are U.S. examples of set maximum embodied carbon (global warming potential) limits for certain categories of construction materials.
At the federal level, the U.S. General Services Administration (GSA) in May of 2023 announced a six-month program to pilot interim requirements for the use of low embodied carbon construction materials in GSA projects funded by the Inflation Reduction Act of 2022.4 In December of the same year, the final requirements were published.5 These requirements set global warming potential limits for asphalt, concrete, float glass, and steel in support of the Federal Buy Clean Initiative, which promotes the use of lower carbon construction materials made in the U.S.6
In other parts of the world, governments have been advancing energy codes to reduce their nations’ overall energy use.
Designers and architects can explore methods to lower carbon emissions through both the embodied and operational carbon avenues. Often, they will organically dovetail together.
Embodied Carbon
Embodied carbon is often considered from the following perspectives, depending on the life cycle stages in question: cradle-to-gate, cradle-to-grave, and cradle-to-cradle.
From a cradle-to-gate perspective, embodied carbon refers to the carbon dioxide equivalent associated with the extraction, processing, transport, and manufacturing of a product, product family, or service.
The cradle-to-grave framework in the building industry includes everything in the cradle-to-gate time frame plus construction, maintenance, repair, and end-of-life stages.
The cradle-to-cradle perspective expands the concept of the cradle-to-grave framework to include options for material reuse and recycling.
Operational Carbon
Operational carbon refers to the amount of carbon emitted while a building is in use through day-to-day activities like lighting and operating its HVAC system—heating, venting and air conditioning–as well as the daily activities of occupants in the building.
An energy grid that relies on renewable sources rather than traditional coal or natural gas power generation can help reduce the impact of operational carbon output. Over the last several decades, new and innovative design techniques along with technology advancements have helped buildings become more energy efficient. Buildings are using less energy overall and, in many areas, the grids supplying the energy have a higher percentage of renewable sources (e.g. solar panels and wind turbines), which contributes to the reduction of the carbon emissions associated with energy generation.
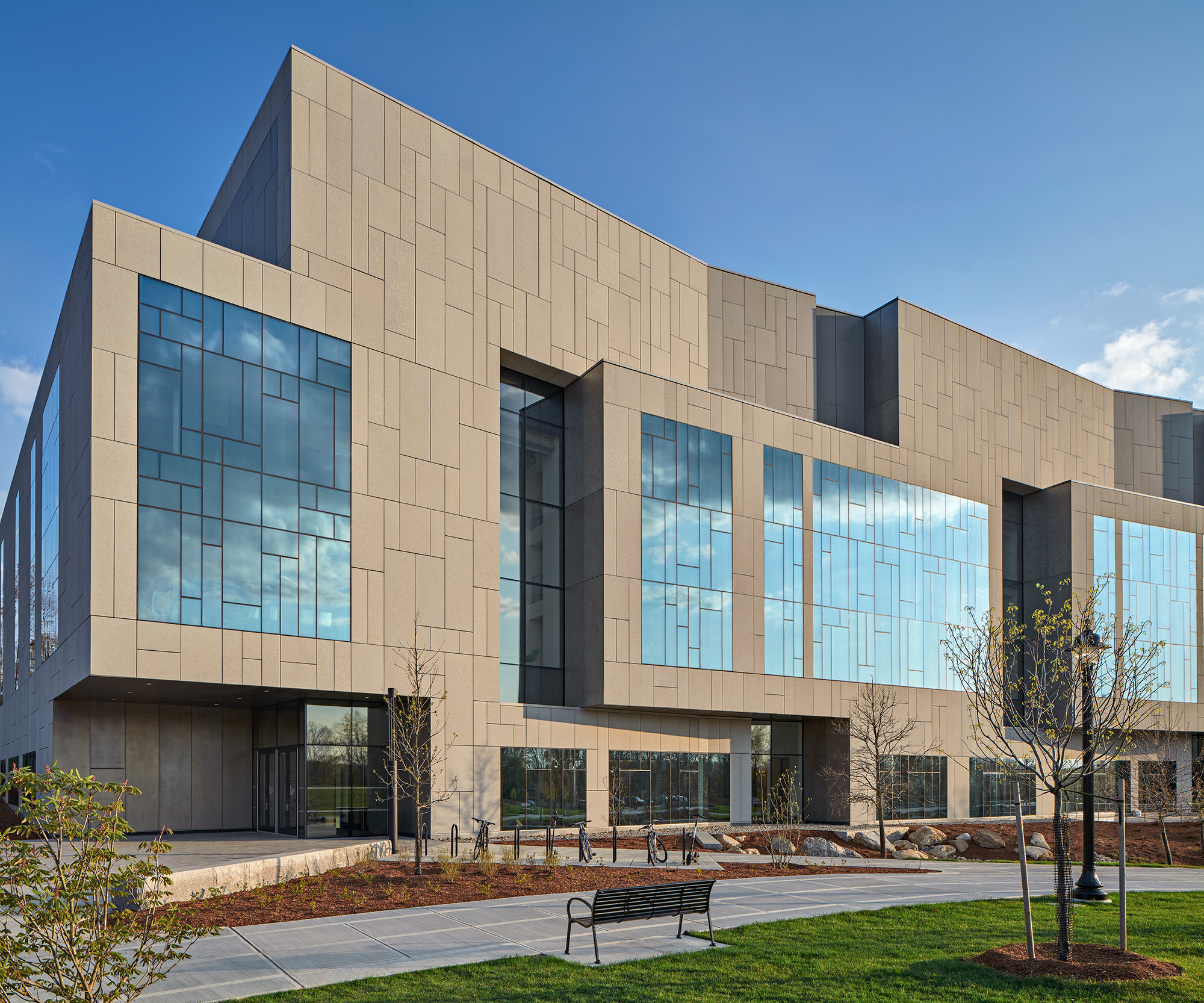
Photo by Robert Benson Photography; courtesy of Guardian Glass
Science 1 Research Center is a three-story, high-intensity academic research building dedicated to the interdisciplinary fields of material science and engineering at the University of Connecticut in Storrs, Conn. High-performance, low-E coated glass helped the project achieve LEED Gold status.
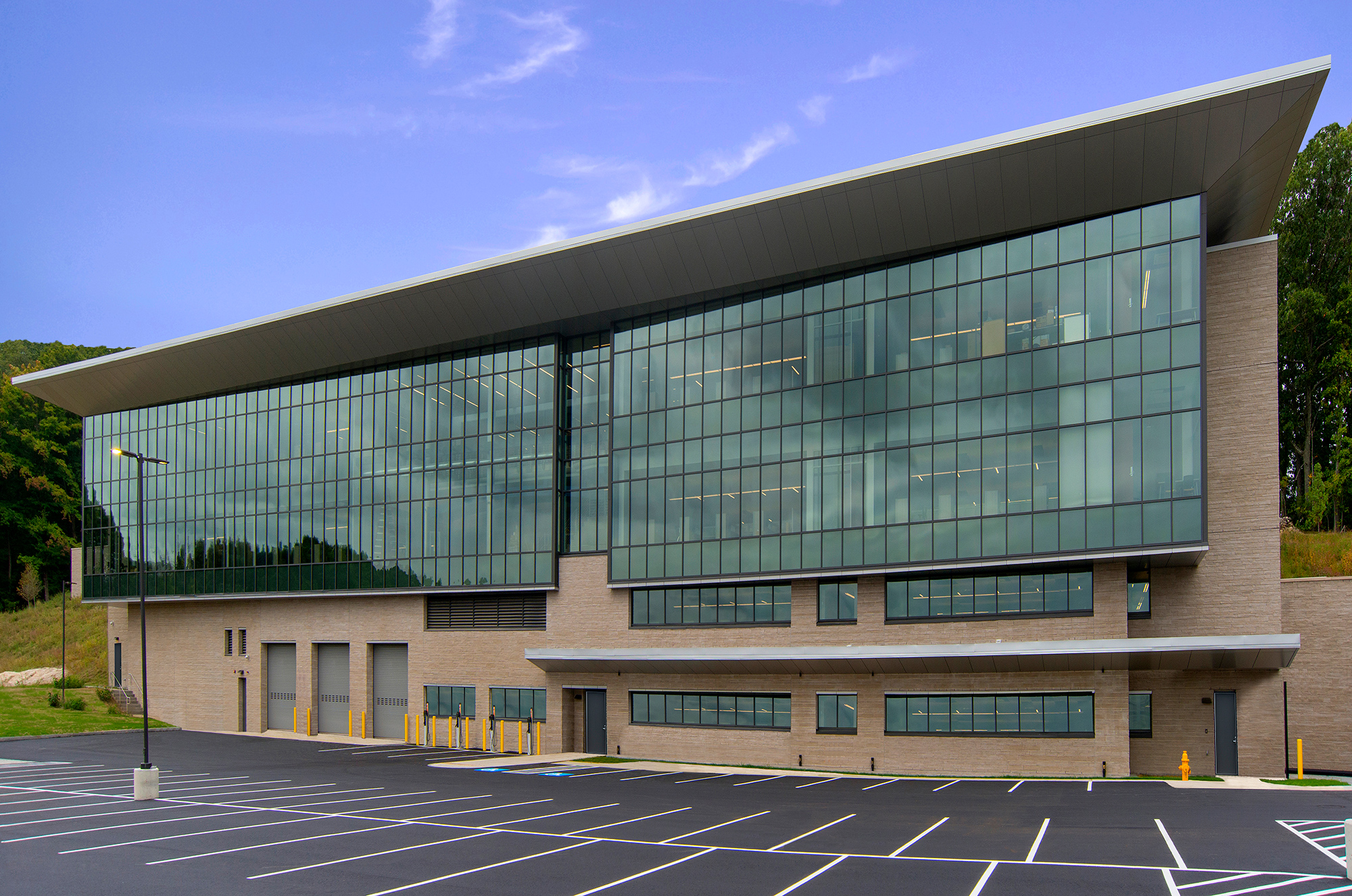
Photo by Casey McNamara; courtesy of Guardian Glass
Designed as a Net-Zero-Energy Building, the Massachusetts Department of Transportation building in Worcester, Mass. incorporates glass extensively into the exterior to allow ample natural daylighting and a modern design.
Life-Cycle Assessments of Buildings
As the name suggests, a Life-Cycle Assessment (LCA) is a way to understand the environmental attributes of a product, product family, service or even building by breaking down attributes by life stages: resources used, processing, manufacturing, distribution, the use of the completed building, and the end-of-life management.
When looking at an LCA for a building, the first stage is materials. This involves assessing the sources and quantities of the materials used in a project and how they are made, following that process from the mine to the construction site.
Next is the building process. For example, how much carbon does the construction process release into the atmosphere? This involves looking at the inputs and outputs of the construction process: energy used, waste produced, and emissions released during the building phase.
The next phase of the life cycle is the use of the completed building. This phase includes use of energy for heating and cooling, for systems like HVAC, for lighting the building, and any other day-to-day operations, as well as maintenance.
The final phase is a building’s end of life stage. What happens once the building is no longer being used? Will it be demolished? Can parts of it be recycled or reused?
The goal of an LCA is to help builders and designers understand the environmental attributes of their projects, and minimize them where possible and feasible, by the design choices made (materials, sourcing, quantities, transportation). LCAs can help you verify you’re moving towards your project or company’s environmental target. While making the LCA of a whole building needs specific knowledge and can bring complexity, collecting and reviewing independent third-party verified EPDs of the main materials selected can point you in the right direction to evaluate the embodied and operational carbon of a building.
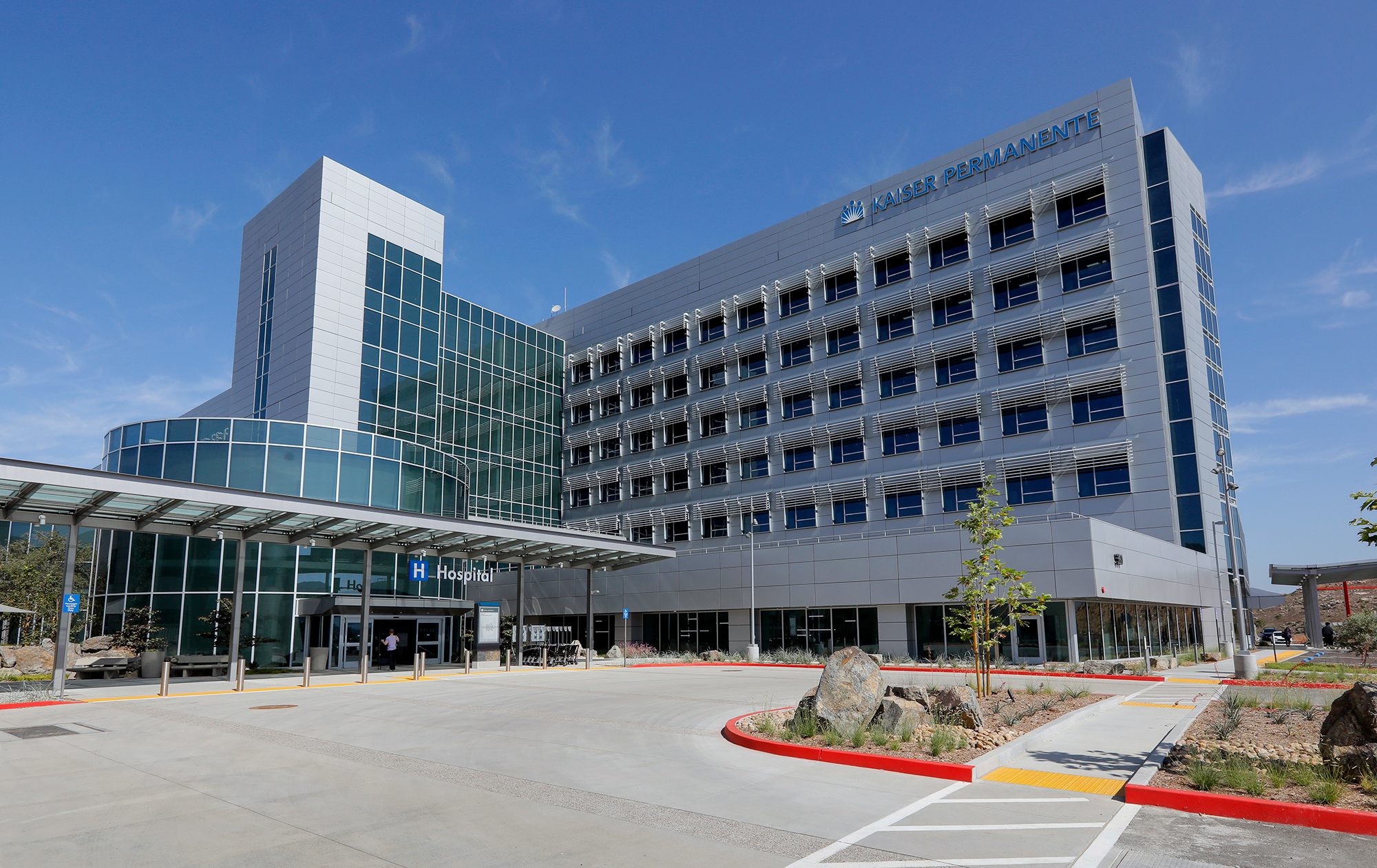
Photo by Charles F. Neuman; courtesy of Guardian Glass
With a sweeping glass facade above the entrance and matching fenestration throughout, the Kaiser Permanente San Marcos Medical Center in San Marcos, Calif., uses natural lighting to imbue the facility with biophilic elements.
Environmental Product Declarations
Environmental Product Declarations (EPDs) are a way for manufacturers to take comprehensive, third-party-verified LCAs, which are quite complex, and turn them into standardized declarations for their products.
According to the U.S. General Services Administration,7 EPDs are environmental declarations that communicate standardized environmental information about the life cycle impact of a product. EPDs are independently verified and registered documents based on industry standard product category rules.
EPDs report a specific set of environmental results, which can only be created after an LCA is conducted. Common categories include product carbon dioxide equivalent (CO2e), ozone depletion potential, potential of acidification of land and water sources, potential for eutrophication, smog formation potential, and primary energy use.8
EPDs are tools architects, builders, and other stakeholders in the construction industry can use to help them make informed decisions based on the environmental attributes of the materials and products they use. However, industry professionals utilizing EPDs should be cautious in drawing direct comparisons between reports, as there are still varying factors that could affect the data such as the timeframe used, regional differences in energy sources and regulatory standards, and general data consistency.
Growing awareness of environmental performance and the desire to make informed choices have driven the adoption of EPDs in the building sector. They’re often voluntary or encouraged through incentive programs, rather than required, though there are some exceptions.
EPDs can support various building certification systems, such as LEED (Leadership in Energy and Environmental Design) and BREEAM (Building Research Establishment Environmental Assessment Method). Some countries and regions are requiring the use of EPDs for certain products for regulatory reasons. Consumer demand has also inspired further use of the tool.
As EPDs become popularized, they are being incorporated into building standards and codes in different ways. For example, the International Green Construction Code (IgCC) is a type of construction code that has similar aims as LEED and Green Globes certifications but is implemented in a code that is legally mandated by some states, governmental agencies, and companies.
In a single project, the IgCC mandates EPDs for at least 20 different products covering more than 25% of building material costs. Requirements currently allow industry-wide EPDs in addition to company-specific EPDs, as long as they apply regionally to where the building is being constructed.
dditionally, the IgCC accepts EPDs submitted for components of assemblies, rather than the full assemblies themselves, if those components cover more than 80% of the product weight or cost. For example, a curtain wall assembly necessitates EPDs for the glass and framing, without the need for EPDs on fasteners, sealants, hardware, spacers, and any other elements of the assembly.
Read the sidebar to understand more challenges and answers to creating and procuring glass-specific EPDs.
APPLYING CARBON REDUCTION TO GLASS MANUFACTURERS
Manufacturers are working to improve resource efficiency and minimize the greenhouse gas emissions across the cradle-to-gate life cycle of their products and product families. This, in turn, reduces the embodied carbon associated with their products.
Glass Manufacturing–Embodied Carbon
Float glass production involves mixing and heating raw materials, including sand, soda ash, dolomite, limestone and cullet (scrap or broken glass) to a liquid state in furnaces at temperatures of between 2700 and 2900 degrees Fahrenheit (or approximately 1500 to 1600 degrees Celsius)9, and then floating the subsequent ribbon of glass atop a bath of molten tin. Once the ribbon has sufficiently cooled, it is transferred onto rollers and annealed to limit residual stresses. Its edges are trimmed and the ribbon is cut to the desired sizes.
The energy consumption and associated carbon emissions can be reduced at various stages of the process, including with the raw materials. For example, there are some raw material substitutions that can be considered.
Natural soda ash can replace synthetic soda ash in a batch, if economically and logistically viable. Natural soda ash, a mined material, typically has a lower embodied carbon than synthetic soda ash, a material produced through a chemical process known as the Solvay Process.
Another potential solution is replacing carbonate batch components with other raw materials. For example, manufacturers could use caustic soda, a non-carbonate material, instead of soda, a carbonate material, to help reduce the release of carbon emissions.
Using decarbonated raw materials such as calcinated lime and calcinated dolomite can help reduce the carbon emissions released during the glass melting process.
Increasing the iron content in the batch improves the glass melt’s ability to absorb heat radiation, which requires less energy for the melting process and reduces the associated energy consumption and carbon emissions.
Of course, there are trade-offs associated with switching raw materials. For example, although using higher iron content can reduce energy consumption and carbon emissions, it can also impact optical properties by reducing solar and light transmission. Similarly, before replacing carbonate batch components with other raw materials, manufacturers should evaluate the full life cycle impact of the materials and also their impacts on quality. Such trade-offs should be considered while making decisions about raw material sourcing.
The bottom line is that ensuring raw material extraction and processing is done in an ecologically and socially responsible manner can help lower the embodied carbon footprint of a product.
Better yet, increasing the use of scrap or broken glass, also referred to as cullet, in the manufacturing process reduces the energy required to melt the batch materials and the demand for new raw materials in the first place, helping conserve natural resources.
Float Glass Furnaces
As discussed in the previous section, forming molten glass requires uninterrupted extremely high temperatures. Therefore, glass furnaces require a lot of energy to operate and are a resource-intensive part of glassmaking.
A float glass manufacturing furnace typically has a lifespan of 16-20 years. After that time, it can be rebuilt from the ground up in what is known as a Cold Tank Repair (CTR).
It’s difficult to make major modifications to the furnace outside of a CTR, as the furnace is rarely, if ever, allowed to cool down. While a furnace is active, automation and the responsible use of resources are the two key aspects manufacturers can focus on to help improve its energy efficiency and reduce the system’s greenhouse gas emissions.
In a float glass manufacturing plant, there are several technologies a manufacturer may consider installing on the furnace during a CTR to help improve energy efficiency and reduce greenhouse gas emissions. Some of these technologies have already been implemented in industrial-scale plants globally and other technologies are relatively new to the industry and their feasibility is still being evaluated.
In a traditional furnace, air is used for combustion. Oxygen combustion technology replaces the air with pure oxygen through a modified geometry of the burner. This substitution reduces the amount of natural gas required to generate the same amount of heat, which is needed to melt the batch materials. By reducing the amount of natural gas consumed, the technology helps improve a furnace’s energy efficiency and decreases the associated greenhouse gas emissions.
Hydrogen-blending technology can replace a percentage of natural gas with hydrogen, using existing furnace infrastructure and burner positions. The burners use a blend of natural gas and hydrogen, which reduces the amount of natural gas consumed by the furnace.
Depending on the type of hydrogen used, this technology can also reduce some of the environmental attributes associated with the extraction and processing of raw materials phase. For example, green hydrogen—hydrogen produced via electrolysis using water and renewable energy such as solar or wind—has a lower embodied carbon value than hydrogen produced with natural gas. However, it’s important to note that implementing green hydrogen technology has both advantages and drawbacks. For example, the electrolysis process consumes large amounts of water. It is also worth noting that the availability of green hydrogen is currently limited.10
Alternate Furnace Designs
Similar to hydrogen-blending technology, hydrogen-combustion technology replaces the natural gas with hydrogen. But instead of replacing only a percentage of the fuel source, hydrogen replaces 100% of the natural gas. The main difference between the two technologies is that hydrogen combustion cannot use the existing furnace technology. A special furnace design and refractories are required. The research associations and universities working on this technology are typically using a lab scale or pilot scale furnace. By replacing the natural gas with hydrogen, this technology maximizes the reduction of the greenhouse gas emissions associated with the combustion of fuel.
It's important to note that additional research and infrastructure is needed to make hydrogen technology a viable alternative.
With the current furnace technology, direct heating with electricity—electrical boosting—can replace a percentage of the energy needed from natural gas. The furnace is modified to install electrodes directly in the furnace melt. This option takes advantage of glass’s electrical conductivity in the molten state and uses the freely moving sodium ions as charge carriers. The applied electrical voltage heats the glass with the help of the friction forces of ion immigration.
Instead of using combustion, direct electric melting relies on 100% electric melting. As with hydrogen-combustion, electrical melting uses a different furnace design. This design has been extrapolated to a production scale furnace; however, with current technological bottlenecks, electrical melting tanks are typically limited to 200 tons per day. The standard capacity of a float glass plant is around 600 to 1,000 tons of product per day. Researchers continue to look for a solution that will allow a larger scale.
By replacing natural gas with electricity, the direct electric melting technology eliminates the carbon emissions generated by the furnace combustion process. This technology also has an efficiency of approximately 95%. This is higher than the efficiency of combustion, which is typically around 50%.
As with the other technologies mentioned, the use of electricity helps reduce the amount of fuel consumed by the furnace and reduce the greenhouse gas emissions associated with the combustion of fuel. When exploring this option, the manufacturer should consider the mix of energy in the electrical grid, on-site energy options (e.g., solar) and virtual options (e.g., power purchase agreement) as the energy mix used by a furnace—whether mostly non-renewable sources, renewable sources or a mix—will influence the reduction in greenhouse gas emissions.
The list presented here is not exhaustive, and it is likely that the "furnace of the future" will use a hybrid solution, or it might use a technology not discussed here or that has not yet been discovered.
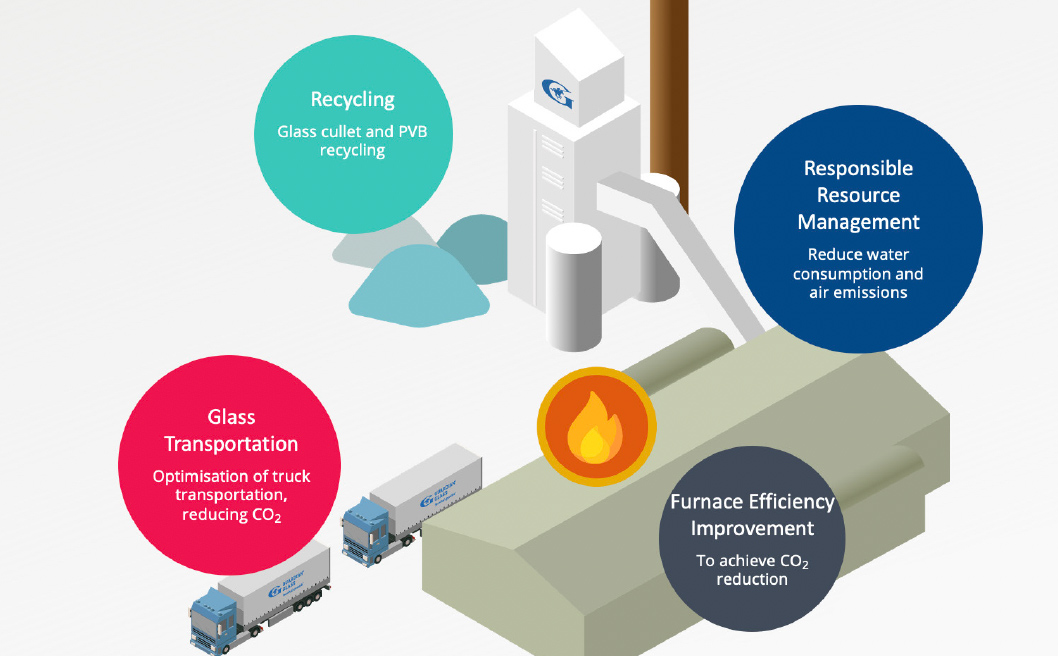
Graphic courtesy of Guardian Glass
Potential solutions to help reduce embodied carbon within a float glass plant include cullet recycling, optimizing transportation, reducing water consumption, and improving furnace efficiency.
CULLET, RECYCLING, AND REDUCING EMBODIED CARBON IN GLASS
There are a few other parts of the glass-making process in which greenhouse gas emissions can be reduced, including transportation and the end-of-life phase of glass: recycling.
Transportation
The greenhouse gas emissions associated with the transportation of raw materials to a glass plant are relatively small when compared to raw materials extraction and processing and the float glass manufacturing process, which are more energy intensive.
But that ratio could change over time as the environmental attributes associated with materials extraction and processing and with the manufacturing are reduced. Both the distance and mode of transportation should still be considered when evaluating ways to reduce a product’s embodied carbon.
Reducing Carbon Emissions with Cullet
One of the primary ways float glass manufacturers can minimize the use of virgin raw materials, save energy, and reduce greenhouse gas emissions is the use of cullet, which is broken or rejected glass, in the process. The three primary types of cullet are internal, pre-consumer, and post-consumer.
Internal cullet refers to broken or rejected glass, often from defects discovered in a manufacturing facility through quality control.
Pre-consumer cullet is broken or rejected from the processing of glass before it goes in a building. That means it’s coming from a process other than float, usually from internal processing or an external source such as a glass fabricator.
End-of-life glass from an external source such as project demolition, retrofits, and other sources is called post-consumer cullet.
Benefits of Cullet
In the float glass manufacturing process, the direct emissions associated with the furnace are the largest contributors to a product or product family’s cradle-to-gate embodied carbon. In a traditional gas-fired furnace, approximately two-thirds of the carbon emissions are generated from the combustion of gas and one-third are from the melting of carbonate batch materials. By using glass cullet, a float glass manufacturer reduces embodied carbon in two ways.
The first way is by reducing the energy needed to convert the raw materials into molten glass during the melting reaction. The energy required to melt cullet is lower than the energy required to melt raw batch materials such as sand, soda ash, and dolomite. Lowering the melting energy helps reduce energy consumption and the associated greenhouse gas emissions. According to a 2019 research report, for every 10% of cullet used on average, the melting energy demands are reduced by up to 3%, and the carbon emissions are reduced by approximately 3.6%.11
The second way cullet helps reduce embodied carbon is by minimizing the amount of carbonate materials consumed in the batch. Soda ash and dolomite are in the carbonate form when melted, which means carbon is released during the chemical reactions that occur during the manufacturing process. Reducing the volume of these materials by increasing the percentage of cullet in batch helps reduce the associated carbon emissions. Additionally, having already been through the mineralization process, cullet melts at a much lower temperature than the raw materials, which helps improve the energy efficiency of the process.
As with raw materials, transportation must be considered when working with cullet. Most of the pre-consumer cullet from float glass processing/finishing and insulating glass production (e.g. clear glass offcuts) is currently not sent to float glass recyclers and is instead used in other industries besides float glass. A lot of pre-consumer glass cullet, especially from specialized and well-organized glass processors, can be and is in some cases directly picked up by glass manufacturers when delivering glass and taken directly back to the float glass manufacturer. Increasing direct cullet supply from glass processors to glass manufacturers will help ensure it is reused to produce float glass and can reduce additional transportation.
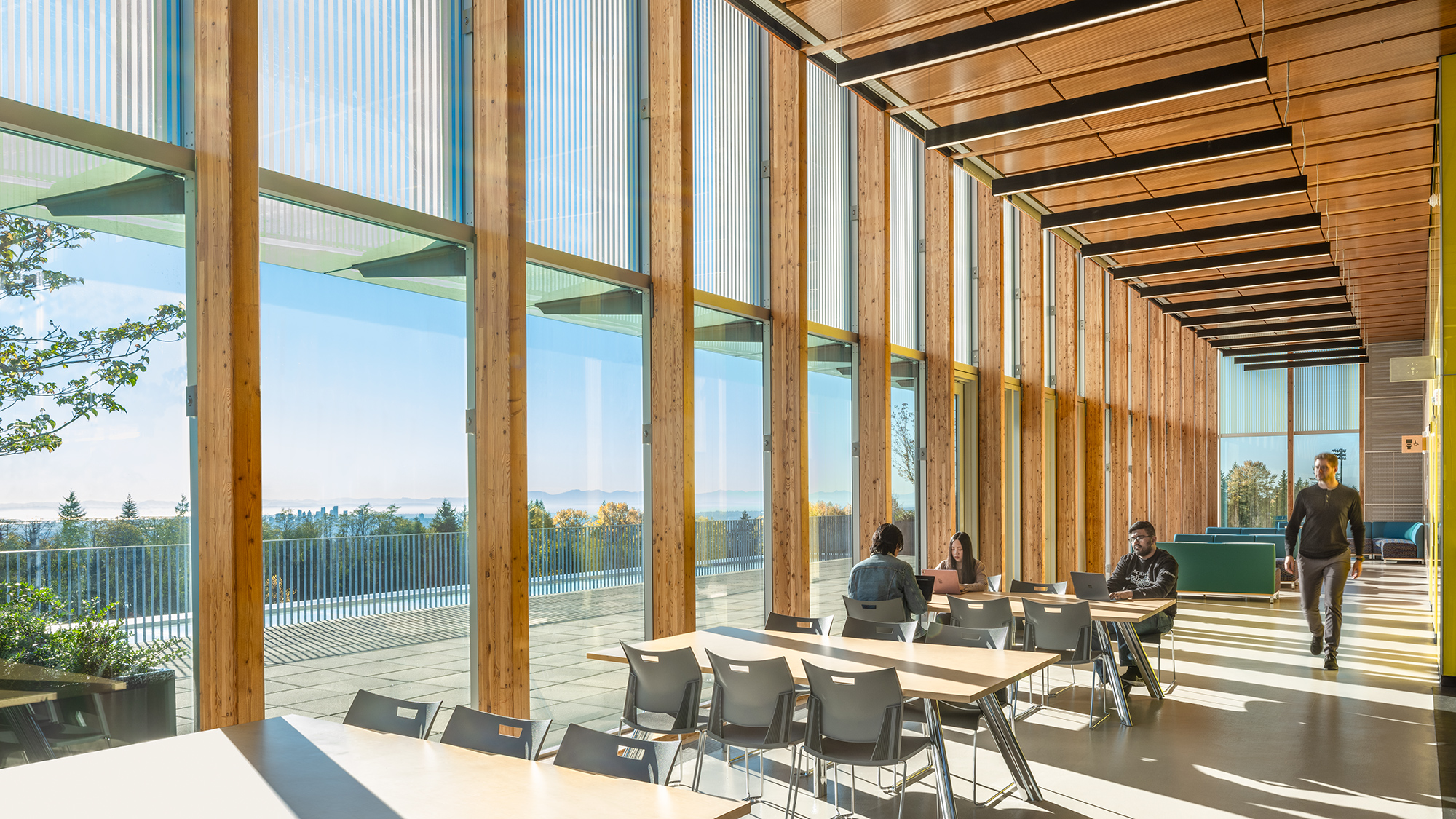
Photo by Michael Elkan; courtesy of Guardian Glass
The LEED Gold Certified Student Union Building at Simon Fraser University in Burnaby, British Columbia, Canada includes oversized windows with sweeping views to specifically improve a sense of mental and physical well-being for students.
Trade-offs of Cullet
As with the raw materials discussed in section four, choosing a cullet may come with some trade-offs. Incorporating cullet can help enhance the environmental attributes associated with the extraction and processing of raw materials and the manufacturing process, but it’s important to note they could increase the emissions associated with other life cycle stages such as transportation of the raw materials to the plant by increasing the distance traveled or changing the transport mode.
A “what if” analysis in an LCA model can help designers understand how changing different batch materials affects the embodied carbon of a product and other environmental indicators such as acidification potential, eutrophication potential, eco-toxicity potential, and water consumption.
CONCLUSION
If we only look at the numbers, the most efficient passive designs wouldn’t feature glass at all—only solid insulated structures, with no views or natural light. Unsurprisingly, most people wouldn’t want to live or work there which, ironically, means those mythical designs do not consider all aspects of stewardship.
Designers must consider many perspectives: that of the clients, building occupants, neighbors, and community members, as well as the less-visible interested parties like construction workers and those who work in raw material extraction.
To effectively take into account all points of view, both the embodied and operational carbon outputs of construction need to be considered.
Environmental product declarations can help architects make informed decisions about sourcing products, choosing manufacturers, and designing structures that meet their stewardship goals.
SOURCES
1 https://www.usglassmag.com/glass-related-construction-activity-remains-elevated/
2 https://worldgbc.org/advancing-net-zero/embodied-carbon/
3 https://www.epa.gov/ghgemissions/overview-greenhouse-gases
4 https://www.gsa.gov/about-us/newsroom/news-releases/gsa-pilots-buy-clean-inflation-reduction-act-requirements-for-low-embodied-carbon-construction-materials-05162023
5 https://www.gsa.gov/system/files/Glass%20-%20GSA%20IRA%20Low%20Embodied%20Carbon%20Requirements%20%28Dec.%202023%29_508.pdf
6 https://www.sustainability.gov/buyclean/
7,8 https://sftool.gov/plan/402/environmental-product-declarations-epds
9 https://glassforeurope.com/continuous-energy-supply-is-essential-for-the-flat-glass-industry/
10 https://www.energy.gov/eere/fuelcells/hydrogen-production-pathways
11 https://www.irbnet.de/daten/kbf/kbf_e_F_3202.pdf
12 https://www.energy.gov/management/build-america-buy-america
Andrew A. Hunt is Vice President of Confluence Communications and specializes in writing, design, and production of articles and presentations related to sustainable design in the built environment. In addition to instructional design, writing, and project management, Andrew is an accomplished musician and voice-over actor, providing score and narration for both the entertainment and education arenas. www.confluencec.com