View course on architecturalrecord.com »
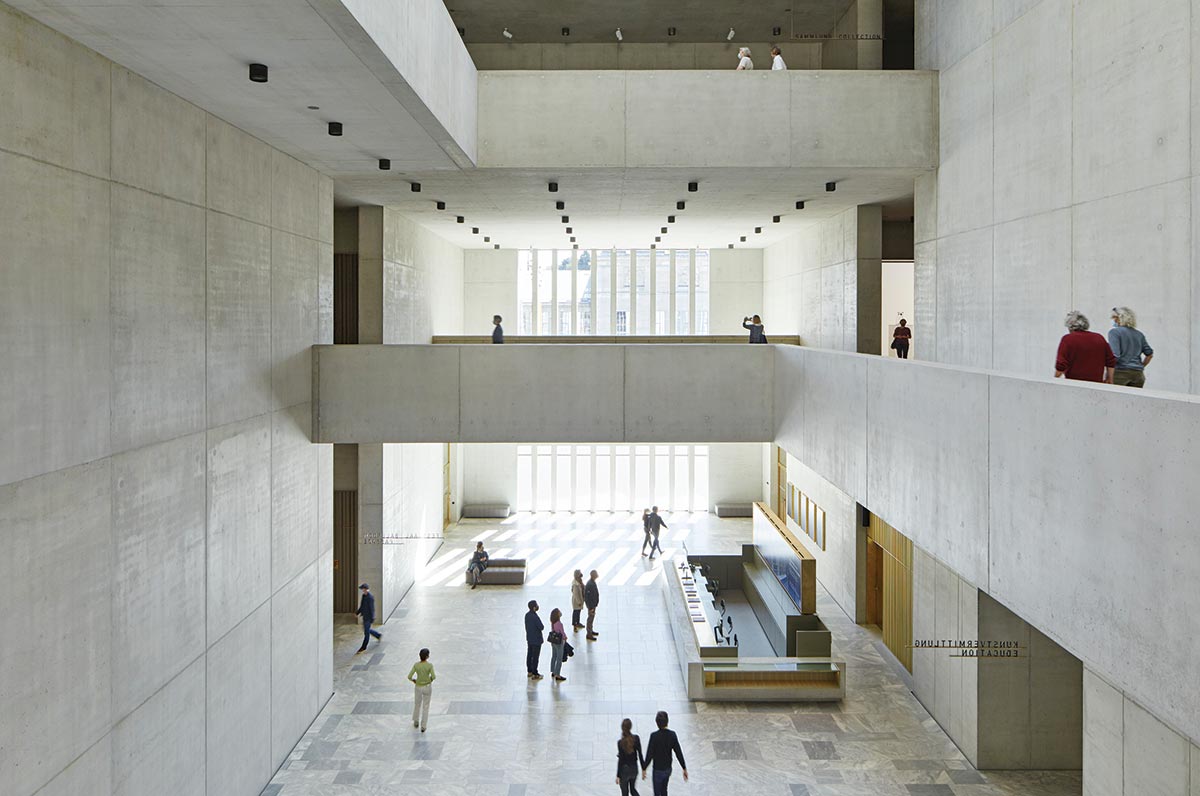
The construction industry is the elephant in the room when it comes to emissions and pollution. It is estimated that nearly half of all annual global CO2 emissions result from the built environment. Building operations account for roughly half of that, with embodied carbon (the carbon associated with building-materials extraction and manufacturing and the construction process) making up the rest. Cement and iron and steel production, the bedrock of contemporary construction, alone contribute nearly 6 billion tons of CO2 on an annual basis. However, such huge environmental footprints, which partially result from waste-heavy and energy-intensive linear supply chains, need not be a given and can be substantially reduced through the reuse and recycling of building materials, also known as circular sourcing. According to the Ellen MacArthur Foundation, approximately 15 percent of building materials are wasted during the construction process, and just 20 to 30 percent of demolition waste is reused or recycled. A number of firms within the AEC industry are seeking to remedy that paradigm through new sourcing protocols and material-tracking software.
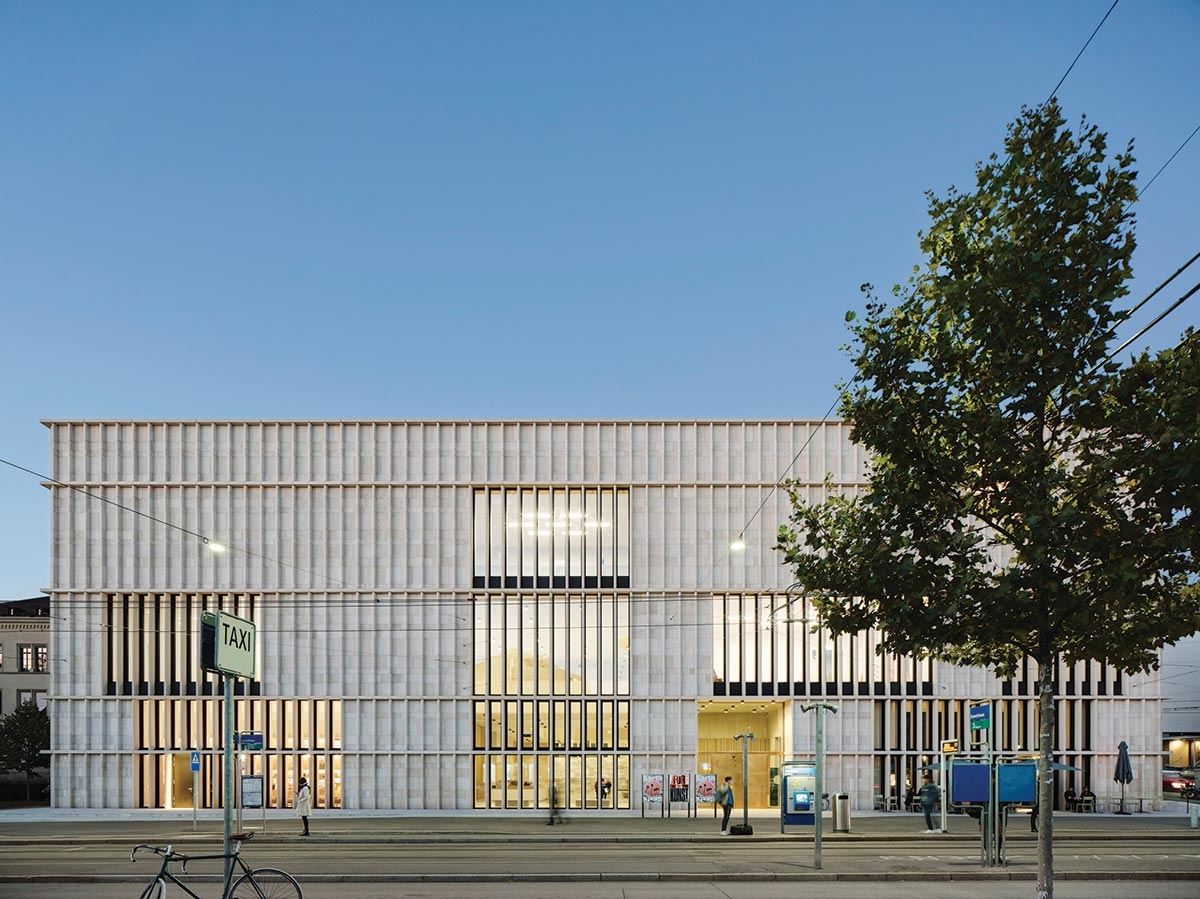
© NOSHE
THE CONCRETE in David Chipperfield Architects' Kunsthaus Zurich contains at least 25 percent recycled aggregate, with some areas containing as much as 50 percent.
Cornell University’s Circular Construction Lab, an interdisciplinary research unit at the College of Architecture, Art, and Planning, is investigating and applying technologies, methods, and strategies that support a transition from a linear model of material consumption to a circular economy. Founded in 2020, the Lab is developing software to measure the potential for circularity in the early-design phases of building projects and is conducting ongoing research into the benefits of deconstruction and waste diversion.
Felix Heisel, director of the Circular Construction Lab, explains that the aim is to develop technologies that classify the material content and circularity potential of existing buildings, supporting the reuse and recycling of these resources at their highest utility and value. But the lab is also looking to the future. “We ask how a building can be designed and built differently, so that it foresees and allows for disassembly and the reuse of materials at the end of service.”
The Catherine Commons Deconstruction Project—a collaborative effort of the Circular Construction Lab with the nonprofit organization Finger Lakes Reuse and the architecture firm Trade Design Build—puts those concepts into real-world practice. The project resulted from the development of 300 new housing units just south of the Cornell campus, which required the demolition of 11 early 20th-century residential structures. The team, in partnership with the Seattle-based Deconstruction Institute, convinced the developer to salvage nonstructural elements from 10 of the buildings and completely deconstruct the last one. Over the course of a week in January 2022, a crew of eight workers painstakingly cut the roofs, walls, and floors into “panelized” sections that were then loaded onto a flatbed truck and delivered to a nearby warehouse for processing. Since that time, over 50 community members and small-scale contractors have signed up to purchase many of the materials, including oak flooring or structural timber.
The Lab is working on a report based on that experience, with the hope that the lessons learned will be scalable in other cities in the region and beyond. It so far has calculated that the structural timbers of the fully deconstructed house translated to over 13 tons of embodied carbon diverted from landfill.
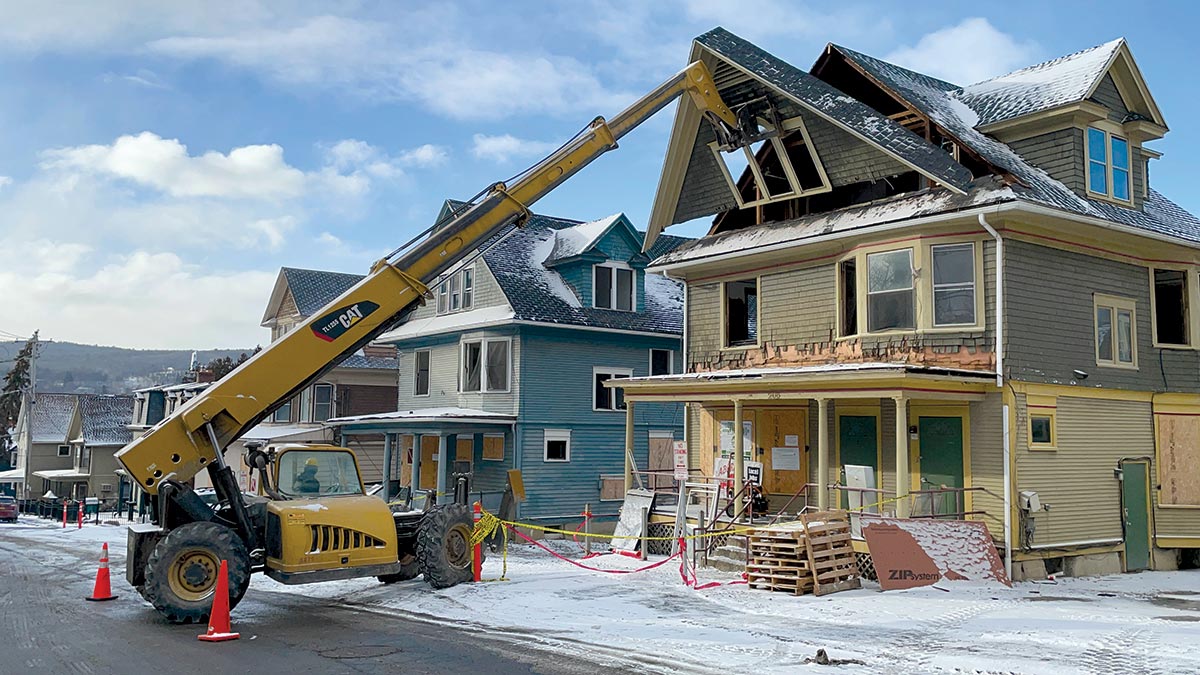
Photos courtsey of FELIX HEISEL AND ALLEXXUS FARLEY-THOMAS
Cornell University's Ciruclar Construction Lab and its partners salvaged materials from 11 residential structures in Ithaca, New York, slated for demolition.
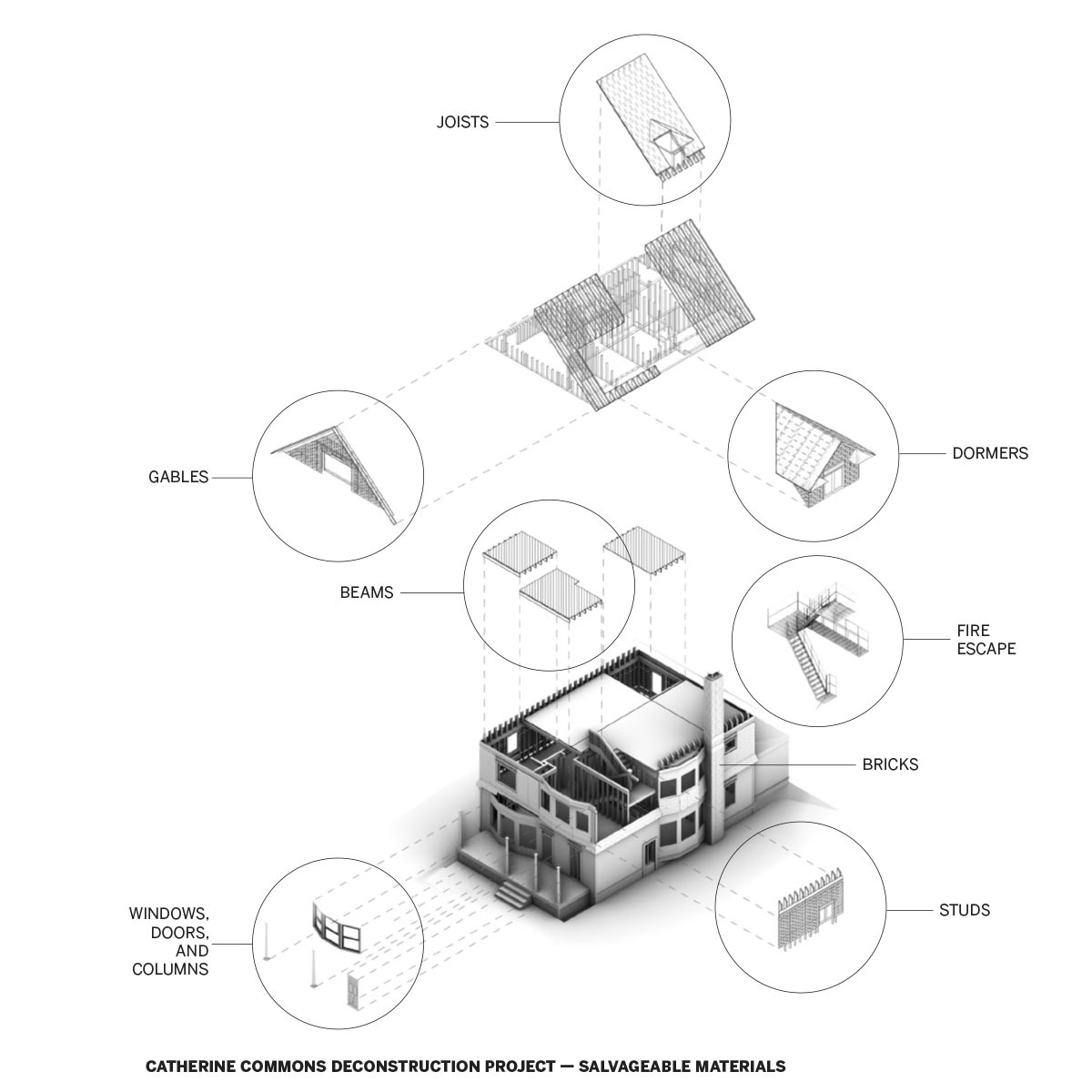
Buro Happold, the international engineering firm, is also placing the issue of circular construction front and center in its methodologies and project management. This includes a life-cycle analysis integrated with the procurement process and the assessment of environmental product declarations (EPDs), which provide information on a product’s impacts, such as global-warming potential and water pollution. According to Buro Happold senior sustainability consultant Luke Lombardi, EPDs are becoming more prevalent and accessible through platforms like the Embodied Carbon in Construction Calculator, or EC3, a database and software that together quantify the embodied carbon of construction materials. Lombardi says that the firm is also examining sustainability and circular construction through the lens of health, equity, and forced labor, with tools like health product declarations, Autocase’s Building Environmental Justice Tool, and the Design for Freedom Toolkit—a transparency initiative created by the Grace Farms Design for Freedom Foundation, to help AEC professionals source forced-labor-free materials.
The engineering firm, through its computational-design group, is also developing its own software to place new projects on the path towards greater circularity and sustainability. One such tool applies material health metrics to building models using databases like the one maintained by the Living Building Challenge (LBC) Red List—which identifies “worst in class” chemicals prevalent in building products known to pose risks to human health—or Mindful Materials.
One project in which these ideas and tools were put into action is the Frederick Fisher and Partners Architects–designed Santa Monica City Hall East, for which Buro Happold provided integrated engineering and sustainability services. The California building wrapped up construction in 2020 and is on track to achieve LBC status. Among the stringent certification program’s requirements are net zero energy and water and the vetting of all materials to ensure they meet the Red List criteria, which increases the likelihood of their recycling. The team also developed a deconstruction plan for the project, which has a projected 100-year lifespan, to ensure that it will meet their circularity goals.
For Boston-based architecture firm Dyer Brown, adopting a more sustainable approach to design and construction required a similar rethinking of both adaptive reuse and material sourcing. The firm is now working with clients to establish waste-reduction and material-circularity targets, an objective recently manifested in a 5,000-square-foot spec office space, in a circa-1970 commercial tower in Boston’s financial district that was recently renovated for a recurring client, CBRE Group. Dyer Brown was able to salvage and donate existing millwork to Boston Building Resources, a provider of new and used home-improvement items. All the ceiling and carpet tiles were palletized and shipped back to the original manufacturers to be recycled into new ceiling and carpet products. The design of the refurbished offices also kept circularity in mind, principally by opting for finishes from manufacturers with take-back programs. Dyer Brown sustainable-design leader Laurel Christensen emphasizes that architects should talk to their manufacturers representatives. “Let them know this is a priority and a selection criterion for you and your firm; your power and influence can go a long way to making the case for a manufacturer to invest in sustainability and circularity.”
Gensler is no stranger to projects of great scale, and the global behemoth’s Climate Action and Sustainability–practice objective of making every building in their portfolio net zero carbon by 2030 could have significant implications for the industry at large. That depends on strategizing with large organizations on defining their environmental and climate-related goals, the modeling of operating-carbon footprints across their portfolios, and adding value through material life-cycle assessments. The firm has also launched a rigorous set of guidelines for materials specified in all their projects. “The first phase of this effort is under way, where any two batches of materials, such as certain types of gypsum board or nonstructural metal framing, will be required to have EPDs associated with them,” says Amanda Carrol, a Gensler principal and co-managing director of the New York office. To support this effort, the firm’s New York product-development and design-resilience leaders have created a series of 20 category-specific prescriptions detailing the preferred reporting format for embodied carbon and other sustainability credentials for its regular vendors. The office has also launched its own “Materials Hub”—an initiative that aims to reduce the firm’s inbound volume of samples and the accompanying carbon emissions that go into manufacturing and transporting them to the office.
Currently, the firm is applying those principles to the interior design of the COOKFOX Architects–led Google headquarters at St. John’s Terminal, in Manhattan. The 1.3 million-square-foot project is being partially fitted out with recycled construction waste, such as scrap gypsum board diverted from landfill, sent back to the manufacturer, and repurposed as new gypsum board. As of April 2022, the project had used 200 tons of recycled materials.
Outside the United States, municipal and national governments are taking the lead in pushing for the greater use of recycled material in architecture and design. Take Switzerland, where the government has mandated that a quarter of the aggregate in concrete must be demolition waste for it to be considered recycled. The city of Zurich is incorporating reused materials in all of their new public buildings, such as the David Chipperfield Architects–designed extension to the Kunsthaus Zurich, opened in Fall 2021 (RECORD, December 2021). Nearly all of the museums’s concrete contains at least 25 percent recycled aggregate, with some parts utilizing as much as 50 percent.
In Oslo, similar ambitions are being rolled out in projects such as the Mad Arkitekter–designed KA13. The 46,000-square-foot office-building renovation and expansion, completed in 2021, is Norway’s first project to incorporate circular solutions at a large scale, with an estimated 80 percent of building materials being recycled, including reused windows, facade tiles, and hollow-core concrete slabs, among other items. For the design team, one of the great challenges was locating reused building materials in the absence of a comprehensive marketplace for buying and selling such components. To solve that quandary, Mad Arkitekter created its own network to source those materials from more than 25 different sites. The project was also designed to be disassembled by, for example, bolting rather than welding steel structural elements.
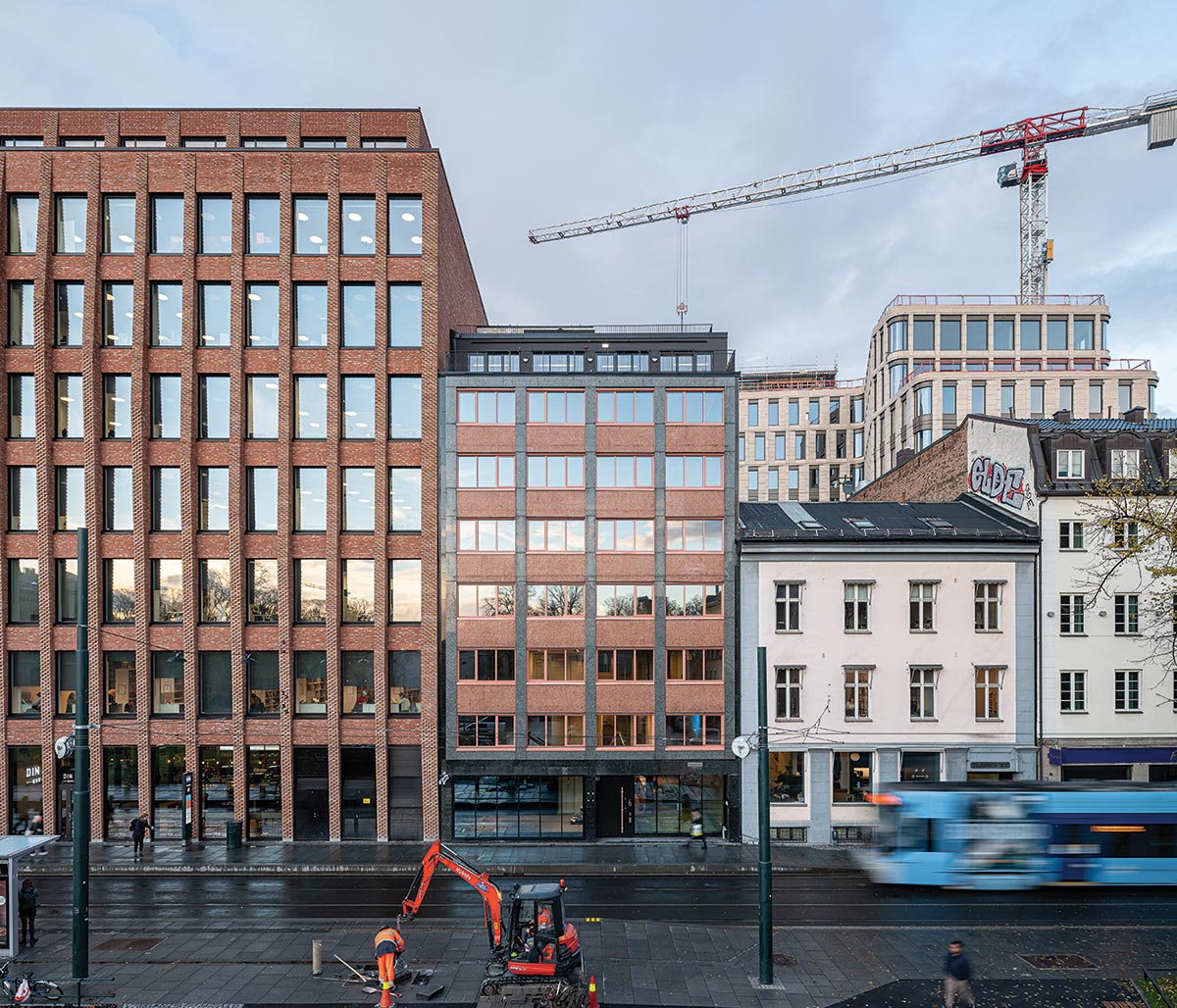
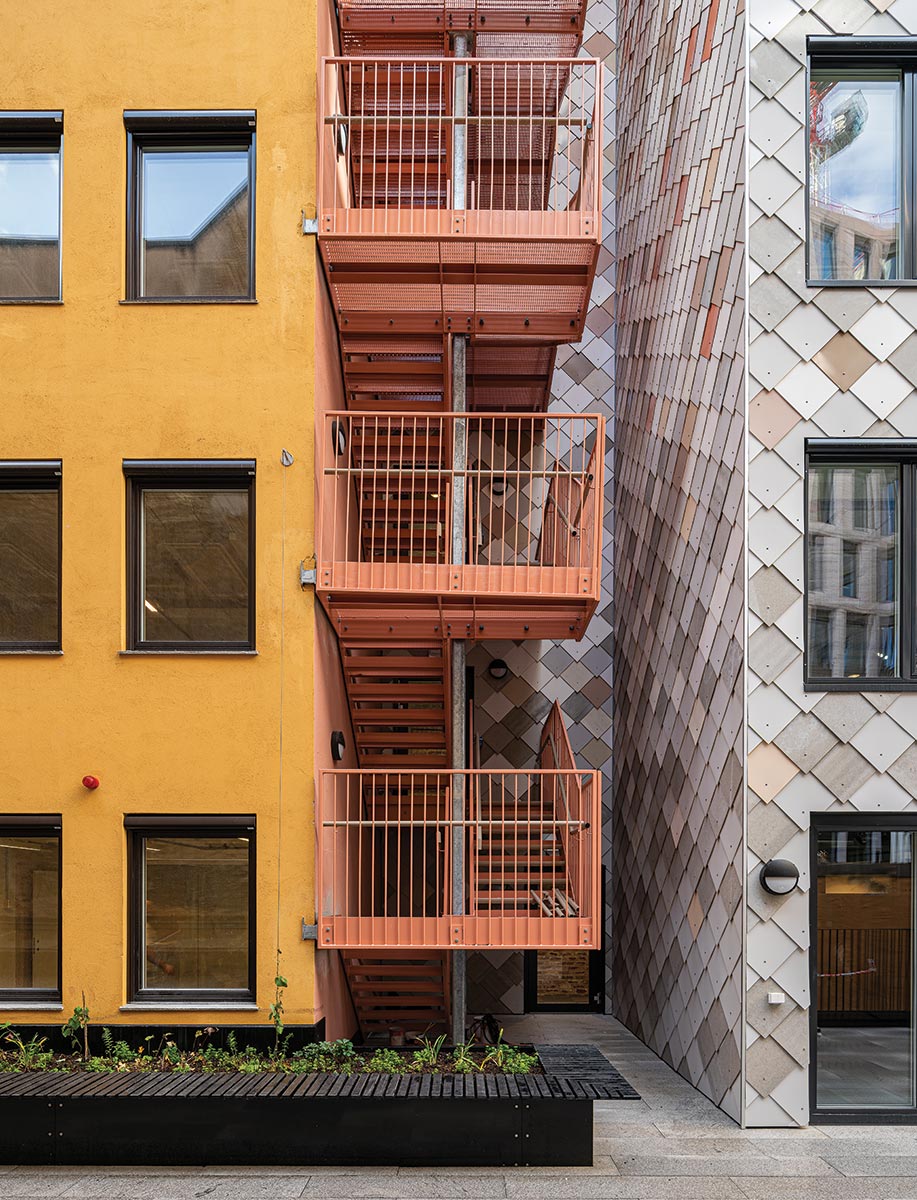
Photos courtesy of KYRRE SUNDAL
EIGHTY PERCENT of the materials in the 46,000-square-foot expansion and renovation project KA13 (top), in Oslo, are recycled, including facade tiles (bottom).
And, in London, mayor Sadiq Khan recently published a set of planning guidelines that require new developments to produce whole-life-cycle carbon and circular-economy statements that must demonstrate how a new development will adopt strategies to aid the transition to a circular built environment, provide numerical targets for the monitoring of waste and recycling, and lay out opportunities to save resources and materials.
While firms can embed a circular approach into their design practices and develop protocols and tools to support that effort, there is also an emerging set of software providers working in this area. Take Concular, for example—a Berlin-based software platform that allows practitioners to digitize materials for both new and existing buildings and, with the help of AI technology, measure their embodied carbon. The platform also serves as a marketplace connecting would-be buyers with building materials. The software can be used via smartphone and 3D scans and, in a matter of hours or days, can create an appraised inventory of building materials and pair them with open orders for new buildings or manufacturers. “Today, we do not know what materials are in a building when the deconstruction process begins, and that limited time frame hinders the possibilities of material reuse,” says Concular cofounder Dominik Campanella. “To avoid this bottleneck, we systemically map the materials of a building at least a year before deconstruction. This allows the demolition team to know what materials must be removed selectively and either reused or recycled.”
The software has been successfully implemented across Germany. At the Mercedes-Benz Arena in Stuttgart, Concular digitized the materials within the approximately 110,000-square-foot main stage and VIP area ahead of the scheduled refurbishment for the 2024 Euro Cup. Existing materials, such as 3,000 seats, were sold off to manufacturers and fans of the local football community. And, in Berlin, the David Chipperfield Architects–led reconstruction of the Karstadt Hermannplatz department store will rely on the software to source certain materials, including recycled natural stone.
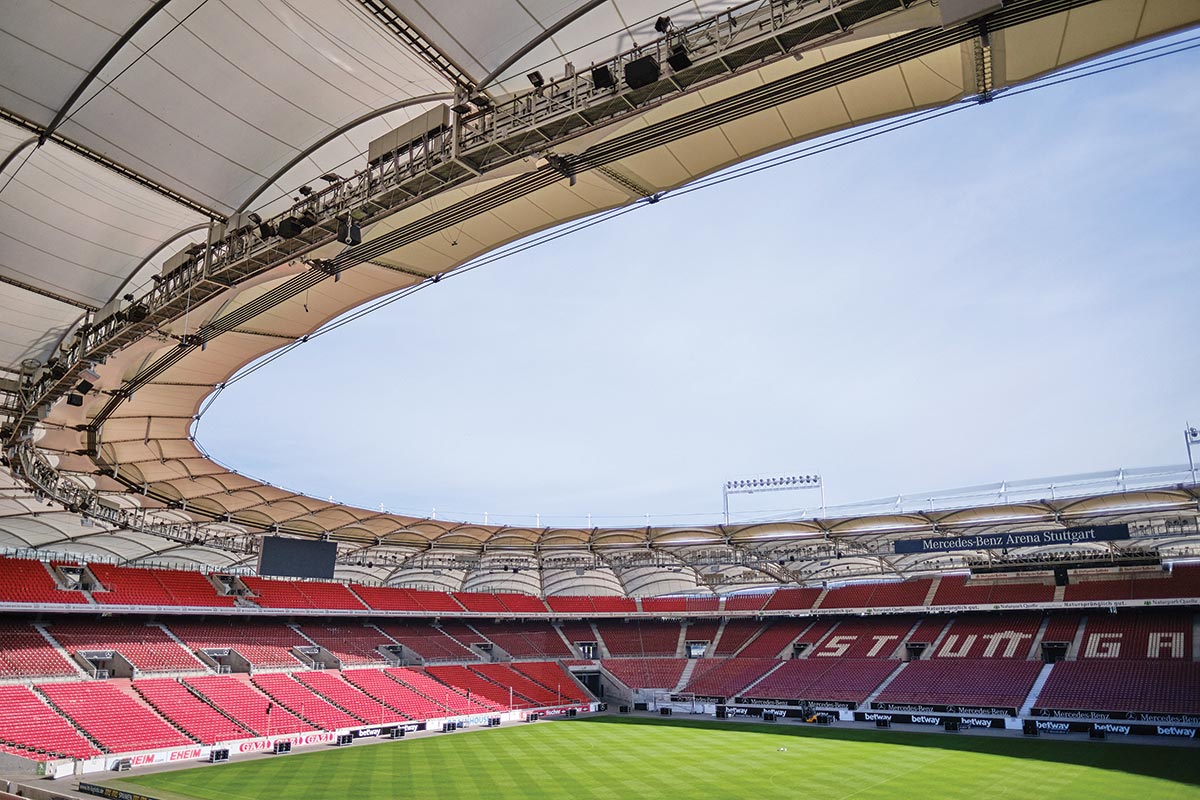
Photos courtesy of THOMAS JONES
AHEAD OF THE renovation of the Mercedes-Benz Stadium in Stuttgart for the 2024 Euro Cup, components were catalogued with the help of the digital platform, Concular.
Toxnot, a software company based in Colorado, is similarly attempting to simplify the notoriously complex global supply chain. The platform maintains a database of approximately 120,000 chemical substances and tracks 20 hazard end point ratings for all of them, such as carcinogens, endocrine disruptors, skin irritants, flammability, and environmental persistence, explains Mason Wambolt, director of business development. “So, a manufacturer can put a formulation for a specific material into the Toxnot system, and it will reveal those hazards.” Identifying toxins prior to specification increases the likelihood that materials will be repurposed.
The shift toward a more circular economy is an imperative step in reducing global greenhouse emissions and environmental pollution. That will entail preserving existing buildings, where possible, for adaptive reuse (to avoid waste associated with new construction), and the recycling of existing materials. There are plenty of obstacles to achieving such goals, but, with the proper specification protocols and material-tracking tools—and enlightened clients—firms can establish internal frameworks to plug themselves into the circular economy.
Supplemental Materials:
A Circular Economy for Buildings: Arup
Ellen MacArthur Foundation
Matthew Marani, writes about architecture and urban design and is studying city and regional planning at Pratt Institute.