
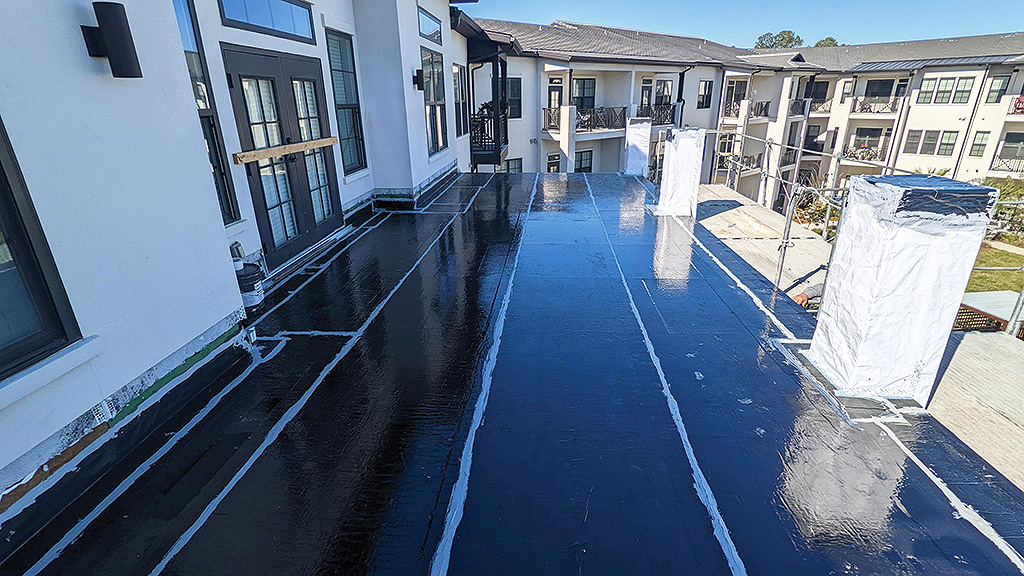
Photo courtesy of Polyguard
Wood-framed balconies are common in multifamily and hospitality projects, offering both aesthetic and functional value. However, their exposure and complexity make them especially vulnerable to moisture-related failures, underscoring the need for architects to understand effective waterproofing design strategies.
This article provides architects and construction professionals with in-depth insights into advanced waterproofing methodologies specifically tailored for wood-framed balconies. The article will cover common weak points, substrate prep, membrane and flashing installation, drainage considerations, and long-term performance enhancements, in alignment with current codes and standards. Resilient, long-term waterproofing solutions that successfully integrate with high-building envelopes are a critical necessity for modern construction, especially in multi-family, hospitality, senior living, and student housing applications. Proper specification and selection of waterproofing systems can not only ensure that balconies are durable and comfortable for occupants, but also resilient and safe.
The Challenge of Waterproofing Wood-Framed Balconies
For many residential buildings, balconies are both an aesthetic enhancement and a value-added design component. Allowing occupants access to fresh air, views, and the outdoors from the comfort of their unit is highly attractive and potentially lucrative for the building owner. However, with this attractive design feature, care must be taken to ensure they are durable, safe, and properly designed and installed. Wood-framed balconies, while economically and structurally advantageous, are prone to water infiltration due to their exposure to weather and the inherent vulnerability of wood to moisture. Wood framing can deteriorate rapidly when exposed to persistent moisture, leading to rot, mold, and structural compromise.
Wood-framed balconies are a ubiquitous feature in contemporary architecture, particularly in mid-rise multifamily residential projects, hospitality developments, and institutional housing. These exterior elements provide far more than just a space for relaxation—they contribute significantly to the building’s marketability, occupant satisfaction, and overall design aesthetic. However, their exposure to the elements, complex detailing, and structural reliance on moisture-vulnerable framing assemblies also make them one of the most failure-prone components of wood-framed construction. As such, a comprehensive understanding of balcony design, especially regarding waterproofing strategies, is essential for architects seeking to deliver safe, durable, and high-performance buildings.
Particularly prevalent in building types where cost efficiency, speed of construction, and maximizing rentable or saleable square footage are key priorities, wood-framed balconies deliver value. In multifamily residential buildings, balconies serve as highly desirable private outdoor spaces that enhance the perceived value of each unit. They often become deciding factors for prospective tenants or buyers.
In the hospitality sector, especially in mid-range hotels and resort developments, balconies enhance guest experiences by offering visual and physical access to the outdoors, improving the overall ambiance, and boosting customer satisfaction. The inclusion of balconies in such settings is frequently tied to increased room rates and longer guest stays.
Student housing is another area where wood-framed balconies see frequent use. They offer students much-needed outdoor respite in dense urban campuses or limited land area scenarios. Balconies in these buildings are often compact, repetitive, and structurally efficient—yet still demand high attention to detailing due to their frequency of use and exposure.
Another common and attractive application of balconies is senior assisted living facilities. These buildings are enhanced with the option to allow occupants access to views of the sky and nature, and the exposure to fresh air and sunshine can be both emotionally and physically important for the aging population.
Balconies are not merely aesthetic or lifestyle enhancements; they serve a multifaceted purpose that can influence a building’s performance and profitability. One of the primary drivers for including balconies is the demand for access to the outdoors. In a post-pandemic world, occupants place an even higher value on private outdoor space. Balconies offer fresh air, sunlight, and a connection to nature, improving quality of life and overall well-being. In high-rise and multifamily residential settings, they provide a space for outdoor activities such as cultivating flowering plants, herbs, and small vegetable gardens. Balconies can also be an ideal spot for attracting birds and observing wildlife. From a design standpoint, balconies break up the monotony of large facades, adding visual interest, rhythm, and articulation to a building’s envelope. They can be used to define hierarchy, enhance curb appeal, or blend in with regional architectural styles.
For building owners and developers, balconies often represent a strategic investment. While they involve additional construction and maintenance costs, balconies can boost a property’s return on investment through higher rental premiums or faster unit sales. In competitive markets, units with balconies tend to command more attention and value.
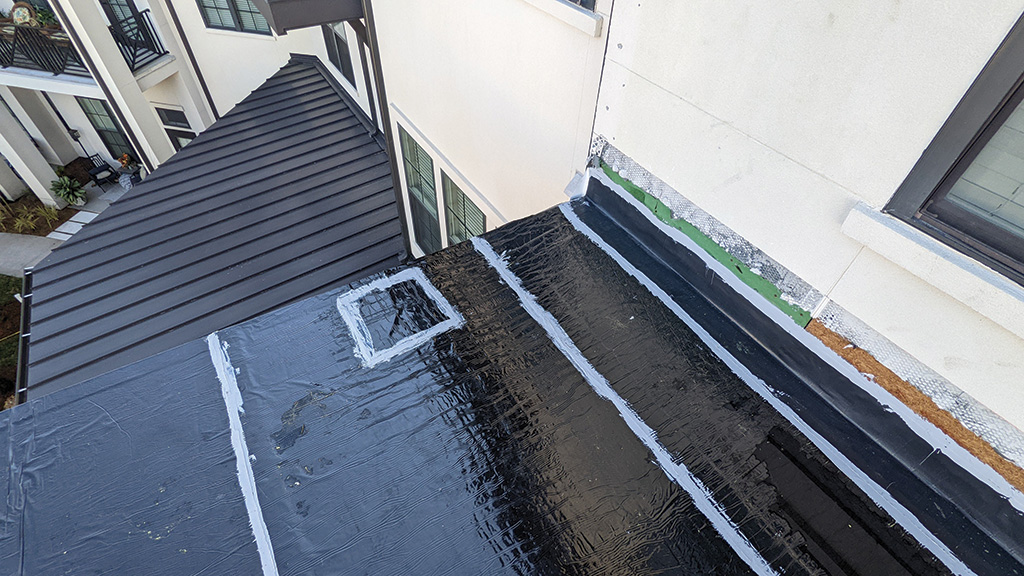
Photo courtesy of Polyguard
Balconies can offer access to the outside for occupants and allow for higher rental premiums for building owners, however, appropriate design and waterproofing must be done to ensure a durable building envelope.
Despite their widespread use, the design of these balconies must be approached with caution. The consequences of design or construction oversight can be severe, ranging from water damage and costly repairs to major structural failures with life safety implications. Balconies, particularly those framed with wood, must be treated as high-risk assemblies subject to rigorous design scrutiny. Several fundamental requirements must be met to ensure performance and durability:
- Structural Engineering: Like any load-bearing component, balconies must be engineered to support live and dead loads—including occupants, furniture, planters, and in some climates, snow accumulation. The design must also consider lateral forces, deflection limits, and long-term material performance.
- Slope for Drainage: Balconies must be sloped away from the building to promote drainage and prevent standing water. This is a basic, yet often overlooked, principle that plays a critical role in extending the service life of the assembly.
- Water Exit Strategy: Water that lands on a balcony surface must have a clear path to exit the structure without penetrating the framing system. Proper detailing of drip edges, scuppers, or integrated drainage planes is critical.
- Waterproofing: Arguably the most vital layer of protection, waterproofing membranes or coatings must be properly selected, tested for compatibility, installed, and integrated with adjacent assemblies. This includes coordination with cladding systems, flashing, and penetrations.
These elements are not isolated—they work in tandem, and a failure in any one area can lead to a cascade of problems. The balcony, as a projecting component of the building, is especially vulnerable to water-related damage because it extends beyond the protective envelope of the structure.
Typical Weak Points in Waterproofing Balcony Assemblies
Despite best intentions, balconies are often built with detailing that introduces weaknesses. Several areas are particularly prone to failure, including thresholds, rail bars, and transitions. Each of these points must be proactively addressed during design and construction, with particular emphasis on field verification and testing.
When balconies are not properly designed or constructed, water intrusion is almost inevitable. And once water gets in, the results can be devastating. Water damage typically begins with staining, swelling, or delamination of finishes. However, the real damage is often hidden behind walls or under decking, where moisture leads to wood rot, fungal growth, and mold. These conditions can affect not only the balcony structure but also adjacent units and the building’s primary structure.
If left unchecked, water intrusion can compromise the load-bearing capacity of the balcony. The deterioration of framing members, connectors, or ledger boards can reduce structural integrity, setting the stage for a potential collapse. There have been several high-profile incidents in recent years where balconies have failed catastrophically, leading to serious injuries and fatalities. These failures are stark reminders that what begins as a waterproofing issue can ultimately evolve into a life safety hazard.
Beyond the human risks, the economic impact is significant. Water-damaged balconies often require full replacement, and remediation may extend into multiple units. Legal liability, insurance claims, and code enforcement actions are common consequences of such failures.
Architects have a critical role to play in ensuring balcony assemblies are designed with durability, safety, and longevity in mind. This includes working closely with structural engineers, waterproofing consultants, and contractors to develop robust detailing, perform thorough quality assurance checks, and prioritize best practices in balcony construction. In the next section of this article, we’ll delve deeper into the specifics of waterproofing membranes, system types, and detailing strategies that can help architects safeguard their designs from failure.
Sustainable and Code Compliant
Durability is no longer a secondary consideration in building design. It is a foundational principle that intersects with performance, resilience, and risk mitigation in the design and construction of buildings. It is now a central objective that intersects with sustainability goals, life cycle cost management, and long-term asset performance. Nowhere is this more apparent than in the detailing and construction of wood-framed balconies, where environmental exposure, material sensitivity, and structural integration all converge. For architects, durability offers a clear path toward achieving multiple project priorities at once: reduced maintenance, lower operational costs, improved occupant experience, and alignment with green building goals.
A durable balcony is more than just a bonus amenity—it is a critical component of a resilient building envelope. When designed and executed properly, waterproofing systems protect not just the balcony deck but also the adjacent structure, finishes, and living spaces. This synergy between design, performance, and environmental protection elevates the role of waterproofing far beyond product selection. It becomes a strategy—one that supports health, safety, and sustainability across the life of the building.
The construction industry is under increasing pressure to deliver buildings that are not only functional and beautiful but also sustainable. Green building certifications such as LEED, WELL, and Green Globes, as well as jurisdictional mandates, have accelerated the demand for materials and systems that reduce carbon footprints, minimize waste, and support long-term energy efficiency. But sustainability is not just about energy performance or recycled content, it also includes minimizing premature material replacement due to avoidable failures. It’s also about durability—ensuring that the building performs as intended over decades, not just during its commissioning phase.
Premature failure of building components, particularly exterior elements like balconies, undermines sustainability. When balconies leak, rot, or fail structurally, they often require invasive repairs or full replacement, generating construction waste, consuming additional materials, and disrupting building operations. From this perspective, sustainable construction is inseparable from durability: a balcony that lasts 50 years with minimal maintenance is inherently more sustainable than one that needs to be replaced after 10.
For balconies, durability means robust structural design, carefully integrated waterproofing, and attention to detailing at every joint and transition. The benefits of a durable balcony design ripple outward, affecting stakeholders at every level—from occupants and property managers to owners and design professionals.
- Lower Maintenance Costs: Durable materials and properly executed waterproofing details significantly reduce ongoing maintenance demands. Sealed transitions, integrated membranes, and proper drainage all work together to minimize the risk of leaks, rot, or corrosion.
- Improved Indoor Environmental Quality: By preventing moisture intrusion, a well-designed balcony reduces the risk of mold growth, structural degradation, and poor air quality within adjacent living spaces.
- Enhanced Property Value: Balconies that maintain their appearance and performance over time add to the curb appeal and functionality of the building. This contributes directly to higher occupancy rates, rental premiums, and resale value.
- Risk Reduction: Waterproofing failures often result in liability claims, insurance disputes, and even litigation. A durable, code-compliant system mitigates these risks and improves peace of mind for all parties involved.
- Life Safety: At the most critical level, durability in balcony construction protects lives. Structural degradation due to water intrusion can lead to catastrophic failure, especially when concealed damage accumulates unnoticed. Regular inspection and early design coordination are key. Ensuring a balcony remains structurally sound is essential to occupant safety.

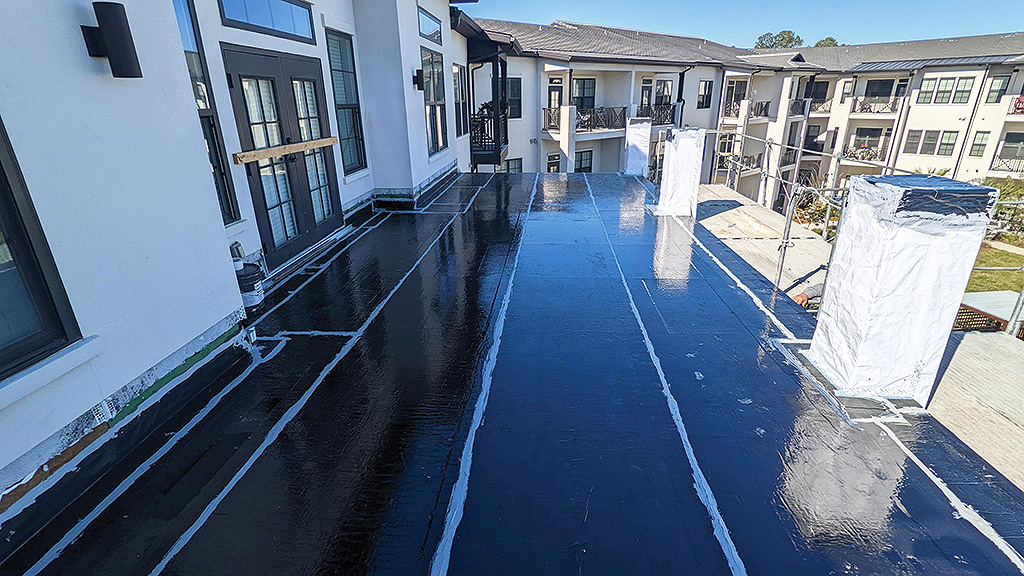
Photo courtesy of Polyguard
Wood-framed balconies are common in multifamily and hospitality projects, offering both aesthetic and functional value. However, their exposure and complexity make them especially vulnerable to moisture-related failures, underscoring the need for architects to understand effective waterproofing design strategies.
This article provides architects and construction professionals with in-depth insights into advanced waterproofing methodologies specifically tailored for wood-framed balconies. The article will cover common weak points, substrate prep, membrane and flashing installation, drainage considerations, and long-term performance enhancements, in alignment with current codes and standards. Resilient, long-term waterproofing solutions that successfully integrate with high-building envelopes are a critical necessity for modern construction, especially in multi-family, hospitality, senior living, and student housing applications. Proper specification and selection of waterproofing systems can not only ensure that balconies are durable and comfortable for occupants, but also resilient and safe.
The Challenge of Waterproofing Wood-Framed Balconies
For many residential buildings, balconies are both an aesthetic enhancement and a value-added design component. Allowing occupants access to fresh air, views, and the outdoors from the comfort of their unit is highly attractive and potentially lucrative for the building owner. However, with this attractive design feature, care must be taken to ensure they are durable, safe, and properly designed and installed. Wood-framed balconies, while economically and structurally advantageous, are prone to water infiltration due to their exposure to weather and the inherent vulnerability of wood to moisture. Wood framing can deteriorate rapidly when exposed to persistent moisture, leading to rot, mold, and structural compromise.
Wood-framed balconies are a ubiquitous feature in contemporary architecture, particularly in mid-rise multifamily residential projects, hospitality developments, and institutional housing. These exterior elements provide far more than just a space for relaxation—they contribute significantly to the building’s marketability, occupant satisfaction, and overall design aesthetic. However, their exposure to the elements, complex detailing, and structural reliance on moisture-vulnerable framing assemblies also make them one of the most failure-prone components of wood-framed construction. As such, a comprehensive understanding of balcony design, especially regarding waterproofing strategies, is essential for architects seeking to deliver safe, durable, and high-performance buildings.
Particularly prevalent in building types where cost efficiency, speed of construction, and maximizing rentable or saleable square footage are key priorities, wood-framed balconies deliver value. In multifamily residential buildings, balconies serve as highly desirable private outdoor spaces that enhance the perceived value of each unit. They often become deciding factors for prospective tenants or buyers.
In the hospitality sector, especially in mid-range hotels and resort developments, balconies enhance guest experiences by offering visual and physical access to the outdoors, improving the overall ambiance, and boosting customer satisfaction. The inclusion of balconies in such settings is frequently tied to increased room rates and longer guest stays.
Student housing is another area where wood-framed balconies see frequent use. They offer students much-needed outdoor respite in dense urban campuses or limited land area scenarios. Balconies in these buildings are often compact, repetitive, and structurally efficient—yet still demand high attention to detailing due to their frequency of use and exposure.
Another common and attractive application of balconies is senior assisted living facilities. These buildings are enhanced with the option to allow occupants access to views of the sky and nature, and the exposure to fresh air and sunshine can be both emotionally and physically important for the aging population.
Balconies are not merely aesthetic or lifestyle enhancements; they serve a multifaceted purpose that can influence a building’s performance and profitability. One of the primary drivers for including balconies is the demand for access to the outdoors. In a post-pandemic world, occupants place an even higher value on private outdoor space. Balconies offer fresh air, sunlight, and a connection to nature, improving quality of life and overall well-being. In high-rise and multifamily residential settings, they provide a space for outdoor activities such as cultivating flowering plants, herbs, and small vegetable gardens. Balconies can also be an ideal spot for attracting birds and observing wildlife. From a design standpoint, balconies break up the monotony of large facades, adding visual interest, rhythm, and articulation to a building’s envelope. They can be used to define hierarchy, enhance curb appeal, or blend in with regional architectural styles.
For building owners and developers, balconies often represent a strategic investment. While they involve additional construction and maintenance costs, balconies can boost a property’s return on investment through higher rental premiums or faster unit sales. In competitive markets, units with balconies tend to command more attention and value.
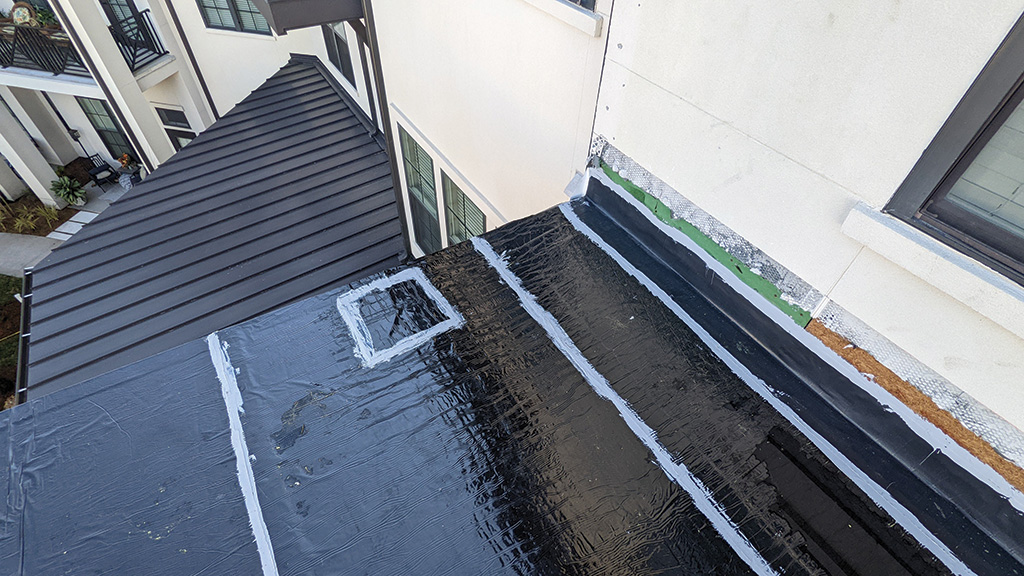
Photo courtesy of Polyguard
Balconies can offer access to the outside for occupants and allow for higher rental premiums for building owners, however, appropriate design and waterproofing must be done to ensure a durable building envelope.
Despite their widespread use, the design of these balconies must be approached with caution. The consequences of design or construction oversight can be severe, ranging from water damage and costly repairs to major structural failures with life safety implications. Balconies, particularly those framed with wood, must be treated as high-risk assemblies subject to rigorous design scrutiny. Several fundamental requirements must be met to ensure performance and durability:
- Structural Engineering: Like any load-bearing component, balconies must be engineered to support live and dead loads—including occupants, furniture, planters, and in some climates, snow accumulation. The design must also consider lateral forces, deflection limits, and long-term material performance.
- Slope for Drainage: Balconies must be sloped away from the building to promote drainage and prevent standing water. This is a basic, yet often overlooked, principle that plays a critical role in extending the service life of the assembly.
- Water Exit Strategy: Water that lands on a balcony surface must have a clear path to exit the structure without penetrating the framing system. Proper detailing of drip edges, scuppers, or integrated drainage planes is critical.
- Waterproofing: Arguably the most vital layer of protection, waterproofing membranes or coatings must be properly selected, tested for compatibility, installed, and integrated with adjacent assemblies. This includes coordination with cladding systems, flashing, and penetrations.
These elements are not isolated—they work in tandem, and a failure in any one area can lead to a cascade of problems. The balcony, as a projecting component of the building, is especially vulnerable to water-related damage because it extends beyond the protective envelope of the structure.
Typical Weak Points in Waterproofing Balcony Assemblies
Despite best intentions, balconies are often built with detailing that introduces weaknesses. Several areas are particularly prone to failure, including thresholds, rail bars, and transitions. Each of these points must be proactively addressed during design and construction, with particular emphasis on field verification and testing.
When balconies are not properly designed or constructed, water intrusion is almost inevitable. And once water gets in, the results can be devastating. Water damage typically begins with staining, swelling, or delamination of finishes. However, the real damage is often hidden behind walls or under decking, where moisture leads to wood rot, fungal growth, and mold. These conditions can affect not only the balcony structure but also adjacent units and the building’s primary structure.
If left unchecked, water intrusion can compromise the load-bearing capacity of the balcony. The deterioration of framing members, connectors, or ledger boards can reduce structural integrity, setting the stage for a potential collapse. There have been several high-profile incidents in recent years where balconies have failed catastrophically, leading to serious injuries and fatalities. These failures are stark reminders that what begins as a waterproofing issue can ultimately evolve into a life safety hazard.
Beyond the human risks, the economic impact is significant. Water-damaged balconies often require full replacement, and remediation may extend into multiple units. Legal liability, insurance claims, and code enforcement actions are common consequences of such failures.
Architects have a critical role to play in ensuring balcony assemblies are designed with durability, safety, and longevity in mind. This includes working closely with structural engineers, waterproofing consultants, and contractors to develop robust detailing, perform thorough quality assurance checks, and prioritize best practices in balcony construction. In the next section of this article, we’ll delve deeper into the specifics of waterproofing membranes, system types, and detailing strategies that can help architects safeguard their designs from failure.
Sustainable and Code Compliant
Durability is no longer a secondary consideration in building design. It is a foundational principle that intersects with performance, resilience, and risk mitigation in the design and construction of buildings. It is now a central objective that intersects with sustainability goals, life cycle cost management, and long-term asset performance. Nowhere is this more apparent than in the detailing and construction of wood-framed balconies, where environmental exposure, material sensitivity, and structural integration all converge. For architects, durability offers a clear path toward achieving multiple project priorities at once: reduced maintenance, lower operational costs, improved occupant experience, and alignment with green building goals.
A durable balcony is more than just a bonus amenity—it is a critical component of a resilient building envelope. When designed and executed properly, waterproofing systems protect not just the balcony deck but also the adjacent structure, finishes, and living spaces. This synergy between design, performance, and environmental protection elevates the role of waterproofing far beyond product selection. It becomes a strategy—one that supports health, safety, and sustainability across the life of the building.
The construction industry is under increasing pressure to deliver buildings that are not only functional and beautiful but also sustainable. Green building certifications such as LEED, WELL, and Green Globes, as well as jurisdictional mandates, have accelerated the demand for materials and systems that reduce carbon footprints, minimize waste, and support long-term energy efficiency. But sustainability is not just about energy performance or recycled content, it also includes minimizing premature material replacement due to avoidable failures. It’s also about durability—ensuring that the building performs as intended over decades, not just during its commissioning phase.
Premature failure of building components, particularly exterior elements like balconies, undermines sustainability. When balconies leak, rot, or fail structurally, they often require invasive repairs or full replacement, generating construction waste, consuming additional materials, and disrupting building operations. From this perspective, sustainable construction is inseparable from durability: a balcony that lasts 50 years with minimal maintenance is inherently more sustainable than one that needs to be replaced after 10.
For balconies, durability means robust structural design, carefully integrated waterproofing, and attention to detailing at every joint and transition. The benefits of a durable balcony design ripple outward, affecting stakeholders at every level—from occupants and property managers to owners and design professionals.
- Lower Maintenance Costs: Durable materials and properly executed waterproofing details significantly reduce ongoing maintenance demands. Sealed transitions, integrated membranes, and proper drainage all work together to minimize the risk of leaks, rot, or corrosion.
- Improved Indoor Environmental Quality: By preventing moisture intrusion, a well-designed balcony reduces the risk of mold growth, structural degradation, and poor air quality within adjacent living spaces.
- Enhanced Property Value: Balconies that maintain their appearance and performance over time add to the curb appeal and functionality of the building. This contributes directly to higher occupancy rates, rental premiums, and resale value.
- Risk Reduction: Waterproofing failures often result in liability claims, insurance disputes, and even litigation. A durable, code-compliant system mitigates these risks and improves peace of mind for all parties involved.
- Life Safety: At the most critical level, durability in balcony construction protects lives. Structural degradation due to water intrusion can lead to catastrophic failure, especially when concealed damage accumulates unnoticed. Regular inspection and early design coordination are key. Ensuring a balcony remains structurally sound is essential to occupant safety.
Integration with High-Performance Building Envelopes
Modern energy codes and green building programs require increasingly airtight and moisture-resistant building envelopes. A wood-framed balcony, which penetrates the wall assembly and is often exposed on multiple sides, can be a weak point if not carefully detailed. Proper integration means aligning air and moisture barriers between wall, floor, and balcony assemblies, ensuring continuous protection without gaps or overlaps.
This is particularly critical at interface zones—where the deck meets the exterior wall, where railing penetrations occur, or where door thresholds bridge interior and exterior spaces. Membrane compatibility, primer selection, material sequencing, and three-dimensional detailing must all be considered holistically.
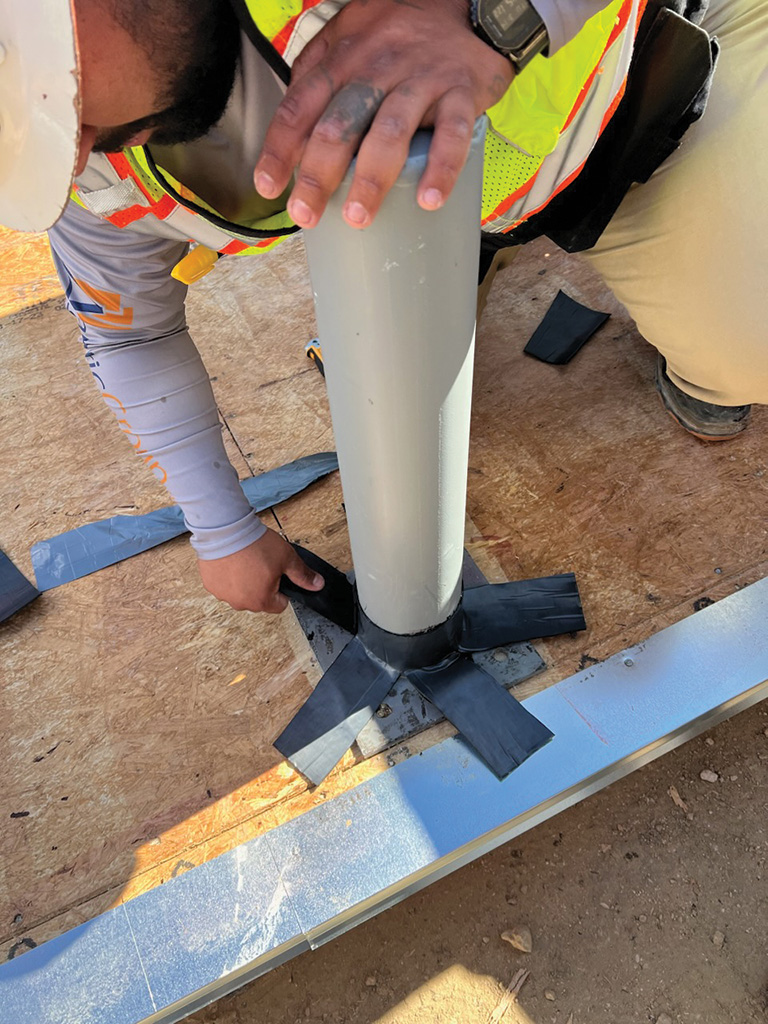
Photo courtesy of Polyguard
Penetrations, transitions, and terminations all must be properly sealed to maintain the integrity of the building envelope.
While product selection is important, the success of any waterproofing system lies in the details—literally. Industry data supports this: approximately 90% of all water intrusion issues occur in less than 1% of the building surface, and those failures are nearly always at transitions, terminations, or penetrations—locations that demand special detailing and should be verified in the field.
- Terminations: Membranes must end cleanly and securely, often transitioning to flashing or adjacent barriers. Poor termination allows capillary action or wicking to occur, compromising the integrity of the system.
- Transitions: Balconies inherently involve multiple planes and intersecting systems—floor to wall, deck to threshold, railing base to deck. These transitions must be designed in three dimensions and tested in the field.
- Penetrations: Any point where an element (e.g., railing post, utility line) passes through the waterproofing layer is a potential leak point. Pre-formed boots, sealants, and gaskets must be used and verified for long-term performance.
A successful waterproofing strategy is not just about selecting a high-performance product—it’s about ensuring that every inch of the installation supports that product’s performance. Quality control, field inspection, and proper training are vital to success.
Codes and Standards
Architects today must operate within a complex framework of building codes, energy regulations, and performance standards. For wood-framed balconies, the intersection of waterproofing, structural integrity, and energy efficiency adds further nuance to this already demanding environment.
Section C402.5.1 of the 2021 IECC (International Energy Conservation Code) mandates a continuous air barrier across the entire building envelope. This requirement directly impacts balcony design, where air and moisture barriers must be uninterrupted, even at cantilevered or recessed conditions.
Similarly, ASHRAE Standard 90.1 outlines minimum energy performance criteria for buildings. Clause 5.4.3.1 requires the air barrier to be continuous and durable, reinforcing the importance of comprehensive detailing at balconies and other envelope protrusions. Discontinuities at the balcony interface can compromise the entire thermal envelope, reducing energy efficiency and undermining sustainability targets.
Product performance is also governed by ASTM standards, which provide testing criteria and classification for waterproofing materials. Relevant standards include:
- ASTM D1970: Specification for self-adhering polymer-modified bituminous sheets used for roofing and waterproofing, often used at balcony thresholds and parapets.
- ASTM D638: Standard test method for tensile properties of plastics, relevant for evaluating the performance of certain liquid-applied membranes and flashing components used in balcony waterproofing.
Compliance with these standards ensures that materials meet minimum performance thresholds under specific conditions. However, these tests cannot guarantee success in the field; that responsibility falls on the architect and construction team through proper design, integration, and quality control.
Achieving Code Compliance Through Design Detailing
For architects, achieving compliance is not merely about product selection. It’s about understanding how systems interact—and how detailing influences real-world performance. A membrane may perform well in a laboratory setting, but if it is not correctly lapped, terminated, or integrated with adjoining materials, it will fail to meet its intended function. Successful balcony detailing includes:
- Alignment of barriers: Ensuring air, water, and thermal barriers are co-planar and continuous.
- Redundancy in protection: Using multi-layered approaches such as protection boards, drainage mats, or overcoats where exposure is high.
- Field testing: Verifying continuity through water spray testing.
The balcony should be treated with the same level of rigor as any other envelope component, especially given its propensity for failure if neglected.
The Way of a Successful Installation
This section will discuss the key aspects of a successful waterproofing installation on wood-framed balconies. The critical element in this process is to ensure the order of operations is followed and key details related to flashing are followed.
Assuming design is complete and approved, materials ordered, arrived, inspected, and accepted, the first task of sheet waterproofing the wood-framed balcony is…worker safety. According to OSHA (Occupational Safety and Health Administration), there were 5,283 fatal work injuries in 2023, that is one death every 99 minutes. Within all industry sectors, construction had the most fatalities (1,075), and of those, 39% were related to falls, slips, and trips. Falls greater than 6 feet accounted for over 64% of the fatalities. What this means, statistically, is that working from heights is dangerous and can be fatal to workers performing tasks on wood-framed balconies.1
Safety is everyone’s job on the jobsite, and if you see a risk, say something. When working on balconies, PPE (Personal Protective Equipment) must be worn. This includes everything from the right boots and eye protection to ventilated masks when installing sealants and coatings. Harnesses and fall-protection measures should also be taken, ladders secured, and safety officers should be on site. Also note that some solvents and coatings may be flammable, so keep sparks and flame away and post “No Smoking” signs as needed.
The next step in installation is to make sure the environmental conditions are ideal for the application. Check the weather forecast and schedule the install for when conditions will be dry and above 40°F. In the realm of balcony waterproofing, no phase is more critical—and more frequently underestimated—than surface preparation. Regardless of how robust or advanced the waterproofing system may be, its performance hinges on the condition of the substrate beneath it. Just as a well-designed envelope can be undermined by poor execution at the smallest transition, so too can a high-quality membrane fail prematurely if applied to an improperly prepared surface.
The substrate for balcony waterproofing is typically constructed using either plywood or oriented strand board (OSB). In traditional applications, CDX plywood is often used, with the C-grade face oriented upward to receive the waterproofing system. This grade of plywood provides sufficient structural integrity while maintaining cost efficiency. Alternatively, OSB is also common in modern construction due to its dimensional stability and widespread availability.
Before any waterproofing product is installed, the substrate must be evaluated for soundness. It must be stable and well-adhered, free of delamination, scaling, or any form of degradation that could compromise adhesion. Cleanliness is equally important: surfaces should be free of dust, oils, and any construction debris that might interfere with the bonding of primers, sealants, or membranes. Moisture content must be controlled —substrates should be dry and free from frost or condensation at the time of application to ensure the integrity of chemical bonds and prevent entrapment of moisture beneath the membrane.
Slope is another essential factor in the equation. A minimum of ¼-inch per foot slope should be designed into the balcony structure to promote positive drainage. Standing water not only accelerates membrane wear but also increases the likelihood of leaks, particularly at terminations and penetrations. Proper slope ensures that water flows away from vulnerable areas such as door thresholds, wall interfaces, and railing bases, supporting the long-term performance of the entire waterproofing assembly.
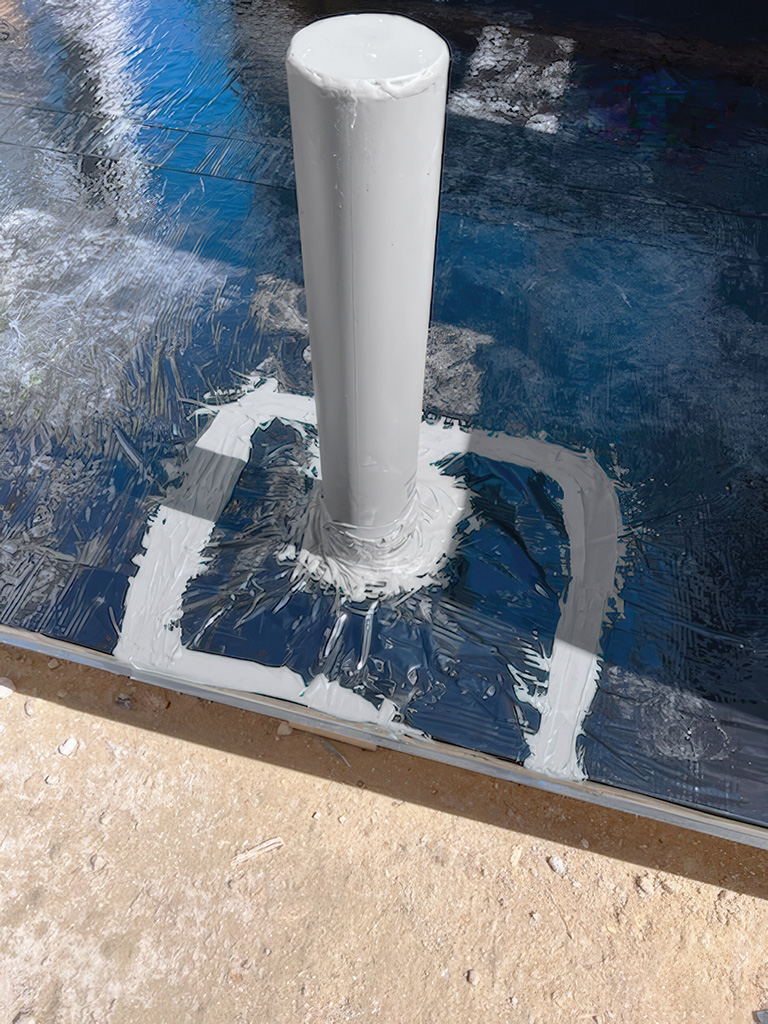
Photo courtesy of Polyguard
Installation of detail tape around the perimeters and flashing membrane installed at the wall transitions is critical, and all cut edges should be detailed with sealant.
Equally important is the treatment of surface irregularities. Any sharp edges, protrusions, or debris that could create point loads or puncture the membrane must be removed. This is especially critical in wood-framed balconies where fasteners, splinters, or surface defects may exist. Gaps between supporting elements—such as those between plywood sheets or at framing interfaces—must be bridged using compatible sealants or fluid-applied membranes. This step establishes continuous support beneath the waterproofing layer, preventing deflection or stretching that could lead to cracking and eventual failure.
A cured cant bead, typically made of polyurethane or similar sealant, should be applied at all right-angle transitions (such as wall-to-deck junctions) to create a smooth, concave profile. This bead helps distribute stress and ensures uniform membrane coverage. Once cured, seal the substrate surface with approved sealant or liquid membrane primer. Primers must be applied uniformly at a rate of 250-300 square feet per gallon and allowed to flash off prior to flashing or membrane application.
The next stage in the process involves flashing. For wood-framed balconies, there are two materials commonly specified for this task, and the selection of flashing material plays a major role in the long-term performance of the waterproofing system.
Galvanized metal flashing has long been a standard in construction for its rigidity and structural stability. It is particularly effective in situations where bridging across gaps or inconsistencies in framing is required. Its metal composition allows it to span small voids and hold shape over time. However, this same rigidity can become a disadvantage when applied to wood-framed balconies, where framing irregularities and subtle shifts in alignment are common. Metal flashing lacks the flexibility to accommodate these inconsistencies, which can lead to lifting, detachment, or stress points at critical junctures.
Moreover, galvanized metal is vulnerable to corrosion over time, particularly in moist or coastal environments. While it is often selected for its durability, its exposure to water and air, especially when installed near untreated wood or incompatible materials, can lead to rust, staining, and eventual failure. For this reason, metal flashing used in waterproofing assemblies should always be covered with a membrane or other protective coating. This shields the metal from direct moisture contact while also improving compatibility with adjacent waterproofing layers.
In contrast, membrane flashings offer a more versatile and high-performance solution, particularly in applications involving complex or inconsistent geometry. These materials are typically composed of rubberized asphalt, butyl, or other elastomeric compounds that offer high elongation properties, allowing them to stretch and move with the building over time. This characteristic makes them especially well-suited for wood-framed structures, where seasonal expansion, contraction, and subtle building shifts are inevitable.
Membrane flashings can conform tightly to framing irregularities and variable angles, creating a continuous, bonded seal that adapts to the real-world conditions of the jobsite. Additionally, because they are often designed to bond to themselves and to similar membrane materials, they offer enhanced compatibility at terminations, overlaps, and penetrations. This continuity reduces the risk of disbondment or failure at critical joints, where dissimilar materials might otherwise separate under stress or over time.
However, membrane flashings are not without their vulnerabilities. Their sensitivity to ultraviolet (UV) exposure means they must be installed with care and protected with an additional layer, such as a coating, overburden, or covering membrane, to prevent degradation. Unprotected exposure to sunlight can lead to brittleness, cracking, and eventual failure of the flashing, especially if the material is left exposed for extended periods during construction delays.
Best practices and general specifications require that installations use a minimum of 12-inch strips of flashing membrane for continuity and proper coverage. Once installed, membranes should be covered within 30 days.
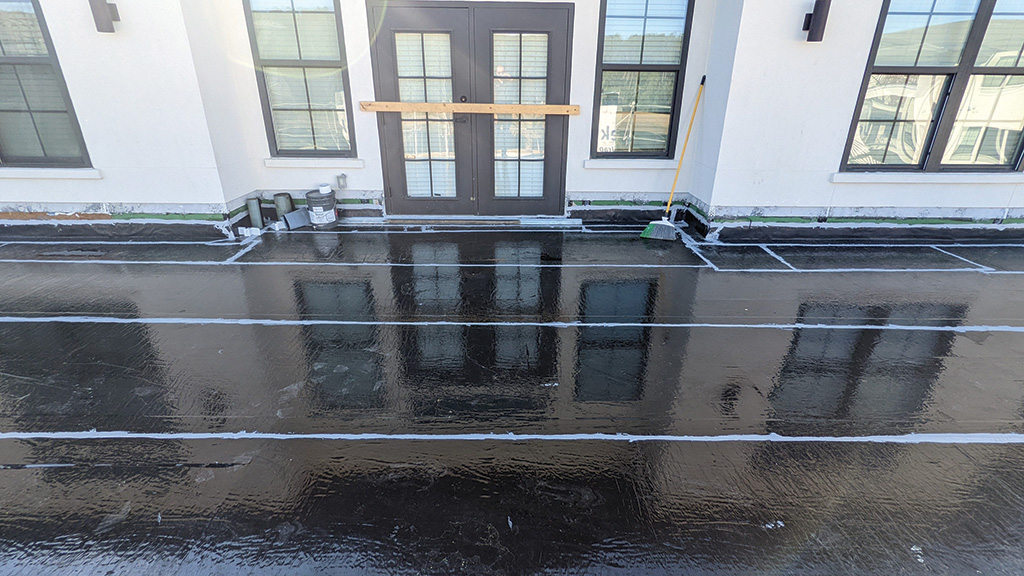
Photo courtesy of Polyguard
All membranes should be installed in a shingled fashion, with overlaps sealed and cut edges reinforced with compatible sealants.
All membranes should be installed in a shingled fashion, with overlaps sealed and cut edges reinforced with compatible sealants. Remember, asphalt mastic is not approved for zero-sloped decks; only use approved sealant material compatible with the membrane. The proper sequence of field membrane installations starts from the balcony edge and works backward toward the building. This ensures a proper shingle lap that naturally allows gravity to move water down and away from the building.
Full membrane adhesion and the use of pressure rollers can help achieve robust bond strength and eliminate voids where moisture could accumulate. Pressure rollers work out fish mouths and wrinkles and specifically help increase uplift adhesions, a critical concern in coastal areas where high wind events are expected. In most cases, use of pressure rollers is required for code-compliant installation.
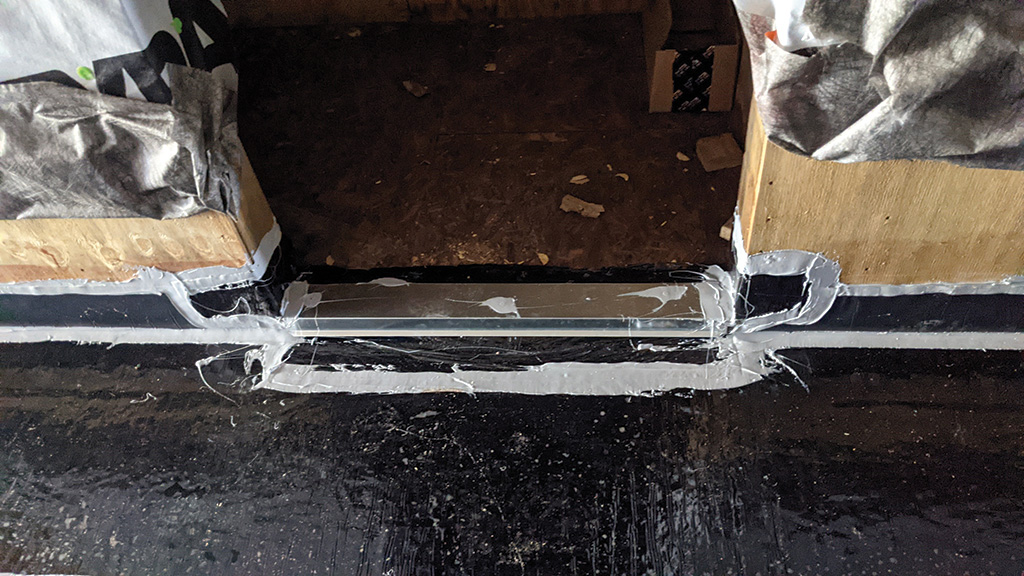
Photo courtesy of Polyguard
Thresholds are critical spaces to ensure proper integration of the waterproofing membrane and building envelope components.
As mentioned earlier, studies have shown that 90% of all leaks occur in less than 1% of the building’s surface. Terminations, transitions, and penetrations are the most vulnerable areas in wood-framed balconies, and therefore, special attention to flashing and waterproofing these areas is so important. Common weak points where water intrusion can occur in the balcony are:
- T-bar Terminations: T-bars are commonly used to support the edge of the balcony. Where waterproofing terminates at or around these elements, improper detailing can allow water to wick into the assembly.
- Corners: Inside and outside corners are inherently complex and require special attention to ensure membrane continuity. They are often the first points to show signs of failure if not properly detailed.
- Railing Attachments: Penetrations for railing posts are notoriously difficult to seal over time, especially when fasteners penetrate the waterproofing layer or lack proper flashing.
- Door Thresholds: Transitions between interior floor levels and balcony decks are a critical interface. Water intrusion here can lead to damage not only in the balcony itself but also in the adjoining interior spaces.
A successful waterproofing installation for wood framed balconies is not technically difficult or arduous but does require care and attention to certain details. The order of operation must be followed, starting with safety and weather conditions. Each step of the process then must be done methodically and purposefully to ensure the integrity of the entire installation. Short-cutting cleaning the substrate will result in poor adhesion of the waterproofing membrane. Likewise, failure to flash and seal penetrations will inevitably lead to water finding a way into the structure. The next section of this article will look at ways you as the architect can help ensure the balcony you design will be installed and live up to your expectations, as well as providing a durable and safe feature for occupants.
Going Above and Beyond
Delivering a high-performance waterproofing system for wood-framed balconies is not simply a matter of choosing quality materials—though that is certainly important. Instead, it involves a holistic approach that prioritizes system-level thinking, meticulous execution, and a commitment to continuous improvement throughout design and construction. For architects and builders, there are multiple points of intervention to raise the standard of quality, increase durability, and enhance sustainability. By leveraging high-performance components, verifying assemblies through testing, and investing in pre-construction mockups and training, project teams can avoid the common—and costly—pitfalls of premature balcony failure.
As the industry continues to evolve under the pressures of energy efficiency, climate resilience, and liability concerns, the imperative is clear: get it right once, or risk getting it wrong hundreds of times.
A high-quality waterproofing system provides immediate and long-term value for every stakeholder in a construction project. For the owner, it reduces long-term maintenance costs, minimizes liability, and contributes to occupant satisfaction. For the architect, it ensures the design intent is preserved and meets building performance goals. For contractors and tradespeople, a well-executed system avoids callbacks, rework, and warranty claims. And for residents, it creates safer, healthier, and more livable spaces.
Delivering high quality in wood-framed balcony construction requires more than just specifying a waterproof membrane. It involves rigorous attention to system compatibility, sequencing, workmanship, and oversight. Opportunities to embed these principles exist throughout the design and construction process—from material selection to on-site execution.
Drain Mats: A Critical Addition to the System
Waterproofing begins with good design, and that includes effective drainage planning. A minimum slope of ¼ inch per foot should be built into the balcony structure to ensure water flows away from the building and toward designated exit points. This is the foundational layer of passive drainage and must be consistent across the entire deck surface.
However, slope alone does not eliminate the need for additional drainage measures. Drainage mats function as a second line of defense. These mats are installed between the membrane and the topping layer and are designed to facilitate water flow, prevent the buildup of hydrostatic pressure, and physically protect the waterproofing membrane from abrasion or mechanical damage. By promoting controlled water movement, these mats ensure that even incidental moisture is directed away from critical areas, such as door thresholds, railing posts, or structural penetrations, and toward drains or drip edges.
A common misconception in balcony construction is the belief that topping slabs alone are sufficient to shed water. While they do divert surface moisture, they do not prevent water migration beneath the slab. In fact, water that infiltrates through surface cracks or joints often becomes trapped between the slab and the membrane—an ideal scenario for degradation and failure.
Drain mats mitigate this risk by creating structured channels for water to escape. This not only extends the life of the membrane by reducing direct exposure to moisture but also accelerates drying and prevents standing water, both of which are key to durability. Their role is especially important on balconies with complex geometries or limited exposure to sunlight, where natural drying is inhibited. As part of an integrated waterproofing strategy, drain mats are strongly recommended, especially for projects where long-term performance is a primary objective. Drainage mats also support passive drying and protect the membrane during topping slab curing.
Water Testing: Test for Success
One of the simplest and most effective ways to enhance quality assurance in balcony construction is through water or flood testing. This process involves temporarily damming the perimeter of a waterproofed area and introducing water to simulate real-world conditions. The goal is to confirm the integrity of the waterproofing membrane before it is covered by a topping slab or finish layer.
This proactive measure helps reveal hidden vulnerabilities, such as punctures, weak seams, or improperly treated transitions. These issues are often invisible to the eye but can result in major failures once the membrane is concealed. Water testing allows teams to correct problems before they are locked beneath permanent layers, significantly reducing the likelihood of post-occupancy leaks or structural damage.
Testing is particularly important on high-risk transitions, such as wall-to-deck junctions, door thresholds, T-bar terminations, and railing penetrations. These are the points where membranes are most likely to fail—and where remediation is most costly. A properly executed water test is not just a box to check; it’s a proactive validation tool that helps avoid post-occupancy failures and is a performance check that validates the assembly as installed.
The Role of Full-Scale Mockups in System Validation
In complex waterproofing assemblies, the value of full-scale mockups cannot be overstated. A mockup provides a physical, hands-on opportunity to construct and test the balcony waterproofing system before it is replicated across dozens or even hundreds of units. For architects, contractors, and trades, it serves as a collaborative tool to refine detailing, sequencing, and coordination. Full-scale mockups allow teams to:
- Validate construction sequencing across multiple trades.
- Establish quality control benchmarks and performance expectations.
- Identify and resolve design conflicts or constructability issues early.
- Train installers and supervisors on correct practices and common failure points.
Most critically, mockups should replicate all key transitions and risk areas, including T-bars, thresholds, corners, door sills, and railing penetrations to give the system a realistic performance trial. By conducting water testing on the mockup itself, the team gains a true indication of how the assembly will perform under real-world conditions.
The phrase “inspect, don’t expect” is especially applicable here. If the system fails in the mockup, it’s a low-cost learning opportunity. If it fails after installation, it becomes a high-cost liability.
Mockups become more than just a technical trial; they are a platform for training and expectation setting. Supervisors can use them to walk crews through every step, ensuring clarity and consistency. Product reps and waterproofing consultants can provide hands-on demonstrations. Architects can observe how design details translate into built form. This alignment across disciplines fosters a culture of accountability and quality, where tradespeople take pride in craftsmanship and project teams understand the true consequences of missed steps.
Quality construction doesn’t happen by accident—it’s the result of training, communication, and shared standards. One of the most impactful ways to ensure durable balcony assemblies is to invest in educating everyone involved in their construction.
Conclusion
Balconies continue to be a defining feature in residential and commercial architecture, from multifamily developments to hospitality and student housing. When thoughtfully designed and properly executed, they provide meaningful access to the outdoors, enrich the aesthetic appeal of a building, and enhance real estate value. However, their exposed location and complex detailing make balconies especially susceptible to failure, particularly in wood-framed structures. When waterproofing is poorly integrated or improperly installed, the consequences can be severe, ranging from water intrusion and mold growth to structural damage and life safety hazards.
Durability must be recognized not as a premium feature, but as a fundamental aspect of sustainable design. A durable waterproofing strategy is critical to protecting the integrity of the building envelope, extending the lifespan of materials, and reducing the need for costly repairs or replacements. It directly supports long-term environmental goals by minimizing waste and improving energy performance through better thermal continuity. It also ensures that buildings remain safe and livable for the people who occupy them.
Architects play a central role in driving this performance. By aligning waterproofing with broader goals of code compliance, thermal efficiency, and air/moisture control, they can create balcony systems that meet today’s standards while anticipating tomorrow’s challenges. This requires not only the right products, but also the right processes—drainage mats, water testing, full-scale mockups, and comprehensive training.
In the end, high-performing balconies are the result of deliberate, detail-driven execution. Every transition, termination, and penetration matters. With the right design approach and construction discipline, projects can include balcony systems that don’t just look good on day one—but continue performing for decades to come. Building it right once isn’t just an ideal—it’s a necessity.
End Notes
- https://www.bls.gov/news.release/cfoi.nr0.htm
Andrew A. Hunt is Vice President of Confluence Communications and specializes in writing, design, and production of articles and presentations related to sustainable design in the built environment. In addition to instructional design, writing, and project management, Andrew is an accomplished musician and voice-over actor, providing score and narration for both the entertainment and education arenas. www.confluencec.com, https://www.linkedin.com/in/andrew-a-hunt-91b747/