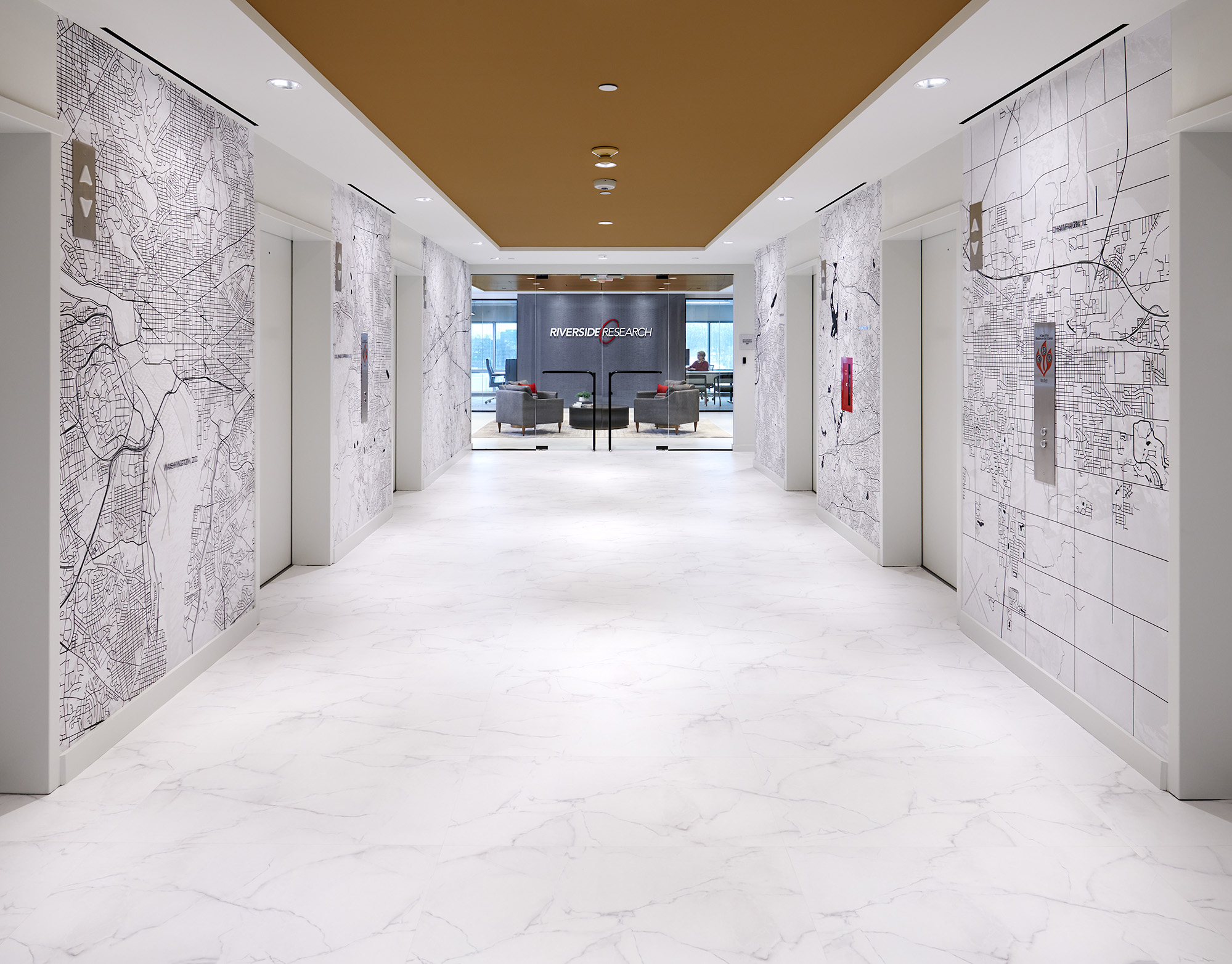
Photo courtesy of Windmoeller Inc., ©Judy Davis, Architectural Photographer
Sunnyvale Elementary, built during a boom of community growth in the 1980s, was overdue for a makeover. The outdated vinyl composite tile (VCT) flooring in the corridors and first-floor classrooms was not only showing its age with scratches, dents, and stains, but the presence of the material itself raised concerns due to potential health risks associated with chemicals of concern in the construction of PVC-based flooring. The school's facilities management team, led by Sarah Rodriguez, along with the school administration and board representatives, embarked on a mission to find a new flooring solution. Additionally, the team’s vision had another layer–to achieve LEED v4 certification. As this green building rating system recognizes and rewards environmentally responsible practices, any flooring product selected would need to uphold those values.
Vinyl flooring commands a significant part of the resilient flooring market, thanks to its versatility, affordability, and performance characteristics. Beyond the fictional case study of Sunnyvale Elementary, vinyl flooring can be and is used in various types of buildings.
However, the PVC (polyvinyl chloride) used to make vinyl flooring products faces rising concerns and government scrutiny about health impacts and environmental hazards involved in its production, transportation, and disposal. PVC is a synthetic polymer that studies have shown when burned releases a group of harmful chemicals called dioxins that are persistent in the environment and can lead to serious health issues. The inclusion of PVC in projects is opposed by various groups and some design firms like Perkins + Will.1 Prominent end users like Kaiser Permanente2 and Harvard University3will not specify it.
On December 14, 2023, the U.S. Environmental Protection Agency (EPA) announced that it is beginning the process of prioritizing five additional toxic chemicals for risk evaluation under the Toxic Substances Control Act (TSCA). Among those substances is Vinyl Chloride (CASRN 75-01-4).
The inclusion of vinyl chloride is notable for the flooring industry because of its wide use in the market. While the EPA’s announcement does not mean an abrupt ban on vinyl chloride or its derivative products is on the immediate horizon, it sparks critical questions about the future of a significant segment of the flooring industry.
The EPA decision aligns with the increased market trend specifying new, resilient flooring materials that are PVC-free. To navigate this wave of change toward both healthier and more sustainable flooring, it is vitally important that design professionals and specifiers understand what is meant by the terms “resilient flooring” and “PVC-free” flooring materials.
WHAT IS MEANT BY RESILIENT FLOORING AND PVC-FREE
The head of Sunnyvale Elementary’s facilities management team Sarah Rodriguez decided to hire Amelia Moore, a seasoned lead interior designer known for her creativity and commitment to healthy spaces. Amelia understood the importance of a durable yet visually stimulating learning environment while keeping sustainability a top priority. She knew the new flooring for the school had to meet a stringent set of criteria:
- High Performance: Withstand the constant activity of hundreds of energetic students. This meant resisting scratches, dents, scuffs, and the relentless rolling of chairs and carts.
- Easy Maintenance: Busy school days demand minimal cleaning downtime. The ideal floor would be stain-resistant and easy to keep clean, minimizing disruption during class hours.
- PVC-Free and Sustainable: The school board prioritized the health and well-being of students and staff. They wanted a flooring solution free of PVC and VOCs, ensuring a healthy indoor environment.
- Impact Absorption: Dropped textbooks, rambunctious playtime–the floor needed to absorb impacts to prevent injuries and increase the life of the flooring.
- Design Flexibility: Sunnyvale wasn't just about function; for their redesign, the school craved a vibrant learning atmosphere. The ideal floor would offer a variety of design options to create themed learning areas within the four sections of the corridor and classrooms.
- LEED: Sunnyvale's pursuit of LEED v4 certification added another dimension to the flooring selection process. The ideal solution would not only be functional and beautiful but also contribute to the school's sustainability goals.
Photo courtesy of Windmoeller Inc.
Advances in resilient PVC-free floors have facilitated exceptional design flexibility. However, it is crucial that the designer and specifier have access to transparent material information to make the best product determination where sustainability is a concern.
Resilient Flooring
Resilient flooring includes any flooring material in which the wear surface is non-textile, non-wood, and non-stone.
The resilient flooring category has a rich history of innovation. Early materials like linoleum, rubber, and cork were pioneers in offering durable, comfortable, and easy-to-maintain surfaces. Over the decades, advancements led to the development of vinyl-based products, which became popular for their versatility and cost-effectiveness. However, growing awareness of the environmental and health impacts of PVC has spurred the next wave of innovation: bio-based polyurethane. This new category builds on the lessons learned from earlier materials, leveraging sustainable resources to create flooring that is not only high-performing but also healthier for people and the planet. Bio-based polyurethane, initially used in underlayment applications, has now evolved into a complete, high-performance flooring solution.
As defined by ASTM, resilient flooring refers to flooring materials known for their durability, flexibility, and ability to bounce back after being compressed or deformed. Resilient flooring products are firm, hard-wearing materials that also have a certain degree of “give” or recovery. They are neither hard and rigid like stone or wood, nor soft like carpet. Resilient materials are generally known for their durability, easy cleaning, low maintenance, and comparatively low price.
While there are 16 ASTM resilient flooring specifications standards (as of June 2024), they can be generalized into 7 material categories:
- Cork
- Linoleum
- Polyurethane including bio-based polyurethane
- Rubber
- Vinyl (includes solid vinyl, tile, vinyl composition, and rigid core)
- Polyester
- Polyolefin
Material formats, such as tile and plank versus sheet flooring, as an example, have their own specification standards but fall into the above general material category.
So What is PVC-Free?
First, PVC-free is not an officially defined flooring material category, despite recognition by CSI. Resilient flooring that is PVC-free simply refers to the grouping of floor materials that meet resilient standards and do not contain PVC. These flooring material ingredients vary widely and can range from alternative chemical compositions to bio-based products. The market types for PVC-free flooring include mineral materials, bio-based materials, and other materials. Linoleum, rubber, and cork are well-known PVC-free materials that have been in the marketplace for many years. Newer resilient PVC-free product examples include polyolefin base and bio-based polyurethane.
Because of the wide span of products that can claim PVC-free status, simply choosing a PVC-free flooring material does not necessarily mean securing a sustainable product or a product with enhanced durability. Not all PVC-free materials would be considered environmentally friendly. Some PVC-free products are even manufactured using petrochemicals. Some may have a higher Global Warming Potential (GWP) than PVC. However, some of the best and most environmentally friendly PVC-free flooring choices do demonstrate low carbon composition, can gain certification as bio-based and Red-List Free, or earn Cradle to Cradle Certified® and FloorScore® status. It is imperative that the designer and specifier have access to transparent material information, which can also be found in the product Health Product Declaration (HPD), to make the best product determination where sustainability is a concern.
Additionally, when it comes to design and durability, it also pays to be discerning. Linoleum and rubber have very limited capabilities to create specific designs or patterns. PVC-free products may also lack the performance characteristics necessary for demanding commercial environments. Nevertheless, technologies in certain PVC-free flooring materials allow for planks, tiles, and sheet goods that perform equal to or better than vinyl, even in high-traffic areas. Many of these products can also replicate the natural wood and stone looks just like LVT or vinyl sheet. Material and manufacturer transparency is vital to allow a specifier to fully understand the design options, performance capabilities, and technical life of each PVC-free product.
Photo courtesy of Windmoeller Inc.
Bio-based polyurethane floor coverings provide a superlative combination of unbeatable performance, limitless design, and incomparable sustainability.
Advances in PVC-Free Materials
A newer resilient flooring material that has been in the US market since 2014 is bio-based polyurethane. This material falls under ASTM F3403 sheet and ASTM F3404 planks & tiles. This PVC-free material includes the same design flexibility as vinyl and the same or better performance. Bio-based polyurethanes represent a major step forward for sustainable and durable resilient flooring alternatives to PVC.
To fully appreciate the performance of bio-based polyurethane, it's important to understand its structure at a chemical level. Bio-based polyurethane is a thermoset material. This means that during production, its polymer chains are irreversibly cross-linked, forming a strong, stable, three-dimensional network. Once cured, a thermoset material cannot be remelted or reshaped by heat.
In contrast, most traditional vinyl (PVC) flooring is a thermoplastic. Thermoplastic polymers have long, linear chains that are not cross-linked. When heated, they soften and can be reshaped, but they can also become susceptible to expansion, warping, or indentation under direct sunlight or high temperatures.
This fundamental difference is key to long-term performance. The thermoset nature of bio-based polyurethane ensures it remains dimensionally stable and resilient, returning to its original form even after being subjected to heat, heavy loads, or extreme stress, mitigating long-term risk for the client.
An example of this bio-based polyurethane material is manufactured in Germany and is the result of many years of research and innovation. Using a unique thermosetting process, the German manufacturing firm succeeded in engineering flooring products in which conventional petrochemical polyols have been replaced by natural oils to formulate the polyurethane formula.
The result is a high-performance composite material made primarily from plant-based oils, like castor, and naturally occurring minerals such as chalk. This material deliberately refrains from using plasticizers, solvents, or chlorine, making it ideally suited to applications with stringent health or sustainability standards. The resulting bio-based polyurethane material makes beautiful, long-lasting flooring solutions more sustainable. The hallmark of bio-based polyurethane material developments is the technologically unsurpassed proportion of renewable and natural raw materials they contain.
The benefits of advances in bio-based polyurethane are many – this material technology offers a sustainable, natural product with no risk to health. These floors are also strong; their physical properties remain unchanged even after being subjected to extreme stress, resist indentation, and are dimensionally stable. The floors are flexible, withstand heavy loads, and have a long life.
To make a confident and clear decision, designers must not only know what the flooring material they are selecting actually is, but also how it is expected to perform. Understanding industry standards and minimum performance is a key to more confident selection.
UNDERSTANDING INDUSTRY TESTING STANDARDS
At Sunnyvale, for designer Amelia Moore, bio-based polyurethane flooring emerged as the clear winner. It ticked all the boxes. The product boasted exceptional durability and resistance to scratches and dents from everyday wear and tear, as well as good impact resistance. It offered the ability to use matching color and design between plank and sheet material, to meet the demands of different application areas. The inevitable shifting of desks and chairs would not cause indentation in the flooring. The bio-based polyurethane would be easy to clean and have stain-resistant properties to minimize future maintenance needs. Most importantly, bio-based polyurethane is free of PVC and VOCs, creating a healthy environment for students and staff. The design flexibility was the ultimate game-changer. Bio-based polyurethane flooring offered a vast array of colors and patterns, allowing Amelia to create a unique theme for each section of the corridor and classrooms, fostering a vibrant and stimulating learning environment. It permitted for those themes to be continued in sheet material for areas like the cafeteria and multipurpose rooms. Yet, Amelia needed to quantify these benefits and the new floor’s performance clearly to the school’s administrators and board. She turned, as a starting point, to industry standards.
The Construction Specifications Institute (CSI)® MasterFormat® is the specifications standard for the built environment and provides the basis for organizing information within contract documents. While this offers invaluable structure and format, the actual information on products should be derived from testing and standards. Industry testing methods and specification standards are created to provide quality control and to set minimum criteria that products must meet to be promoted. To use these standards when making product decisions, it is important to understand the meaning behind industry testing and to recognize what truly drives performance.
Standards Organizations
The American Society for Testing and Materials (ASTM), American National Standards Institute (ANSI), and International Organization for Standardization (ISO) are three prominent organizations involved in setting product standards, each with unique purposes, missions, and structures. While ASTM and ANSI provide guidelines that are based more for the US market, ISO offers a global perspective. Each organization's standards can affect everything from material selection and design specifications to installation processes and sustainability considerations. ASTM’s mission is to improve product quality, enhance safety, facilitate market access and trade, and build consumer confidence. In the context of resilient flooring, ASTM standards cover aspects like material composition, performance testing, installation, and maintenance of flooring materials.
Using ASTM Standards in Decision-Making and Clarification
ASTM's resilient floor covering standards are instrumental in specifying and testing the physical and mechanical properties, as well as in providing the installation procedures for resilient flooring, which includes linoleum, vinyl composition tile, and sheet vinyl among others. These criteria help to determine the abrasion, puncture, and impact resistance, flexibility, electrical resistance, thickness, and heat and light stability permitted. By adhering to these standards, manufacturers can ensure that their products meet minimum performance requirements, designers and specifiers can select appropriate materials for specific applications, and users can have confidence in the durability and safety of the flooring installed in their spaces. Overall, ASTM standards play a crucial role in promoting quality and reliability in the resilient flooring industry.
New ASTM Standards for Polyurethane Resilient Flooring
Bio-based polyurethane resilient flooring materials offer great promise for the flooring market. However, it is important that they and their claims have been tested appropriately and in a manner where results are repeatable. Two newer ASTM Standards covering performance requirements for resilient polyurethane flooring were issued in 2022. The ASTM Technical Committee for Resilient Flooring, F06, approved the standards that define compositional and performance requirements for heterogeneous polyurethane flooring. According to ASTM F06 member Todd Jones, the performance requirements section of the standards (F3403 and F3404) includes resistance to chemicals, heat and light, static load recovery, residual indentation, flexibility, and caster chair testing.4
“The standards will validate the differentiated performance characteristics of this entirely new category of floorcovering,” says Jones, Vice President, Windmoeller Inc.
For the design professional and specifier, it is important that a selected PVC-free flooring material can satisfy these minimum required standards. However, the test methods and standards from these organizations are created to set only minimum benchmarks and quality control for products entering the market. Test methods typically only demonstrate a repeated performance by the product that satisfies test requirements. Selecting a high-performance flooring material among various flooring options means placing a detailed lens on performance and environmental attributes.
Photo courtesy of Windmoeller Inc.
Bio-based polyurethane floor coverings provide a superlative combination of unbeatable performance, limitless design, and incomparable sustainability.
ATTRIBUTES OF RESILIENT FLOOR PERFORMANCE
The industry tests performed on flooring are used for a product to achieve a “pass” or “fail,” or to meet a minimum threshold requirement to satisfy the accepted industry standard. Passing or meeting the threshold requirements does not necessarily prove that one material is better than another material. However, the absence of performance testing is always a red flag for specifiers. Flooring at a specific job may also need to satisfy additional project criteria, like flammability and smoke requirements (ASTM E648 and ASTM E662), static load (ASTM F970), dimensional stability (ASTM F2199), or special chemical resistance (ASTM F925). Unique building codes and provisions established by state and local governments may apply. Finally, the most suitable material should meet specific project and design goals, like low embodied carbon thresholds or environmental certification, found in a product-specific Environmental Product Declaration (EPD), while providing durability and ease of maintenance. Clearly understanding the type of material and its assembly and options will help inform a best choice.
Flooring Product Structure Types
It is beneficial to understand the two types of resilient flooring structures before discussing resilient flooring performance. Resilient flooring structures can fall into one of two categories: homogenous and heterogeneous structure.
A homogeneous floor covering is uniform in both structure and composition—a homogeneous mixture of raw materials throughout the entire thickness of the finished product. Rubber, linoleum, vinyl, and cork can be examples. A single layer of raw materials and pigments compose the floor with the possible addition of a surface treatment at the top.
Heterogeneous flooring consists of a wear layer and other layers which differ in composition or design and can contain a reinforcement. This composition can consist of a backing, a stabilization layer, décor, a protective layer, and a surface treatment layer on the top. Polyurethane and vinyl are examples of this structural type.
Defining Wear Surface and Wear Layers
Recognizing the role of the wear layer and wear surface helps in understanding the expected performance and durability of the flooring.
Understanding the difference between the wear layer and the wear surface is crucial for cutting through marketing claims and specifying the right product for the application.
- The Wear Layer: This is a measurable, physical layer of a flooring product, typically found in heterogeneous vinyl flooring. It's a clear vinyl coating applied over the printed design layer, and its thickness is measured in mils (thousandths of an inch). For LVT, a thicker wear layer (e.g., 20 mil) generally correlates with greater durability.
- The Wear Surface: This is the functional topmost coating of the floor that is in direct contact with foot traffic, furniture, and spills. It is an engineered finish applied to enhance performance characteristics like scratch resistance, stain resistance, and cleanability. In bio-based polyurethane flooring, this high-performance polyurethane coating is the primary durability component.
It's a common misconception to compare the "mil thickness" of a vinyl wear layer directly to the performance of a polyurethane wear surface. They are engineered differently. The durability of a polyurethane floor comes from the chemical makeup and factory-cured strength of its surface, not a simple measurement of thickness. Therefore, traditional "mil layer" comparisons are not applicable and can be misleading when evaluating advanced materials like bio-based polyurethane.
While these terms may seem similar, they have distinct meanings in the context of flooring materials. Knowing the difference between the wear layer and wear surface enables designers to make informed choices to ensure the chosen flooring can meet the specific needs of the intended application, level of foot traffic, and desired longevity. By distinguishing between the wear layer and wear surface, designers can compare different flooring products more effectively. They can evaluate factors such as wear layer thickness, wear surface material, and overall performance attributes to determine which product best aligns with their requirements and preferences.
In current ASTM standard specifications for vinyl flooring, the wear layer is a specific component within the flooring construction often used to classify products into residential, light commercial, commercial, and industrial applications. Meanwhile, the wear surface represents the overall top face enduring daily wear and tear, forming the basis for manufacturers' marketing performance claims.
The thickness and material makeup of the wear layer and wear surface are both significant. A thicker wear layer typically indicates better resistance to wear and tear, making it suitable for high-traffic areas. The wear layer is a tangible layer within the construction of the resilient flooring. In resilient heterogeneous vinyl flooring, it's usually a clear vinyl layer applied atop the decorative or printed layer. Its primary role is to provide additional protection in case the wear surface or factory coating is compromised. The thickness of this wear layer matters: measured in mils (thousandths of an inch), thicker layers (e.g., 20 mils) offer superior durability, making them ideal for high-traffic areas. However, the wear layer is known as the performance layer in bio-based polyurethane flooring is not vinyl. It is pure polyurethane that retains the strength and performance of traditional polyurethane coatings, enhancing confidence in its long-term performance.
The composition and characteristics of the wear surface influence factors such as stain resistance, scratch resistance, and ease of maintenance. It is the topmost layer of the resilient flooring that interacts with foot traffic, furniture, and other objects. Sometimes referred to as the factory coating, it's extremely thin, akin to a few hairs. The wear surface, or specialty coating, is incorporated into the wear layer, which may include any embossed or textured patterns applied on top. Polyurethane is commonly used for the wear surface due to its strength and exceptional performance in resisting stains, scratches, and wear, while being easy to clean and maintain.
Aesthetics
Flooring choice is also about design. A floor that performs but fails to satisfy the desired aesthetic is a mismatch from the start. Certain resilient materials, such as rubber or linoleum, offer durability but a limited design palette. Bio-based polyurethane formulations can accommodate custom design capabilities as well as a wide range of standard colorways. When produced as tiles or planks, bio-based polyurethane can mimic classic marble, biophilic design, textiles, wood planks, and a variety of other patterns and designs, which are also offered in sheet format for preferred application areas. Bio-based polyurethane flooring solutions can be produced in almost any form and design using digital printing.
SAFE, SUSTAINABLE FLOORING: THE FUTURE IS RESILIENT
At Sunnyvale, beyond its functionality, performance, and aesthetics, bio-based polyurethane flooring's sustainability attributes perfectly aligned with the school’s LEED aspirations. Many bio-based polyurethane options boast certifications like Cradle-to-Cradle Certified Silver, which signifies a product's positive impact on human and environmental health. Additionally, the availability of an Environmental Product Declaration (EPD) and Health Product Declaration (HPD) provided valuable transparency regarding the flooring's environmental footprint and ingredient disclosure. These factors contributed to Sunnyvale's potential for LEED credits.
Photo courtesy of Windmoeller Inc.
Overcoming the challenge of limited design palettes common to some resilient materials, bio-based polyurethane can mimic classic marble, wood planks, and a variety of other patterns and designs.
Decision Points
When selecting a flooring product, designers should know what the flooring is: what material they are choosing and ultimately specifying, how it is expected to perform and be maintained, and how it contributes to a more sustainable built environment. For flooring products, it is not just the what, but also the how. How the product impacts the health of building occupants and is cared for within the structure has serious ramifications. An all-encompassing approach to assessing flooring material sustainability covers every point of a product's life cycle, from the raw materials used, manufacturing process, distribution, installation methods, and end-of-life recycling.
What assets make a flooring product sustainable? Marks of a sustainable product can include:
- Human health
- Lower carbon footprint and GWP
- Material transparency
- Life cycle impact and longevity
- Durability
- Maintenance and cleanability (low operational carbon involvement)
- Circularity
Specifying healthy flooring is a complex project, requiring knowledge about the comfort, health, and safety of building occupants and an understanding of how to control common indoor source pollutants to provide quality indoor air. Determining the floor material type is the beginning of a process that includes how to mitigate exposure to VOCs and minimize the impact of cleaning and maintaining the flooring.
Once a project’s sustainability goals have been defined, there is a large toolset that can help in making sustainable product decisions. First, using resources on a manufacturer’s website and product specifications pages is a great place to start. Manufacturers should make the information about their products transparent. Product transparency is the state in which all relevant information is fully and freely available. This disclosure and accountability help designers, specifiers, and end-users make informed purchasing decisions about what materials should be placed in buildings.
Focusing on all attributes of sustainability, from the original elements that compose a flooring material all the way to its end of life, is essential. Zeroing in on one single aspect, such as carbon or recycled content is not enough. All of the points – human health, carbon footprint and GWP, lifecycle and durability, and transparency – should be considered.
Using materials that meet multiple third-party certifications offers added assurance that the product, its production, materials, and lifecycle, have been thoroughly examined. There are numerous programs, organizations, and certifications that can assist in determining the right flooring for the building, occupants, and activities.
Tools to Determine Material Transparency
Several third-party organizations enable design professionals to make sustainable, healthy product choices with the best knowledge possible. Declare Labels disclose ingredients, red-list ingredients, chemicals of concern, location of manufacturing, VOC content, and material status within Living Building Challenge. Material transparency aims to reduce and eliminate the proliferation of 26 red list ingredients within over 800 building products. UL GREENGUARD and GREENGUARD Gold Certification for low emissions products are additional certifications that demonstrate both compliance with key chemical emission standards and a commitment to healthier indoor environments.
Health Product Declarations (HPDs) report exact product contents and associated health information. HPDs are created and run by a collaborative of building industry architects, designers, and consultants. Greenhealth Approved and Prop 65 Approved products are certified to be PVC-free; Health Care Without Harm also offers additional product certifications for specific applications.
Environmental Product Declarations (EPDs) are comprehensive documents that cover the life cycle impacts of a product including global warming potential, water pollution, smog potential, ozone depletion, and material sourced distances. It is important to request a product-specific EPD, versus an industry-wide EPD, as the product-specific EPD contains information for the exact product itself. Meanwhile, the industry-wide EPD is an average of the products within that category. Transparency, raw materials, and a manufacturer’s energy source, methods, and production are also assessed. Cradle to Cradle® is an example of an EPD certification demonstrating product circularity and environmental responsibility.
Tools for IAQ
Because of its large footprint within a building, it is essential to know a flooring material’s potential impacts on air quality. An excellent assessment tool to test for VOC emissions is the Resilient Floor Covering Institute (RFCI) FloorScore program. FloorScore, developed by the Resilient Floor Covering Institute (RFCI) along with Scientific Certification Systems (SCS), is a program designed to test and certify resilient flooring materials and adhesives. It is based on compliance with indoor air quality emission requirements adopted in California. Recognized by a variety of environmental programs, FloorScore certified products can contribute to better indoor air quality.
UL GREENGUARD and GREENGUARD GOLD Certification for low emissions products also validate a flooring material's support of IAQ. Selecting flooring that can be installed with low-VOC adhesives and coatings to minimize the indoor air pollution load and health risks to both installers and occupants furthers a product’s potential health benefits. The best flooring should also be easily cleaned and maintained with low-VOC cleaners and no supplemental finishes.
Holistic Analysis Tools
There are also tools and certifications that evaluate product and material sustainability in a comprehensive approach. The analysis may include assessing and selecting good materials and eco-design products that are recyclable and effectively recycled, as well as stewarding of resources in operation, shifting to more renewable energy use, and considering social equity in the value chain.
Ecomedes is a comprehensive database and enterprise-grade SaaS platform that allows for product selection matching criteria. Products can be searched based on specific sustainability criteria such as energy efficiency, recycled content, or environmental certifications. Design professionals can also organize a search by design inspiration, rating system, or impact.
Mindful MATERIALS offers a materials list that connects and aligns sustainability information. With the launch of its collaboration with Ecomedes, the new Common Materials Framework aims to provide the industry with a consistent, connected framework for sustainability in decision-making.
The Cradle to Cradle Certified® Product Standard provides a framework to assess the safety, circularity, and responsibility of materials and products across five categories of sustainability performance: Material Health – Ensuring materials are safe for humans and the environment; Product Circularity – Enabling a circular economy through product and process design; Clean Air & Climate Protection – Generating clean energy and protecting the environment; Water & Soil Stewardship – Safeguarding air, water and soil resources; and, Social Fairness – Embracing safe, fair and equitable labor practices that advance human rights and strong communities.
Material Future: What a Healthy, Sustainable PVC-Free Resilient Flooring Spec can Look Like
Demand continues to grow for sustainable alternatives to PVC flooring. From the raw materials chosen to the energy source used during production to the safety and lasting performance of the flooring solution, manufacturers are bringing out new flooring solutions that take human and environmental health seriously.
Photo courtesy of Windmoeller Inc.
Understanding what drives performance and the meaning behind industry testing standards allows designers to identify PVC-free resilient flooring materials suitable for commercial environments. Identifying the sustainability and carbon footprint attributes of PVC-free resilient flooring materials allows for confident environmental decision-making.
Photo courtesy of Windmoeller Inc.
Not only can bio-based polyurethane flooring achieve exceptional durability and performance, but leading compositions can also attain certifications including Cradle to Cradle Certified®, FloorScore, and GREENGUARD Gold.
Advances in highly resilient bio-based polyurethane flooring allow the product to attain both high performance and a composition of natural ingredients. Newer composite materials are being produced from plant-based oils such as castor oil and naturally occurring mineral components like chalk. These formulations completely avoid the use of plasticizers, solvents, or chlorine. Leading bio-based polyurethane compositions meet ASTM F3403 and F3404 specification standards, are up to five times more durable than LVT, and surpass the standard chair caster test requirement for commercial flooring by more than 25 times. Certifications for bio-based polyurethane resilient flooring include Cradle to Cradle Certified®, FloorScore, and GREENGUARD Gold, as well as third-party verified Declare LBC compliance. Leading manufacturers make products in facilities powered by electricity from renewable sources, such as solar photovoltaic systems, climate-neutral green electricity, and climate-neutral process heat.
Sunnyvale Elementary's hallways and classrooms were transformed. The bio-based polyurethane flooring gleamed in an array of colors, each section reflecting a different learning theme–from a calming ocean scene to a stimulating jungle adventure. The easy-to-clean surface meant less time spent on maintenance and more time for learning. The school community had peace of mind knowing their environment was not only beautiful but also healthy and sustainable. The "Colorful Crusade," as it came to be known, proved that functionality and aesthetics could co-exist, creating a space that nurtured both the minds and bodies of Sunnyvale's young learners, all while contributing to a greener future.
SOURCES
1 “Healthy Environments: What’s New (and What’s Not) With PVC". Perkins & Will Research. January 6, 2017. Accessed May 20, 2024.
2 Kaiser Permanente. Safer Products. Accessed May 20, 2024.
3 Harvard University. Sustainable Purchasing Guide. Accessed May 20, 2024.
4 “Two New Standards Cover Performance Requirements for Polyurethane Flooring.” ASTM International. February 25, 2022. Accessed May 21, 2024.
Amanda Voss, MPP, is an author, editor, and policy analyst. Writing for multiple publications, she has also served as the managing editor for Energy Design Update.