This CE Center article is no longer eligible for receiving credits.
In considering cement vs. epoxy, the latter is thinner, lighter weight, uses fewer strips, offers better crack and chemical resistance, and more colors. It offers a lower labor cost, but the material is more expensive than cement. At the same time, cement, particularly sand cushion, requires a greater level of craftsmanship. If the application has a known moisture issue, cement is preferred since the material breathes. In its simplest monolithic form, cement terrazzo is a mixture of portland cement and marble chips, poured into place, ground, polished, and sealed.
To create sand-cushion cement, a thin layer of sand is poured and then a piece of plastic sheet is inserted to prevent the material from bonding to the structural concrete. To keep this in place, a 2½-inch minimum of sand and cement is then poured. Divider strips on a grid pattern are inserted, minimally 4 x 4 inches, and then ½ inches of marble and cement tops it off.
With a typical weight of 25 to 30 pounds per square foot, it’s the best choice for flattening a slab. Its main application is slab- on-grade due to its weight. Found in building lobbies and many schools, sand-cushion cement terrazzo is also used in airports.
While sand cushion cement is terrazzo at its best, not all contractors offer it. The benefits of epoxy end up making it the preferred choice in most terrazzo installations today. Because of epoxy’s unlimited design capabilities, it is the standard for terrazzo art-in-public-places installations.
Vertical Terrazzo Applications
While terrazzo’s traditional application has largely been flooring, in reality, the material’s versatility and advances in technology has helped enable it to break out into a number of vertical applications, including stairs and curbs, walls and columns, ramps, counters and bar fronts, seating and planters.
“We have seen a rise in vertical applications,” observes Rickman. “We think this is driven by the knowledge that architects and designers can match their floor colors on vertical surfaces to create a continuous flow for projects.” Similarly, Menconi states, “In the past few years, we have seen more vertical, wall base and countertops. The ability to provide a seamless surface is quite appealing. We have installed floor, wall, and vanity tops on a few projects and it looks great.”
Because terrazzo can be designed to fit any dimension, it is well suited for matching horizontal and vertical designs that incorporate symmetry, such as wrapping around ramps, curbs, and stairs. Vertical applications, in particular, are popular with schools, higher education, hospitals, and municipal or public work buildings. With enhanced accessibility requirements for additions like ramps, terrazzo is a nice design option. In addition, these facility types tend to make longer term investments, and terrazzo offers long-term durability and the ability to withstand heavy traffic.
Stair treads in particular must withstand the constant pressure of foot traffic. As opposed to hardwood, vinyl, or carpet, terrazzo stair treads are not easily scuffed or scratched. Suitable for all types of staircase systems—including self-supporting stairs, wedge-shaped stairs, treads, and risers—terrazzo stairs are popular with shopping malls, hospitals, and multifamily buildings.
The same applies for seating and planters in these facility types. “The durable nature of terrazzo allows for an easy transition to exterior planters, seating, or water features in exterior public spaces and hotels,” says Ebner. For interior spaces, popular applications for walls, columns, and elevators include hotels, office buildings, retail, stadiums, and arenas as well as schools and hospitals. Particularly with hotels and upscale corporate and retail, vertical terrazzo helps create the sense of grandeur often associated with these spaces. “With the rise of terrazzo floors in lobby applications, the floor translates directly into the elevator cab floors, creating a seamless transition between spaces,” she adds.
Ebner likes to design terrazzo for bathroom walls as a durable alterative to tile or natural stone. Because the binder is impervious, hygiene is enhanced in bathroom environments. In addition, the seamless application means there are no grout joints to keep clean. The seamless, monolithic blending of poured-in-place floor and wall application is also a popular strategy for bathroom designs.
As for counters, bars, and bar fronts, they’re trending in multifamily clubhouse spaces, restaurants, and hotels. “Terrazzo counters and bars are a great way to incorporate the material in a very intimate way because these spaces are focused on creating great experiences that impress,” reports Eyink. With tenant amenity spaces, owners are looking for durable, high-end materials and terrazzo fits the bill. Style-wise, Ebner likes to combine metal, wood, and terrazzo on bar tops and kitchen counters to create a warm hospitality vibe.
When designing terrazzo for bathrooms, epoxy resins offer better chemical resistance, particularly when combined with porcelain or granite chips. Bathroom applications typically incorporate eco-friendly sealers like polyaspartic or water-based polyurethane. While these sealers are easy to maintain, it’s important that building owners/facility managers follow proven maintenance procedures.
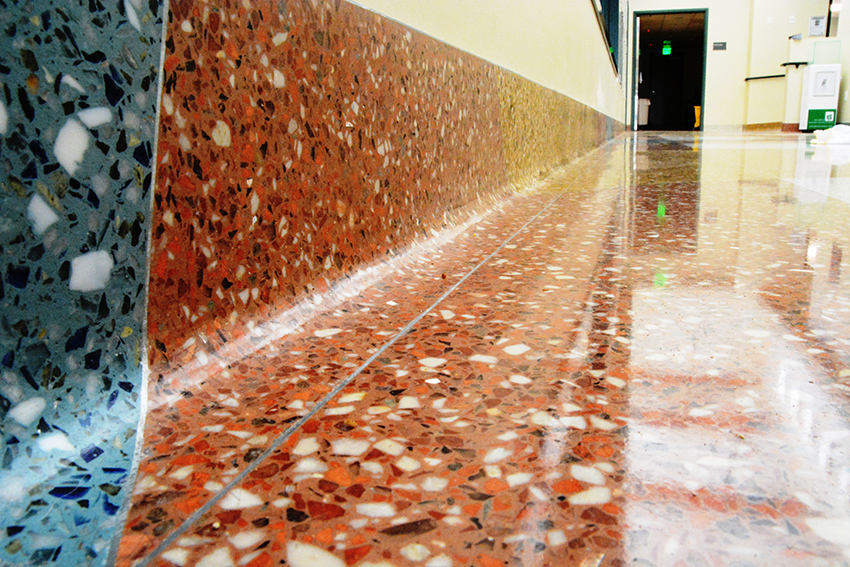
Photo courtesy of Corradini Corp.
At the Pasadena Humane Society, terrazzo flooring seamlessly extends to the wall base.
Poured-In-Place Vs. Precast
Terrazzo is either precast in the factory or poured-in-place on site. Precast is a quicker installation as the panels have already been mixed, ground, and polished, and are all ready to be adhered to the substrate. They can also be cast into molds to create terrazzo designs in just about any shape.
With poured-in-place, all the work is done on site, affording more design flexibility and a seamless look. So while the installation takes longer, the lead time to receive all the materials is shorter than precast. The aggregate terrazzo materials—i.e., marble, granite, recycled glass, porcelain, etc.—are mixed with the resin or cement on site. Craftsmen then hand trowel the terrazzo to the substrate where it is given time to cure. Next, the installer grinds and polishes the material to a seamless finish. The poured-in-place method also allows for thinner terrazzo, as slim as 3/8 inch, which offers the lowest weight per square foot. To determine which method to go with, Maraldo points out that every terrazzo project is different, and the design, schedule, and application need to be evaluated to help identify the best approach.
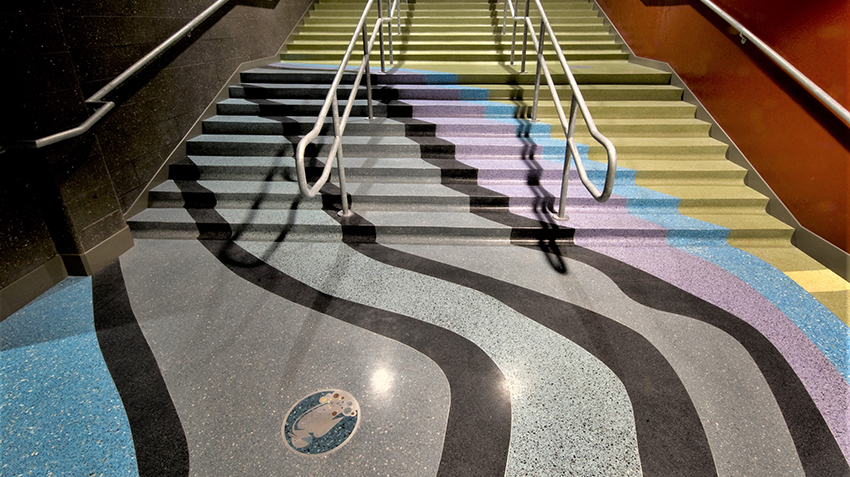
Photo courtesy of Grazzini Brothers and Company
Special attention was paid to create the impression of water cascading down the poured-in-place stairs at Minnesota’s Duluth Entertainment and Convention Center.
Highly robust, long lasting, and hygienic, terrazzo is a designer’s playground, with endless choices of aggregate color, size, and style.
“Timeless, elegant and extremely durable, we have seen a significant resurgence in terrazzo,” relates terrazzo contractor Kevin Rickman with St. Louis-based Missouri Terrazzo. “Architects and interior designers love the idea that they can utilize any color, coupled with just about any aggregate, to create real statement pieces in the design of the building.”
In a similar vein contractor Steve Menconi, general manager, Menconi Terrazzo, Bensenville, Ill., states, “the flexibility of design and color, allows the architect/designer/artist to use all their creative energies to create something very unique and personal.”
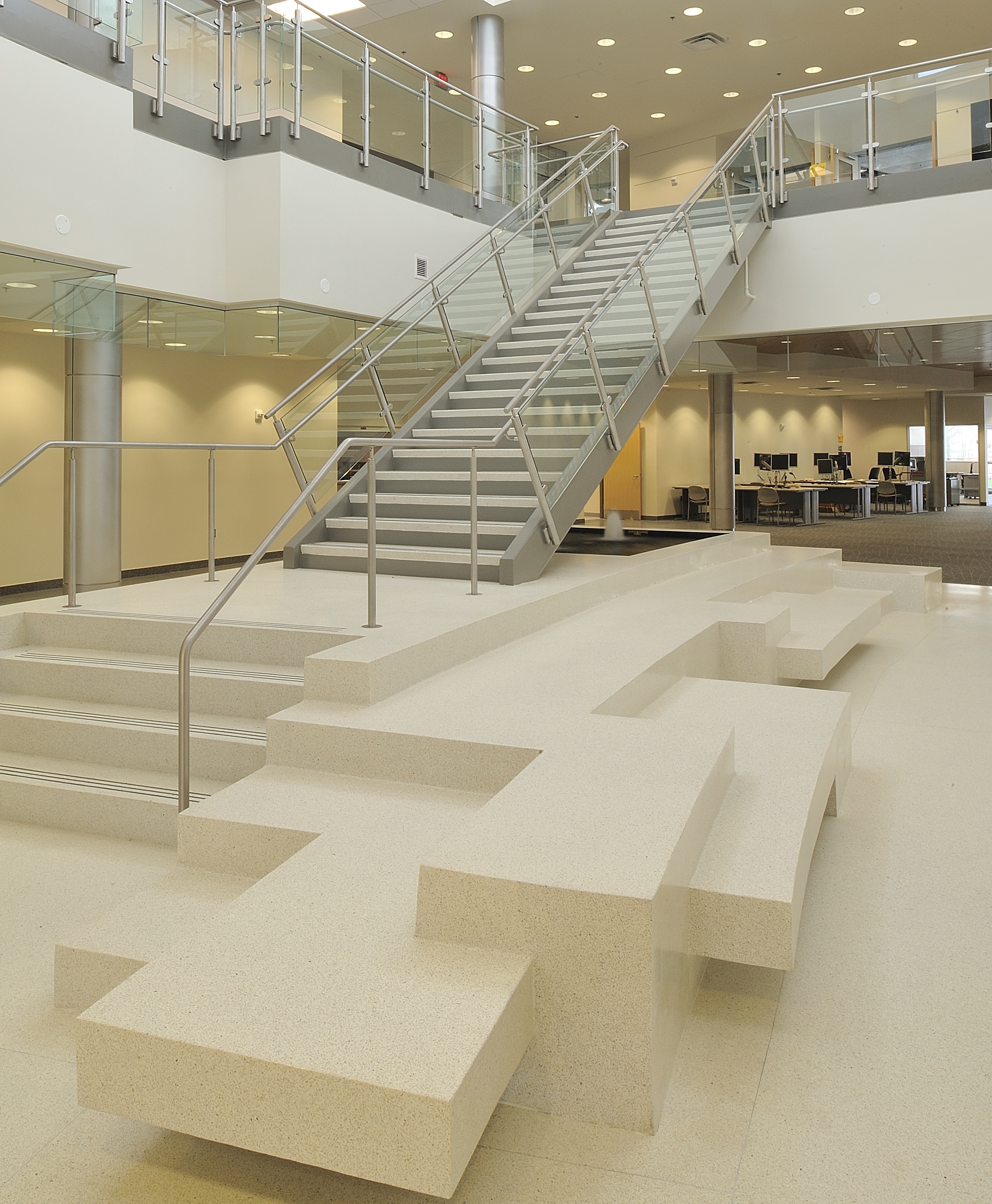
Photo courtesy of David Laudadio
A great example of vertical terrazzo, this sculpture of poured-in-place epoxy terrazzo seating at Tidewater Community College in Norfolk, Va., doubles as an ADA barrier.
Largely known for its flooring designs for airports, hotels, and institutional spaces, terrazzo is not limited to these horizontal designs. In reality, its flexibility and adaptability is propelling terrazzo into a variety of vertical applications from walls to stairs to ADA-accessible ramps to bar fronts.
“Terrazzo can be used on many surfaces and is not limited by the curves and angles that can create issues for other products,” relates Jonathan Maraldo, executive vice president, Southern Tile & Terrazzo, Houston. “The ability to have a seamless transition from the floor to walls, stairs, plinths, or columns can provide a clean and classic finish.”
Sustainability Factors Driving Terrazzo Trends
The concept of terrazzo dates back to the 15th century when workers discovered that they could reuse scraps of marble leftover from the construction of palazzos and villas and mix the fragments with concrete to create a new material. These workers named the material terrazzo, which means terrace in Italian, as they would use it to build inexpensive terraces for their homes. Terrazzo eventually made its way to the U.S. and became a popular flooring material in the early 20th century. But at some point interest faded, until recently.
Riding the sustainability wave and the opportunity to make what’s old new again, terrazzo is making a return. “This eco-minded material falls in line with ‘scrap culture’ and trends in recent years, which are heavily influenced by regenerative reuse, handcrafting, and meaningful imperfections,” states Kelly Eyink, senior interior designer, M+A Architects, Columbus, Ohio. “Highly customized in color, scale and substrate, terrazzo also lends itself to a variety of color palettes. For example, there are a lot of visuals the material can take on, with colors ranging from calming and organic to a playful rainbow effect.”
Shannon Suess, a principal with the Seattle-based MG2 also sees this customization trend as driving interest in terrazzo. “Customization is key today, and terrazzo—a composite material of aggregates that includes shells, stone, marble, glass, etc.— provides infinite colorways and design combinations.” Terrazzo also fits well with designs trending towards large format, seamless, and monolithic looks.
Acknowledging that the reintroduction of terrazzo in this country has been on a steep trajectory for the last few years, S. Paul Singh, vice president/general manager, North American Terrazzo, Seattle, believes the pandemic sped up this resurgence thanks to its antimicrobial qualities of resins and epoxies. As a nonporous, easy-to-maintain material, terrazzo is one of a few surfaces that does not promote microbial growth, which is particularly important in a post-pandemic society.
For any sloped surface, a non-skid can be added to the sealer or non-skid strips can be applied to significantly reduce the risk of falls. The latter involves putting a groove into the terrazzo with a resin, typically aluminum oxide. With a ramp, for example, the general contractor builds the ramp and then the terrazzo contractor will install a terrazzo veneer as the top layer. Then the non-skid is either added into the sealer or as strips.
The epoxy in the terrazzo doesn’t support the growth of mold or mildew and as a polished, smooth surface, it’s very easy to clean. And unlike other materials such as carpeting, terrazzo can last 50 to 75 years or more and it can be recycled, so it does not take up space in landfills.
As a very current and on-trend material, Eyink further describes terrazzo as having a sense of permanence and timelessness. As society transitions from a throw-away culture to one that conserves resources, Debra Babcock, a project manager and director of interiors with Chesney Morales Partners in San Antonio, sees terrazzo as a great fit. Design-wise, “the beauty of terrazzo is that it is at home in a wide range of applications from a classic to an ultra-contemporary interior. Also, through the use of water-jet cutting, intricate custom designs and logos can be created.”
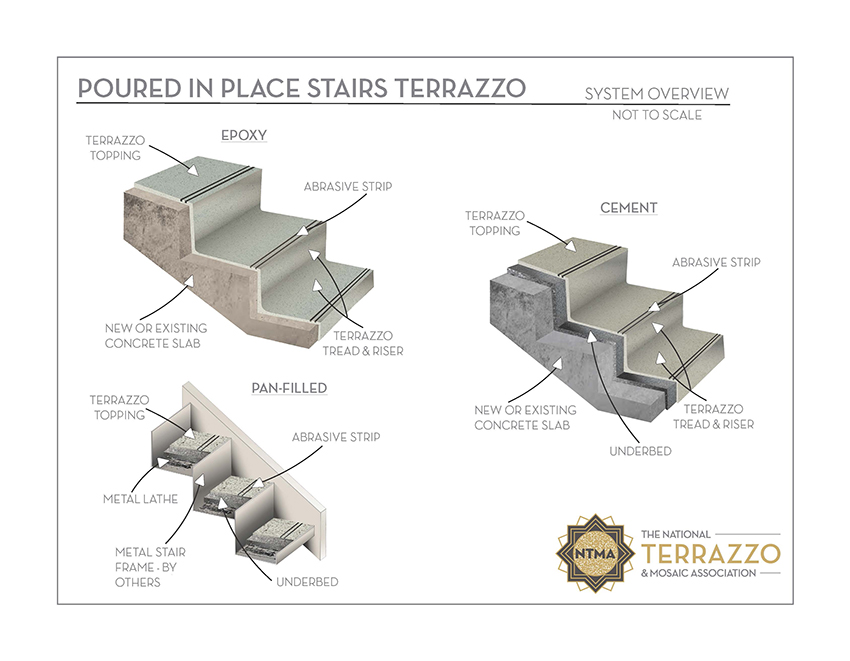
Photo courtesy of NTMA
Whether epoxy, cement, or pan-filled, terrazzo stairs are a highly durable, long-lasting material offering great aesthetics.
Breaking It Down
Terrazzo is made up of 70% crushed aggregate or chips in a wide range of colors and sizes. For example, traditional terrazzo aggregate sizes vary from 1/8 inch to 3/8 inch in diameter. There is also micro terrazzo with very fine aggregate that is just 1/16 inch in diameter. If the terrazzo application calls for strips, designers most commonly select from aluminum, zinc, brass, or plastic.
On the other end of the spectrum, Venetian terrazzo uses larger aggregate sizes, between 5/8 inch and 7/8-inch diameter. Venetian is considered premium terrazzo and must be poured at 5/8 inch or more to accommodate the larger stone, explains Brad Hedges, an Alpharetta, Ga.-based architectural consultant with expertise in terrazzo. Craftsmen will either add all the aggregate to the binder (cement or epoxy), or mix partial amounts of aggregate with the binder and sprinkle in the rest. The mix is applied to the floor, allowed to cure, and is then ground and polished.
Another style is Palladiana terrazzo, which uses fractured pieces of natural stone. Also considered premium terrazzo on account of the extra labor involved in setting the stones, designs can be varied and spaced based upon the architect’s preference. Palladiana is actually terrazzo in its original form, involving palazzo construction workers collecting the marble leftover to create terraces for themselves.
Created with stone, ranging from 2 to 12 inches, workers “butter” the back side of the pieces and place them onto the concrete. Or in some cases, they are adhered to a piece of fiber mesh and then placed inside the mix in the pattern created by the artist, architect, or building owner. Ideally, the pattern has already been vetted in a pre-job mock-up before it is created onsite. These designs can be random or uniform, and can incorporate various shapes of aggregate. Though Palladiana was not in common use for some time, within the past few years it has made a comeback and is now showing up in retail, lobbies, and plazas.
Another terrazzo style is rustic, also called exposed aggregate terrazzo. Instead of polishing, the excess cement is washed off and the aggregate is exposed. This creates a textured surface and therefore provides more slip resistance.
As noted, the binder, or resin, can be either cement or epoxy. Resins are typically devoid of VOCs and are often GREENGUARD certified. They offer exceptional compressive, tensile, and flexural strength. If epoxy resin is used, this also contains recycled materials. Aesthetically, “the resin sets the tone for the color of the sample and can be matched to any paint or Pantone color,” explains Hedges.
In considering cement vs. epoxy, the latter is thinner, lighter weight, uses fewer strips, offers better crack and chemical resistance, and more colors. It offers a lower labor cost, but the material is more expensive than cement. At the same time, cement, particularly sand cushion, requires a greater level of craftsmanship. If the application has a known moisture issue, cement is preferred since the material breathes. In its simplest monolithic form, cement terrazzo is a mixture of portland cement and marble chips, poured into place, ground, polished, and sealed.
To create sand-cushion cement, a thin layer of sand is poured and then a piece of plastic sheet is inserted to prevent the material from bonding to the structural concrete. To keep this in place, a 2½-inch minimum of sand and cement is then poured. Divider strips on a grid pattern are inserted, minimally 4 x 4 inches, and then ½ inches of marble and cement tops it off.
With a typical weight of 25 to 30 pounds per square foot, it’s the best choice for flattening a slab. Its main application is slab- on-grade due to its weight. Found in building lobbies and many schools, sand-cushion cement terrazzo is also used in airports.
While sand cushion cement is terrazzo at its best, not all contractors offer it. The benefits of epoxy end up making it the preferred choice in most terrazzo installations today. Because of epoxy’s unlimited design capabilities, it is the standard for terrazzo art-in-public-places installations.
Vertical Terrazzo Applications
While terrazzo’s traditional application has largely been flooring, in reality, the material’s versatility and advances in technology has helped enable it to break out into a number of vertical applications, including stairs and curbs, walls and columns, ramps, counters and bar fronts, seating and planters.
“We have seen a rise in vertical applications,” observes Rickman. “We think this is driven by the knowledge that architects and designers can match their floor colors on vertical surfaces to create a continuous flow for projects.” Similarly, Menconi states, “In the past few years, we have seen more vertical, wall base and countertops. The ability to provide a seamless surface is quite appealing. We have installed floor, wall, and vanity tops on a few projects and it looks great.”
Because terrazzo can be designed to fit any dimension, it is well suited for matching horizontal and vertical designs that incorporate symmetry, such as wrapping around ramps, curbs, and stairs. Vertical applications, in particular, are popular with schools, higher education, hospitals, and municipal or public work buildings. With enhanced accessibility requirements for additions like ramps, terrazzo is a nice design option. In addition, these facility types tend to make longer term investments, and terrazzo offers long-term durability and the ability to withstand heavy traffic.
Stair treads in particular must withstand the constant pressure of foot traffic. As opposed to hardwood, vinyl, or carpet, terrazzo stair treads are not easily scuffed or scratched. Suitable for all types of staircase systems—including self-supporting stairs, wedge-shaped stairs, treads, and risers—terrazzo stairs are popular with shopping malls, hospitals, and multifamily buildings.
The same applies for seating and planters in these facility types. “The durable nature of terrazzo allows for an easy transition to exterior planters, seating, or water features in exterior public spaces and hotels,” says Ebner. For interior spaces, popular applications for walls, columns, and elevators include hotels, office buildings, retail, stadiums, and arenas as well as schools and hospitals. Particularly with hotels and upscale corporate and retail, vertical terrazzo helps create the sense of grandeur often associated with these spaces. “With the rise of terrazzo floors in lobby applications, the floor translates directly into the elevator cab floors, creating a seamless transition between spaces,” she adds.
Ebner likes to design terrazzo for bathroom walls as a durable alterative to tile or natural stone. Because the binder is impervious, hygiene is enhanced in bathroom environments. In addition, the seamless application means there are no grout joints to keep clean. The seamless, monolithic blending of poured-in-place floor and wall application is also a popular strategy for bathroom designs.
As for counters, bars, and bar fronts, they’re trending in multifamily clubhouse spaces, restaurants, and hotels. “Terrazzo counters and bars are a great way to incorporate the material in a very intimate way because these spaces are focused on creating great experiences that impress,” reports Eyink. With tenant amenity spaces, owners are looking for durable, high-end materials and terrazzo fits the bill. Style-wise, Ebner likes to combine metal, wood, and terrazzo on bar tops and kitchen counters to create a warm hospitality vibe.
When designing terrazzo for bathrooms, epoxy resins offer better chemical resistance, particularly when combined with porcelain or granite chips. Bathroom applications typically incorporate eco-friendly sealers like polyaspartic or water-based polyurethane. While these sealers are easy to maintain, it’s important that building owners/facility managers follow proven maintenance procedures.
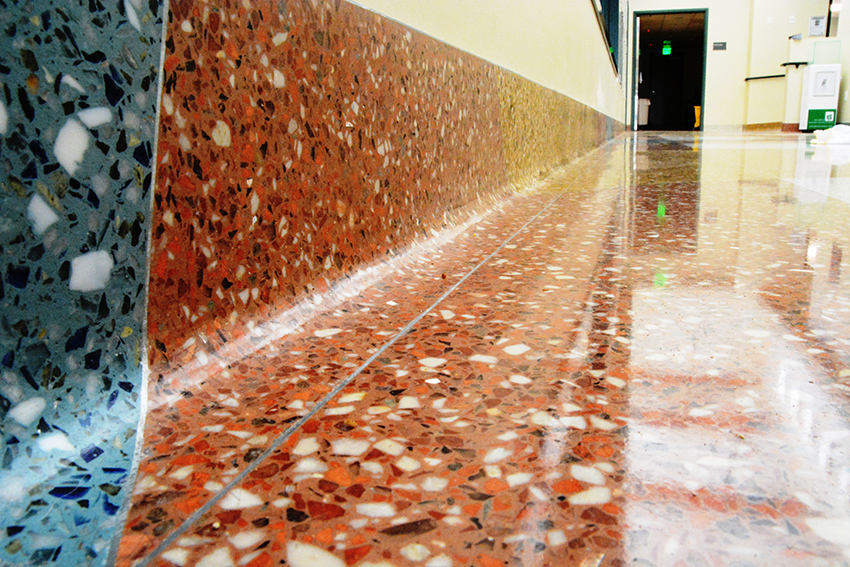
Photo courtesy of Corradini Corp.
At the Pasadena Humane Society, terrazzo flooring seamlessly extends to the wall base.
Poured-In-Place Vs. Precast
Terrazzo is either precast in the factory or poured-in-place on site. Precast is a quicker installation as the panels have already been mixed, ground, and polished, and are all ready to be adhered to the substrate. They can also be cast into molds to create terrazzo designs in just about any shape.
With poured-in-place, all the work is done on site, affording more design flexibility and a seamless look. So while the installation takes longer, the lead time to receive all the materials is shorter than precast. The aggregate terrazzo materials—i.e., marble, granite, recycled glass, porcelain, etc.—are mixed with the resin or cement on site. Craftsmen then hand trowel the terrazzo to the substrate where it is given time to cure. Next, the installer grinds and polishes the material to a seamless finish. The poured-in-place method also allows for thinner terrazzo, as slim as 3/8 inch, which offers the lowest weight per square foot. To determine which method to go with, Maraldo points out that every terrazzo project is different, and the design, schedule, and application need to be evaluated to help identify the best approach.
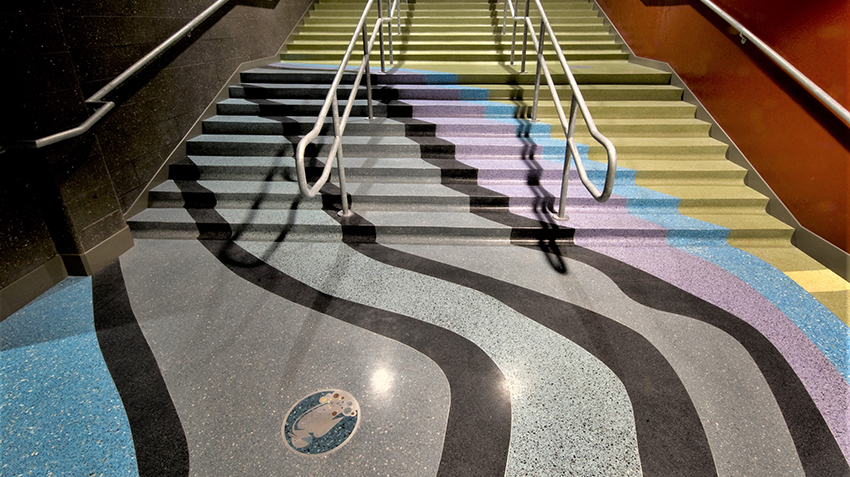
Photo courtesy of Grazzini Brothers and Company
Special attention was paid to create the impression of water cascading down the poured-in-place stairs at Minnesota’s Duluth Entertainment and Convention Center.
Best Practices For Installing Vertical Terrazzo
For vertical applications, they can be poured-in-place or precast, though there are advantages and disadvantages to each method. “Personally, I prefer poured-in-place for vertical applications,” relates Hedges. “The key is to field-measure the concrete or steel structure for the manufacturing of the precast,” advises Rickman. “The precast is then installed using a bonding/adhesive material and the joints are then caulked with a predetermined color.”
If the project calls for long runs of stairs or complex curves, Hedges recommends poured-in-place. “Poured-in-place allows for custom dimensions and flexibility when dealing with ‘out of whack’ site dimensions,” adds Menconi. Rickman explains that the most important part of the poured-in-place stairs installation is making sure they are installed as flat as possible so that the grinding and polishing are minimal.
If the project only calls for one or two stairs, or a small landing, then precast terrazzo will be the most efficient. Another possibility is a precast radius or a column wrap terrazzo cove base. “Precast terrazzo can be used at existing steel stairs to create a new elevated look without requiring new structure,” adds MdeAS Senior Associate Tricia Ebner. For precast stair treads, they can be produced in a maximum length of up to 8 to 9 feet before requiring a seam. Project managers should anticipate lead times of 10 to 12 weeks.
For designs with a terrazzo plinth or seating around the bottom of the stair, these can be either precast or poured-in-place. If there are other poured-in-place terrazzo applications for the project, then the latter is likely the way to go. Otherwise, precast will likely make more sense.
For terrazzo column installations, contractors use both poured-in-place and precast methods. “Poured-in-place is installed on a radius, using divider strips for the top edge, a base bead, and a strip to separate it from the floor pour – a toe strip,” explains Rickman. With precast, it’s important to take careful field measurements to accurately determine the diameter of the columns. They typically range between 4 and 12 inches in height and are manufactured in two, three, or four sections, depending on the size. “After installing, the joints will be grouted or caulked to fill in the voids in the pieces as well as along the floor and top edge of the sections,” says Rickman.
With a terrazzo wall design, precast is easier and cost effective, but poured-in-place is also an option. “Terrazzo’s precast application creates the opportunity for monolithic wall sources – as if carved out of giant block – it is powerful and bold,” observes Dan Shannon, partner, MdeAS Architects, New York City. With poured-in-place, the wall surface is first prepped, a prime coat is mixed, and then a thick mixture of cement (or epoxy) and aggregates are troweled on the wall. Then every inch is ground four to five times. According to Rickman, other vertical surfaces, such as wainscoting or planters, can also be clad with precast terrazzo, which is usually made at a ½-inch thickness.
When selecting a terrazzo system for an elevator design, Hedges advises against cement terrazzo as it’s not suited to handle the stresses of the elevator cab movement. “Epoxy terrazzo is the correct system because the epoxy binder provides excellent physical properties, particularly a very high flexural strength which allows the terrazzo system to flex and accommodate the loading of the elevator cab,” he explains.
If poured-in-place is selected, this offers the most design flexibility, the ability to accommodate larger elevator cab sizes, and offers the lowest weight per square foot as the panels are at just 3/8 inch. Precast offers the advantage of a quicker installation, but weighs a bit more, with a typical ½-inch thickness plus 1/8 inch of setting material.
If a project calls for terrazzo ramps, poured-in-place is the preferred method, but precast can be used as well. Regarding the former, Ebner recommends epoxy. “The epoxy system allows for long uninterrupted spans allowing for a level uniform ramped surface. This is an ideal solution for commercial lobbies where a consistent floor finish is required to negotiate floor level transitions.”
Sharing a best practice for these applications, Rickman relates, “We usually use a laser to shoot a line on the sides to make sure the finished terrazzo follows all the ADA requirements in the amount of slope allowed. If needed, non-slip tape or an epoxy with non-slip additive may be used to avoid any chance of slipping,” explains Rickman. Whether precast or poured-in-place for any of these applications, Maraldo explains that the best way to maintain quality and craftsmanship is by working with an experienced NTMA contractor who can help the design team navigate the details and intricacies of their project.
Vertical Terrazzo Case Studies
A number of noteworthy projects do a great job of demonstrating the versatility and beauty of vertical terrazzo applications. For the renovation and expansion of the Emancipation Park Community Center in Houston, Perkins+Will was looking for a stylish yet easy-to-clean material capable of withstanding the foot traffic in this public space.
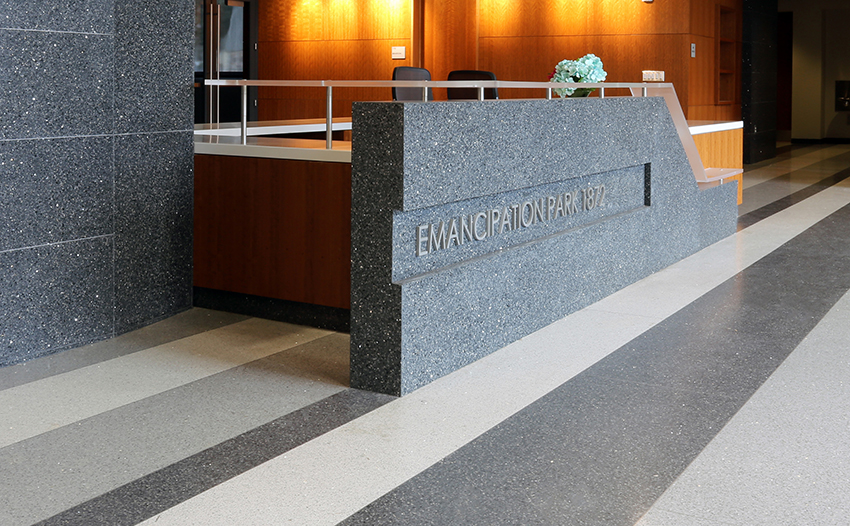
Photo courtesy of Mark Dean Photography
White and gray precast epoxy terrazzo was designed for the desks, walls, base, and donor wall at Emancipation Park Community Center in Houston.
Offering a seamless transition from the flooring, precast epoxy terrazzo was designed for the desks, walls, base, and donor wall. Matching the colored strips of the floor, the terrazzo was created in white, medium gray, and dark gray. The terrazzo slab pieces were originally cast as 5-by-8-foot panels and then cut to the required sizes, relates Maraldo. “The biggest challenge that we faced creating the precast panels was maintaining the flatness of the pieces. Consistency was necessary because the panels were then spread around the building in various applications. Variation in the different sizes and colors would have resulted in lippage at the edges during installation,” he explains. In all, the project called for 1,500 square feet of precast terrazzo in various sizes, connected with terrazzo strips and hand-ground for a seamless appearance.
For another project, traditional sand-cushion cement terrazzo was installed on the floors, ramps, and stairs in the basement level of Houston’s 35-story Bank of America. The Understory—a 35,000-square-foot hub—houses a market, bar, restaurant, and tunnels connecting to the buildings across the street.
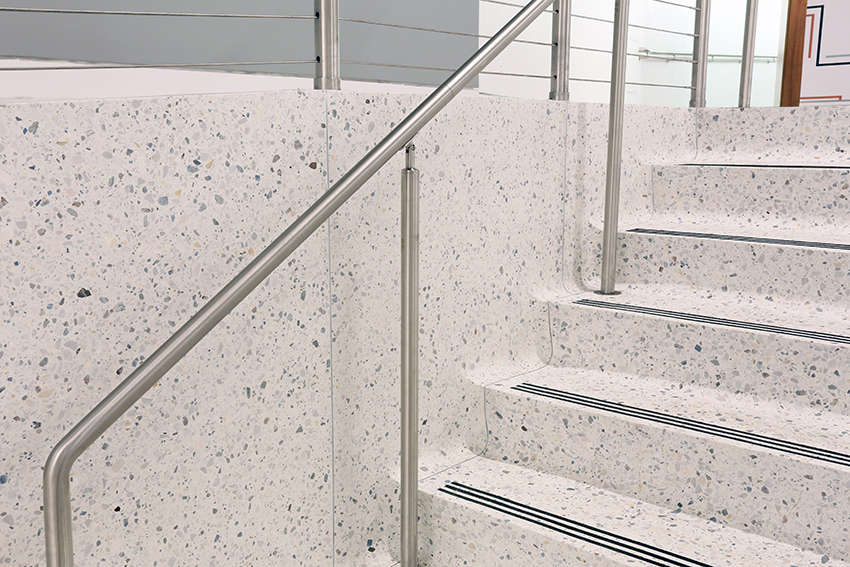
Photo courtesy of Mark Dean Photography
Venetian aggregate and a handcrafted, heavy-top divider strip create a clean, classic aesthetic for the floors, ramps, and stairs in the basement level of Houston’s Bank of America.
The monolithic Venetian terrazzo serves as the focal point of all interior finishes, and was selected as the common denominator to coordinate the aesthetic of this classically simple, multi-use space. The larger Venetian aggregate and handcrafted, heavy-top divider strip beautifully complement the scale and elegance of the site. The aggregates and divider strips were poured-in-place and required a high level or craftsmanship to install the tread and risers, and grind the large chips on the edge of the ramps to achieve the perfect flatness of vertical surfaces and consistent aggregate density on all surfaces.
“With the larger aggregate, the terrazzo had to be poured thicker than usual, and there was difficulty working the large aggregate into the mix at the stairs and ramp. The installation and grinding were both more tedious than with epoxy terrazzo,” reports Maraldo. In order to maintain a high chip density and consistency, the crew tried to incorporate as much aggregate into the mix as possible, while seeding any areas that appeared to lack the required density. To match the ramp and its wall with the floor, this involved constantly checking to ensure that the proper tolerances were being maintained. The Bank of America Tower also bears the distinction of being the first LEED v4 Platinum Core & Shell certified project in the U.S.
Another Houston project earned the 2022 Job of the Year award from the National Terrazzo & Mosaic Association – the city’s Museum of Fine Arts, featuring extensive sand-cushion Venetian terrazzo flooring, staircases, raised seating, coves, and a plinth.Paying homage to the still beautiful and functioning green terrazzo floor installed by the contractor’s grandfather some 65 years ago, the project incorporates a transitional lobby space replicating the original terrazzo.
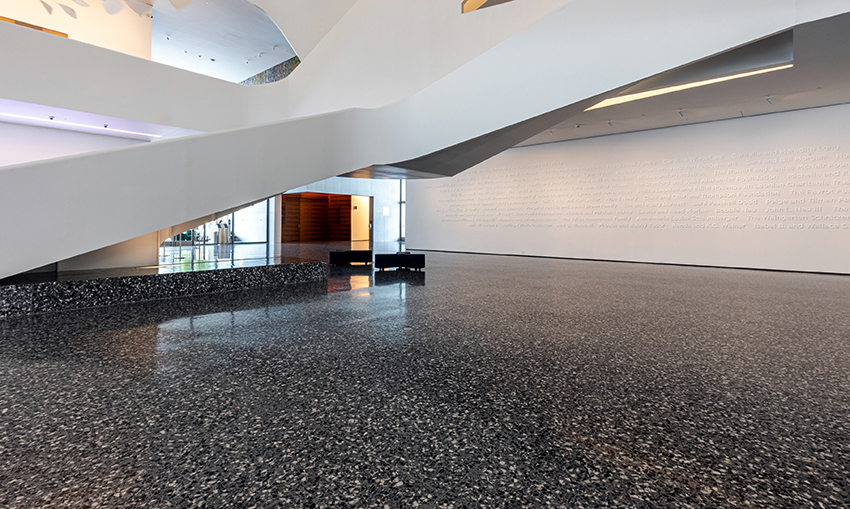
Photo courtesy of Jaime Leigh Sonnier-Casa de Camera
At Houston’s Museum of Fine Arts, terrazzo is significantly featured in flooring, staircases, raised seating, coves, and a plinth.
In the Kinder Building, which houses international collections of modern and contemporary art, more than 48,000 square feet of sand-cushion Venetian terrazzo with larger (sizes 4-7) chips were installed.
Complementing the gallery’s stairways and glass, Steven Holl Architects specified a blue-gray color for the terrazzo. Since a level, flat floor was critical for the art display, and to accommodate air vents located on the floor flush with the terrazzo, a high level of craftsmanship was required. All the zinc divider strips were formed by hand onsite and the craftsman delivered consistent color throughout all the spaces.
From the museum’s lower level, a cementitious terrazzo raised seating platform anchors the 61 steps leading to the intermediate level and the main floor with a rear cove, requiring precise installation. The staircase’s three landings were poured in place. The coved base was precast, installed with a zinc toe strip, and polished top with a 1/8-inch bevel. The next poured-in-place suspended staircase was designed with 41 steps of varying lengths and widths, set on a plinth, and serves as an architectural element for the space.
A tunnel connecting the Kinder Building to another part of the complex incorporates 4,000 square feet of white sand-cushion terrazzo where smaller size-1 and size-2 chips were installed.
Terrazzo also played a key role in the expansion and upgrade of the Denver Art Museum, most notably the creation of a seamless, elliptical staircase. In celebrating the 50th anniversary of the museum’s Martin Building, Fentress Architects modeled the new staircase after famous Italian architect Gio Ponti’s original poured-in-place cement terrazzo staircases. Now functioning as the visual and logistical center of the complex, the epoxy thin-set terrazzo was designed as a two-story central spiraling balustrade which unfurls like a ribbon. Appearing as a monolithic whole, the treads and risers are precast terrazzo; the landings are poured-in-place to eliminate joints; and the guard walls are poured-in-place, hand-ground, and polished. During construction, terrazzo artisans mocked up the section of the stair with the tightest curve to demonstrate the handwork and allow for refinements to the design. Each precast tread was templated prior to the installation of the walls, and the guardrails were installed to align perfectly with a 2-inch stainless-steel reveal.
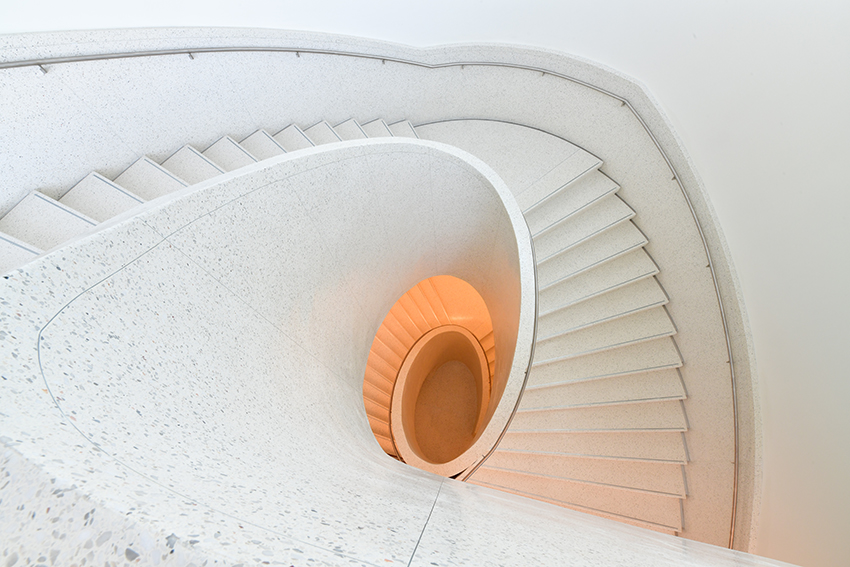
Photo courtesy of David Laudadio
At the Denver Art Museum, an upgrade and expansion of the Martin Building incorporated a spilling terrazzo staircase modeled after the famous Italian architect Gio Ponti’s original poured-in-place cement terrazzo staircases in the building.
The original 50-year-old staircases in the Martin Building were also fully restored through regrinding, grouting, patching, and polishing to like-new condition. In addition, terrazzo was installed in each of the building’s seven lobby floors, and numerous terrazzo window sills were created along with a top-set base.
Another heavily trafficked area benefitting from terrazzo’s durability is Chicago’s Midway International Airport, which recently added three new bridges. Architect Muller & Muller specified 95,000 square feet of terrazzo flooring and 20 4-foot-tall, wrapped columns, with an integrated cover base perfectly clad to the wood and steel structures.
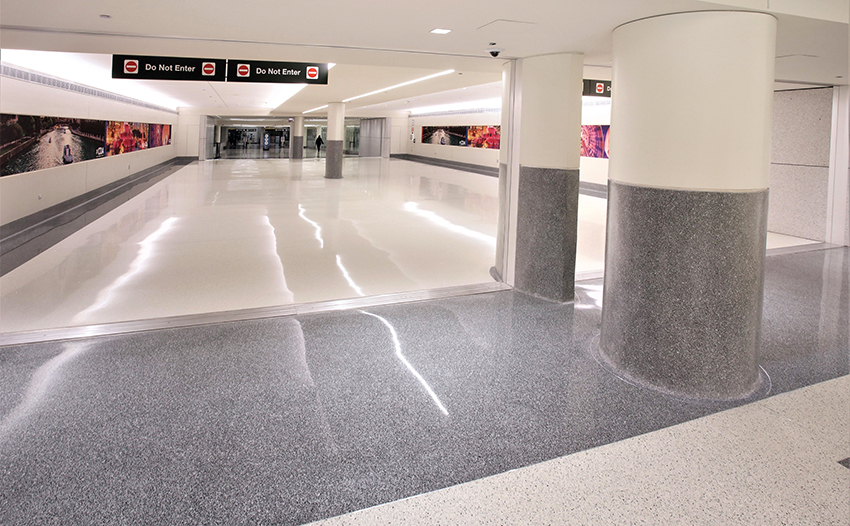
Photo courtesy of FotoGrafix
Three new bridges at Chicago’s Midway International Airport feature expanses of terrazzo flooring, columns, and cove bases.
“Terrazzo column bases meet a high design standard while still being a cost-effective solution for high-trafficked areas, specifically in an airport where column bases in queuing areas are continuously subject to abuse from luggage, carts, and even vehicles,” explains Ed Frankowski, AIA, LEED AP, Muller & Muller, Chicago. Sharing some details on the installation’s predominant challenge, Menconi Terrazzo’s Menconi says the column was carved out of a random piece of stone, yet his team was tasked with creating a solid stone look. “We also had to create a surface that is flush with the rest of the column, and provide the same dimensions at all areas.” The team’s hard work paid off, as the polished floors flow seamlessly into the coves at the columns.
Showcasing Vertical Terrazzo In Schools
When Eureka High School in Eureka, Mo., added a new STEM addition, the design included a patterned epoxy terrazzo floor with short walls, a 20-foot-long tread and risers, and a handicapped-accessible ramp. The classic terrazzo was crafted in four muted tones with glass and marble aggregate and aluminum divider strips, and showcases the Wildcat mascot in school colors.
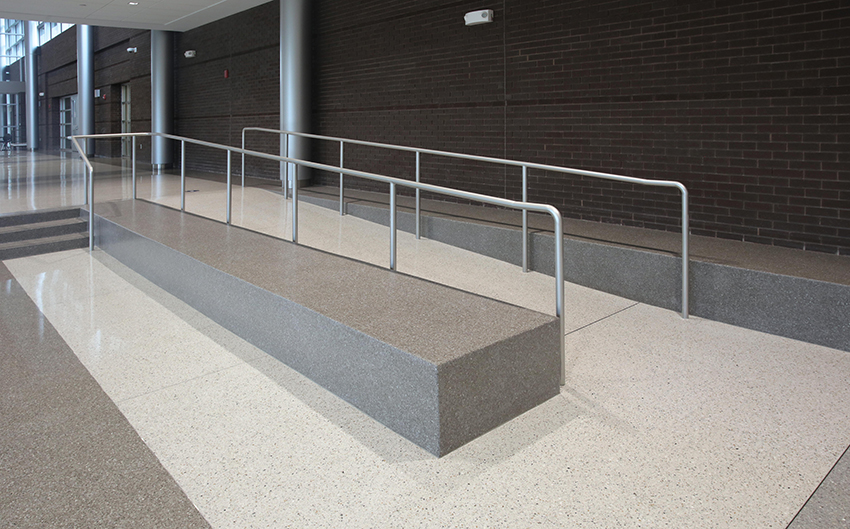
Photo courtesy of Viken Djaferian; FotoGrafix
A patterned epoxy terrazzo floor with short walls, 20-foot-long tread and risers, and a handicapped-accessible ramp lend durability and aesthetics to Eureka High School’s new STEM addition in Eureka, Mo.
Relating how Missouri Terrazzo installed the terrazzo, Rickman explains that the ramp, short walls, tread, and risers where formed with concrete along with the concrete floor pour. “We infilled all the areas with a sand and cement mixture to make sure when the terrazzo was installed it would be perfectly straight and flat.” The infill typically ran from 1/16 inch to ¼ inch, depending on the existing concrete, and the terrazzo in these areas was normally 3/8-inch thick. In addition, a cove was installed at the base of the step and riser. “After the terrazzo installation, the crew made sure to grind, grout, polish, and seal the terrazzo while maintaining the flatness of the install. The ramp, stairs, and stringers were also carefully installed and ground to be as flat as possible. The nosings are ground off with a nosing tool to give it a nice round appearance,” states Rickman.
Missouri Terrazzo was also involved with the renovation and expansion of Ladue Horton Watkins High School in Ladue. Mo., where the main lobby area is amphitheater-style seating with benches of poured-in-place terrazzo, inlaid maple seats, and precast terrazzo steps. Terrazzo, in a four-color design, continues throughout the new addition in the art room, commons area, hallways, and cafeteria with a 4-inch precast wall base. “This was a very interesting project as the bench seating was poured-in-place terrazzo, while the stairs were precast terrazzo,” relates Rickman.
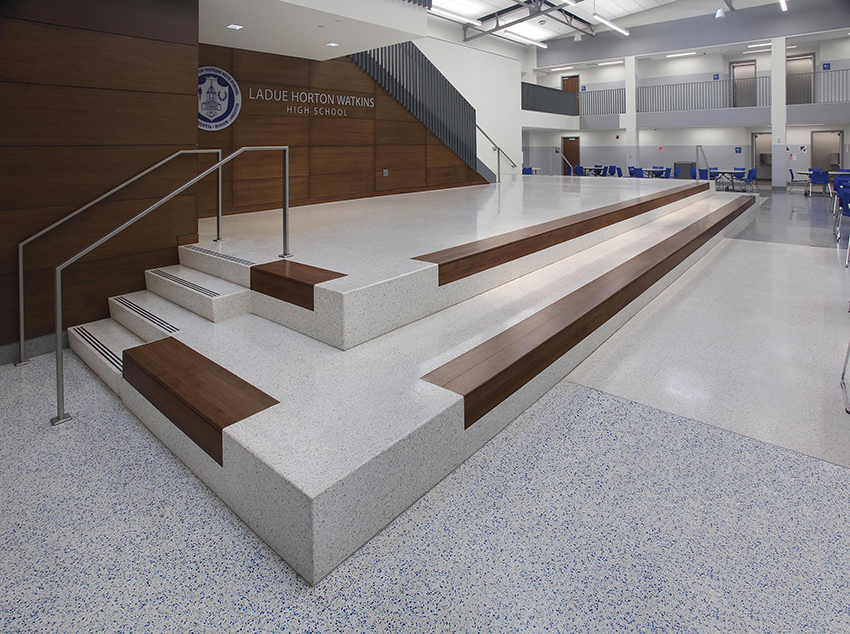
Photo courtesy of FotoGrafix
At Ladue Horton Watkins High School in Ladue. Mo., amphitheater-style seating with benches of poured-in-place terrazzo, inlaid maple seats, and precast terrazzo steps are featured in a new renovation and expansion.
Another challenge was making sure the benches and stairs met at the desired height and locations. With the precast terrazzo, caulk joints were needed between the pieces, and the joints had to be mimicked in the poured-in-place style to make sure the design met the architect’s requirements for aesthetics. “The most common thickness of the epoxy terrazzo is 3/8 inch, but as a result, the bench seating was left with a 2-inch gap to meet the existing floor. This area was then infilled with an epoxy and sand mixture to make certain that when the terrazzo was installed, it would meet all of the needed heights elevations,” explains Rickman.
In addition, wooden seats were placed within the terrazzo. “Wood grounds were used to mimic the wood seats so the terrazzo could be poured, rough ground, grouted, polished, and sealed to the exact height of the wood. Every aspect of the terrazzo had to be perfect to match adjacent design choices,” he explains.
Unique Applications
In early 1964, the Beatles performed their first U.S. concert at the iconic Uline Arena, also known as the Washington Coliseum in Washington, D.C. Unfortunately, over the years, the historic venue fell into disrepair until Douglas Development brought in Antunovich Associates Architects to help revitalize it. “It was an exciting opportunity for me as a designer,” says Kevin Crosby, associate principal at Antunovich. We had “seen this decaying industrial building with its iconic shape for many years, never realizing its full potential, [and were] then given the opportunity to investigate and explore the buildings to revitalize them to what they are today.”
Contributing to the NoMa (“north of Massachusetts Avenue”) neighborhood restoration near Union Station, the architect was interested in doing something playful and compelling with the lobby. Their concept was to create an inlaid planter, flush with the floor and filled with succulents, moss, river rock, and a grand ficus tree.
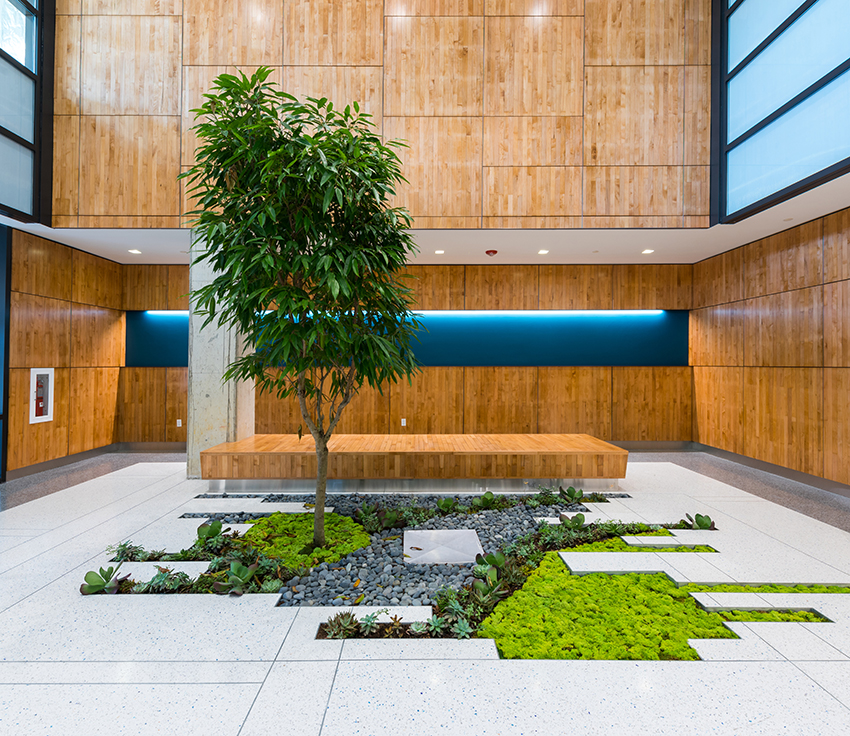
Photo courtesy of Brycen Fischer
Washington D.C.’s historic Uline Arena is now a restored mixed-use facility featuring a terrazzo floor with an inlaid planter of succulents, moss, river rock, and a grand ficus tree.
Capitalizing on terrazzo’s versatility, particularly as a poured-in-place material, the team was able to create terrazzo shapes that extend into the planting pit in varying lengths and widths. “The great thing is being able to set an intriguing form and fill it in to be seamless,” Crosby explains. To make the installation work, careful substrate preparation was essential, particularly at the planter, where scrupulous work was required to make it dimensionally correct, square, and plumb. With a 4-inch sand/epoxy substrate on top of the mason’s rough dimensional installation of concrete masonry units, a perimeter was created. The extensions were built up with 3/8-inch epoxy and the exposed perimeter was then finished with a custom 3-inch zinc edging with an integrated L-angle. Due to the size and configuration of the extensions, all surfaces had to be hand-ground and polished to match the rest of the floor.
Antunovich Associates Architects currently houses its offices next to the main lobby and its terrazzo floor with planters. “We are proud to have brought the historic Uline Arena back to life,” reports Crosby.
As another visually compelling example of vertical terrazzo adding a sense of beauty and flair, for the Pacific Gate Condominiums in San Diego, Kohn Pedersen Fox Associates specified contoured and flat terrazzo wall panels and a terrazzo floor in the lobby area. Inspired by the curving forms and materials of the local waterfront, large rock, and mother-of-pearl aggregate allude to the sand, sea, and sunlight. In addition, randomly intersecting brass ring inlays decorate the floor and the textured terrazzo fascia panels. One particular challenge was setting the contoured terrazzo fascia panels along a 10-foot-tall curved wall. The precast panels were predrilled and then attached to one side of the plywood substrate. A heat gun was then applied to the panel to bend it to the wall and then attached to the other side.
In a unique adaptive reuse project, terrazzo from the century-old St. Vincent’s Hospital in Indianapolis was restored as Ivy Tech Community College’s student center. Blending the old with the new, cementitious terrazzo in both the main entry and a monumental stairway was refurbished and new epoxy terrazzo in complementary colors was installed in the common areas of the building’s new sections. While original terrazzo’s natural patina and irregularity of colors made color matching quite challenging, the resulting surfaces present a well-earned character in the form of a classic, retro design. “Terrazzo allows for a design of patterns to flow from space to space that you can’t do with other materials, and it is a hard surface with a high level of durability,” explained project architect Kevin Shelley, AIA, LEED AP, principal at Schmidt Associates in Indianapolis. “Your imagination is almost the limit of what you can do with it.”
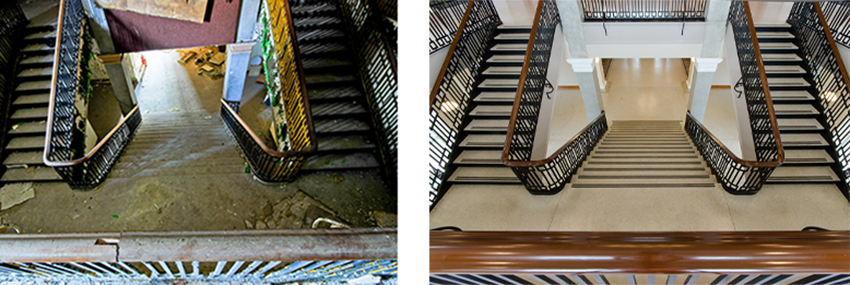
Photo courtesy of Blakley Corporation
Ivy Tech Community College's student center in Indianapolis features a century-old, restored terrazzo staircase combined with newly built terrazzo flooring.
On another adaptive reuse initiative, the beauty of terrazzo is showcased as a paneled bar front and its durability as seamless floor-to-ceiling restrooms, Nashville’s 81-room boutique Fairlane Hotel is a transformed mid-century bank building. Requiring a high level of craftsmanship to design to vertically install the poured-in-place vertical bar front, the team utilized hand bent divider strips to enhance the retro tones and patterns of the lobby and café. The three-color epoxy terrazzo floor unifies the aesthetic of the lobby, with its brass feature wall and original oak paneling, while adding value as a low-maintenance, durable floor.
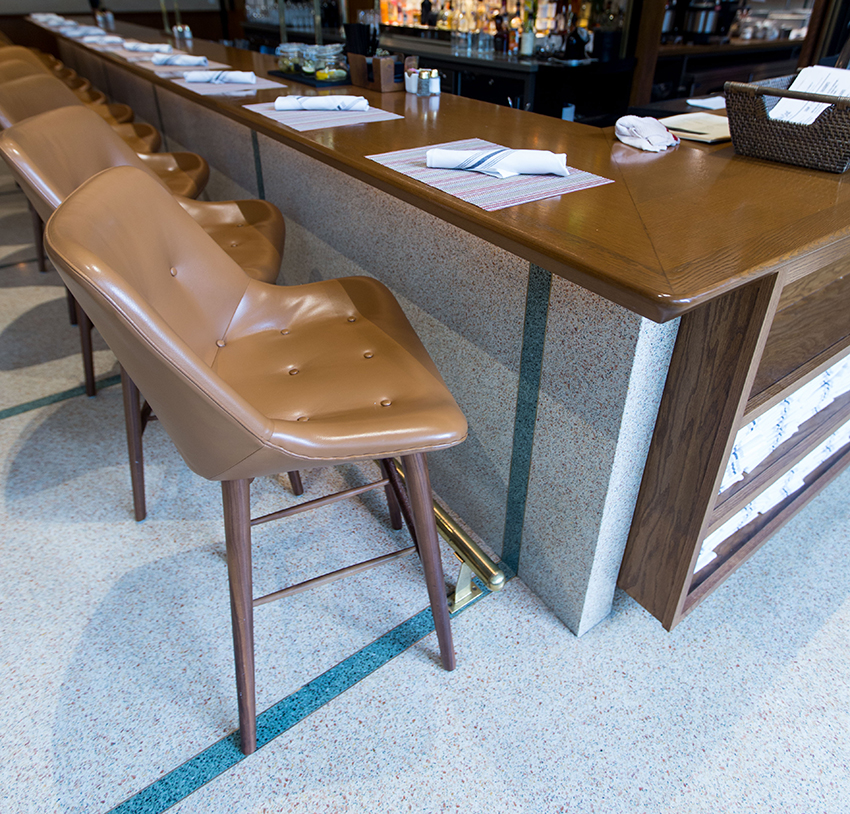
Photo courtesy of Brad Hedges
A terrazzo bar front and floor-to-ceiling terrazzo surfaces deliver a beautiful aesthetic for the adaptive reuse of a mid-century bank building into the boutique Fairline Hotel in Nashville.
Highlighting one more noteworthy project, at the Statewide Library Archives Museum in Juneau, Alaska, a 10,000-square-foot, accurately scaled state map in the lobby is made from epoxy terrazzo, and precast terrazzo stairs and landings match the concrete sidewalks outside of the museum. The crafted lobby installation uses three contrasting colors, incorporating 100-percent recycled concrete aggregate. Zinc and brass divider strips form the intricate shoreline and highlight specific features on the map. To support a radiant heat system below the floor, expansion joints were placed in the terrazzo and color-matched so as to not detract from the terrazzo design.
On The Horizon
Looking forward, fine speckled terrazzo is forecasted to be a trend this year, reports Eyink. “With the base color coming through, the more understated look is a fresh take on the popular look. Not only is the elegance of the material attractive, but it also has benefits from a broadened opportunity for recycled content and more streamlined manufacturing capabilities.”
As a slip-resistant, low-maintenance, bacteria-resistant surface, terrazzo is well suited to meet today’s post-pandemic needs. Continuously demonstrating its versatility for a variety of vertical applications, designers and contractors anticipate that new and exciting vertical terrazzo designs will continue popping up in hotels, schools, airports, municipal facilities, retail, and more. “The ability to easily customize terrazzo’s colors and designs has given new meaning to an old art,” concludes North American Terrazzo’s Singh.
Barbara Horwitz-Bennett, is a veteran architectural journalist who has written hundreds of CEUs and articles for various AEC publications. BHBennett.com