View course on architecturalrecord.com »
Great claims have emerged from the field of 3-D-printed architecture, including reports of entire houses, costing barely a few thousand dollars, built robotically, within a day or two, from digital instructions delivered via cellphone app. It almost seems the stuff of science fiction, yet—with growing numbers of “printed” buildings delivered—it’s clear that the technology is rapidly evolving. Less immediately apparent is which parts of these structures are actually printed and just how affordable, sustainable, and quickly producible—from start to finish—such projects are. Is this technology really on the cusp of revolutionizing home-building, putting environmentally sensitive, customizable, high-quality yet swiftly produced houses within reach across the entire economic spectrum, even to underserved populations?
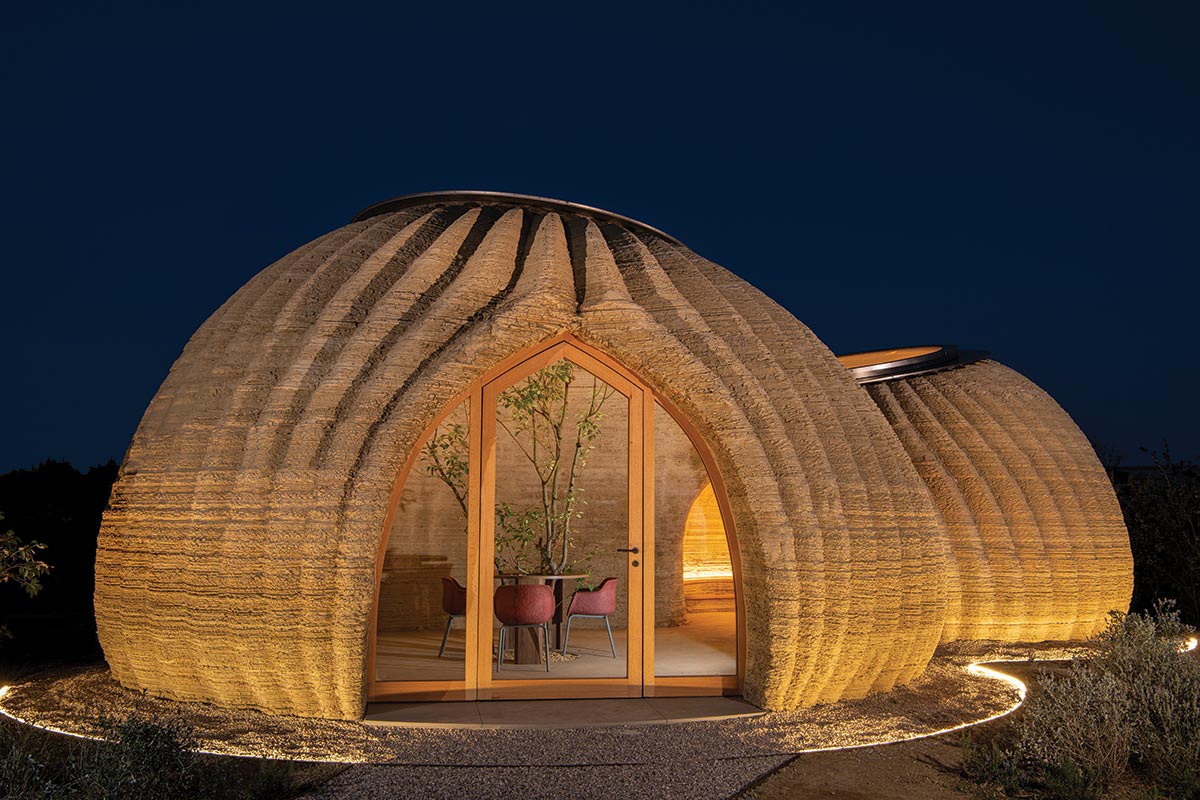
Photo © Iago Corazzo
In Ravenna, Italy, Mario Cucinella Architects has built a twin-domed prototypical house of earth reinforced with corn husks.
The term 3-D printing refers to a range of digitally guided techniques that lay down sequential layers or deposits of soft or fluid material—such as concrete, polymers, or metals—which fuse together, acquiring hardness, solidity, and strength. In the 1980s, rapid-prototyping techniques emerged for small objects, but it wasn’t until this millennium that 3-D-printing technology took off with applications in fields as diverse as automotive design, biomedical engineering, and architectural model-making. For construction, the approach only gained traction in the U.S. within the past few years.
Whether the print medium is piped out toothpaste-style as an extrusion, or laid down in a powdery or cellular manner, the process is always additive, in contrast to traditional construction’s subtractive means—cutting, stamping, or otherwise extracting desired sections of material. As a result, 3-D printing, also called “additive manufacturing,” dramatically reduces waste or scrap.
Whereas conventional construction tends to be a slow, fragmented, inefficient process, often yielding less-than-optimal energy performance, 3-D printing—which, so far, produces primarily building shells or wall systems—offers the promise of accelerated production time (as the machines can theoretically run 24/7); significant reductions in construction labor (which is often in short supply); and the potential to replace multiple wall layers—including sheathing, cladding, insulation, and interior finishes—with a single printed entity. The technology also allows for the creation of continuous thermal envelopes, with printed-in channels for m/e/p systems. And it can produce complex geometries—with curves, slopes, and intricate internal cavities—at no greater expense or effort than flat, orthogonal planes. “In fact, the more curving and complex the form, the easier it usually is to print,” says Stephan Mansour, a Toronto-based 3-D-printed-construction specialist. The technology also has the potential to produce simultaneously, with a single printer, multiple neighboring houses—each with a different customized design—thereby scaling production and reducing cost.
Most construction printers are either robotic-arm or gantry style—both operatable on- or off-site. The choice inevitably involves trade-offs. Robotic versions tend to be less expensive and more mobile, usually requiring significantly less setup and disassembly time. A gantry, for example, often needs a tractor and crane for on-site installation, whereas many robotic printers can simply be forklifted into place; and gantries, in most cases, call for underlying poured-concrete pads. With up to six axes, robotic arms can also be nimbler with extremely sloped, complicated volumes. On the other hand, gantries typically offer the advantages of greater stability and reach, with the capacity to print taller, bigger buildings. Gantry systems also tend to require less specialized operating skill or expertise than their robotic-arm counterparts—and, yes, it’s true: some printers are cellphone-app-controlled.
Many companies—including ICON, in Austin, Texas, and Advanced Intelligent Construction Technology (AICT), in Torrance, California—build directly on-site. But others, such as Mighty Buildings, in Oakland, California, take a prefab approach with factory-controlled conditions—as Mighty has done for its composite, partially 3-D-printed wall panels, as well as entire small Accessory Dwelling Units (ADUs), trucked to their final locations.
One key challenge has been the formulation of printing media that flow and cure appropriately, while retaining abilities to bond or fuse without collapsing or deforming under the weight of subsequent layers. “Advances with admixtures, binders, and accelerants have been essential,” says Mansour. While admixtures make materials, such as concrete, pumpable and optimally fluid, binders enhance strength and fusing, and accelerants modulate or speed curing rates. As ambient temperature and humidity change, concrete requires ongoing adjustments. By contrast, Mighty Buildings has developed its own UV-cured polymer, inspired by dental bonding techniques, that hardens instantly, forming a strong, self-supporting, lightweight stonelike substance, enabling the company to reduce the material needed—and print horizontal ADU roofs without formwork.
Last year, the Italian firm Mario Cucinella Architects (MCA) 3-D-printed, in Ravenna, Italy, a prototypical house, called TECLA, made of local raw earth, reinforced with rice-husk fibers. Borrowing from ancient beehive-shaped houses, MCA’s twin-domed building shares their natural temperature-retention traits and biodegradability. (During the life of the structure, a binder prevents the material from degrading, or breaking down.) As in many additively manufactured buildings, TECLA’s exterior walls are printed with multiple layers of thickness, including a truss-like inner cavity for strength and insulation.
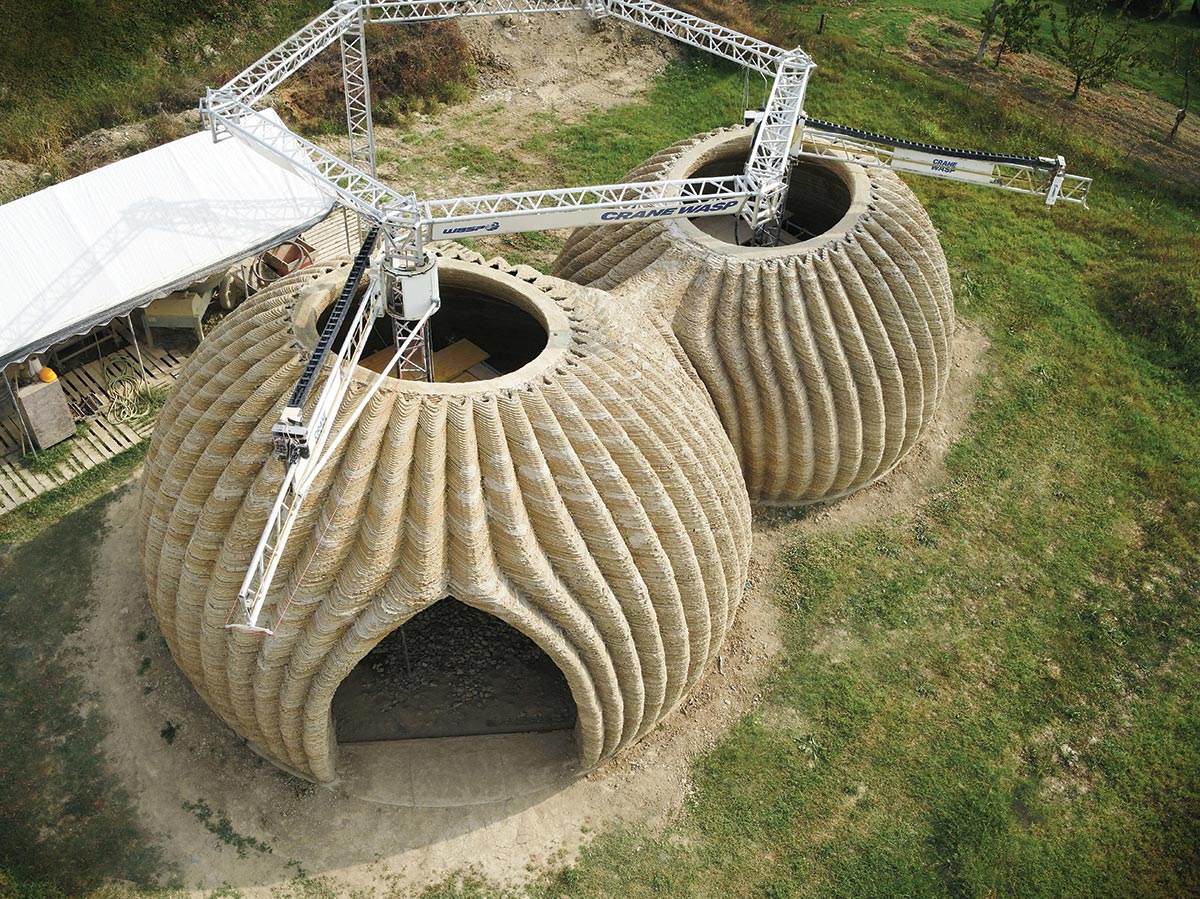
Photo courtesy of Wasp and Mario Cucinella Architects
The Ravenna house was built using a crane printer.
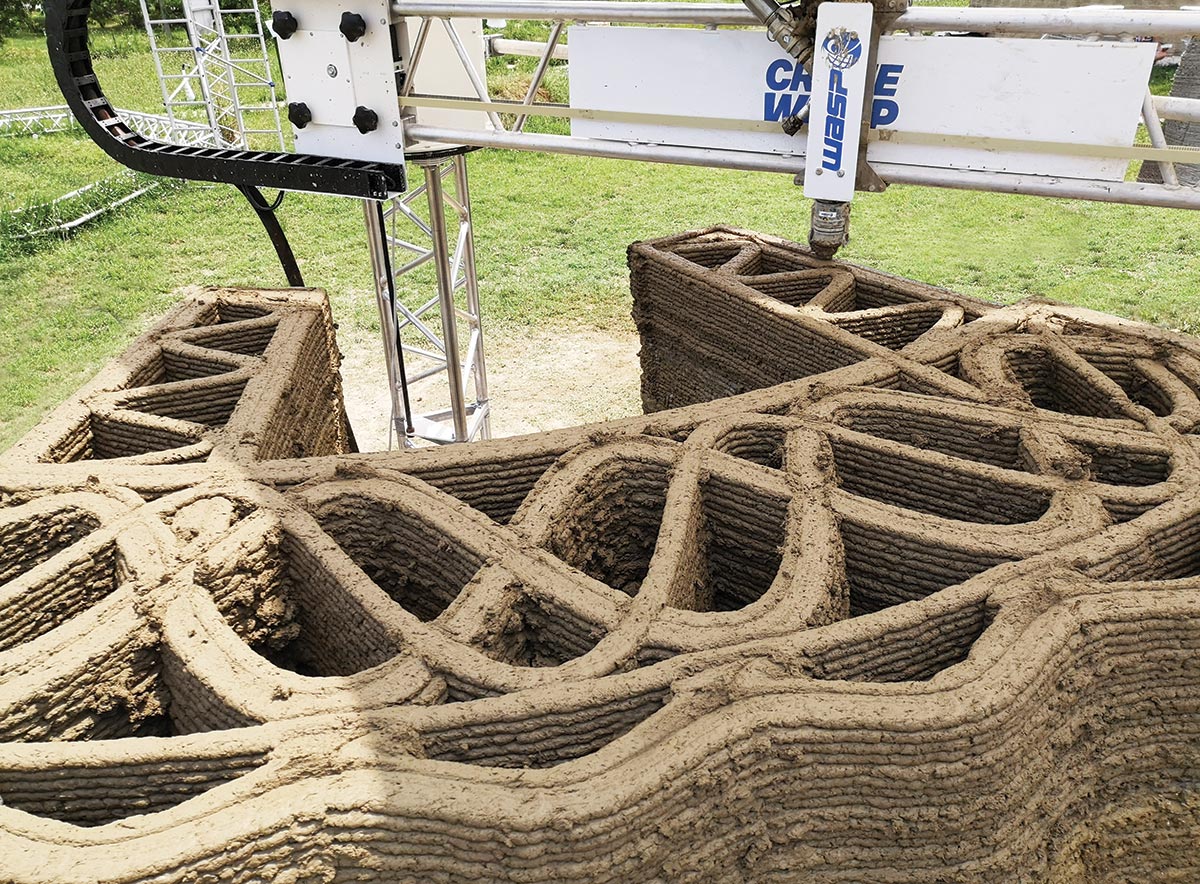
Photo courtesy of Wasp and Mario Cucinella Architects
The walls have truss-like inner cavities.
The most common material for 3-D-printed houses is modified concrete, or mortar with minimal fine aggregate, or none at all. While such buildings may be sustainable in their material-waste and thermal efficiencies, the concrete—especially if it contains Portland cement—tends to have high embodied energy and carbon. Several companies are exploring ways to reduce that footprint by, for example, substituting fly ash for at least some Portland cement; revisiting eco-friendlier ancient-Roman techniques for attaining cementitious properties; and adding carbon-sequestering ingredients, such as hemp fiber or biochar. “You can print with almost anything—wood sawdust, recycled, crushed glass, or used coffee grounds—and people are experimenting with it all,” says Mansour. “But concrete, with its building-safety and construction record, is more familiar and therefore still more publicly acceptable.”
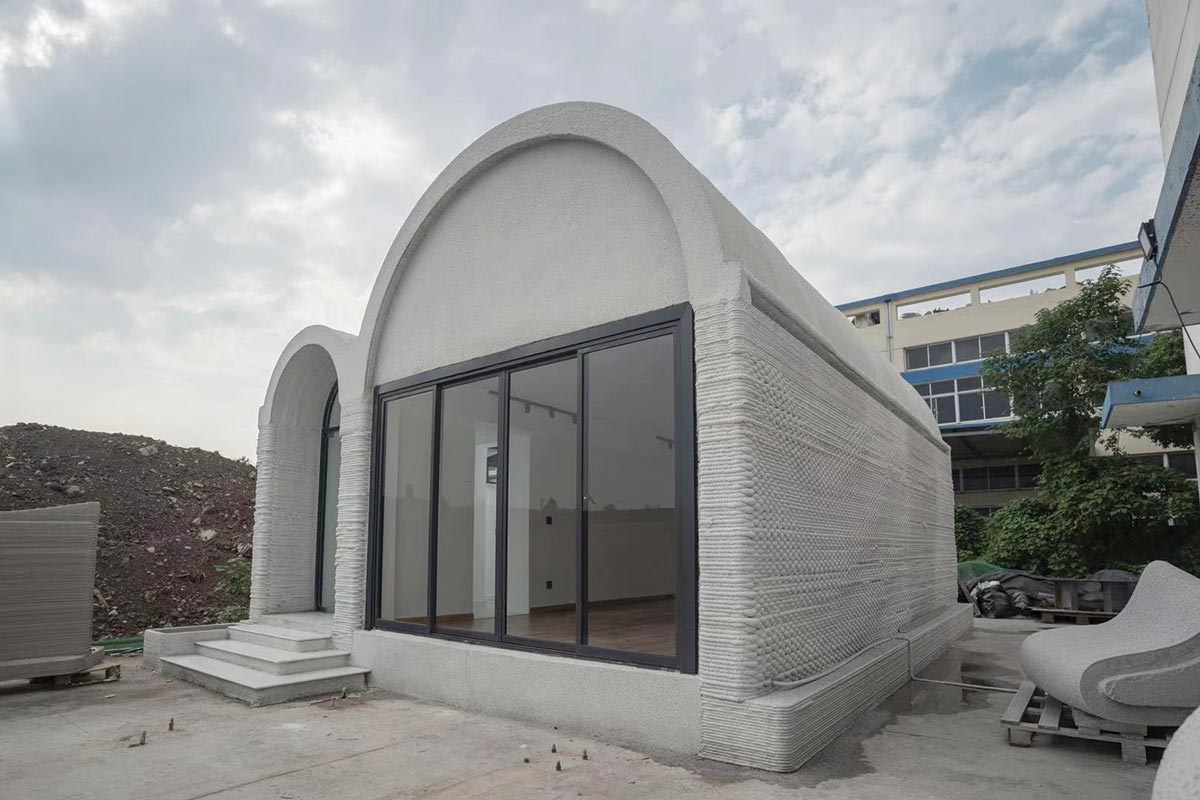
Photo courtesy of AICT
The barrel-Vaulted ROOF on a house developed by AICT for low-income families was additively manufactured lying on end, and then hoisted atop the 3-D-printed walls.
Overcoming general reluctance and, perhaps more critically, regulatory issues, remain hurdles for 3-D-construction printing. Building codes and regulations are gradually making more applications of the technology permittable, but “it’s an ongoing process,” says Mighty Buildings cofounder Sam Ruben. “We’ve been working with UL [Underwriters Laboratories] and others for years to help create new standards and open the space for more innovation.” His company’s prefabricated wall panels—which include some conventional layers—incorporate a structurally redundant steel frame, for instance, because it’s still required. And many industry colleagues continue to install rebar, even where integral reinforcing fibers, along with truss-like sections, technically provide adequate strength. “Once we have reliable standards at the top levels, they will trickle down to national, state, city, and more local authorities,” says Mansour, who is working with the standards- development organizations ISO and ASTM to establish international 3-D-printed-construction guidelines and requirements.
Meanwhile, most “printed” structures today are actually hybrids that include conventional methods and components. Many companies—such as ICON or Mighty Buildings (in its non-ADU projects)—still use traditional, wood-framed roofs above printed walls, bypassing the conundrum of how to print horizontally overhead without formwork. Notable exceptions include the small, prototypical house by AICT, designed in 2020 for low-income families in Kenya—although its barrel-vaulted roof was additively manufactured lying on end, as a separate component, and then hoisted atop the building. As with TECLA or Mighty’s ADU, printed roofs today typically have vaulted, domed, or partially curved configurations that essentially extend vertical walls, relying on the structural properties of arches. And the few companies that print foundations tend to produce hybrids, with, for instance, permanent printed-concrete formwork becoming the perimeter of a traditionally poured slab.
For most other building components or fixtures, such as toilets or windows, there’s still an efficiency, economy, and overriding feasibility in conventionally fabricated options. Printers are not yet designed to shift back and forth among different nozzles and material reservoirs, or coordinate dissimilar curing times. And even with walls alone, print constructors often build interior partitions traditionally to retain flexibility for future renovation.
With the learning curve still steep for 3-D printing, new works increasingly push the potential. ICON explored a technology-specific architectural language, along with technical innovation, in its House Zero—a 2,000-square-foot demonstration project with a separate ADU, designed by Lake | Flato and presented at the SXSW Conference, in Austin, in March. While significantly boosting sustainability and strength, its 3-D-printed walls are also sculpturally expressive. And, whereas many builders cut manually into soft printed walls to insert windows, Lake | Flato innovated with more precise openings (mostly floor-to-ceiling), programmed with high-performance thermal breaks, ready to receive window assemblies.
The goal of achieving, as ICON cofounder/CEO Jason Ballard puts it, “twice the quality, at half the cost, in half the time” remains elusive. While many companies are reluctant to reveal monetary figures, rough comparisons between printed and framed walls suggest meaningful savings in time, labor, and materials. House Zero and its ADU were printed simultaneously with a single gantry machine in 10 days at approximately half the cost of comparable stick-frame walls, according to one traditional contractor. For a 1,700-square-foot house for Habitat for Humanity, in Tempe, Arizona, built in collaboration with German-based Peri Group construction company, the walls took two to three workers about three weeks. “By contrast,” says project lead Samuel Hager, “that usually takes our crews of 20 to 30 volunteers one to two months.”
Ideally, the walls, once printed, are completely done. Lake | Flato exposed the concrete inside and out at House Zero, celebrating the process while achieving a surprisingly soft look from a hard material. But not every designer and builder finesses the technique so deftly, and not every client appreciates a corduroy texture. Though robotic techniques exist for smoothing printed surfaces, interior walls often get old-school treatments, including drywall and paint. But even then, most 3-D-printed shells, eliminating needs for vapor barriers, cladding, and more, have fewer layers than conventionally built ones, while achieving, it is believed, thermally superior results. (Along with their precise and complete seal, layered printed walls can be designed to eliminate energy-inefficient thermal bridging, as found in stud construction.)
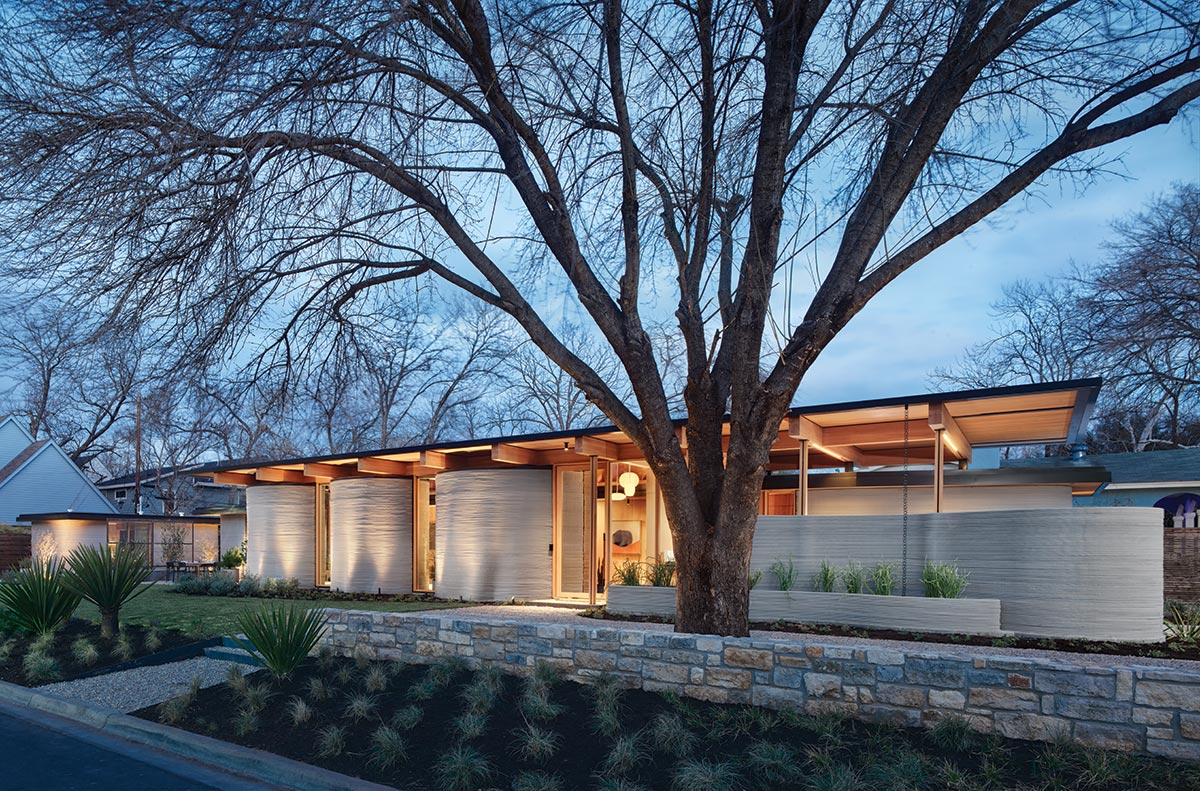
Photo courtesy of Casey Dunn
3-D-Printed structures by ICON include House Zero..
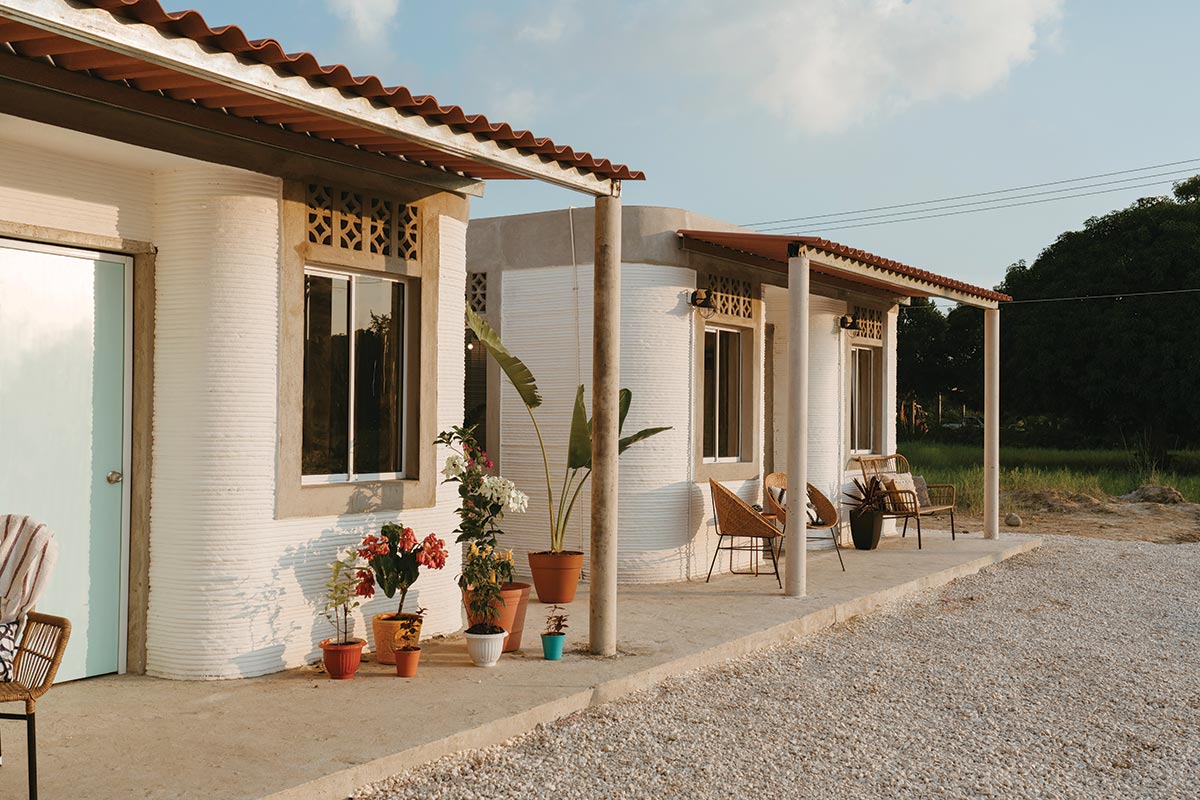
Photo courtesy of Joshua Perez
Housing for families experiencing extreme poverty in Mexico.
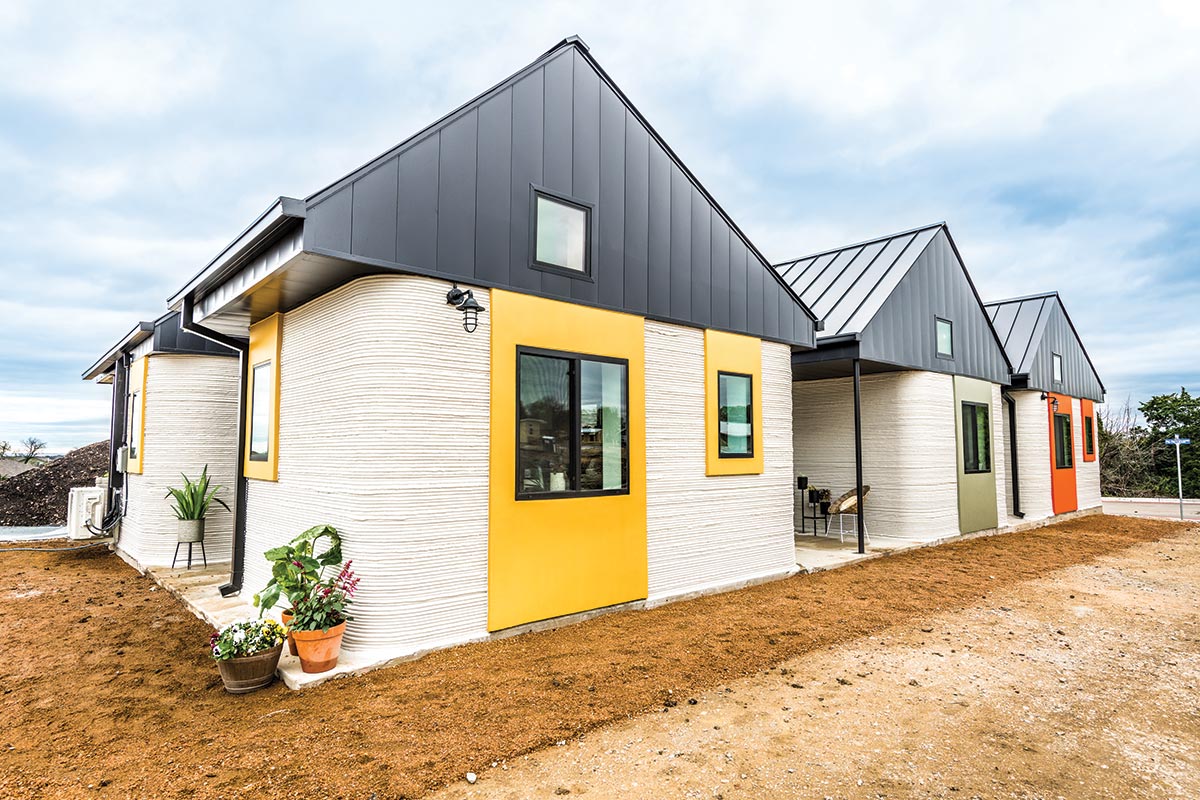
Photo courtesy of Regan Morton
A demonstration project in Austin designed by Lake | Flato; housing for the chronically homeless, also in Austin.
Another important advantage to 3-D printing, says AICT cofounder Zoey Zhao, is “the digital files created by architects with engineers are exactly what gets printed—with certainty up front about the time required.” (Assuming no glitches.) Also, with chases printed into walls, says Hager, “you’re not waiting for framing to finish before beginning electrical or plumbing—it’s so different from the linear one-trade-at-a-time schedule of conventional home construction, where a single hiccup can have ripple effects, causing delays and cost overruns.”
When companies cite the number of printing “days,” however, the total hours aren’t necessarily sequential, but spaced out over longer periods. And the assumption that the machines will run 24/7 can also be misleading, as many neighborhoods don’t allow around-the-clock construction; some printing materials require curing time between layered sections; and the equipment still needs continual oversight from human beings. Besides, claims of quick-printed houses don’t often publicize the time taken to finish the traditional parts. Both House Zero—a high-end design with top-quality finishes—and the affordable, traditional-style Habitat home in Arizona took nearly a year, including pandemic and supply-chain delays, to complete.
A myth, propagated across the internet, is that ICON has printed small houses for only $4,000 each. “I wish it were true,” says Ballard, “but not yet, anyway.” Although his company generally declines to disclose costs, it has confirmed that, more realistically, it built a 350-square-foot house in 2018 for $10,000—but that amount only covered the walls.
Still, without compromising quality, the method offers some cost and time savings that can help address global housing shortages. “Even if we worked nonstop with traditional methods, there aren’t enough hours for human laborers to meet the growing need,” says Ballard. “Every year, we’re millions of homes deeper in that hole—particularly for affordable options. This calls for a paradigm shift.”
ICON has already built clusters of small but thoughtfully designed houses for impoverished families in Mexico, in collaboration with the nonprofit New Chapter, and for chronically homeless people at Community First! Village, in Austin. Habitat for Humanity has printed a house in Virginia, in addition to the one in Arizona. And AICT’s design for housing in Kenya (so far, a single prototype, constructed in China) was commissioned by the United Nations Refugee Agency, UNHCR. 3-D printing could also potentially address emergency disaster relief.
With housing shortages spanning income levels, Mighty Buildings is currently focused on the “forgotten middle—firefighters, teachers, and others,” says Ruben, adding that his company aspires to ultimately address a broad demographic spectrum. Scaling and speeding up the process, Mighty is working with the developer Palari Group and L.A.-based Ehrlich Yanai Rhee Chaney Architects to print a cluster of 15 houses in Rancho Mirage, California. ICON is partnering with Lennar homebuilders to print a community of 100 houses near Austin, co-designed with BIG-Bjarke Ingels Group.
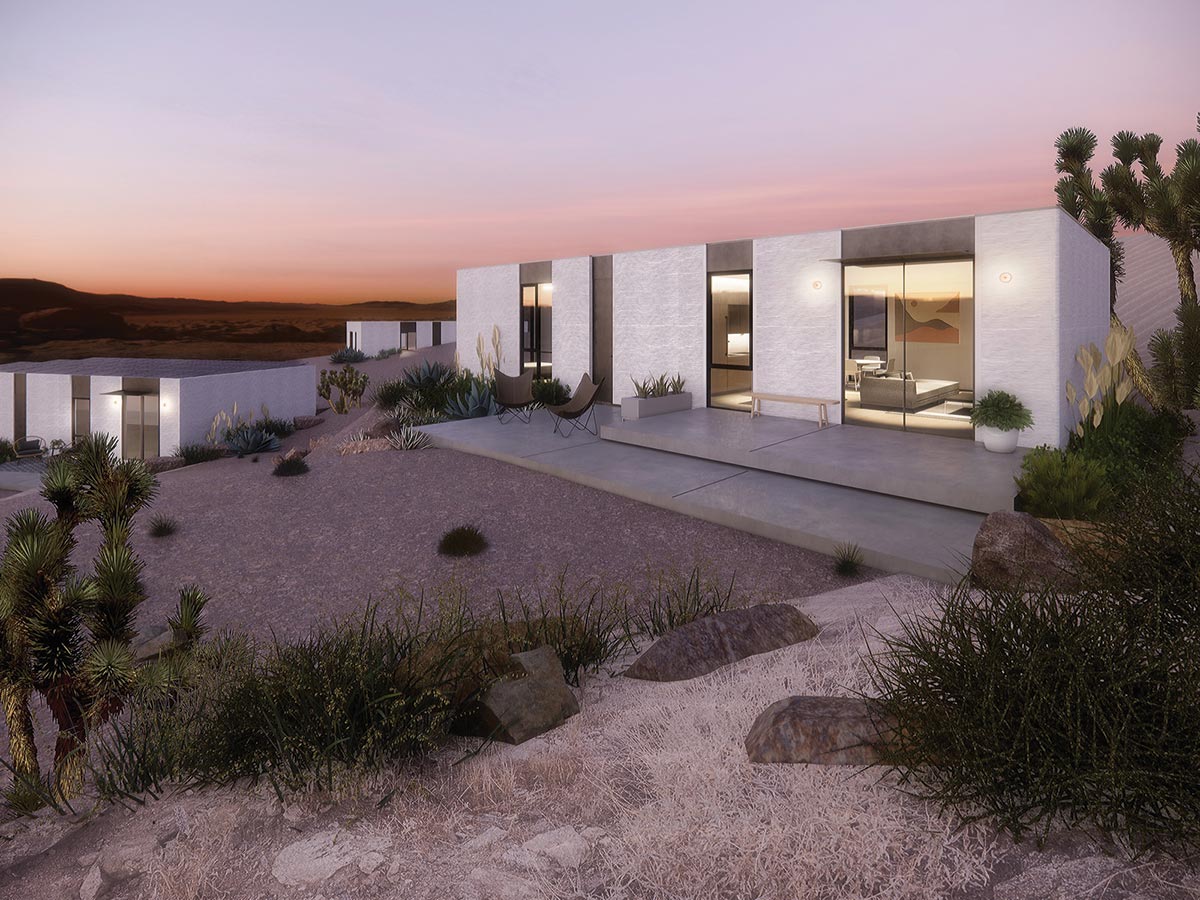
Photo courtesy of EYRC Architects
Some Companies print and assemble modules in a factory, as Mighty Buildings plans to do for a group of houses in Rancho Mirage, California, designed by Ehrlich Yanai Rhee Chaney.
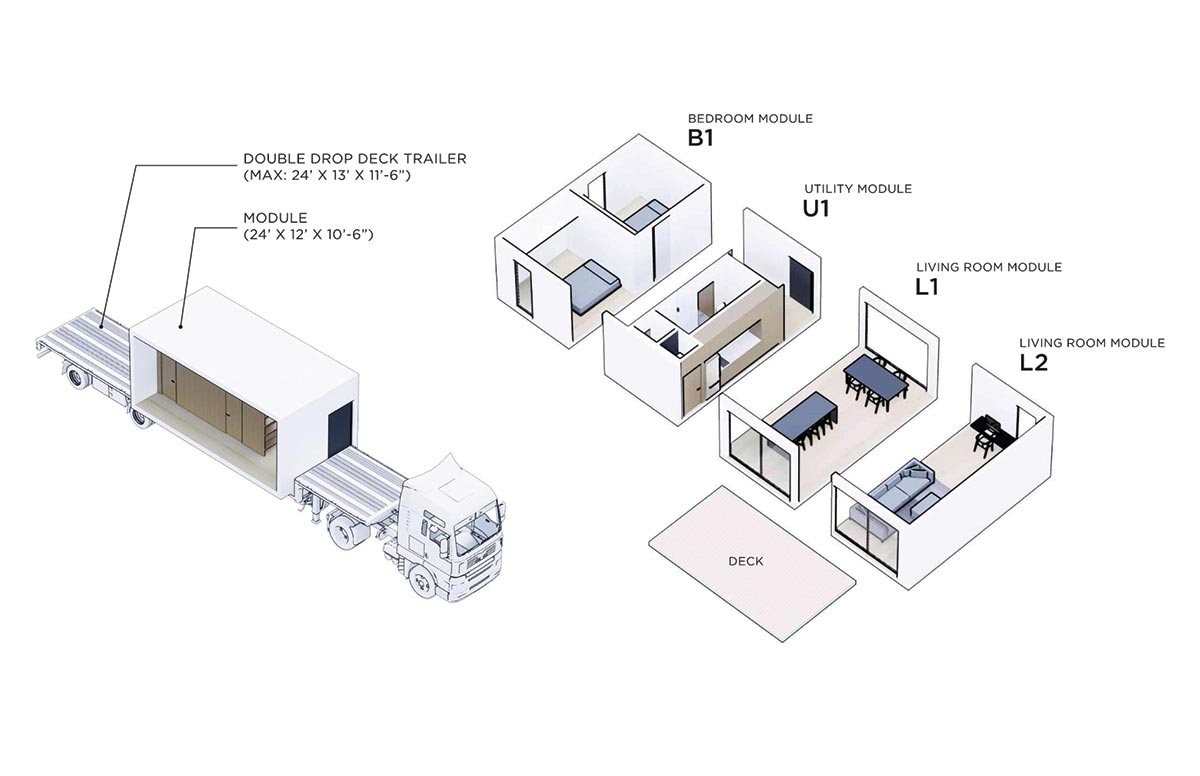
Illustration courtesy of Mighty Buildings
While the U.S. has not yet permitted 3-D-printed construction above one story, changes allowing taller buildings are in the works. In Asia and Europe, where the technology took off years ahead of the U.S., higher structures already exist. In China, in 2015, Winsun completed a five-floor apartment building incorporating printed walls; and a three-story residential low-rise went up in Germany last year.
Regarding concerns that 3-D printing will eliminate work opportunities, proponents maintain that it will introduce different (although probably more skilled) jobs; that the current labor shortage is real; that automation in other forms is already happening, by necessity, across construction industries; and that printing will provide one valuable approach among others that will remain.
Meanwhile, the industry continues to gain momentum. Last year, Dubai—known for showcasing cutting-edge approaches—issued a decree, requiring 25 percent of its new buildings to be 3-D-printed by 2030. And ICON is collaborating with NASA for printed dwellings in outer space. But the idea that we can press a button, and a finished house will pop out—we’re not quite there yet.
Supplemental Materials:
“A Systematic Review and Analysis of the Viability of 3D-Printed Construction in Remote Environments”, Steven J. Schuldt, Jeneé A. Jagoda, Andrew J. Hoisington, Justin D. Delorit, Automation in Construction, Volume 125, May 2021
[Section 4. Results: Evaluation of Viability Factors]