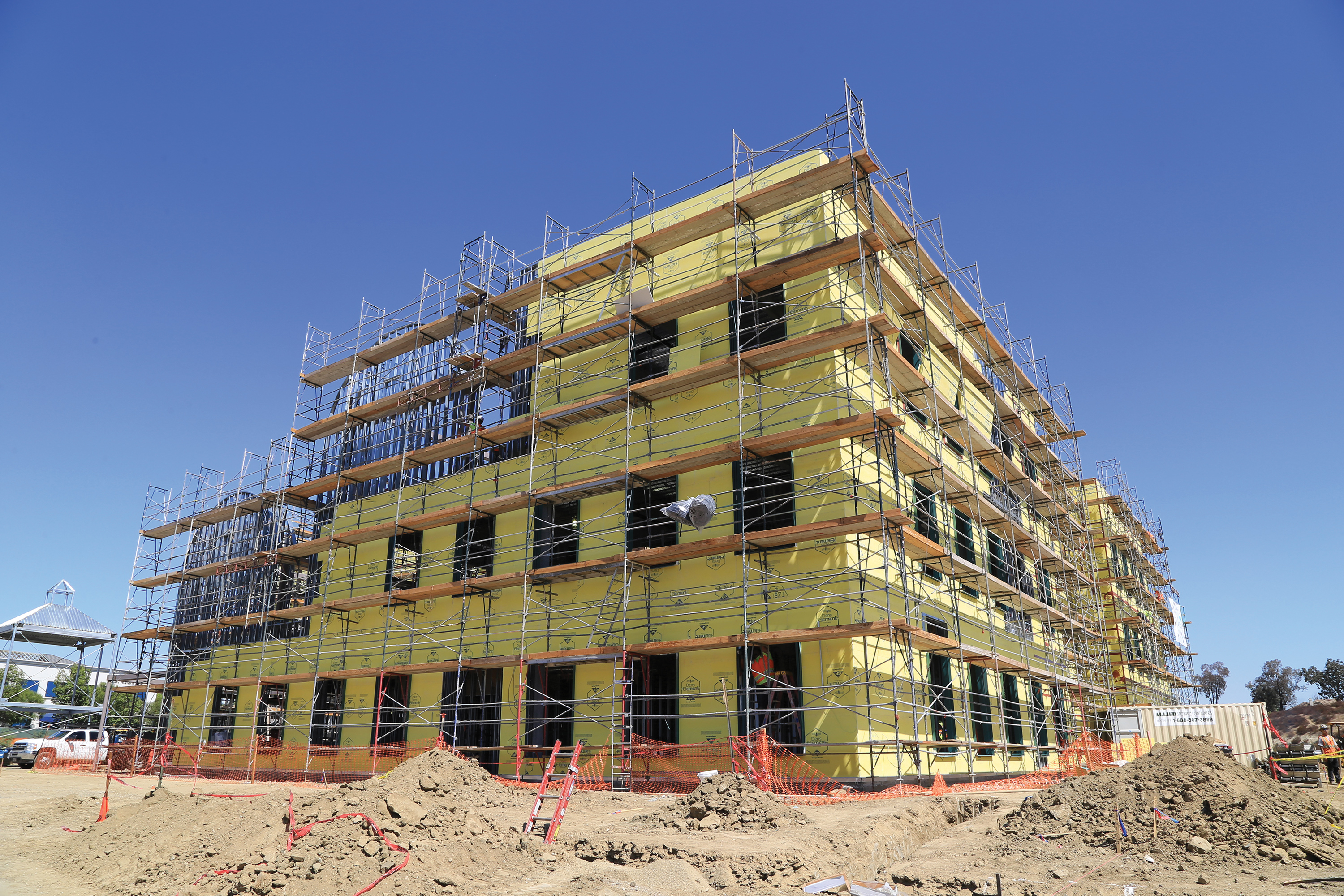
Photo courtesy of Georgia-Pacific Gypsum
Healthcare facilities of all types can be designed to address the needs of people and the long-term performance requirements on the exterior and interior by specifying the most appropriate construction products, such as fiberglass mat-faced gypsum board.
Healthcare buildings of all types are generally considered important and desirable facilities in communities for the health and well-being of the residents. Not only do they need to be centers for providing healthcare, but they also need to be designed and constructed to address the rigors of high use and the health and safety concerns of all the people who use the buildings. That includes attention not only to the design, but also to the materials and assemblies used in the building for durability, cleanliness, and hygiene. In particular, measures to reduce or inhibit the growth of mold and bacteria carry special importance. Similarly, interior spaces need walls and surfaces constructed to be durable and resistant to damage. Beyond routine operations, in-patient facilities in particular—such as hospitals, long-term care facilities, and rehab centers—often become “mission critical” buildings that must remain functioning during severe weather events or other types of natural disasters. While a lot of attention is paid to operations and emergency preparedness in those cases, the reality is that the building construction itself plays a significant role in the resiliency of healthcare facilities. In this course, we look at some of the current issues related to healthcare buildings and examine several methods for safeguarding against risks and damage to the roof, exterior skin, and interior walls in numerous healthcare projects.
RISK MANAGEMENT, DURABILITY, AND RESILIENCE
Healthcare building owners and operators typically have many different concerns about their buildings functioning safely. In addition to being able to perform the basic operations needed for patient care, whether direct services or support services, there is an ongoing need for the facility to be clean and free of any potentially harmful conditions. While the positive motivation here is to focus on providing excellent care, there is always a need to mitigate risk to protect patients and staff from any adverse consequences.
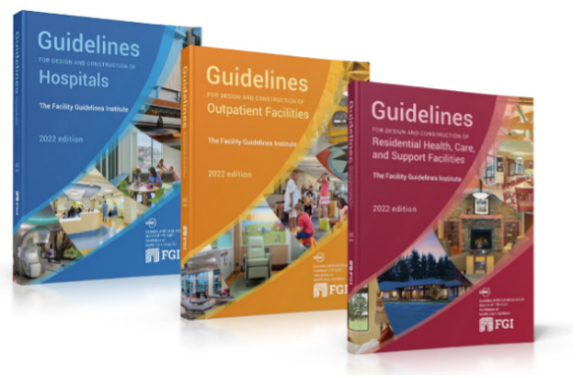
Image courtesy of Facility Guidelines Institute
The Facility Guidelines Institute provides a set of industry standards for the design of Hospitals, Outpatient Facilities, and Residential Health Care and Support Facilities.
The design or renovation of healthcare facilities plays directly into the need for safety, cleanliness, and mitigated risk of these buildings. They need to be designed not only to function well, but also to have materials specified and properly installed that work and look good when first put into use, but also hold up over time. That means they must withstand whatever might get thrown at them. On the exterior, healthcare buildings need weather resistance that holds up in extreme conditions to keep out unwanted water and wind. This resilience could mean the difference between remaining operational or shutting down, all or part of a facility, during an emergency or disaster event—a time when healthcare facilities are needed most. Inside, surfaces need to be durable enough to resist use from multiple people (i.e., patients, staff, cleaning crews, maintenance teams, etc.) and the necessary equipment and cleaning products. In all cases, all healthcare functions must be maintained—including those for rooms with air pressure that is higher or lower than most of the other rooms (i.e. patient rooms, operating rooms, etc.)
In addition to designing for durability and resiliency, the building itself must not create or contribute to any additional risk to patients or staff. For patient care settings, that means that the building construction needs to avoid using any materials known to be harmful to health or safety. Further, materials must not contribute to the creation of harmful conditions, such as the development of mold or mildew. This is a very common and pervasive concern since buildings often provide conditions conducive to mold and mildew growth. Those conditions include a moderate temperature (i.e. room temperature), the presence of water (either as airborne vapor/moisture or bulk water), and organic materials such as wood or paper that act as food stocks for mold growth.
Healthcare Design Standards
Architects, construction professionals, and building owners and operators have some great resources available to help address these concerns, particularly related to moisture, mold, and related health impacts, when designing facilities. Some of these are:
- The Joint Commission: This is perhaps the best-recognized organization for accrediting and certifying healthcare facilities. Their stated focus is on enabling and empowering healthcare organizations around the world to build a foundation for quality care and patient safety. Their website (jointcommission.org) indicates that they have accredited and certified over 22,000 healthcare organizations in over 70 countries around the world. They also offer a wealth of resources with over 2,000 available to support patient safety and care quality.
A significant part of accrediting a facility is based on the building design and construction, including renovations which are omnipresent in healthcare. In that light, the Joint Commission has prioritized infection control and sustainability as significant aspects for architects to address. That includes attention to indoor environmental quality issues that contribute to the safety and health of patients, staff, and visitors, as well as the general well-being of all who are in the facility.
Among other things, the Joint Commission has specific guidelines for facilities to manage their environment during demolition, construction, or renovation to reduce risk to the people in the facilities. Beyond state rules and regulations, they reference the Facilities Guidelines Institute for Design and Construction of Healthcare Facilities, and ANSI/ASHRAE/ASHE Standard 170 – “Ventilation of Healthcare Facilities. These guidelines state that the installation of clean materials (i.e., ductwork, drywall, wood/paper/fabric materials) that have not been damaged by water is paramount to mitigating risk.
- The Facility Guidelines Institute: This organization is referenced by the Joint Commission, specifically for their published guidelines on the design and construction of three different types of healthcare facilities: 1.) Hospitals 2.) Outpatient Facilities and 3.) Residential Health, Care, and Support Facilities (https://shop.fgiguidelines.org/). These publications are the most widely recognized standard for planning, designing, and constructing health and residential care facilities. The Guidelines address programming, space usage, risk assessment, infection prevention, architectural detail, surface, built-in furnishing, and building system requirements all in a singular place. State and federal agencies use these guidelines to regulate new construction and major renovations of health and residential care facilities.
The guidelines have a wide variety of public and private uses, including adoption by states for regulatory purposes and reference in laws, codes, rules, and regulations. They are also used for the promotion of safe practices and methods in the planning, design, and construction of various types of healthcare facilities. As such, they are directly concerned with details of durability, safety, and patient protection in the ways that walls, roofs, and other building assemblies are designed and constructed.
- National Institutes of Health (NIH):At the Federal level, the National Institutes of Health has published a 2023 manual of “Moisture and Mold Remediation Standard Operating Procedures.” This document recognizes that “the presence of excessive moisture in buildings has been linked with occupant illnesses and deterioration of building material.” Specifically, they see the linkage to the creation of mold within healthcare buildings as the primary problem. While they indicate that there are currently no federal regulations for airborne concentrations of mold spores, they do cite two standards that are the basis for the NIH Mold and Water Intrusion Program - ANSI/IICRC S500-2021, Standard and Reference Guide for Professional Water Damage Restoration and ANSI/IICRC S520-2015, “Standard for Professional Mold Remediation.” Regarding acceptable moisture levels for selected building materials, gypsum wallboard is listed at 7-10 percent before it needs to be replaced.
- Green Building Design: The movement is still very strong to continue designing new and renovated healthcare facilities that address not only general environmental concerns but also the health and wellness issues of people related to their time spent inside these facilities. This is true for patients, staff, visitors, and any others who spend time in the buildings. Toward that end, there are several well-known and common strategies.
The LEED Green Building Rating System is still the best-known and most widely used basis for sustainable buildings. There are versions specifically dedicated to hospital design that address the particular needs of these facilities. It also recognizes other related standards as a basis for LEED certification, including the WELL standard which has become a premier methodology for addressing human wellness in buildings. All of these are based on strategies of design and the selection of materials, products, and systems that enhance human health, safety, and well-being.
- Material and Product Standards: When it comes to the specific materials or products used in healthcare facilities, there are several strategies and organizations that are helpful. While LEED and other organizations use Environmental Product Declarations (EPDs) as a basis for assessing the environmental impacts of different materials, there are also Health Product Declarations (HPD) that follow the protocols established by the HPD Collaborative (HPDC). These independently verified analyses of the components of construction materials provide a basis for designers to assess different products for any potential health risks or ability to mitigate concerns. This information can be used to contribute to LEED certification or other certifications required through the Joint Commission or following the FGI standards.
Other programs that also address the make-up of materials and products include the well-known GREENGUARD program, with different levels of certification for different applications, such as for schools (i.e., indoor environments for children) or other settings. The Living Futures Institute has also developed the “Declare” program as part of the Living Building Challenge. This program allows manufacturers to reveal what is in their products and to specifically address whether or not they contain any harmful elements or compounds identified on the Declare “Red List” of things to avoid.
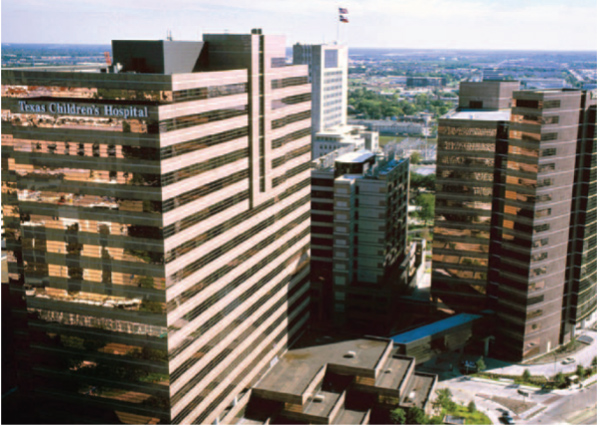
Photo courtesy of Georgia-Pacific Building Products
The Texas Children’s Hospital in Houston, Texas, specified building products resistant to mold and moisture, challenges never welcome in a healthcare environment.
MOISTURE CONTROL
Attention to the choice of materials and the design standards for healthcare facilities is important. But, there is another significant point: ensuring that those materials, systems, and people won’t be adversely impacted by moisture. Water and moisture-related issues in buildings are often among the most cited risks and problems that are encountered during the operation of a facility. For example, the Chubb Insurance Group cites the top five sources of interior water damage loss in buildings as roofs (15%), toilets (15%), sprinklers (14%), water heaters (11%), and HVAC (8%). They also note other sources such as vacancies, boilers/machinery, sewer backups, water storage tanks, and water mains (https://www.chubb.com/us-en/businesses/resources/10-most-common-sources-of-commercial-water-damage.html). The good news is that a lot of those potential problems can be addressed through the proper design, specification, and construction of different parts of the building, such as roofs, walls, and interiors.
One approach to tackle water and moisture issues head-on is to develop a moisture control strategy that incorporates the “four D’s” of design.
Deflect: The first, most fundamental approach, is to deflect water away from sensitive areas in the building construction. This includes rainwater, water from snow melt, water from internal operations, excess water from HVAC systems, or any other source of water. By first deflecting it away, the potential for problems is greatly reduced.
Drain: Water will always follow gravity to flow downhill and drain to a lower point. This is the basis for most building plumbing and roof drainage systems. Areas that are prone to have water present should have adequate drainage properly built in. In addition, exterior wall assemblies need to be designed so that they can drain away any water that penetrates, rather than allowing it to build up and sit inside the assembly. Rainscreen systems are being used to accomplish this purpose.
Dry: It is reasonable to expect that most building construction assemblies will find water or moisture inside of them at some point. The issues often arise only if that water is not able to dry or evaporate so that it no longer poses a threat to the integrity of the assembly or other nearby construction. Therefore, allowing for assemblies to “breathe” to remove any moisture can be very important. Strategies for achieving this will vary depending on the building, type, location, and risk of level.
Durability: A backstop approach to supplement the strategies of deflect, drain, and dry is to use materials and assemblies in construction that are durable enough to withstand the potential effects of water and moisture. This typically means specifying materials that won’t be harmed either on the surface or by the penetration of water. It can also mean adding materials to protect the primary surface material so it can be more durable against weather or heavy usage.
One of the key reasons to focus on a moisture control strategy in a healthcare setting is to prevent harm to the building while also protecting the people. Moisture is a key ingredient needed for the creation of mold and mildew which has been shown on numerous occasions to have negative health impacts. Moist environments can also lead to the growth of bacteria which can be detrimental or even deadly to people whose health is already compromised from other conditions.
A further strategy to help prevent such growth in buildings is to use materials that simply don’t support their growth. That means specifying materials that are non-organic, either on the surface, their interior make-up, or both. In that way, even if water is present and the temperature is favorable, there is nothing to feed the mold spores, so they will either die or simply be dissipated by the drainage or drying aspects of the assembly.
With all of these things in mind, we turn our attention in the following sections to three main areas of consideration for the design and construction of all healthcare facilities, namely, the roof, the exterior walls, and interior walls.
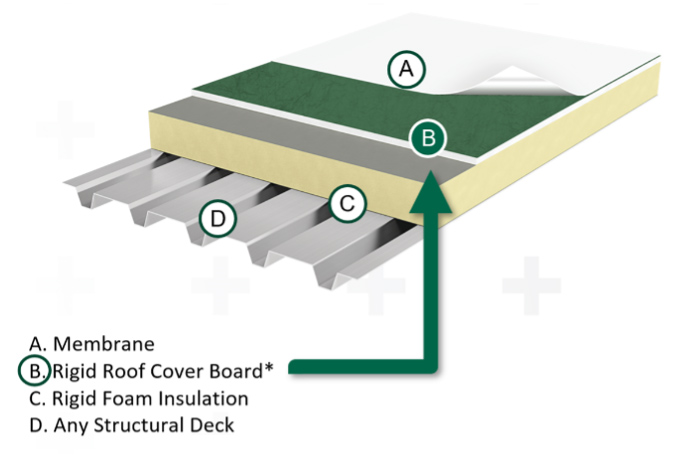
Image courtesy of Georgia-Pacific Building Products
A cover board, also known as a protection board or rigid board, is installed in a roof assembly to enhance the resiliency and durability of the roofing system.
ROOF PROTECTION
On most healthcare buildings, roofing is a big investment whether at the time of first construction or when it is time for it to be replaced. A common benchmark used by roofing consultants is that roofing typically represents five percent of the initial building costs but up to 77 percent of the capital expenditures during building operations—not to mention approximately 50 percent of the construction litigation cases. That’s why the durability of the roof is so important—it contributes to a lower likelihood of problems arising and a longer lifespan for a lower total cost of ownership. For commercial buildings, including most healthcare buildings, the roofing is usually a membrane system (e.g., EPDM, TPO, PVC, Modified Bitumen) installed over rigid foam insulation that is secured or anchored to a roof deck (e.g., steel, concrete, wood). The membrane durability will depend, in large part, on the type and thickness of the roofing membrane selected and attention to what is installed beneath it.
A durable, well-designed roof can also make a difference in terms of how the roof protects the building construction and its occupants under normal and severe weather conditions. Once bulk water or even air-borne moisture penetrates a building’s roof and works its way into the occupied portions, the damage can be both extensive and very noticeable but unfortunately, the damage typically starts long before detection. If moisture accumulates in the roofing system, it can break down water-soluble adhesives, delaminate roofing materials, and corrode metal components, collectively shortening the lifespan of the entire roofing assembly. It can also lead to embedded water in the roof system which may become ideal breeding grounds for mold, mildew, or bacteria.
How best to guard against these roofing issues and risks to the operation of a facility? The answer lies in understanding that there are essentially three potential sources of moisture intrusion in a roofing system.
Construction Activity:First, it can be introduced during construction. Since roof construction is completed outdoors, and the weather conditions can’t be controlled, a contractor may need to work under damp conditions to satisfy construction schedules or to protect the building’s interior. In these instances, rain and dew may become trapped and retained in roofing materials.
Membrane Punctures: The second potential source of water in a roof is from a puncture of the roofing membrane, thus causing a roof leak, whether during construction or after it is complete. Even the smallest penetration in a roof membrane allows water to enter the roof assembly. Punctures can result from both man-made causes and environmental, including foot traffic, and hail or windblown objects that can pierce the roofing membrane. When a puncture exists and a storm hits, gravity or the building’s diaphragm draws the moisture into the roofing assembly. In addition, nearly 70 percent of commercial roofs tend to house HVAC systems and other mechanical equipment that require routine maintenance, which puts stress on the membrane and makes it prone to perforations. The increasing use of roof-mounted solar panels also creates an added concern about maintaining the integrity of the roofing if additional intentional penetrations or maintenance are needed.
Of particular note regarding roof puncture protection is the well-documented rise in the frequency of severe storm disasters between 1980 and 2022. The NOAA National Centers for Environmental Information indicates that the frequency of severe storm disasters is increasing faster than any other disaster type, with 70 percent of their average property losses attributable specifically to hail damage. Property losses are documented by insurance companies who report that in 2022, insured losses related to hailstorms exceeded $10 billion in the U.S. for the 15th consecutive year.
Just as significant, FM Global (formerly known as Factory Mutual), a world-leading property insurance company, has identified hail zones classified by the size of hail commonly reported in an area. Moderate Hail Zones (defined as hail measured up to 1.75 inches in diameter) are common west of the Rocky Mountains, along the East Coast, and around the Great Lakes. Severe Hail Zones (with hail 1.75-2.0 inches in diameter) have grown to reach a large part of the United States, including the South and parts of the Midwest. Very Severe Hail (VSH) Zones (starting at 2 inches but may exceed 4 inches in diameter) carve a path through the center of the country affecting 14 of the 48 contiguous states. As hailstones increase in size, they pick up speed such that hailstones in VSH Zones can fall at over 100 miles per hour. When hundreds or even thousands of large stones fall, it is easy to see how building damage can occur, particularly by puncturing the roofs of healthcare buildings.
Vapor Drive: The third moisture source is vapor drive. Roofing products get wet from the outside (i.e., from rain and leaks in the membrane) and from moisture originating inside the building. When high-humidity indoor air meets the cooler underside of the roof membrane, the water vapor can reach the dew point and condense into liquid water. Hence, vapor drive occurs when there is a significant temperature discrepancy between the inside and outside of a building. The laws of physics dictate that moisture flows in specific ways to find equilibrium. It migrates from warm areas to cooler ones, from areas where it is dense to areas where it is sparse, and from areas of high pressure to low-pressure zones. As a result, frigid temperatures outside buildings located in cold-weather regions will create a vapor drive that causes the accumulated warmth and humidity inside to move up into the roofing assembly where—depending on the amount of insulation included in the assembly—it condenses into liquid water and causes damage. Conversely, if the building is located in a hot, humid climate, the moisture outside the building will attempt to make its way inside, where it will condense on the cold side of the roofing assembly. Rigid insulation is typically installed on roofs in layers with offset seams to reduce the vapor drive that can pass through the assembly.
By addressing all three of these areas with proper roofing design and materials, all following the strategy of the four D’s, the risk of water and moisture entering the roof assembly can be lessened.
Solution Strategy: Rigid Cover Boards
Recognizing the need for durability and protection in roofing, the National Roofing Contractors Association (NRCA) has recommended, for many years, the inclusion of a rigid cover board in all single-ply, commercial roofs. This best practice, which is growing to be more common, involves placing a rigid board between the roofing membrane and the foam insulation. While several different materials have been used in the past, coated fiberglass mat-faced gypsum cover boards are now preferred. This type of product is compatible with all types of roofing membrane installations, is a durable and rigid material, contains no organic materials that could contribute to mold, and has some built-in capacity to resist damage from water. It also has inherent fire resistance, can be cut and installed like other gypsum products, and typically weighs only 2.7 pounds or less per square foot.
Deciding to include a rigid fiberglass mat gypsum cover board into a roof assembly addresses at least the four following things:
Puncture/ Hail Resistance: Rigid gypsum cover boards form a solid substrate for the roofing membrane to help it absorb impact from forces such as hail, foot traffic, and equipment movement, helping to make the membrane less susceptible to punctures.
Insulation Preservation: Cover boards protect insulation from damage due to foot traffic and weather conditions. They also help preserve maximum R-value and energy efficiency by helping to provide an added barrier to water entering the insulation which would otherwise reduce the R-value. Nonetheless, in order to minimize the amount of water absorption in roof boards and contribute to a more resilient roof, it is recommended to specify roof cover boards that have been tested not to exceed five percent maximum total water absorption by weight.
Wind Uplift Protection: A roof assembly with a rigid cover board stands up to high winds that can produce damaging uplift pressure, preserving the integrity of the building and preventing future repairs.
Fire Resistance: Gypsum-based cover boards can also add fire-resistance protection when they are included in fire-rated assemblies, specifically those with a UL or FM fire-resistance rating. Gypsum board has been used for decades as a standard means to add fire resistance since it is inherently a mineral-based product that is non-combustible and has been shown to successfully slow the rate of fire damage. In many cases, a minimum thickness of ¼ gypsum cover board can help achieve a class A fire rating with unlimited slope.
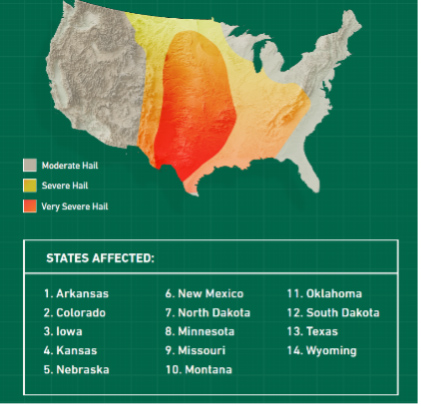
Image: FM Global; courtesy of Georgia-Pacific Building Products
FM Global has identified different hail zones in the United States with the noted growth of Very Severe Hail Zones in recent years.
Rigid cover board products that can hold up to water intrusion, can maintain or regain their original strength, and continue to perform are obviously the most resilient and effective in protecting healthcare buildings.
Cost-Effectiveness
Of late, new technologies, new studies, and experiences both with and without cover boards have pointed to the fact that rigid roof boards are not only a logical choice but also an economical one. It is a common misperception that roofing cover boards are only needed on high-performance roofs or in areas where severe weather is common. As such, they are sometimes “value-engineered” out of a project.
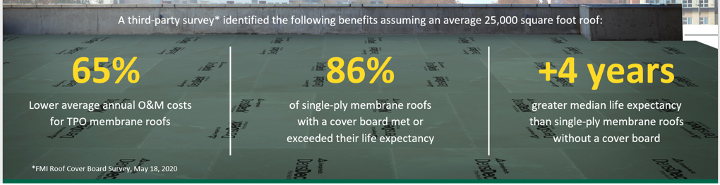
Image courtesy of Georgia-Pacific Building Products
The cost-effectiveness of a roof cover board has been demonstrated by independent studies concluding the findings shown here.
The reality, however, is that they were studied by FMI in May 2020 and found to have a very strong return on investment (ROI). They conducted an independent survey of 74 organizations responsible for 112 single-ply roofs with an average size of 25,000 square feet. In addition to the ability to reduce risk exposure, they found that using a cover board as part of a single-ply membrane roof increased the median life expectancy significantly. The percentage of roofs that met their full 20-year life expectancy increased from 52 percent without a cover board, to 86 percent when a cover board is used—an overall median increase of four years in life expectancy. The study also found that annual operation and maintenance costs were reduced by an average of $1.40 per square foot or up to 65 percent for TPO membrane roofs. These significant savings and increases in life expectancy can only help with the ongoing operation and budgeting of healthcare facilities.
EXTERIOR WALLS RESILIENCE
Vapor drive and water intrusion are significant factors not just in roofing, but also through building walls when designing healthcare facilities. This is particularly important in light of the move toward tighter building envelopes with restricted airflow designed to improve energy efficiency. In theory, the tighter the building envelope, the less impact the vapor drive should have. But without proper airflow control through the walls, warmer air can easily move inside and outside, carrying moisture with it. That air movement can allow more moisture into the building and other assemblies, such as the roof. This can lead to vapor drives through temperature change and diffusion. Tighter building envelopes also make it harder for moisture to escape if it does manage to find its way in, making the ability to dry out quickly after exposure even more important. The key then, is to include effective air, water, and vapor control in exterior walls.
Water-Resistive Barriers (WRBs): This barrier is intended to do exactly what its name implies—resist bulk water from penetrating a wall assembly from the exterior side. WRBs are specifically required by the International Building Code (IBC) to protect the materials and components of a wall assembly from water that may penetrate past the exterior cladding. A properly tested WRB is typically called for behind the exterior cladding of a wall assembly on the face of the sheathing or similar surface. The WRB then needs to function as a water control layer by channeling water down its exterior face to drain harmlessly away from the exterior. In so doing, it reduces or eliminates potential water and moisture problems inside a wall assembly, particularly in cavity wall-framed construction.
Continuous Air Barriers (AB): This barrier has received a lot of attention in recent years since unwanted air infiltration has been seen as both a significant drain on energy performance and a means to transfer unwanted air-borne moisture into buildings. In particular, the International Energy Conservation Code (IECC) now has very specific, mandatory requirements for providing continuous air barriers in building envelopes aimed at restricting or preventing the passage of air to ensure minimum levels of code-required energy performance. Its purpose is to essentially “wrap” the building shell to prevent air from passing from the outside to the inside due to wind, building “stack effects,” or mechanical ventilation pressure differences. To achieve this in exterior walls, the AB is most typically located behind wall cladding on the face of sheathing or a similar surface, just like a WRB.
Vapor Retarders: While WRBs address bulk water and ABs address airborne moisture from one side of an assembly, there is also a concern for vapor penetration from the interior side of the assembly. Therefore, the IBC requires the use of vapor retarders to protect the building. Most commonly, a vapor retarder is required and should be installed on the interior face of an exterior wall, roof, or floor assembly in cold climate zones and the exterior in warm climate zones. The intent is to prevent warm, moist air from penetrating the assembly and condensing to form water that can become trapped and cause damage. The International Building Code indicates what type of vapor retarder is needed in different building and climate situations. A Type I retarder provides virtually no permeability of vapor while a Type II allows some permeability. A Type III vapor retarder slows the passage of vapor, or diffusion, but allows more permeability than either Type I or Type II. In this case, it is presumed that any vapor that enters will also exit.
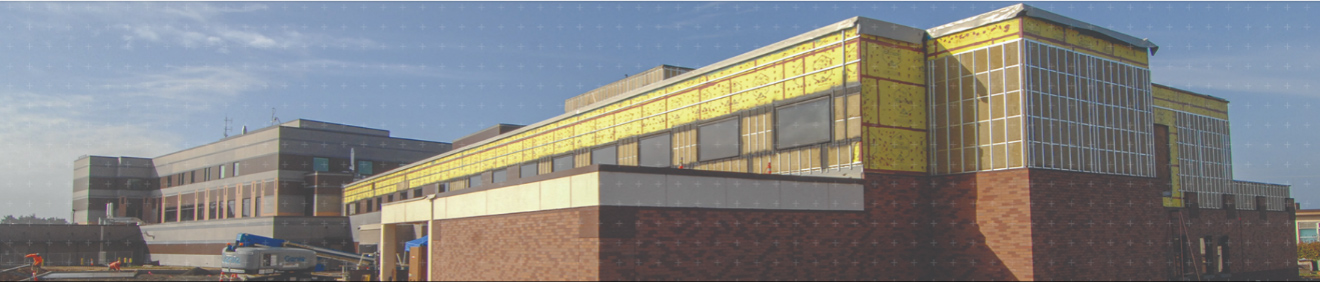
Photo courtesy of Georgia-Pacific Building Products
The Samaritan Pacific Communities Hospital in Newport, Oregon, used an integrated fiberglass mat gypsum sheathing and waterproofing system to overcome construction schedule demands in a wet, coastal environment.
In light of the above, some gypsum manufacturers have developed, and now offer, the latest innovation in exterior wall technology, namely, incorporating both a WRB and AB directly into fiberglass mat gypsum sheathing. To ensure continuity in an assembly, they also offer a complete system of compatible liquid flashing materials to seal joints, seams, openings, penetrations, etc. This reduces the dependence on a field installation for effectiveness while taking advantage of the best properties of all products involved. Fiberglass mat gypsum sheathing with properly treated seams has the potential to dramatically reduce the risk of water and moisture intrusion and mold production.
These products may use different technologies, but they typically meet the code and performance requirements for use as a WB and AB provided the joints, sheathing fasteners, penetrations, openings, and material transitions are sealed per the manufacturer’s instructions. They also serve as a continuous drainage plane behind cladding to drain water away from the wall assembly. Fire resistance ratings can be achieved where needed based on tested assemblies using gypsum-based products. All of these claims are readily backed up by a variety of independent testing.
INTERIOR WALL DURABILITY
Many healthcare facilities are high-use environments with many people, a lot of rolling equipment, and daily deliveries. Therefore, the wall finish material needs to be durable enough to withstand this heavy use, including bumps and bangs from equipment or delivery carts and people rubbing against the walls. There is also the regular and extensive use of cleaners and cleaning equipment for sanitary health reasons that need to be accounted for. Conventional gypsum board is often used for these installations but has limitations for healthcare use meaning it is often covered with a durable covering or not used at all and instead, heavier-duty materials are applied.
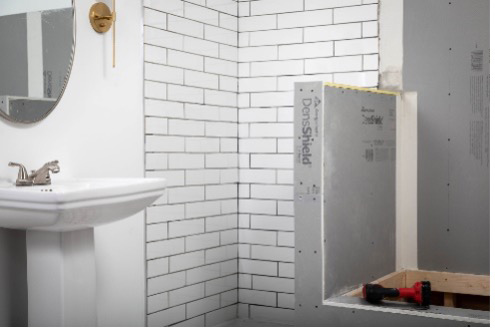
Photo courtesy of Georgia-Pacific Building Products
Interior “wet areas” benefit from fiberglass mat gypsum products that are specifically formulated to resist water and mold growth at the surface.
A superior option is to use fiberglass mat gypsum panels on interior wall surfaces throughout a healthcare facility. The fiberglass mat facing makes it more durable to resist damage and more able to resist heavy cleaning. It also provides a non-penetrating surface to resist moisture intrusion if the surface does get wet or is subject to high moisture content in the air. The non-organic surface is also able to resist mold growth on interior surfaces. The gypsum content helps interior assemblies meet fire-resistance rating requirements. During construction, its use allows for streamlined construction sequencing since it can be installed before the building is completely closed in without impacting its performance. The fiberglass mat gypsum panels stand up to ambient moisture and incidental wetting, both during construction and after the building is in use.
In terms of resilience, an August 2008 FEMA Technical Bulletin (Flood Damage-Resistant Materials Requirements for buildings located in special flood hazard areas in accordance with the National Flood Insurance Program) provides guidance under the National Flood Insurance Program (NFIP) regulation. This guidance indicates that the use of non-paper-faced gypsum board (i.e., fiberglass mat gypsum panels) for walls and ceilings is acceptable for certain special flood hazard areas. The use of paper-faced gypsum board is unacceptable for walls and ceilings in these flood-hazard areas.
Interior Specialty Areas
A few common interior wall types are a bit more specialized in their use and purpose. For example, shaftwalls around stairways and elevators need to achieve code-designated levels of fire resistance but also need to meet the other requirements of interior walls. Fiberglass mat gypsum panels are available in one-inch thickness and are intended to be used in UL fire-rated shaftwalls, stairwells, and area separation wall assemblies in addition to horizontal shaftwalls and duct assemblies. These products are non-combustible, dimensionally stable, and resistant to mold and moisture.
Additionally, walls in “wet areas” in healthcare facilities often need some special attention, particularly if they are covered by ceramic tile or subject to high moisture levels. For these situations, specialty gypsum backer board is available that is engineered with a built-in moisture barrier to prevent damage to the sub-floor or wall cavity. It can be cut and installed like drywall without special tools or fasteners. It can be used for ceramic tile underlayment, including in restroom/bathroom remodeling, therapy pool areas, and other high-humidity areas.
CONCLUSION
Healthcare facilities need to address many different aspects of design, operation, and performance. The design of exterior and interior walls, roof systems, and other parts of the buildings all need to mitigate human risks related to health, durability, and resilience. The use of fiberglass mat gypsum panel products is one effective strategy to achieve these stated goals.
Peter J. Arsenault, FAIA, NCARB, LEED AP is a nationally known architect and a prolific author advancing positive acoustical experiences through better building design. www.pjaarch.com, www.linkedin.com/in/pjaarch