This CE Center article is no longer eligible for receiving credits.
All multifamily buildings must meet code requirements for fire resistance between dwelling units, both horizontally (i.e., side by side) and vertically (i.e., above and below). They also need to meet requirements for acoustical performance such that sound transmission between dwelling units is controlled or minimized. The means for constructing these outcomes can vary depending on the types of materials and products used in floor and demising wall assemblies. One product that has been used extensively overseas is now becoming very popular in the United States as well. Boards or panels made from magnesium oxide (MgO) are showing up on projects across the country to act as a subfloor, sheathing, wall board, or underlayment material. In the process, they are bringing enhanced fire resistance and acoustical performance to many building types, most notably multifamily projects. Based on this emerging popularity, this course looks more closely at designing and constructing with MgO panels. Beginning with a description of the material and its properties, its code compliance characteristics related to fire resistance are discussed. Recognizing the latest code requirements for acoustic control in multifamily buildings, the sound attenuation capabilities are also reviewed. Finally, a discussion of its installation, particularly compared to other alternatives such as a wet-laid gypsum underlayment, is presented. Overall, the suitability and advantages of using MgO panels is provided for consideration in the specifications and design of multifamily projects all around the country.
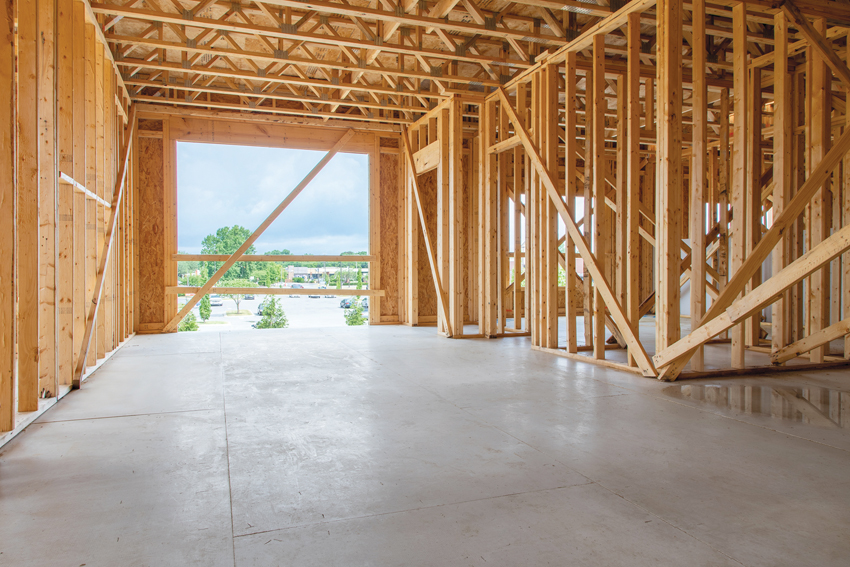
All images courtesy of Huber Engineered Woods, LLC
Multifamily buildings commonly use wood framing as the basis for their construction. Subfloor panels made from magnesium oxide (MgO) are installed on this project, providing characteristics related to fire resistance and acoustical performance.
Magnesium Oxide (MgO) Panels Overview
What makes for a good building product for subflooring and wall sheathing? Most professionals would include traits such as predictable performance, consistent quality, ease of installation using common tools, compatibility with other materials, sustainability, and affordability all as important. Criteria such as these have typically driven the creation and proliferation of many board products such as plywood, engineered wood, cement board, and gypsum boards, all of which are commonly used for subflooring, wall sheathing, and other applications. Nonetheless, there is always room for improvement and creative product development to better meet the needed criteria.
Beginning around the year 2010, a new board product emerged as a popular choice. Made primarily from magnesium oxide (MgO) with some other added compounds, it is similar to a cement panel product. When the MgO products are formed, it is actually a controlled chemical reaction that allows the boards to become solid, much the same way that concrete is a controlled chemical process that creates a hardened material. Note that the primary ingredient is oxidized magnesium, which is a very stable and inert mineral, not the raw metal magnesium (Mg) itself, which can react dramatically with other chemicals. This is a significant difference since it makes MgO very suitable for a building product while Mg by itself is not.
Manufactured MgO board products have also been available in the United States and other countries for a number of years. The formulation of compounds or materials added to the MgO will vary by manufacturer but can include magnesium chloride (a type of salt), perlite, or wood fiber. These added ingredients help define the overall performance characteristics of the finished products or help to benefit the manufacturing process. High-quality panels incorporate an integrated mesh core as a means to increase some preferred characteristics such as dimensional stability and strength. In any of these cases, the general process of creating MgO boards is similar to creating gypsum board or cement board products. Carefully selected ingredients are assembled and run through a quality-controlled process in a factory that results in uniformly produced end products.
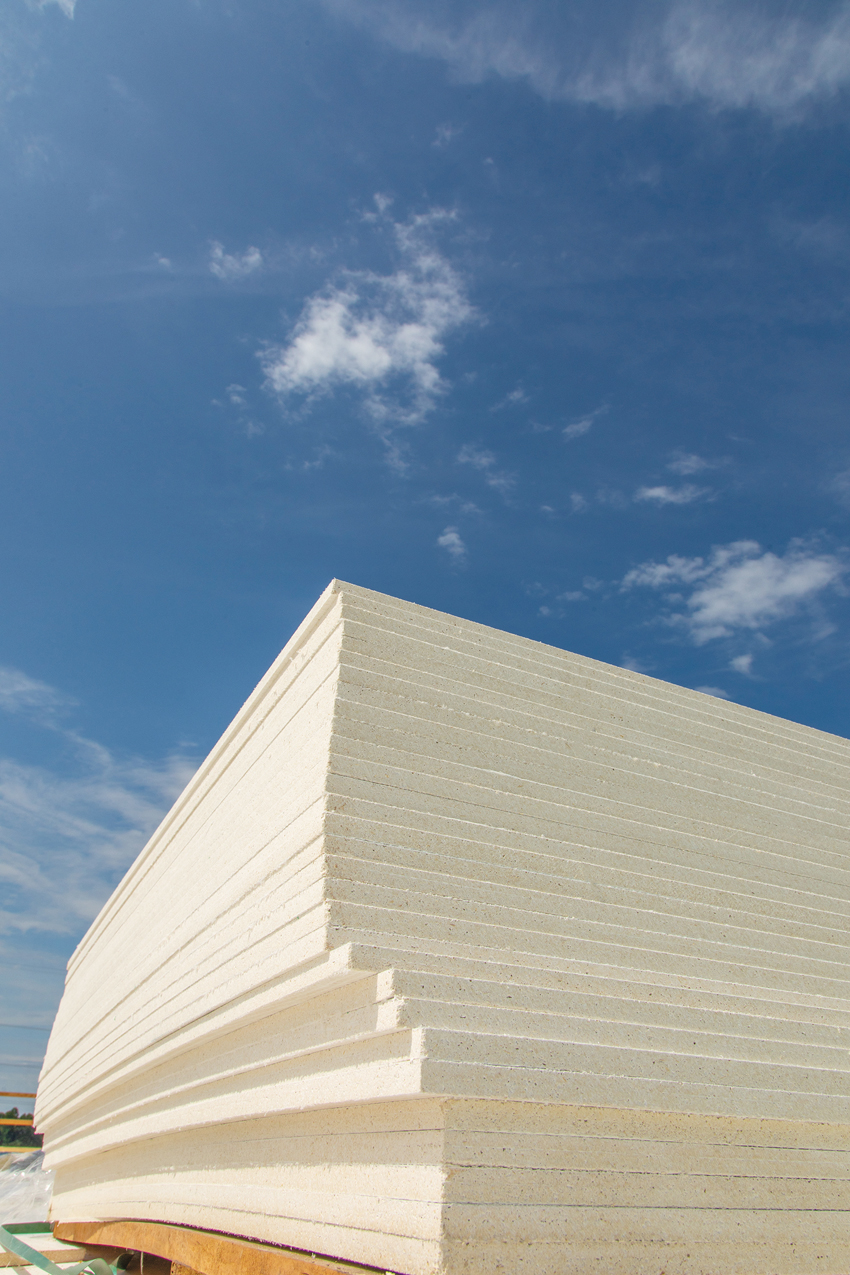
MgO panels are stacked and installed similarly to wood panels.
Characteristics
What has led to the development and use of MgO board in buildings? Primarily the fact that it is a demonstrated alternative to some other traditional products and offers some compelling characteristics.
Two traits in particular are especially relevant to using MgO boards in multifamily buildings, and they are discussed in more detail later in this course. These traits are:
- Fire resistance: Inorganic materials typically do well with providing fire resistance, and that is the case with MgO boards too. With a melting point over 5,000 degrees Fahrenheit, it is able to provide considerable levels of fire resistance in buildings as part of a floor or wall assembly.
- Sound absorption: The ability of materials to transmit, absorb, or reflect sound waves is directly related to their makeup. MgO boards have been tested and shown to provide very favorable performance.
Additional characteristics of MgO board include the following:
- Environmentally friendly: Made primarily from inorganic materials, MgO boards rely on natural ingredients that can be responsibly obtained and processed.
- Inherent strength: The combination with other materials and compounds, including mesh cores, helps assure that the strength and rigidity of the boards is achieved and maintained over time. As a hardened board product, it handles compression loads readily.
With the appropriate added materials, tension forces are absorbed and dissipated. It is reported that some people have a misperception about the strength of MgO boards since they assume that the product is brittle or non-structural like fiber cement. In fact, that is not the case for many products which are able to carry and withstand some notable loading. This can vary by product of course, so the exact structural capabilities of any product should be verified or confirmed with the manufacturer.
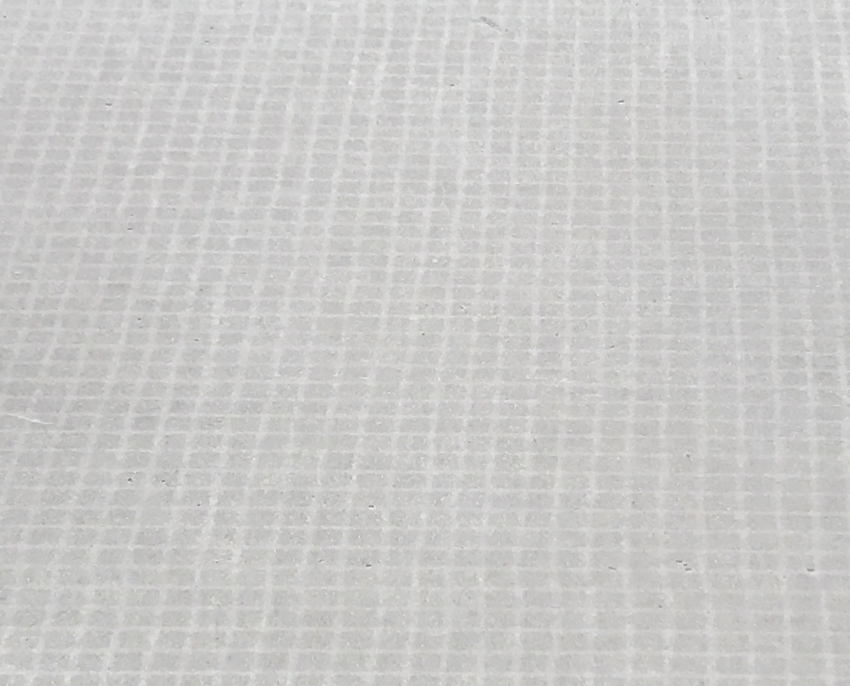
High-quality MgO panels have an integrated mesh core that enhances strength and dimensional stability.
- Dimensionally stable: The inorganic nature of the product means that it is very dimensionally stable. It is not prone to swell or expand and contract due to moisture and temperature changes.
- Resistance to mold and mildew: The inorganic makeup helps in this regard too. Products have been tested in accordance with ASTM G21 "Standard Practice for Determining Resistance of Synthetic Polymeric Materials to Fungi." This standard is designed to test the resistance of synthetic polymeric materials (molded materials, surface treated articles or similar objects) to fungal attack. While MgO board is not a synthetic polymer, this has become the accepted standard to test manufactured building products of this type, particularly those that may be exposed to moisture. The test itself is based on a 28-day period where the product is exposed to specific fungi (molds, etc.) in conditions of temperature and humidity conducive to their growth. The results of this test on MgO boards produced multiple scores of zero, meaning the tested specimens remained free of any fungal growth.
- Water vapor permeability: Manufacturers of MgO board generally do not recommend lifelong outdoor exposure, but the products have been tested for water vapor permeability. The standard test for this situation is ASTM E96: Standard Test Methods for Water Vapor Transmission of Materials. There are two basic methods provided: 1) the Desiccant Method and 2) the Water Method. While either is valid, the one that most closely matches the installed conditions is preferred with the understanding that different test methods may produce somewhat different results. MgO has been tested under both options, with the results of Method A indicating a rating 5–10 perms and Method B on the order of 15–20 perms.
- Insect damage resistance: With the absence or extremely limited presence of any wood or other organic materials in the board, insects and vermin are not typically attracted to it. Therefore, the damage from such infestations can be avoided, differentiating MgO board from common all-wood based products.
Physical Properties
To be appropriate for use in construction, boards for subflooring and wall sheathing need to be manufactured with some familiar physical properties allowing them to be integrated into the rest of the building assemblies. Along those lines, manufacturers of MgO boards commonly provide products within the following physical parameters:
- Panel size: The most typical size for any construction board product is a nominal 4 feet by 8 feet, and MgO boards are readily available in that size. Some high-quality manufacturers also offer longer length panels in nominal 4-feet by 9-feet and 4-feet by 10-feet sheets.
- Thickness: The thickness of a panel is usually a direct determinant of both the strength and weight of the product. Recognizing that there may be times when MgO is used alone or in combination with other materials, it is offered in different nominal thicknesses of 3⁄4 inch, 5⁄8 inch, or 1⁄2 inch.
- Weight: As noted, this can vary; but for a nominal 3⁄4-inch-thick sheet, the weight of MgO panels are approximately 4.5 pounds per square foot.
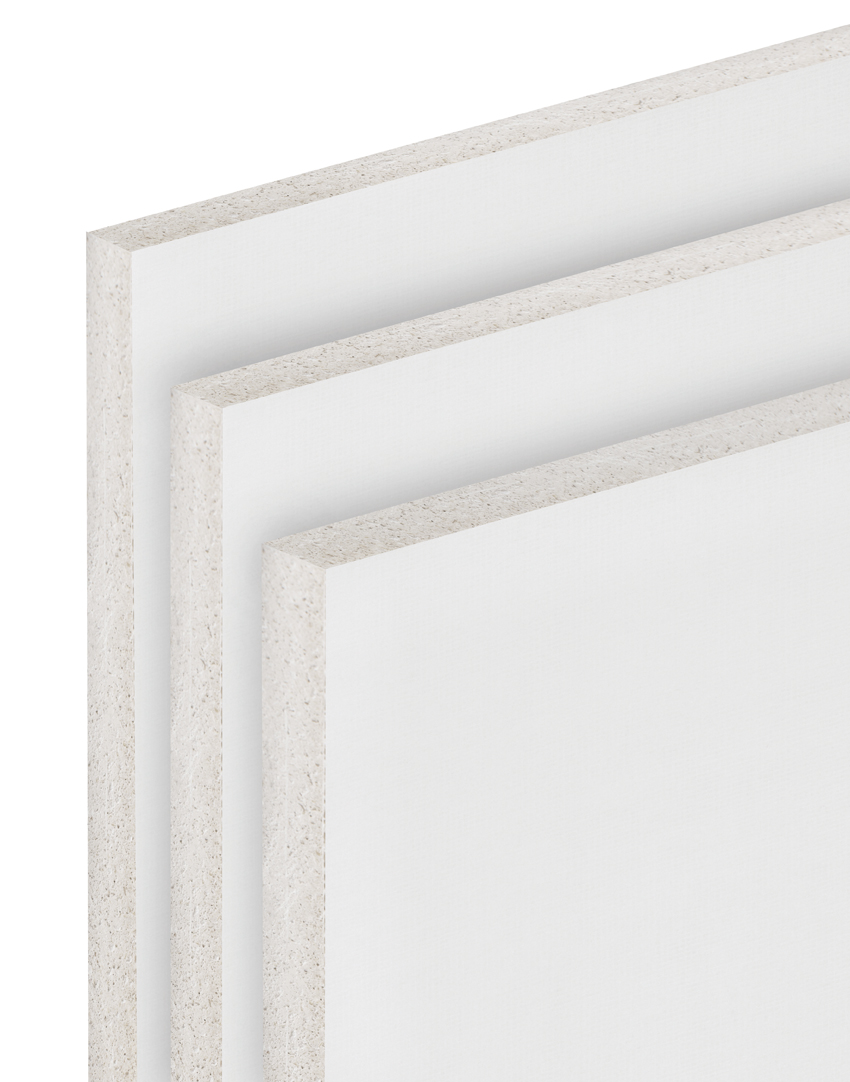
MgO sheathing panels are typically available in nominal 4 feet b by 8 feet, 4 feet by 9 feet, and 4 feet by 10 feet sizes. Though thickness may vary between brand, it is typical to see nominal 3⁄4-inch, 5⁄8-inch, and 1⁄2-inch product.
- Edge profile: There is no need for a gap between MgO boards as there is for other panel products. Therefore, the edges can be butted directly up against one another using a straight edge profile. Single-layer subfloor applications require edge support per IBC/IRC, so a tongue-and-groove option may also be available.
Allowable Uniform Floor Loading
MgO panels used for subflooring are intended to be used in one of two ways.
- MgO underlayment: One application of MgO in a floor assembly is to use it on top of a structural OSB subfloor panel. The MgO in this case would be a non-structural application as the OSB layer is acting as the structural element. The MgO underlayment is essentially acting as a replacement for poured gypsum underlayment to add better sound performance and assist in fire resistance.
- Single layer: At least one manufacturer is pursuing a product that will allow for MgO to be used as a standalone subfloor material ready to receive finish flooring. Not all MgO products are capable of this, however, so it is very important to verify any structural information with specific manufacturers. Standard structural analyses for subflooring is based on deflection value limits of L/360 for live loads or L/240 total load. The assumption is made that standard common practice is followed whereby the long end of the panels are installed perpendicularly across at least three floor supports (joists, trusses, etc.) In these circumstances, the typical residential structural floor code requirement of 40 psf live load (60 psf total load) needs to be met. At least one ¾-inch-thick product has been tested to achieve that level of uniform loading when the floor supports are spaced at 24 inches on center. For conditions where the loading requirements are higher, a version of the same product has been shown to support up to 100 psf live load (120 psf total load) with floor supports spaced at 16 inches on center.
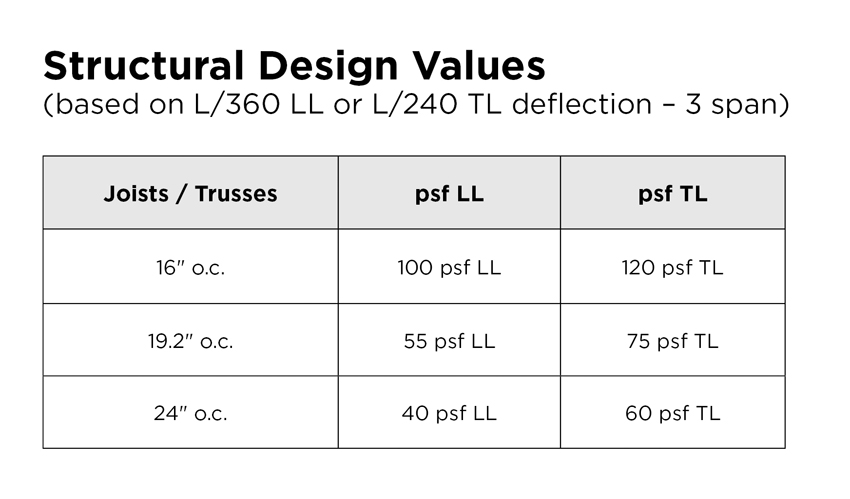
Structural design values shown are based on one selected MgO panel. Structural design values will vary between different products. Always consult the manufacturer for product-specific information.
Suitability for Construction Types
Multifamily buildings are commonly constructed based on different categorized construction types defined in the International Building Code (IBC). Types I and II construction are commonly required for high-rise and mixed-use buildings and typically do not allow wood members. Instead they require fire-resistive or noncombustible materials. While MgO boards may be appropriate for use in these situations, thus far their use has not been common here since other materials such as fire-protected steel, concrete, and gypsum board tend to dominate these construction types. The fire resistance and other characteristics of MgO boards are such that they may be well suited for certain installations in Types I and II buildings and architects are certainly encouraged to consider their use where appropriate.
In cases where wood is allowed, however, MgO boards, particularly when used in conjunction with OSB subflooring, are seen as a very appropriate material choice. In that regard they are very appropriate for use in Types III, IV, and V construction which are described more fully as follows:
- Type III: The code refers to this as “ordinary” construction since it was historically a very common way to build using brick or CMU exterior walls and wooden interior framing. Buildings of this type are still built as new construction, but many older existing buildings of this type are commonly being renovated into loft style apartments or other multifamily housing. This is particularly true in older urban areas where warehouse and industrial buildings were commonly constructed this way. When seeking the appropriate fire-resistance ratings for this type of construction, there are one of two conditions that may apply based on other code compliance factors related to building use, size, fire areas, etc.:
- Type III-A: Protected Combustible requiring 2-hour rated exterior walls (with some specific exceptions), 1-hour rated structural frame and 1-hour floor/ceiling/roof protection
- Type III-B: Unprotected Combustible requiring 2-hour exterior walls (also with some specific exceptions) and no fire resistance for the structural frame, floors, ceilings, or roofs.
- Type IV: This is referred to as heavy timber construction and, while historically has been thought of as “post and beam” solid wood framing, there is a current resurgence in this construction type using engineered and laminated heavy wood products. This approach is seen as more sustainable and with less embodied energy than steel and concrete and has become popular for new low to mid-rise construction of multifamily and mixed-use buildings.
In this construction type, 2-hour rated exterior walls (with some specific exceptions) and a 1-hour rated structural frame or heavy timber frame are required. It also includes heavy timber floor/ceiling/roof assemblies. In these cases, the heavy or laminated timbers are shown to achieve fire resistance by maintaining the minimum required structural strength after being exposed to fire for the determined time and, while exhibiting signs of charring, remains structurally intact due to its total mass.
- Type V: This is common wood stud frame construction used in many different types of low-rise residential construction. There are two subcategories here:
- Type V-A: Protected Wood Frame is what is commonly used in the construction of newer apartment buildings with no exposed wood visible. It requires 1-hour fire-rated exterior walls, 1-hour fire-rated structural frame and 1-hour fire-rated floor/ceiling/roof.
- Type V-B: Unprotected Wood Frame is commonly used in single-family/two-family homes and garages but is not typically allowed in multifamily (three or more dwelling units in a building). Often, exposed or unprotected wood is involved so there is no fire-resistance requirement.
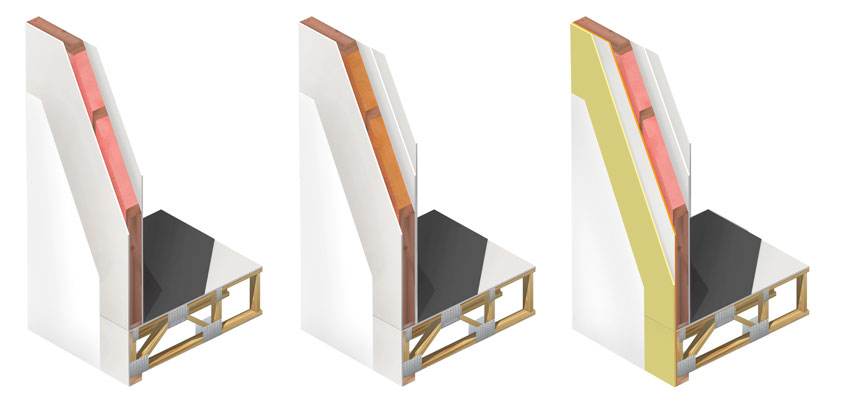
Categorized construction types as defined in the International Building Code (IBC) with associated fire ratings.
MgO board products are suitable for any of these construction types and can add to the fire resistance of the assemblies in which they are used. They are appealing to construction contractors since they can be cut and installed using common carpentry tools making it very similar to working with other wood products on the project.
Fire-Resistance Performance
The excellent fire resistance of high-quality MgO panels deserves some detailed attention, particularly as it relates to their use in multifamily buildings. (Always check to ensure that the manufacturer has completed the required testing.)
The proof of fire resistance for any building product is based on independent testing and verification of results. Some of the most relevant tests and their results for MgO boards are summarized as follows:
- ASTM E136: Standard Test Method for Assessing Combustibility of Materials Using a Vertical Tube Furnace at 750°C is a very focused evaluation of the specimen (piece) material that is carried out under specified laboratory conditions. The test method includes two options, both of which use a furnace to expose test specimens to a temperature of 750 degrees Celsius (1,382 degrees Fahrenheit) for a specified amount of time. The intent behind the test is to determine the combustibility of building materials, not to replicate the conditions of a building that is on fire. As such, at the end of the test, the results are either the material being tested did not combust/catch fire (pass) or it did combust/catch fire (fail) based on one of two possible conditions:
- Condition 1: If weight loss of the test specimen is 50 percent or less: No flaming combustion of the specimen after the first 30 seconds; the recorded temperatures do not at any time rise more than 30°C above the stabilized furnace temperature prior to test commencement.
- Condition 2: If weight loss of the test specimen exceeds 50 percent: No flaming combustion observed throughout the entirety of the test; the recorded temperatures do not at any time rise above the stabilized furnace temperature prior to test commencement.
The building codes rely on the result of this test and will typically classify those materials that pass as “noncombustible” and those that fail as “combustible” (those terms are not used in ASTM E136, only in the codes). Be aware that while MgO itself can meet the noncombustible standard, different manufactured MgO products use a variety of other ingredients that may be combustible. Therefore, if a noncombustible rating is needed in a project (e.g., exterior walls of Type III Construction) then verification will be required from the manufacturer showing that it passed ASTM E136.
- ASTM E84/UL 723: Standard Test Method for Surface Burning Characteristics of Building Materials. Both ASTM and UL use essentially the same test, it is just that UL refers to it by their own number when they are the independent testing laboratory. This is a very common and widely specified test since it is a reliable way to determine building safety in a fire. Specifically, it looks at the way the surface of a material reacts in fire conditions. The concerns are flame spread and the amount of smoke that develops when exposed to a flame. In this laboratory test, a 24-inch by 24-foot sample is placed in a horizontal position with the surface to be evaluated facing downwards. The sample is then exposed to a standard controlled fire, under draft, for 10 minutes.
There are two output measurements that come from this test. The first is the Flame Spread Index which is obtained by measuring the distance that a flame travels along the sample surface and the amount of time that it takes for it to travel. The second is the Smoke Developed Index which is measured by a photo cell that looks at the total smoke developed throughout the test. The data related to both of these are then used to calculate the final test results.
The building codes use the results from the test to then classify materials, such as Class A or Class I ratings, which indicate a maximum flame spread rating of 25, for example. The maximums for smoke developed are based on ratings of 50 Index or 450 Index as determined by the test. If a manufacturer wants to improve its ratings, then it needs to reformulate or otherwise modify the product and have it tested again to show compliance with the desired performance level.
These tests have been applied to MgO boards and the results are, again, impressively positive. Products demonstrated zero flame spread and zero smoke developed putting them at the top of these ratings and classifications for fire safety under the code.
- ASTM E119: Standard Test Methods for Fire Tests of Building Construction and Materials and UL 263: Fire Tests of Building Construction and Materials are two different names for essentially the same test and have been recognized as equal in terms of testing results. They are used to determine fire-resistance ratings expressed in hourly ratings such as 1-hour rated, 2-hour rated, etc. The tests are done on specific assemblies of materials such as wall assemblies, floor/ceiling assemblies, etc. The intent is that the tested assembly contains all of the specific construction components that will be used in the construction of a particular wall or floor/ceiling including framing, (wood or metal), insulation (if any), gypsum board, (for walls or ceilings) underlayment or subfloor (for floors), nails, screws, etc. Since it is easy to imagine many different variations and permutations of these assemblies, it should not be surprising to learn that there are many results from this test. They are also categorized according to ratings for either “load-bearing” or “non-load-bearing” assemblies. Gypsum board companies, for example, are well known for publishing pages of different assemblies and showing the resulting hour rating of those assemblies tested according to ASTM E119/UL 263 and then bearing a specific fire-rated assembly design number and rating. To show code compliance, the actual construction must match exactly the tested assembly without any substitutions or changes.
The test itself is based on an actual full-size specimen of the assembly submitted by manufacturers or others. For wall assemblies, the typical sample size is 10 feet by 10 feet. For floor/ceiling assemblies the typical sample size is 14 feet by 14 feet. The specimen is then exposed to a standard controlled fire (from a furnace) for a specified time period following a time-temperature curve. That means that at different set times during the test, the furnace shall be at different designated temperatures. So, for example, at 5 minutes into the test, the temperature may be specified at 1,000 degrees Fahrenheit; at 10 minutes, 1,300 degrees Fahrenheit; and at 1 hour, 1,700 degrees Fahrenheit; and so forth. If the assembly remains intact as described in the test method at the end of the designated test period, it is rated accordingly (i.e., 1-hour assembly, 11⁄2-hour assembly, 2-hour assembly, etc.).
Following this rigorous testing protocol, MgO board has been found to be very suitable for wall and floor construction when installed in accordance with UL tested and rated assemblies. It has successfully been used to help achieve 1-, 2-, and 3-hour ratings depending on the overall assembly.
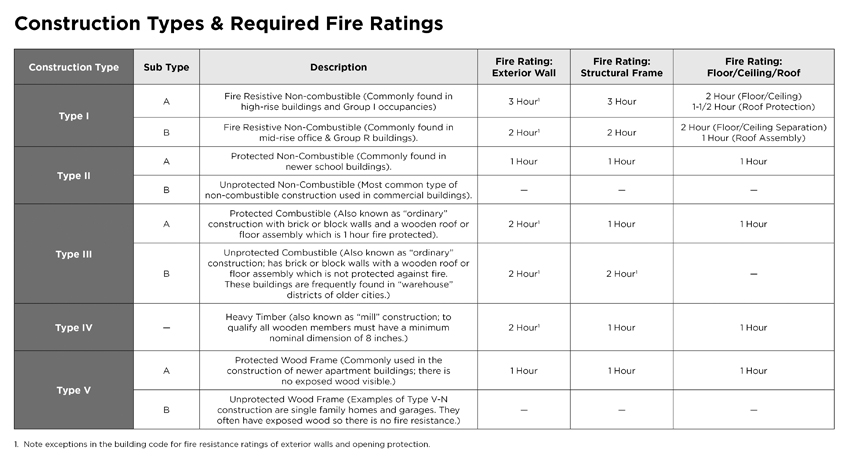
MgO can be used to achieve 1-hour and 2-hour fire-rated wall assemblies and has the potential to eliminate additional layers in 2-hour rated wall assemblies. (*Not all MgO panels are manufactured to the same standard. Always consult the manufacturer for product-specific information.)
All of this fire-resistance performance is critical for the safety and welfare not only of multifamily residents and visitors, but also for firefighters and other first responders. Having the ability to incorporate the inate noncombustibility of MgO products that are easy to install helps make the process of building fire-rated assemblies easier and more reliable.
Acoustical Design Performance
In multifamily buildings, sound transmission between dwelling units is understandably a significant design issue. In an ideal setting, the only sound that we would hear inside buildings and spaces would be the intentional, desirable ones. But, we all know that is not automatically true since unwanted sound or background noise can readily penetrate between walls or floor/ceiling assemblies. Such sound intrusion can create a lack of privacy or disrupt the normal activities of the people inhabiting the dwelling units. A certain amount of background noise is certainly commonplace and sometimes preferable depending on the setting. However, excessive background noise can seriously degrade the ability to understand speech, listen to music, or most notably, to sleep. Based on all of this, architects and others have routinely sought out effective methods, materials, and assemblies that can reduce or control noise intrusions into dwelling units. As already noted, MgO panels offer a means to provide enhanced acoustical performance and improved living conditions.
Acoustics Principles
Sound is typically characterized both by loudness and frequency. Loudness is measured in decibels (dB) such that the higher the dB rating, the louder the sound. The commonly referenced range is 0 dB (threshold of hearing) to around 130 dB (threshold of pain) with human speech being in the middle around 50 to 65 dB. Sound frequency, meaning the time frequency of radiating waves of sound, is measured in Hertz (Hz). One Hz is equal to a frequency of one cycle per second. The human ear can typically hear frequencies or sound “pitch” between about 20 Hz (very low pitched, bass sounds) up to around 20,000 Hz (very high-pitched, piercing sounds). Sound exists above and below this range, but our ears do not hear it, unlike some animals such as dogs or bats that do indeed hear very high-pitched sounds (over 20,000 Hz) or elephants that can hear lower sounds (below 20 Hz).
To limit or reduce the amount of sound entering or leaving a space, the different materials and assemblies that enclose that space must be addressed. The goal is to control or attenuate the amount of sound passing through walls, ceilings, floors, etc. such that an acceptable level of background noise is achieved. Conversely, it may be equally important to contain the sound in a given space so it does not spill out to other areas. Either way, there are some common and useful means to measure sound transfer and attenuation.
- Transmission loss (TL) is a fundamental measurement of the ability of a material or building assembly to block or reduce sound. It is measured in decibels at different frequencies to determine how much sound transmission is lost at each measured frequency. Generally speaking, a TL of 10 means that the sound is 10 dB quieter on the listening side compared to the sound originating side.
- Sound transmission class (STC) is determined by ASTM E90: Standard Test Method for Laboratory Measurement of Airborne Sound Transmission Loss of Building Partitions and Elements. The results of this test determine the STC rating of the tested materials or assemblies. A higher STC rating (50–60 or above) means that more sound is abated while a lower STC rating (35 or less) means that more sound is transmitted through. The STC number is derived from values tested at sixteen different standard frequencies ranging from 125 Hz to 4000 Hz. Acoustical engineers fit these values to the appropriate Transmission Loss curve to determine a final STC rating. There is also an option to determine STC levels based on field measurements of a space, which may be appropriate for testing existing buildings. Note that the STC measurement is accurate for speech sounds but less so for amplified music, mechanical equipment noise, transportation noise or any sound with substantial low-frequency energy below 125 Hz.
- Impact insulation class (IIC) is a measure of the ability of a floor-ceiling assembly to absorb or deflect sound from impacts (such as people walking or objects dropping) and keep it from being transmitted to the space below. As such, IIC is a measure of structure borne sound, not a measure of airborne sound. It is determined by ASTM E492: Standard Test Method for Laboratory Measurement of Impact Sound Transmission Through Floor-Ceiling Assemblies Using the Tapping Machine. This test method prescribes a uniform procedure for reporting laboratory test data, that is, the normalized one-third octave band sound pressure levels transmitted by the floor-ceiling assembly created by a standard tapping machine. The results are based on the measured impact sounds in the space below and result in a numeric rating. A higher IIC rating means that more sound that is absorbed while a lower number means more structure borne sound is transmitted through.
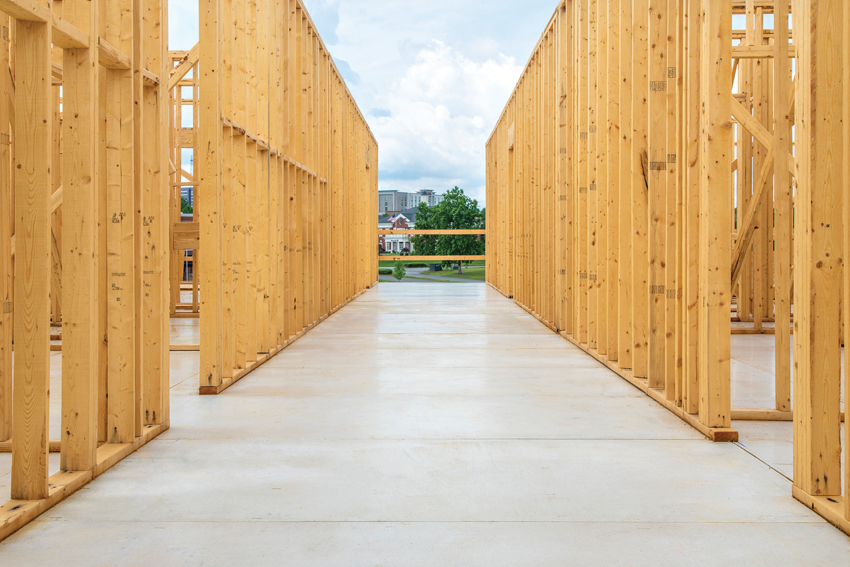
Shown are magnesium oxide (MgO) subfloor panels being used on a multifamily construction project.
Building Codes and Sound
Building codes and other standards have long recognized the significance of acoustical control, particularly in dwelling units. Historically, Chapter 12 of the IBC dealing with interior environments has included a section on sound transmission. In the 2015 version of the code, these requirements were expanded to apply not only to dwelling units but to any sleeping rooms as well. That means that not only multifamily buildings, but other residential occupancies such as hotels, motels, dormitories, boarding houses, etc., all need to address the requirements of Section 1207 on sound transmission (changed to Section 1206 in the 2018 IBC).
The background for the development and updates to the code language can be found in a publication by the International Code Council (ICC) titled ICC G2 2010 – Guideline for Acoustics. Cited there is a 1995 British report titled “Building Regulation and Health” that, among other things, looked at the number of extremely severe health risks that are due to noise. Also cited is a Canadian study of over 600 families living in multifamily housing that concluded “Noise from neighbors in multi-unit buildings is a serious problem that degrades the quality of life of the residents.”
Based in part on this research, the IBC has consistently set the minimum threshold for airborne sound transfer in common interior walls, partitions, and floor/ceiling assemblies as no less than an STC rating of 50 for laboratory determined levels and 45 if field tested. Similarly, the IBC calls for a minimum structure borne sound transfer in floor/ceiling assemblies as no less than an IIC of 50 for laboratory-determined levels, 45 if field tested. The research cited above, however, suggests that these code minimums might fall short of satisfying many people when it comes to acoustical control in their spaces.
Based on all of the above, the ICC Guideline for Acoustics actually recommends acoustical performance beyond the current code minimum. While this higher performance is not mandated by the IBC, it does point to the common evidence-based need to exceed the code minimums to satisfy the greatest number of people and protect their health and welfare.
Achieving Acoustical Performance
To reach the STC and IIC levels that are either minimally required, acceptable, or preferred, especially in wood framed construction, attention to detail and material choices is required. In conventional terms, that can mean adding sound-deadening material, adding more sound reflective material, offsetting components, or using other extraordinary means to achieve the intended results.
One alternative to some of these conventional approaches is to consider the use of MgO panels in the floor/ceiling assembly as a primary or secondary subflooring material. There may be a misperception by some designers that adding a material such as MgO to a floor assembly will add mass and some sound deflection but not really increase STC or IIC values. In fact, MgO has been used as a subfloor material in a variety of different assembly types and has been tested according to the code requirements and guidelines. The results show that ratings of STC-60 are indeed readily achievable using MgO underlayment along with rather conventional methods and materials in the floor/ceiling assembly. Similarly, ratings of IIC 53–58 have been demonstrated in the same manner, thus exceeding code minimums in these cases.
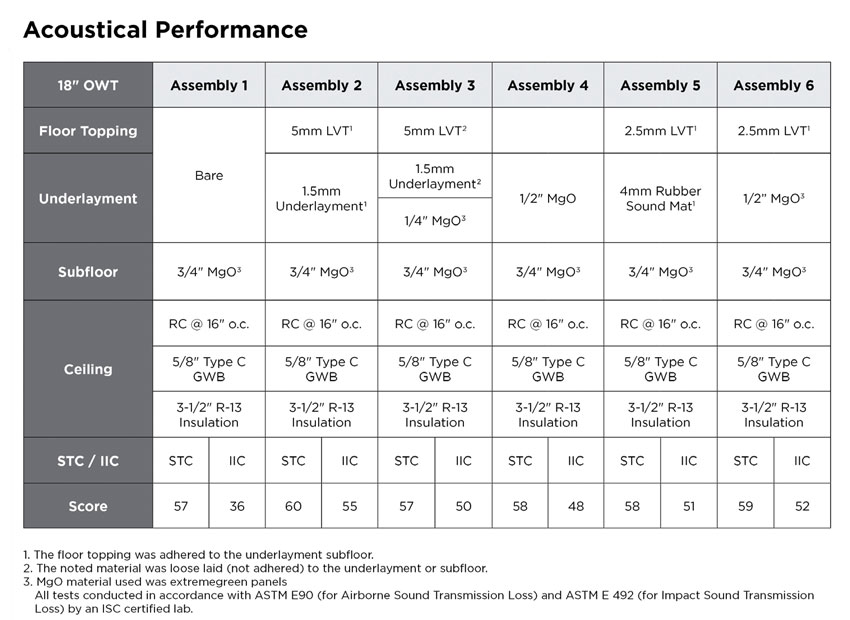
MgO can be used in different flooring assemblies to help improve the acoustical performance of those assemblies.
Overall, MgO can be a significant acoustical contributor to floor/ceiling assemblies in multifamily buildings or other building types that contain sleeping rooms. It can help designs meet or exceed the code minimum or the preferred levels of sound control that is best suited for human health and wellness.
Comparison of MgO Panels with Wet-Laid Gypsum Underlayment
Based on all the foregoing discussion, the design and construction of multifamily projects requires that some decisions are made on how to achieve the code minimum or preferred levels of fire-resistance and acoustical performance in wall and floor/ceiling assemblies. Those decisions ultimately come down to selecting the right mix of products and materials to meet the criteria and there are, as already noted, many variations and choices. The role of the architect is to assess those choices not only for achieving the desired results, but also in terms of determining their impact on the construction process and overall cost of a project. In this light, we look at a comparison of two common floor/ceiling assemblies: wet laid gypsum underlayment and MgO panels.
Wet-Laid Gypsum Underlayment
Gypsum underlayments are used in both new and existing construction as a means to provide a level subfloor ready to receive a finished floor system. They are often described as “self-leveling” by virtue of the fact that they are poured as a wet mixture that settles down to a level condition.
Self-leveling underlayment products are generally an aqueous mixture of gypsum or hydraulic cements (i.e., cured with water), fillers, polymeric binders and additives. The type and amount of these ingredients as well as the amount of water in the binder are used to control the key properties such as flow, setting behavior, and compressive strength. The dry product is usually mixed with water on-site and applied to a subfloor to achieve a smooth surface. There are a range of self-leveling underlayment products which come with a wide variety of performance attributes to suit different job site requirements including the ability to enhance fire resistance and help increase STC/IIC ratings. Hence, they are sometimes considered as an option for multifamily construction.
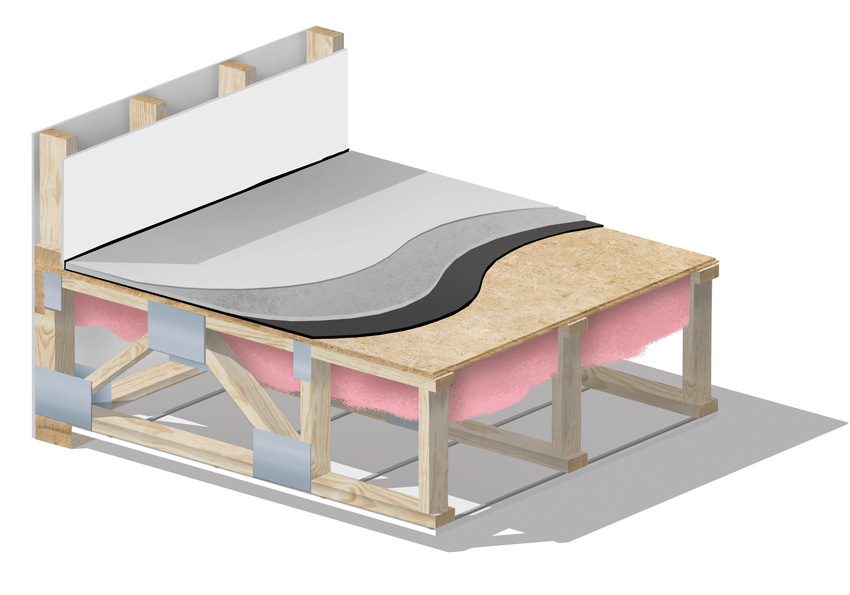
Wet-laid gypsum underlayment has the potential to introduce excess moisture into wood-frame structures and cause cycle time delays.
There are, however, some impacts on the construction process by using self-leveling underlayment. The most notable is the “wet-laid” installation, which necessarily introduces excess moisture into wood-framed structures. If that moisture is not properly controlled or dealt with, it can end up trapped inside wood-framed construction and cause deformation, deterioration, or mold growth.
The other notable impact on construction is the time schedule. An additional specialty subcontractor/crew is needed to install the wet-laid underlayment and they need to work through the different areas of the building to apply the material. This typically occurs after all framing is complete and the building is dried in from exterior weather. This means the underlayment does not continue under framed partitions, so fire and acoustical resistance/performance could be lessened in those locations. Further, if a partition ever needs to be moved, there is the issue of filling in the gap to be level with the rest of the underlayment.
More significantly, wet underlayment products typically need five to seven days under ideal conditions for curing, meaning no work can be performed on the floor during that time. This is exacerbated by unfavorable conditions of heat, high humidity, or cold temperatures that can cause longer delays and, perhaps, added expense to keep the temperature within the optimum curing range.
MgO Panels as Underlayment
MgO panels as described already are very well suited as an alternative to wet-laid underlayments. The MgO panels are installed in a “dry” manner, meaning no water is involved and no curing is required. That eliminates exposing wood framing to excess moisture. It also simplifies the construction process by eliminating the need to control the conditions for curing. Without any need for curing, there are also no time delays in the project while the curing takes place.
The installation of MgO panels can also streamline construction. Since it installs like typical wood subfloor products with common wood working tools and fasteners, framers who are already on-site can install it readily—thus eliminating the need for an extra specialty subcontractor or crew. This also means that the MgO underlayment can be installed before the framing of the walls and partitions to create a continuous layer that does not compromise acoustical or fire-resistance performance. Variations might include a wood structural panel and MgO underlayment producing a two-layer acoustical assembly. Or, a single layer of structural MgO may be part of an assembly plus an acoustical sound mat where needed. Details and variations can be reviewed and worked out with manufacturers during design to ensure the best performance while keeping the construction process flowing.
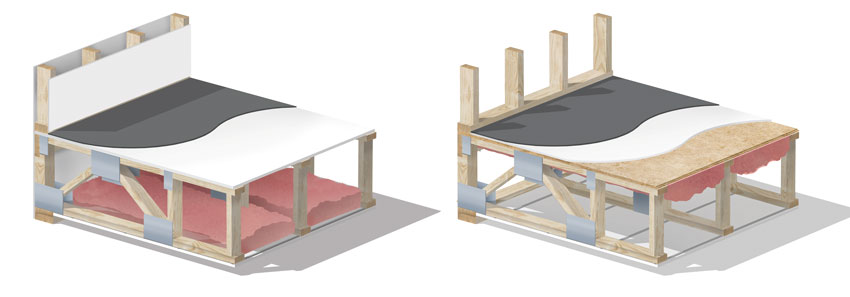
By using MgO subfloor panels, introducing excess moisture is avoided, and potential savings on cycle time are possible as well.
Ben Richardson is the MgO technology manager at Huber Engineered Woods and has direct experience in working with design and construction professionals. He points out, “When it comes to managing timelines for multifamily and light-commercial construction jobs, every hour counts.” His advice is, “To contribute to cycle-time savings and help save headaches associated with managing multiple trades on-site, consider using MgO panels. They can be installed similarly to traditional wood structural panels, which means traditional framing crews can manage the work. Plus, MgO does not require cure-time like wet-laid gypsum underlayment, potentially shaving weeks of time off a job.”
Conclusion
Based on the aforementioned information, design professionals should consider the following when designing multifamily buildings:
- MgO panels have been shown to be a desirable and effective alternative to conventional wood-based panel products.
- Using materials that allow for optimum time savings without sacrificing required sound or fire-resistance performance for subfloor assemblies is possible with MgO panels.
- Choose materials that eliminate the need for products that introduce high amounts of moisture into a wood-framed structure during the build cycle (e.g., wet-laid gypsum underlayment)
- Remember that not all magnesium oxide panels are the same. High-quality magnesium oxide panels use an engineered formulation of MgO and include an integrated mesh core for added structural performance.
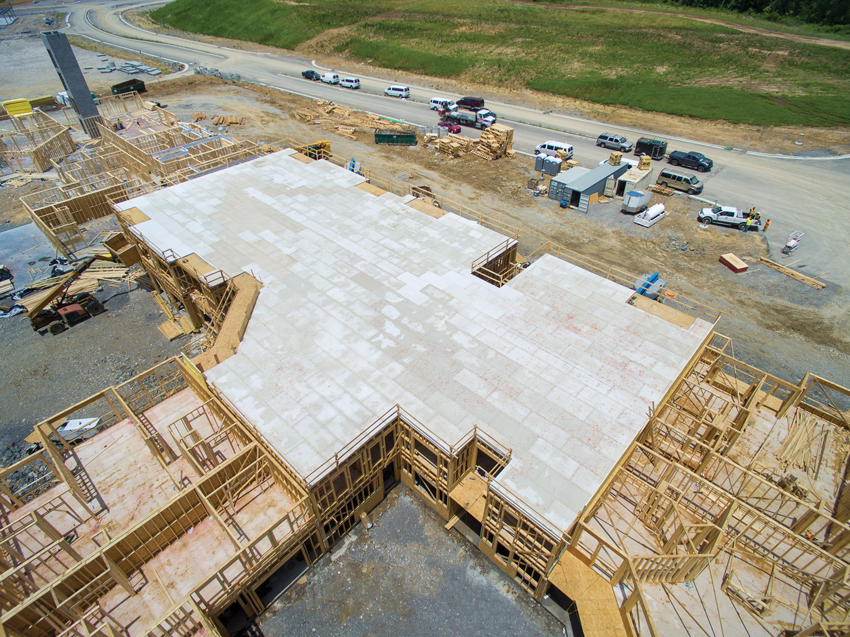
Shown is an aerial view of magnesium oxide (MgO) subfloor panels being used across the entire floor as part of a multifamily construction project.
Peter J. Arsenault, FAIA, NCARB, LEED-AP is a nationally known architect, continuing education presenter, and prolific author advancing building performance through better design. www.pjaarch.com, www.linkedin.com/in/pjaarch