When designing and installing metal roofs, the stakes are high in hurricane- and tornado-prone areas.
The eastern seaboard and Gulf States from upper Maine all the way down to Texas are contending with a significant increase in the frequency and intensity of hurricanes. And tornadoes are pounding the Midwest and South with alarming regularity.
In 2017 alone, damage from hurricanes were off the charts. Texas bore the brunt of Hurricane Harvey which caused a total of $125 billion in damages. Hurricane Maria hit the Caribbean in September with a $91.6 billion price tag on the heels of Hurricane Irma, which ravaged through the Caribbean and Florida earlier that month causing $77.5 billion in damages, according to the U.S. National Hurricane Center.
Just last year, the U.S. documented a record of seven tropical cyclones and 13 severe storms.
Causing death, injury, and unprecedented property damage, the 2020 billion-dollar disaster report from the National Oceanic and Atmospheric Administration’s National Centers for Environmental Information documents an astounding $1.3 trillion in damages from storms and cyclones since 1980.
For buildings, the first line of defense against these intense forces of nature is the roofing system.
“Because roof covering damage has historically been the most frequent and costly type of wind damage, special attention needs to be given to roof system design,” said Tom Smith, AIA, TLSmith Consulting in the National Institute of Building Sciences Whole Building Design Guide’s (WBDG) “Wind Safety of the Building Envelope.”
From the assorted materials and systems available on the market, high-quality metal roofing is arguably one of the best choices for protection from high winds.
Says the Metal Roofing Alliance, “Metal roofing is in high demand in hurricane-prone regions, due to its exceptionally long-lasting durability and protection against heavy rain, hailstones, and hurricane force winds.”
With larger interlocking panels, and fewer seams and overlaps than other roofing systems, there is less opportunity for the wind to penetrate. In the event that some wind manages to get in between the metal covering and the underlayment, metal’s ability to breathe and expand enables it to endure a high level of wind pressure. Consequently, many metal roofs are rated up to 150 miles per hour—the equivalent of a major Category 4 hurricane and an F2 tornado.
“Out of all the roofing types that are out there, you have got the best chance of survival with a properly installed metal roof,” stated Jim Bush, Metal Construction Association Chairman (MCA) and a member of the Roofing Industry Committee on Weather Issues (RICOWI) wind investigation teams.
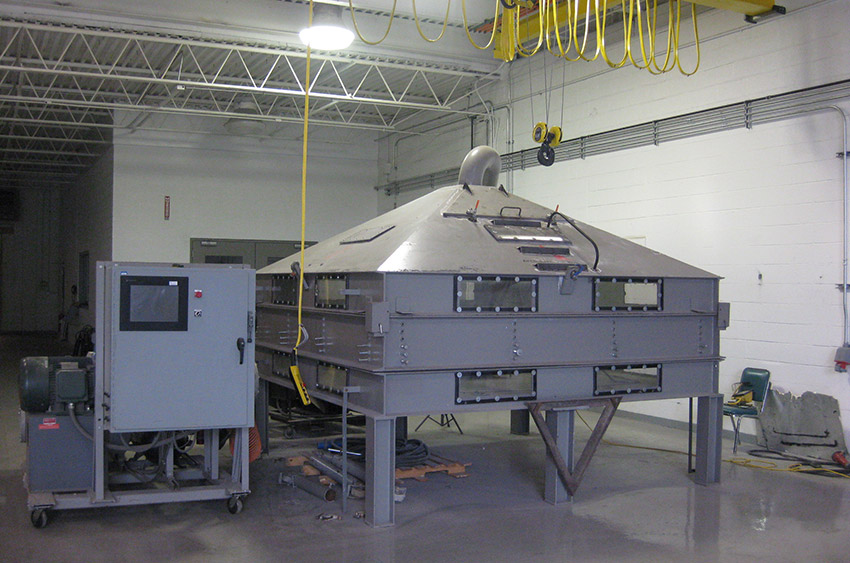
Photos courtesy of ATAS International
Underwriters Laboratories (UL) 580 tests and assigns a category based upon the roof deck
and coverings’ level of uplift resistance.
Installation and Testing Standards
While high-quality metal roofing systems have been engineered to deliver enhanced durability and longevity, their performance is ultimately dependent on professional installation by roofing experts who are familiar with these systems and committed to following the manufacturer’s installation instructions.
William A. Hayward Jr. AIA, CSI, CCCA, LEED Green Associate, a senior associate and architect with Michael Baker International’s Tampa location, stated, “If designed and installed properly, then metal roofs perform well in Florida. The key to success is in the details regardless of the material type/product.”
But before a commercial roofing project reaches the installation stage, architects are strongly advised to ensure that the metal roofing systems they select meet several key testing protocols. By understanding these tried-and-true wind resistance tests and standards, and better visualizing how high winds can impact product performance, architects will be much better informed when designing metal roof systems. As well, this knowledge is valuable to the specifiers when creating the project specifications.
In addition, an analysis of roofing successes and failures in the aftermath of a high wind event provides valuable lessons learned in approaching the next tornado and hurricane season.
Metal Roofing Panel Types
Prior to delving into the details of the different tests and standards that the metal roofing industry relies upon, an overview of metal roofing panel types is in order.
Mechanically Seamed Standing Seam – One of the more popular metal roofing systems, mechanically seamed panels offer a sleek, modern appearance. Because the panels are seamed together mechanically and are installed to the roofing substructure with clips, the surface has no exposed fasteners and is therefore better protected from moisture, UV rays, and other elements that can cause the fastener to wear over time.
Snap-Type Seam – A type of standing seam roof, the male and female legs of the panel are snapped together creating the seam, with no need for mechanical seaming. They require less labor and are less expensive to install than mechanically seamed panels.
Batten Seam – In a metal batten panel roofing system, a vertical leg is formed as an extra water barrier, with a wide batten seam creating bold aesthetics.
Two-part Batten or Standing Seam – the two panel legs are roll-formed and then butted one next to the other. A metal cap, batten, or standing seam style, is then used to create a seam. As the seam is a separate component of this system, designers can select contrasting colors for the panels and caps, if desired.
Shingles – Lightweight metal shingles help buildings better blend in to surrounding structures, while still benefitting from the durability, longevity, and thermal performance properties of a metal roof.
Shakes – Mimicking the look and style of wooden shingles, shake-inspired metal roofing panels offer a more classic look.
Tiles – Tile-inspired metal roofs are a more cost-effective and lightweight option delivering a high level of resistance against wind, fire, rain, and hail. Easy to maintain, the metal tiles are designed in the style of clay/concrete tiles.
Insulated Metal Panels (IMPs) – An insulating foam core is injected in between two metal sheets to create insulated metal panels. As a turnkey option—delivering a full vapor and water barrier, and continuous insulation—IMPs are an increasingly popular option.
Roofs fall under two categories from a performance perspective: low slope and steep slope. A low slope roof has a slope of less than 2:12, meaning that for every horizontal foot, the roof level goes up less than two inches vertically. Steep slope roofs have a slope of 2:12 or higher.
Steep slope roofs are lower maintenance as debris rolls off easily and standing water is less of an issue. They offer a more classic, aesthetically pleasing appearance.
Low slope requires fewer building materials and are easier to install. At the same time, they have a great need for proper flashing, drains, and coping. Further, the debris, snow, and rainwater doesn’t flow down as easily, so the roofs need to be maintained and inspected on a more regular basis.
When designing and installing metal roofs, the stakes are high in hurricane- and tornado-prone areas.
The eastern seaboard and Gulf States from upper Maine all the way down to Texas are contending with a significant increase in the frequency and intensity of hurricanes. And tornadoes are pounding the Midwest and South with alarming regularity.
In 2017 alone, damage from hurricanes were off the charts. Texas bore the brunt of Hurricane Harvey which caused a total of $125 billion in damages. Hurricane Maria hit the Caribbean in September with a $91.6 billion price tag on the heels of Hurricane Irma, which ravaged through the Caribbean and Florida earlier that month causing $77.5 billion in damages, according to the U.S. National Hurricane Center.
Just last year, the U.S. documented a record of seven tropical cyclones and 13 severe storms.
Causing death, injury, and unprecedented property damage, the 2020 billion-dollar disaster report from the National Oceanic and Atmospheric Administration’s National Centers for Environmental Information documents an astounding $1.3 trillion in damages from storms and cyclones since 1980.
For buildings, the first line of defense against these intense forces of nature is the roofing system.
“Because roof covering damage has historically been the most frequent and costly type of wind damage, special attention needs to be given to roof system design,” said Tom Smith, AIA, TLSmith Consulting in the National Institute of Building Sciences Whole Building Design Guide’s (WBDG) “Wind Safety of the Building Envelope.”
From the assorted materials and systems available on the market, high-quality metal roofing is arguably one of the best choices for protection from high winds.
Says the Metal Roofing Alliance, “Metal roofing is in high demand in hurricane-prone regions, due to its exceptionally long-lasting durability and protection against heavy rain, hailstones, and hurricane force winds.”
With larger interlocking panels, and fewer seams and overlaps than other roofing systems, there is less opportunity for the wind to penetrate. In the event that some wind manages to get in between the metal covering and the underlayment, metal’s ability to breathe and expand enables it to endure a high level of wind pressure. Consequently, many metal roofs are rated up to 150 miles per hour—the equivalent of a major Category 4 hurricane and an F2 tornado.
“Out of all the roofing types that are out there, you have got the best chance of survival with a properly installed metal roof,” stated Jim Bush, Metal Construction Association Chairman (MCA) and a member of the Roofing Industry Committee on Weather Issues (RICOWI) wind investigation teams.
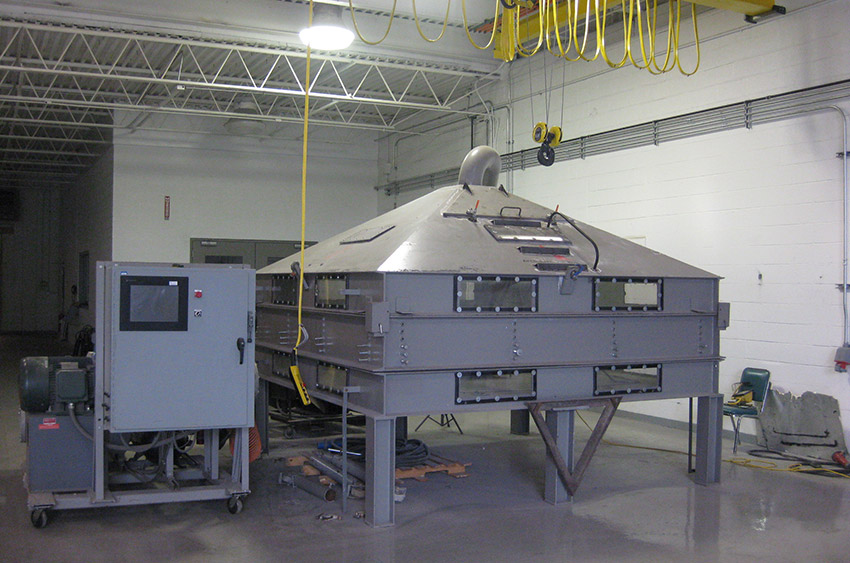
Photos courtesy of ATAS International
Underwriters Laboratories (UL) 580 tests and assigns a category based upon the roof deck
and coverings’ level of uplift resistance.
Installation and Testing Standards
While high-quality metal roofing systems have been engineered to deliver enhanced durability and longevity, their performance is ultimately dependent on professional installation by roofing experts who are familiar with these systems and committed to following the manufacturer’s installation instructions.
William A. Hayward Jr. AIA, CSI, CCCA, LEED Green Associate, a senior associate and architect with Michael Baker International’s Tampa location, stated, “If designed and installed properly, then metal roofs perform well in Florida. The key to success is in the details regardless of the material type/product.”
But before a commercial roofing project reaches the installation stage, architects are strongly advised to ensure that the metal roofing systems they select meet several key testing protocols. By understanding these tried-and-true wind resistance tests and standards, and better visualizing how high winds can impact product performance, architects will be much better informed when designing metal roof systems. As well, this knowledge is valuable to the specifiers when creating the project specifications.
In addition, an analysis of roofing successes and failures in the aftermath of a high wind event provides valuable lessons learned in approaching the next tornado and hurricane season.
Metal Roofing Panel Types
Prior to delving into the details of the different tests and standards that the metal roofing industry relies upon, an overview of metal roofing panel types is in order.
Mechanically Seamed Standing Seam – One of the more popular metal roofing systems, mechanically seamed panels offer a sleek, modern appearance. Because the panels are seamed together mechanically and are installed to the roofing substructure with clips, the surface has no exposed fasteners and is therefore better protected from moisture, UV rays, and other elements that can cause the fastener to wear over time.
Snap-Type Seam – A type of standing seam roof, the male and female legs of the panel are snapped together creating the seam, with no need for mechanical seaming. They require less labor and are less expensive to install than mechanically seamed panels.
Batten Seam – In a metal batten panel roofing system, a vertical leg is formed as an extra water barrier, with a wide batten seam creating bold aesthetics.
Two-part Batten or Standing Seam – the two panel legs are roll-formed and then butted one next to the other. A metal cap, batten, or standing seam style, is then used to create a seam. As the seam is a separate component of this system, designers can select contrasting colors for the panels and caps, if desired.
Shingles – Lightweight metal shingles help buildings better blend in to surrounding structures, while still benefitting from the durability, longevity, and thermal performance properties of a metal roof.
Shakes – Mimicking the look and style of wooden shingles, shake-inspired metal roofing panels offer a more classic look.
Tiles – Tile-inspired metal roofs are a more cost-effective and lightweight option delivering a high level of resistance against wind, fire, rain, and hail. Easy to maintain, the metal tiles are designed in the style of clay/concrete tiles.
Insulated Metal Panels (IMPs) – An insulating foam core is injected in between two metal sheets to create insulated metal panels. As a turnkey option—delivering a full vapor and water barrier, and continuous insulation—IMPs are an increasingly popular option.
Roofs fall under two categories from a performance perspective: low slope and steep slope. A low slope roof has a slope of less than 2:12, meaning that for every horizontal foot, the roof level goes up less than two inches vertically. Steep slope roofs have a slope of 2:12 or higher.
Steep slope roofs are lower maintenance as debris rolls off easily and standing water is less of an issue. They offer a more classic, aesthetically pleasing appearance.
Low slope requires fewer building materials and are easier to install. At the same time, they have a great need for proper flashing, drains, and coping. Further, the debris, snow, and rainwater doesn’t flow down as easily, so the roofs need to be maintained and inspected on a more regular basis.
Wind Resistance Testing
For most of the above-mentioned systems, different wind uplift tests and ratings are utilized, and various specification sections are applied to the different panel types.
The main product specifications for metal roofs are American Society for Testing and Materials’ ASTM E1514 Standard Specification for Structural Standing Seam Steel Roof Panel Systems and ASTM E1637 Standard Specification for Structural Standing Seam Aluminum Roof Panel Systems. In addition, Underwriters Laboratories’ UL 580 Standard for Tests for Uplift Resistance of Roof Assemblies, UL 1897 Uplift Test for Roof Covering Systems, and ASTM E1592 Standard Test Method for Structural Performance of Sheet Metal Roof and Siding Systems by Uniform Static Air Pressure Difference are used to determine a metal roof system’s uplift rating. These are all a series of tests.
Starting with ASTM E1592, this test is used to measure the bending capacity and attachment strength for standing seam, trapezoidal, ribbed, or corrugated metal panels in the thickness range of 0.012 inches to 0.050 inches, when the roofing system is subjected to a uniform static pressure. Air pressure is applied beneath the panels and attachments with a loosely installed plastic bag beneath the panels to maintain the pressure.
Deflections in the test panels are measured in at least six locations. Here, baseline measurements are taken at a nominal pressure and then at each of the specified test pressures or until the point of failure. Before moving to the next higher pressure, the test pressure is relieved so that the roof can be examined for permanent deformation. ASTM E1592 test results are then used along with wind design standards to determine required spacing of supports or attachments.
UL 580 assigns three classes—30, 60, and 90—based upon a roof deck and coverings’ level of uplift resistance. Suitable for systems where a structural panel is installed over open framing without the need for a solid deck, or where the roof covering is attached to a solid substrate when the two are specified as a system.
To achieve an ordinary class 30 or class 60 rating, pressure is applied beneath the system and a vacuum from above in an oscillating manner so that the maximum total pressures equal 45 pounds per square foot (psf) and 75 psf respectively. To qualify for the UL 580 class 90 rating, the system must withstand a maximum positive pressure—pressure from below—of 48.5 psf combined with a maximum negative pressure—a vacuum from above—of 56.5 psf, yielding a combined pressure differential of 105 psf.
First, the test is only run to the specified limit, not run to failure. In the second scenario where the roof covering is fastened to a solid deck, the deck aids in resistance to the pressure from below (positive), and the roof covering may only resist the vacuum from above of 56.5 psf. To aid in capturing the positive pressure below and transferring it to the metal panel itself, an air bag system is used between the panel and roof deck and/or purlins. Due to this requirement, and to distribute pressure to underside of panel, underlayments are not used within the test assembly.
Once the UL Class 90 test is completed, it’s common practice to transition to the UL 1897 test protocol to obtain ultimate pressure resistance values.
UL 1897 is used to evaluate the attachment of the roof covering systems to the roof decks by simulating negative pressures.
The test can be conducted by either pulling a vacuum above the assembly or, more commonly, by pressurizing an air bag placed loosely between the deck and the roof covering. The results are reported as the highest uplift pressure achieved prior to failure, usually in pounds per square foot. The test does not consider the strength of the roof deck and does not necessarily simulate the actual dynamic uplift pressures encountered by roofing systems.
In some cases, the tested panels are instrumented for observation of deflection and reaction during the panel loading process. This information can then be fed into high performance modeling computer programs which can assist in analyzing panel performance and panel clip interaction, and consequently predict the modes of failure.
With the aid of these key tests, architects will better understand how a metal roof system can withstand both external and internal pressures, which will than help guide the roof design and specification. The test result information will better inform decisions with regards to substrates, material gauges, clip spacing, fastener type, and panel profile.
While these tests can go a long way toward analyzing performance, it’s important that they don’t take the place of site-specific analysis by a design professional.
In a Metal Construction News article “Don’t be blown away by metal building requirements for high-wind areas,” MCA’s Director of Codes and Standards Andy Williams states, “The contractor should seek the assistance of a local design professional to ensure the project is designed to withstand the anticipated wind loads.”
Additional Metal Roofing Tests
A number of other tests can provide important performance information for metal roofing systems.
FM 4470 is an accreditation by Factory Mutual (FM). It is a series of tests which includes a determination of hail-resistance classes. Class 1-MH can withstand moderate hail, with a Class 1-SH rating, the roof can tolerate severe hail, and a Class 1-VSH is given to roofs capable of handling very severe hail. Following simulated hail impact, the roofing material cannot show any signs of cracking or splitting under 10x magnification. The roof seams cannot show any signs of cracking, splitting, separation, or rupture when examined under 10x magnification. For a roof system with a VSH rating, FM also requires that the substrate below the roof material does not crack. Minor surface indentations in the substrate are allowed at the point of impact.
FM 4471 tests product performance for combustibility, wind uplift resistance, hail damage resistance, and foot traffic resistance. This test determines if the product meets certain quality control requirements. FM 4471 is a common test reference for insulated metal panel roofs.
ASTM E108 is the Standard Test Method for Fire Tests of Roof Coverings.
UL 790 is basically identical to ASTM E108 and assigns roofing classifications. Class A roof coverings can withstand severe fire test exposures, Class B roof coverings are effective against moderate fire test exposures, and Class C roof coverings can handle light fire test exposures.
ASTM E283 is the Standard Test Method for Determining the Rate of Air Leakage through Exterior Windows, Curtain Walls, and Doors Under Specified Pressure Differences Across the Specimen for Steep Slope Roofs.
ASTM E331 is the Standard Test Method for Water Penetration of Exterior Windows, Skylights, Doors, and Curtain Walls by Uniform Static Air Pressure for Steep Slope Roofs.
ASTM E1680 is the Standard Test Method for Rate of Air Leakage through Exterior Metal Roof Panel Systems.
ASTM E1646 is the Standard Test Method for Water Penetration of Exterior Metal Roof Panel Systems by Uniform Static Air Pressure.
UL 2218 is the Standard for Impact Resistance of Prepared Roof Covering Materials. Roofs are classified from 1 to 4 with Class 4 offering the best resistance against hail. Most metal panel systems are capable of obtaining a Class 4 impact resistance.
ASTM E2140 is the Standard Test Method for Water Penetration of Metal Roof Panel Systems by Static Water Pressure Head.
Testing Metal Flashing Performance
A key component contributing to the resilience of metal roofing systems are the flashings which help prevent penetration of water. To better support metal roofing performance, the Metal Construction Association developed a new standard for testing metal flashing performance: ANSI/MCA FTS-1-2019 Test Method for Wind Load Resistance of Flashings Used with Metal Roof Systems.
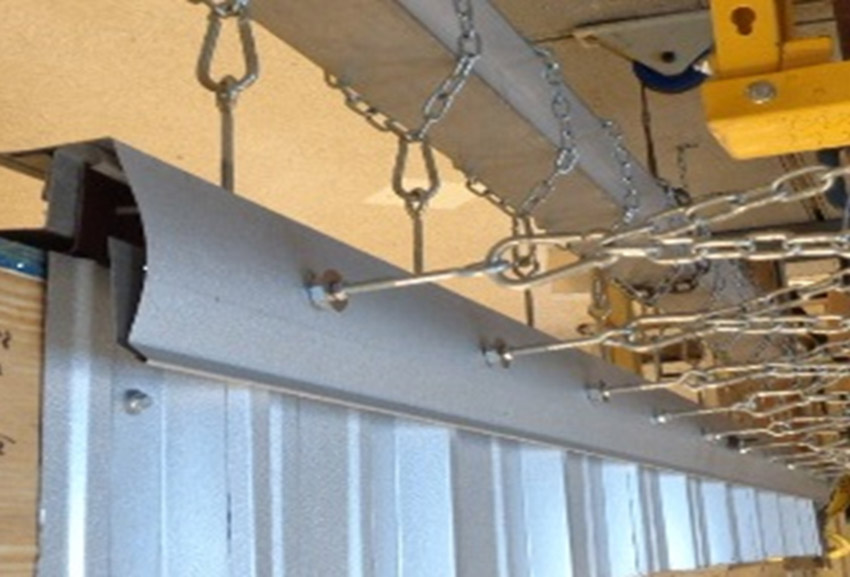
Photos courtesy of ATAS International
The Metal Construction Association’s ANSI/MCA FTS-1-2019 Test Method for Wind Load Resistance of Flashings Used with Metal Roof Systems focuses on the flashings preventing water intrusion for better resilience in metal roofing systems.
“Metal roofing systems of all types have proven to perform well in high winds. Properly detailed and installed, metal roofing typically withstands the forces of nature better than most traditional roof systems,” state the experts at MCA. “However, when a roof failure does occur, research shows that flashing failure may be a main contributor to the event.”
In investigating roof failures from several hurricane events including Charley, Ivan, Katrina, Ike, and Irma, researchers found that metal flashing failures were cited as a leading cause of all roofing system failures of various roofing material types.
Installed at the perimeter and at the eaves, gables, hips, and ridges, these locations are where the highest wind uplift pressures occur, which is why the high-quality manufacturing, design, and installation of flashing is essential.
The International Building Code (IBC) currently requires that all Perimeter Edge Metal be tested per ANSI/SPRI ES-1 for low slope membrane roofing systems. In particular, a special code section in IBC 2012 and 2015 on edge securement for low slope roofs states that low slope built-up, modified bitumen, and single-ply roof system metal edge securement, except gutters, shall be designed and installed for wind loads and tested for resistance.
This new ANSI/MCA FTS-1-2019 standard consists of four key sections: Test Apparatus, Test Specimen, Loading Procedure, and Test Report. It is MCA’s hope that testing metal roof flashings per this standard will be included in the next version of the IBC in 2024. For the time being, the standard is available to specifiers and manufacturers of metal roof systems to assure proper performance of the edge flashings with metal roof systems and assemblies as a best-practice approach.
A related standard, ANSI/SPRI GT-1, is used to test gutters by measuring the resistance of the gutter system.
“Particularly in low slope metal membrane-type roofing, if gutters blow off, and if they’re tied into the roof system, that can propagate failure,” explained Bush.
In response, this standard was developed and applies to all material types and membrane installation methods for low slope roofs.
Testing Standards Required By The Building Codes
In addition to the above-mentioned ANSI/SPRI ES-1, the IBC also requires UL 580, ASTM E1592, FM 4474, and UL 1897.
Per the International Code Council, the following reference documents are connected to the required wind resistance tests: FM 4470, UL 1897, and ASTM E1592. For systems installed over solid and closely fitted deck, UL 1897 is required; for metal roofing installed over spaced sheathing or space supports, UL 580, ASTM E1592, or UL 1897 are required; and for non-structural standing seam over solid wood sheathing, UL 580 is required.
Per the Florida Building Code (FBC), the following wind resistance tests are enforced:
- UL 580, Class 90 with supplemental pressures applied per UL 1897 to meet code requirements
- ASTM E1592
- TAS 125 which includes TAS 100 Wind Driven Rain, ASTM E 1592, and UL 580
- FM 4450
- FM 4470
- UL 1897
Hayward explained, “For example, in the state of Florida, all exterior building envelope elements must either have a Florida Product Approval, Miami-Dade Notice of Acceptance (NOA) or an engineered third-party design and calculations. In fact, these documents must be submitted the Building Department or Authority Having Jurisdiction prior to ordering material and installation. Having the physical test data/Miami-Dade NOA is validation that the manufacturer’s design works. People don’t want to find out after a hurricane event that the engineering was flawed. The test standards identify the allowable wind resistance (including safety factors) of the metal panel system for use on particular structures.”
Building Design Considerations
In addition to ensuring that metal roof systems pass key wind uplift and other performance tests, architects need to ask a number of important questions when designing commercial roofing system.
Essentially, the main issue here is whether the roof can withstand wind loads, so specifiers must determine the strength of the roofing system under consideration and the size of the potential wind load.
The American Society of Civil Engineers ASCE 7 Minimum Design Loads for Buildings and Other Structures is used to determine wind pressure. Adjusted design wind pressure can be determined using allowances in AISI A5.1.3 for steel products only. Adjustments for air permeability are permitted per ASCE 7.
It should also be noted that the interpolation of test results is often necessary for the varied deck assemblies used today. This analysis should be performed by a qualified engineer.
Overall, key information used to inform the design of a roof for wind loads includes the applicable codes or standards, as noted, in addition to occupancy classification nature, physical building considerations, and building location characteristics.
Nature of Occupancy Classification are as follows:
- Classification 1 – Low hazard to human life including agricultural, minor storage, and certain temporary facilities
- Classification II – Most typical buildings.
- Classification III – Substantial hazard to human life including facilities for more than 300 people, i.e., schools, jails, healthcare, power generation, and toxic chemicals.
- Classification IV – Essential facilities including surgery, fire and rescue, communications, emergency shelters, and national defense.
For physical building considerations, the building height and parapet height are important variables. The wind speed and uplift load increases as the building height increases. Any hills or cliffs surrounding the area will also increase wind speed. Further, an increase in parapet height will result in reduced peak loads and will spread the load to the interior roof surfaces.
For building location characteristics, the architect must evaluate basic wind speed, the surrounding terrain, and exposure.
The following are key exposure categories:
- Exposure B covers urban and suburban areas and single family dwellings.
- Exposure C includes open terrain and scattered obstructions.
- Exposure D includes flat, unobstructed areas and open water extending one mile or greater.
Effects Of Wind
To understand wind turbulence, wind speed is considered as two components: mean wind speed and fluctuating component.
Wind turbulence is caused by wind speed variability and short term wind variability. The speed is always fluctuating, and therefore the energy content of the wind constantly changes. The extent of the variation depends both on the weather and on local surface conditions and obstacles.
The fluctuating aspect is caused by meteorological movement and/or ground roughness/mechanical turbulence. In the boundary layer at high wind speed, mechanical turbulence predominates. Mechanical turbulence is higher in rough terrain than in smooth terrain and decreases with increasing height.
Another factor is aerodynamics. This is the effect of the wind flowing over and around a building which produces pressures on the external surfaces and may also produce internal pressures caused by the effect of wind/structure interaction.
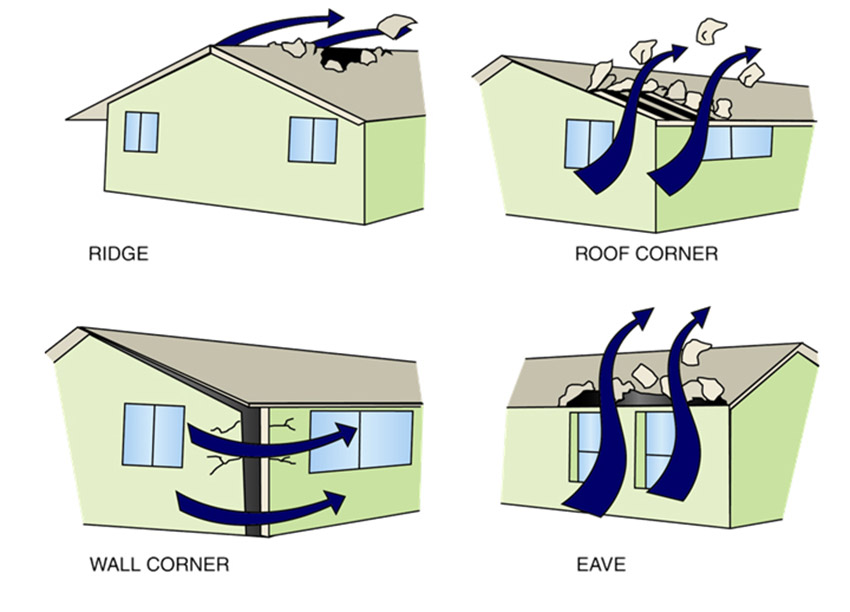
Photos courtesy of ATAS International
As air accelerates past sharp corners, the air flow separates creating very high negative pressures at the roof and wall corners, eaves, and ridge.
Windward walls can experience inward acting pressures called positive pressures. Local pressures are caused by the acceleration which occurs as air flows past sharp corners. Due to air flow separation, very high negative pressures develop at wall corners, eaves, ridge, and roof corners.
For canopies, the wind effects depend on the size of the canopy and its location on the windward wall. Pressures on the canopy’s upper and lower surfaces are approximately the same as those exerted on the adjacent wall surfaces. The overall wind load may be downward or upward depending on the location of the canopy on the windward wall.
Channeling between two buildings leads to increased wind speed and lower negative pressures on the facing walls of the building. Pressures are highest near the windward edge of the wall. Channeling would tend to affect walls cladding more than the roof cladding.
Analysis After Disaster
After a wind event has occurred, it’s important to analyze what went wrong with the roofing design and installation as valuable lessons can be gleaned for the future.
The first step is gathering information about the roofing system. This includes the roof deck type; structural dead load and live load capacity; roof length, width, and slope; fastener pull-out and metal pull-over results.
Experts are then brought in to help determine which aspect/aspects of the roof design contributed to the damage/failure.
“Typically, what I do right after a hurricane is I’ll rent a helicopter to get up there and do an aerial survey. You can really get a good lay of the land and see what worked and what didn’t,” explained Sean Reid, managing director, Precision Industries, Cayman Islands.
As borne out by testing, the metal itself very often survives the weather event, and the failure is ultimately attributed to a problem with the installation.

Photos courtesy of ATAS International
This roof experienced edge failure creating a “domino effect” where the failure propagates the continued peeling back of the roof panels.
“In many cases, you can pretty much pinpoint a deficiency in the as-installed portion where an attention to detail wasn’t done,” said MCA’s Bush. “Or 90% of the roof was properly done, but somewhere along the line during the course of installation, somebody got lazy and a portion of that roof gets breached. When that happens, it often propagates failure in surrounding areas as well.”
In a similar vein, Roger Bressi, managing director, Rooftops Silicone Distributors, Inc., U.S. Virgin Islands, said, “If the installers do the job properly, there should be no reason that the roof should come off. Most all failures where we live are due to improper installations and lack of inspecting via the authorities.”
To better understand common causes of failure, the following is a list of roofing problems which can occur from a high wind event:
- Poor edge securement identified as a flashing failure – This is why the ANSI/MCA FTS-1-2019 test protocol was created
- Edge failure creating a “domino effect” where the failure propagates the continued peeling back of the roof panels
- Open framing failure – With a metal roof panel being applied to an open frame assembly in lieu of solid decking, the internal positive pressures along with the external negative pressures create a mode of failure as the system cannot handle the combined loads
- Load path deck failure
- Fasteners pull out failure into the metal decking supporting the roof panels – Tighter clip spacing may prevent this
- Pull-over values are not strong enough to support wind loads
- Failure at the first course of panels causes a progression of panels blowing off
- Panel disengagement
- Door or window failure causes building pressurization
- The anchor system at the eave fails. This reveals how the gutter is an integral component of the roof assembly
- The door or window on the windward side of the enclosed structure fails. Pressurization of the building can also cause the roof and walls to blow out
Bressi added to the list improper screw lengths and/or sizes, using nails instead of screws, and improper clip spacing.
Best Practices
Working on everything from high-scale industrial to multifamily housing throughout the Caribbean over the past few decades, Precision Industries’ Reid has seen it all. His firm is often called in, post-hurricane, to assess roofing damage and assist with rebuilding efforts.
With a firm handle on what works and what doesn’t, he’s developed a number of his own best practices, above and beyond the manufacturer’s installation guides.
“One of the major changes we made in the region, even before we even started having these back-to-back hurricanes, was closing soffits,” he explained. “Everyone likes to have circulation in the attics, but here in the Cayman Islands—and in the Caribbean as a whole—the buildings were so damaged. Even if the roof stayed on, the wind and water came in through the soffits. So we’re now eliminating soffit vents and closing in ridges as well.”
Bush added that contractors have started closing attic spaces in Florida, not only for wind resistance, but to cash in on energy savings. “By conditioning the attic spaces and keeping the ductwork cooler, it’s more energy efficient and it keeps that building tighter where it minimizes that internal positive pressure.”
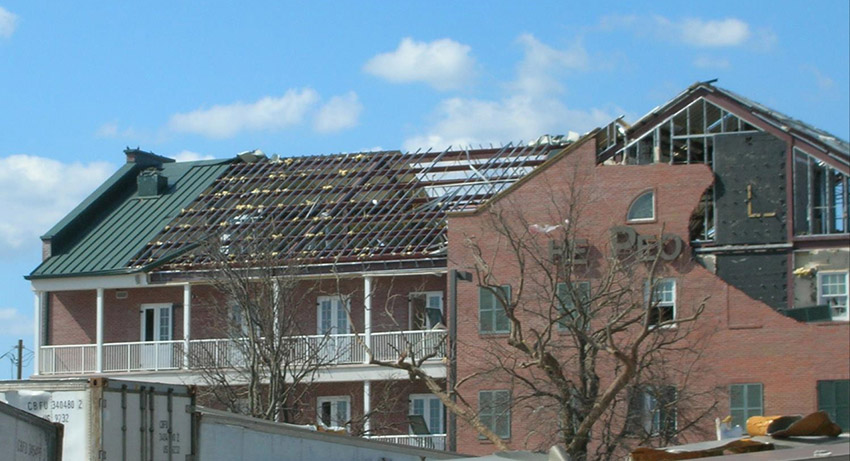
Photos courtesy of ATAS International
As opposed to more secure solid decking, this metal roof panel was installed in an open frame assembly. In the presence of high winds, the internal positive pressures combined with the external negative pressures to create a mode of failure.
Granted, through the process of completely sealing the enclosure, this alters the pressures in the structure, as noted, but if the envelope is not breached, a well-designed metal roof should stay on.
Another best practice Reid has adopted is hooking all the drip edges. “We created an offset to cleat so that we can still get gutters up underneath the drip. We like to have that drip all the way around and completely cleated.”
If the drip edge system is not properly attached and secured, which is the primary start on a standing seam roof, the gutter will typically fail if it’s peeling on the leading edge.
The contractor also puts in additional clips, thereby reducing the clip spacings, and has increased the number of rivets on all the hips and ridges of the roof.
Bush adds that the perimeter and corner areas of a building are subject to the greatest pressures created by the wind. Consequently, these zones often employ additional clips and fasteners to resist these greater forces.
These strategies seem to be working, as Reid reported not losing a single roof to Hurricane Ivan, which was the worst to hit the Cayman Islands. “Even the roofs that were in process remained on,” he said. The hurricane peaked at 165 mph as it passed within 30 miles of Grand Cayman and ultimately caused $2.86 billion in property damage.
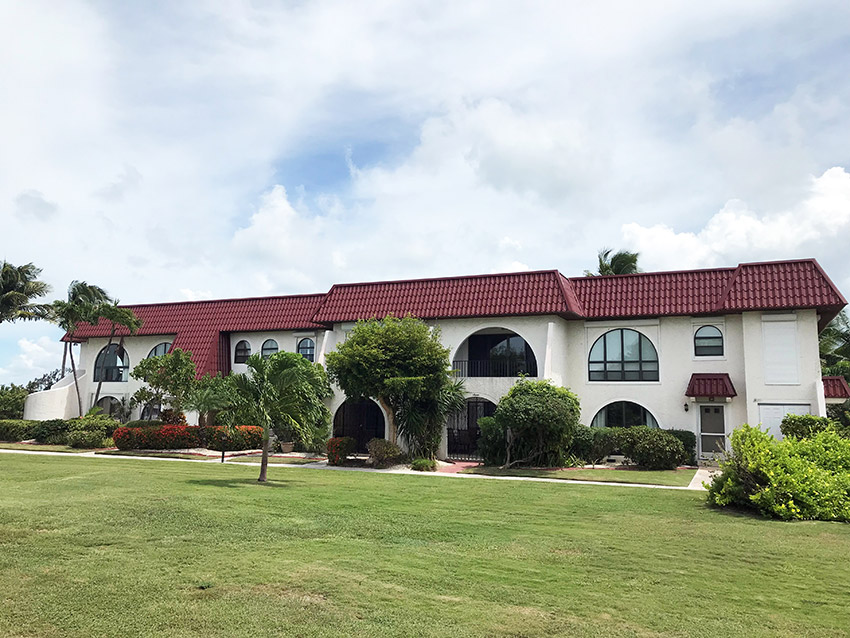
Photos courtesy of ATAS International
At the Lime Tree Bay Condominiums in Grand Cayman, Cayman Islands, Precision Industries installed a metal tile roof for enhanced durability and high wind protection.
Meanwhile, Bressi has observed that the roofs which best withstand the high winds have no overhangs and very steep roofs. “There is a reason that the old timers in the Caribbean built everything without overhangs and pitched the roofs 7, 8, or 9 on 12.”
In Hayward’s experience rebuilding damaged condo units in Homestead, Fla., after Hurricane Andrew, he found that several sliding glass doors were broken by flying debris or high wind pressure at the corner of buildings where there was a significant amount of positive pressure interjected within the building. This, combined with the negative pressure/uplift on the exterior, resulted in the roofs’ failure and consequently significant interior damage from rainwater intrusion. Therefore, he said, the design of the entire building envelope is critical.
Offering his own list of best practices for metal roof designs, the architect recommended specifying concealed fasteners and specifying appropriate metal finishes near coastal environments, including material gauge, roof substrate, sub-roof requirements, and insulation.
He added that generating a dew point analysis of the roof and wall assemblies are critical considerations when preparing specifications and drawings for the metal roofs or building elements. “The metal flashings, sub-roof membrane, and penetration details are critical for design and installation of a successful metal roof. Additionally, check with product representatives to make sure that the specs are up to date, and that a substitution procedure and form is included with the Division 01 specifications. If an alternate material is being proposed by the contractor, make sure that there is a way to compare ‘apples to apples’ and identify any costs savings, or required re-design efforts that must be accounted for.”
Reid works closely with roofing manufacturers and has been involved in testing different types of systems.

Photos courtesy of ATAS International
By spacing the purlins closer together in the perimeter zones, metal roofs are better equipped to withstand high winds.
“We’ve gone into the lab, built different systems and blew them up to see what they would do,” he explained. “I’ve always been fascinated about the stretch of a standing seam roof, how the aluminum will bubble and raise up significantly between the seams. If you have proper seaming, your clips are properly placed, and you utilize the proper fasteners, it’s incredible the amount of pressure that metal roofing can handle when it balloons like it does. It truly breathes.”
Reid has also partnered with manufacturers to test and develop an extruded base cleat for all their coping systems. “Utilizing a 0.080 extruded base cleat and minimum of 0.050 aluminum for the coping has made a tremendous difference,” he said.
Also of note are metal roof selections for coastal environments. While steel is a stronger material, it is prone to rust and can cause corrosion issues. Consequently, aluminum is the product of choice for buildings located next to the water. Architects usually specify 0.040 thickness, which is typically the heaviest gauge that can be easily roll formed and properly shaped to accommodate metal roof panel designs.
In the WBDG article, Smith offered the following recommendations for metal roof system installations:
- If the panels are attached to wood or metal nailers, detail the connection of the nailer to its support. Pay particular attention to where the nailers are spliced over a support. Screws are recommended in lieu of nails to attach clips.
- Develop secure perimeter securement and flashing details (i.e., panel eaves, rakes, hips, valleys and ridges, and flashings at hips, rakes and ridges). Common problems are excessive fastener spacings at these areas. Depending upon design wind loads, fasteners should typically be spaced from 3 inches to 12 inches on center.
- In areas with a basic wind speed greater than 90 mph and for buildings with an eave height of 100 feet or greater (regardless of basic wind speed), along eaves, hips, and ridges, it is recommended that two clips be used at each rib. This conservative redundant practice recognizes the importance of the end clip in these critical locations.
Partnerships
In partnering with the right professionals to support a successful metal roofing design and installation, Hayward recommends selecting a product rep that offers good technical support, and preferably one that is a member of the Construction Specifications Institute (CSI) with Construction Documents Technology (CDT) or Certified Construction Product Representative (CCPR) certifications. “These professionals will be your trusted advisors, whether you’re an architect or contractor, and hopefully keep you on the path to a successful roof and building installation. As architects, we do not have time to keep up with all the available and appropriate products or product changes, so it is important to build these relationships with product reps well before the project goes out to bid.”
Ultimately, Bush places much value on contractors and manufacturers working hand in hand to deliver the best metal roofing solutions.
This starts with contractors trusting that manufacturers have created an optimized set of details based upon much hands-on experience and expertise in this realm. Consequently, at the minimum, contractors are highly encouraged to follow the manufacturer’s installation instructions. If they choose to enhance and go beyond the details, based upon their own experience in their region and climate, this is encouraged.
It is possible to encounter a contractor who works in a particular geographic area, who is set on a particular detail and is unwilling to take the advice of the manufacturer. The contractor might claim that their way of doing things has worked, and that they have never experienced significant roofing failures from wind.
Experts would counter that the contractor has been very lucky and may never have encountered that one high-wind event that the code dictates, but it’s a risky endeavor not to follow the installation instructions.
“You can always expand upon that and do a little heavier, or a little better, or decrease fastener spacing, but at the very least, use the intent of the manufacturer’s details,” said Bush.
In summarizing recommendations for architects, specifiers, and engineers looking to design the best roofing system to withstand high winds, Bush said:
- Write proper test protocols into the roofing specification based upon the panel system type, i.e., structural, non-structural, metal shingle versus metal panel.
- Enlist the services of an engineer to review the panel capacity and fastening to ensure performance of the metal roof system in its actual geographical location.
- Provide proper supporting data to ensure performance based upon testing.
- Properly recommend the type of metal roof panel for the project design, roof slope, and resistance to the local environmental loads, i.e., wind, rain, snow, hail, etc.
Ultimately, it’s in the building team’s best interest to pay heed to wind resistance testing, careful review of the building site and geographic location, consultation with experts, and careful attention to installation details to ensure the best results.
“All over the world, metal roofing has been battle tested by Mother Nature. For those who are increasingly concerned about extreme weather and storms, that makes the durability, long-lasting protection and reliability of metal roofing very appealing,” concluded Renee Ramey, executive director, Metal Roofing Alliance.
Barbara Horwitz-Bennett is a veteran architectural journalist who has written hundreds of CEUs and articles for various AEC publications. www.bhbennett.com