View course on architecturalrecord.com »
BEING the “tallest” was never the goal for the Ascent, a 284-foot-high timber-framed residential tower in Milwaukee, says Jason Korb, principal at Korb + Associates Architects, the building’s design firm. Nevertheless, over the course of the project’s design phase, the scheme grew several times, starting at 19 stories and eventually reaching 25, as codevelopers New Land Enterprises and Wiechmann Enterprises sought economies of scale. Now complete, it was designated, by the Council on Tall Buildings and Urban Habitat (CTBUH), a Chicago-based nonprofit, the world’s tallest timber tower in July, just days after the first residents started moving into the 259 one- to three-bedroom market-rate apartments. The Milwaukee project supersedes the previous record holder, the mixed-use 280-foot, 18-story Mjøstårnet, in Brumunddal, Norway, completed in 2019, by only 4 feet.
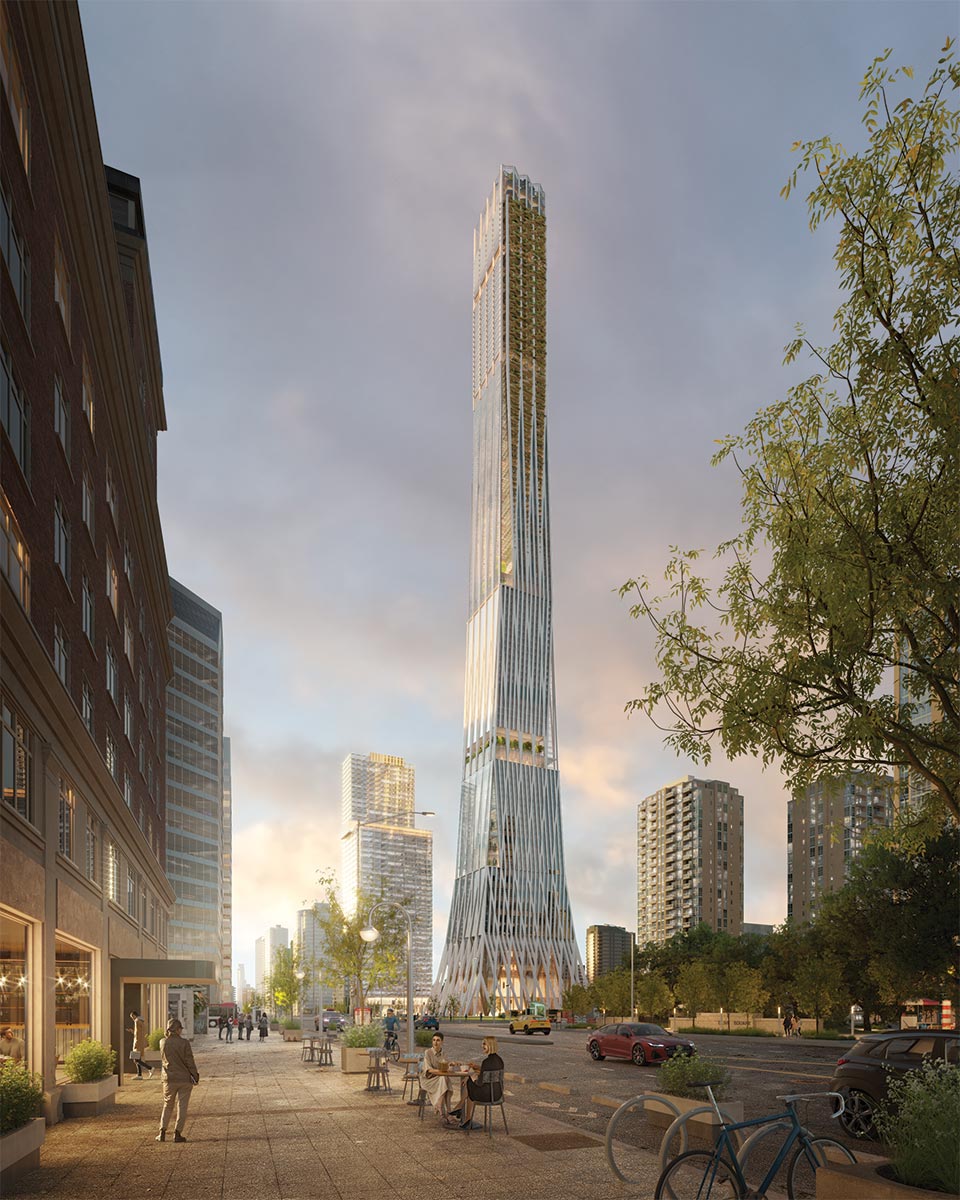
Photo courtesy of DIALOG
DIALOG'S SUPERTALL tower concept includes a floor plate system using mass timber.
The Ascent and Mjøstårnet have not been built using traditional light-frame wood construction. Instead, they rely on “mass timber,” a term that encompasses a group of engineered wood products made from small-dimension lumber, wood plies, or other types of wood fibers assembled under pressure and fixed with adhesives, producing construction components of exceptional strength. These include glue-laminated (glulam) columns and beams, cross-laminated timber (CLT) panels, and laminated-veneer lumber (LVL). And there are more and more buildings using these types of structural elements worldwide. In its State of Tall Timber 2022 report, released this past February, CTBUH counts 139 mass-timber buildings, eight stories or higher, that are complete, under construction, or proposed, globally. The number might sound small, but the total has more than tripled in the past five years since the last time the council published a similar accounting, when there were only 39 such buildings.
What is behind the rise of mass timber? One factor is the growth in off-site construction, which pairs well with these products, as the components are typically fabricated in a factory and brought to the site for just-in-time installation. Many architects and their clients are, of course, drawn to wood’s natural warmth and beauty. However, the chief attraction is environmental. When the forest from which they are obtained is responsibly managed, the trees perform important ecological functions, such as filtering water and air and providing habitat for wildlife. And, most critically, timber stores carbon, even after the tree is cut down: when wood is transformed into structural components, or other durable products, it sequesters carbon for the life of those elements—only releasing it back into the atmosphere when the wood decays or burns. The amount of this so-called “biogenic carbon” varies by species, but for many of the softwoods used in mass timber, the rate of sequestration is approximately 1 metric ton of CO2 equivalents per cubic meter.
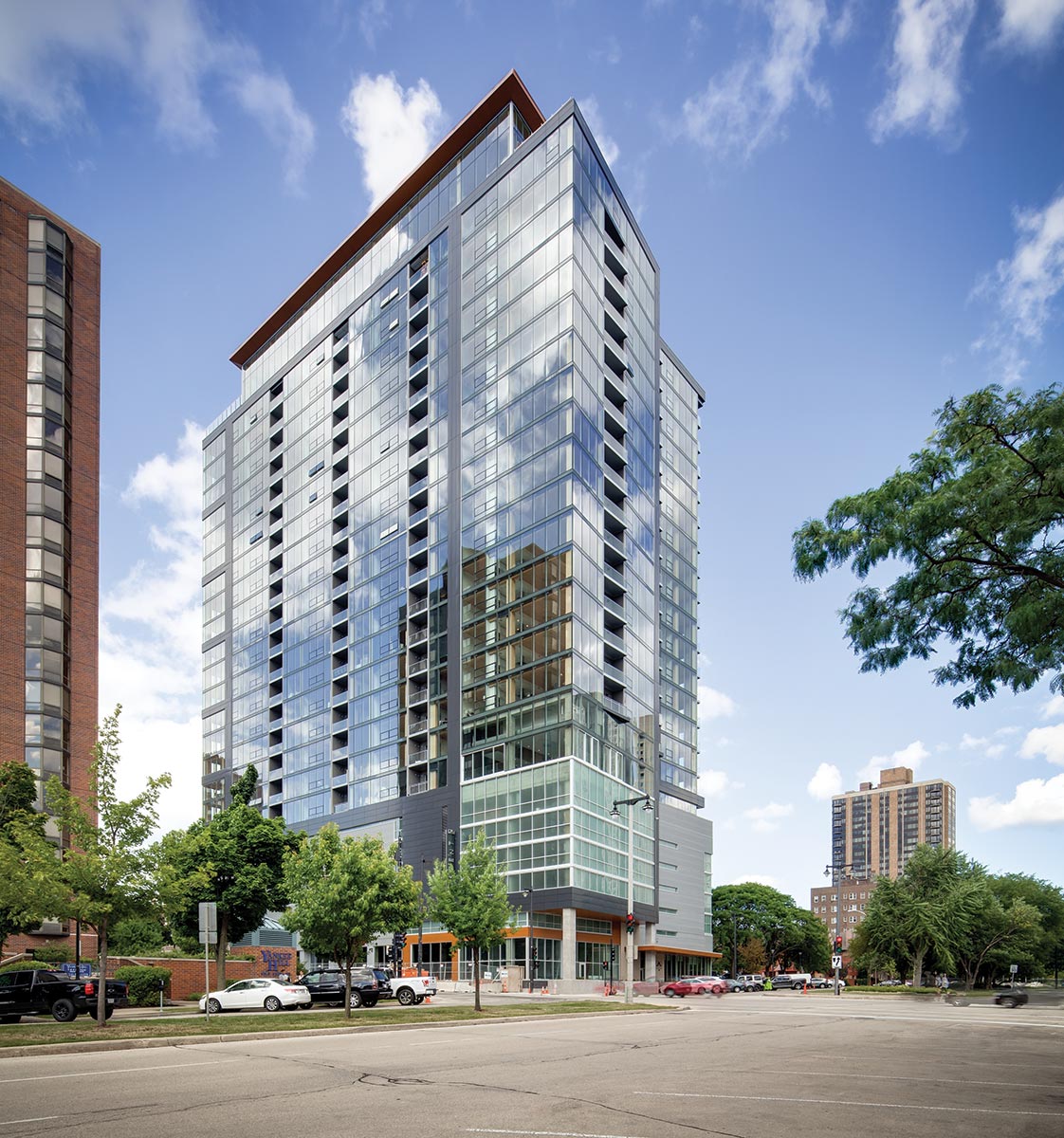
Photo courtesy of KORB + ASSOCIATES ARCHITECTS
The ASECENT, now the world's tallest timber tower, comprises 19 mass-timber floors over a six-story concrete podium. Much of the timber is exposed on the interior.
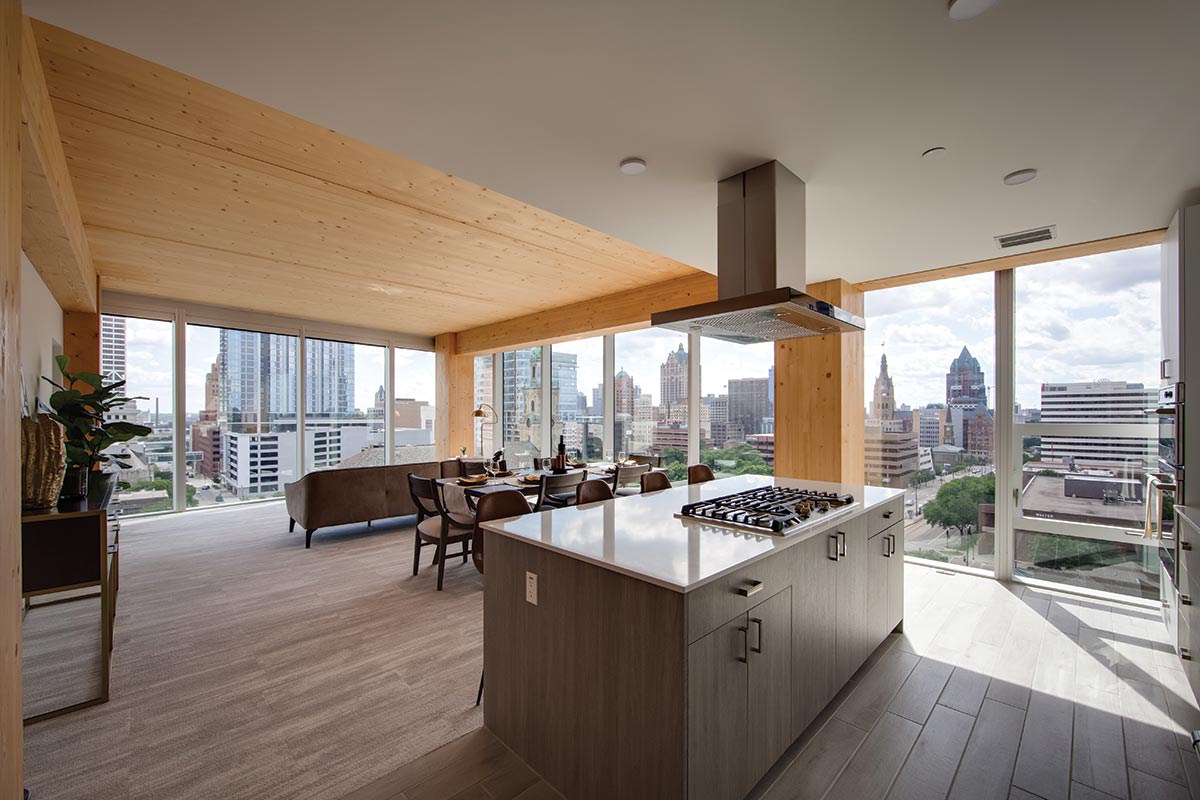
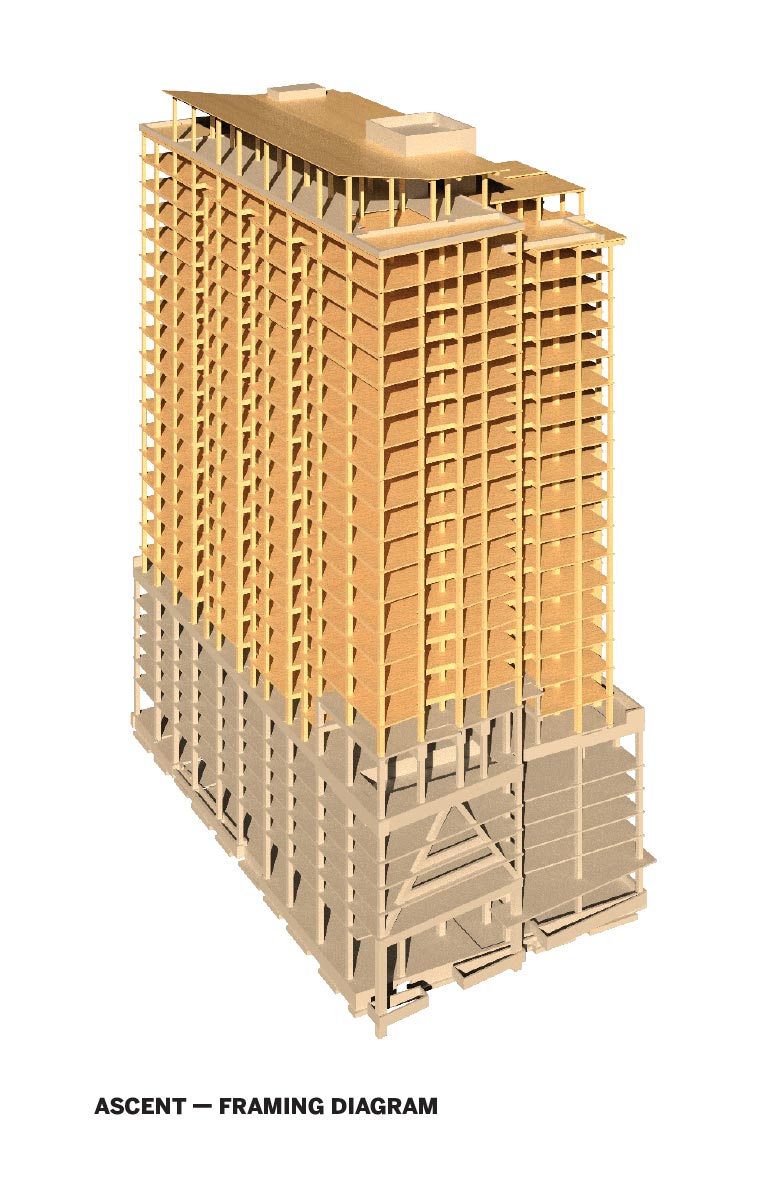
Photo courtesy of THORNTON TOMASETTI
Changing regulations are helping build mass timber’s momentum. Until recently, in most American cities, the height limit for wood buildings was 85 feet, about seven stories. But the latest versions of the International Building Code (IBC), the model code used by most jurisdictions in the U.S., permit mass-timber structures up to 18 stories. These tall mass-timber provisions have been adopted, either in whole or in part, by eight states, as well as Maryland’s Howard County, Denver, and seven cities in Texas.
In 2018, when the Ascent started permitting-process discussions, Milwaukee’s prescriptive height limit of 85 feet for wood structures was—and is still to this day—in place. So, in order to satisfy code officials and build a timber tower that exceeded this mark by nearly 200 feet, consultants conducted extensive simulations, studies, and evaluations. They needed to demonstrate that the structure—19 stories of glulam columns and beams, floor slabs of CLT, and a pair of reinforced-concrete cores over a six-story post-tensioned concrete parking podium—would not compromise the safety of occupants. “We had to show that the building meets the intent of the code,” says John Peronto, principal at Thornton Tomasetti, the project’s structural engineer.
Fire, of course, was a particular concern. When heavy timber burns, it develops a protective char that then insulates the member’s interior from damage. Though this phenomenon is well understood, physical tests were needed to validate that the Ascent’s wood elements—about 40 percent of which are exposed on the building’s interior—were properly oversized to account for the sacrificial layer. Testing for the project involved a three-hour controlled burn on exposed glue-laminated timber. Other safety measures included the installation of a temporary standpipe in the elevator core to protect the structure during construction and until the building’s permanent fire-suppression system could be activated.
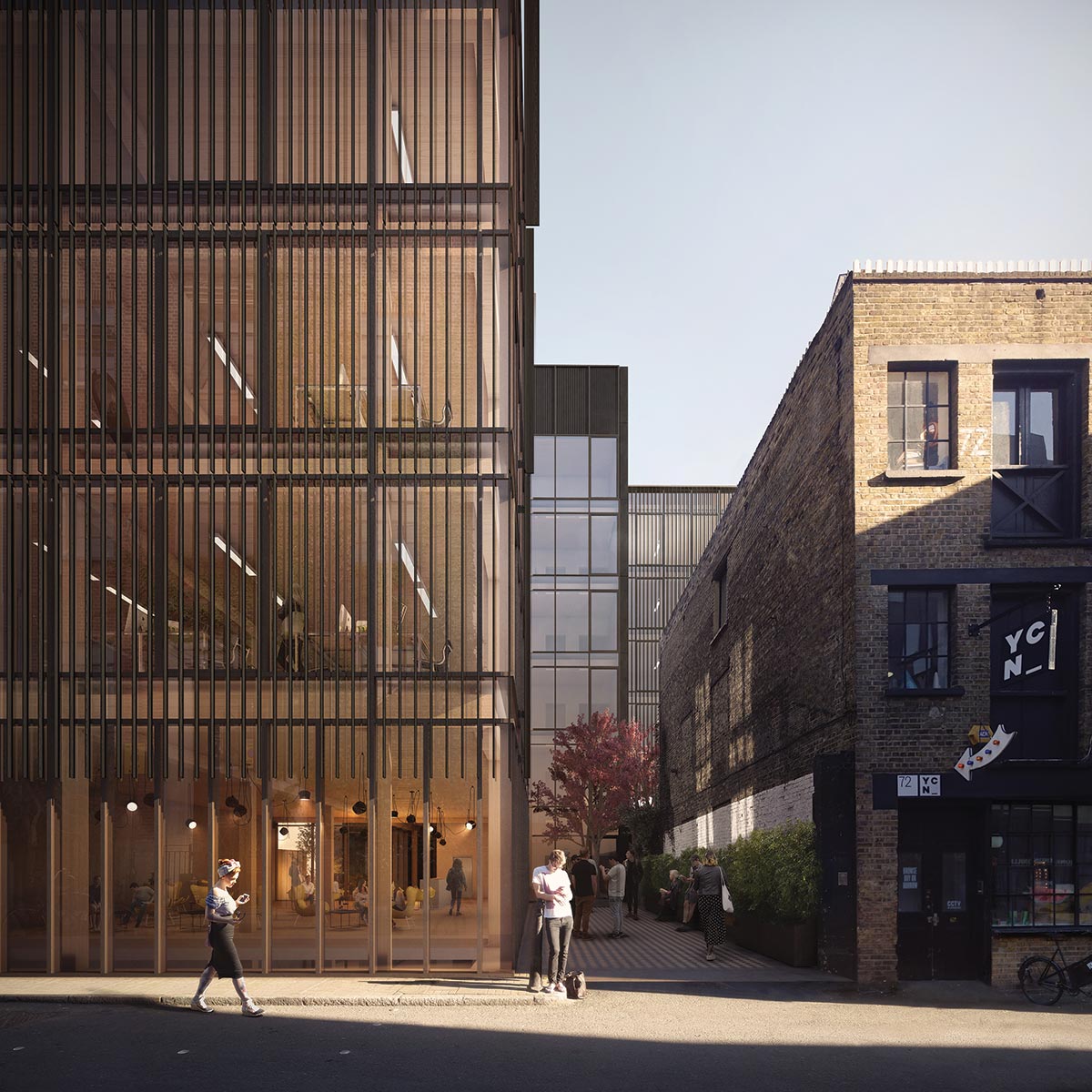
Photo courtesy of THE OFFICE GROUP
THE TALLEST timber office building in Central London will be Waugh Thistleton's Black & White Building, though it will be only 58 feet high.
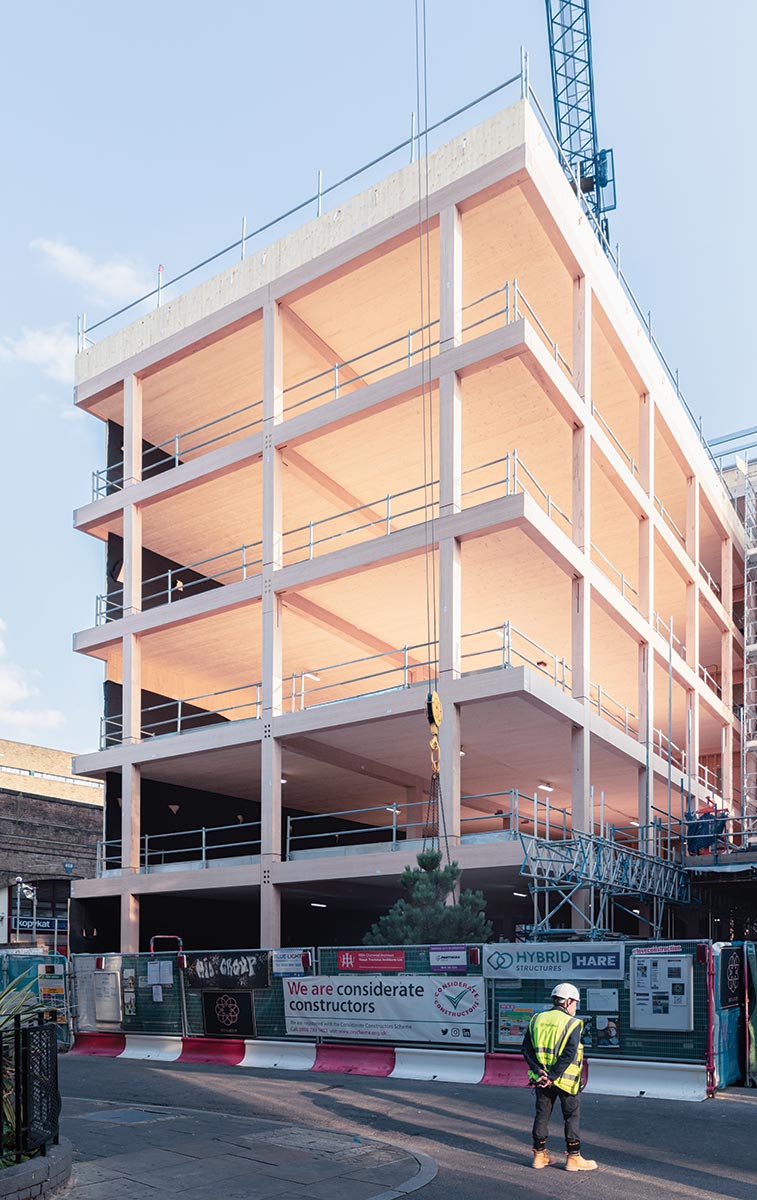
Photo courtesy of THE OFFICE GROUP
Korb estimates that the premium for the wood structure was about 30 percent when compared to an equivalent one in concrete. But there were savings too—in the foundations, for instance—since the superstructure weighs about a quarter of what a concrete one would. And there were other cost offsets: the factory fabrication of the timber components and their steel connectors, aided by a highly detailed digital model, shaved two to three months off the construction schedule, says Korb. “The model included every last screw.”
Ascent could soon be superseded by any number of proposed timber buildings, including one designed by Korb + Associates, a 313-foot-tall, 29-story apartment tower planned for St. Louis. Other, even taller, on-the-boards timber towers are a 600-foot-high, 42-story headquarters for software company Atlassian, in Sydney, by SHoP Architects; a 427-foot-tall, 37-story mixed-use tower in Rotterdam, by PLP Architecture; and a 328-foot-high, 32-story residential building, in Winterthur, Switzerland, by Schmidt Hammer Lassen Architects.
Although tallness grabs attention, for some mass-timber proponents, all the talk about height is a distraction. “Tall buildings should be the exception rather than the rule,” says Andrew Waugh, director of UK-based Waugh Thistleton Architects. Waugh cites studies showing that, compared to shorter structures, taller buildings have increased operating energy and embodied carbon (the emissions associated with materials manufacturing and construction) relative to their floor area. Instead, he advocates for a high-density but low-rise approach. “If the primary reason to build in timber is to reduce the impact of carbon, we have to ask ourselves, ‘Why we are building tall?’ ”
Waugh’s firm is nearing completion on the Black & White Building, which will be Central London’s tallest engineered-
timber office building—but at only six-stories and 58-feet high. Built with laminated-veneer-lumber columns and beams, and a core and floor slabs of CLT, the building could have been several times taller using the same structural diagram, maintains Waugh. But, instead, the 48,000-square-foot coworking space is at the same scale as the adjacent buildings. “It is the appropriate height,” he says.
Black & White’s embodied carbon is 410 kilograms of CO₂ equivalents per square meter—based on a comprehensive analysis that includes the enclosure and its mechanical systems—which represents a 33 percent reduction compared to a building constructed of more conventional materials, according to the architects. That’s without subtracting the nearly 1,000 metric tons of biogenic carbon stored in the timber structure. The two totals are kept separate, in part, says Waugh, because combining them would incentivize the use of more timber than is structurally necessary. To deploy the material as efficiently as possible, his firm worked with its engineering consultants, Eckersley O’Callaghan, refining and optimizing the framing system. The strategy also helped control costs, keeping the structure to $390 per square foot, which Waugh says is roughly equivalent to concrete.
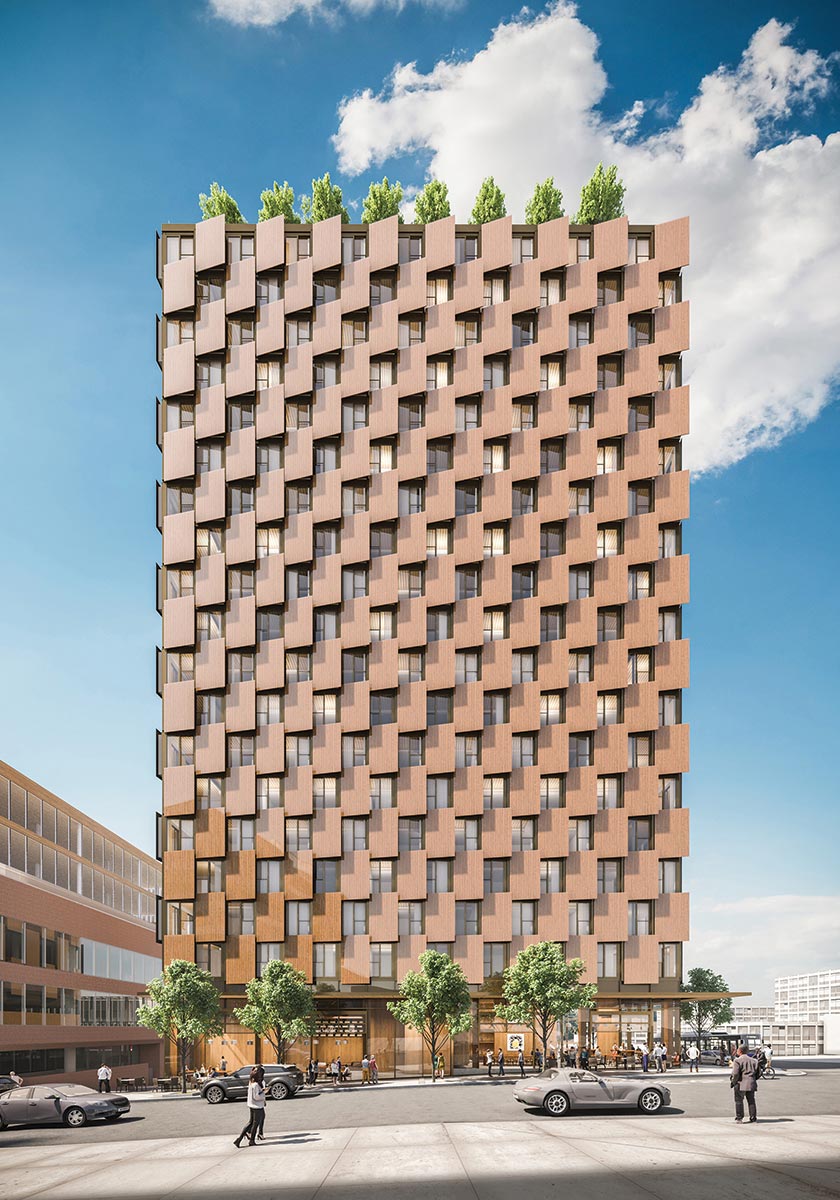
Photo courtesy of HENRIQUEZ PARTNERS
THE STRUCTURE of a Vancouver residential tower by Henriquez Partners will combine timber, steel, and concrete. The skin includes veneer laminated within glass.
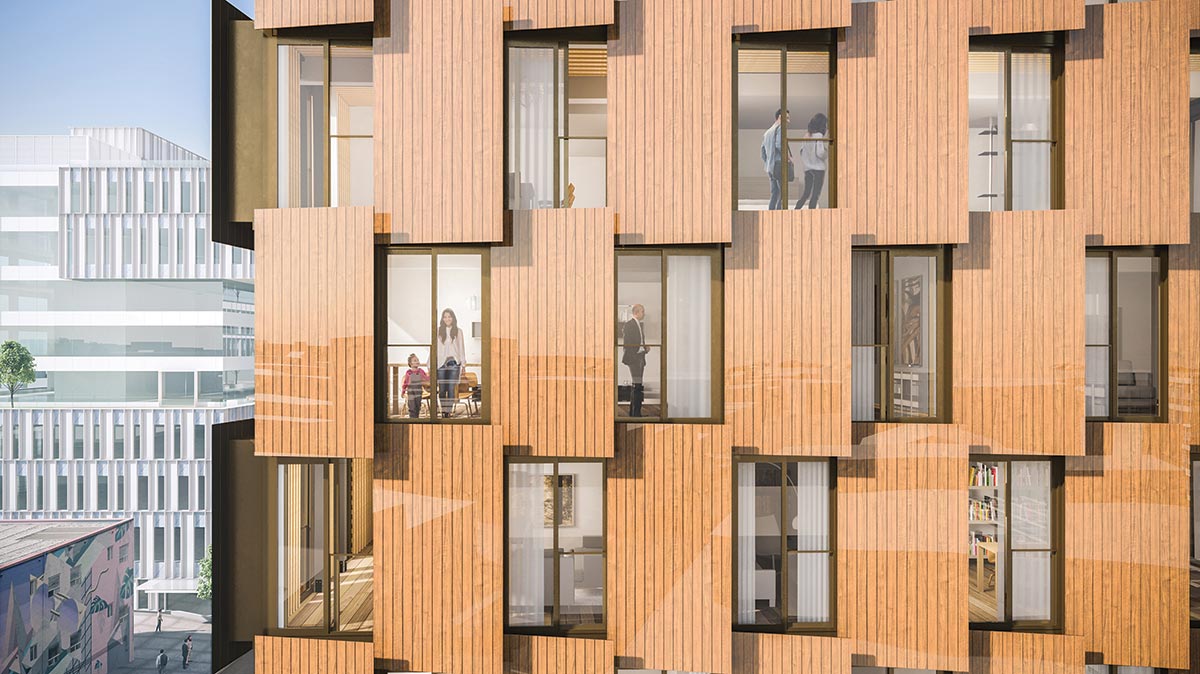
Photo courtesy of HENRIQUEZ PARTNERS
Despite the arguments of those like Waugh who favor a low-rise approach, tall buildings will continue to be built, especially in rapidly growing cities. In Vancouver, British Columbia, for instance, the City Council has recently approved the Broadway Plan, a rezoning initiative whose chief aim is to increase the supply of housing. Henriquez Partners Architects is designing Prototype (M5), a residential tower in this part of the city for the developer Westbank. As a result of the new zoning, the firm expects to be able to expand from the scheme’s current height of 21 stories to 25 stories, with about 20 percent of its approximately 210 apartments slated to rent at below-market rates. The building will have a concrete core, seven-ply CLT floor slabs, and steel for its vertical structure. “Timber columns would get too large at the base,” says Shawn Lapointe, Henriquez Partners principal. The hybrid strategy, combining low-carbon concrete, mass timber, and steel, will cut the structural system’s embodied carbon in half, compared to a more conventional frame.
Prototype (M5)’s high-performance facade, which invokes traditional basket-weaving techniques, will also incorporate wood. Its interlocking panels include a sheet of wood veneer laminated between glass sheets in order to protect it from the elements. The panels’ backup structure will be CLT, which the firm plans to expose on the apartment interiors, says Lapointe.
Some firms are working on concepts for using timber in buildings that aren’t just tall, but supertall (a supertall tower is one that is higher than 300 meters, or 984 feet). The Canadian practice DIALOG has created a theoretical scheme for a mixed-use supertall tower—105 stories high—with a patent-pending CLT-composite timber floor plate system to go along with it. Designed for Toronto, the tower has a so-called double-tube structural system with a concrete core and an external steel diagrid that widens at the base.
To reduce embodied carbon, DIALOG’s design uses mass timber, but only as part of the floor plate. The firm focused on this element because of studies that show floor systems are responsible for as much as 73 percent of a tall building’s environmental impact. A pure timber solution would be impractical, they say, since wood is less efficient structurally at greater heights, and the long column-to-column spans considered desirable in commercial buildings would be unachievable.
DIALOG’s concept, which it has dubbed the hybrid timber floor system, or HTFS, is a prefabricated composite panel, 40 feet by 10 feet, made of seven-ply CLT and post-tensioned concrete. According to the firm’s calculations, using this element to create a supertall tower’s floor slabs would result in a modest 9 percent reduction in embodied carbon compared to a baseline design for a 105-story traditional steel-and-concrete structure. If biogenic carbon is taken into account, however, the reduction would be 46 percent. “If the wood is harvested ecologically, the strategy offers an effective way to tie up carbon for as long as the building exists,” says Craig Applegath, founding partner in DIALOG’s Toronto office.
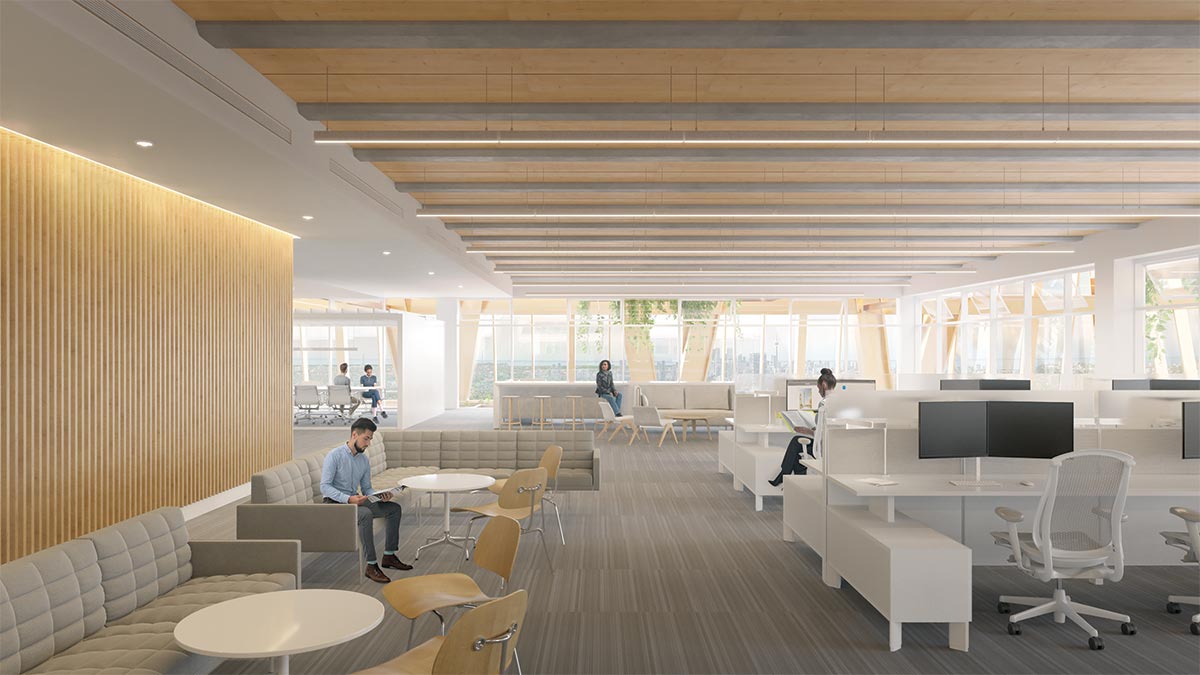
Photo courtesy of DIALOG
Dialog's floor plate system for supertall towers includes CLT panels, 10 by 40 feet, and post-tensioned cables within recessed reinforced-concrete bands. It would be capable of the long spans considered desirable in commercial towers.
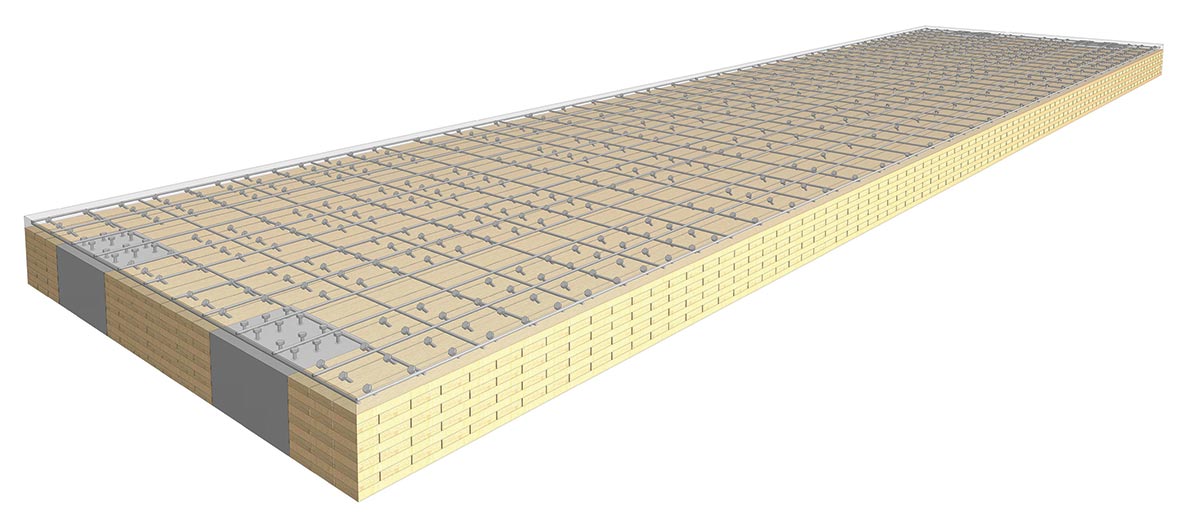
Photo courtesy of DIALOG
DIALOG'S floor plate system (above) for supertall towers includes CLT panels, 10 by 40 feet, and post-tensioned cables within recessed reinforced-concrete bands. It would be capable of the long spans considered desirable in commercial towers (top).
The contractor EllisDon, DIALOG’s partner, is currently testing the HTFS system at its modular-fabrication facility in Ontario. With the help of a grant from the Canadian government, sample panels are being assessed for properties that include the integrity of the bond between concrete and timber, loading capacity, the potential for creep (permanent deformation), and susceptibility to vibration. Lastly, the samples will be burned in an oven to determine charring rates and their resistance to fire.
With the aim of achieving net zero performance, DIALOG’s supertall combines a range of efficiency and energy-generation strategies, including a double skin, building-integrated photovoltaics, and thermal-energy storage, as well as some still exotic technologies, such as an algae bioreactor. The bioreactor would transform the CO2 produced by the tower’s gas-fired combined cooling, heating, and power trigeneration plant into algae, which could then be used as feedstock for products such as fertilizers, plastics, or pharmaceuticals. A similar system is currently being piloted at a Toronto power station, says Charles Marshall, a DIALOG sustainability engineering partner. “It is not so out there as to be pie in the sky,” he says.
With its range of accompanying technologies, DIALOG’s HTFS acknowledges that addressing the climate crisis will require a multipronged approach. Given the problem’s urgency, “we can’t afford to be purist about any one solution,” says Marshall. But mass timber, in not-so-tall, tall, and very tall buildings, could be a big part of the answer.
Supplemental Materials:
Craig Applegath, Cameron Veres, Thomas Wu. ““The Zero-Carbon Hybrid Future of Tall Timber.” CTBUH Research Paper, 2021.