View course on architecturalrecord.com »
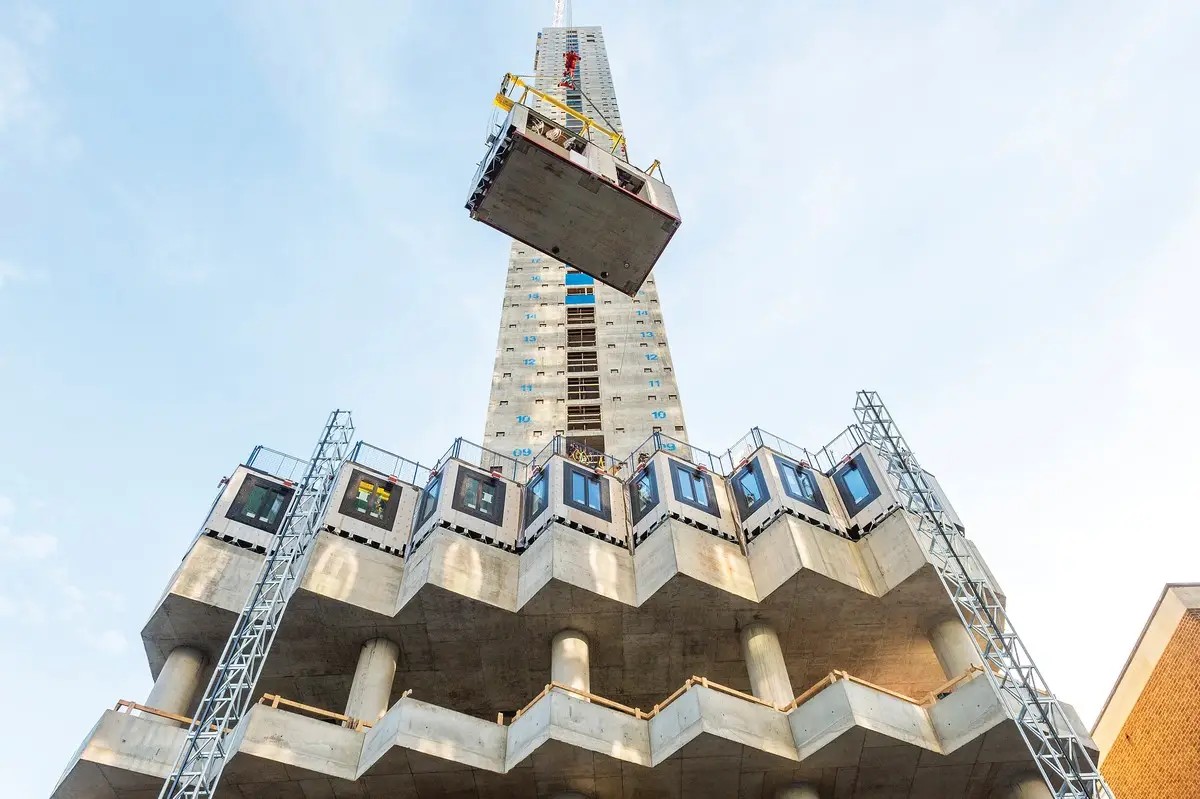
Photo © Emphasis Photography
College Road, London, by HTA Design.
This special section explores the latest in prefabrication. It highlights technological advances in residential modular construction, both flat-pack and volumetric. It examines structural innovations, like a low-embodiedcarbon concrete floor system, feats of infrastructural engineering, easy-to-build pop-up retail and public amenities, and novel accessory dwelling units.
Select an article to read more.
Click course title to be directed to architecturalrecord.com »
Stack ’em up!
BY MATTHEW MARANI
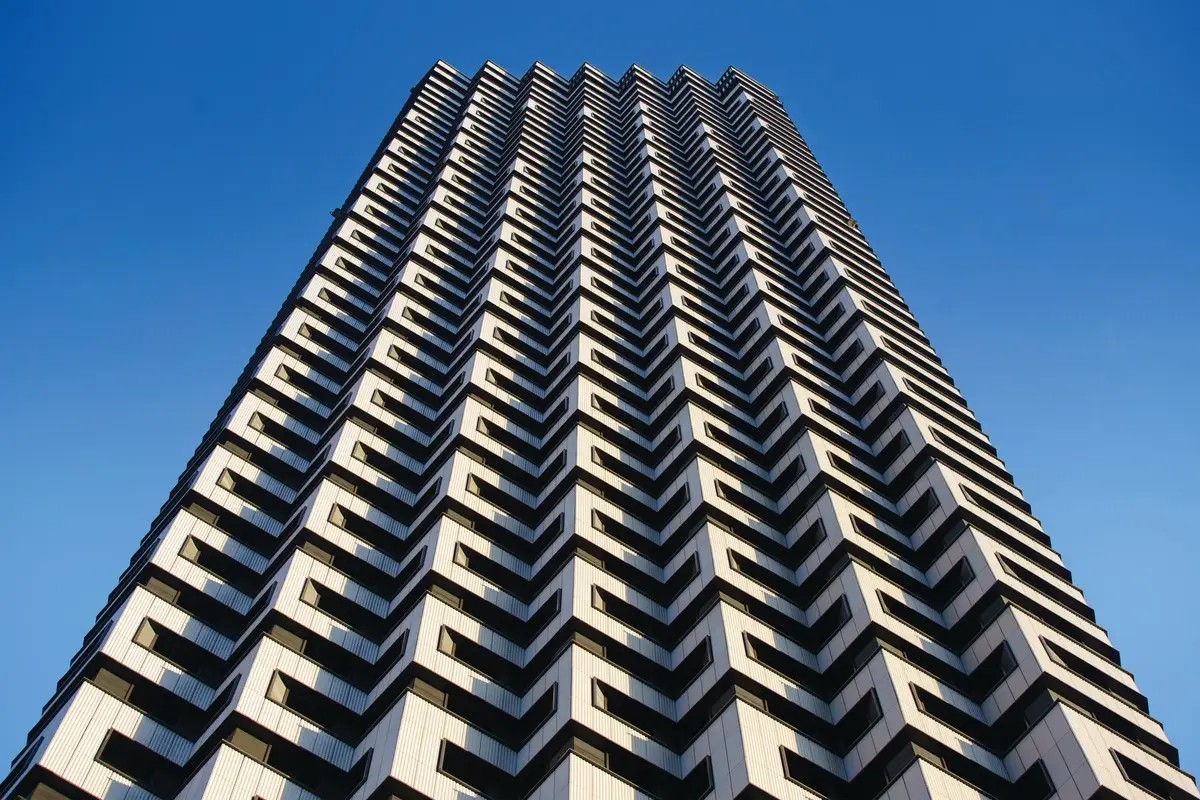
Photo © Simon Toplis
College Road’s modules are stacked to achieve a chevron-like massing.
A new generation of projects could reshape the residential-construction market
THE CONSTRUCTION industry is known for its slim profit margins and erratic market cycles—this despite accounting for $13 trillion in spending worldwide in 2023, or approximately 7 percent of global gross domestic product. Many of the sector’s inefficiencies stem from low gains in productivity, which, according to a report released by McKinsey & Company in August 2024, lags that of other industries. The construction sector saw just a 10 percent improvement in productivity between 2000 and 2022, compared to a 50 percent gain across the entire economy and 90 percent within the manufacturing sector.
Modular construction has long promised to address industry roadblocks such as a decline in skilled workers and the lack of standardization from one project to the next. Successive high-profile construction startups, like Katerra, which filed for bankruptcy in 2021, have seemingly been unable to crack the code of long-term viability. But the fact remains, modular construction—with components manufactured within controlled settings and shipped as either flat-pack assemblies (think IKEA, but with building systems and components), or volumetric forms (fully integrated stacked boxes)—can offer a suite of advantages when compared to traditional modes of building, especially in residential construction.
GOTHIC TECH
BY ANDREW AYERS
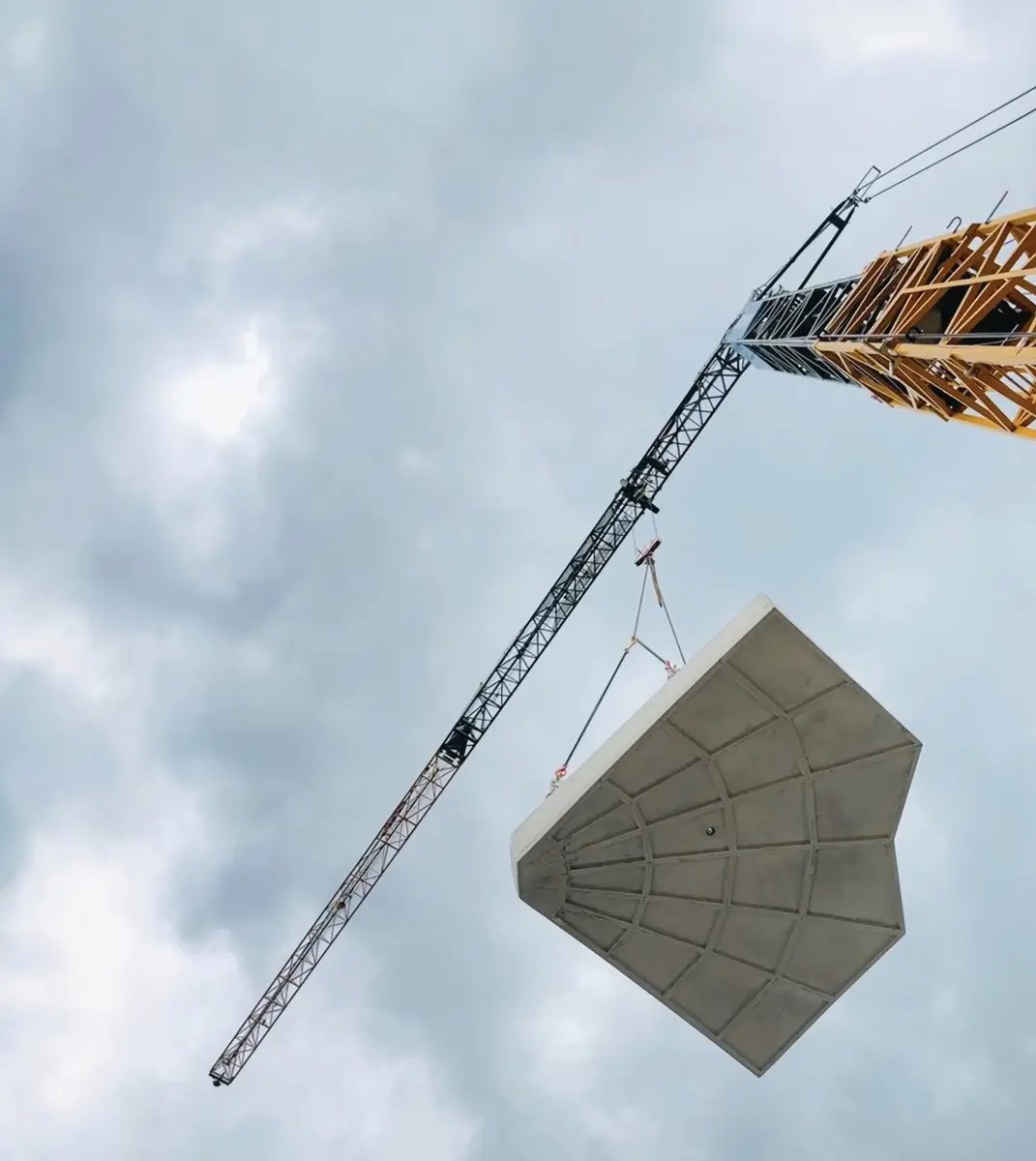
Photo © Philippe Block
CreaTower I, in Switzerland, will be the first new building to use Vaulted’s technology (above). The interior will feature double-height spaces that could be filled in at a later date (below).
In Switzerland, a fully demountable lower-carbon concrete floor system harnesses an age-old technique
IMAGINE fully demountable, prefabricatedconcrete floors that reduce emissions by two-thirds and are beautiful to boot. This is what Swiss company Vaulted claims to deliver with its Rippmann Floor System (RFS), named for the late Matthias Rippmann, a member of the Block Research Group (BRG) at ETH Zurich, Switzerland’s prestigious polytechnic university.
The RFS uses concrete only “where it wants to be in compression,” says the company. Unlike the Gothic technology on which they are based, Vaulted’s RFS shells are stiffened by ribs located on their hidden, upper surface, with the lines of force inscribed on their visible face underneath. As currently available, they come in two versions: double span (RFS-D) and single span (RFS-S). While the RFS-D modules fit together to form what resembles a classic quadripartite vault, which is to say curved in two directions and supported at the corners of its square perimeter, RFS-S is curved in just one direction, its components forming a barrel vault that must be supported along its two edges. This dual offer, says Francesco Ranaudo, Vaulted’s CEO, responds to RFS-D’s limited flexibility with respect to internal partitions, since running them through the middle of the vault is inelegant; with its narrower spans, RFS-S is better suited to housing, for example, which generally requires smaller rooms than offices. “We’re really going back to a tectonic appreciation of architecture,” comments Ranaudo.
A Pad in a Pod
BY RUSSELL FORTMEYER
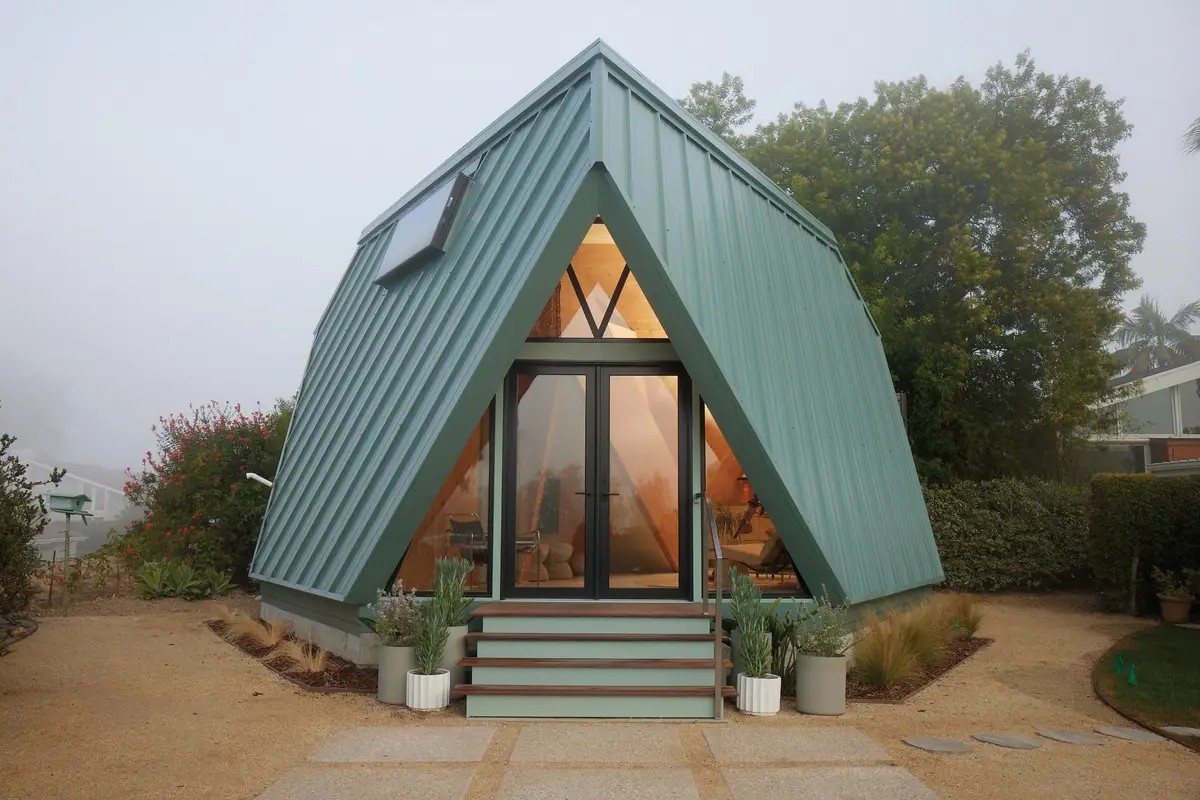
Photo © Andy Cross and Cody Cloud
The first Polyhaus.
A tiny mass-timber structure offers a possible solution to a very big housing problem.
UNLIKE MANY of the prefabricated accessory dwelling units (ADUs) flooding the California market, the Polyhaus does not fit on a flatbed truck fully assembled. The polyhedron- shaped house was conceived by Daniel López-Pérez as a solution for expediently producing quality housing at scale in the smallest footprint possible, rather than as a rectangular box for ease of shipping. With his wife and Polyhaus LLC cofounder, Celine Vargas, López-Pérez built the first two-story, 540-square-foot proof-of-concept in 2024 in the backyard of the couple’s 1962 Palmer & Krisel house, in San Diego.
López-Pérez, who is professor and architecture- program director at the University of San Diego, developed the Polyhaus system by starting with a simple cube and then repeatedly truncating the edges until he optimized the form for the largest volume and smallest footprint. The 440-square-foot ground floor includes a living room, kitchen, bathroom, and nook for a desk and washer/dryer, with the bedroom on the 100-square-foot mezzanine. “Polyhaus is a design and constructiontechnology company,” says López-Pérez, which he contrasts to ADU manufacturers that provide a built product. The couple view their 17-foot, 4-inch-tall Polyhaus as a research- and-development investment to bring the timber innovations revolutionizing largescale construction down to smaller scales.
TRANSPORT A POTTY
BY PANSY SCHULMAN
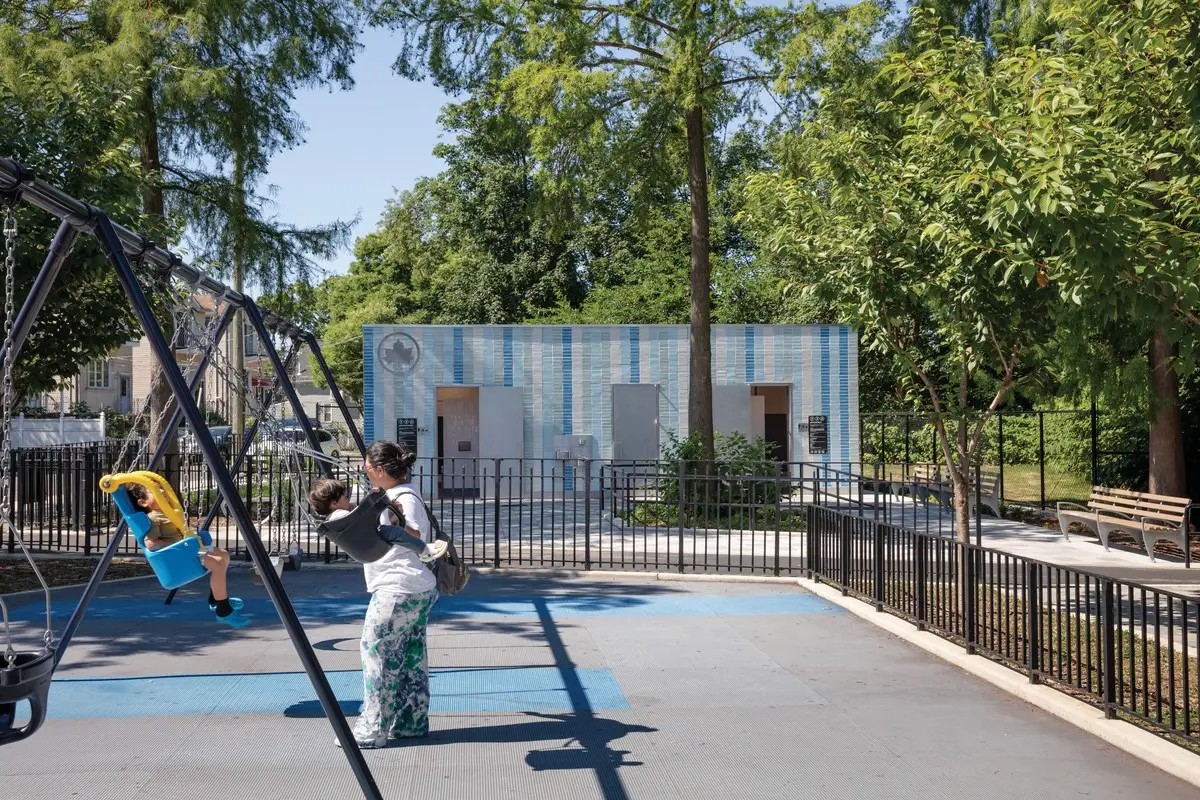
Photo © Ty Cole
Lopez Playground Restroom.
New York’s first modular public restroom prioritizes speed, budget, and easy upkeep.
A QUIET residential block on Staten Island is the unlikely location of a potentially gamechanging project: the first modularly constructed public bathroom in New York. The modest structure, designed by 1100 Architect, was completed last winter and has been a boon for visitors at Lopez Playground, which previously had no public facilities within walking distance.
Composed of three steel-frame modules, the restroom is enclosed with a facade of structural glazed tile, making it durable, low-maintenance, and vandal-resistant. At 34 feet long and 20 feet wide, the design aligns with dimension standards for New York City Department of Parks & Recreation (NYC Parks), and consists of separate men’s and women’s toilets flanking a mechanical room Transport a pott y New York’s first modular public restroom prioritizes speed, budget, and easy upkeep. BY PANSY SCHULMAN and employee storage space. Small skylights and generous windows, treated with a translucent film for privacy, bring natural light inside the three-stall restrooms. The architects also incorporated a green roof, adding a green touch to the ultra-pragmatic program.