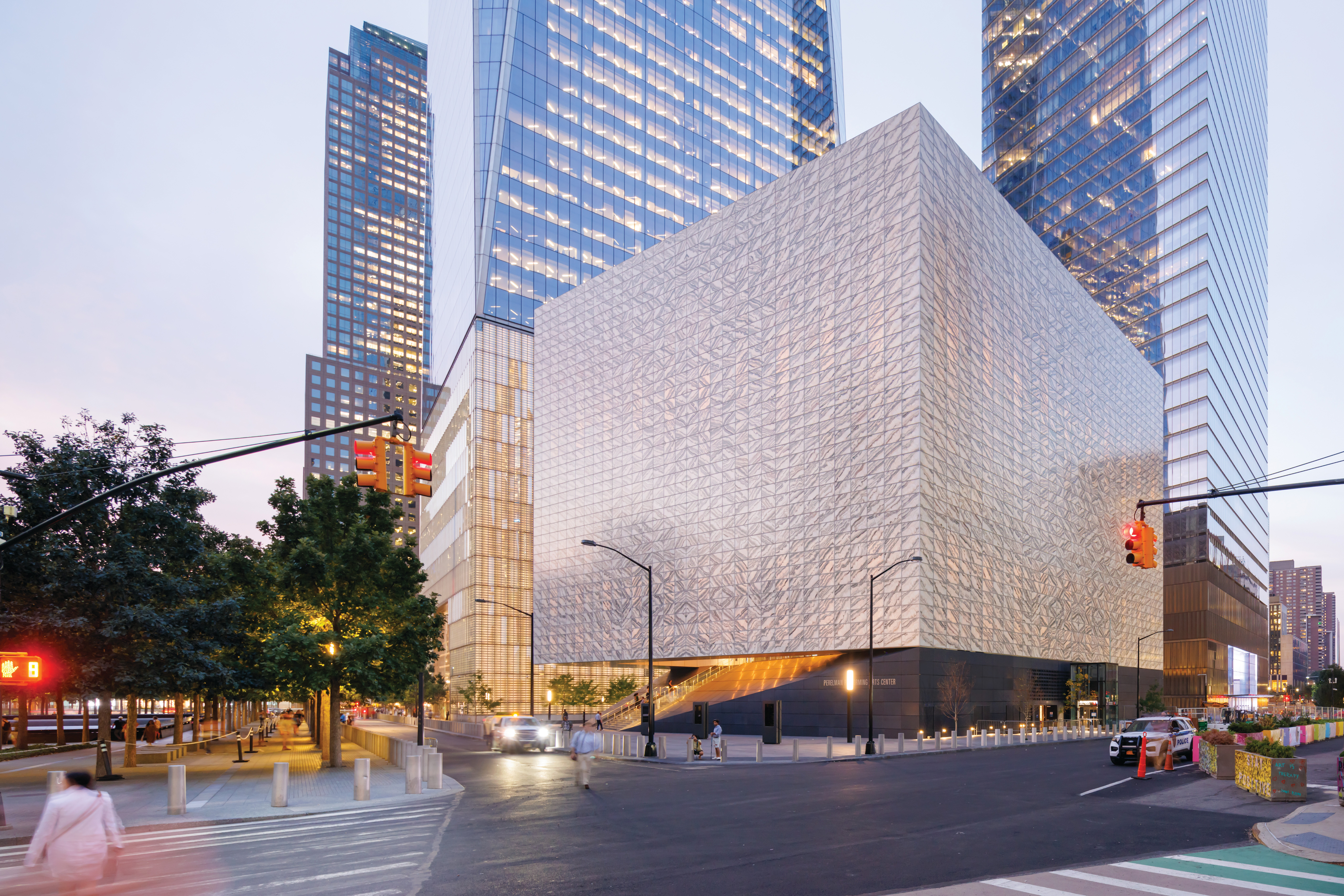
Photo © Iwan Baan
Perelman Performing Arts Center in New York City, designed by REX.
Working architects understand that the media image of an architect as a solitary genius who hands down his vision to underlings for execution—the latest iterations of which are the characters Cesar Catalina in Francis Ford Coppola’s Megalopolis (2024) and László Tóth in Brady Corbet’s The Brutalist (2024)—is mythical. The process that translates design concepts into successful buildings has many fathers (and, it shouldn’t need saying, mothers). Yet the idea that information flows entirely in one direction from design to construction phases remains prevalent, though nearly as unrealistic as the films.
Architects, engineers, consultants, and installation specialists agree on the essential metrics for facade performance: thermal control, occupants’ comfort and utility, energy and resource management, efficiency in the construction process, and the economic expressions of all these values. For professionals who have extensive experience with curtain-wall systems, a working approach involving purposeful communication in multiple directions is also crucial to yielding the best results. The experience of the participants at the later stages of construction is an essential resource for architects working at the initial stages to draw on, whether that communication is formally encoded in design-assist arrangements (AIA; Koger) or emerges organically from trusted relationships. When the expertise of participants in product selection, logistics, and installation informs the expertise of design conceptualizers, everyone involved benefits.
“The idea of a curtain wall is a very abstract framework,” says Sameer Kumar, AIA, NOMA, founder and principal at the New York-based enclosure consultancy firm Techne. “But to make it appropriate for the project, one will have to think about not only what the architectural design is trying to do, but also where it is going to be built; who’s going to be potentially asked to design, fabricate, and install it; who is the client who’s going to own it and pay for it—what are their aspirations, in terms of cost appetite or in terms of its iconic nature; and what all of them are seeking out of it. So there are many forces that shape the design that are beyond the architect’s intent. The architect’s intent is of course primary, but there are many forces outside the purview of the architects that shape design.”
Building a facade correctly, on budget, and on schedule “begins at the choice of system,” Kumar continues: a window wall, a punched window, a true curtain wall, or a hybrid system. “A part of logistical shaping of the building is related to the ease of installation. Gradually we help the design team understand whether the choice is correct by testing that system against the various requirements of the project. It could be the thermal requirement or the environmental-performance requirement, and the system will succeed or fail when tested against the requirements. And then if it fails, you say ‘Okay, we need a different system,’ or ‘We need to improve the system.’”
It is rare, Kumar finds, for an architect’s design to be so overcomplicated that problems arise onsite; potential problems usually appear earlier, and mechanisms exist to catch them well before construction begins. “There are many layers of safety net that exist within our method of working,” with legal relationships among the architect, owner, contractors, and subcontractors giving all parties the opportunity to review the drawing set and ensure that a system can be built or appropriately modified.
“It is okay that at every stage, new knowledge comes in, and it makes the project better,” Kumar continues; “it doesn’t have to be that the architect has to have thought of everything. But at the same time, there is a problem if the architect imagined something, put it down, and then the contractor came and bought it without asking questions, set a price to it, and now they say, ‘Actually, we cannot build it, because now the price is going to change.’ If the process works correctly, then we should never face that situation.”
Considering “all the goals of the owner, the architect, the designers, the consultants, the contractors, the subcontractors, you can’t just go down one path,” says Michael Haber, managing partner at W&W Glass, a curtain-wall system contractor based in Nanuet, N.Y. “You need to decide to bring everybody together and have a consensus on what the building wants to look like, how it has to perform, and how we’re actually going to build this job. And if you leave one of those out, you leave yourself open for some problems down the road.”
“There are many manufacturers and fabricators that can produce curtain walls and windows,” Haber continues. “There are a multitude of glass manufacturers that can make insulated glass units. But the real trick is to take that knowledge and then combine it with how we actually get this job built, with logistics. [For] a big curtain-wall section or a big window: how do we actually get it up in the building? How do we get into the job site? How do we move it around? So from an installation perspective, that’s the one thing I think that most designers miss the boat on: the logistics component, which eventually comes back and sometimes changes the design.”
Reining in certain architectural flourishes or experiments is part of the process, regardless of which party pulls the reins. “In the world of custom curtain wall, having fewer wall types on a project makes a difference, because the contractor needs to have a certain amount of area to make the final design and engineering process feasible financially,” says principal Areta Pawlynsky, AIA, of the envelope and curtain-wall consulting firm Heintges. “Thinking about realistic unit sizes shapes the architects’ layout of modulation. These are components coming from a factory on a truck, and you’re trying to get as many of these on a truck at one time, and so respecting those parameters makes sense.”
Her colleague Karen Brandt, AIA, principal in charge of Heintges’s San Francisco office, recalls instances where enhanced articulation through introducing depth and changes of plane looks appealing at early design stages but proves difficult to implement. “Maybe as a reaction to the taut glass tower,” she says, “either the client or the architect or both, or the community, wants to have a building with more in-and-out shadow play, and to contextualize it, maybe to break down the massing.” Vertical recesses and horizontal setbacks, “from an air- and weathertight perspective and also a constructability perspective, are very different because of the way they deal with precipitation, runoff, and gravity.”
For example, a recessed balcony running around a building may include design for an exterior space above occupiable space that essentially turns a facade sometimes into a “mini-roof,” says Brandt. “This can become really challenging when we’re trying to utilize a unitized cladding system, because those joints from one unit to the next are terrific in terms of their ability to accommodate movement, and when they’re vertical they’re using gravity to drain water from the system,” she explains. “But when those moving curtain-wall-unit joints become a roof, it becomes a lot harder to waterproof because the units are moving and accommodating building structural movement. The curtain walls are not as good with horizontal joints as they are with vertical joints.” Designs that appear advantageous from the perspective of rentable square footage relative to thermal envelope and energy-code requirements may create technical challenges in managing air, water, and gravity. The consultant’s function, she says, is that “if we’re involved in a project, we’ll get ahead of that before it can metamorphosize from maybe a bad idea into a bid document.”
Planning with ease of construction in mind can also advance the aim of controlling the carbon footprint of a project, Pawlynsky observes. “With the increasing awareness of embodied carbon and how more materials affect that, you’re going for one big move as opposed to multiple—you’re taking the opportunity to shape building enclosures in a more simple, repetitive way. And so there ends up being less framing, fewer caps, fewer fins,” leading to generally simpler detailing and often material savings.
“Right now, you’re seeing a lot of changes in the marketplace, particularly New York and Boston and the East Coast, in which the energy codes are changing rather rapidly in a concise framework,” notes facades principal John Ivanoff of the international engineering firm Buro Happold. “Maybe 20 years ago, they’d change every 20 years, and now they’re changing every three years.” This puts pressure on contractors to ensure systems are in compliance. “Particularly within that curtain wall, the assembly U value becomes really critical, because it is a driving factor for the performance of the facade and ensuring that thermal breaks, the mullions, and the shadow box are all actually calculated and engineered correctly. At the same time, there’s this push and pull between energy-code initiatives asking for more insulation and clients understanding the embodied carbon of that facade system. How much aluminum is there? How much insulation is there? You need to strike the right balance of saying that you need X amount of insulation and understanding that it has a performative benefit on the overall energy savings, while not just simply increasing the embodied carbon.”
Minimizing material quantities can entail evaluating cantilever conditions, Ivanoff continues, or “adjusting anchor points to ensure that you’re having these incremental savings. And on a facade system, you might be getting incremental savings on a piece of aluminum, but when you look at the whole building and you actually start to add that up, it actually starts to make a bigger impact. And if each team has that goal, then if you look at the whole building and every team incrementally did their job well, then it was a success.” The calculations of facade consultants thus help harmonize the aims of environmental performance, design, constructability, code compliance, and cost control.
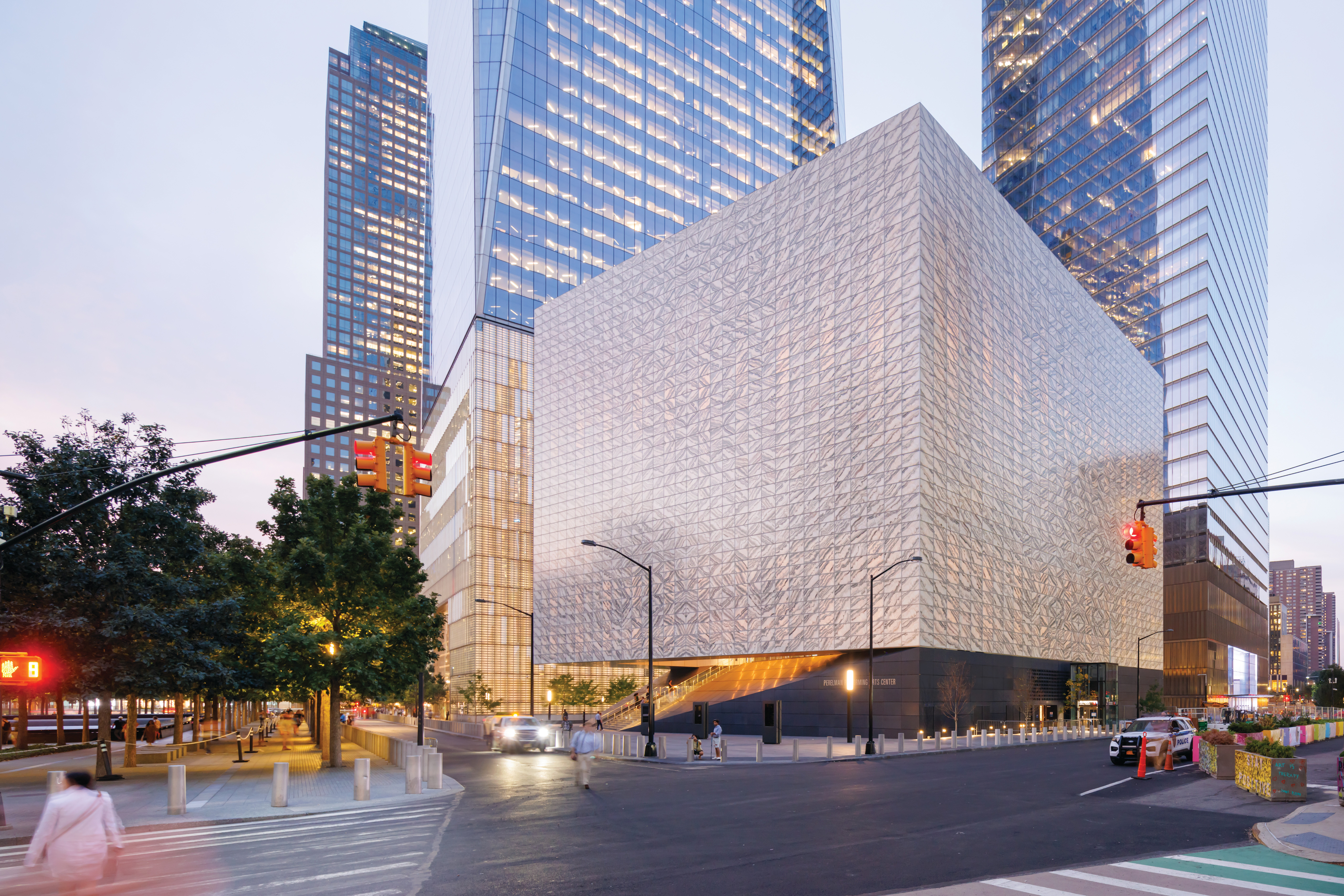
Photo © Iwan Baan
Perelman Performing Arts Center in New York City, designed by REX.
Working architects understand that the media image of an architect as a solitary genius who hands down his vision to underlings for execution—the latest iterations of which are the characters Cesar Catalina in Francis Ford Coppola’s Megalopolis (2024) and László Tóth in Brady Corbet’s The Brutalist (2024)—is mythical. The process that translates design concepts into successful buildings has many fathers (and, it shouldn’t need saying, mothers). Yet the idea that information flows entirely in one direction from design to construction phases remains prevalent, though nearly as unrealistic as the films.
Architects, engineers, consultants, and installation specialists agree on the essential metrics for facade performance: thermal control, occupants’ comfort and utility, energy and resource management, efficiency in the construction process, and the economic expressions of all these values. For professionals who have extensive experience with curtain-wall systems, a working approach involving purposeful communication in multiple directions is also crucial to yielding the best results. The experience of the participants at the later stages of construction is an essential resource for architects working at the initial stages to draw on, whether that communication is formally encoded in design-assist arrangements (AIA; Koger) or emerges organically from trusted relationships. When the expertise of participants in product selection, logistics, and installation informs the expertise of design conceptualizers, everyone involved benefits.
“The idea of a curtain wall is a very abstract framework,” says Sameer Kumar, AIA, NOMA, founder and principal at the New York-based enclosure consultancy firm Techne. “But to make it appropriate for the project, one will have to think about not only what the architectural design is trying to do, but also where it is going to be built; who’s going to be potentially asked to design, fabricate, and install it; who is the client who’s going to own it and pay for it—what are their aspirations, in terms of cost appetite or in terms of its iconic nature; and what all of them are seeking out of it. So there are many forces that shape the design that are beyond the architect’s intent. The architect’s intent is of course primary, but there are many forces outside the purview of the architects that shape design.”
Building a facade correctly, on budget, and on schedule “begins at the choice of system,” Kumar continues: a window wall, a punched window, a true curtain wall, or a hybrid system. “A part of logistical shaping of the building is related to the ease of installation. Gradually we help the design team understand whether the choice is correct by testing that system against the various requirements of the project. It could be the thermal requirement or the environmental-performance requirement, and the system will succeed or fail when tested against the requirements. And then if it fails, you say ‘Okay, we need a different system,’ or ‘We need to improve the system.’”
It is rare, Kumar finds, for an architect’s design to be so overcomplicated that problems arise onsite; potential problems usually appear earlier, and mechanisms exist to catch them well before construction begins. “There are many layers of safety net that exist within our method of working,” with legal relationships among the architect, owner, contractors, and subcontractors giving all parties the opportunity to review the drawing set and ensure that a system can be built or appropriately modified.
“It is okay that at every stage, new knowledge comes in, and it makes the project better,” Kumar continues; “it doesn’t have to be that the architect has to have thought of everything. But at the same time, there is a problem if the architect imagined something, put it down, and then the contractor came and bought it without asking questions, set a price to it, and now they say, ‘Actually, we cannot build it, because now the price is going to change.’ If the process works correctly, then we should never face that situation.”
Considering “all the goals of the owner, the architect, the designers, the consultants, the contractors, the subcontractors, you can’t just go down one path,” says Michael Haber, managing partner at W&W Glass, a curtain-wall system contractor based in Nanuet, N.Y. “You need to decide to bring everybody together and have a consensus on what the building wants to look like, how it has to perform, and how we’re actually going to build this job. And if you leave one of those out, you leave yourself open for some problems down the road.”
“There are many manufacturers and fabricators that can produce curtain walls and windows,” Haber continues. “There are a multitude of glass manufacturers that can make insulated glass units. But the real trick is to take that knowledge and then combine it with how we actually get this job built, with logistics. [For] a big curtain-wall section or a big window: how do we actually get it up in the building? How do we get into the job site? How do we move it around? So from an installation perspective, that’s the one thing I think that most designers miss the boat on: the logistics component, which eventually comes back and sometimes changes the design.”
Reining in certain architectural flourishes or experiments is part of the process, regardless of which party pulls the reins. “In the world of custom curtain wall, having fewer wall types on a project makes a difference, because the contractor needs to have a certain amount of area to make the final design and engineering process feasible financially,” says principal Areta Pawlynsky, AIA, of the envelope and curtain-wall consulting firm Heintges. “Thinking about realistic unit sizes shapes the architects’ layout of modulation. These are components coming from a factory on a truck, and you’re trying to get as many of these on a truck at one time, and so respecting those parameters makes sense.”
Her colleague Karen Brandt, AIA, principal in charge of Heintges’s San Francisco office, recalls instances where enhanced articulation through introducing depth and changes of plane looks appealing at early design stages but proves difficult to implement. “Maybe as a reaction to the taut glass tower,” she says, “either the client or the architect or both, or the community, wants to have a building with more in-and-out shadow play, and to contextualize it, maybe to break down the massing.” Vertical recesses and horizontal setbacks, “from an air- and weathertight perspective and also a constructability perspective, are very different because of the way they deal with precipitation, runoff, and gravity.”
For example, a recessed balcony running around a building may include design for an exterior space above occupiable space that essentially turns a facade sometimes into a “mini-roof,” says Brandt. “This can become really challenging when we’re trying to utilize a unitized cladding system, because those joints from one unit to the next are terrific in terms of their ability to accommodate movement, and when they’re vertical they’re using gravity to drain water from the system,” she explains. “But when those moving curtain-wall-unit joints become a roof, it becomes a lot harder to waterproof because the units are moving and accommodating building structural movement. The curtain walls are not as good with horizontal joints as they are with vertical joints.” Designs that appear advantageous from the perspective of rentable square footage relative to thermal envelope and energy-code requirements may create technical challenges in managing air, water, and gravity. The consultant’s function, she says, is that “if we’re involved in a project, we’ll get ahead of that before it can metamorphosize from maybe a bad idea into a bid document.”
Planning with ease of construction in mind can also advance the aim of controlling the carbon footprint of a project, Pawlynsky observes. “With the increasing awareness of embodied carbon and how more materials affect that, you’re going for one big move as opposed to multiple—you’re taking the opportunity to shape building enclosures in a more simple, repetitive way. And so there ends up being less framing, fewer caps, fewer fins,” leading to generally simpler detailing and often material savings.
“Right now, you’re seeing a lot of changes in the marketplace, particularly New York and Boston and the East Coast, in which the energy codes are changing rather rapidly in a concise framework,” notes facades principal John Ivanoff of the international engineering firm Buro Happold. “Maybe 20 years ago, they’d change every 20 years, and now they’re changing every three years.” This puts pressure on contractors to ensure systems are in compliance. “Particularly within that curtain wall, the assembly U value becomes really critical, because it is a driving factor for the performance of the facade and ensuring that thermal breaks, the mullions, and the shadow box are all actually calculated and engineered correctly. At the same time, there’s this push and pull between energy-code initiatives asking for more insulation and clients understanding the embodied carbon of that facade system. How much aluminum is there? How much insulation is there? You need to strike the right balance of saying that you need X amount of insulation and understanding that it has a performative benefit on the overall energy savings, while not just simply increasing the embodied carbon.”
Minimizing material quantities can entail evaluating cantilever conditions, Ivanoff continues, or “adjusting anchor points to ensure that you’re having these incremental savings. And on a facade system, you might be getting incremental savings on a piece of aluminum, but when you look at the whole building and you actually start to add that up, it actually starts to make a bigger impact. And if each team has that goal, then if you look at the whole building and every team incrementally did their job well, then it was a success.” The calculations of facade consultants thus help harmonize the aims of environmental performance, design, constructability, code compliance, and cost control.
Time and Space Management
Vishwadeep Deo, associate principal at Thornton Tomasetti, offers a set of points to consider when designing facade components with logistics in mind: “The panel sizes, the dimensions, geometry, and actual weight of the panel; how it could be brought to site, taken off the trucks, and lifted and hoisted in position. That whole mechanism to pick the panel up and install it in its right place needs to be pre-planned. And in most cases, it has, but in certain special cases there will be some limitations in terms of the size, the access to the site, and the structure we are attaching to. It’s a matter of information, and at the end of the day, if the series of information can then drive the design and better inform the design in the early processes, you will have less friction when it actually hits the site for installation.”
Haber breaks the installation process down into “buckets” or procedural categories based on building scale and location. On lower-rise buildings, often outside dense urban settings, “we can get a small crane around the perimeter of the building, where we don’t have to actually load the curtain-wall units or window units into the building and set them with [mobile hoists] and crab units or monorails, and we can certainly stay on the outside of the building, that allows the designers to get much bigger sections of curtain wall where they come on a flatbed truck. We lift them with a crane, put them in place from the outside, and we never have to go inside the building. So those types of applications allow designers to have much bigger sections of curtain-wall units.”
On high-rise projects, Haber says, when closing down vehicular traffic for a street crane isn’t possible, “we look to the construction manager, often with the hoisting companies, to design the outside elevators and hoisting systems to either accommodate larger units or, if we have certain restrictions where the elevators might come out too far in the street and we can’t use an oversized hoist, then we’ve got to break the curtain-wall units down to fit into smaller hoists.” When access to use a mobile hoist is impossible, as in elevator areas or around core walls or shear walls, a monorail system on the exterior can support either scaffold systems for manpower or chain falls that hold lifting mechanisms for curtain wall panels.
The “least likely and less preferred method,” in Haber’s view, is to use a tower crane to set the curtain wall, not only because of weather and other unpredictable factors, but because of the sequence of operations. Depending on the building size, a tower crane is often taken down when the structural component (either steel or concrete) is done and HVAC equipment is lifted and installed, before curtain-wall installation customarily begins. “While that tower crane is coming down, typically we’re coming up with curtain wall. So unless we decide to set curtain wall out of sequence, which presents different detailing questions–in other words, set the higher units or the oversized units with the tower crane up in the building, the tower crane goes away, and then we continue setting the curtain wall–then we’ve got a situation.”
The implications are clear for the choice of curtain-wall systems: Haber recommends choosing dimensions that fit the available exterior hoists. “The typical hoist sizes don’t exceed 17' in length,” he notes, “so if you can keep your curtain-wall units down to 16' of curtain-wall unit itself, and allow a little bit of extra room for packing and crating and whatnot, that will typically fit into a construction hoist in New York City.” Widths should be in the 5' to 6' range. “Curtain-wall units are typically shipped on edge on their landscape orientation, so you have three to four curtain-wall units in a crate. The crate’s about 4' wide. If the curtain-wall unit is 5' wide, the crate is about 6' wide on edge, so it’s 6' tall, and if the curtain-wall units are 16' long, the crate will be 17' long. So a 4' by 6' by 17' crate fits nicely in the larger hoists in the city. There are some oversized hoists that we’ve seen that go into 21' range, but that’s not typical.” The position of the hoist motor can take up some of the width of the hoist car, he adds, “but normally you’re dealing in the 4' to 5' width range. The door could be anywhere; it’s typically from 7' to 8' tall.”
Haber has observed that European and U.S. curtain-wall systems have differences that may require different handling. “The European products, for us anyway, were the flavor of the month for a while,” he notes, “and then it seems that due to different political issues or whatever might be going on in the world, owners and some developers wanted to have more control over their product and keep it to basically North American-made systems. That’s been a moving target for us, depending on the owner and developer.” When clients prefer glazing from overseas manufacturers for a range of reasons, including differences in thickness or flatness and coating processes “some of the European systems are a little more complicated to install,” he notes. “They take a little bit more time; a little bit more finesse is needed.” Even with well-trained union personnel who have installed domestic systems for 20 or 30 years, he has noticed, “when you throw a European system at them, sometimes it’s a little bit of a learning curve.”
Pawlynsky notes that since Heintges began operating in 1989, insulating glass units have grown larger, initially driven by the capacity of European glass fabricators and now applicable to U.S. firms as well. “If you want to tie embodied carbon into that,” she adds, “when we think about the least amount of material that could be used, we’re talking about leveraging: finding that sweet spot in the largest unit that can be shipped and then hoisted, because with the larger ones, they need to find ways to lift those without causing damage.” Particularly in cities where crane time is at a premium, she notes, loading speed (for curtain-wall units and every other component) is a critical variable in job planning, she says; at sites in less dense areas, such as university campus projects, megapanels that would be unwieldy in Manhattan or similar cities are more of an option.
Brandt highlights several other variables affecting that dimensional sweet spot: program, interior layout, and structural system as well as transport. “A 10' would be ideal from a commercial office perspective, because it’s two bays, and it fits with the furniture layout,” she says. “The typical office 5' curtain wall makes a lot of sense, because it’s tied to a furniture grid. We found for labs that an 11' bay, or 20', and a 22' spacing is more on par for what happens.” Planning how to move the units, Brandt asks, involves questions like “Will the floors be stocked with curtain-wall units using something like a Preston deck [a retractable loading platform system], where they’re using the tower crane to bring in crates, or will they be using the hoist to fit in the units? On every recent project I’ve worked on, the size of the hoist and what size unit will fit in the hoist has been a really critical part of the conversation about the ideal unit size.”
Questions of units’ size take on extra complexity at sites where seismic forces are a major concern. In such areas, Haber comments, “you’re going to want to design the curtain-wall system to make sure that it accounts for certain movements, which typically means that your stack joints become a little bigger. Architects love to have very slim stack-joint sizes, but depending on the movements of these buildings, some of those stack joints can get to be larger than they might like to see, but unfortunately, that’s what we need to use.”
Brandt’s experience in high and low seismic-risk areas informs her views: “Early on, there is often a discussion where the structural engineer is asking for input on the approximate weight per square foot of the facade, and curtain-wall units [of] glass and aluminum are always going to be the lightest compared to GFRC [glass fiber-reinforced concrete] or precast,” she says. “That’s a question that comes up in these early design phases of thinking about the efficiency or optimization of the facade, more than what I had seen when I worked on East Coast projects. That question about weight per square foot comes up earlier and is an important discussion for seismic; also, depending on how stiff the structure is, the orientation of unit joints. If you have very tall floors, that means that the seismic joint needs to get bigger from one unit to the next, because the seismic movement is a function of the height, and that’s what you have to accommodate in the joints. So that is also a discussion that I think happens earlier than on the East Coast.
“Even in something like anchor design,” she continues, “with curtain-wall anchors on the East Coast, pocketing them and hiding them in the slab—basically making a depression in the slab, casting a piece of essentially foam as a blockout, and putting the curtain-wall anchor in later—was fairly normative on the East Coast. On the West Coast, it is frowned upon in many ways, and sometimes it’s because we use so much more prestressed concrete in structures than on the East Coast.... Almost any project with concrete, almost all residential that we see on the West Coast, all have post-tensioned slabs, and the location of those tendons has a big impact on anchors. And putting pocketed anchors when you have tendons not only increases the complexity, but sometimes it just can’t be fit into the design. So the post-tensioned slab in concrete is coming from seismic behavior, and it’s the preferred structural methodology for residential out here. That’s another early-phase conversation that then can impact the location of the anchor, the size of the anchor, and then where the stack joint is on the curtain wall itself.” A further early discussion that can prevent painful scenarios, she says, involves the distances between the edge of a slab, the exterior face of the facade, and the center line of any columns near a building’s perimeter, establishing a zone for placing curtain-wall anchors, with enough space to install units and seals and avoid a “pivot to an edge-of-slab anchor,” compromising consistency around the perimeter. “Having a very clear discussion about that zone between structure and the edge of slab and the facade is invaluable,” Brandt says, to avoid repeating layout work several months into schematic design. “For the facade to have to push the columns in, that’s the tail wagging the dog.”
Tension between the design objectives of slender profiles, elegant surfaces, and minimal visible support hardware, on the one hand, and the physical properties of materials on the other can call for close and early communication within design/construction teams. At New York City’s two major airports, Haber points out, where unusually large curtain-wall units and a desire for clear sightlines posed special challenges, W&W joined the teams early in design-assist mode and helped achieve impressive results.
Fear Not the Obvious Questions
Christoph Timm, technical design principal at Skidmore Owings + Merrill, raises certain practical points that can prevent head-slapping regrets after construction documentation reaches the job site. Since the firm has an in-house Enclosure Group as well as specialists in structural engineering, thermal modeling, and other relevant disciplines, he says, the combination of internal consultations and on-site training helps SOM architects internalize the overarching principle that “you have to be able to install what you design.”
One standby is what Timm calls “the fat finger test”: how do the dimensions of curtain-wall components and the spaces that personnel must reach into during installation match up with the hands that will do the reaching? “Installers usually are not the piano players of the world,” he observes; “these are hands that can operate big, heavy equipment.” Transportation of building components requires attention, he adds: “Can you use a crane? Can you use a hoist? What’s the site access? How many loading docks do you have? How can you get the jumbo panels that you’re planning into the city?” SOM raises these topics with checklists and sends its personnel to complicated projects to “observe and learn by doing; learn by seeing.”
The details of facades look different from outside and inside, Timm notes, as well as from a distance and from the closer vantage points available on terraces and balconies. “If you have access [via] a terrace, then make sure you treat it as if this was an interior condition, where you have up-close, hands-on experience, where you can touch the material and can feel it.” Designers should avoid cavities where screws, bolts, fasteners, and other unsightly hardware are visible from the back of a curtain wall, he adds; “be mindful of how a facade is experienced up close and/or from a distance.... If you have a visual connection into a reveal, make sure that you paint it all black so it recedes in the background, for example. Be mindful where the eye can go: not just the hands, but also the eyes.”
Attention to component dimensions is a high priority in preventing installation complications, particularly at transitions between trades. “Understand tolerances,” Timm advises, “tolerances of your trade, but also tolerances of the other trade: what the capabilities are of the industry, like concrete or steel, and design toward that.” This is particularly valuable in the emerging market of retrofits and reskinning projects, where new components connect with old. “You’ve got to have plenty of tolerances built into your details [so] that you can accommodate a structure that’s moved over 50 or 60 years [and was] maybe not built to tolerances of today’s standards.” Built-in flexibility to accommodate site conditions is a cardinal principle; “if your unit is fabricated, and it doesn’t fit, then you have a real problem.”
Deo is aware of communication gaps at intermediate stages producing headaches onsite. “There was a project, without naming names: when the panels went to the site and it was all fabricated and ready to be installed, the realization happened that the slab edges were not as what was assumed by the facade contractor, and the slab edges were totally in a different location,” he notes. “Superstructure was up, ready to take the facade panels. But when the facade panels came, there was some miscoordination.... The design of the slabs was done based on a structural engineer’s documentation, and that piece of information was not accurately captured by the facade subcontractor at that point. So the facade panels were fabricated assuming slab edges at a certain location, and it ended up being different, and that resulted in a lot of site modifications and cutting of the concrete to accommodate the panels. It was a big point of contention there.”
Another project included fire-rated glazing in a curtain-wall system. “Fire-rated glazing is a very specialized sort of product,” Deo says; “it has certain limitations, some constraints, some handling restrictions. And those handling restrictions were not really followed, so there was a miscommunication or lack of clarity from the fire-rated insulated glazing manufacturer to the facade contractor.” Protective strips on the glazing were damaged, but the entire curtain wall was installed anyway. “The moment it was installed in that fashion, those damaged strips created openings for water to go into the fire-rated glaze, and that created a lot of issues–obviously a heartache for the owner.” Rain resulted in delamination and degradation, and the entire set of panels had to be removed and replaced.
A similar cautionary tale involved a mismatch of materials. “If you switch the silicon sealant that you’re using to apply with beam panels, you need to prep the substrate, which is aluminum, with a certain solution and a solvent and a cleaner,” Deo says. “If you switch the cleaning agent and it is incompatible with the silicon sealant, the silicon will not cure.... Silicon, when it cures, it goes from a pasty consistency to a rubbery consistency. And the solid consistency was not achieved for weeks because that cleaning agent was not compatible with that, so that required the entire construction team to go back, remove all the sealants, and reapply all the sealant, really having a big impact on the schedule of installation.”
In all these cases, Deo concludes, “the common thread is information and coordination. The information needs to flow freely. Coordination needs to happen diligently. Everybody who is handling a product needs to know if there are any specific requirements.... Every expert in the field is trying to keep pace with what’s going to get incorporated into the design; it is a big, complex project. Are we diligent in terms of disseminating that information to everybody who is involved with their task? If a new material or a product is brought on board for its valid merits, we would want to understand the long-term behavior of that material and the special handling and design considerations.” One well-managed project that Deo worked on incorporated a curtain wall so advanced that passersby may not recognize it as a curtain wall: the laminated stone and glass facade of downtown Manhattan’s newest major arts facility.
The Right Team at the Right Time
Firms with a well-established record of curtain-wall construction, in some cases engaging external facade consultants and in some cases maintaining an in-house facade specialist department, follow an orderly process that brings the parties with hands-on expertise into the conversation early. The design-assist method of construction, in which contractors and subcontractors are involved in the design phase from the outset, differs from design-build, design-bid-build, informal involvement, and delegated design in that it explicitly puts designers and builders in communication early enough for the latter’s experience with materials, methods, and constructability to inform the former’s early decisions.
Buro Happold’s Ivanoff, after over a decade of experience on its Facades and Specialty Structures team, notes that the preferred approach “in most markets now, and this ranges from commercial projects to university-type projects, is early engagement from subcontractors that are actually supplying the curtain wall or facade component.” By considering installation possibilities or limitations, shipping issues, “bespoke elements that are unique to that particular contractor,” and other variables affecting the constructability of a design, he says, a clearly defined design-assist arrangement lets architects “work from an initial level of documentation and work through a certain phase, and try to make not just educated guesses of assuming this is going to be cheaper or more expensive, but actually having someone at the table [who] can provide somewhat immediate feedback.” Though it is critical to define an end goal for the design-assist process, he adds–sometimes “it can just evolve and keep going forever”–having a team comprising the general contractor, facade subcontractor, engineers, architect, and client “all at the table, or all on the same Zoom call, is probably the most meaningful, beneficial thing that we see.”
Ivanoff and other commentators find that there is rarely such a thing as bringing in consultants and contractors too early. Of the AIA’s standard five-phase process (schematic design [SD], design development [DD], construction documents [CDs], bidding/procurement, and construction administration [CA]), he says, “we’d love to be at the table as soon as we can, during the SD phase,” though the customary ideal time is in DD, “to ensure that there’s enough information developed that the contractor can evaluate and provide a bid and provide some initial feedback.” If they are brought in too late, “the team may have made decisions that are so baked into the project it becomes really problematic to change them.” Joint spacing or module spacing, for example, may be a mismatch for the optimal fabrication dimension for shipping.
“Usually where things fail is not within the system of one contractor,” says Timm. “It’s usually where contractors interface: where the curtain wall ends and waterproofing of the roof or whatever happens. This is where the issues are. So whenever there’s multiple trades involved, the alarm bells go off a little bit.” Particularly when designs are complicated, he recommends, “make sure that you have all the trades that are involved participate early on.” Another essential ground rule is to match the level of complexity or innovation in a design to the local circumstances, particularly the familiarity of contractors with the systems in the design; an advanced curtain wall that SOM would attempt unhesitatingly in one city, with reliable specialists available, may be inappropriate elsewhere. “Know your market conditions, know the players you’re working with, and design towards that,” Timm advises.
Timm places more emphasis on timely consultation than on the formal arrangements. “It doesn’t matter what the delivery methodology is like, whether it’s design-assist or design-bid-build,” he says. “We talk to our friends in the industry, of course, [and perform] smell tests very early: in SD, making sure that we’re on the right track here, that we’re not going above or beyond the limit of what should be done.” There could be major differences between 10' and 8' curtain-wall panels if the latter fits on the available trucks or in the available hoists and the former doesn’t. One should ask whether specialty hoists are an option at the location before choosing components that require them; whether units can be installed from the outside straight out of the container (usually the more efficient approach) or need to go into the building and up on a hoist to be installed from the inside; and whether crane time is available (especially with large precast panels) for morning or evening shifts. “These kind of discussions should happen as early as possible,” he says, “with a CM or general contractor to sequence, how could this be done? Full transparency with the stakeholders, discussing your approach, or how your design gets built and installed, discussing this ASAP with people is the most important thing, to get everyone on the same page.”
There can be costs to design-assist procedures and early bidding, Timm acknowledges. “I always say, ‘If you were a contractor, would you pad your numbers more or less, given you know exactly what you’re building, or maybe not knowing exactly what you’re building?’ The more precise and the more coordinated the set is, let’s say after CD, the better the price will be, I would think, because the contractor knows exactly what they’re going to do. And so people need to understand that the earlier you bid, the more uncertainty is there–potentially. You have to find the right vehicles to make sure that you get competitive pricing as an owner. But if you want to get input from the industry, that’s always possible; you don’t need to have a bid for that. You can always talk to people, because you’ve done five projects in the past together. You have a relationship, and that’s why it’s also important to have relationships, get honest feedback and sit together. Sometimes the contractor gets the job, sometimes they don’t, but then they know they’ll get another job in the future. That’s what we’re certainly in for: building relationships of trust and working together.”
Toh Tsun Lim, AIA, partner at PEI Architects in New York, advocates an orderly process with well-defined phases. “The normal practice for us is that we always go through a systems review during the bidding phase,” he says, after engaging both their own curtain-wall staff and independent curtain-wall enclosure consultants once SD is complete and approved by the client. Particularly on large jobs, the first phase of DD includes decisions whether to use unitized panels or a stick system and the level of customization required, with the contractor’s input on choice of systems and how they affect the design. “Sometimes we’ve had them actually do the detailing for us; other times, they just advise on the detailing,” Lim notes; “this is budgetary, based on the client.”
In the CD phase, PEI’s specialists work with the consultants on details–from mullions, glass type, glass positioning, and sill depths to energy metrics–and on how the intended design can be built and attached to the structure. At the bidding phase, contractors usually redraw the shop drawings to fit their construction methods and supply chains. “Some of them have access to mullions that can be produced cheaply abroad,” Lim says, and “others have access to steel at certain areas, and others don’t, so it all affects the way they want to build the curtain wall as we’ve designed it.” PEI and the consultants review each bid set for how well it matches the design. Occasionally, despite an initial assumption in favor of a unitized system, a contractor will say “we think we can do it better, cheaper, faster on a stick system, and they will revise the details completely to do that.” Negotiations during the bid period may lead to rejection of a system that “fundamentally affects our design” or to a solution regarding which details are and aren’t workable, considering reasons grounded in engineering, environmental/energy, or installation factors. “It’s good to have a curtain-wall consultant on our side,” Lim says, “because they see it both from the contractor side, the practical construction and installation,” and the architectural side. “They’re always watching out for the design, so that we never get this issue where we as designers are dilettantes, designing what we think is right, and just letting the contractor do what they do without a conversation in between. They help mitigate that conversation.”
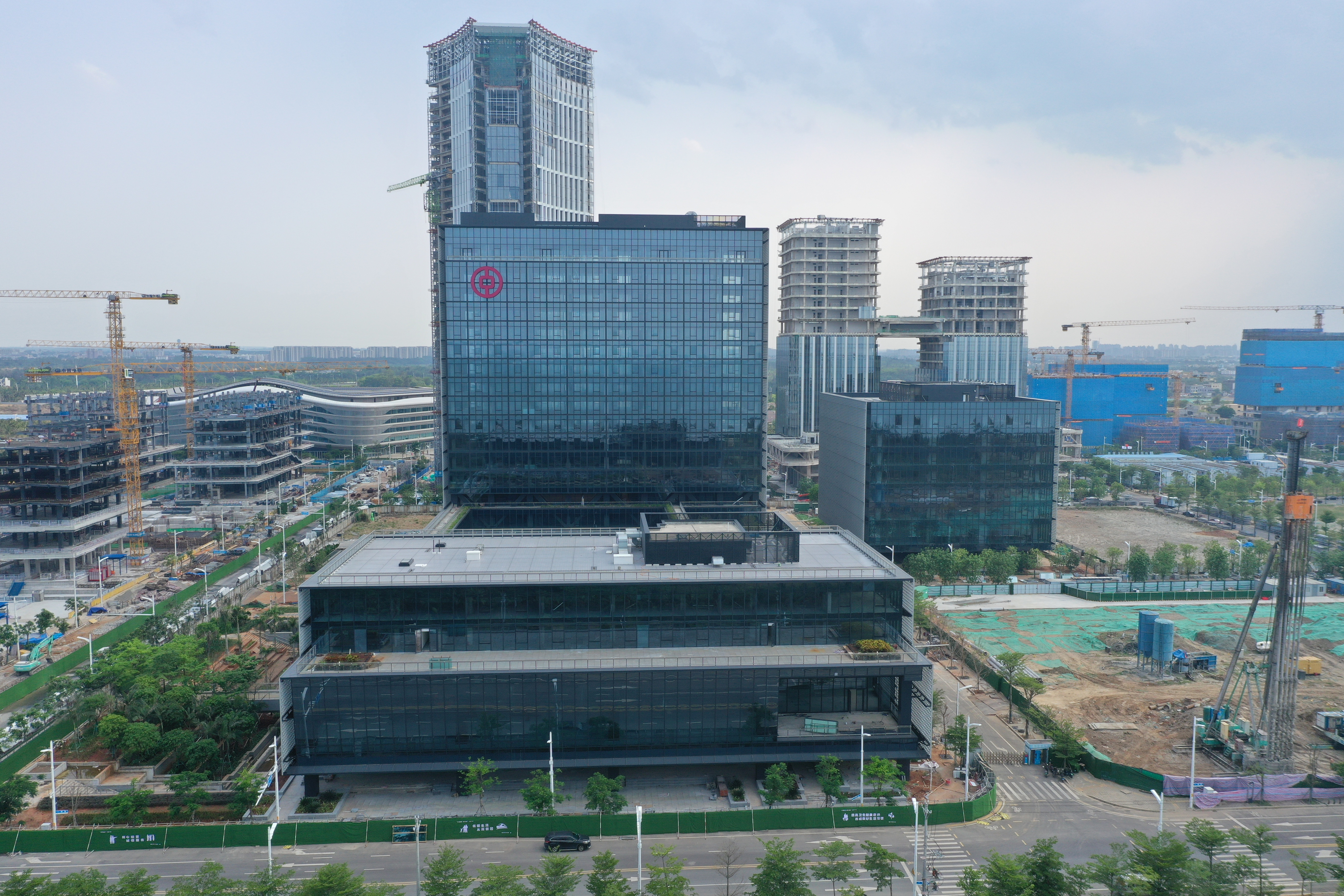
Photo courtesy of PEI Architects
Figure 4. Haikou Jiangdong International Financial Building.
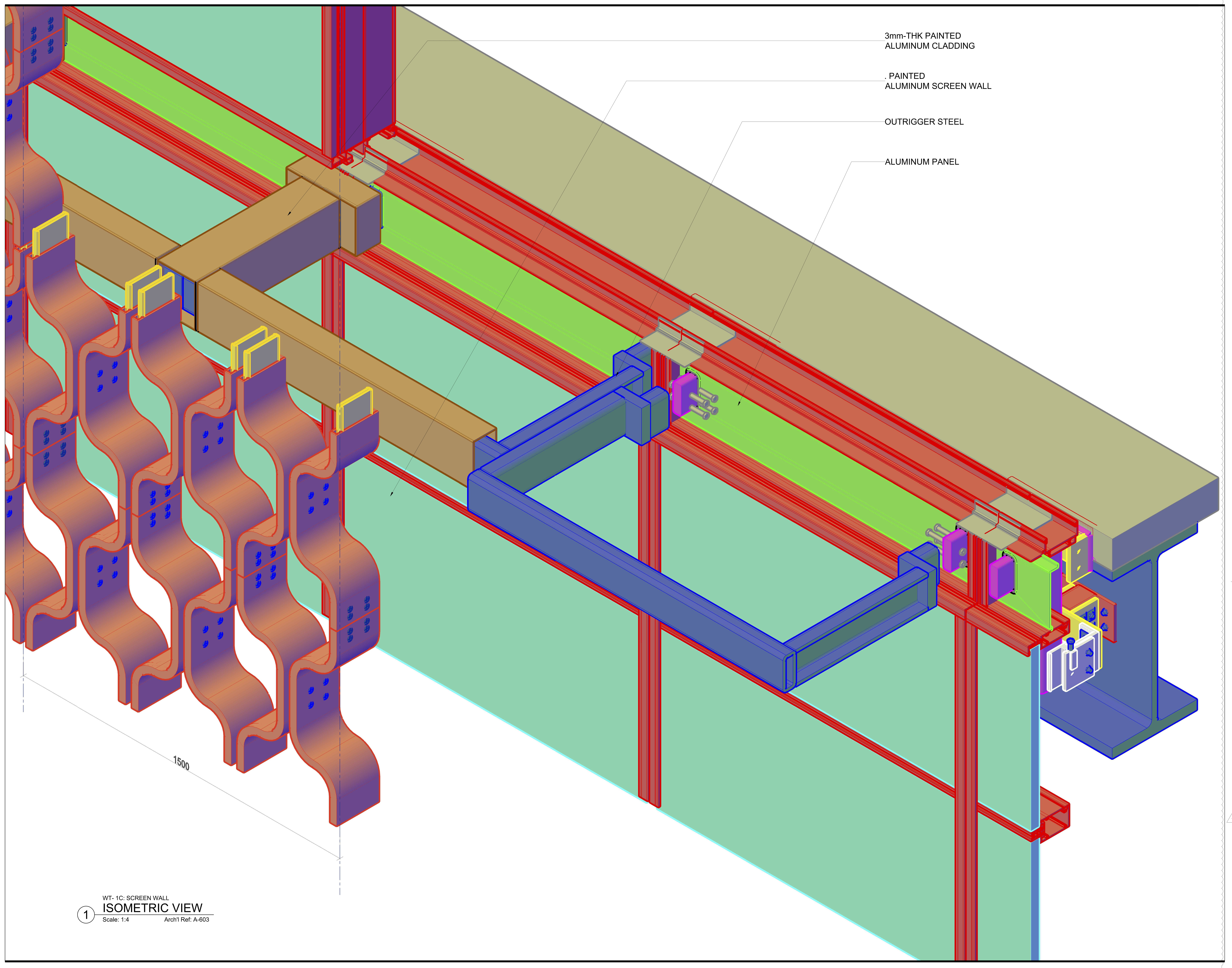
Image courtesy of PEI Architects
Figure 5. Haikou Jiangdong International Financial Building, facade diagram, isometric view.
One project Lim recalls, the Haikou Jiangdong International Financial Building, a bank tower in China, involved a double-skin wall, a common source of complications in breaching the primary enclosure for outriggers tying the secondary wall back to the structure (see Figs. 4 and 5). “The double skin has its advantages,” he says, “in the sense that the second skin can create a different shading element, or it can create a void space that allows for natural ventilation up the building; it also allows you to sculpt the building,” with “no performance requirements whatsoever, other than to be structurally secure in space.” Negotiations were necessary with the curtain-wall consultant and contractor over steel types and sizes and connections to either the slab or the existing curtain wall. Structural soundness required larger pieces than the architects initially recommended. “Had we not been able to have that conversation with them, the contractor may not have been able to bid on the job,” Lim recalls; “either no contractor would have bid on it, or we would have had to abandon the secondary wall.”
Not every firm has the resources, professional networks, or cooperative clients that PEI, SOM, and their peers customarily enjoy. Lim recognizes that on some jobs, “for budgetary reasons, “you’re not going to get that many bids. You’re not going to get the time to review it all. And what happens is, the owner selects a contractor, probably more on budget than anything else.... During the bid phase, you’re just thrown together in a shotgun marriage.” If a firm is not large enough to have curtain-wall consultants, “you will always have–at least in this country–the opportunity to review shop drawings,” and “the issue is who controls the process once we’re into the construction phase,” which may be too late to save a design from “changes that are reflected in the shop drawings that you can do nothing about.”
Where design documents are insufficiently specific, Lim says, “you’ve given free reign to the contractor to build it his way or her way, and in that process what happens is that what you thought were very specific details in your things get erased because of budget issues, if we’re talking smaller jobs, and therefore you won’t have a chance to react to that. If you don’t get this systems-review phase, you are much more beholden to the contractor at that time, and you have to be prepared for that.” Fortunately, he adds, smaller and more standardized jobs are usually less complicated than ones where clients have the resources for curtain-wall consultants. The recommended option after the DD phase, when detailing is left to the contractor in the CD phase, is for the architect to review construction details; “in that case, that’s the collaborative effort that comes in when you don’t have a systems-review phase.”
Almost Always Essential: The Performance Mockup
“For our systems-review phase,” Lim continues, “the mockup is the end-all and be-all. Unfortunately, the reality is, some people’s version of a mockup is different from others.” Building a visual mockup allows the team to review the materiality, color, scale, and proportion of a design but lacks realistic supporting components; a performance mockup (PMU) is better-constructed and more detailed, accurately representing what will go onto the building; a constructability mockup, sometimes identical to the PMU but occasionally requested separately for novel projects, serves as a trial installation. The PMU is “where everything gets reviewed with the client for compatibility, for constructability, and for performance,” Lim says: “literal performance on wind and water infiltration.” On smaller jobs with standardized systems, contractor-vendors may provide “pre-designed, pre-engineered, and pre-built” system mockups, Lim says; “they’re not customized, like they would be on ours, which is a purely custom curtain wall... The architect becomes more of a selector of options within that system, rather than a custom designer. It’s like the IKEA of curtain walls,” a kit-of-parts approach with “no installation issues, no customization issues.” The tradeoff for the extra cost of a fully bespoke system, he finds, is that the “multiple bid phases and cost checks” mitigate risks and prevent surprise cost overruns. “We’ve never gotten to the point where we’ve had a client that asked for something but was not prepared to ensure that the process was checked along the way.”
Mockups are “not just for the architect and to look at the pretty picture, whether this glass is silver or bright,” Timm says, “but also for the contractor to learn how to install.” SOM always specifies that “whoever is going to install that curtain wall is the one also installing at the PMU.” Mockups at full scale are universal problem-solvers, he says: “On every project, you learn something, or the installer learns something. And of course, the less standard a project it is, the more the likelihood that you learn something, especially if it’s a stick-built system with specialty waterproofing conditions on site, lots of on-site work... not a Kawneer 1600 or something that is tried and tested, but something that’s special.”
On New York’s Moynihan Station, for example, a custom job that Timm likens to “the Champions League, the Super Bowl of projects that you do once in your career,” the team built two PMUs for the mid-block and Train Hall skylights. “We ran the entire spectrum of typical PMU testing, and the contractor used these mockups specifically for verification of their installation concept.... Nothing was flat, everything was in 3D.” Testing verified tolerances for the steel, the cut of the aluminum, and the system being sealed with wet silicone on site; “the people doing this work had to have abseiling ropes and caulk guns with weather (structural) silicone. This whole thing had to be a dry run for the installation [and] had to be thought through from A to Z, from steel to aluminum to glass, fritting of the glass, making it watertight; how to install all this, how to have access to all this, how to replace the glass post-accidental breakage.” The curved shape was generated with flat glass and an offset joint with an angle change, “a pixelated approach rather than generating a continuous shape with curved glass. It’s a faceted approach, which is much more economic, usually, and easier technically.” The lessons learned on Moynihan, Timm notes, inform “almost every project that has shape that is not a box.”
“It’s rare that we don’t have a mockup on a project,” says Pawlynsky, except for small projects using well-tested standard systems. “Working out the interlock conditions, how units aim together, and where there were problems with water draining: that has been figured out in PMUs. Sometimes the failures take time to investigate and see what’s wrong, but they are so important in terms of the ultimate performance of the building. And even though it’s only on a chamber that’s representing two column bays and two or three floors, it’s the first time they’re lifting units and dropping them onto these specific anchor types. So I think it’s informative in terms of that as well. We always recommend that the actual foreman that will be on the project also be the one that is at the PMU test.”
Brandt adds that the metric for justifying the expense of a PMU or constructability mockup is “if the owner or client has had a similar negative experience in the past that has cost them money.” She recalls two back-to-back projects for the same owner, the first of which had a complex exterior interface involving a vertical wall stepping into a terrace, engaging multiple trades and sequencing challenges. After headaches, cost overruns, and revised work on this building, the owner took a different tack on the second, using the same architect, consultant, and construction team but deciding, “Let’s not repeat the mistake we did last time. Let’s build this ahead of time and make sure all of the trades understand what’s happening.’ I haven’t seen someone actually quantify that in terms of dollars; it was more in terms of tears.”
Conclusion
“Installation is the last stage in the journey of curtain-wall design and execution,” Kumar says, “and because it is such a prefabrication-intensive system, everything about the curtain wall should have been resolved by the time you come to installation. If you’re having a problem in installation, there has been something missed by all the teams that are responsible for ensuring that that doesn’t happen.”
Kumar summarizes the work of a facade consultant as thinking systematically and methodically about the purposes and functions of a curtain wall, the expectations of the various parties involved, and ways of bringing the different perspectives into alignment. “We are building a process which is based on protecting everyone’s interest through the gradual evolution of the project, where at the right time the right knowledge is being produced for the project, which de-risks the project for each entity, so that by the end of it, there are no surprises. The success is holistic: it comes for everyone, and we meet the schedule, we meet the cost.... It’s never too early, but it’s also never too late.” Since “the value that we could provide to a design team does improve if fewer decisions are already concretized,” getting on board early has benefits–though “we know the way the architectural industry works,” with multiple forces affecting the timing of team formation. “Once the project has gone out to bid,” he finds, “it is kind of pointless to bring in a new party.”
In some cases, though, quality control may benefit when a different type of player enters the game. Buro Happold maintains a separate division for investigation and remediation, and Ivanoff points to one of its strategies as an invaluable adjunct to the customary collaborations: on-site testing, partnering with “an independent testing agency that’s coming along for the process and doing incremental testing. Often, a lot of the projects of scale that people work on have off-site testing for the unitized curtain wall. That’s fantastic and should be ensured, but ensuring that during the installation process–say, 30 percent, 60 percent, and maybe at 90, these critical milestones–that there’s on-site testing, to ensure that what has been approved is really being executed in the field, aligns with what was done in a perfect test laboratory.” The stagewise testing, he says, controls for changes in installation teams or other variables that can affect the work. “Most of the time what happens is you get to the end of a project, or you get to post-occupancy, and someone has a leak or a problem, and at that point, all your interior fit-out work has been done. Well, you have a much bigger headache on your hands.”
Along with having a testing agency or firm included at the table, Ivanoff emphasizes the value of communication and mutual respect among the collaborators, “making sure that the design team should appreciate the work that the installation team has to be doing.... The installers need to physically have tools or fit their hands behind panels and have access, and concealing different connections only makes things much harder in the field and may delay things later on.” The contractors and general contractors he has worked with, he adds, have an impressive ability to master the complexities of equipment and logistics, particularly in challenging urban conditions; “delivering material and getting something onto a building,” he says, “is somehow remarkably done in New York City.” Knowing what these specialists do, not just in major centers but in every location, one can design with their skills in mind and have confidence in the results.
Works Cited:
AIA Contract Documents. Comparing design assist and delegated design in construction projects. Aug. 16, 2023. https://learn.aiacontracts.com/articles/comparing-design-assist-and-delegated-design-in-construction-projects/.
Koger M. Design assist vs. delegated design industry trade associations release guidance. American Bar Association, Dec. 11, 2020. https://www.americanbar.org/groups/construction_industry/publications/under_construction/2020/winter2020/design-assist-vs-delegated-design/.
Bill Millard is a New York-based journalist who has contributed to Architectural Record, The Architect’s Newspaper, Oculus, Architect, Common Edge, Annals of Emergency Medicine, OMA’s Content, and other publications.