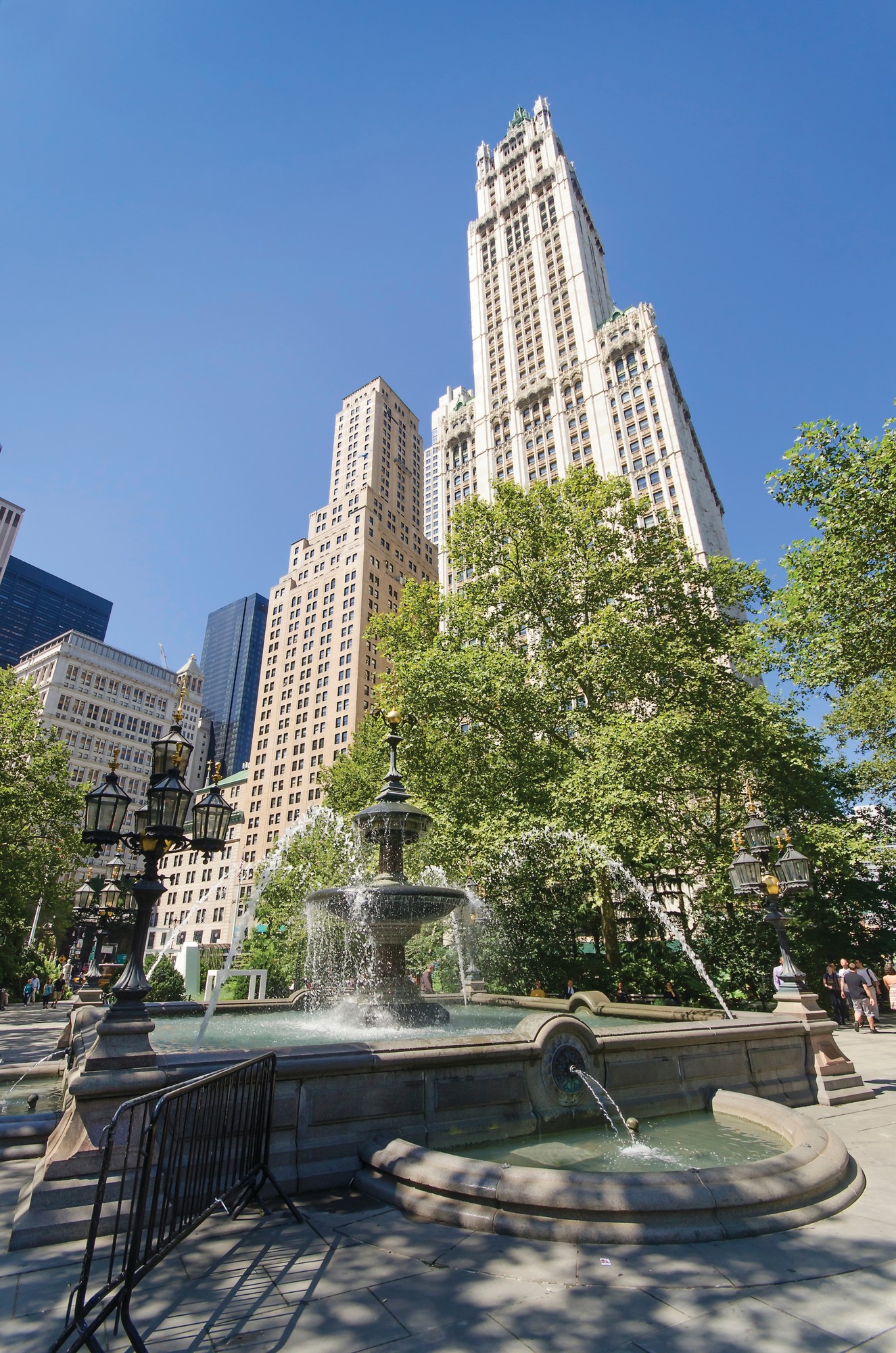
Photo courtesy fo Geberit
Existing buildings are being repurposed across the country to create vibrant places, addressing current design and programmatic needs.
Architects are increasingly tasked with finding ways to transform existing buildings to meet current needs, whether to update and upgrade an ongoing operation or to completely change the type of occupancy and use of a building such as changing underused office buildings into multifamily housing. For example, according to the International Association of Plumbing and Mechanical Officials (IAPMO), “The United States faces a significant housing shortage, with an estimated deficit of 3.8 million homes. Adaptive reuse offers a viable solution to this crisis by revitalizing urban cores and reducing the environmental impact of new construction.” And according to the apartment website RentCafe.com, “The number of apartments set to be converted from office spaces has skyrocketed from 23,100 in 2022 to a record-breaking 70,700 in 2025. Office conversions now make up almost 42% of the nearly 169,000 apartments in future adaptive reuse projects.”
This is a notable surge in such conversions that is no doubt fueled by the nationwide shortage of apartments and a corresponding decline in the need for centralized office space due to the popularity of remote working. This trend is being seen across the country from New York City and Washington D.C. on the East Coast to Los Angeles on the West Coast. More than just creating new housing, though, this trend also reflects a shift toward urban living that is sustainable and community-focused. Other types of buildings are seeing similar changes either in terms of upgrading their use or converting them to a different use. In this course, strategies, techniques, and examples are given of ways that many existing buildings are being creatively by adapting sites, replacing floors, and modernizing plumbing.
Adapting Sites
In existing buildings, there are often outdoor areas that are underutilized or rooftop surfaces that have been ignored. These spaces have the potential to enliven a renovated building by providing outdoor community spaces or even living areas.
Incorporating outdoor spaces into a building renovation or adaptive reuse is consistent with many current trends and can go a long way toward improving the design character and usability of the building. Often this can be accomplished without impacting any of the historic nature of the building itself. Some of the design trends to consider in this regard include the following.
- Biophilic Design: This concept is described as “the deliberate attempt to translate an understanding of the inherent human affinity to affiliate with natural systems and processes—known as biophilia—into the design of the built environment.” This can be done through a visual connection to the outdoors, the incorporation of natural elements indoors, or expanding the indoor spaces to flow into outdoor spaces. Creating outdoor spaces can achieve this indoor/outdoor environmental connection through physical proximity and the creation of decks, terraces, etc. It is also appropriate to use natural materials such as wood and stone plus incorporating vegetation and greenery through the use of planters and flowerpots. The advantages of biophilic design are based on regular interactions with the outdoors, which are proven to have positive health benefits, such as lower blood pressure, reduced stress, expedited healing, and improved mood and focus.
- Green Roof Decks: Relatedly, roof areas, particularly in urban settings, are being transformed into environmentally beneficial and people-friendly places. This includes creating “green roofs” which can provide shade to a building or people, improve stormwater management, reduce temperatures of the roof surface, mitigate “heat islands,” and reduce energy demands on the building as a result. When a green roof is built on top of a raised deck system, it creates an air space between the deck and the building roof structure. This cavity space can help reduce cooling loads, protect the roof and its membrane from damage from the elements (hail, wind, and UV rays), and significantly extend its lifespan.
- Pop-Up Parks: Reclaiming car-designated zones in urban areas is being done to transform them for pedestrian or hospitality and entertainment use. Referred to as “Pop-Up Parks,” these spaces can vary in size from a one-car parking space of about 150 square feet to many spaces linked together to a whole block or lane. Such Pop-Up-Parks can be considered in adaptive reuse building renovations allowing for temporary installations for events, for seasonal use, or even permanent year-round use.
All of these trends can be useful for an adaptive reuse building renovation. However, there are often construction issues to address such as the lack of a level ground or roof deck surface, the need to easily incorporate natural materials and plantings, and an eye toward working within project budget restraints.
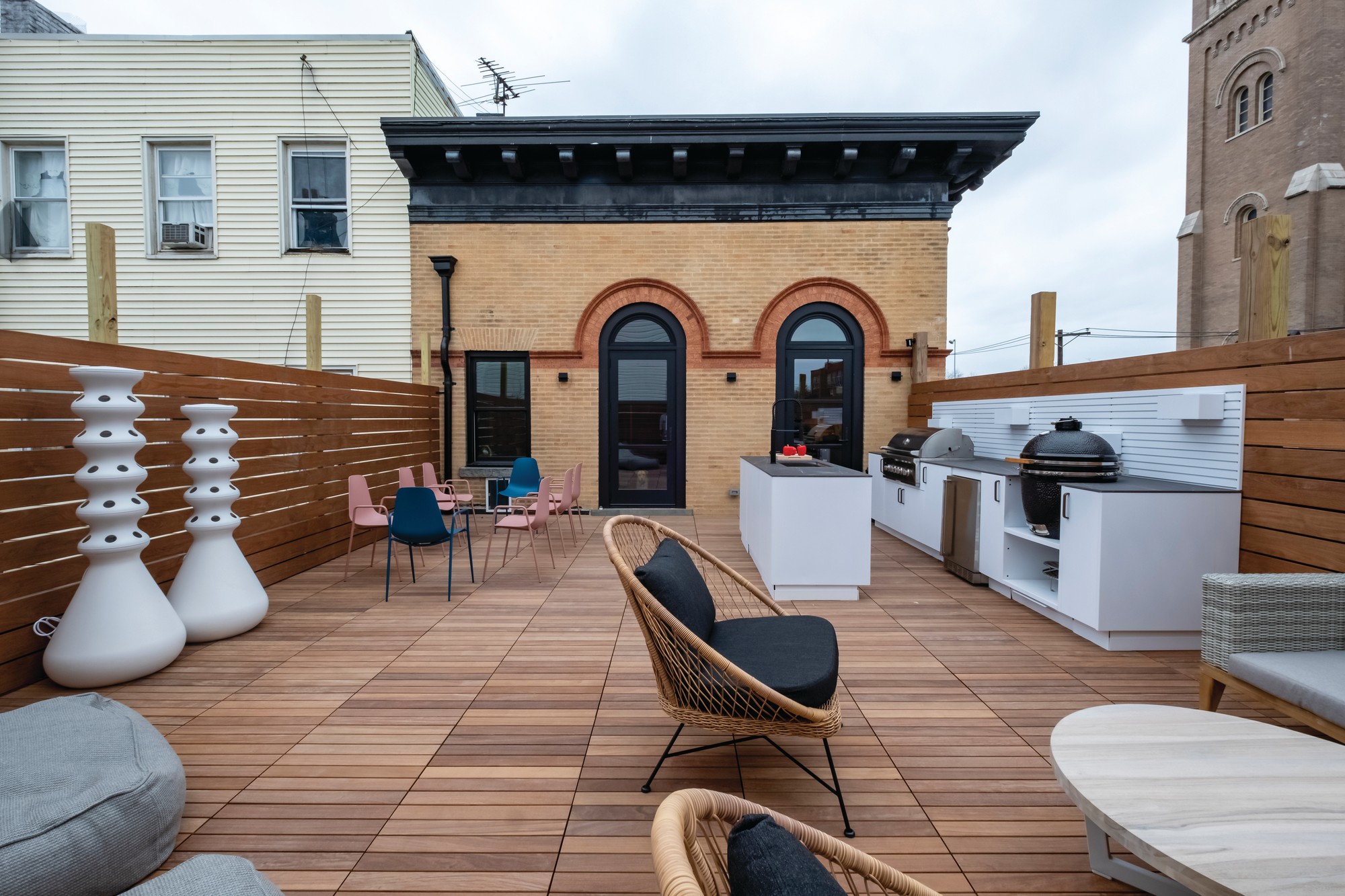
Photo: Anthony Carrino; courtesy of Bison Innovative Products
Reclaiming unused space in existing buildings, such as this rooftop area, allows for the creation of outdoor spaces with many health and wellness benefits to the users.
Raised Modular Decks
A commonly available solution to address these design trends in building renovations/re-use is the incorporation of a raised modular deck system. Such modular systems are versatile and give architects and others the design flexibility to create unique and beautiful rooftop environments and outdoor spaces. By utilizing pedestals that adjust for height and slope to support the deck, uneven or pitched surfaces can easily be accommodated. This creates the opportunity to use underutilized outdoor spaces and turn an otherwise wasted space into a functional outdoor amenity, such as a kitchen, bar, lounge, or garden area. Rooftop decks help to boost morale and strengthen relationships within the community of building users. They can also incorporate natural elements such as planters or natural materials and thus create biophilic design opportunities within a renovation project. Incorporating a pedestal deck system can also provide pedestrian access to green roofs with native plants and natural building materials to offer occupants a visual and material connection with nature.
Adjustable pedestal deck systems are also ideal for Pop-Up-Park installations that can include wood tile, stone, or concrete paver surfaces covering the existing pavement. Popular accessories include attachment hardware, planters, railings, and benches. Some manufacturers offer all the built elements required for a Pop-Up Park installation which creates a smooth installation as well as offering a consistent warranty for the entire system.
Designing Pedestal Decks Using Modular Components
As noted already, modular pedestal deck systems are versatile and can be incorporated into almost any renovation/adaptive reuse project type to create usable, sustainable, and affordable outdoor spaces. They consist of standardized components that can be selected, specified, and customized to meet project needs, budget requirements, or green building goals. Regardless of where or how they are used, adjustable deck systems commonly incorporate three primary types of components as described in the following sections.
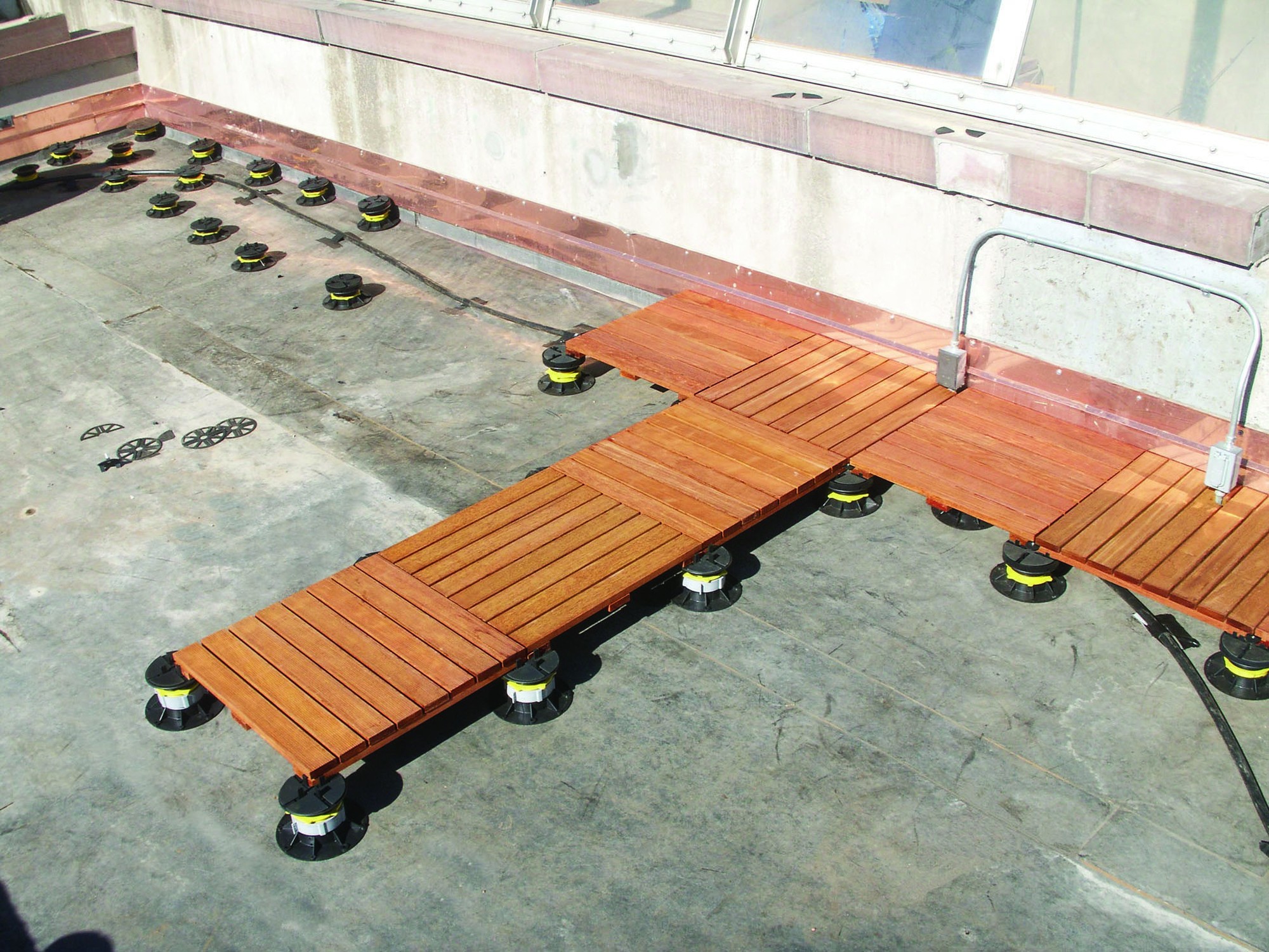
Photo courtesy of Bison Innovative Products
Standard components can be used to create raised pedestal decks with a variety of surfaces and final design layouts.
Deck Supports
Fixed or adjustable height pedestals are the fundamental support system for outdoor decks and have become recognized as one of the most labor- and cost-efficient methods of creating a level deck over a moderately sloped surface. High-density polypropylene plastic that is 100 percent recyclable is a common material used to manufacture the supports. This makes them impervious to water, mold, and freeze-thaw cycles. Their adjustability offers tremendous design flexibility compared to traditional deck building materials and methods. Using a gravity system, the supports do not penetrate but rather protect roofing and waterproofing membranes thus causing no damage or harm to the surface below. The pedestals can be used to elevate the deck surface to meet the threshold, therefore providing an even and level transition from one space to another. This allows easy access for building occupants with varying levels of mobility.
Deck Surfaces
The versatility of adjustable pedestal deck supports means that they can be used to elevate a variety of decking surface materials. The common options include pavers made from concrete or stone, such as granite or travertine. Similarly, structural porcelain tiles, fiberglass grating, composite materials, or conventional wood decking systems can be used in a grid pattern to meet different design requirements. Typically, a galvanized steel paver tray is adhered to the back of structural porcelain pavers or other materials prone to breakage to provide impact resilience. The paver trays are available in a variety of standard sizes, compatible with large format ceramic tile sizes, and allow accommodation for thicknesses of 2 cm. With or without a support tray, the deck surface materials can be removed during building use for routine maintenance, repairs to the roof, or to gain access to other systems.
If a lighter-weight surface material is preferred or required, wood tiles are a good alternative, weighing only one-third as much as concrete tiles. Typically made from hardwoods in a variety of species, wood tiles are generally commercial-grade products. If maintaining the wood color is desired, wood tiles can be periodically cleaned and sealed. Left to weather naturally, the wood tiles will develop a silvery-gray patina. Wood tiles can be crafted from premium-grade remnants and harvested in an environmentally responsible method designed to preserve the economic viability of rainforest hardwoods. Some manufacturers of wood tiles associate with governing groups such as the Forest Stewardship Council (FSC) to ensure the quality standards and practices of wood acquisition and plantation farming.
Site Furnishings
Manufacturers of pedestal deck systems also offer coordinated, modular elements that are designed to integrate with their deck systems while giving the architect complete design flexibility. Modular wood cubes are available with an array of design options to incorporate seating, storage, and planters. Such cubes are available with a polyurethane lining and drainage holes to host plant life. At other times of the year, the cubes can be repurposed for seating and storage of seasonal items (i.e., cushions and pillows) by placing a manufactured hardwood top on the cube.
If a different look is desired, aluminum cubes are also an option. Designed to withstand temperature extremes, these low-maintenance, durable planters are constructed of lightweight, partially recycled aluminum. Some use an industrial-strength powder-coated finishing process that is applied electrostatically and cured under heat, creating a more resilient finish than conventional paint. There are a variety of sizes and color choices available.
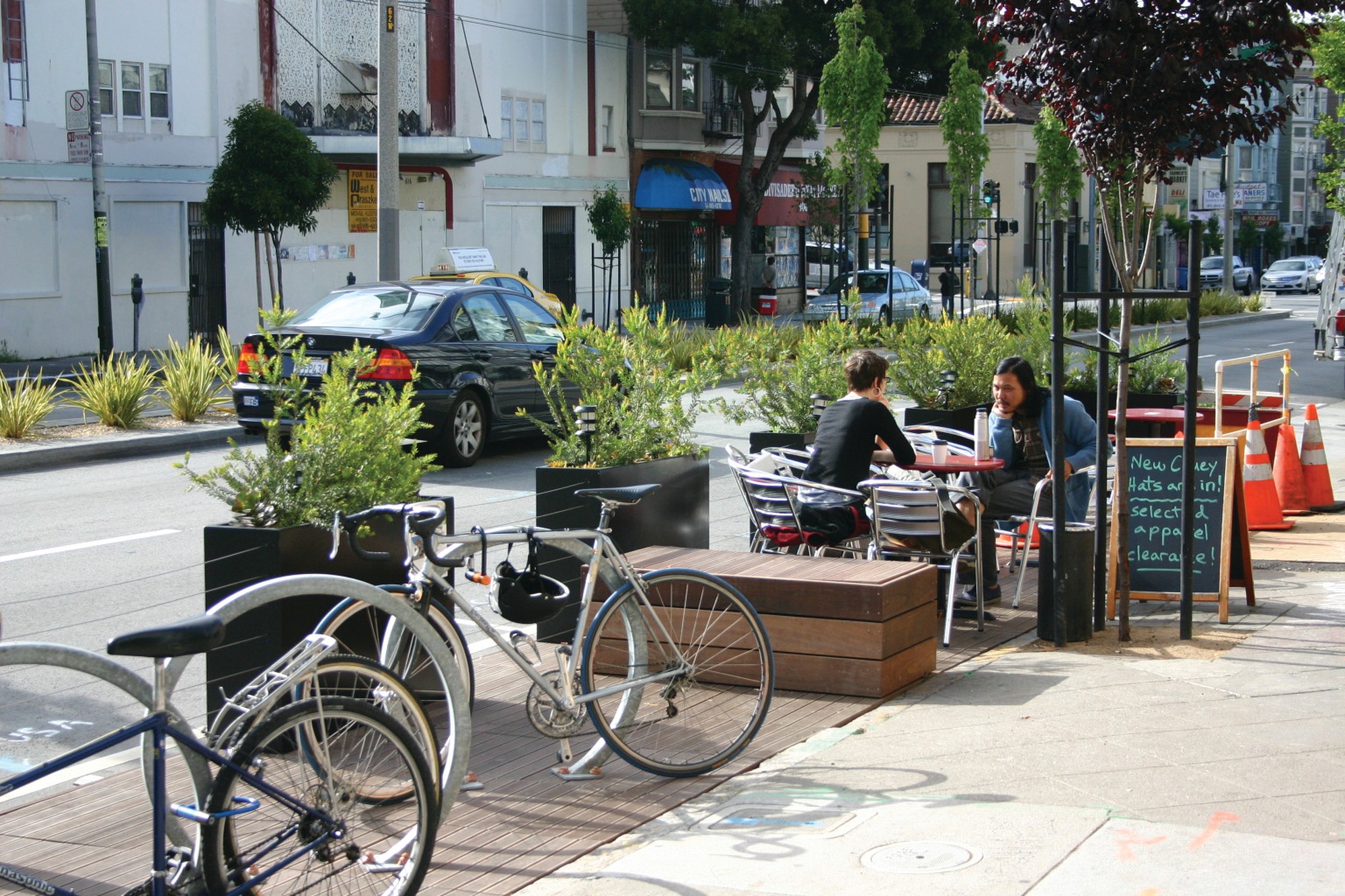
Photo courtesy of Bison Innovative Products
Standard outdoor deck components can be customized and used to create outdoor spaces such as “Pop-up Parks” consistent with changing needs.
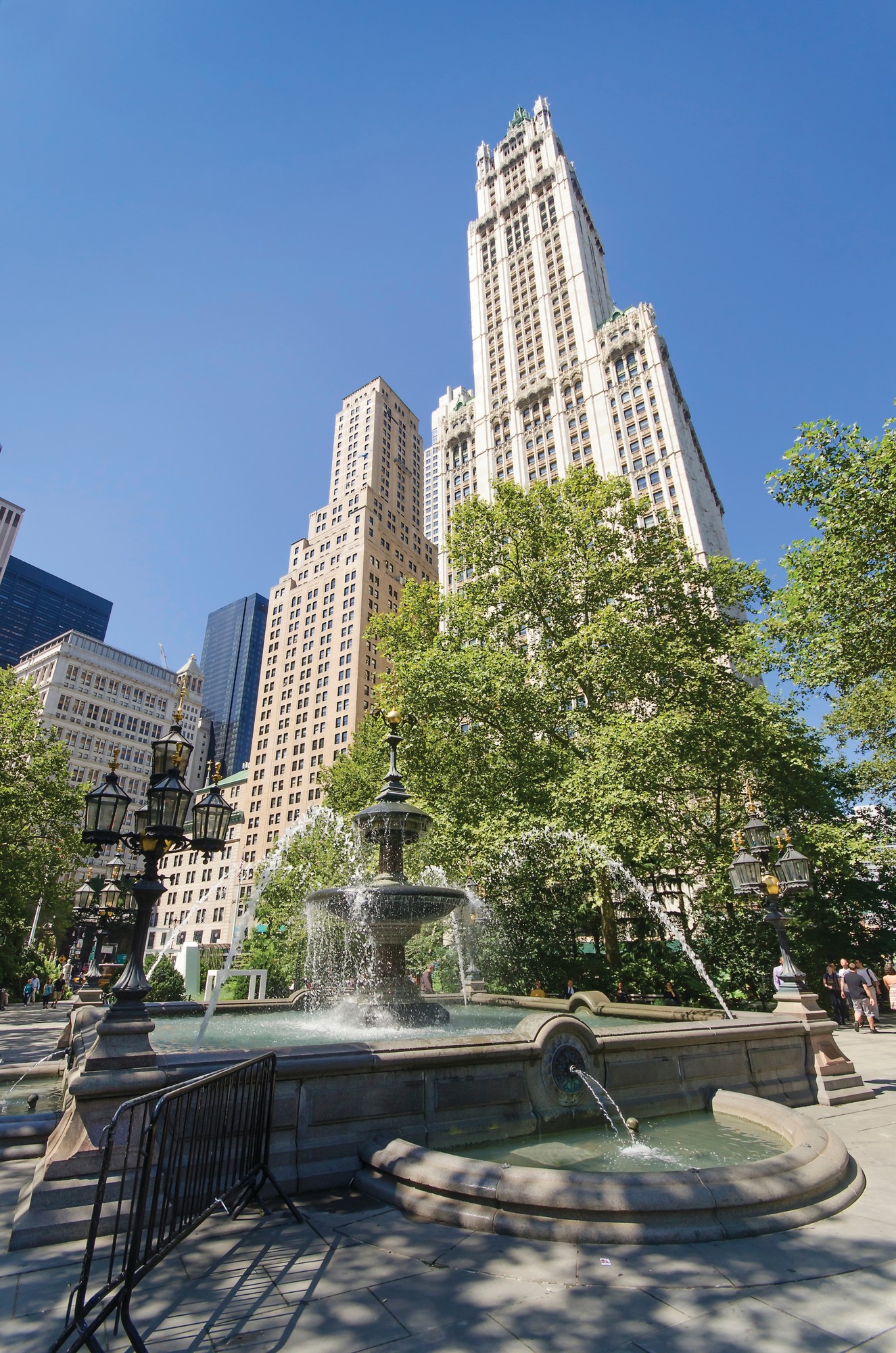
Photo courtesy fo Geberit
Existing buildings are being repurposed across the country to create vibrant places, addressing current design and programmatic needs.
Architects are increasingly tasked with finding ways to transform existing buildings to meet current needs, whether to update and upgrade an ongoing operation or to completely change the type of occupancy and use of a building such as changing underused office buildings into multifamily housing. For example, according to the International Association of Plumbing and Mechanical Officials (IAPMO), “The United States faces a significant housing shortage, with an estimated deficit of 3.8 million homes. Adaptive reuse offers a viable solution to this crisis by revitalizing urban cores and reducing the environmental impact of new construction.” And according to the apartment website RentCafe.com, “The number of apartments set to be converted from office spaces has skyrocketed from 23,100 in 2022 to a record-breaking 70,700 in 2025. Office conversions now make up almost 42% of the nearly 169,000 apartments in future adaptive reuse projects.”
This is a notable surge in such conversions that is no doubt fueled by the nationwide shortage of apartments and a corresponding decline in the need for centralized office space due to the popularity of remote working. This trend is being seen across the country from New York City and Washington D.C. on the East Coast to Los Angeles on the West Coast. More than just creating new housing, though, this trend also reflects a shift toward urban living that is sustainable and community-focused. Other types of buildings are seeing similar changes either in terms of upgrading their use or converting them to a different use. In this course, strategies, techniques, and examples are given of ways that many existing buildings are being creatively by adapting sites, replacing floors, and modernizing plumbing.
Adapting Sites
In existing buildings, there are often outdoor areas that are underutilized or rooftop surfaces that have been ignored. These spaces have the potential to enliven a renovated building by providing outdoor community spaces or even living areas.
Incorporating outdoor spaces into a building renovation or adaptive reuse is consistent with many current trends and can go a long way toward improving the design character and usability of the building. Often this can be accomplished without impacting any of the historic nature of the building itself. Some of the design trends to consider in this regard include the following.
- Biophilic Design: This concept is described as “the deliberate attempt to translate an understanding of the inherent human affinity to affiliate with natural systems and processes—known as biophilia—into the design of the built environment.” This can be done through a visual connection to the outdoors, the incorporation of natural elements indoors, or expanding the indoor spaces to flow into outdoor spaces. Creating outdoor spaces can achieve this indoor/outdoor environmental connection through physical proximity and the creation of decks, terraces, etc. It is also appropriate to use natural materials such as wood and stone plus incorporating vegetation and greenery through the use of planters and flowerpots. The advantages of biophilic design are based on regular interactions with the outdoors, which are proven to have positive health benefits, such as lower blood pressure, reduced stress, expedited healing, and improved mood and focus.
- Green Roof Decks: Relatedly, roof areas, particularly in urban settings, are being transformed into environmentally beneficial and people-friendly places. This includes creating “green roofs” which can provide shade to a building or people, improve stormwater management, reduce temperatures of the roof surface, mitigate “heat islands,” and reduce energy demands on the building as a result. When a green roof is built on top of a raised deck system, it creates an air space between the deck and the building roof structure. This cavity space can help reduce cooling loads, protect the roof and its membrane from damage from the elements (hail, wind, and UV rays), and significantly extend its lifespan.
- Pop-Up Parks: Reclaiming car-designated zones in urban areas is being done to transform them for pedestrian or hospitality and entertainment use. Referred to as “Pop-Up Parks,” these spaces can vary in size from a one-car parking space of about 150 square feet to many spaces linked together to a whole block or lane. Such Pop-Up-Parks can be considered in adaptive reuse building renovations allowing for temporary installations for events, for seasonal use, or even permanent year-round use.
All of these trends can be useful for an adaptive reuse building renovation. However, there are often construction issues to address such as the lack of a level ground or roof deck surface, the need to easily incorporate natural materials and plantings, and an eye toward working within project budget restraints.
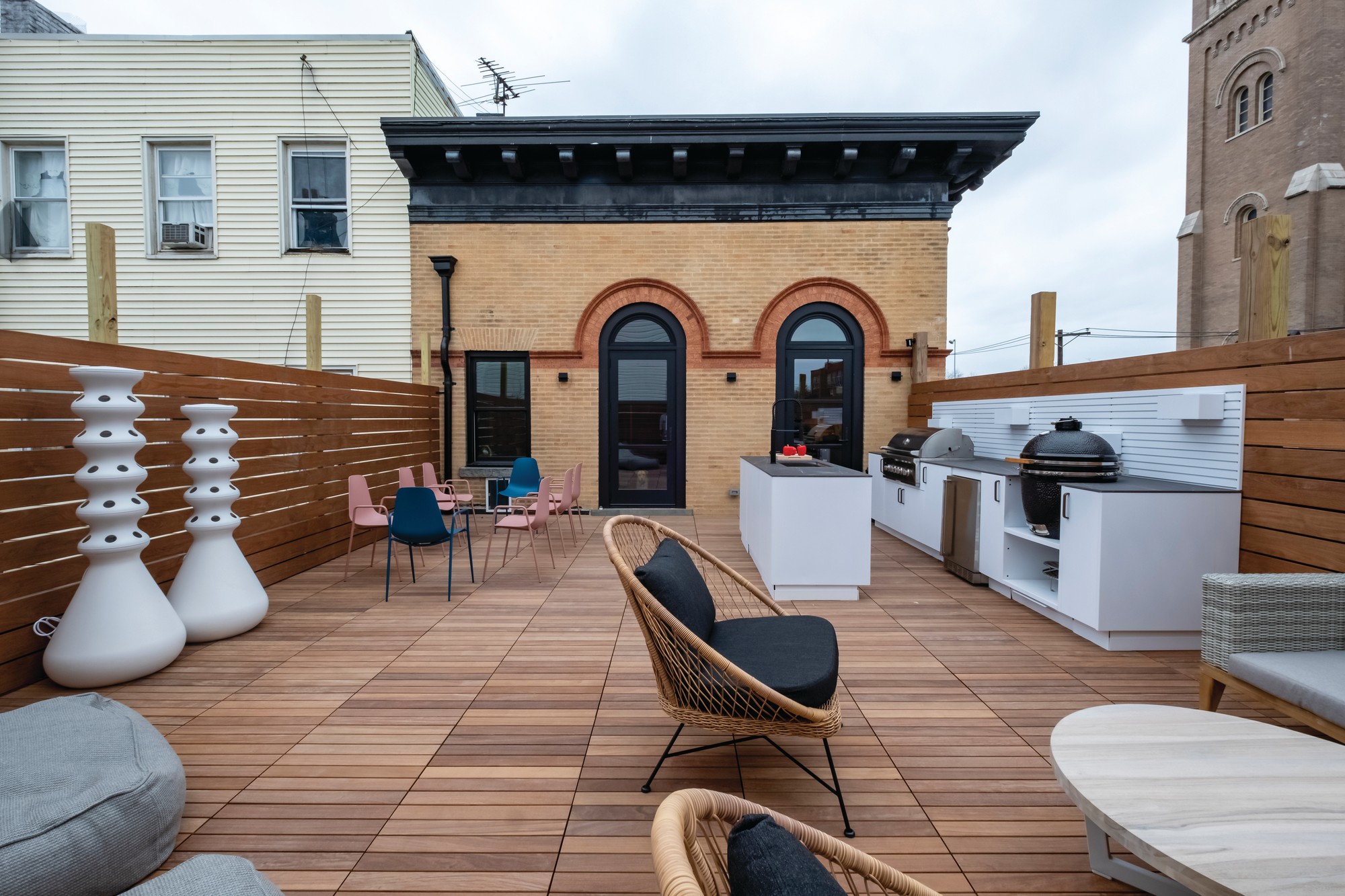
Photo: Anthony Carrino; courtesy of Bison Innovative Products
Reclaiming unused space in existing buildings, such as this rooftop area, allows for the creation of outdoor spaces with many health and wellness benefits to the users.
Raised Modular Decks
A commonly available solution to address these design trends in building renovations/re-use is the incorporation of a raised modular deck system. Such modular systems are versatile and give architects and others the design flexibility to create unique and beautiful rooftop environments and outdoor spaces. By utilizing pedestals that adjust for height and slope to support the deck, uneven or pitched surfaces can easily be accommodated. This creates the opportunity to use underutilized outdoor spaces and turn an otherwise wasted space into a functional outdoor amenity, such as a kitchen, bar, lounge, or garden area. Rooftop decks help to boost morale and strengthen relationships within the community of building users. They can also incorporate natural elements such as planters or natural materials and thus create biophilic design opportunities within a renovation project. Incorporating a pedestal deck system can also provide pedestrian access to green roofs with native plants and natural building materials to offer occupants a visual and material connection with nature.
Adjustable pedestal deck systems are also ideal for Pop-Up-Park installations that can include wood tile, stone, or concrete paver surfaces covering the existing pavement. Popular accessories include attachment hardware, planters, railings, and benches. Some manufacturers offer all the built elements required for a Pop-Up Park installation which creates a smooth installation as well as offering a consistent warranty for the entire system.
Designing Pedestal Decks Using Modular Components
As noted already, modular pedestal deck systems are versatile and can be incorporated into almost any renovation/adaptive reuse project type to create usable, sustainable, and affordable outdoor spaces. They consist of standardized components that can be selected, specified, and customized to meet project needs, budget requirements, or green building goals. Regardless of where or how they are used, adjustable deck systems commonly incorporate three primary types of components as described in the following sections.
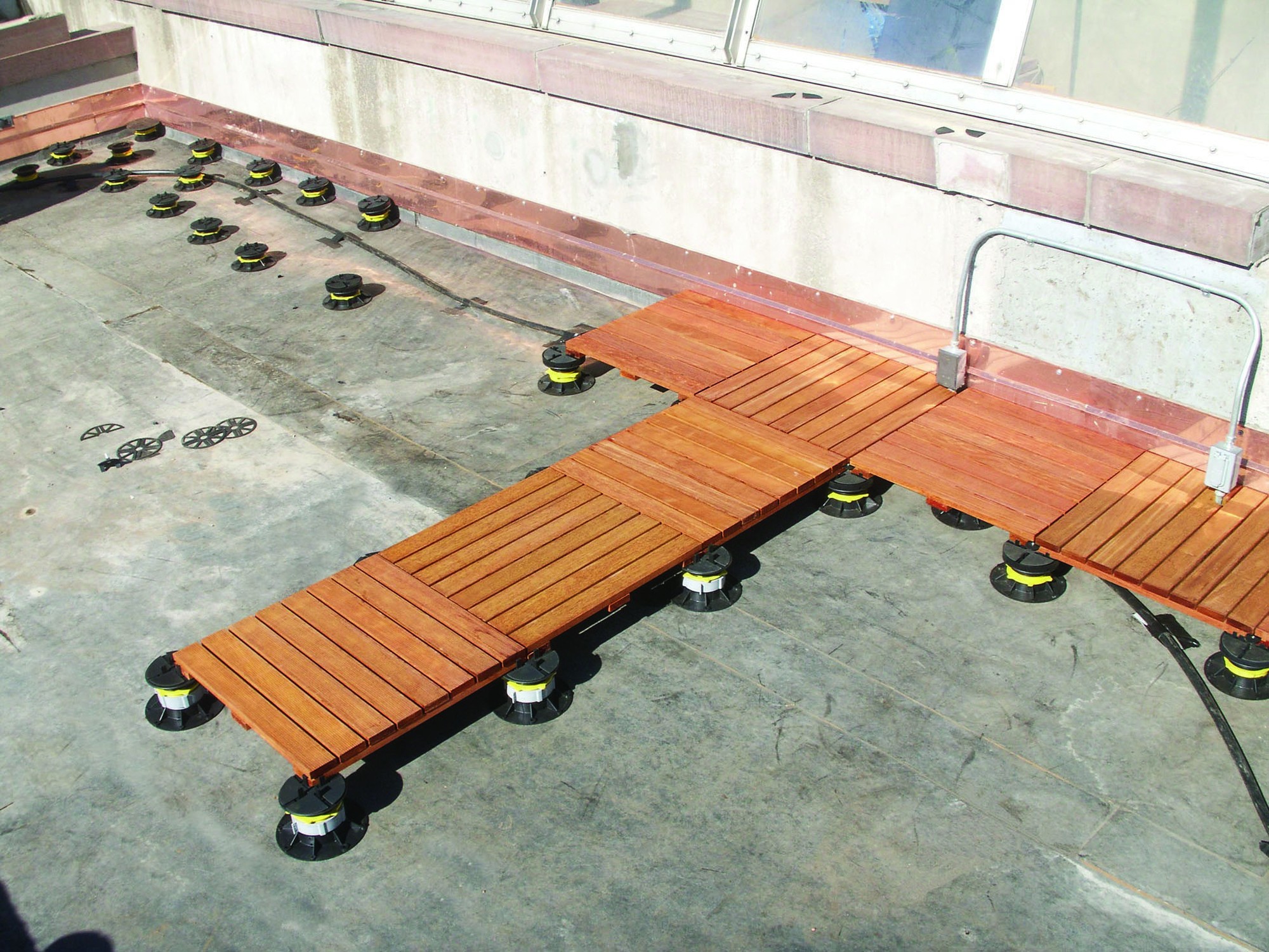
Photo courtesy of Bison Innovative Products
Standard components can be used to create raised pedestal decks with a variety of surfaces and final design layouts.
Deck Supports
Fixed or adjustable height pedestals are the fundamental support system for outdoor decks and have become recognized as one of the most labor- and cost-efficient methods of creating a level deck over a moderately sloped surface. High-density polypropylene plastic that is 100 percent recyclable is a common material used to manufacture the supports. This makes them impervious to water, mold, and freeze-thaw cycles. Their adjustability offers tremendous design flexibility compared to traditional deck building materials and methods. Using a gravity system, the supports do not penetrate but rather protect roofing and waterproofing membranes thus causing no damage or harm to the surface below. The pedestals can be used to elevate the deck surface to meet the threshold, therefore providing an even and level transition from one space to another. This allows easy access for building occupants with varying levels of mobility.
Deck Surfaces
The versatility of adjustable pedestal deck supports means that they can be used to elevate a variety of decking surface materials. The common options include pavers made from concrete or stone, such as granite or travertine. Similarly, structural porcelain tiles, fiberglass grating, composite materials, or conventional wood decking systems can be used in a grid pattern to meet different design requirements. Typically, a galvanized steel paver tray is adhered to the back of structural porcelain pavers or other materials prone to breakage to provide impact resilience. The paver trays are available in a variety of standard sizes, compatible with large format ceramic tile sizes, and allow accommodation for thicknesses of 2 cm. With or without a support tray, the deck surface materials can be removed during building use for routine maintenance, repairs to the roof, or to gain access to other systems.
If a lighter-weight surface material is preferred or required, wood tiles are a good alternative, weighing only one-third as much as concrete tiles. Typically made from hardwoods in a variety of species, wood tiles are generally commercial-grade products. If maintaining the wood color is desired, wood tiles can be periodically cleaned and sealed. Left to weather naturally, the wood tiles will develop a silvery-gray patina. Wood tiles can be crafted from premium-grade remnants and harvested in an environmentally responsible method designed to preserve the economic viability of rainforest hardwoods. Some manufacturers of wood tiles associate with governing groups such as the Forest Stewardship Council (FSC) to ensure the quality standards and practices of wood acquisition and plantation farming.
Site Furnishings
Manufacturers of pedestal deck systems also offer coordinated, modular elements that are designed to integrate with their deck systems while giving the architect complete design flexibility. Modular wood cubes are available with an array of design options to incorporate seating, storage, and planters. Such cubes are available with a polyurethane lining and drainage holes to host plant life. At other times of the year, the cubes can be repurposed for seating and storage of seasonal items (i.e., cushions and pillows) by placing a manufactured hardwood top on the cube.
If a different look is desired, aluminum cubes are also an option. Designed to withstand temperature extremes, these low-maintenance, durable planters are constructed of lightweight, partially recycled aluminum. Some use an industrial-strength powder-coated finishing process that is applied electrostatically and cured under heat, creating a more resilient finish than conventional paint. There are a variety of sizes and color choices available.
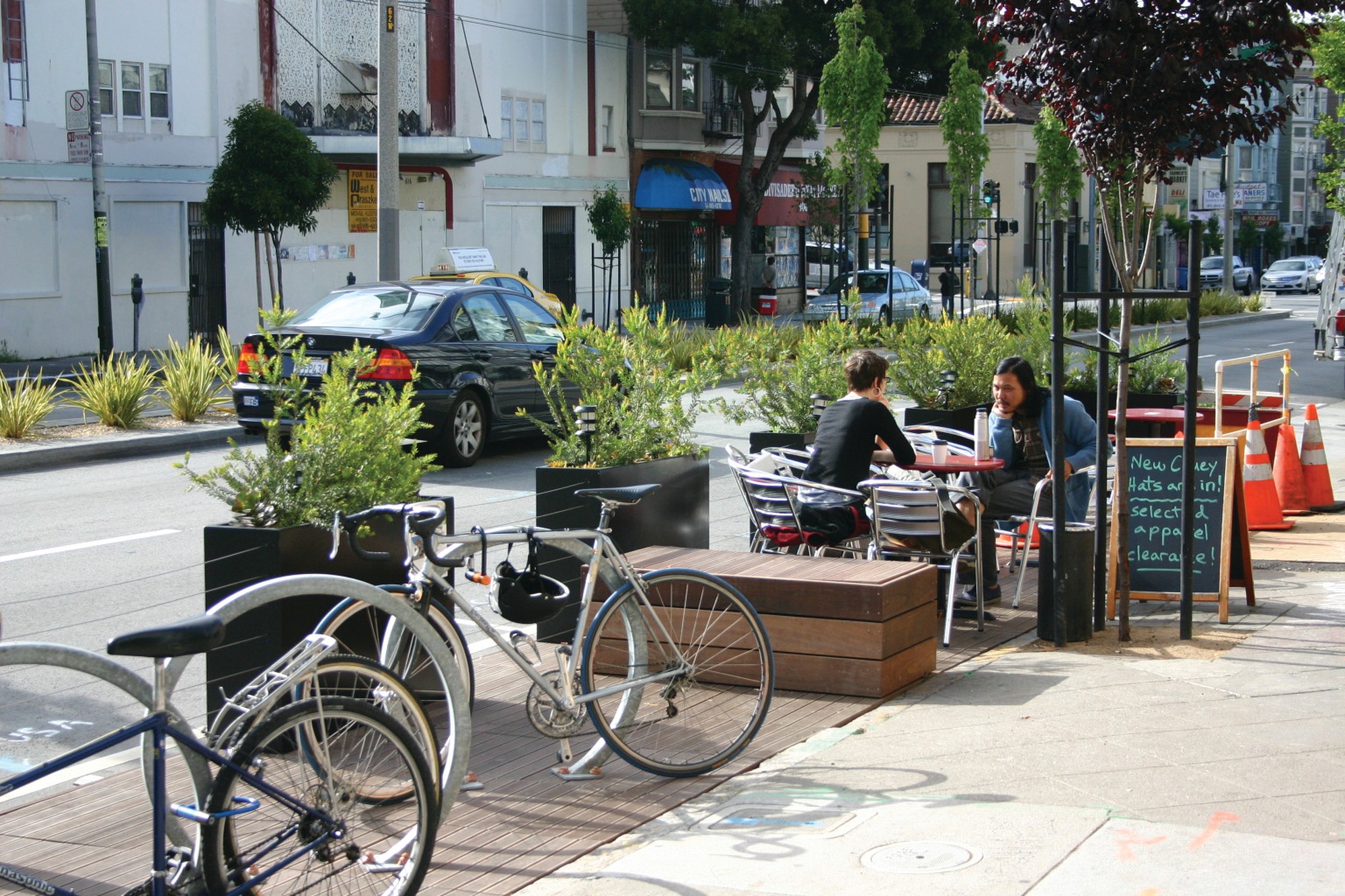
Photo courtesy of Bison Innovative Products
Standard outdoor deck components can be customized and used to create outdoor spaces such as “Pop-up Parks” consistent with changing needs.
Flooring Replacement or Renovation Using Terrazzo
One of the heaviest used surfaces in any building is the flooring. Therefore, in any renovation or adaptive reuse project, it is likely one of the first interior design elements to be addressed. The use of terrazzo has long been regarded as an ideal choice for a variety of adaptive reuse applications.
Fundamentally, terrazzo is a composite system consisting of either a cement or resinous matrix (binder) with aggregates added that can be made of marble, granite, onyx, or glass. Terrazzo is most commonly poured-in-place, cured, and ground to a smooth hard surface finish. There are also pre-cast terrazzo products available that can be installed like tiles or that can form stair treads and risers. As such, it is commonly used for flooring, stairs, and even corridor walls whenever durable, easy-to-clean, and attractive surfaces are sought. In adaptive reuse and renovation projects, terrazzo can play a significant role whether the existing flooring is terrazzo or something else.
- Renovating Existing Terrazzo: Properly maintained, existing terrazzo will likely last the life of the building. However, sometimes it needs some refreshing, perhaps due to neglected maintenance, changes in building use, or new interior designs or layouts. In these cases, it is fairly simple to make existing terrazzo flooring look like new for very little cost. Fundamentally, the process involves the repair and re-polishing of the existing surface. This can restore the shine, bring back the original colors, and make it easier to maintain going forward.
- Renovating Buildings with New Terrazzo: Existing buildings are a prime candidate for cost-effective flooring upgrades using terrazzo. There are lightweight formulations that make it ideal for upper floors by not adding undue dead loads to the structure. It is also a very sustainable and durable choice for projects seeking to meet green building and sustainability goals.
- Dividers: Beyond the basic materials of the terrazzo, metal dividers are used for both design and performance reasons. Dividers can be set to separate colors or as an accent themselves. Beyond the decorative aspect, dividers are primarily used to maintain the integrity of the terrazzo over concrete. Their proper use and placement help overcome any potential cracking in the terrazzo. That is because terrazzo by itself is not likely to crack but can be impacted by the substrate below it which, if it cracks, can telegraph up into the terrazzo surface.
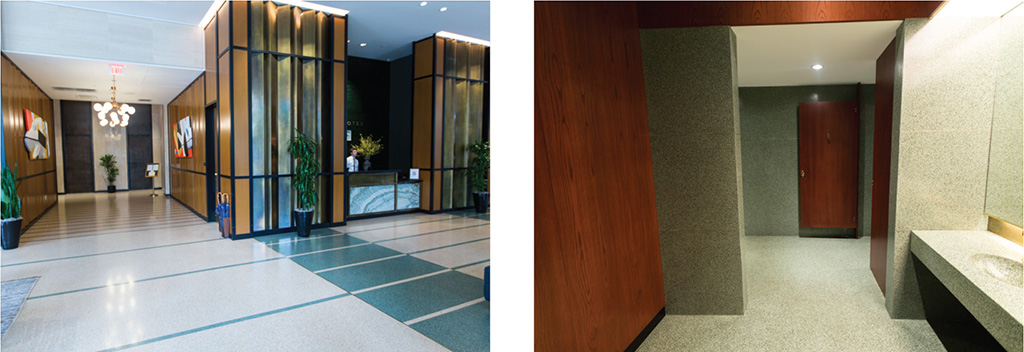
Photos courtesy of National Terrazzo and Mosaic Association (NTMA)
This 1970s era bank building in Nashville was renovated into a boutique hotel using new terrazzo flooring as a key design element for floors, some walls, and other locations.
Terrazzo Design Versatility
Perhaps most appealing to many architects and interior designers is the versatility of terrazzo. The custom nature of terrazzo installations means that designs of all types, patterns, and colors can be incorporated into flooring, walls, stairs, platforms, balconies, countertops, walls, columns, or other surfaces. For example, imagery such as logos, government seals, mascots, maps, historical events, scientific facts, numbers, or other purposeful information can be displayed on the floor or walls of a lobby or public space. In large facilities, wayfinding information can become part of the terrazzo design to help building users and visitors become oriented and find specific areas of a building. In other cases, a simple pattern can be used to create a subtle background for a space or for some featured coloring along a corridor or other circulation space. In short, the vast color, shape, pattern, and design options provide great freedom to create spaces that can meet virtually any design intent.
Terrazzo Performance
While some flooring and surface treatments might look good when first installed, their long-term performance may be lacking. Terrazzo, on the other hand, is well known for its ability to hold up and continue looking great over the long term. There are countless historic buildings where the original terrazzo looks just as good as when first installed. Further, terrazzo has been documented numerous times to withstand not only normal wear and tear but dramatic events such as floods and hurricanes as well.
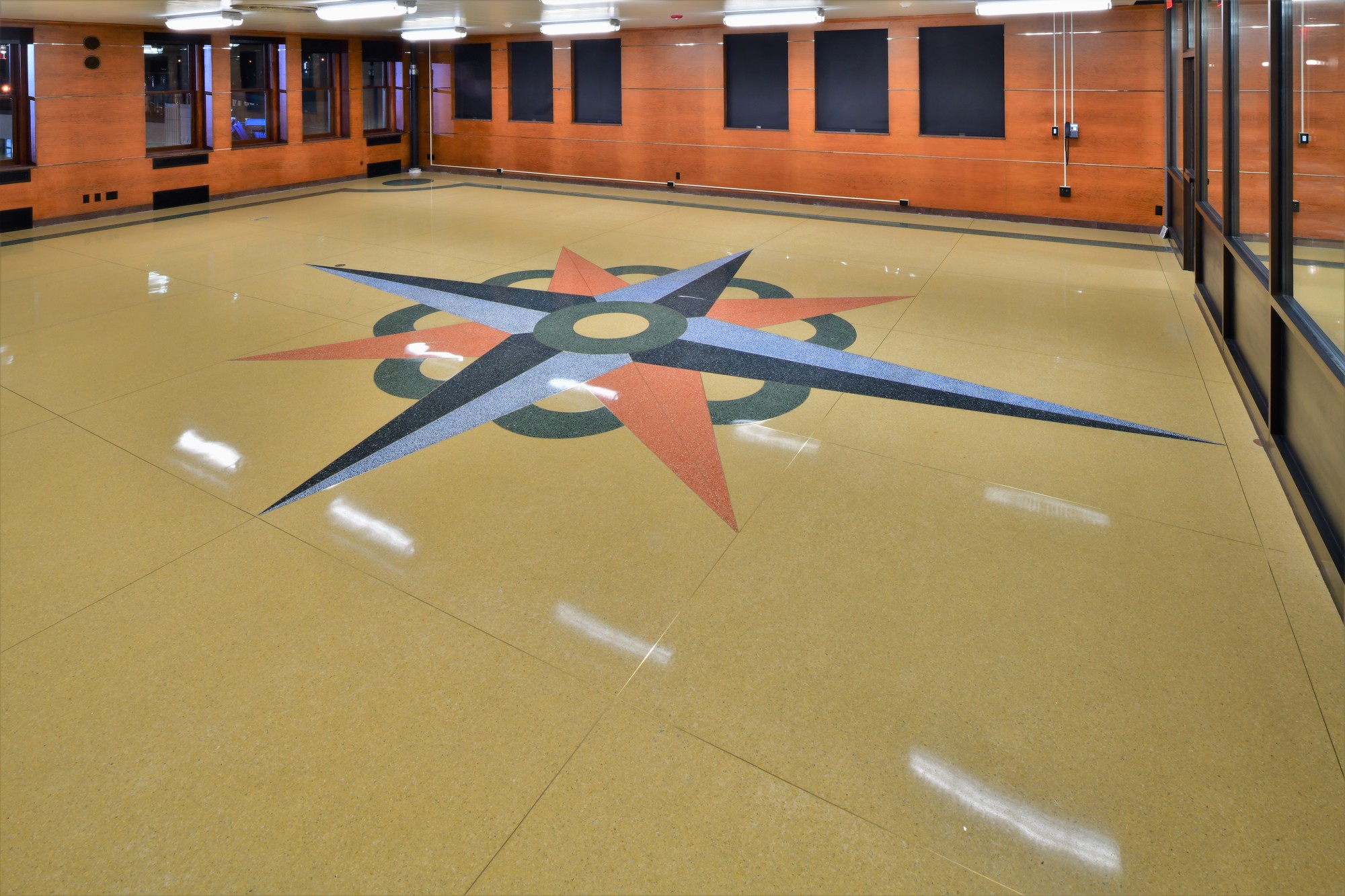
Photo courtesy of National Terrazzo and Mosaic Association (NTMA)
When a school in Illinois was flooded, the terrazzo floor remained intact, needing only cleanup work. The vinyl tiles elsewhere popped up, so the school decided to extend the terrazzo into those areas, too, for greater resilience.
Among the factors that contribute to this impressive performance, the first is the inherent strength of the materials. Terrazzo has been shown repeatedly that it can readily hold up to heavy foot traffic or other demands. This helps with maintenance and sanitary conditions too, since the non-absorbent sealed surface keeps dirt and debris on top while resisting staining. When epoxy terrazzo is used, color control, resiliency, chemical resistance, and tensile-compressive strengths are all increased compared with cement-based systems.
Terrazzo Installed Over Existing Flooring
Contrary to what some design professionals may think, new installations over existing flooring in building renovations don’t always require the existing flooring to be demolished or removed. In some cases, with a proper assessment, existing flooring can be determined to be sound and secure enough to remain in place, perhaps requiring only spot repairs where needed, and mitigating height adjustments at doorways and transitions to adjacent flooring materials. As such, it can serve as the substrate for a terrazzo installation thus saving dramatically on project costs since demolition, removal, and disposal of the existing floor may be avoided.
What types of pre-existing flooring are appropriate? The National Terrazzo and Mosaic Association (NTMA) is the recognized authority for best practices and standards for terrazzo work. They have provided detailed guidance for very successful terrazzo installations over many hard surfaces, including quarry tile, polished concrete, ordinary concrete, and even hardwood flooring. In certain cases, it can also be used over properly installed and prepared plywood. Of course, it is not suitable to go over soft goods such as vinyl tile, sheet goods, carpet, etc.
Working with Terrazzo
When considering the use of terrazzo for an adaptive reuse or building renovation design, there are several things to keep in mind regarding optimizing both design and performance. Some of that starts by overcoming misconceptions about the material. First is the myth that terrazzo is only for new construction, which is clearly not the case, since it is used widely in adaptive reuse projects. Second, there is the misperception that terrazzo takes too long to install, which is also belied by the numerous projects where it has worked smoothly into the overall schedule. Finally, there is a misperception that 3 inches of material are needed to install terrazzo which is very outdated thinking since formulations of less than one-half inch are common.
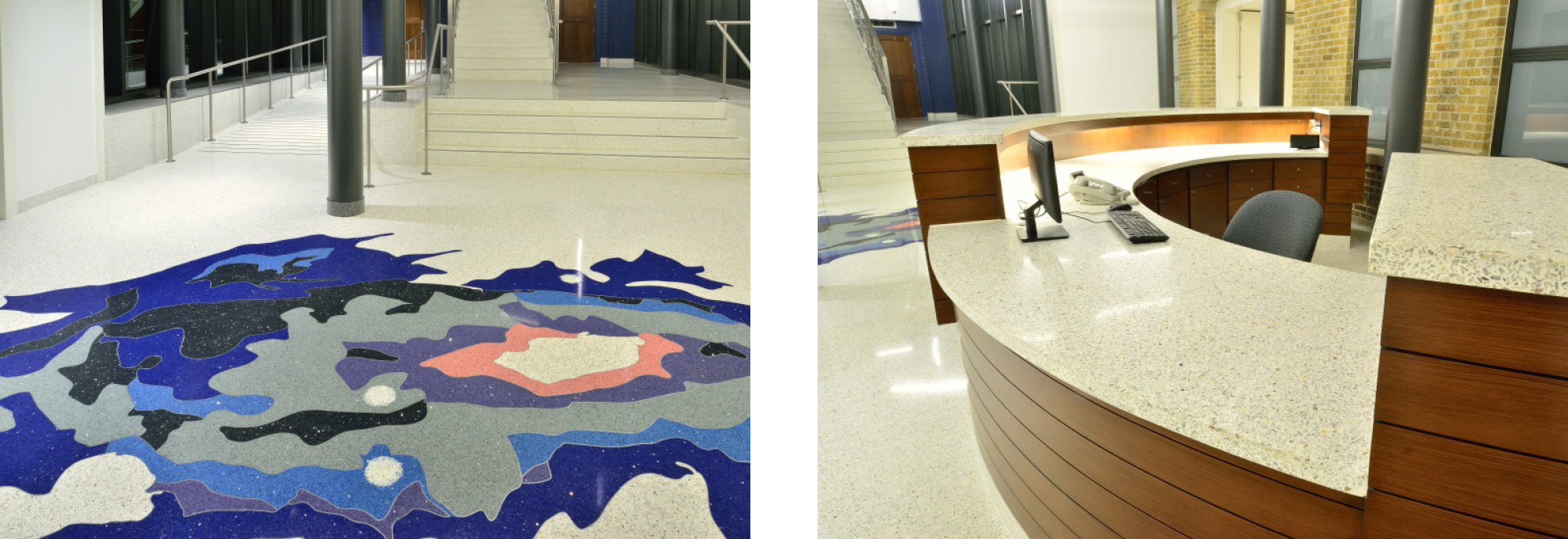
Photos courtesy of National Terrazzo and Mosaic Association (NTMA)
Different types of terrazzo can be used to meet different needs while creating designs to upgrade an existing building like the one shown here near New Orleans.
Current Formulations
While terrazzo has in fact been used for centuries, new formulations are available that are being widely used and sought after because of the design and long-term benefits it provides. These include the following:
- Epoxy Terrazzo: This is a nominal 1/4” or 3/8”-thick resin matrix veneer placed upon a level concrete slab. It can be specified with glass, synthetic, or granite aggregates in lieu of marble to provide brilliant colors or chemical resistance. Recognized as the best “thin set” system, it accounts for approximately 95 percent of all the terrazzo installed today. It offers unlimited matrix colors, color control, resiliency, chemical resistance, and tensile-compressive strengths not found in cement-based systems. It is excellent for multi-colored patterns and designs. Epoxy Terrazzo is lightweight (approximately 4-1/2 PSF for 3/8” thickness) and somewhat flexible making it ideal for multi-story use. It has the lowest maintenance cost due to epoxy’s non-absorbency. In sanitary areas, it can be installed with minimal dividers providing seamless characteristics. When used in conjunction with a flexible membrane, it can absorb some horizontal concrete crack or control joint movement. From an installation standpoint, it has the quickest pour-to-grind installation time. It can be used over a variety of properly installed and prepared substrates including plywood.
- Polyacrylate Terrazzo: A nominal 3/8” think polymer-modified cement matrix veneer is placed upon a flat concrete slab provided by others. The polyacrylate polymer provides strength to allow for thinner applications of cementitious systems. It provides fast installation and moderate price range making it ideal, similar to epoxy, to replace vinyl or carpet without depth transition difficulties. It is also good to use in areas subject to moisture vapor transmission where Epoxy Terrazzo or other non-breathing floors require additional steps to make them applicable.
- Monolithic Terrazzo: This is a 1/2”-thick cement matrix veneer placed upon a concrete slab provided by others. It is dependent on the concrete quality for flatness and crack prevention. It is appropriate for on-grade or below-grade. Its fast installation and economical price make it ideal where time and budget are critical but where the beauty, low maintenance, and performance of terrazzo are desired.
- Bonded Terrazzo: A cement matrix and underbed system used for interior and exterior areas. It is meant for conditions that require 1-1/4” to 1-3/4” of recessed depth to be filled in addition to the 1/2” terrazzo topping. With the sand-cement underbed, it has less dependence on the concrete slab for flatness compared to monolithic.
- Sand Cushion Terrazzo: A ½” cement matrix topping is used with a 2-1/2–3” underbed of low-slump sand cement. The complete system includes wire reinforcing, isolation sheet, and a sand dusting layer over a new or existing concrete slab. As an independent system, and unbonded from the substrate, this is considered the best cement system and is intended for interior use. Due to the underbed’s depth, wire mesh reinforcing, isolation sheeting, and sand layer, it will absorb minor substrate defects and prevent mirroring to the surface.
- Rustic Terrazzo: This is a terrazzo produced with a non-ground, textured surface intended for exterior use. This system is available with Bonded and Monolithic Terrazzo. It offers infinitely variable textures, colors, and patterns that may be created in a weather-resistant, skid-resistant deck surface.
Note that in any of these terrazzo formulations, the aggregate chip sizes used can be selected to suit the intended design appearance. The sizes are only limited by the thickness of the terrazzo such that chips can be #0 or #1 in ¼” terrazzo with the option of #2 in 3/8” terrazzo. Venetian terrazzo that uses size #3-#7 chips as well as Palladiana terrazzo that utilizes large broken pieces of marble both require ½”. As mentioned, marble, and granite, are the most common type of aggregate, but other types are possible. The use of glass and other decorative aggregates can increase costs.
Modernizing Plumbing
Renovating or modifying an existing building, particularly an older building, means addressing ways to upgrade the mechanical, electrical, and plumbing (MEP) systems to meet current standards and user expectations. That often creates challenges in a number of ways including the following:
- Existing Building Shell: Architects can be faced with the need to meet current code requirements and apply them to existing (often historical) buildings, particularly if there is a change of use or occupancy. Yet there may also be preservation or budget requirements that limit the work that can be done in existing buildings. Hence, there is a strong need to find ways to upgrade MEP systems that are compatible with adaptive reuse, can work within the existing building structure, and comply with requirements for historical buildings.
- Space Optimization: Space is often at a premium in renovation projects as new user programs try to work within existing geometries. There may also be a requirement from building owners to make as much square footage usable or rentable as possible without encroachment from utilitarian things such as plumbing chases or walls enlarged to carry MEP lines. Finding systems that don’t further encroach on usable space, can re-use existing supply and drainage lines, and minimize floor coring are all desirable in this regard. It also means keeping plumbing chase or MEP walls minimized to allow for increased space usage or revenue generation.
- Regulatory Compliance: Current codes and standards need to be followed whenever MEP systems and fixtures are upgraded. Future planning comes into play too since actual construction may take place months after design document completion. For example, the EPA is planning to revise specifications for Water Sense dual-flush toilets, effective July 1, 2025, which will require a maximum of 1.28 gallons per flush for both single-flush and full-flush modes of dual-flush toilets.
- Cost-Effective Solutions: All of the above is typically carried out in the context of needing to control construction costs both in terms of material costs and labor efficiency for simplified installations.
Successfully navigating these challenges— existing building shells, space optimization, regulatory compliance, and cost-effectiveness —often requires an integrated approach to plumbing design, making solutions like in-wall mounted toilet systems a valuable asset in streamlining renovations and new builds alike.
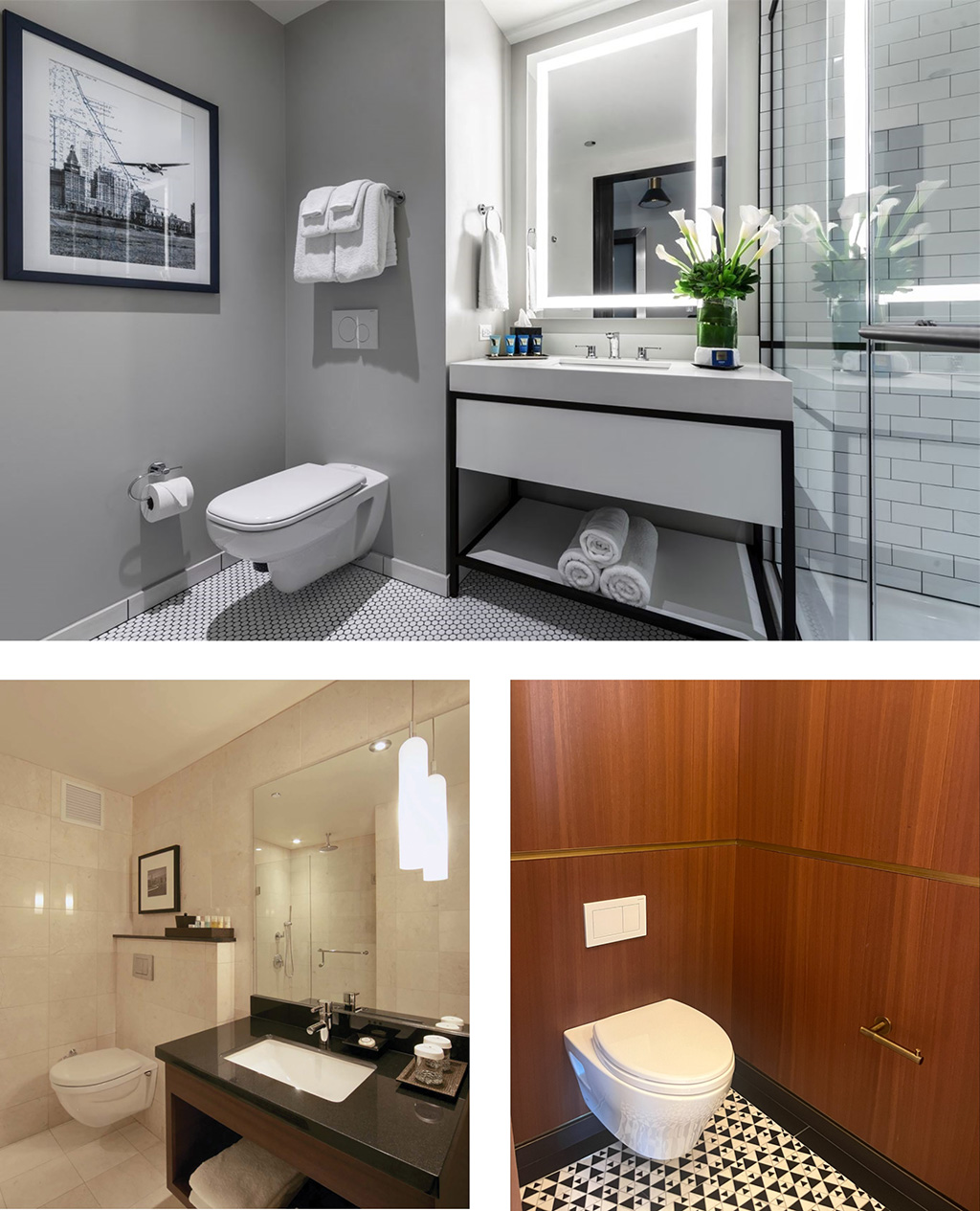
Photos courtesy of Geberit
In-wall concealed toilet tank carrier systems and dual flush plates transformed these hotel and multifamily projects by overcoming space constraints, and offering a sustainable and sleek solution for modern bathrooms in repurposed buildings.
In-Wall Mounted Toilet Systems
A good example of how to address MEP renovation and design upgrade questions is by looking at bathrooms or restrooms in an adaptive reuse/renovated building. Existing site conditions often limit design options, but in-wall carrier systems help to maximize space and simplify cleaning as the flooring can run beneath the toilet. Where every inch in a bathroom is important, saving up to nine inches with the tank in the wall makes a big difference. Plus contractors can take advantage of existing stack locations and plumbing chases. Wall-mounted, concealed-tank toilets avoid core drilling, and minimize the number of new plumbing chases required.
In terms of accessible design, the wall-mounted units can provide the added inches needed to meet clearances for maneuverability. The height of the toilet is also readily adjustable to meet accessibility standards where needed or provide standard heights where otherwise preferred and acceptable. The system typically includes wall-mounted, recessed actuators above the toilet since the tank is not visible for a flush valve handle or buttons. These actuators are essentially large buttons making them easier to use than standard options and thus more accessible for more people. Typically, two actuators are present for dual flushing capability—built-in dual flush saves up to 6,000 gallons annually. This, coupled with typically smaller water storage tanks, equates to a more sustainable lower water use, and related cost savings. In many cases, touchless flushing, with hands-free activation, is also available where that option is desired or needed.
Overcoming Misperceptions
There are some misperceptions or questions that exist about wall-mounted plumbing fixtures, addressed as follows:
- Are These Challenging to Plan? While wall-mounted fixtures require careful planning, they are not inherently more challenging than traditional fixtures. The key is to collaborate closely between the design team and plumbing contractors or suppliers during design. This is particularly true in existing buildings where the existing plumbing infrastructure needs to be considered. Precise measurements and placement are needed in the field, of course, the same as with any plumbing installation, but some manufacturers offer a frame that allows greater flexibility in piping. This is especially important in reuse projects where it is desirable to use existing waste pipe locations while allowing flexibility on where to mount wall-hung toilets.
- How Difficult Are They to Install? Many people mistakenly believe that wall-mounted fixtures are significantly more complex to install than traditional ones. However professional plumbers with experience can handle the installation as efficiently as any other fixtures. Many manufacturers provide detailed installation guides to facilitate proper installation in either 2” x 4” or 2”x 6” wood or metal framing. With proper planning, installation can be fast and efficient.
- Does the cost make sense for building owners? It is critical to look at the long-term benefits in order to realize full value. In-wall carrier systems save on coring and plumbing costs at onset and lead to more usable space, water savings, and potential increased property value in the future.
- Are They Only for Contemporary Designs? Wall-mounted actuators and toilets are versatile and can complement various design styles—they can be integrated into traditional, transitional, or modern designs. A wide range of flush plate finishes and styles are available to suit different aesthetics. In-wall carrier systems are suitable for various bathroom sizes and layouts, especially for urban areas where real estate is at a premium.
- Are Wall-Hung Toilets as Strong or as Reliable as Floor Mounted Toilets? Wall-hung toilets are extremely strong. In-wall frame systems are typically designed to hold weights of more than 800 pounds. Wall-hung toilets have been in use in Europe for over 50 years, and the high-density plastic tank is durable and lasts for a long time. There are millions installed globally, and are proven as well-established and reliable technology.
By addressing these misconceptions, architects and designers can make more informed decisions about incorporating wall-mounted fixtures in their projects, potentially leading to more innovative and efficient bathroom designs.
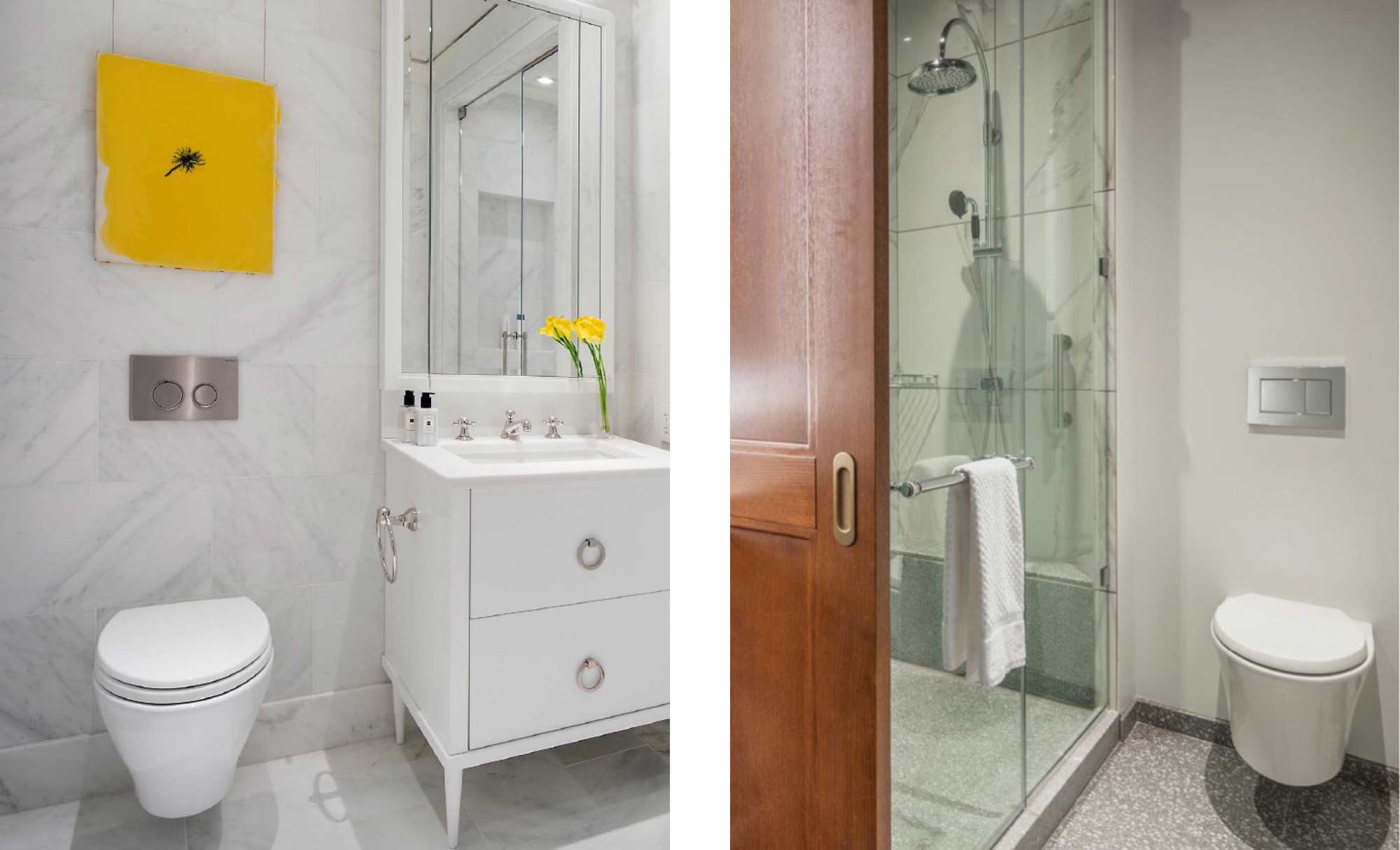
Photos courtesy of Geberit
Wall-hung toilet systems are being successfully used in a variety of building types with different design styles and aesthetics.
Wall-Hung Toilet Installations
It is clear that sanitation, safety, and sustainability have been and will remain important considerations for all users of renovated buildings and are regulated by well-known standards and codes that in-wall toilet systems are proven to meet or exceed. These include the International Building Code (IBC), International Plumbing Code (IPC), the Universal Plumbing Code, and the National Plumbing Code of Canada (NPCC) as well as standards of the American Society of Plumbing Engineers (ASPE), the American Society of Mechanical Engineers (ASME). In-wall carrier systems accommodate the leading toilet brands, with many combinations also meeting the EPA WaterSense® standards and counting towards LEED points.
Based on these codes and standards, one common design goal in restrooms is to control the amount of water used. This is particularly true for flushable toilets where the design of the flow mechanism and the controls that actuate it are critical. Wall-hung toilets and touchless flush pates are becoming the new standards in many cases since they offer superior features in performance as well as design. In particular, those that use in-wall tanks concealed from view and user access provide improved water flow control with cleaner looks, quieter operation, and the potential for cleaner restrooms in general.
While some may think that a high-performance toilet solution needs to look clinical or austere, the reality is that there are contemporary design alternatives. That means architects do not have to lose their design concepts to achieve critical performance features. Rather, there are innovative product solutions that meet the demand for sanitation, safety, and sustainability while also providing a high level of design. In order to accommodate a range of different project types, particularly for renovation, retrofit, or adaptive re-use, there are multiple options available. Beyond the aesthetic benefits, there are also clear space savings achieved by recessing the toilet tank system into the wall, allowing for more usable space in restrooms in many cases.
In addition to better water control that is available from dual flush actuators, in-wall systems are a reliable and high-quality solution for designing contemporary bathrooms that meet the demands of all involved. Overall sanitation and safety are improved by having less of the toilet system exposed and the bowl raised up from the floor. This adds to the comfort and convenience for users as well as ease of cleaning for janitorial crews. In terms of maintenance, all working parts remain easily accessible, although the high reliability of this type of unit reduces the need for maintenance crews to access it in the first place. Commonly, the support frame is based on solid steel construction with a seamless, one-piece tank made of durable, leak-free, high-density polyethylene.
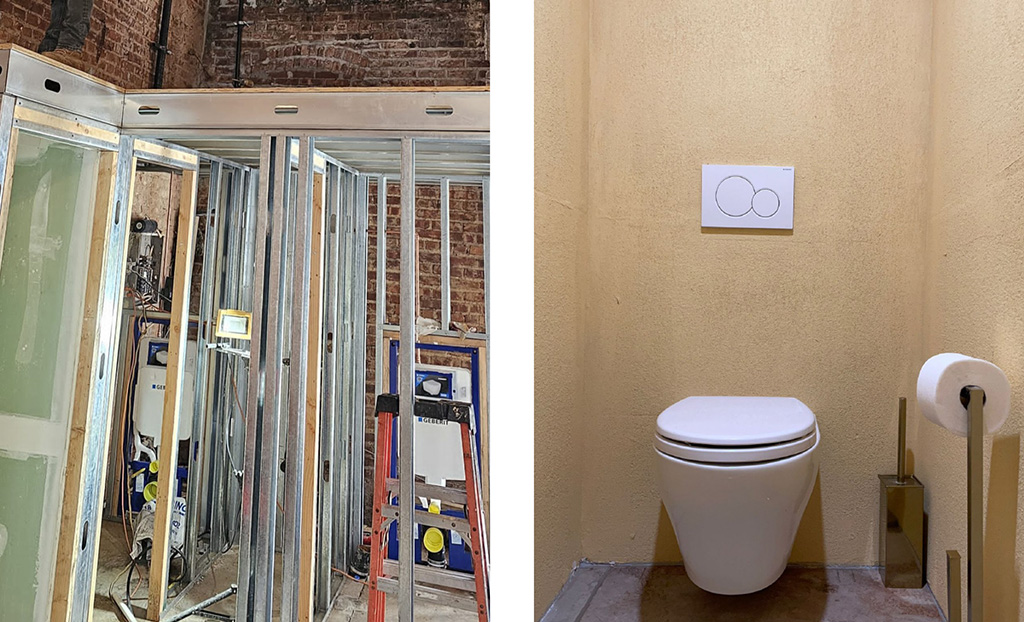
Photos courtesy of Osher Bier Construction
The use of in-wall toilet tank carrier systems, even in the conversion of a 100-year-old single-story building, makes it easier to clean under and around the toilet while freeing up valuable floor space.
Conclusion
Working to improve or transform an existing building requires blending the existing conditions with current user needs, code requirements, accessibility standards, and methods of construction. Outdoor spaces should be considered as part of any such existing building renovation with many potential benefits for users, occupants, and owners. Renovating flooring to meet current demands and correct safety issues has been shown to be done quite effectively using modern terrazzo techniques. Upgrading MEP systems by embracing innovative solutions like in-wall installation toilet systems, specifiers can successfully transform existing buildings into sustainable and user-friendly spaces for the future. Incorporating some of the concepts and ideas presented in this course can benefit architects and designers and their projects.
Peter J. Arsenault, FAIA, NCARB, LEED AP is a nationally known architect who has authored nearly 300 continuing education courses focused on advancing building performance through better design. www.pjaarch.com, www.linkedin.com/in/pjaarch