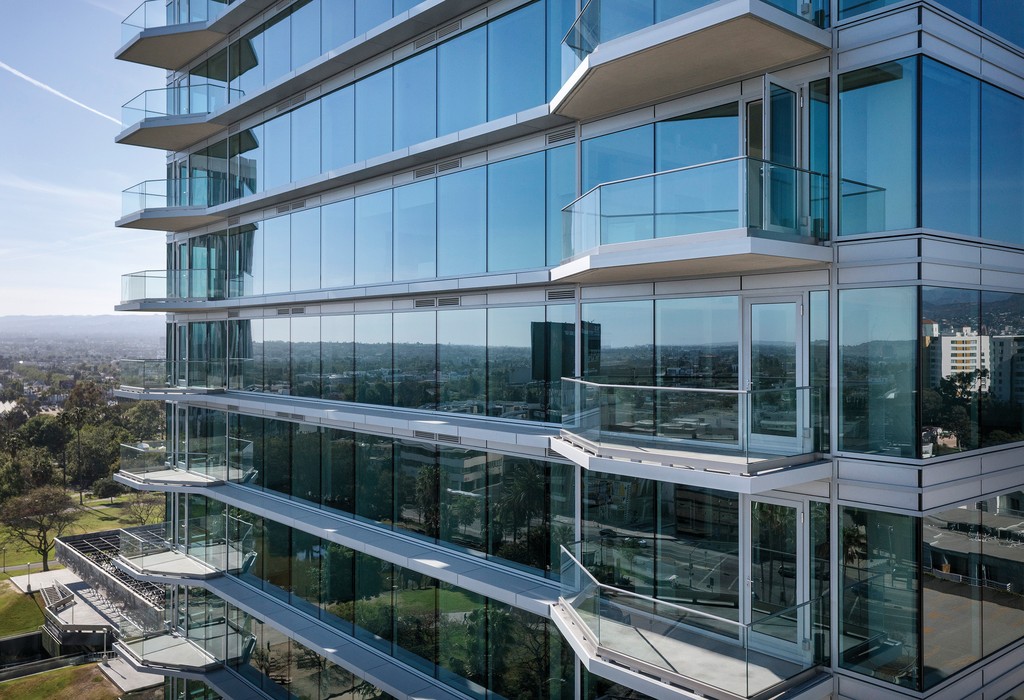
Photo courtesy of CRL; © Chipper Hatter
Multifamily buildings of all types hold the promise of affordable, sustainable, and very livable housing solutions for a growing number of people.
It’s no secret that it has been getting tougher for Americans to find and even afford the housing of their choice in a lot of different cities and towns across the country. Many of the reasons for this are outside of an architect’s control such as the general economy, interest rates, and the changing nature of housing supply and demand. Nonetheless, architects are continuing to be asked to meet the critical demand for multifamily housing for many different income classes with units being offered by developers either for rent or sale. In many cities, this has been serving a basic need, since some multifamily units are often seen as the new “starter home.” In other cases, the market is being transformed with an influx of luxury or higher-end housing catering to changing demographics and evolving households. The ability of many people to work remotely away from an employer’s workplace is also clearly influencing some housing markets but also bringing the need for workspaces to be designed as an integral part of the design of residential units. All of this is coupled with the ongoing need and market desire for sustainable construction that reduces energy use and provides green building construction. This course reviews all of these issues with some specific approaches focused on achieving appealing, well-designed, multifamily housing solutions.
Efficient Structural Systems
There are always choices for determining the best structural system to use for a particular multifamily project. Often, the size and height directly influence the final selection since different systems are better suited or more economical for different situations. Low-rise construction (3-4 stories) will likely be most economical using wood framing though other types of construction make sense if prioritizing long-term investment. For larger projects, creating multifamily buildings that are between 5-12 stories often makes sense for density and economy. It can, however, be overwhelming to weigh all of the pros and cons of different structural systems for design flexibility and cost-effectiveness. For this type and size of multifamily building, the most common structural systems are based on either post-tension concrete or composite steel construction. The selection is typically determined by the specific criteria and needs of a given project not only for structural capacity, but for fire, acoustics, and bay size. Some of those criteria are dictated by code and life safety concerns while others by comfort and marketing issues.
Composite steel construction design takes advantage of the complementary relationship between concrete and steel. The engineered combination of the two materials provides great strength with notably less weight than typical concrete construction. In many cases, this type of floor system can be supported by bearing walls of conventional metal framing of cold-formed steel (CFS). Properly engineered and specified, this composite approach creates a long-span, non-combustible floor system that has been used quite effectively in apartments, hotels, student housing, and assisted living facilities. While such an approach can be used on any size or type of project, it has been found to be particularly appealing when building heights approach 75 feet or greater – all the way up to 12 stories.
Attributes of Composite Structural Systems
Composite steel deck and concrete systems supported by CFS framing generally incorporate thinner floor slabs and lighter-weight construction compared to many of the alternatives. As such, they are known for the following attributes.
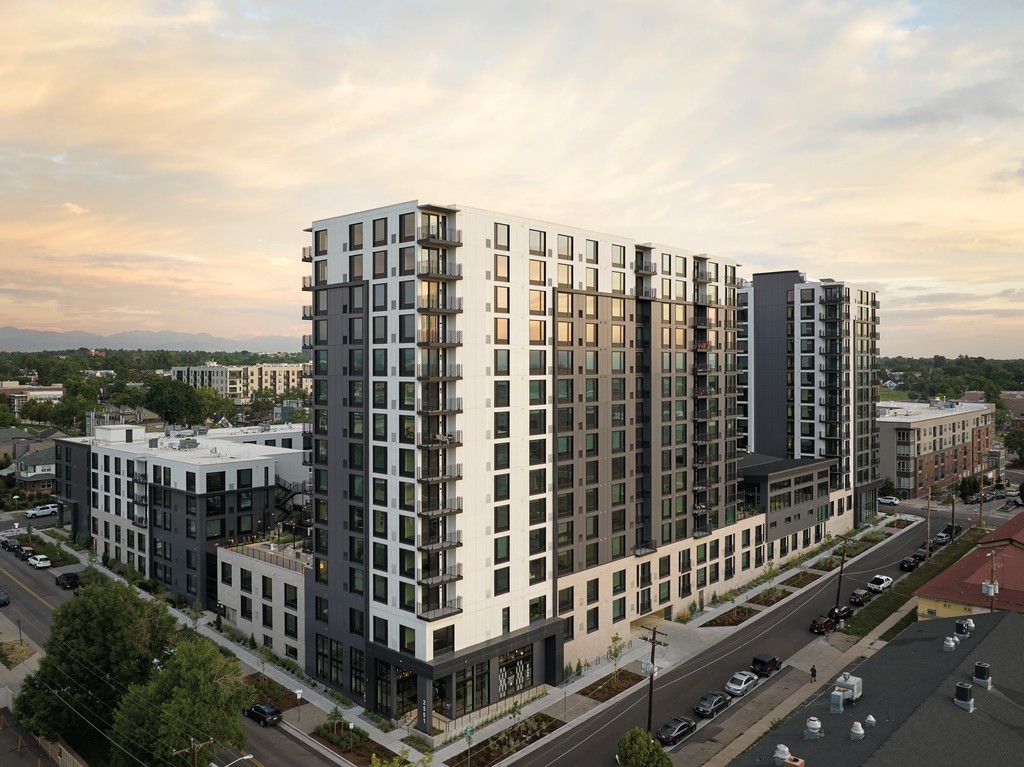
Photo courtesy of New Millennium
Multifamily buildings constructed using composite floor construction have many attributes that contribute to buildings that are better designed, more efficient, and cost-effective.
- Design Flexibility: Composite system design takes advantage of the complementary relationship between concrete and steel, maximizing design flexibility. There are solutions for designs that choose to expose the composite system, whether using the steel deck as a ceiling or the concrete as a floor for an industrial aesthetic. Finished or not, composite decks that use dovetail profiles, as opposed to the conventional trapezoidal deck profile, put greater mass in the bottom of the decking flute. The result is less concrete, eliciting a lighter deck slab with a collection of dovetail composite details to accompany a wide range of structural systems and requirements. This facilitates greater span capacities and lighter overall structural systems.
- Fire Resistance: Concrete is well documented as an excellent material for fire resistance ratings and combining it with dovetail profiled steel decking has been tested for up to 2-hour and even 3-hour ratings. This is a considerable benefit of the system as it achieves increased fire ratings with less concrete and allows the system to be sufficient without the need for additional protection. Deck manufacturers are able to provide UL-rated details for floor assemblies and head-of-wall conditions (perpendicular and parallel to party walls) to assist design professionals in meeting project-specific fire resistance ratings. It is worth noting that traditional composite decks (i.e., trapezoidal) require time-consuming “castle cutting” at the head-of-wall condition – the installer needs to make tracing cuts along the underside of the trapezoidal section at bearing walls. With the dovetail profile, the solution is easy and concise by simply offsetting the flutes of the deck and using break metal where needed following the appropriate UL Rated design details.
- Acoustics: Composite design is beneficial for acoustics, particularly in a multifamily building where sound transmission needs to be controlled between living units. The mass of the materials used is a key for sound attenuation (i.e., Sound Transmission Class (STC) ratings per ASTM E90) as is decoupling the materials to mitigate impact sound transfer (i.e., Impact Insulation Class (IIC) per ASTM E492). The relative mass of concrete and steel in a composite system helps address the sound transfer requirements. The use of finish flooring over sound mats or padding used in concert with furring in the ceiling can easily meet or exceed code minimums for STC and IIC. Proper attention to acoustics also helps with the wellness of the occupants.
- Ease of Construction: Cold-formed metal studs are commonly used in many types of construction with design and installation similarities to building with wood. As such, there is a ready labor force already familiar with building load-bearing light-gauge metal framing walls on metal or composite floor decks. Compared to wood framing, there is also the benefit of meeting fire resistance requirements and reducing the possibility of fire during construction, reducing the cost of Builder’s Risk Insurance. One of the unique features of dovetail profile floor decking is the use of hanging devices that speed up the rate of installation for anything that needs to be suspended (i.e. mechanical, electrical, plumbing, etc.) Specifically, wedge hangers are fabricated to rely on tightening in place rather than drilling through steel and concrete. Such hangers that carry UL ratings save other trades time and effort as they are able to adjust such hangers quickly and easily to respond to different field conditions. Overall, dovetail composite systems combine the quality of post-tension concrete with the labor and material cost stability of platform frame construction.
- Modularity: The panelizing of wall sections in multistory buildings continues to be gaining popularity. In part, this is due to more factory-controlled fabricators being available using modular construction innovations. As such, designers can work with contractors and fabricators to optimize framing solutions to match their design intent. Collaboration on slab design, span, and shoring needs allows for efficient framing that can be adapted to different geographic locations and regional capabilities. Unlike wood framing or light-gauge trusses, the floor or roof members do not necessarily need to align with the CFS studs, allowing for increased tolerance and more flexibility. The expanding ecosystem of prefabricated components adds to the aesthetics, quality, and cost savings of multifamily construction.
- Sustainability: The embodied carbon content of construction materials is a significant concern related to carbon dioxide emissions and global warming. Strategies that reduce the amount of concrete used in buildings are increasingly being used, since concrete as a material is very energy-intensive with a high carbon footprint. Composite structural systems help reduce the amount of concrete used in buildings and thus reduce the carbon footprint of a project. Similarly, the steel components offer longevity and resilience which align with sustainability goals. Steel components routinely contain a significant amount of recycled content and producers have widely adopted innovative energy reduction strategies in production of decking and other products.
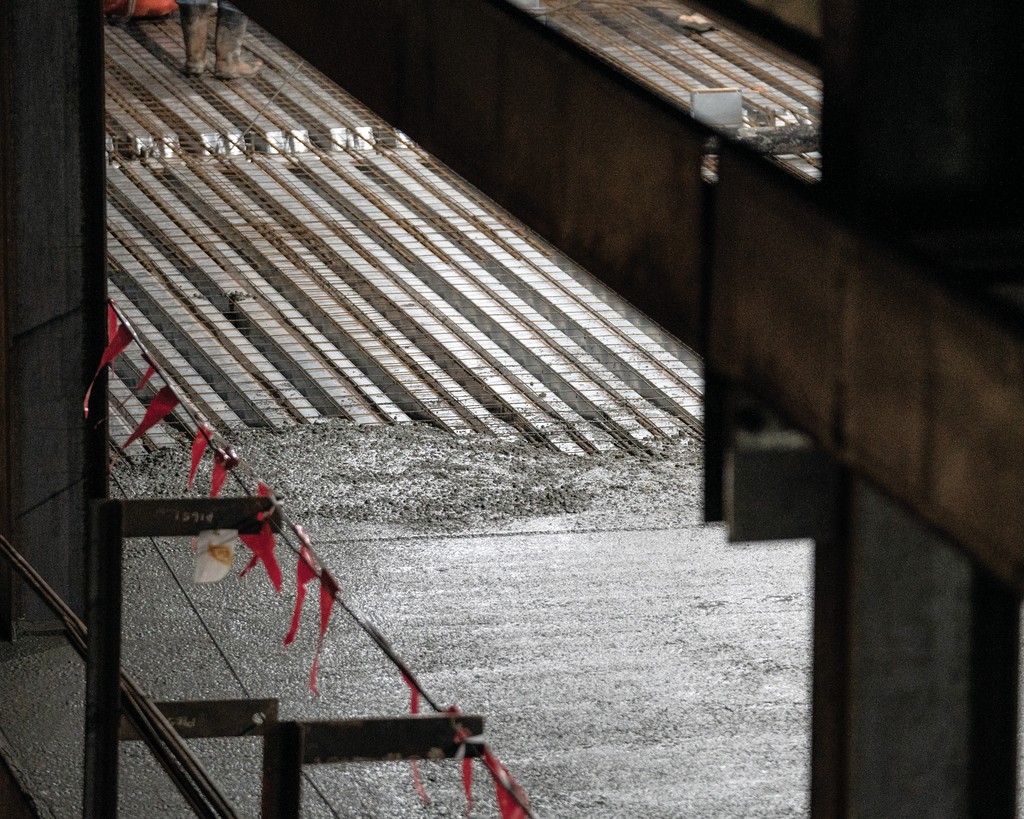
Photos courtesy of New Millennium
After all the deck panels are in place, the concrete pour can be completed to create the composite floor system.
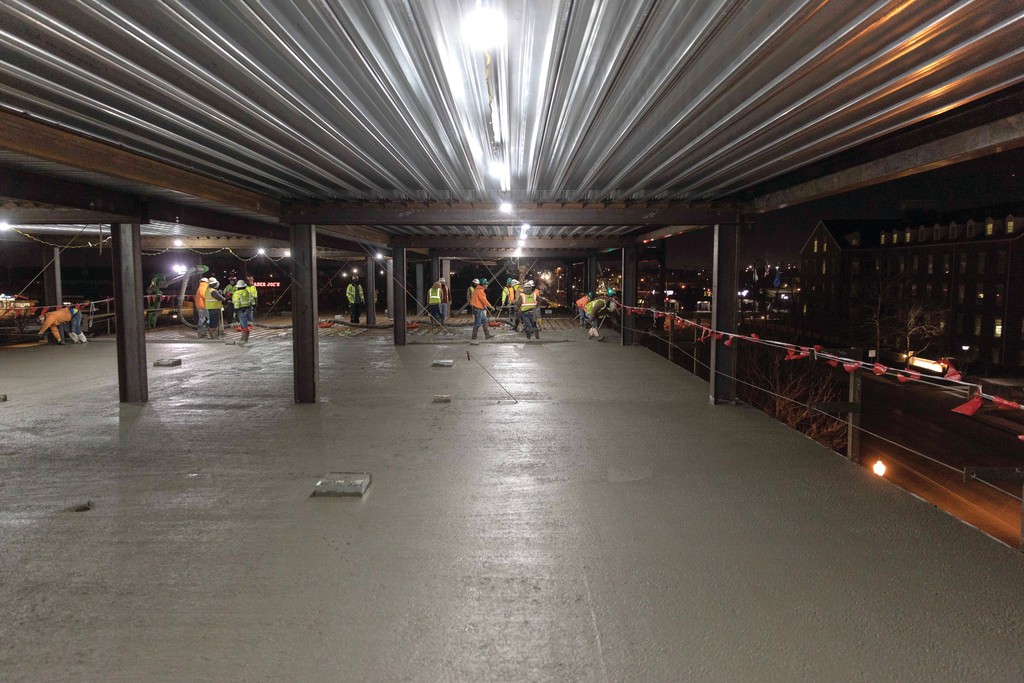
Architects using long-span composite-floor systems can achieve reductions in the construction timeline and the total cost of a multi-story project. Specifying dovetail composite floor deck and CFS load-bearing demising walls have provided a surprising set of cost benefits, compared to other construction approaches such as post-tensioned concrete. For example, the significantly lighter weight dovetail composite floors can often be supported by a spread of concrete footing foundations and may eliminate the need for piles and pile caps in some cases. By virtue of the longer composite floor spans, up to 28 feet, the number of support columns can be reduced and those required can be smaller in girth. During construction, decking spans can reach 16 feet without the need for temporary shoring support. The thinner, faster-curing composite system allows for tighter scheduling of the trades that follow after in the schedule, including plumbing and other rough-in work. There are documented cases where many weeks were removed from the project timeline using this approach.
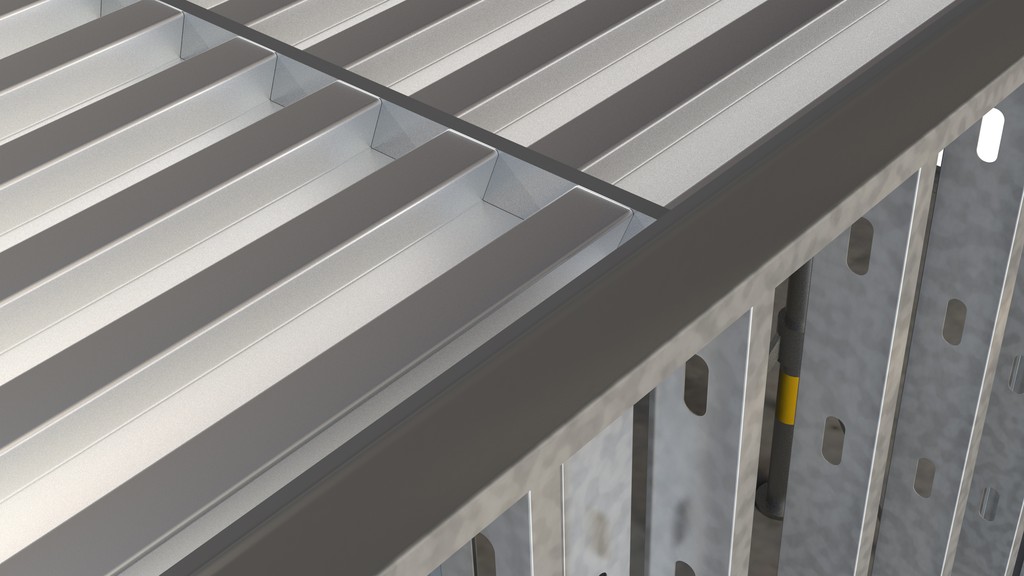
Photo courtesy of New Millennium
Composite steel deck supported by cold-formed steel framing is an economical and effective system for multifamily buildings.
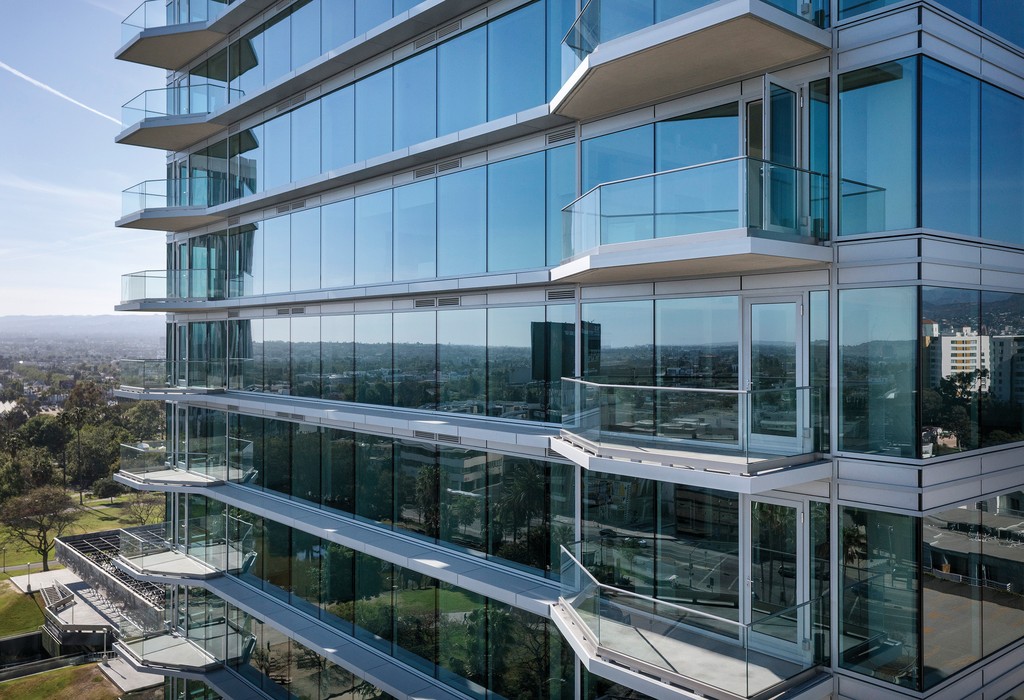
Photo courtesy of CRL; © Chipper Hatter
Multifamily buildings of all types hold the promise of affordable, sustainable, and very livable housing solutions for a growing number of people.
It’s no secret that it has been getting tougher for Americans to find and even afford the housing of their choice in a lot of different cities and towns across the country. Many of the reasons for this are outside of an architect’s control such as the general economy, interest rates, and the changing nature of housing supply and demand. Nonetheless, architects are continuing to be asked to meet the critical demand for multifamily housing for many different income classes with units being offered by developers either for rent or sale. In many cities, this has been serving a basic need, since some multifamily units are often seen as the new “starter home.” In other cases, the market is being transformed with an influx of luxury or higher-end housing catering to changing demographics and evolving households. The ability of many people to work remotely away from an employer’s workplace is also clearly influencing some housing markets but also bringing the need for workspaces to be designed as an integral part of the design of residential units. All of this is coupled with the ongoing need and market desire for sustainable construction that reduces energy use and provides green building construction. This course reviews all of these issues with some specific approaches focused on achieving appealing, well-designed, multifamily housing solutions.
Efficient Structural Systems
There are always choices for determining the best structural system to use for a particular multifamily project. Often, the size and height directly influence the final selection since different systems are better suited or more economical for different situations. Low-rise construction (3-4 stories) will likely be most economical using wood framing though other types of construction make sense if prioritizing long-term investment. For larger projects, creating multifamily buildings that are between 5-12 stories often makes sense for density and economy. It can, however, be overwhelming to weigh all of the pros and cons of different structural systems for design flexibility and cost-effectiveness. For this type and size of multifamily building, the most common structural systems are based on either post-tension concrete or composite steel construction. The selection is typically determined by the specific criteria and needs of a given project not only for structural capacity, but for fire, acoustics, and bay size. Some of those criteria are dictated by code and life safety concerns while others by comfort and marketing issues.
Composite steel construction design takes advantage of the complementary relationship between concrete and steel. The engineered combination of the two materials provides great strength with notably less weight than typical concrete construction. In many cases, this type of floor system can be supported by bearing walls of conventional metal framing of cold-formed steel (CFS). Properly engineered and specified, this composite approach creates a long-span, non-combustible floor system that has been used quite effectively in apartments, hotels, student housing, and assisted living facilities. While such an approach can be used on any size or type of project, it has been found to be particularly appealing when building heights approach 75 feet or greater – all the way up to 12 stories.
Attributes of Composite Structural Systems
Composite steel deck and concrete systems supported by CFS framing generally incorporate thinner floor slabs and lighter-weight construction compared to many of the alternatives. As such, they are known for the following attributes.
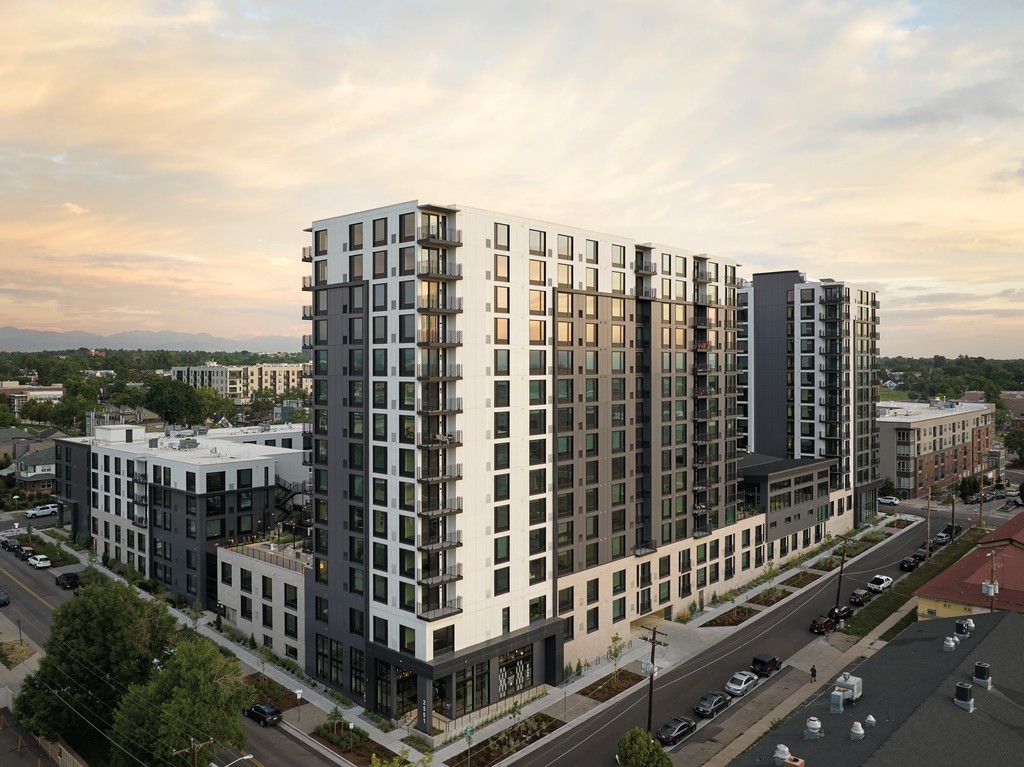
Photo courtesy of New Millennium
Multifamily buildings constructed using composite floor construction have many attributes that contribute to buildings that are better designed, more efficient, and cost-effective.
- Design Flexibility: Composite system design takes advantage of the complementary relationship between concrete and steel, maximizing design flexibility. There are solutions for designs that choose to expose the composite system, whether using the steel deck as a ceiling or the concrete as a floor for an industrial aesthetic. Finished or not, composite decks that use dovetail profiles, as opposed to the conventional trapezoidal deck profile, put greater mass in the bottom of the decking flute. The result is less concrete, eliciting a lighter deck slab with a collection of dovetail composite details to accompany a wide range of structural systems and requirements. This facilitates greater span capacities and lighter overall structural systems.
- Fire Resistance: Concrete is well documented as an excellent material for fire resistance ratings and combining it with dovetail profiled steel decking has been tested for up to 2-hour and even 3-hour ratings. This is a considerable benefit of the system as it achieves increased fire ratings with less concrete and allows the system to be sufficient without the need for additional protection. Deck manufacturers are able to provide UL-rated details for floor assemblies and head-of-wall conditions (perpendicular and parallel to party walls) to assist design professionals in meeting project-specific fire resistance ratings. It is worth noting that traditional composite decks (i.e., trapezoidal) require time-consuming “castle cutting” at the head-of-wall condition – the installer needs to make tracing cuts along the underside of the trapezoidal section at bearing walls. With the dovetail profile, the solution is easy and concise by simply offsetting the flutes of the deck and using break metal where needed following the appropriate UL Rated design details.
- Acoustics: Composite design is beneficial for acoustics, particularly in a multifamily building where sound transmission needs to be controlled between living units. The mass of the materials used is a key for sound attenuation (i.e., Sound Transmission Class (STC) ratings per ASTM E90) as is decoupling the materials to mitigate impact sound transfer (i.e., Impact Insulation Class (IIC) per ASTM E492). The relative mass of concrete and steel in a composite system helps address the sound transfer requirements. The use of finish flooring over sound mats or padding used in concert with furring in the ceiling can easily meet or exceed code minimums for STC and IIC. Proper attention to acoustics also helps with the wellness of the occupants.
- Ease of Construction: Cold-formed metal studs are commonly used in many types of construction with design and installation similarities to building with wood. As such, there is a ready labor force already familiar with building load-bearing light-gauge metal framing walls on metal or composite floor decks. Compared to wood framing, there is also the benefit of meeting fire resistance requirements and reducing the possibility of fire during construction, reducing the cost of Builder’s Risk Insurance. One of the unique features of dovetail profile floor decking is the use of hanging devices that speed up the rate of installation for anything that needs to be suspended (i.e. mechanical, electrical, plumbing, etc.) Specifically, wedge hangers are fabricated to rely on tightening in place rather than drilling through steel and concrete. Such hangers that carry UL ratings save other trades time and effort as they are able to adjust such hangers quickly and easily to respond to different field conditions. Overall, dovetail composite systems combine the quality of post-tension concrete with the labor and material cost stability of platform frame construction.
- Modularity: The panelizing of wall sections in multistory buildings continues to be gaining popularity. In part, this is due to more factory-controlled fabricators being available using modular construction innovations. As such, designers can work with contractors and fabricators to optimize framing solutions to match their design intent. Collaboration on slab design, span, and shoring needs allows for efficient framing that can be adapted to different geographic locations and regional capabilities. Unlike wood framing or light-gauge trusses, the floor or roof members do not necessarily need to align with the CFS studs, allowing for increased tolerance and more flexibility. The expanding ecosystem of prefabricated components adds to the aesthetics, quality, and cost savings of multifamily construction.
- Sustainability: The embodied carbon content of construction materials is a significant concern related to carbon dioxide emissions and global warming. Strategies that reduce the amount of concrete used in buildings are increasingly being used, since concrete as a material is very energy-intensive with a high carbon footprint. Composite structural systems help reduce the amount of concrete used in buildings and thus reduce the carbon footprint of a project. Similarly, the steel components offer longevity and resilience which align with sustainability goals. Steel components routinely contain a significant amount of recycled content and producers have widely adopted innovative energy reduction strategies in production of decking and other products.
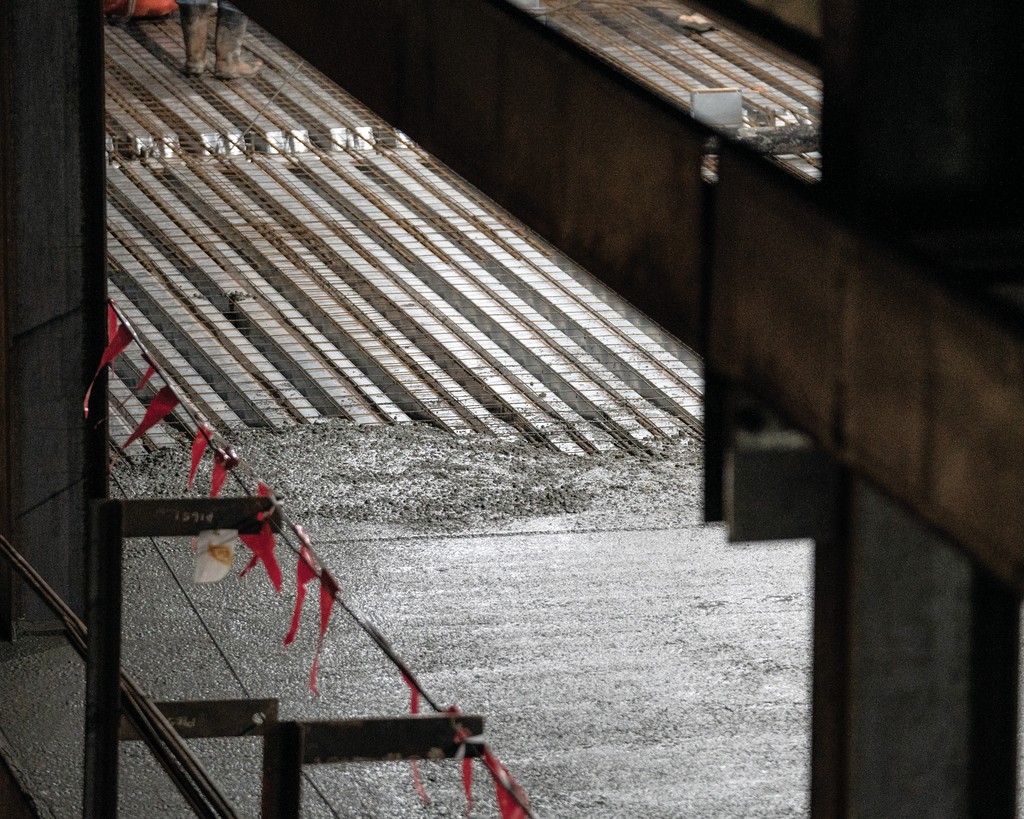
Photos courtesy of New Millennium
After all the deck panels are in place, the concrete pour can be completed to create the composite floor system.
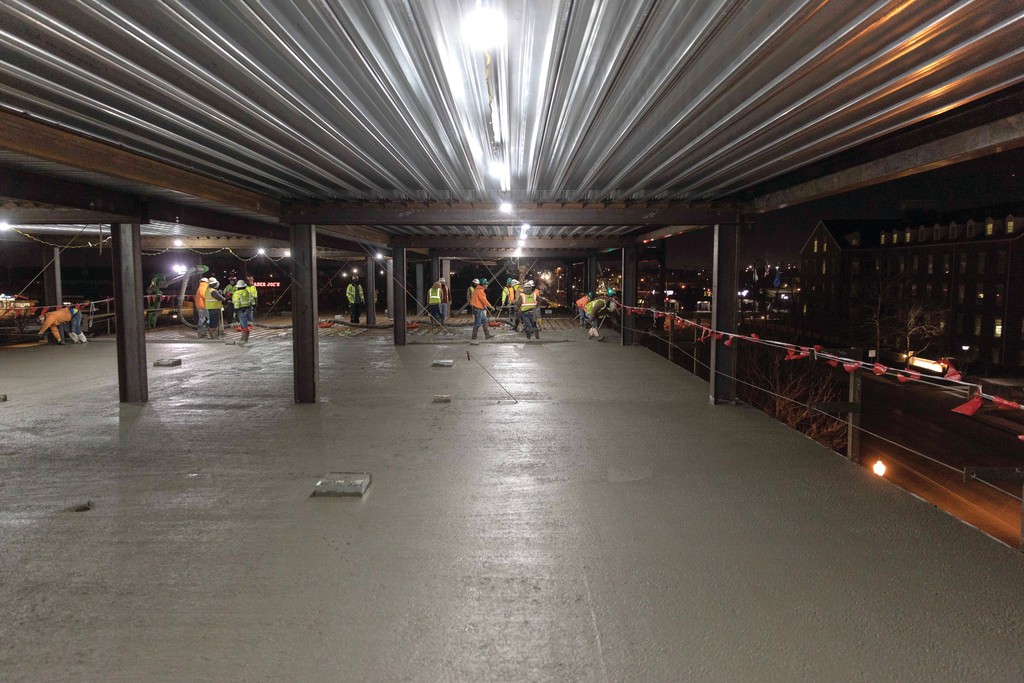
Architects using long-span composite-floor systems can achieve reductions in the construction timeline and the total cost of a multi-story project. Specifying dovetail composite floor deck and CFS load-bearing demising walls have provided a surprising set of cost benefits, compared to other construction approaches such as post-tensioned concrete. For example, the significantly lighter weight dovetail composite floors can often be supported by a spread of concrete footing foundations and may eliminate the need for piles and pile caps in some cases. By virtue of the longer composite floor spans, up to 28 feet, the number of support columns can be reduced and those required can be smaller in girth. During construction, decking spans can reach 16 feet without the need for temporary shoring support. The thinner, faster-curing composite system allows for tighter scheduling of the trades that follow after in the schedule, including plumbing and other rough-in work. There are documented cases where many weeks were removed from the project timeline using this approach.
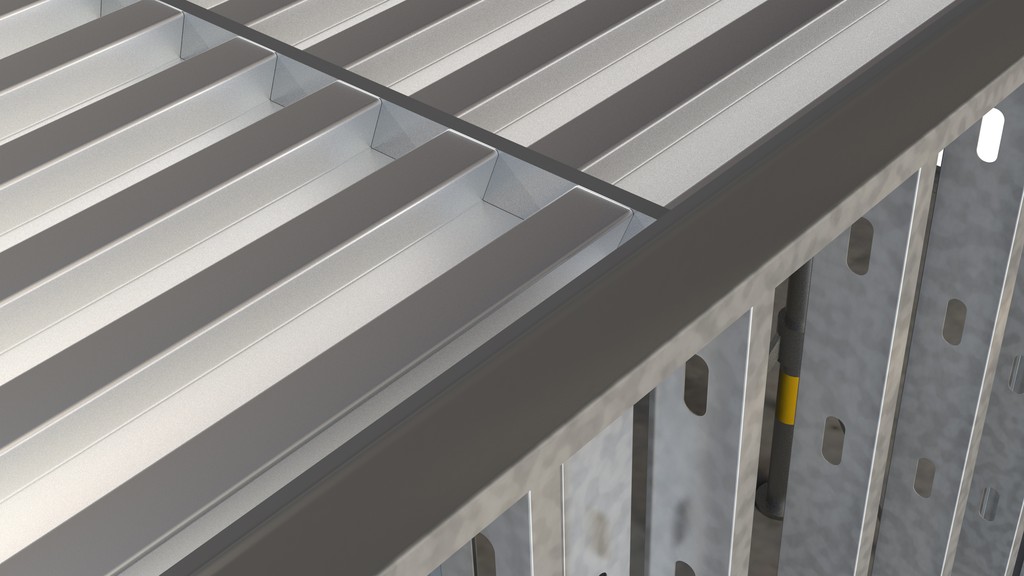
Photo courtesy of New Millennium
Composite steel deck supported by cold-formed steel framing is an economical and effective system for multifamily buildings.
Glass and Glazing Systems in Living Units
Multifamily designs often seek to provide occupants with expansive views and a visual connection to the surrounding landscape or cityscape. This design feature can directly enhance the occupant experience, which is why they are often a sought-after feature in many multifamily developments. There are several aspects to incorporating appropriate fenestration in multifamily buildings.
- Daylighting: The addition of daylight into a building is the strongest contributor of fenestration to indoor environmental quality. Daylight has been shown to provide human health benefits as well as productivity boosts—all contributing to improved wellness for people. Operable windows and doors also allow for beneficial natural air ventilation in a building.
- Energy Usage: While daylighting is important in multifamily buildings, so is energy performance. Modern fenestration systems incorporate thermally broken frames and insulating glazing units (IGUs) up to 1 inch thick to help keep interiors warm during the winter and cool during the summer, thus reducing energy costs from heating/cooling systems. From a total building design standpoint, multifamily units often have fenestration limited to one or two sides of the units. In some cases, the building is designed so windows or views are similarly focused on only one or two sides of a building. That means the total amount of fenestration in a building can be controlled for overall energy performance, but a living unit can appear to have large-scale, dramatic openings.
- Total Exterior Design: On the exterior facade using systems and designs that don’t impede daylight or views, particularly on balconies, porches, etc. is important. Beyond just glass windows and doors, then, the selection of railing materials or windbreaks should be selected with daylight and views in mind. In particular, glass railing systems are available that further improve daylighting while maintaining uninterrupted views of exterior landscapes or cityscapes.
These points typically apply to the exterior and facade design of a building, but there is a growing interest in other glass uses too.
Interior Design with Glass
There is an observable growing trend for people to work remotely from home, either full-time or for a certain number of days per week. All of those people need a place to do their work at home, and that includes homes in multifamily buildings. While some are content to open a laptop on the breakfast table or a comfortable chair, others need a defined space for support materials like books, papers, etc. And when the living unit is shared with others, either humans or pets, there is often a need for some separation and privacy for teleconferencing or audio calls. As such, many multifamily unit designs incorporate a workspace (den, office, etc.) into new or renovated multifamily dwelling units.
A fundamental tenet of good design is to address all of the spaces within a building so that they all have the benefit of good, balanced, and sustainable features. This is noticeably true for work-at-home spaces where an individual might spend a lot of hours every week. That means such a space shouldn’t be thought of as an “add-on” or a way to use a leftover, windowless area to stick a desk into. Rather, it should be designed with the same attention and care as the rest of the living unit. That includes having daylight and views, even if that light is “borrowed” from another space.
One means of achieving better interior design for work-at-home spaces is to use a glass partition and door. This approach provides an opportunity for a more appealing and functional space. It provides needed separation but allows visual connectivity and transparency. This helps the person working to still have access to daylight and views while also being able to observe others in the dwelling unit. Conversely, it allows other people in the unit to see when someone is engaged and working and may not be willing to be disturbed. There are certainly numerous ways to design and achieve these results – the arrangement could be a stationary glass partition system and a separate operable door, simply a sliding interior glass door system, or others.
Photo courtesy of CRL
Work-at-home spaces in living units can benefit from all glass partitions or sliding doors which can be configured in a variety of ways.
Mark Suehiro is Senior Product Manager at C.R. Laurence (CRL) and has been deeply involved in this issue. He points out “Multifamily housing, like all other types of housing, should continue to evolve to reflect the changing needs of homeowners, particularly those who work remotely. That’s why it’s important to specify glazing systems that create defined workspaces and improve well-being and productivity via better daylighting, transparency, and exterior views.”
Designing with Composite Structural Systems
Composite floor systems using dovetail profiled floor decking with lightweight concrete, all supported by CFS bearing walls or conventional steel framing are fairly straightforward to specify and incorporate into multifamily building designs. Keep in mind that the composite slabs, consisting of deck, concrete, and supplemental reinforcing, can reach spans up to 28 feet (8.5 m), allowing for more open space in a building layout. In some cases, shallow profile beams can replace supporting walls often with little, if any, soffit protruding below the deck ceiling plane. By more evenly distributing floor loads over CFS-bearing walls, composite floors also help lighten top-of-wall distribution headers.
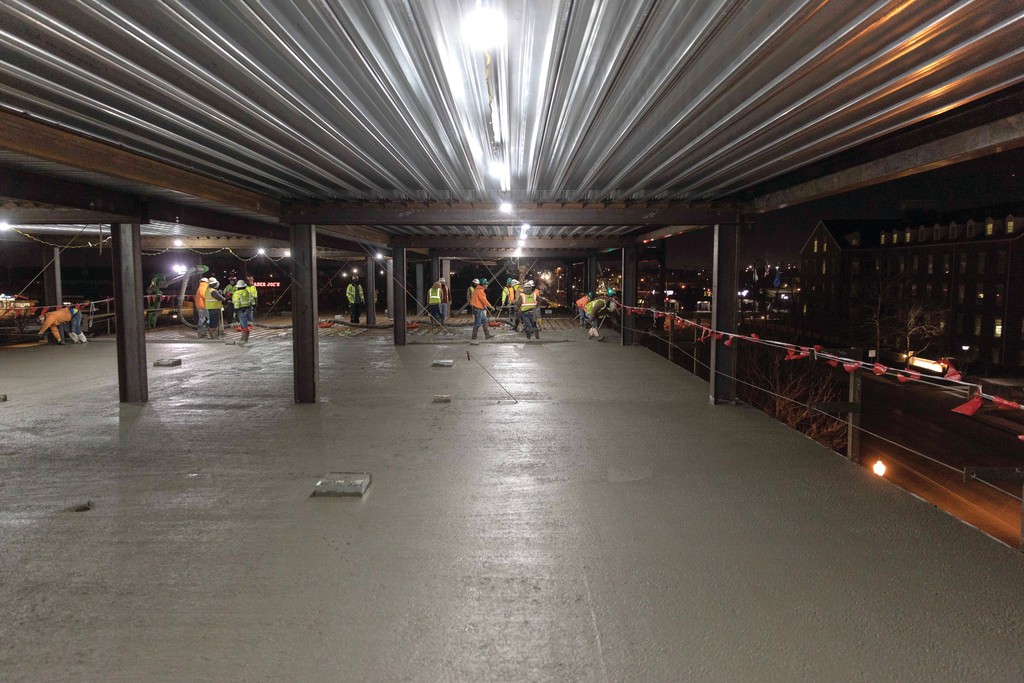
Photo courtesy of New Millennium
Dovetail long-span composite may require shoring, depending on deck gauge, slab depth, and span. Framing strategies, studying these inputs, can be devised to eliminate temporary shoring altogether.
In terms of space optimization, comparatively shallow slabs as thin as 4 inches (102mm) help create design options while still being effectively engineered to meet specific structural requirements and achieve needed fire resistance ratings. The thinner floor systems mean floor-to-floor heights can be shorter while still maintaining desired ceiling heights. For example, a 12-story building using conventional concrete floor deck and beam can alternatively be designed using a dovetail profile composite floor and may end up accommodating an entire extra floor within the same overall building height. This is particularly helpful in locations where the overall building height is limited due to zoning requirements. Often an added story means more income for a building owner and may improve the overall project financial picture considerably. Similarly, a six-story building can be reduced in height, without reducing floor-to-ceiling heights. This space-efficient design translates into effective cost control for the project owner with increased area and occupancy options. It can also help to optimize multi-story construction since the floor-to-floor heights are reduced. This occurs because the structure spanning between load-bearing walls or beams is only comprised of the composite slab without the use of additional joists, trusses, or girders hanging down below.
The dovetail shape of the decking provides some design benefits too. First, it serves as a concrete form and working platform during construction and “keys” to the concrete topping to create a superior composite bond. Second, using hangers that fit into the underside of the decking allows for the ready design layout of suspended lighting and other MEP items. Finally, if the underside of the deck is left exposed, the deck provides a clean, linear aesthetic.
In terms of code compliance, the Steel Deck Institute recommends that all steel roof and floor deck systems should have third-party testing. ICC Evaluation Service (ICC-ES) is an example of reliable testing and reporting to show code compliance for structural design criteria for different deck products including any ancillary or accessory components that need to be used. Fire-rated designs are typically third-party tested separately by testing authorities such as United Laboratories or others. Using a UL-tested product that incorporates a head-of-wall feature makes it very straightforward to utilize staggered flute placement to create fire, smoke, and sound breaks over demising walls and corridor walls. This eliminates the need for specifying costly fire sealants in the open deck flutes.
From the standpoint of the owner and occupants of the buildings, the upfront investment of steel and concrete more than outweighs the long-term maintenance costs of other building materials. During the life of the building, composite structural systems offer a solution that is both durable and dimensionally stable. From an internal comfort perspective, the thermal mass of the system helps retain room temperatures and provide good acoustic performance. Since the products are non-organic, they are not susceptible to termites, mold or rot. Over time, if MEP adjustments or alterations are needed after installation, easy to use hangers can be used or holes may be core-drilled if needed.
With all of the above as a basis, it is clear that many multistory residential design projects can benefit in terms of the total project cost and performance advantages made possible by a dovetail long-span composite floor system.
Design Options for Glass and Glazing Systems
Multifamily building designs incorporate many different approaches to fenestration using glass and glazing systems. In part, that is because manufacturers of these systems have responded to the variety of design needs and offer some appealing and high-performing solutions for architects to consider. These include the options discussed further in the following section.
Sliding Glass Doors
Exterior sliding glass door systems act as movable walls, offering a grand scale and sophisticated design that makes a visual statement. One of the design benefits of sliding glass door and wall systems is their large panel size. Manufacturers can provide panel heights of up to 13 feet tall and widths of up to 7 feet, thus creating an expansive scale and a look of elegance. To keep the visual “clutter” at bay, ultra-slim panel rails and stiles are available that create a minimal and uniform frame. The sliding panels can stack in front of one another on one or both sides or they can disappear into a wall pocket designed by the architect for that purpose. These various design approaches help buildings achieve both a visual and physical connection between indoor and outdoor spaces with relative ease and simplicity. They come in a range of standard and custom offerings related to size, frame color, frame materials, glass types, and other options.
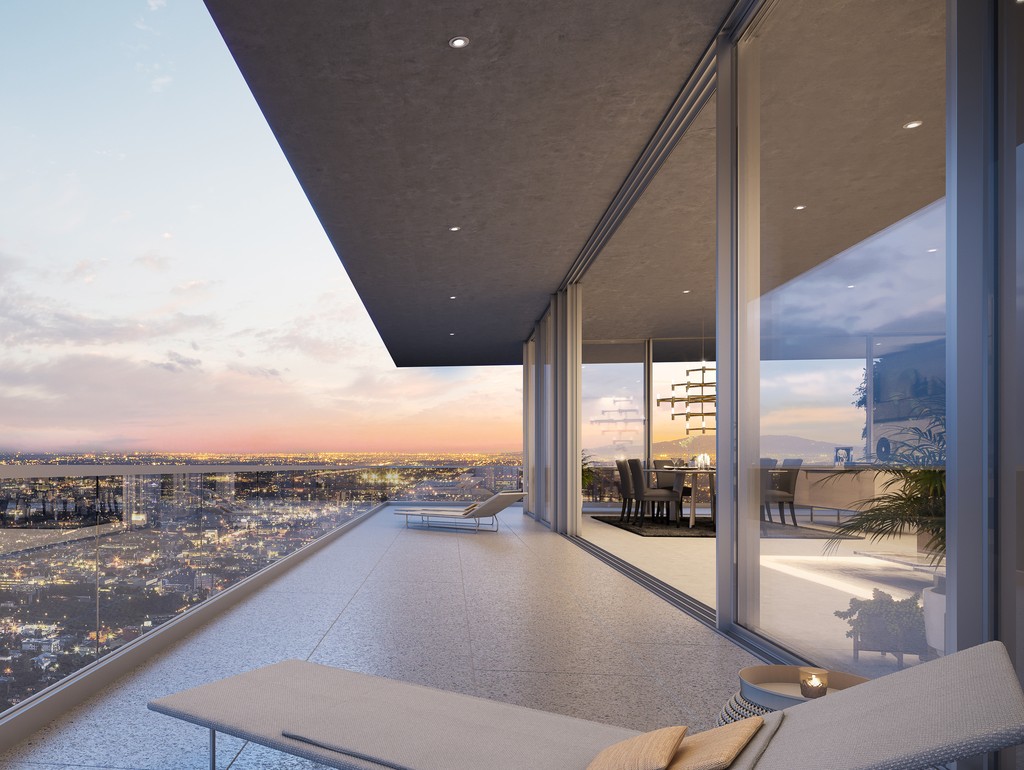
Photo courtesy of CRL
Exterior sliding glass doors can provide large format openings for daylight and views along with performance ratings for weather resistance and energy performance.
From a performance perspective, sliding glass door and wall systems can be specified to work within the requirements of relevant codes and standards. They are available with tested ratings, making them ideal for exterior applications where high loads, limits on deflection, and heavy use are expected. They can employ a thermally broken frame with insulating glass up to 1 inch thick and achieve a U-factor of 0.38 or less. These attributes also contribute to achieving a sound transmission rating of STC-33.
Despite the large sliding panels, this type of door is engineered to provide fairly effortless operation. Some of the best large-format sliding glass door systems use a bottom rolling mechanism with stainless-steel wheels and a precisely engineered stainless-steel track. This helps the large sliding panels, which can weigh up to 700 pounds, move rather effortlessly with one-person operation. That is because panel loads are evenly distributed across the bottom rolling components resulting in a fluid, frictionless glide. The track is set into a sill which may be flush with the surrounding floor surfaces or can be raised for greater protection from wind, rain, and other weather. The sliding operation of the doors means that everything needs to be flat or recessed on the panels so as not to conflict with the proper door movement. This includes the hardware that operates the door, so manufacturers provide integrated, flat handles made of a choice of metals including stainless steel. Since the handle is integral to the door, so is the locking hardware. While there are different ways to use locking hardware, the preferred approach is for a multipoint locking mechanism—internal hardware that locks the sliding panel into place at the top and bottom of the frame. It’s important to note the cycle testing of these systems since they speak to their long-term durability. A 40,000-cycle test is as good as it gets for these types of sliding door systems.
Bi-Folding Glass Doors
Bi-folding glass doors use glazed panels that can enclose and open up a variety of interior and exterior spaces. They can be configured into a small grouping for a wide door opening or can span across an entire wall of a facade. A bi-folding glass door or wall system consists of a number of hinged panels that fold together and then slide out of the way to one or both sides of the opening. Unlike sliding glass doors which typically keep at least one panel fixed, bi-folding systems can all move and be stacked to create a full opening. The panels may be hinged together in pairs or in a large number of connected panels. Many opening configurations are possible with inward or outward swinging options. A locking swing panel can be incorporated into a run of bi-fold doors as a swing door for easy entry or egress within the wall. Like sliding glass doors, bi-folding systems also come in a range of standard and custom offerings related to size, frame color, frame materials, glass types, and other options.
On the aesthetic side, the latest bi-folding doors feature 12-foot frame heights, slim 4-3/4-inch vertical posts, and ultra-narrow 1-7/16-inch panel rails. Such products reduce visible components, produce a minimalistic aesthetic, promote daylighting in buildings, and maximize views. When closed, door hinges can be completely concealed to deliver a minimal, streamlined look.
Since bi-fold doors are a fundamentally different product compared to sliding glass doors, the panels in bi-fold systems are commonly smaller and more frequent than in sliding glass doors. While the specific dimensions and attributes of panels can certainly differ between manufacturers, it is possible to find that the maximum frame height is 12 feet, and the maximum panel width is 4 feet. Weight is certainly a factor for the proper operation of the doors, so a maximum panel weight of 200 pounds can be expected. Similarly, there is a practical limit on how many connected panels make sense before they become too unwieldy to operate. Typically, that equates to a maximum of 9 connected panels per jamb (i.e., 18 per opening with two jambs).
Bi-folding glass door and wall systems have fairly similar performance attributes compared to sliding door systems. They similarly employ a thermally broken frame with insulating glass up to 1 inch thick and achieve a U-factor of 0.36 and a sound transmission rating of STC-32. When closed, bi-folding door systems offer minimal obstruction to preserve views and can seal up tightly to effectively protect against air and water infiltration.
Bi-fold doors move differently than sliding door systems but can be just as easy to use and design into a building. A bottom rolling system is an option similar to sliding doors which eliminates added loading on the beam or header above the opening. Some incorporate compensating channels and adjustable spacers to fine-tune the operation for smooth movement and ease of use. The bottom track for bi-fold doors is set into a sill which may be flush with the surrounding floor surfaces or can be raised for greater protection from wind, rain, and other weather.
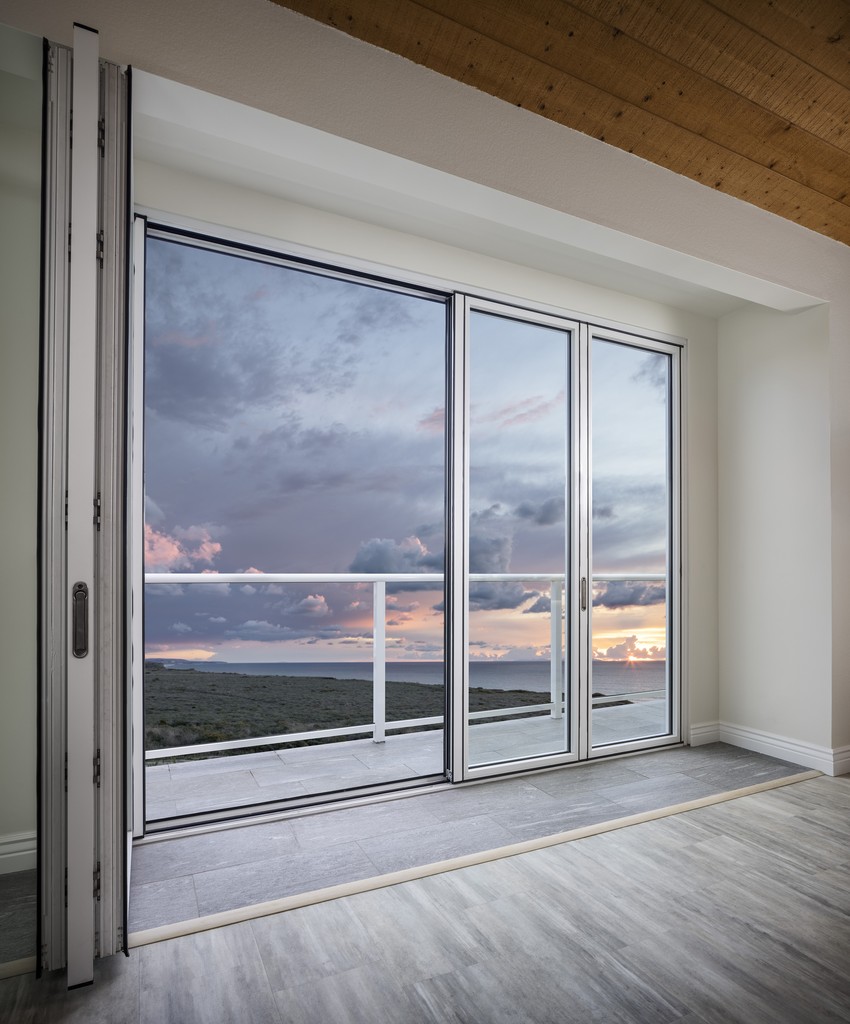
Photo courtesy of CRL
Folding panel glass doors allow an entire opening to be accessed with door panels folded up on the sides or closed in line with the opening.
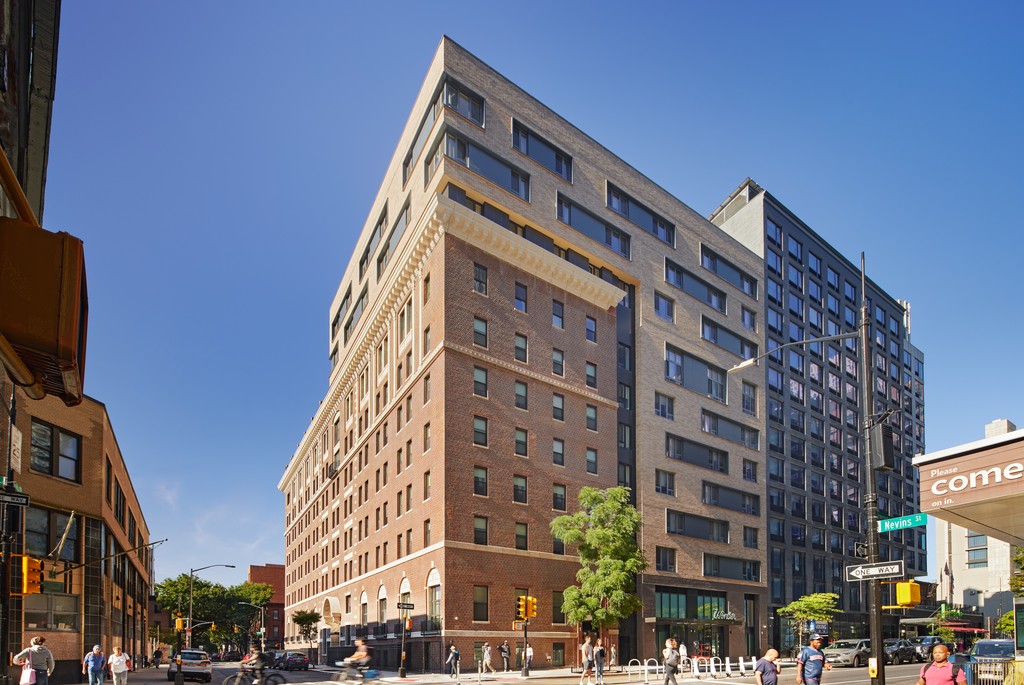
Photo courtesy: © Ines Leong / L-INES Photo
The historic site of 50 Nevins Street, with its new 10-story addition, now features 129 new apartments serving those in need. 78 are supportive units reserved for formerly homeless individuals, including formerly homeless veterans, individuals with histories of substance use, and people with serious mental health concerns, including young adults who have aged out of foster care. On-site supportive services include case management and mental health services, designed to address the whole health of residents.
Glass Railing Systems
The use of glass for a safety guardrail has become more popular for use on balconies, decks, plazas, etc. This is because advances in glass technology have produced a durable and safe glass panels, commonly using laminated or tempered glass. Equally important, methods to attach and secure the glass panels have been developed that have been tested and approved for commercial building use. Specifying such systems should include the testing results for specific glass rail products. One of the most relied upon certifications is
from the ICC Evaluation Service, associated with the International Code Council. The process for obtaining an ICC-ES report starts with the manufacturer providing detailed product information and engineering data. The ICC-ES then reviews all of that information against the prevailing code requirements and reports on the compliance or limitations of the different products reviewed.
One such tested glass railing system is based on a unitized approach as a more efficient way of fabricating and installing glass railings. In addition to saving multifamily projects time and money, this type of product offers long, uninterrupted glass spans with minimal vertical breaks. The process begins in the manufacturing facility where base shoe units are glazed with the specified glass, then shipped to the jobsite, ready to install. The glass arrives aligned to be plumb and level within the base shoe unit to provide precise sightlines. It can then be installed in two simple steps. First, the glass railing units are set in place in core-drilled holes in a concrete balcony. Next, the prefabricated cap rails are attached, and the installation is done. This highly efficient installation method expedites project completion and reduces on-site labor costs – a unitized system can be installed 40-50 percent faster than standard glass railing systems.
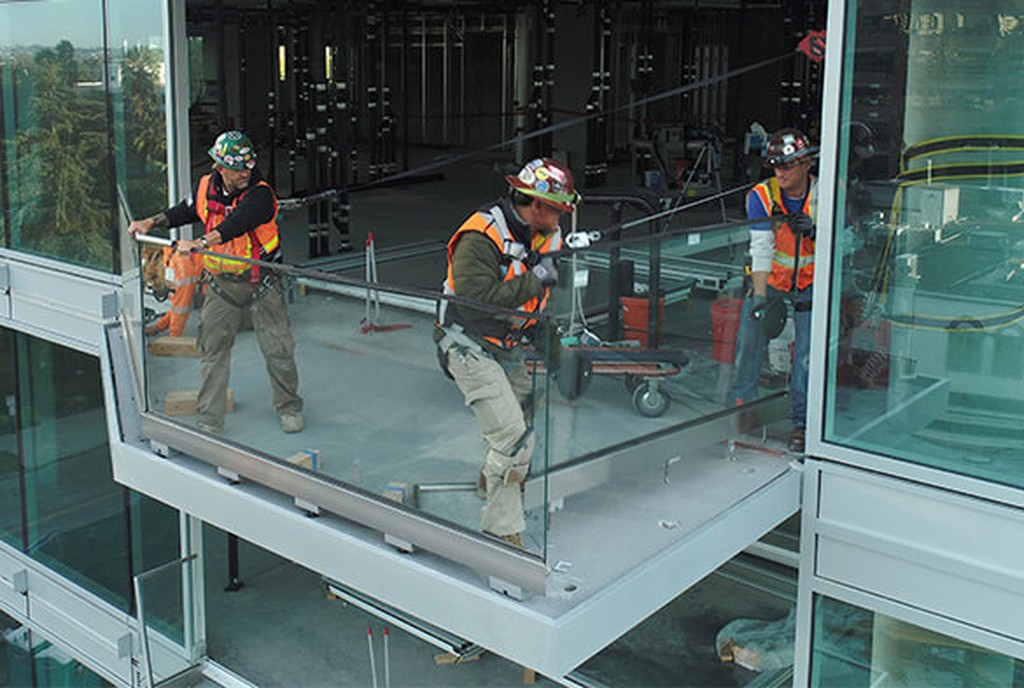
Photo courtesy of CRL
Unitized glass railing systems combine factory efficiencies with onsite conditions to allow for high-quality installations in less time than conventional construction techniques.
Interior Glazed Doors
Adding glazed doors to an interior design can be fairly straightforward for both new construction and retrofit projects. A common swing door can certainly be glazed and provide the desired degree of openness or separation. However, sliding doors can also play a worthwhile design role in this application. A single-panel door can slide from one side of an opening to the other, thus sealing off the space when needed, and opening it up when preferred. The glass can be clear (i.e., transparent) patterned (translucent), or a combination of both as project conditions (or occupants) might prefer.
The method of attaching and installing interior sliding glass doors can vary as well. A conventional floor or ceiling track can allow for a full-height glass panel to be used. Alternatively, for a more residential look consistent with some current trends, the use of a “barn door” style arrangement may be more appealing and functional. Essentially, this approach uses a wall-mounted top bar placed above the door opening. A glass panel is then suspended from the bar resting on wheeled assemblies and other hardware. The glass panel is then able to move freely in front of the wall and opening allowing its full functional operation. Since the wall itself only needs a finished opening, this approach is ideal for retrofitting situations without the need to otherwise disturb and repair the existing wall. The manufacturers of such systems now offer quite a range of hardware systems in a variety of styles, materials, and colors for design professionals to choose from. That means that they can accommodate the design intent of many different types of dwelling unit designs.
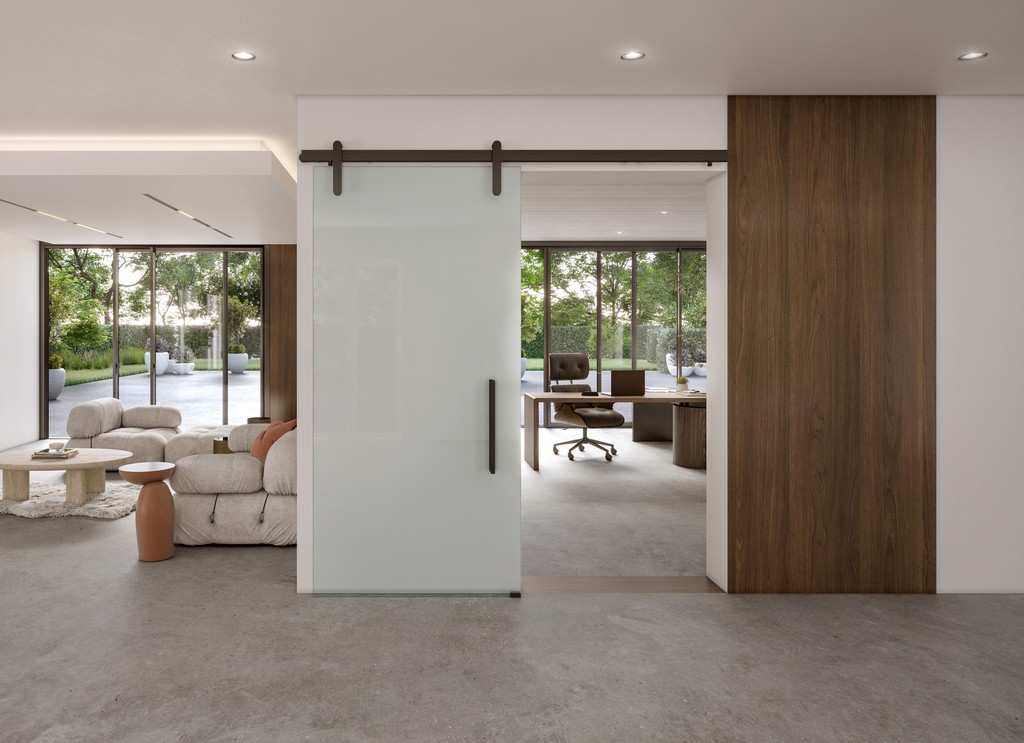
Energy Performance
All of the glass and glazing systems described have the potential to create well-designed living units that achieve goals for wellness, safety, and indoor environmental quality. However, architects must be careful when specifying fenestration systems that offer all-glass visuals. The reason is that more glass typically means lower thermal performance which is also a key aspect to sustainable design. Fortunately, manufacturers of architectural glazing systems have been on board with this need for some time now.
Innovations in product engineering have produced large, movable glass wall systems such as those described here. Many of them offer ultra-slim frames providing uninterrupted views and maximizing daylighting opportunities. That same level of innovation has been used to mitigate heat transfer in their products using thermal breaks and insulating glass. While this reduces energy usage and costs, it also helps to maintain comfortable interior temperatures throughout the year, thus enhancing occupant satisfaction as well as the energy efficiency of multifamily developments.
Conclusion
Creating well-designed multifamily housing is a multi-faceted task. Structural systems need to meet the demands of engineering integrity, durability, fire safety, and acoustics. Fenestration is required in all buildings to provide views and daylight but still achieve targeted thermal performance. Interiors need to consider changing needs, particularly related to work-at-home situations. The strategies discussed in this course can help architects and designers address these multiple design criteria to meet the needs of the building owner, the occupants, and the environment.