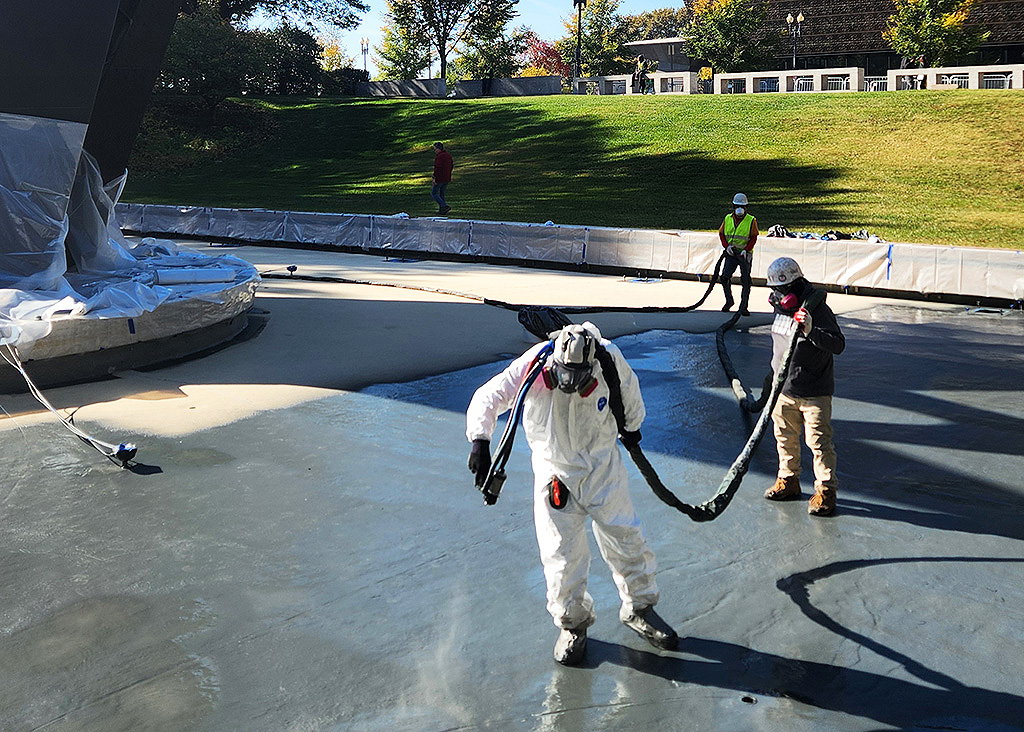
Photo courtesy of Henry, a Carlisle Company
Thanks to a two-part, 100 percent solid polyurea hybrid formulation, these membranes achieve high elongation, tensile strength, and crack-bridging capacity—all without the need for fabric reinforcement.
Spray-applied, instant-setting membranes are reshaping how design professionals approach below-grade and above-grade waterproofing. Once primarily used in European markets and parts of the northeastern United States, this technology is now gaining broader traction due to its ability to reduce installation complexity and minimize cure times. These membranes are particularly well-suited to projects with irregular substrates, tight construction schedules, or challenging sequencing requirements. In this article, we’ll explore how the chemistry and performance characteristics of instant-setting membranes make them adaptable to a wide range of conditions. We’ll also examine their compatibility with other systems, how to build out a complete assembly from primer to topcoat, and where this approach can provide meaningful advantages over traditional sheet or fluid-applied systems. With project-specific design considerations in mind, participants will gain practical tools for evaluating membrane performance, specifying the appropriate system, and ensuring quality during installation.
The Evolution of Instant-Setting Waterproofing System
Traditional waterproofing systems often struggle to keep pace with today’s performance expectations. Complex architectural detailing can make conventional membranes difficult to apply cleanly, potentially limiting the design freedom of the building envelope. Installations are frequently slow, which introduces schedule risk and complicates sequencing. Membrane damage during installation or from subsequent construction activity remains a persistent issue, and many conventional systems rely on hot-applied materials or high-solvent content products that raise serious safety and indoor air quality concerns. These conditions not only threaten worker health but also introduce risks to building occupants during renovation or phased construction.
Durability and low maintenance are key components of any sustainable design, and systems that require full replacement after just a few years run counter to long-term performance goals. Even when warranties are offered, they may contain exclusions for overburden conditions or transfer risk back to the installer with limited manufacturer accountability. Instant-setting membranes offer a response to many of these challenges, combining rapid application, seamless performance, and compatibility with varied substrates and conditions, often with a simplified, safer installation process.
The origins of instant-setting waterproofing systems trace back not to conventional building design, but to the high-performance demands of infrastructure and industrial sectors—environments where materials must be delivered under extreme conditions. Though a common and successful waterproofing approach in Europe, these systems were first recognized domestically in the early 1980s. Bridge rehabilitation projects in the Northeast and Midwest regions of the United States started applying instant-setting waterproofing membranes because they could be applied quickly, cure almost instantly, and remain intact under continuous mechanical stress. In such settings, failure was not just a matter of inconvenience—it could lead to structural degradation and safety hazards. The performance bar was exceptionally high, and products had to demonstrate resistance to abrasion, cracking, and moisture penetration over long service lives. For bridge deck protection, this included punishing and near-constant vehicular traffic, heavy vibration, de-icing salts, and wide temperature swings.
This necessity to find a better solution than traditional waterproofing membranes in extreme infrastructure projects laid the foundation for today’s instant-setting membranes, which have since been adapted for use in the built environment. By the 1990s, this technology made its way into the U.S. construction market. Contractors and architects alike began to recognize the value it brought to complex building environments where traditional waterproofing methods often fell short. Instant-setting membranes proved especially valuable on sites with schedule pressures, aggressive weather, or demanding detailing.
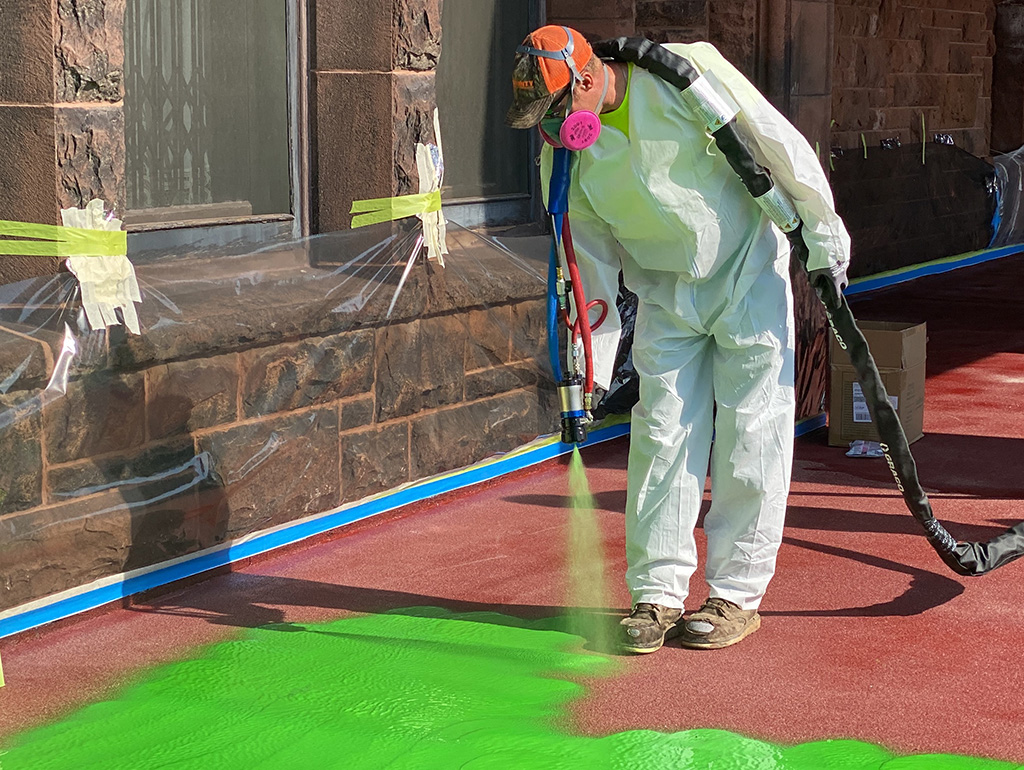
Photo courtesy of Henry, a Carlisle Company
High-performing waterproofing relies on coordinated components, with each layer working together to form a seamless, durable barrier against water intrusion.
As confidence in the system grew, applications expanded beyond infrastructure to include architectural assemblies. Today, instant-setting membranes are routinely used in a variety of protected and inverted systems, including plaza decks, green roofs, and protected membrane roofing assemblies. The breadth of applications continues to grow thanks to the product’s ability to form seamless, monolithic barriers that resist water intrusion while accommodating movement and integration with other envelope systems.
From a construction bottom-line management perspective, instant-setting waterproofing systems have proven to be particularly well-suited to fast-paced construction environments where time, safety, and durability are paramount. One of the primary advantages is their ability to eliminate many of the detailing and reinforcement steps traditionally associated with waterproofing. Thanks to a two-part, 100% solid polyurea hybrid formulation, these membranes achieve high elongation, tensile strength, and crack-bridging capacity—all without the need for fabric reinforcement. The result is a monolithic, fully bonded membrane that performs even when applied in multiple phases or under complex site conditions.
On the jobsite, these systems offer several advantages that help streamline construction and protect the building. They allow for foot traffic and overburden installation within an hour of application, helping to maintain critical project momentum. The use of an epoxy primer not only enhances substrate adhesion but also mitigates water migration and prevents vapor drive as it seals the concrete deck to allow for earlier installation windows. Odor and solvent content are minimal, ensuring compliance with VOC regulations and making the system appropriate for both new builds and occupied renovation projects. In terms of lifecycle value, these membranes resist abrasion, tolerate heavy construction traffic, and do not require separate root barriers when used beneath vegetative roofing systems. With no seams, no flashing assemblies, and fewer weather delays, instant-setting waterproofing systems offer a streamlined, performance-driven solution that aligns with the realities of modern construction schedules.
How it Works

Image courtesy of Henry, a Carlisle Company
The four main components of a system build-up include: 1) Primer; 2) Spray applied, instant-setting waterproofing; 3) Optional polyurethane wear coat with an aggregated surface; 4) Optional color stable topcoat (not shown).
A high-performing waterproofing system is more than just a single product—it’s the result of a carefully coordinated set of components working together to address specific challenges. Instant-setting waterproofing systems are no exception. Each layer in the system is purpose-built to support long-term membrane performance, accelerate installation, and adapt to the realities of construction sequencing. From substrate to topcoat, these components are formulated to interact chemically and physically, creating a seamless barrier against water intrusion and damage. Whether the project involves new construction or retrofit applications, understanding the function of each layer is essential to specifying a resilient, high-performance solution.
Primer
Standard Primers: At the foundation of any instant-setting waterproofing system is the primer layer, which plays a critical role in ensuring both short-term adhesion and long-term performance. The primary function of the primer is to seal the substrate, reducing moisture migration and promoting a strong chemical bond between the surface and the subsequent waterproofing membrane. Unlike traditional adhesives, these primers are engineered specifically for compatibility with polyurethane- and polyurea-based systems and variable site conditions.
Standard epoxy primers are often the preferred choice with instant-setting waterproofing systems, especially when applied to horizontal surfaces. These primers are formulated as two-part, 100 percent solids epoxy products, meaning they contain no solvents and are VOC compliant, making them suitable for use in both exterior and occupied interior applications. With a high-viscosity profile, the primer adheres effectively to concrete and other structural substrates, creating a robust surface for membrane bonding. The standard primer is installed by squeegee and back-rolled to make sure the membrane fully encapsulates substrate pores. Brushes are used to install primer in critical areas such as drains or challenging transitions.
A key feature of this system is the use of a fully broadcast (i.e., fully spread or dispersed) silica sand aggregate while the primer is still wet. Typically using a sieve size of #20–50, the sand is applied to rejection and then allowed to cure with the primer. This broadcast not only provides a mechanical anchor for the membrane but also serves a dual-purpose during installation: it offers a visual cue that the waterproofing membrane has achieved its target thickness—usually around 100 mils—once the sand texture is fully obscured. Prior to membrane application, excess aggregate is removed to ensure even coverage and eliminate buildup at transitions.
One of the distinct advantages of this primer system is its open working time. Once cured, the sand-broadcast surface does not impose a strict time limit for membrane installation, allowing greater flexibility in sequencing and coordination with other trades. This durability, combined with its environmental compliance and installation tolerance, makes standard epoxy primers a reliable choice for high-performance waterproofing assemblies.
Optional Primers: In addition to standard epoxy primers, a range of optional primers has been developed to accommodate specific jobsite conditions and substrate types. These alternatives are essential when the project requires greater flexibility due to weather, schedule, or material compatibility.
Low-viscosity primers are designed for fast-track construction schedules where the waterproofing membrane is applied within 24 hours. Unlike the standard formulation, these primers do not require a broadcast aggregate, making them a streamlined solution for interior or vertical surfaces where texture is unnecessary or where membrane adhesion relies solely on chemical bonding. For projects taking place in colder climates, low-temperature primers include an aggregate broadcast and are formulated to perform effectively below 50°F. This allows installation to proceed in conditions that would otherwise delay schedule-critical work.
Projects involving non-concrete substrates such as aluminum, stainless steel, copper, or rigid PVC pipe call for specialty primers—often based on PMMA (polymethyl methacrylate) chemistry. These primers enable secure bonding where conventional epoxies cannot form a reliable interface. Finally, moisture-mitigating primers serve a vital role when working over green concrete, typically as soon as five days after formwork removal. These primers suppress moisture vapor transmission from within the slab, preventing future blistering or adhesion loss in the membrane layer. By matching the primer to the substrate and site conditions, specifiers and installers can ensure that the entire waterproofing assembly performs as intended across a wide range of applications.
Note: Best practices include preparing and priming vertical surfaces at least 2 inches above the area of anticipated installation. Do not install waterproofing beyond primed surfaces.
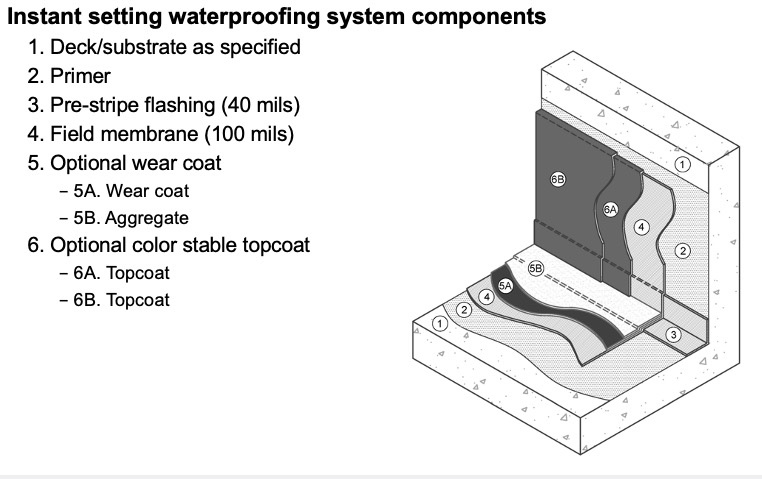
Image courtesy of Henry, a Carlisle Company
Instant-setting cold fluid applied waterproofing systems work well in both vertical and horizontal applications; however, care must be taken to ensure all steps are followed to ensure a successful installation.
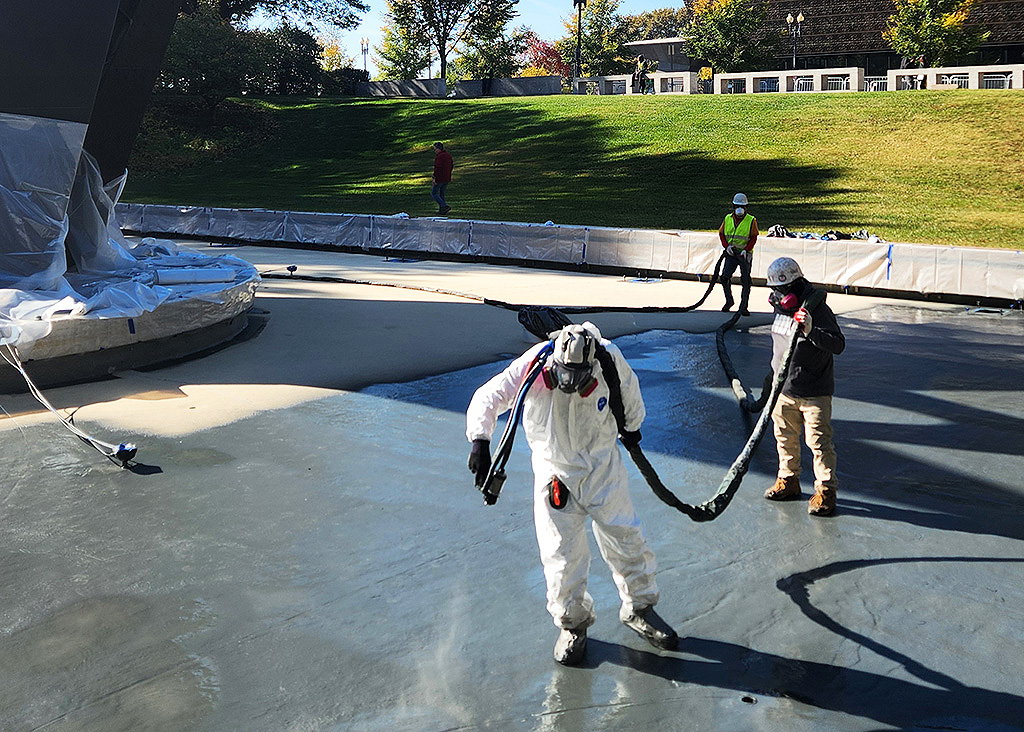
Photo courtesy of Henry, a Carlisle Company
Thanks to a two-part, 100 percent solid polyurea hybrid formulation, these membranes achieve high elongation, tensile strength, and crack-bridging capacity—all without the need for fabric reinforcement.
Spray-applied, instant-setting membranes are reshaping how design professionals approach below-grade and above-grade waterproofing. Once primarily used in European markets and parts of the northeastern United States, this technology is now gaining broader traction due to its ability to reduce installation complexity and minimize cure times. These membranes are particularly well-suited to projects with irregular substrates, tight construction schedules, or challenging sequencing requirements. In this article, we’ll explore how the chemistry and performance characteristics of instant-setting membranes make them adaptable to a wide range of conditions. We’ll also examine their compatibility with other systems, how to build out a complete assembly from primer to topcoat, and where this approach can provide meaningful advantages over traditional sheet or fluid-applied systems. With project-specific design considerations in mind, participants will gain practical tools for evaluating membrane performance, specifying the appropriate system, and ensuring quality during installation.
The Evolution of Instant-Setting Waterproofing System
Traditional waterproofing systems often struggle to keep pace with today’s performance expectations. Complex architectural detailing can make conventional membranes difficult to apply cleanly, potentially limiting the design freedom of the building envelope. Installations are frequently slow, which introduces schedule risk and complicates sequencing. Membrane damage during installation or from subsequent construction activity remains a persistent issue, and many conventional systems rely on hot-applied materials or high-solvent content products that raise serious safety and indoor air quality concerns. These conditions not only threaten worker health but also introduce risks to building occupants during renovation or phased construction.
Durability and low maintenance are key components of any sustainable design, and systems that require full replacement after just a few years run counter to long-term performance goals. Even when warranties are offered, they may contain exclusions for overburden conditions or transfer risk back to the installer with limited manufacturer accountability. Instant-setting membranes offer a response to many of these challenges, combining rapid application, seamless performance, and compatibility with varied substrates and conditions, often with a simplified, safer installation process.
The origins of instant-setting waterproofing systems trace back not to conventional building design, but to the high-performance demands of infrastructure and industrial sectors—environments where materials must be delivered under extreme conditions. Though a common and successful waterproofing approach in Europe, these systems were first recognized domestically in the early 1980s. Bridge rehabilitation projects in the Northeast and Midwest regions of the United States started applying instant-setting waterproofing membranes because they could be applied quickly, cure almost instantly, and remain intact under continuous mechanical stress. In such settings, failure was not just a matter of inconvenience—it could lead to structural degradation and safety hazards. The performance bar was exceptionally high, and products had to demonstrate resistance to abrasion, cracking, and moisture penetration over long service lives. For bridge deck protection, this included punishing and near-constant vehicular traffic, heavy vibration, de-icing salts, and wide temperature swings.
This necessity to find a better solution than traditional waterproofing membranes in extreme infrastructure projects laid the foundation for today’s instant-setting membranes, which have since been adapted for use in the built environment. By the 1990s, this technology made its way into the U.S. construction market. Contractors and architects alike began to recognize the value it brought to complex building environments where traditional waterproofing methods often fell short. Instant-setting membranes proved especially valuable on sites with schedule pressures, aggressive weather, or demanding detailing.
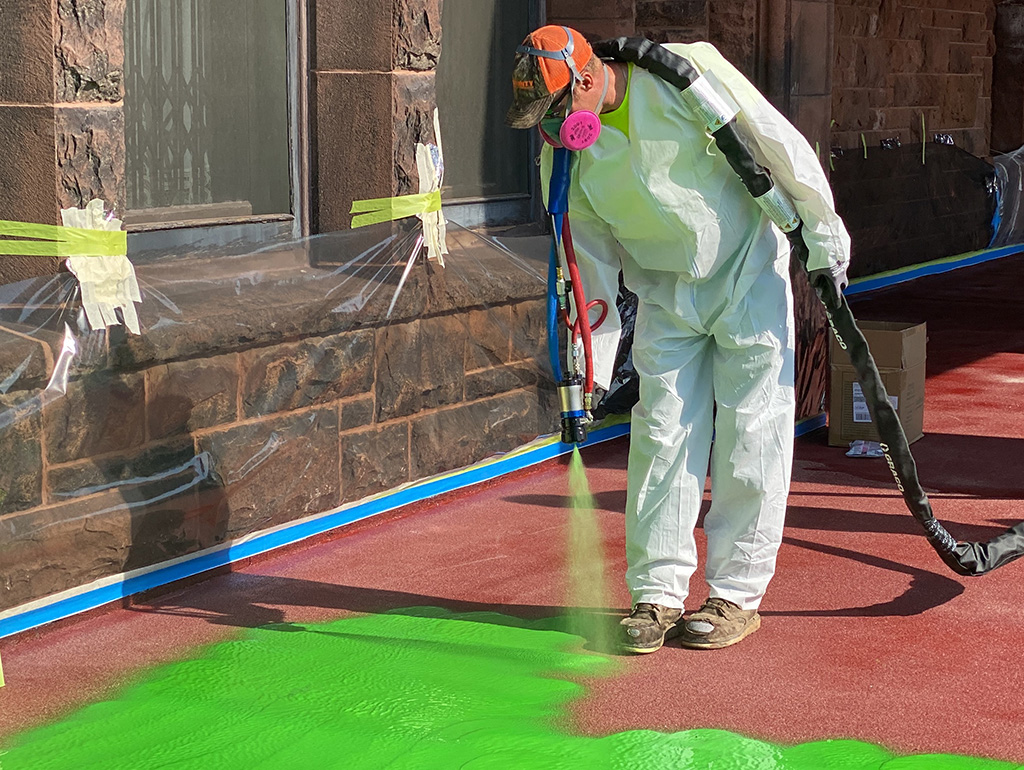
Photo courtesy of Henry, a Carlisle Company
High-performing waterproofing relies on coordinated components, with each layer working together to form a seamless, durable barrier against water intrusion.
As confidence in the system grew, applications expanded beyond infrastructure to include architectural assemblies. Today, instant-setting membranes are routinely used in a variety of protected and inverted systems, including plaza decks, green roofs, and protected membrane roofing assemblies. The breadth of applications continues to grow thanks to the product’s ability to form seamless, monolithic barriers that resist water intrusion while accommodating movement and integration with other envelope systems.
From a construction bottom-line management perspective, instant-setting waterproofing systems have proven to be particularly well-suited to fast-paced construction environments where time, safety, and durability are paramount. One of the primary advantages is their ability to eliminate many of the detailing and reinforcement steps traditionally associated with waterproofing. Thanks to a two-part, 100% solid polyurea hybrid formulation, these membranes achieve high elongation, tensile strength, and crack-bridging capacity—all without the need for fabric reinforcement. The result is a monolithic, fully bonded membrane that performs even when applied in multiple phases or under complex site conditions.
On the jobsite, these systems offer several advantages that help streamline construction and protect the building. They allow for foot traffic and overburden installation within an hour of application, helping to maintain critical project momentum. The use of an epoxy primer not only enhances substrate adhesion but also mitigates water migration and prevents vapor drive as it seals the concrete deck to allow for earlier installation windows. Odor and solvent content are minimal, ensuring compliance with VOC regulations and making the system appropriate for both new builds and occupied renovation projects. In terms of lifecycle value, these membranes resist abrasion, tolerate heavy construction traffic, and do not require separate root barriers when used beneath vegetative roofing systems. With no seams, no flashing assemblies, and fewer weather delays, instant-setting waterproofing systems offer a streamlined, performance-driven solution that aligns with the realities of modern construction schedules.
How it Works

Image courtesy of Henry, a Carlisle Company
The four main components of a system build-up include: 1) Primer; 2) Spray applied, instant-setting waterproofing; 3) Optional polyurethane wear coat with an aggregated surface; 4) Optional color stable topcoat (not shown).
A high-performing waterproofing system is more than just a single product—it’s the result of a carefully coordinated set of components working together to address specific challenges. Instant-setting waterproofing systems are no exception. Each layer in the system is purpose-built to support long-term membrane performance, accelerate installation, and adapt to the realities of construction sequencing. From substrate to topcoat, these components are formulated to interact chemically and physically, creating a seamless barrier against water intrusion and damage. Whether the project involves new construction or retrofit applications, understanding the function of each layer is essential to specifying a resilient, high-performance solution.
Primer
Standard Primers: At the foundation of any instant-setting waterproofing system is the primer layer, which plays a critical role in ensuring both short-term adhesion and long-term performance. The primary function of the primer is to seal the substrate, reducing moisture migration and promoting a strong chemical bond between the surface and the subsequent waterproofing membrane. Unlike traditional adhesives, these primers are engineered specifically for compatibility with polyurethane- and polyurea-based systems and variable site conditions.
Standard epoxy primers are often the preferred choice with instant-setting waterproofing systems, especially when applied to horizontal surfaces. These primers are formulated as two-part, 100 percent solids epoxy products, meaning they contain no solvents and are VOC compliant, making them suitable for use in both exterior and occupied interior applications. With a high-viscosity profile, the primer adheres effectively to concrete and other structural substrates, creating a robust surface for membrane bonding. The standard primer is installed by squeegee and back-rolled to make sure the membrane fully encapsulates substrate pores. Brushes are used to install primer in critical areas such as drains or challenging transitions.
A key feature of this system is the use of a fully broadcast (i.e., fully spread or dispersed) silica sand aggregate while the primer is still wet. Typically using a sieve size of #20–50, the sand is applied to rejection and then allowed to cure with the primer. This broadcast not only provides a mechanical anchor for the membrane but also serves a dual-purpose during installation: it offers a visual cue that the waterproofing membrane has achieved its target thickness—usually around 100 mils—once the sand texture is fully obscured. Prior to membrane application, excess aggregate is removed to ensure even coverage and eliminate buildup at transitions.
One of the distinct advantages of this primer system is its open working time. Once cured, the sand-broadcast surface does not impose a strict time limit for membrane installation, allowing greater flexibility in sequencing and coordination with other trades. This durability, combined with its environmental compliance and installation tolerance, makes standard epoxy primers a reliable choice for high-performance waterproofing assemblies.
Optional Primers: In addition to standard epoxy primers, a range of optional primers has been developed to accommodate specific jobsite conditions and substrate types. These alternatives are essential when the project requires greater flexibility due to weather, schedule, or material compatibility.
Low-viscosity primers are designed for fast-track construction schedules where the waterproofing membrane is applied within 24 hours. Unlike the standard formulation, these primers do not require a broadcast aggregate, making them a streamlined solution for interior or vertical surfaces where texture is unnecessary or where membrane adhesion relies solely on chemical bonding. For projects taking place in colder climates, low-temperature primers include an aggregate broadcast and are formulated to perform effectively below 50°F. This allows installation to proceed in conditions that would otherwise delay schedule-critical work.
Projects involving non-concrete substrates such as aluminum, stainless steel, copper, or rigid PVC pipe call for specialty primers—often based on PMMA (polymethyl methacrylate) chemistry. These primers enable secure bonding where conventional epoxies cannot form a reliable interface. Finally, moisture-mitigating primers serve a vital role when working over green concrete, typically as soon as five days after formwork removal. These primers suppress moisture vapor transmission from within the slab, preventing future blistering or adhesion loss in the membrane layer. By matching the primer to the substrate and site conditions, specifiers and installers can ensure that the entire waterproofing assembly performs as intended across a wide range of applications.
Note: Best practices include preparing and priming vertical surfaces at least 2 inches above the area of anticipated installation. Do not install waterproofing beyond primed surfaces.
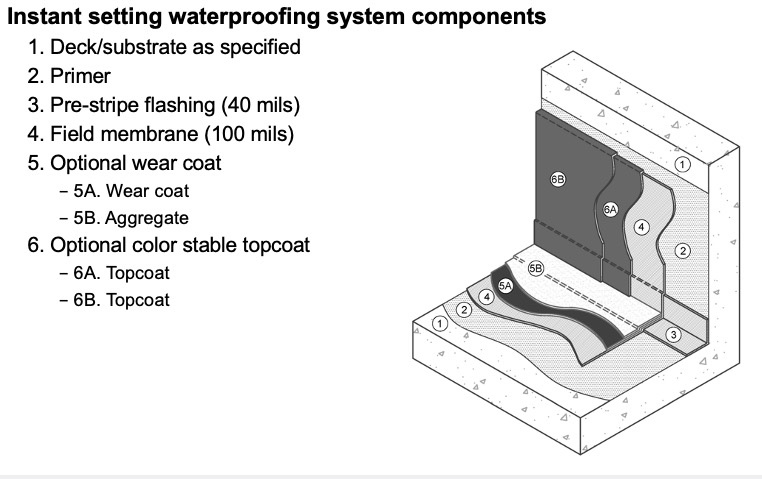
Image courtesy of Henry, a Carlisle Company
Instant-setting cold fluid applied waterproofing systems work well in both vertical and horizontal applications; however, care must be taken to ensure all steps are followed to ensure a successful installation.
Spray-Applied, Instant-Setting Waterproofing
At the core of the instant-setting waterproofing system is the spray-applied membrane—a two-part, 100% solid polyurea hybrid engineered for performance and speed. Applied directly over a prepared and primed surface, this membrane cures almost immediately upon contact, creating a fully bonded, seamless layer of protection. The rapid cure time allows for same-day resumption of construction activities, which is a significant advantage in projects where time, sequencing, or weather windows are a factor.
What distinguishes this membrane from more conventional waterproofing products is its ability to form a uniform, monolithic barrier without the need for fabric reinforcement or traditional detailing accessories. The performance characteristics of spray-applied, instant-setting waterproofing membranes are grounded in a set of physical properties that directly address the challenges of modern construction.
These membranes exhibit elongation values greater than 300 percent, allowing them to stretch and accommodate dynamic movement, thermal cycling, or substrate shifts without tearing or debonding. With tensile strengths exceeding 1600 psi, they maintain structural cohesion even under stress, offering a reliable barrier that won’t deform or degrade under normal loads.
The absence of seams eliminates one of the most common points of failure in sheet-applied systems, and its full adhesion to the substrate reduces the potential for water migration beneath the membrane. Together, these properties support a robust and flexible solution that meets modern construction demands without compromising long-term performance.
One of the most critical metrics for a waterproofing system is its ability to bridge cracks. Spray-applied, instant-setting waterproofing membranes are capable of spanning cracks up to 1/8-inch wide without the aid of reinforcement fabrics, making them particularly effective for installations over aging concrete or conditions where substrate movement is expected. In addition to its flexibility, the system offers high abrasion resistance and a Shore A hardness rating (see definition later in this article) above 90, which allows it to endure heavy foot traffic and construction activity without compromising integrity.
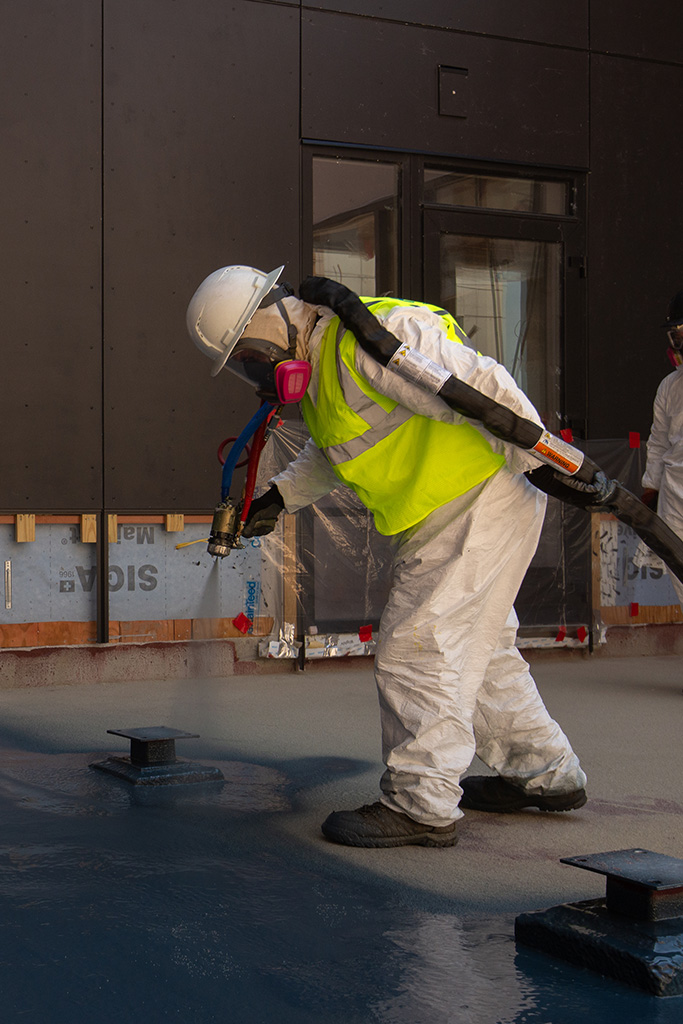
Photo courtesy of Henry, a Carlisle Company
Spray-applied, instant-setting waterproofing membranes are capable of spanning cracks up to 1/8-inch wide without the aid of reinforcement fabrics, making them particularly effective for installations over aging concrete or conditions where substrate movement is expected.
Another noteworthy benefit is its root resistance when used under vegetative surfaces. According to German FLL guidelines—a widely recognized standard for vegetative roof assemblies—this membrane does not require a separate root barrier to guard against root penetration and damage. The assemblage of layers reduces both the cost and complexity of green roofing systems. These physical attributes make the spray-applied waterproofing membrane a resilient, adaptable component within an integrated building envelope strategy.
Wear Coat (Optional)
Spray-applied, instant-setting membranes are known for their ability to create a seamless and highly durable waterproofing barrier. However, while the membrane itself offers strong resistance to moisture and environmental stressors, the construction industry acknowledges the need for added protection in situations where the surface is subject to repeated heavy traffic or where overburden materials like concrete, mortar, or pavers are installed directly over the membrane. In these cases, an optional polyurethane wear coat can be applied to reinforce the system.
This wear coat is formulated as a 100 percent solids polyurethane and is typically installed using a squeegee, followed by back rolling to evenly distribute the material. Low odor and solvent-free, the wear coat can meet even stringent VOC compliance standards and is suitable for both indoor and outdoor environments. Once the product is applied but still wet, it is covered with a broadcast of dry silica sand—typically sized between #20 and #50 sieve—to rejection. It cures quickly, even in lower temperatures, allowing construction to continue without delay. The result is a textured, high-friction, durable surface that safeguards the membrane underneath from mechanical damage during ongoing construction activities. This additional layer is particularly beneficial in high-traffic zones or staging areas, and it can significantly extend the life and performance of the waterproofing assembly while allowing construction to proceed without compromising the integrity of the membrane.
Its resistance to heavy traffic makes it ideal for conditions involving scaffolding, carts, or rolling equipment, while its mechanical strength allows for direct application of mortar, concrete, or asphalt toppings.
The gray color of the wear coat also plays a practical role—it provides clear visual confirmation of full and even coverage over colored membranes, such as green or blue systems, which helps ensure application consistency. Though optional, the polyurethane wear coat offers a robust, jobsite-ready solution that safeguards the system’s long-term integrity and reduces the likelihood of premature repairs.
Color Stable Topcoat (Optional)
While the primary membrane in an instant-setting waterproofing system is designed for robust protection and durability, and formulated to be able to withstand prolonged exposure to ultraviolet (UV) light, it is not color stable. Over time, continuous UV exposure can lead to discoloration or surface degradation in many standard membrane materials. To address this, a specialized color-stable topcoat can be applied in areas where long-term UV exposure is unavoidable. This optional finish layer is a two-component, aliphatic polyurethane coating designed to resist color change, chalking, and deterioration from sunlight. The color stable topcoat is installed in two layers, first layer at 10 mils and second layer at 10 mils for a 20 mils coverage total. Color options usually fall in the gray or tan range, promoting solar reflectance.
The color-stable topcoat is typically reserved for exposed details such as pipe penetrations, mechanical curbs, vertical terminations, and other transition points that remain visible or unprotected by overburden. In these conditions, the topcoat not only maintains the visual appearance of the waterproofing system but also reinforces its performance by adding an additional layer of protection. Its aliphatic composition provides excellent weathering resistance, making it suitable for both vertical and irregular surfaces. Although not required across the entire field membrane, this targeted use of a UV-resistant finish helps preserve the integrity and aesthetics of the waterproofing system in locations most susceptible to environmental exposure.
Understanding Component Installation
Instant-setting waterproofing systems are a monolithic solution with minimal components and no fabric reinforcement, making it easy to install with little risk of human error. With a working knowledge of the layers and how the physical attributes contribute to a complete waterproofing assembly, understanding how each component is installed is the next step. This is important because proper installation is the best practice to ensure that the system will work as intended.
Equipment
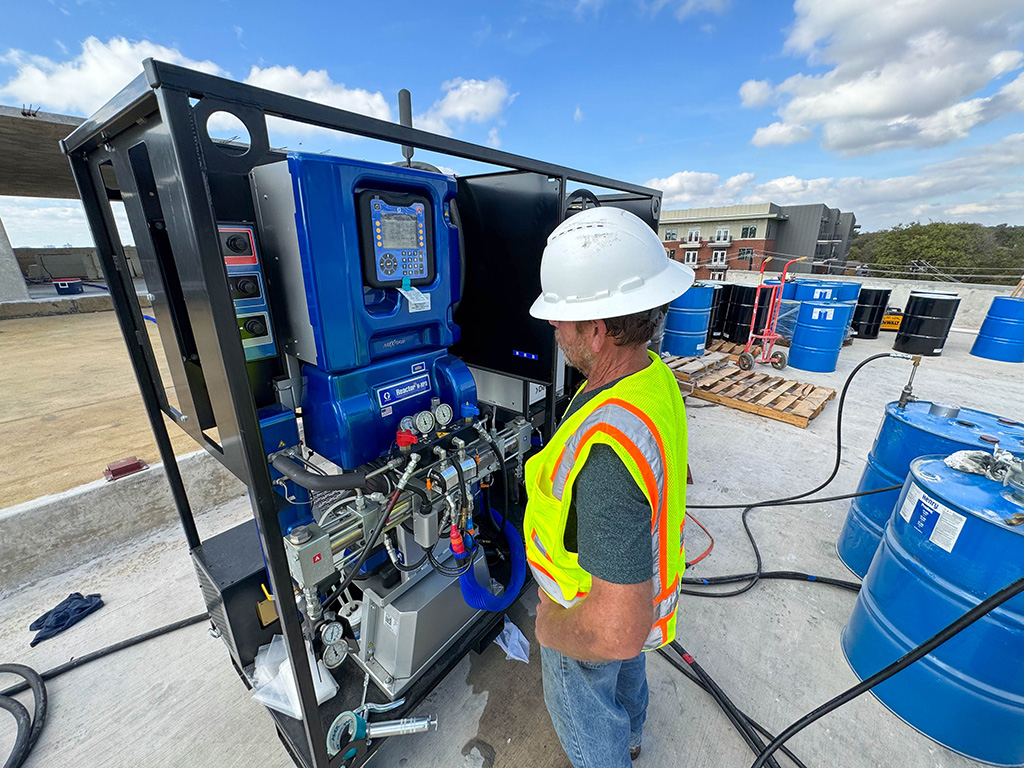
Photo courtesy of Henry, a Carlisle Company
Although the equipment for installing instant-setting cold fluid-applied waterproofing systems may seem complicated, in practice, the use of digital controls to monitor and adjust material mixing makes the process efficient and practical for large areas and rapid application.
Spray-applied, instant-setting waterproofing systems are known for their remarkable speed and performance, especially in complex or irregular construction conditions. These systems rely on advanced plural-component spray equipment, which mixes two reactive materials right at the spray tip to begin an immediate curing reaction. To those unfamiliar with the process, the machinery might appear daunting, especially with its demands for precise material ratios, controlled temperatures, and consistent membrane thickness. However, most of these technical requirements are managed by integrated digital controls. Modern spray rigs come equipped with onboard monitoring systems that automatically regulate mixing, pressure, and heating, giving the installer real-time feedback and allowing fine adjustments as needed.
In practice, the application process is typically handled by a two-person team—one technician applies the membrane while the other manages the mixing station and replaces 50-gallon drums of material as necessary. Once the method is understood and the crew is trained, installation becomes a streamlined, low-strain operation capable of covering thousands of square feet in a single day. The portability of the spray equipment is another advantage, with hoses and rigs capable of reaching up to 400 feet vertically, making the system particularly useful on high-rise buildings and other vertical applications.
Despite this efficiency, the system does require a higher degree of specialization than conventional waterproofing methods. Installers must be manufacturer-authorized, having completed certification and training programs to ensure proper use of the equipment and adherence to strict installation standards. This level of oversight isn’t just a formality—it’s a critical part of maintaining the quality and performance of the waterproofing system. In fact, premium warranties from manufacturers often depend on this level of quality assurance, covering not only the materials but also the labor and technical supervision. In many cases, a certified technician is dispatched by the manufacturer to the site to oversee the spray rig setup and ensure the application meets all performance benchmarks. This comprehensive approach gives designers, builders, and owners greater confidence in the long-term durability of the system.
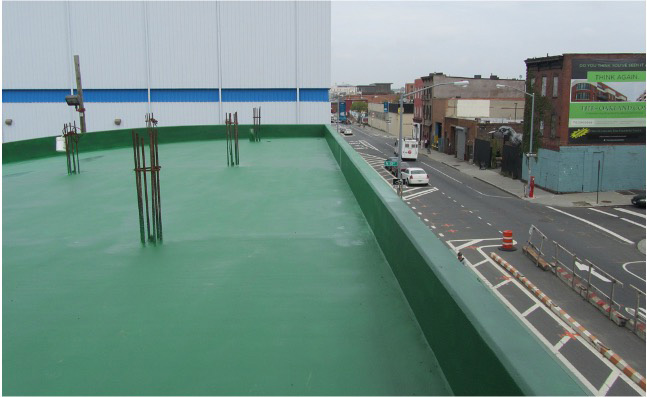
Photo courtesy of Henry, a Carlisle Company
The instant-setting properties of cold fluid-applied waterproofing systems allow for the field membrane to be installed onto both vertical and horizontal substrates.
Substrate Preparation
Spray-applied, instant-setting waterproofing membranes are highly versatile and compatible with a wide range of construction substrates, making them suitable for a variety of project types and detailing conditions. These membranes can be applied directly to common materials such as cast-in-place concrete, exterior-grade sheathing, plywood, cement board, wood decking, and rigid insulation cover boards. They also adhere effectively to metals and plastics, including aluminum, steel, and rigid PVC pipe penetrations, provided that appropriate primers are used to ensure chemical compatibility and bonding strength. Additionally, the system can be installed over masonry surfaces and select roofing materials, including SBS-modified bitumen cap sheets.
SBS, or Styrene-Butadiene-Styrene, is a synthetic rubber modifier commonly used in roofing and waterproofing membranes to enhance flexibility, strength, and weather resistance. When applied to granulated SBS cap sheets, the spray-applied membrane can conform to the textured surface and form a continuous, fully bonded layer. This compatibility makes it an effective option for detailing tie-ins or transitions where different waterproofing systems converge. The ability to adhere to such a broad range of materials allows architects and contractors to detail complex assemblies with fewer products and fewer transitions, improving long-term performance while simplifying installation.
Structural concrete is one of the most used substrates for waterproofing systems due to its strength, durability, and widespread application in commercial and institutional construction. However, despite its popularity, proper surface preparation and curing practices are essential to ensure compatibility with spray-applied, instant-setting membranes. When using a standard epoxy primer, structural concrete must be allowed to cure for a minimum of 28 days. This curing period allows the concrete to achieve a sufficient degree of hydration, stabilize its moisture content, and reach the required compressive strength of at least 2,500 psi. For lightweight structural concrete, which contains aggregates like expanded shale or clay and retains more internal moisture, the required cure time extends to 60 days. In both cases, a minimum tensile bond strength of 200 psi is recommended to ensure long-term membrane adhesion.
In time-sensitive projects or conditions where full cure periods cannot be met, instant-setting membranes can still be installed onto green concrete. However, this requires the use of a moisture-tolerant or vapor-mitigating primer specifically designed for uncured substrates. Green concrete, typically defined as concrete less than seven days old, presents unique challenges due to high moisture vapor transmission and incomplete hydration, both of which can interfere with standard primers and membrane bonding. Manufacturers often provide guidance on acceptable primer options and installation timing for green concrete applications, and consultation is recommended for project-specific recommendations.
Surface preparation of concrete is another critical factor. If a curing compound has been used to slow the hydration process and reduce shrinkage cracks, only sodium silicate-based compounds are considered acceptable. Oil- or resin-based curing compounds can leave residues that prevent proper adhesion and must be avoided.
To ensure proper adhesion, the surface must have the correct texture or roughness, commonly referred to as a concrete surface profile, or CSP. These profiles are defined by the International Concrete Repair Institute (ICRI) and range from CSP 1 (nearly smooth) to CSP 10 (extremely rough). For waterproofing membranes, the recommended range is CSP 3 to CSP 5, with CSP 3 to CSP 4 being ideal for achieving the published application rates of both primer and membrane.
CSP profiles in this range can be achieved through methods such as light shot blasting, grinding, or using a broom or wood float finish during concrete placement. These finishes create a surface that promotes mechanical interlock between the concrete and the waterproofing materials. If the surface profile is too smooth—classified as CSP 1 or CSP 2—it may not provide enough surface area for the membrane to bond effectively, increasing the risk of delamination or system failure. Conversely, if the profile exceeds CSP 4 or CSP 5, the increased surface area may require higher volumes of primer and membrane to adequately cover and seal the surface.
Additionally, all concrete substrates must be free from laitance, the weak, chalky layer that forms during curing. This layer impairs bonding and must be removed prior to primer or membrane application. Industry-recognized methods for laitance removal include shot blasting or mechanical grinding, both of which roughen the surface and expose sound, absorbent concrete. Addressing these preparation requirements ensures that the waterproofing system performs as intended, maintaining adhesion, continuity, and resistance to water migration over the life of the structure.
Metal surfaces require careful surface preparation prior to the application of a spray-applied, instant-setting waterproofing membrane to ensure proper adhesion and long-term performance. Unlike porous materials such as concrete or cement board, metal does not absorb primer or membrane materials, so achieving a secure mechanical and chemical bond is essential. The first step in this process is to remove any sharp edges, burrs, or welding slag that could puncture the membrane or interfere with application. Once the surface is physically smooth and safe, it must be mechanically abraded to create a profile that enhances adhesion.
Mechanical abrasion is commonly achieved through sandblasting, wire brushing, or grinding. This process removes any surface oxidation, mill scale, oil, or contaminants that could prevent proper bonding. After abrasion, the surface should be cleaned of dust and debris using compressed air or solvent wiping and then allowed to fully dry. At this stage, it is critical to apply the specified metal primer immediately to avoid flash rusting. For non-ferrous metals such as aluminum or copper, special primers may be required to address differences in surface chemistry.
PVC (rigid pipe) is a common feature for roofs and decks and must be prepared appropriately to ensure proper membrane adhesion. PVC, by nature, is a smooth and nonporous material, which means that without adequate preparation, the membrane or primer may not adhere reliably. The first step is to sand the surface of the pipe to create a uniform, roughened texture.
After sanding, the pipe must be thoroughly cleaned to remove all dust, plastic residue, and oils. Any remaining contaminants can act as a barrier between the primer and the pipe surface, potentially leading to blistering or delamination over time. Once clean and dry, the appropriate primer can be applied to promote strong chemical adhesion between the PVC and the waterproofing membrane.
In conditions where the pipe is expected to carry fluids at temperatures exceeding 150°F, a protective cool sleeve should be installed over the pipe before membrane application. This sleeve helps insulate the membrane from thermal stress, preventing softening or degradation of the waterproofing layer over time.
Addressing Gaps and Cracks in the Substrate
Imperfections in the concrete substrate, such as bug holes, voids, or cracks, are common, even in new construction projects. The surface must be carefully inspected, and any gaps or cracks need to be addressed before the primer and membrane are applied.
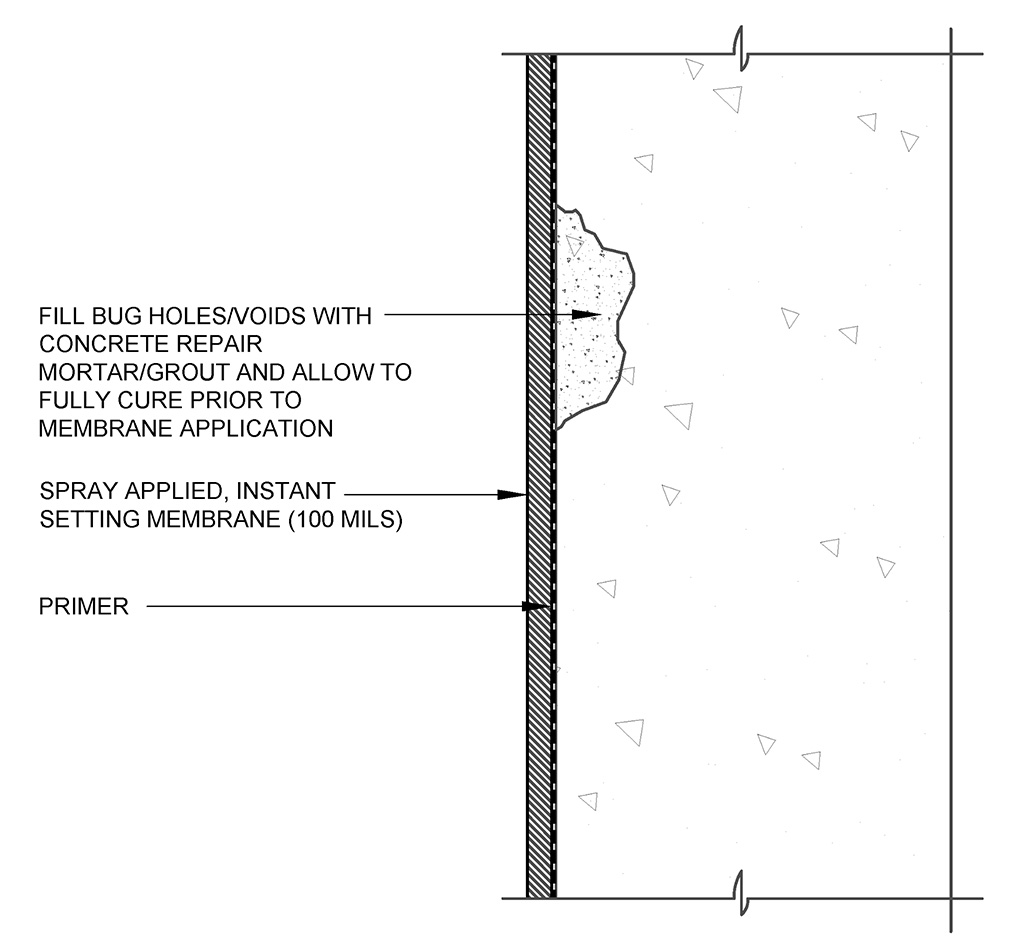
Image courtesy of Henry, a Carlisle Company
Bug holes—small air pockets formed during concrete placement—must be filled with a concrete repair mortar or grout before installation of a waterproofing system.
Bug holes—small air pockets formed during concrete placement—are common, especially on vertical surfaces. If left unaddressed, these surface irregularities can compromise the uniformity and bond of the waterproofing membrane. For vertical substrates, any bug holes or voids larger than ¼ inch by ¼ inch should be repaired using a compatible concrete repair mortar or grout. The repair material must be allowed to fully cure before primer or membrane is applied to ensure a stable, durable surface.
On horizontal deck surfaces, small bug holes of this size typically do not require a separate mortar repair. Instead, they can be treated during the pre-stripe phase of the waterproofing application, which we will discuss in the next section. After primer has been applied and any excess has been removed from the voids, the spray-applied, instant-setting membrane can be used to fill and seal these imperfections directly. This method simplifies the process while still maintaining the integrity of the waterproofing system. For any surface irregularities or deficiencies that exceed the ¼ inch by ¼ inch guideline, it is recommended to contact the membrane manufacturer for project-specific instructions.
Pre-Striped Layer
One of the defining advantages of instant-setting waterproofing systems is their simplified installation process, particularly when it comes to detailing and flashing. Unlike traditional sheet-based or fabric-reinforced systems, which often require multiple products and layers to manage transitions, penetrations, and substrate changes, this system is fully self-flashing. Before applying the main field membrane, installers use a technique known as pre-striping, in which the spray-applied membrane is applied at a thickness of approximately 40 mils to critical areas. This includes cracks, curbs, drains, posts, and any structural transitions where water intrusion is most likely to occur.
The pre-striped layer conforms easily to complex shapes and penetrations, forming a continuous, watertight seal without the need for fabric reinforcement or separate flashing materials. For instance, at mounting plates or base plates with mechanical fasteners, the membrane is sprayed to fully encapsulate bolts and edges, eliminating the traditional need for cutting and wrapping sheet materials. Once cured, the main field membrane—typically applied at 100 mils—is sprayed directly over these areas, resulting in a combined thickness of roughly 140 mils at vulnerable details. This approach not only reduces material complexity and labor but also enhances performance through monolithic continuity. With its high elongation, tensile strength, and crack-bridging capabilities, the system addresses common failure points without relying on patchwork methods.
After the pre-stripe flashing is set, the field membrane is quickly installed to 100 mils thick with little effort or wait time. The flashing material and field membrane are the same product, so there is no concern for chemical compatibility or adhesion. Additionally, due to the instant-setting properties, the field membrane can be installed on the same day onto both vertical and horizontal substrates.
Other Considerations
Transition details, especially at expansion joints, require careful attention during the design and installation of waterproofing systems. Expansion joints are critical components of a structure, allowing for controlled movement caused by thermal expansion, contraction, or seismic activity. Because these joints are designed to open and close over time, the waterproofing membrane must be terminated and detailed in a way that preserves this functionality.
Spray-applied, instant-setting waterproofing membranes should not be applied directly over open expansion joints, as the movement can exceed the membrane’s capacity for elongation and may lead to cracking, delamination, or leakage. Instead, the detailing at these locations must incorporate a joint-specific waterproofing solution, such as a preformed expansion joint cover or an engineered joint system compatible with the surrounding materials.
Installers and specifiers should refer to the expansion joint manufacturer’s technical guidelines to ensure proper integration with the waterproofing system. These details often include provisions for bond breakers, sealant joints, or mechanical covers designed to move independently from the adjacent waterproofed surfaces.
New Technologies Versus Old Ways
When comparing spray-applied, instant-setting waterproofing membranes to traditional hot rubberized asphalt systems, several advantages emerge that align well with modern construction demands, particularly in terms of ease of installation, speed, safety, and coordination with other trades. One of the most notable differences is the installation speed. Instant-setting membranes can cover up to 4,500 square feet per day per machine, nearly doubling the rate of hot-applied asphalt systems, which average around 2,500 square feet per day. This gain in efficiency can significantly reduce time on site, freeing up schedules for other scopes of work and minimizing weather-related delays.
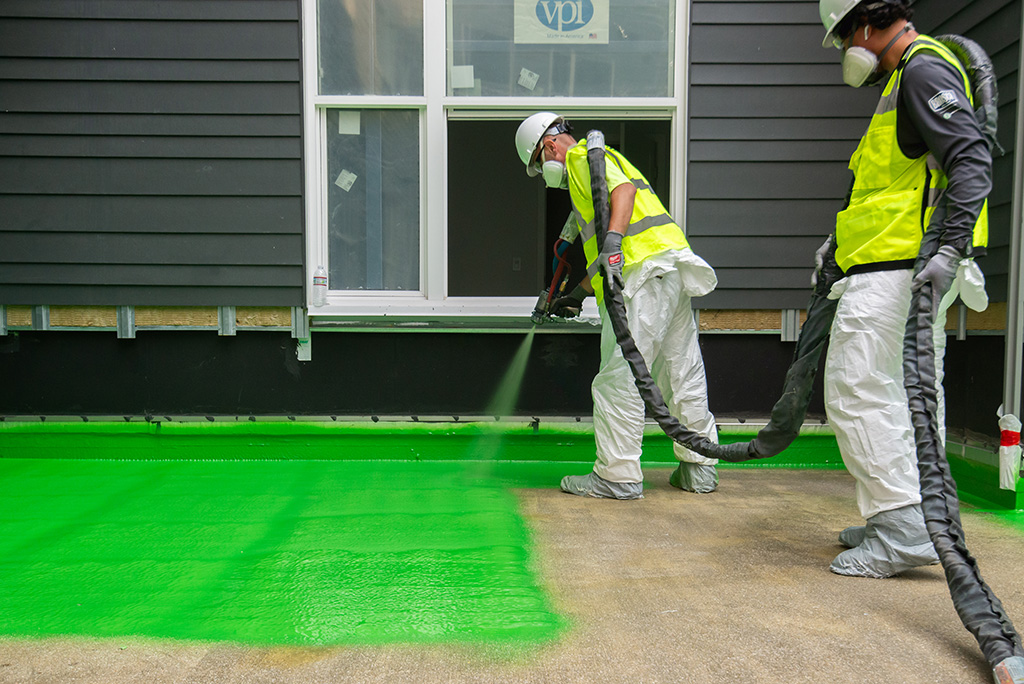
Photo courtesy of Henry, a Carlisle Company
Instant-setting membranes can cover up to 4,500 square feet per day per machine, nearly doubling the rate of hot-applied asphalt systems, which average around 2,500 square feet per day.
By contrast, instant-setting membranes are cold-applied and do not require open flames or hot kettles, eliminating the need for fire watches and reducing potential hazards to workers and building occupants. There are no fumes, hot materials, or odors, making these systems particularly well-suited for occupied buildings, sensitive environments, and projects with strict indoor air quality standards. Hot rubberized asphalt, by contrast, involves melting materials at high temperatures, posing both a logistical challenge and a safety concern, especially on enclosed job sites or near fresh air intakes.
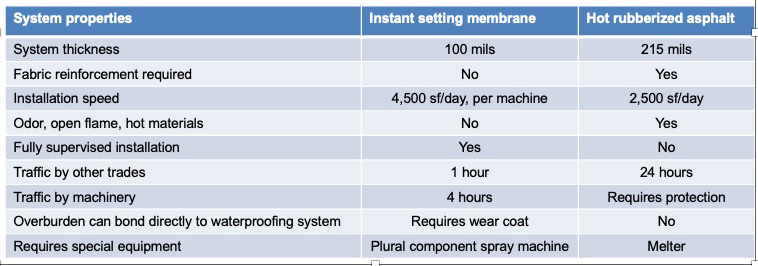
Image courtesy of Henry, a Carlisle Company
The benefits of instant-setting waterproof membranes are listed compared to traditional hot rubberized asphalt systems.
Waterproofing warranties are an important consideration when evaluating long-term performance and risk mitigation for a building envelope system. These warranties typically fall into three categories: material, system, and premium warranties. Each offers a different level of protection and responsibility, and understanding the distinctions can help project teams select the right coverage for their needs.
A material warranty is the most basic level of coverage. It guarantees that the product is free from manufacturing defects at the time of sale and that it will not degrade, break down, or disintegrate under normal conditions. While this type of warranty protects against faulty materials, it does not cover labor or the cost of removing and reinstalling the system should a problem occur.
System warranties go a step further by including the benefits of the material warranty and covering the cost of removing and replacing the overburden in the event of a leak caused by defective materials. This type of warranty does not include installation errors, but it adds meaningful value by covering the logistical and labor-related costs associated with accessing the membrane for repair. System warranties are typically available at no additional charge and are often offered in terms of up to 20 years, making them the most common and practical option for many projects.
Premium warranties provide the most comprehensive protection. In addition to covering manufacturing defects and the removal and replacement of overburden due to material failure, these warranties also extend coverage to include workmanship issues. If a leak is caused by faulty installation, the premium warranty ensures that both the labor and material costs are addressed, including the reinstallation of any overburden or finishes above the membrane. This level of coverage requires installers to be manufacturer-authorized and comes with a fee that varies based on the product type and the total square footage of the project. For high-value or mission-critical installations, a premium warranty can offer the highest level of assurance and peace of mind.
Conclusion
Traditional waterproofing systems, while proven in some applications, present a variety of challenges during both design and installation that can limit their effectiveness and increase project complexity. One of the most common obstacles is the slow and labor-intensive nature of their application. Many traditional systems require multiple layers—such as primer, reinforcement fabric, and topcoats—which translates into longer installation times and increased labor costs, as well as complicated sequencing and timing on the jobsite. This can place strain on project schedules, particularly when waterproofing is a critical path item that must be completed before other trades can proceed.
Design flexibility is another concern. In areas where architectural tolerances are tight—such as low door thresholds, shallow parapets, or confined mechanical enclosures—traditional systems may not be feasible or may require custom detailing that adds time and risk. Complex geometry, irregular penetrations, and transitions between materials can further complicate the installation and increase the likelihood of failure at weak points.
Occupant safety and health are also important considerations. Many traditional systems use hot-applied materials, open flames, or solvent-based components that pose fire hazards or release harmful fumes during installation. This can be particularly problematic in occupied buildings, healthcare environments, or facilities with sensitive operations where air quality and fire safety are non-negotiable.
In terms of durability and life cycle, traditional waterproofing systems may be more susceptible to damage during construction, especially from foot traffic or heavy equipment. Membrane punctures or displacement during the build phase can compromise the system’s integrity before it is ever put into service. Long-term performance may also be limited by materials that degrade over time or under UV exposure, requiring eventual removal, disposal, and replacement, resulting in increased environmental and financial costs. Warranty coverage is often restricted as well, with limited terms and minimal manufacturer oversight, particularly when overburden or specialty assemblies are involved. These cumulative factors highlight the need for more resilient, adaptable, and streamlined waterproofing technologies in modern construction.
In terms of coordination, instant-setting membranes allow for foot traffic within one hour and construction equipment access within four hours. This enables other trades to resume work quickly and reduces downtime between waterproofing and follow-on activities. Hot rubberized asphalt systems typically require a full 24-hour cure before foot traffic is allowed and additional protective layers to support machinery, adding complexity and delay to the construction sequence. Furthermore, instant-setting membranes require no fabric reinforcement, simplifying detailing and reducing the number of installation steps, whereas hot rubberized asphalt systems depend on multiple layers and embedded reinforcement to achieve system integrity.
Overall, instant-setting waterproofing offers a more streamlined and performance-oriented solution for today’s fast-paced, safety-conscious, and tightly scheduled projects. Its combination of rapid cure, minimal disruption, and durable performance makes it a compelling choice for architects and contractors seeking to deliver high-quality enclosures efficiently.
Andrew A. Hunt is Vice President of Confluence Communications and specializes in writing, design, and production of articles and presentations related to sustainable design in the built environment. In addition to instructional design, writing, and project management, Andrew is an accomplished musician and voice-over actor, providing score and narration for both the entertainment and education arenas. www.confluencec.com, https://www.linkedin.com/in/andrew-a-hunt-91b747/