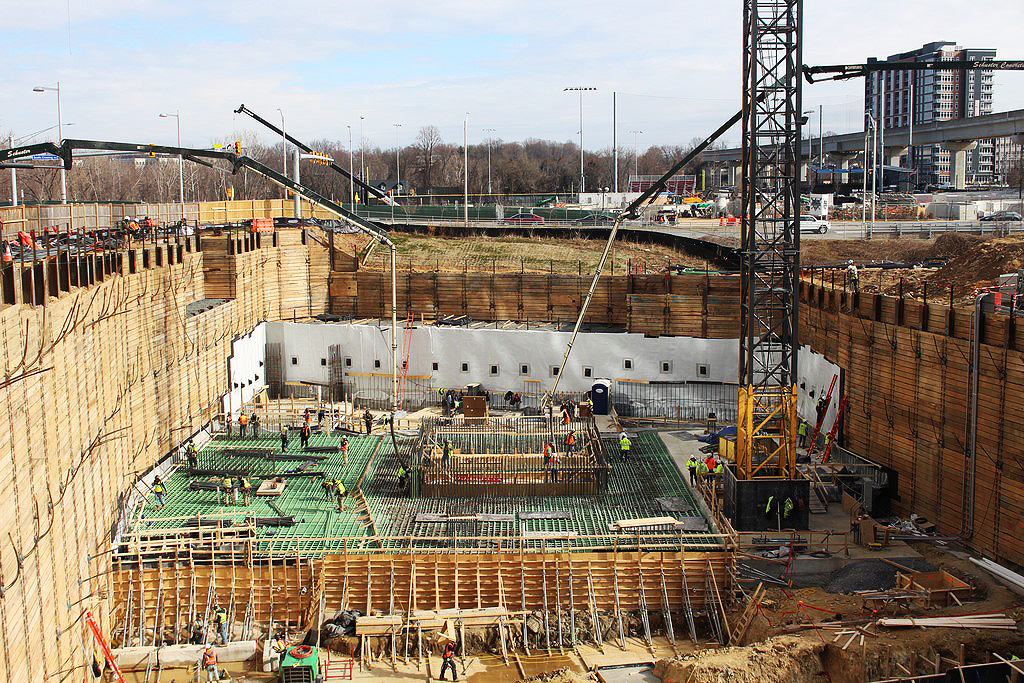
Image provided by Carlisle
Blindside waterproofing is applied before the concrete is placed. There is only one chance to get it right.
Few systems pose the serious number of challenges the designer finds in blindside waterproofing. The system must be designed and installed with extra attention because there is no going back once the concrete is placed. The most critical factor in creating a successful waterproofing barrier for below-grade spaces is the selection of the system. Blindside waterproofing has evolved over the past few decades, and relatively new and innovative systems, such as a dual-bond system that bonds both mechanically and chemically to concrete, provide better outcomes and prevent lateral water migration in case of leakage. This course explores the evolution of and need for blindside waterproofing and dives into the various materials and systems to meet that need. It also provides valuable specification types to ensure the process of installing the blindside waterproofing system and protecting its integrity until concrete placement. With careful execution, the system will achieve the goal of a continuous below-grade waterproofing barrier that ensures a dry and functional building.
What Is Blindside Waterproofing?
Blindside waterproofing is the foundation waterproofing method of choice whenever excavation past the foundation walls isn’t possible. Think zero lot line sites where the new foundation will border existing walls or locations otherwise inaccessible to heavy equipment. Two sets of terms are pertinent here: Pre-applied vs. post-applied waterproofing and positive-side vs. negative-side waterproofing.
Post-applied waterproofing is applied to the exterior foundation wall after the concrete placement. Pre-applied waterproofing, also known as blindside waterproofing, is installed before the concrete foundation is placed. In other words, the waterproofing membrane is applied to the adjacent wall or shoring, which can be soldier pile, metal sheet piling, caissons, or shotcrete. Once the waterproofing membrane is in place and fully detailed, the structural walls are placed, and the foundation is poured.
Positive-side waterproofing applies to both post-applied and pre-applied applications mentioned above, which means putting the waterproofing product at the source of where the water will come from.
For positive-side waterproofing, refer to ASTM D1079—Standard Terminology Relating to Roofing and Waterproofing. “Application whereas the waterproofing system and the source of hydrostatic pressure are on the same side of the structural element.” Structural concrete and steel reinforcement are protected. Interior space is protected.
Negative-side waterproofing, on the other hand, is placement of the waterproofing product on the opposite side of where the water will come from. In a positive post-applied application, the concrete is in place, and the waterproofing membrane goes on top of it, with or without protection board or drainage composite, followed by the backfill.
Another form of pre-applied or blindside application is an underslab, which will be a familiar concept to most designers. The waterproofing membrane sits on the substrate, which could be soil, compacted stone, or even a mud slab, with the reinforcing steel and concrete on top. It’s most important to understand that blindside means there will not be a second chance to address what’s on the other side. So, you’re going into it blind.
Why Is the Need for Blindside Waterproofing Growing?
Blindside waterproofing increased as more buildings were constructed in heavily populated areas. This precluded the luxury of extending the soil retention system sufficiently beyond the foundation to permit application on the positive side of foundation walls. The construction of underground parking garages grew to accommodate increased automobile use in bustling cities.
Many strategies to keep water out of below-grade spaces have been tried over time, including additives to concrete to resist water infiltration and aggressive and costly water pumping with discharge to sewage systems. The former had limited success, and the latter found resistance from local utilities that didn’t want to process the discharge. Another downside was frequent disruptions resulting in damage due to loss of power.
Increasingly, superior below-grade waterproofing was needed for high-risk occupancies, such as IT spaces, museum storage, and hospital mechanicals. This prompted manufacturers of waterproofing membranes to develop new products, with some robust innovations emerging in just the past few years.
History of Blindside Waterproofing Technologies
Pre-1990: Bentonite and Conventional waterproofing (asphalt) technologies dominated the market.
The 1990s: Fully adhered introduced: Manufacturers either redesigned/tweaked post-applied technologies or developed blindside-specific technologies.
The 2000s: Hybrid waterproofing: “Next generations” and prefabbed detailing accessories were developed and introduced.
The 2020s: Fully adhered/welded dual bond: Fully adhered with welded seams proliferated, and dual-bond technology was introduced.
Blindside Waterproofing Challenges
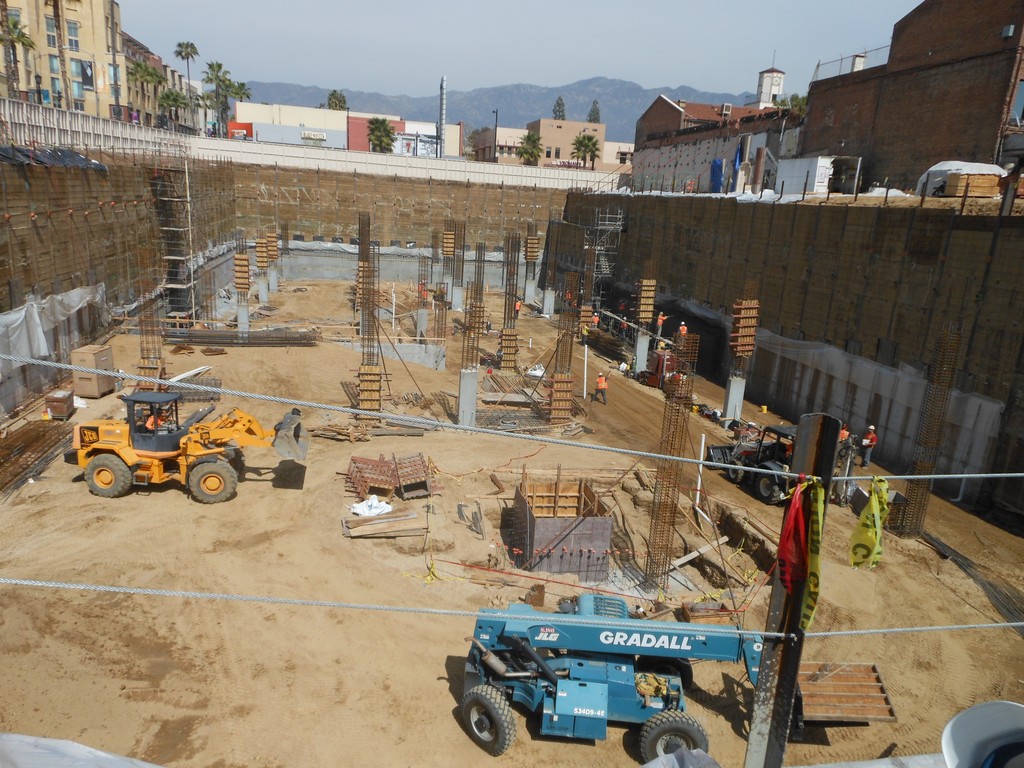
Image courtesy of Carlisle
Mitigating and managing risks to a blindside waterproofing product are necessary for a successful installation.
Maintaining the integrity of the waterproofing membrane is essential for an effective blindside system, but several risks can push this goal out of reach. Selecting and installing an effective waterproofing product is about managing and mitigating these risks since, in most cases, factors other than the waterproofing membrane itself are responsible for water intrusion.
Know the Hydrogeology
Hydrogeology is a specialty of geology focused on the distribution and movement of groundwater in the soil. Knowing the hydrogeological condition of the project site is essential since maximum water table height directly impacts waterproofing membrane selection, as does the hydrostatic pressure it produces at different times of the year.
Environmental Concerns
Temperature restrictions at the time of installation are also necessary. Certain waterproofing products can be impacted by low-temperature conditions, which affect membrane pliability in severe cold. Many waterproofing membranes also contain adhesives or hydrophilic materials that can be compromised by prolonged UV exposure. In addition to UV considerations, groundwater and site contaminants can impact the performance of blindside membranes. In urban areas, repurposing land that was once an industrial site can influence the technology associated with ensuring waterproofing performance.
Substrate Impact
Selecting a waterproofing type depends on the substrate type and/or the substrate condition. Most pre-applied waterproofing technologies have different substrate requirements depending on the excavation support system type (soldier pile, metal sheet piling, caissons, or shotcrete). If the substrate is unsuitable for a given waterproofing membrane, the membrane may not bond appropriately to the concrete, resulting in a failed seam and leading to water intrusion.
Substrate Preparation
Prior to installing the waterproofing membrane, the substrate surface must be as smooth, clean, and dry as possible. The presence of voids, wires, or any other surface irregularities will affect membrane effectiveness, so proper substrate preparation is as essential as selecting the proper waterproofing membrane for the substrate.
Installation Issues
Even with careful substrate preparation, installers must contend with penetrations in the waterproofing membrane. They must be detailed before the foundation wall is poured, as such penetrations will allow water to bypass the membrane and reach the foundation. Corners, joints, transitions, or any area with a seam will also require additional detailing.
Accordingly, waterproofing products that have high puncture resistance and are installation-friendly generally perform best in pre-applied applications. Membranes that are easier to transition up a wall or detail offer a greater chance of success than more labor-intensive systems. After all, more labor-intensive systems requiring more intense detailing by nature offer a greater likelihood of membrane damage.
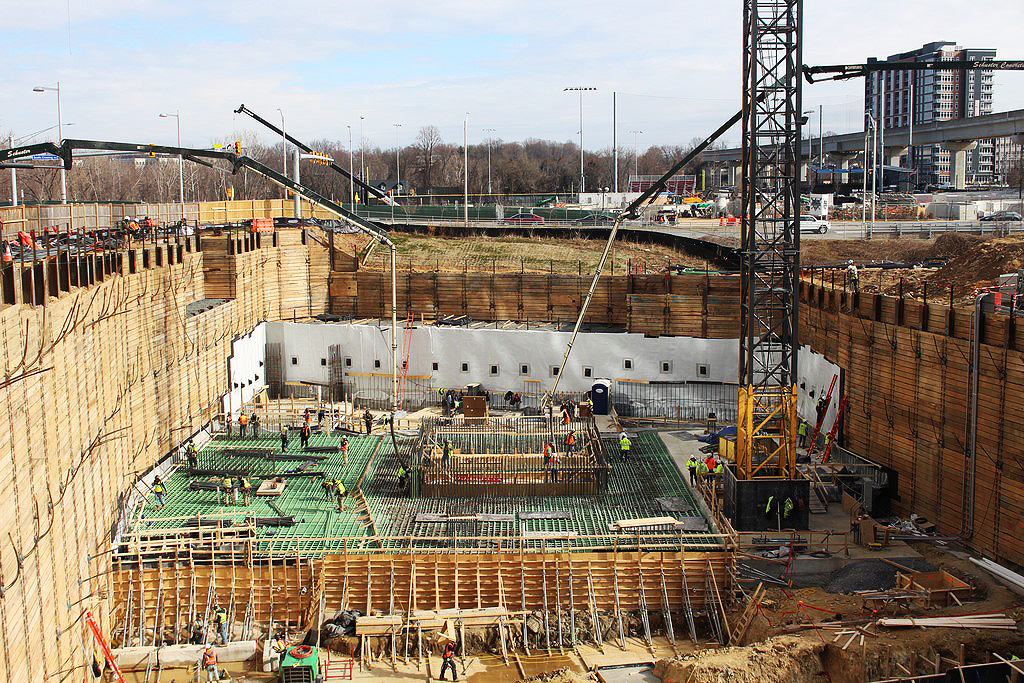
Image provided by Carlisle
Blindside waterproofing is applied before the concrete is placed. There is only one chance to get it right.
Few systems pose the serious number of challenges the designer finds in blindside waterproofing. The system must be designed and installed with extra attention because there is no going back once the concrete is placed. The most critical factor in creating a successful waterproofing barrier for below-grade spaces is the selection of the system. Blindside waterproofing has evolved over the past few decades, and relatively new and innovative systems, such as a dual-bond system that bonds both mechanically and chemically to concrete, provide better outcomes and prevent lateral water migration in case of leakage. This course explores the evolution of and need for blindside waterproofing and dives into the various materials and systems to meet that need. It also provides valuable specification types to ensure the process of installing the blindside waterproofing system and protecting its integrity until concrete placement. With careful execution, the system will achieve the goal of a continuous below-grade waterproofing barrier that ensures a dry and functional building.
What Is Blindside Waterproofing?
Blindside waterproofing is the foundation waterproofing method of choice whenever excavation past the foundation walls isn’t possible. Think zero lot line sites where the new foundation will border existing walls or locations otherwise inaccessible to heavy equipment. Two sets of terms are pertinent here: Pre-applied vs. post-applied waterproofing and positive-side vs. negative-side waterproofing.
Post-applied waterproofing is applied to the exterior foundation wall after the concrete placement. Pre-applied waterproofing, also known as blindside waterproofing, is installed before the concrete foundation is placed. In other words, the waterproofing membrane is applied to the adjacent wall or shoring, which can be soldier pile, metal sheet piling, caissons, or shotcrete. Once the waterproofing membrane is in place and fully detailed, the structural walls are placed, and the foundation is poured.
Positive-side waterproofing applies to both post-applied and pre-applied applications mentioned above, which means putting the waterproofing product at the source of where the water will come from.
For positive-side waterproofing, refer to ASTM D1079—Standard Terminology Relating to Roofing and Waterproofing. “Application whereas the waterproofing system and the source of hydrostatic pressure are on the same side of the structural element.” Structural concrete and steel reinforcement are protected. Interior space is protected.
Negative-side waterproofing, on the other hand, is placement of the waterproofing product on the opposite side of where the water will come from. In a positive post-applied application, the concrete is in place, and the waterproofing membrane goes on top of it, with or without protection board or drainage composite, followed by the backfill.
Another form of pre-applied or blindside application is an underslab, which will be a familiar concept to most designers. The waterproofing membrane sits on the substrate, which could be soil, compacted stone, or even a mud slab, with the reinforcing steel and concrete on top. It’s most important to understand that blindside means there will not be a second chance to address what’s on the other side. So, you’re going into it blind.
Why Is the Need for Blindside Waterproofing Growing?
Blindside waterproofing increased as more buildings were constructed in heavily populated areas. This precluded the luxury of extending the soil retention system sufficiently beyond the foundation to permit application on the positive side of foundation walls. The construction of underground parking garages grew to accommodate increased automobile use in bustling cities.
Many strategies to keep water out of below-grade spaces have been tried over time, including additives to concrete to resist water infiltration and aggressive and costly water pumping with discharge to sewage systems. The former had limited success, and the latter found resistance from local utilities that didn’t want to process the discharge. Another downside was frequent disruptions resulting in damage due to loss of power.
Increasingly, superior below-grade waterproofing was needed for high-risk occupancies, such as IT spaces, museum storage, and hospital mechanicals. This prompted manufacturers of waterproofing membranes to develop new products, with some robust innovations emerging in just the past few years.
History of Blindside Waterproofing Technologies
Pre-1990: Bentonite and Conventional waterproofing (asphalt) technologies dominated the market.
The 1990s: Fully adhered introduced: Manufacturers either redesigned/tweaked post-applied technologies or developed blindside-specific technologies.
The 2000s: Hybrid waterproofing: “Next generations” and prefabbed detailing accessories were developed and introduced.
The 2020s: Fully adhered/welded dual bond: Fully adhered with welded seams proliferated, and dual-bond technology was introduced.
Blindside Waterproofing Challenges
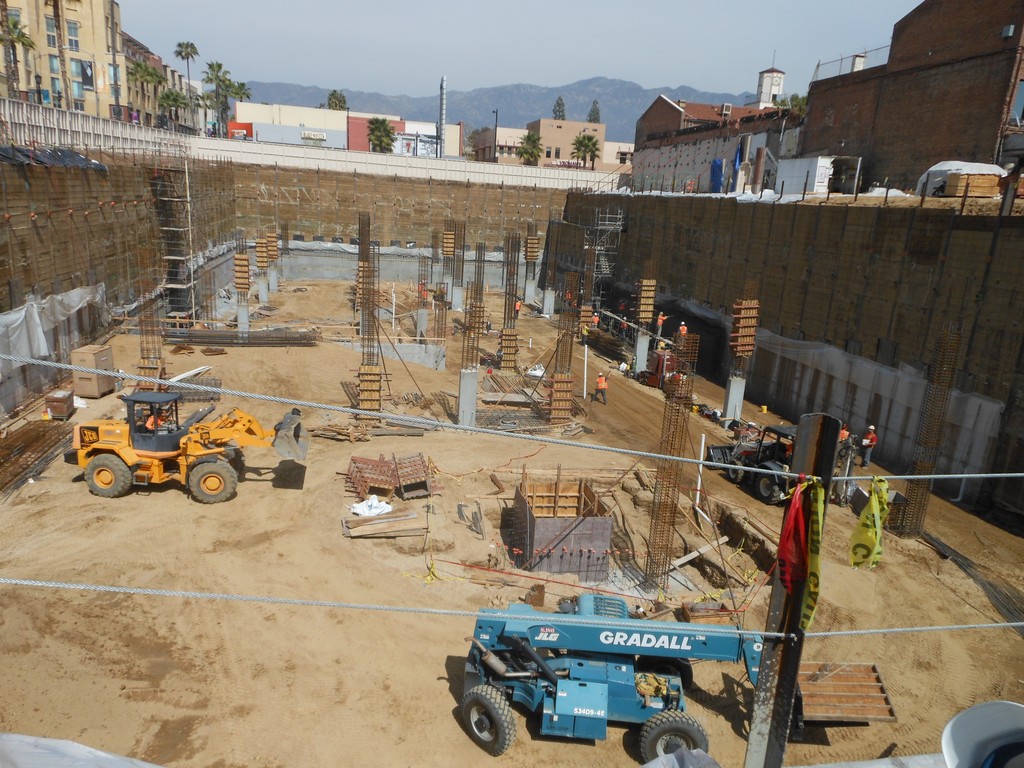
Image courtesy of Carlisle
Mitigating and managing risks to a blindside waterproofing product are necessary for a successful installation.
Maintaining the integrity of the waterproofing membrane is essential for an effective blindside system, but several risks can push this goal out of reach. Selecting and installing an effective waterproofing product is about managing and mitigating these risks since, in most cases, factors other than the waterproofing membrane itself are responsible for water intrusion.
Know the Hydrogeology
Hydrogeology is a specialty of geology focused on the distribution and movement of groundwater in the soil. Knowing the hydrogeological condition of the project site is essential since maximum water table height directly impacts waterproofing membrane selection, as does the hydrostatic pressure it produces at different times of the year.
Environmental Concerns
Temperature restrictions at the time of installation are also necessary. Certain waterproofing products can be impacted by low-temperature conditions, which affect membrane pliability in severe cold. Many waterproofing membranes also contain adhesives or hydrophilic materials that can be compromised by prolonged UV exposure. In addition to UV considerations, groundwater and site contaminants can impact the performance of blindside membranes. In urban areas, repurposing land that was once an industrial site can influence the technology associated with ensuring waterproofing performance.
Substrate Impact
Selecting a waterproofing type depends on the substrate type and/or the substrate condition. Most pre-applied waterproofing technologies have different substrate requirements depending on the excavation support system type (soldier pile, metal sheet piling, caissons, or shotcrete). If the substrate is unsuitable for a given waterproofing membrane, the membrane may not bond appropriately to the concrete, resulting in a failed seam and leading to water intrusion.
Substrate Preparation
Prior to installing the waterproofing membrane, the substrate surface must be as smooth, clean, and dry as possible. The presence of voids, wires, or any other surface irregularities will affect membrane effectiveness, so proper substrate preparation is as essential as selecting the proper waterproofing membrane for the substrate.
Installation Issues
Even with careful substrate preparation, installers must contend with penetrations in the waterproofing membrane. They must be detailed before the foundation wall is poured, as such penetrations will allow water to bypass the membrane and reach the foundation. Corners, joints, transitions, or any area with a seam will also require additional detailing.
Accordingly, waterproofing products that have high puncture resistance and are installation-friendly generally perform best in pre-applied applications. Membranes that are easier to transition up a wall or detail offer a greater chance of success than more labor-intensive systems. After all, more labor-intensive systems requiring more intense detailing by nature offer a greater likelihood of membrane damage.
Substrates
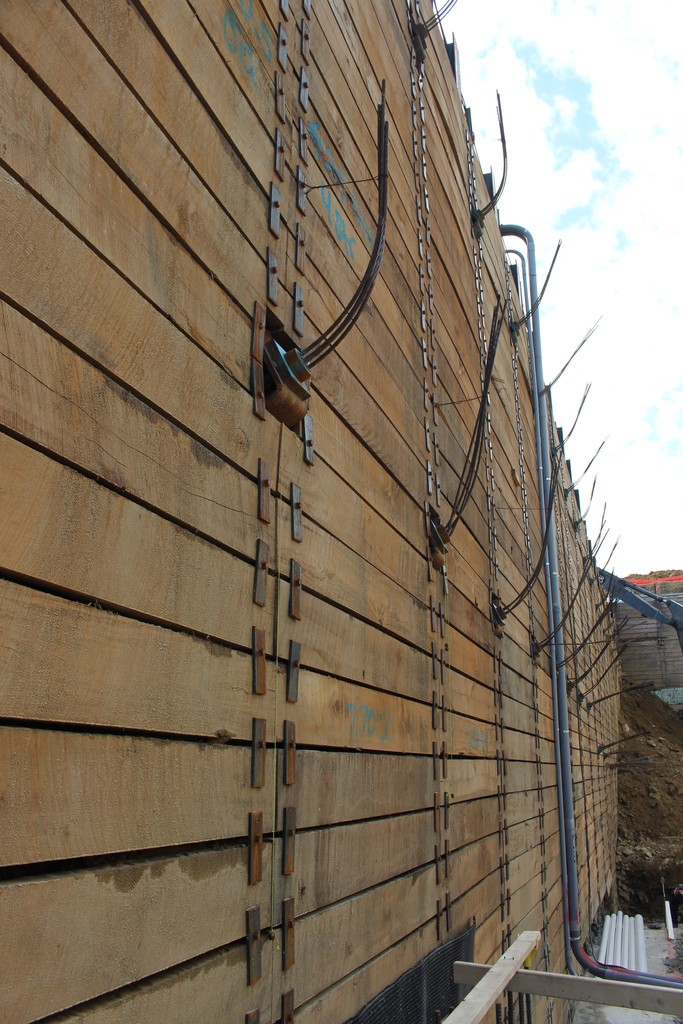
Image courtesy of Carlisle
The substrate, such as a lagging wall, provides a surface to receive a waterproofing system.
It’s helpful to understand that the substrate is not being waterproofed. Instead, it provides a surface to receive a blindside waterproofing system. The structure being waterproofed doesn’t exist yet. The substrate holds the waterproofing system in place until the concrete placement.
There are various substrate types for both underslab and foundation wall substrates. Site conditions can change during construction. Both groundwater and rainwater can compromise the quality of the substrate and, potentially, the waterproofing system.
Underslab Substrates Challenges
In a subgrade application, subbase and base materials must be adequately prepared prior to blindside waterproofing. Refer to American Concrete Institute Report 360R-10: Design of Slabs-on-Ground. A mud slab, also called a rat slab, is a non-reinforced concrete working surface. It should be smooth with no exposed aggregate.
Dewatering
As experience has shown, in some cases, the specified dewatering plan is not always adequate for a blindside waterproofing system. The typical “sump and pump” is designed to collect and discharge groundwater and “some” inclement weather. Additional dewatering may be required. The contractor should submit a revised or supplemental dewatering plan per project-specific conditions.
Inspect, Then Inspect Again
Doing it right the first time is the goal for all aspects of building construction, but for blindside waterproofing, it’s essential. Once the foundation concrete is poured, repairing damage from water intrusion will be extremely difficult, if not impossible. All detailing and membrane areas should be carefully inspected and reinspected before any foundation concrete is poured. Coordination and sequencing are crucial to creating what all parties want: a continuous, defect-free waterproofing barrier/envelope. This is unlike a roofing project, for comparison, where the roofing can be pulled up and fixed later on if there is a leaking problem. In the case of pre-applied waterproofing, there is only one chance to get it right. A broader discussion of coordination and sequencing appears later in the course.
Blindside Waterproofing Products and Technologies
One size does not fit all for pre-applied waterproofing jobs. So, what tips the scale for one solution over another? The main factor is risk tolerance. Before selecting a pre-applied waterproofing system, design professionals should determine the property owner’s risk tolerance or ownership plan. The primary factors that influence risk tolerance include building use (new development or owner-occupied) and geotechnical conditions. Manufacturers offer pre-applied waterproofing solutions that address high-, medium-, and low-risk profiles.
Types of Bonds
How a blindside waterproofing membrane interacts with the building may influence how it performs and how easy it is to repair. Here are the types of bonds.
Adhesive bond: An adhesive bond fully seals the waterproofing membrane to the concrete, effectively halting lateral water movement. This close and continuous seal ensures that the waterproofing membrane acts as a continuous barrier, significantly reducing the risk of water intrusion and safeguarding a structure’s integrity.
Mechanical bond: A mechanical bond is a physical connection typically between the pre-applied membrane and the concrete cast against it. The absence of a close and continuous seal to the concrete surface falls short when resisting lateral water migration. For example, a geotextile fabric cannot wholly penetrate the concrete, allowing water to travel laterally within the geotextile fabric, and potentially leading to widespread water ingress issues.
- Dual bond: The membrane forms both an adhesive and mechanical bond to concrete. It does not allow water to travel between the membrane and the structure. It allows for early form removal while ensuring a close and continuous seal to the concrete.
- Non-bonded: The membrane is “loose laid” and forms no bond to concrete. It allows water to travel between the membrane and the structure.
ASTM Standards for Lateral Water Migration
Safeguarding investments from lateral water migration begins with choosing the right waterproofing membrane. Not all membranes are created equal. How they bond to concrete is key to preventing lateral water migration and is critical to their success or failure. Adhesively bonded membranes will not allow water to travel between the membrane and the substrate. Mechanically bonded and non-bonded membranes will allow water to travel between the membrane and the substrate. This is especially relevant when the structure is exposed to groundwater and a membrane defect exists due to poor workmanship or damage by other trades.
The American Society for Testing and Materials (ASTM) is currently developing a standardized test method to assess the resistance of pre-applied (or blindside) waterproofing membranes to lateral water migration. ASTM describes lateral water migration as the movement of water from a breach in the waterproofing system along the interface between the cured concrete and the pre-applied waterproofing membrane. Lateral water migration can lead to extensive and expensive leak remediation repairs.
Blindside Technologies
- Fully adhered sheet
- Dual-bonded sheet
- Active waterproofing technologies
- Mechanically bonded sheet
- Non-bonded sheet
This is a polymeric or elastomeric sheet bonded to a specialty adhesive. No curing is required. It is unaffected by temperature and weather. It does not require confinement/constant pressure to perform. It has adhesive or welded seams. It forms an adhesive bond/seal to concrete. Limitations include that seams and laps must be watertight. The membrane must be clean before concrete placement.
Dual-Bonded Sheet
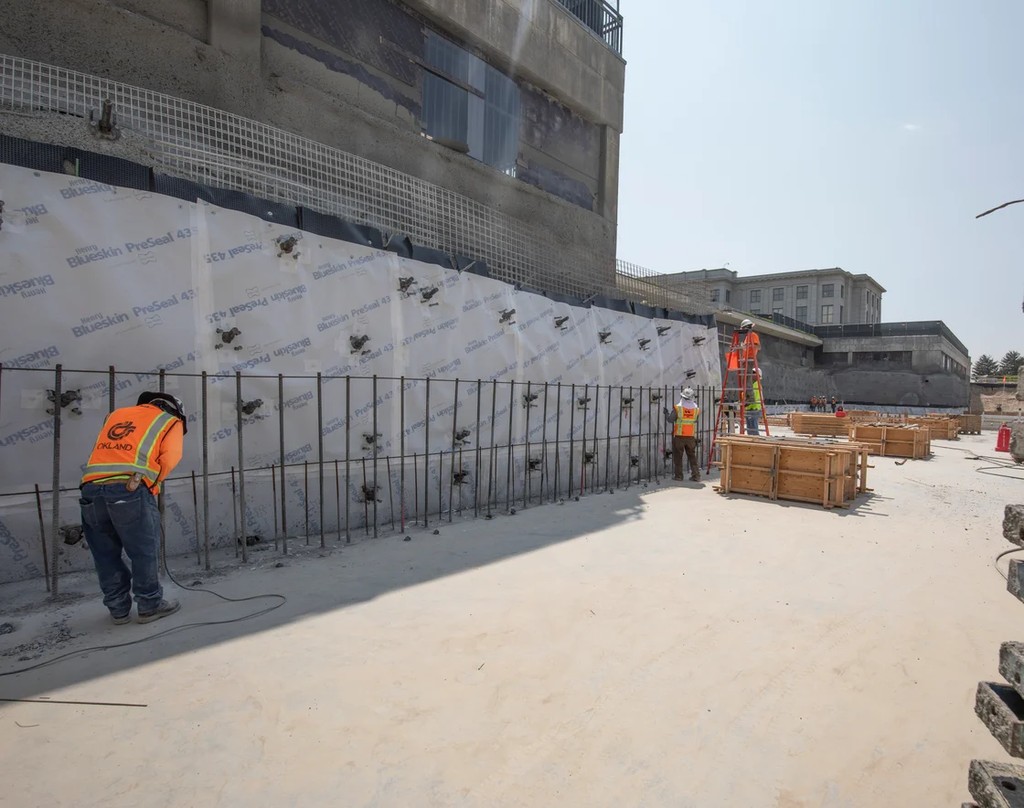
Image courtesy of Carlisle
Dual-bonded sheets offer both mechanical and adhesive protection.
Dual-bonded sheets are among the most innovative blind waterproofing options available today, offering a double dose of protection for a building. For example, one particular advanced system consists of a polypropylene membrane laminated to a chemically enhanced non-woven geotextile fleece with a dimpled surface. The membrane contains an adhesive and provides a mechanical attachment to wet concrete to form a permanent barrier seal. It easily installs with “kick-out” rolls, self-adhering laps, and splices without the need for special tools or torches. Additionally, it is highly resistant to harmful substances in soil and groundwater, as well as water vapor and radon gas. The membrane performs better than HDPE systems for excellent low-temperature flexibility and crack bridging. The dual bond system requires no curing and helps accelerate scheduling by reducing sequencing delays tied to concrete cure time and form removal. This would be a good option for projects with especially tight timeframes. Further, this waterproofing system is unaffected by temperature and weather. It does not require confinement/constant pressure to perform. To function, the seams and laps must be watertight, and the membrane must be clean prior to concrete placement.
“The new (blindside waterproofing system) is the only passive, pre-applied waterproofing solution in North America featuring dual bond technology, marking the latest milestone in our 50-year legacy of waterproofing expertise,” says Bart Rowland, Director, Strategic Initiatives (Pre-Applied) at Henry Company. “With the addition of this system, Henry Company now offers a comprehensive range of pre-applied and post-applied foundation waterproofing solutions. These systems are compatible with plaza deck and green roofing systems, air barrier systems, and roofing systems—providing customers with a convenient, all-in-one solution for complete commercial building envelope protection.”
Active Waterproofing Technologies: Super Absorbent Polymer
This is a polymeric or elastomeric sheet bonded to a hydrophilic polymer/bentonite membrane. It provides redundancy with a dual membrane. It can “self-heal” minor cuts and punctures. It forms a mechanical bond to concrete. However, pre-hydration reduces or eliminates effectiveness. It must be confined under constant pressure to perform in order to have the redundancy or active waterproofing technology to work. It needs to be installed by qualified and properly trained installers/welders.
Active Waterproofing: Bentonite
This blindside waterproofing technology is using sodium bentonite clay encased between two layers of woven or non-woven fabric or bonded to a plastic liner. It swells and hydrates in the presence of water, creating a gasket seal. It can “self-heal” minor cuts and punctures. It is easy to install and forms a mechanical bond to concrete. However, pre-hydration reduces or eliminates effectiveness. It must be confined under constant pressure to perform and it does not do well with wet/dry cycling. Bentonite became popular in the mid-1960s as a below-grade waterproofing membrane. It is a widely used, cost-effective solution suitable for projects where the groundwater is less of a concern and is typically used for low-risk projects. Because bentonite is a naturally occurring mineral, site water testing helps ensure the bentonite is suitable for the conditions in the water or soil.
Mechanically Bonded Sheet
This is an asphalt or polymeric sheet bonded to a geotextile fabric via a thermal weld or an adhesive layer. Curing is not required, and it is unaffected by temperature. It’s easy to install and does not require confinement or constant pressure to perform. It forms a mechanical bond to the concrete. For the system to work effectively, the seams and laps must be watertight, and it may be affected by groundwater or rainwater.
Non-Bonded Sheet
Non-bonded sheets are elastomeric membranes such as EPDM, TPO, and PVC. Curing is not required, and the system is not affected by temperature or weather. It’s easy to install. Sheets generally come in widths up to 10 feet (3 meters). To perform as intended, the seams and laps must be waterproof. These sheets do not form any bond to concrete, meaning lateral water migration will occur if there is a leak. Lateral water migration creates a situation where isolating and repairing the source of a water leak becomes incredibly challenging.
Know the Risk
The level of risk tolerance that a property owner is comfortable with should be the basis for selecting a pre-applied waterproofing system.
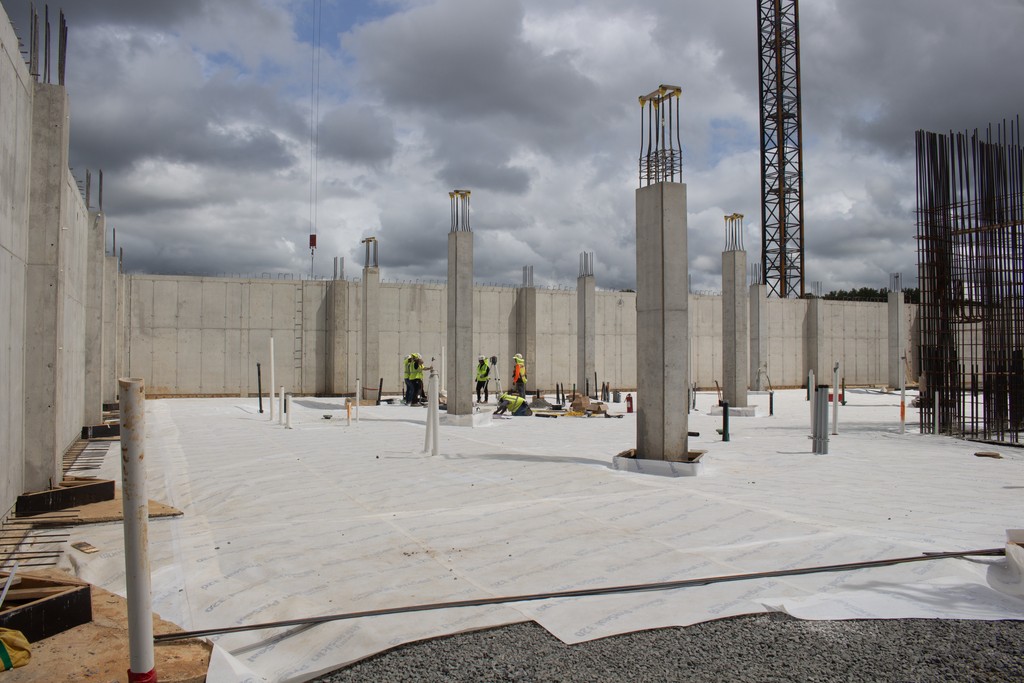
Image courtesy of Carlisle
The waterproofing manufacturer provided continuous guidance to meet challenges in this large installation.
The above table illustrates the properties of each type of blindside waterproofing technology.
- In terms of the bond to concrete, fully adhered and dual-bonded systems perform best. Bentonite hybrid, bentonite, and mechanically bonded systems create a moderate bond to the concrete. Fluid-applied and non-bonded systems create a poor bond.
- For seam integrity, fully adhered, dual-bonded, bentonite hybrid, and fluid-applied systems have excellent seam integrity. Bentonite creates poor seam integrity. Moderate seam integrity is achieved with mechanically bonded and non-bonded systems.
- Self-healing properties are moderately successful with bentonite hybrid, bentonite, and fluid-applied systems but unsuccessful with fully adhered, dual-bonded, mechanically bonded, and non-bonded systems.
- Toughness and durability are moderately successful across all technologies.
- Ease of use matters because the most straightforward system to apply typically means less chance of applicator error. The easiest-to-use technology is bentonite, and the most difficult is bentonite hybrid. All others are moderately easy to use.
- For installed cost, the bentonite hybrid system is the most expensive, and bentonite is the least costly, with moderate cost for all other technologies.
Specification Tips
Coordination is key to a successful project. Coordinate quality assurance sections to include the waterproofing pre-installation meeting:
- Division 03 – Concrete
- Division 07 – Thermal and Moisture Protection
- Division 22 – Plumbing
- Division 23 – HVAC
- Division 26 – Electrical
- Division 31 – Earthwork
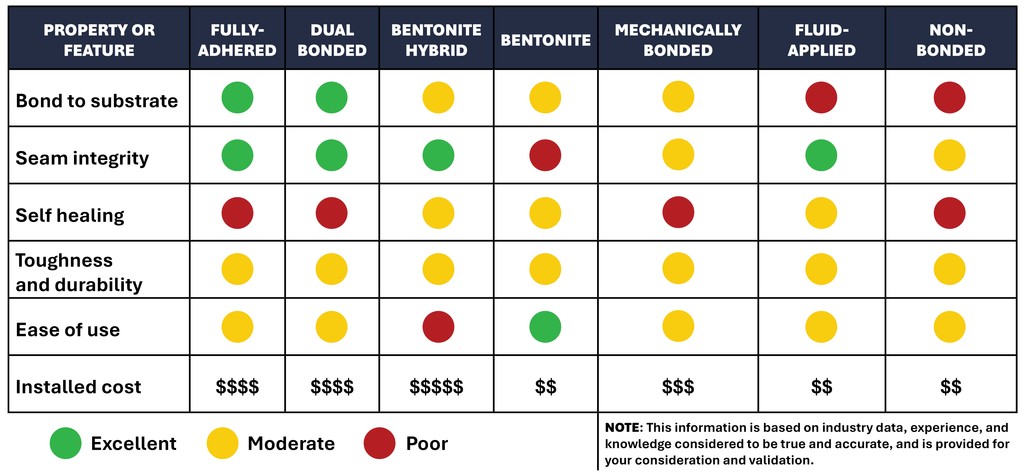
Image courtesy of Carlisle
Properties of blindside waterproofing technologies.
Single Source Components
Coordinate these system components from one manufacturer for single-source warranties:
- Drainage composites
- Passive waterstops
- Active waterstops
- Injectable waterstops
Using system components from a single manufacturer ensures that the materials of the components are chemically compatible with the waterproofing membrane.
Drainage Composites: A high-strength, thermal molded polymeric dimpled core is bonded to a filter fabric to reduce hydrostatic pressure and collect and transport water away from the structure. Features include filter fabric that prevents the passage of soil particles into the core while allowing water to pass freely. The “soften” shoring system spans up to 2-inch (50mm) gaps and voids. They are time-saving and labor-saving installations. Note that these are not standalone waterproofing systems but are part of a more extensive, complete system.
Passive Waterstops: Passive waterstops are embedded within the concrete pour to seal concrete Features. They have excellent physical properties and may be designed for moving joints as part of the overall waterproofing design. In terms of limitations, splices and seams may be labor-intensive. This technology does not swell when in contact with water. It is not a standalone waterproofing system.
Active Waterstops: Various configurations of waterstops swell when in contact with water and are used to create watertight concrete joints. They seal construction joints to minimize and eliminate water travel. They are easy to install and are part of the overall waterproofing design. Regarding limitations, active waterstops must not be allowed pre-swell (hydrate) before the concrete pour, or they lose effectiveness. These types of waterstops are not intended for moving joints, and they are not standalone waterproofing systems.
Injectable Waterstops: This technology is a tube or hose that provides a conduit or channel for chemical grout to seal concrete joints to minimize or eliminate water travel. They can be grouted after the concrete cures or in the future if water intrusion occurs. Fill tubes must extend beyond the concrete and must be protected from physical damage. Injectable waterstops are not intended for moving joints. Again, this is part of the overall waterproofing design, not a standalone system.
Quality Assurance
Quality assurance hinges on understanding the following quality assurance requirements:
- Approved applicators
- Geotechnical review
- Pre-installation meeting
- Blindside waterproofing manufacturer technical representative
- Third-party inspections
- Approved Applicators
The terms approved, trained, certified, or authorized are commonly used interchangeably to describe applicators, but they do not have the same meaning. The waterproofing manufacturer should have a dedicated installer training program, training facility, and certificate requirements.
Specification Considerations
- “Installer has been trained at the manufacturer’s training facility.”
- “At least one member of the Installation field crew must have a training certificate.”
Geotechnical Review
A geotechnical report for soil or groundwater contaminants should be forwarded to the waterproofing manufacturer to confirm that the product specified is suitable. Different blindside materials may have different chemical resistance properties; reviewing contaminants lets the manufacturer approve or recommend the appropriate material based on site contaminants and concentrations.
Boring samples showing groundwater elevations should also be presented to the waterproofing manufacturer to confirm proper product selection. Again, materials may have different properties, including how much hydrostatic pressure they can resist. Reviewing groundwater elevations lets the manufacturer approve or recommend appropriate materials, allowing the design professional to specify different compatible materials or detailing at various elevations.
Specification Considerations
- “Waterproofing manufacturer provides review services of geotechnical report and environmental study to confirm specified products are acceptable, clearly stating if detailing enhancements are required for warranty eligibility.”
Pre-installation Meeting
To maintain warranty eligibility, a pre-installation meeting specific to the pre-applied waterproofing should be mandatory. The meeting should include other trades that could influence the waterproofing integrity. Trades that work on, are adjacent to, or are above the waterproofing should all participate. This will ensure the waterproofing is protected and continuous, and that the work between all trades is adequately coordinated and sequenced.
A pre-construction meeting just for the pre-applied or blindside waterproofing is crucial. That’s where schedules and particular challenges on site can be discussed, such as the details necessary for that project. This includes timing for which plumbing, landscaping, mechanical, different trades, and concrete placement will be coordinated with the waterproofing. Should the waterproofing be installed before or after which trade? Those things can be vetted at a pre-construction meeting with everyone involved in the pre-apply.
It is vital to get the waterproofing consultant, the design team, the owner’s representative, and inspection firms involved to help ensure everybody has a clear understanding and is on the proverbial same sheet of music to ensure the project goes well. It also creates a communication chain where everyone involved with that project gets the appropriate information and knows exactly how to address a challenge. This challenge could be a new detail that wasn’t in the original bid documents and how that will be installed to maintain warranty eligibility. It starts with the pre-construction meeting and getting everybody in a clear communication channel.
Common meeting attendees:
- General contractor
- Owner or owner’s representative
- Architect
- Engineer
- Waterproofing consultant
- Installer
- Manufacturer
- Best practice meeting attendees:
- Concrete contractor
- Steel reinforcement contractor
- Foundation contractor
- Mechanical contractor
- Electrical contractor
- Plumbing contractor
- Carpenter
- Landscape contractor
- Hardscape contractor
- Specification Considerations:
- “Manufacturer’s Pre-Installation Conference Checklist.”
- “Manufacturer must offer dedicated, local support.”
- “Specify relevant trades by listing them in the project specification.”
Third-party Inspections
Perhaps the most important form of quality assurance is third-party, independent inspectors. These inspectors can be paid for by the building owner and trained by the manufacturer in the same type of training program that the applicator will go through. An inspector can get everybody on the same page, understand the substrate, and ensure it is suitable for application. They can evaluate after the rebar has been placed to determine if there’s any damage and have the waterproof contractor address it prior to concrete placement.
An inspector can provide necessary communications to the construction team with inspection reports, photos, and site maps. The inspectors have a very positive value for the owners, as they can be present when a salesperson or technical representative cannot be. That is the best way to ensure the owner is getting what they pay for: a valid warranty and a watertight building with a robust, continuous waterproofing system.
Specification Considerations: Listed below are common inspection stages/hold points to specify.
- “Substrate preparation completion.”
- “After steel placement, before concrete is installed.”
- “Periodic intervals during concrete placement or backfill per project-specific requirements.”
- “Any work that could compromise the waterproofing.”
Transitions and Tie-ins
It is imperative to sequence work to ensure continuous waterproofing; this includes sequencing how the blindside waterproofing transitions at grade with the rest of the building envelope.
Dissimilar materials and/or different manufacturers may create an incompatible tie-in, for example, between the blindside waterproofing and the air barrier. Various contractors may perform these transitions, creating an additional layer of complexity.
Specifications typically cross-reference each other, but due diligence in specifying compatible materials will better ensure transitions and tie-ins are correctly designed. If materials are submitted and approved as alternates, the blindside waterproofing and air barrier manufacturers should be consulted.
Conclusion
The need for blindside waterproofing has increased over the decades as more below-grade spaces are built for increasingly sensitive uses. With blindside waterproofing, there is only one chance to get it right. All blindside waterproofing systems are not equal. Each system has features and limitations. Variables include the use of the structure, the owner’s risk tolerance, the hydrogeology, and other factors. Preventing lateral water migration is the key. The designer is faced with a number of simple and sophisticated blindside waterproofing solutions, from a non-bonded membrane to a dual-bond system with the redundancies of a chemical and mechanical bond. After the best system is selected, there should be a focus on improving and strengthening specification language to enhance quality assurance. There is also no substitute for working with a reliable, technically knowledgeable waterproofing system manufacturer who can help assess the project’s specific needs and select the best blind waterproofing system to meet them. With all issues carefully addressed, there is an increased likelihood that the owner will end up with a robustly waterproofed structure.
Kathy Price-Robinson writes about building and design. Her remodeling series “Pardon Our Dust” ran for 12 years in the Los Angeles Times. She specializes in writing about buildings that are durable and resilient to climate disruptions, as well as products and designs that provide shade in hot climates. www.kathyprice.com