Building science has advanced in recent decades to the point where manufacturers now offer a wide range of exterior barrier products designed to meet specific performance needs for limiting airflow, resisting water, and controlling thermal properties. Some of those products address a single barrier need while others have advanced capabilities in that they can meet the requirements of 2 or more of these barrier types. When thinking about barrier products, large-scale building envelope systems such as opaques walls or curtain walls come to mind. However, fenestration systems such as entrances and movable glass walls play an important role as well. When specified correctly, they can meet several barrier objectives including thermal, air, and water performance. The choice of which products to use is determined by the architect or the designer of a project and is usually called out in the specifications. Understanding the difference between different fenestration products and where they are most suitable is the prerequisite knowledge for writing such specifications and is the overall focus of this continuing education course.
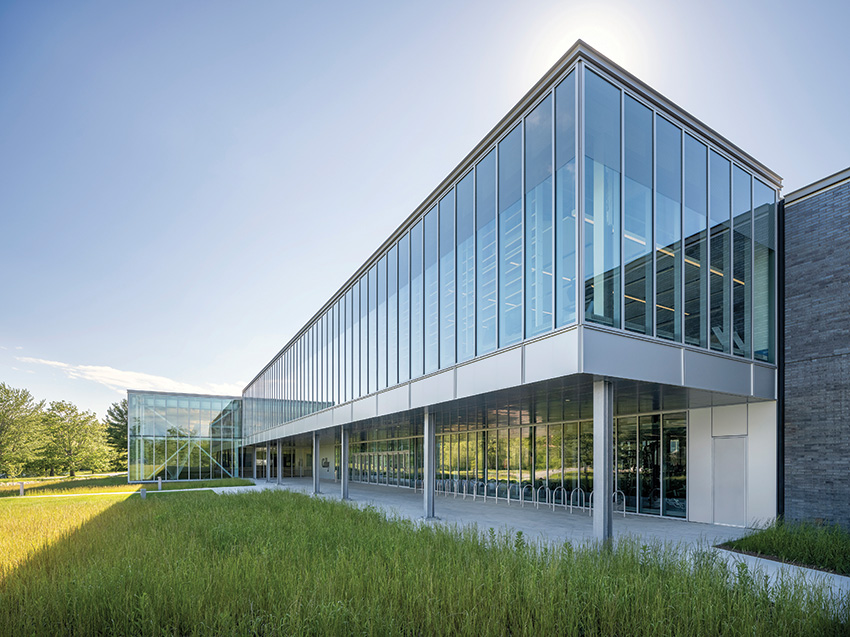
Photo courtesy of CRL - © Trent Bell
Fenestration systems can make up a significant portion of the exterior of a building and need to provide all of the necessary air, water, and thermal barriers too.
PERFORMANCE AND QUALITY STANDARDS
The higher performance of building facades is a resounding focus of many building designs. This is driven in part by building owners who want their buildings to use less operational energy. It is also a response to the observable increase in the intensity and frequency of storms which raises concerns about water resistance. Similarly, air infiltration and wind resistance need to be addressed to counteract both energy loss and storm damage.
In addition to these voluntary efforts, architects also need to comply with the mandates of different codes and standards. For commercial buildings, these include not only the International Building Code (IBC) but also the International Energy Conservation Code (IECC) or ASHRAE 90.1 for minimum energy performance. Some states also have their own, specific standards on top of the International Codes such as California Title 24 or the Florida Product Approvals standards. All of these point to added requirements for higher quality and performance demands on fenestration of all types.
Glass and glazing are usually significant design features of most commercial building facades. There are many variables related to their design such as the type, size, shape, color, and configuration of the glazing, which often receive plenty of attention. There are also many variables that affect the performance and the energy code compliance of the glazing system including the percentage of glazed to opaque wall areas, the number of layers of glass, the type of glass used, glass treatments or coatings, the framing system that holds the glass, and even the type of spacers between double- or triple-paned products. It is important to recognize that all of these variables are essentially different components of a glazing system that can be controlled and specified to suit specific project conditions, climate zones, and code requirements. It is not about any one item alone (i.e., the framing system or the glass) but the entire make-up of all of them.
Based on all of the above, we turn our attention to some of the common standards and codes that directly address the performance of glazed fenestration systems of all types.
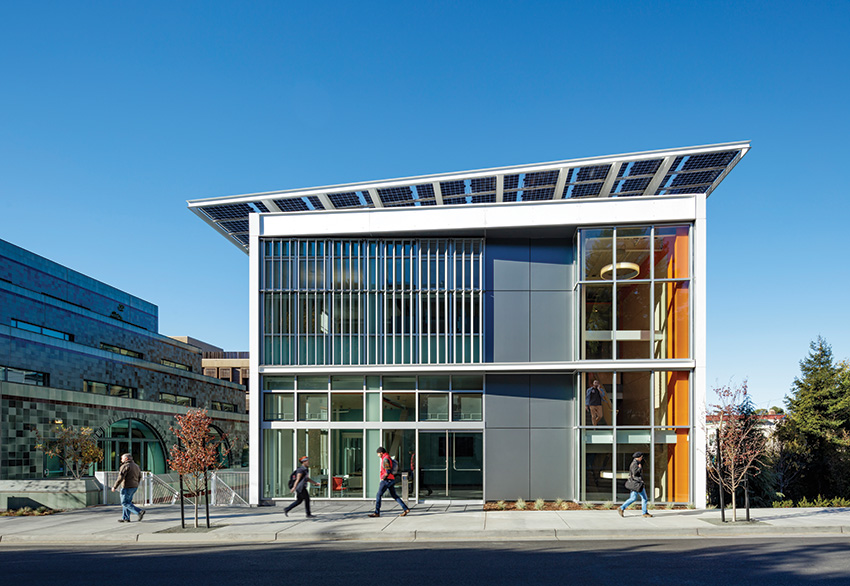
Photo courtesy of CRL; Tim Griffith
Standards have been developed by independent organizations to address the ability of fenestration products to meet stated criteria as a part of the building envelope.
Fenestration Product Standards
The most widely recognized and relevant strength standard for fenestration is the North American Fenestration Standard (NAFS) which governs windows, doors, and skylights. Known as AAMA/WDMA/CSA 101/I.S.2/A440, this standard is familiar to many specifiers and fenestration manufacturers and includes four Performance Grade categories. Classification of products is based on independent testing based on the design pressure of wind forces acting on the fenestration (measured in pounds per square foot – psf) at a stated pressure difference (measured in pascals Pa). The entry-level or “gateway” criteria for tested fenestration units in each of the Performance Grades (PG) is as follows:
- R Class (Residential) Fenestration: 15 psf (720 Pa) This class is commonly used in one- and two-family dwellings.
- LC Class (Light Commercial) Fenestration: 25 psf (1200 Pa) This class is the minimum designation appropriate for low- and mid-rise buildings where larger sizes and higher loading requirements are expected.
- CW Class (Commercial) Fenestration: 30 psf (1,440 Pa) This newest class is better suited to low- and mid-rise buildings where larger sizes, higher loading requirements, limits on deflection and heavier use are expected.
- AW Class (Architectural) Fenestration: 40 psf (1,920 Pa) This is geared toward mid and high-rise buildings to meet increased loading requirements and limits on deflection in buildings where frequent and extreme use of the fenestration products is expected.
To qualify for any one of these performance grades, a representative specimen of the product must pass all required performance tests for the following, in addition to all required auxiliary (durability) tests for the applicable product type and desired performance class:
- Operating force (if applicable)
- Air-leakage resistance
- Water-penetration resistance
- Uniform load deflection test
- Uniform load structural test
- Forced-entry resistance (if applicable)
After the completion of all of these tests, the product is either deemed to have passed or failed to meet the designation tested for.
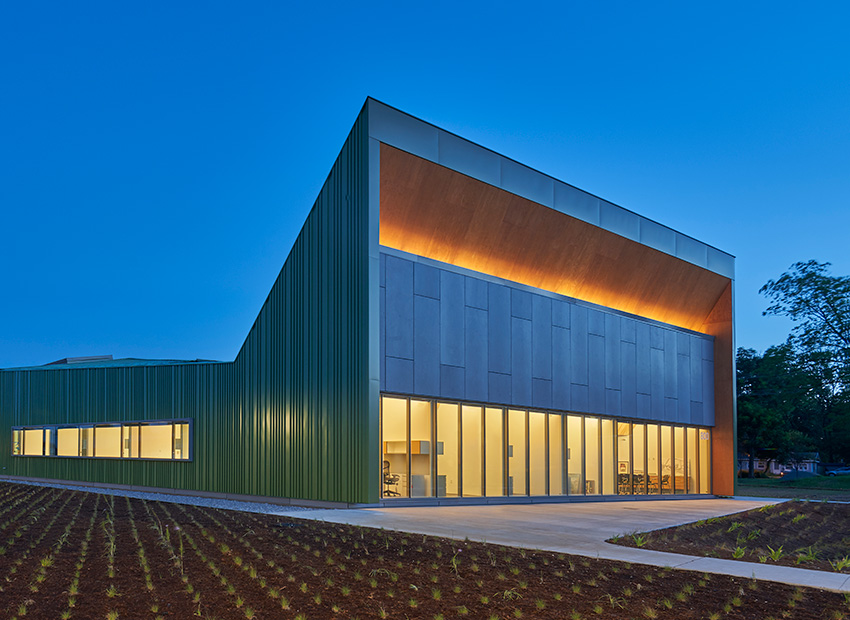
Photo courtesy of CRL; Tim Hursley
Energy codes identify the minimum requirements for building envelopes, including fenestration, to conserve energy and reduce operating energy consumption.
Fenestration Energy Standards
While the NAFS standard addresses the strength and integrity of fenestration products, the National Fenestration Rating Council (NFRC) is the most widely used standard for energy performance. A commonly cited rating is NFRC 100, which is a set of procedures and guidelines for determining the U-factors of all types of windows and doors. This is the fundamental rating that many people look for in regard to demonstrating thermal energy performance both for influencing the building design and for demonstrating compliance with the IECC. Note that this standard looks at all of the components of a glazing product or system (i.e., window, curtain wall, entrance, storefront, etc.) and shows an overall U-Factor for the product, not just a U-Factor for the glass. This allows design professionals to make comparisons and decisions based on the total product, not just the glass used.
A similar rating is NFRC 200 which is used to determine the Solar Heat Gain Coefficient (SHGC) and Visible Transmittance (VT) of glazing in windows and doors. The SHGC is useful for determining how much heat is contributed by the sun through the glass. It is regulated by the IECC and has particular significance in warm climates. The VT is helpful in determining the effectiveness of daylighting and views in a building space. Both of these NFRC ratings are essentially technical documents intended for use by testing labs and other window and door professionals. Hence, when window and door companies indicate that their products are tested or certified to NFRC 100 and 200, it simply means that they have had simulations and/or physical testing performed on their products in accordance with the guidelines published in NFRC 100 and 200.
The things that manufacturers control which directly influence the results of the NFRC ratings are many and varied. The glass can be standard double-glazed or higher-performing triple-glazed. The spaces between the glass panes can be separated by standard aluminum spacers or high-performance “warm edge” spacers. The air in those spaces can be replaced with an inert gas such as argon. The glass itself can be treated with coatings to improve thermal emissivity (i.e., Low-E) or to change the SHGC─either of which may directly affect the VT of the glass and its coloration. The frames of the glazing systems used in commercial buildings are typically made out of aluminum, which is great at conducting heat and not good at restricting it. Hence, manufacturers incorporate one or more thermal breaks in the aluminum framing such that inner and outer aluminum members are held together with materials that conduct less heat but maintain appropriate strength.
All of these performance details can be specified in a project, along with the preferred appearance characteristics to achieve the desired outcomes. However, working with an experienced glazing systems manufacturer can help ensure that particular combinations of characteristics are indeed possible and available. It can also help determine the relative cost impact of different selections. If code compliance is a concern, they may also be able to help in that regard by offering systems that have been accepted in similar climate zones for similar projects.
ENERGY PERFORMANCE CODES
While industry standards set the bar for quality and the basis for testing, codes dictate the level of performance needed to show compliance for the health, safety, and welfare of the public. The codes reference the standards and use them to document the required performance. Some of the applicable codes are reviewed in the following sections.
International Energy Conservation Code (IECC)
Energy performance in buildings is a good case in point of the design and construction industry moving out in front and the codes needing to be updated to keep pace. Since the 1980s, there has been a concerted movement that has taken hold in design, construction, product manufacturing, and building operations to reduce the amount of energy used in buildings. Energy codes emerged during this time – not to regulate energy consumption (i.e., there are no violation orders issued if a monthly utility bill is too high), but to regulate design and construction so that energy usage in buildings is better controlled. That control falls into two categories; 1) energy conservation, which is the act of reducing the amount of energy needed in the first place, playing out most notably in a better-performing building envelope (insulation, air sealing, glazing traits, etc.); 2) energy efficiency, which means reducing the amount of energy required to power equipment, lighting, etc. and still achieve the desired outcomes (heating, cooling, light levels, etc.). Taken together, we refer to the energy performance of a building as a combination of conservation and efficiency measures that achieve a measurable outcome. The International Energy Conservation Code (IECC) addresses all of these aspects of energy performance. It also recognizes that different climate zones exist around the country that directly impact the energy performance of buildings.
Pushed by this movement, the IECC has undergone a number of revisions and updates, this time focused on establishing the “code minimum” level of energy performance while still allowing these other voluntary programs to go beyond that level. Note that the health, safety, and welfare significance of the IECC is more than just a concern for the environment in general related to air quality and climate change. It is also based on addressing the adequacy of the supply of energy to buildings. The energy crisis of the 1970s demonstrated that real or imposed shortages of energy supply posed a significant threat to the public (think about how long is too long when experiencing a power outage). Virtually all buildings now rely on energy to operate the heating, cooling, lighting, appliances, electronics, and equipment. If that supply is compromised or interrupted, so is the safety and quality of life of the people who are in those buildings.
ASHRAE 90.1
The American Society of Heating, Refrigeration, and Air Conditioning Engineers (ASHRAE) has long been involved in optimizing the engineering of energy-using equipment in buildings. They have also recognized the significance that the building envelope has on the amount of energy needed to operate that equipment, both in terms of capacity and in the amount of time it needs to run. As such, ASHRAE has committees and work groups made up of members and associates to generate some recognized standards for building design. ASHRAE 90.1 “Energy Standard for Buildings Except Low-Rise Residential Buildings” is meant to apply to most commercial, industrial, and institutional buildings. The International Code Council has recognized this standard as “equivalent” to, albeit not identical to, the requirements of the IECC. Hence, it is a recognized alternative to use when showing code compliance for non-residential buildings. While there are indeed differences between ASHRAE 90.1 and the IECC, a building designed to meet the minimum standard of either one should yield approximately the same overall energy performance. Note that in some jurisdictions, such as New York City and elsewhere, commercial buildings must use ASHRAE 90.1, not the IECC to show compliance with the Energy Code.
California Title 24
The state of California codes are referred to as the California Building Standards Code, which is embodied in the California Code of Regulations, Title 24. It is commonly referred to simply as “Title 24” and includes 1) some adopted I-Codes as written; 2) some I-Codes with adaptations to suit California; and 3) some California-generated standards to suit particular state concerns. As such, the Title 24 codes are generally more stringent, particularly in regard to energy performance and seismic issues, than the model I-Codes alone. That means that the “code minimum” threshold for energy performance can be expected to be higher in California than elsewhere in comparable climate zones. It has also been observed that other states, particularly those in the Pacific Northwest, have begun to follow California’s lead and are starting to incorporate their own state adaptations to the model codes.
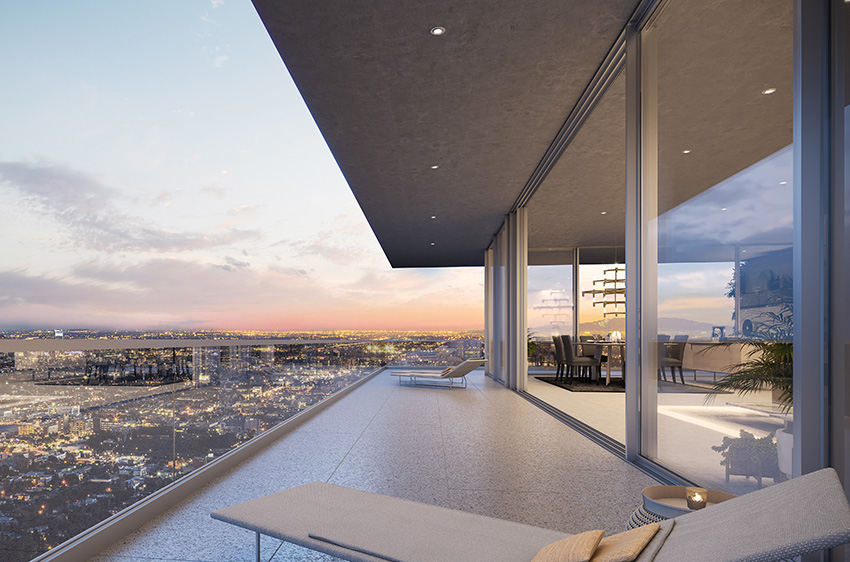
Photo courtesy of CRL
Sliding glass door and wall systems provide a sophisticated and elegant look but can also meet needed performance and operational requirements.
International Green Construction Code (IgCC)
The International Code Council has collaborated with a number of non-profit organizations to create a model green building code. Referred to as the International Green Construction Code (IgCC), it addresses more than just energy but also other common aspects of a green building such as site design, water usage, material selections, and indoor environmental quality. This code has primarily been adopted by localities, as opposed to statewide adoptions, and provides multiple options for achieving minimum performance levels. It works in a very similar manner to the voluntary programs (such as LEED) but codifies it so that code enforcement officials have a tool to work with similar to other codes.
Outside of the IECC and the IgCC, there are numerous organizations that have been addressing the issues related to energy performance in buildings. Accordingly, many well-known voluntary programs such as the Architecture 2030 Challenge, The AIA 2030 Commitment, LEED, ENERGY STAR for Buildings, Passive House, The Living Building Challenge, and others have emerged and evolved in the past 20 years and become very much a part of the mainstream of building design. Based on all of these developments, it is clear that the current direction of building design is to continue to seek better energy performance in buildings and reduce the emissions caused by the use of fossil fuels in the heating, cooling, and operation of buildings or the generation of electricity.
With all of the above in mind, we look next at three common types of operable fenestration systems used in commercial buildings. Fixed glazing systems (i.e., fixed windows, curtain walls, storefront systems, etc.) are fairly predictable since they do not open or close. Hence the thermal and strength performance of these products relates directly to the nature of the frame or support design, the characteristics of the specified glass, and the ability to seal the glass permanently in the frame. Operable doors and windows need to do all of these same things but have the added requirement of being able to open to allow for passage or ventilation, or both, but then be able to close and seal tightly again,─not just once, but repeatedly over time. The three systems addressed here are sliding glass door and wall systems, bi-folding glass door and wall systems, and glazed entrance systems.
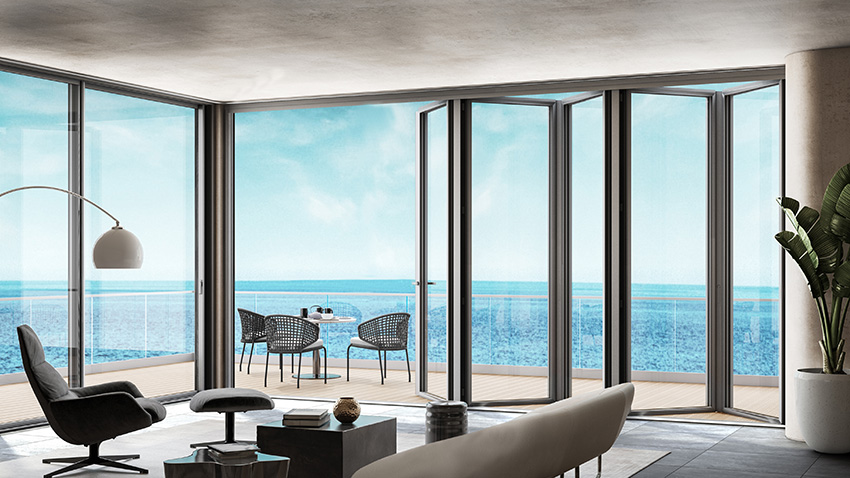
Photo courtesy of CRL
Bi-folding glass door and wall systems provide a different design and operational option for large format openings compared to sliding glass doors and wall systems.
SLIDING GLASS DOOR AND WALL SYSTEMS
Large-format sliding glass doors are often used in commercial buildings of many types including hospitality, retail, and luxury multifamily projects. They can provide architects with a means to create expansive views and daylighting possibilities with a visually uncluttered and uninterrupted expanse of glass. Products are available that offer a rather sophisticated look that can make a visual design statement with remarkable simplicity.
- Design Features: One of the design benefits of sliding glass door and wall systems is their large panel size. Manufacturers can provide panel heights up to 13 feet tall and widths of up to 7 feet wide, thus creating expansive scale and a look of elegance. To keep the visual “clutter” at bay, ultra-slim panel rails and stiles are available that create a minimal and uniform frame. The sliding panels can stack in front of one another on one or both sides or they can disappear into a wall pocket designed by the architect for that purpose. These various design approaches help buildings achieve both a visual and physical connection between indoor and outdoor spaces with relative ease and simplicity. They come in a range of standard and custom offerings related to size, frame color, frame materials, glass types, and other options.
- Performance: From a performance perspective, sliding glass door and wall systems can be specified to work within the requirements of relevant codes and standards. They are available with a CW Performance Class rating which is ideal for exterior applications where high loads, limits on deflection, and heavy use are expected. They can employ a thermally broken frame with insulating glass up to 1 inch thick and achieve a U-factor of 0.38 or less. These attributes also contribute to achieving a sound transmission rating of STC-33.
- Operation: Some of the best large-format sliding glass door systems use a bottom rolling mechanism with stainless-steel wheels and a precisely engineered stainless-steel track. This helps the large sliding panels, which can weigh up to 700 pounds, move rather effortlessly with a one-handed operation. That is because panel loads are evenly distributed across the bottom rolling components resulting in a fluid, frictionless glide. The track is set into a sill which may be flush with the surrounding floor surfaces or can be raised for greater protection from wind, rain, and other weather.
- Hardware: The sliding operation of the doors means that everything needs to be flat or recessed on the panels so as not to conflict with the proper door movement. This includes the hardware that operates the door, so manufacturers provide integrated, flat handles made of metal including stainless steel. Since the handle is integral to the door, so is the locking hardware. While there are different ways to use locking hardware, the preferred approach is for a multipoint locking mechanism – internal hardware that locks the sliding panel into place at the top and bottom of the frame.
BI-FOLDING GLASS DOOR AND WALL SYSTEM
Bi-folding glass doors use glazed panels that can enclose and open up a variety of interior and exterior spaces. They can be configured into a small grouping for a wide door opening or can span across an entire wall of a facade. A bi-folding glass door or wall system consists of a number of hinged panels that fold together and then slide to one or both sides of the opening. This makes them desirable for many different building types ranging from multifamily, hotel and spa, restaurants, retail spaces, and institutional buildings including K-12 schools and higher education projects.
- Design Features: Unlike sliding glass doors which typically keep at least one panel fixed, bi-folding systems can all move and be stacked out of the way to create a full opening. The panels may be hinged together in pairs or in a large number of connected panels. Many opening configurations are possible with inward or outward swinging options. A locking swing panel can be incorporated into a run of bi-fold doors as a swing door for easy entry or egress within the wall. Like sliding glass doors, bi-folding systems also come in a range of standard and custom offerings related to size, frame color, frame materials, glass types, and other options. Some are available with distinctly slim vertical and horizontal panel rails that reduce visible components, produce a minimalistic aesthetic, and maximize views. When closed, door hinges are completely concealed to deliver an elegant and streamlined look.
- Panel Attributes: Since bi-fold doors are a fundamentally different, albeit similar, product compared to sliding glass doors, the panels in bi-fold systems are more commonly smaller and more frequent than in sliding glass doors. While the specific dimensions and attributes of panels can certainly differ between manufacturers, it is possible to find that the maximum frame height is 12 feet, and the maximum panel width is up to 4 feet. Weight is certainly a factor for the proper operation of the doors, so a maximum panel weight of 200 pounds can be expected. Similarly, there is a practical limit on how many connected panels make sense before they become too unwieldy to operate. Typically, that equates to a maximum of 9 connected panels per jamb (i.e., 18 per opening with two jambs).
- Operation: Bi-fold doors move differently than sliding door systems but can be just as easy to use and design into a building. A bottom rolling system is an option on sliding doors that eliminates added loading on the beam or header above the opening. Some incorporate compensating channels and adjustable spacers to fine-tune the operation for smooth movement and ease of use. The bottom track for bi-fold doors is set into a sill which may be flush with the surrounding floor surfaces or can be raised for greater protection from wind, rain, and other weather.
- Performance: Bi-folding glass door and wall systems have fairly comparable performance attributes compared to sliding door systems. They are also available with a CW Performance Class rating which is ideal for exterior applications where high loads, limits on deflection, and heavy use are expected. They similarly employ a thermally broken frame with insulating glass up to 1 inch thick and achieve a U-factor of 0.36 and a sound transmission rating of STC-32.
It is important to note that bi-folding glass doors are always stacked perpendicular to the opening. The amount of space that the folding doors will take away from the opening is dependent on the number of panels, panel width, height, and thickness. There are a multitude of configuration options with paired panels allowing for the best flexibility in configuration.
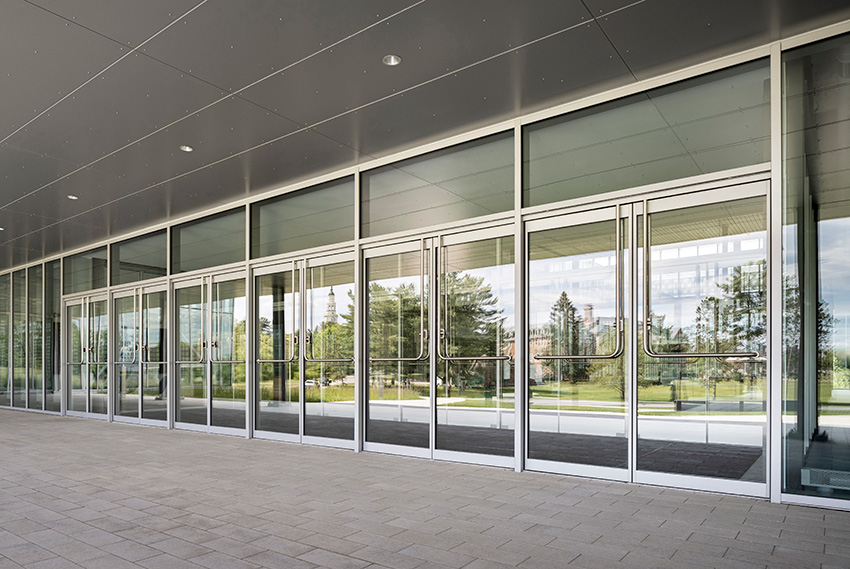
Photo courtesy of CRL; © Trent Bell
Glazed entrance systems can provide an attractive, contemporary, and welcoming building entry and still meet the water, air, and thermal barrier requirements needed when the doors are closed.
GLAZED ENTRANCE SYSTEMS
A great example of glazing systems that are widely used and need to address building envelope barrier requirements are swinging door glass entrance systems. These are often sought after as a visual focal point because they create an inviting sense of transparency leading into the building while offering contemporary, elegant all-glass aesthetics. Hence, many commercial, institutional, and industrial buildings incorporate glass entrance systems on the main floor. While these are fairly common, although some have more distinctive looks than others, there are real differences in the way these types of entrance products perform. In the case of energy performance and code compliance, attention needs to be placed on the specification of all of the component parts and materials of these glazed entrance systems.
Achieving the desired level of performance is based fundamentally on three things: the structural and material integrity of the aluminum frame and glass; the insulating value of the system; and the ability to prevent air and water infiltration through the system. Fortunately, there are products available that address all three of these criteria and manage to do so with great aesthetic qualities. For example, there are ultra-narrow stile entrance systems available that provide an elegant, all-glass appearance, while still delivering exceptional thermal performance normally found in full-frame doors. Excellent thermal performance translates to U-factors as low as 0.43 to help control heat transfer. This is achieved in part by allowing insulating glass units (IGU) to be used that are up to 1 inch thick. In addition, such entrance systems can demonstrate that they meet or exceed the air infiltration requirements of the International Energy Conservation Code (IECC) and ASHRAE 90.1, both of which contain mandatory provisions on this topic. They can also be specified to pass ASTM E331 water penetration testing.
When it comes to the hardware used for door pulls and panic devices, there are options in this regard too. Commonly, such door hardware is attached directly to the frame. However, some manufacturers have developed a means to secure door pull hardware directly onto 1-inch insulating glass panels using unique through-glass fittings. Styles include sleek tubular panic devices that yield an attractive floating-on-air appearance because the handles don’t have to be attached to door stiles. This provides an added aesthetic and functional benefit without compromising the performance of the doors. That means architects don’t have to sacrifice aesthetics in place of thermal performance.
Other options for such systems include premium door cladding in customizable finishes to blend with or accentuate any design intent. In terms of size, doors can be fabricated successfully up to 10 feet in height. The frame system and the threshold should always include thermal breaks for best performance.
By specifying an all-glass entrance system with the appropriate details, the glass composition of the surrounding framing system can match the entrance system, thus avoiding high variations in either performance or looks. Maria A. Gomez, Principal with GFF Architects sums it up this way, “The ultra-narrow stile entrance products we have specified solve the requirement for thermal performance and weather protection while maintaining an upscale look.”
GREEN BUILDING CONSIDERATIONS OF FENESTRATION
The green building movement in this country has given rise to quantifiable rating systems that seek to establish specific levels of achievement in the creation and performance of green buildings. The best-known of these green building rating systems has been developed by the US Green Building Council and is known as the LEED rating system. This is actually a family of ratings that apply to different building situations (e.g., new or existing buildings, core, and shell, interiors) and in some cases building types (schools, healthcare, retail, homes, etc.). All of the LEED rating systems have been subject to ongoing changes and updates since their inception, but the basic categories of defining green buildings have remained the same across the different versions over time. With that in mind, the contributions that operable glass walls can fall into several green building categories.
Energy and Atmosphere
As a primary part of the building facade, a computerized energy performance model can be developed based on using the appropriate NFRC ratings for U-factor, Solar Heat Gain Coefficient, Visible Transmittance, and Air Leakage if available. Further, the coordination between using natural daylight and electrical lighting should be incorporated as part of the computer model for total energy performance. Adjusting or changing the fenestration design of different facades on a building can yield significant differences in energy performance. Building variables can include high-performance triple-glazed windows, super-insulation, an airtight building shell, limitation of thermal bridging, and balanced energy recovery ventilation. Therefore, it is common to run several energy performance models with some of these different attributes to compare the impacts of those differences on a specific building and facade design. For accuracy, the data used for the computerized model should reflect the actual values obtained from the manufacturer’s tested products, not generic values.
Materials and Resources
The aluminum components of a fenestration system can contain significant recycled content. Further, glass and aluminum components can be salvaged and re-used in other buildings or recycled at the end of their service life. The pre-manufactured nature of the products reduces the amount of construction waste and scrap materials. All of these attributes help to reduce their environmental impact which can be demonstrated in a life cycle assessment (LCA) or environmental product declaration (EPD) for these products. Some industry-wide versions of these documents are available for fenestration products, but, where available, it is always advisable to obtain specific information from a manufacturer.
Indoor Environmental Quality
The addition of daylight into a building is clearly the strongest contributor of fenestration to this LEED credit category. Daylight has been shown to provide human health benefits as well as productivity boosts. Clear glazing in building facades can also be designed to provide appropriate views as well, which is also recognized as an indoor environmental quality issue in LEED. Operable windows and doors, particularly bi-fold and sliding door systems, also allow for beneficial natural air ventilation into a building. Further, for systems that avoid sealants and adhesives, requirements for low-VOC emitting materials can be met. This is carried through in the prefinished nature of the panels since no paints, coatings, adhesives, or sealants are needed.
Innovation in Design
With green design, size matters. Building size is a significant contributing factor to resource efficiency and, in the end, will affect energy use also. The move to smaller and more efficiently planned spaces makes flexibility, functionality, and expansion capabilities all the more important. Sliding and bi-folding glass walls do just this, whether in an exterior wall providing a variable connection to the outdoors or in an interior space allowing for different room configurations with the operable glass wall opened or closed.
As part of an overall building design, large format high-performance fenestration systems can be a significant part of achieving LEED certification or a similar green building recognition. Fixed systems become part of the continuous air, water, and thermal barriers of a building. Operable systems are dynamic and need to provide those same barrier characteristics when closed, but obviously, allow the desired free flow of air and temperature when open.
CONCLUSION
Building enclosure systems include fenestration. The design of fenestration into facades is undoubtedly significant, but so is the performance in terms of inherent integrity, wind and water resistance, and thermal control. The numerous codes and standards that have been developed related to fenestration all address these performance issues in a comprehensive manner. When considering large, glazed areas on a building facade, understanding the different product options and the details of specific products can help achieve a better understanding of the things that influence the performance of those products. That allows architects and other design professionals to specify effective fenestration that meets project targets for green buildings and elegant designs.
Peter J. Arsenault, FAIA, NCARB, LEED AP is a nationally known architect and a prolific author advancing positive acoustical experiences through better building design. www.pjaarch.com, www.linkedin.com/in/pjaarch