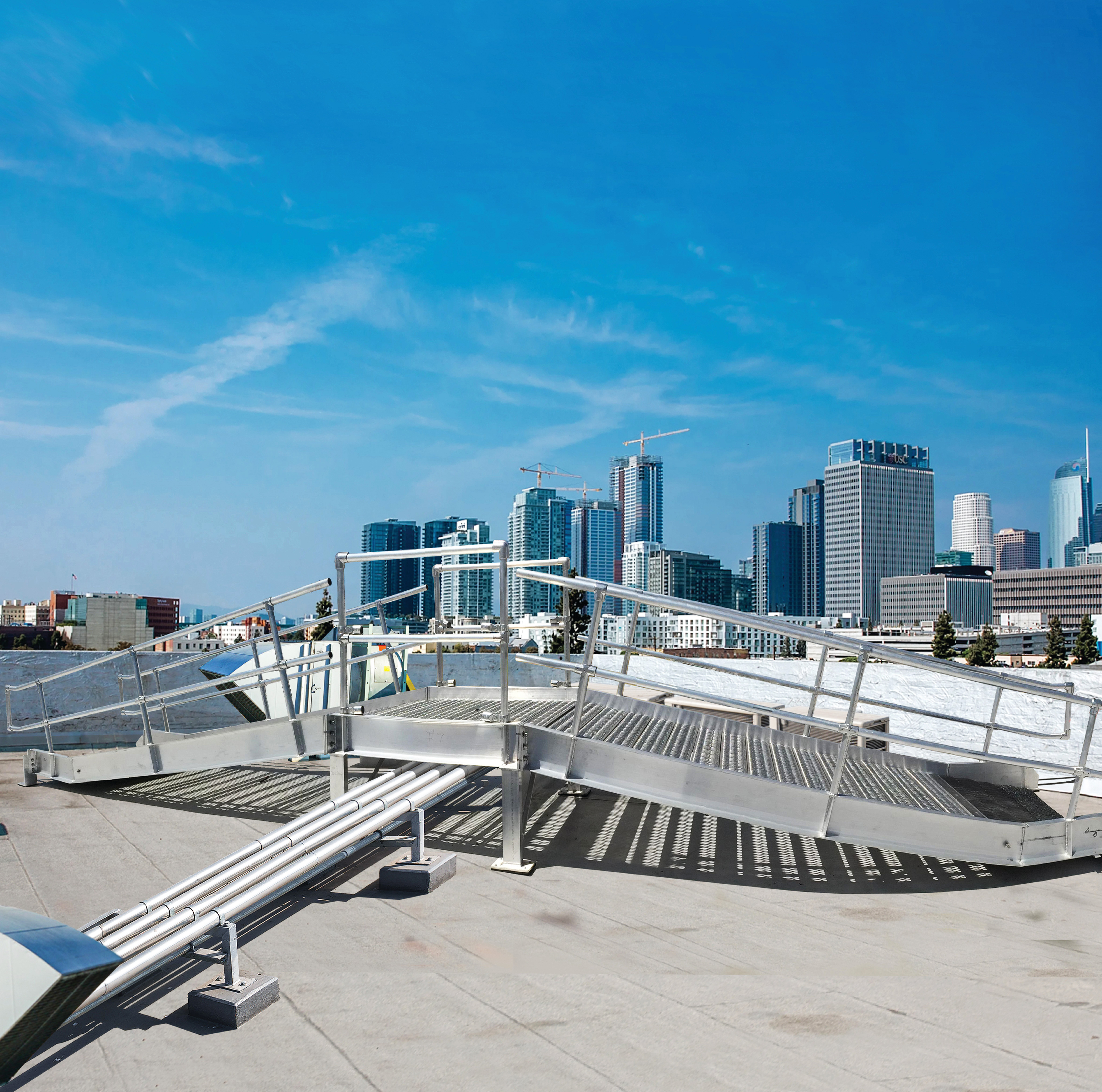
Photo courtesy of Alaco Ladder
Aluminum ladders such as this crossover model are ideal for outdoor use as they are lightweight, durable, and corrosion resistant.
Materials are so crucial to the advancement of humanity that they define some eras. The Stone Age lasted from about 2.6 million years ago until about 3,000 B.C. The Bronze Age began about 3,000 B..C and lasted until about 1,200 B.C. The Iron Age began around 1,200 B.C. and lasted until 550 B.C. In all cases, these materials revolutionized the critical making of tools and weapons.
The current era is also defined by the modern materials available to us, and some refer to this era as the Aluminum Age. As a relatively new metal in human history, aluminum creates a mind-bogglingly vast array of products from spacecraft to aluminum foil, and thousands more products that move contemporary humans forward.
Heavy-duty aluminum ladders are prime examples of commonly specified building components that are far more practical and usable than their steel counterparts.
Aluminum Mining and Refining
Aluminum occurs naturally in bauxite ore and is the most common metal in the earth’s crust. It is almost twice as abundant as iron. Bauxite is typically found near the earth’s surface, meaning it can be mined economically without creating deep pits. In 2023, 400 metric tons of bauxite were mined. Small amounts of bauxite ore are in Arkansas, Alabama, and Georgia, but little mining is done in the United States today. The leading countries in bauxite mining are Brazil, China, Australia, India, and Guinea.
Alum, a naturally occurring aluminum-containing compound, has been used since Greek and Roman times for various purposes, including setting dyes. However, until relatively recently, there was no economical way to extract aluminum (unlike iron) from ores. In the 1820s, a German chemist extricated a few aluminum slivers, and the novel metal was an instant sensation.
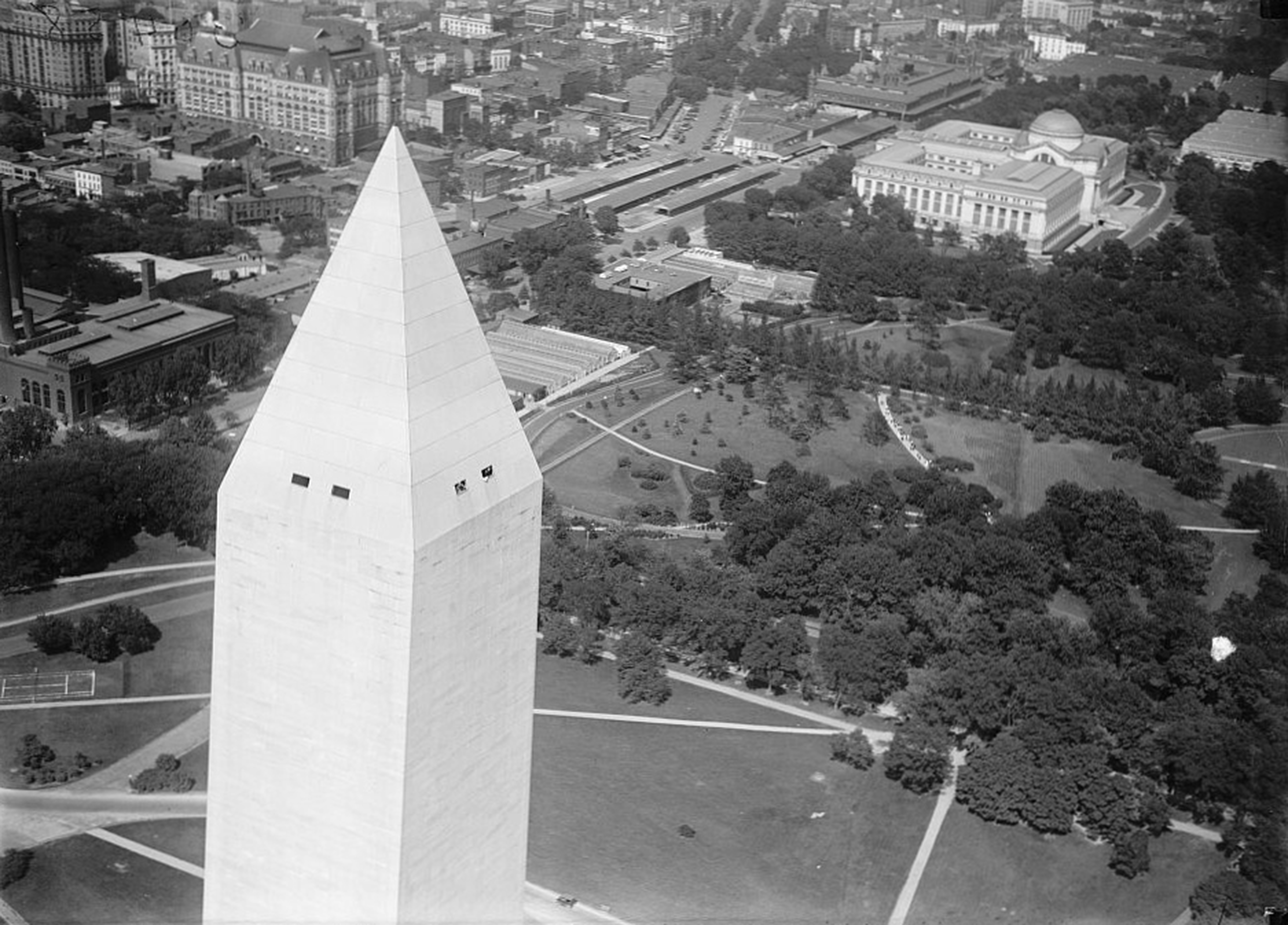
Harris & Ewing, Public Domain (https://en.wikipedia.org/wiki/History_of_aluminium#/media/File:NATIONAL_MUSEUM,_NEW._AIRVIEW._AT_REAR.jpg)
The 6.3-pound capstone of the Washington Monument in Washington, D.C., was made from aluminum in 1884. At the time, it was the largest piece of aluminium ever cast.
People admired the gleam of aluminum (designated the 13th element), which reminded them of the luster of gold and silver. It became a brand-new precious metal. In the 19th century, aluminum became more prized than silver and gold because it was harder to obtain. It is said that Napoleon III offered a cherished set of aluminum knives and forks for special guests at banquets, while less esteemed visitors used gold cutlery.
Scientists developed many ways to create aluminum, but none were economical enough for widespread production, so it remained a precious metal. Aluminum became more available to the public with the Hall–Héroult process, which was developed independently by American engineer Charles Martin Hall and French engineer Paul Héroult in 1886, and the Bayer process, which was developed by Austrian chemist Carl Joseph Bayer in 1889. Modern-day aluminum production is still based on the Hall–Héroult and Bayer processes. Today, aluminum is produced in greater quantities than all other combined non-ferrous metals (those containing iron).
Differences Between Aluminum and Steel for Use in Ladders
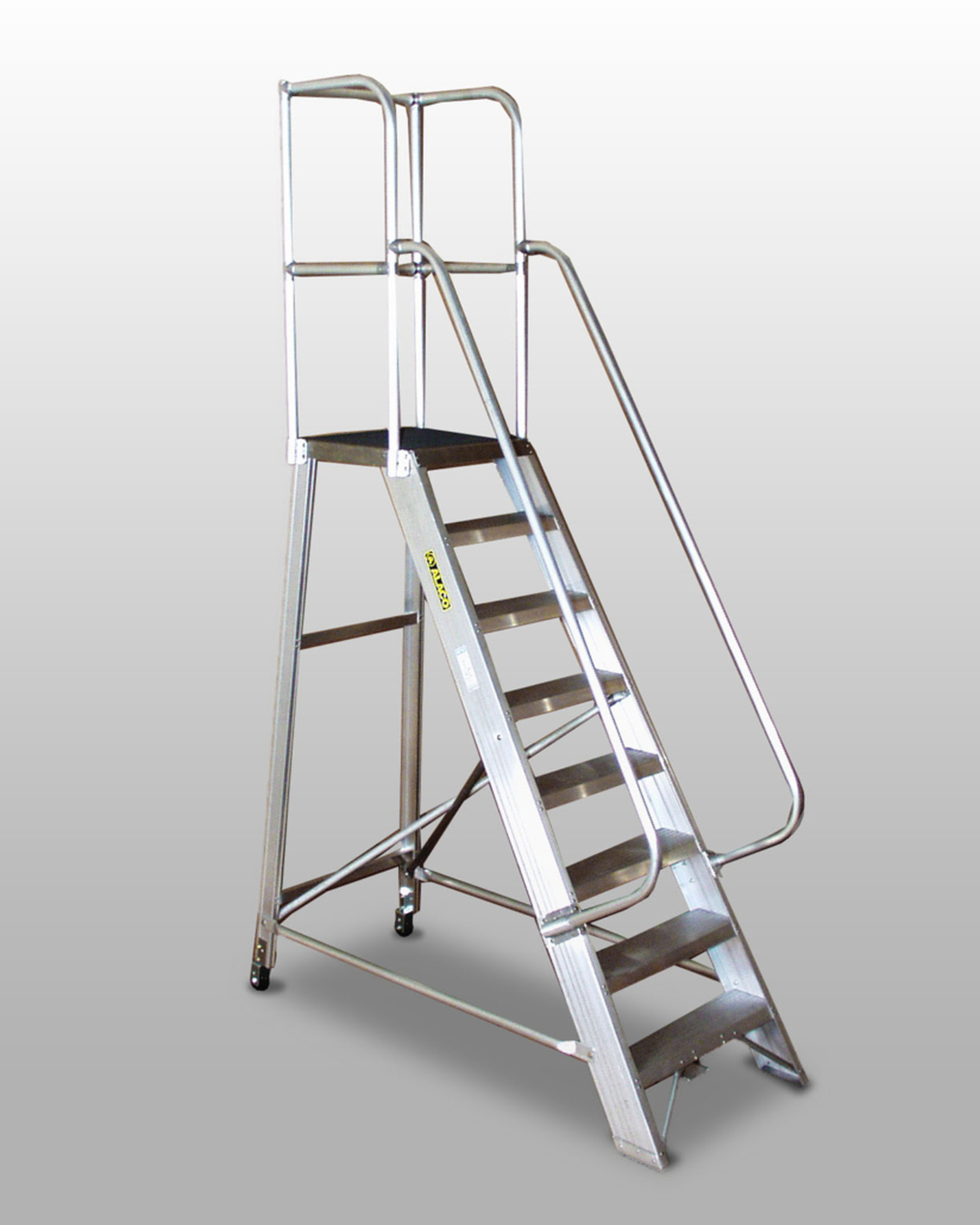
Photo courtesy of Alaco Ladder
Aluminum ladders are lightweight but strong.
While at a glance, a steel and an aluminum ladder might look the same, the difference in materials brings several distinct advantages and disadvantages. Some core differences between aluminum and steel ladders matter most for architects, developers, construction managers, retail store operators, and contractors.
Aluminum Ladders
Aluminum is significantly lighter than steel, weighing roughly one-third the weight of steel. If you have two identical pieces of metal, one made of aluminum and one made of steel, the steel piece will be about three times heavier than the aluminum piece.
Aluminum does not rust or fade, and it resists corrosion. It’s a maintenance-free material, so users do not incur ongoing costs over an aluminum ladder’s service life. This is important for aesthetic reasons and to ensure repeatable and safe operation. Plus, customization and modification are more manageable and safer with aluminum.
The lighter weight means aluminum fixed ladders don’t often require cranes or lifts for installation, which provides operators with considerable savings. They also place fewer loads onto roof and wall surfaces.
Steel Ladders
Some industrial-strength ladders made of steel are in environments where the additional weight and potential rusting and corrosion issues are not a primary concern. These ladders can offer strong platforms in high-use environments where load-bearing is the primary goal.
However, steel ladders placed outside in many environments will corrode in the sun or rain, making them less suitable for construction projects, fire ladders, outdoor ships ladders, and other installations. Rust on a steel ladder can be a sign that the ladder’s structure is compromised and should not be used.
Weight can be an issue. People typically move extension ladders, platform ladders, and other movable ladders. A steel ladder of comparable size and function to an aluminum one will weigh considerably more. This extra weight means the ladder is often impractical for repeated moving and might be unwieldy or dangerous for a single operator. Aluminum ladders are lighter, so they’re easier and safer to transport, and put less strain on workers.
On construction sites, steel ladders can pose issues on several fronts. They can produce sparks if they clang against another ladder. Aluminum ladders won’t spark, so they’re safer on construction sites around flammable materials. Steel ladders are also magnetic, so they can pose a risk in areas where magnetic equipment is used.
Characteristics of Aluminum for Ladders
- Contemporary Aesthetic: Aluminum can be anodized, polished, or buffed.
- Corrosion-Resistant: Aluminum protects itself against corrosion by creating a thin reactive layer when exposed to oxygen.
- Customizable: Aluminum is easy to fabricate, making it an ideal metal for custom products.
- Lightweight: Aluminum weighs about one-third the weight of iron, copper, brass, and steel.
- Low Maintenance: As it is naturally corrosion-resistant, aluminum does not require a protective finish or paint layer.
- Ductile: Aluminum is malleable and easy to form, extrude, and machine into complex shapes.
- Nontoxic: Aluminum is considered safe and nontoxic for building and residential applications.
- Exacting: Aluminum conforms to very close or tight tolerances to create products where precision is essential.
- Quality: When extruded, aluminum has a uniform quality.
- Recyclable: Aluminum is 100 percent recyclable and can be recycled indefinitely without losing its structural integrity. It is estimated that almost 75 percent of all the aluminum ever produced is still in use today.
- Strong: Aluminum extrusions are very strong and have a high tensile strength. Aluminum works well for cold-weather applications and strengthens as temperatures fall.
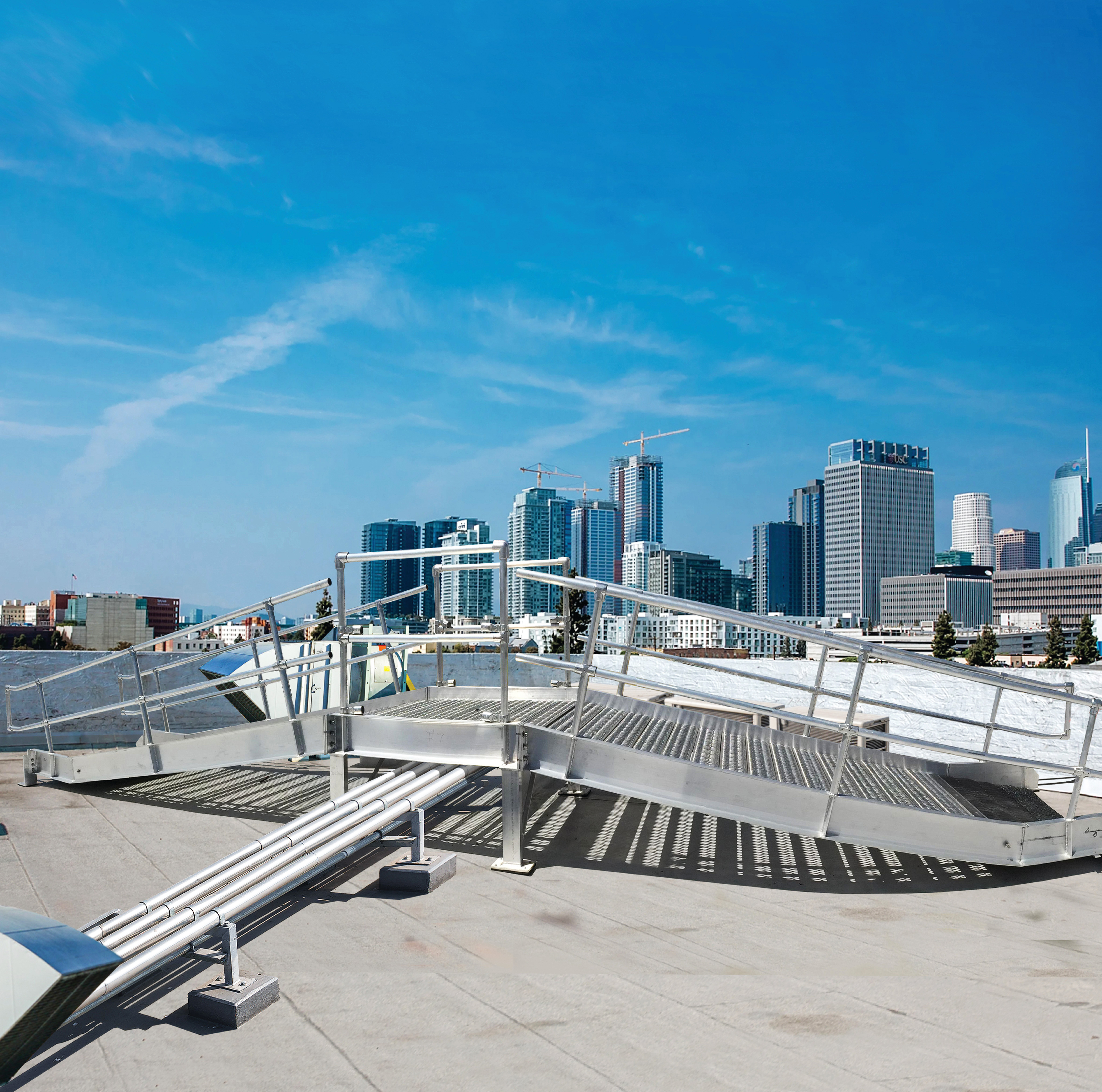
Photo courtesy of Alaco Ladder
Aluminum ladders such as this crossover model are ideal for outdoor use as they are lightweight, durable, and corrosion resistant.
Materials are so crucial to the advancement of humanity that they define some eras. The Stone Age lasted from about 2.6 million years ago until about 3,000 B.C. The Bronze Age began about 3,000 B..C and lasted until about 1,200 B.C. The Iron Age began around 1,200 B.C. and lasted until 550 B.C. In all cases, these materials revolutionized the critical making of tools and weapons.
The current era is also defined by the modern materials available to us, and some refer to this era as the Aluminum Age. As a relatively new metal in human history, aluminum creates a mind-bogglingly vast array of products from spacecraft to aluminum foil, and thousands more products that move contemporary humans forward.
Heavy-duty aluminum ladders are prime examples of commonly specified building components that are far more practical and usable than their steel counterparts.
Aluminum Mining and Refining
Aluminum occurs naturally in bauxite ore and is the most common metal in the earth’s crust. It is almost twice as abundant as iron. Bauxite is typically found near the earth’s surface, meaning it can be mined economically without creating deep pits. In 2023, 400 metric tons of bauxite were mined. Small amounts of bauxite ore are in Arkansas, Alabama, and Georgia, but little mining is done in the United States today. The leading countries in bauxite mining are Brazil, China, Australia, India, and Guinea.
Alum, a naturally occurring aluminum-containing compound, has been used since Greek and Roman times for various purposes, including setting dyes. However, until relatively recently, there was no economical way to extract aluminum (unlike iron) from ores. In the 1820s, a German chemist extricated a few aluminum slivers, and the novel metal was an instant sensation.
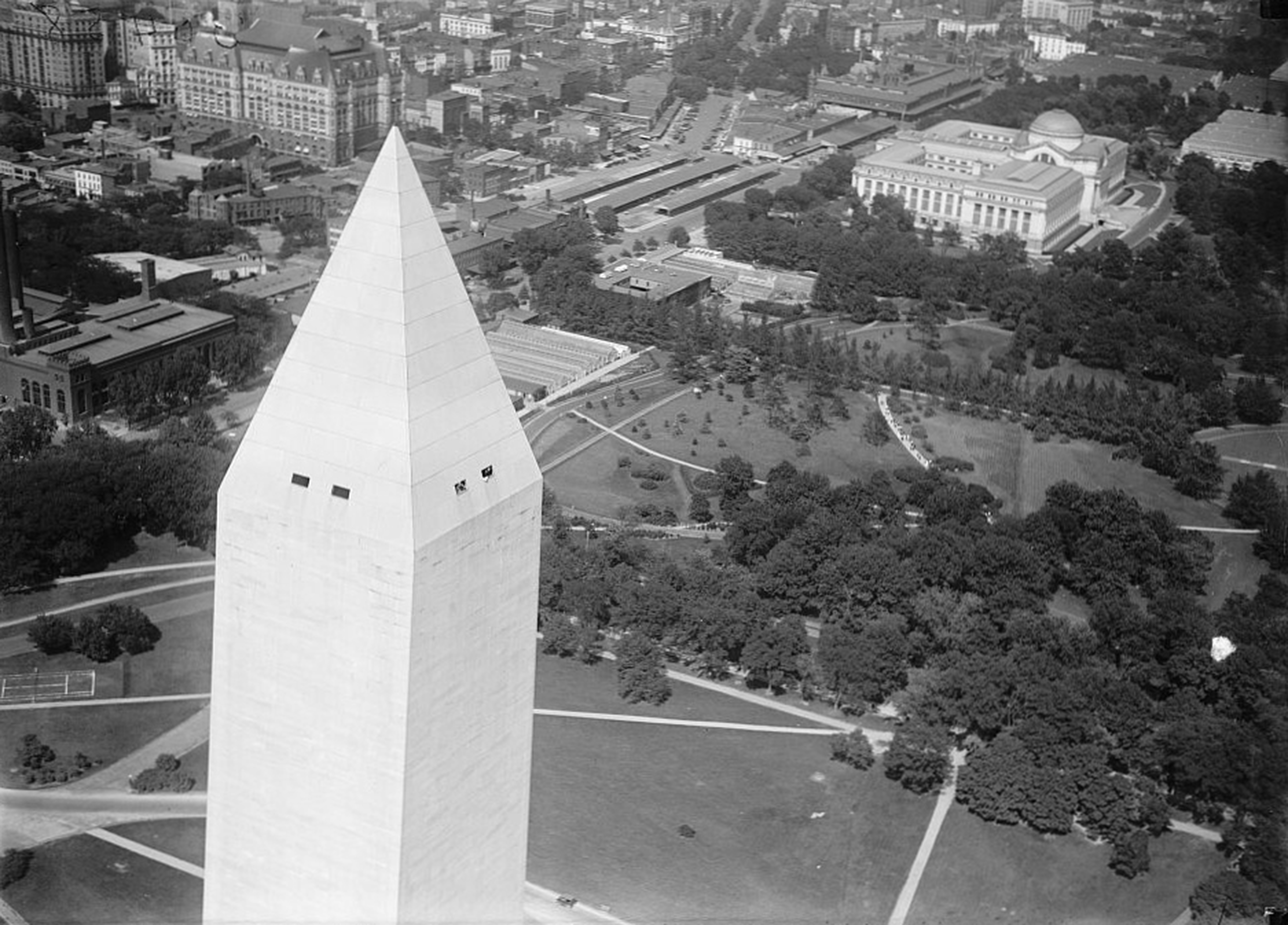
Harris & Ewing, Public Domain (https://en.wikipedia.org/wiki/History_of_aluminium#/media/File:NATIONAL_MUSEUM,_NEW._AIRVIEW._AT_REAR.jpg)
The 6.3-pound capstone of the Washington Monument in Washington, D.C., was made from aluminum in 1884. At the time, it was the largest piece of aluminium ever cast.
People admired the gleam of aluminum (designated the 13th element), which reminded them of the luster of gold and silver. It became a brand-new precious metal. In the 19th century, aluminum became more prized than silver and gold because it was harder to obtain. It is said that Napoleon III offered a cherished set of aluminum knives and forks for special guests at banquets, while less esteemed visitors used gold cutlery.
Scientists developed many ways to create aluminum, but none were economical enough for widespread production, so it remained a precious metal. Aluminum became more available to the public with the Hall–Héroult process, which was developed independently by American engineer Charles Martin Hall and French engineer Paul Héroult in 1886, and the Bayer process, which was developed by Austrian chemist Carl Joseph Bayer in 1889. Modern-day aluminum production is still based on the Hall–Héroult and Bayer processes. Today, aluminum is produced in greater quantities than all other combined non-ferrous metals (those containing iron).
Differences Between Aluminum and Steel for Use in Ladders
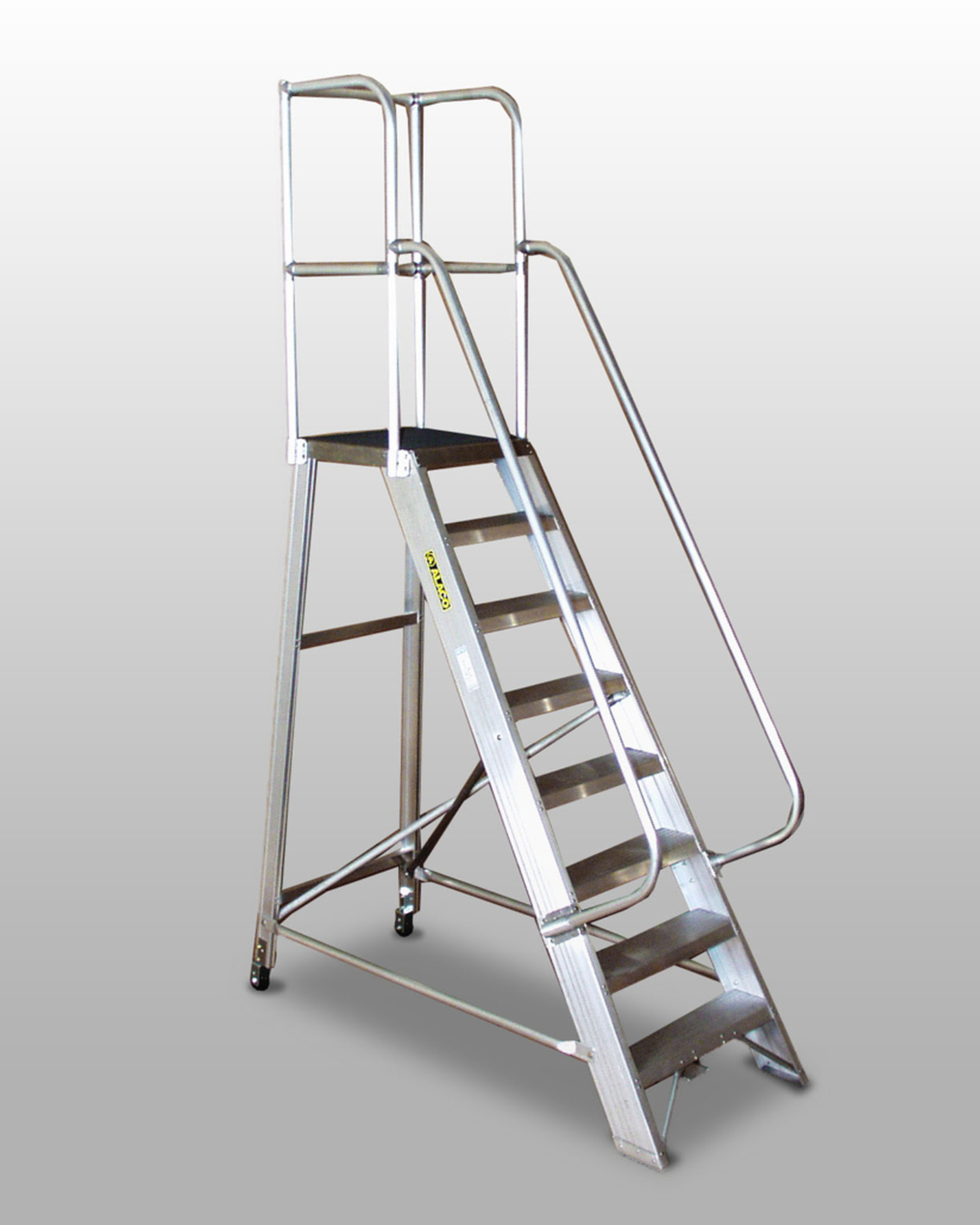
Photo courtesy of Alaco Ladder
Aluminum ladders are lightweight but strong.
While at a glance, a steel and an aluminum ladder might look the same, the difference in materials brings several distinct advantages and disadvantages. Some core differences between aluminum and steel ladders matter most for architects, developers, construction managers, retail store operators, and contractors.
Aluminum Ladders
Aluminum is significantly lighter than steel, weighing roughly one-third the weight of steel. If you have two identical pieces of metal, one made of aluminum and one made of steel, the steel piece will be about three times heavier than the aluminum piece.
Aluminum does not rust or fade, and it resists corrosion. It’s a maintenance-free material, so users do not incur ongoing costs over an aluminum ladder’s service life. This is important for aesthetic reasons and to ensure repeatable and safe operation. Plus, customization and modification are more manageable and safer with aluminum.
The lighter weight means aluminum fixed ladders don’t often require cranes or lifts for installation, which provides operators with considerable savings. They also place fewer loads onto roof and wall surfaces.
Steel Ladders
Some industrial-strength ladders made of steel are in environments where the additional weight and potential rusting and corrosion issues are not a primary concern. These ladders can offer strong platforms in high-use environments where load-bearing is the primary goal.
However, steel ladders placed outside in many environments will corrode in the sun or rain, making them less suitable for construction projects, fire ladders, outdoor ships ladders, and other installations. Rust on a steel ladder can be a sign that the ladder’s structure is compromised and should not be used.
Weight can be an issue. People typically move extension ladders, platform ladders, and other movable ladders. A steel ladder of comparable size and function to an aluminum one will weigh considerably more. This extra weight means the ladder is often impractical for repeated moving and might be unwieldy or dangerous for a single operator. Aluminum ladders are lighter, so they’re easier and safer to transport, and put less strain on workers.
On construction sites, steel ladders can pose issues on several fronts. They can produce sparks if they clang against another ladder. Aluminum ladders won’t spark, so they’re safer on construction sites around flammable materials. Steel ladders are also magnetic, so they can pose a risk in areas where magnetic equipment is used.
Characteristics of Aluminum for Ladders
- Contemporary Aesthetic: Aluminum can be anodized, polished, or buffed.
- Corrosion-Resistant: Aluminum protects itself against corrosion by creating a thin reactive layer when exposed to oxygen.
- Customizable: Aluminum is easy to fabricate, making it an ideal metal for custom products.
- Lightweight: Aluminum weighs about one-third the weight of iron, copper, brass, and steel.
- Low Maintenance: As it is naturally corrosion-resistant, aluminum does not require a protective finish or paint layer.
- Ductile: Aluminum is malleable and easy to form, extrude, and machine into complex shapes.
- Nontoxic: Aluminum is considered safe and nontoxic for building and residential applications.
- Exacting: Aluminum conforms to very close or tight tolerances to create products where precision is essential.
- Quality: When extruded, aluminum has a uniform quality.
- Recyclable: Aluminum is 100 percent recyclable and can be recycled indefinitely without losing its structural integrity. It is estimated that almost 75 percent of all the aluminum ever produced is still in use today.
- Strong: Aluminum extrusions are very strong and have a high tensile strength. Aluminum works well for cold-weather applications and strengthens as temperatures fall.
Grades of Aluminum and Which is Better for Ladders
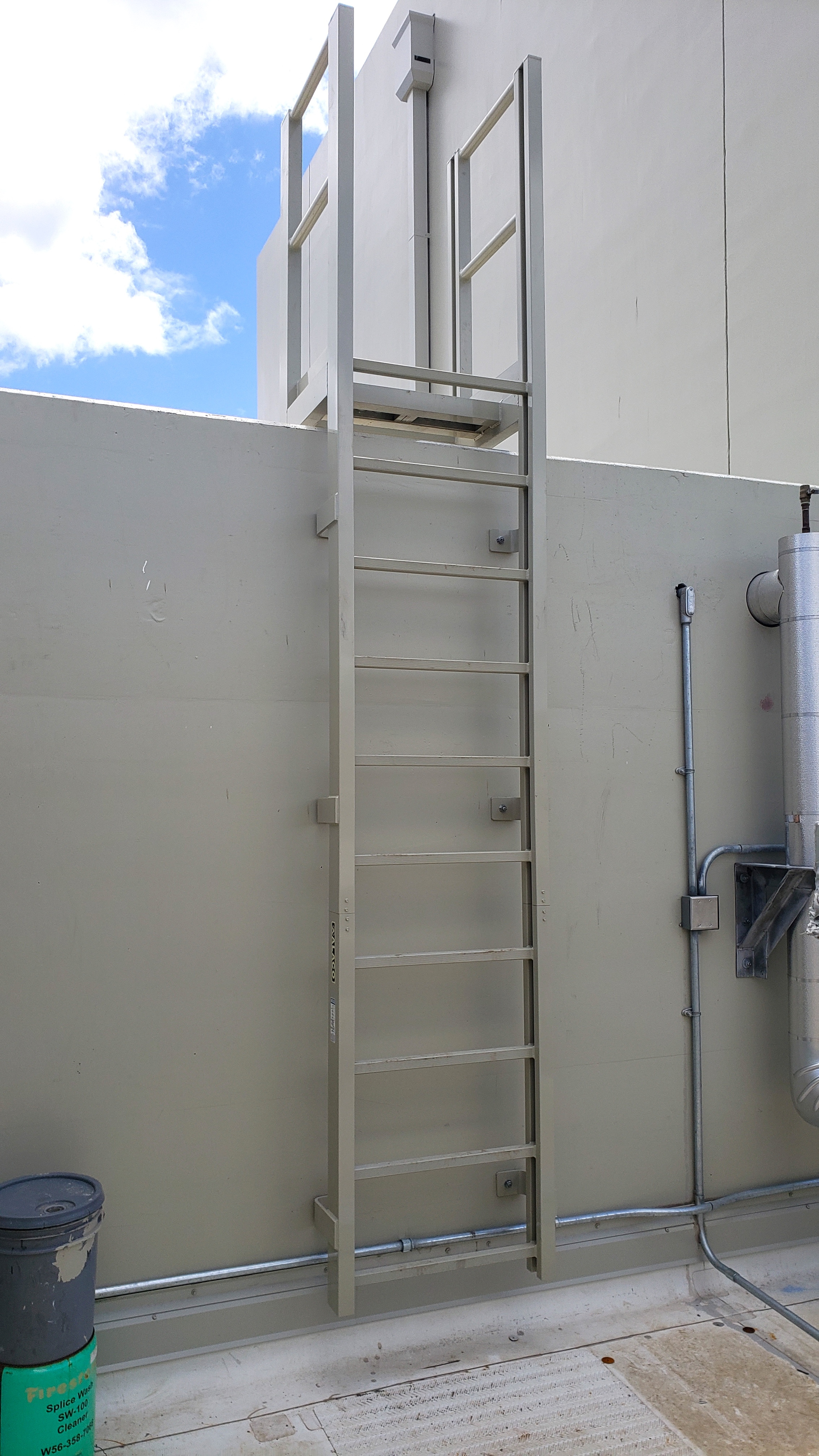
Photo courtesy of Alaco Ladder
Unlike steel ladders, aluminum ladders do not rust.
To reiterate, pure aluminum does not occur naturally as it always bonds to other metals, such as bauxite ore, from which must be refined into aluminum powder. That powder is alloyed with other materials to create different grades of aluminum. Two common grades of aluminum are 3003 and 6061-T6 aluminum are:
- Grade 3003 Aluminum: A standard aluminum alloy grade is in the wrought aluminium-manganese family (3000 series). It can be cold-worked (but not heat-treated, unlike other aluminum alloys) to produce tempers (the degree of hardness and elasticity of a metal) with a higher strength but a lower ductility. Grade 3003 is a general-purpose alloy with moderate strength, good workability, and corrosion resistance, like most other aluminum-manganese alloys. It is commonly used in such sheet metal applications as siding, downspouts, gutters, and roofing.
- Grade 6061-T6 Aluminum: When considering a ladder for a job site or retail installation, it’s vital to review the quality of the materials. Industrial-strength aluminum ladders are often made from 6061-T6 aluminum alloy. This type of aluminum is referred to as “aircraft grade” and is stronger and higher quality than some other aluminum types. It is used for transportation, architecture, and tooling. Diverse applications include bridge railings, automobile frames and running boards, platforms, steps, walkways, bicycle frames, scuba tanks, and fishing reels. The T6 refers to the temper, which is the degree of hardness achieved by precipitation hardening, a heat treatment process.
Grade 6061 aluminum alloy (Unified Numbering System designation A96061) contains silicon and magnesium as its major alloying elements. Developed in 1935, it was initially known as “Alloy 61S.” Grade 6061 aluminum exhibits good mechanical properties, has good weldability, and is often extruded. For general-purpose use, it is one of the most common aluminum alloys.
Despite steel’s greater strength, aluminum’s lower density provides a superior strength-to-weight ratio compared to steel. Carbon steel, for instance, might have a tensile strength of 500 MPa (megapascal), but its density is about three times that of aluminum alloys. However, an aluminum alloy like 6061 has a tensile strength of around 310 MPa while weighing significantly less. In applications like aircraft manufacturing, where weight reduction is as essential as structural integrity, aluminum is a good choice.
Technological Advances in Aluminum
As the Aluminum Age advances into another century, innovations continue. Researchers are developing new alloys that create aluminum with improved durability, corrosion resistance, and strength while remaining lightweight. According to data, these new alloys can withstand higher stress levels. Automation has found its way into the aluminum manufacturing process, creating more efficiencies and precision. And AI (artificial intelligence) is improving quality control to degrees impossible in the past.
The metal’s potential is so great that technology is being developed to use aluminum in a battery storage concept called Aluminum-CO2 as an alternative to lithium-ion batteries. Recent successful testing at the Battery Innovation Center has moved the concept one step closer to commercial production. From battery storage to lightweight body panels, aluminum has become a significant factor in the viability of electric vehicles.
Aluminum is also a key material used for renewable energy. Solar panels and wind turbines benefit from the metal’s strength, durability, light weight, and corrosion resistance.
In addition, aluminum production is getting greener, which is critical as the demand for aluminum is expected to skyrocket in the coming decades. Hydro, a Norwegian aluminum and renewable energy firm, has developed a proprietary technology that could fully decarbonize aluminum smelting. For its pioneering work on green aluminum, the company received an award at the 2023 UN Climate Change Conference in the United Arab Emirates. Hydro president and CEO Hilde Merete Aasheim was quoted in Trellis (formerly GreenBiz) stating, “We are changing the game for aluminum. This is an important recognition of our efforts to develop new technology that could be the biggest thing to happen in aluminum production since the invention of the Hall-Héroult process in 1886.”
With the rapidly increasing adoption of electric vehicles worldwide, growing needs for innovative batteries that run them, the rise in solar and wind energy, and the greening of the industry, technological advances in aluminum—including the aluminum used to manufacture industrial-strength ladders—are sure to continue.
Types of Aluminum Ladders and the OSHA and ANSI Standards Relevant to Each
Ladder accidents are a serious concern in the U.S. The CDC reports that in 2020, there were 21,710 injuries and 161 fatalities from ladder falls. Industries that experience higher ladder fall injury rates are construction, maintenance, repair, and small businesses. The causes cited are inappropriate ladder selection, improper use of ladders, incorrect extension ladder set-up angle, insufficient ladder inspection, and lack of access to ladder safety tools and information. Several factors affect ladder safety. However, ladder manufacturers can help address the nationwide issue by strictly following the OSHA standards for ladders.
Ladders that comply with ANSI A14 standards are compliant with and accepted by OSHA. The approved developer of ANSI safety standards for the ladder industry is the American Ladder Institute.
Standards are technical specifications that prescribe rules governing the safe construction, design, testing, care, and use of various types of ladders. Standards are developed on a five-year renewal cycle. Subcommittees comprised of industry experts exist for each standard.
For maximum safety, exterior ladders should meet the following OSHA standards for ladders:
- Weight Capacity [OSHA 1926.1053(a)]: Exterior ladders have varying weight capacities, depending on what the manufacturer uses for the frame and steps. Aluminum alloy ladders meet the OSHA standards for exterior ladders and can easily accommodate a couple hundred pounds. However, OSHA dictates that a ladder’s breaking point should exceed its marketed weight capacity. It should have enough strength for tools and equipment. OSHA standard 1926.1053(a) states that self-supporting and portable ladders should be able to accommodate 3.3 times and 4 times their intended loads, respectively.
- Ladder Safety [OSHA 1926.1053(b)]: OSHA standard 1926.1053(b) focuses on ladder safety. It requires users to place their grease-free, damage-free exterior ladders on flat surfaces, guaranteeing sturdy footholds. The section also prohibits users from exceeding the rated capacity.
- Ladder Condition [OSHA 1926.1053(b)(17)]: Under OSHA standard 1926.1053(b)(17), consumers can’t use fixed ladders with corroded components, split rails, or missing steps, among other damages. The OSHA standards for ladders dictate that using damaged ladders is an act of negligence on the victim’s part; they can’t blame the manufacturer. While the ladder condition is the user’s responsibility, ladder manufacturers offer warranties that cover necessary repairs to return the ladder to a safe condition. Specifiers should review a ladder manufacturer’s warranty and willingness to repair ladders under warranty.
- Basic Safety Guidelines [1910.25(b)]: Standard 1910.25(b) explains the basic guidelines for all fixed staircases, including ships ladders (discussed later in the course) in industrial settings. First and foremost, all ships ladders and staircases must have guardrails and handrails. If the architect or employer claims it’s impossible to set up rails, they must propose an alternative fall protection system.
As for overhead obstructions, they must always have a vertical clearance of at least 6 feet, 8 inches. Note that tread depths and riser heights must be uniform. Also, landings at the sides should meet a minimum width of 30 inches.
Also, OSHA has a minimum 1,000-pound stair capacity. However, note that 1910.25(b) specifies each stair should accommodate at least five times the anticipated live load of typical foot traffic. Ladders made of industrial-strength aluminum alloy easily meet the OSHA standards for ships ladders and minimum load requirements.
Crossover Ladders
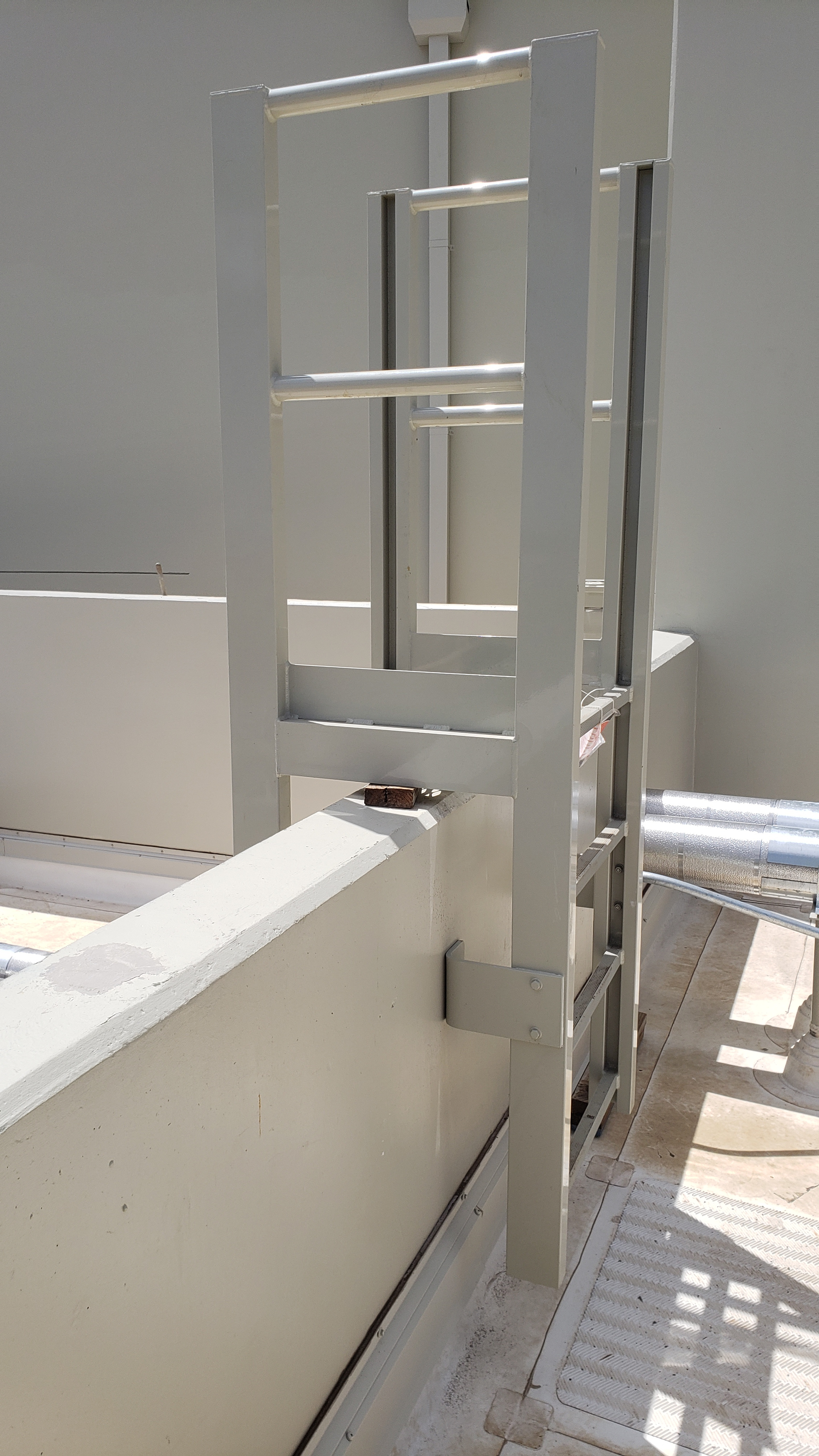
Image provided by Alaco Ladder
Aluminum crossover ladders help users safely navigate obstacles.
Exterior ladders provide access to the roof. These are fixed ladders mounted on the exterior wall of the structure or building. Crossover exterior ladders, on the other hand, are ladders used on rooftops to provide a safe platform for crossing over electrical conduits, water pipes, and other obstacles. The primary function of a crossover exterior ladder or platform is to prevent tripping accidents.
Crossover ladders or platforms are not exclusive to exterior and roofing applications. These are common in industrial workplaces such as manufacturing plants and factories. Crossover ladders provide a safe passage over equipment and hazardous materials inside the factory. Instead of building platforms above fixed machinery, installing an industrial crossover ladder is an alternative. They consume less space and are more economical. However, note that machinery cannot be installed on top of crossover ladders.
Crossover ladders can also be installed over deep holes and pits. The ladder will let people quickly cross these hazards, and the handrails will prevent accidents.
It is essential to understand that not every crossover ladder on the market is OSHA-compliant. An engineer, building contractor, roofing contractor, architect, or specifications writer should ensure ladders specified for a project are designed and manufactured according to OSHA standards and applicable to local building codes. This diligence protects the company from liability and, more importantly, protects workers and general users by reducing their exposure to slip and fall accidents.
Crossover exterior ladder safety features include:
- Heavy-duty aluminum construction
- Appropriately sized rungs
- Deflection devices for wider gaps
- Adequate side rail sizes and positions
It is important to note that rung size is just as crucial as other ladder components. Some buyers neglect to check the size of the rung, focusing mostly on handrails and rubber feet that secure the bottom of the ladder. A rung that is either too big or too small and spaced unevenly between rungs could cause the user to become unstable, which increases their risk of a slip-and-fall accident.
Crossover ladders should conform to the following OSHA standards:
- Distances [OSHA 1917.118(d)(4)]: OSHA requires at least 4 inches between the nearest structure and the rung central line. However, if a ladder were installed before 1983, it would need to maintain a distance of 7 inches.
- Overhead Openings or Obstructions [OSHA 1917.118(d)(5)]: If the aluminum ladder passes through overhead openings or obstructions (i.e., pits, walls), there should be a minimum clearance of 24 inches. This could occur in a tunneled aluminum crossover ladder, elevator pit access, or roof return.
- Rail Positions [OSHA 1917.118(d)(6) and (7)]: Standards 1917.118(d)(6) to (7) focus on side rail positions. The first standard number dictates that rails must extend no less than 36 inches over the top landing surface. Otherwise, there is a need for an alternative grab bar. Meanwhile, 1917.118(d)(7) prohibits consumers from using exterior ladders horizontally slanting 90 degrees.
- Manufacturer Limits [OSHA 1917.118(e)(4)]: According to the standard 1917.118(e)(4), OSHA-compliant exterior ladders and aluminum crossover ladders must be installed according to the manufacturer’s rated limits. Safety inspectors will also use manufacturer guidelines as the standard.
Ships Ladders
Standard-sized ladder and stair units are used indoors and outdoors for a variety of applications. However, for smaller spaces, these conventional ladders and stair units are not practical. For areas with limited space, aluminum ships ladders are the preferred choice of safety engineers, contractors, architects, and specification writers. These are narrower and steeper than standard-size ladders or stairs, making them ideal for smaller spaces.
Ships ladder units were initially designed to provide ships with sturdy and stable ladder units that don’t take up much space, given that rooms and passageways in vessels are relatively small and tight. These were typically used on decks, in control rooms, and for mezzanines. Today, ships ladder units are used in various applications, both in commercial and industrial settings, and sometimes in multifamily residential applications as well.
Aluminum ships ladders minimize accident risks when these standards are followed:
- Fall Prevention [OSHA 1910.25(b)(1)]: This standard states that aluminum ships ladder units have handrails and guides. If a space does not permit rails, a manufacturer can devise an alternative fall prevention system.
- Weight Capacity [OSHA 1910.25(b)(6)]: According to this standard, each stair can support at least five times the normal anticipated live load but never less than a concentrated load of 1,000 pounds applied at any point.
- Dimensions [OSHA 1910.25(d)]: [OSHA has specific OSHA dimension standards for ships ladders and spiral stairs. Standard 1910.25(d) requires a minimum headroom of 6 feet, 6 inches, a tread depth of 7.5 inches, and a clear width of 26 inches. OSHA has also set maximum riser height limits of 9.5 inches.
Exterior Ladders
OSHA-compliant exterior ladders are fixed ladders connected to structures less than 20 feet high. They are found on chimneys, tanks, elevator pits, low-rise rooftops, and other applications. However, note that they differ from staircases used for emergencies. To ensure the safety of users, OSHA-compliant exterior ladders follow these standards:
- Distance from Structure [1917.118(d)(4)]: The rung central line should be around 4 inches to 7 inches away from the nearest structure (i.e., wall, tank, post).
- Exceeding 20 Feet [1917.118(e)(2)]: This standard requires exterior ladders exceeding 20 feet to follow different structural requirements. Fixed ladders exceeding 20 feet need a cage or barricade, while portable or retractable ladders need a stable platform every 30 feet.
Cage Ladders and Platform Ladders
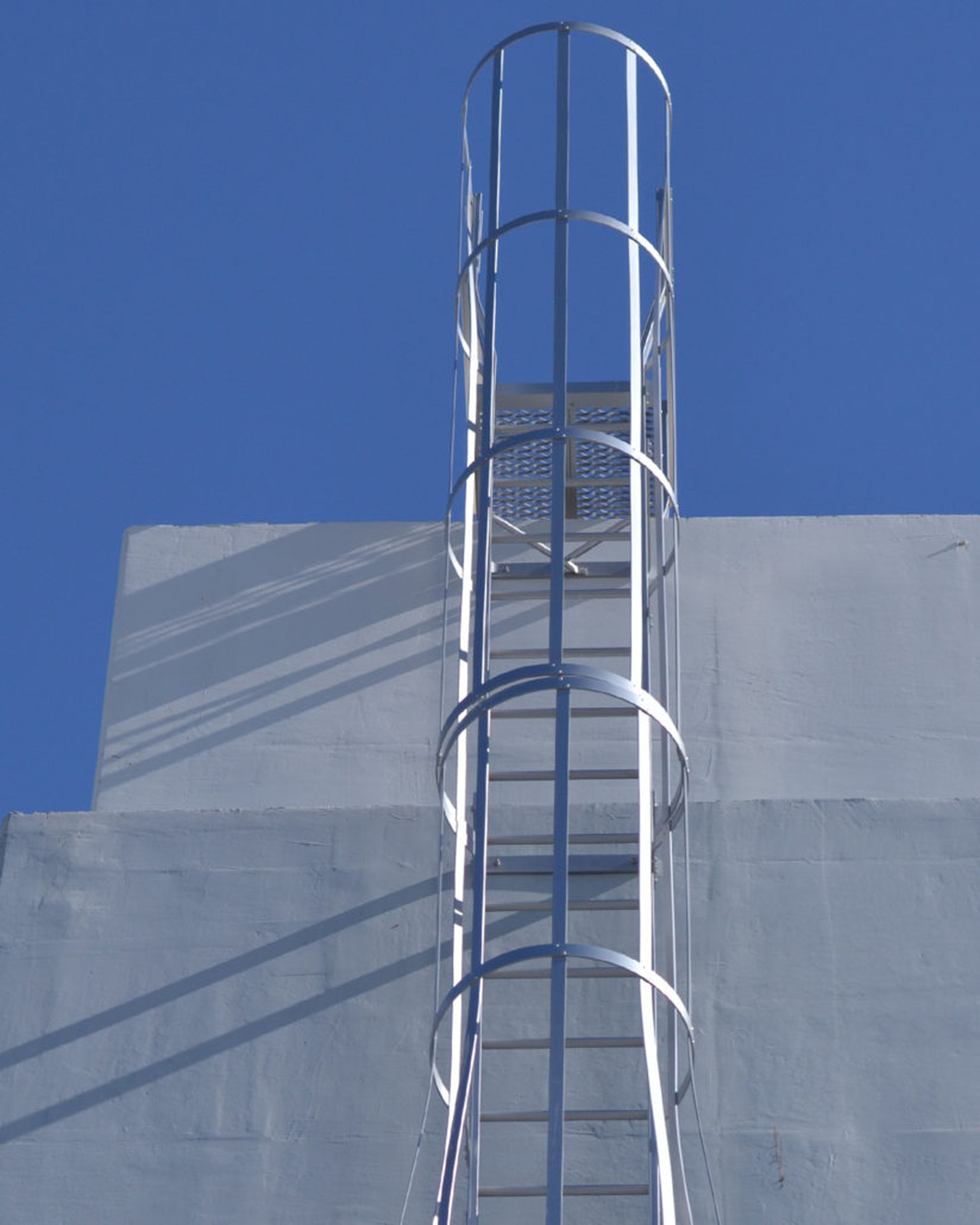
Photo courtesy of Alaco Ladder
An aluminum cage ladder protects users from falling.
OSHA states that ladders only classify as exterior ladders if they don’t exceed 20 feet. Structures that need an exterior ladder exceeding 20 feet will likely need one of the following options:
- Cage Ladder or Platform Ladder: Cage ladders look exactly like exterior ladders for a fixed ladder that exceeds 20 feet, but guardrails surround the rail and rungs about 10 feet up the ladder. The actual basket consists of hoops riveted around vertical bars.
As for OSHA compliance, aluminum cage ladders should abide by the following standards:
- Durable Rigid Barricade [1917.118(e)(5)(i)]: OSHA standard 1917.118(e)(5)(i) requires aluminum cage ladders to have a durable, rigid barricade that prevents people from falling. Aluminum alloy guardrails can support thousands of pounds to prevent the barrier from buckling.
- No Jagged Edges [1917.118(e)(5)(ii)]: Rigid, sturdy cage ladders prevent falls. However, OSHA standard 1917.118(e)(5)(ii) prohibits rough, jagged cages because they might puncture the skin if someone falls hard against the structure. These barriers must have smooth, even surfaces to protect users.
Platform Ladders
Aluminum platform ladders function as portable exterior ladders that exceed OSHA’s 20-foot limit. They can scale structures exceeding 30 feet, such as billboards, signages, telephone lines, and mid-rise buildings. However, note that platform ladder heights aren’t adjustable. As its name suggests, the most defining feature of a platform ladder is its broad platform. Platforms only have space for one person. However, they should leave enough leeway for mid-sized tools and equipment, plus any additional safety harnesses and gear. The platform gives users a secure resting area when climbing very tall ladders. Serrated aluminum floor grating allows for safer footing and is virtually self-cleaning.
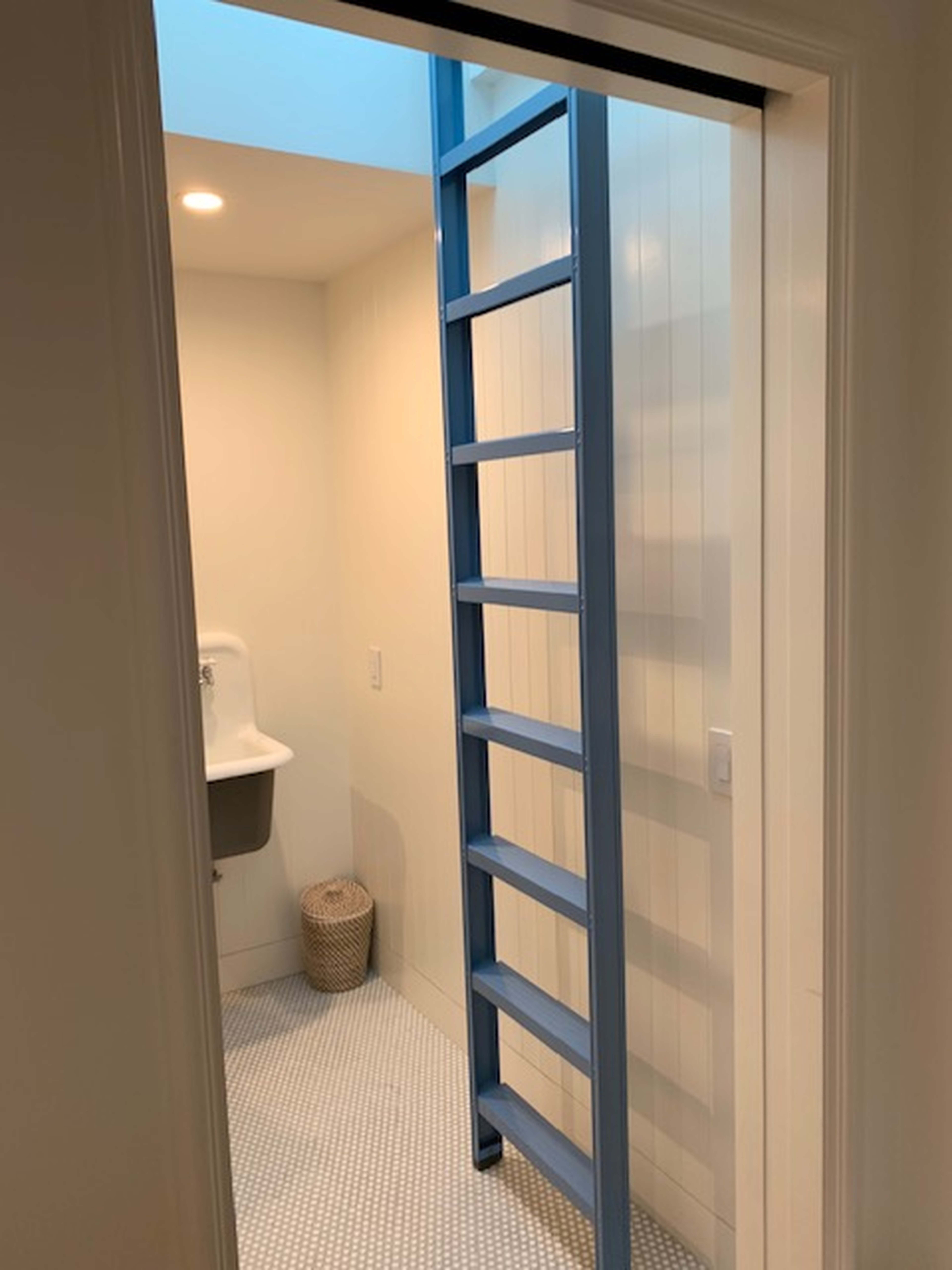
Photo courtesy of Alaco Ladder
Aluminum roof access ladders are specified for both commercial and residential applications.
- Roof Hatch Access: Roof hatch ladders play an essential part in commercial buildings, allowing access to the roof for maintenance of air conditioning units, checking and repairing the roofing, and other purposes. There are several ladder configurations to allow access to a roof hatch.
- Ships Ladders: Aluminum ships ladders are designed for a fixed, permanent installation with heavy-duty aluminum brackets. Flush handrails are standard.
- Folding Wall Ladders: Designed with special mounting brackets to save space when not in use, convenient folding wall ladders fold against the wall when not in use. They should feature solid, no-scuff feet for a steady, superior grip.
- Fixed Wall Ladders: For permanent access to roof hatches, fixed ladders are attached to the wall with heavy-duty mounting brackets.
- Retractable Fixed Wall Ladders: A space-saving design for use in areas with tight access to roof hatches, retractable fixed wall ladders are attached to the wall with specialized mounting brackets that enable the ladder to retract flat against the wall when not in use.
- Ladder Extension Safety Posts: Extension posts provide safer, easier access through roof access hatches. Extension posts mount permanently to the top two rungs of fixed or ships ladders, providing a positive hand-hold that enables users to enter or exit openings in an upright and balanced position.
Extension and Single-Section Ladders
Heavy-duty aluminum extension ladders and single-section ladders are engineered for safety, comfort, mobility, and a long service life. Ideally, extension ladders are manufactured from 6061-T6 aircraft aluminum alloy for a superior strength-to-weight ratio. A round rung shape provides maximum strength, while serrated rungs allow for sure-grip footing. The rivets supporting each rung are critical for strength. For instance, solid aluminum alloy aircraft rivets will support each rung for 1,250 pounds of shear strength.
Heavy-Duty Mezzanine Ladder Units
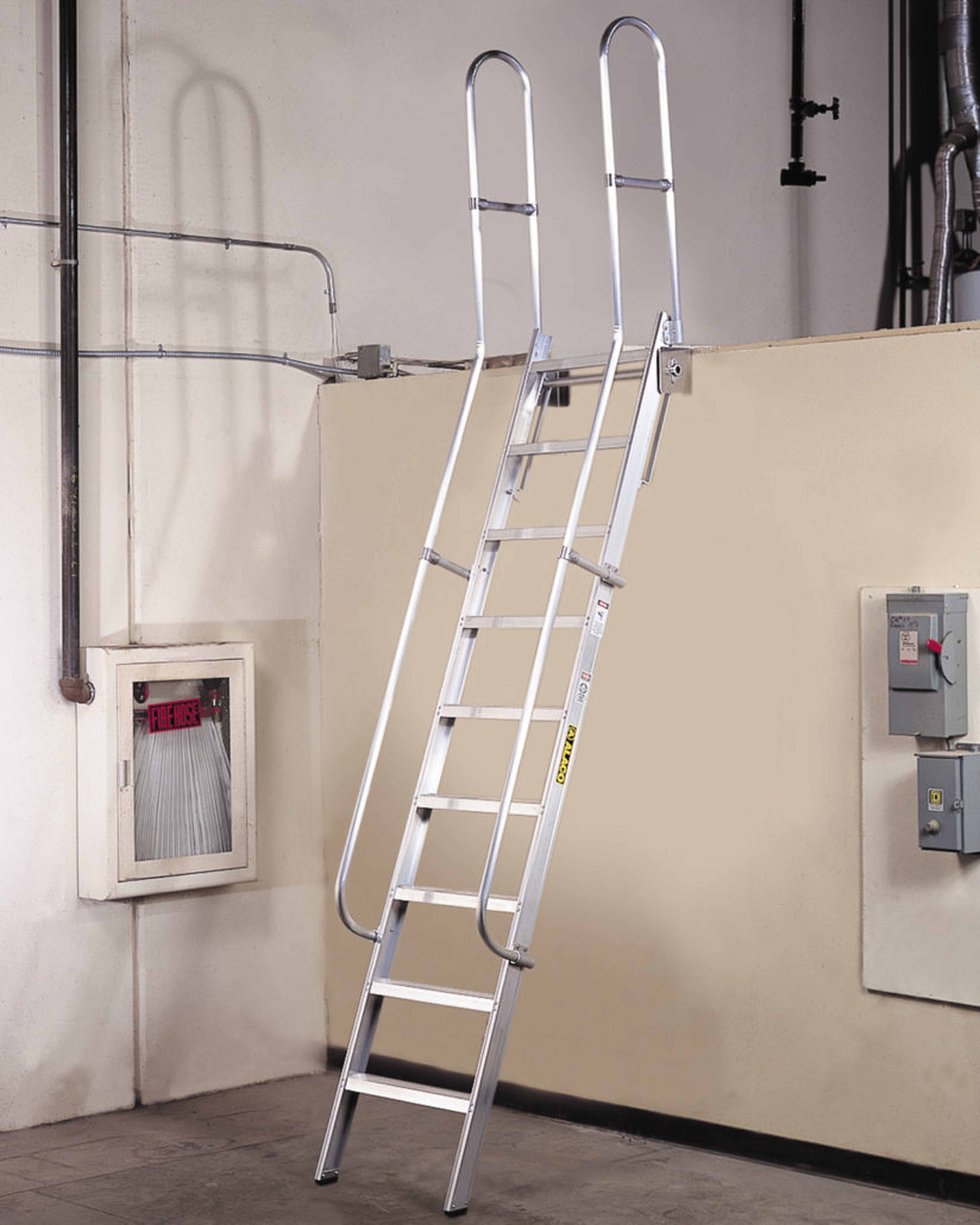
Photo courtesy of Alaco Ladder
This aluminum mezzanine ladder has handrails for safety.
A mezzanine is generally an elevated open space built or installed between the ground floor and the first floor or between the main floor and the floor above it in residential, commercial, and industrial spaces.
One of the challenges of having a mezzanine is providing safe access to the space for all users. A ladder or a staircase is usually provided to access this elevated space.
Should the ladder be a fixed installation? Should it be a temporary or portable ladder? And with each choice, what occupational safety standards must be met as dictated by OSHA? What safety features must be installed?
Two types of aluminum ladder models are commonly specified for mezzanine access:
Ships Ladders or Folding Wall Ladders
OSHA defines ships ladders as special fixed staircases with treads, risers, and steps that slope 50 degrees to 70 degrees horizontally. They are much steeper than standard stairs and are designed for a fixed, permanent installation.
Although they consume much less space, mobility-impaired individuals might find them challenging to climb. However, OSHA helps users prevent accidents by imposing specific guidelines. As with all staircases, they need handrails on the sides. To opt out of rails, the engineer or property manager must prove that extra handrails will only compromise workplace safety. In this instance, they must create an alternative fall prevention system.
OSHA classifies folding wall ladders as portable ladders. Like ships ladders, they slope steeper and consume less space than standard stairs. Designed with special mounting brackets to save space when not in use, convenient folding wall ladders should feature solid, no-scuff feet for a steady, superior grip. However, unlike ships ladders, they can be moved around as they aren’t attached to the floor or wall.
While convenient, portable ladders create several new risks that are mitigated by OSHA guidelines. Poorly spaced steps lead to accidents. OSHA generally dictates that steps should have a 10-inch to 14-inch distance between each other. Narrower-spaced steps cause fumbling, while wider-spaced steps are tiring to navigate.
Stockroom Ladders and Rolling Workstands
Heavy-duty aluminum is ideal for stockroom ladders and rolling workstands due to its strength and light weight. A stockroom ladder model has wide-spread feet for better stability and a safety platform of about 16 inches by 20 inches. Handrails offer additional security when climbing, and disengaging casters provide ease of movement. A rolling workstand offers enhanced safety and convenience with an extra large, 20-inch-by-20-inch top plate with a non-skid surface and 42-inch guardrails. A more gradual 60-degree climbing angle allows fast, comfortable use facing either toward the steps or away. Specific models have rated workloads of up to 500 pounds and can be ordered with many standard variations. Several different types of feet are available, with or without casters, and the handrails and guard rails can be made removable or assembled in unique configurations.
Loft Ladders
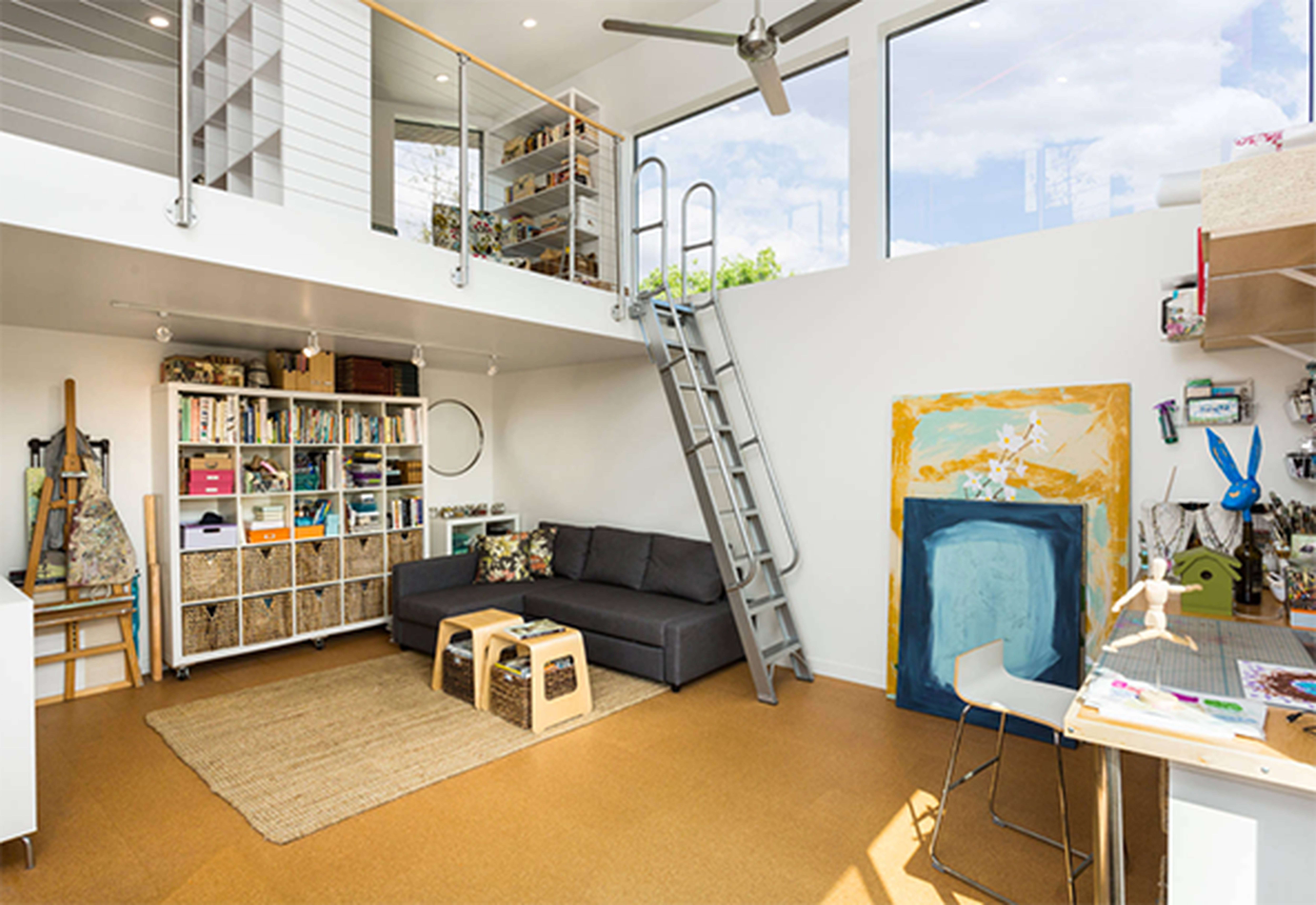
Photo courtesy of Clark Dugger
An aluminum loft ladder is smaller and more flexible than a staircase.
Aluminum loft ladders can be used in a room, garage, or workspace with a loft. There are two general ways to access a loft: a ladder or a staircase. A staircase may be too bulky and take up more space than a loft ladder. Staircases are also more complicated to install than a ready-made or prefabricated ladder unit, which takes an hour or two to configure and install. Additionally, should needs or tastes change, an existing aluminum ladder can be easily uninstalled and replaced by the preferred product.
A loft ladder must be made from a sturdy material, such as 6061-T6 aluminum, and its design and manufacturing process must follow safety standards. The ladder must follow load/weight capacities and have safety measures installed for easy and convenient use.
Aluminum loft ladders are typically available in natural milled or powder coat finishes. Custom colors may be available. Various metallic and enamel finishes may be available for the ladder hardware. Hardware may be finished to blend in with the ladder or to contrast as a design element.
Loft ladders are available in a variety of options for different applications:
- Rolling track loft ladders roll along a sturdy metal track for easy access to any section of a loft. The track can be installed along a single wall or connected to multiple walls via curved corner track sections.
- Pivotal loft ladders help access areas where access space is limited. They are permanently fixed and fold against the wall when not in use for convenient and compact storage.
- Fixed loft ladders are designed for use with lofts with a single access point and are permanently affixed to the wall with sturdy brackets for fast and easy access.
Environmental Aspects of Aluminum Ladders
While the form and function of aluminum ladders have been examined, the following environmental features of aluminum over steel should be considered.
Recyclability
Ladders made with aluminum produce less waste because the material is frequently recycled. Most of the aluminum ever produced is still contained within products because the recycling rate is so high. According to The Aluminum Association, making recycled aluminum takes only 5 percent of the energy needed to create new aluminum. Industry recycling efforts in the U.S. are estimated to save more than 90 million barrels of oil equivalent each year. The association states that aluminum recycling has risen steadily from an annual average of 5 billion tons of aluminum scrap collected in the 1980s to 11.3 billion tons collected in the 2010s.
Less Weight on Building
The lighter weight means that aluminum fixed ladders place fewer loads onto roof and wall surfaces. There is no need for structural upgrades to accommodate heavier steel components.
Less Cost to Transport
Compared to steel ladders, aluminum ladders are lighter to transport, use less fuel, and produce less carbon. That means less stress on transport vehicles, less wear on roads, and less stress on equipment or workforce moving the products.
Fewer Maintenance Requirements
Because high-quality aluminum does not rust and is corrosion-resistant, maintenance requirements are lessened. This saves time and money for the building owner and operator. It also reduces the need for paint and other coatings that might produce unwanted volatile organic compounds.
Mine Rehabilitation
Bauxite ore is mined close to the earth’s surface, meaning deep mining is unnecessary. Some aluminum manufacturers prioritize avoiding or minimizing impacts on biodiversity and ecosystems wherever possible. “When impacts are unavoidable,” states Alcoa, a global manufacturer of aluminum, “we turn to restoration through progressive rehabilitation, which is carefully planned and considered from the early stages of mine development. At sites where our mines operate within forest ecosystems, rehabilitation is focused on returning native vegetation to the habitat, which helps address the direct and indirect effects of deforestation.“ In 2023, the company had five active mines, with two bauxite mines each in Australia and Brazil, one coal mine in the United States, and several inactive mines in the process of final rehabilitation and closure in the United States, Australia, and Suriname.
Low-Carbon Aluminum
In the future, innovations will create even more sustainable aluminum. A new low-carbon brand of aluminum has been developed with average emissions from bauxite mining and refining that are less than half of the global industry average. The footprint data on cradle-to-gate carbon is verified by third parties and made available to customers.
Conclusion
When the primary purpose of ladders is noted—functional safety for users—the specification of OSHA-compliant aluminum ladders makes the most sense. Unlike steel, which can rust and corrode when exposed to the elements, aluminum will not rust and is naturally corrosion-resistant. That means the ladder remains safe to use. This lack of corrosion also saves the building owner or operator time and money as the aluminum ladder remains strong and undamaged by weather. The light weight of aluminum ladders has many benefits, particularly for movable ladders. When compared to steel, aluminum has a greater strength-to-weight ratio. In terms of sustainability, aluminum gains points for the metal’s abundance in the earth’s crust, efforts by mining companies to rehabilitate mining sites, and the robust aluminum recycling industry. Finally, aluminum has a sleek, contemporary aesthetic that appeals to users, architects, contractors, and specifiers who increasingly select aluminum ladders for their projects.
Kathy Price-Robinson writes about building and design. Her remodeling series “Pardon Our Dust” ran 12 years in the Los Angeles Times. She specializes in writing about buildings that are durable and resilient to climate disruptions, as well as products and designs that provide shade in hot climates. www.kathyprice.com