This CE Center article is no longer eligible for receiving credits.
While many products are marketed as metal composite materials, a significant number are not actually metal composite materials at all. Metal composite material (MCM) is made from several different components. It is a factory-manufactured panel consisting of metal skins bonded to both faces of a solid plastic core.
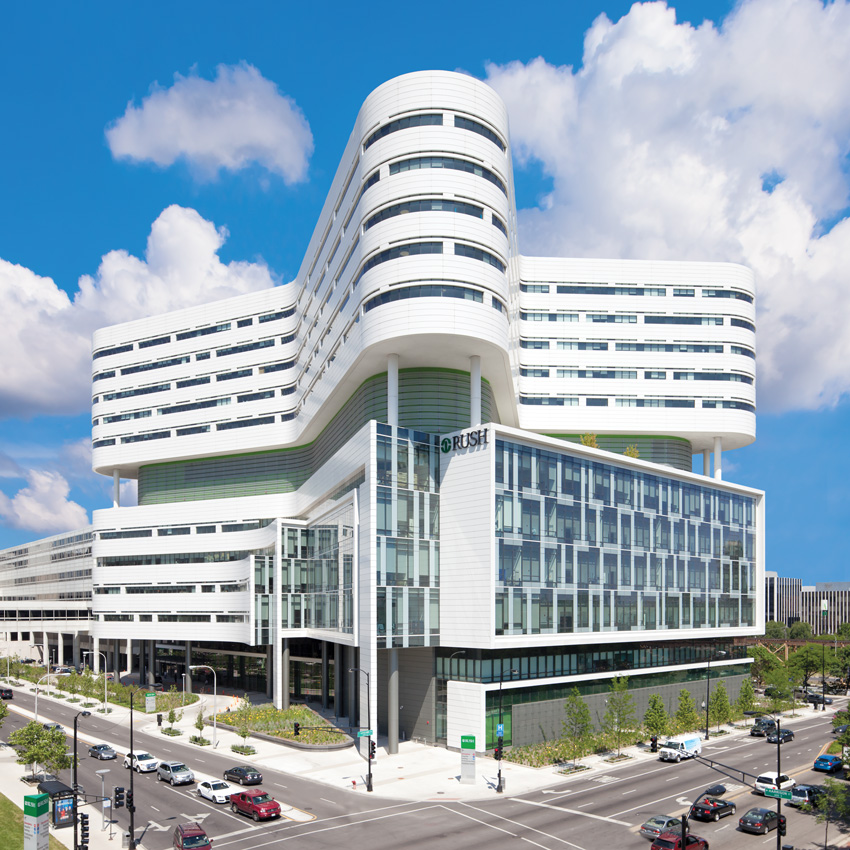
Photo: Robert R. Gigliotti; courtesy of Metal Construction Association
Rush University Medical Center's Tower Hospital in Chicago features a unique and functional exterior facade made of metal composite material, or MCM.
Metal Composite Material (MCM) History and Background
The term metal composite material is a more general and inclusive term than its predecessor, aluminum composite material (ACM).
The first ACM was developed in Europe in 1969. It was not until 1979 that the first ACM was produced in North America. In the early 1980s, there were a number of companies worldwide producing ACM and shipping to North America for architectural projects. By the 1990s, there were several ACM manufacturers producing products in North America. In addition, several other countries around the world were also manufacturing and providing ACM for North American import.
While the name ACM originally referred to products primarily made using aluminum coil, innovations and technological advances led to the use of alternate skin materials, such as copper, zinc, steel, stainless steel, and even titanium. With all these new skin material options, the common name of this material was changed to metal composite material (MCM).
Incorporating additional metals did not only provide more variety in function and cost, but it also provided more options when specifying aesthetically pleasing facades. MCM is often used in exterior cladding or rainscreens to help protect the building envelope from unwanted air and water intrusion. MCM products are available in many colors and finishes, allowing specifiers to provide unique facades while also providing health, safety, and occupant comfort. Today, the number of MCM manufacturers continues to grow worldwide, and the amount of variation in product offerings and quality continues to expand along with it.
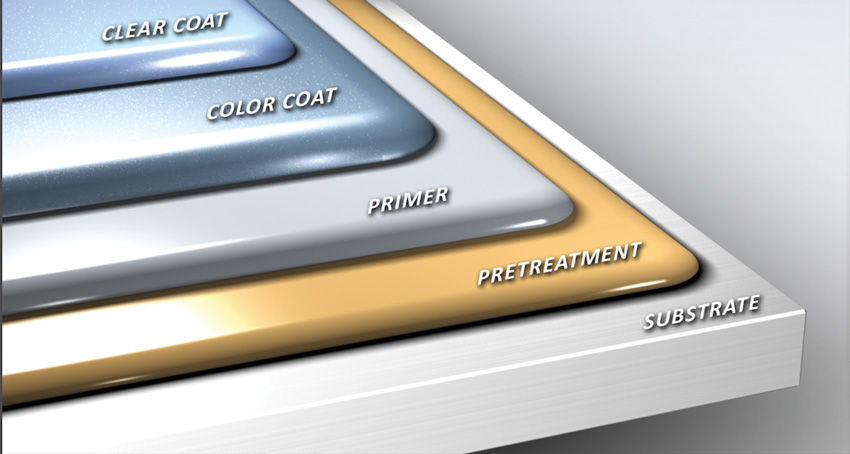
Image courtesy of Metal Construction Association
This illustration shows the layers of an MCM panel.
MCM Materials
MCMs are comprised of “skins” on both sides of the core. Skins often have finishes that enhance the appearance of the facade.
Skins
Skins can be a variety of metals, including stainless steel, zinc, copper, and even titanium just to name a few. Variations in metal, metal thickness, and finish are now much more common than they were just a few years ago.
When specifying materials, one should consider skin thickness first and foremost. A minimum thickness of 0.019 inch (0.5 millimeter) is required as a weather covering by the International Building Code (IBC). This thickness provides an acceptable protection layer for the material that resists normal exposure without significant visual damage.
Skins have three main purposes: to provide a substrate that can be painted or left in its natural state, providing a visually appealing product for a long period of time; to transfer the wind loading from the surface of the panel to the anchorage system; and to play a role in the overall fire performance of the panel.
Together, the panel limits unwanted air and moisture intrusion that impacts the facade performance, causes costly damage to building materials, and affects occupant safety and comfort.
Finishes
The metal skins provide a surface for the application of finishes. These skins will not expand or contract excessively due to temperature and will not negatively impact the finish.
There are many finish options and colors available for aluminum skins. Skins are typically painted with any one of a variety of finishes meeting the performance requirements of American Architectural Manufacturer’s Association (AAMA) 2605. These finishes are available in everything from earth tones with low-gloss finishes to rich, vibrant colors with high-gloss finishes. Other options include finishes imitating wood, marble, granite, and other natural materials. Some finishes also have an additional clear coat added to protect the finishes and enhance the look to be metallic, prismatic, brushed, polished, or anodized.
Other sold metal plates, such as copper, zinc, stainless steel, and titanium, which would otherwise be very expensive for an architectural facade, could also be utilized at a fraction of the cost.
Structural Performance
MCM panels not only provide aesthetically pleasing facades but also protect buildings from the elements. Weather is uncontrollable. From high winds to ice and snow to excessive rainfall, the exterior cladding must protect the building from the overall impact of severe weather. Durability, long-lasting building materials and installation systems that perform over many years are critical for both new construction and retrofit.
Due to the extreme flexibility of MCM panels, with metal skins on both the interior and exterior sides, excessive wind loads generally do not create a permanent problem with the visual appearance of the panels. While the MCM does deflect in high winds, the panel returns back to the flat appearance that was originally fabricated and installed on the building.
To meet certain code requirements, aluminum profiles may be adhered to the backside of the panel using structural adhesive. These profiles limit the deflection of the panel; however, MCM panels have been known to deflect 3 inches or more and return to flat with no permanent negative effect on the panel’s visual appearance. The engineering completed by the panel fabricators determines if stiffener extrusions are required and how the final panels are designed.
Having been in use for more than 50 years, MCM panels have shown resilience to excessive wind load without compromising the high-quality paint finishes or the metal skins used in the manufactured products.
The images above illustrate the tight radius that can be achieved using MCM panels. While there is a maximum limit to how far the finish layer can be stretched without “whitening,” if fabricated correctly, this point of flexure can perform through many years of wind loading.
To form this tight return, the interior skin and a significant thickness of the core material are removed, leaving the exterior skin to act as a hinge and allowing attachment of the panel to the anchor profiles.
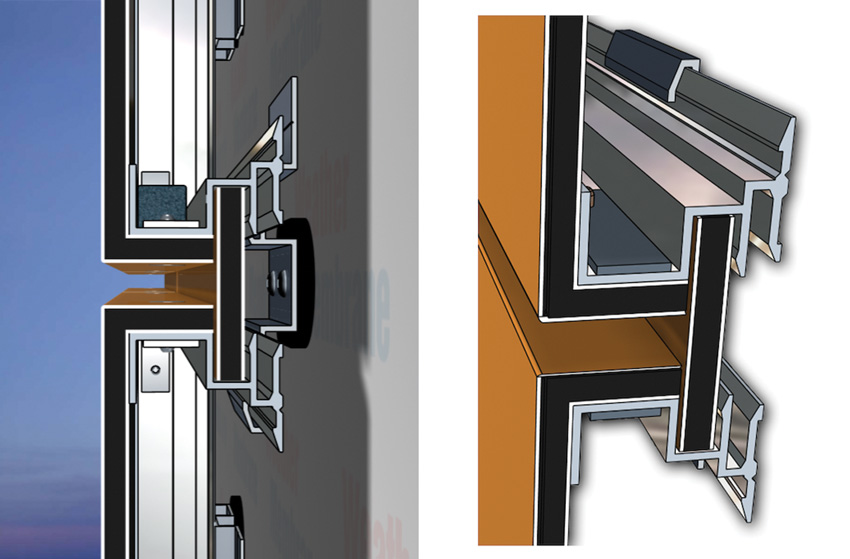
Images courtesy of Metal Construction Association
This illustration shows the back skin and a portion of the MCM core.
While many products are marketed as metal composite materials, a significant number are not actually metal composite materials at all. Metal composite material (MCM) is made from several different components. It is a factory-manufactured panel consisting of metal skins bonded to both faces of a solid plastic core.
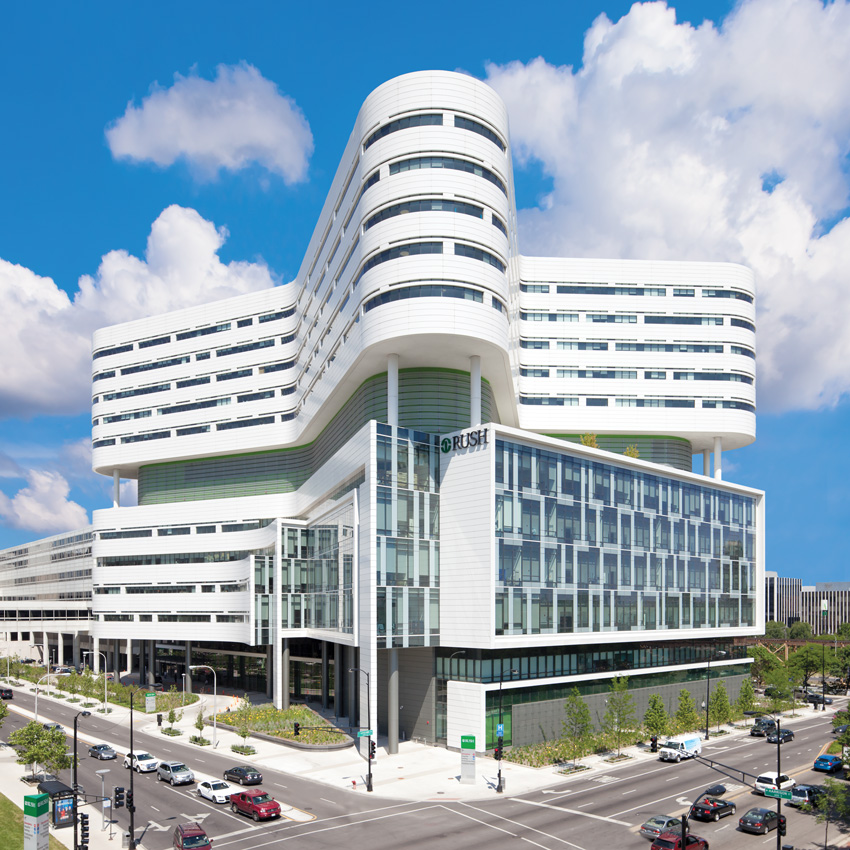
Photo: Robert R. Gigliotti; courtesy of Metal Construction Association
Rush University Medical Center's Tower Hospital in Chicago features a unique and functional exterior facade made of metal composite material, or MCM.
Metal Composite Material (MCM) History and Background
The term metal composite material is a more general and inclusive term than its predecessor, aluminum composite material (ACM).
The first ACM was developed in Europe in 1969. It was not until 1979 that the first ACM was produced in North America. In the early 1980s, there were a number of companies worldwide producing ACM and shipping to North America for architectural projects. By the 1990s, there were several ACM manufacturers producing products in North America. In addition, several other countries around the world were also manufacturing and providing ACM for North American import.
While the name ACM originally referred to products primarily made using aluminum coil, innovations and technological advances led to the use of alternate skin materials, such as copper, zinc, steel, stainless steel, and even titanium. With all these new skin material options, the common name of this material was changed to metal composite material (MCM).
Incorporating additional metals did not only provide more variety in function and cost, but it also provided more options when specifying aesthetically pleasing facades. MCM is often used in exterior cladding or rainscreens to help protect the building envelope from unwanted air and water intrusion. MCM products are available in many colors and finishes, allowing specifiers to provide unique facades while also providing health, safety, and occupant comfort. Today, the number of MCM manufacturers continues to grow worldwide, and the amount of variation in product offerings and quality continues to expand along with it.
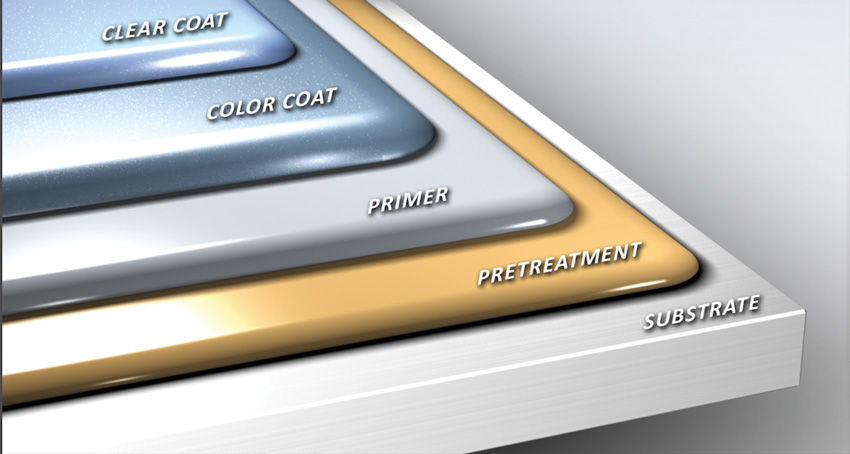
Image courtesy of Metal Construction Association
This illustration shows the layers of an MCM panel.
MCM Materials
MCMs are comprised of “skins” on both sides of the core. Skins often have finishes that enhance the appearance of the facade.
Skins
Skins can be a variety of metals, including stainless steel, zinc, copper, and even titanium just to name a few. Variations in metal, metal thickness, and finish are now much more common than they were just a few years ago.
When specifying materials, one should consider skin thickness first and foremost. A minimum thickness of 0.019 inch (0.5 millimeter) is required as a weather covering by the International Building Code (IBC). This thickness provides an acceptable protection layer for the material that resists normal exposure without significant visual damage.
Skins have three main purposes: to provide a substrate that can be painted or left in its natural state, providing a visually appealing product for a long period of time; to transfer the wind loading from the surface of the panel to the anchorage system; and to play a role in the overall fire performance of the panel.
Together, the panel limits unwanted air and moisture intrusion that impacts the facade performance, causes costly damage to building materials, and affects occupant safety and comfort.
Finishes
The metal skins provide a surface for the application of finishes. These skins will not expand or contract excessively due to temperature and will not negatively impact the finish.
There are many finish options and colors available for aluminum skins. Skins are typically painted with any one of a variety of finishes meeting the performance requirements of American Architectural Manufacturer’s Association (AAMA) 2605. These finishes are available in everything from earth tones with low-gloss finishes to rich, vibrant colors with high-gloss finishes. Other options include finishes imitating wood, marble, granite, and other natural materials. Some finishes also have an additional clear coat added to protect the finishes and enhance the look to be metallic, prismatic, brushed, polished, or anodized.
Other sold metal plates, such as copper, zinc, stainless steel, and titanium, which would otherwise be very expensive for an architectural facade, could also be utilized at a fraction of the cost.
Structural Performance
MCM panels not only provide aesthetically pleasing facades but also protect buildings from the elements. Weather is uncontrollable. From high winds to ice and snow to excessive rainfall, the exterior cladding must protect the building from the overall impact of severe weather. Durability, long-lasting building materials and installation systems that perform over many years are critical for both new construction and retrofit.
Due to the extreme flexibility of MCM panels, with metal skins on both the interior and exterior sides, excessive wind loads generally do not create a permanent problem with the visual appearance of the panels. While the MCM does deflect in high winds, the panel returns back to the flat appearance that was originally fabricated and installed on the building.
To meet certain code requirements, aluminum profiles may be adhered to the backside of the panel using structural adhesive. These profiles limit the deflection of the panel; however, MCM panels have been known to deflect 3 inches or more and return to flat with no permanent negative effect on the panel’s visual appearance. The engineering completed by the panel fabricators determines if stiffener extrusions are required and how the final panels are designed.
Having been in use for more than 50 years, MCM panels have shown resilience to excessive wind load without compromising the high-quality paint finishes or the metal skins used in the manufactured products.
The images above illustrate the tight radius that can be achieved using MCM panels. While there is a maximum limit to how far the finish layer can be stretched without “whitening,” if fabricated correctly, this point of flexure can perform through many years of wind loading.
To form this tight return, the interior skin and a significant thickness of the core material are removed, leaving the exterior skin to act as a hinge and allowing attachment of the panel to the anchor profiles.
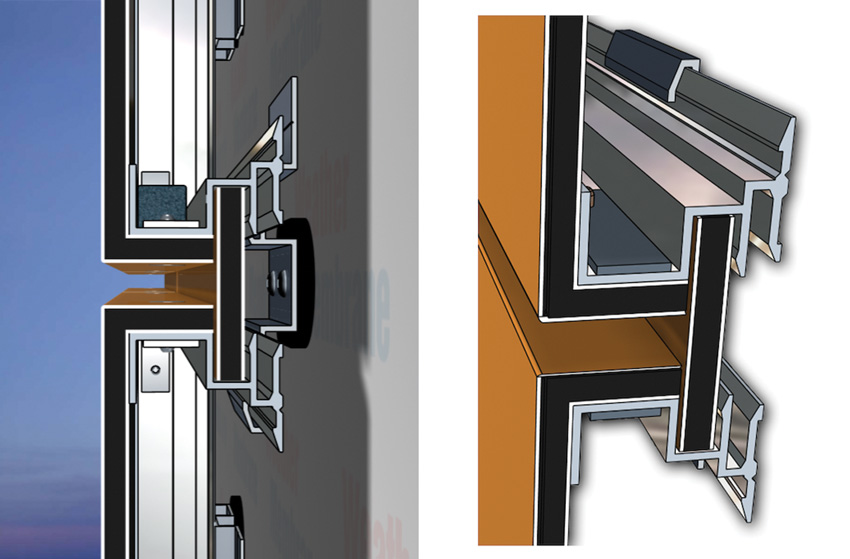
Images courtesy of Metal Construction Association
This illustration shows the back skin and a portion of the MCM core.
Fire Performance
MCM panels are defined as a metal skins bonded to each side of a solid plastic core. This “composite” panel serves a number of functions when the building is exposed to fire. The metal skins deflect the heat and fire away from the combustible core of the panel. While this is not a permanent condition, and the metal skins eventually melt, when the metal skins are in place, the skins serve to limit both the amount of combustible core available to the fire and the spread of flame.
Concern for fire performance of MCM systems is a major issue in today’s construction world. Several high-rise projects around the world have shown significant flame spread of the exterior cladding when an untested assembly is misapplied on a high-rise structure. Many of today’s MCM panels contain fire-retardant chemistry that limits the amount of available fuel and potential for flame spread. In every reported case of high-rise fires around the world, the MCM panel and installation system have not been manufactured with the newer fire-retardant chemistry, and the overall assembly has not been tested to the rigid standards applicable in North America. In the United States, the NFPA 285 multistory test is a benchmark test for the performance of exterior cladding when exposed to fire. The IBC requires that when MCM is used above 40 feet or when foam plastic insulation is a component of the wall assembly, the MCM cladding systems must successfully meet the NFPA 285 test criteria. These code requirements have existed since the 1990s in various code documents and have successfully limited significant high-rise fires.
Simply put, the cladding systems involved in the significant high-rise fires around the world would not be considered code compliant in North America. It is important to note that there have been no high-rise fire experiences in more than
30 years where the MCM panels with fire-resistant core materials have been used in construction. Compliance with the local building codes is critical to the overall performance of MCM systems.
Manufacturing and The Production Process
The MCM production process is fairly basic regardless of where the product is manufactured. Skin material is bonded to both sides of a solid plastic core. The main challenge is that the different materials do not want to stick to each other (and this only gets worse over time). The other issue is that the manufacturer is taking three individual components that want to move in different directions and trying to make them into a single element that will start off completely flat and stay that way when manufactured, after fabrication, and when exposed to changing temperatures and environmental conditions. However, there are some manufacturing variations that can significantly reduce quality and performance if not implemented correctly.
Typically, in a quality manufacturing process, an extruded core material is produced, followed by the application of metal coil. These components are bonded together through the controlled application of heat, pressure, and tension. The metal skin provides structural stability and a medium that can be finished in a number of colors and finish types. The last stage of the production process is controlled cooling of the bonded sheet to maintain the bond integrity and flatness.
While this process may sound simple, many complex interactions are taking place inside the MCM. The semi-soft malleable core is becoming more rigid as it cools between the two metal skins. The skins are generally aluminum and at a high temperature during the bonding process. Controlled cooling is essential as the process continues. Metal has a high expansion rate and contracts as it cools, making the entire assembly susceptible to moving, twisting, and bowing until the completed panel reaches ambient temperature. Without the controlled addition of heat and pressure, the required bond strength is generally not attained. It is this controlled cooling process that creates a flat panel.
This “continuous process” is vital to ensuring consistency in the quality manufactured products. This is why selecting a quality manufacturer is integral to securing the building envelope against the elements and ensuring the building’s longevity.
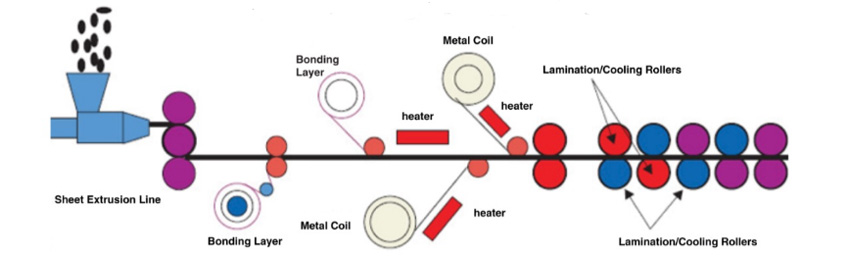
Image courtesy of Metal Construction Association
This illustration shows the typical MCM building panel lamination manufacturing line.
The Fabricator's Systems Approach
The second important element in this process is the fabricator’s MCM system, providing a comprehensive solution to building exteriors and envelopes to not only improve the appearance and performance of the facade, but also prevent unwanted air and water intrusion. Undetected moisture intrusion causes costly and catastrophic damage to underlying building materials. Mold and contaminants can not only damage building materials but also create air-quality concerns that can endanger occupants.
While manufacturers can provide superior MCM products, a comprehensive solution will not be successful without a systems approach that includes fabrication and installation. “MCM is a state-of-the-art building material,” says Tom Seitz, executive director of the Metal Construction Association’s (MCA’s) MCM Alliance. “This article is all about understanding the complete MCM package for quality materials, fabrication, and installation. All three of these factors are important for not only a great-looking MCM project but also a quality engineered architectural facade.”
Now that we understand the manufacturing processes and structural performance benefits of MCM, we will outline ways to not only distinguish the differences between MCM manufacturers and MCM fabricators, but highlight characteristics to look for when selecting each for a project.
Distinguishing Between A Manufacturer and Fabricator
In the industry, the terms MCM manufacturer and MCM fabricator are often confused. There are, however, distinct differences between the two.
The MCM manufacturer is responsible for the process of bonding the skins and core together in a continuous process, creating the flat sheet.
The MCM fabricator is responsible for cutting, routing, folding, and otherwise processing the MCM to fabricate panels to be installed on the building. These fabricators can either have a proprietary installation system using aluminum extrusions or use a third party’s extrusion system.
In the manufacturing, fabrication, and installation process, there are many testing requirements that must be met along the way. Some pertain to the manufacturer, some to the fabricator, and certain tests can only be accomplished by a cooperation and coordination of the two. The manufacturer is responsible for anything related directly to the MCM sheet, including surface finishes and material fire performance. Testing pertaining to wind loads and water penetration generally applies to the fabricator, as the MCM is simply a transfer component moving wind load from one location to another. Some of the more extensive fire testing is a combination of manufacturer and fabricator performance since the MCM is a primary combustible element. The installation system allows the panel to maintain its position and has an impact on the direction of the flames.
Securing a Quality MCM Sheet Manufacturer
There are many MCM manufacturers across the globe, offering varying levels of quality and pricing options. When specifying MCM products, it is important to choose a quality manufacturer to ensure the health, safety, and welfare of occupants while also providing a long life for the building.
As previously discussed, the typical MCM manufacturing process is to extrude or place a core material between two skins of metal with some type of continuous bonding technology to keep the components together. These components are run through a series of heated rolls under a considerable amount of pressure, then each panel is cut to length. Various manufacturers have tried to create composite panels in a batch process; however, consistent visual appearance and bond strength between the core and the skins has generally been a limiting factor in production. Continuous panel production in a controlled factory environment has proven to be the most common practice to ensure a high-quality, consistent panel product. For the best results when specifying a manufacturer, ensure that the materials produced are manufactured using a continuous production process. Manufacturers should provide warranties on the finish quality, bond integrity, and appearance (flatness). Warranties will be discussed in more detail later in this article.
Characteristics of a High-Quality, Tested MCM Sheet Manufacturer
Throughout the manufacturing process, a quality manufacturer must regularly and consistently test the product to ensure that it meets certification requirements, as well as perform quality checks on features pertaining to both performance and appearance. Quality sheet manufacturers provide products and materials that meet a variety of standards, including those released by ASTM, American Architectural Manufacturer’s Association (AAMA), National Fire Protection Association (NFPA), and the International Code Council (ICC).
Look for a manufacturer that meets the performance requirements of the International Code Council Evaluation Service (ICC-ES) Acceptance Criteria (AC) 25 and provides a valid product evaluation report including a third-party inspection agency. It is important to ensure that product performance provides a minimum bond integrity when tested in accordance with ASTM D1781. Other criteria such as continuous core density, panel thickness, and flatness are also important and identified in the manufacturer’s production standards or AC25. When anodized coil is used, the anodizing must meet the requirements of C-22, A-41, Class 1 (per the Aluminum Association), and the aluminum coil quality must meet ASTM B-209.
Due to MCM’s longevity and prevalence in the market, the IBC has dedicated a specific code section (1407) to the requirements for MCM in construction. IBC Section 1407.14 defines labeling requirements that show manufacturing and performance compliance for an installed panel and also serves to ensure future material traceability. IBC 1407.14 refers to Section 1703.5, which requires all materials and/or assemblies to be labeled in accordance with procedures in Section 1703.5.1 through 1703.5.4.
After deciding on a quality manufacturer, next you will need to work with a quality MCM fabricator.
Securing a Quality MCM Fabricator
MCM fabricators design, engineer, and fabricate panel systems meeting the defined project performance requirements in the areas of water penetration and structural performance.
Fabricators are responsible for creating project and shop drawings while also providing engineering calculations showing the adequacy of the panel system design to meet the load requirements, including wind, gravity, and (in certain cases) impact loads. After the material specification phase is complete, the fabricator helps in the determination of material choice, including structural components such as extruded aluminum profiles, fasteners, and engineered clips required to fabricate MCM sheets into cladding panels.
Fabricators are responsible for tests of the cladding systems that include wind-load resistance and water penetration. The fabricator is also heavily involved in fire-performance testing to meet the specification and local code requirements. Warranties for system performance are also provided by the MCM fabricator who is often responsible for the installation.
Characteristics of a Quality MCM Fabricator
Quality fabricators will not only fabricate the MCM, but they will also test and thoroughly engineer all of the systems. When selecting a quality fabricator, confirm that it will provide project shop drawings and engineering calculations stamped by a registered design professional to show the adequacy of the panel system design for the project. Ensure that your fabricator is using materials from quality sheet manufacturers and provides the specified warranties on products as well as installation.
The MCA also has a Certified MCM Fabricator Program through which fabricators maintain their qualifications, ensuring that they are current on the latest codes and technological advances.
Ensuring Quality Installation
The installer, whether the MCM fabricator or an independent project manager, is responsible for safeguarding that each step of the installation process is properly completed. As part of the installation process, MCM fabricators are responsible for the coordination of material deliveries to the job site. They are also responsible for coordinating with individuals and companies from other trades regarding installation of the cladding system, and providing the materials and labor required to provide weathertightness for the designed system.
Final field measurements including framing/substrate tolerances and the “field” fabrication of panel components must be completed on-site. Final project closeout items are typically a joint effort between the MCM installer and the fabricator. The MCM installer typically provides warranties for the workmanship and installation, which we will discuss in more detail later in this article.
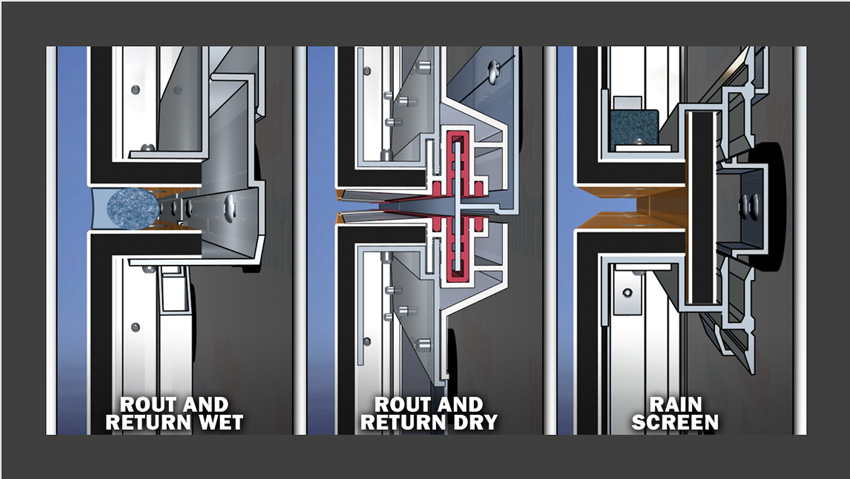
Images courtesy of Metal Construction Association
During installation, panels are routed and fabricated into formed pans with flexible exposed sealant applied at each panel and attached to interlocking or clip extrusions to join, thus minimizing air and water infiltration.
Wet-Seal, Dry-Seal, and Rainscreen Systems
Since MCM products were introduced to North America, installations have been performed using three different styles: wet-seal, dry-seal, and rainscreen systems. These systems have been utilized on many hundreds of different types of buildings. Variations of these systems are still commonly used today. Regardless of the installation system used, the primary goal is to ensure that exterior cladding and/or rainscreens prevent unwanted air and moisture from breeching the building envelope.
All of these systems are required to meet certain performance requirements, which can include air infiltration (ASTM E 283), water resistance (ASTM E 331), structural performance (ASTM E 330), and specific rainscreen requirements identified in AAMA 508 or 509 for these type of systems. All installations where panels are used in excess of 40 feet must meet the fire-protection requirements of NFPA 285.
Wet-Seal System and Testing
The wet-seal system is also known as a “single-line barrier wall” or “fully sealed wall” because there is a joint located between adjacent panels that is fully sealed with sealant. Silicone or a medium modulus sealant are typically used to fill this joint. These sealant types are used because they are flexible and will remain adhered to the panels as they move due to thermal expansion/contraction.
During this installation process, a single barrier is created between the exterior environment and the cavity behind the panel. Panels are routed and fabricated into formed pans and anchored to the substrate using extrusions. The joints are sealed with exposed sealant to minimize air and water infiltration.
The proper installation of sealant and adhesion to the panel is critical to keeping unwanted air and water out of the building. This installation must be inspected regularly to ensure that the sealant remains flexible and adhered to the panel. This is especially important as the exterior envelope ages. While this system is designed to stop water infiltration at the exterior panel surface, any condensation that makes its way into the panel cavity can still cause issues for the building interior and materials. A properly designed and installed panel system should have openings for cavity moisture to exit via weeping or evaporation without entering the building.
No additional testing is required for wet-seal systems other than the aforementioned air-infiltration requirements tested to ASTM E 283, water-resistance requirements tested to ASTM E 331, structural performance requirements tested to ASTM E 330, and fire-performance requirements tested to NFPA 285.
Dry-Seal System and Testing
Dry-seal systems do not use exposed wet components, such as sealants, in the panel joint design. The dry-seal system has a few more components when compared to the wet-seal system. MCM panels are formed into pans and joined with aluminum interlocking extrusions and/or gaskets. The infiltration of water is primarily controlled by the interlocking aluminum extrusions. Just like properly designed wet-seal systems, dry-seal systems allow for any water or condensation that finds its way into the panel cavity to drain or evaporate out before penetrating the building envelope. The type and location of an air/water barrier should not have an impact on the panel performance of a dry-seal system.
Dry-seal systems allow for a panel reveal from 1⁄2 inch to 12 inches. Joints can be finished with color matched or complementary accent strips to provide a sleek, clean, and aesthetically pleasing exterior.
When hiring a fabricator to provide and/or install a dry-seal system, it is important to ensure that it completes the same basic ASTM E283, ASTM E331, and ASTM E330 testing to ensure proper performance.
Raincreen Systems and Testing
Rainscreen encompasses two basic categories of systems: drain/back ventilated (D/BV) and pressure-equalized rainscreen (PER).
Both systems employ open joinery and allow a controlled amount of water into the wall cavity and between the outer and inner leafs. D/BV systems rely on the ventilation cavity to both drain and dry out any residual water.
PERs also employs a ventilation and drainable cavity but add compartmentalization, limiting the amount and duration of a pressure difference between the exterior environment and the air cavity behind the cladding. Compartmentalization of the wall cavity facilitates rapid pressure equalization.
Rainscreen systems allow for a panel reveal from 1⁄2 inch to 12 inches depending on the type of system and the required performance. Joints can be finished with color-matched or complementary accent strips to provide a sleek, clean, and aesthetically pleasing exterior.
The performance of all D/BV and PER systems rely on properly selected, detailed, and installed air/water barrier appropriate for the project’s climate zone. Air/water barrier imperfections introduced into the system test (AAMA 508 and 509) create a worst-case assembly that causes reduced pressure equalization.
As materials change and technological advancements are made, we have a better understanding of how exterior cladding and MCM products perform under loads and in severe weather conditions. These new developments are regularly incorporated into design and manufacturing processes as well as building codes.
Warranty Information
Nearly all MCM products and services come with some type of warranty. Not only are warranties available on the manufacturered products, but oftentimes a separate warranty is available on the work done by the fabricator and the installer. Warranties vary, so it is important to confirm all material and system warranty information with the manufacturer or fabricator prior to specifying and installing materials. Confirm terms other than the length of the warranty, as different finishes warrant different performance.
Because services and warranties vary by each MCM manufacturer, fabricator, and installer, it is important to review all warranty information early in the planning process.
Conclusion
MCM products produced by a quality sheet manufacturer, engineered and fabricated by a quality fabricator, and installed on the building by a quality erector provides superior building protection, a beautiful architectural facade, and a long-lasting building exterior for many years.
Jessica Jarrard is an independent writer and editor focusing on health, science, and technology. She contributes to continuing education courses and publications through Confluence Communications. www.confluencec.com