Architecture Extraordinaire: A Primer on Fabric Structures
Continuing Education
Use the following learning objectives to focus your study while reading this month’s Continuing Education article.
Learning Objectives - After reading this article, you will be able to:
- Explain the benefits of using permanent fabric structures in a variety of outdoor situations to improve the health and safety of the public.
- Discuss the basics of fabrics and membranes as well as their associated components related to the successful design and engineering of fabric structures.
- Compare materials in terms of efficacy in different regions and climates to maximize cost-effective and durable solutions that promote the physical and social well-being of users.
- Describe trends in fabric structures in terms of green building goals.
They can be visually striking, dramatic and distinctive, even seeming to defy gravity with fluid, organic exteriors and light clear-span interiors. They are sustainable solutions with reduced materials and environmental performance, all with the durability of a permanent building or facility. These compelling building types are fabric structures, and while they have been around since the time of primitive man who fashioned simple shelters of animal skins that hung between sticks, today’s versions offer a wide range of sophisticated opportunities for designers interested in doing more with less, while enhancing aesthetic appeal and providing a high-quality user experience. This article will serve as a primer on fabric structures as a sustainable architectural solution, explaining the overall benefits, the various forms and fabrics, and the step-by-step design through implementation process. Also presented will be trends in the industry, as well as profiles of fabric structures in various applications.
Fabric Structures—The Basics and the Benefits
Fabric architecture involves three components: a structural system, a tensioning and/or compression system, and a membrane. A fabric structure is generally characterized by tensioning of a material with wire, cable and/or other hardware incorporated with some type of structural support. Typically, framing and fabric work together under tension and compression, often achieving a strong yet airy look. Fabrics range from coated and laminated products to woven and knitted architectural materials, sometimes with synthetics added to increase durability, strength and ability to stand up to environmental forces. Many fabrics also meet flame retardant and fire code standards. Fabric structures can be temporary or permanent, and they can take on nearly any shape and size. Applications range from a lightweight roof or protective cover for sun or weather protection to canopies, awnings and larger shade structures, all the way up to high-profile, massive projects such as domed stadiums, millennium domes, arenas, band shells, shopping malls and airports. The focus of this article will be on permanent, engineered fabric structures.
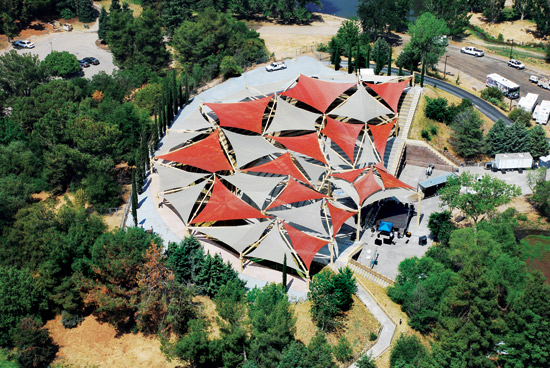
Photo courtesy of Shade Structures, Inc.
Fabric architecture is a striking and sustainable solution for a host of applications.
Benefits of Fabric Structures
Fabric structures offer a host of benefits to architects, to owners, to the public and to the environment.
An Opportunity to Help Prevent Skin Cancer. One of the greatest benefits of simple fabric shade structures is their contribution to human health and wellness by protecting people from harmful exposure to ultraviolet radiation (UV). According to the U.S. Environmental Protection Agency (EPA), in 2007, melanoma, the deadliest form of skin cancer, was diagnosed in an estimated 59,940 individuals in the United States. Melanoma is now one of the most common cancers among adolescents and young adults ages 15-29. While melanoma accounts for about 3 percent of skin cancer cases, it causes more than 75 percent of skin cancer deaths. Ultraviolet (UV) exposure and sunburns, particularly during childhood, are risk factors for melanoma. In fact, one or two blistering sunburns in childhood may double the lifetime risk of developing melanoma. Overexposure to the sun can also lead to other illnesses, including less serious forms of skin cancer which, if left untreated, can cause disfigurement and more serious health problems. Chronic exposure to the sun also causes premature aging, which over time can make the skin become thick, wrinkled and leathery. Research has shown that UV radiation also increases the likelihood of certain cataracts which, although curable with modern eye surgery, diminish the eyesight of millions of Americans and cost billions of dollars in medical care each year. Scientists have also found that overexposure to UV radiation may suppress proper functioning of the body’s immune system and the skin’s natural defenses. While the skin normally mounts a defense against foreign invaders such as cancers and infections, overexposure to UV radiation can weaken the immune system, reducing the skin’s ability to protect against these invaders.
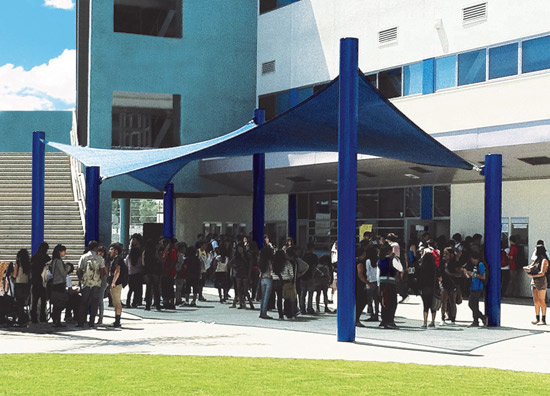
Photo courtesy of Shade Structures, Inc.
A shade structure helps limit exposure to damaging UV rays, which is especially important for children.
Primary prevention strategies for skin cancer include increasing knowledge and awareness in individuals, changing sun-protection behaviors, and implementing policy and environmental interventions. In 2000, the EPA launched SunWise, a program to educate K-8 teachers about the UV-related health effects and the steps for sun protection. Through this program, the EPA estimates that more than 50 premature deaths and 11,000 cases of skin cancer will be prevented, and that every federal dollar invested in SunWise saves $2–$4 in public health costs, such as medical care costs and productivity losses. Many organizations from the Skin Cancer Foundation to the Centers for Disease Control and Prevention recommend ways to limit exposure to UV rays. Prime among them is seeking out shade, especially between the hours of 10 AM and 4 PM, the period during which the sun's rays are usually strongest. The Skin Cancer Foundation urges people to “head under a pavilion roof or leafy tree, or carry a sun umbrella” during this time.
For years, these and countless other organizations have espoused the same sun protection message. Yet despite the high awareness of the connection between skin cancer and exposure to the sun, many people still have not changed their behavior. “Americans are aware of sun dangers, but ignore warnings. According to the National Cancer Institute, skin cancer is the most common cancer in the United States, and its prevalence keeps growing. And despite an abundance of initiatives designed to increase sun protection and early detection, people don't seem to be acting on what they know,” states Dermatology Times.
Still, the facts are clear: Reducing exposure to ultraviolet radiation appears to be the best preventive strategy for skin cancer. In view of this situation, architects are in an ideal position then to make a meaningful contribution to public health as they design outdoor spaces, particularly for children. During summer months and when temperatures are high, conventional playgrounds may become too hot, with some of the equipment even dangerous to touch. Parents’ decisions then about where to take their children to play often hinge on the availability of shade. The addition of a fabric structure to an outdoor space brings welcome—and necessary—shade while shielding participants from harmful UV rays that have the potential to cause life- threatening disease down the line.
Design Freedom. From standard forms to unique custom applications, fabric structures afford architects a myriad of solutions to meet client needs. Probably more than any other building material, fabric expands the potential for design freedom, and it can translate to a distinctive building aesthetic that cannot be achieved with conventional construction materials. Because of their flexibility and formability, fabric structures can be designed in an impressive variety of shapes and configurations for an array of spaces. They also offer architects a cost-effective way to transform an existing space by adding to a design theme or by creating an interesting new focal point for a location that stands out and adds value to the community.
Environmental Performance. Tensioned fabric structures have high sun reflecting properties and absorb less sunlight. These attributes significantly reduce the solar energy and heat that enters a space, while maintaining constant internal temperatures. This makes the space more comfortable for users, more available for use, and extends the life of equipment.
Low Embodied Energy. Compared with brick-and-mortar construction, fabric structures use substantially less raw material, resulting in a much lower carbon footprint. Their transportation requirements are also less than conventional structures, because of the lower initial weight. Though it is one of the lightest-weight building materials, fabric can create structures with the largest building footprints, offering architects and owners an environmentally sound way of designing large-scale facilities. Many fabrics also have post-consumer recyclability. Some components within a tensioned fabric structure, such as the steel cable columns and hardware, can be recycled.
Unobstructed Interiors. Unlike other building types, fabric structures can be designed to require little or no internal support columns or poles. This enables a clear span structure with more usable space and higher ceilings that can be achieved with traditional buildings. The result is a light, spacious interior that is both inviting and practical with fewer supports, allowing long unsupported spans.
Translucency. Fabric structures can allow natural daylight to filter in, reducing the need for artificial lighting, heating and cooling, and the associated energy costs. Coated fabrics have very good UV absorbing and reflection properties. Appropriately coated woven fabrics, for example, allow a light transmission value from 8 percent to 16 percent, offering a very comfortable level of illumination from a natural light source, while providing shade to all users.
Safe Shade Structures. Fabric shade structures protect people and property and are a better option than wood or metal shade systems, because fabrics can be porous, which allows air to pass through, keeping the area beneath much cooler and more comfortable. Specialty fabrics such as high density polyethylene (HDPE) can block out up to 96 percent of the sun’s harmful UV rays and, as they are a mesh material, allow for cool air circulation. Other products simply trap the heat and don’t allow for cool air circulation. Metal structures, for instance, heat up and radiate heat downwards, which creates an oven effect. Wood structures require significant maintenance such as re-painting and/or water sealant treatment on a regular basis.
Durability. Properly designed and built, architectural quality fabric structures have life spans that range from 10 to 25 years or more. They have proven to be weather resistant, and have been successfully deployed in Alaska, the Northwest Territories, Greenland and many countries in the Middle East, as well as many other extreme locations around the world. Fabric structures can be designed and engineered to meet the wind, snow load and seismic conditions particular to the area in which they are to be used.
Reduced Materials. When efficiently designed, the tensile capacity of the fabric itself has the potential to mitigate some of the load requirements, resulting in a significant reduction in the size and quantity of the supporting framework. The “whole system” then works to mitigate some of the tension load requirements. This in turn leads to a much more lightweight and less costly structure than other types of construction. Even in instances where sizable foundations are required, often times there are fewer costs than are associated with conventional construction materials.
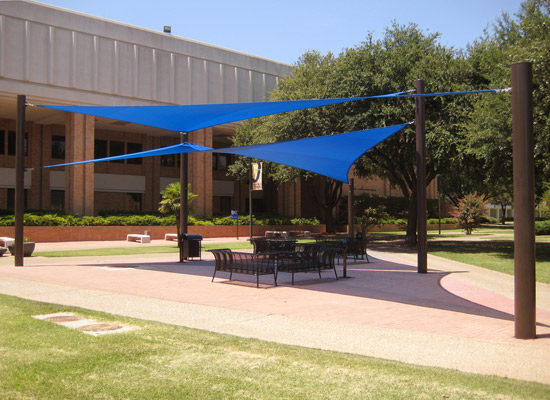
Photo courtesy of Shade Structures, Inc.
A fabric structure can create an outdoor room.
Community Value. A fabric structure can transform an ordinary space into a stylish outdoor room, and with correct illumination, it can ratchet up the visual appeal of the location during nighttime hours. These unique and distinctive structures serve to increase community pride and can be a magnet for tourism and commercial investment.
Revenue Enhancement. Increased appeal means increased usage, which translates to more revenue to owners. Fabric structures also play a part in revenue enhancement. Locations such as water parks will often rent areas with permanent shade structures for special events such as birthday parties, corporate events, school retreats and more, which results in bottom line benefits. Incorporating fabric structures into locations like outdoor amphitheater locations and other civic spaces can lead to revenue-generating opportunities such as special events, concerts and other performances. Fabric-covered venues can gain income from year-round activities via rental and cover charges.
Contribution to LEED Points. The goal of being sustainable is to make places and products, and to offer services in a way that reduces the use of non-renewable resources, minimizes environmental impact and respects the natural environment. One of the leading ways to measure sustainability is the U.S. Green Building Council’s Leadership in Energy and Environmental Design (LEED) rating system. While LEED has undergone several iterations over its lifespan, the basic categories in which credits can be earned have remained constant. Fabric structures have the potential to earn LEED points in the following categories: Heat Island Effect (examples: roof top shade, covered parking); Energy and Atmosphere (examples: renewable energy credits for fabrics with integrated photovoltaics); Sustainable Sites; Materials and Resources (examples: use of recycled materials); Indoor Environmental Quality; and Innovation in Design (examples: use of PV design, water collection, adaptability/design excellence).
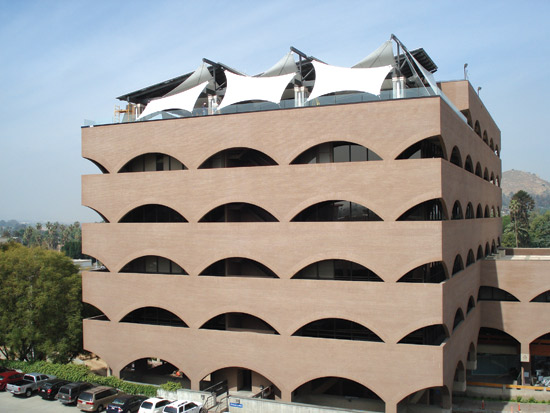
Photo courtesy of Shade Structures, Inc.
Fabric architecture can contribute to LEED points in several categories, including Heat Island Effect.
Common Types of Fabric Structures
Fabric structures can either be custom designed or pre-engineered, depending on the needs of the project. Pre-engineered structures offer the benefits of standard forms and quick turnaround times, making them less costly than their custom-designed counterparts. But whether pre-engineered or custom designed, fabric structures typically take the following basic shapes and configurations.
Mast Supported. These structures are tent-like in form, characterized by one or several peaks supported by central poles and perimeter cables. They typically use a compression ring or “bale” ring and have traditional conical shape.
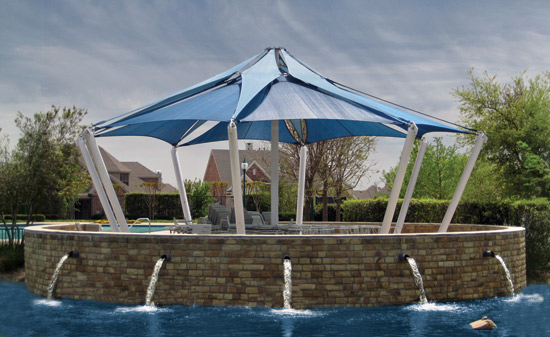
Photo courtesy of Shade Structures, Inc.
Mast-supported structures are a common type of pre-engineered structure.
Point Supported. In these structures, a clear span avoids a center mast. This type of form uses an exterior frame or series of peripheral masts and utilizes high and low points to create a series of ridge and valleys.
Arch Supported. A curved compression member supports the membrane in these structures, which are often visually dramatic. Cross arches are often used. In this case, the fabric is often not taking its natural shape, but rather conforming to the lines of the curved steel members.
Simple Saddle. Often resembling a bird poised to take flight, these structures have a double curvature created by two high points and two low points. Their saddle shape can be either horizontal or vertical.
Tensioned Awnings. This is an awning with minimal framing, held in place by lateral forces. It can be a self-supporting or a hybrid structure. A variety of edge details are available.
Architectural Fabric Structures: The Design Process
Designing and building a fabric structure should involve close collaboration among the owner, the designer, the engineer, the manufacturer and the contractor, and should include the input of all parties at the earliest possible stage. Successful fabric architecture requires a strong beginning platform of thoughtful design and qualified engineering that meets intentions for longevity and permanence, in addition to building code requirements and industry standards. Multiple factors must be considered at the outset, including integration of the fabric structure with the site location and the project orientation, as well as its interaction with other site activities and functions. The selection of all professional parties should be carefully considered, and it is advisable to choose a turnkey (designer/manufacturer/supplier) provider: with a long, proven track record of expertise and qualified experience with permanent structures; that provides ongoing customer support; that has facilities that meet current industry standards; and that provides quality products that are certified by organizations such as IAS (International Accreditation Service); and that has an experienced maintenance and service department.
It is important to note that architectural fabric structures are the marriage of engineering and architecture and rely on the “engineer’s aesthetic” to determine the size and shape of structural components. Designers and engineers look at the project holistically and consider an extensive array of criteria, including form, function, economy, material, production, transport and maintenance. The main stages involved in the realization of a typical fabric architecture project are outlined below.
Conceptualization. A fabric structure begins with an idea, which will determine its form, and its plan, elevations and sections. The idea can be as simple or as intricate as desired.
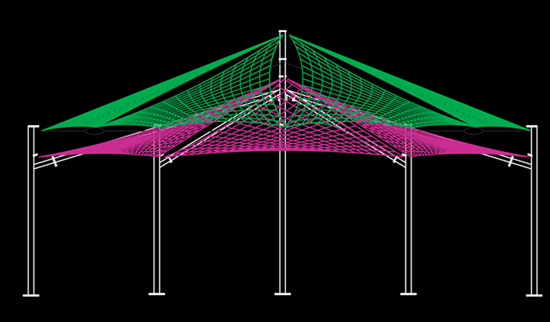
Image courtesy Shade Structures, Inc.
The fabric structure begins with an idea, which will determine its form.
Visualization. But what will the structure actually look like? A typical CAD program will not be able to properly “shape” fabric. Rather, sophisticated 3D/CAD rendering and animation software enables clients to better understand the fundamentals of shape, form and function of the desired fabric structure, with a 3D version of a concept suitable for construction. Animation in CAD format can represent the actual final product and is the starting point for converting the concept into reality. Physical models, in which material is stretched over wire frames, allow designers and clients to “get inside” the structure, and are often used for presentations and fund raising.
Geometry and Structural Analysis. The CAD model is imported into specialty non-linear engineering software which enables analysis that will determine if the structure is stable, whether the membrane is shaped correctly, and if it is over-stressed or in a position to pond. Further, it can provide sufficient information on the sizing and weight of the elements for an accurate cost estimate. Once the required centerline geometry of the structure has been determined, it is modeled in 3D using highly specialized software to define a final equilibrium shape that meets the requirements of the client. The equilibrium shape is then analyzed under various loading conditions to determine the steel, cable and fabric requirements.
Membrane Engineering. The fabric requirements are carefully engineered in terms of seam layout and membrane details.
Biaxial Testing. This is a test where a small sample of fabric from the roll being utilized for a specific project is tested to ensure it has the assumed industry standard tensile properties.
Compensation Factor. Typically, architectural membranes elongate less than 1 percent over the life of the fabric. When the fabric is received for production, it is in a relaxed state. At this point, loads are applied in specialty software to determine the amount the fabric will “creep” from a relaxed into a tension state. This compensation factor is applied during the cutting of the fabric to the desired shape.
Membrane and Hardware Details. The engineering and analysis process also includes determining the type, size, capacity etc., of components that will be utilized in fabric structures where they connect to a structural element such as columns or buildings. These membrane details can include items such as fabric corner reinforcements, perimeter cable pockets or cuffs, membrane plates, turnbuckles, clamping and cables, etc.
“Nesting” Panels. Fabric comes in rolls of certain widths. In order to arrange the patterns in the most efficient way and to avoid unnecessary fabric waste, nesting is necessary. This is a process in which the designed fabric patterns are superimposed on pieces that represent the fabric roll, and the size and orientation are manipulated to achieve the best layout possible.
Patterning. The fabric shape is then patterned. Patterning is the art of representing three-dimensional shapes by connecting a series of flat, two-dimensional templates into one fabric assembly. The size and shape of the panels are determined by engineers using specialized software, and then provided to fabricators who cut and assemble the fabric. Selected to meet the specific project requirements, fabrics have varying degrees of translucency, light reflectivity, UV and weather protection, and non-combustibility. Certain fabrics offer self-cleaning surfaces and all are easily maintained to preserve their appearance and ensure a long life. Strong, durable seams applicable to the individual fabric are critical, and include heat sealing, radio frequency (RF) sealing and sewn seams utilizing heavy-duty thread, depending on the membrane selected for the structure. Advanced computer controlled cutting technology provides precision load analysis and tight tolerances.
Fabrication of Membrane/Fabric, Attachment Components and Structural Supports. Based on fabrication drawings, material is purchased, actually fabricated and packaged for delivery to the site.
At this point, steel shop drawings should be completed by steel fabricators and reviewed by a project engineer and/or designer prior to commencing the actual manufacturing of the steel components. Some of the more complex projects require installation engineering and input before the construction process begins, and may include things such as specialized hydraulic tensioning components, rigging design and sequencing plans. Steel fabrication should be certified by the International Accreditation Service (IAS) board as meeting, or exceeding, the highest standards in the steel fabrication industry. Some steel plants are equipped with state-of-the-art machinery, including robotic welding, computerized roll benders, custom swagers, massive sand blast booths and powder coat ovens and booths, with highly specialized tools and equipment used to cut raw steel and fabricate plates.
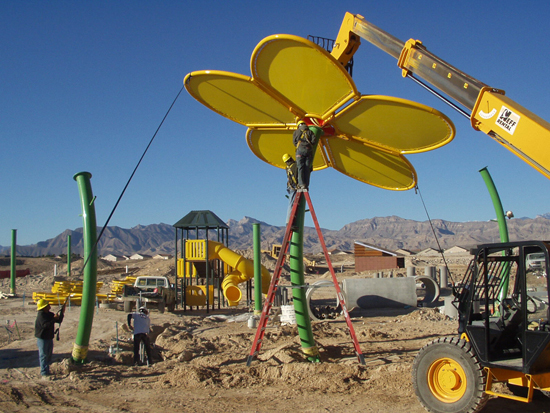
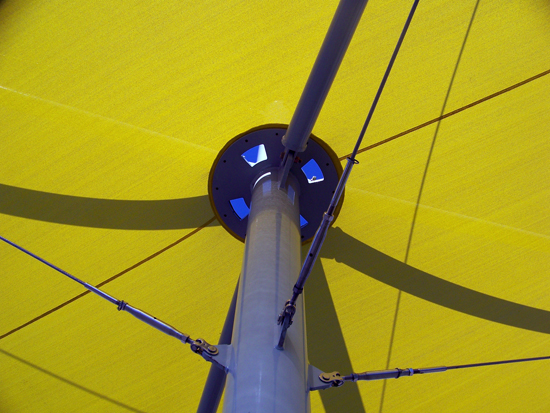
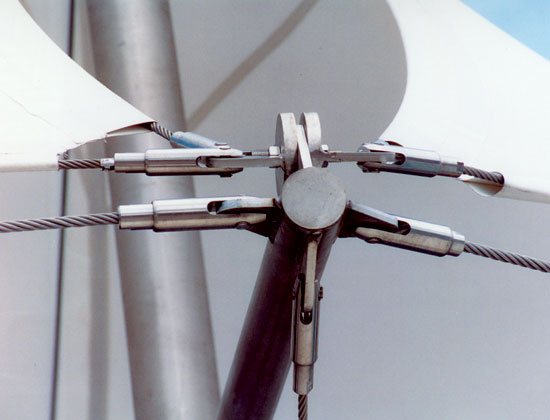
Photos courtesy of Shade Structures, Inc.
The proper components and details are critical to the successful installation of a fabric structure.
Load requirements will help determine the type of details and components that are required for support, and whether they are off-the-shelf or custom made. The forms are derived from the bridge building and yacht racing industries, making them both ultra strong and light weight. Several basic forms come into play with fabric structures. A base plate serves as a connection to the ground, wall or the adjacent structural system. It is welded to the bottom of a compression member. Mast or arch structures will require cleats, tabs and gussets, along with struts and bale rings for maximum stability. It is important to note that the membrane plate is one of the most critical components to design and produce. It is the link from the membrane to the structural support and is used to accept the membrane catenary cables.
Permitting. Ease of obtaining a permit will depend on the city and county in which the structure must be installed. Most cities do require a building permit for the shade structures. Quality fabric structures should be fully engineered to meet or exceed the local building code requirements. Typically the turnkey provider will assist in obtaining the necessary documents to obtain a permit.
Installation. The complexity of the installation depends on the intricacy of the structure and a number of other issues. Some fabric structures do not require permanent foundations and need minimal site preparation. That said, installation is a very important part of the process and essential to the service life and functionality of the fabric structure. The erection procedure must be considered and often takes into consideration site surveys, site preparation, reports on soils and water tables, and weather conditions, particularly wind gusts. Generally they are designed and engineered to meet the wind load requirements of the area in which they are to be used, which normally range from 90 to 125 mph.
Site and soil conditions will determine the foundation configuration. Spread footers are used where the soil is unstable and more support is necessary, such as in areas of high water tables, sugar sand, coral rock, or where a soils analysis indicates other unfavorable conditions. Generally, “uplift” governs the load values of fabric structures. By using a pier foundation, the soil friction values can help reduce its size. Spread footings are constructed of concrete and often reinforced with rebar or steel for additional support. Because of their size, they require additional concrete, rebar and dirt removal, and thus spread footings are generally more expensive than other types of foundations.
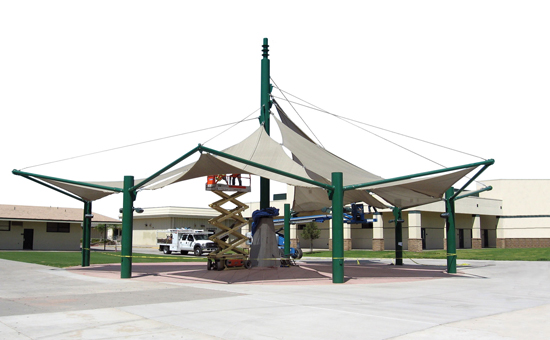
Photos courtesy of Shade Structures, Inc.
The complexity of the installation depends on the intricacy of the fabric structure.
Proper mounting types must also be considered. In a direct embed situation, there will be a surface mount and/or a recessed base plate. If these elements are used, anchor bolts are required.
It is also advisable to have a plan for unloading materials, installation and tensioning in order to minimize delays and potential problems on site.
All this being said, with the many facets and integrated details of a tensile fabric structure, and in order to maximize results and help assure a successful project, an experienced and qualified design-build tension fabric company should be involved in the project from the onset of conceptual design, and should continue to be involved throughout the entire process, including final installation.
Fabric Choices—Finding the Right Material
Architects may want to review the options in terms of several environmental parameters including natural ventilation, reduction in direct sunlight, heat loss or gain, admittance of natural light and contribution to LEED credits. Often the choice of fabric will be climate dependent. For example, in a mixed and hot humid climate, the appropriate approach would encompass rain protection, passive cooling, shading, ventilation, day lighting and reduced heat gain. In snow areas, the slope and snow load of the structure must be considered.
Generally speaking, architectural fabrics have a woven substrate that is finished with a coated material. This substrate is what gives fabric its tensile strength. Following are the most popular fabrics on the market today.
Teflon coated fiberglass (PTFE). This product is a woven fiberglass substrate, and is used for large-scale permanent structures with a required life span of more than 25 years. The Teflon coated material comes to the site as buff in color but bleaches to a milky white over time by exposure to UV rays, typically four to eight weeks. The biggest drawback of the Teflon coated material is its stiffness; the material is brittle and must be handled very carefully to avoid breaking the fibers. Advantages include its longevity, self-cleaning attributes and fire rating. In most states, permanent, totally enclosed structures require “non-combustible” or Class A ratings according to building codes. The most recognized and accepted material used for architectural application is Teflon coated fiberglass or PTFE.
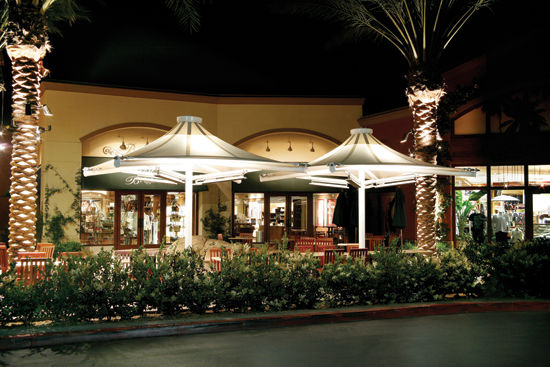
Photo courtesy of Shade Structures, Inc.
PTFE fabrics are used for permanent structures requiring long life spans.
It is critical to note that many factors can dramatically influence a project’s pricing, including economies of scale, accessibility, site conditions, equipment requirements and engineering requirements, to name a few. Hence the following costs are presented for general consideration relative to the listed fabrics and for reference only, and should NOT be used for project-specific budgeting without an experienced industry professional. The stated range is based on the fabric area rather than the plan area. PTFE pricing can average between $85 and $165 per square foot.
Ethylene tetrafluoroethylene (ETFE). This ultra-high transparency material (97 percent) has a life span of more than 25 years. While this is considered an architectural fabric, there is no woven substrate, thus giving it such a high translucency factor. The elimination of the substrate also comparatively reduces its tensile strength. It is self-cleaning and 100 percent recyclable, and can be deployed in single or multiple layers. ETFE is not really a fabric, but is a film presently promoted as an alternative to glass. It is “green” friendly and is considered to be the hot new architectural fabric internationally. ETFE fabrics have been used or are being specified in high-profile mega projects worldwide, including the FIFA stadiums in Germany, the Olympic venues in China, governmental buildings in Washington, D.C., and have become the preferred choice in creating enclosures for artificial rainforest and water parks in colder climates. ETFE pricing can average between $125 and $185 per square foot.
Vinyl coated polyester (PVC/PVDF). Of all the shade fabrics, PVC/PVDF is the most common material used on the market today. It is suitable for both temporary and permanent structures. The woven substrate material is polyester, which makes it soft, pliable and easy to handle, and is available in a variety of colors, weights, topcoats and textures. PVC with a PVDF topcoat has a typical life span of more than 20 years and is fire resistant (Class C, NFPA 701). The majority of fabric structures being considered today are for uses which do not require complete enclosure— that is, they are most likely “open air” or do not require a Class A rating. Class C is the most common rating and NFPA 701 is the most accepted certificate for most fire marshals. PVC/PVDF pricing can average between $65 and $120 per square foot.
High density polyethylene (HDPE). Today, more and more fabric structures are being designed for shade only, with structural mesh fabrics being specified as the preferred membrane. The material most often used is high density polyethylene (HDPE) mesh. This fabric is a shade fabric, which does not have a woven substrate. It provides up to 84 percent shade, 92 percent UV Protection, and approximately 85 percent water run-off, depending on shape, and has a life expectancy of 12 to 15 years. This UV stable fabric comes in a variety of styles, colors and shade factors. It has a high tensile strength and can be fire-resistant if required. Well suited for dry/hot climates, the HDPE cloth also offers protection from sun and hail and is relatively inexpensive. HDPE pricing can average between $18 and $60 per square foot.
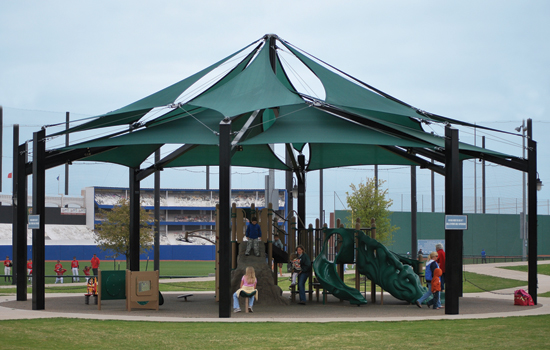
Photo courtesy of Shade Structures, Inc.
HDPE is an UV stable fabric that offers protection from the weather.
The Next Generation of Fabric Architecture—Some Trends
The fabric architecture industry is one that is constantly innovating to create more options with ever greater sustainability, aesthetic appeal and functionality. Custom colors, textures and patterns are being used for multipurpose structures, and strides have been made in using fabric to produce energy. Currently, photovoltaic film can be applied to fabric to harness power from the sun. In the next generation for photovoltaic application in the fabric architecture industry, designers will be developing the capacity for tensile strength fabrics to have PV “receptors” woven directly into the fabric, while still maintaining its tensile strength. Or, PV films will be developed to meet tensile strength qualities and requirements.
Building with Fabric: Architecture for the Future
While fabric structures have been around since the cave man, they hold enormous potential for future applications. Architects would do well to educate their clients on the benefits of these striking, sustainable forms. With attributes such as low energy requirements, high environmental performance, low costs and high design capability, fabric structures embody those parameters that green builders desire and that green rating systems reward. Of utmost importance is the potential contribution of fabric structures to human health and well being. In terms of providing shade in outdoor spaces, fabric structures constitute a key asset in preventing harmful effects of the sun, particularly on children. As materials become more advanced, and as the structures themselves more multi-functional, fabric architecture will realize its fullest potential to the benefit of architects, users, owners, and the environment.
![]() |
USA Shade |