Cost Efficiency and Budgeting with Extruded Aluminum Trim
Thoughtful selection and investment in materials can yield positive results when specifying for multifamily housing
Continuing Education
Use the following learning objectives to focus your study while reading this month’s Continuing Education article.
Learning Objectives - After reading this article, you will be able to:
- Describe the process of life cycle cost analysis and how it can be used to guide design choices for long-term value.
- Explain why investing in higher-quality and durable extruded aluminum will reap financial benefits for building owners and occupants over the duration of the building.
- Discuss the various types of coatings and finishes available on extruded aluminum trim and how each type can impact cost, durability, and overall project goals.
- Describe the inherent characteristics of aluminum that can help promote sustainable design and successful integration with green building programs.
Material performance and sustainability are two top requirements in modern architectural design. Whether we’re talking about the overall design or individual interior and exterior material selections, choosing durable, long-lasting products and systems that support human and environmental health will pay dividends across the lifetime of the project.
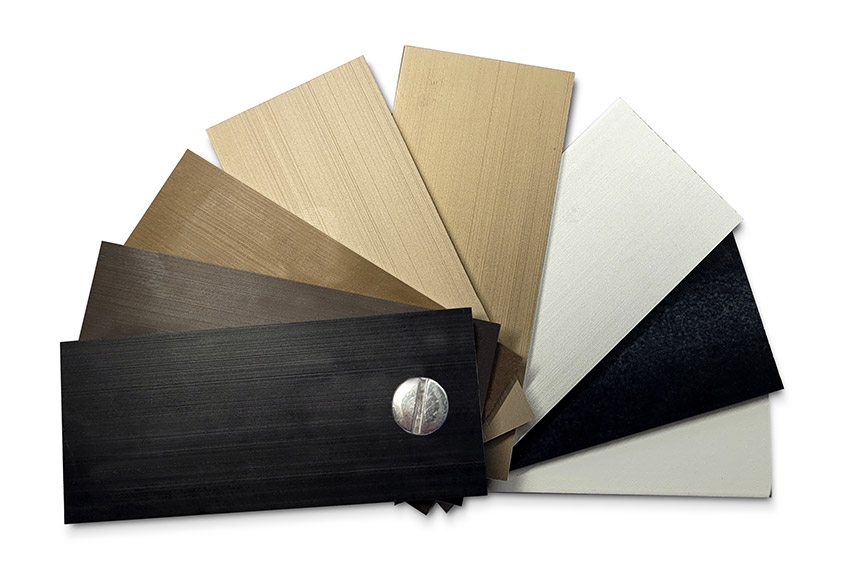
Photo courtesy of Tamlyn
Examples of different metallic color options in an anodized finish.
Trim is a key design choice that contributes significantly to the aesthetics of multifamily buildings. Although there are many options available, extruded aluminum rises to the top. Not only does aluminum have the design flexibility to enhance just about any project, but it is also a sustainable and durable material. Its performance characteristics make it a practical and affordable choice for both exteriors and interiors, especially when you compare the full lifetime cost of extruded aluminum to other materials. In this course, we will compare the performance and sustainability of extruded aluminum trim to other options, focusing on the long-term value that this material choice brings to multifamily projects. We will also explore how to use Life Cycle Cost Analysis to compare various trim options, and we will explore the pros and cons of various coatings and finishing options.
TODAY’S MULTIFAMILY BUILDINGS: A GENERATION APART
The multifamily building market includes an aging stock of poorly designed (and even more poorly finished) multifamily units, most built in the 1970s and 1980s. This unfortunate legacy is the consequence of a mindset focused on short-term gain: how many units can be crammed on a given site for as little as possible?
Today’s multifamily building sector is no longer a race to the bottom, and both owner and occupant expectations are higher. Retirees, millennials, and Gen-Zers don’t mind a smaller square footage of living space, but they are also looking for more amenities and shared community spaces, and they are drawn to mixed-use projects, with shopping or workspace located conveniently on site. They are also concerned with sustainability and are much more aware of the health impacts of their surrounding environment than generations before. And of course, aesthetics matter, too, with clean, modern lines and high-quality materials appealing to these tech-savvy residents.
In this course, we will discover why extruded aluminum trim, whether used in the interior or exterior, contributes to the long-term value of multifamily projects. First, let’s take a closer look at the total costs of ownership, and the critical role of the life cycle cost of key material choices.
Pay Now or Pay Later
It’s important to understand that the construction costs of a multifamily building represent a fraction of the total cost of owning it over the long term. Over time, operation, repairs, staff salaries, replacement or upgrades to materials and systems, utilities, and the cost of disposal and recycling eclipse the initial cost of construction. And that’s not including costs that are typically out of the owner’s control, such as property taxes and interest payments.
The same is true of specific building systems or finish materials: their initial, or first cost, is just the beginning. There are several categories of costs to consider over the lifetime of ownership of these materials, including the initial cost to acquire and install them, operation costs, maintenance and repair, replacement, and disposal or recycling. {{question1}}
It likely makes intuitive sense that some design choices will have a greater impact on certain costs of ownership. The selection of HVAC systems and windows, for example, will significantly affect how much energy the building uses. It is also not surprising that some choices with a lower initial price tag cost more in the long run. Take flooring—an important consideration for multifamily projects. Cheap carpeting may not cost much up-front, but it will likely need replacing every three to five years, and it requires frequent maintenance such as steam cleaning. In contrast, a durable, stain-resistant flooring product may outlast the carpet several times over, and require less maintenance, to boot.
There is a strong relationship between sustainability and long-term value. A building system that requires less maintenance and that lasts longer doesn’t just save money, but valuable resources, too.
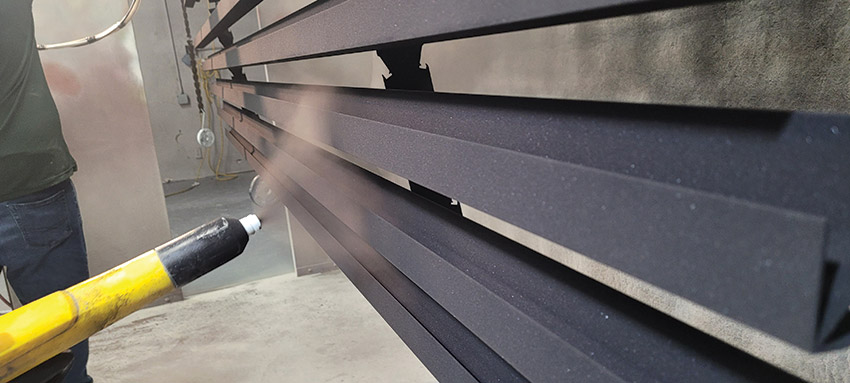
Photo courtesy of Tamlyn
The first layer of powder coat is applied to the extruded aluminum trim profile in a black-gloss finish.
What Is Life Cycle Cost Analysis?
Life Cycle Cost Analysis, or LCCA, is a tool that allows you to calculate the full cost of ownership and to compare one building material or system to another.
Here is a simple formula for calculating life cycle costs:
LCC = C + O + M + D
Where C = Construction, or the initial cost of acquiring the product or system
O = operational costs
M = Maintenance costs, including regular and periodic maintenance, repairs, and replacement
D = the costs associated with disposal or recycling
Before conducting an LCCA, you will have to work with the project owner to determine the appropriate life span of ownership—20 or 30 years, for example.
Some building components, such as lighting and heating systems, for example, come with obvious operational costs, since they require energy to operate. Others, such as trim and cladding, do not. However, the maintenance costs for these materials can be quite high, especially if the material requires full replacement during the ownership life cycle. Notably, maintenance refers to routine tasks, such as cleaning, to periodic maintenance, such as a deep cleaning, touch-up painting, or minor repairs.
Disposal and recycling costs will vary depending on the type of material and available recycling facilities.
Don’t worry if you can’t pinpoint every cost down to the dime; the goal is to calculate a reasonable estimate of the life cycle costs of products and materials so you can adequately compare them. Spreadsheet software can help, as can online tools such as One Click LCA.
It is strongly recommended that project teams address life cycle costs early in the design process, before major decisions have been made. Conducting a Life Cycle Cost Analysis early on, whether for an entire building or a specific system, such as a trim package, can yield several benefits:
- It can guide the design to ensure long-term value.
- It can provide the project owner with better estimates of the total costs of ownership.
- It can reveal hidden costs, such as costly maintenance.
- It can ensure sustainable choices by encouraging the owner to think about the long-term impacts of design options.
Now, let’s take a closer look at extruded aluminum trim and how it contributes to long-term value of multifamily projects.
THE ATTRIBUTES OF EXTRUDED ALUMINUM
Aluminum is one of the most specified materials in the residential and commercial buildings construction industry, and no wonder: it’s durable, stiff yet flexible, strong but light, impermeable, and resistant to bugs, rot, and wear. It is also noncombustible and non-toxic and can be endlessly recycled; in fact, recycling rates for aluminum used in the building industry exceed 90 percent.
The most abundant mineral in the earth's crust, aluminum is derived from bauxite, which is mined from the earth. After processing, the resultant alumina undergoes a smelting and alloying process that produces solid logs of cast metal, known as billets, from which extruded aluminum shapes or profiles are made.
Aluminum trim products are made by extruding aluminum alloy through dies to create distinctive profiles. Most extruded shapes for architectural use are fabricated from AA 6063, an aluminum alloy containing magnesium and silicon. Type 6063-T5 Aluminum, commonly referred to as the architectural alloy, has a very smooth surface and is the best alloy suited for anodizing applications. The T5 designation indicates it has been artificially aged and moderately heat-treated; this process is what gives the aluminum its rigidity. Extruded trim products are protected from rust by an oxide film that naturally forms during the extrusion process.
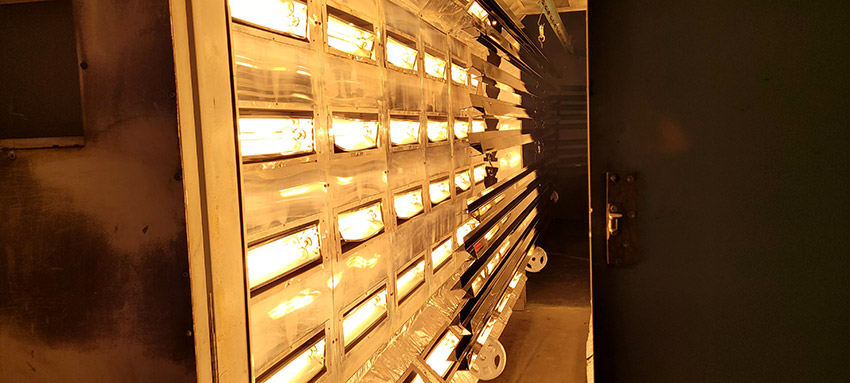
Photo courtesy of Tamlyn
As the final stage of the powder coating process, the oven is where the powder itself will integrate with the aluminum substrate, which will provide a highly durable, long-lasting finish.
Comparing Extruded Aluminum with Other Trim Options
Extruded aluminum trim can work with many common cladding types, including fiber cement panels, lap siding, and even tongue and groove cedar. It is manufactured to integrate with and complement most major siding products, and it can be used on both exteriors and interiors.
Extruded aluminum has several advantages over other common trim options. Aesthetically, it matches the clean, modern look of many contemporary projects, and it can be used strategically to break up flat panel walls with large expanses of cladding, or to add distinctive profiles to corners.
When it comes to durability, extruded aluminum has greater longevity than materials like galvanized steel and polyvinyl chloride (PVC). Thinking about the Life Cycle Cost Analysis framework introduced earlier, let’s compare extruded aluminum with two common trim alternatives.
Galvanized steel has a lower first cost than extruded aluminum, but it is less durable. In addition, installing bare mill galvanized steel and aluminum flashing in direct contact with most claddings will increase the chances of a chemical reaction, which can cause wear and breakdown in both products. Maintenance costs, including potential replacement or major repairs, will likely be higher for galvanized steel than for extruded aluminum, leading to a higher total life cycle cost for the trim or cladding package. And in the meantime, before repair or replacement, the exterior with galvanized trim may show noticeable signs of the damage, reducing the visual appeal of the building.
Polyvinyl chloride, or PVC, is the least expensive trim option; however, it has some drawbacks and limitations. For one, all-vinyl trim is susceptible to swelling and buckling when exposed to direct sunlight. Painting it with dark colors, which are increasingly popular with both architects and developers, may cause the product to warp. PVC absorbs heat, and in hot climates, the trim may experience extreme expansion and contraction, causing it to warp. Over time, paint may blister and peel.
As you have likely concluded, PVC is a classic case of a product with low first cost but a high life cycle cost. Maintenance is likely to be costly, and the product will have to be replaced long before an alternative like extruded aluminum. In fact, one manufacturer, which used to produce PVC trim profiles for fiber cement siding and soffits, has converted these profiles into more durable extruded aluminum. {{question3}}
Moisture Management for Long-Term Value
Water intrusion is a leading cause of damage or deterioration in buildings and can compromise the long-term durability of building components. For this reason, building codes have strict requirements for managing moisture. The joints where trim panels meet, transition points between different materials, and the joints around windows and other openings, are especially vulnerable points of entry for water. Just as they make trim products to integrate specifically with popular cladding options, most trim manufacturers also offer or recommend code-compliant moisture management products that will work best with their products.
Section 1403.2 of the ICC lays out the performance requirements for exterior walls:
1403.2 Weather protection.
Exterior walls shall provide the building with a weather-resistant exterior wall envelope. The exterior wall envelope shall include flashing, as described in Section 1405.4. The exterior wall envelope shall be designed and constructed in such a manner as to prevent the accumulation of water within the wall assembly by providing a water-resistive barrier behind the exterior veneer, as described in Section 1404.2, and a means for draining water that enters the assembly to the exterior. Protection against condensation in the exterior wall assembly shall be provided in accordance with Section 1405.3.
There are two common strategies for mitigating moisture in the building envelope: housewraps and rainscreens. Housewraps that integrate drainage by, for example, including small spacers that separate the cladding from the sheathing, thereby allowing moisture to drain. Such housewraps don’t require any alterations to the exterior building design or add steps to the installation. A rainscreen is an assembly that includes a water-resistive barrier and an element that creates air space immediately behind the cladding. The air space reduces the chances for moisture intrusion through the cladding and ensures that any moisture that does penetrate can drain out before penetrating further. {{question4}}
Extruded Aluminum Trim for Interiors
Typically, walls and ceilings in multifamily projects are finished with drywall and paint, or with some other type of affordable panelized product. Trim is used as baseboard, openings, and transitions between walls and ceilings, or between two material types. It can also be used to house lighting or to mitigate noise. Conventional choices for interior trim are wood (or an engineered wood product such as MDF) and vinyl; however, extruded aluminum can also be used for interior trim applications, and it can enhance multifamily projects by introducing high design to drywall and panelized surfaces at a fraction of the cost of custom designed and fabricated metalwork.
In addition to introducing clean, modern design to interiors, projects benefit from aluminum’s performance benefits and sustainability characteristics. Because of the frequent turnover of occupants, multifamily interiors are subject to more wear and tear than single-family homes; most damage typically occurs when residents are moving in and out, as furniture and other large items ding corners, damage baseboards, and puncture drywall. Repairing or replacing damaged surfaces can be expensive; however, such damage must be addressed to maintain the building’s quality and visual appeal. Here, extruded aluminum shines. This durable material holds up to the challenges of daily use and long-term wear and keeps units and common areas looking fresh and clean.
Thinking again about life cycle costs, extruded aluminum trim will create long-term value for multifamily projects, as it requires less maintenance and will last longer than other trim choices. It is also easy to recycle, which is not the case for vinyl. And as we shall see in the section on sustainability and occupant health, extruded aluminum is also the best choice for both indoor environmental quality and for minimizing the whole life-cycle health and environmental impacts of the project.
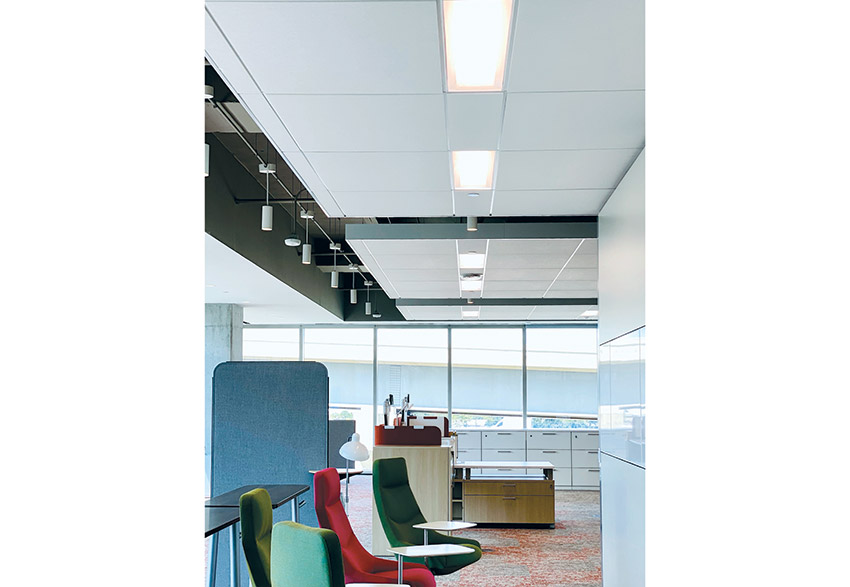
Photo courtesy of Tamlyn
Extruded aluminum is an ideal choice for both indoor environmental quality and for minimizing the whole life cycle health and environmental impacts of the project.
{{question6}}
ALUMINUM PLUS COATINGS FOR ENHANCED PERFORMANCE
As the previous section detailed, the inherent physical attributes of aluminum make it the ideal choice when specifying trim packages for multifamily projects. In particular, its strength and durability are enhanced by the extrusion process, which creates an oxide film on the surface that naturally prevents corrosion. These benefits can be expanded even further when coatings and finishes are included in the speci47fication process.
There are several coatings and finishes available for extruded aluminum trim, including powder coatings, liquid paints, and anodized finishes. It is critical that architects understand and convey to project owners how these coatings can impact the aesthetics, performance, durability, and cost of the extruded aluminum trim. Let’s take a closer look at each of these.
Powder Coatings
Powder coating is a dry finishing process that is used in many industrial applications. Powder coating is a popular choice for finishing extruded aluminum trim, and for good reason: the process creates a high-quality finish that’s resistant to scratching, chipping, corrosion, and fading. It’s also available in a plethora of color options. A basic understanding of the powder coating process reveals why it results in such a resilient finish.
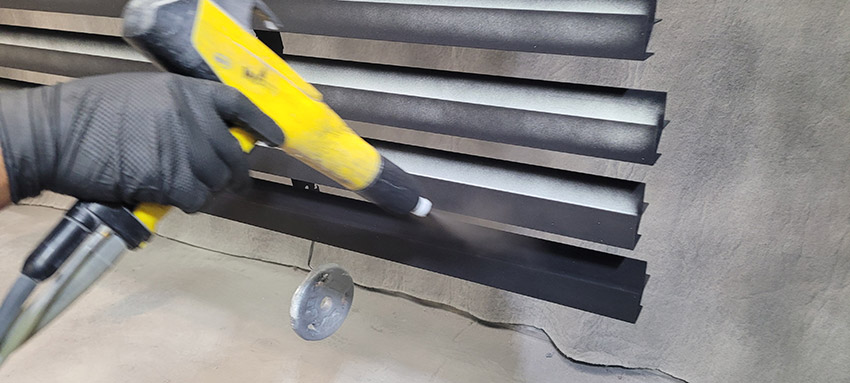
Photo courtesy of Tamlyn
Another angle of the first layer of powder being applied to the profile before eventually being tossed in the oven to cure.
Powder coatings start with a polymer resin blended with curatives, pigments, leveling agents, modifiers, and other additives. These ingredients are melted together, mixed, cooled, and ground into a powder which is applied to the aluminum substrate using a spray gun—a process called electrostatic spray deposition. (Alternatively, powder coatings may be applied using a fluidized bed application. Here, preheated parts are dipped in a hopper of fluidizing powder, and the coating melts and flows over the substrate.) As the substrate is heat cured, the coating chemically reacts with the aluminum, creating long and strong molecular chains that are very difficult to break down. The resulting coating is more durable than liquid paints, which can degrade as they are exposed to weather, temperature extremes, and UV light.
Then there are the aesthetics. Not only are a plethora of color options possible, but coatings that start with high-quality powder tend to be remarkably consistent. It’s easy to match colors, and recent technological advances have enabled new looks, such as matte and chrome finishes. {{question7}}
Liquid Paint
Ever popular and familiar, liquid paint is available in more colors than just about any other finish option. Several types are appropriate for use on extruded aluminum, including acrylics, polyesters, silicone polyesters, and PVDF. Because liquid paint can be custom-mixed for each job, however large or small, it offers great flexibility; however, it does have a few key drawbacks when compared to powder coating. The first concerns its sustainability and environmental health. Some liquid paints contain volatile organic compounds, or VOCs, which have been shown to harm human health and the environment. The paint is typically spray-applied, and some of the product inevitably goes to waste. In addition, a painted finish may not be as consistent as a powder-coated finish.
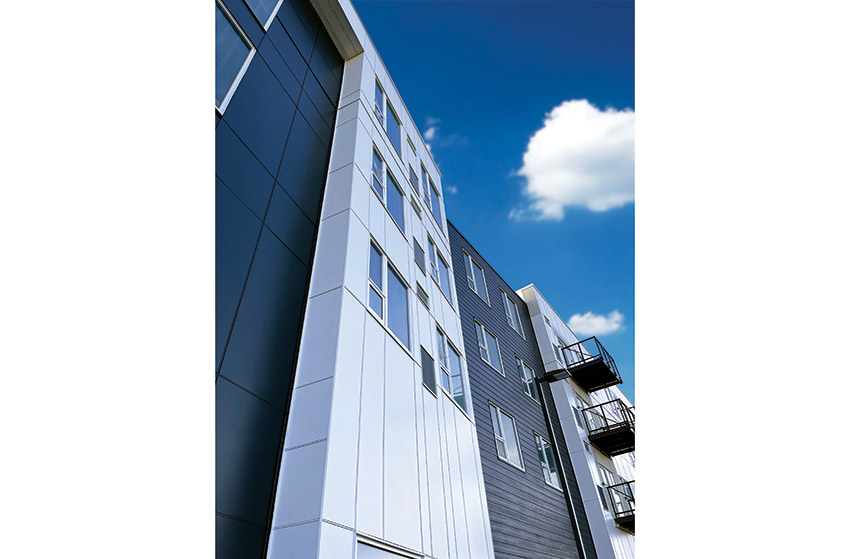
Photo courtesy of Tamlyn
Liquid paint can be custom-mixed for each job and offers great flexibility in final finish.
Anodized Finishes
Anodizing is a controlled electrochemical process that deposits an oxide film on the surface of the aluminum trim. The resulting finish is decorative, durable, and more corrosion resistant than the untreated substrate. The process is accomplished by dipping aluminum into an acid electrolyte bath and passing an electric current through the medium. The process allows aluminum oxide to fully integrate into the substrate of the product. Although anodizing helps guard against corrosion, it does not increase the strength of the aluminum itself.
Anodizing creates a shiny, dynamic surface with an undeniably modern aesthetic. It is available in a clear finish or limited color selection such as bronze, gold, and black. Note that trim with an anodized finish may vary slightly from piece to piece; a design utilizing such trim should account for this natural variation.
The anodizing process creates a more porous surface that can receive paint; in fact, when color is applied, the dyes are locked into the substrate and will not peel or fade when exposed to sunlight.
Some companies have started to skip the traditional anodizing process and are instead opting for a powder coating that imparts an anodized sheen. The coating is available in several popular colors, including dark bronze, medium bronze, light bronze, gold, and black. Powder coating is faster and less involved than anodizing; it is also ideal for smaller projects since it can accommodate smaller batches than anodizing.
SUSTAINABLE FROM START TO FINISH
Aluminum is naturally sustainable. Thanks to aluminum’s inherent strength and durability, products made from this material will last decades before they need to be replaced and recycled. Because it is so lightweight, it is also less expensive to transport than other architectural metals.
Aluminum does not off-gas, and manufacturing or recycling it does not create hazardous waste. It is a good material choice for project teams seeking to achieve LEED or WELL certification, or to meet the stringent requirements of the Living Building Challenge (LBC), as it does not appear on the Red List, an inventory of “worst-in-class” materials, chemicals, and elements known to pose serious risks to both human health and the environment.
Aluminum is the only material that more than pays for the cost of its own collection. It is a completely recyclable material that does not degrade with reuse. Once the material is produced, it can be recycled indefinitely. In fact, approximately 75 percent of all aluminum ever produced is still in use today. This is especially significant when you consider the carbon emissions required to manufacture new aluminum. Recycled aluminum saves more than 90 percent of the energy costs needed for primary production, and it generates just 8 percent of the emissions.
The consequences of aluminum recycling are profound, saving not just energy and greenhouse gases, but other resources, too. Every year aluminum recycling saves approximately 70 million barrels of crude oil, 45 million tons of fresh and sea water, 7.5 million tons of solid waste, and 27 million tons of CO2.
The Benefits of Sustainable Buildings
Extruded aluminum trim products can help support sustainable building goals and can help projects achieve certification under several popular green building programs. Increasingly, green buildings are becoming the norm in new construction. This is thanks in part to ever more stringent building codes, but also because of leadership at the federal, state, and local level. The US government, for example, had mandated that all new federal building be net-zero energy by 2045. The state of California has required new state buildings to be built to LEED standards since 2004, and Massachusetts recently mandated that large non-residential buildings achieve net-zero energy by 2035.
More and more project owners are realizing that “green” buildings come with a multitude of benefits: they save money over the long term, as they use much less energy than conventional buildings. As we learned earlier, they also save resources and money by promoting products, materials and systems with long-term value, which don’t require as much maintenance and don’t have to be replaced as often. These buildings also promote the health and well-being of occupants—a chief concern for multifamily project owners, as residents who are happy in their dwelling units are likely to stay longer. Green buildings are also likely to be more resilient, which means they buffer occupants from extreme weather and temperatures, and are more likely to remain functional during disasters.
In fact, sustainable features can give multifamily projects a competitive edge, especially among younger residents, who increasingly value health and wellness, and who are deeply concerned about climate change and environmental degradation. Certification under one or more green building programs can signal to potential residents that a multifamily project was designed and built in an environmentally responsible way, and that the units are healthy, comfortable, and energy efficient. In addition, more multifamily real estate investors are adopting environmental, social, and governance criteria for their investments, in part because green buildings yield better returns.
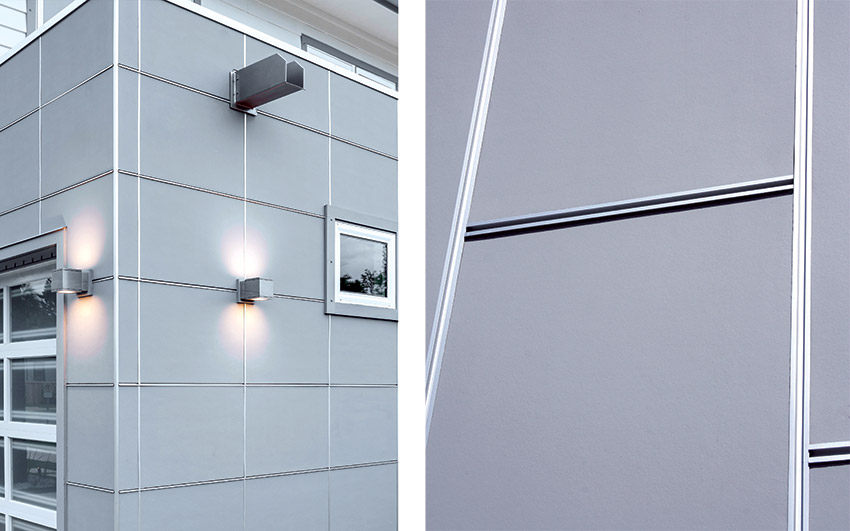
Photo courtesy of Tamlyn
Anodizing creates a shiny, dynamic surface with an undeniably modern aesthetic. It is available in a clear finish or limited color selection such as bronze, gold, and black. The close-up image on the right shows the finished texture which helps lock in the dyes into the substrate for enhanced durability when exposed to sunlight.
Green Building Programs and Standards
There are several green building standards and programs in use today, and they have become increasingly aligned with each other. The US Department of Energy and the US Environmental Protection Agency jointly manage the ENERGY STAR program, which focuses on energy performance, while the US EPA’s Indoor AirPLUS program promotes healthier indoor environments. The more ambitious Zero Energy Ready Homes program, which now has a multifamily pathway, builds upon the foundation of other federal programs and requires that projects meet both ENERGY STAR and Indoor AirPLUS standards as a baseline.
LEED, which stands for Leadership in Energy and Environmental Design, is the world's most widely used green building rating system. LEED is a points-based rating system; projects can earn credits across eight categories: carbon, energy, water, waste, transportation, materials, health and indoor environmental quality. LEED provides a framework for healthy, highly efficient, and cost-saving green buildings; with each iteration, it has become more holistic and comprehensive. The newest iteration of the standard, LEED v5, addresses “critical imperatives” such as equity, health, ecosystems, and resilience.
The WELL Building Standard is “a vehicle for buildings and organizations to deliver more thoughtful and intentional spaces that enhance human health and well-being.” WELL v2 includes evidence-based design strategies and operational protocols aimed at promoting human health. Drawing on expertise from a diverse community of users, practitioners, public health professionals and building scientists, the standard utilizes a points-based rating system organized around 10 “Concepts”: Air, Water, Nourishment, Light, Movement, Thermal Comfort, Sound, Materials, Mind and Community. The Living Building Challenge is a rigorous green building standard hosted by the International living Future Institute. It is comprised of 20 Imperatives organized under seven Petals: Place, Water, Energy, Health & Happiness, Materials, Beauty, and Equity. The Challenge does not utilize a point system; rather, project teams may choose how to best achieve the requirements of each Imperative for their particular projects.
{{question9}}LEED Credits
Extruded aluminum trim, whether used on the interior, exterior, or both, can contribute to LEED credits. LEED v4 takes a whole life cycle approach to credits, and requirements cover the performance of materials as a whole rather than assessing the performance of individual products or brands. As a consequence, specific products or materials like extruded aluminum trim can only contribute toward earning LEED certification points; they cannot earn points individually themselves.
Here are the specific credits to which extruded aluminum trim products can likely contribute:
Materials and Resources - Building product disclosure and optimization - environmental product declarations (up to 2 points)
The intent of this credit is “to encourage the use of products and materials for which life-cycle information is available and that have environmentally, economically, and socially preferable life cycle impacts”; and to “reward project teams for selecting products from manufacturers who have verified improved environmental life cycle impacts.”
Option 1. environmental product declaration (EPD) (1 point)
Use at least 20 different permanently installed products sourced from at least five different manufacturers that meet one of the disclosure criteria below.
- Product-specific declaration.
- Products with a publicly available, critically reviewed life cycle assessment conforming to ISO 14044 that have at least a cradle to gate scope are valued as one quarter (1/4) of a product for the purposes of credit achievement calculation.
- Environmental product declarations which conform to ISO 14025 and EN 15804 or ISO 21930 and have at least a cradle to gate scope.
- Industry-wide (generic) EPD Products with third-party certification (Type III), including external verification, in which the manufacturer is explicitly recognized as a participant by the program operator are valued as one half (1/2) of a product for purposes of credit achievement calculation.
- Product-specific Type III EPD Products with third-party certification (Type III), including external verification in which the manufacturer is explicitly recognized as the participant by the program operator are valued as one whole product for purposes of credit achievement calculation.
- USGBC approved program – Products that comply with other USGBC approved environmental product declaration frameworks.
Materials and Resources - Building product disclosure and optimization - sourcing of raw materials (up to 2 points)
The intent of this credit is “to encourage the use of products and materials for which life cycle information is available and that have environmentally, economically, and socially preferable life cycle impacts”; and to “reward project teams for selecting products verified to have been extracted or sourced in a responsible manner.”
Option 2. leadership extraction practices (1 point)
Use products that meet at least one of the responsible extraction criteria below for at least 25%, by cost, of the total value of permanently installed building products in the project.
- Recycled content. Recycled content is the sum of postconsumer recycled content plus one-half the preconsumer recycled content, based on cost. Products meeting recycled content criteria are valued at 100% of their cost for the purposes of credit achievement calculation.
Materials and Resources - Building product disclosure and optimization - material ingredients (up to 2 points)
The intent of this credit is “to encourage the use of products and materials for which life cycle information is available and that have environmentally, economically, and socially preferable life cycle impacts”; and to reward manufacturers who produce products with verified improved life cycle impacts and project teams for selecting such products.
Option 1. material ingredient reporting (1 point)
Use at least 20 different permanently installed products from at least five different manufacturers that use any of the following programs to demonstrate the chemical inventory of the product to at least 0.1% (1000 ppm).
- Manufacturer Inventory. The manufacturer has published complete content inventory for the product following these guidelines:
- Health Product Declaration. The end use product has a published, complete Health Product Declaration with full disclosure of known hazards in compliance with the Health Product Declaration open Standard.
- Cradle to Cradle. The end use product has been certified at the Cradle to Cradle v2 Basic level or Cradle to Cradle v3 Bronze level.
- Declare. The Declare product label must indicate that all ingredients have been evaluated and disclosed down to 1000 ppm.
- ANSI/BIFMA e3 Furniture Sustainability Standard. The documentation from the assessor or scorecard from BIFMA must demonstrate the product earned at least 3 points under 7.5.1.3 Advanced Level in e3-2014 or 3 points under 7.4.1.3 Advanced Level in e3-2012.
- Cradle to Cradle Material Health Certificate. The product has been certified at the Bronze level or higher and at least 90% of materials are assessed by weight.
- Product Lens Certification
- Facts - NSF/ANSI 336: Sustainability Assessment for Commercial Furnishings Fabric at any certification level
- USGBC approved program. Other USGBC approved programs meeting the material ingredient reporting criteria.
CONCLUSION
The multifamily housing market has never been more competitive, and expectations have never been higher. Developers and owners who commit to providing healthy, sustainable, long-lasting dwellings will not only enjoy a competitive edge and attract investors committed to ESG principles, they will reap financial rewards by creating long-term value.
Extruded aluminum trim can help impart a desirable aesthetic to both interiors and exteriors of today’s multifamily buildings, while at the same time supporting sustainability goals and contributing to the long-term value of the project. Long-lasting, durable, and 100 percent recyclable, extruded aluminum trim holds up to a life cycle cost analysis and comes out ahead of other common alternatives such as PVC.
From shiny, modern anodized finishes to a rainbow of power coating choices, durable, visually appealing coatings can be used to affordably achieve design goals and make multifamily projects stand out.
When specified for interiors, extruded aluminum trim can be used to meet the challenges particular to multifamily projects, including high turnover rates and every-day wear and tear that comes with having occupied dwelling units. At the same time, these products can contribute to healthy indoor environments and help attract Millennial and Gen-Z residents, who care deeply about health, well-being, and environmental responsibility.
Extruded aluminum products can help achieve the goals of popular green building programs, including LEED, signaling a commitment to sustainability and creating buildings that will stand the test of time. {{question10}}
Juliet Grable is an independent writer and editor focusing on building science, resilient design, and environmental sustainability. She contributes to continuing education courses and publications through Confluence Communications. www.confluencec.com