Multi-Family, Mid-Rise Wood Buildings A Code-Compliant, Cost-Effective and Sustainable Choice
A code-compliant, cost-effective, and sustainable choice
Continuing Education
Use the following learning objectives to focus your study while reading this month’s Continuing Education article.
Learning Objectives - After reading this article, you will be able to:
- Identify the sustainability and economic benefits of using wood construction for mid-rise multi-family or mixed-use buildings.
- Summarize building code requirements and provisions for mid-rise multi-family wood-frame structures.
- Discuss wood framing solutions that address issues such as shrinkage, fire protection and seismic requirements while minimizing the carbon footprint of the building.
- Explore innovations in wood framing design techniques and wood product technologies that enhance energy efficiency.
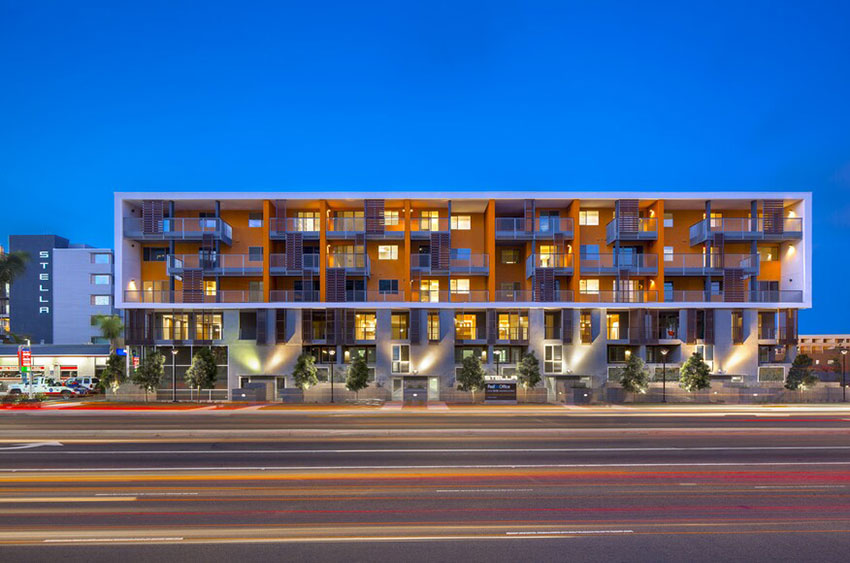
Photo courtesy of Lawrence Anderson Photography
Demand for multifamily housing continues to play an important role in the overall U.S. construction market. The National Multifamily Housing Council estimates that more than 325,000 new apartment homes are needed each year to meet demand.1 Multifamily projects include apartments and condominiums as well as other residential uses like affordable housing, student housing, senior living, hotels and motels, and vacation timeshare properties.
One of the most fundamental decisions facing a multifamily design team is choosing the building’s structural material. While dominant in single-family residential construction, the cost-effective, code-compliant, and sustainable attributes of wood construction apply to mid-rise, multifamily projects, too. This CEU explores the reasons for the increasing popularity of wood in multifamily buildings, reviews code compliance and fire safety technical considerations, and discusses techniques for successful wood building designs. In addition, it addresses trends expanding the opportunities for wood use in multistory design.
Why Wood?
Developers and design professionals are increasingly recognizing the benefits of wood construction as an effective way to build high quality multifamily housing at a lower cost while reducing the carbon footprint of their projects.
Cost Savings, Increased ROI
Building professionals often find wood-frame structures to be more economical, for reasons including speed of construction and lower material costs. Since wood is lighter weight than other structural materials like concrete or steel, a wood structure may have lower foundation costs.2 Cost of wood construction can also be lowered by using prefabricated components and assemblies, which speed installation.
After completing the first phase of a five-story student housing project at Illinois State University using steel construction, OKW Architects in Chicago switched to wood for the remaining phases. “Because the structure had so many openings, the metal studs for the first building, Flats on Main, needed to be 12-gauge, but they were heavy and it was difficult for the crews to screw and attach our finishes. So, the contractor encouraged us to switch to wood bearing walls for Flats on Osage, the second building. As a result, it ended up being a more economical project,” said OKW’s Eileen Schoeb.3
1430 Q, a multifamily, mixed-use development in Sacramento, California, is another example of how wood was used to improve the return on investment for a mid-rise project. The developer collaborated with WoodWorks and a code consultant to file an Alternate Means and Methods Request (AMMR) with the City of Sacramento, which gave its approval for six and a half stories of wood, including the top-level mezzanine, over a two-story podium. This allowed more tenants and more lease income from the one- and two-bedroom apartment complex. It also allows the developer to realize premium rents for the top floor view units. When it was completed, 1430 Q was the first residential building in the U.S. to be constructed using a 6.5-over-2 building configuration and the country’s tallest light-framed wood building.
Code-Compliant, Marketable Structures
Design professionals familiar with wood construction for two-to-four-story residential structures may not be aware that the Table 504.4 of the 2021 International Building Code (IBC), Allowable Number of Stories Above Grade Plane, allows up to five stories of Type III wood-frame construction for residential occupancies and six stories for business occupancies. Type V buildings have a maximum of four stories.
Designers can also use concrete podiums under wood-frame construction to add additional stories. Table 510.2 limits the height above grade to the most restrictive building’s normal height, though additional stories can be fit within that height-above-grade restriction. For instance, a Type VA of a 1-A podium can have two stories of 1-A plus four stories of VA as long as the VA building does not exceed 70 feet above grade (sprinklered), its normal height-in-feet limit.
Since the 2009 edition, the one-story limit for the 1-A lower building was removed but the upper building still cannot exceed height above grade for its construction type, as noted above. This means developers can build four or five stories of wood over a single- or double-level podium (which would be referred to as a 4-over-1 or a 5-over-2).
Mahlum Architects worked with engineers at Coughlin Porter Lundeen to design five buildings of student housing for the University of Washington. They made the most of the urban campus location in Seattle, designing each of the buildings with five stories of light-frame Type V-A wood construction over a two-story Type I-A concrete podium. This approach helped them meet code requirements, ambitious design goals and the university’s tight budget. The 668,800-square-foot project, completed in 2011 and 2012, was constructed for $177 per square foot.4
Building codes are meant to be material neutral, which means that mid-rise wood-frame buildings are required to meet all the same safety and performance requirements as a similar building made from any other material. With the assurance that wood meets code, building owners and designers often use wood because of its cost benefits. Wood buildings can usually be constructed more quickly, which helps developers increase the return on their investment through earlier completion. Wood’s versatility, sustainability, and aesthetic attributes help make it a desirable choice for many design teams.
Sustainability
Wood construction offers advantages for project teams seeking green building certification or simply interested in reducing the environmental impact of their buildings. Wood grows naturally and is renewable, and life cycle assessment studies show that wood offers environmental advantages in terms of embodied energy, air pollution, water pollution, and other impact indicators.5
From a carbon footprint perspective, wood continues to store carbon absorbed during the tree’s growing cycle, keeping it out of the atmosphere for the lifetime of the building—or longer if the wood is reclaimed at the end of the building’s service life and reused or manufactured into other products. The manufacturing of wood products also results in less greenhouse gas emissions than other materials.6
The Berkshire Terminus development in Atlanta is one such example. The property includes three buildings, each with five stories of wood-frame construction over a concrete podium. The online Wood Carbon Calculator for Buildings7 shows that the project’s wood construction has contributed to storing and avoiding 13,523 metric tons of CO2, equivalent to the annual emissions from 2,583 cars.
In terms of long-term durability and life cycle, a 2004 survey of 227 buildings demolished in Minneapolis/St. Paul found that buildings are often torn down within 50 years.8 This was true regardless of the construction materials used. It was not due to material performance issues, but was instead due to changing occupation needs and increasing land values. Overall, wood buildings in the study had the longest life spans, showing that wood structural systems are capable of meeting a building’s longevity expectations. In addition, when the embodied energy in demolished buildings is considered along with the implications of material disposal, it is clear that longer lasting buildings are more sustainable. Further, the fact that wood can be reused at the end of its service life in a building, either through renovation or deconstruction and reuse (with minimal additional processing), is also a significant advantage.
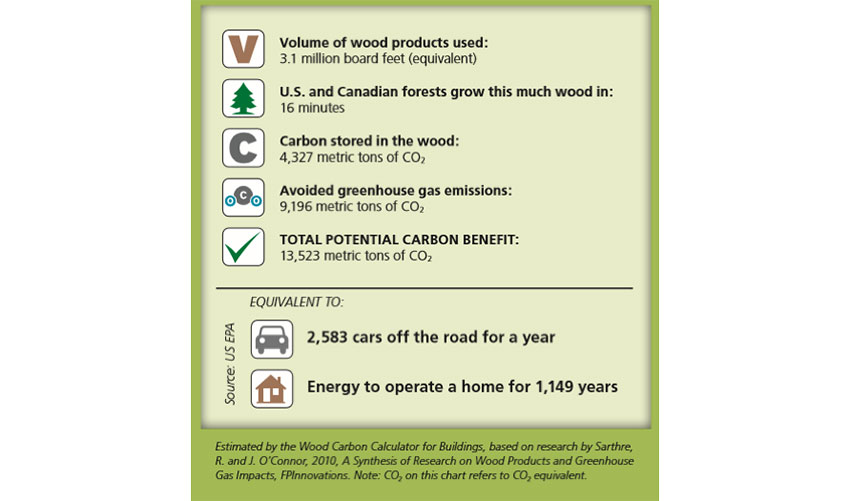
The Building Code And Wood Construction
As with any type of construction, mastering the technical details of wood-frame construction is critical to creating cost-effective buildings that are durable, safe, and code compliant. Building codes require all building systems to perform to the same level of safety, regardless of material used, and wood-frame structures can be designed to meet or exceed standards for fire protection, seismic performance, and resistance to high winds.
The International Building Code (IBC) is a model building code developed by the International Code Council (ICC). It is the predominant model building code in the United States, having been adopted by most jurisdictions with or without amendments. It is reviewed and/or amended over a three-year cycle, with the 2021 edition being the current version.
Construction Types
Chapter 6 of the IBC categorizes buildings into five distinct types of construction. With the exception of Type IV, each construction type is further subdivided into A and B subtypes, with A indicating higher fire-resistance ratings than B. Wood framing is permitted in some aspects of all five.
- Construction Types I and II are generally limited to noncombustible materials such as concrete and steel for structural and some nonstructural items. Wood may be used in nonbearing walls and partitions that do not require a fire-resistance rating. In addition, fire retardant-treated (FRT) wood is permitted in nonbearing partitions, with a required fire rating of no more than 2 hours, in nonbearing exterior walls that are not required to be fire rated, and in most roof construction.
- Type III is defined as noncombustible exterior walls and interior walls of any material allowed by code. Fire retardant-treated (FRT) wood framing is allowed for exterior wall assemblies of a 2-hour rating or less.
- Type IV, also known as Heavy Timber (HT), also requires noncombustible exterior walls. However, exterior walls of a 2-hour rating or less can be FRT wood, or cross-laminated timber that is protected with gypsum, FRT wood, or a noncombustible material. Interior building elements are defined as made from solid or laminated wood of minimum dimensions, and without concealed spaces. The IBC elaborates on different types of solid and laminated wood products and requirements for each.
- Type V allows structural elements, exterior walls, and interior walls to be constructed of any material allowed by code, including common wood-framing systems.
The 2021 IBC includes three new construction types, Type IV-A, IV-B, and IV-C, which allows the expanded use of mass timber. The new construction types are based on the previous Heavy Timber construction type (renamed Type IV-HT) but with additional fire-resistance ratings and levels of required noncombustible protection. The code includes provisions for up to 18 stories of Type IV-A construction for business and residential occupancies, paving the way for increased use of mass timber for multifamily construction.
Permissible Increases in Area and Height
The allowable height and area of a building is determined by construction type, the level of passive fire resistance provided to the structure, and by the intended occupancy. Chapter 5 of the IBC addresses General Building Heights and Areas. There are several considerations here for construction Types III, IV, and V, which are the most common building types for multifamily construction:
- Allowable heights are determined based on occupancy classification and construction type, as shown in Table 504.3, Allowable Building Height in Feet Above Grade Plane. Multifamily buildings (Group R occupancy) are required to be protected by an automatic sprinkler system in accordance with IBC Section 903.2.8. Therefore, new multifamily buildings with sprinklers can be up to 60 feet tall if the sprinkler system is installed in accordance with NFPA Standard 13R. If a sprinkler system is installed per the broader NFPA Standard 13 requirements, then the allowable height can be increased up to 85 feet tall, depending on construction type.
- Number of stories is treated separately from building height, meaning that both must meet compliance requirements. The code limits the number of stories above the grade plane based on occupancy and construction type, per Table 504.4. This means that multifamily R-1, R-2, R-3, and R-4 occupancies may be limited to five stories, depending on construction type and sprinkler system type. For example, an R-2 apartment building with an NFPA 13R sprinkler system with Type III or IV construction is limited to four stories. If the sprinkler system is changed to a general NFPA 13 system, they are allowed to go up to five stories.
- Mezzanines are not considered stories under the building code. Rather, they are defined as intermediate levels between the floor and ceiling of a story and are considered to be part of the story below the mezzanine. Mezzanines can be inserted into stories if their floor area falls within code area limits and the total allowable building height is not exceeded. Effective use of mezzanines can increase the return on investment for a developer. For example, the extra half-story mezzanine for Marselle, a 160,000-square-foot condominium complex in Seattle, added about $250,000 to the cost of the building. But the extra space and views it provided to units on the top floor increased the value of the complex by $1 million.9
- Allowable floor areas are based on occupancy, sprinkler type, and construction type. For multifamily projects, that allowable area can vary widely based on these factors. For example, an R-2 apartment building with an NFPA 13R sprinkler system and Type V-B construction is limited to 7,000 square feet per story, up to three stories (assuming no increases for open frontage), which may be fine for some situations. If larger floor areas are sought, then switching to a standard NFPA 13 system would allow an increase to 21,000 square feet per story, whereas changing to Type V-A construction would only allow up to 12,000 square feet per story. Keeping the NFPA 13R sprinklers and going to Type IV (HT) construction would increase the allowable area up to 20,500 square feet; going to Type III-B would allow 16,000 square feet; Type III-A would allow 24,000 square feet per story. But switching to the standard NFPA 13 sprinkler system would triple each of those allowable per-story areas for two- and three-story buildings, and quadruple them for single-story buildings. Additionally, Types III and IV construction can be five stories as opposed to four. Total building floor area for these buildings is limited to what would be permitted for a three-story building.
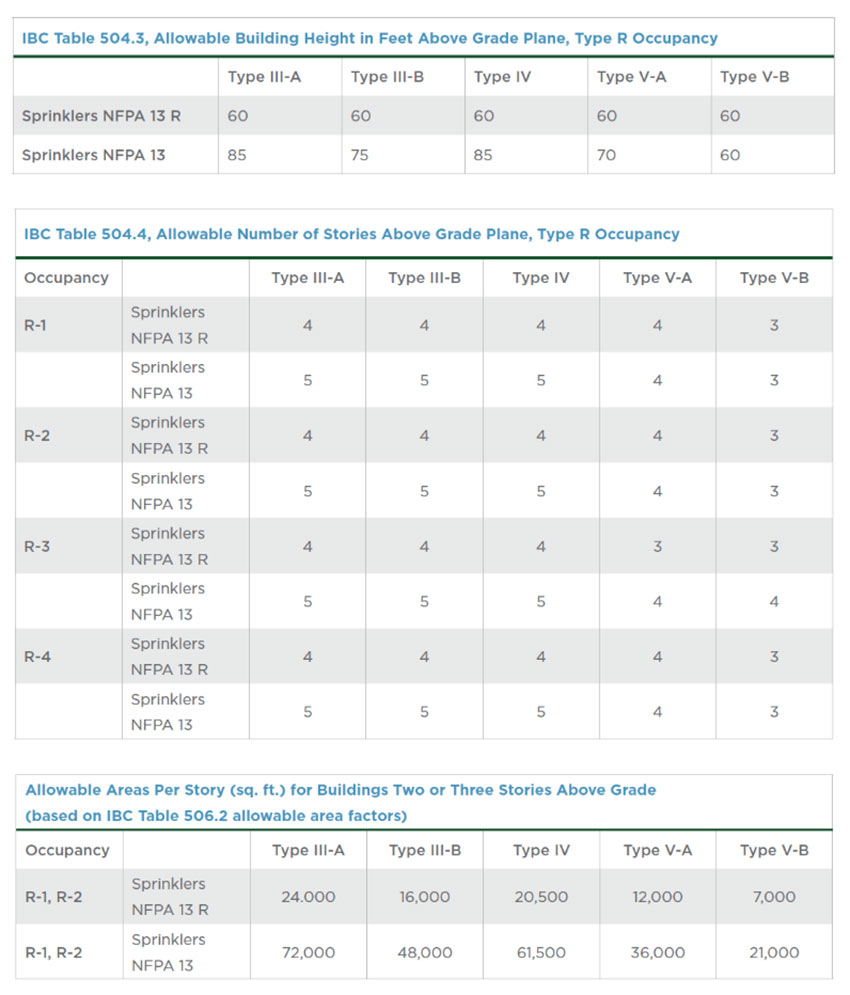
Fire Protection Requirements
Regardless of material used, all buildings, including multifamily structures, must be designed to protect the health, safety, and welfare of occupants and first responders. When proper fire protection systems are designed into a wood-framed structure, the dangers associated with fire are mitigated. The code recognizes that there are different ways to accomplish this and requires that design professionals demonstrate that required levels of fire protection are provided. The minimum fire-resistance rating requirements for building elements (i.e. structure, walls, floor, roof, etc.), based on construction type are provided in IBC Table 601. Specific details of fire- and smoke-protection features are detailed in Chapter 7. The building code’s intent is that the combination of fire resistance and active protective systems provides containment of a fire within a defined space (such as an apartment) so that building occupants have time to evacuate before the fire can move to other parts of the building.

Based on these requirements, wood-frame building elements, just like other materials that require fire-resistance ratings, typically show compliance per independent test procedures. Two common testing standards are ASTM E119, Standard Test Methods for Fire Tests of Building Construction Materials, and UL 263, Fire Tests of Building Construction and Materials. The code also provides alternative methods for determining fire resistance per IBC Section 703.3, which includes prescriptive fire resistance as shown in tables in Section 721 and other approved sources, calculated fire resistance as provided in Section 722, and engineering analyses based on comparisons of tested assemblies or building elements.
Maximizing Building Size Limits
Designers need not avoid wood construction due to the tabular height or area limits provided in the code. There are at least two ways the code allows a design to exceed the area and height limits for construction types.
- Fire Walls – IBC Section 706 specifically addresses fire walls and permits portions of a building separated by one or more of them to be considered as separate, side-by-side buildings for purposes of allowable size and height. In this way, wood-frame buildings can be designed as separate but connected buildings for code-compliance purposes.
- Podium Design – For mid-rise wood-frame buildings, architects and engineers are increasingly turning to podium or pedestal design instead of building directly on a concrete slab on grade. This can provide for additional floor levels for the building compared to what is typically permitted. Section 510 of the IBC addresses Special Provisions and allows five stories of Type III-A wood-frame structures over one or more levels of Type I-A construction. These typically 5-over-1 and 5-over-2 buildings are treated in the code as two structures when they are separated by a 3-hour fire-resistance-rated horizontal assembly. The podium is considered as a separate and distinct building for the purpose of determining height and area limitations and vertical continuity of fire walls. The overall height of the two buildings together is measured from grade plane, and the height-above-grade limitations of Chapter 5 for the upper building apply.
Fire-Resistance-Rated Assemblies
1- and 2-hour fire-resistance requirements for light-frame construction are generally met by using assemblies of products and materials, often including gypsum sheathing over wood, which have been tested in accordance with ASTM E119 or UL 263, although there are other methods based on testing that can be used as indicated in Section 703.3. Lists of wood floor and wall assemblies with accepted ratings are available from the American Wood Council (DCA 3: Fire-Resistance-Rated Wood-Frame Wall and Floor/Ceiling Assemblies, www.awc.org ). Other sources include Underwriters Laboratories (UL)’ fire-resistance-rated systems and products, the UL Fire Resistance Directory, and the Gypsum Association’s Fire Resistance Design Manual.
Fire Resistance of Heavy Timber
Part of the reason heavy timber has effective fire resistance is that it takes a long time to burn through large wood members. That means that heavy timbers have an advantage in a fire because they char on the outside while retaining their strength and load-carrying capacity, slowing combustion and allowing time for occupants to evacuate the building and improving safety for first responders. Heavy timber sizing is addressed in the code to allow for structural safety under fire conditions to be built in. When heavy timber is required to be fire-resistance-rated and the calculation methods of Section 722 of the IBC and Chapter 16 of the AWC National Design Specification (NDS) for Wood Construction are used, a defined percentage of the wood member is provided as sacrificial protection (considered to burn or char in a fire). Wood fiber beneath the char layer retains much of its strength during the fire, so by oversizing the member, structural integrity remains despite the loss of cross-sectional area.
This has direct application to multifamily construction. According to IBC Table 601, Fire-Resistance Ratings Requirements for Building Elements, heavy timber is permitted in roof construction as an alternative to 1-hour (or less) fire-resistance-rated construction for all occupancies, and in all construction types except Type IA.
Mass timber is well suited for fire resistance in multifamily construction. This was reflected in a case study showing the general liability insurance risks of a mass timber building to be no different than that of a concrete or steel building.11
Fire Retardant-Treated Wood (FRT)
IBC Section 2303.2 defines requirements for FRT wood. Building designers must be aware that design values should be adjusted when FRT wood and sheathing is used. Strength adjustments are provided by the treaters based on proprietary chemical formulations. Sections 602.3 and 602.4.1 of the 2021 IBC clarify that both wood framing and sheathing are permitted in exterior walls of Type III and IV buildings where FRT wood is used. CLT is also permitted within exterior wall assemblies of Type IV construction not less than 6 inches thick with a 2-hour rating or less when the exterior surface of the wood panel is protected by FRT wood sheathing, gypsum board, or a noncombustible material. There are also applications for FRT wood in Types I and II construction, such as nonbearing partitions and exterior walls, roof construction, and balconies, subject to the limitations in Section 603.1.
Designing Building Elements for Different Adjacent Fire Ratings
One design consideration for some construction types is that floors and walls may have different fire rating requirements. For example, in Type III-A construction, load-bearing exterior walls are required to have a 2-hour rating, but a floor may only require a 1-hour rating. If it is necessary to address the continuity of fire resistance for the wall at the intersection of the floor, detailing to achieve this smoothly and effectively is important to a good design. The American Wood Council has developed fire resistance details for these intersections in their Design for Code Acceptance (DCA) 3 Fire-Resistance-Rated Wood-Frame Wall and Floor/Ceiling Assemblies, available at https://awc.org/codes-standards/publications/dca3. Designers should work with their local building official to determine acceptable solutions to fire-resistance detailing at the floor-to-wall intersection.
Design Considerations For Framing With Wood
Traditional practices and code provisions for wood framing are established and well-known such that wood framing options and details are readily available to designers. Chapters 16, 17, and 23 of the IBC cover structural wood design, construction, and inspection techniques in considerable detail. However, in addition to selecting the appropriate framing technique, designers of wood buildings must consider factors such as shrinkage, differential movement, and seismic requirements.
Framing Types
There are three common types of framing for wood construction. For Type V-A buildings, where walls require a 1-hour fire-resistance rating, designers usually use traditional platform framing, where the joists sit on top of the double top plates of the wall. Balloon framing is based on the joists hanging off a ledger that is attached to the structural studs which frame the building. In modified or semi-balloon framing, the floor framing hangs off double top plates; it is often used as an alternative to platform-framed structures for both Type V-A and Type III-A construction.
Wood Shrinkage
Regardless of the framing type, IBC Section 2304.3.3 requires that designs for buildings over three stories consider the fact that wood shrinks as it dries. Shrinkage continues until wood reaches its Equilibrium Moisture Content (EMC), which averages 8 to 12 percent moisture content for most structures in the U.S.
Shrinkage effects must be considered for horizontal framing members (width or thickness) in the wall (top/sill plates) and floor (joists) design. Wood is anisotropic, meaning the dimensional change in wood is unequal in different directions. In most softwoods, radial shrinkage (across growth rings) is approximately 4 percent and tangential shrinkage (parallel to growth rings) is approximately 8 percent from green (unseasoned) to typical EMC for structures in the U.S. Longitudinal shrinkage (parallel-to-grain) for vertical framing members is generally negligible and does not affect building performance. Therefore, the majority of shrinkage will occur in the top plates, sill plate, and sole plates, and possibly the floor joists—depending on how the floor framing members are framed to the wall. If the design uses balloon- or modified balloon-framing, then sawn lumber joists won’t play a huge role in overall movement from shrinkage because balloon framing, unlike platform framing, does not accumulate shrinkage over all floors.
Initial MC, or MC at the time of manufacture, is typically specified on a project’s structural drawings. In many parts of the country, the specification would read “a maximum MC of 19 percent.” To achieve this, lumber is generally kiln dried. Although there are regional variations, less commonly used green lumber (which typically hasn’t been kiln dried and has a MC above 19 percent), surface dried lumber, or KD-15 (i.e., kiln dried lumber with a maximum MC of 15 percent at time of manufacture) may also be specified. The American Softwood Lumber Standard, PS 20, a voluntary product standard under the rules of the U.S. Dept. of Commerce, defines dry lumber as “lumber of less than nominal 5-inch thickness which has been seasoned or dried to a maximum moisture content of 19 percent.”
Ways to minimize shrinkage include (among others) specifying kiln dried lumber, letting the wood dry during construction before closing in the walls, and using products and systems such as pre-engineered metal-plate-connected wood trusses for floor and/or roof framing, and engineered wood products (laminated veneer lumber, I-joists, cross-laminated timber, etc.). I-joist floor systems are dimensionally stable and offer minimal inter-floor shrinkage.
Additionally, some overall settlement of the building may occur due to gaps in the building construction that can contribute to the overall vertical movement. Some designs will address this by distributing the dead load throughout the height of the building and allow time for the building to acclimate to the environment and/or air dry prior to installation of the drywall, thus allowing the building to naturally settle.
Fire Safety During Construction
Although less than 2 percent of building fires occur during construction, this phase presents unique risk scenarios that make any building more vulnerable, regardless of material used.
IBC Chapter 33 provides minimum safety precautions for fire during construction, and guidelines for the protection of adjacent public and private properties. The section also includes provisions for fire extinguishers, standpipes, means of egress, and sprinkler system commissioning. The International Fire Code also contains detailed requirements. Fire safety measures such as extended fire watches, site security, safety inspections, and record keeping are now incumbent on owners and contractors during construction.
The most common causes of fire in wood-framed buildings under construction are arson and hot work, making site security, rigorous procedures for workers, and access to fire hydrants critically important. Education is also important, since fires that occur during this phase can spread more quickly when required elements such as gypsum wall coverings, fire doors, smoke alarms, and sprinklers have not been put in place. The Construction Fire Safety Coalition is a resource for codes, standards, and best practices in fire prevention.12
Differential Movement
Allowing for differential movement between wood and non-wood structural elements and building finishes is critical. Steel, concrete, and brick continue to expand and contract over time due to temperature changes, while wood generally maintains its dimensions after having reached its EMC.
Differential movement occurs when, for example, floor joists are supported by a wood-framed wall at one end and by the masonry block of an elevator shaft at the other end. Areas such as stairwells, shafts, and vaulted ceilings require attention for differential movements as do plumbing, electrical, and mechanical systems. Using flexible joints such as flexible pipe, conduit, couplings, and elbows and tees for electrical, mechanical, and plumbing between floors can prevent potential mechanical problems. Design of joints between building envelope components, such as windows and doors, must also allow for differential shrinkage.
Seismic Requirements
While earthquake and seismic requirements are a well-known aspect of building design on the west coast, other parts of the country are not immune to earthquake activity and must also comply with seismic codes. Wood construction provides high strength with relatively low weight, and the high strength-to-weight ratio makes wood a good choice for earthquake-resistant construction.13,14 In wood-framed buildings, walls and floors are often used to transfer lateral loads from winds and seismic forces.
Wood-frame construction also provides numerous load paths through shear walls and diaphragms, which typically have hundreds of structural elements and thousands of nail connections, adding ductility and redundancy to the system. Redundant load paths give additional assurance that loads will be transferred if one connection fails. In contrast, structures supported by heavy non-wood frames have relatively few structural members and connections, resulting in fewer load paths. Moreover, the large number of walls in a typical multifamily project reduces the loads shared by each individual wall. Tests and observations from past earthquakes show that wood buildings have performed well. For example, a six-story light-frame wood building tested on the world’s largest shake table in Japan resisted a major earthquake (projected to occur, on average, approximately every 2,500 years) with minimal damage.15
Building code requirements for wood diaphragms, shear walls, and hold-down devices work effectively in creating earthquake-resistive structures. Horizontal diaphragms in roofs and floors transfer the horizontal forces to the shear walls. Shear walls with hold-downs, such as a continuous tie-down rod system, resist tension forces in an overturning scenario, while wood studs or columns absorb the compression forces. Wood structural panel shear walls are typically used throughout the building to provide vertical lateral resistance.
Acoustical Control
As with any type of building performance goal, the acoustics of a mixed-use and multifamily wood-framed building can be designed to meet or exceed minimal requirements, depending on the expectations of the developer, buyers, and tenants. Requirements for acoustical performance of floor and wall assemblies for multifamily buildings are covered in Section 1206 of the 2021 IBC. These assemblies must have STC (sound transmission class) and IIC (impact insulation class) ratings of 50 or higher. Ratings can be reduced to 45 if field-tested.
For wall systems, sound isolation can be accomplished in two ways. One is to use partitions with a high mass of 75 pounds per square foot (psf) or greater, or to use low-mass systems (2 to 5 psf) separated by air spaces of 3 to 6 inches. The goal in party walls or exterior walls is to keep other people’s noise out of the living unit, while keeping tenant noise in. In lightweight wood structures, this can be achieved by separating the materials with an air space (e.g., stud or joist construction). In terms of acoustical performance, the most effective wood-frame wall is a double-stud wall, followed by staggered-stud, and then single-stud configuration.
In mid-rise wood-frame buildings, some options for improving acoustic performance include:
- Sheathing – The mass of the sheathing is just as important as the air space provided by the stud or joist cavity. In acoustical detailing, 5/8-inch thick type ’X’ gypsum board is typically required.
- Insulation – The most cost-effective acoustical improvement to a sound isolation system is the addition of batt insulation or any open-cell foam system to the stud or joist cavity. While closed-cell spray foams have higher R-values and offer improved building envelope energy performance by sealing the partition and improving air tightness, the closed cells do not allow the vibrating air molecules to interact with the insulation product so sound attenuation is less. It is this interaction that helps reduce the sound.
- Resilient channels – When double- or staggered-stud construction is not possible, it is possible to decouple the sheathing from the framing with resilient channels to reduce the acoustical energy transfer through the framing system.
- Floor finishes – Impact noise can be reduced considerably with the use of soft finishes such as carpet. When carpeting is not practical or desired, the addition of a floating wood or tile floor system offers another solution.
The American Wood Council has developed Technical Report 15: Calculations of Sound Transmission Parameters for Wood-Framed Assemblies (TR15) as a tool to estimate STC and IIC sound ratings of floor/ceiling assemblies. Additionally, a calculator is available on the AWC website to simplify the calculation of these estimated STC and IIC values, using the methodology presented in TR15. In 2018, Sections 1206.2 and 1206.3 of the IBC were amended to allow STC and IIC sound ratings to be established by engineering analysis, creating the opportunity for design flexibility without the need for laboratory testing every assembly.
Mass timber buildings provide unique acoustical considerations, particularly since many designers want to leave the wood structure exposed as finish. Acoustic performance expectations can still be met for most designs. For example, concrete floor toppings are often added to mass timber floor assemblies to improve acoustics; sometimes, underlayments or acoustical mats are placed between the mass timber panel and the topping.
Designing With Innovative Wood Products And Building Systems
Beyond conventional framing, there are numerous innovative technologies and building systems that are increasing the opportunities for multifamily wood buildings.
Prefabricated Systems and Modular Construction
The use of prefabricated or factory manufactured wall and roof panels can provide better quality wall construction since the panels are constructed off-site in moisture-controlled environments. Wall panelizing is particularly useful for job sites without adequate space to construct the walls, and panelization can speed erection time considerably. Wall panels can also optimize stud design and increase soundproofing and energy efficiency. Panel lengths can range from 4 to 30 feet long, and are lifted into place by a crane.
Full modular construction is a growing element of multifamily construction because it offers a fast, cost-effective construction option. Building modules are fabricated off-site, complete with finished exteriors and interiors, including mechanical systems. The modules are simply lifted into place and connected at the job site. In many cases, these modules can arrive up to 95 percent complete. For example, 38 Harriet, a four-story apartment project in San Francisco, was completed in just six months, from groundbreaking to completion. And Mountaineer Hall, a student housing structure at Appalachian State University in North Carolina, met the university’s deadline to add 460 beds for students in just nine months.16
Mass Timber
While traditional light-frame wood construction is a proven building solution for mid-rise structures up to six stories tall, mass timber products, including cross-laminated timber (CLT), are creating new design possibilities. CLT is a multilayer, solid-sawn lumber or structural composite lumber (SCL) wood panel in which each layer is oriented crosswise to its adjacent layer for increased dimensional stability and structural performance.
Widely used in Europe and increasingly available in North America, mass timber is an innovative construction option for mid-rise and, in the 2021 IBC, tall multifamily buildings. Several tall wood buildings, including the 18-story UBC Brock Commons student housing project in Vancouver, British Columbia, have already demonstrated mass timber’s suitability for this building type.
The 2015 IBC was first to incorporate CLT as a structural building product when it was recognized for use in Type IV (heavy timber, HT) construction. In response to the increasing use of CLT and other mass timber building components in Types III, IV, and V construction, the 2018 IBC added more detail to clarify the requirements of heavy timber construction. Comprehensive new mass timber construction types were added to the 2021 IBC through the work of an ad hoc committee of the International Code Council that was ratified by the membership in 2018. These new construction types permit mass timber buildings of considerably more allowable area and with heights up to 18 stories to be built under the code.
Among CLT’s attractive structural characteristics are high dimensional stability, high axial-load capacity, high shear strength, rigidity around openings, and negligible settlement effects. CLT assemblies also offer inherent fire resistance due to thick cross sections that, when exposed to fire, char at a slow and predictable rate. Other benefits include speed of construction, thermal performance, and the environmental advantages offered by all wood products— including a low carbon footprint.17
Conclusion
Wood use for multifamily construction is growing, driven by wood’s acceptance in building codes and the value, safety, and durability that wood building products and systems provide. Design professionals recognize that wood can provide value and versatility in designing projects ranging from affordable housing to luxury condominiums. Building with wood also helps achieve efficiencies that allow developers to provide amenities more commonly found in higher-end projects. Wood is recognized as a renewable and energy-efficient material helping with green building certification and sustainability overall. There are numerous design techniques that can be used to accommodate some of the special considerations required with wood construction for mid-rise, multifamily wood-frame construction, including shrinkage, fire protections, and seismic requirements. Wood can also contribute to the energy efficiency goals of the project. Since building codes recognize the inherent safety and performance capabilities of wood in multifamily buildings, innovative technologies and products can be expected to propel designers to even greater heights.Additional Resources
American Wood Council
The American Wood Council is committed to ensuring a durable, safe, and sustainably built environment. To achieve these objectives, AWC contributes to the development of sound public policies, codes, and regulations which allow for the appropriate and responsible manufacture and use of wood products. The AWC develops consensus standards, comprehensive technical guidelines, and tools for wood design and construction, as well as providing education regarding their application. www.awc.org
Wood Products Council, WoodWorks
WoodWorks provides education and free technical support related to the design, engineering, and construction of commercial and multifamily wood buildings in the U.S. A nonprofit staffed with architects, structural engineers, and construction experts, we have the expertise to assist with all aspects of wood building design. For assistance with a project, email help@woodworks.org. www.woodworks.org
Design Guidance And Resources
There are many resources available to architects and engineers designing light-frame and mass timber projects.
- For general information, the Think Wood website (www.thinkwood.com) offers an expanding library of materials on mass timber products, research, building examples, and developments related to tall wood buildings.
- The National Design Specification (NDS) for Wood Construction (www.awc.org) is the IBC-referenced design standard for lumber, glulam, SCL, and CLT, including fire design, fasteners, and connections, etc. A mass timber building in the United States cannot be designed without the NDS.
- The U.S. CLT Handbook (www.thinkwood.com) includes detailed technical information on the use of CLT. It should be used in conjunction with information provided by manufacturers since most CLT currently available in North America is proprietary (i.e., lay-ups aren’t standard across suppliers).
- American Wood Council’s 2018 Code Conforming Wood Design
- WoodWorks’ Five-Story, Wood-Frame Structure over Podium Slab
End Notes
1National Multifamily Housing Council
2Project Efficiencies, ThinkWood
3Wood Brings the Savings Home, WoodWorks,
4Student Housing gets Extra College Credit from Wood, WoodWorks,
5Life Cycle Environmental Performance of Renewable Building Materials in the Context of Building Construction, Consortium for Research on Renewable Industrial Materials, Phase I 2005, Phase II 2010; A Synthesis of Research on Wood Products and Greenhouse Gas Impacts, Sarthre, R. and J. O’Connor, 2010, FPInnovations; Werner, F. and Richter, K. 2007, Wooden building products in comparative LCA: A literature review, International Journal of Life Cycle Assessment
6See endnote 5.
7The Wood Carbon Calculator for Buildings was developed by FPInnovations, WoodWorks and the Canadian Wood Council.
8Survey on Actual Service Lives for North American Buildings, Jennifer O’Connor, Forintek Canada Corporation,
9WoodWorks, Maximizing View and Value with Wood.
11Tall with Timber: Seattle Mass Timber Tower Case Study. (2018). DLR Group, p. 67
12https://constructionfiresafety.org/
13The ShakeOut Scenario—Woodframe Buildings, URS Corporation, prepared for the U.S. Geological Survey and California Geological Survey, 2008
14youtube.com/watch?v=c25HuZeQsyo&context=C3f612acADOEgsToPDskLH3EQs-aodM9-NsZgF2lGi
15Van de Lindt, John W.; Gupta, Rakesh; Pei, Shiling; Tachibana, Kazuki; Araki, Yasuhiro; Rammer, Douglas; Isoda, Hiroshi. 2012. Damage assessment of a fullscale six-story wood-frame building following triaxial shake table tests, Journal of Performance of Constructed Facilities 26(1): 17-23.
16Putting the Pieces Together, WoodWorks,
17U.S. CLT Handbook