2021 IBC: Building Bigger and Taller with Low-Carbon Wood
Continuing Education
Use the following learning objectives to focus your study while reading this month’s Continuing Education article.
Learning Objectives - After reading this article, you will be able to:
- Explore the evolution of building with wood and the impact new IBC changes are having on the ability to specify mass timber in tall buildings that meet safety requirements for occupancy.
- Examine the new 2021 International Building Code changes related to tall wood construction, including three new building types that allow for wood buildings up to 18 stories and even taller using an Alternate Materials and Methods Requests (AMMR).
- Analyze design tactics and relevant code applications used to boost the density of light-frame wood construction and the impact these tactics have on the safety of the occupants within the built environment.
- Review the science related to wood’s embodied carbon and life-cycle assessment in the context of curbing a building’s impact on climate change.
THE EVOLUTION OF BUILDING BIGGER AND TALLER WITH WOOD CONSTRUCTION
The built environment in the U.S. is growing at a rapid rate as a result of an ever-rising need for housing and infrastructure. It’s estimated that America is short more than 5 million homes1, and a boost in infrastructure spending is further accelerating new construction2. At the same time, buildings and their construction account for more than a third of global carbon dioxide emissions3, with 11% of carbon emissions generated from the building materials and construction4. This embodied carbon can account for half of the total carbon footprint over the lifetime of a building5.
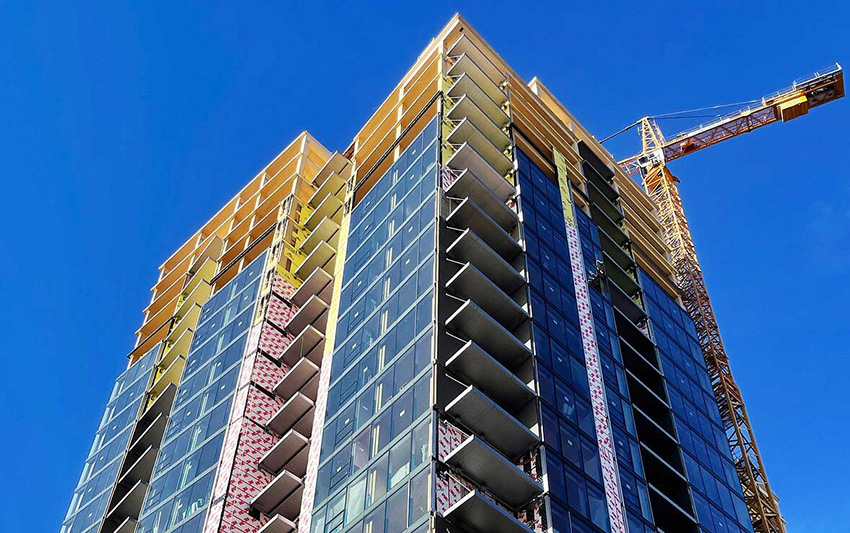
Photo: CD Smith
Ascent in Milwaukee, completed July 2022, is 25 stories tall and constructed from CLT floor panels supported on glulam beams and columns with two reinforced concrete cores by architect Thornton Tomasetti.
To address these concerns, some policymakers6 and design teams7 are turning, in part, to timber—a naturally renewable building material that, being 50% carbon by dry weight8, can lock in carbon over the lifetime of a building9. Product advancements, new capabilities of hybrid-timber construction, fire testing, and fire-resistant designs have all contributed to an increased capacity to build larger and taller buildings using low-carbon wood products.
In this course, you’ll learn about the 2021 International Building Code (IBC) changes related to tall wood construction, including three new building types that allow for wood buildings up to 18 stories10 and even taller using an Alternate Materials and Methods Requests (AMMR)11. Rigorous fire testing was conducted as part of these code changes to validate the safety of tall mass timber construction.
Along with advancements in tall mass timber construction, the course explores design tactics and relevant code applications used to boost the density of light-frame wood construction. Finally, this course will review the science related to wood’s embodied carbon and life-cycle assessment in the context of curbing a building’s impact on climate change, including a growing body of research demonstrating how building with timber represents an opportunity to increase the long-term storage of carbon in today’s built environment12.
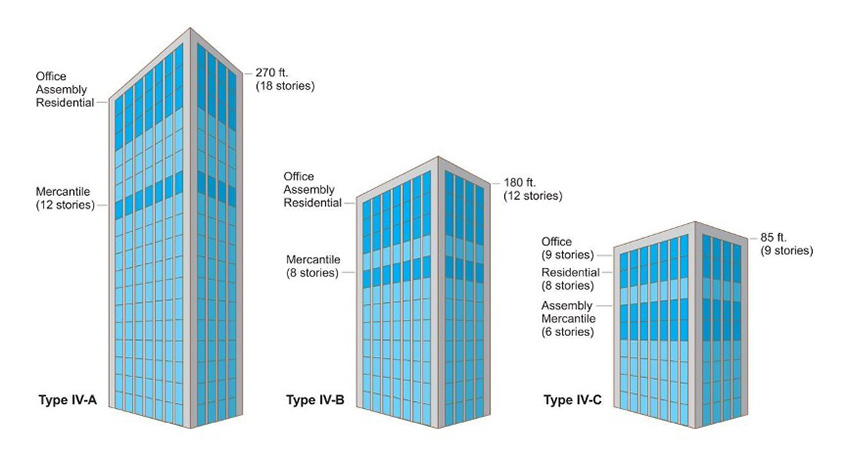
Photo courtesy of WoodWorks
Representative Building Sizes for Business Occupancy.
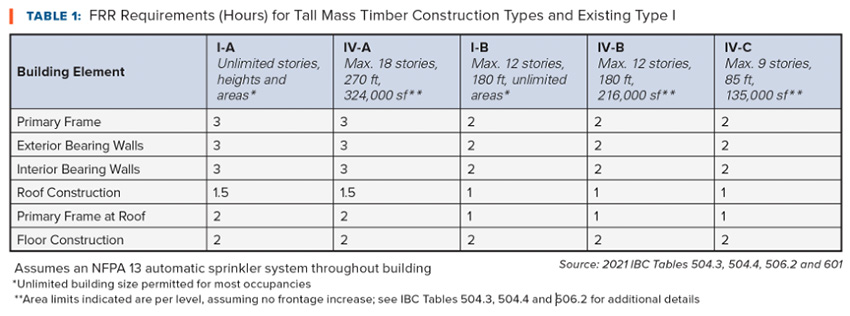
GLOBAL TREND TOWARDS TALL MASS TIMBER BUILDINGS
Over the past 15 years, there has been a growing interest in tall buildings constructed from mass timber materials. This has been coupled with technical advancements that one architect described as “a timber renaissance, with new milestones in timber construction being reached at a breakneck pace13.” Around the world, there are now dozens of timber buildings constructed above eight stories tall. International examples include Brock Commons in Vancouver, BC (18 stories), Mjøstårnet in Norway (18 stories), and HoHo Wien in Austria (24 stories).
In the United States, such buildings have been constrained by a strong reliance on prescriptive building code limits and less willingness to use performance-based fire protection engineering. That said, mass timber construction has grown significantly, and changes to the 2021 IBC have greatly increased the pace at which new tall mass timber projects are being proposed. As of early 2022, more than 1,300 mass timber projects have been built, are under construction, or in design in the US14; more than 160 of these are considered tall mass timber projects, exceeding the height and/or story limits for mass timber under the 2018 IBC.
THE PATH TO 2021 CODE CHANGES: ICC TALL WOOD BUILDING AD HOC COMMITTEE
In response to the growing interest in tall wood buildings, particularly those constructed from new mass timber materials, the International Code Council (ICC) chartered the Ad Hoc Committee on Tall Wood Buildings (TWB) in December 2015. The purpose of this committee was to “explore the building science of tall wood buildings and investigate the feasibility of and take action on developing code changes for tall wood buildings.” Initial activities included reviewing the technical state of mass timber knowledge and building performance and developing a series of compartment fire tests to test the proposed construction types.
In January 2018, the Committee submitted a set of 14 IBC code change proposals to the ICC 2018 Group A code development process, targeting changes to the 2021 IBC. In January 2019, 3 additional code change proposals were submitted by the TWB as part of the Group B cycle. All 17 code change approvals were approved for inclusion in the 2021 IBC, some as submitted and some with modifications.
Concurrently with the development of the IBC code change proposals, the committee overseeing the code-referenced CLT product standard, ANSI/APA PRG-320 Standard for Performance-Rated Cross-Laminated Timber (PRG-320), responded to the desire by fire service representatives on the TWB for higher assurances of CLT behavior in high-rise construction by incorporating a new required test for adhesives used in CLT production. Passing this test is required for adhesives used in all CLT complying with the 2019 edition of PRG 320, referenced in IBC 2021. This test is based on a 4-hour compartment-like fire test designed “to identify and exclude use of adhesives that permit CLT char layer fall-off resulting in fire regrowth during the cooling phase of a fully developed fire.”
2021 IBC CODE CHANGES FOR WOOD CONSTRUCTION
New Tall Timber Construction Types
In looking at the existing tall wood buildings proposed and built around the country and world, the TWB decided to propose expanding the existing Type IV construction by adding three new sub-types—IV-A, IV-B, and IV-C—and renaming Type IV as Type IV-HT. Similar to the noncombustible construction types I and II, the four “mass timber” construction types are arranged from the highest fire resistance and safety requirements (IV-A) to the lowest (IV-HT).
These three new construction types introduced in the 2021 IBC each have different maximum allowable heights, stories, and areas. Type IV-A allows the greatest height and area and has the most stringent fire protection requirements (e.g., fire-resistance ratings, noncombustible protection, etc.), followed by Types IV-B and IV-C. Conceptually, Type IV-A is similar to the existing construction Type I-A (which requires a fully non-combustible structure), with equal or greater fire-resistance rating requirements and no exposed mass timber.
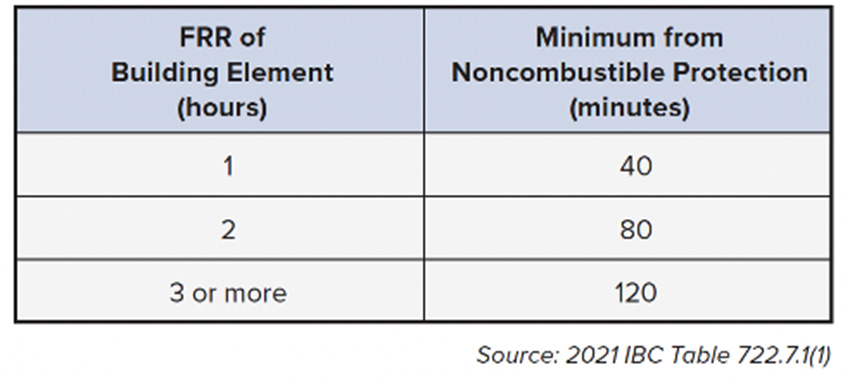
Type IV-C is similar to Type IV-HT with almost all of the interior mass timber permitted to be exposed; however, most structural building components have a 2-hour FRR in addition to minimum heavy timber sizes, resulting in an increase in the allowable number of stories when compared to IV-HT. The TWB also determined that an intermediate construction type between IV-A and IV-C was needed, resulting in Type IV-B. For multi-family occupancies, Type IV-A permits a timber structure of up to 18 stories and 270 feet, Type IV-B permits up to 12 stories and 180 feet, and Type IV-C permits up to 8 stories and 85 feet.
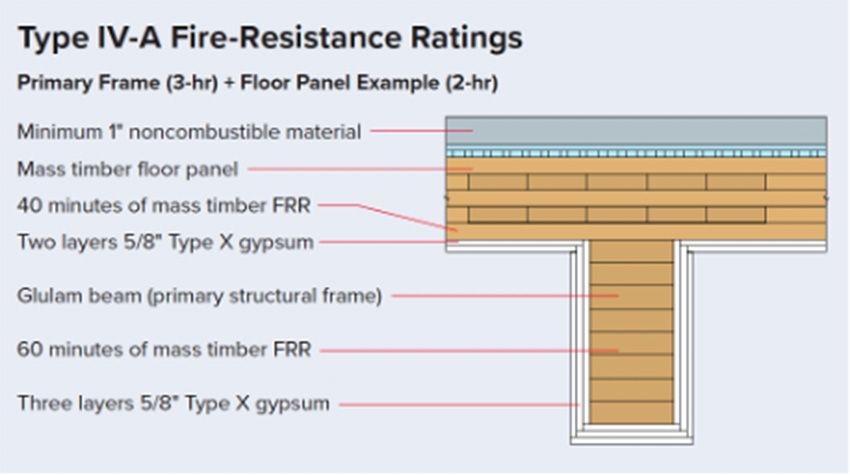
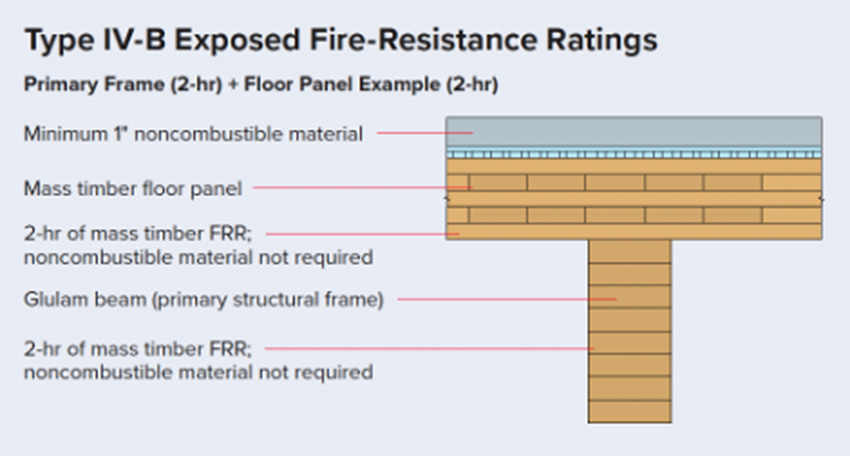
Fire-Resistance Design
A requirement unique to the new construction types is noncombustible protection for some mass timber elements. This noncombustible material applied to the mass timber helps determine fire behavior by delaying the contribution of the mass timber structure in a fire and has an added benefit of increasing the fire-resistance rating of the overall assembly or member. A summary of the fire-resistance rating for the new construction types is shown in the table below. Allowances for Type I-A and I-B are included for comparison.
A provision commonly used in Type I construction for high-rise buildings that do not exceed 420 feet in height allows a reduced FRR if the building has sprinkler control valves equipped with supervisory initiating devices and water-flow initiating devices for each floor (per IBC Section 403.2.1.1). With this provision, the FRR requirements for elements in a Type I-A building may be reduced to the lesser requirements of Type I-B construction (with the exception of columns that support floors), and the requirements for a Type I-B building may be reduced to the lesser requirements of Type II-A construction. These reductions are not available for the new construction types, making them more conservative than Type I requirements.
In addition to meeting FRR requirements, all mass timber elements used in Types IV-A, IV-B, and IV-C construction must meet minimum size criteria prescribed in IBC Section 2304.11.
Definitions of the new construction types (found in IBC Sections 602.4.1, 602.4.2, and 602.4.3) dictate that only mass timber or noncombustible materials can be used for the structural systems. Where mass timber elements are used, the definitions also include guidelines for whether the wood may be exposed on the building’s interior or must be covered with noncombustible protection. General allowances for exposed timber are:
- Type IV-A: No exposed timber permitted
- Type IV-B: Limited exposed timber permitted as follows:
- Ceilings (including integral exposed beams) up to 20% of floor area in dwelling unit or fire area,* or
- Walls (including integral exposed columns) up to 40% of floor area in dwelling unit or fire area,* or
- A combination of each using sum of ratios (actual exposed/allowable exposed wood) not to exceed 1.0
- Type IV-C: All exposed timber permitted*
*Exceptions: No exposed timber is allowed at shaft walls, within concealed spaces, or on the exterior side of exterior walls.
When noncombustible protection is required to cover timber elements, it must provide at least two-thirds of the FRR. For example, a beam that requires a 2-hour FRR and requires noncombustible protection must achieve at least 80 minutes of protection from the noncombustible coverings. Section 722.7, which is new to the 2021 IBC, has been introduced to codify the demonstration of FRR using a combination of time assigned to the noncombustible coverings and inherent fire resistance of the mass timber framing members.
Any noncombustible material used as protection of mass timber elements can be tested by following the procedure outlined in IBC Section 703.6 to determine its contribution to FRR. However, two prescriptive options are presented in IBC 2021 Section 722.7.1. These options are 25 minutes per layer of ½" Type X gypsum board or 40 minutes per layer of 5/8" Type X gypsum board. Using these options, where mass timber is required to have noncombustible protection, two layers of 5/8” Type X gypsum board covering would meet the noncombustible protection requirements for a 2-hour FRR, and three layers would meet the noncombustible protection requirements for a 3-hour FRR.
The remaining one-third of the mass timber member’s FRR must be achieved through inherent fire resistance of the mass timber element. For example, a mass timber floor assembly requiring a 2-hour FRR would require 80 minutes of noncombustible protection, with the remaining 40 minutes achieved from the mass timber. In applications where the timber is exposed, the full FRR must be achieved through inherent fire resistance of the mass timber element.
There are several options for demonstrating the contribution of various elements to the FRR. One method is to provide the results of testing undertaken in accordance with ASTM E119 (or UL 263). However, if the exact assembly has not been tested, IBC Section 703.2 provides a number of alternatives. These alternatives are all founded on ASTM E119 testing. Item 3, which permits the use of calculations in accordance with Section 722, is frequently used to demonstrate the fire-resistance rating of exposed mass timber. IBC Section 722.1 notes that the fire resistance of exposed wood members and wood decking shall be permitted to be calculated in accordance with Chapter 16 of the ANSI/AWC National Design Specification (NDS) for Wood Construction. Chapter 16 of the NDS can be used to calculate up to a 2-hour fire resistance rating for a variety of exposed wood members including solid-sawn, glulam, and CLT.
Hybrid Construction for Shafts & Lateral Resistance
Provisions addressing materials permitted in shaft wall construction can be found in both the shaft enclosures section (713.3) and fire barriers section (707.2) of the IBC. These sections state that shaft walls can be constructed of any material permitted by the building’s type of construction. As noted, construction Types IV-A, IV-B, and IV-C permit the use of mass timber or noncombustible materials (or a combination thereof). This would indicate that the use of mass timber shaft walls in tall buildings is also permitted. This is true with one exception. Section 602.4 of the 2021 IBC notes that shaft walls in buildings taller than 12 stories or 180 feet must be constructed of noncombustible materials. Tall mass timber buildings which do not exceed these limits may utilize mass timber shaft walls; however, those shaft walls must have noncombustible protection on both faces of the wall.
While the code permits the use of mass timber shaft walls in many instances, worth noting is that most tall timber buildings are hybrids, utilizing non-wood materials for shaft enclosures such as concrete cores or steel braced frames with infill light gauge steel stud walls. One of the primary reasons for this is to use these materials as the building’s vertical lateral force resistance system. Until recently, the IBC and referenced standards, such as the American Wood Council’s Special Design Provisions for Wind and Seismic (SDPWS) and ASCE 7 Minimum Design Loads and Associated Criteria for Buildings and Other Structures, did not prescriptively recognize mass timber as an allowable seismic force resisting system. While this did change in the 2021 version of SDPWS and the 2022 version of ASCE with new options for the use of CLT shearwalls, the current provisions limit the overall system height of CLT shearwalls to 65 feet in areas of high seismic hazard. Mass timber vertical lateral force resisting systems have not been implemented to date on tall mass timber buildings in the US, with project design teams choosing to use primarily either concrete cores as shearwalls or structural steel-braced frames.

Photo courtesy of Atelier Jones
Type IV-B building with 12 stories.
TRENDS FOR INCREASED DENSITY IN LIGHT WOOD-FRAME
Although not specific to a change within the 2021 IBC, the past several years have continued to see an increasing trend of light wood-frame projects using innovative approaches to achieve greater density, site utilization, and value. Several examples of how this has been done include more incorporation of amenity spaces (roof decks, fitness centers, retail) as well as on-site parking, all located within the same building. Below is a discussion of the code provisions and design methodologies implemented to achieve these innovative projects.
For years, the IBC has allowed light wood-frame buildings up to five stories for residential occupancies (and six stories for office use) over a single-level podium. The 2015 IBC evolved to recognize multi-level podiums, which had been permitted in the Seattle Building Code for some time. Across the country, designers began maximizing the value of their midrise projects with 5-over-2 and 5-over-3 configurations; however, for one Sacramento project called 1430 Q, 5-over-2 still wasn’t sufficient to make the investment in pencil out. Sacramento’s competitive building market required that 1430 Q have at least six floors of wood-frame residential units to make the project profitable, in a 6-over-2 configuration. By using the City’s Alternate Means and Materials Request (AMMR) process, the design team was able to successfully achieve the extra height and, in so doing, build the country’s tallest light wood-frame building. Several additional projects in Sacramento, which are currently under construction, have been permitted and are using a similar 6-over-2 approach.
In Washington, six stories of Type IIIA construction are permitted when certain criteria are met. Two example projects which are leveraging these code allowances are called Analog and Moraine, both of which are located in Tacoma.
Incorporating Parking in Light Wood-Frame Mid-Rise
A common configuration in multistory, multifamily wood-frame construction is parking on the first level(s) with three to five stories of wood-frame residential on top. Many designers assume that the parking level is required to be noncombustible and utilize the podium provisions within IBC 510.2; however, there are several opportunities for alternate provisions and/or wood framing within the parking levels that can offer significant cost savings.
Section 406 provides several provisions specific to motor vehicle-related occupancies. Section 406.5 provides requirements for open parking garages. The natural ventilation requirements for a garage to qualify as open are discussed in Section 406.5.2 and generally require openings on at least 40% of the garage’s perimeter, with some exceptions specified. Section 406.5.1 permits open parking garages to be of Types I, II, or IV construction.
Enclosed parking garages are covered by Section 406.6 and require both mechanical ventilation and NFPA 13 sprinklers, per Section 903.2.10. There are no limitations on construction type for enclosed parking garages, indicating that parking garages of Types III, IV or V construction can be used and framed with wood, concrete, steel and all other materials as permitted for each of these types of construction per the IBC Section 602 definitions.
Occupancy separation is a cost-effective design option frequently overlooked when a parking garage is classified as enclosed. This design route utilizes a single construction type for the entire building (i.e., the Type I-A podium of Section 510.2 is not necessary). The parking garage can still be framed with concrete or steel, for example, but there is no code requirement to use Types I or II simply due to the presence of noncombustible materials.
In a building that has an NFPA 13 sprinkler system throughout, only a 1-hour rating is required when separating parking from occupancies such as Group B, M, and R, per Table 508.4. This indicates that a mixed-use building consisting of an enclosed parking area and other occupancies could be completely framed with wood if allowable building size calculations permit the use of Types III, IV, or V construction. Even if other materials are used in the building (perhaps as columns, beams, or walls on lower levels), there is economic value in using Section 602.1.1 to classify the entire building as the lowest construction type allowed.
Utilizing the options presented in Section 510.4 offers the ability to capitalize on an increased number of stories—similar to the horizontal separation provision of Section 510.2—by stacking a Group R building on top of a single-story Group S-2 parking garage, gaining an additional story.
The main benefit of utilizing Section 510.4 is that it provides the benefit of an additional story while not requiring the full podium provision limitations of Section 510.2 (i.e., the lowest level doesn’t have to be Type I-A with a 3-hour podium slab). Specifically, this provision allows the use of a heavy timber-framed parking level (if open) and only requires a 1-hour rating (if the parking level is Type IV) or 2-hour rating (if the parking level is Type I) to separate the parking from adjacent residential units above.
Incorporating Occupied Roof Decks in Light Wood-Frame Mid-Rise
ccupied roof decks are becoming more common in multifamily and commercial buildings as designers and owners seek to increase the marketability of their rental spaces with more amenities. In most instances, these roof decks are open-air, without roof coverings, and have partial-height guards or wall parapets around their perimeter. Designers often wonder if a roof deck of this kind needs to be included as a story when calculating the required construction type, building area, and number of stories. Language was added to the 2018 IBC stating that a roof occupied in full or in part with the same occupancy as the story immediately below does not need to be included in the building area regulated by Section 506. Further, if the building is fully equipped with an NFPA 13 or NFPA 13R sprinkler system and an occupant notification system in accordance with section 907.5, the roof occupancy is not restricted to the occupancy of the story below.
In most instances, an occupied roof deck with a roof covering or walls that are taller than 48 inches is considered a separate story and must be included in building area calculations. If considered a mezzanine or accessory occupancy (Sections 505.2 and 508.2), it may be possible to exclude the occupied roof deck (and its enclosing elements) as a separate story when determining the construction type.
2024 IBC CODE CHANGES
While the 2021 IBC has been adopted by several jurisdictions, with others in the process of updating as discussed below, the code development cycle for updates to the 2024 IBC is now underway. Most notably with respect to tall mass timber is a proposed change to the ceiling exposure allowances for Type IV-B. Under the 2021 IBC, Type IV-B is permitted up to 20% ceiling exposure as noted. However, a planned update would allow 100% ceiling exposure in the 2024 IBC. Several projects currently in design are looking to leverage these future code allowances, and several jurisdictions are including this change in their code amendments and code adoption processes.
JURISDICTIONAL CODE ADOPTIONS
While the list is constantly changing, the following jurisdictions have adopted the tall mass timber provisions in the 2021 IBC, either in whole or with local amendments.
- Oregon
- Washington
- City of Denver
- Utah
- California
- City of Austin, Texas
- City of Bryan, Texas
- Maine
- Georgia
- Idaho
- Connecticut
- Maryland
- New Jersey
- South Carolina
- South Dakota
Several other jurisdictions are considering or are in the process of adopting the tall mass timber provisions or the 2021 IBC in whole. Note that several jurisdictions including Denver and Oregon have already adopted the tall mass timber provisions of the 2021 IBC and will be adopting the 2024 IBC allowance for 100% ceiling exposure under the 2022 Denver Building Code, scheduled to be adopted in the summer of 2022.
THE URGENT NEED TO LOWER BUILDING CARBON FOOTPRINTS
Advancements in tall wood construction and codes are being made just as the call for low-carbon construction reaches new levels of urgency. The built environment is growing at a record pace in the United States. It is estimated that 2.5 million new housing units are needed to make up for the nation’s housing shortage15.
Buildings and their construction account for 39% of global carbon dioxide emissions; 28% of those emissions come from operational carbon—the energy used to power, heat and cool a building16. Buildings’ operational carbon can be reduced through energy efficiency measures and policymakers, architects, developers, and engineers have made significant advances in this arena. The remaining 11% of carbon emissions are generated from building materials and construction17. This embodied carbon can account for half of the total carbon footprint over the lifetime of the building18.
Embodied carbon is a priority for many environmental, architecture, and urban planning organizations including C40 Cities19, Architecture 203020, Urban Land Institute21, and the World Green Building Council22. Many experts believe addressing embodied carbon for buildings and building materials is critical to achieving the goals of the Intergovernmental Panel on Climate Change (IPCC) and the 2016 Paris Climate Agreement.
EMBODIED CARBON IN A BUILDING’S LIFE CYCLE
Embodied carbon is determined by conducting a life-cycle assessment (LCA) of a product, assembly, or building over declared life- cycle stages. An LCA study returns results for a number of environmental metrics, including the potential to impact climate or “global warming potential” (GWP). Embodied carbon is the GWP result. Embodied carbon is measured for each stage of the product’s life cycle, allowing comparisons across any combination of stages.
As buildings become more energy efficient, the upfront embodied carbon from materials begins to account for a higher proportion of a building’s carbon footprint23. Very soon, embodied carbon is likely to become the dominant source of building emissions.
Embodied carbon varies dramatically between concrete, steel and wood, making product decisions key in achieving lower carbon buildings. Manufacturing wood products requires less total energy, and in particular less fossil energy, than manufacturing alternative structural materials including metals, concrete, or bricks24.
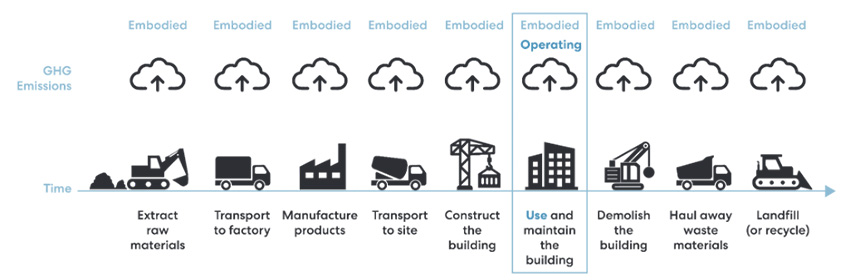
STORED CARBON IN WOOD PRODUCTS
Wood products are approximately 50% carbon by dry weight25. The use of wood products in buildings provides an additional environmental benefit by storing carbon removed from the atmosphere. This ability to store carbon sequestered during tree growth in the forest makes wood an ideal product for buildings, which are designed for long service lives. Essentially, a wood building is a large carbon sink26.
Timber as a tactic for curbing climate change is backed by a growing body of research and advancements in calculating the carbon footprint of building materials27. In a recent paper published in the journal Nature Sustainability, experts at the Potsdam Institute for Climate Impact Research28 in Germany delved into four possible scenarios of timber use in buildings over the next 30 years. In the first case, “business as usual,” 0.5% of buildings are made with wood while the vast majority remain constructed of concrete and steel. There’s a 10% timber building scenario; a 50% timber building scenario; and a fourth in which the vast majority—90% of new construction—is made with wood. Their findings suggest that the lowest scenario could result in 10 million tons of carbon stored per year and in the highest, nearly 700 million tons29.
“Buildings, which are designed to stay for decades,” researchers write in the paper, “are an overlooked opportunity for a long-term storage of carbon, because most widely used construction materials such as steel and concrete hardly store any carbon."30
THE ROLE OF WOOD CONSTRUCTION NOW AND IN THE FUTURE
There is an urgent need to decarbonize the built environment, combat climate change and find advanced ways to reduce and store carbon emissions. The exigency to cut carbon is demonstrated by the environmental priorities set by such organizations as C40 Cities31, Architecture 203032, Urban Land Institute33, and the World Green Building Council34 advocating for significant changes in how we plan, build, manage, and power cities and towns—including a reduction in embodied carbon over a building’s life cycle. Wood has an increasing role to play as design professionals look to tackle the climate crisis and reduce the environmental footprint of buildings, now and in the future.
Buildings and infrastructure built from bio-based materials such as timber that store carbon during their service lives can serve as constructed carbon sinks. They could increase the existing carbon pool of urban areas (1–12 GtC) by 25 to 170%35. Backed up by testing and research, code changes in jurisdictions across the country are making it possible to increase the height and density of wood construction. With a comprehensive understanding of these code changes, design teams can bring innovation and ingenuity to the buildings they design.
ADDITIONAL RESOURCES
To help building designers compare options, WoodWorks has compiled a web-based inventory of completed mass timber fire tests. The Inventory of Fire Resistance Tested Mass Timber Assemblies & Penetrations is updated as new tests become available and can be found at www.woodworks.org.
For additional information on both the calculation-based method and the ASTM E119 testing method of demonstrating FRR of mass timber elements, see the WoodWorks publication Fire Design of Mass Timber Members.
END NOTES