Exploring Large Aggregate Terrazzo
Palladiana and Venetian terrazzo surfaces meet the durability, versatility, aesthetics, and creative expression that high-end corporate, retail, and hospitality designers are seeking
Continuing Education
Use the following learning objectives to focus your study while reading this month’s Continuing Education article.
Learning Objectives - After reading this article, you will be able to:
- Identify the unique characteristics driving growing interest in larger aggregate Palladiana and Venetian terrazzo.
- Compare the pros and cons of epoxy vs. sand-cushion cement binders, from both a sus-tainability and performance standpoint, for different large aggregate applications.
- Gain best practices for optimized Palladiana and Venetian terrazzo user-focused designs and installations.
- List the many advantages of working with an experienced, certified terrazzo contractor, and involving these tradesmen early in the design process.
- Review recent project profiles showcasing the beauty and versatility of Palladiana and Ve-netian terrazzo, and the enhanced user comfort they provide.
Reemerging in recent years as a striking, sustainable, and highly flexible material, terrazzo continues to beautify the floors, walls, ramps, and columns of lobbies, airports, schools, and municipal facilities. Terrazzo’s limitless customization potential makes it an attractive option for a wide range of applications and budgets while providing the same durability and ease of maintenance regardless of design details. High-profile projects such as David Chipperfield’s New York City Valentino flagship store and actress Mandy Moore’s Pasadena home have further created a media buzz around the design opportunities afforded by this desirable material.
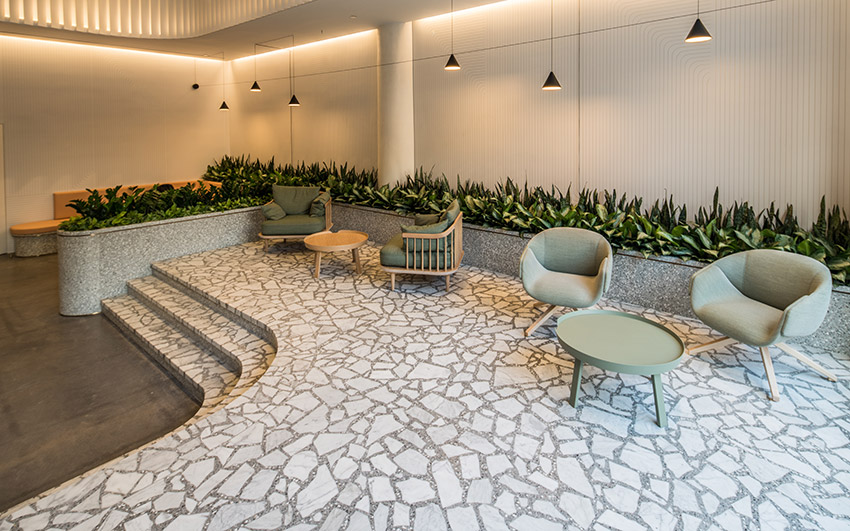
Photo courtesy of Michael Blackburn
Large aggregate terrazzo designs, as pictured here in this Hudson Square lobby in Manhattan, are growing in popularity as attractive, high-end spaces for corporate lobbies, hospitality settings, and museums.
“Terrazzo is a sought-after material due to its numerous qualities and aesthetic charm. Moreover, terrazzo can be custom made to include various hues and patterns offering an unparalleled degree of versatility. The marbled visual effects produce a distinct and attractive look to any design,” reports Margine Biswas, AIA, NCARB, LEED AP, Archiphy Architects, Dallas. In a similar vein, Seattle-based architect Alison Wilkinson, AIA, NCARB, LEED AP BD+C, affirms that designers and architects love terrazzo for its versatility and durability. “It can be successfully used in a sleek office building, a high-volume grocery store, or a residential space due to the endless design combinations of aggregate and matrix,” she says.
Made from a mix of a wide variety of possible aggregates, such as stone or recycled glass, terrazzo’s qualities as a sustainable, highly hygienic, and nonporous surface are further propelling interest. “There are few products that are 100 percent customizable and offer the use of designs and patterns in the same way that terrazzo does. The ease of maintenance and lack of grout joints also play a role,” adds terrazzo contractor Jonathan Maraldo, executive vice president of Southern Tile & Terrazzo, Houston. As designers continue to enjoy the opportunity to play with aggregate types, sizes, colors, mix compositions, and binding matrixes to create signature surfaces, designs are trending toward larger aggregate Venetian and Palladiana terrazzo.
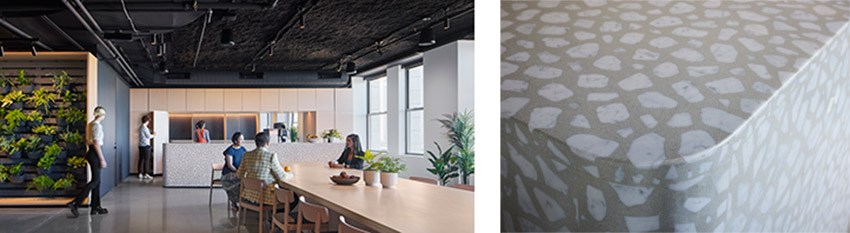
Photo courtesy of David Burk
To achieve a specific look, SOM created a Venetian terrazzo design for the pantry area in their Chicago office.
LARGE AGGREGATE TERRAZZO
“Large aggregate terrazzo designs are gaining interest due to their unique and eye-catching visuals, textured patterns, and customizability,” explains Biswas. “The material can be tailored to the specific style of a space.” Whereas the finest microaggregates are 1/8 to 3/8 inch in size and create a minimal, monochromatic look, larger aggregates produce more contrast. Institutional buildings and airports tend to go with the more uniform, streamlined terrazzo, while the larger aggregate’s higher-end look is attractive to commercial spaces. “Larger aggregate can offer a bolder look, with the color and character of each stone curated and visible, allowing the design of the floor to stand out as the centerpiece of a room,” Biswas adds. Also unique is the fact that large aggregate terrazzo is custom created, which makes it a desirable, one-of-a-kind material.
With this larger composition, explains Carolyn Kiernat, AIA, principal, Page & Turnbull, San Francisco, the stone’s natural color and texture are more prominent. This enhanced transparency creates a more dramatic appearance. In viewing these large aggregate designs through the lens of larger societal trends, Andrew Barwick, RA, senior associate with Cooper Robertson, New York City, observes, “Large aggregate terrazzo has a bold, graphic, visual quality that feels contemporary and modern. This distinct expression of the material where legibility is favored over subtlety feels synonymous with other contemporary trends in visual design (e.g., web, print, etc.) where visual complexity is often eschewed in favor of more simple, sober, legible expressions.”
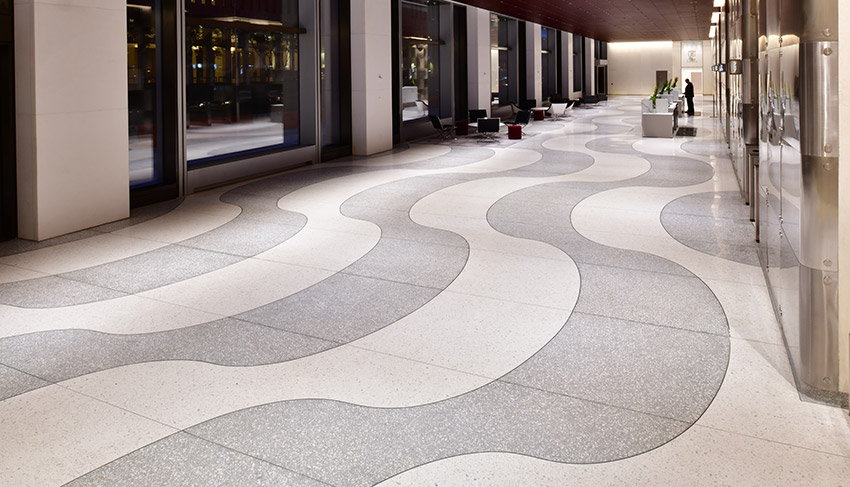
Photo courtesy of David Laudadio
Due to major building renovations, the original 1959 Venetian sand-cushion terrazzo floor was removed and replicated for this iconic lobby inside 1271 Avenue of the Americas in Manhattan.
TERRAZZO’S PALLADIANA ROOTS
Dating back to the 15th century in Italy, marble artisans would gather stone remnants and use them to build residential terraces. They would embed them in clay, grind them smooth, and seal them with goat’s milk to bring out the luster and shine, explains Brad Hedges, an Alpharetta, Ga.-based architectural consultant with expertise in terrazzo.
This original terrazzo floor with marble slabs was Palladiana. The larger-sized marble fragments would be hand laid into a clay or a cement-like material. The entire floor would then be ground and polished. “Named after the illustrious Andrea Palladio, renowned for his creative material utilization and intricate focus on details, Palladiana terrazzo was developed in Italy and boasts a luxurious, polished surface,” explains Biswas.
In contrast to some other terrazzo styles, Gilad Naftaly, CEO of Tel Aviv-based terrazzo contractor C.R.Contech, believes that Palladiana appeals to people’s interest in seeing the stones within the flooring or surface and the mosaic-type look that it lends. “Thanks to Palladiana terrazzo’s smooth surface and easy maintenance, the application of this mosaic style can be extended to floor spaces such as lobbies, kitchens, and sitting areas, allowing designers to come up with beautiful, unique, and exciting designs,” adds CR Contech’s Director of Sales and Marketing Tali Lahav. “Architects can also combine new materials such as large brass ornaments, pebbles, glass, and stone tile fragments.”
The pieces are often irregularly shaped, paver-like stone slabs that can be as large as 18 inches.
While the installation process requires more labor and material, the craftsman has greater control over the process since the aggregate is hand laid, and the result is a beautiful, luxurious finish. “Palladiana terrazzo can make a statement with its larger scale,” adds Ximena Rodriguez, principal and director of interior design, CetraRuddy Architecture, New York City. “It is very flexible and allows for variety with the possibility of making a very graphic statement with ultra-high contrast materials, or a subtle look with tone-on-tone terrazzo.” Wilkinson adds, “The large stone pieces are placed carefully by the installer to create a flagstone effect. Best used for larger spaces, the end result is a puzzle of fragmented stone pieces floating between a matrix color.”
Gensler architect Paul Manno likes the warm, authentic, uniquely crafted appeal of Palladiana, and the fact that it’s neither directional nor patterned. He specifies it for a change of scale in reception and lobby spaces or break rooms.
“Palladiana has a wonderful artisanal quality to it, and we’ve enjoyed exploring its versatility on many projects—including in our own office in Chicago,” relates Julie Michiels, SOM senior associate principal and interior design director. The design intent for SOM’s office pantry island was to find material that looked monolithic against the concrete floor, yet with a refined feel. “To achieve this look, I actually went to the Menconi Terrazzo shop and worked with the team to break the stone inlay into various shapes and lay out one of the panels. It was a little bit of an experiment for everyone, and I think it turned out beautifully,” she reports.
Walking architects through the terrazzo design process, the first step is selecting the type of natural stone, which is Palladiana terrazzo’s main feature, instructs Hedges. “Typically, we are working with marble as it is easier to grind and polish.” Designers can choose one type of stone or pick a mixture of stones. Then the next step is determining the size, spacing, and edge profile of the frac-tured stones. For example, the stones can be arranged in a tighter or more spacious laying pattern. For the edge, the design can be irregular or clean cut. Next, the terrazzo grout color is chosen. Serving as the background or base, if epoxy is selected as the binder, any paint or Pantone color can be chosen. With both Palladiana and Venetian terrazzo, Menconi Terrazzo President Steve Menconi explains that the architect/designer plays a more artistic role in the selection process. Once all the specs are in order, architects can request a mock-up to see what the finished product will look like. Then, any aspects of the terrazzo mix can be adjusted prior to final approval.
{{question2}} {{question3}}VENETIAN TERRAZZO
Similar to Palladiana, Venetian terrazzo is crafted using premium materials such as marble, granite, and other natural stone. “Venetian terrazzo offers a unique combination of luxury and finesse. Experienced artisans utilize their specialized skill set to craft intricate patterns and designs that are unique to each piece, a process that has been perfected through generations of practice,” said Biswas.
Offering some historical perspective, Hedges explained that craftsmen from Italy’s northeast Friuli region would gather various colored pebbles from nearby rivers and incorporate them into the first “battuto” (meaning “beaten down”) mixes. These finishes came to be highly sought after in Venice, France, and eventually all of Europe and the U.S. “Terrazzo became known as one of the most elite and desired trades in the construction industry due to the meticulous skill and unparalleled quality of their ‘battuto venezia.’ Venetian aggregates, which are larger in diameter than the standard size, offer a refreshing take on an antique style of flooring that works well in today’s interiors, be it ec-lectic, minimalist, rustic, or contemporary,” relates Hedges. “Venetian terrazzo can offer a more monolithic appearance to a floor with fewer joints and seams than stone or tile, and can also produce complex patterns,” adds Michiels. “You can get pretty specific with colors, and use the aggregate to create a subtle effect or one that is more expressive.”
The slab may need to be recessed to allow for the larger Venetian aggregate. Typically, with aggregates between 3/8-inch and 7/8-inch in diameter, the terrazzo must be poured at 5/8-inch or more to accommodate the larger stone. It’s added to an epoxy or cement mix and troweled on the prepared substrate. It’s also possible to sprinkle the aggregate on the troweled mix and then roll out. Once the mix cures, it is ground and polished. {{question4}}
EPOXY VS. SAND-CUSHION CEMENT
As the matrix for Palladiana or Venetian terrazzo, sand-cushion cement is the traditional choice while epoxy is a popular alternative offering a number of benefits. Both matrixes are typically devoid of VOCs and are often GREENGUARD certified, and offer a high level of compressive tensile and flexural strength. “Epoxy is a powerful adhesive that provides an impenetrable bond between the substrate and terrazzo mixture, generating a lasting and secure surface. Furthermore, it is impervious to stains, chemicals, and water, rendering it a great option for highly trafficked spaces,” explains Biswas.
Epoxy’s physical properties are at least six times greater than cement terrazzo, which gives it better crack resistance. In addition, it is available in more colors and installs faster. Another advantage of epoxy is that it has no shrinkage therefore the demand for divider strips is less than a cement system. Because epoxy terrazzo requires much less depth, it is ideal for applications where the floor finish weight or depth is restricted, particularly in a renovation where a thinner floor finish may have been previously accommodated. It is also possible to apply the epoxy directly to an existing concrete slab in many cases. The thicker cement system offers the advantages of greater tolerance for an imperfect slab. “The cementitious and layered system is about 3 inches thick in total. It is more forgiving of uneven, imperfect floors because of the thick underbed below what is still a relatively thin layer of terrazzo,” relates Michiels. “I actually think it has a great aesthetic quality as well as the cementitious matrix has a warmth and authenticity to it that is quite nice.”While a designer might be aware of the pluses and minuses of epoxy vs. cement for a given application, additional intricacies may arise that only an experienced terrazzo contractor would be able to uncover. “The advantages or disadvantages to both cement and epoxy terrazzo will make one system good for a project. However, this changes with the details and design of each project, which is why it is so important to bring in an NTMA contractor early in the design process,” advises Menconi. For example, if sand-cushion terrazzo is used with a thicker assembly, this greater depth must be accommodated by the structure, meaning that slabs must be lowered or otherwise depressed, requiring more planning and coordination during the design phase.
Additionally, sand-cushion terrazzo is isolated from the concrete slab by a plastic membrane to aid in the suppression of cracking. Because cement is a breathable material, it can be installed in areas where a vapor drive is suspected, such as a slab-on-grade. The plastic membrane can be installed over areas where cracking in the concrete is a concern, says NTMA Technical Director Gary French.
Divider strips must be placed at a much greater frequency in sand-cushion than in epoxy, typically every 4 feet in each direction to control shrinkage in the finish panels. However, the thinner epoxy system means that less consideration of its depth and weight is required.
An epoxy system is suitable for retrofit application on existing slab on grade where the presence or integrity of a vapor barrier below the slab is suspect, with a moisture control system, he explains. Because epoxy is sensitive to vapor drive, a moisture control system typically must be applied.
A good example of both sand-cushion terrazzo and epoxy terrazzo, selected in response to differing design and technical requirements, can be seen in Cooper Robertson’s renovation and expansion of the Museum at Gateway Arch National Park in St. Louis. For this 2019 NTMA Honor Award project, sand-cushion terrazzo was used for the new public exhibition spaces on the expansion’s lowest level and to replace a terrazzo installation in the existing museum, which was possible because a sufficient depth was available in the floor. “Sand-cushion terrazzo was primarily chosen for this application due to its capacity to accommodate larger aggregate, which was selected to match the grand scale of the public spaces it was installed in,” explains Barwick.
In addition to the concrete installations, Missouri Terrazzo installed epoxy terrazzo at elevated slabs at smaller-scaled spaces within the building on account of its thinner, lightweight assembly. “Epoxy terrazzo’s high strength and color range were particularly capitalized upon in the installation of an expansive map of North America that traced the path of westward expansion in the U.S. This permanent installation was comprised entirely of epoxy terrazzo in varying colors to represent land masses, rivers, lakes, trails, and landmarks,” Barwick adds. {{question5}} {{question6}}
EASE OF MAINTENANCE
Another commonality shared by both epoxy and sand-cushion cement is the fact that they’re both extremely durable and low maintenance like all terrazzo systems. Since terrazzo floors are solid surfaces, if they are prepared and installed correctly, and if adequate room is allowed for potential future movement, they are resistant to cracking and breakage. That said, the cement-based binder used in sand-cushion terrazzo is naturally porous and is therefore more susceptible to staining. To guard against this, a nonporous sealer should be applied over both epoxy and cement-based terrazzo installations to protect it and help ensure its longevity.
“Regular cleaning with a damp mop or soft brush and a mild cleaning solution is all that is needed to keep these floors looking their best. They do not require any special cleaning products or equipment, which makes them very convenient to maintain,” reports Biswas. Not only are maintenance costs and labor is lowered, but building occupants benefit from a cleaner, healthier environment.
Terrazzo is particularly suited for high-traffic areas, as well as both dry and wet environments, making it appropriate for kitchens and bathrooms. It’s food safe and non-slip when used with the correct sealers and finishes.
DURABILITY
Terrazzo’s exceptional durability regardless of aggregate size or matrix is evident in its toughness under damaging conditions. For example, in New Orleans following Hurricane Katrina, most of the terrazzo there required nothing more than polishing and refinishing, according to Alton Davis, with Richard C. Lambert Consultants, Mandeville, La., who led the architectural team on the $17-million restoration of Lakefront Airport terminal. “Katrina just reemphasized what I already knew about terrazzo,” Davis says. “When they tear down the building, it will still be there. If the building lasts hundreds of years, the terrazzo will last hundreds of years.”
Historic installations throughout the country further illustrate the value of using materials that last. When four historic courthouses in the Pacific Northwest marked their centennials a decade ago, they also celebrated 100 years of embodied energy in their historic terrazzo floors. Putting this into perspective, no new flooring materials had to be manufactured for this floor for an entire century. Very few building materials can offer this same level of longevity. Consequently, terrazzo is considered a highly sustainable material.
“Terrazzo is a very durable, beautiful substance for buildings with high traffic,” reports Rebecca Nielsen, LLED AP, an historic preservation program specialist with the U.S. General Services Administration (GSA) in Auburn, Wash. She oversees 20 historic register federal buildings in the Pacific Northwest. “Terrazzo was obviously a good choice because 100 years later we are still using it,” Nielsen notes. “On the whole, these floors are in really great shape and look great. We feature them and maintain them. We are proud of them.”
BEST PRACTICES
Due to the highly specialized nature of terrazzo projects, onboarding the terrazzo contractor early in the design process is essential to the project’s success. “When the contractor is brought on board at the point of material selection, designers can collaborate on the design aesthetic, including aggregate size and jointing, while establishing a realistic budget for the project,” says Tricia Ebner, AIA, director, MdeAS, New York City.
A local contractor also offers the advantage of producing samples to help dial in aggregate selection. “Availability and sourcing limitations of the raw aggregate material can play a major role in the final aggregate mix design, so understanding these sourcing limitations early in the design process, whether regional or national, is important, particularly if the terrazzo floor will play a primary role in the building's material palette,” notes Barwick.
Contractors also play an important role in advising on constructability and making sure the drawings are specified correctly. If the drawings and specifications are correctly listed, this avoids gaps in scope that can create issues further into the project.
The terrazzo installation can impact the building’s structural requirements—yet another incentive to work out all the details with the contractors as early as possible. With the contractor’s early involvement in a Palladiana terrazzo project, designers and architects have the opportunity to learn about the different techniques to fracture the aggregate pieces that will create a variety of looks. As noted, the contractors can also assist with Palladiana stone selection, sizing, and spacing. Other important issues to discuss with the contractor include spacing of the joints, detailing, and juncture of the vertical and horizontal surfaces.
Whereas many finishes in a building are produced in a controlled environment, terrazzo is unique in that the labor-intensive installation process is performed on site. If precast terrazzo is specified in the design, it must be fabricated inside a proper terrazzo shop. In either case, working with a highly qualified and experienced terrazzo contractor is very important. “Because the installation process can be messy, many contractors prefer to install before other finishes are brought on site. They can then come back for final polish after the remaining elements like cabinets, paint, trim work, etc., are completed,” notes Wilkinson.
To ensure essential quality assurance, selecting an NTMA terrazzo contractor member is highly recommended, says Hedges. “NTMA is a very useful resource and can provide feedback and answer questions regarding what type of terrazzo assembly is most appropriate for a given application," adds Barwick. “Standard terrazzo is a specialty product and the larger aggregate terrazzo is an even more specialized product,” notes Maraldo. “The involvement of an NTMA contractor as early as possible will make sure that the terrazzo is installed to the highest quality. Terrazzo will last the life of the building and is often a focal point of the design. Not having an experienced and qualified contractor could provide a substandard installation, which will create problems during the installation and throughout the life of the product."
Another important ingredient in a successful large aggregate project is mock-ups. For highly customized installations like Palladiana, Janet Lina, associate at Architecture Plus Information, says, “Contractors should be required to provide mock-ups to ensure that the right mix of materials is used to achieve the design intent.” Essentially, the mock-up process is an important strategy to confirm that the client’s expectations have been met, ultimately preventing unexpected costs and delays. While design teams may be tempted to rely on a small sample, this is often an insufficient way to envision the full picture of what the final terrazzo installation will look like. “Mock-ups are so important!” exclaims Michiels. “In most cases, terrazzo is not an off-the-shelf product; it is the work of artisans.”
In conclusion, the case for early terrazzo contractor involvement—from concept to completion—is strong. Offering some advice, Michiels states, “Work with these contractors to understand what they do and to help them understand what you are trying to achieve. Making terrazzo is a highly specialized craft, developed through years of experience. Good terrazzo contractors are artisans, capable of working with designers and clients to achieve beautiful work.” {{question7}}
IN SUMMARY
While terrazzo projects, in general, are anticipated to increase, experts predict that large aggregate designs will comprise a strong portion of this work. “The design pipeline certainly has a decent amount of larger aggregate terrazzo, so I expect you’ll continue to see this style of terrazzo for years to come,” confirms Hedges.
“Large aggregate terrazzo offers a diverse selection of design possibilities that can be made a reality with improved manufacturing methods and sustainable materials,” agrees Biswas. “As architects, designers, and clients gain an appreciation for the creative capabilities of this sturdy and dependable material, it is certain to be a popular choice for projects in the near future.”
Wilkinson believes the flexibility of Venetian and Palladiana is enticing to designers who are looking for something more than a cool tile lay. “As long as there are specialty trades who can support the installation, I think this is a product we will continue to see employed in hospitality, residential, and luxury commercial spaces,” she predicts.
{{question8}} {{question9}} {{question10}}
Barbara Horwitz-Bennett is a veteran architectural journalist who has written hundreds of CEUs and articles for various AEC publications. BHBennett.com