Weathering the Storms: How PVF Film Technology Preserves and Elevates Building Exteriors
In an accelerated and real-time test, PVF film proves a multitude of aesthetic and structural benefits
Continuing Education
Use the following learning objectives to focus your study while reading this month’s Continuing Education article.
Learning Objectives - After reading this article, you will be able to:
- Describe how outdoor environments can stress exteriors, leading to high maintenance and early replacement issues in building exteriors.
- Explain how using a laminated film offers optimal coverage and uniform thickness on substrates to aid the performance and durability of the exterior.
- Discuss how materials that consider environmental, durability, and maintenance factors can aid in sustainability and long-term upkeep.
- Illustrate the ways that accelerated tests and case studies have predicted long-term outdoor performance.
The convenience of material goods and consumerism culture have created a throwaway society—one that has become used to cheap products that will break and can be replaced. But in the world of architecture, it is not desirable or even feasible to invest in materials that will degrade easily or require constant maintenance. When a building is constructed, it needs to last for decades with little maintenance required in order for it to be cost-effective.
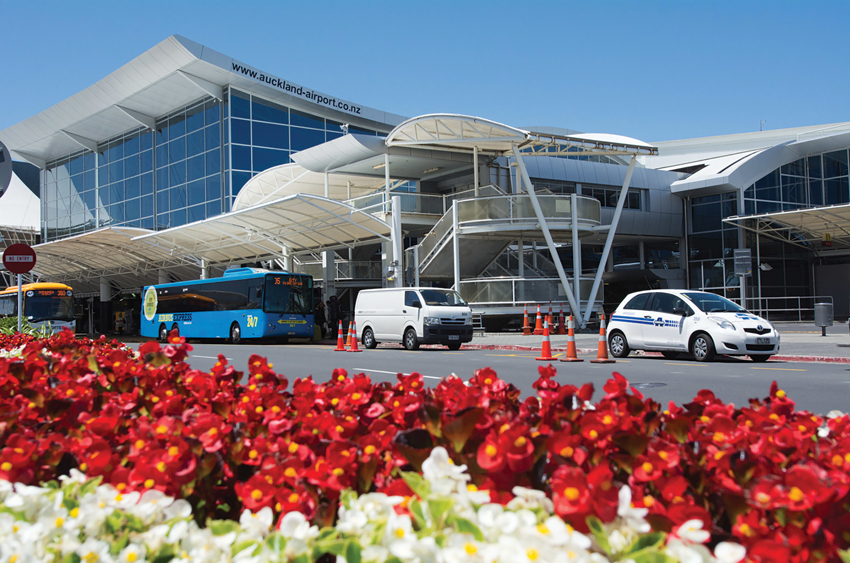
All images courtesy of DuPont Tedlar
Polyvinyl fluoride (PVF) film is a technology that works as a laminate on exterior surfaces to protect buildings from a variety of climates, as in the case of this airport located in hot and humid Auckland, New Zealand.
The challenge in the AEC industry is with materials that are impacted by events out of our immediate control, such as pollution and the elements. Building exteriors protect us in all kinds of weather and from a multitude of external forces, but what protects the buildings themselves? The next section will discuss the negative impacts that building exteriors face and how polyvinyl fluoride (PVF) film offers a solution.
The Problem with Building Exteriors
Buildings go through a variety of stresses—and one is the weather. The first component that weather refers to is temperature, which includes the fluctuation of temperatures within day and night cycles as well as longer cycles within seasons. The second component of weather is water, which can come in the form of snow and rain, and which happens in cycles of dry and humid environments. The third component is the wind, which can bring mechanical strain onto structures through a range of force, but it also brings with it particulate that contributes to the erosion of surfaces. All of these weather components can also come in the form of sudden weather events, such as hurricanes, and happen within a short period of time and on an extreme scale.
There are also other environmental stresses that can affect a building. If a building is next to a coastline, it is likely to be impacted by saltwater. Saltwater will be more corrosive toward metallic structures. Other stresses come from human impact. Urban environments often deal with graffiti on surfaces, though graffiti can be found in rural areas as well. The graffiti itself can damage a surface, but the process of cleaning up graffiti using any variety of cleaning solvents can also do damage to a surface. A building in a heavily polluted area, such as in an industrial town or in polluted urban locations, will deal with issues like acid rain or particulates in the air that cause stress on building exteriors. Finally, a building surface can suffer from general daily use from people or animals nearby, such as dogs who might relieve themselves on a building’s siding and, just like with weather, damage the integrity of a building envelope.
All of these stresses can wreak havoc on building surfaces. In coastal and tropical or subtropical environments, where temperatures, humidity, and salt spray are high, these pollutants concentrate and stagnant, creating an atmosphere of corrosion. Metals and other surfaces exposed to these environments are highly susceptible to damage from oxygen, moisture, impurities, acids, salt ions, dust, and surface deposits. The issue may be most apparent in environments where extreme weather events happen regularly or where pollution is overwhelming, but still, all buildings—no matter where they are located—will need some mechanism for protecting themselves from chemicals, abrasion, water, wind, and other problems that over time lead to corrosion, coating failure, mold and mildew, cracking, gloss loss, and color change.
In light of all these issues, what is the best exterior protection for a surface?
First, it is necessary to have a surface that is resilient to physical damage—not just in use but in installation. Second, it is necessary to have a surface that is chemically inert. Paint used for graffiti tends to be solvent based, so the surface needs to be able to resist the solvent-based paint while also needing to resist the potentially damaging chemicals found in cleaning solutions that would be used for graffiti removal. Third, it needs to resist the weather by having a surface with ultraviolet (UV) protection through UV-reflective material. This means having a material that can handle thermal changes, seasonal changes, day and night cycles, and sudden weather events. Finally, it is necessary that the surface protection be permanently adhered to the substrate so it can carry out its mission of protecting it.
If these aspects are not managed, there will be a failure of the surface to protect the underlying substrates, and these failures can be seen in different shapes and forms. Gloss loss on the surface, in which a shiny surface is reduced to a low-gloss appearance, changes the original aesthetic. Color changes and cracking of the surface are also symptoms of failed protection. Cracking of the surface associated with a metallic substrate can create corrosion issues, leading to further color problems such as brown and green stains. On other surfaces when there is cracking, mold and mildew can begin to appear, changing the aesthetic and ultimately the strength of the surface.
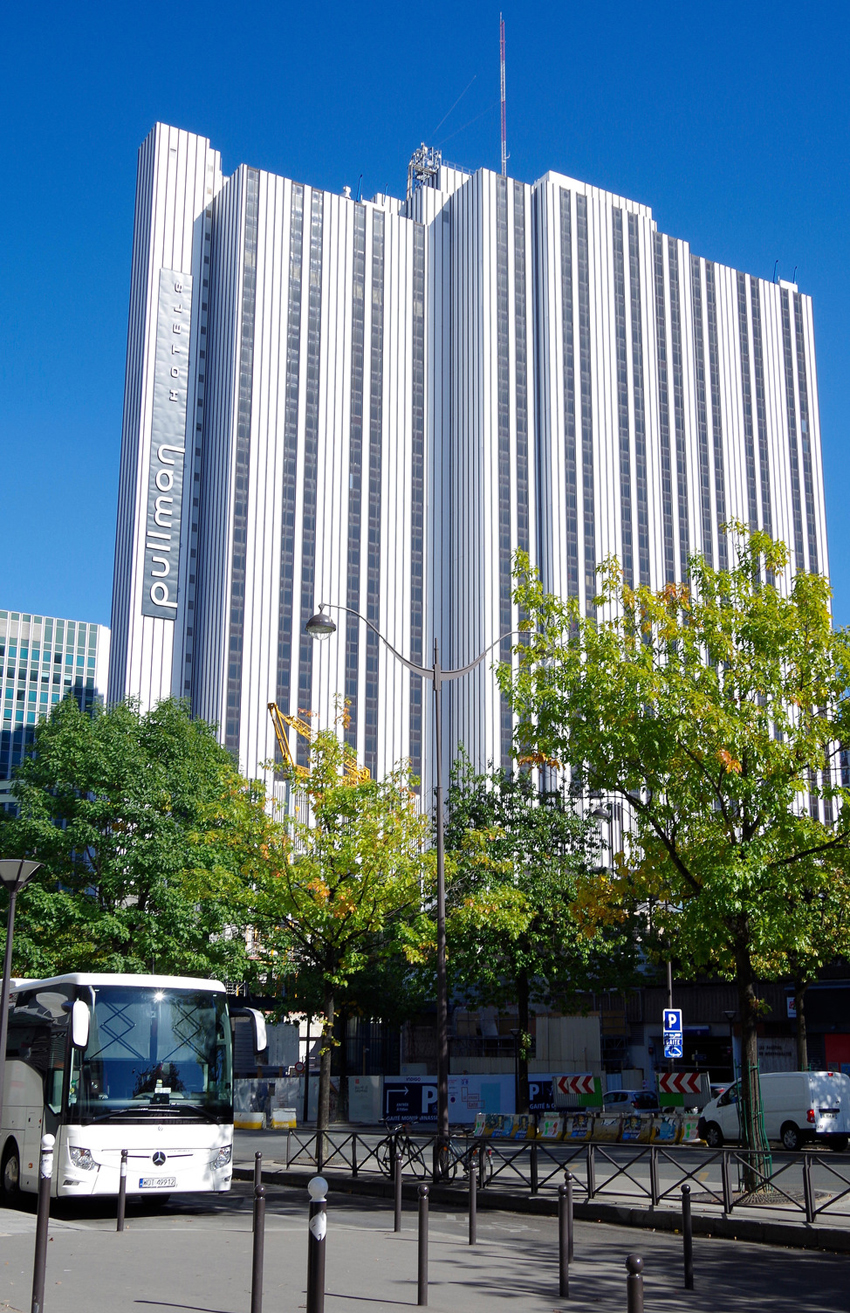
A true test of PVF film’s capabilities is in real-time examples, such as the Pullman Hotel Montparnasse in Paris, France, whose laminated exterior has not had to be updated since it was built in 1974.
PVF Film Resistance: A Flexible, Durable Solution
Around the world, we see buildings that stand the test of time—that appear to remain virtually unchanged for decades. What is their secret? One solution that has helped building surfaces withstand these issues is PVF, a technology that works as a laminate on surfaces. While many other protective coatings, including paint, often fade, chalk, crack, blister, or check from UV exposure, acid rain, or dirt, PVF film has shown to prevent UV degradation and the breakdown of building material due to external forces.
It is a film that makes materials more durable, and it also provides aesthetic properties such as colors and textures that can be incorporated into the design of a building.
Even projects within 1,500 feet of the ocean, including direct oceanfront properties, show resistance to degradation from sea water and salt spray when PVF film is used as an exterior laminate. Its imperviousness to harsh chemicals and its pliability can be fabricated to the tightest of radii without cracks, loss of adhesion, or color change.
PVF film is available as transparent film or in a variety of colors and gloss levels. It is typically applied to the surface of other materials to provide added durability, cleanability, and chemical resistance. It is especially powerful as a solution when it is applied to metal substrates. PVF film is naturally transparent and flexible, enabling its use without the addition of co-resins or plasticizers. It is formulated to provide a desired color, gloss, or special functionality using only inert additives that do not sustain microorganisms such as mold, mildew, fungus, and bacteria. When sterilization is required to remove residual microbes, it has very high resistance to degradation by chemicals and disinfectants for even the most rigorous disinfection protocol.
PVF film can be stretched to more than twice its original length without breaking, which is what makes it highly durable, formable, and resistant to damage. It has been used in architectural applications for decades, preserving the appearance and quality of surface materials, including metal facade and architectural fabric. The flexibility of PVF film allows it to be applied as surface protection to many different angles and surfaces found in a building. It can be used to protect wallcovering, around doors and windows, on ceiling or acoustical panels, case goods, and on graphic signage.
Another architectural application for PVF film is associated with metal bending. Bendability is important to create design elements. But bending can create microcracks in certain coating systems. When PVF film was applied to the metal before it was bent, it was able to keep it from cracking, even at a zero T-bend.
The PVF film material resists fading and corrosion from weather and sun exposure, as well as harsh chemicals and pollution. Its high resistance to the growth of mold, mildew, and bacteria aids the cleanability and durability. In addition, PVF film offers exceptional stain and abrasion resistance. They provide a protective barrier against most staining agents and cleaning solvents, including bleach, alcohols, ketones (acetone, MEK), and even strong acids and alkalis. This barrier ensures staining agents can be easily cleaned, leaving an undamaged, good-as-new appearance that can be maintained over a long period of time.
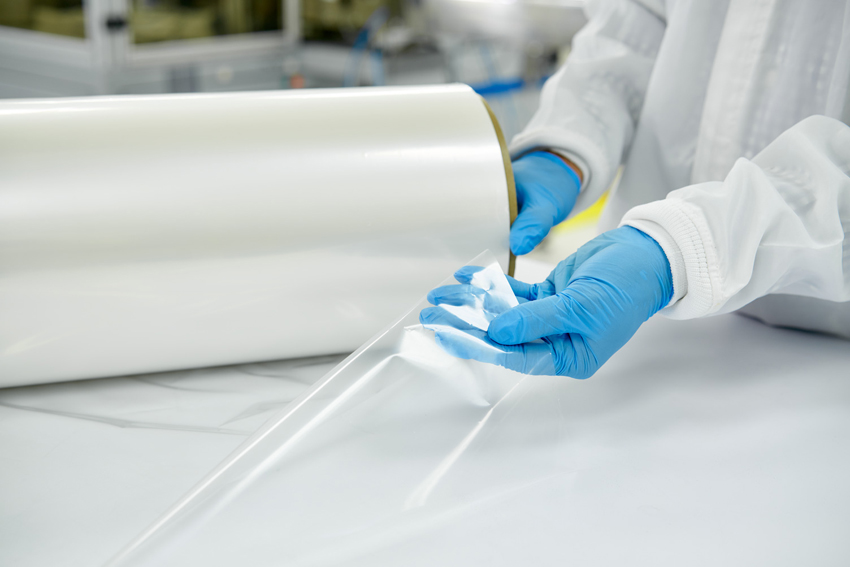
PVF film can be stretched to more than twice its original length without breaking, and its flexibility allows it to be applied as surface protection to many different angles and surfaces found on a building.
Broad Applications: The Film That Goes Everywhere
Long-lasting and resistant to graffiti and pollution, PVF film preserves the appearance of graphics in even the harshest environments, making it the ideal choice for various graphics overlay, outdoor awnings, and advertising signage. Other applications for the film include a wide variety of other industries. The high-performance protective film can be applied to photovoltaic module backsheet in solar panels and for printed circuit boards (PCB).
PVF film applications span a range of industries, including transportation, aerospace, building and construction, graphics and signage, and electronics. In its use in transportation, its easy-to-clean surface and UV resistance are helpful traits on interior and exterior surfaces in vehicles and vessels that are heavily used by people and often exposed to the outdoor environment. PVF film can be applied to automobile interior surfaces and fiberglass-reinforced plastic, and it is used in aluminum board protection for trucks and trailers. It is also an ideal film for covering graphics overlay, advertising signage, and architectural fabric to protect them from pollution or graffiti and preserve their appearance.
PVF film’s use in aerospace applications include interior ceilings and sidewall decorative panels, window shades, stow bins, bathrooms and galleys, moisture barriers, and composite noise panels, among many others. It was even used as a biobarrier for the Phoenix Mars Lander so that bacterial spores that might have attached just before launch would not affect the vehicle’s robotic arm.
The film can be an ideal technology for the construction industry in the form of exteriors because it is lightweight and impervious to harsh chemicals and pollution. PVF film meets several important industry standards. When applied to metal, it exceeds standards in humidity resistance, Florida Weathering Data on Color Change, salt spray test, and pencil hardness. It meets standards in terms of chemical, fire, abrasion, and fade resistance, and it is UL GreenGuard certified for mold and mildew resistance. In terms of building health, it has proven low emissions of dangerous volatile organic compounds (VOCs). Its durability means that it is less likely to need maintenance, which reduces costs for a building owner.
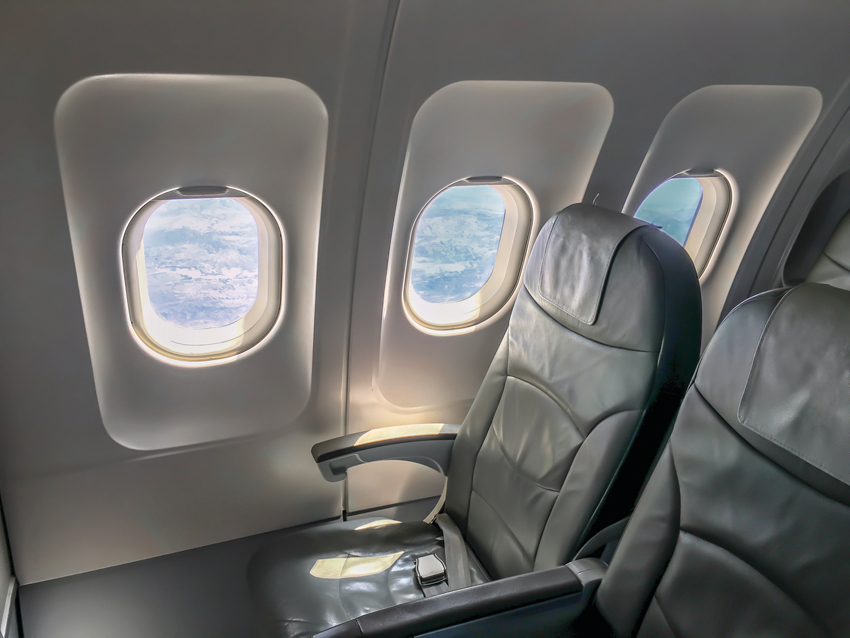
PVF film’s use in aerospace applications includes interior ceilings and sidewall decorative panels, window shades, stow bins, bathrooms and galleys, moisture barriers, and composite noise panels, among many others.
Coverage and Uniform Thickness Impacts During Lamination
There are many ways to cover a substrate for the exterior or buildings. Paint or coatings are one choice used for covering certain materials, of which polyvinylidene flouride (PDVF)-based coatings are commonly used for protection of metal.
The advantages of PVF film begin even in the production process when the film is being laminated onto a substrate. In all instances where a metal substrate is being treated with a protective coating or film, it is vital that three aspects of the process work together in the highest-quality way possible. These aspects are: preparation of the substrate, the quality of the exterior layer material, and the application process.
In most instances, the substrate needs to be thoroughly cleaned, the material used for lamination or coating needs to be of super-high quality, and the application process needs to be done well so that the coated substrate is covered in a uniform manner for both strength and aesthetics.
In the case of applying paint to a substrate, for instance, the substrate would need to be cleaned so that the paint does not clump or pit on the surface. The paint itself should be of high quality so that it does not run and create uneven coverage and thickness. And the application process needs to be done carefully so that the paint is even with a consistent color appearance across the entire substrate. These three aspects must all work together to form a painted substrate of the highest quality—one that looks aesthetically pleasing and will not need to be replaced in a short period of time.
When it comes to laminating a substrate with PVF film, it is easier to get high quality because the benefits desired for a protected substrate are inherent in the film. PV film provides 100 percent coverage because it is a continuous plane that has no holes or means of cracking. It can cover areas that even the highest-quality paint cannot. In fact, high-quality paint, since it does not run, can leave uncovered holes on the substrate, giving it a pimpled complexion.
PVF film also provides all the properties that would be needed to obtain UV resistance and mechanical resistance. This is regardless of the application process and regardless of the preparation of the substrates. The film is customized to have the optimum surface adhesion and also has a uniform thickness and uniform color, which is something the quality control of the film ensures. These aspects are already built into the protective film.
The film also comes in a broad array of colors and other aesthetic qualities. And because it is a film, it is easy to have a direct gauge of the aesthetics of the film before it is applied, which, unlike paint and other coatings, will not depend on the application process. The film also already has corrosion and fungi protection built into it.
Not all films have the characteristics necessary to achieve the best exterior protection. PVF film has UV resistance, fungi and bacteria resistance, and water resistance—meaning that it will not react with water. It features temperature resistance between -94 degrees Fahrenheit to 320 degrees Fahrenheit, and it is chemically inert, meaning it reacts to no solvent. So, if someone writes or paints on it, a solvent can be used to remove the writing or painting, restoring the surface to its original, pristine condition without damaging the surface. PVF is also a compliant polymer, which means it has some amount of elongation to it. If it is applied onto a metal substrate and the design calls for shaping the substrate, it can be bent—even achieving a zero T-bend—without damaging the film.
Design Elements of PVF Film
A lasting facade is important, but if an exterior of a building cannot keep up with aesthetic trends, its preservation is harder to justify. PVF films preserve exteriors but also lean into current color and texture trends, providing flexible styles and conforming to the vision of a building’s architecture. This section will look at color and texture opportunities with PVF film and provide a case study for a PVF film aesthetic success story.
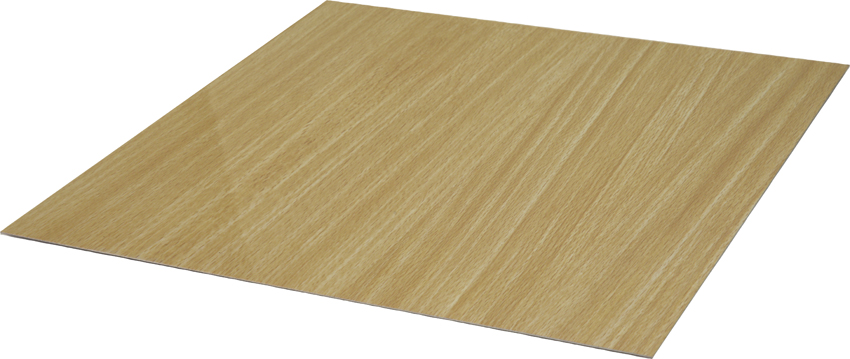
PVF film can be used to create textures that look like leather, wood, stone, metal—stainless steel and chrome—or other designs.
PVF Film Design Possibilities with Color and Texture
PVF film comes in a range of colors with the diversity of household paint. Examples of colors include gray, sandstone, green, blue, cream, bayberry, and sand. PVF film’s color uniformity and fade resistance means that one can match architectural elements and count on long-lasting color, thanks to PVF film’s durability and ability to be cleaned. The fact that fading is not an issue with PVF film means that even if a design element needs to be replaced or added, matching colors is not difficult.
Another design benefit of PVF film is the ability to add texture to color to emulate other materials. During the process of lamination, transfer papers can be used along with the film to create textures that look like leather, wood, stone, metal—stainless steel and chrome—or other design elements. This capability is as desirable for interiors as it is for exteriors, especially when furniture such as kitchen cabinets, panels and flooring, ceiling, window, or door surfaces, and trims might benefit from design details that still require a certain level of durability because of heavy use.
In the paint world, pearlized additives commonly add dimension to a surface and even create a light-bending effect that results in a softer glow in a room. Pigments can be added to PVF film dispersion prior to casting, which can create the same pearlized look in the film when it is laminated to a substrate.
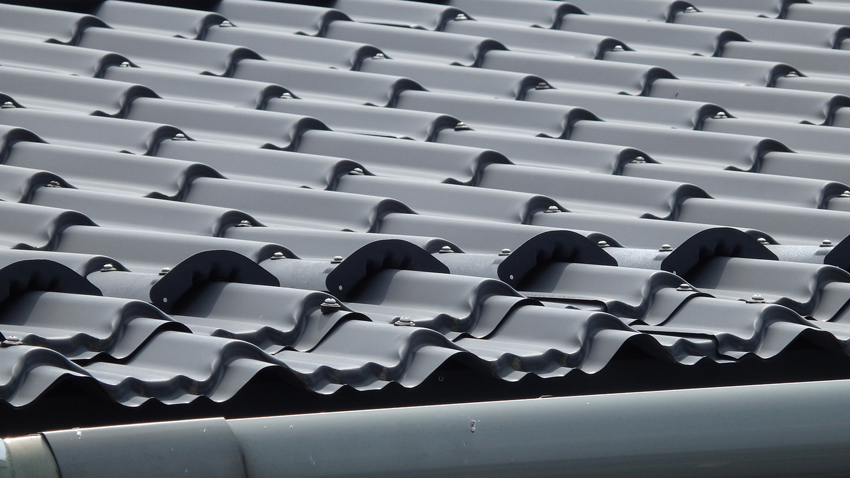
When selecting materials for construction, it is important to consider the surrounding environment and select the best possible material. PVF film protects substrates and roofs, like this railway rooftop in Japan, which has not needed to be replaced for 30 years.
Case Study: Colored PVC Film
A covered stairway at the Komoro Station railway in Nagano, Japan, is made with steel roof tiles laminated with colored PVC and specially shaped by press machines. The frontside and entrance of the stairway has colored ceramic tiles installed in 1994, the same year as the metal PVF rooftop on the stairway corridor. Color-matching of the ceramic roof tiles and the formed metal roof tiles with colored film—two very different styles of architecture—has withstood more than two decades of exposure to harsh weather conditions and heavy snow in Japan’s Northern Alps without showing any signs of corrosion, fading, or wear and tear.
Sublimated PVF Film Designs
Dye sublimation is a digital printing technology that allows for reproduction of colorful images on surfaces. The high-resolution quality provides something of a tattoo on architectural materials, including panels. (imagine having a color-saturated photograph embedded on a wall for a more personal effect). High-resolution dye sublimation inks can be diffused into PVF film to create these effects. Because it is in the durable and resistant film and not on the direct surface, the high-resolution image is encapsulated and protected by the clear film, making it a permanent design feature.
In the same way, sublimated dye can be diffused with clear PVF film and combined with embossed textures to create surfaces that resemble wood and stone. These high-resolution images can be uniquely created for a personal touch that does not feel like it was bought in a store.
Thermoformable Film and Conductive Inks
Some PVF film design features serve a functional purpose. Thermoformable film allows PVF film to be treated with heat and adhered to partially polymerized composite material that is not flat. The composite resin acts as an adhesive; the adherence between the material and PVF film is obtained through two pressing stages and a heating procedure. This process works well with small concave or convex radial shapes. For example, metal roofing that has dips and curves and needs to resist cracking can benefit from the PVF film thermoform process. But PVF film can also offer color and texture elements for design.
Conductive inks are another element that can be used with PVF film to provide both aesthetics and function. Conductive ink is created by infusing graphite or other conductive materials into ink. It combines the ability of conduction electricity with the utility of ink and is sensitive enough to capture energy created by the touch of finger. It is one way that a surface can be used to control an array of technologies. Conductive inks can be printed directly on the back of PVF film and then laminated and thermoformed, enabling lighting, temperature, and volume controls by way of touch.
Selecting Materials with Environmental, Durability, and Maintenance in Mind
Selecting durable building materials from the beginning of a building project benefits the structure’s lifetime, and it especially impacts building owners in terms of financial costs and savings. This section will explore how reducing the need for renovations and maintenance leads to both lower costs and better sustainability elements.
Selecting for Environment
When selecting materials for construction, it is important to consider the environment around you, including what problems may affect the material you choose. Living near the coast means you might encounter more salt and moisture, which leads to corrosion—one of the main causes of deterioration in coastal construction projects. Accelerated corrosion of reinforced steel will ultimately expose concrete and other materials that are vulnerable to the elements. This will weaken them and lead to safety hazards and high-cost maintenance. If you are on the coast or near other large bodies of water, flood and wind also can lead to major repairs.
If you live on the East Coast of the United States, you might encounter more issues with acid rain, which also can speed up corrosion and completely degrade other materials over time. An array of particulates can have similar impacts, and big cities and towns with polluting industries will see the most damage to their building structures. Even considering things such as graffiti or other situations where a building might be affected by chemicals can help inspire a better choice in materials to resist these assaults and last into the future.
PVF film can be laminated to make it resilient to physical damage, chemically inert, UV light reflective, flexible to handle thermal changes, and permanently adhere to substrates to help defend against many of the problems associated with the human environment.
Case Study: Wembley Stadium, London
Wembley Stadium in London is iconic for epic matchups and known for hosting extremely passionate fans. But above all of the action on the field is another tough player: PVF film. The stadium features more than 50,000 square feet of rooflights that are protected with a UV-blocking PVF film in order to provide resistance to weathering as well as outstanding chemical and pollution protection. The rooflights cover and brighten a significant area of the stadium directly beneath its iconic arch, providing 70 percent transmission of diffused natural light. The PVF film significantly reduces UV discoloration and weathering, which means that the stadium rooflights will look as good as the day they were installed—likely for more than 30 years.
Accelerated Tests and Real-World Examples
The high performance of PVF can be verified in accelerated testing in laboratories, simulating chemical, weather, and abrasion resistance. However, the real test for PVF—which has been around for four decades—is in the real world. This section will discuss results of lab tests and offer a case study that provides a clear illustration of PVF's success.
Lab Testing and Resistance
PVF film has extremely high chemical resistance and compatibility with acids, bases, oxidizers, and a variety of solvents, including polar, non-polar, aromatic, aliphatic, hydrocarbon and chlorinated solvents, and other harsh chemicals. Even under extreme conditions with high concentrations, extended exposure times, and high temperatures, the PVC film retains all or most of its original properties and appearance. In a series of accelerated and long-term lab tests—some of which lasted hours; some months and years—PVF was immersed various times between 77 degrees Fahrenheit and boiling temperatures in acids, bases, solvents, and miscellaneous chemicals. The result was that there was no perceptible change in either appearance or mechanical properties to the film, except for a slight change from bleach after a month. The tests show both a resistance and compatibility with these chemicals. Though it was not an exhaustive list of all possible chemicals a film might encounter, it was an extensive one using a broad range of chemistries, simulating conditions that were well beyond any real exposure conditions that the film would endure in the real world, demonstrating its extreme robustness.
In other lab tests, PVF proved to be impermeable to greases and oils. This makes the films easy to clean because so many staining agents remain on the surface of the films rather than seeping into the material. They can be easily removed by cleaning without the cleaning process leaving behind shadow ghosting streaks.
When stain removal is necessary—and it is probably necessary in any industry—PVF film offers one solution to address staining so that materials do not need to be replaced. It has excellent resistance and is easily cleanable. In one test, a variety of potential staining agents were placed on the surface of PVF film and left for 24 hours prior to cleaning. The residue was then wiped first with a dry cloth, followed by a wet cloth, then mild detergent, moderate household solvents such as isopropyl alcohol, and finally as needed, stronger solvents such as acetone, toluene, or MEK. After the test was done, the PVF film had no changes in appearance or mechanics.
Stains come in all kinds of forms, including food and drink, household items, or even chemicals. Each stain removal may require a different cleaning agent, and each cleaning agent has a different chemical makeup. Since PVF films can be compatible with many aggressive solvents, an entire range of cleaning products can be used without worry of permanent material damage. This includes even the harshest cleaners found in industrial applications for tough stain and graffiti removal.
Cleaning removes dirt, debris, and other matter from the surface of the film, but it often does not kill bacteria, viruses, fungi, or other pathogens that can persist on the surface. In many public areas and especially health-care settings, proper disinfection after cleaning is vital to ensuring public safety and controlling the spread of disease. Disinfection is most often performed by exposing surfaces to chemical disinfectants, but sometimes it is also supplemented with exposure to UV light. When used on PVF film, chemical disinfectants should be employed as described on their labeling.
Resistance to mold, mildew, and fungus also was tested in labs using two standard tests. ASTM G21, the standard practice for determining resistance of synthetic polymeric materials to fungi, was conducted by placing samples onto the surface of nutrient agar and spraying it with a mix of spore suspension made up of five fungal strains: Aspergillus brasiliensis, Penicillium funiculosum, Chaetomium globosum, Trichodermavirens, and Aureobasidium pullulans. These samples were incubated for four weeks and observed at the end of each week. Agar has everything it needs in terms of trace nutritional elements to support fungal growth, but in order for it to work, it needs a primary carbon source. The PVC would need to provide that nutrient source for any microorganism to grow. However, even after the four-week test, the PVF film only showed trace growth—not enough to sustain substantial growth or fungus, mold, or mildew.
UL 2824, the standard method for measuring microbial resistance for various sources using static environmental chambers, is a part of the annual UL GreenGuard Certification Program that recognizes products exhibiting superior performance for indoor air quality. In this test, the PVF was placed in a sterile petri dish and inoculated with a known concentration of Penicillium brevi-compactu. The dish was placed in an environmental chamber at 95 percent humidity and 77 degrees Fahrenheit for three weeks. At the same time, a positive control sample susceptible to fungal growth was run as a test to verify microbial activity. Colony-forming units (CFUs) are counted at the beginning and end of the test, and a rating is provided. The PVF achieved the highest rating, showing its high resistance to mold growth.
PVF films are created without plasticizers, processing aids, or other additives that can be a nutrient source for microbes. They also do not appear to support bacterial growth, even in tests where they are placed in agar inoculated with Pseudomonas aeruginosa. In this test, the samples and negative control samples were incubated for 28 days at 82–86 degrees Fahrenheit and evaluated for visible evidence of growth. The results showed there was no growth on or around all five replicate samples, showing the specimens do not contain nutritive components for this bacterium.
While PVF films do not contain nutritive components that support the growth of mold, mildew, fungus, and bacteria, microbes still can find their way to the surface of the material from the environment. To eliminate these microorganisms from the surface, the surface must be cleaned and disinfected. PVF films have outstanding chemical resistance and durability to withstand repeated cleanings with even the harshest chemicals and disinfectants. The resistance of PVF films to several common disinfectants used in a health-care setting was proven. The surface exhibited no cracking, delamination, or changes in either color or gloss after five days of continuous contact. The resistance to growth of mold, mildew, fungus, and bacteria is complemented by the outstanding chemical resistance and ease of cleaning and disinfecting. This combines with the durability, versatility, and timeless aesthetics to provide unique surface protection with unparalleled performance, both indoors and out.
Finally, it was important to test how much water might have a chemical breakdown effect on PVF films over time, considering rain and snow conditions and especially places with extreme precipitation. In one hydrolysis resistance test, the PVF was run through an accelerated stress test at 250 degrees Fahrenheit and 100 percent relative humidity. Even after 100 hours of this harsh environment, the films showed no change in mechanical properties or color. In another longer-term test, the PVF was exposed to 185 degrees Fahrenheit and 100 percent relative humidity for 4,000 hours. Afterward, the films showed very little change in mechanical or color stability. The tests showed PVF films do not readily absorb water and are highly resistant to degradation by way of hydrolysis, even under extreme and unlikely weather.
A True Test of Time Case Study: Pullman Hotel, Paris
This skyscraper hotel located in central Paris—designed by Pierre Dufau et Associés and built in 1974—has had several different owners, from the Sheraton to the Méridien, before finally becoming the Pullman Hotel Montparnasse in 2011. The hotel’s interior has gone through some major changes to refurbish it and keep it from falling into disrepair. In 2020, it went through a 24-month renovation that modernized the hotel’s 953 rooms as well as its meeting center and common areas, bringing it back to life and updating its overall look.
But the exterior of the 31-story hotel has remained the same since it was built. Its 18,000-square-meter facade features steel cladding laminated with PVF film. It is shaped into vertical, angular lines that seem to reach toward the sky and gleam in elegant silver. The PVF application of galvanized sheet steel laminated with white film installed when the hotel was built remains untouched—no sign of the yellowing, chalking, or corrosion seen on metal without PVF. This has allowed the hotel to maintain its original style and beauty for generations as a recognizable Parisian landmark—with no substantial cost to the hotel’s many owners.
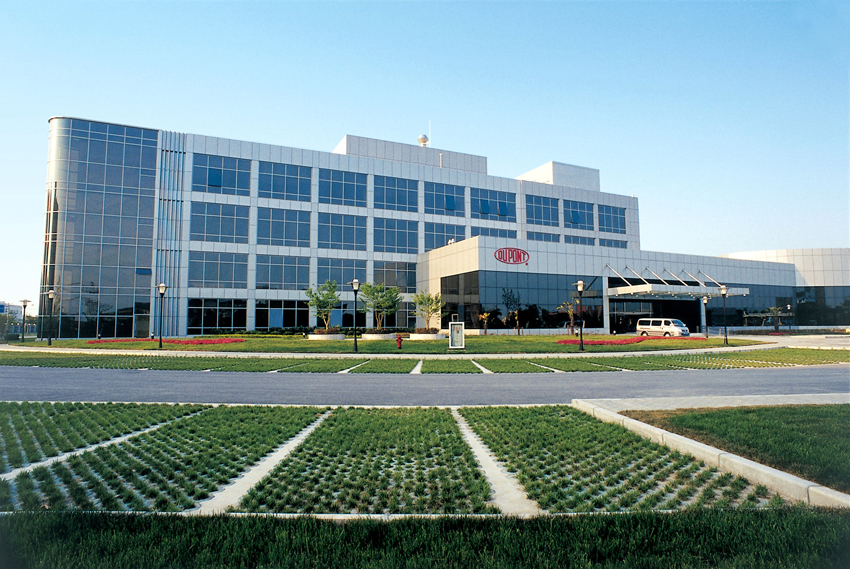
PVF film resists chemicals, abrasions, mold and mildew growth, and can be cleaned by disinfectants without showing signs of harm—and in terms of exteriors, it provides the kind of durability that a building needs to operate in a cost-effective manner.
Conclusion
Environmental issues, including pollution and weather, can lead to corrosion of building exteriors over time, requiring extra cost for maintenance and a shorter building lifespan. PVF film is a technology applied to surfaces of exterior and interior materials of buildings to help protect them from added costs. As a thin, lightweight material that resists chemicals, abrasions, mold and mildew growth—and can be cleaned by disinfectants without showing signs of harm—PVF provides the kind of durability that a building needs to operate in a cost-effective manner.
PVF requires knowledge in the manufacturing process to make sure that it is applied correctly using heat and adhesive. From the consumer point of view, choosing materials with PVF that suit a building’s environment is important to be able to provide the preventative benefits PVF promises.
In the greater AEC world, PVF holds a lot of promise, not just in terms of protecting structures, but also by providing design elements that meet the aspirations of architects and customers. The design potential of PVF is far reaching, and the ability for the film to preserve its own aesthetic value even decades later makes it both a cost-effective and environmentally friendly option.
Erika Fredrickson is an independent writer and editor focusing on technology, the environment, and history. She is a frequent contributor for continuing education courses and publications through Confluence Communications.