Moisture Durability, Roofing and Green Standards
A review of changes in codes, examples of roof and vertical assembly integrations, and tools to assess potential moisture challenges
Continuing Education
Use the following learning objectives to focus your study while reading this month’s Continuing Education article.
Learning Objectives - After reading this article, you will be able to:
- Apply recent changes in energy codes to building enclosure roof and wall assemblies for improved energy efficiency.
- Evaluate effectiveness in existing green standards for a project’s long-term moisture durability regarding the scope and impact to the building enclosure.
- Identify how to utilize and supplement various green standards across the various project phases, including design and material selection, construction-related activities, field performance testing, and Building Enclosure Commissioning (BECx).
- Apply examples of best practices and tools to assist in designing energy-efficient and durable roofing and building enclosures.
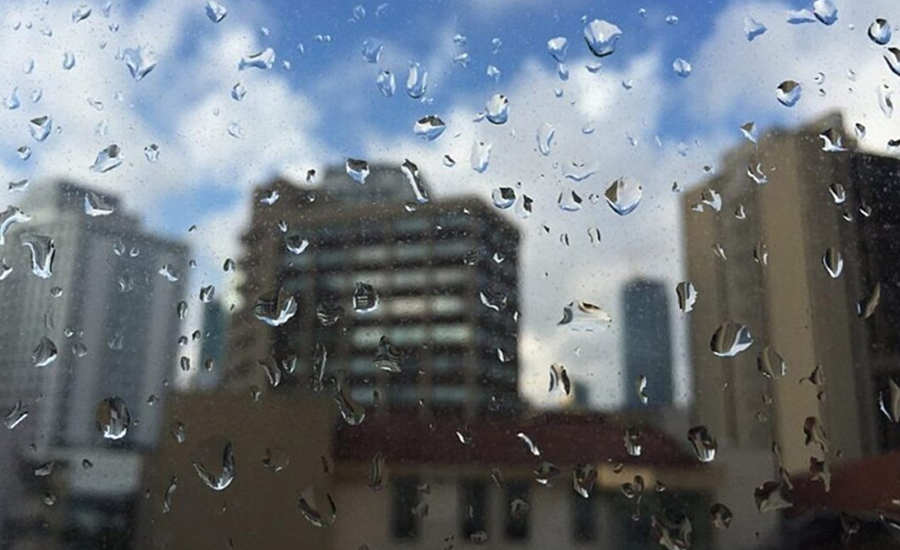
All photos courtesy of GAF
The requirements in green standards alone, such as LEED, Green Globes and IgCC may lack comprehensive measures to address resiliency related to the long-term performance of the building enclosure. We will review changes in codes, examples of roof and vertical assembly integrations, and tools to assess potential moisture challenges to enable energy-efficient and durable enclosure assemblies.
Part 1—Context
Recent changes in building model energy codes include envelope criteria that minimize building enclosure thermal loads and, in turn, reduce a building’s energy consumption. These changes require modifications in traditional building enclosure designs to meet evolving energy code requirements. Unfortunately, some energy-efficient designs, while code compliant, may adversely impact a building’s durability.
The minimum requirements in green standards alone, such as LEED, Green Globes, and IgCC may lack comprehensive measures to ensure long-term durability of the enclosure assemblies. Optional and required credits included in green standards are beginning to address moisture durability and, in this article, are compared regarding the scope and impact of the building enclosure, across the project phases:
- Material Selection
- Design & Procurement
- Construction Activities
- Performance Testing
- Operation & Maintenance
- Enclosure Commissioning
This article reviews various aspects among the green standards including gaps and similarities in the rating systems, and strategies to utilize the best parts of each rating system to improve project performance related to moisture durability. Detailed roof system examples will also be provided, demonstrating how these measures can enable energy-efficient AND durable enclosure assemblies.
GREENBUILDING
There can be a perception in the market that a “green building” is a better building, and that the risks associated with “building differently” are inherently covered by the green certifications driving the industry forward from a sustainability standpoint. Both better buildings and risk mitigation can be accomplished through building green, and this article will discuss some of the key principles to accomplish this for building enclosures and roof assemblies.
Moisture durability of enclosure systems focuses on the interaction of the materials, assemblies, and their design configurations in the building. The goals of managing moisture durability are to establish performance expectations, allow enclosures to perform as intended as well as continue to perform through the project lifecycle, and be serviced or maintained in a way that minimizes risk of damage to the enclosure and performance of other critical building systems. This discussion focuses on the moisture durability aspects of buildings and how they relate to energy performance and lifecycle expectations. While other aspects of resilience are also important, moisture durability targets risks that are not necessarily related to climate change, yet are related to the design of enclosure and roof assemblies directly.
MOISTURE DURABILITY IN CONTEXT
The American Institute of Architects (AIA) defines resilience2 as “mitigating risk for hazards, shocks, and stresses and adapting to changing conditions.” Resilience goes beyond the minimum code requirements to address issues that influence long-term performance. The “hazards, shocks and stressors” can come from external sources as well as from the design decisions of the built environment. Some external sources can be extreme events such as tornadoes and wildfires, and some are common and persistent adverse events from design decisions, resulting in moisture risks in the building enclosure. This perspective of moisture durability as a risk fits within many existing terms and goals that stem from Sustainability, Resilience, Adaptability and Mitigation initiatives; moisture durability fits within these goals and is not separate from them, as demonstrated in Figure 1.
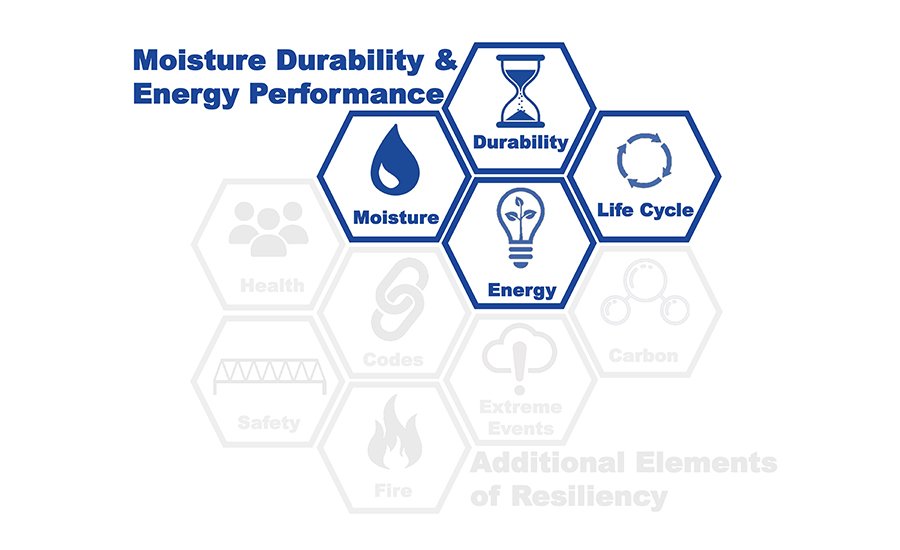
Figure 1. Moisture durability and energy efficiency are part of resilient design.
Part 2—Complexity
ENERGY EFFICIENCY IS A MOVING TARGET
The minimum or baseline energy efficiency in the code requirements and owner’s performance expectations have been a moving target over time. The cost-effective and validated energy savings has increased in each of ANSI/ASHRAE/IES Standard 90.1 (ASHRAE 90.1) three-year publications, which is one of the underlying national energy standards.3 The ASHRAE 90.1—2019 version was validated by the Pacific Northwest National Laboratory as an additional 5 percent of savings over the previous 2016 version.17
Compounding the energy savings, green building rating systems generally require additional savings beyond the baseline and provide points for exceeding the baseline. In addition, the energy performance requirements within green certification systems are also improving. As an example highlighted in Figure 2, the same energy savings that would have contributed 10 points to the LEED v3 rating system is roughly equivalent to the starting energy savings required in LEED v4.1, which is in the pilot phase13 at the time this article was published. Not every local jurisdiction adopts the same base model codes and standards at the same time and rate, which leads to additional confusion in the design and construction industry.
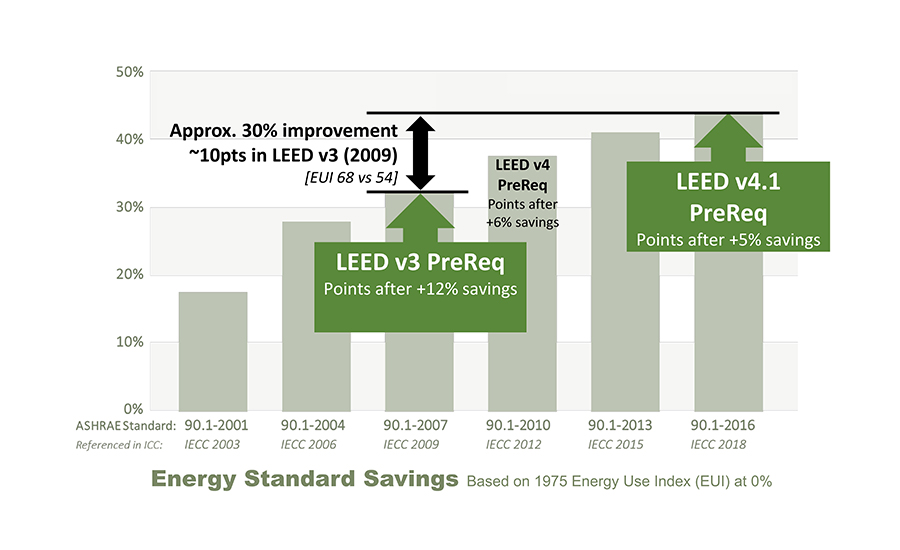
Figure 2. Increasing efficiency requirements are compounded by green rating systems.3, 7
INTERACTIVE COMPLEXITY AND TIGHT COUPLING
The book Normal Accidents by Charles Perrow explains how significant technological advancement can lead to failures.16 Perrow describes two main components of “normal accidents.” The first component being “interactive complexity” as a function of the number and degree of system interrelationships; when this factor is high… surprises are to be expected. The second component is “tight coupling,” the degree at which initial failures can concatenate rapidly to bring down other parts of the system; the more highly-linked… surprises are not easily isolated and resolved. If a system has only one of the two components then it is still a risk, but is more easily managed. When “interactive complexity” and “tight coupling” are combined, accidents could be considered “normal” or expected according to Perrow.
As more materials and additional requirements are added to enclosures, it is important to recognize when materials and assemblies need to change in order to achieve higher energy performance. In a broad sense, as energy efficiency is improved in building enclosures, moisture risks can increase from decreased heat flow across the assemblies, as shown in Figure 3. The changes in enclosures can manifest as generally lower exterior surface temperatures (during heating months) as the exterior is less dependent on the interior space conditioning. As we improve energy efficiency, we may also be increasing moisture risks in building enclosures. And the increased risk of “normal accidents” may result from more complex designs that are more tightly coupled to the building’s HVAC operations, structural elements, and occupant-use conditions.
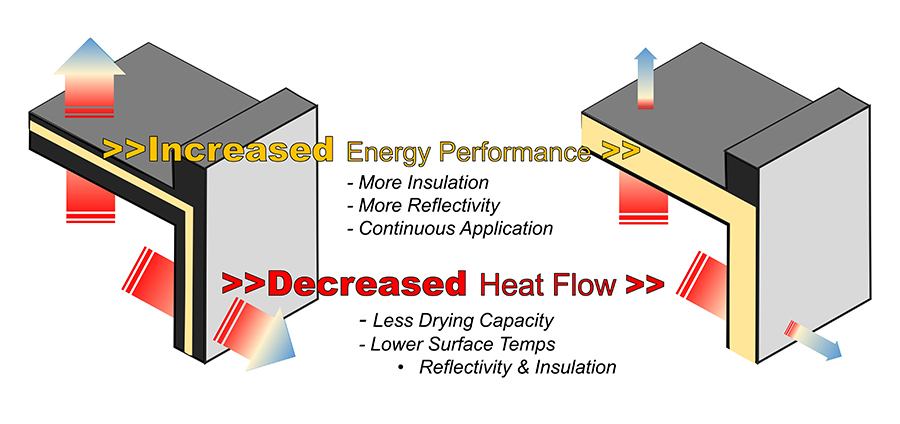
Figure 3. Energy efficiency improvements can lead to increased moisture risks in a building enclosure.
Consider the following real-world example of the “normal accidents” concept in practice and how it relates to a client’s awareness of or willingness to accept this risk for an innovative building. This relevant example comes from the first-ever LEED platinum building and a recently closed legal case.14 The example demonstrates the building enclosure’s technical complexity and tight coupling across various building systems. In the court’s findings, the decision lays out the framework mirrored in Normal Accidents stating “the inappropriate use of Parallams as structural support without proper weather protection”—it’s a complex system—and “these beams would have failed… well before they got around to doing any remedial measures at all.”—the systems are tightly coupled.
The concept of predictable outcomes from Perrow’s book makes sense in theory, but in practice, it can be complicated as this case demonstrates. Such case studies help bring awareness to potential issues and highlight the importance of establishing processes to manage the unanticipated moisture risks as early as possible. It is important through this green rating system assessment to recognize the options and limitations that exist with the rating systems and their actual coverage to mitigate moisture risks in the face of complexity and system coupling.
COMPLEXITY AND COUPLING IN ROOFING
In the article “Structural Concrete Decks, Vapor Retarders and Moisture—Rethinking What We Know” in the February 2020 issue of IIBEC Interface,20 the authors provide a clear example of how increasingly complex structural systems can have detrimental effects on the interconnected performance of traditional roof system.If a roof designer is worried about interior moisture vapor drive impacting a low-slope roof system, a traditional rule-of-thumb would be to add a self-adhered vapor barrier to the roof deck, prior to installing the roof insulation and membrane. But what if changes to the roof structure greatly increase the risk of adhesive failures that lead to assembly failure in these systems? As the authors of the IIBEC Interface article note:
- “The concept of cost of failure is critical to understanding the potential magnitude of the issue… if a concrete deck does not dry or retains moisture and the [rule of thumb] solution to address this condition does not work, the cost of failure is generally high.”
The authors identify the causes of the increased moisture risk over the last 30 years in roof systems come from two key changes in roof structural design. The first is the increased use of non-removable forms or composite steel and concrete decks. These decks allow for much shorter construction timelines, eliminating much of the expense of building and stripping temporary form structures, and are very structurally efficient. But by leaving the steel formwork in place at the bottom of the concrete slab, the concrete mix water has limited opportunities to dry out after the curing process is complete.
The second key change in roof structural design is the increased prevalence of lightweight aggregates in the concrete mix of roof slabs. Originally thought to only be a problem with lightweight structural concrete, recent research also raises concerns with moisture migration from normal weight concrete decks as well.21 The authors describe the added complexity:
-
”The use of lightweight aggregate that can hold more initial water than traditional ‘hard rock’ aggregate, combined with the use of metal forms that are left in place, has resulted in a significant likelihood of having to deal with what should be considered a ‘wet deck.’”
With both of these added complexities to the roof structure, non-removable forms and lightweight aggregate, the moisture retained in the concrete creates a new challenge that needs to be addressed to ensure the installed roof system will perform. Specifically, the logistics of applying a self-adhered vapor barrier to a “wet deck” are very problematic. It is unlikely that the bond would be sufficient over time as the moisture migrates out of the roof concrete slab over a period of years. To make matters worse, often subsequent layers of roof insulation and roof membrane are also adhered together, relying on the initial self-adhered vapor barrier’s bond to the “wet deck” to attach the entire roof system.
Due to the added complexity of the structural design and the interconnectivity of the structural system and the roof assembly, the authors state, “the standard of care may not be enough.” They go on to provide six alternate design configurations and attachment methods to navigate various scenarios and the attachments, assembly layers, and the fundamental physics that are at work across the interconnected structure and roof systems. Figure 4 is an example of one of the scenarios provided, with the non-traditional design elements highlighted in red for clarity.

Figure 4. Example of added roof complexity from evolving structural designs.
This example demonstrates the challenges of seemingly small and incremental changes in complexity that can have a dramatic impact on interconnected systems, like concrete structures and roofing assemblies. The first challenge for designers is to recognize that the increased risk of moisture exists when designing roof systems with potentially “wet decks.” After identifying the increased risk, the design should be detailed to manage the potential for moisture from the concrete and/or decouple the concrete structure and roof system.
Part 3—Project Phases
MOISTURE MANAGEMENT ACROSS THE PROJECT PHASES
It is tempting to assume that the building enclosure will work perfectly and water won’t get where it doesn’t belong. Such a belief can lead to a lack of risk mitigation from a very likely hazard (water) throughout the useful life of the building. A more realistic mindset is—moisture intrusion cannot be completely avoided, it must be managed. Enclosures should be designed and installed not only to keep out bulk water and drain it away, but also to manage incidental water with minimal long-term impact. The key is for the enclosure design to have a greater capacity for drying than its risk of wetting.15
This moisture durability assessment looks at six primary categories for an enclosure. Roughly working across the project life-cycle, they are shown in Figure 5, starting at the bottom:
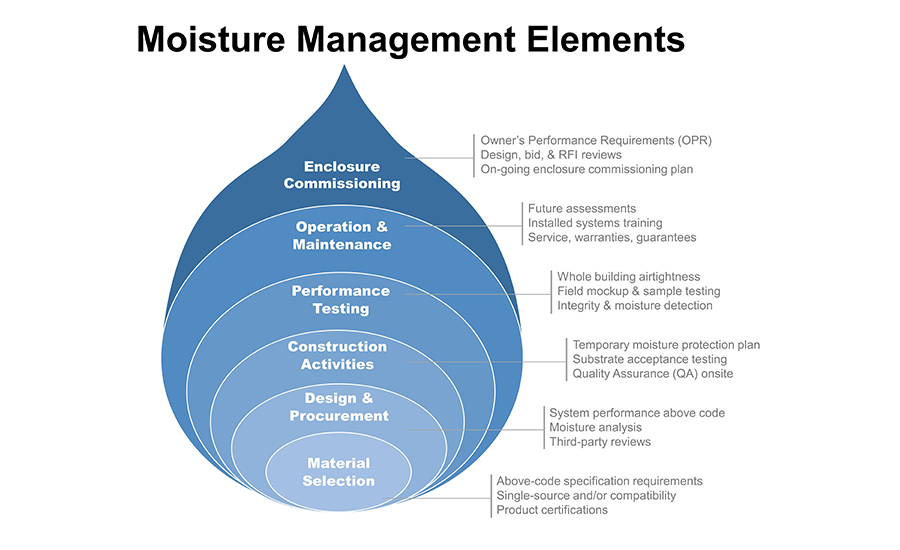
Figure 5. Moisture durability elements and assessment project life-cycle details.
There are a number of aspects to manage moisture risks in this phase that green building rating systems can address. Below is a brief summary of the elements highlighted in this assessment:
Material Selection
The material selection phase can start early in the project process. It can often carry over into a firm master specification, or even be dictated as a line-item budget before the schematic concept is complete. Improving material selection can include above-code specification requirements, such as exceeding minimums for attachments and roof edges, dedicated air barriers, and material properties like solar reflectivity. Single-sourced manufacturer systems for building enclosures don’t mean only specifying one manufacturer per product, but it does mean to consider the bids for all components within an enclosure system, like a roof, and their ability to properly integrate with adjoining systems. In a roof system, all of the components such as the membrane, cover board, insulation, air/vapor retarder, and structural deck are tested by third parties as a system, and should really be specified as a system, not separately. Coordinated manufacturer systems can be key to installed performance, such as prior system testing and single-source responsibility for future service and repair. Third-party product certifications, such as HPDs and EPDs, can be useful in the product selection process for green building ratings, but unless the product certification addresses performance in specific applications, it may not address moisture durability.
Design & Procurement
In the design and procurement phase, project teams solidify design decisions and look for unexpected building-system interactions. When it comes to designing an enclosure, the overall system performance becomes really important, such as expected resistance to anticipated extreme weather events and clarifying the expected enclosure system service life. Rather than relying on heuristics and rules of thumb for long-term moisture performance of the building enclosure, performing a moisture analysis can identify areas where “tight-coupling” of moisture mechanisms may be occurring in the building. Specifically, performing ASHRAE 160 Hygrothermal analysis early in the design process allows the outcomes to inform the project team.4,12 Also, engaging professionals for third-party reviews with specific expertise in moisture risk mitigation is important. These can be consultant constructability reviews, manufacturer reviews for conformance with the published requirements, and contractor shop drawing reviews across the enclosure systems.
The inclusion of performance testing can lower the risks related to moisture durability. When these tests are specified with defined pass/fail criteria, the project team is able to vet out performance at the intersection of design and construction. Potential risks, including air and water leaks, are identified early and are able to be addressed before the building is occupied.
Construction Activities
In the construction phase, project teams are bringing designs to reality. During the lengthy process of construction, moisture has a direct opportunity to find its way into areas where it was never intended. To protect the building and the integrity of the enclosure, a temporary moisture protection plan is important. The plan should include measures for material storage and specifications for in-process protection while the enclosure systems, like roofs, are being applied across many weeks or months. When installing materials onsite, rather than in a controlled environment, it is important to identify that conditions are appropriate to proceed. Qualifying the site conditions can be performed by substrate acceptance testing such as adhesion tests, compatibility qualification, and fastener withdrawal resistance methods. Whether it's a system-based verification, or specific third-party auditors, like ABAA Quality Assurance Program (QAP)1 or the IIBEC Registered Roof Observer (RRO)9 programs, having a third-party quality assurance program, aside from the GC’s quality control, can also contribute to managing moisture risks.
Performance Testing
When performance testing is required, it’s important that the owner’s expectations are taken into account early in the design and carried through to the trades in the field. The point of performance testing is not to make buildings “fail” after they‘re built, but to ensure the constructed building meets the initial minimum performance targets set out by the owner and design team when they started the project. A whole building airtightness test is a good example of this. It doesn’t attempt to “over-pressurize” the building, but to uniformly pressurize the enclosure to identify inconsistencies in the overall construction. Stopping these air leaks can enable the mechanical systems to perform as designed during the use-phase of the building, limiting leakage and potential occupant discomfort. Testing can also be performed on a smaller scale with field mockup and sample tests. These can be useful to establish acceptable installation and sequencing methods onsite and provide representative results, rather than the expense of comprehensive testing. Another set of moisture durability tests are integrity and moisture detection testing, such as infrared scans, electronic leak detection (ELD), or nuclear moisture surveys. These can be useful to demonstrate a moisture protection plan was successfully implemented—that there is no concealed moisture, and that systems are continuous where they are intended to manage rain, like in a roof or waterproofing system and at interfaces.
Operation & Maintenance
It’s important to begin recognizing the operational challenges early in the design phase. This could be in terms of future assessments using climate projections, such as an increase in the intensity of rainstorms, and understanding how the project can adapt for changed uses at the end of the building’s expected life, such as capturing rainwater for irrigation. After the completion of the building, and beginning the use-phase, installed systems training is important for occupants and facility managers on the expected operation of enclosure systems, such as the clearing of roof drains and the maintenance requirements associated with rooftop solar. Use-phase training can also include the hand-off of warranties and guarantees from the construction process to the building operators. This is important because it can help inform facility management of ongoing inspection schedules and long-term maintenance contracts necessary to meet the initial design expectations. Like most things, roofs and enclosure systems need to be maintained, and service contracts can be a critical part of scheduling and performing inspections to ensure that long-term guarantees aren’t voided.
Building Enclosure Commissioning
Building Enclosure Commissioning (BECx) isn’t a separate project phase like the previous elements. BECx is a holistic process that starts in pre-design and continues through to the use-phase of the completed building.5 Along the way, the commissioning process can manage moisture risks by identifying “system complexities” and assist a project team to take steps to manage the “tight coupling” of the enclosure and related systems. As part of the project team and across the project phases, BECx can coordinate with the Owner’s Performance Requirements (OPR) through documentation reviews, installation observations, guiding performance testing, and establishing the on-going commissioning plan for the enclosure. When incorporated into the project, BECx can be a great tool to manage moisture durability and the associated risks.
Part 4—Ratings Systems
MOISTURE MANAGEMENT IN GREEN BUILDING RATING SYSTEMS
For the moisture durability assessment, the four most common green building rating systems available for new construction projects are compared against the six construction phase categories as shown in Figure 6. The green building rating systems reviewed are:
- Leadership in Energy & Environmental Design (LEED®), version 4.113
Note: LEED® is a registered trademark of the U.S. Green Building Council. - Green Globes®, version 20196
Note: Green Globes® is a registered trademark of Green Building Initiative, Inc. - Living Building Challenge (LBC™), version 4.010
Note: LBC™ is a registered trademark of International Living Future Institute. - 2018 International Green Construction Code (IgCC®)8
Note: IgCC® is a registered trademark of International Code Council, Inc.
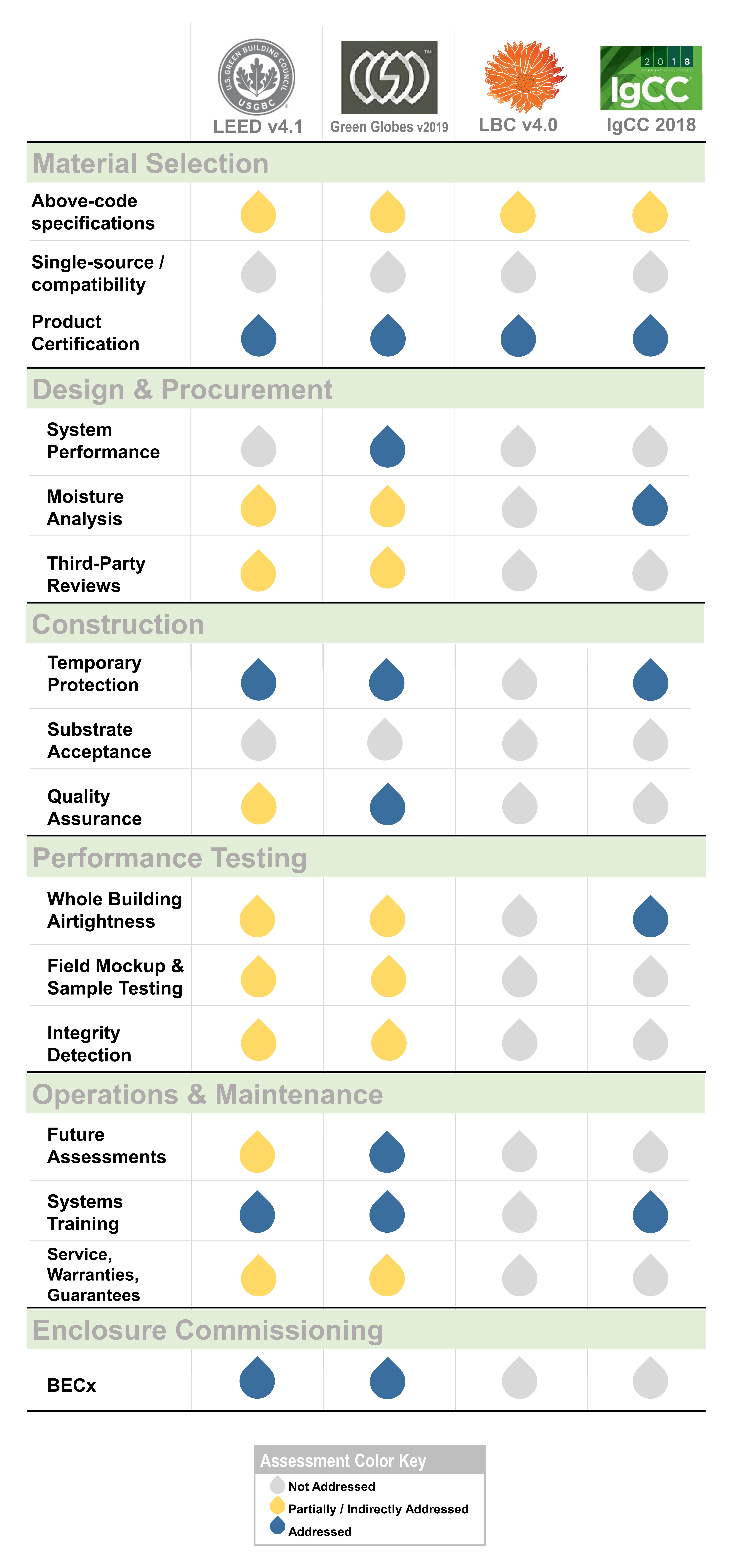
Figure 6. Green building rating systems moisture durability assessment.
SUMMARY OF GREEN RATING SYSTEM ASSESSMENT
Compiled across the typical project life-cycle phases, below is a summary of the notable factors that apply to moisture assessments across the highlighted green building rating systems:
Material Selection
In terms of material selection, there is some consistency across all four rating systems. Starting with above-code specifications in the top row of Figure 5, all four are shown in yellow or “partially or indirectly addressed.” This is because all four have requirements for improved energy efficiency over the code minimum, including light colored or reflective roofing. The enclosure is generally above the code minimum, but there aren’t direct above-code measures related to moisture durability mitigation. None of the four rating systems have measures that encourage comprehensively sourced products to mitigate future risks within and across enclosure systems. Though none are specific to material moisture certifications, all four systems do provide a mechanism to reward products for third-party certifications; these are shown in blue in the last row, indicating this element is clearly “addressed” in the green standards.
Design & Procurement
The design phase is where the specifications can enable success mitigating moisture throughout the later project phases and helping align with the OPR. A number of items in this phase are “partially or indirectly addressed” by both LEED v4.1 and Green Globes through the enclosure commissioning credits; see additional discussion in the commissioning section below. In the Green Globes column, the rating system addresses system performance by providing credit for performing a Building Risk Assessment of the design to resist extreme events. Green Globes also touches on moisture control design analysis, but the credit is focused on managing interior generated moisture, and indirectly includes building enclosure components as part of an ASHRAE Standard 160 moisture analysis when interior moisture is expected. The 2018 IgCC addresses moisture control design analysis directly by requiring all designs to perform dynamic heat and moisture analysis, including ASHRAE 160, of the enclosure and across interior space conditions. The Living Building Challenge, as a rating system, doesn't provide specific or prescriptive moisture mitigation requirements for many aspects of the design and procurement process.
Construction Activities
The construction phase is a period of the building’s life that is often not designed to manage moisture and can lead to a reduced life-cycle if it is not performed well. All green rating programs, except for the Living Building Challenge, include measures to address temporary moisture protection during construction. None of the rating systems have minimum substrate acceptance to provide “stoplight conditions” for enclosure installations, such as moisture on the roof deck. The project specifications and the various construction trades are left to manage these acceptance handoffs. Notably, Green Globes provides direct measures for onsite quality assurance and verification, while LEED v4.1 indirectly captures this scope in its enhanced enclosure commissioning credit. The previous version of Green Globes also included the RRO program by reference but is now described generally as elements of a third-party observations verification program.
Performance Testing
The IgCC is the only one of the four green rating systems to directly address field performance testing by providing enhanced guidance on whole building air tightness testing. The comprehensive testing of the built enclosure can have broad performance impacts on achieving the intended energy efficiency from the design to the field, mitigating ongoing moisture accumulation due to air leakage condensation, and enabling the HVAC design to deliver a comfortable space to the occupants. LEED v4.1 and Green Globes do not include specific measures for performance testing, but they can be a part of the Enhanced Commissioning Credit of the Building Enclosure; see additional discussion in the commission section below. By not identifying scope in the LEED and Green Globes enclosure commissioning credits and minimum performance requirements, field testing can lead to a lot of variation in actual, built outcomes. For this reason, both rating systems are shown as “partially or indirectly addressed.” The Living Building Challenge, as a rating system, doesn't provide specific or prescriptive requirements for performance testing.
Operation & Maintenance
LEED v4.1 includes occupant training directly in the Enhanced Commissioning Credit for the Building Enclosure, but the inclusion of future assessments and specifically addressing manufacturer system documentation is left up to the project team. Green Globes provides additional points for evaluating the building’s “operational continuity” or a “recovery assessment” in the event of extreme weather conditions. Green Globes also provides specific credit for enclosure systems training in the use-phase, and similar to LEED, yet manufacturer system documentation is left up to the project team. The IgCC includes requirements for a detailed Service Life Plan (10.3.2.3), which includes documenting, planning, and providing access to the enclosure elements based on their expected service life. It does not, however, deal with future-use assessments nor specific service, warranty, or guarantee documents of the building enclosure. The Living Building Challenge, as a rating system, doesn't provide specific or prescriptive requirements for the operations and maintenance of the building’s use-phase.
Building Enclosure Commissioning
Both LEED v4.1 and Green Globes provide additional points for enclosure commissioning. It is important to clarify that even though points are being given for enclosure commissioning, there are very few minimum tasks for project teams to accomplish. The decisions about many critical moisture durability aspects are left up to the project team to decide how to proceed. A notable improvement in LEED v4.1 provides additional guidance over the older LEED 4.0 by now referencing ASTM E2947 Standard Guide for Building Enclosure Commissioning.5 This standard provides an exhaustive list of optional performance tests. It’s incumbent upon the designer to establish a minimum scope to vet out project performance and achieve credit for the Enhanced Commissioning Credit. The Living Building Challenge and IgCC do not include requirements or credits to include enclosure commissioning in the rating systems. The IgCC does have a commissioning requirements section, but unfortunately, the building enclosure is not included in the list of “Systems to be Commissioned” (IgCC 10.3.1.2.1).
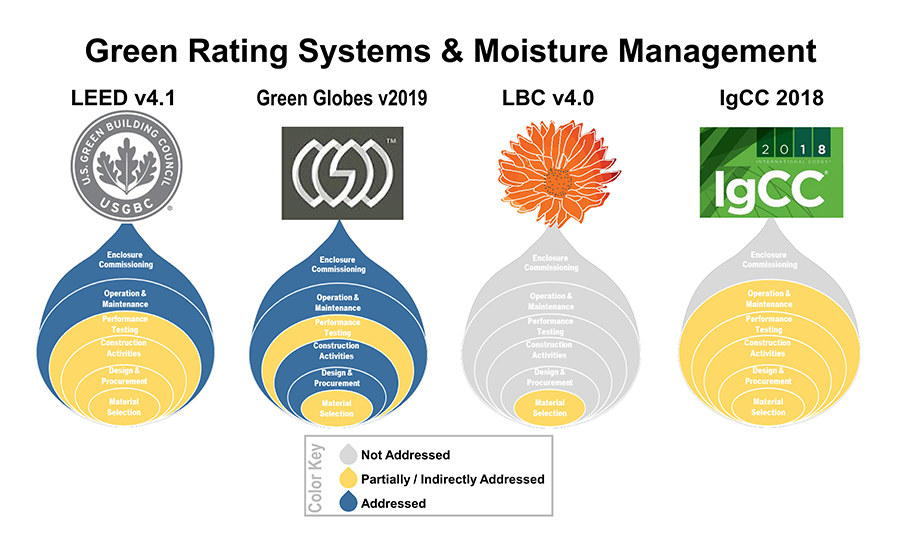
Figure 7. Green building rating systems moisture durability summary.
Figure 7 summarizes each of the six individual detailed assessments reviewed across the project life-cycle phases. There is quite a range of results across the green building rating systems assessed.
Part 5—Moisture & Roofing
Moisture has numerous opportunities to impact roof systems across the project life-cycle phases. Roofing systems must be designed and installed to address the many sources of moisture that can affect a building across the project phases. The primary root causes of moisture in roofing come from the following sources:
- Construction-related moisture
- Occupancy generated moisture
- Exterior leakage of water and air
Early in the design process, roofing professionals need to identify and plan for moisture from construction-generated sources, anticipated occupancy-related moisture, and moisture for discontinuities in the air and water control of roof systems.
CONSTRUCTION-RELATED MOISTURE
During the construction process for roof systems, moisture has a direct opportunity to find its way into areas where it was never intended. Temporary moisture protection plans discussed earlier in many green rating systems, are a good start but do not fully protect a building from experiencing excessive construction-related moisture.
Most construction practices release some amount of moisture into the building space. These can be as straightforward as wet-applied processes such as drywall installation and painting, although these are typically relatively short-term. However, some specific construction-related practices can release large amounts of water over a considerable time frame into the building. Concrete floor slabs, concrete roof decks, and temporary heating during construction are significant sources of moisture. Figure 8 demonstrates the relative construction moisture impact of these practices.
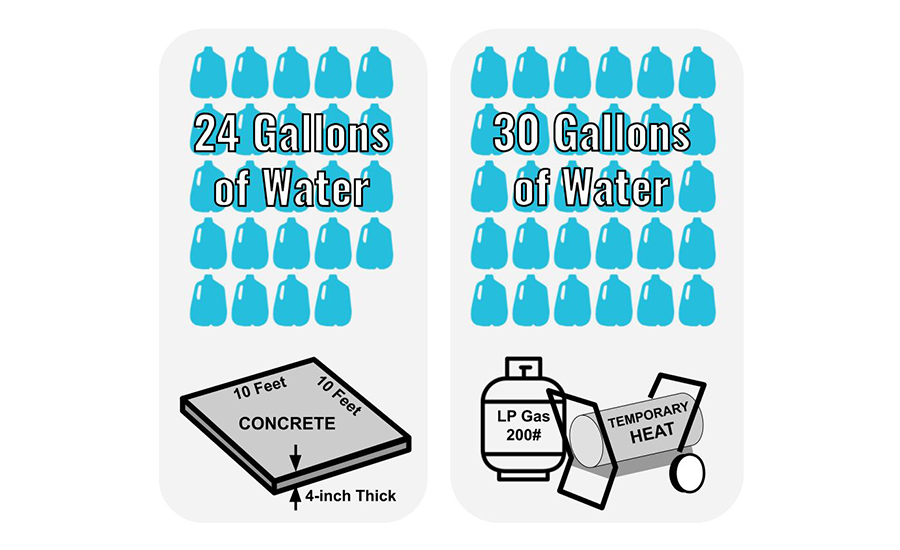
Figure 8. Examples of construction moisture sources.18
Concrete in new construction can appear dry but is rarely dry enough. Water takes a long time to diffuse out of a 4-inch-thick slab. Earlier when discussing complexity and interconnectivity, concrete decks in low-slope roof systems were used as an example. In the example scenario, the inherent moisture in the concrete structure is exacerbated by new concrete mix designs and the cascading adhesion problems that can occur in roof systems that rely on “rules of thumb” for roof design.
The flooring industry is well aware of the challenges that come with installing some flooring materials on freshly placed concrete slabs and have guidelines in place to use the building’s mechanical equipment to manage this moisture prior to installing the flooring finishes. Regardless of the type of concrete, significant amounts of water remain after curing is completed. In concrete roof decks, there is very little correlation between cure time and the amount of water remaining. Guideline “rules of thumb,” such as not installing the roof system until a minimum of 30 days after pouring and forming, are not particularly effective at reducing or eliminating issues.
The Single-Ply Roofing Industry (SPRI) has previously issued an advisory bulletin18 on construction-related moisture and provides the following guidance:
-
“...buildings under construction should be adequately ventilated during concrete hydration and other high moisture-related construction activities. Temporary, high-volume ventilation systems are commercially available and should be used during construction. These high-volume air-handling systems include dehumidification that is essential to remove large amounts of moisture from the air. HVAC systems designed for temperature control of finished buildings are not sufficient to remove construction-generated moisture.”
When measures are not taken, construction-related moisture can delay the installation or shorten the lifespan of installed building systems that are moisture sensitive.
OCCUPANCY GENERATED MOISTURE
Understanding the building occupancy is a good way to think about the main building-use scenarios. Occupancies can be categorized into small and large groupings, relative to the amount of occupancy-generated moisture anticipated during the operation of the building.
Buildings with Small Amounts of Occupancy-Generated Moisture. These are the most common situations, covering office, retail, and warehouse spaces, for example. In this scenario, using two layers of insulation with staggered joints can help prevent the migration of warm, moist air up to the underside of the roof membrane. Warm air and moisture generally move upward, so drying out the roof system during warmer/sunnier days is a slow and difficult process. In northern climates, regardless of the membrane type, condensation can occur between the membrane and the insulation. If a single layer of insulation is used, install cover boards, especially a high-density polyiso board, and use staggered joints. Both of these approaches use the staggered roof components to limit uncontrolled interior air intrusion that could by-pass the insulation and result in condensation.
Buildings with Large Amounts of Occupancy-Generated Moisture. This category includes paper mills, laundries, buildings with indoor swimming pools, and the like. In this scenario, the building's air handling and ventilation systems should be carefully specified to take into account the significant moisture loading. Also, the entire building envelope needs to be designed and constructed in such a way that damaging condensation and moisture build-up do not occur. It is prudent to include a building science professional experienced in these types of building occupancy and designs be involved.
By being aware of the use of the building, the roof can be designed and installed to accommodate the scenario. It’s important to take the occupancy-generated moisture into account when designing a new space or changing the use of an existing building.
EXTERIOR LEAKAGE OF WATER AND AIR
Bulk water (i.e., rain and snow) is kept out of buildings with roof membranes and facades of all types. Air-transported water, as the name implies, is carried into a building by air that leaks through the building enclosure. Water vapor enters a building by the process of diffusion of water molecules through an envelope material. There is an order of priority for the prevention of water intrusion. Bulk water is most critical, then air-transported water, and finally, of least concern—although still important—is vapor diffusion.
The design, manufacturing, and construction industries are quite good at keeping bulk water out of buildings. Only recently has there been a focus on the importance of stopping air leakage in buildings. That is why the International Energy Conservation Code (IECC), since 2012, requires all new buildings to include an air barrier. Including an air barrier prevents conditioned air from escaping and exterior air from infiltrating, saving energy. Preventing air-leakage across building enclosures also keeps the moisture in the air from being deposited as condensation in roofs and walls as it passes through. In a warm climate, air transports 10x more water than diffusion, and in a cold climate, air transports 100x more water than diffusion. This is why air-transported moisture is much more critical to prevent than water vapor that enters a building by diffusion.19
Vapor retarders do just as they are named—they reduce vapor diffusion, but not all vapor retarders are equal. There are 3 classes of vapor retarder materials, as shown in the figure. The lower the perm rating, the less diffusion occurs through a material. Most roof membranes are Class I vapor retarders as shown in Figure 9. Remember, perm ratings are material ratings; the full system needs to be designed and installed correctly for proper functionality.
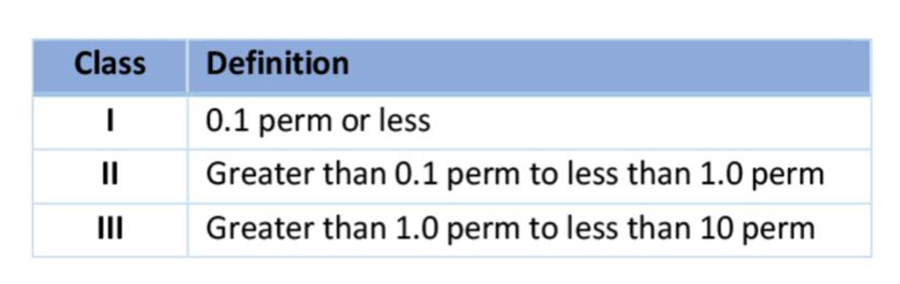
Figure 9: Three classes of vapor retarders.
The roofing industry continues to use the term “vapor retarder” as a shorthand, but the discussion should be focused on the continuity of the building’s air barrier to managing energy and condensation moisture in buildings. All vapor retarders block air, but not all air barriers block vapor diffusion. Not all vapor retarders in roof systems are installed as part of the building’s continuous air barrier; the caveat is that the vapor retarder needs to be sealed at all perimeters and penetrations to act as an air barrier, and tied to the wall air barrier so it is continuous to prevent air to from bypassing the vapor retarder layer. So, practically speaking, the vapor retarder in the roof assembly can be part of the building’s continuous air barrier if it is installed to block the passage of air.
A roof assembly configuration that manages moisture potential from both air leakage and vapor diffusion is shown in Figure 10. An adhered roof system is shown with multiple layers of insulation (with board joints offset and staggered) over a vapor retarder that is connected to the wall air barrier, contributing to the building’s continuous air control layer. When installing an adhered membrane with a water-based adhesive, make sure the adhesive will not reliquefy in the presence of moisture. This roof design configuration helps lower the risk of condensation from diffusion and air leakage from occurring inside the roof assembly. The end result can be a roof system with increased longevity, thermal performance, and improved energy efficiency for the building.
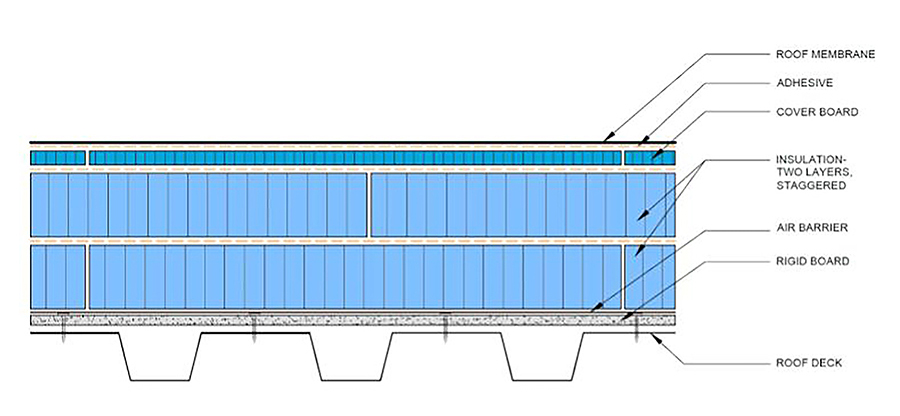
Figure 10: A roof design that improves longevity and thermal performance.
ROOFING MOISTURE SUMMARY
The vast majority of roof systems provide trouble-free performance for many years. When problems do occur within a few years of installation, it could be due to construction-related moisture, occupancy-generated moisture, or leakage of air and/or water. Roofing manufacturers provide a wide range of material choices so that the design professional can configure the optimum system for each building.
It is important to install building systems, like roofing, in conditions that allow it to perform the full duration of its intended useful life. This may require addressing roof designs, sequencing, and site conditions that are evolving along with the building industry. As with buildings that have occupancy-generated moisture, care must be taken to ensure that these are specified and installed correctly. It is key that when a vapor retarder is utilized to prevent moisture accumulation, it should also be designed and installed to be sealed at deck-to-wall joints, at gaps, and around roof penetrations to limit air leakage.
Locating the air control layer in the roof towards the inside of the roof insulation in the assembly prevents warm moist air from entering the roof system and potentially condensing on a colder surface beyond the insulation. Also, using multiple layers of insulation (minimum of two) and cover board, each with staggered joints helps prevent moist airflow from the interior of a building up into the roofing system assembly. Importantly, make sure professionals who have experience with the specific construction types are involved early in the project process. These could include structural engineers, building science experts, roofing installers and concrete suppliers.
Part 6—Takeaways
KEY TAKEAWAYS
When designing for moisture durability and energy efficiency in enclosures and roof systems, consider all project phases. This includes utilizing the building enclosure commissioning process to more formally ensure the relevant moisture durability risks are being assessed by an enclosure professional. It is important to recognize that overlooking one of the project phases may result in unmanaged risk for the long-term building performance. Some of the green rating systems have direct coverage of individual elements of moisture risk mitigation, but the certification frameworks may not be sufficient to rely on to provide comprehensive moisture durability mitigation. This is especially important knowing all four rating systems have mandatory energy efficiency improvements beyond code-minimum requirements, but none of the four have a complete set of mandatory credits to accommodate the increased moisture risk associated with the added enclosure complexity.
To accomplish long-term durability, it’s recommended to manage risk when interactive complexity and tight coupling are inherent in a roof and enclosure system design. This assessment provides a framework for applying enclosure moisture risk elements that can be used to supplement any of the green rating systems or to just enhance a project’s performance. It is recommended to use or borrow the best features from each system to shore up any project’s specifications. And if the owner is seeking a specific green rating system certification, be sure to look across the alternative rating systems to fill in the gaps where one may leave out elements or is vague regarding enclosure moisture durability.
REFERENCES
1 Air Barrier Association of America, Quality Assurance Program (QAP), www.airbarrier.org/qap, accessed September 2020.
2 American Institute of Architects, AIA Resilience and Adaptation Online Certificate Program, aiau.aia.org/aia-resilience-and-adaptation-online-certificate-program, accessed September 2020.
3 ANSI/ASHRAE/IES. Standard 90.1-2019, Energy Efficiency Standard for Buildings Except Low-Rise Residential Buildings. ANSI/IES/ASHRAE, 2019.
4 ANSI/ASHRAE/IES. Standard 160-2016, Criteria for Moisture-Control Design Analysis in Buildings. ANSI/IES/ASHRAE, 2016.
5 ASTM International. E2947-16a Standard Guide for Building Enclosure Commissioning. West Conshohocken, PA; ASTM International, 2016. doi: doi.org/10.1520/E2947-16A
6 Green Building Initiative, Inc. Green Globes® for New Construction 2019 Technical Reference Manual, Version 1.0, Green Building Initiative, Inc, December 2019.
7 International Code Council. 2018 IECC - International Energy Conservation Code. International Code Council (ICC), November, 2017.
8 International Code Council, Inc. and ASHRAE, 2018 International Green Construction Code powered by ANSI/ASHRAE/ICC/USGBC/IES 189.1-2017 Standard for the Design of High-Performance Green Buildings Except Low-Rise Residential Buildings. International Code Council, Inc. and ASHRAE, 2018.
9 International Institute of Building Enclosure Consultants, Registered Roof Observers – RRO, https://iibec.org/professional-registrations/rro/, accessed September 2020.
10 International Living Future Institute, Living Building Challenge 4.0, International Living Future Institute 2019.
11 U.S. Department of Energy. Energy Savings Analysis: ANSI/ASHRAE/IES Standard 90.1-2016. Report prepared by Athalye, R.A, M.A. Halverson, M.I. Rosenberg, B. Liu, J. Zhang, R. Hart, V.V. Mendon, S. Goel, Y. Chen, Y. Xie, and M. Zhao, Richland, WA, Pacific Northwest National Laboratory, 2017.
12 U.S. Environmental Protection Agency. Moisture Control Guidance for Building Design, Construction and Maintenance. EPA 402-F-13053, December 2013. doi: www.epa.gov/iaq/moisture
13 U.S. Green Building Council, Inc., LEED Credit Library, LEED BD+C: New Construction, Version 4.1. Washington DC: U.S.Green Building Council. Accessed September 2020.
14 Kaplow, Stuart, “Lawsuit over First LEED Platinum Building is Over,” Green Building Law Update, www.greenbuildinglawupdate.com/2015/12/articles/leed/lawsuit-over-first-leed-platinum-building-is-over. December 13, 2015, accessed September 2020.
15 Meyer, Benjamin,“Addressing Moisture Management and Energy Performance in Wall Assemblies,” Journal of the National Institute of Building Sciences (JNIBS), Winter 2018.
16 Perrow, Charles. Normal Accidents: Living with High-Risk Technologies New York: Basic Books, 1984.
17 M. Rosenberg and J. Zhang, Ph.D. “Energy Savings Analysis of ANSI/ASHRAE/IES Standard 90.1-2019 Final Progress Indicator.” Pacific Northwest National Laboratory. Presented at ASHRAE SSPC 90.1 Winter Meeting in Orlando FL, February 2, 2020.
18 Single-Ply Roofing Industry (SPRI). “SPRI Advisory Bulletin: Construction-generated Moisture And Its Effect On Roofing Systems.” August 2008.
19 Pettit, Betsy. “Thermal and Air Leakage Control.” Building Science Corporation. Presented at Build Boston. Boston, MA, November 2005.
20 Pierce, H. H. and Crowe J. P. “Structural Concrete Decks, Vapor Retarders and Moisture—Rethinking What We Know,” IIBEC Interface, February 2020.
21 SRI Consultants. “Moisture in New Concrete Roof Decks.” 2020.
Benjamin Meyer, AIA, LEED AP is a Roofing & Building Science Architect with GAF. His previous experience includes: enclosure consultant principal, technical management for enclosure products, architecture, real-estate development and construction management. Benjamin serves as a Member of the LEED Technical Committee, Member of the ASHRAE 90.1 Envelope and Project Committees, and a Director of ABAA. Visit him at www.linkedin.com/in/benjamin-meyer-728740a