Healing Environments for Health Care
Architects of health-care facilities are incorporating design innovations to help speed patient recovery
Continuing Education
Use the following learning objectives to focus your study while reading this month’s Continuing Education article.
Learning Objectives - After reading this article, you will be able to:
- Identify and recognize the significance of good restroom design, including plumbing fixtures, storage, and showers as a means to provide positive health-care experiences.
- Assess the health and safety performance aspects of wall and floor surfaces as they relate to durability and sustainability.
- Explain the importance of proper attention to details related to accessibility for the safety and well-being of wheelchair-bound persons.
- Determine ways to incorporate principles presented into buildings as shown in case studies.
Health-care facilities of many different types continue to drive a lot of design and construction activity. Some are responding to the burgeoning needs of aging baby boomers, while others are focused on ways to provide a better health-care experience. Hospitals and other in-patient facilities, for example, are trending toward providing private suites, with rooms looking more like hotel rather than institutional settings. This seems to be driven by a goal of creating outstanding patient experiences, adding to the perceived value and overall satisfaction provided by the facility, which helps with competition from other options in a geographic area. There is also a definitive trend toward providing medical treatments and surgical follow-ups in outpatient-care facilities, where overnight stays are not required. Nonetheless, outpatient-care facilities need to be designed and built to the same standards as hospitals, have the same appealing environments for patients, and be built affordably. Recognizing the need to balance high standards of care, hygiene, and functionality for health-care personnel with the comfort and overall experience of the patient, this course looks at some techniques and approaches to address this. Specifically, it will cover different aspects of health-care design that can be used to enhance all types of facilities.
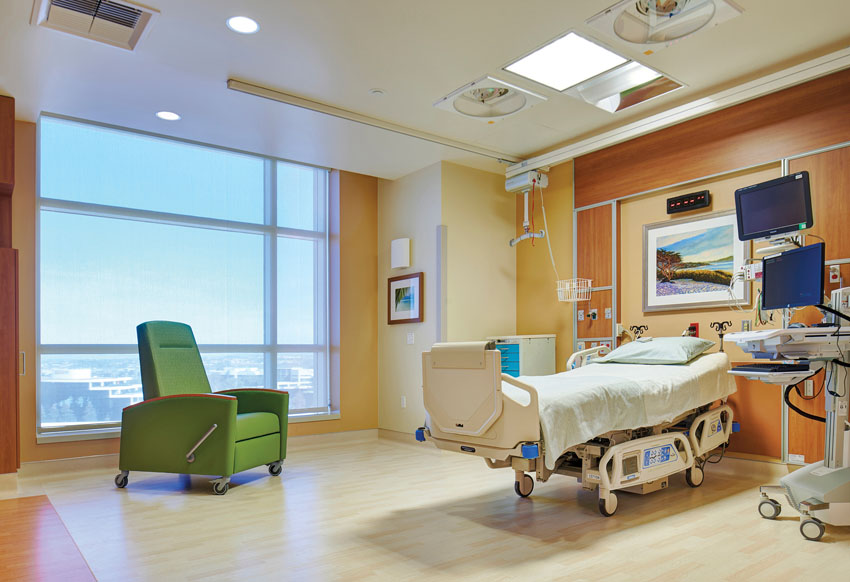
Photo courtesy of Lonseal
Health-care designs are increasingly focused on improved patient experiences while still meeting the clinical needs of care providers.
WELL-DESIGNED RESTROOMS
All people, whether patients, care providers, or visitors, will likely need a restroom during their time in a health-care facility. So, whether designers realize it or not, this is one of the rooms that can make a widespread impression on everyone, and that impression can be either a positive or negative one. While restrooms need to be designed around good hygiene, that doesn’t mean they need to look sterile and cold. Rather, consistent with the general trend of making health-care facilities look more welcoming, restrooms in health-care settings are being designed to look and feel more comfortable. At the same time, attention is being paid to ways to limit the spread of germs and bacteria. A number of products and design approaches that meet these criteria are discussed in the following sections.
Plumbing Product Options
Since all restrooms are designed around the plumbing fixtures, that is the best place to start to keep things positive. To help with that, it is important to recognize that there are commercial plumbing products currently available that offer unique solutions specifically for all kinds of health-care facilities with all types of users. Manufacturers of commercial plumbing products recognize that there are different needs for different parts of a hospital or other health-care facilities. Therefore, they offer a wide range of products for design professionals to choose from to match the best selection with the specific needs of a facility. From a functional standpoint, that includes, for example, plumbing products well suited to meet the particular needs of patients requiring special care. For less-specialized locations, there are other commercial plumbing products very suitable for access by the general public or for staff areas, such as nurse’s stations, etc.
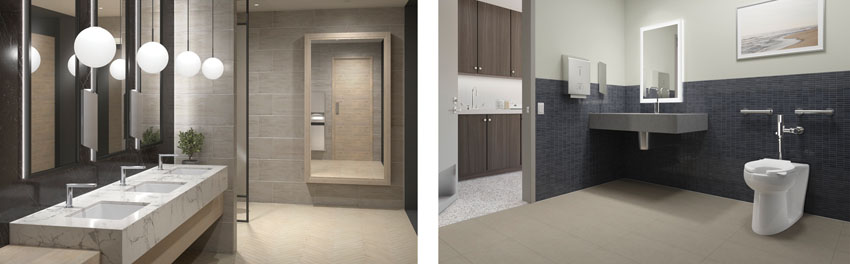
Photos courtesy of Kohler Co.
Well-designed restrooms in health-care settings can help provide both a positive impression and experience for patients, care providers, and visitors.
Commercial plumbing manufacturers also respond to design trends in the creation of their products. Along that line, it is worth recognizing that there are choices available that offer a less-institutional look and more of a familiar residential appearance, even though they are in fact heavier-duty commercial fixtures. This fits right in line with the trend of helping patients feel more comfortable and “at home” when needing to spend time in an otherwise institutional setting of a hospital or outpatient center.
Due to their typically high use, toilets in particular are subject to needing replacement over time in health-care buildings. Such replacement can be part of either a general renovation project or the regular operations and maintenance of the facility. One of the common issues with such toilet replacements is related to the fact that health-care facilities have bariatric and geriatric patients, for example, that require more support than a wall mount is capable of providing. It is a trend for facilities to move to a floor-mount bowl to offer more support. Normally, this replacement from a wall- to floor-mount toilet requires extended renovation scheduling. The added time and complexity of this situation adds cost, not just for the material and labor needed, but also for the possibility of lost room revenue during the work.
At least one manufacturer has addressed this renovation issue by offering a rather revolutionary retrofit solution. Instead of a wall-bowl toilet, it has designed a floor-mount bowl that does not require any work behind the wall during a replacement. This takes what would normally be several days of work and thousands of dollars in material, labor, and lost room revenue ($5,000–$20,000 estimates) down to only less than 1 hour in labor time and less than $1,000 in cost. This type of commercial toilet was strategically designed for health care based on specific requests from health-care facility personnel to be able to provide these wall-to-floor renovations.
There are other innovations that manufacturers are incorporating into toilets for healthcare facilities. These include having options for bed-pan lugs in the toilet bowls to help secure or position a bed pan to collect samples or dispose of waste and clean the bed pan. Manufacturers also offer antimicrobial finishes that inhibit the growth of mold-, mildew-, stain-, and odor-causing bacteria on the fixture surface. (The standard disclaimer on these is that an antimicrobial agent does not protect the user from disease-causing bacteria.)
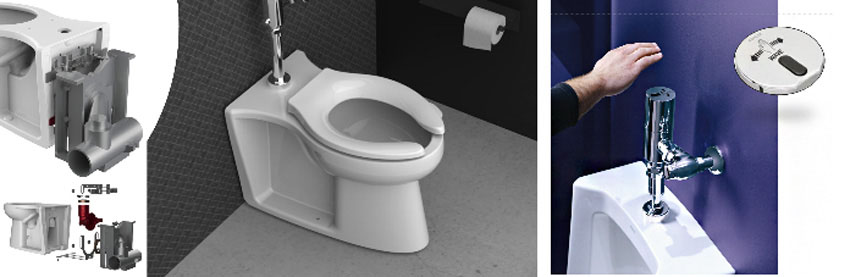
Photos courtesy of Kohler Co.
Innovative commercial plumbing products are available for health-care set-tings that make renovations easier and provide better touchless controls.
Touchless Operation
All health-care environments must maintain certain infection-control standards, particularly when it comes to the transfer of bacteria andother contagions. Another way to address hygiene concerns in restrooms is to use “touchless” technology wherever possible, such as faucet handles and toilet levers. Toward that end, a series of touchless options are available to use in these situations.
Touchless flush sensors have been used on toilets and urinals for some time; however, they may not be the best choice in a health-care setting. For example, a care taker helping someone on and off a toilet can unintentionally trigger multiple flushes, which can be disconcerting or problematic for many patients. A better solution is to install a manual, touchless flushometer to actuate the flush by waving a hand over the sensor. This restores control back to those using it by not flushing until the time is appropriate. And since it is fully touchless, it still provides the needed safety and hygiene.
For faucets, there are commercial touchless products that provide the same type of sensor technology to minimize the spread of bacteria by allowing users to start and stop the flow of water by waving their hands instead of touching the product. Equally important for hygiene is the selection of faucets that will not spread airborne or waterborne pathogens. It is critical to select faucets with laminar flows so there is no chance to aerate the water and introduce airborne pathogens into the water. Conversely, it is important to not select rose-spray faucets, as they can aerosolize the water and introduce waterborne pathogens into the air. Waterborne and airborne concerns are as significant as direct transfer on surfaces, so addressing all of these in a single product makes inherent sense. From a design standpoint, touchless faucets with a residential aesthetic help with the “feeling at home” experience sought in many cases, while still providing products made for commercial environments.
Environmental Friendliness
Any products that use water have an environmental impact during consumer use simply due to the consumption of this natural resource. The water use also requires energy for pumping, purifying, and treating it after use, so reducing the amount of water used can be a significant benefit for the environmental impact. Commercial plumbing products that require less water for each use are therefore preferable, and faucet or flush controls that do not use excess water are best.
Many of the sensors in the plumbing fixtures we have discussed require some electricity to operate. That may mean running electrical wiring and can force a compromise in the case of a power outage. Some products may use regenerative recharging of a battery, such as a solar cell on top of the faucet (collecting energy from the lights in the restrooms) or hydro charging (using the water flow to generate electricity). These are all good but need to be investigated for their durability and longevity for trouble-free operation. At least one manufacturer provides another simpler option in the form of a 30-year battery (875,000 cycles) that provides uninterruptable power and is maintenance free.
Overall, higher-level technology is being incorporated into commercial plumbing products for health-care use to assure ease of installation, long-term performance, quality, and ease of maintenance.
Hygienic Partitions and Lockers
Group restrooms and locker rooms typically contain partitions that need to address a variety of conditions. Toilet-stall partitions first need to address privacy, which some do better than others. Partitions are now available that have zero sightlines into the stalls and create a more safe feeling with regard to the bathroom experience. Many different partition heights are now available, allowing stall partitions to be much closer to the floor for increased privacy.
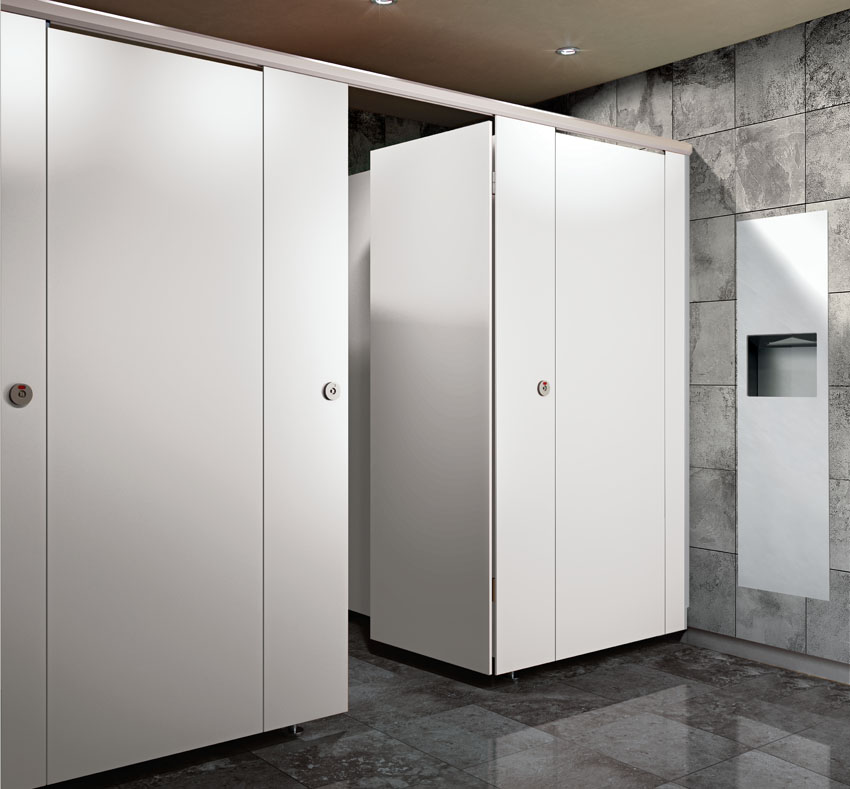
Photo Courtesy of ASI
Restroom partitions are available in more appealing materials and finishes that can also be specified as taller to provide more privacy.
There are a variety of materials that can be selected for partitions that also address appearance, functionality, hygiene, and durability. Plastic or phenolic products are particularly appropriate for very wet/humid environments like locker rooms, shower areas, etc. Powder-coated steel or stainless steel has also been successfully used for common areas where water and humidity are less of a concern. Of course, since there is a desire to move away from cold, institutional appearances, such partitions need to provide an appropriate aesthetic. Plastic laminate partitions have been used as a cost-effective solution for this type of application, but they need to be properly selected and specified in order to avoid delamination or other problems. Toward that end, at least one manufacturer offers an edge-banding system (often the common weak point in the finish) that fuses with the substrate, creating a seamless beveled profile that eliminates any unsightly black lines that normally appear in standard plastic laminate. ASTM tests on this type of system confirm up to three times greater durability with increased resistance to moisture and humidity than standard plastic laminate. From a design standpoint, the edge banding is available in more than 45 different colors and patterns to match laminate on partition doors, panels, and pilasters.
Antimicrobial Grab Bars
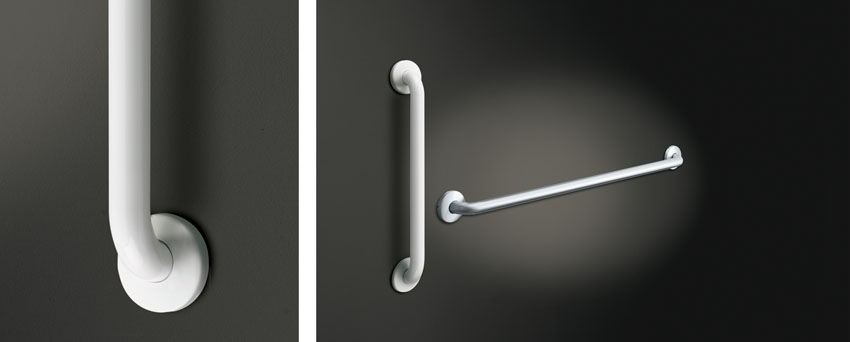
Photo Courtesy of ASI
Stainless-steel grab bars coated with an antimicrobial powder coating have been shown to be effective at reducing the number of certain microbes that can spread desease and infection in health-care facilities.
Many things in health-care restrooms, showers, and similar areas are designed to be “touchless” to help avoid the transfer of germs and bacteria between people. However, grab bars used around plumbing fixtures need, by definition, to be touched—and tightly. While routine and frequent washing/cleaning of such grab bars is usually undertaken, there is also the option of specifying antimicrobial products to help reduce the spread of microbes such as mold, bacteria, and yeasts. These microbes can grow quickly in warm, moist environments such as health-care facilities and have been attributed to a number of hospital-acquired diseases.
Antimicrobial grab bars, made of stainless steel, or galvanealed steel, are available that are finished with an antimicrobial powder coating. The powder coating is formulated to incorporate the slow release of antimicrobial agents like silver ions (Ag+). The antimicrobial agents are not topical because they are impregnated into the powder before it is electrostatically fused with the metal grab bars—and this increases their effective lifetime. In these coatings, the silver ions are the active agent that imparts antimicrobial properties into the surface. When the coating on the grab bar comes into contact with moisture, silver ions are released to the surface. Those ions penetrate the cell membrane of microbes present on the surface and create a reaction within the organism, which renders it inactive.
Lab tests have shown a significant decrease in the number of living bacteria found on the antimicrobial surface in a 24-hour period, with a documented bacterial kill rate of greater than 99.95 percent. Under similar circumstances, the number of living bacteria present on a surface that is not treated with antimicrobial agents grows exponentially. Antimicrobial grab bars can be used in any location where hygiene and infection control are of the utmost importance. Common applications include hospitals, doctor offices, senior and assisted living communities, and mental health facilities.
RESTROOM ACCESSIBILITY
Beyond the basic functionality and appearance of restrooms in health-care facilities, there is clear indication to address accessibility needs for patients and visitors. Since there is a higher likelihood of accommodating elderly and/or disabled people in these buildings, the need for proper attention to all aspects of accessibility is heightened. Plumbing fixtures and controls are all readily available to be specified with the appropriate accessibility features provided by the manufacturers, and that is routinely done. However, there are other aspects of restrooms and residential health-care facilities that need to be addressed by the design professionals involved. In particular, there has been a design emphasis placed on allowing people to remain independent when performing some common functions or activities in bathrooms. While many people reference the civil rights legislation known as the Americans with Disabilities Act (ADA) as the standard for this type of independent accessible design, in fact, architects are bound by the code standard ICC ANSI 117.1: Accessible and Usable Buildings and Facilities. Fortunately, in recent years, these two standards agree on most of the language and details related to building construction. (There are some minor differences, but the ADA covers things beyond construction too). For our purposes though, we will refer simply to ICC ANSI 117.1 as it applies to some specific bathroom issues.
Accessible Medicine Storage
People who need health care usually need medications. If someone is also wheelchair bound, then being able to access that medicine or other health-related items (bandages, lotions, toiletries, etc.) needs to be thought through. Many people would store such items in a medicine cabinet over a sink, but if that is beyond reach in a wheelchair, then it clearly will not work—so what does?
Identifying Standards
ICC ANSI 117.1 addresses sinks and wheelchair accessibility pretty thoroughly. It also addresses high and low reaching heights from a wheelchair and differentiates between unobstructed and obstructed reaching conditions. In the case of a medicine cabinet over a sink, an obstructed situation is created. The 117.1 standard defines that obstruction since it defines the parameters for the sink in Section 606: Lavatories and Sinks. First, the required clear space in front of the sink is defined based on Section 305 and a forward approach, meaning that the person in a wheelchair is able to reach forward to access the sink. The sink itself is required to be no higher than 34 inches from the floor. An enhanced reach range is acknowledged if the sink is no more than 11 inches deep. If a more standard condition occurs where the sink is in a countertop that is approximately 17 to 24 inches deep, then the reach range is not considered to be enhanced.
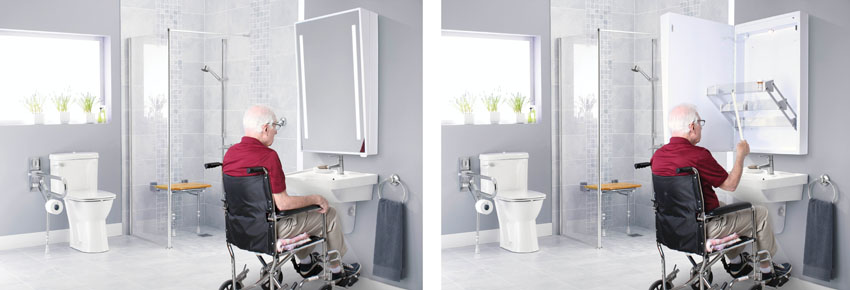
Photos courtesy of Aamsco Lighting, Inc.
An innovative, accessible, illuminated, and mirrored medicine chest allows a wheelchair user to independently access medications and toiletries.
In terms of reaching something above the sink, Section 308: Reach Ranges is the applicable part of the 117.1 standard. Section 308.2.2 related to Obstructed High Reach points out that “the clear floor space complying with Section 305 shall extend beneath the element…” thus allowing full access by pulling forward to reach the wall above the sink. It goes on to indicate that there are two different high forward-reach height limits: a 48-inch maximum above the floor applies where the reach depth is 20 inches or less, while 44 inches is the maximum reach height if the depth exceeds 20 inches but up to a maximum of 25 inches.
In the case of providing an accessible medicine cabinet over a sink, then, the standard dictates that the bottom of that cabinet (and the access to anything in it) must fall between 34 inches above the floor (maximum sink height) and either 44 or 48 inches above the floor depending on the depth of the sink/counter. Where a mirror is on the face of the medicine cabinet, the bottom of the mirror is dictated in the 117.1 Standard in Section 603.3: Mirrors. In this case, it requires it to “be mounted with the bottom edge of the reflecting surface 40 inches maximum above the floor.” This simply places the mirrored surface a bit closer to the sink height but does not change the maximum reaching height inside the medicine cabinet.
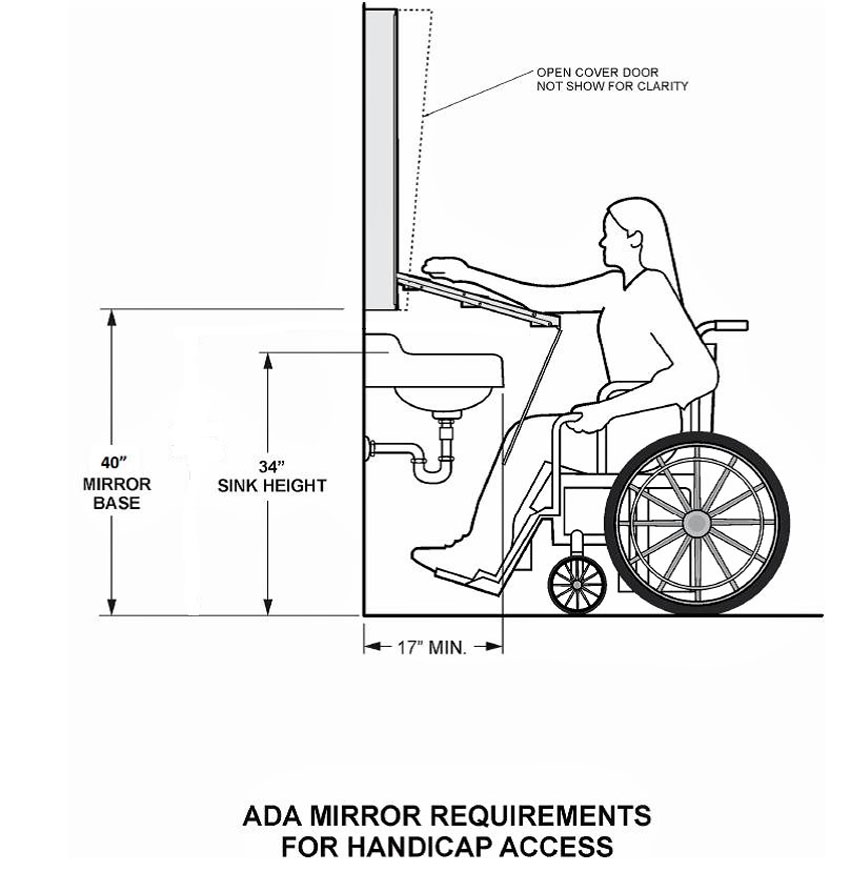
Image courtesy of Aamsco Lighting, Inc.
Maximum reaching height from a wheelchair is governed by the depth of a sink or other obstruction between the person and the wall.
Providing Solutions
Based on the above, the accessible range of someone in a wheelchair is pretty limited: on the order of 10–14 inches of height or less above a sink. That does not allow a lot of room to access medications or other needed health products. Of course, everyone’s individual needs are different, and there is usually not a one-size-fits-all answer to the day-to-day living in an accessible situation. So, innovation is often needed to provide the best outcomes.
An excellent example of such innovation is found in a medicine cabinet now on the market that combines accessibility and ingenuity. It allows someone in a wheelchair to reach the bottom of the cabinet door above the sink and open it to reveal the contents inside. While normally someone would only be able to reach the bottom shelf of the cabinet, this design includes a vertically hanging handle inside that is connected to a cleverly designed shelf system that the user can pull easily downward. The individual shelves adjust with gravity as they are lowered, allowing all of the contents to remain on the shelf and be placed directly above the sink in front of the person. Hence, all of the contents of the cabinet are now accessible to the user. When done, the shelves are simply pushed back up into place and the door closed. This synchronized operation allows the user to act completely independently from the wheelchair without requiring assistance or standing.
In addition to this helpful functionality, a residential style and intentionally simple aesthetic are provided. This medicine chest provides a clean-looking mirrored cabinet that is angled downward on the front so that wheelchair users can see themselves easily. The cabinet is also illuminated both on the outside and inside, providing light above the sink and easy visibility of the contents of the chest.
Liz Congero is vice president of sales and marketing for Aamsco Lighting and has seen the results of this type of innovation. She says, “The overall net effect is that elderly or physically challenged people are able to remain in their homes or a long-term care facility and maintain a level of independence. This helps with a person’s well-being, which can also be linked to addressing concerns about being able to have access to their medications without assistance.” Clearly, more innovation like this is called for that provides the needed accessibility in a way that blends with architectural design in health-care facilities.
Accessible Showers
Shower stalls are an area where accessibility is paramount in many health-care facilities. ICC ANSI 117.1, Section 608: Shower Compartments is the governing standard here and offers guidance based on the type of shower being provided. Three specific types of showers are covered: transfer showers where a wheelchair bound person can transfer to a (usually) ell-shaped seat; roll-in showers that may or may not include a rectangular fold-down seat; and an alternate roll-in shower with a partially enclosed configuration. For each of these options, minimum clearances, sizes, and dimensions are identified for adequate accessibility by a person in a wheelchair.
Beyond the physical makeup of the shower stalls, there are specific requirements for some details too. These include requirements for grab bars showing the locations, dimensions, orientation (horizontal or vertical), and details of the size and shape of the grab bars are provided. Additionally, requirements for the different types and shapes of shower seats are spelled out in detail. All of these parameters are fairly straightforward to address but need to be coordinated based on the type and size of the shower being designed.
In addition to the above, there are several notable design considerations for accessible showers. One is the use of a trench drain along the leading edge of the shower to allow for a true roll-in condition with a minimum threshold. Another consideration is the use of shower curtains instead of doors. One advantage of employing shower curtains is the potential for easier compliance where space may not allow for shower doors. Employing a shower curtain with a wide lip and Velcro® side-seals edge can lessen the occurrence of overspray, thus reducing slip-fall risk for the bather and attending staff. Further, the location of convenience items such as soap dishes and caddies is important. The key here is to be aware of and avoid any conflicts with other elements in the shower space, specifically grab bars. Also, do not forget to take into account ADA Section 308 regarding unobstructed forward and side reach ranges when positioning soap dishes and caddies.
In the interest of simplifying the design of accessible shower stalls, there are fully prepared and assembled shower stalls available that have taken all of these things into account. Some of the preferred ones use solid-surface panels as a shower-enclosure material. Since solid surface is non-nutritive, it does not promote the growth of mold and mildew, and it resists bacterial growth. Solid surface also offers a great alternative to tile, with no grout to trap mold and mildew. Where grout cracks or falls out, there is risk of water getting behind the tile, leading to tiles failing or moisture seeping into the substrate. Further, installation of solid-surface shower surrounds can be finished in one-third the time of traditional tile.
Shower Seating
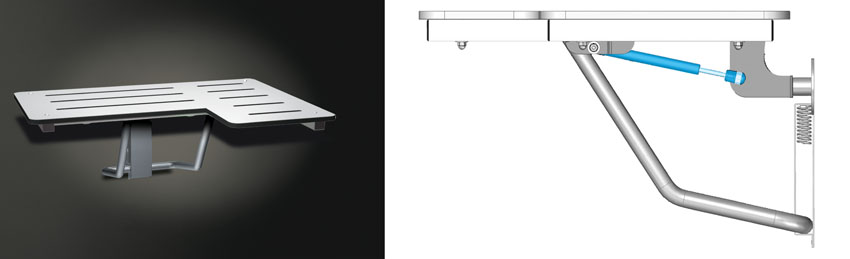
Photos courtesy of ASI
A slow-closing shower seat with damped gas springs does not slam down when lowered.
Many health-care facilities contain showers with a seat to allow for patient comfort or accommodate a temporary or permanent inability to stand through a shower. The preferred option is to provide a seat that moves or folds up out of the way to allow the greatest flexibility. Of course, its design and materials need to address hygiene and ease of cleaning too, all while providing an attractive appearance.
While there are a number of choices for such shower seating, the preferred option is for an L-shaped seat that closes smoothly. Specifically, models that use gas-charged struts assist one-handed opening by allowing the slowly lowering seat to drop into its operating position. The mechanism also assists in partial closing without creating any unexpected movements or disturbing loud noises. Guide brackets with a spring detent prevents the seat from dropping and provides positive support while in use, as well as locking in its storage position. A typical left-hand arrangement meets ADA Accessibility Guidelines and the needs of the physically disabled and elderly. For cleanliness and durability, a seat made from ½-inch-thick, one-piece solid-core phenolic is preferred. The frame, support legs, flanges, and bracket should be specified as type 304 satin-finish stainless steel.
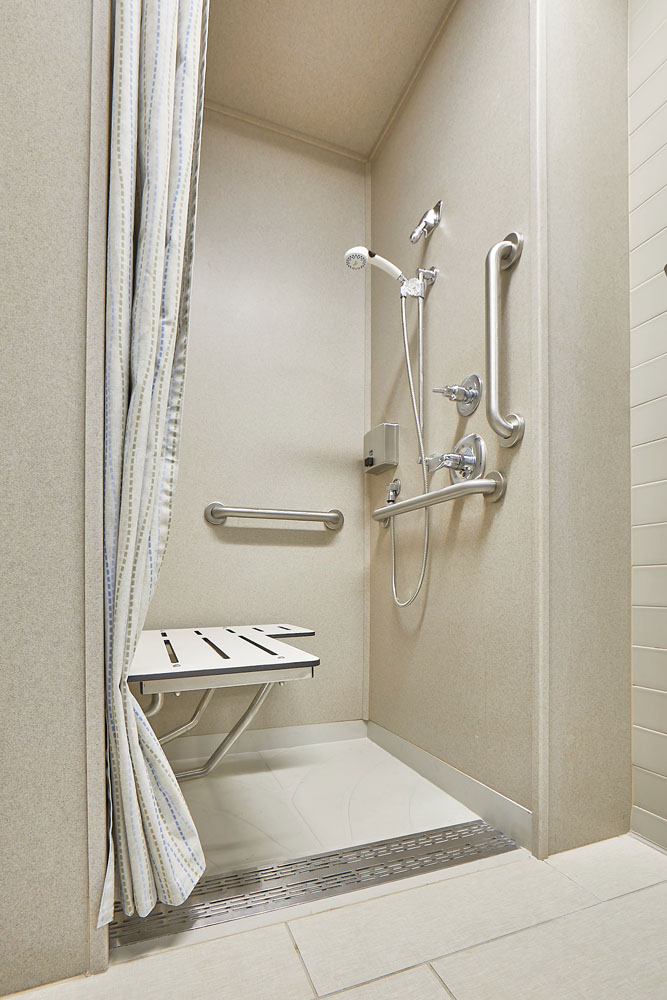
Photo courtesy of Inpro
Accessible shower stalls made from durable solid-surface material can be fabricated in advance to meet health-care project needs and requirements.
INTERIOR TREATMENTS
The interior treatments of health-care spaces can have a direct effect on the way people feel and recover from procedures and the care they receive. With that in mind, we look closer at a few things to consider.
Cordless Window Shades
Controlling daylight and glare while providing some privacy along windows is a design necessity in many cases for health-care buildings. In response, textured roller shades can be used, which allows diffused daylight to pass through but the fabric appearance of the shade to reduce the total light. Thus they reduce glare, add comfort, and produce a favorable light quality inside the building while still providing a degree of privacy or views through to the outdoors as needed.
Cordless window shades for commercial use are made of long-lasting, durable fabrics and side channels. A spring roller system allows manual adjustment of the shade with considerable ease. The cordless design, incorporating spring roller mechanisms, makes them a safer option for areas where cord safety is a concern, particularly in pediatric or mental health areas. Typically made from a combination of materials, they are easy to clean without removing the shade. From a design and light-control standpoint, they are available in single- or dual-shade configurations for partial or total light control. A privacy track can also be included to keep the shades in place and provide additional light blocking.
For areas where damage or tampering may occur, there are cordless window shades that are a self-contained system specifically designed to resist such damage. This type of system features side channels and an extremely durable security box fascia to protect its mechanical components, making it one of the toughest cordless window shades on the market.
Beyond these functional features, it is possible to design and create a theme from room to room by custom printing the shades with a graphic design selected by the designer. Printed shades can create a welcoming atmosphere in addition to hiding unsightly outdoor scenery. They are also less likely to be damaged or vandalized. It is entirely possible to use custom landscapes or artwork, or simply apply standard fabric patterns to a shade for simplicity.
From an energy standpoint, cordless window shades have been studied and shown to help with the rejection of solar heat with a positive impact on reducing energy needs for cooling. For example, independent research using computerized energy models showed that annual energy savings related to space cooling, heat rejection, and ventilation fans could be realized between 5–9 percent. These savings were attributed to the ability of the fabric to reflect solar heat and keep the building from overheating on sunny days.
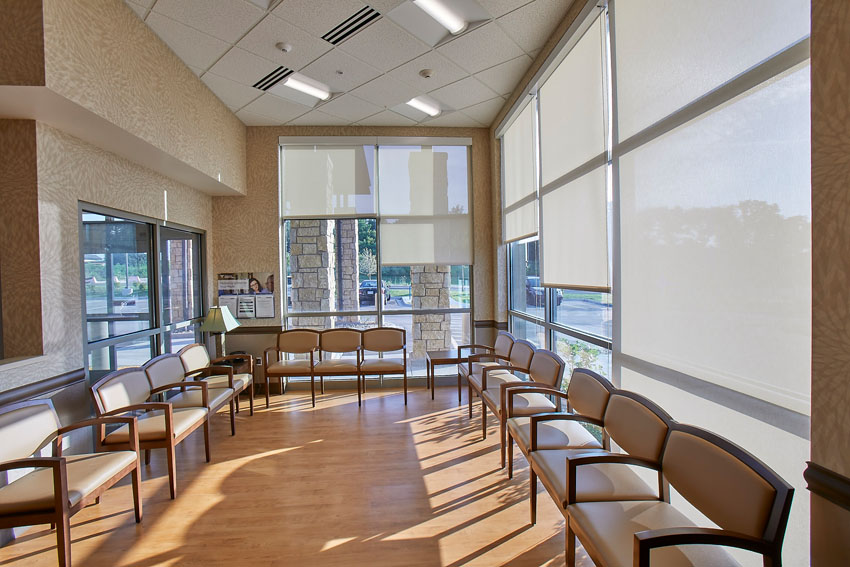
Photo courtesy of Inpro
Interior cordless window shades with textured fabric can provide privacy or maintain connections to the exterior while helping with energy perfor-mance by reducing solar heat gain.
Handrails Addressing Multiple Safety Issues
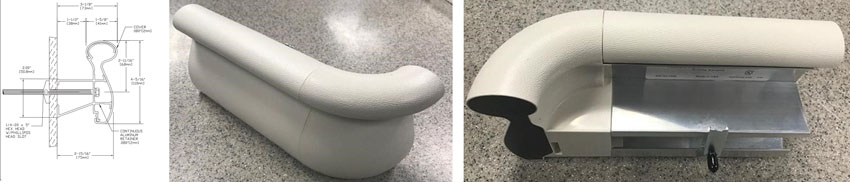
Images courtesy of Inpro
Interior elements such as wall handrails in health-care and mental health facili-ties need to be addressed for their ability to curtail patient harm in addition to being a walking aid and wall-protection item.
Handrails are commonly used along interior corridor walls in health-care facilities to assist patients with stability and mobility when walking. However, in certain cases, such as mental health facilities, everything needs to be scrutinized for preventing patients from inflicting harm on themselves, including handrails. An open handrail could become a place for a suicidal patient to attach or tie something around and attempt self-harm.
Recognizing this issue, at least one manufacturer has developed an innovative handrail system that eliminates any gap between the handrail and the wall. It is based on a continuous aluminum retainer and solid one-piece returns to reduce wedge points where anything could be affixed. The continuous retainer works in tandem with the solid one-piece wall returns. The top of the vinyl cover sets within the integrated aluminum channel, removing a pick point, while the oval-shaped top rail provides a comfortable and secure surface for gripping and leaning.
Based on all of these attributes, this new handrail offers an innovative, easy-to-install railing system that is a durable, stylish, and ligature-resistant option for behavioral health facilities. In fact, this type of handrail is the only one accepted for use by the New York State Office of Mental Health (NYSOMH). A midsize version of the handrail (45/16 inches, or 110 millimeters, in height) also offers wall protection with a lower profile than conventional handrail products. It is available in standard solid colors and simulated wood patterns.
FLOORING
There are many options for floor coverings in health-care facilities, but one of the go-to choices for many design professionals is vinyl flooring. There are a lot of reasons for this, not the least of which is the virtually endless color and design selections, including vibrant colors, textured patterns, and material replication such as wood or stone that play well in contemporary health-care designs. Vinyl flooring is typically less expensive than many other options in part because it is easy to install, including the ability to affordably create coved wall bases for more hygienic installations. From an operations standpoint, vinyl flooring is resistant to moisture, stains, insects, mold, and mildew, plus it is easy to clean, offers low maintenance, and is extremely durable. There are patient reasons to consider vinyl flooring as well, such as noise-reducing qualities. A cushion underlayment can be put under the vinyl flooring, which helps to absorb sound from footsteps and creates a quieter, more desirable place to be.
With all of these attributes making vinyl flooring appealing for health care, a closer look is worthwhile as follows.
Sheet Vinyl or Tile?
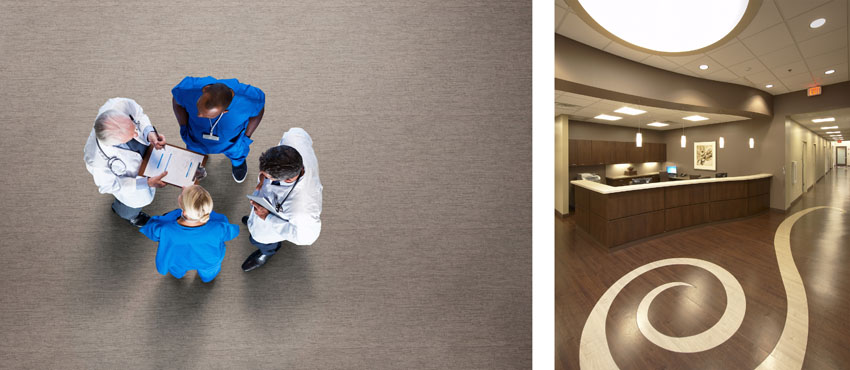
Photos courtesy of Lonseal Flooring
Sheet vinyl flooring has been used very successfully in health-care settings to create a variety of looks in different colors, material appearances, and patterns.
Sheet vinyl flooring is most often used in areas where seams need to be as nonexistent as possible. Health-care facilities are such an area since the seams or joints in any flooring, including some tiles, can breed bacteria or mold and jeopardize meeting hygiene requirements. Using seamless or welded seamed sheet vinyl flooring eliminates the concern altogether. Some products are also available with increased infection control through an antimicrobial formulation.
One of the main reasons why architects choose sheet vinyl flooring is that it can be printed in a wide range of different looks. Unlike vinyl tiles, sheet flooring allows the creation of very large designs or images that do not force a floor based on repeating smaller patterns. Nonetheless, if a tile or plank look is desired, that too can be printed without the concern of the joints or seams. Sheet vinyl can also be fabricated to look like a number of different materials such as wood, stone, and cloth in a variety of tones and colors. Many of these options can also be specified with a factory-applied urethane-finish top surface. This treatment protects the floor pattern, reduces scuffing, and simplifies routine maintenance. As such, it extends the life of the flooring by protecting it from wear. Overall, all of these attributes of sheet vinyl floor make it particularly well suited to produce an appealing health-care experience and still perform to meet the needs of the staff.
Green Building Attributes
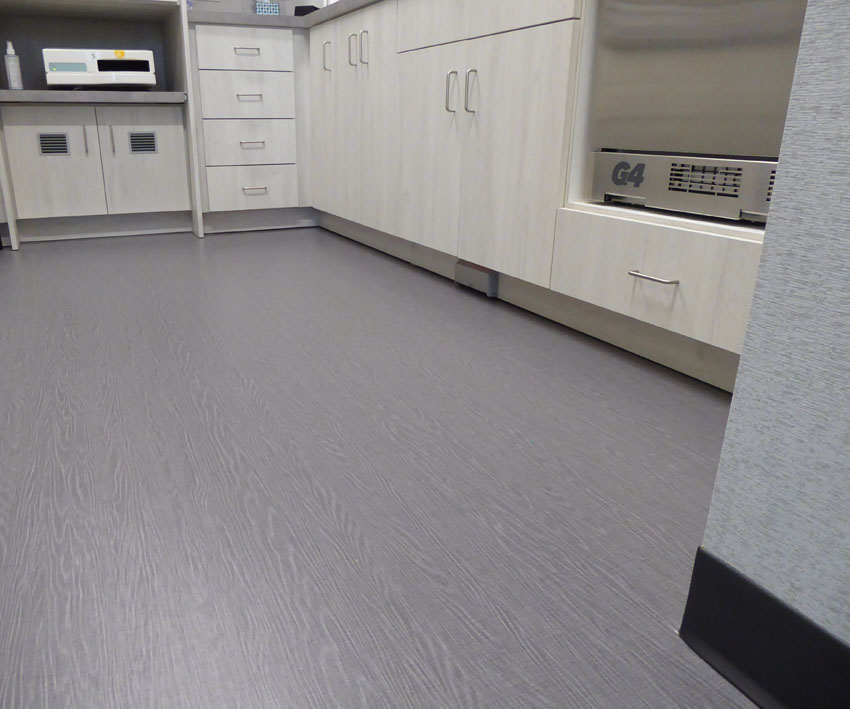
Photo courtesy of Lonseal Flooring
Biophilic design was used for the flooring of this endodontist clinic to cre-ate a more natural pattern and help ease the anxiety of patients and staff.
There have been notable advances in the way resilient sheet vinyl is pursuing and achieving greater sustainability and green building recognition. Of course, not all vinyl flooring is made the same. There are some bargain-priced products that consist of a basic and minimum formulation to be considered resilient and can typically wear out within five years. High-quality vinyl flooring is formulated with higher quality and can last up to 10–20 years—which is clearly a more sustainable solution. Some of the eco-friendly features found in quality vinyl flooring can be summarized as follows:
- LEED contributions: High-quality vinyl interior flooring products are available that contribute toward LEEDv4 Building Product Disclosure: Environmental Product Declarations (EPDs) (Option 1). This qualifies the materials and sources using an industry-wide EPD. They can also contribute toward the Sourcing of Raw Materials (Option 2), which means the products have post-industrial recycled content, commonly ranging from 10–20 percent, with some reaching 50 percent or more. Interior flooring products and adhesive products are also available to meet the requirements of Indoor Environmental Quality credits for general emissions evaluation and VOC content requirements.
- FloorScore certification: This well-known program from the Resilient Floor Covering Institute (RFCI) and Scientific Certification Systems independently tests and certifies flooring products for compliance with indoor air-quality emission requirements. Some products have recently been developed and certified for low VOC content, a notable distinction from other products.
- Collaborative for High Performance Schools (CHPS): Some manufacturers are a member of and meet the standards for the CHPS program, a well-known green building rating system especially designed for schools but used as a benchmark for other settings too.
- ISO 9001 and 14001 compliance: Flooring products can be specified to be obtained from a facility that has certifications from the International Organization for Standardization (ISO), which provides a rigorous external third-party verification process. Specifically, ISO 9001: Quality Management Systems ensures a manufacturer’s compliance to its own internal quality standards. In addition, ISO 14001: Environmental Management Systems addresses ever-changing environmental laws and regulations.
While vinyl flooring manufacturers have made great progress in recent years, some are never satisfied with the status quo and are always striving to raise the bar with ever-more eco-friendly products and new product offerings. Some monitor the use of recycled pre- consumer (post-industrial) content, achieving an average of 20–50 percent recycled content. They also promote the factory-applied, urethane finish, which, due to their low-maintenance and matte finish, reduces the chemicals required during maintenance from finishes and strippers.
In the spirit of healthier indoor environments, at least one manufacturer has embraced the idea of biophilic design for it vinyl flooring products. Biophilia is simply our native tendency to want to connect with nature and has been found to have a significant impact on health and well-being. Products are available that use the science behind biophilia studies and incorporate colors, patterns, and textures that are reminiscent of outdoor settings as a result. Patterns that are most likely to hold our attention and reduce eye-muscle fatigue are typically those found in nature. Incorporating such patterns into health-care settings can contribute to the overall sense of satisfaction and a positive experience for everyone in the facility.
Lace Greene-Cordts is the marketing manager for Lonseal flooring. Reflecting on the industry and its engagement with green building principles, she comments, “Being ‘green’ is no longer enough—products need to contribute to the physiological needs architects are now providing in building designs.” She goes on to point out that “a good design is something that will allow a user perception to process an experience toward healthy and restorative feeling.” Working with manufacturers to understand their specific product offerings can help design professionals make the best selections and achieve the ideal results in health-care projects.
EFFECTIVE INTERIOR LIGHTING
In the quest for hospitals and outpatient facilities to make patients feel more “at home” while still meeting the needs of medical and health-care staff, interior lighting is a significant factor. Further, lighting design must also meet the infection-control and electrical requirements to support the equipment needed for procedures. With all of this in mind, we can look at some specific interior lighting strategies as follows.
Layered LED Lighting Design
Within all health-care settings, there are several layers of lighting needs. Care providers need task lighting for better visual acuity, and the commonly bright lights in these settings provide that. However, patients are more comfortable with different levels of lighting and some ability to control it. That can include lighting that is dimmable, indirect lighting, or location-specific fixtures that put the light only where it is most needed. Further, safety lighting is needed, particularly in overnight facilities where low-level, low-brightness, and color-selected light is not disruptive to sleeping patients.
The incorporation of layered lighting, including decorative lighting, makes a noticeable difference in meeting the multiple needs of patient rooms. One approach is to incorporate cove lighting to provide indirect illumination on ceilings and behind patient headboards for comfortable glare-free ambient light, decorative wall sconces can provide a home-like atmosphere and offer sufficient task lighting. Ceiling and safety lighting can be added to this scheme as needed to create a total lighting design.
Outpatient facilities are also paying more attention to their lighting design, particularly in check-in areas and lobbies. The incorporation of decorative pendants over reception areas communicates an updated contemporary design. Architectural lighting, along with decorative luminaires, offers smooth lines and easy-to-clean surfaces for a sleek, modern aesthetic.
All of these different lighting fixtures of course raise the question of light color and energy use. Both concerns are increasingly being answered with the rapid advancement of some very sophisticated LED lighting products. The color of the light is inherently controllable in LED fixtures, such that warmer-colored lighting (e.g., 3000K) can be used where appropriate for a more “homey” look, while brighter and whiter lighting (e.g., 6000K) can be used for high lighting needs. Energy efficiency comes from the very low energy-usage needs of LED lights to produce the same or more light output (lumens) as other types of fixtures, such as fluorescent, halogen, or incandescent.
LED Lighting Controls
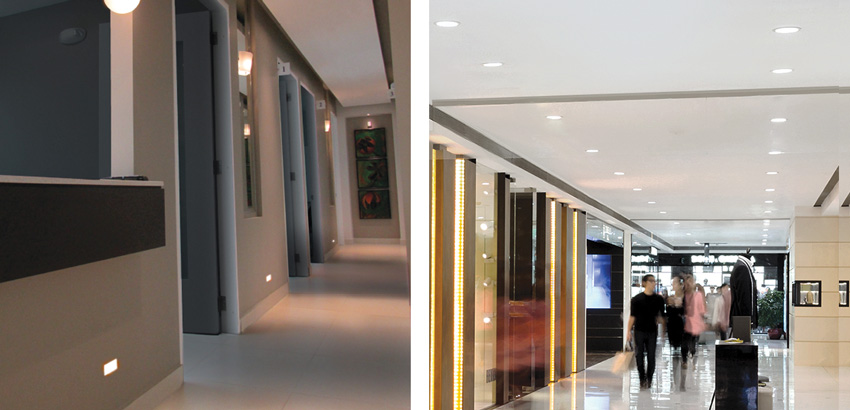
Photos courtesy of WAC LIGHTING
Different conditions and spaces in health-care facilities require different layers of light to be designed. LED lights offer a variety of options to achieve just that.
One of the benefits of LED lighting is that it is very easy to provide controls in any room to dim or switch on/off the fixtures. This provides patients with more autonomy over their environment, resulting in an improvement of their personal comfort and satisfaction. Further, it offers care providers options for lighting when checking on patients at different times of the day or night. So, hourly checks may still be required, but the entire room should not need to be illuminated for routine actions like checking blood pressure, etc.
Designing lighting for human welfare in health-care projects also means utilizing light sources that can provide full-spectrum light, similar to daylight. Some LED luminaires can be color tuned to adjust the spectrum and brightness of light throughout the day to emulate changes in natural daylight. Studies show that patients exposed to natural daylight have better recovery outcomes, while exposure to blue and bright light inhibit the body’s natural production of melatonin, the hormone responsible for sleeping restfully through the night.
WAC LIGHTING President Shelley Wald comments on the relationship between light and rehabilitation. “Many health-care facilities are seeking certification to maximize the well-being of patients, employees, and other visitors. Therefore, the lighting in patient rooms is being designed around the visual comfort of the patients, while providing caregivers with visual acuity and enhancing circadian rhythms for personnel working the day or night shift.” Recognizing this approach, health-care spaces can be beautifully enhanced with architectural and decorative lighting that provides patients with the best possible outlook, well-being, and recovery.
Infection Control
For optimal lighting design, a key requirement is the ability to spray and wipe to disinfect lighting fixtures and other materials directly contacted by patients, visitors, and employees. Lighting built into coves and case-goods also needs to be regularly disinfected. LED lighting responds to these needs with smooth surfaces and protective damp- and wet-location finishes that can be regularly cleaned. Fixtures can be specified with specialty powder-coated finishes that actually deter and restrain the growth of bacteria on their surfaces, while others can be specified with materials that have been shown to be antimicrobial. Beyond the fixtures, the controls for lighting can address infection control as well. Incorporating motion sensors, vacancy sensors, and time-scheduled controls make it possible to limit contact with switches that may spread infection.
CONCLUSION
Health-care facilities are trending toward providing more comfortable, welcoming environments for patients, staff, and visitors. Manufacturers are offering products that support that trend while still meeting the requirements for hygiene, durability, and sustainability. Design professionals who stay up to date on these trends and offerings can provide better health-care facilities to support client goals and improve user experiences.