Revolutionary, Permanent Tensioned Membrane Aluminum Frame Supported Structures
Unique tensioned membrane aluminum frame supported structures are a permanent solution for architects seeking rapid, cost-effective construction, sustainability, and energy efficiency
Continuing Education
Use the following learning objectives to focus your study while reading this month’s Continuing Education article.
Learning Objectives - After reading this article, you will be able to:
- Describe the architect’s role in managing the installation of rapidly constructed tensioned membrane aluminum frame supported structures.
- List performance standards, including improved daylight, acoustic, and fire-safety measures, engineered into these high- performance buildings to enhance the physical environment and provide emotional and social well-being to occupants.
- Identify strict code-compliance regulations for these buildings that benefit the physical environment through increased energy efficiency and recyclability.
- Discuss project management and design of these buildings from pre-design to post-occupant evaluations that allow for a wide range of configurations, including multistory interiors, various surface colors, and massing alternatives.
Fast tracking, value engineering, sustainability, and integrative design are driving the delivery of most 21st century buildings. These initiatives are supported and encouraged by architects and owners racing toward ever-tightening project-delivery schedules, budgets, and energy-efficient mandates.
It takes a remarkable structure to meet the goals of a remarkable company. When constructing their headquarters in Kent, Washington, Blue Origin opted for a solution that incorporates energy efficiency, sustainability, and speed: a tensioned membrane aluminum supported structure.
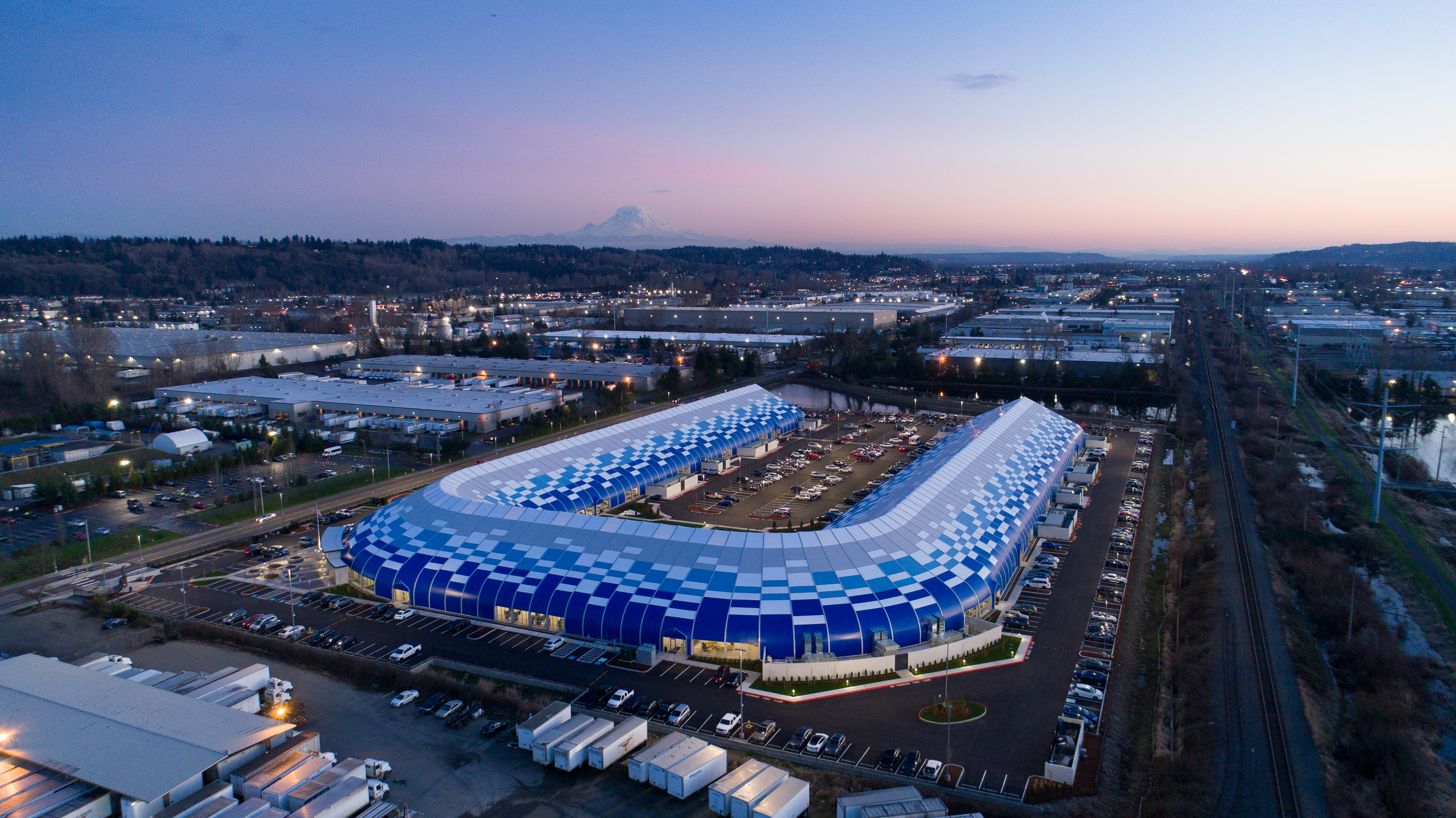
Photo courtesy of Sprung Structures, Inc.
The 270,000-square foot head office for Blue Origin in Kent, Washington, erected from ground breaking to completion in just eleven months.
Design teams often confront owners with a “devil’s bargain.” There is too often a trade-off between two of three choices: cost, schedule or quality. Design and technological advances in tensioned membrane aluminum frame supported structures may provide an alternative for owners and architects who want it all. TESLA to SpaceX, Harvard to Blue Origin, homeless navigation centers to ice arenas, clients are choosing to fast-forward into the 21st century with sustainable buildings that deliver on cost, quality, and schedule without sacrificing permanence and beauty.
A high-performance tensioned membrane aluminum frame supported structure is eco-friendly, and components exceed building codes and some of the most stringent green rating system criteria. These structures provide the same functionality of a traditional building type at a much lower cost and much faster construction time. The tensioned membrane exterior, which is also the interior surface of the building, provides a high-performance insulated airtight barrier for protection in any climate. The interior membrane is the interior wall surface requiring no additional drywall, plaster, painting, or resurfacing, as it is part of a complete building package. As with many new models for building financing, these buildings can be leased. In fact, many manufacturing companies start by leasing these structures to assist with cash flow and end up purchasing them at a later date.
Many design professionals are not aware of this new building type, particularly as a permanent building system rather than a temporary alternative. According to Sprung Structures Vice President Jim Avery, “One of the most common misconceptions is that tensioned membrane aluminum frame supported structures are tents and only considered as a temporary construction solution. Quality starts with the intelligent design of these buildings. Considering the rapid construction time, superior energy efficiency, long-term flexibility, and lower overall costs, tensioned membrane aluminum frame supported structures perform as well or better than other traditional building types.”
The following guidelines and case studies will provide more detail as to how to select tensioned membrane aluminum frame supported structures as a permanent solution to complex programming requirements. From visioning and programming to post-occupancy, design professionals are finding these structures an unconventional solution for new 21st century problems.
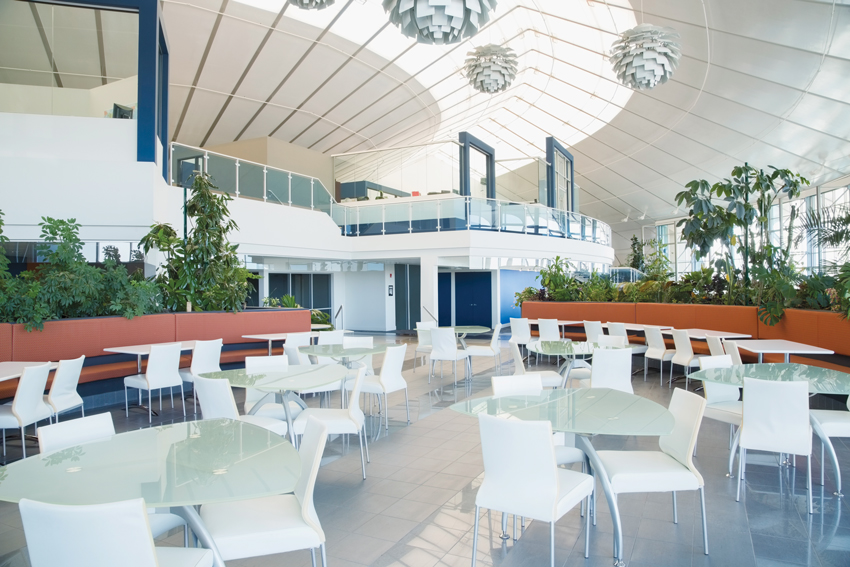
Photo courtesy of Sprung Structures, Inc.
This membrane manufacturer’s permanent headquarters makes employees feel as though they’re working in a large botanical conservatory with high-end atmospheric and environmental controls. Translucent daylight panels allow for reflected light throughout the building without the use of electricity.
Project Management
According to the American Institute of Architects (AIA), project management is vital for the success of every project. As with any project the, selection of a pre-engineered building such as a tensioned membrane aluminum frame supported structure requires careful planning. The architect articulates client goals, creates a vision, and analyzes planning and code requirements before developing construction documents. Any successful project begins by listening and developing strong communications between all members of the team. A tensioned membrane aluminum frame supported structure is engineered from the baseplate forward, which means incorporating the manufacturer as a key team player.
This building type is similar to that of a modular construction system. According to the AIA, “An increasing number of building projects across several markets are using modular construction, the process by which components of a building are prefabricated off-site in a controlled setting and then shipped to the project site and assembled. This approach allows projects to capture the efficiencies gained by integrating the processes and technologies of design, manufacturing, and construction—without having to compromise on aesthetic intent. According to research conducted by McGraw-Hill Construction, when implemented effectively, this approach has been shown to result in a higher-quality building, delivered in a shorter time frame, with more predictable costs and fewer environmental impacts—for example, through reduced material use and waste.”1
Aesthetically, design modifications can include changes in shape, color, building orientation, entry components, daylight strategies, and interiors. All of these are driven by the architect’s vision. Early discussions with municipal planners will pave the way for those communities unfamiliar with the permanence of these structures. One of the key differences in the project delivery of these structures is how quickly they can be assembled. The rapid construction of a revolutionary manufacturing plant in 19 days is a demonstration of how quickly a building can be raised. Coordination of the building envelope with machinery, equipment, and even elaborate interiors is key to successful project delivery.
Blue Origin and New Life Christian Academy, highlighted later in this course, are examples of buildings with multistory mezzanine interiors. By code, a membrane structure, no matter how tall, is classified as a single-story structure. Other examples that follow demonstrate projects that meet LEED Silver criteria and are reused over a period of 25 years in three different locations and for homeless shelters. Some of these projects are located on existing parking lots, while others are on more traditional foundations. They are designed to adapt to all climate challenges. In all of the following examples, the tensioned membrane aluminum frame supported structure provides numerous economic and environmental advantages while exceeding client expectations.
Mission Complete at Blue Origin
It takes a remarkable structure to meet the goals of a remarkable company. When looking to construct their headquarters in Kent, Washington, Blue Origin explored conventional building options but could not wait the estimated two to three years it would take for their structure to be completed. Realizing a traditional construction route was not going to meet the company’s needs, Blue Origin opted for a much faster solution that incorporates energy efficiency, sustainability, and the highest of quality: a tensioned membrane aluminum supported structure by Sprung.
Built in just 11 months, the high-tech facility is visually striking both inside and out, with vibrant colors, acoustically insulated partition walls, and seemingly endless amounts of space for employees to work, gather and collaborate. Featuring ample natural light and amenities that include a garden, fitness facilities, an auditorium and more than 100 conference rooms of varying sizes, the structure was completed on time and on budget, and it now serves as an ideal setting for inspiration and innovation. At a time that requires the reimagining of the construction industry around the world, the demand for a faster, more flexible, cost-effective building solution to adapt to changing needs and emerging markets is more important than ever before.
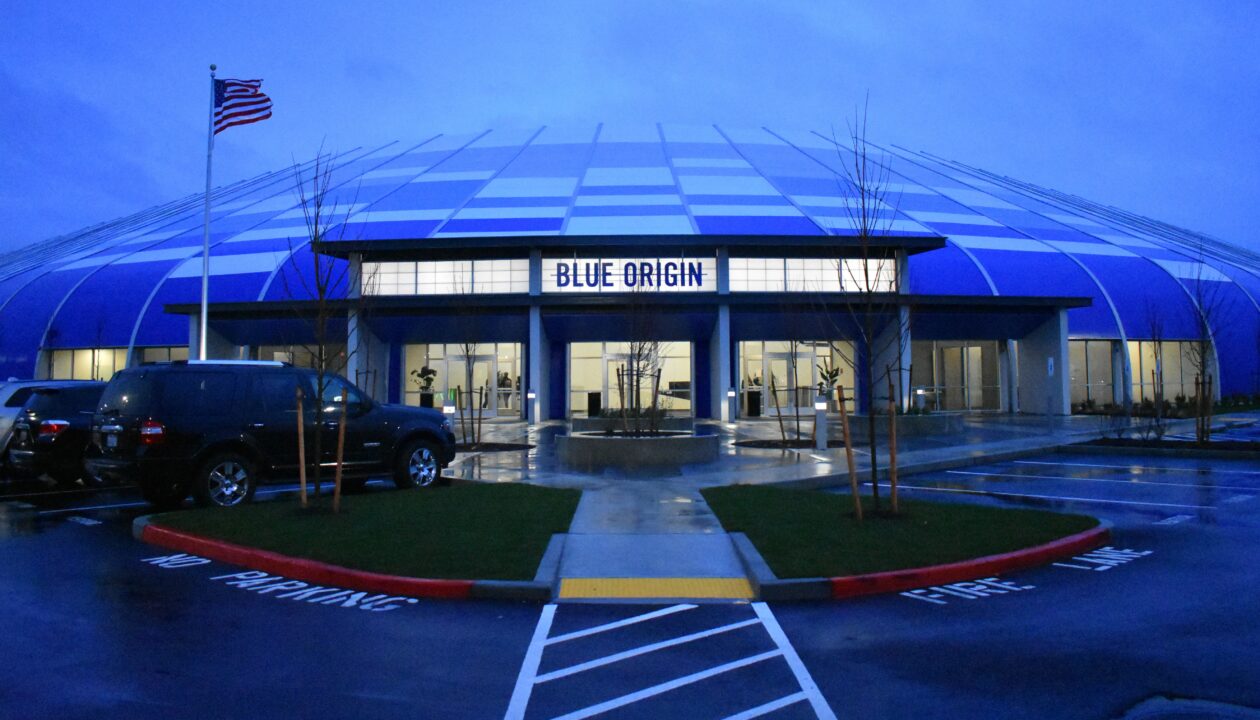
Photo courtesy of Sprung Structures, Inc.
Performance Standards: Analyzing Code Compliance
Engineered tensioned membrane structures have several components. Modular, vaulted frames are assembled as a system braced by intermediary members. The materials and their environmental benefits that comprise these systems include bolted aluminum frames, architectural coated interior and exterior membranes, optional formaldehyde-free insulation packages and skylights, and window and door systems.
As with more conventional modular systems, when selecting a tensioned membrane aluminum frame supported structure, the design professional is required to make more decisions at earlier stages in the project. Communication between the design team, the owner, the manufacturers, mechanical and electrical engineers as well as the contractor and manufacturer’s technicians are critical components of a successful project. The professional armed with certifications of code compliance to strict energy, structural, fire-safety, and occupancy requirements will ease the path to planning and building department approvals. The International Building Code (IBC) include the following definitions to describe membrane supported aluminum frame supported structures:
- A membrane-covered frame structure is defined in the International Building Code (IBC) in Chapter 2: Definitions as a “non-pressurized building wherein the structure is composed of a rigid framework to support a tensioned membrane which provides the weather barrier.”
- Membrane structures are addressed in Chapter 31, Section 3101. Section 3102.1: General states: “The provisions of Sections 3102.1 through 3102.8 shall apply to air-supported, air-inflated, membrane-covered cable and membrane-covered frame structures, collectively known as membrane structures, erected for a period of 180 days or longer. Those erected for a shorter period of time shall comply with the current International Fire Code.”
- The type of construction for membrane structures in defined in Section 3102. They can either be defined as Type IIB or Type V construction. The code states: “…Noncombustible frame or cable-supported structures covered by an approved membrane in accordance with Section 3102.3.1 shall be classified as Type II B construction…Other membrane structures shall be classified as Type V construction.”
- The membrane portion of the structure is to be designed as per the ASCE Standard 55: Tensile Membrane Structures, which states, “This standard provides minimum criteria for the analysis, design, and performance of membrane-covered cable and rigid member structures, collectively known as tensile membrane structures, including permanent and temporary structures…The requirements of this standard shall apply whether the tensile membrane structure is independent of or attached to another structure.”
The code does not restrict the use of this structure to temporary installations. As long as the assembly meets code requirements, these structures can last as long as traditional building systems. Along with the codes that define membranes, the other key areas to consider are the supporting aluminum structure and necessary fire-code requirements.
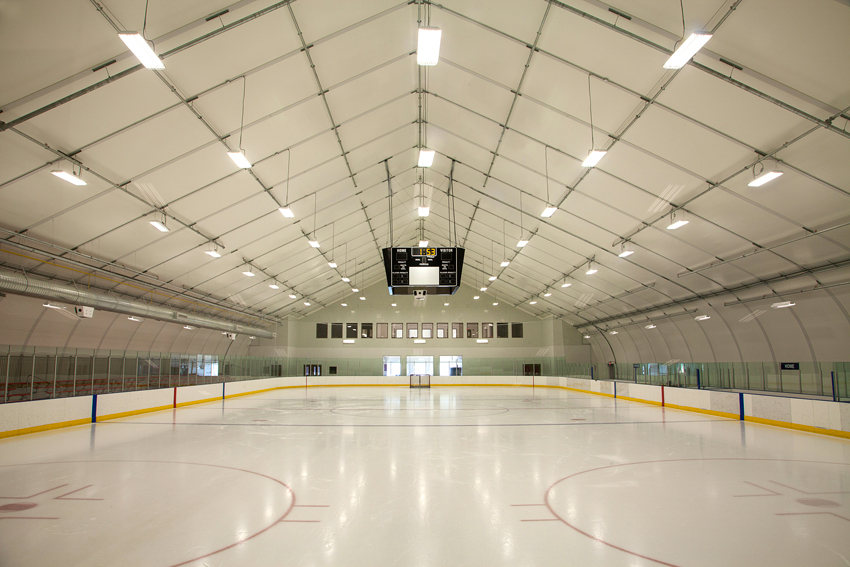
Photo courtesy of Sprung Structures, Inc.
Lightweight aluminum frames allow for large clear-span buildings as demonstrated in the Central Park Arena building in Collingwood, Ontario.
Lightweight Aluminum Frames
The code is specific regarding the aluminum frames. Lightweight aluminum frames provide numerous advantages when used in buildings. Aluminum is recyclable and can be selected with a high content of recycled materials. The use of aluminum in construction allows for easy assembly of components using lighter equipment such as cranes, delivery systems, and crew handling.
The assembly of frames begins with the delivery of premanufactured, engineered aluminum frames. These frames are placed on the site in well-marked pieces in order of assembly. Assembled in place, the frames are hoisted into space and secured to the appropriate foundation. After a review of the structural loading of the building as well as an analysis of soil conditions, an engineer may select an earth anchor as an alternative to a traditional foundation. The lightness of the aluminum frame and membrane building skin contribute to the equation that allow the engineer to select earth anchors instead of concrete footings, which allows these structures to be built on existing parking lots. Commonly used in geotechnical or construction of tents and sports arenas, earth anchors are devices that are engineered for use both in temporary or permanent applications.
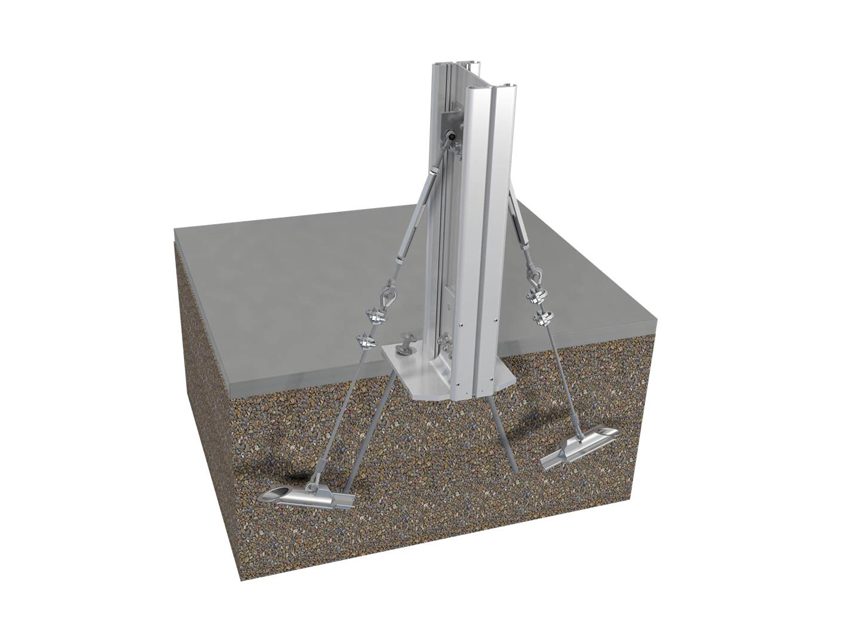
Image courtesy of Sprung Structures, Inc.
This rendering shows earth-anchoring systems for tensioned membrane aluminum frame supported structures.
These aluminum frame supported structures can meet the requirements of Section 507 of the IBC, Unlimited Area Buildings. Structures can be set back accordingly and sprinkler systems can be installed. Chapter 20 of the IBC, section 2002 does allow for aluminum to be an acceptable structural building material.
The large structural aluminum frames are designed to support the weight of the structure and any additional utility or equipment loads as well as wind and snow loads. This type of building can be engineered to meet even the most stringent hurricane loading conditions. After the frame is erected, an exterior membrane is winched into place between the frames, then tensioned with a 10-ton hydraulic jack and ram. This provides an exterior skin for the building. Electrical and mechanical systems are placed in the frame along with an extensive network of accessible power requirements and ventilation systems that maximized flexibility for future equipment modifications.
An interior membrane is winched into the frame. This membrane can be insulated and provides the finished surface of the interior. Mechanical and electrical access panels are placed along the interior walls. Skylights, doors, windows, transparent panels enclose the finish structure. Attachments to the structure of mechanical systems, sprinklers, lighting, and heavier equipment is engineered into the structure using direct connections to the bottom flange of the beams reviewed on a case-by-case basis.
The IBC Chapter 20, Section 2002: Materials allows the use of aluminum for structural materials. The Aluminum Association’s Aluminum Design Manual 1 (ADM1), Chapter 35, references Part 1-A: Specification for Aluminum Structures, Allowable Stress Design and Part 1-B: Aluminum Structures, Load and Resistance Factor Design (1604.3.5, 2002.1). Structures are to be designed using the minimum load requirements as referenced in Chapter 16 using accepted engineering practices.
Aluminum is durable, lightweight, long lasting, and one of the most recycled metal products in today’s market. Aluminum frames used as the skeletal spine are as easy to mount into place as well, as they are easily demountable to be reused. Connections are fitted and bolted rather than welded, as would be typical in a steel substructure. The structural system is engineered to withstand high wind loads and shed snow. These substructures are 100 percent recyclable with no loss of quality when reused in another product.
Fire Code Advantages
As listed above, the approved membrane to which Section 3102.3.1 is referring is to “meet the fire propagation performance criteria of NFPA 701 and the manufacture’s test protocol.” Typically, architectural membranes that are used as membrane structures would need to comply with NFPA 701, ASTM E-84, California State Fire Marshall, and the Canadian standards CAN/ULC-S-109 and CAN/ULC-S-102 fire-test standards to meet the intent of the building code. Typically, the architectural membrane is considered non-rated and the aluminum supporting framework can be considered noncombustible. This would define this structure configuration as Type IIB construction. Type IIB construction is the most common type of construction used in building materials. In conjunction with the membrane, and as per testing on behalf of the American Aluminum Association, 6,000 series aluminum also meets the noncombustibility requirements of ASTM E-136. Therefore, Type IIB construction for tensioned membrane aluminum frame supported structures is applicable.
Tensioned membrane aluminum frame supported structures are a complete building system. The interior is the finished wall system. Depending on the use and occupancy classification, the membrane acts as the interior finish and will need to meet the requirements of Section 803.1. Membranes can be specified with a Class A rating as per the testing requirements of ASTM E-84 with a flame spread of 25 or less and a smoked developed index of 450 or less. The membrane manufacturers need to provide the necessary documentation to ensure that the membrane meets the requirements of the IBC.
Based on experience with this type of structure and as attested to in the commentary section Appendix CA of ASCE 55, membrane structures can be considered as safe or safer than conventional structures for the following reasons:
- An internal fire source may generate sufficient heat to damage the architectural membrane, which allows for the venting of smoke and heat.
- High-vaulted ceilings create a smoke reservoir in the roof area, leaving the floor clear of smoke. This makes it easier for the public to safely exit the structure and for fire fighters to locate and extinguish the fire. This also provides early heat and smoke venting reducing the risk of flash over.
- Roof monitors with dampers can be installed to remove smoke as it collects in high roof (smoke reservoir) areas.
- Conventional sprinkler and fire alarm systems can be installed into membrane structures. Low-heat sprinkler heads are also available for these structures.
Although first generation tensioned membrane aluminum frame supported structures tend to be one-story clear-span buildings, new projects include those with interior partitions, and some include mezzanines which can be used based upon one-third of the structure area. When designing a path or travel, emergency exits with panic hardware can be installed into the membrane structure as well as into interior partitions. Exit distances and widths can be adjusted based on occupancy accordingly.
Photo courtesy of Sprung Structures, Inc.
Performance Architectural Membrane
The architectural membrane of a tensioned membrane structure provides the exterior wall, the roof and the finished interior surface of the building. Architectural membranes weigh from 18 to 24 ounces per square yard, making them one of the lightest finish building envelope materials available to a design professional. All-weather outer membranes are delivered on-site in rolls and winched along the frame from one side to the other using spacer bars, similar to the lofting of a sail. The membrane panels are tensioned across a spreader bar in the frame, and insulation is added to the ribs as well as an interior membrane, tensioned into place by hydraulic machinery. Manufacturers supply training and assistance to contractors as to the handling of the unique interior and exterior finish materials that are also part of the structural system. Jobsite quality standards for handling membranes to avoid scratches or blemishes on interior walls and ceilings should be developed and monitored during construction. The membranes have a selection of protective coatings available, from acrylics and polyurethanes with 15- to 20-year life expectancies to Tedlar and Kyner with 20- to 30-year life expectancies.
Membranes can have translucent surfaces to allow for additional daylight. Membranes can also be fitted with door and wall sections. The top sections of both the exterior and interior surface of the membranes are designed to allow for optional skylights along the apex of the spine of the building. These provide an abundance of natural light for high-ceiling structures.
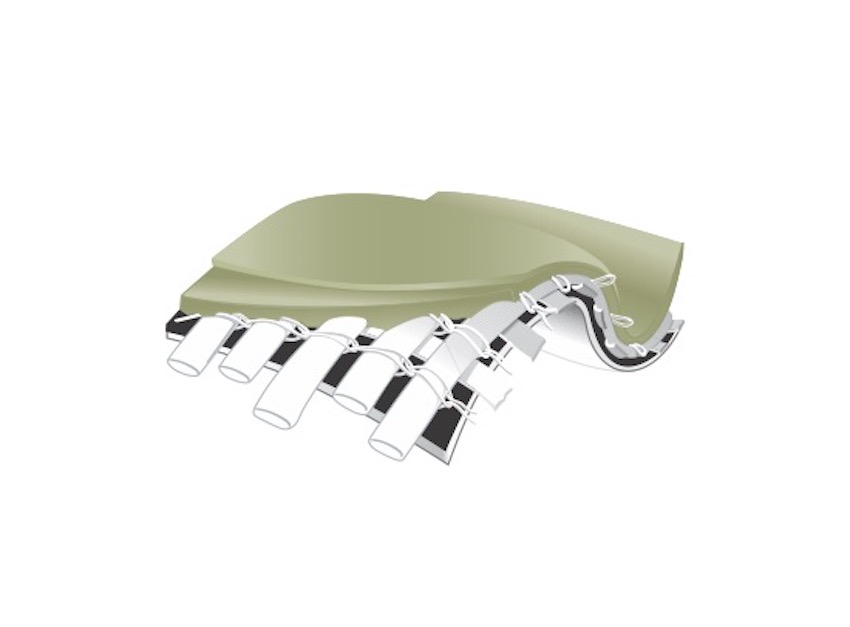
Photo courtesy of Sprung Structures, Inc.
Guaranteed Architectural Fabric Membrane.
By code, a fabric is defined as a two-dimensional cloth made up of yarns or slit tapes that may be impregnated with a matrix that binds them together. The yarns may be woven or laid, frequently coated or laminated. Membranes are defined as the flexible, coated, or laminated structural fabric of film that supports imposed loads and transmits them to the supporting structure. The membranes in a tensioned membrane structure carry only tension or shear in the wrap direction of the membrane. Although tension membrane structures are engineered to have some movement in the frames, because the membrane is fed through extruded channels in the aluminum I beam, there are no wear points. When it is time to replace the membrane, sections can be replaced in segments without exposing any interior furnishings or fixtures. These surfaces can be specified with a protective film coating that will guard against ultraviolet rays as well as airborne contaminants. A durable, colorfast membrane can be provided with a warranty for 25 years. Membranes can be specified with a solid color or printed with an unlimited selection of patterns, logos, photos, and symbols. They can be selected in multiple colors to match existing surfaces.
A Complete Building Enclosure
When the engineering of the building’s climate protection is delivered as a complete wall system, the skin of the building contains the thermal insulation plus air and vapor barriers. Providing excellent thermal performance, air permeability is close to zero in these buildings. Insulated floor surfaces are completed in a similar manner to that of a traditional slab-on-grade building. All building systems that penetrate the exterior are achieved by the use of engineered fittings using framed penetrations or frameless penetration kits.
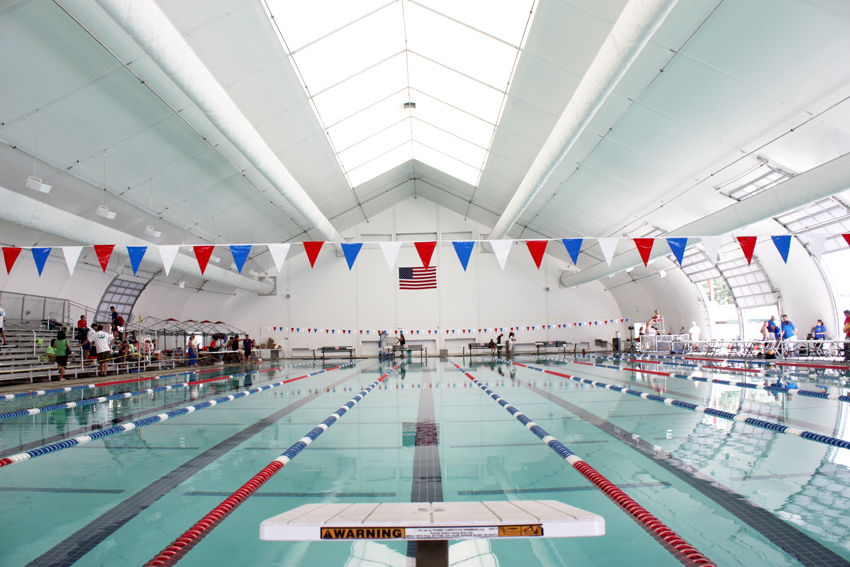
Photo courtesy of Sprung Structures, Inc.
Kearns Oquirrh Park Fitness Center houses a 50-meter Olympic-size pool in a 23,400-square-foot, state-of-the-art, daylit swimming facility.
Architectural membranes can be selected with high-performance insulation to meet arctic climates or designed for relocation. These high-strength rip-stop membranes are fire resistant and durable. A blackout layer can be specified to prevent solar gain to manage climate control and a daylight membrane specified to provide an abundance of natural light, reducing lighting costs.
Examples of the climate adaptability of these structures include those that are installed at the North Pole and South Pole, as well as those used by the U.S. Military in the Kuwait desert. The Missile Defense System integrated architecture at Fluor Alaska, located in Shemya, Alaska, is engineered to withstand wind loads of 120 miles per hour. The Warwick Le Lagon Resort & Spa in Vanauata, in the South Pacific, was used as a storm shelter on March 13, 2015 during Cyclone Pam, a category 5 cyclone. The facility at Kirkwood Mountain Resort in Lake Tahoe performed perfectly during a period of record snowfall of almost 10 feet by continuously shedding the snow off its roof. These are among the many examples of the strength of the membranes supported on aluminum frames.
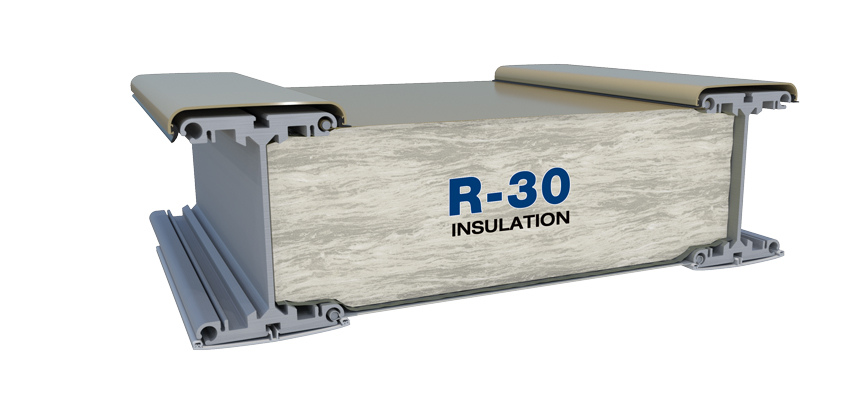
Image courtesy of Sprung Structures, Inc.
Shown is a cross section of a 9- and 8-inch beam with R-30 formaldehyde-free insulation.
Energy Ratings: High-Performance Insulation
Insulation provides comfort in both hot and cold climates. Insulation reduces the cost of climate control as well as absorbs sound for better acoustics. A comprehensive insulation package for a tensioned membrane structure includes vapor barriers, thermal breaks, and a tensioned, finished interior liner. Additionally, membranes are designed to have low air and vapor permeance.
Frames are designed to accept a “sandwich” of fiberglass batting and are part of the membrane system. In any building, holes in the insulation can dramatically reduce its performance, and multiple layers of insulation may merely add to dead air spaces between each layer, negating much of the insulation value. An engineered insulation system remains in place and does not slide down the roof and bunch at the base of the wall. The specified R-value is uniformly maintained, as there are no pinch or bunching points from floor to ceiling throughout a membrane system.
Formaldehyde-free fiberglass insulation is available as part of a complete insulated building package and assists with meeting green rating system goals. Formaldehyde is a colorless, flammable gas at room temperature and has a strong odor. It can be found in numerous building products. According to the Environmental Protection Agency, exposure to formaldehyde may cause adverse health effects from mild allergic reactions to more serious neurological effects. An insulated membrane system can be specified as part of the membrane system in up to a 9-inch thickness (R-30). R-values are a measure of thermal resistance. ENERGY STAR recommends an R-30 value for most climate zones in the United States for roofs. In a membrane system, an R-30 system is both the roof and the walls, and the system can be designed to meet climate standards from -60 degrees Fahrenheit (-51 degrees Celsius) to 122 degrees Fahrenheit (50 degrees Celsius). Fiberglass insulation can be specified with third-party certifications to have a minimum recycled content of 25 percent, comprised of 20 percent post-consumer bottle glass and 5 percent post-industrial glass. Innovative insulation systems have already been developed to improve the overall R-value of the roof of the structure (above R-30) to meet some of the new energy codes.
A 20-year life-cycle analysis of a full-size hockey rink tensioned membrane aluminum frame supported structure in Canada provides some startling statistics. The rink features an ultra-high-efficiency refrigeration system designed to dehumidify the ice arena, heat the domestic hot water, and heat the arena offices, arena, and lobby. The refrigerant was designated to have no negative effects on the environment in line with the Montreal Protocol. After its completion in January 2015, actual energy data and energy bills were collected and compared with the average Canadian ice arena using a comprehensive Natural Resource Canada report. The results show that Shawnigan Lake School will save the school more than $850,000 in future energy cost. These energy savings considered the base electrical charge, power factor, and demand charge of Shawnigan Lake School.
Comparisons with Traditional Construction
In addition to favorable comparisons on energy savings, there are numerous other ways that tensioned membrane aluminum frame supported structures stack up to other building types. When comparing oranges to oranges, this chart shows a few key advantages of tensioned membrane aluminum frame supported structures.
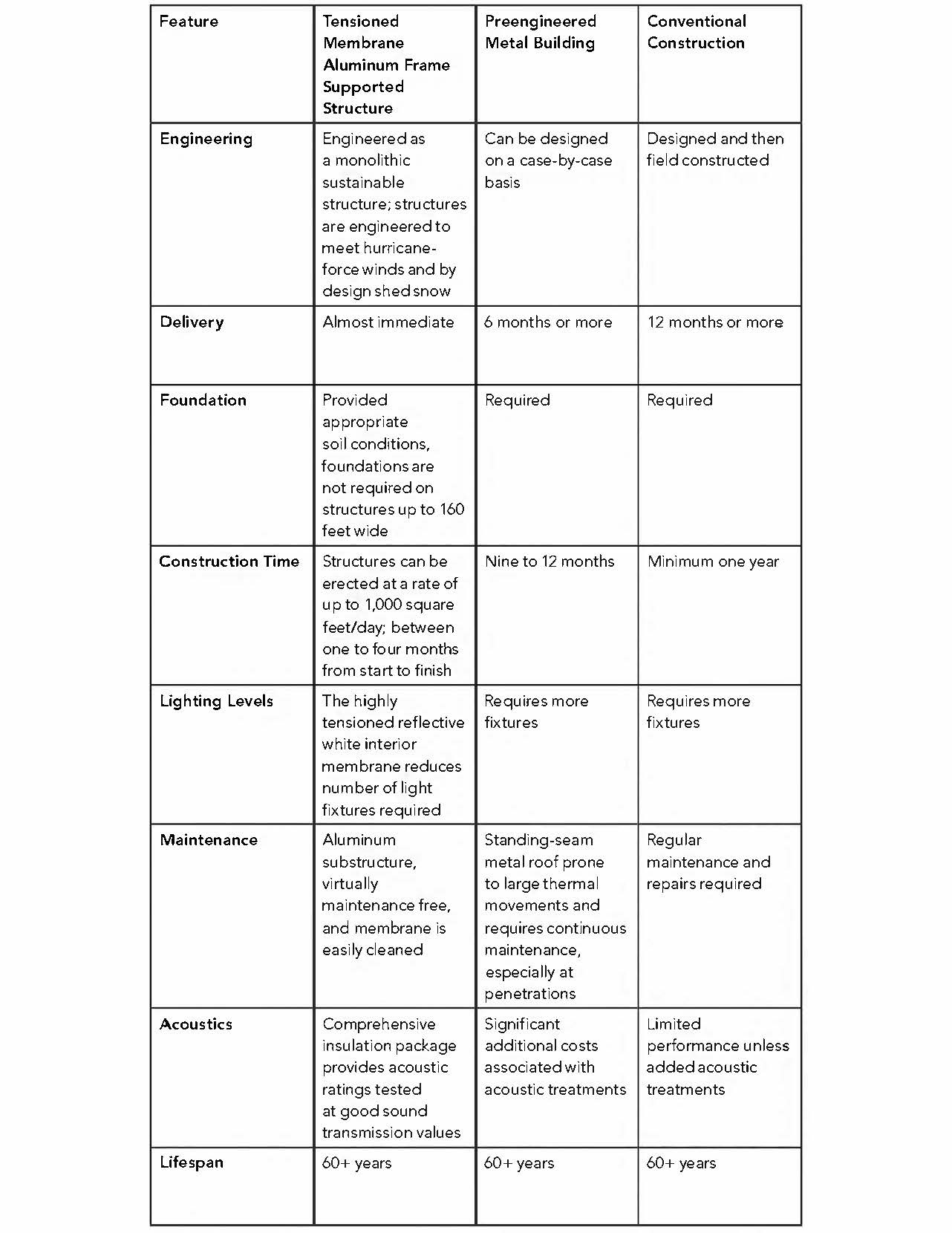
As a new building type, tensioned membrane aluminum frame supported structures are a new way of thinking through the construction process and the delivery of a green building.
Going for Silver: LEED Certification Submittals
The South Carolina Criminal Justice Academy provides basic and advanced training to law enforcement personnel. Planning for a new basic training village included the construction of a new dining, classroom, and gymnasium as well as a new four-story dormitory building. Section 48-52-830 of the South Carolina Energy code requires that all major projects “must be designed, constructed, and at least certified as receiving two globes using the Green Globes Rating System or receiving the LEED Silver standard.”4 The team chose the LEED standard. In obtaining certification as meeting the LEED Silver standard, a major facility project must earn at least 40 percent of the available points for energy performance under Energy and Atmosphere: Optimize Energy Performance credit.
Tensioned membrane aluminum frame supported structures were chosen for the 60-foot by 150- foot dining facility, the 70-foot by 157-foot classroom facility, and the 90-foot by 178-foot gymnasium. All three of these buildings achieved LEED Silver status (under the LEED BD+C 2009 V3) in time for the grand opening. The manufacturer submitted certified product test reports that supported the following credit points:
- Sustainable Sites 7.2: Heat Island Effect Roof Test Results from Membrane Manufacturer
- ASTM C1549: Total Solar Reflectance
- ASTM C1371: Emmitance
- ASTM E1980: Solar Reflectance Index (SRI)
- LEED Energy and Atmosphere: Optimize Energy Performance (P1: Fundamental Commissioning and P2: Minimum Energy Performance both required)
- ASHRAE 90.1-2007: Certificate of Compliance
- Report on Envelope Airtightness Testing
- LEED Materials and Resources 4.1: Recycled Content and Materials and Resources 4.2: Recycled Content
- Aluminum Recycled Content Certificate (In this case, the manufacturer was able to certify a recycled content greater than 50 percent.)
- Insulation Recycled Content Certificate: A minimum recycled content of 25 percent comprised of 20 percent post-consumer bottle glass and 5 percent post-industrial glass
- LEED Environmental Quality 4.1: Low-Emitting Materials: Adhesives and Sealants
- Door Transition Package (VOC) Certificate
- Additional innovation credit for the ability of this building to be dismantled and reconstructed demonstrated by the reuse of the Canyons Ski Resort.
Over the past eight years, new advances in technology since this certification have only increased the sustainability properties of this energy-efficient building system.
Occupant Well–Being
The following two examples highlight the benefits to occupants of tensioned membrane aluminum frame supported structures. The first is one of many churches that have adapted these buildings as worship facilities. The second is a corporate office that pushes design and maximizes the use of natural daylight to create a state-of-the-art open office facility.
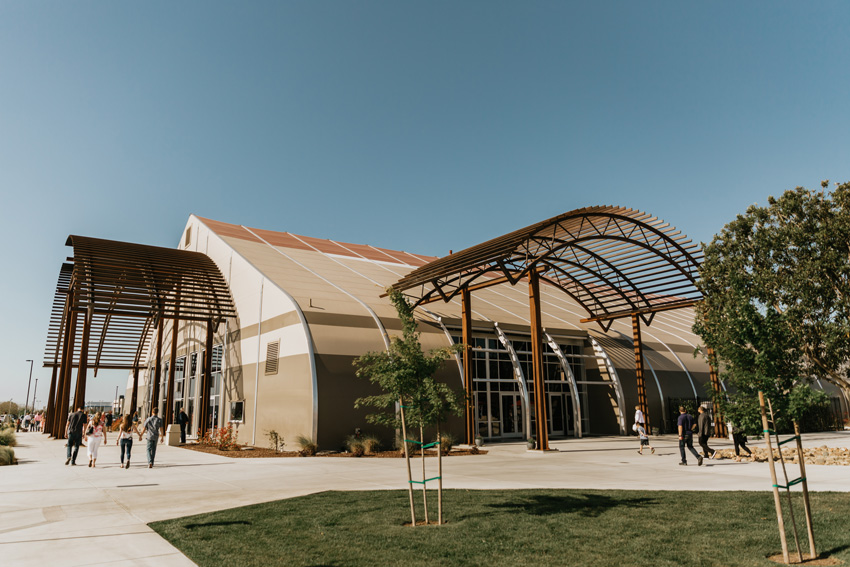
Photo courtesy of Sprung Structures, Inc.
The pastor of New Life Christian Center in Turlock, California, reports that the “facility is state of the art, half the cost of traditional construction, and three times faster to build.”
Ministry Not Mortgages
Dr. Brett C. Avery, executive pastor at New Life Christian Center in Turlock, California, is enthusiastic about the tensioned membrane aluminum frame supported structures chosen for their ministry. This is an “innovative, highly creative, kingdom-focused building. The team gave us a permanent facility that exceeded our expectations and allowed us to invest in ministry not mortgages,” he says. “This facility is state of the art, half the cost of traditional construction and three times faster to build.” After evaluating the cost of a new structure for a growing congregation, the pastor chose an unusual alternative. This 150-foot-wide by 212-foot-long building includes an open-concept foyer with daylight panels that serves as a gathering area.
The facility is comprised of a three-story mezzanine core. This core includes a state-of-the-art worship center with seating for 1000 people, a cafe, an expansive lobby, and a kid’s space. The facility provides more than 31,000 square feet on the first floor and more than 8,000 square feet of mezzanine space. The third floor provides space for the mechanical systems. The core of the building is constructed of traditional building materials, and this mezzanine is designed to allow parishioners to overlook the meeting areas and sanctuary.
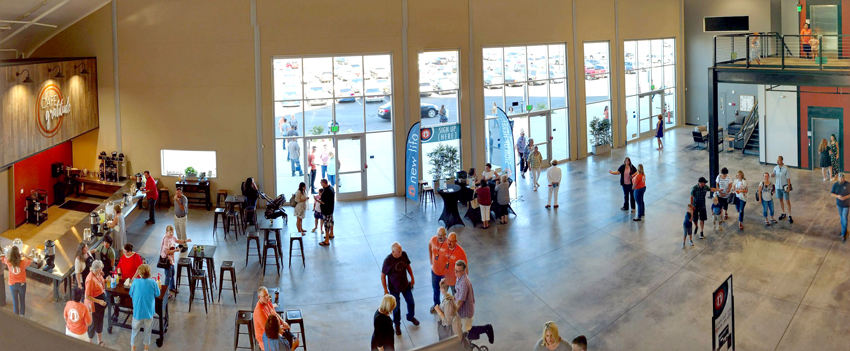
Photo courtesy of Sprung Structures, Inc.
The design of the New Life Christian Center includes an impressive open-concept foyer that serves as a gathering area.
The design includes an impressive open-concept foyer that serves as a gathering area. This high-ceiling daylit space provides access to a break area, meeting rooms, and leads into the sanctuary. The sanctuary seats almost 1,100 people and houses a large platform stage, a prayer room, an usher’s room, and a nursing room with a view to the sanctuary. The long-term cost of ownership was a major consideration for this congregation. The insulation factor and eco-friendly construction provided both a lower dollar per square foot initial investment and significant savings in heating and cooling in the hot, dry climate of the Central Valley in California.
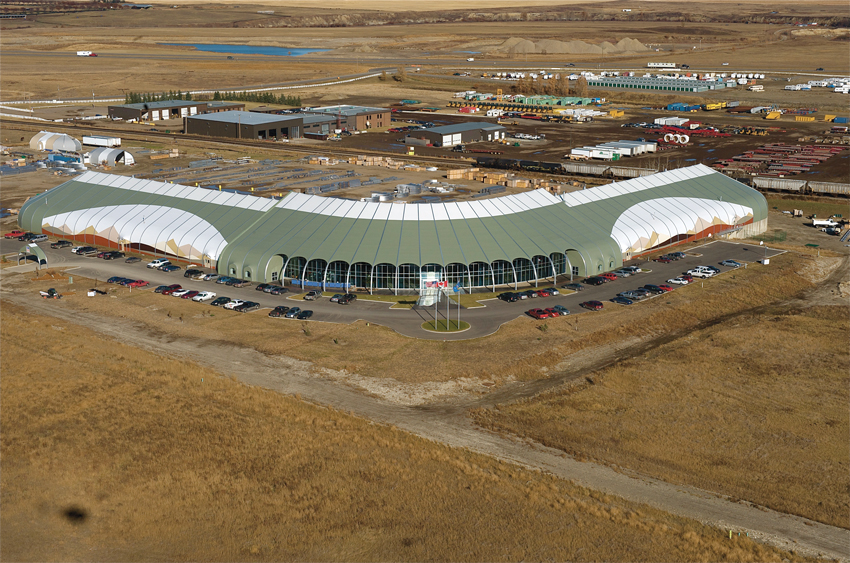
Photo courtesy of Sprung Structures, Inc.
This 150,000-square-foot fully insulated tensioned membrane aluminum frame supported structure equipped with two manufacturing wings and office space meets the stringent environmental and occupational goals of its owners.
View of the Rockies
Completed in 2007, one of the factories of this membrane manufacturer is located on 100 acres in Alberta, Canada. This 150,000-square-foot fully insulated tensioned membrane aluminum frame supported structure includes two manufacturing wings and office space. The building is fully insulated with R-30 formaldehyde-free insulation. Translucent panels are set into the peak of the architectural membrane.
The center core of the facility includes a 30-foot-high glazing wall that provides breathtaking views of the Rocky Mountains. The facility includes a restaurant, gymnasium, indoor gardens, lounge, athletic center, and corporate offices. The two wings of the structure house state-of-the-art manufacturing facilities for aluminum and membrane fabrication. The open plan of this office complex provides views through the building. Most employees have direct access to natural daylight, and high translucent skylights provide additional natural light. This facility feels as though one is working in a large botanical conservatory with high-end atmospheric and environmental controls.
The building is open and welcoming. An arcade of aluminum arches that surrounds the membrane allows for large windows. The mezzanine core of the building provides additional offices, meeting rooms, and balconies that overlook the gardens and first floor offices and lobbies. The campus also includes a new greenhouse that grows up to 17,000 plants 365 days a year for employees and local restaurants. The temperatures in Alberta, Canada, can range from 35 degrees Celsius (95 degrees Fahrenheit) in the summer to a frigid -40 degrees Celsius (-40 degrees Fahrenheit) in winter. The buildings are energy efficient and meet high-performance standards as well as environmental standards for the comfort of its occupants.
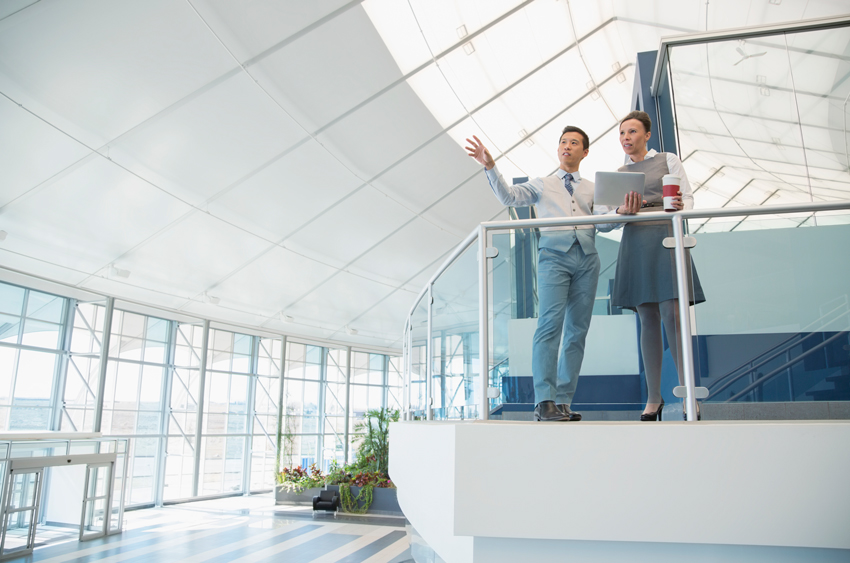
Photo courtesy of Sprung Structures, Inc.
Shown is the garden interior of the membrane manufacturer’s Canadian headquarters.
Aesthetic Revolution
Tensioned membrane aluminum frame supported structures are part of a 21st century aesthetic and engineering revolution. There are many designers challenging the norms of construction and working with engineers to find new sustainable solutions to modern-day problems. Breakthroughs in prefabrication, material science, and engineering are creating new building types with high-performance energy ratings.
The uses range from high-end office buildings to manufacturing. Portable, affordable, and permanent membrane structures are being used to support disaster assistance and homeless shelters throughout the world. As Musk discovered, tensioned membrane aluminum frame supported structures can provide the same functions as traditional buildings at a lower cost and faster construction time.
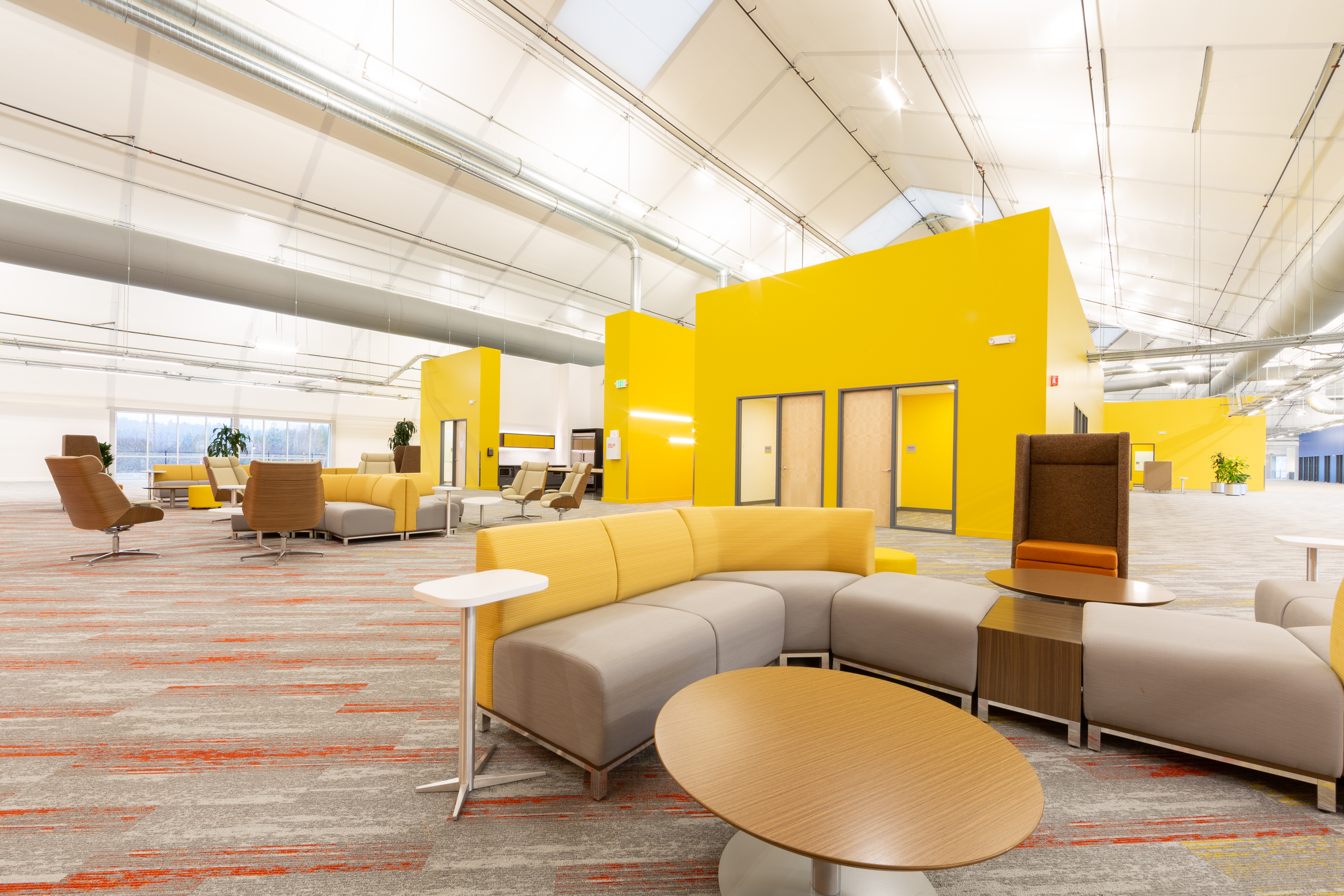
Photo courtesy of Sprung Structures, Inc.
These buildings provide expansive natural light both as part of a window or skylight system but also by providing an overall translucent light throughout the structure that maximizes occupant well-being. They provide a superior building enclosure that’s airtight and energy efficient. They are modular and can be deconstructed for relocation. They can provide large, open clear-span spaces used in facilities such as pools, gymnasiums, hockey rinks, aviation sheds, and even manufacturing plants. A structure up to 160 feet wide where appropriate soil conditions exist can be built on an existing parking lot. They are affordable and can be leased, or purchased.
Membrane supported aluminum structures are a sustainable alternative to traditional construction for the future. As Musk points out while discussing the new TESLA plant: “If conventional thinking makes your mission impossible, then unconventional thinking is necessary.”
End Notes
1Design for Modular Construction: Modular Construction. National Institute of Building Sciences. The American Institute of Architects. Web. 2 April 2019.
2Boudette, Neal E. “Inside Tesla’s Audacious Push to Reinvent the Way Cars Are Made.” The New York Times. 30 June 2018. Web. 2 April 2019.
3Lesley Stahl. Tesla CEO Elon Musk: The 60 Minutes Interview. CBS News. 9 Dec. 2018. Web. 2 April 2019.
4The South Carolina Code of Laws Unannotated. Title 48 – Environmental Protection and Conservation. South Carolina Legislature. Web. 2 April 2019.
Celeste Allen Novak is an architect and author whose Michigan practice focuses on sustainable and universal design. www.linkedin.com/in/celestenovak