Digital Fabrication and Natural Stone
Transformative digital technology now provides enhanced opportunities to choose natural stone for contemporary and traditional projects
Continuing Education
Use the following learning objectives to focus your study while reading this month’s Continuing Education article.
Learning Objectives - After reading this article, you will be able to:
- Discuss the benefits in the design and specification for natural stone fabricated and installed through the adoption of precision digital technology.
- Define new standards developed to measure, document, and verify efficient, sustainable practices throughout the life cycle of natural stone.
- Identify key considerations in the selection, design, and specification of natural dimension stone to maximize performance, durability, and sustainability.
- Explore innovative examples of natural stone used for its functional and artistic potential in buildings and landscapes around the country.
For more than 30 years, Sidney Hornstein, a geologist and environmental educator emeritus at the American Museum of Natural History, has provided tours for architects to walk through time by visiting some of Manhattan’s iconic stone buildings and parks.1 This tour of building stones in lobbies, on facades, sidewalks, and curbs provides a trip through time and across the globe. He identifies rock varieties from North America, Europe, Asia, South America, and Africa ranging in age from 1 to 3 billion years. From Rockefeller Center to the Empire State Building, these permanent icons of the city were also expressions of geological history. Natural stone used in buildings provides a record of prehistoric events and connects humans to the natural world.
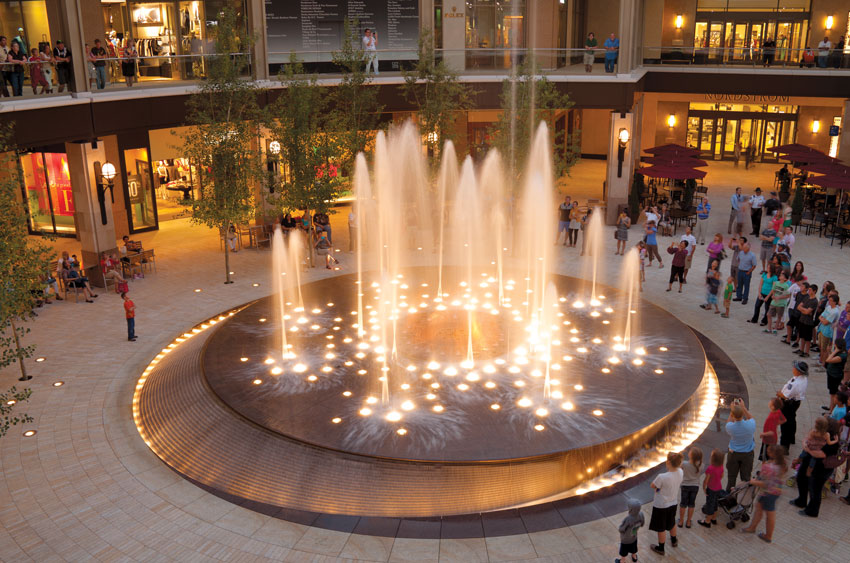
Photo courtesy of Martin van Hemert
New digital fabrication techniques allow the eruption of fire and water from this natural stone fountain at City Creek Center in Salt Lake City. The stone manufacturer meticulously fabricated a total of 176 perfectly positioned holes for water jets and light fixtures and 49 holes for gas-fueled fire nozzles, providing the exacting precision required for this dramatic public space.
Today, the curious can also take a guided walk through London, using an interactive map of natural stone in the urban setting. The walk directs observant geologists and curious design professionals to places where they can see crushed shells, bones, fossils of prehistoric reptiles, a variety of limestone seams, and granite crystals created by a meteor hit.2
The authenticity of a material has been a hot topic of aesthetic research and discussions from the beginning of the Industrial Age through the Modern era. In the “Seven Lamps of Architecture,” John Ruskin argues for material structural and functional purity. This document and others were the basis of continued design initiatives by Modernists and others to choose materials that were not imitations of the original material. When used as a contemporary cladding and not a structural system, natural stone retains its original unique characteristics. No two stones are alike, and the variations provide a wealth of creative opportunities.
In order to provide a change of light reflectance on buildings, walkways, and other exteriors, a monolithic surface needs to be manipulated. The surface of natural stone can be varied to change its characteristics. For example, granite may both sparkle in the sunshine or provide a mirror reflection of its surroundings.
Whether specified for a building facade or for exterior stairs, ramps, walls, fountains, and walkways, the performance, permanence, durability, versatility, resiliency, and beauty make stone a primary construction material for buildings and landscape applications that are meant to last for centuries when specified correctly.
Natural stone provides a connection to the environment and a history of human construction. This material is timeless and chosen by architects for buildings meant to last for centuries. Granite, limestone, marble, onyx, quartzite, sandstone, serpentine, slate, soapstone, and travertine are just some of the natural stones used in buildings.
Granite (from the Latin granum, or grain, signifying its characteristic structure), an igneous rock, was formed billions of years ago when magma cooled deep beneath the earth’s crust. Nearly as durable as diamond, granite owes its density and hardness to its origins, solidified deep within the earth under extreme pressure. Marble (and its wildly varying relatives: travertine, limestone, and onyx) is a metamorphic form of limestone.
Granite is a hard rock suitable for use on exteriors for paving, walls, and building exteriors. Marble was formed when sediment and other materials forged together beneath the weight of heavy bodies of water. After millions of years, these crystallized minerals resulted in a natural stone that is typically white with streaks of color, capable of taking a hard polish. Different types of stone can be used for different applications depending on the technical properties and the applied use on a building interior, exterior, or landscape areas. All natural stone is classified as a nonflammable, Class A building material, and design professionals examine technical properties such as the natural stone’s water absorption, compressive strength, and frost resistance before selecting a type of stone for their project.
There are many misconceptions about the use of natural stone. Architects may avoid this material if they feel that their creativity will be limited when using natural stone in contemporary design. This happens if they don’t realize that this product can be used when designing complex geometric shapes. The following examples are proof that today’s architects are applying natural stone in creative and inventive designs because of new digital advances in the stone industry as well as the timeless beauty inherent in this natural material. These architects, landscape architects and artists, are exploring the value of using various finishes and new fabrication technologies to achieve their aesthetic objectives. The following case studies demonstrate the many benefits of using natural stone as well as the new and creative ways that technology continues to enhance the way stone can be used.
Identical Granite + Multiple Finished = Unified Design
Diocese of Wheeling-Charleston Campus Plan, Wheeling, West Virginia
Finishes bring variety and versatility to a project and can unify the design palette. Some fabricators have developed a wide variety of finishes that increase a designer’s choices for applications throughout a project, both inside and outside.
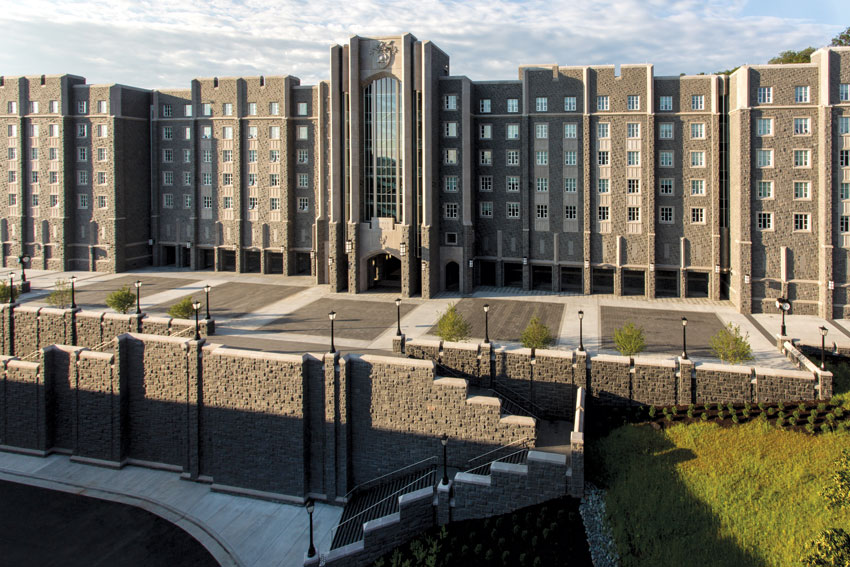
Photo: © Amesse Photography
When constructing the new barrack at West Point, the design team chose to match the existing feel and color of the 200-year-old campus’s gothic revival architecture. It chose two types of black granite in order to provide the Army with new campus structures that will last another 200 years.
Different finishes accent different surfaces, and they can be used as clues for wayfinding. For example, a different finish can indicate the approach to a bench, stairs, or object. A different finish can be used to help create a slip-resistant surface applied as a universal design principle or create a highly reflective, smooth surface that magnifies the stone’s appearance.
The new Diocese of Wheeling Campus Plan in Wheeling, West Virginia, provides the first example of how a design team used the change of finish for both practical and dramatic effect.
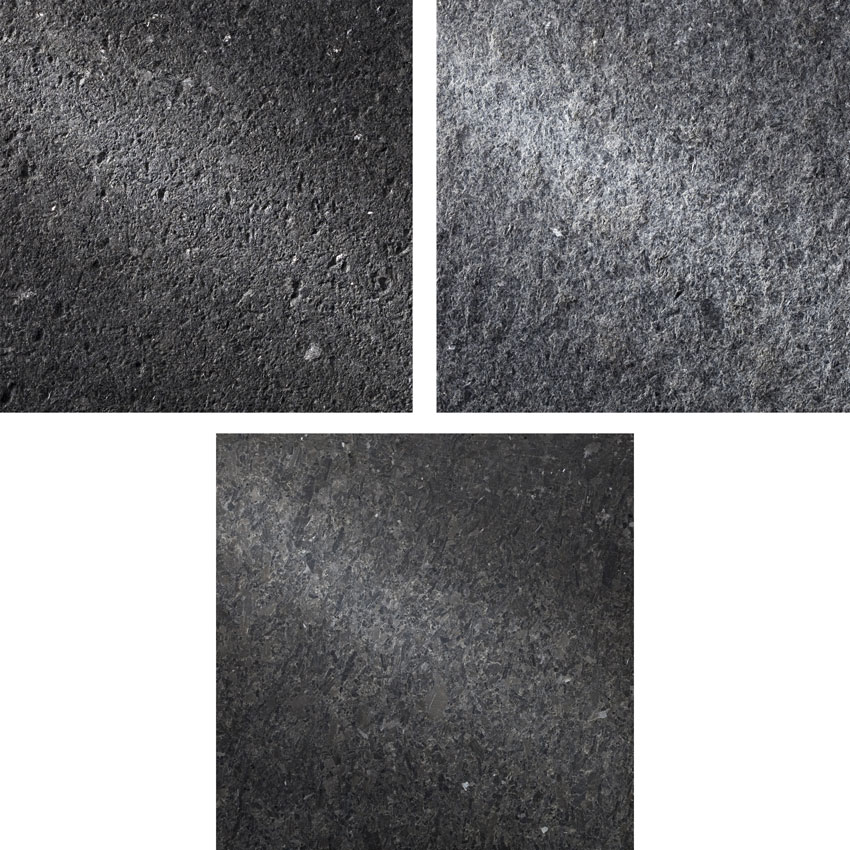
Image courtesy of Coldspring
Approximately 6,000 square feet of black granite unified the design of the new Campus Diocese of Wheeling, West Virginia. Working closely with the fabricator and granite supplier, Michael Stern ASLA, LEED AP, notes, “By varying the finishes, we created different looks with the same stone.” Multiple finishes are available from the same natural stone that change the look of the stone while unifying the projects materials.
The architect and landscape planner chose black granite with a complex crystalline structure as the primary finish material. “We used the same black granite for many elements in this project—from fountains and pools to paving and steps,” says Michael Stern, ASLA, LEED AP, founding principal of Strada Architecture, Pittsburgh and Philadelphia.” This granite is known for its medium black and gray hues, which are more or less pronounced depending on the finish selected.
The existing rectory was built of sandstone that was echoed for key design elements on the chancery’s new wing. Designed by architect Edward Weber and completed in 1926, the historic Cathedral of Saint Joseph is a Neo-Romanesque style with windows laced with decorative stone elements. Limestone and many other natural stones are present at the site. “With the variety of natural stones at the site, the use of granite for all walkway areas creates a uniform contrast on the ground plane,” says Stern. “Granite was the unifying material at the site—tying together all the other materials.”
In 2011, the diocese initiated a major reorganization project for the campus of St. Joseph Cathedral, where the diocese had outgrown its existing 1950s-era chancery that houses the diocese’s administrative offices. The existing campus included numerous buildings serving the area’s Catholic community: St. Joseph Cathedral, the chancery, rectory, and archives, as well as a high school and elementary school. Plans for the reorganization included closing the existing elementary school due to low enrollment and renovating the building into a new chancery.
This reorganization also involved the construction of landscape elements that would connect the old and new areas of the site and create enduring public spaces. These included the development of a community central courtyard and a garden dedicated to the Virgin Mary, adding to the sense of place and worship. A new fountain in the courtyard adds elements of movement and sound, creating an inviting and serene gathering area.
Approximately 6,000 square feet of black granite unified the design of the new campus. Working closely with the fabricator and granite supplier, Stern notes, “By varying the finishes, we created different looks with the same stone.”
The lightest finish was selected for the pedestal of the St. Joseph statue in the plaza and the paving around the plaza tree bosque. (A bosque is a group of trees planted in a geometric grid. An element of spatial design that can be seen in ancient to contemporary gardens, the bosque symbolizes a forest and provides shade in public settings.)
A hone finish that highlights the stone’s crystal structure while deepening its background hues was selected for cubic benches in the Marian garden area, the fountain’s paving and coping, and the main fountain feature. It also provided the ideal finish for a pedestal for a statue of the Virgin Mary, which stands peacefully in the Mary Garden outside the archives building. This was a darker shade than the more textured finish used in the granite for pavers and stairs.
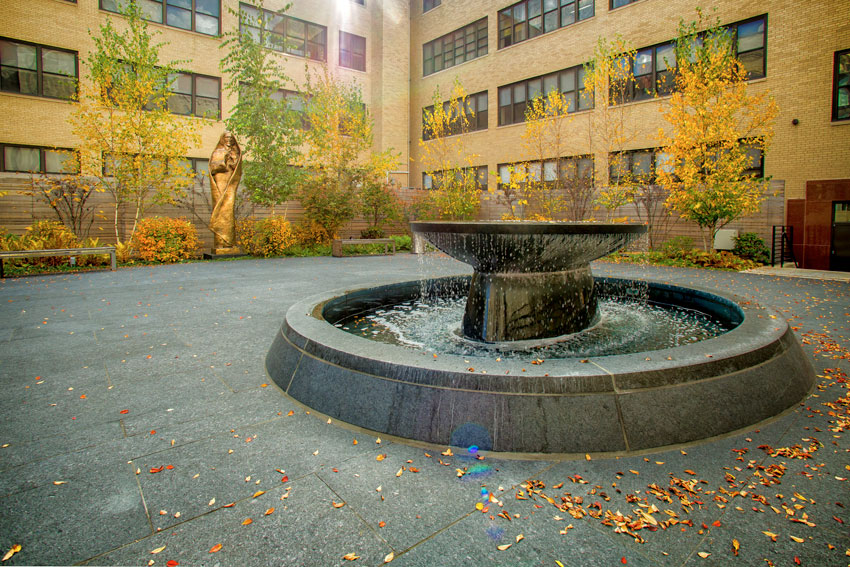
Photo: Prestige Photography
Precise fabrication using computer-aided design and CNC machines was essential for the fabrication of the fountain’s base and bowl. A hone finish that highlights the stone’s crystal structure while deepening its background hues was used for the fountain and paving in the courtyard.
For pavers and steps, a rough, slip-resistant surface was required for pedestrian areas. Natural stone materials vary with finishes, and the fabricator recommended a surface treatment that would provide the safest surface for exterior paving, stairs, and ramps. The rough-surface granite used throughout this campus sparkles in the sunshine while providing a safe walking surface for pedestrians in the courtyards and exterior passageways.
Precise fabrication using computer-aided design and computer numeric control (CNC) machines was essential for the fabrication of the fountain’s base and bowl. Tight seams and exact placement of each stone controls and directs water in this central water feature. “The manufacturer was able to take our design drawings and implement them with precision. The pieces they fabricated were really well executed. I think the diocese is very happy with the way the project turned out,” Stern says. “It’s resulted in a whole new public space for the campus. We were able to open up an area to be enjoyed by the Catholic community and the people of Wheeling.” The design complements the historic structures on the campus and adds value in the creative value of designing with contemporary stone fabrications and finishes
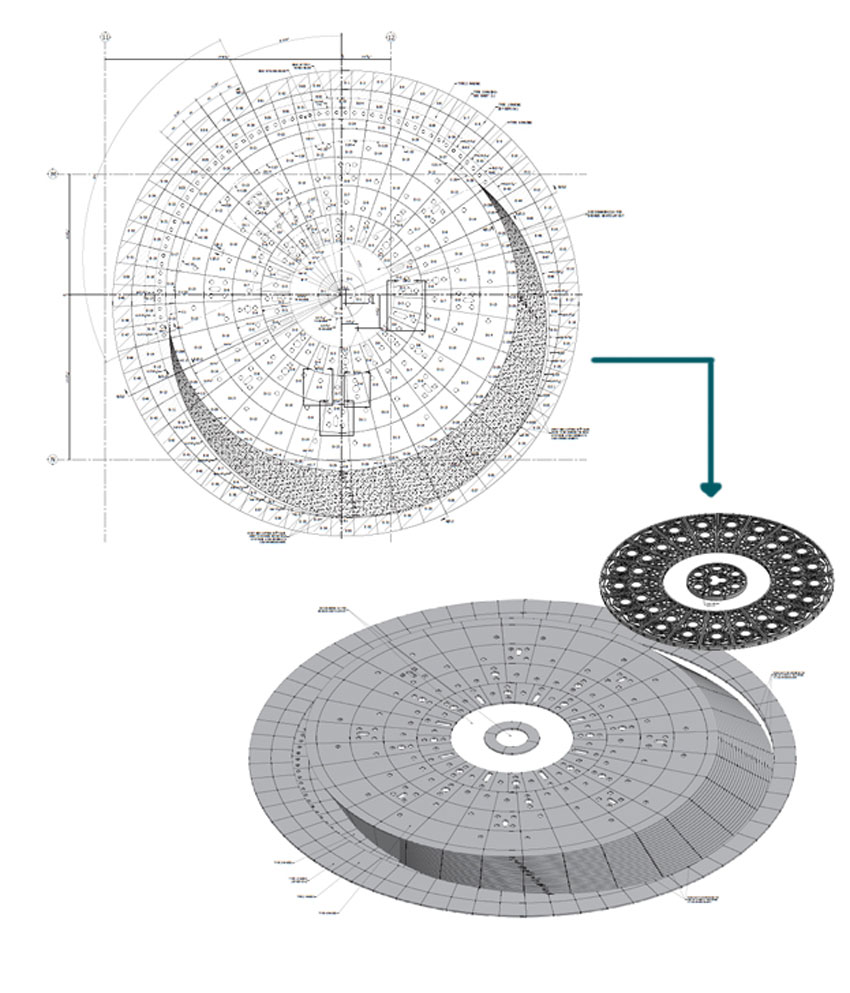
Image courtesy of Coldspring
According to the design team, choosing a manufacturer with high-performance digital fabrication allowed the design team to produce shapes that would have been nearly impossible years ago for this spectacular fountain in Salt Lake City.
Increased Creativity with CNC Fabrication
City Creek Center, Salt Lake City
Modern technology has made its mark on stone design and fabrication. Today, design teams that take advantage of technology are experiencing increased freedom in design and control of the design concept from development through fabrication. What’s more, improvements in quality control and greater accuracy of the stone’s shaping and final fit and finish are possible.
These high-tech fabrication techniques, which include 3-D modeling, sandblasting, and CNC capabilities, are changing stone fabrication. But while the technology for it is advanced, it’s not cost prohibitive. The process reduces fabrication time, which often makes custom designs more cost efficient for clients.
Architects may feel they have a limited palette of design options when using natural stone. In fact, digital craftsmanship has transformed the natural stone industry. Ross Nadeau, principal, SWA Group, sums up the changes in this industry reflecting on their project in Salt Lake City. “The beauty of technology is that it allows the production of shapes and designs in stones, such as the ones for City Creek Center, that would have been nearly impossible 50 years ago.”
City Creek Center, Salt Lake City’s newest mixed-use development, features no humble task—a replica of the area’s historic City Creek running through it, complete with 300 live trout, more than 600 trees, and hundreds of native plants. In addition, the 23-acre site features numerous fountain experiences constructed of natural stone to enhance the locale, which highlights Utah’s native landscape. There were many man-made materials available and considered for this site, but in the end, the authenticity of the creek was what mattered most to the design team.
For the fountains, the client desired the inclusion of fire and water programmed to music for entertaining City Creek Center patrons. As such, three fountains titled Flutter, Transcend, and Engage were created. Flutter captures attention with dancing fire on sheets of water, spilling out in the shapes of bells in a union of pyrotechnics and nature. Transcend entertains with musically choreographed displays using the elements of fire and water and spewing streams of water upward in playful patterns. Engage invites children to interact with its animations.
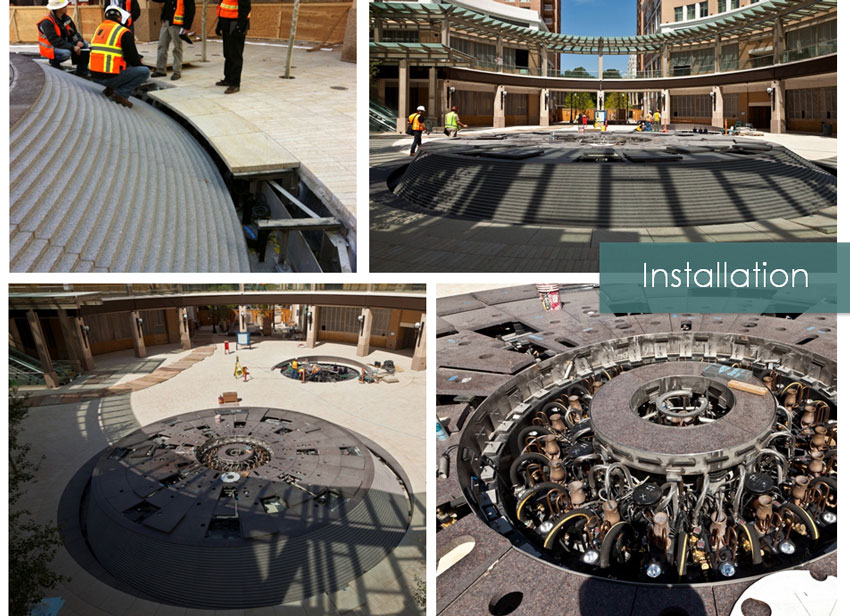
Photos courtesy of Coldspring
The design team knew that the fabricator for the fountains at City Creek Center had the technical capabilities, precision with modeling software, and variety of fabrication techniques that would be required to produce the stone fountain’s complex geometries with exact precision.
The design team selected a natural stone fabricator with the modeling software, building information modeling (BIM), and CNC fabrication technology that would be required to produce the stone fountain’s complex geometries with precision. The fountains required extremely tight measurements and exacting precision during fabrication and installation of the stone.
CNC technology enabled the disc to be fabricated with the precision required. In the field, the stone installer painstakingly installed the fountain disc to be level at every point within the thickness of a single piece of paper. This allows for the perfect flow of water to cascade over the entire perimeter evenly and beautifully. The fountain was installed in 2012, and after almost five years, there have been no issues with maintenance or damage on a surface that manipulates both fire and water, demonstrating natural stone’s durability and strength.
Hundreds of critically placed nozzle holes were needed for accurate production of the fountain performances. The stone fabricator meticulously fabricated a total of 176 perfectly positioned holes for water jets and light fixtures and 49 holes for gas-fueled fire nozzles for the dancing fire and water performance for Transcend. The precise stone fabrication eliminated the need for handwork on-site. A LEED Gold-certified project, City Creek Center has played a critical role in Salt Lake City’s sustainable design project to revitalize its downtown.
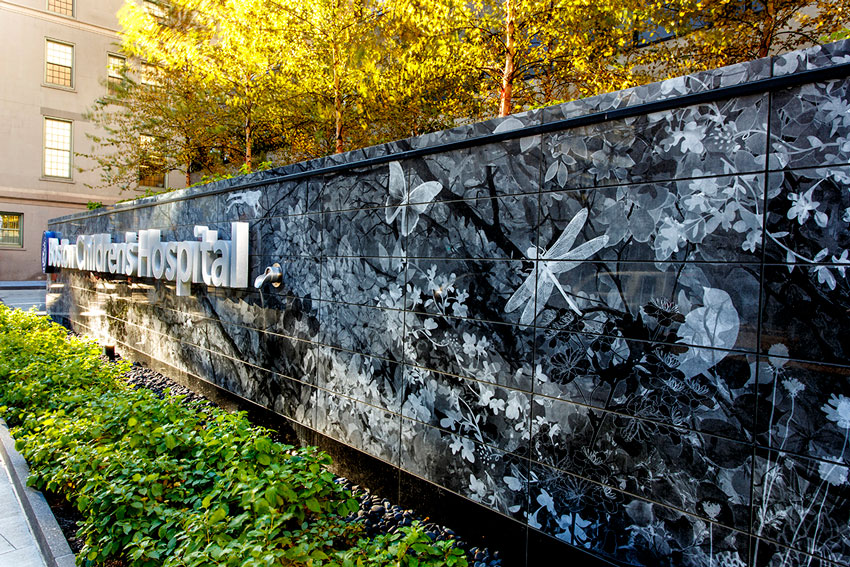
Photo: © Amesse Photography
The flight of dragonflies, butterflies, and birds that highlight the entry wall for the Boston Children’s Hospital is sandblasted into granite through the application of new stone digital fabrication technology.
Intricate Digital Stone Art Entry Wall
Boston Children’s Hospital
When a project’s design calls for images to be etched into stone, high-tech sandblasting capabilities bring the artist’s vision to life. Such was the case with the granite entrance to Boston Children’s Hospital, where an intricate dot matrix stenciling and sandblast process transferred the artist’s images to polished gray-black stone When guests and visitors approach the entrance of the Boston Children’s Hospital, they are greeted by a hide-and-seek style natural stone wall. The stone provides a backdrop for the intricate design of animals and foliage, which the project’s architect and designer calls “Playful Nature in the City.”
The design team knew that the stone chosen for the 1,200-square-foot structure would have to provide needed contrast and act as a suitable canvas for the project’s engraved art. Black granite was a natural choice and different finishes on this material allows light to dramatically change its appearance without using another stone. The stone selection was an integral part of the design process, as the architect wanted to integrate natural, durable materials into the design of an entry wall exposed to the harsh Boston climate.
The team challenged the fabricator with the task of creating a permanent structural wall surface that was developed from a digitally designed and complicated outdoor sculpture. An intricate dot matrix stenciling and sandblasting process was used to get the graphics onto the face of the polished stone. The light portions of the image are recessed slightly by sandblasting and a white color enhancement applied to the stone to give the images dimension.
The art files were provided to the stone supplier and fabricator in a vector format, which allowed them to be converted to a mask that was then applied to the stone and sandblasted. A great deal of coordination was required to ensure that the artwork looked exactly as the architect intended. Once the artwork was perfected, the rest was up to the craftsman in the fabricator’s facility. With more than 200 pieces of granite and unique images on each piece, the craftsman had to lay out and line up each adjacent piece to ensure that the full image flowed across the entire block.
The sheer size of the 102-foot-long by 7-feet-high wall complicated the scope of this project. The stencil was applied in sections both horizontally and vertically. The installation included 231 facing pieces in the main wall, 14 facing pieces on the return wall, and 35 coping/cap stones for a total equaling 280 pattern pieces. The stone fabricator was required to assure each section was scaled correctly and that the steps to create the halftone pattern were identical on each section to make sure that the final graphics matched. Long-term maintenance of the black granite is minimal, and the art is expected to stand the test of time, delighting visitors for many years to come.
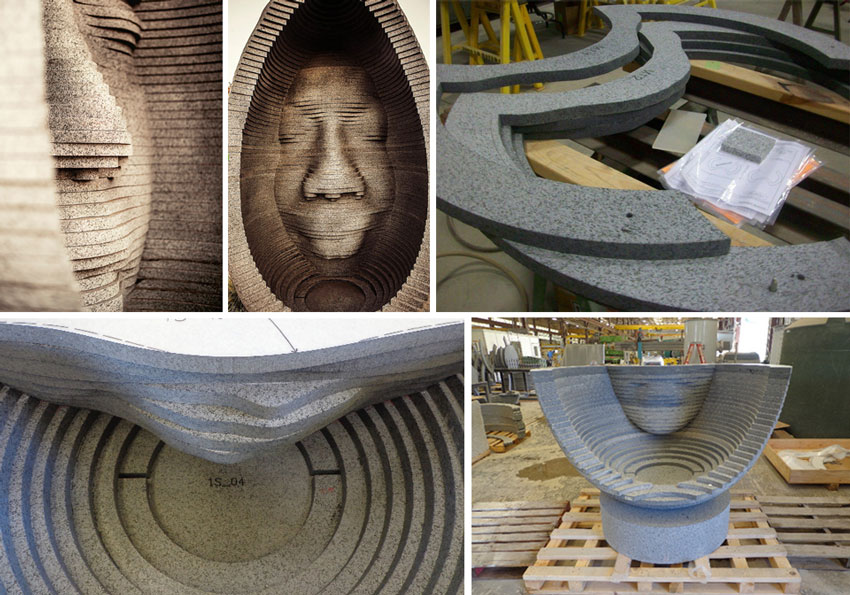
Photos courtesy of Makena Hunt and Coldspring
The faces of individuals from the Los Angeles community are a feature of this modern roundabout. The artist provided detailed drawings that required pieces to be assembled precisely to form the egg sculptures.
Three-Dimensional Modeling
Riverside Roundabout, Los Angeles
This project is an example of how an artist used new three-dimensional fabrication modeling in a major sculptural installation. The Riverside Roundabout is the first modern roundabout in Los Angeles and will help control negative environmental impacts on the community, with extensive plantings and water storage.
The centerpiece of the roundabout, designed by Greenmeme Art & Design Studio, includes the installation of nine egg-shaped stone sculptures constructed of black granite with a sawn finish from a California quarry. Measuring 8 to 12 feet tall, the sculptures feature the faces of individuals from the community, randomly chosen throughout two years.
The design team took advantage of digital technology to control the fabrication of these sculptures from development through installation. It carefully coordinated the entire process from the artist’s three-dimensional drawings to its final installation. The adaptation of CNC machinery to natural stone fabrication machinery provides both quality control and greater accuracy of the stone’s shaping and final fit and finish.
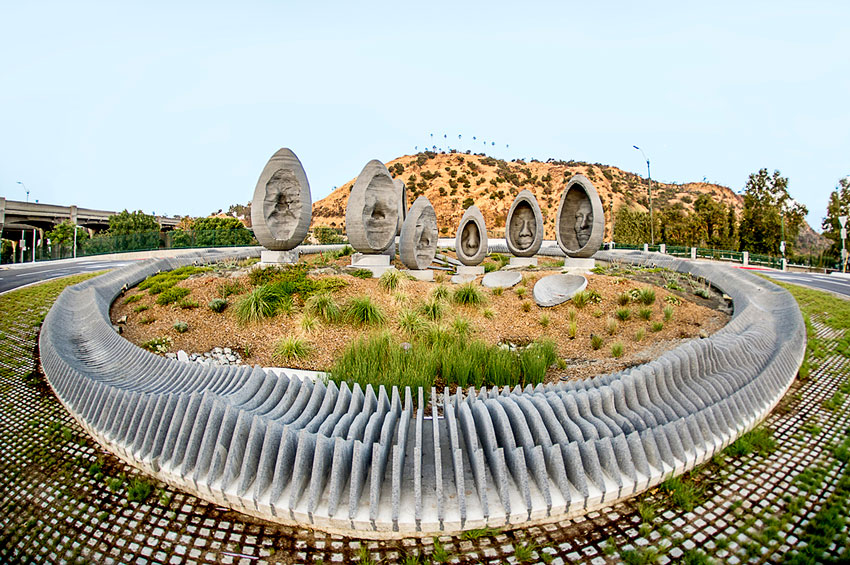
Photo courtesy of Makena Hunt
Employing three-dimensional modeling and CNC fabrication, the artist and the granite supplier created a monument to sustainability and the community.
A significant amount of coordination between the local public artist Greenmeme and the granite supplier and fabricator ensured the artistic vision came to life. The granite supplier and fabricator used the designer’s electronic files to create the cutting information needed to fabricate the sculptural pieces. Greenmeme provided detailed drawings that required pieces to be numbered and assembled precisely to form the egg sculptures. Each piece was laid out on a slab per the design. The granite supplier selected and cut the slabs with CNC cutting equipment to provide full utilization of the slab, reducing any waste material from the quarried stone. Sculpture pieces were then epoxied together per the design drawings.
The roundabout serves as a stormwater bioretention landscape, with the capacity to capture and treat a 10-year rainfall event (500,000 gallons) off an adjacent bridge and roads. The system also includes a 25,000-gallon cistern supplying a water feature as well as a solar tracking photovoltaic system powering irrigation, lighting, and the artwork. A 100-percent sustainable project, all parts of the granite slabs were used to create the eggs, with the remaining parts of the slab creating a stone border around the roundabout.
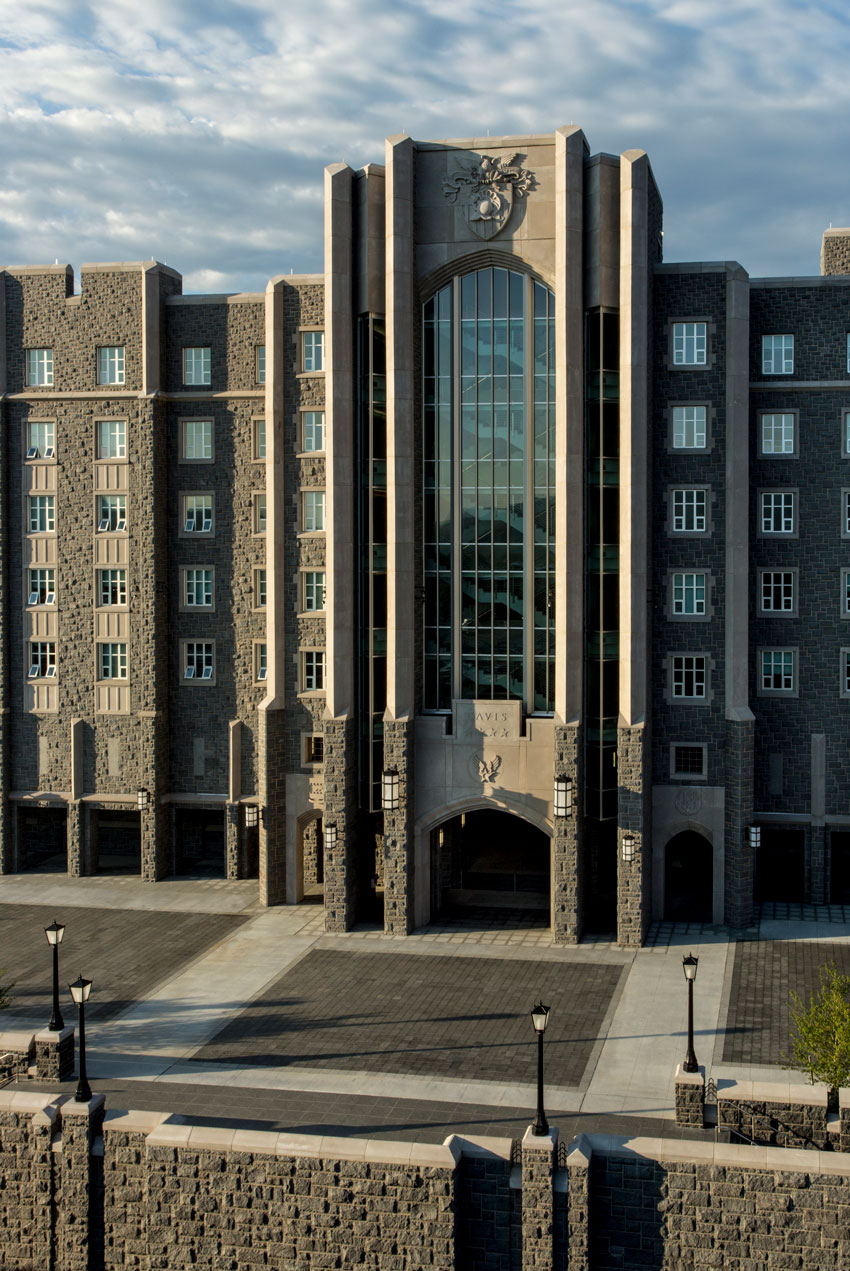
Photo: © Amesse Photography
Nearly 200,000 square feet of beautiful, custom-cut, and hand-crafted pieces were used for the exterior, site wall, stair treads, coping, sills, and paving of West Point’s newest cadet barracks.
Construction, Waste Reduction, and Scheduling
West Point, New York
The use of natural stone for the West Point Military Academy is an example of how a project team maximized all of the benefits of natural stone. They met the challenge of tight site conditions on this historic campus as well as managed a shifting schedule. Careful coordination and constant communication with the stone supplier and fabricator was a key to the success of this project.
Since 1802, the U.S. Military Academy at West Point in upstate New York has played a significant role in the instruction of some of the nation’s finest military leaders. With the large numbers of men and women entering West Point, the addition of a new barracks was crucial. The new cadet barracks are named after Benjamin Davis Jr., a former Tuskegee Airman named the first African-American general officer in the U.S. Air Force.
When constructing the new barracks, it was important to West Point to match the existing feel and color of the 200-year-old campus’s gothic revival architecture as well as use a product that will last another 200 years, making granite a natural choice. The architect visited the stone supplier and fabricator’s facilities and local quarry to help envision the project.
Many design teams choose to visit the quarry that may supply the natural stone for their project. A visit to a quarry and to a fabrication facility allows a design team to review the natural stone deposits. Natural stone may have a wide range of color variations and material characteristics. Quarry personnel can provide critical insight on a quarry’s history, equipment operations, and capacity. Touring a fabrication plant allows the design team to evaluate the facility and its capability to collaborate with digital technology. The fabricator can provide information on three-dimensional and physical modeling, and explain its approach to sustainable waste management and installation sequencing.
Nearly 200,000 square feet of beautiful, custom-cut, and hand-crafted granite pieces were used for the exterior, site wall, stair treads, coping, sills, and paving of West Point’s newest cadet barracks. Two types of black granite were selected, and the design team modulated finishes and placement to create a rich palette of materials throughout the site. The stone facade and interiors complement the existing buildings on the 200-year-old campus, and the new buildings are designed to last for the next 200 years.
With a tight deadline, it was essential that the granite supplier and fabricator had complete control over shipping the 200,000 4-inch-thick, split-face pieces of granite from central Minnesota to upstate New York. It’s not typical for split-face applications to be shipped in their finished state to a job site, but the precise installation process utilized on this project made it possible. Each piece was handcrafted and numbered to fit into a specific spot, and once on-site, all of the pieces were easily assembled. This cut down time and on-site work significantly. This process also supported the tight construction conditions, as this project was essentially being built into a hill without room for extra construction material on-site. The barracks were dedicated on May 1, 2017 and began occupancy fall of 2017. The stone supplier and fabricator was able to provide the colors, quality, coordination, and schedule needed for the project.
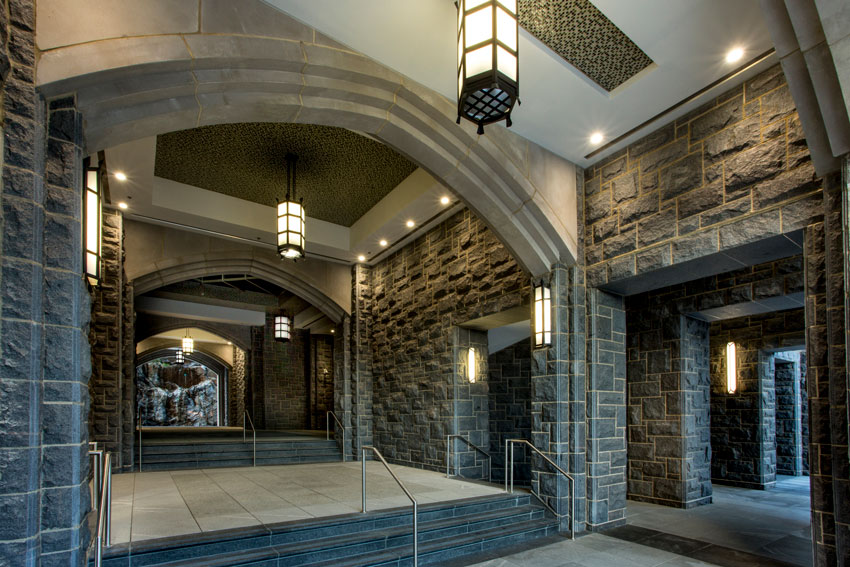
Photo: © Amesse Photography
Two types of granite were fabricated in multiple finishes to provide variety of textures in each application as well as unify the architectural composition.
The Greenest Museum on the Mall
The National Museum of African American Culture and History, Washington D.C.
Materials selected for museums require permanence and durability. When designing a new museum on the National Mall in Washington, D.C., all of the design team focused on selecting materials that would require very little maintenance, last for centuries, and fit within the context of one of American’s largest cultural places.
After nearly 10 years of planning and fundraising efforts, the Smithsonian Institution’s new museum in Washington, D.C., features granite hardscape elements that relied on 3-D modeling technology and CNC fabrication. The National Museum of African American Culture and History, which opened in September of 2016, is the only museum dedicated to documenting the history, life, and culture of African Americans. In 2017, the museum celebrates its first anniversary. The landscaped space has become a community gathering area surrounded by gourmet food trucks and is now considered to be one of D.C.’s hottest places to go for lunch.
Located on a 5-acre site on the National Mall between the National Museum of American History and the Washington Monument, the museum, designed by Freelon Group, Adjaye Associates and Davis Brody Bond, encompasses 322,600 square feet with five levels above grade and four below grade. Appropriately, the museum’s design is distinctive among other structures on the National Mall. Its facade consists of 3,600 customized, cast-aluminum panels known as the Corona. These bronze-colored panels call to mind the craftsmanship of enslaved workers in the pre-Civil War cities of Charleston and New Orleans and create a distinctive impression for the museum representing traditional African architecture.
Just as the museum’s architecture makes a unique design statement, its landscape design also distinguishes it among nearby museums and monuments. The landscape architects, GGN, incorporated the site design of the museum into the larger configuration of the National Mall, integrating the site within the museum’s larger story. According to the landscape architecture firm, “The site is designed to encourage visitors to extend the museum experience outside and to linger and reflect on the important narratives being told within.”
Granite played an important role in meeting design goals, as approximately 37,000 square feet of black granite in various finishes were used for numerous hardscape elements, such as paving, wall facing, wall coping, steps, curbs, benches, and bollards. A majority of the stones for the project were modeled in 3-D software, which allowed the fabricator to coordinate with the landscape architect and ensure the design expectations were met. Due to the project’s complex nature, an extensive amount of coordination between the fabricator’s drafting team and the architect ensured the 3-D models were accurate prior to fabrication. Once the design team approved the fabricator’s drawings and models, the fabricator converted the models into a file for use on a 5-axis CNC machine.
CNC technology was critical for creating the intricately crafted cubic wall of black granite encompassing the site’s perimeter. Most of the walls feature a highly polished finish. However, a combination of polish coping and a less reflective facing were selected for the museum’s north wall, which serves as the museum’s main entrance. The north wall spans approximately 340 feet across the front of the museum, running parallel to Constitution Avenue. The less-reflective finish was selected due to concerns over too much reflection off the wall at the highly traveled entrance.
Fabrication of the granite pieces for the north wall proved particularly challenging because of the wall’s slight radius and continuous bullnose creating many unique pieces. The fabricator had to produce each of these stones at precisely the same thickness to ensure an exact alignment at installation. Most of the wall’s cap pieces were milled by the fabricator’s 5-axis CNC machine and then finished by hand to create the bullnose. With multiple workers applying a bullnose to hundreds of pieces, accomplishing the precision required for alignment required an exceptional level of coordination and craftsmanship.
In addition to the honed and polish finishes used for the site’s walls, various finishes were used for additional granite elements at the site. A honed finish with an applied additional process enhances the color of granite and removes microscopic crystals that may leave a hazy appearance. The curbing features a honed finish. Bench seats feature a polish finish. The paving—encompassing 25,000 square feet of granite—and stair treads feature a rough finish that provides an ideal slip-resistant surface.
Having a majority of this project modeled in a 3-D software allowed the fabricator to provide a virtual model of the final product. They were able to coordinate with the architect to assure design integrity and quality control prior to fabrication. According to a leader in sustainable design, author and architect Lance Hosey, FAIA, reports in The Huffington Post that the Smithsonian’s National Museum of African American Culture and History received the U.S. Green Building Council’s LEED Gold Standard, making it the greenest museum in Washington.3
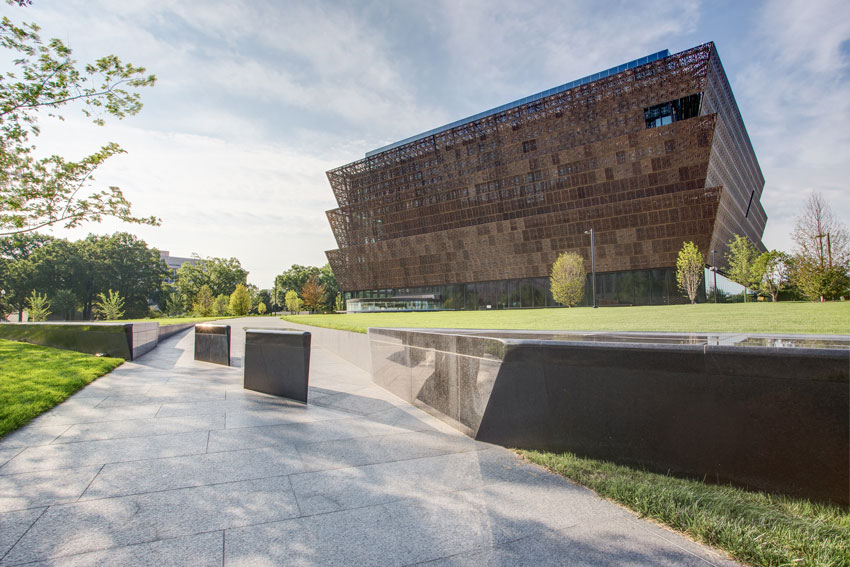
Photo courtesy of DC Real Estate Photo
Granite played an important role in meeting design goals, as approximately 37,000 square feet of black granite in various finishes were used for numerous hardscape elements, such as paving, wall facing, wall coping, steps, curbs, benches, and bollards.
NSC 373: The Story of Certified Natural Stone
Many of the design professionals in the examples above and many more across the United States are choosing natural stone as a material that contributes to their goals to protect the environment and deliver healthier buildings. While natural stone is inherently a naturally sustainable material, a new certification program, ANSI/NSC 373: Sustainable Production of Natural Dimensional Stone, establishes criteria to measure the extent to which natural stone is extracted and processed in an environmentally preferred way. Compliance with ANSI/NSC 373 requires third-party verification to the standard as well as the companion chain-of custody.
The goals of NSC 373: Sustainable Production of Natural Dimension Stone are to:
- Establish a set of well-defined environmental, ecological, social responsibility, and human health metrics for extraction and processing of natural stone.
- Educate key members of the design and building professions on the value and benefit to them, and connect to green building programs.
- Provide a method for improving baseline environmental performance for the stone industry.
- Be applicable domestically and internationally, from quarry through fabrication and installation.4
This consensus-driven standard encourages material selection transformations aligning with the way green building programs have shifted as well. This approach encourages design professionals to look beyond single attributes of a material, such as the use of recycled material, and instead look at a multi-attribute approach.
The chain of custody tracks the stones as the material moves from the quarry to processing and through the supply chain. For a product to be claimed as Genuine Stone certified, there must be an unbroken chain of certified organizations that conform to the COC standards covering every change in the legal ownership of product, from the certified quarry up to the point where the product is finished and delivered to a project site for installation. More information on this standard can be found in the continuing education article “Sustainable Stone From Cradle to Gate.”5
In 2016 The Natural Stone Council (NCS) announced that the ANSI/NSC 373 certification is recognized by the U.S. Green Building Council’s LEED v4 building certification program and the International Living Future Initiative’s Living Building Challenge (LBC) version 3.1.
Natural stone provides numerous environmental benefits. This material is durable, easy to maintain, and does not off-gas. Many architects and landscape architects are exploring the benefits of designing with natural stone as a better choice for a healthy environment in buildings and landscapes.
Conclusion
The ultimate goal of any project is beauty. Whether designing buildings, sculptures or public spaces, materials matter. Today’s ancient and enduring natural stone products are more diverse and sustainable than ever before due to 21st century technology. As in the past, today’s architects, artists, and landscape architects are choosing natural stone as a material of choice for some of their most complex and creative designs.End Notes
1Panek, Richard. “A World’s Geology on a City’s Face.” The New York Times. 4 Oct. 1991. Web. 19 Oct. 2017. www.nytimes.com/1991/10/04/arts/a-worlds-geology-on-a-city-s-face.html?pagewanted=all.
2O’Sullivan, Feargus. “Where to Find Fossils, Lava, and Meteorites in London’s Buildings.” City Lab. 11 July 2016. Web. 11 Oct. 2017. www.citylab.com/life/2016/07/where-to-find-fossils-lava-and-meteorites-in-londonsbuildings/490766/.
3Hosey, Lance. “DC’s Museum of African American History Is the City’s Greenest.” The Huffington Post. 30 Dec. 2016. Updated 19 July 2017. Web. 14 Oct. 2017. www.huffingtonpost.com/entry/the-greenest-museum-in-washington_us_5866e66de4b068764965c1c9.
4Natural Stone Certification Program Fact Sheet. Web. 14 Oct. 2017. www.naturalstonecouncil.org/manage_files/d7b77b4eb63-D7d94b4b88ac50ae926ad.pdf.
5Allen Novak, Celeste. “Sustainable Stone From Cradle to Gate.” Continuing Education Center. Architectural Record. BNP Media. Web. 19 Oct. 2017. continuingeducation.bnpmedia.com/courses/miabsi-the-natural-stoneinstitute/sustainable-stone-from-cradle-to-gate.
Celeste Allen Novak, FAIA, LEED AP BD+C, is an architect, writer and planning consultant in Michigan. www.celesteallennovakarchitect.com
From all types of natural stone and bronze to industrial and diamond tooling products, Coldspring® has been serving the architectural, memorial, residential, and industrial markets since 1898. With headquarters and primary operations in Cold Spring, Minnesota, including a bronze foundry, the company has fabrication facilities and quarries across the country. www.coldspringusa.com