Concrete-Filled Hollow Structural Sections (HSS), an Unbeatable Combination
Filling HSS members with concrete offers the most effective way to meet fire-protection requirements while achieving high compression strength, a smaller footprint, and the desirable aesthetics of exposed steel
Continuing Education
Use the following learning objectives to focus your study while reading this month’s Continuing Education article.
Learning Objectives - After reading this article, you will be able to:
- Explain the structural, construction, and aesthetic benefits of exposed steel hollow structural sections.
- Identify the fire-protection and structural benefits of concrete-filled HSS as compared to other exterior fire-protection methods.
- List the variables that will determine the calculated level of fire resistance delivered by the concrete-filled HSS members.
- Discuss construction efficiencies and best practices for erecting the steel and piping concrete into HSS tubes.
- Define the benefits of a performance-based design approach over prescriptive design when specifying concrete-filled HSS.
Exposed columns of steel hollow structural sections (HSS) are a striking and cost-effective design option, combining the aesthetics of exposed steel with the structural support and reduced footprint of structural steel.
As exposed elements, HSS eliminate the need to furnish and install column covers, minimizing the column’s profile. The tubular form in particular presents a clean, exposed steel surface that exudes a modern appearance.
Exposed steel offers an appearance that is often missing in other types of construction, explains Dr. Venkatesh Kodur, director of the Center on Structural Fire Engineering and Diagnostics at Michigan State University in East Lansing, Michigan. It provides not only the illusion of larger, more uninterrupted space by its slim profile but also a visual cue that the structure is both sound and in good condition.
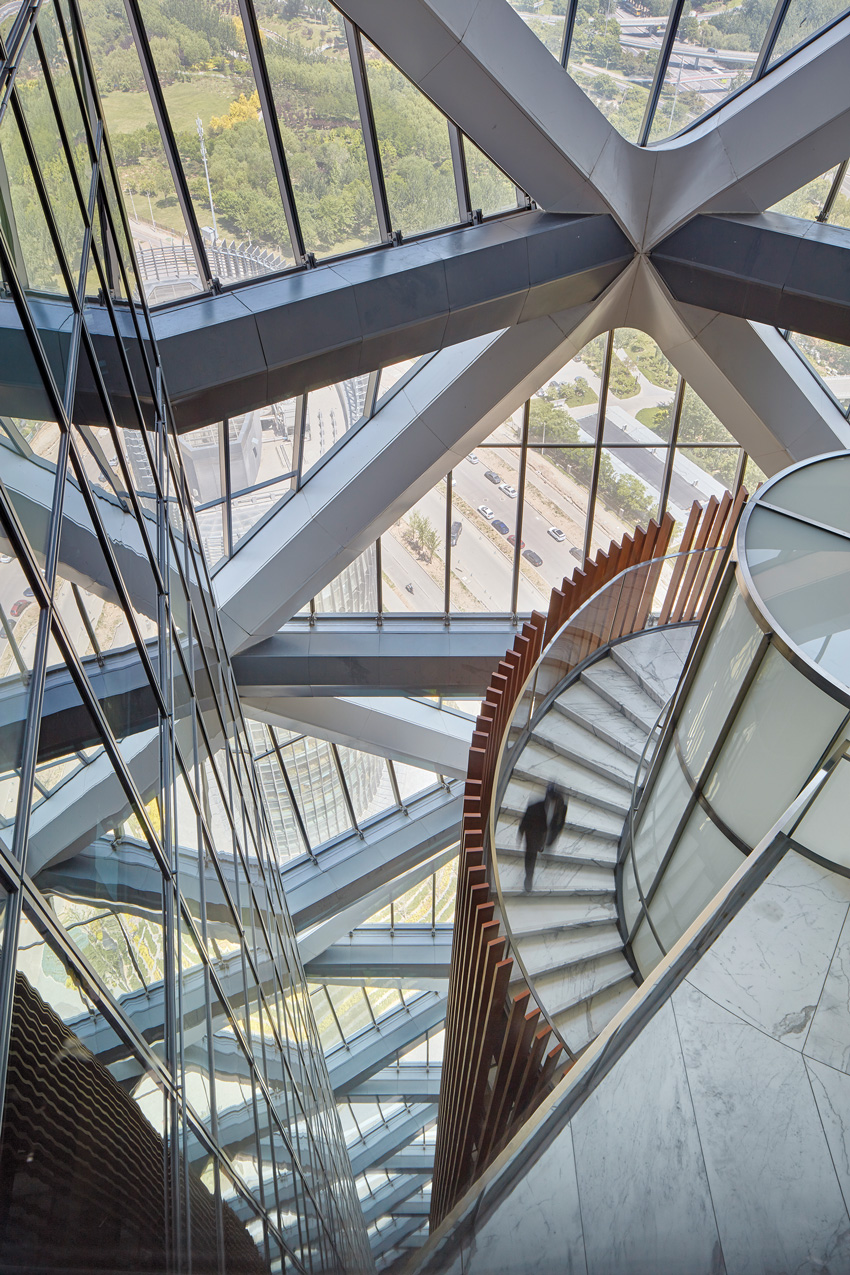
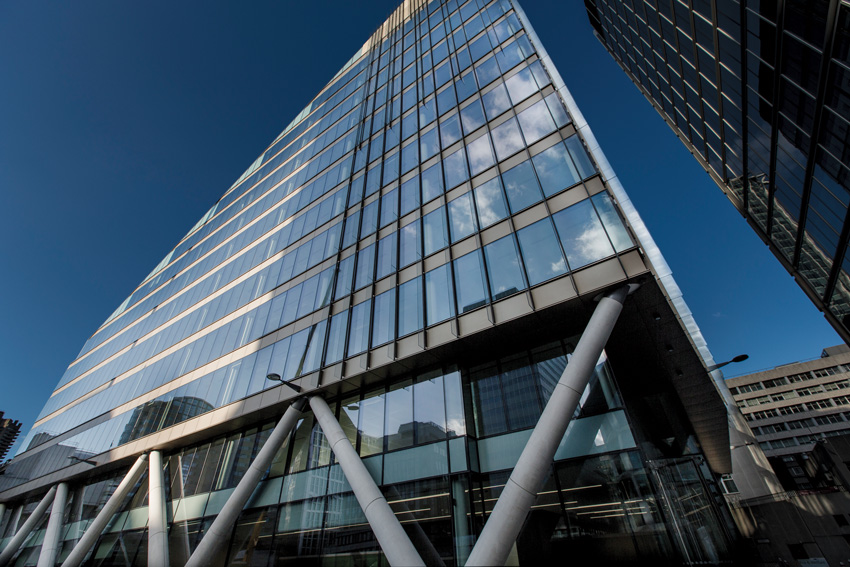
Photos courtesy of Tata Steel and SOM/Bruce Damonte
As pictured here at London’s Moorgate Exchange (bottom) and Beijing’s Boy International Plaza (top) concrete-filled exposed steel hollow structural sections present a beautiful aesthetic, a smaller structural footprint, and cost-effective fire protection.
Available in round, square, or rectangular tubular forms, HSS deliver a clean, simple aesthetic. Each shape has rounded edges that effectively soften its appearance and minimize shadows. “When used as columns, the way light bends around the round HSS shapes in particular can make them appear slimmer,” says Andrea Reynolds, S.E., P.E., LEED AP, director of structural engineering, SmithGroupJJR, Detroit. Structural engineers are drawn to the high capacity-to-weight ratio and excellent torque and resistance of HSS, while building owners, architects, and engineers alike appreciate their clean, visual appeal.
“Exposed steel provides a rugged industrial look, providing a sense of authenticity and direct feel for the structure of a building that is appealing to many clients,” says Ali Ashrafi, Ph.D., P.E., LEED AP, associate principal, Thornton Tomasetti, New York.
As a torsionally stable member, HSS eliminate the need for other structural bracing members, thereby reducing clutter, simplifying the structure, and producing a more elegant solution, adds Preetam Biswas, P.E., associate director, senior structural engineer, SOM, New York. They also eliminate the need for formwork, which typically accounts for one-third of concrete construction costs.
“Structural hollow sections are particularly suitable for exposed steelwork, as they do not have reentrant corners, are easier to paint, have a smaller perimeter, and give a smoother appearance,” explains Yong Wang BA, Ph.D., CEng, FIStructE, professor of structural and fire engineering at the School of Mechanical, Aerospace and Civil Engineering, University of Manchester, United Kingdom.
He adds that circle-shaped sections are the most efficient shape in terms of compression. “This means for an equal steel weight, the column will be smaller, with a reduced footprint, as compared to other shapes, resulting in increased leasable area for building owners,” he says.
This is particularly applicable in high-rise construction, which has high compressive loads.
HSS and Fire Protection
In fire-rated applications, external fire-protection methods for HSS are not only expensive but also cover up the exposed steel, negating its aesthetic appeal.
Fortunately, concrete-filled HSS offer a solution. In addition to meeting a building’s fire-protection requirements, this method retains the beauty of HSS as an architectural element and enhances each structural member’s load-carrying capacity.
“These two materials—steel and concrete—complement each other in that the steel section confines the concrete laterally, allowing it to develop its optimum compressive strength, while the concrete, in turn, enhances resistance to elastic local buckling of the steel wall,” Kodur says.
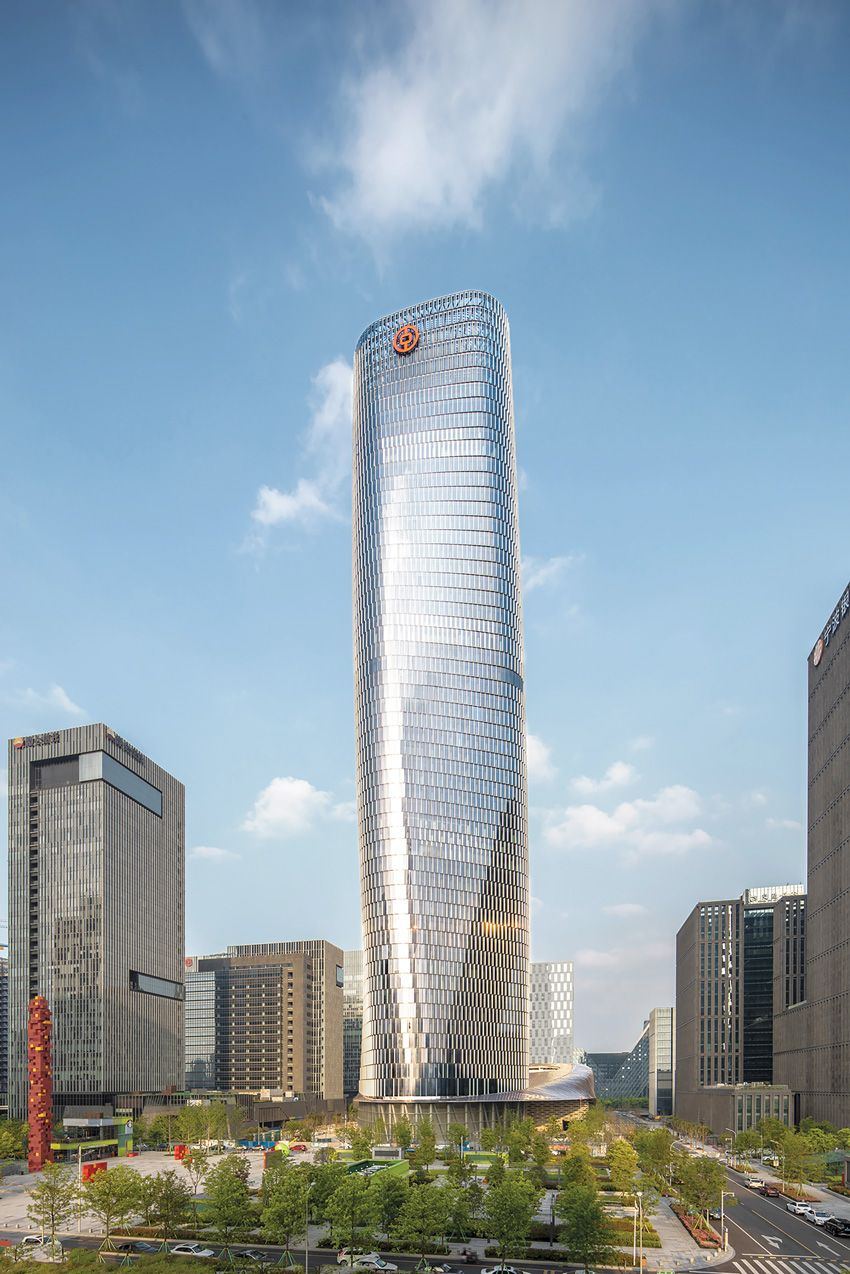
Photo courtesy of SOM/Archexist
SOM specified concrete-filled hollow steel sections for the Ningbo Bank of China Headquarters in Ningbo, Zhejiang, China, described as a site-specific tower with the exterior’s triangular shape and rounded corners gradually rotating around a vertical axis facing the city, the mountains, and the sea.
Beyond their fire-protection qualities, concrete-filled HSS also “optimize the strength and stiffness of the member by placing the steel at the outer perimeter where it is most effective in resisting bending moment and has the greatest impact on the moment of inertia of the member,” explains Reynolds. “The concrete core is ideal for withstanding compressive column forces and prevents local buckling of the steel tube, while the steel tube confines the concrete that can impact the compressive strength and ductility.”
Similarly, Biswas points out that, structurally, concrete-filled HSS columns provide the optimal use of materials and smaller member cross sections, as opposed to regular concrete. Yet another benefit is the fact that the concrete fill, protected by the steel, is maintenance free and not subject to any issues of deterioration or detachment that would affect its performance. “This is advantageous because it prevents the spalling of concrete so the entire volume of concrete participates in resisting forces,” he says. “Eliminating the spalling of the unconfined outer layer of concrete results in a more optimal use of concrete material for both strength and stiffness.”
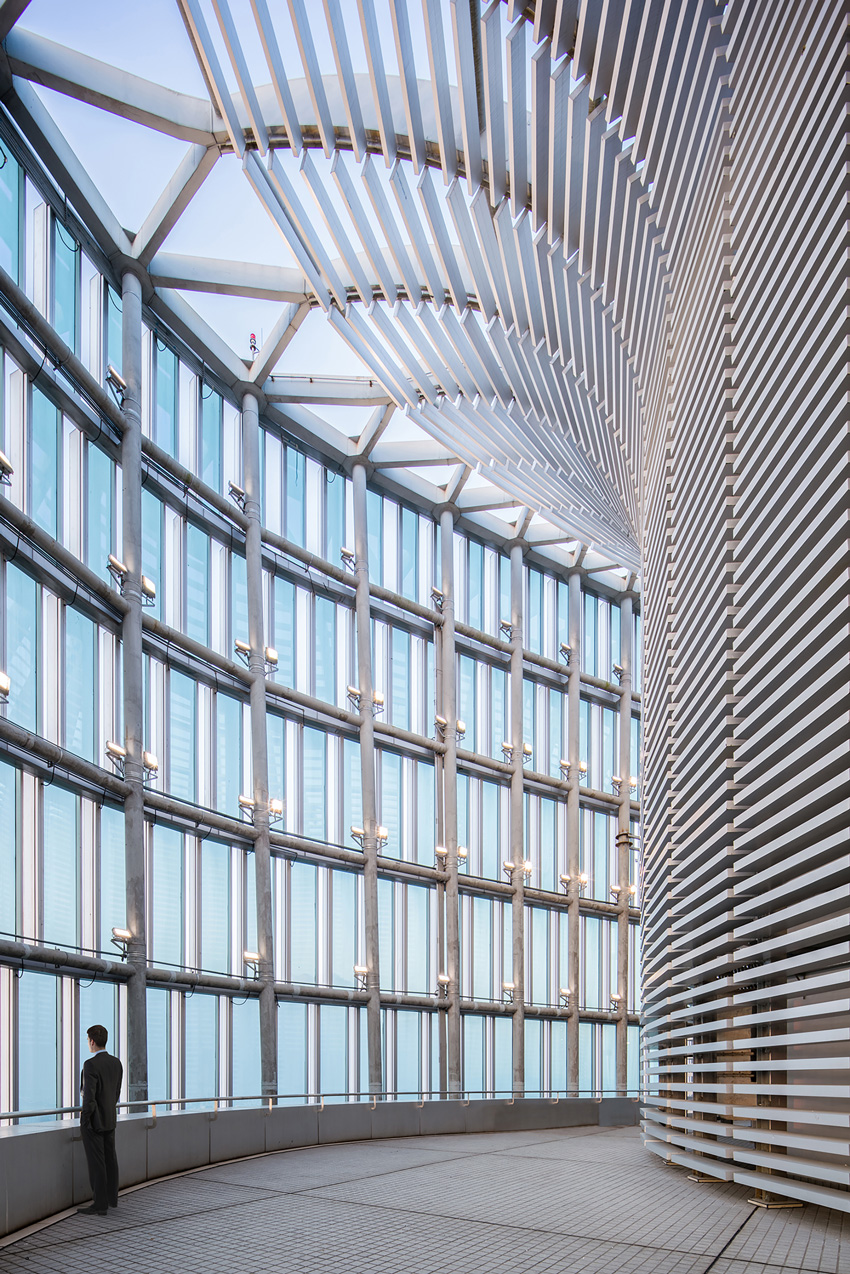
Photo courtesy of SOM/Archexist
At the Ningbo Bank of China Headquarters, 400-millimeter-diameter to 850-millimeter-diameter concrete-filled hollow structural section columns with wall thickness ranging from 15 millimeter to 25 millimeter deliver structural support and fire protection.
“While HSS are already efficient shapes for columns, filling them with concrete increases this efficiency by having the concrete share in the load-carrying duties,” Olson says. “Filling an HSS with concrete can also increase a connection capacity by stiffening the HSS wall and thereby negating a failure mode that sometimes may control the connection capacity.”
In terms of other HSS benefits over conventional steel columns, Ashrafi points out that the strength of the steel HSS columns is determined not only by their section areas but also by how far most of the section material is from the center of the section, which is called the radius of gyration.
“By placing all of the material on the perimeter of the section, an HSS shape increases this distance, hence reducing the propensity of the column to buckle and achieving higher efficiency in comparison to I-shape steel columns,” he explains.
In addition, concrete-filled HSS sections have less exposed surface, as compared to regular I-shape columns, thereby reducing the cost of intumescent paint and other fireproofing.
Because of their closed shape, HSS columns are stronger than a wide-flange with the same weight, explains Kim Olson, P.E., technical consultant to the Steel Tube Institute with FORSE Consulting, Denver. Although the price per pound of HSS generally exceeds wide-flange I-beams, less steel is required and the increased capacity of an HSS is so much greater that these columns are ultimately more cost effective.
External Fire Protection
Before delving into the design and construction aspects of concrete-filled HSS, it is important to understand how alternative fire-resistance methods applied to the exterior compare to this method.
In a recent Steel Tube Institute webinar titled “Fire Protection of HSS,” Brady Golinski, P.E., technical consultant for the Steel Tube Institute and a structural engineer with FORSE Consulting, Denver, notes that an unprotected HSS will fail at approximately 850 degrees Fahrenheit to 1,000 degrees Fahrenheit within 20 to 30 minutes.
If the HSS is loaded to less than 50 percent of its capacity, the failure temperature rises to more than 1,200 degrees Fahrenheit. However, this will not be sufficient to meet fire-protection code requirements in occupancies that require it.
One external fire-protection strategy is gypsum insulating boards. Containing a high percentage of water in its chemical composition, the gypsum releases steam as its temperature increases in the presence of a fire, thereby creating a barrier between the building structure and the fire. However, the downsides are the cost of gypsum and the fact that even if only members are covered with the material, and not the entire wall, the exposed tubes will still disappear under an unaesthetic layer of fire protection.
Another option, fibrous spray-applied fire-resistive material (SFRM), consists of melted rock or iron slag spun into a noncombustible mass of filaments. With reactive properties similar to gypsum, steam is released and creates a barrier as the material heats in the presence of fire. With cementitious SFRM, which usually contains gypsum and expansive aggregates, the material expands and insulates the steel in extreme heat conditions.
Minimum column sizes and fire ratings for both gypsum board and SFRM have been calculated for different assemblies, tested, and published in table form in the American Institute of Steel Construction (AISC) Design Guide 19 Table VI.3 for gypsum board column designs.
“We don’t have to go through and do an equation every time. We can simply pick an assembly from the table,” Golinski says.
Intumescent coating, yet another option, is a mixture of binders, resins, and ceramics that also expands in the presence of fire. The expanded foam acts as heat sink and insulator and can deliver fire resistance for up to three hours. While this type of coating is applied like paint and therefore maintains the appearance of exposed steel, it can be costly.
Concrete-Filled HSS in a Fire
As a cost-effective fire-protection alternative, concrete-filled HSS enable the members to remain exposed and are typically 5 percent to 10 percent less expensive than external fire-protection measures. In addition, concrete-filled HSS eliminate the need for a separate fireproofing contractor, which can further reduce construction time and cost.
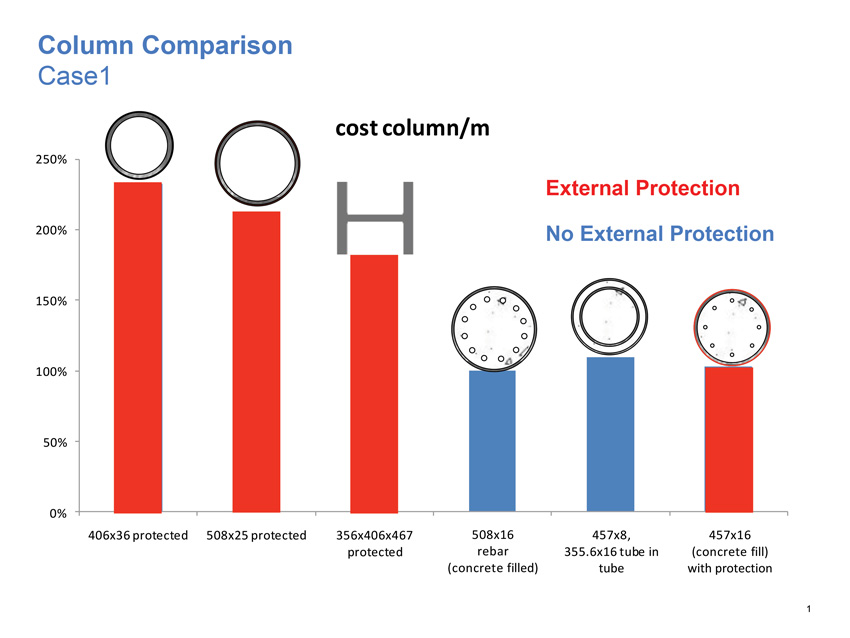
Image courtesy of Tata Steel
Building teams can benefit from significant fire-protection cost savings by choosing concrete-filled steel tubes over externally applied intumescent coatings.
In a white paper titled “Design Guide for Concrete Filled Hot Finished Structural Hollow Section Columns,” Wang explains that under ambient conditions, the steel and concrete move together, so the longitudinal steel and concrete strains are equal. “Accordingly, the stress in each material is proportional to the ratio of the elastic moduli of the two materials,” he writes.
In the presence of heat, the steel expands more rapidly than the concrete and begins resisting a greater proportion of the applied load. Simultaneously, the steel yield stress and modulus of elasticity begin to reduce to the point where the steel begins shedding load into the concrete.
“As the steel heats up and loses its strength, the load can be transferred to the concrete core,” explains Golinski. “The concrete mass absorbs heat much better than the steel and retains its strength longer.”
“Heat from the steel shell will be transferred to the outer layers of the concrete core, causing their temperature to rise,” writes Wang. “However, concrete is not a good conductor of heat, and the rate of heat flow through the core will be slow.”
At the point when the concrete starts to degrade, moisture from the concrete is converted into steam, further slowing the burning process.
An American Institute of Steel Construction’s Engineering Journal article, “Design of Concrete-Filled Hollow Structural Steel Columns for Fire Endurance,” authored by Kodur when he ran the fire risk management program at the Institute for Research in Construction, National Research Council of Canada, and David M. MacKinnon, M.A.Sc., P.E., codes and standards engineer, Canadian Steel Construction Council, describe a “temporary reprieve of sorts” that is created when the moisture turns to steam, thereby absorbing considerable quantities of heat.
However, that steam needs to be released into the atmosphere to prevent a potential bursting hazard. To allow the steam to escape, proper venting must be provided.
As a point of reference, the British Standards Institution, in Eurocode 4 – Design of composite steel and concrete structures – Part 1-2: General rules – Structural fire design, recommends that the sections contain one vent hole, with a minimum diameter of 20 millimeters, at the top and bottom of each story, and that the longitudinal spacing does not exceed 5 meters.
The standard also advises the vent holes to be within the ceiling zone, and that care should be taken to ensure that these vent holes are not cast within the slab.
Offering some additional pointers in a Steel Tube Institute newsletter article, “Practical Guidance for Concrete Filled HSS Columns,” Olson and Benjamin Kaan, P.E., associate, Thornton Tomasetti, cite AISC 360-10, Section I1.3(1), which states that the normal weight concrete compressive strength be between 3 ksi and 10 ksi, and that lightweight concrete compressive strength be between 3 ksi and 6 ksi. If bar reinforcement is used, then the yield strength of bar reinforcement must be less than 75 ksi, and the area of reinforcement within a concrete-filled HSS composite column must be at least 1 percent of the total composite cross section area, per the same AISC standard.
“If reinforcement inside the HSS column has been specified, the designer should carefully consider the constructability of the column assembly,” write Olson and Kaan.
“Is there adequate space in the cavity of the HSS for both a concrete tremie and the reinforcement? Have the type of connections to the column been selected such that they won’t interfere with the placement of the reinforcing?” they ask. (A tremie is a vertical pipe, through which concrete is piped by a gravity feed below water level.)
Furthermore, if the top of the column is a bearing condition—meaning that the load being transferred directly to the top of the column is a beam bearing on a column cap plate, for example—then it is important to determine if the steel section is capable of carrying all of the load.
“The designer must detail the top of column condition to ensure load is transferred to the column in a manner that is consistent with the design assumptions,” Olson and Kaan explain. “Due to concrete shrinkage, a void can be expected to form between the top of concrete and underside of a column cap plate.”
To address this, the top 2 to 4 inches of the column can be filled with non-shrink grout, in which case fill and vent holes are required. As an alternative, an embedded anchorage can be designed at the underside of the cap plate, such as headed studs or anchor rods, similar to a base plate condition.
Boosting Fire Performance
A number of variables will ultimately determine the level of fire resistance, such as load-capacity ratio, the size and shape of cross section, and buckling length.
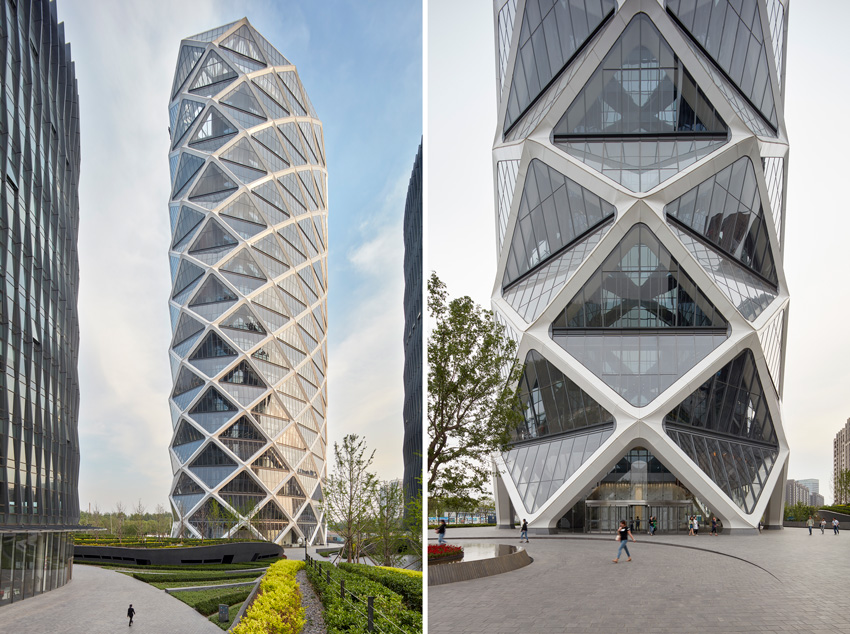
Images courtesy of SOM/Bruce Damonte
Inspired by Chinese paper lanterns, the design of Beijing’s Poly International Plaza main tower’s exterior is formed with a continuous diagrid pattern. Thanks to hollow structural steel, ranging from 600 millimeter diameter to 1,300 millimeter diameter with wall thickness ranging from 15 millimeter to 50 millimeter, the long-span structural design opens up the interior, creating a column-free work environment.
In order to boost fire-protection performance, Wang states in his white paper, “The presence of reinforcement in the concrete will improve the flexural and axial properties of the core and so improve the fire resistance, particularly where buckling stability and/or bending moments are major factors.”
As born out through testing conducted by the National Fire Laboratory, Institute for Research in Construction, National Research Council Canada, in partnership with the Canadian Steel Construction Council and the American Iron and Steel Institute, reinforced concrete fill in the form of fiber or reinforcing bars provides a higher level of fire resistance than plain concrete fill.
According to these test results, unprotected HSS columns were capable of resisting flames for 15 to 20 minutes, whereas plain concrete-filled tubes resisted fire for 1 to 2 hours, and bar-reinforced and steel-fiber-reinforced concrete delivered fire protection for as long as three hours.
Golinski also states that higher-strength concrete provides better fire resistance, as do larger column dimensions, whereas the concrete will heat up more rapidly with smaller columns.
That said, the NRC studies found that increasing the diameter of the concrete core beyond 25 millimeters did little to increase the fire endurance period.
Similarly, the HSS thickness was not found to have significant influence on fire endurance. In fact, increasing the wall thickness reduces the size of the concrete core and ultimately reduces the member’s load-carrying capacity in fire conditions.
Along these lines, Golinski also points out that it’s not practical to overdesign every column to have a lower than average load-to-capacity ratio of 1.0. “Engineers need to find a balance between efficient gravity design and one that works well for fire resistance,” he says in the Steel Tube Institute webinar.
As recommended by Kodur and MacKinnon, it is more economical to keep wall thickness to a minimum unless other factors, such as connection details, otherwise dictate.
Additional parameters that will ultimately determine the fire-resistance performance levels of concrete-filled HSS include the outside diameter/outside width of the column, column load, effective column length, concrete strength, type of aggregate, type and percentage of reinforcement, and the concrete cover thickness to reinforcement, if any.
In order to establish the fire resistance of a concrete-filled HSS column, it must first be determined what temperatures the steel tube, concrete core, and reinforcing bars will reach at the fire-resistance time. Then the mechanical properties of the materials are reduced accordingly, explains Wang.
“The reduced mechanical properties are then used to evaluate the load-carrying capacity of the column, in the same way that the column’s load-carrying capacity would be calculated in a normal, cold state. If the load-carrying capacity of the column at the fire-resistance time is not less than the applied load, then the column can achieve the required fire resistance,” he explains.
When calculating specific fire-resistance values, the equation VI-6 given in AISC DG19, which is taken from ASCE 29, takes into account concrete fill strength, column length, outside dimension of the steel shape, and compressive load that the column is carrying.
Golinski points out that the equation distinguishes between a round shape and rectangular shape.
“With the latter, the corners are relatively thin and can be approached from both sides by the heat. The corners tend to heat faster than the main concrete core,” he explains. “Therefore, the rectangular shape loses its strength more quickly than the round shape.”
Reynolds adds that eliminating the weak dimension also reduces the cross-sectional area required, as these members are less susceptible to buckling. “This can be particularly important for columns with a greater unbraced length, such as those found in a building atrium. The equal section properties of HSS and the elimination of the weak direction can also be advantageous in cases where columns experience lateral loads or require stiffness in both principal directions.”
Breaking down some of the other variables, the longer the length, the less fire resistance provided due to the slenderness of the member. That said, this will only come into play under “severe” fire conditions, as opposed to “medium” or “mild” conditions.
Furthermore, as the load ratio increases, fire resistance decreases. This reduction occurs more rapidly as the load ratio approaches 40 percent and decreases at a slower rate after that.
“Part of this reason is that the concrete fill generally provides 30 percent to 40 percent of the overall composite column capacity,” explains Golinski. “For load ratios over 40 percent, we need to reinforce our concrete fill in order to achieve higher fire resistance.”
Another variable is the cross section size. For instance, a larger cross section will contain a higher percentage of concrete to steel, thereby boosting fire resistance.
At the same time, testing has shown that when specifying unreinforced concrete-filled HSS, once the column edge dimension exceeds 16 inches, there is no longer a fire-resistance advantage. This value is the width or depth of the column, if the member is square or rectangular, or the diameter, if the column is round.
In terms of the effect of the concrete aggregate type, carbonate limestone aggregate temperatures will increase at a slower rate, yielding a slower loss of strength, as compared to siliceous quartz aggregate.
Because these calculations are best carried out with Excel spreadsheet-based software, Tata Steel enlisted the University of Manchester to write such a program, Firesoft, which is now freely available to the industry at: software.tatasteeltubes.com.
That said, Reynolds points out that a simple approach to utilizing concrete-filled steel in construction is to use prefabricated column systems because these systems have already been tested, rated, and labeled by Underwriters Laboratories for their fire-retardant capabilities.
Steel Erection and Concrete Placement
Filling HSS with concrete is most efficient when first erecting the steel, which only requires connecting prefabricated steel sections and afterwards piping the concrete into the tubes. This way the contractor doesn’t have to wait for the concrete to dry prior to erection.
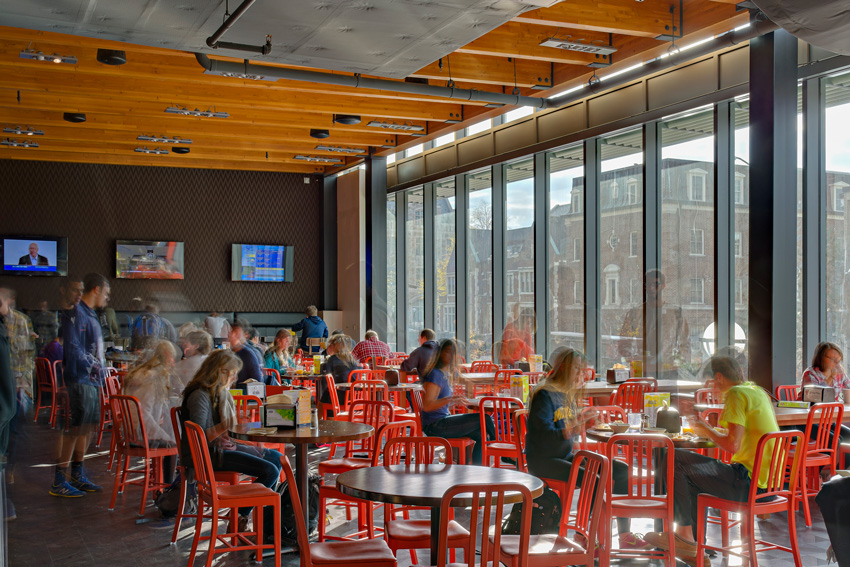
Photo courtesy of SmithGroupJJR
For an expansion and renovation of the dining hall at the South Quad dorm at the University of Michigan in Ann Arbor, SmithGroupJJR used prefabricated UL-tested HSS columns that arrived on-site with a shop-applied concrete wrap or infill.
With reinforced concrete construction, columns have to first be cast so that they can provide support for casting floors afterwards, explains Wang. “This is a sequential process with waiting time. In contrast, when using concrete-filled tubes, the basic steel tubes have sufficient resistance to support floors so filling the steel tubes with concrete can happen at the same time as casting the floor.”
Enabling both the steel and concrete trades to work independently facilitates a much more efficient process with less coordination required, resulting in more economical construction overall, according to Ashrafi.
Placing the concrete after erecting the steel simplifies the delivery and handling of the members since the hollow members are lighter to lift and maneuver. “Also, the quality of the concrete fill is better if placed on-site to avoid damage that could occur during delivery—damage that could be very difficult to detect,” says Reynolds. “In addition, field connections can be easier to perform prior to the installation of the concrete fill.”
Since the concrete trade is already on-site for pouring slabs, it is also possible to detail fill holes in the HSS at floor level so that the concrete filling can happen simultaneously with the floor deck concrete placement.
Concrete can then be pumped through an opening in the top or bottom of the column, using the same equipment used for filling tall concrete wall forms.
“Alternately, a staging area can be set up on-site where the columns are filled in a vertical or inclined position. Employing this method means that all columns can be filled at one time,” writes Olson.
Whether filled in place or in a separate area, the concrete contractor must take steps to ensure that the concrete does not segregate during placement and to prevent the concrete from free-falling and hitting the HSS walls, reinforcement, or other appurtenances present within the HSS cavity.
“For this reason, a good rule of thumb is that concrete should not free fall more than 3 to 5 feet. In order to achieve this, concrete placed through an opening in the top of an HSS column should be done so by means of a tremie chute, AKA, an elephant’s trunk,” state Olson and Kaan in the Steel Tube Institute article.
One noteworthy construction benefit leveraged by HSS columns is that they eliminate the need for formwork. “Additionally, during the process of regular concrete construction, the concrete must gain minimal initial strength for construction to progress,” explains Biswas. “HSS carries the initial load for structures so initial concrete strength is not a factor in speed of construction.”
As previously noted, while prefabricated UL-tested concrete-filled columns are available on the market, they are heavier to erect and can be challenging to achieve field connections for the framing, adds Reynolds.
Performance-Based vs. Prescriptive Design
While a prescriptive approach to code and building design requires that individual components be built to a certain standard, the goal of a performance-based approach is for the entire building to meet a certain standard based on its unique conditions.
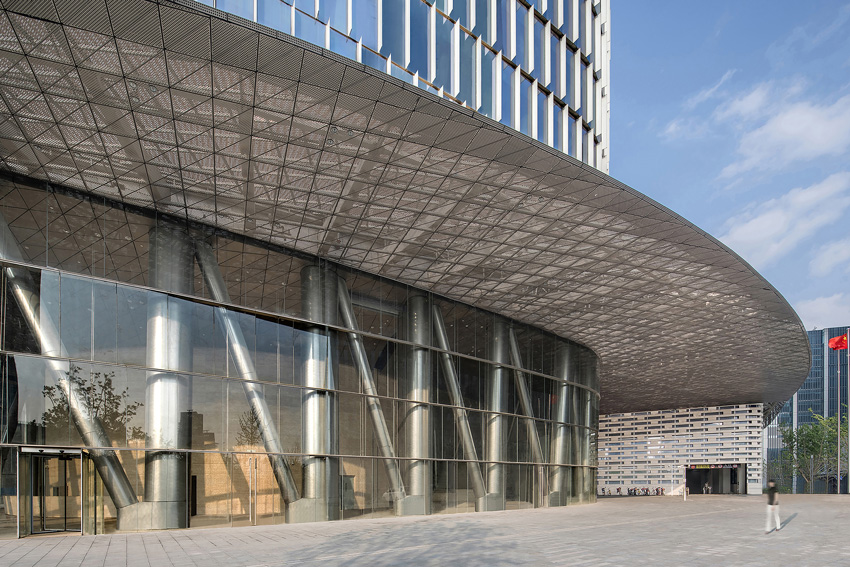
Image courtesy of SOM/Archexist
Concrete-filled HSS deliver a modern, clean facade at the Ningbo Bank of China Headquarters.
While the majority of building projects in the United States are still designed in accordance with a prescriptive approach to meeting code, concrete-filled HSS are generally part of a performance-based design (PBD) approach (outside of prefabricated, UL-listed products).
With a prescriptive approach, concrete-filled members are generally treated as basic HSS columns according to nominal steel assessment temperatures of approximately 550 degrees Celsius, which yields very thick fire protection, according to Wang.
A standard prescriptive fire rating is based on ASTM E-119 testing in a furnace that exposes the test specimen to a predetermined time history of temperatures. However, Ashrafi points out that this furnace test is not tied to any actual fire scenarios that the structure is likely to experience.
“In addition, prescriptive requirements typically come with certain limitations on their applicability based on the data used to derive those prescriptions,” he explains. “By contrast, PBD allows for designing based on realistic fire scenarios and considering the expected performance of the individual structural components as well as the structure as a whole, considering the wide range of geometries and other parameters of design.”
“PBD tends to look more at each specific building and its conditions rather than just developing a procedure and applying it to all buildings,” agrees Olson. “PBD yields more accurate fire-protection requirements and less overdesign.”
In addition, designers and engineers also appreciate the creative freedom and potential efficiencies in design offered by PBD.
“Such solutions provide realistic and improved fire performance over currently used prescriptive provisions in codes and standards, which are very restrictive and too simplistic in nature,” states Kadur.
Although more prevalent in Europe and the Far East, PBD is catching on more in North America, particularly with high-rise construction.
“Performance-based design provides an opportunity for the designer to develop creative solutions, including alternate materials or construction methods that comply with the intent of the code,” explains Reynolds. “This can also lead to innovation and solutions that are far superior to the prescriptive-based approach.”
In order to meet code requirements, she explains that the PBD approach usually enlists the use of analytical tools, such as computer analysis and simulation, to predict performance under extreme fire conditions. Bench top and full-scale testing is also used, and precedents set by past testing and/or applications are taken into consideration as well.
In Conclusion
By preserving aesthetic elements, enhancing structural support, and delivering cost-effective fire protection, concrete-filled HSS offer a solution architects, engineers, and building owners alike can agree on.“Exposed steel structure elements can be used as final architectural elements, eliminating cladding and reducing the overall appearance of structural elements, creating a smaller and more aesthetically pleasing appearance,” says Biswas.
As exposed steel designs continue to gain popularity, building experts anticipate that concrete-filled HSS, particularly where fire resistance is required, will gain traction as well.
![]() |
The Steel Institute of New York is a not-for-profit association created to advance the interests of the steel construction industry by helping architects, engineers, developers, and construction managers develop engineering solutions using structural steel construction. www.siny.org |