Large-Size Porcelain Slabs for Building Surfaces
Interiors and exteriors finished with half-inch slabs can create lightweight and beautiful results
Continuing Education
Use the following learning objectives to focus your study while reading this month’s Continuing Education article.
Learning Objectives - After reading this article, you will be able to:
- Identify and recognize the characteristics of large-format, half-inch-thick porcelain slabs as defined by industry standards.
- Explain the life cycle of porcelain slabs from raw material extraction through manufacturing, building installation and use, and end of service life.
- Assess the safety and functional contributions of large-format porcelain slabs for both interior and exterior surface treatments.
- Specify porcelain slabs in a variety of new and renovated buildings, and make appropriate selections related to specific applications.
When it comes to selecting materials for building surfaces, a number of factors come into the decision-making process. The appearance of the material and the way it fits with an overall design scheme is often paramount, but so is the durability and strength of the material. Special uses may dictate the need for easy-to-clean surfaces or even hygienic surfaces if used in kitchen and bathroom areas. And of course, the material has to fit within the overall project budget. Among the choices, porcelain ceramic tile is often selected for its ability to meet all of these criteria, particularly in areas that are heavily used or require clean and hygienic surfaces. One of its historical drawbacks, however, has been its comparatively small size, which necessitates grouted joints to take up a fair amount of a floor or wall area. The grout can be susceptible to damage or the promotion of organic growth if not maintained properly. However, this limitation, and others, have been overcome with the recent availability of large-size porcelain slab panels that can be specified in sizes to match or exceed large sheet stock products. These large but relatively thin (half-inch) porcelain slabs retain all of the superior characteristics of porcelain tile plus add new ones, such as the ability to simulate natural stone, wood, and other materials. In this course, we will take a closer look at this innovative update on a well-known and proven material that is suitable for a wide variety of both indoor and outdoor applications.
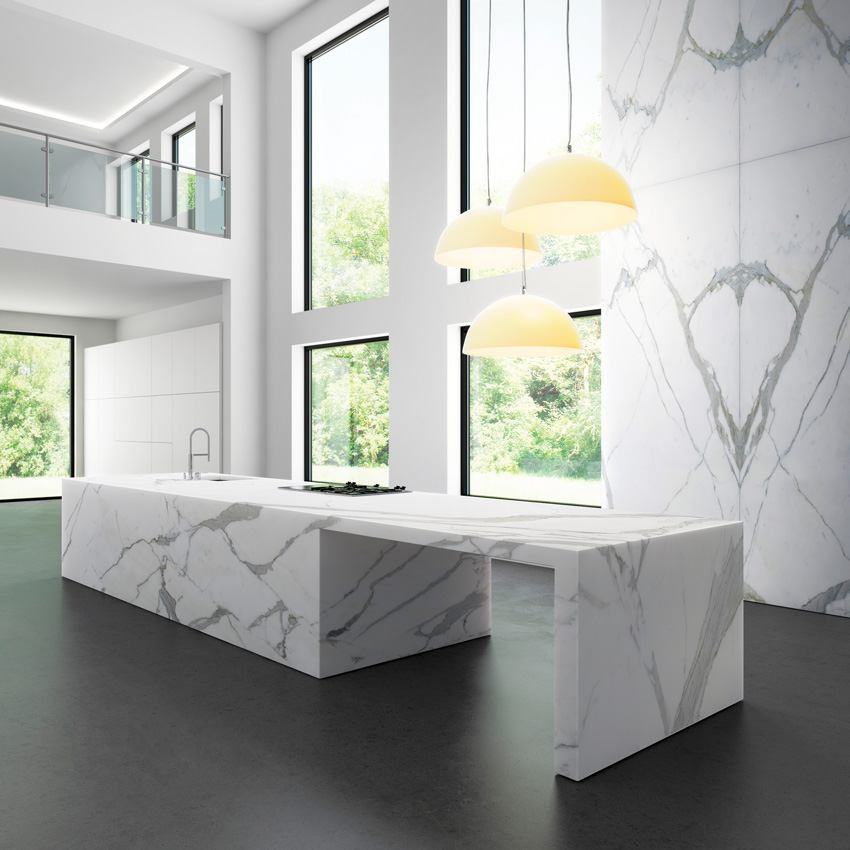
All images courtesy of Walker Zanger, except as noted
Large-size, thin porcelain slabs are now available in the United States, offering dramatic looks for interior and exterior applications with minimal grout lines.
Large Porcelain Slabs
Some clients and even design professionals can get confused over the difference between ceramic tile and porcelain tile products. The process and materials to create both types of tiles are essentially the same. The difference really lies in the quality of the raw materials used. Compared to ceramic, porcelain clays are cleaner, whiter, and higher quality with less impurities. This makes the raw materials a little more expensive, but overall the final product cost is still very competitive. The higher-quality materials also allow for more finish options, including through-body coloring, specialty patterns, and even high-quality unglazed tiles.
Building on a long history of creating porcelain tile products, some manufacturers in Europe and the United States have developed advanced techniques to make larger and thinner porcelain tile products. Using sophisticated machinery and careful quality control, designers are no longer limited to common sizes, such as 12-inch square porcelain tiles or 18-by-7-inch porcelain planks. Instead, many more face sizes have become available, with technology now allowing for large porcelain slabs to be produced up to 63 inches by 126 inches (5 feet 3 inches by 10 feet 6 inches). That is noticeably larger than common 4-by-8 or 4-by-10 sheet good wall and floor panel products, meaning that seams and joints can be reduced even more compared to those products. Further, for things like kitchen islands, countertops, or wall surrounds, a single slab may be able to be used, thereby eliminating joints altogether.
In terms of thickness, some large porcelain products are available in very thin (less than ¼ inch) profiles. However, once the material gets down to that size, it can be brittle and difficult to work with since it could be more prone to cracking and breakage. That is why many industry professionals suggest that half-inch thickness is ideal for most building applications. The half-inch material is thick enough to be strong, rigid, and durable but still thin enough to be lighter in weight than some other choices like natural stone. Further, the half-inch-thick material is commonly made so it is competitively priced.
Since porcelain and ceramic tile products have been in use for some time and are fairly well understood, it is not surprising that there are industry standards for its manufacture. Specifically, ANSI A137.1:2012: American National Standards Specifications for Ceramic Tile presents voluntary standard specifications for ceramic tile. It was developed by the Accredited Standards Committee (ASC) on Ceramic Tile 108, which includes representatives from across the industry, including the Tile Council of North America (TCNA). As described by the writers, “It lists and defines various types, sizes, physical properties, and grading procedures for ceramic tile, including mosaic tile, quarry tile, pressed floor tile, glazed wall tile, porcelain tile, trim units, and specialty tile. This standard provides quality criteria for buyers, specifiers, installers, manufacturers, and the public in general. It is intended for reference or inclusion in the ceramic tile section of project specifications and contracts.” As such, this standard is a good general reference for the quality levels and criteria for porcelain ceramic products of all sizes and thicknesses. In addition to establishing physical criteria for tile for quality and strength, it also describes procedures for testing for safety, particularly when used on walking surfaces.
Some additional relevant standards include ANSI A137.3: American National Standard Specifications for Gauged Porcelain Tiles and Gauged Porcelain Tile Panels/Slabs and ANSI A108.19: Interior Installation of Gauged Porcelain Tiles and Gauged Porcelain Tile Panels/Slabs by the Thin-Bed Method Bonded with Modified Dry-Set Cement Mortar or Improved Modified Dry-Set Cement Mortar. These standards provide more specific information related to large-size porcelain slabs.
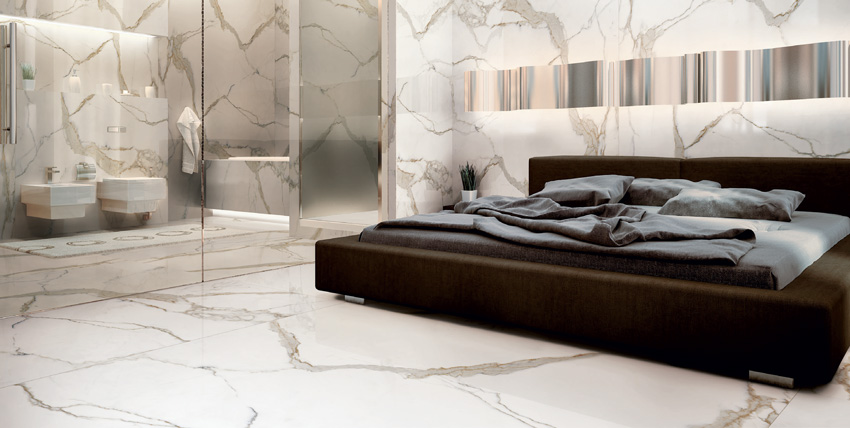
Porcelain tile that is only half-inch-thick but up to 5 feet by 10 feet in size can be used for a variety of building surfaces.
Manufacturing Process
To get a better understanding of the nature of porcelain products, let’s take a look at the basic life cycle of the product, starting with the extraction process. The basic raw materials are mined from the earth and can include clay, silica, kaolin, sand, and feldspar. These are transported to the manufacturing facility, sorted, and stored until they are needed for production. In addition, glazing raw materials can include things like feldspar, clay, frit, and coloring agents that are also sorted and stored. Some of the coloring agents can contain precious metals, which makes them more costly but also less commonly used.
In a typical production process, the raw materials needed for a specific porcelain product are selected and mixed along with 30 percent water. This usually occurs in a ball mill machine, which turns the mixture into a homogenous slip. That slip is dried into prills (spheres) in a spray drier that reduces the moisture content down to 6 percent or so. At this point, the material is stiff but pliable and ready for pressing. Essentially, pressing involves placing the prepared prills into a pressing machine and exerting an immense, uniform load to create thin, flat tiles or slabs. There are several different press types based on different manufacturing processes and brands, but they all rely on pressures on the order of 7,000 pounds of force per square inch or total pressures up to 15,000 tons depending on the size and configuration of the pressing machine. It is the advanced development of these large presses that has made the large-size porcelain slabs possible. Such presses are among the largest in the world and necessary in order to press the prills to be large enough and dense enough to produce the needed characteristics for the large porcelain slabs.
Once pressed, the porcelain mixture is ready for further drying and finishing. The details of these steps will vary based on the type of product being produced and the type of finish sought. For example, smooth surface products will rely on smooth-faced pressing and processes, while molds may be used during or after the pressing to create texture in the surface of the porcelain. Additional drying may also occur to bring the pressed slab to the preferred moisture content for a particular finish. If the slab is to have a glossy colored surface finish, then glazing may be added if appropriate. In other cases, the glaze may be omitted and the color of the material itself be retained or a pattern within the material can be created to replicate stone, wood, etc. Once these details are finalized and carried out, then the slabs are ready for firing in a large kiln that can reach temperatures up to 2,200 degrees Fahrenheit. The time required for firing will vary based on slab thickness, but the goal is to achieve a 4 percent moisture content at the end of the firing. The porcelain is now hardened and, once cooled, achieves its final characteristics of strength, durability, and basic finish. Any final finish enhancements can be made at this point, such as cleaning, polishing, or edge cutting (rectifying) to final precise sizes.
The finished large porcelain slabs need to be transported to the building site and handled properly both in the factory and on-site to protect both the finished slabs and the people working with them. As such, they are commonly handled using carefully placed suction cup lifting devices, much the same way large glass panes are carried and transported. Then they are set into protective crates and made ready for shipment. Once received on-site or in a fabrication ship, the crates need to be carefully opened and the large slabs lifted out again with suction cup based carriers. This means that experienced tradesmen are needed to handle, and prepare the slabs for final installation.
With an understanding of the material, we can now look at some of the applications, both interior and exterior, where large porcelain slabs can become an integral part of a building design.
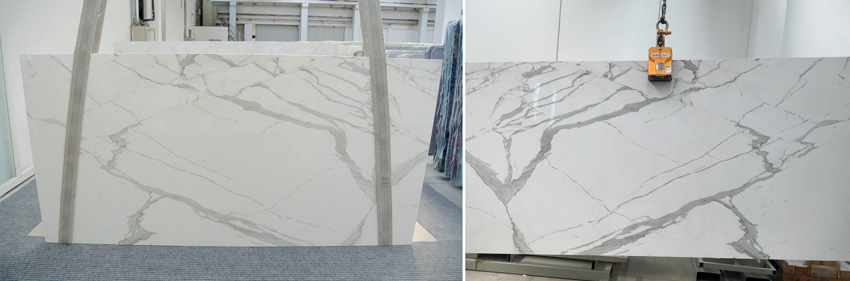
Large porcelain tile slabs are handled and shipped from the factory to the site within much the same way stone slabs or glass sheets are handled.
Interior Building Applications
Large half-inch-thick porcelain slabs can basically be used in interiors anywhere other ceramic or porcelain products are used. That includes traditional applications, such as new or existing rooms for walls and floors, as well as specialty treatments in kitchens and bathrooms, such as backsplashes and countertops. However, it is also durable enough that it can be used in commercial spaces, such as public circulation corridors, elevator cabs, and stairwells.
From a design standpoint, large-format porcelain slabs offer a variety of looks that are not limited to traditional tile appearances. In particular, they can be patterned to look like white or black marble, other stone, or even wood grain in a choice of patterns. The large size of the slabs allows coverage of floors or walls with minimal joint lines, replicating again the look of natural stone or other large slab materials. Of course, the large slabs can be combined with smaller tiles, planks, or other porcelain products to create a varied appearance that is coordinated in style and uniform in performance.
The edge condition of the slabs can be selected based on the final appearance and performance as well. Common edges are square and quite acceptable for most installations with common joint widths. For installations that seek the appearance of minimal joint lines and tight tolerances, then precision-cut (i.e., rectified) panels can be specified to be created in the factory. This creates very thin grout lines, giving the porcelain the appearance and control of solid stone slabs. For countertops in particular, porcelain slabs can be preferable since they overcome some of the maintenance requirements of some natural stone. For example, recommendations for stone slabs include avoiding the use of certain abrasive cleansers or cleaning pads. In addition, acidic materials, such as lemon juice and vinegar, can etch some stone surfaces, especially limestones with low porosity. And because normal wear and tear can affect even the most durable stone, some scratching and chipping may occur over time. Porcelain slabs can overcome many of these issues if denser and less porous products are selected.

Large-size porcelain slabs are a preferred material for countertops since they overcome some of the limitations of natural stone for this use.
When reviewing porcelain products for commercial or residential projects, it is important to recognize that different products will be rated for different levels of durability. A common rating breakdown follows:
- Light duty: These products are intended for use on interior vertical surfaces only. This may include commercial spaces, depending on the intended use of the space. Light-duty tile may have special cleaning or care requirements.
- Medium duty: These products are intended for use on interior vertical and some horizontal surfaces in most residential and some commercial applications. This includes bathroom walls, showers walls and floors, vanity tops, wainscoting, kitchen backsplashes, as well as light use kitchen counters. Commercial applications may be limited to interior vertical applications.
- Heavy duty: These products are appropriate for use in all residential applications and many commercial applications, including all medium-duty applications as well as all kitchen counters, residential flooring, pools, and exterior vertical surfaces, but only areas that do not experience freeze/thaw conditions. Commercial uses include most wall and floor applications, with the exception of heavy-traffic flooring.
- Commercial duty: These products are manufactured to the highest standards of durability, and are recommended for all interior and exterior residential and commercial applications, including heavy pedestrian traffic flooring. Recommended uses include heavy-traffic residential areas, commercial lobbies, and other areas that require a tile with maximum durability.
When considering heavy-duty or commercial-duty porcelain for flooring, there is also a safety concern that needs to be addressed, namely, slip resistance. This is specifically addressed in ANSI A137.1-2012, which defines an updated method for assessing and rating tile surfaces (including large porcelain slabs). Previously, ASTM C-1028 was the standard test method for determining the nonmoving or static coefficient of friction (SCOF) of ceramic tile and other like surfaces. Static coefficient of friction is a term used in physics to describe the amount of force required to cause an object in contact with a surface (e.g., shoe sole on tile floor) to start moving across that surface. A higher coefficient indicates increased resistance of shoe sole material to start moving across a flooring material. While this produces a measured value, no standards have a specifically determined ‘safe’ SCOF value.
Due to the difficulty in measuring SCOF and lack of a specific recommendation, ANSI A137.1-2012 changed the testing requirement to a moving or dynamic coefficient of friction (DCOF). DCOF differs from SCOF in that the shoe material is made to move across the flooring surface and the resistance to movement is constantly recorded and averaged. This test uses an automated device (i.e., the BOT 3000 recommended) instead of the human hand, which reduces the variation in the test method from 30 percent in the SCOF measurement to less than 10 percent for DCOF. As such, ANSI 137.1 now includes a method for measuring (DCOF) with a recommended minimum value of 0.42 for interior, level floors that are likely to be walked upon when wet. Specifically, it states, “Unless otherwise specified, tiles suitable for level1 interior spaces expected to be walked upon when wet shall have a wet DCOF of 0.42 or greater when tested using SLS solution as per the procedure in Section 9.6.1.” With all of this in mind, most manufacturers have their porcelain floor products independently tested using the procedures and guidelines in this standard and report the results in product literature with the goal of achieving the DCOF of 0.42 or greater.
Keep in mind that when selecting a tile for slip resistance, however, the ANSI standard is very clear to state, “Because many variables affect the risk of a slip occurring, the COF shall not be the only factor in determining the appropriateness of a tile for a particular application.” Therefore, it also makes clear that “tiles with a DCOF of 0.42 or greater are not necessarily suitable for all projects. The specifier shall determine tiles appropriate for specific project conditions, considering by way of example, but not in limitation, type of use, traffic, expected contaminants, expected maintenance, expected wear, and manufacturers’ guidelines and recommendations.” This professional judgement and prudent assessment is true for all flooring, and in this case, applies equally to porcelain slabs as well.
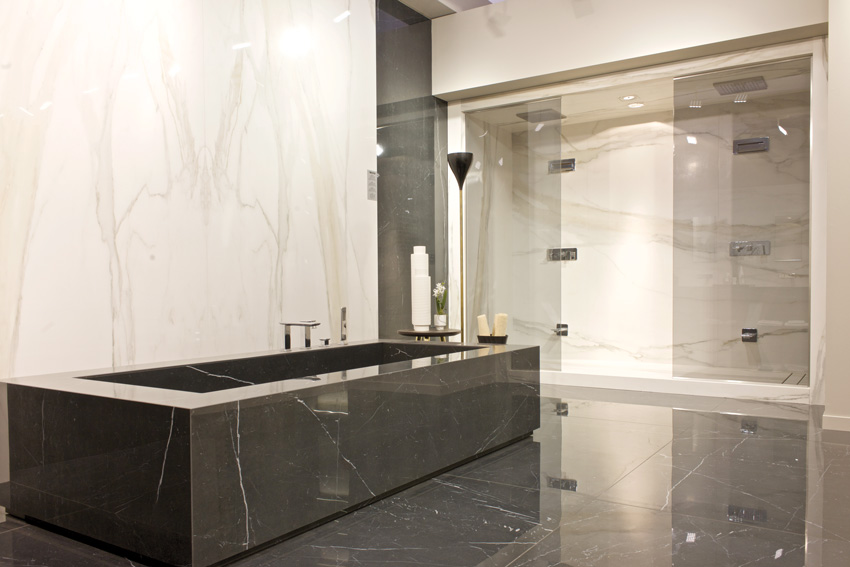
Porcelain tile used for flooring needs to be tested for slip resistance based on the requirements of ANSI A137.1-2012 and is particularly important in wet areas.
Slip resistance is important on flooring but also important in places that are expected to be wet, such as bathrooms and shower areas. Those areas will need some special attention when porcelain is used on the floor. In addition to the surface, all shower floors need to be detailed to include appropriate waterproofing in the event that any seams or joints seep water over time. The general industry recommendation is for shower floor substrates and adjacent walls around the perimeter (12 inches up) to include a waterproof membrane on the top surface of the fully cured mortar bed prior to tiling. No allowances or claims are normally accepted by manufacturers or suppliers of porcelain, or other shower flooring materials for that matter, for damage to products installed in shower flooring that do not have a waterproof membrane system installed.
Exterior Building Applications
While interior applications of large porcelain slabs are commonly thought of, exterior applications on building facades are a logical and attractive choice too. Panel-type building facades have been common for decades and often include wood or steel framing for the structural support, plus a supported finished panel as the exterior weathering surface. Large porcelain slabs can easily replace stone panels or other panels, thus creating a lightweight but durable surface, coming in at about 5.5 pounds per square foot. With the range of colors and patterns available, they can be used to replicate wood, stone, or smooth surfaces in a consistent pattern across a facade or with contrast and variety built in. Further, with the growth in the need for continuous insulation in exterior wall assemblies to comply with energy codes, porcelain slabs can readily cover the face of continuous insulation, creating a full cladding surface.
The key to successfully using porcelain slabs for the outermost surface for any exterior wall assembly is the method of attaching or securing them in place. In some cases, adhering the tile to an appropriate wall sheathing or backer board on the exterior wall may be appropriate for residential or light commercial buildings. The joints would then be grouted with an appropriate watertight grout and sealed if needed. Checking with manufacturers and following specific recommendations and guidelines for the adhesive and grout used will be important here to assure proper installation and durability. Also checking for guidelines on height will be important; a slab placed above another may need some additional support to avoid creep and movement over time.
For commercial installations, a common approach for panelized facades is to use an aluminum support system of vertical and/or horizontal channels or tees that are secured to the building structure with adjustable aluminum clip angles. Porcelain slabs can be set into such a support system that carries the weight and wind load of the slabs, transferring directly to the building structure. The depth and spacing of the clips and channels can be designed to allow for continuous insulation to be installed between them and satisfy thermal envelope requirements.
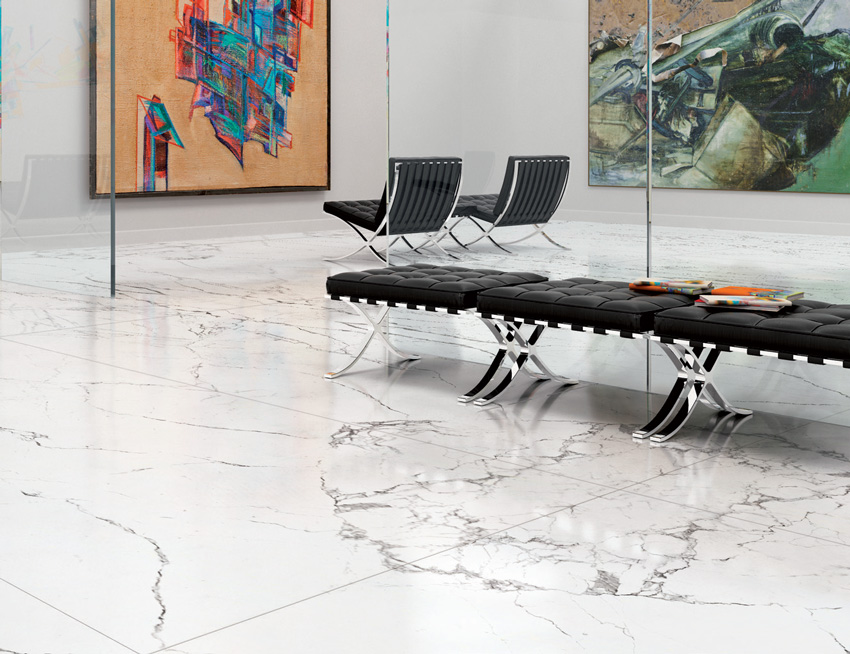
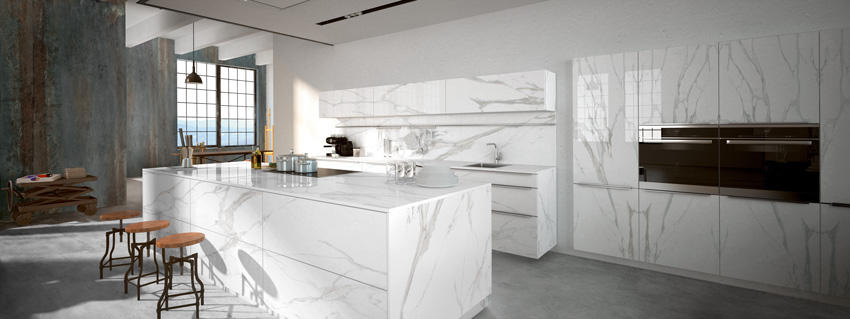
Large porcelain slabs can be used on interior and exterior walls and installed with concealed mounting, allowing the exposed face of the porcelain to be the only visible component.
When it comes to attaching the panels to the support system, there are several common methods of attachment that can be used. In the simplest form, panels can be attached using adhesives to create a chemical bond between the panel and the support system. Instead of adhering to the substrate, as may be done for residential systems, porcelain slabs can be adhered to the aluminum support system based on tested and certified adhesive materials and techniques. One of the visual benefits of this approach is that, since the anchoring is done completely on the back side of the slabs, the joints are the only thing seen on the face. From a performance standpoint, this type of mounting uses the continuous nature of the adhesive anchoring to distribute stress evenly, preventing any concentration of stress in the adhesion surface and minimizing critical points where ruptures could begin. Further, the nonconductive properties of such anchoring enables the connection of different types of materials and prevents galvanic corrosion.
In some cases, it is desirable to have a full mechanical support system that wraps over the edges of the panels with exposed clips or clamps. Such systems have been developed for facades by a number of different manufacturers based on using aluminum trim type of profiles that attach to the support system. Visually, the aluminum trim can be a minimal profile that simply secures the slabs in place or a pronounced profile that adds shadow lines and reveals to the facade. In doing so, the popular building facade design approach of using a ventilated rainscreen system can be considered. In this case, the facade is based on the principle of separating the exterior cladding from the rest of the wall assembly. A space between them is intentionally designed to allow for air to enter and ventilate the wall as well as allow any water that enters to drain out of the bottom and away. The idea is that the cladding is the first line of defense against the weather but allows for air and water to enter a small space behind it. The surface of the substrate wall is treated to provide the full and continuous air and water seal and is protected by the cladding, in this case, the porcelain slab.
For tall buildings subjected to higher wind loading, ventilated rainscreens need to be looked at a bit closer. Higher wind loads mean more pressure is applied to the exterior cladding, and that can cause problems either to the cladding or the systems behind it. The solution is a pressure-equalized rainscreen that relies on creating smaller compartments across a facade rather than one continuous ventilation cavity. These ventilation compartments respond independently to constantly changing wind pressure. When wind-driven air enters openings in the bottom of the rainscreen and finds no way to exit, the air pressure inside the cavity matches the wind’s pressure and “pushes back” against it, preventing wind-driven rain from entering. If a small amount of rain is driven into the cavity, the same openings allow the water to drain.
In addition to the main facade cladding material, porcelain slabs can be considered for trim, accent, soffits, and other feature areas of a building. The selected textures, patterns, or colors can be precut or cut in the field using common tile-cutting techniques to create simple or ornate exterior designs.
Fabrication and Installation
Regardless of how the porcelain slabs are being used, it is important to fabricate and install them according to industry standards and in accordance with manufacturers’ recommendations and instructions for specific application. In all cases, the large sizes available help reduce installation time, thus saving labor costs, but proper workmanship and appropriate attention to detail is needed as with any finish material. It is also worth noting that field fabrication is possible with results that can rival factory precision for mitred edges and other details. This can be particularly important for custom items, such as countertops and stairs.
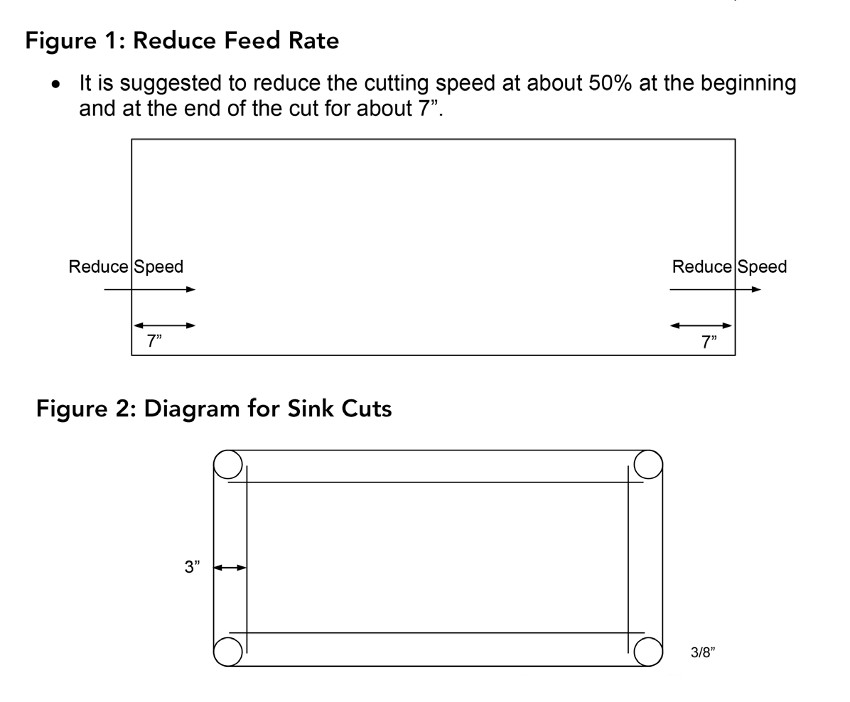
Illustrated fabrication instructions are commonly available from porcelain slab manufacturers and should be followed carefully for best results.
When porcelain slabs are being fabricated with cutouts or custom shaping, then water-cooled bridge saws or waterjet machines are called for, as with most porcelain and ceramic tile work. Commonly for saws, a 400-millimeter segmented blade spinning at 1,600 RPM and advancing on the order of 36 inches per minute is the norm, with water feeding directly onto the spot where the blade contacts the slab. Before fabrication starts, it is advisable to trim approximately ¾ inch from each of the slab’s four edges to remove any possible tension stress that may be within the slab. For all cuts, it is also recommended that the beginning and finishing portion (approximately 7 inches along either end of the cut line) be done 50 percent slower or 18 inches per minute. For 45-degree-angle cuts, the feed rate should be reduced to 24 inches per minute.
For cutouts, it is recommended that at least 2 inches of porcelain remain between the edge and the cut out to retain the integrity of the slab edge. Use of a drill for the corners will help assure precise fabricating. Within a cut out, the main body of the opening should be cut and removed first, leaving approximately 3 inches to be cut separately in a more controlled manner.
When installing the porcelain slabs using an adhered method, flooring installations and some small-sized applications could be installed with thin-set or regular-set adhesive common to many porcelain installations. However, for wall applications, whether interior or exterior, some manufacturers recommend a two-part epoxy adhesive due to the potential for the material to creep or slide down vertically. If a backer board is being used, it can be adhered or otherwise fastened to the structure or supporting layer first and then the epoxy applied between the porcelain slab and the backer board. In all cases, the installer needs to assure a 100 percent bond with no air pockets or voids that could allow breakage. If there are any details about the fabrication or installation that need clarification, then it is best to consult the manufacturer since it has probably encountered the situation before.
Technical Specifications
When specifying porcelain slabs, there are, as we have seen, numerous choices and options to select from. Coordination with manufacturers during the design phases of a project will help gain insight into project-specific details, cost drivers, installation nuances, and the latest finish options. In a standard CSI or master spec format, the usual location to include this spec is in Section 09 30 13 Ceramic/Porcelain Tiling. Some of the relevant items to address in a standard three-part specification format are highlighted as follows.
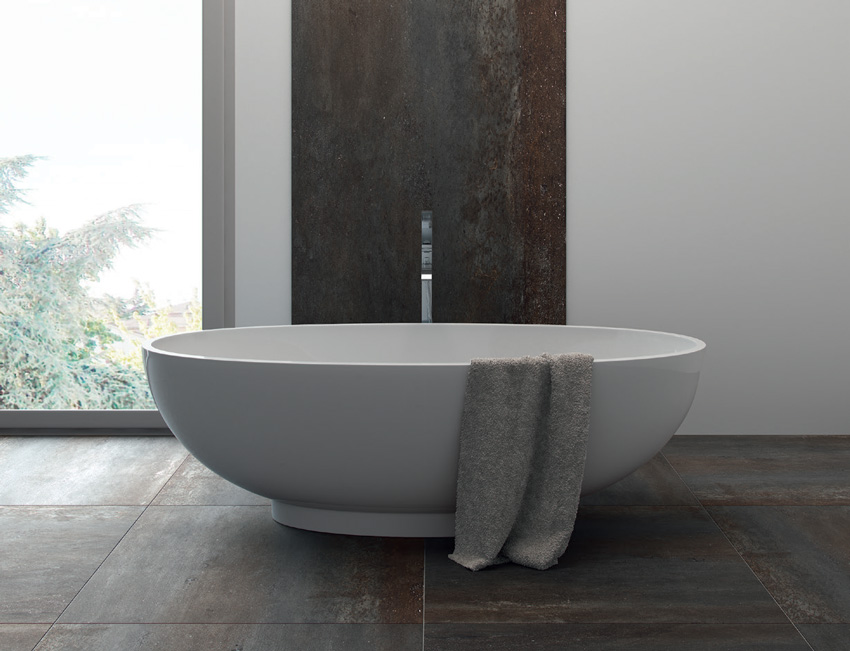
Color, pattern, and edge conditions of large porcelain tile can all be specified with a range of results possible, as shown on the wall and floor of this bathtub area.
Part One: General
The scope of specification work can include all preparation work, substrate review, product choices, and final installation. In carrying out the work, the following standards can be referenced:
- ANSI A137.1: American National Standards Specifications for Ceramic Tile
- ANSI A137.3: American National Standard Specifications for Gauged Porcelain Tiles and Gauged Porcelain Tile Panels/Slabs
- ANSI A108.19: Interior Installation of Gauged Porcelain Tiles and Gauged Porcelain Tile Panels/Slabs by the Thin-Bed Method Bonded with Modified Dry-Set Cement Mortar or Improved Modified Dry-Set Cement Mortar
- ASTM F1869: Standard Test Method for Measuring Moisture Vapor Emission Rate of Concrete Subfloor Using Anhydrous Calcium Chloride.
- ASTM F2170: Standard Test Method for Determining Relative Humidity in Concrete Floor Slabs Using in-situ Probes
Submittals for porcelain products should include the usual manufacturer’s data and information for all products used, plus recommended maintenance and cleaning information to be passed on to the building owner/operators.
Quality assurance is clearly an important part of any field-installed system, and the same is true here. It begins with the use of trained installers and applicators with a prescribed minimum number of years of experience. Evidence of such qualifications can be requested as a submittal, but it is important that the people actually in the field are the ones with the qualifications and experience needed. Protecting products and materials at the site is always important. Fortunately, since the interior work is often done at the very end of a project, the environmental conditions should be controllable.
Part Two: Products
All of the relevant porcelain products used in the building should be called out and specified, whether for interior or exterior applications. Each porcelain product should be identified by type in the specifications and shown on a schedule as appropriate in either the drawings or specifications. The details of the specified products can include:
- specific color and texture or pattern. Manufacturer’s literature should be consulted for this as with any finish product.
- recommended level (i.e., light duty, heavy duty, commercial duty, etc.).
- dynamic coefficient of friction (DCOF) for floor or stair materials.
- glaze hardness measured in standard units.
- shade variation tolerance on color.
- breaking strength as measured using standard tests.
In addition, the particular finishing details of the product should be specified for each type of porcelain product used. Hence, if back mesh (BM) fiberglass reinforcing is needed, it should be specified. Similarly, if rectified edges are desired, that should also be specified for the particular product.
In general, most porcelain ceramic tile does not require sealing so sealants do not need to be included or called for unless there are conditions or situations where the manufacturer recommends it or requires it.
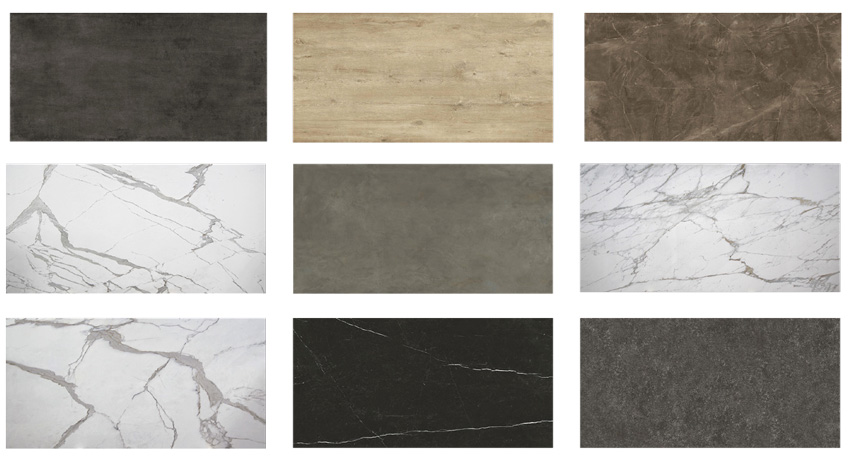
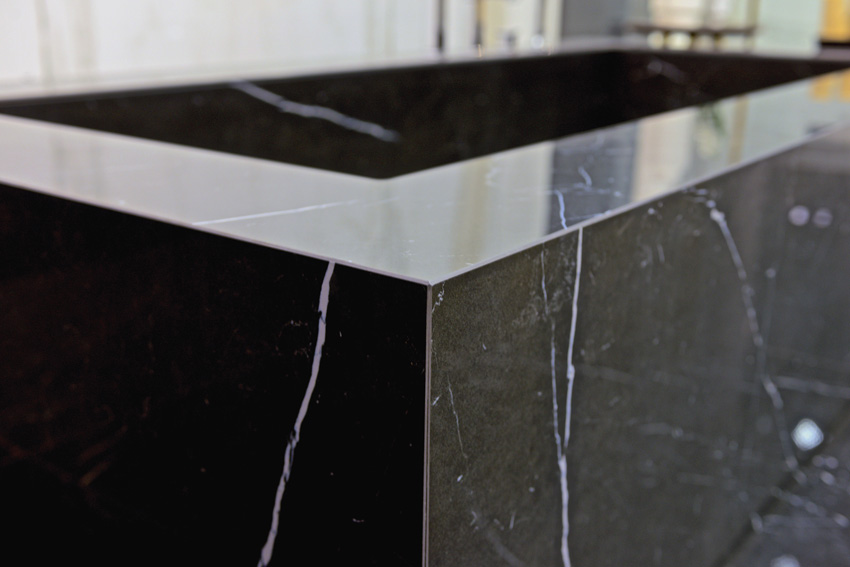
Bottom: Photo courtesy of FLORIM
Large, thin porcelain slabs can be specified in a range of colors, textures, and finishes based on offerings from manufacturers.
Part 3: Execution
As with any finish product, the installation requires multiple steps that need to be clearly articulated in the specification in order to receive the best results.
- Examination and preparation: The importance of this work should be stressed. In addition to the architect, the installer should review and examine the substrate for conditions affecting the performance of the porcelain. Any issues will need to be corrected if they are found to be out of compliance with the requirements of the specifications. All surface defects must be repaired, and all joints and cracks shall be repaired using appropriate materials. Ultimately, the goal is to provide a substrate surface that has been prepared to an acceptable level, is clean of all contaminants, and free of any debris.
- Attachment: For some exterior applications, the method of attachment may require a separate aluminum system to hold and secure the porcelain in place. Such a system should be specified and installed accordingly. For other applications, the method of attachment may be based on standard ceramic tile installation methods using epoxy adhesive or regular- or thin-set compound and grout.
- Placement: The porcelain panels should be placed in the prepared areas according to the patterns and layouts shown on the drawings and in accordance with manufacturers' instructions or recommendations.
- Protection: Once applied, the finish surface needs to be protected during any remaining construction work, including final mechanical or electrical trimming, painting, or any punch list work. If the porcelain is the finish flooring, it needs to be covered and protected just like any other flooring.
Upon completion, all of the porcelain surfaces should be cleaned following manufacturers’ recommendations to produce a complete installation. Cleaning instructions should be provided to the building owner/operators as well. Porcelain ceramic is a relatively maintenance-free product that requires little continuing care beyond regular cleaning. Most cleaning can be done with a damp cloth and a gentle non-acidic soap. More resistant staining, such as calcium spotting and soap scum, can be handled using pH-neutral cleaning products designed for such purposes. Some manufacturers also offer products specially formulated for ceramic tile care. Take care to avoid over-the-counter ceramic tile cleaners that contain phosphoric and glycolic acids that could etch some ceramic tile surfaces.
When specified and installed correctly, large porcelain slabs can work quite well with other construction and help achieve excellent finished results.
Conclusion
Large porcelain slabs provide all of the beneficial characteristics of porcelain tile with dramatic design possibilities. They can have the appearance to rival natural stone, but in a product that is only half-inch-thick and lighter in weight than stone. Or they can provide a rich color, wood grain, or other pattern to a surface. The technical capabilities of porcelain slabs allow them to be used in a wide variety of interior and exterior applications and perform well over time in both new construction and renovation projects. Engaging with the manufacturers to review product information and details helps assure that the best products are selected and specified for a particular building. Properly done, the result will be a long lasting, durable, and well-designed solution for all involved.
References
American National Standards Institute (ANSI) A137.1: American National Standards Specifications for Ceramic Tile and A108.01–A108.19: Installation Standards (www.ansi.org)
International Organization for Standardization (ISO) Working Group 4 Thin Ceramic Tiles and Panels – Definitions, classification, characteristics and marking, installation (www.iso.org)
Tile Council of North America (TCNA) 2014 Handbook of Ceramic, Glass, and Stone Tile Installation (www.tcnatile.com)
United States Green Building Council (USGBC) LEED rating system (www.usgbc.org)
Peter J. Arsenault, FAIA, NCARB, LEED AP, is a practicing architect, green building consultant, continuing education presenter, and prolific author engaged nationwide in advancing building performance through better design. www.linkedin.com/in/pjaarch.
![]() |
Since 1952, Walker Zanger has combined traditional tile-making techniques with a modern sophistication that transcends any singular design style. A leading choice for design professionals and consumers, its natural stone and tile products are found in luxury homes, trendy boutiques, and fine restaurants around the globe. www.walkerzanger.com |