Below-Grade Waterproofing Systems and Design
Exploring modes of failure and the negative impact of moisture infiltration into a structure
Continuing Education
Use the following learning objectives to focus your study while reading this month’s Continuing Education article.
Learning Objectives - After reading this article, you will be able to:
- Describe the importance of below-grade waterproofing.
- Discuss the history of below-grade waterproofing and associated product types.
- Explain important industry terms and definitions, as well as their relevance to below-grade waterproofing.
- Discuss possible failure modes and the serious impact such failures can have on the building and the occupants.
- List keys to success in below-grade waterproofing.
The practice of waterproofing has existed in some form for more than 2,500 years, and it is an essential element for ensuring building longevity. Since humans first began creating dwellings, we have found a need to separate ourselves from the elements, and subsequently, we have taken various approaches to treating our structures’ surfaces to prevent the passage of water into or through the walls.
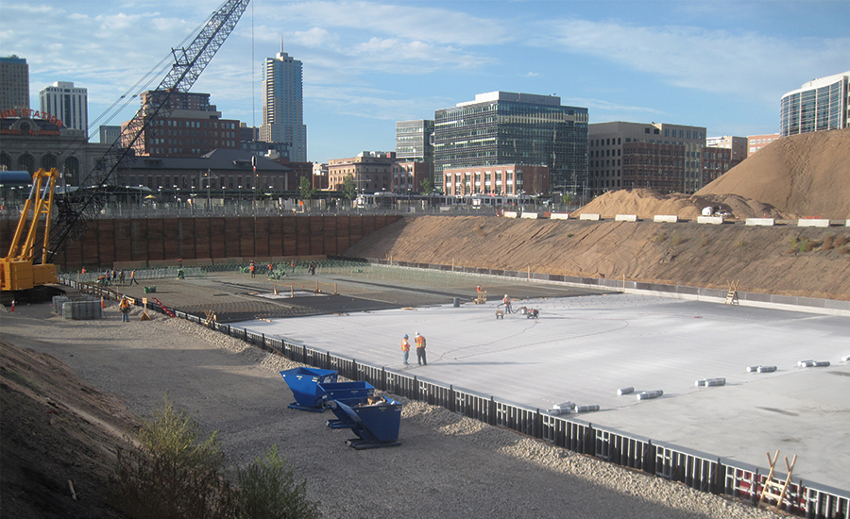
All photos courtesy of SOPREMA
Construction at the Denver Union Station.
Over time, our methodology for controlling moisture infiltration has evolved. People have long relied on natural materials like wax, pitch (bitumen) or clay to control moisture flow, but the technologies have been refined throughout the years. Today, we typically see waterproofing materials and practices fall into one of three categories:
- Liquid-applied waterproofing, which can either be carried out via hot or cold application systems to waterproof surfaces.
- Prefabricated membranes, which can take the form of modified bitumen, elastomeric or thermoplastic sheets that can be easily applied to surfaces.
- Mineral-based systems, which include bentonite clay (which expands when wet to protect concrete and fill small cracks and voids) and crystalline waterproofing materials (which penetrate concrete and seal capillaries) to keep moisture infiltration at bay.
A full understanding of the properties, strengths and limitations of various materials, as well as the forces you might be working against when attempting to protect a structure, is critical to “getting it right” when designing a waterproofing system. For this reason, this course will cover not only why below-grade waterproofing (specifically) is important, but also the environmental, installation and other factors that play into designing and deploying a successful waterproofing assembly.
Why Focus on Below-Grade Waterproofing?
While the highly visible elements of a building typically receive the most attention, we know it’s the unseen components that often have the greatest impact on the building’s performance and lifespan, as well as potential cost overruns and delays during construction. This is as true with waterproofing elements as it is with anything else—the most visible materials gain the most mindshare, but the hidden materials may make the most difference when protecting the building.
Consider the foundation of a building. As a construction professional, you know that the foundation is the core of an amazing structure, yet we collectively have a tendency to avoid spending much time on the foundation when designing and constructing buildings. Part of the issue is that foundations are seldom the most glamorous parts of a building. Below-ground levels, whether building basements, parking garages or otherwise, sometimes suffer from an “out of sight, out of mind” mentality when buildings are being designed, yet the quality of their construction could not be more important to building longevity.
Failure to pay adequate attention to below-ground levels when designing a building can lead to significant problems. If the design, installation and inspections of foundations/basements are ignored, or if below-grade waterproofing (i.e., waterproofing below ground level) is not installed or is inappropriately installed, this can lead to serious negative impact on the building lifespan and performance.
Repair or remediation work can be very expensive when leaks are found in below-grade waterproofing. In some cases, repairs may not even be possible given that the cause of leaks could be literally buried and difficult to access. As a result, if you want to avoid future expensive fixes, it is worth your time to focus up front on mitigating the potential for migration of moisture in the foundation of a building.
The following sections of this article will cover the finer points of below-grade waterproofing, including the environmental forces that create the need for below-grade waterproofing, the design and decision-making process that should be followed, installation challenges and also what happens when there are failures with below-grade waterproofing systems.
Understanding the Science Behind Below-Grade Waterproofing
Environmental Forces
There are three major environmental forces that we must contend with to avoid unwanted moisture infiltration: hydrostatic pressure, capillary action and the water table.
Hydrostatic pressure is pressure exerted by a stationary liquid in all directions against adjacent surfaces. Water exerts 0.43 psi of pressure for every foot of water present, and this pressure increases with depth and seasonal rainfall levels.
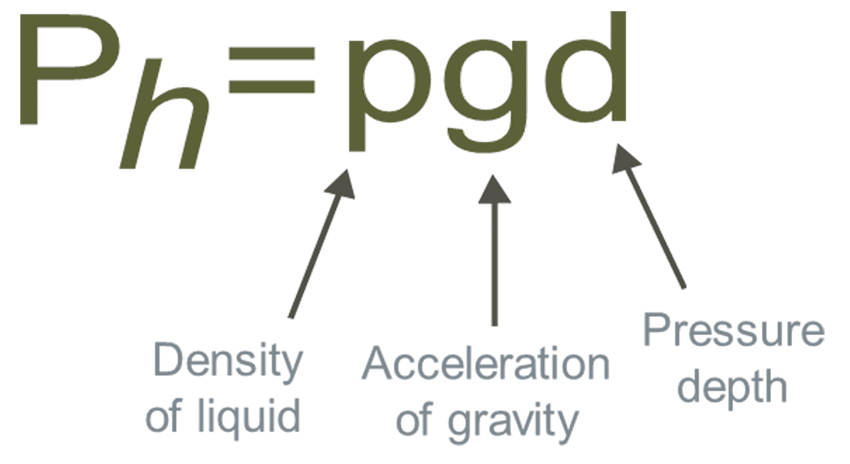
Hydrostatic pressure is determined by multiplying liquid density by gravitational force by depth-related pressure.
As this equation shows, hydrostatic pressure is determined by multiplying liquid density by gravitational force by depth-related pressure. Think about what happens when you dive to the bottom of a pool, or better yet, picture what happens to a submarine as it dives. You feel more pressure exerted upon you the deeper you dive, and the same happens to the submarine’s hull on a more intense level. If you’ve experienced this phenomenon, you’ve experienced hydrostatic pressure.
Foundations below the groundwater line, often called the water table, are subjected to hydrostatic pressure. This pressure from the force of the water-saturated soil can occur against vertical foundation walls as well as under-the-floor slabs.
Hydrostatic pressure creates two difficulties:
- It puts additional loads on the structural elements
- It makes waterproofing more difficult as the pressure tends to force water into any crack or imperfection in the structure
Capillary action is the second environmental force of which you should be aware. Capillary action (sometimes denoted as “capillarity,” “capillary motion” or “wicking”) refers to the ability of water to flow in narrow spaces without the assistance of—and in the opposite direction of—gravity due to hydrostatic pressure.
Capillary action will vary by soil types. For example, water will rise in all soils except gravel and can rise as much as 6 feet above the water table in clay and silt. But why does capillary action matter for your building? Consider this example.
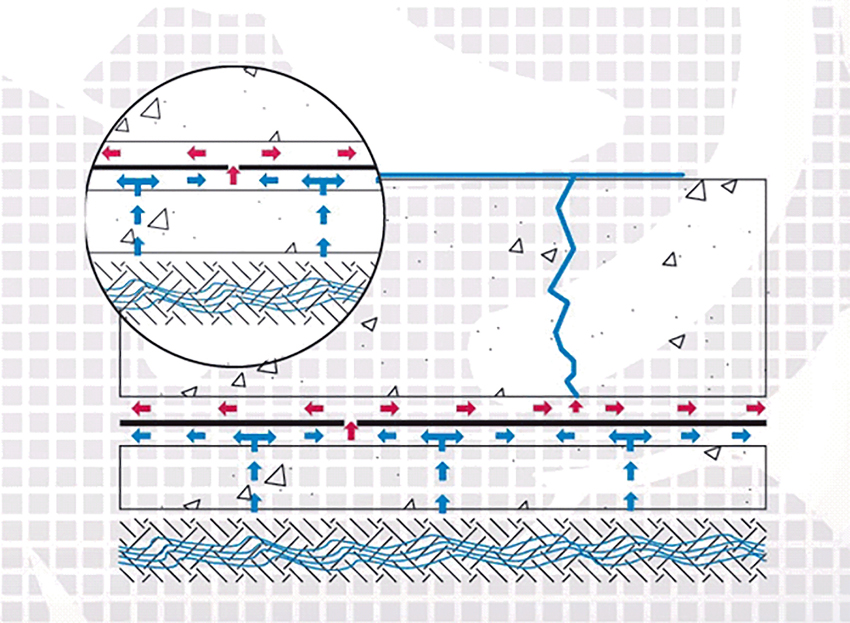
Water migrating into and through a foundation from water saturated soil can cause the structure to become vulnerable with expensive repairs.
The image above shows how capillary action affects the migration of water through a slab foundation. Hydrostatic pressure can force the migration of water through any punctures or gaps in the membrane ultimately leading to water infiltration inside the building. It is also worth noting that additional construction in nearby locations can affect the water table, i.e., the level below which the ground becomes saturated with water. As a result, the hydrostatic pressure exerted on your building could change, subsequently affecting the capillary action within your building materials.
Now that we have established the ground moisture-related environmental forces affecting your building, it is time to cover how these forces should impact your waterproofing-related design decisions.
Design & Decisions
You have choices in how you protect your foundations. First and foremost, you need to decide whether you are dampproofing or waterproofing.
In the context of below-grade protection, dampproofing refers to treating a surface to resist the passage of moisture in the absence of hydrostatic conditions (e.g., if your surface is above the water table). Waterproofing, alternatively, refers to treating a surface to prevent the passage of water under hydrostatic conditions.
Note that dampproofing is not a substitute for waterproofing if there’s a realistic chance of hydrostatic conditions forming. For the sake of this article, we will focus primarily on waterproofing materials and methods.
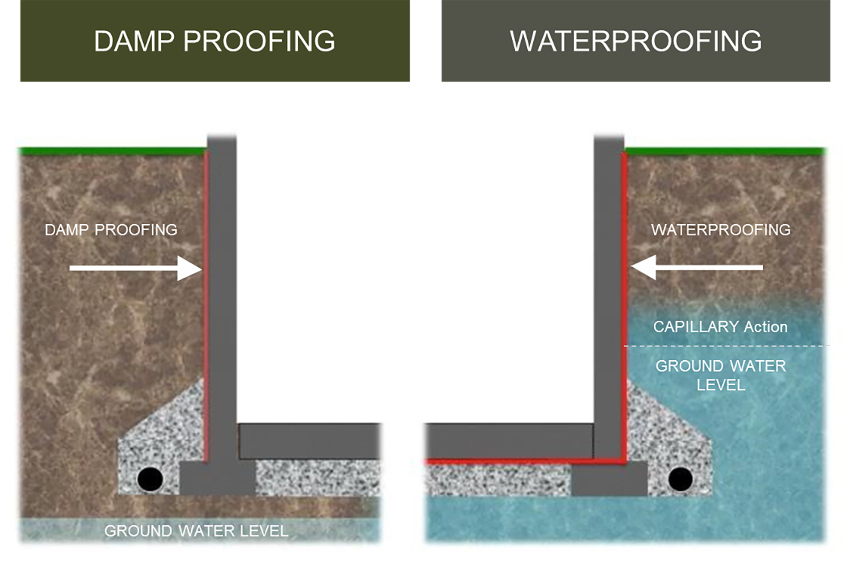
When working at or below the ground water level, waterproofing must take the place of damp proofing.
This visual highlights the difference between dampproofing and waterproofing. It shows us that when you are working within range of the water table (where the ground water level is above the waterproofing or structure level), you need to have a waterproofing material that can handle those hydrostatic conditions that the water table creates.
There are a few ways to go about below-grade waterproofing design. First, there is positive-side waterproofing, which consists of installing a waterproofing membrane/layer between the substrate you are protecting and the source of water. This type of application is commonly referred to as exterior side waterproofing, as the waterproofing materials are applied to the outside of the building.
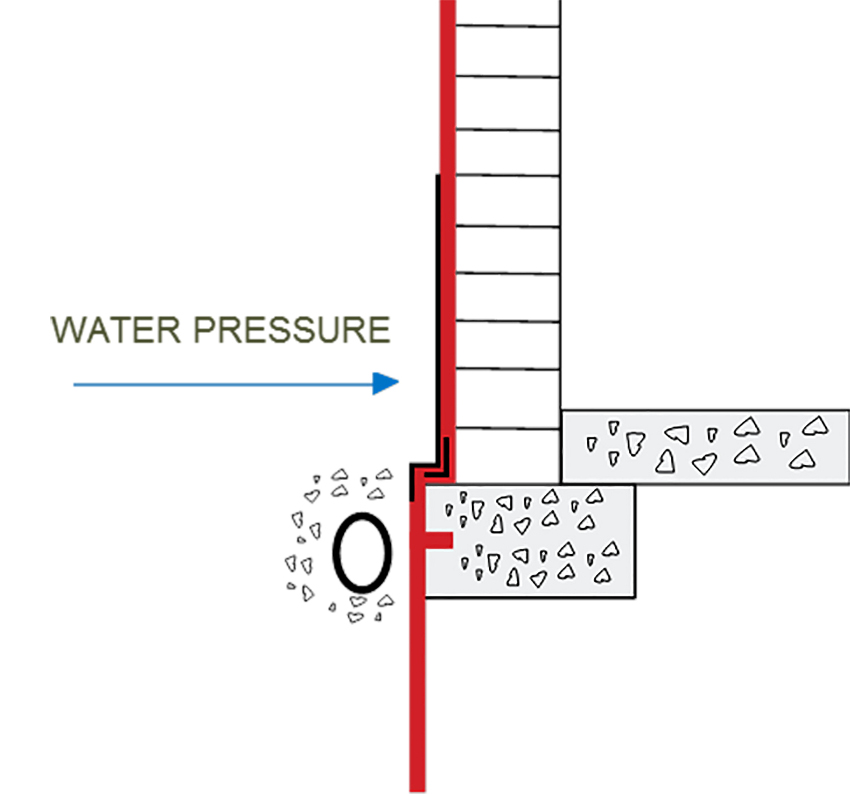
Waterproofing materials are placed on the outside of the building to block the supply of water in positive-side waterproofing.
Positive-side waterproofing is generally seen as the least problematic option to pursue and tends to be the most successful, since it keeps water out and is actually benefitted by the external water pressure forcing it to work. It also allows the design team to inspect all lap joints and defects with full visibility. The biggest drawback, however, is that once areas have been filled in with earth around the foundation, post-backfill inspection is not possible. If leaks occur due to building movement or faulty installation, repairs can only be made via excavation or interior retrofits.
There are a variety of systems that can be employed for positive-side waterproofing, including:
- Prefabricated membrane systems
- Modified bitumen sheets
- Elastomeric sheets
- Thermoplastic sheets
- Liquid-applied membrane systems
- Cold liquid-applied
- Single component
- Multi component
- Hot liquid-applied
- Mineral-based system
- Bentonite clay
- Crystalline
The prefabricated membrane systems are typically self-adhered, post-applied products (applied after the structure is put in place), but in some cases can be preapplied (or blindside) products—a term we will cover in more depth shortly. Liquid systems are typically post-applied, and mineral-based systems are typically preapplied.
On most projects, below-grade waterproofing is applied after the foundation walls have been poured. On some projects, however, this simply is not possible. That’s where blindside waterproofing comes in.
Blindside waterproofing systems are required when the exterior faces of the foundation walls are inaccessible but a desire to apply positive-side waterproofing is present. The name “blindside” comes from the fact that blindside waterproofing is often attached to an adjacent structure or soil-retention wall rather than the new structure’s wall, and the finished product cannot be seen after installation. These systems are applied prior to the final structure placement, and thus blindside waterproofing is often also referred to as preapplied waterproofing. Although blindside waterproofing is still technically a positive-side application, as it is installed on the outside of the structure, the protection/drainage and waterproofing layers of the assembly are installed before the concrete structure is poured with this type of system.
A common situation dictating blindside waterproofing would be when the proximity of adjacent property lines in “zero lot line” scenarios preclude excavation outside of foundation walls. Picture a densely built-up city block, for instance. Blindside waterproofing is also used in pits—think about elevator pits and tunnels. We also see blindside waterproofing in split- or mud-slab horizontal applications when products are waterproofing the underside of the structural slab. In all of these cases, the common factor is lack of accessibility. When you do not have the capability to access the structure to waterproof it after it is in place, the waterproofing can only be preapplied.
The graphic shown below depicts the difference between positive-side and blindside waterproofing installation. As you can see on the left side of the graphic, a wider excavation zone allowed for positive-side waterproofing installation on the outside of the already-poured foundation. On the right, however, the proximity of the already-built environment around the excavation site meant the blindside waterproofing layer had to be installed first, and the pouring of the foundation will come as a next step.
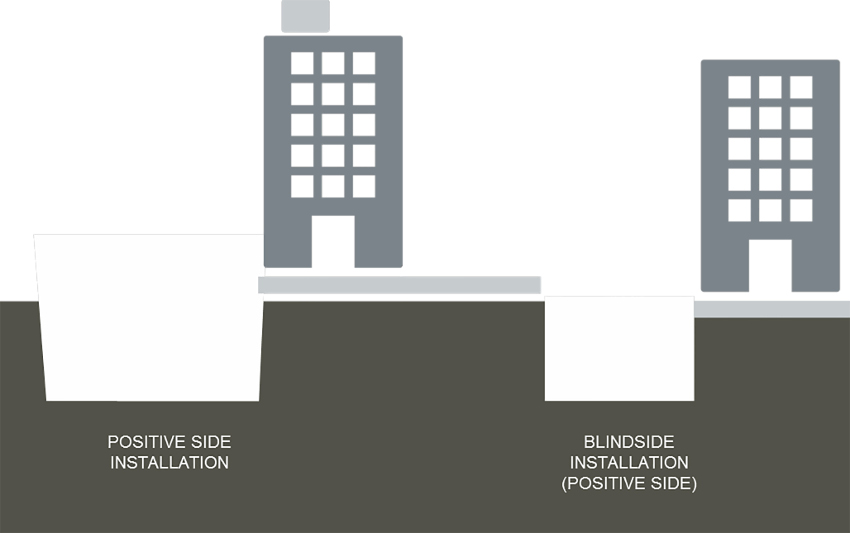
When outside factors prevent adequate excavation to allow installation of waterproofing layers on the exterior of a foundation, it may be necessary to install the waterproofing layer before the foundation is poured via blindside waterproofing.
As is the case with positive-side waterproofing, there are a variety of materials used in blindside waterproofing, including:
- Bentonite sheets
- Styrene Butadiene Styrene (SBS)-modified bitumen membranes
- Polyvinyl Chloride (PVC) membranes
- High-Density Polyethylene (HDPE) membranes
- Hybrid membranes
Bentonite sheets have been historically popular in blindside applications, but other materials often prove to be better options depending on specifics of the application. All these materials listed above differ in chemical composition and therefore have different physical properties. Some of these materials are more affected by outside factors than others. For example, a modified bitumen system will not be adversely affected by inclement weather or shotcrete applications, whereas bentonite and HDPE systems will. HDPE, for example, can be adversely affected by overexposure to UV rays, and bentonite can be damaged by exposure to even light precipitation.
When choosing materials, keep in mind that some of the key performance properties to analyze for any blindside waterproofing system are adhesion to poured concrete, puncture -resistance and resistance to lateral water migration.
As you might imagine, blindside waterproofing is considerably more complex than the regular way of doing things, but sometimes it’s the easiest—or only—way to get it done. This does not mean blindside waterproofing is explicitly relegated to being chosen as a last resort. In some cases, blindside waterproofing can substantially reduce the area of a jobsite that must be disturbed to waterproof a foundation, and it can reduce the overall developed footprint of the building. Due to its ability to decrease the amount of excavation required and thus minimize site disturbance, choosing blindside waterproofing can help with progress toward environmental accreditations, achieving LEED prerequisites or Sustainable Sites–site development credits. Whether these accreditations are of interest or not, blindside waterproofing may also be of interest if the landholders wish to preserve existing wildlife habitats/plant life or otherwise maintain the grounds.
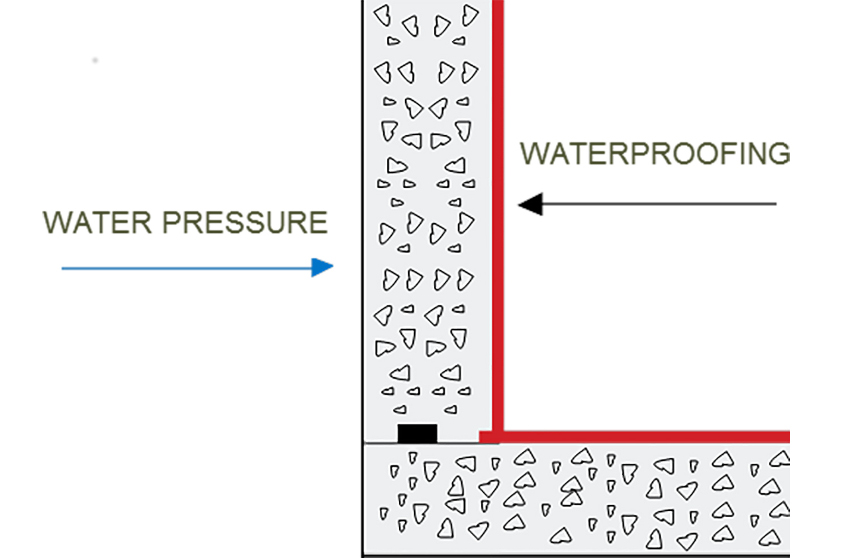
With negative-side waterproofing, membranes are installed on the interior side of the wall, preventing moisture from penetrating inside the space, but potentially allowing damage within the wall.
There is one additional form of below-grade waterproofing to know, as well: negative-side waterproofing. As you might guess from the name, negative-side waterproofing protects the surface opposite the side of applied hydrostatic pressure (e.g., the inside of a basement wall). Negative-side waterproofing keeps water from entering an occupied space and is applied to what is known as the dry face. Negative-side waterproofing is primarily used for water-holding purposes (preventing water from entering a space), but it does not prevent the water from entering the substrate (wall).
The main advantage of negative-side waterproofing is that it is accessible after installation for repairs or updates. Also, since the negative (interior) side of walls tends to be more accessible, it is easier to identify leak locations than with positive-side systems.
The fact that negative-side waterproofing allows moisture into the substrate is generally seen as a disadvantage, however. While moisture promotes active curing of the concrete substrate, it also contributes to the corrosion of the concrete and steel reinforcements from the groundwater and chemicals. The constant presence of moisture can also lead to mold growth or damage to interrelated building elements like floors or windows. This type of membrane does not protect against the effects of the freeze-thaw cycle and can only be used on cementitious systems. Additionally, if the building moves or cracks over time, additional negative-side waterproofing products may need to be added to close new gaps.
The materials used for negative-side waterproofing must be able to withstand hydrostatic pressure. Prefabricated membrane systems are typically installed in negative-side waterproofing applications via epoxy or urethane injections, cementitious coatings, metallic mineral application or crystalline application.
Since the goal of waterproofing is to protect both structures and the content within, but negative-side waterproofing does not necessarily protect the structure itself, negative-side waterproofing should generally be looked at as a temporary solution or problem-solving method that is mainly considered only if the positive-side waterproofing has failed or could not feasibly be installed in the first place.
Water Management & Protection
Keeping water out is one challenge; managing water and protecting newly installed below-grade waterproofing assemblies is another. This is why we also install protective layers, drainage layers and waterstops.
Protective layers, as their name implies, protect below-grade membranes from damage. This damage can either occur from backfill or consecutive trades. Depending on the membrane, common materials used in protective layers include insulation, asphaltic boards or an additional layer of HDPE. In some cases, layers serve dual purposes, such as insulation and drainage layers.
Drainage layers, alternatively, assist in the relief of hydrostatic head pressure and prolong the membrane life. Proper design means having the least possible amount of water reach the membrane, and water management is highly recommended in all below-grade assemblies. These panels are typically impact-resistant, dimpled plastic attached to a woven geotextile fabric, and they channel water away from the membrane.
Almost all below-grade waterproofing projects will have either a protection layer (board) to protect against possible damage from backfill operations or a drainage solution to manage the water away from the waterproofing membrane. Some drainage solutions can protect both the membrane and manage the water.
Waterstops provide a final level of protection for the building, existing within concrete sections, especially joints. These premanufactured joint seals are often comprised of PVC or chloroprene rubber that must be fused together, bentonite clay that expands when wet or hydrophobic injectable expanding grouts.
Causes of Waterproofing Failure
As is often the case with construction quality, the “devil is in the details” when it comes to effective below-grade waterproofing. It does not matter how great a waterproofing product is if it is not installed correctly—it can instantly perform worse than the worst waterproofing product in the world.
Improper Flashing & Detailing
Gaps in the integrity of the waterproofing due to incorrect detailing or damage from other trades are a leading cause for failure. The picture on the next page shows one example: rather than use the proper installation techniques, the contractors took it upon themselves to assure this elevator pit’s preapplied waterproofing was snug to the forms by using a staple gun to shoot staples through the modified bitumen membrane and into the wood forms. This created approximately 30 penetrations through the membrane that had to be detailed properly after the staples were removed (which you can see on the right). The correct repair procedure in this case was a patch over all the holes once the staples were removed … which added up to out-of-scope costs in excess of $10,000 once labor and materials were factored in.
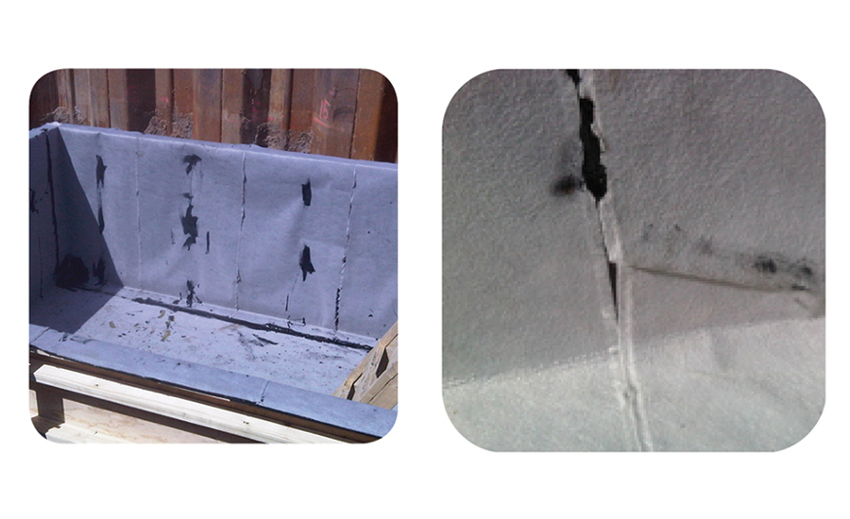
Improper installation techniques can add up to costly fixes that are not within the original scope of projects.
Substrate Preparation & Damage
Substrate preparation, in general, is key to the success of any waterproofing system. If the substrate isn’t adequately prepared, the correct application of the waterproofing system is next to impossible. In the picture below, the substrate was inadequately prepared, and the hot fluid applied system exhibited an adhesive bond failure.
Beyond preparation, issues with the substrate itself (such as cracked masonry) can lead to failure. You might wonder why anyone would attempt to apply waterproofing materials to a failing substrate, but unfortunately it does happen. In these cases, team members should always be notified of unsatisfactory substrate conditions.
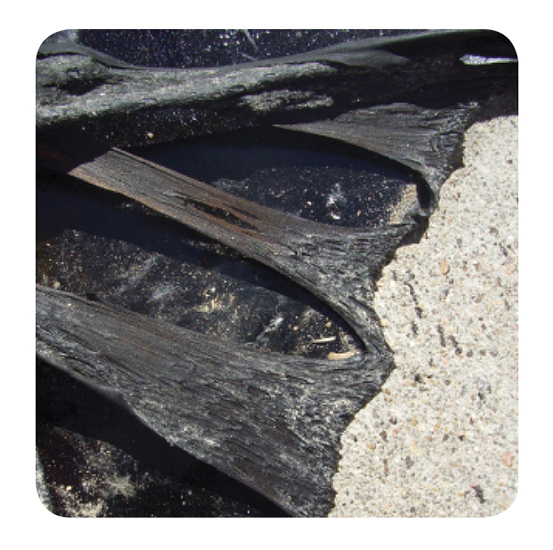
Improper substrate preparation can lead to loss of adhesion during assembly.
Incompatible Materials
On any given below-grade waterproofing project, there will be various materials that will come into contact with each other. Assuring that these materials are “compatible” is essential to the success of the overall waterproofing. Be careful because the term “compatible” may have different definitions depending on whom you ask … answers of “Sure?,” “It will stick; don’t worry,” and “I don’t know,” are far too common. It is safe to assume that it is nearly impossible to make a statement about the compatibility of materials without first determining the function of the interactions between these materials.
Material Storage & Installation Conditions
As covered previously, there are various materials available for waterproofing applications. Each of these materials will have different restrictions and guidelines related to storage and application conditions. For example, a modified bitumen-based sheet will be less affected by low temperature conditions when compared to a water-based spray-applied product.
It is not uncommon to see materials become negatively affected when left improperly exposed. Whether or not a material can be brought back to a functional state after an event like this all depends on the material being used—you should always rely on the manufacturer’s requirements and recommendations. As a rule, if a pail of viscous material has polymerized or reacted, do not plan on using it. Polymerization is a chemical reaction in which two or more small molecules combine to form larger molecules that contain repeating structural units of the original molecules, and once this level of change has taken place, it is unlikely your material will be usable.
Keys to Success
As you have likely noticed, many of the leading causes of waterproofing failure are related to mistakes during installation, so Rule #1 for a successful installation is to follow best practices/directions precisely. Beyond this, also abide by the rules of good project design.
Good Initial Design
A good initial design begins with good communication between all team members. All involved team members need to be on the same page before and during the project to ensure a successful outcome. Waterproofing needs to be considered at the front-end of any building construction project—in the design phase of a project. Designers and architects should consult with waterproofing manufacturers and contractors during the design phase to ensure that all requirements are fulfilled. Many major problems with projects can be traced back to parties failing to talk with one another or pre-construction meetings not being scheduled properly, so take special care to avoid potential oversights early on.
When selecting a system design and what materials you will use for the project, there are a number of questions worth asking yourself in order to make an informed decision. Consider, for instance:
- What sort of site conditions exist? If a building site is right up against a property line, or there is no way to carry out positive-side waterproofing due to existing structures or other obstacles, you may know right away that a blindside waterproofing installation is your best bet.
- What are the soil conditions? At the start of a below-grade waterproofing project, a soil analysis needs to be conducted to help determine what type of waterproofing material will perform best in the given environment. Contaminated soil conditions may also limit your options. For example, contaminated ground water can turn sodium bentonite into less desirable calcium bentonite, effectively changing the properties of that waterproofing option. Sodium bentonite swells about 16 times its original volume whereas calcium bentonite will swell only about 5 times its original volume. Since the functionality of bentonite waterproofing is based on its ability to swell and seal, this makes a significant performance difference.
- What temperature limitations exist? Many waterproofing products—especially those requiring sealants, solvents or adhesives—become difficult to install in cold temperatures (below 40 degrees Fahrenheit or 4 degrees Celsius), meaning your material choice may be limited by your environment. Consult manufacturer-provided directions to know what sort of installation and storage limits exist.
- What is the hydrostatic pressure at the location? Different products have different tensile strengths, and the amount of pressure that must be withstood could affect your design. For instance, bentonite products and elastomeric sheets are more likely to withstand high hydrostatic pressure than fluid-applied systems or self- adhered membranes.
- What sort of drainage is there? Different waterproofing materials and applications lend themselves to different drainage designs, but regardless of the choices you make, some sort of drainage will need to be developed adjacent to membranes to efficiently remove water from surfaces.
- What will construction sequencing look like? Consider factors such as work benching (as you will need durable materials that can hold up to the abuse of consecutive trades), clear detail sequencing (to allow for a proper installation by contractors) and scheduling (as some products may not be able to cope with unforeseen project delays or weather conditions during certain times of the year).
- Are all applicable materials compatible? As discussed earlier, there are a lot of ways to describe compatibility, yet if several different types of waterproofing are to interact, compatibility at tie-ins and other intersecting locations must be properly defined and confirmed. If literature is not immediately available or you find yourself questioning compatibility, your best bet is to contact material manufacturers and ask.
- What are the code requirements? Local organizations approve certain products for certain types of projects. Codes that require a waterproofing membrane usually define the minimum required waterproofing system and give guidance around options for bridging nonstructural cracks. As a result, it is important to understand the code requirements for the project’s geographic location to ensure that the product specified meets all requirements.
- How much do you expect the building to move? Over time, and even by design, every building moves. This movement must be accounted for in the design phase, and waterproofing materials need to be selected to accommodate this movement through both material properties and adequate details. It is hard to predict where cracks will develop due to shifting structures, but pay special attention to any existing penetrations and construction joints when detailing, as these are the areas most likely to develop leaks when movement does occur.
- What will be the primary function of the building? The intended use of a building needs to be considered when choosing waterproofing systems. The approach may differ when waterproofing a museum versus a parking garage, for example. You should consider level of disruption installations could cause, the sensitivity of the contents of the building being waterproofed and how difficult repairs could be down the line depending on the type of system you select.
Strong Manufacturer Support
While there are often several factors that may cause a deviation from the original material selection for a project, and these factors are sometimes out of your control, you should never compromise on the right material for the job. Even after the design team identifies the right material for the project, economic reasons and warranty wars can alter that material selection—all performance characteristics aside.
It is not uncommon for a manufacturer to attempt to substitute their products on a project using the warranty as leverage, for instance, consider what happens to the warranty if that manufacturer goes bankrupt. Keep in mind that a proven track record is important. Companies often emerge touting the next revolutionary product that will never fail, but there is no substitute for a proven track record of success. Do your research not only on products, but also the companies offering them before making any choices for the best chance at success. Keep in mind that proper design inspection is crucial to system success, regardless of warranties.
Also, always assure both the installation and storage instructions are clear and appropriate to the project. It happens all too often that conflicting information can be found from a manufacturer, and this can jeopardize a successful installation.
Quality of Workmanship
It is always recommended that designers work with qualified professional waterproofing contractors, starting in the design phase. Installers on waterproofing projects should be manufacturer-approved, meaning they went through the manufacturer’s application and product-specific training program, and they understand how and when to use specific waterproofing materials.
It is also crucial to assure the people that were trained within the contractor crew are actually the ones doing the work. This can be verified by training certificates or applicator cards issued by the manufacturer. Be sure that if there are multiple crews, they are communicating with one another and that there is awareness regarding what others are doing to elicit the best outcomes.
Summary
Remember that protecting a structure from the elements is about more than just which roof to choose—integral and continuous building protection should be implemented from top to bottom. Although the cost associated with the below-grade waterproofing may not seem like a significant expenditure in the overall scope of a new construction project, it is not an area that should be overlooked, as it plays a vital role in building envelope protection. Do your due diligence up front, be sure you are familiar with the particulars of the materials you will be using and think carefully through the proper design for the project, and you will be well on your way toward avoiding installation problems, waterproofing failures and (possibly very expensive) reworks later on.
Thomas G. Bauer is the Product Manager—Waterproofing & Wall Systems for SOPREMA, and focuses his time and effort on perfecting the performance of wall systems and foundations to manage air, water and moisture movement. He has 12 years of experience within the waterproofing bitumen industry and more than eight years of product management experience. Prior to working in the waterproofing industry, Thomas spent eight years in environmental manufacturing development.
![]() |
SOPREMA offers a comprehensive line of roofing, waterproofing, wall protection and civil engineering solutions combining superior products and systems with decades of proven performance. Our solutions include industry leading SBS-modified bitumen membranes, polymeric PMMA/PMA liquid applied membranes and synthetic single ply PVC membranes. www.soprema.us |