The Future of Fire-Rated Glass and Framing
A look at the top five innovations in fire-rated glass and framing, and how they are providing aesthetic and code-compliant design solutions
Continuing Education
Use the following learning objectives to focus your study while reading this month’s Continuing Education article.
Learning Objectives - After reading this article, you will be able to:
- Explain the differences between fire-protective and fire-resistive glass and framing.
- Describe five main innovations in fire-resistive glass and framing, and how they are expanding design freedom in areas with stringent fire and life safety code requirements.
- Discuss performance, fire-rated building codes and how innovative, fire-resistive glazing products can help meet more stringent codes, particularly NFPA testing standards and 2015 IBC.
- Identify misconceptions and potential misuse of fire-resistive glazing products, and discuss solutions to ensure maximum benefits.
From a purely aesthetic perspective, glass undeniably adds contemporary and sleek beauty to modern buildings—whether it’s a big city landscape of soaring high-rise towers or mixed-use spaces with generous windows bringing in natural light to its inhabitants. From offices and education facilities to medical centers and residential apartment complexes, glass has become the go-to choice for designers looking to create open, light-filled interiors and spectacular exteriors with high-design interest.
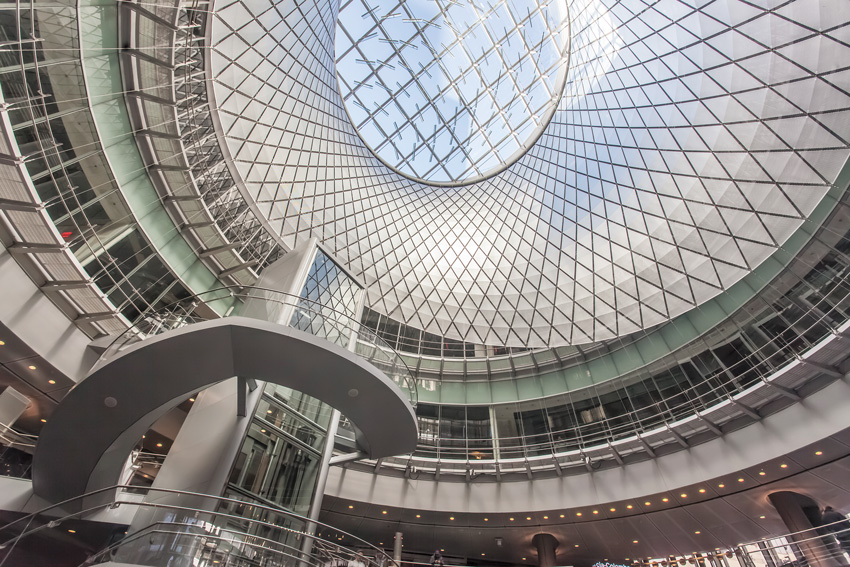
Photo courtesy of Technical Glass Products (TGP)
What is not as obvious to the casual observer, though, is the degree to which today’s sleeker and more sophisticated glazing assemblies can provide defense against fire. As new combinations of fire-rated glass and frames make their way to the market, design teams can navigate complex code and performance requirements and provide enhanced functionality alongside greater aesthetic appeal and versatility.
When specifying fire-rated glazing products, it is key to understand the differences between the terms fire protective and fire resistive (technically referred to as fire-protection rated and fire-resistance rated). “Fire protective” simply means the glazing defends against the spread of flames and smoke. “Fire resistive” glass provides the same defense against flames and smoke as fire-protective glazing, but it adds further protection by blocking the transfer of radiant and conductive heat.
This course will primarily focus on fire-resistive glass and framing, their performance, how they help meet stringent safety codes, and ways in which five of the latest innovations—narrow-profile fire-rated frames; versatile cover caps and finishes; structural silicone-glazed (SG) fire-rated curtain walls; butt-glazed fire-rated glass walls; and fire-rated glass floor systems—are changing the future of fire-rated glass and framing from both safety and aesthetic standpoints.
Understanding Fire-Rated Glazing Products: Fire Protective Versus Fire Resistive
The term “fire-rated glass” refers to the complete class of fire-rated glazing products available in the market. Within that wide category, designers can choose from both fire-protective and fire-resistive glazing products. Fire ratings for glass, which are noted on a product’s label, can range from 20 minutes to 3 hours, with the specified number corresponding to manufacturer testing (in accordance with national fire test standards).
How the National Fire Protection Association (NFPA) Testing Works
NFPA testing regulations specify a standard time-temperature curve. For the fire test itself, the standards must be carefully followed while a large furnace heats window frames or doors holding glass. In order to receive a particular rating, the assembly remains in the wall for the duration of the test; there can be no flaming on the exposed surface of the assembly or openings.
Additionally, glass must pass a mandatory hose stream test in which the glass and framing must remain intact. After heating the glass and framing components in a furnace, they are then sprayed with water from a fire hose. This evaluates such aspects as impact, erosion, and the cooling effects of water, as well as eliminating any inadequate materials or constructions that may fail under similar conditions. This test is a critical consideration since most modern buildings include fire sprinkler systems. It is, therefore, imperative to ensure the door or window assembly can withstand the stress and thermal shock levied by the hose stream. A failure of the hot glass would create unsafe conditions in that flames and smoke could spread throughout a building.
In the United States, the hose stream test is required for fire ratings in excess of 20 minutes (in Canada, all fire-rated glass products must pass the test). To earn a fire-resistive classification, glass and framing products must pass both tests, as well as meet temperature-rise criteria.
Fire protective: Fire-protective glazing means the glazing assembly defends against the spread of flames and smoke for its designated fire rating. Such materials include traditional wired glass, glass ceramics, and specially tempered glass. Fire-protective glazing typically is suitable where building codes allow “opening-protective” assemblies, including doors, sidelites, and windows. Such glazing is available with fire ratings ranging from 20 to 180 minutes, with varying impact safety ratings. Since it does not block the transfer of radiant and conductive heat, it is subject to area and size limitations under the applicable building code and/or authority having jurisdiction, specifically the International Building Code (IBC).
Fire resistive: Fire-resistive glazing provides the same defense against flames and smoke as fire-protective glazing, and adds further protection by blocking the transfer of radiant and conductive heat. It is tested to the stringent fire-resistance test standards for walls, including ASTM E119: Standard Test Methods for Fire Tests of Building Construction and Materials and Underwriters Laboratories (UL) 263: Fire-resistance Ratings. While numerous fire-rated building materials are capable of providing this extra safeguard, many are opaque, preventing people from viewing nearby hazards and restricting views within a building. Fire-resistive glazing can serve as a clear alternative.
The product is generally a multilaminate that incorporates several layers of glass with fire-resistive interlayers. The interlayers react during a fire to keep the temperature rise on the non-fire side of the glass below approximately 250 degrees Fahrenheit for the duration of its fire rating. This helps ensure people can safely pass through corridors, stairs, and other areas of egress during a fire. It also helps prevent rapid-fire buildup, which can be catastrophic in high-rise buildings, schools, and other facilities where large numbers of people may be present during a fire.
Given these performance benefits, fire-resistive glazing assemblies are typically suitable where building codes require an assembly designated “fire resistant” to enclose a space. Examples include wall applications requiring a 60-minute or greater fire rating that must meet temperature-rise criteria, such as stairwells, exit access corridors, or other fire barriers dividing interior construction. Due to its heat-blocking characteristics and classification as fire-resistive wall construction, it is not restricted to 25 percent of the wall area. This provides design teams with great flexibility when working to create light-filled and inviting spaces that meet strict fire and life safety criteria.
Where codes deem it necessary, fire-resistive glazing can also protect against the spread of fire between buildings. Its classification as nondirectional fire-resistive construction (meaning it can maintain the same fire rating from both sides) indicates that it can prevent a fire from traveling to or from neighboring buildings for its designated fire rating. Its transparent form allows it to do so without restricting visibility.
Value of Building with Fire-Resistive Glazing Products
Fire-resistive glazing systems have seen the most number of innovations in recent years. This is due in part because they meet the stringent temperature-rise criteria described above and also pass the test standards for fire-rated wall construction. The fact that they are not limited to 25 percent of the total wall area expands design use.
Additionally, in the last decade, manufacturing advances have given rise to new ways to retain fire-resistive glazing, giving professionals a wide degree of creative design freedom in meeting fire and life safety goals, and providing effective building compartmentation.
Trends and Improvements
Numerous fire-rated glass and framing industry advancements in recent years have set the stage for innovative solutions to be implemented. Before we look in depth at some of those key innovations, let’s take note of some of the trends and challenges that led to the need for those innovations.
- Improved optical quality of fire-rated glazing has stemmed from a transition from traditional wired fire-rated glass to clear fire-rated glass that matches the look of nonrated glazing. Fire-rated glass used to be wired (i.e., it had institutional wires in the glass). As such, the product was simply not as attractive as float glass and also had performance limitations. The wires help hold the glass together under high heat from building fires; however, they do not provide high impact resistance. Injuries can result from people breaking through the glass and getting snagged on the wires. Due to these concerns, the 2003 IBC prohibited traditional wired glass in hazardous locations (e.g., doors, sidelites, windows near the floor in schools, daycares, and athletic facilities). In 2006, the IBC extended this restriction to hazardous locations in all facilities. Over the past two decades, all fire-rated glass manufacturers have worked on creating new, clearer, larger, oversized fire-rated glazing that matches the aesthetic of nonrated glazing and provides critical impact safety.
- Fire-rated frame advances have included the transition from bulky, wraparound, hollow metal steel frames to narrow steel fire-rated frames. For inspiration, manufacturers started looking at how European manufacturers were using precision engineering—that is, taking long steel frames and rollforming them into tubes instead of sheets into very custom-tailored framing systems. Fire-rated frames developed in this way can be much narrower, have crisp edges, and vertical-to-horizontal framing joints without visible weld beads or fasteners. Advanced frames made with thermal insulation and isolation concepts can even earn fire-resistive classifications. So, now they are still fire-rated but also are slender and exceptionally strong due to the strength of steel material.
These improvements have given us stronger frames and larger, clearer fire-rated glass lites, allowing manufacturers to combine the two in a range of different applications in order to create innovative solutions critical to the industry.
For example, designers were once limited to smaller sequences of fire-rated glass, such as doors, sidelites, transoms, and windows. Now, with various fire-resistive glass options and slender, fire-resistive frames at their disposal, they can specify full-lite doors, walls, and floor assemblies, as well as glass installations that exceed 25 percent of the wall area. This includes sophisticated assemblies, such as fire-rated glass floor systems that use a fire-resistive steel framing grid with fire-resistive glass to serve as a code-approved fire barrier between floors and provide sufficient strength to support live, dead, dynamic, and seismic loads.
In addition, fire-resistive glazing products are now multifunctional, providing impact safety, bullet resistance, and even hurricane-resistance.
Five Innovations Changing the Future of Fire-Resistive Glass and Framing
While design professionals need to be aware of both fire-protective and fire-resistive product categories, as previously noted, many recent industry innovations have occurred within the fire-resistive arena as opposed to fire protective. This is due in part to the fact that fire-resistive products pass more codes and give designers more flexibility on the whole.
The following will highlight five innovative solutions in fire-resistive glass and framing systems, including case studies to illustrate each system type.
Narrow-Frame Profiles
Modern fire-rated frames have a slender profile and sleek aesthetic that allow for smooth visual integration with neighboring nonrated applications. Manufacturers are now able to apply thermal insulation and isolation concepts to these fenestration systems, creating narrow frames that earn fire-resistive classifications. When paired with fire-resistive glass, they allow for sophisticated, unlimited areas of glazing in fire separations.
As these innovative updates have taken hold in the industry, today’s fire-rated glass systems have been able to sideline a key design challenge that has traditionally vexed designers in areas requiring fire resistance: creating and maintaining visual harmony between fire-rated and non-fire-rated materials. As previously stated, historically, fire-rated glazing tended to have much thicker frames and glass in order to ensure the required fire protection. Although functional in blocking fire and keeping people safe, they lacked the sleek aesthetic commonly available with non-fire-rated frames. This created visual discrepancies with neighboring nonrated curtain walls, windows, and doors. Fortunately, the advancements we’ve seen in fire-rated frame manufacturing offer solutions to this design challenge. Steel fire-rated frames that are shaped in an extrusion-like process similar to that of other advanced steel frames feature sharp, crisp corners and narrow frame dimensions, enabling a visual match with surrounding applications.
The sleeker aesthetic of steel fire-rated frames is particularly beneficial when the fire-rated glazing is in a highly visible location and can be readily compared to other building elements, such as an expansive curtain wall in an entryway, lobby, or atrium. Crisp frame profiles can also increase internal viewing areas and accentuate the external appearance of modern curtain wall applications, which feature minimalist designs.
Taking integration one step further, some manufacturers are now offering SG fire-rated curtain walls. Such systems feature silicone-sealed glass that provides a smooth, frame-free exterior surface that visually ties with neighboring structural SG curtain wall systems (as discussed later in the course).
Whatever fire-rated frame is selected to match the aesthetic of nonrated systems, it is important to note fire-rated glass requires stiffer frame deflection criteria (under wind load) than nonrated glass. It can also weigh between 100 to 350 percent more than nonrated glass. As a result, design teams may need to increase the framing member size, or reinforce smaller profiles, to limit deflection. This is particularly important when designing fire-rated curtain walls for exterior applications. In instances where a larger profile may restrict the design intent, another viable option is to reinforce the profiles.
However, this can increase the cost of the framing. To aid in finding the best solution, fire-rated framing manufacturers are available to provide design assistance.
Frame Cover Caps and Finishes
In addition to specifying narrow fire-rated frames, designers can select from a wide array of versatile frame cover caps and finishes to help match fire-rated frames to nonrated frames used in other parts of the building. This means that architects can now more closely mirror the aesthetic of nonrated systems, providing greater design freedom. In terms of the appearance of fire-rated frames, there are ever-expanding opportunities for building teams to achieve virtually any look to complement non-fire-rated frames. This “match” can be accomplished in a number of ways, including:
Custom paints or powder coats: Frames can be custom painted, anodized, or powder coated to match nearly any color scheme. This includes the more traditional material matches like the silver color of aluminum to bold colors like purples and reds.
Materials and cover caps: Designers now have fire-rated frame options ranging from authentic hardwood to products with the look of stainless steel. For example, one popular finish option is durable stainless steel. It matches the bright, contemporary aesthetic of stainless steel used in other building finishes. Fire-rated frames are also available with custom aluminum cover caps for a cohesive look.
Shapes and sizes: The face caps are available in numerous shapes and sizes, from H and I shapes to custom configurations.
Alternatively, while achieving a seamless, complementary visual match between fire-rated and non-fire-rated elements is an important design goal, other building projects demand a way to differentiate designs through framing. This can be achieved through various options, including the installation of fire-rated glass and frames featuring custom corners and angles, which is one way to create a visual point of interest while working within the parameters of code-driven applications. Additionally, custom finishes (e.g., wet painting or powder coating carbon steel frames in a variety of colors) can be used to create a one-of-a-kind aesthetic and make a visual statement.
Silicone-Glazed (SG) Fire-Rated Curtain Wall Systems
Over the past decade, manufacturing advances have given rise to fire-rated curtain walls with narrow mullion profiles and large expanses of fire-rated glass. Yet, despite these developments, it remained challenging for designers to match the seamless aesthetic of structural SG curtain wall systems.
To achieve the functionality of a clean, uninterrupted exterior surface, manufacturers began producing fire-rated curtain walls that emulate the smooth, monolithic appearance of SG curtain walls. One available assembly is silicone sealed and requires no pressure plates or caps. Its patented toggle retention system anchors the glazed lites and becomes completely hidden once installed, creating an attractive frame-free look. The system is available with up to 120-minute fire ratings and can accommodate full-lite doors for a complete curtain wall entrance solution. Such silicone-glazed fire-rated curtain walls can satisfy life safety requirements without sacrificing transparency. In application, these sleek, high-performing fire-rated glass systems are ideal for architects with stringent design and life safety criteria in highly visible areas, including prominent entryways, lobbies, and corridors.
Butt-Glazed Systems
Over the past decade, manufacturing advances have created fire-rated glass wall panels with butt-glazed joints in a heat-resistive, fire-rated perimeter frame, providing yet another rung in the ladder of fire-rated glazing with aesthetics comparable to those of nonrated systems. These systems are unique in their ability to allow designers to more closely match the continuous glass wall aesthetic, which is widely seen in interior nonrated glazing applications. In fact, the sleek, monolithic look of these systems makes it almost impossible for the average occupant to visually discern that there are space subdivisions providing unparalleled fire safety.
One of the key ways that some manufacturers are able to reduce the width of vertical butt joints and create this sophisticated aesthetic is to use fire-resistive glass with a solid multilaminate glass makeup. This eliminates the need for internal spacers and edge sealants, resulting in butt joints as narrow as 5 millimeters (butt joints on current fire-rated systems are typically 41 millimeters or greater). It also allows the system to have virtually unobstructed transitions between adjoining pieces of fire-resistive glass. The result is longer spans of uninterrupted glass free of vertical mullions, and with improved views and enhanced light transmission.
To further enhance design flexibility, some manufacturers offer systems in which the perimeter of each butt-glazed elevation can be maintained by the fire-rated framing choice most conducive to meeting the designer’s specific project goals. This includes predetermined fire-resistive framing options from the manufacturer, as well as L-angle steel frames by others.
Overall, today’s butt-glazed fire-rated glass wall systems are a great choice for interior applications in fire-rated corridors, fire-rated stairwells, and other interior areas of egress where it is key not only to match the aesthetic of nearby nonrated systems but also to provide effective compartment divisions.
Fire-Rated Glass Floors
Gone are the days when architects and specifiers found themselves limited to concrete, gypsum, and masonry for code-approved fire barriers between floors. While these opaque materials technically get the job done, aesthetically, it’s a different story. By their very nature, these traditional materials limit views and light transfer through building levels. With recent manufacturing advances in fire-rated glass floors, however, design professionals now have an alternative.
Fire-rated glass floor systems can provide fire resistance while transmitting light deep into a building’s core. The innovative systems can provide a dramatic way to expand glazing in a host of building types. They can facilitate views and increase admissible daylight while supporting structural loads and blocking flames, smoke, and heat.
Design professionals can now specify fire-rated glass in a range of horizontal applications, including:
- non-egress floor applications requiring 60- to 90-minute fire ratings;
- egress floor applications requiring 2-hour fire ratings;
- glass punch-outs in fire-rated corridors; and
- atriums.
Current advanced fire-rated glass floor systems on the market typically have three main components:
- top-surface glass;
- a structural framing grid; and
- fire-resistive glass
Performance Criteria and Building Codes
While fire-rated glass systems can be a boon to aesthetics, the primary reason for their specification is always to improve fire and life safety and meet building-code criteria. Building codes outline where fire-rated materials are required and spell out the necessary performance criteria. However, since fire and life safety codes and best practices differ depending on factors such as building height, occupancy group, and the location in the building where a given fire-rated material is to be used, building industry professionals are left with significant room for variance as they work within the parameters set forward in codes. To further complicate the matter, codes are regularly updated but not always adopted on a uniform schedule across jurisdictions.
For architects, this can make it challenging to navigate increasingly complex building design and performance requirements in areas with stringent fire and life safety code criteria. There are a few key ways to address these concerns and guide appropriate specification, including understanding common misconceptions and proper use. The main criteria in this category is the 2015 IBC.
Understanding Proper Use and Misuse
Fire-rated glass that provides protection other than intended could jeopardize the safety of building occupants. A big issue is using mismatched fire-rated glass and framing components that compromise the effectiveness of the system.
For instance, fire-rated glass needs to be installed into an appropriately rated frame for the required protection level. As an example, if you’re working with an application where building codes mandate the use of 60-minute or greater fire-resistant materials, specifying 45-minute fire-protective glass would be a mismatch for the assembly’s required protection level. This disconnect can also put occupants at risk if the fire-rated glazing fails before the frame, which would allow flames and smoke to spread throughout the building.
There are a couple of steps that can be taken to avoid this scenario.
- Verify that the fire-rated glass, framing, seal, and other components have the same or greater ratings than the required code minimums for the opening.
- Confirm that the fire-rated glass and frame provide the same type of protection (i.e., fire protection or fire resistance). The easiest way to confirm consistent ratings and required levels of defense against fire is simply to check the product label. IBC requirements mandate that the fire-rated glass product labels clearly state where it is suitable for use and whether it meets temperature-rise criteria. Of course, if there are still questions after referring to the label, it is always good practice to confirm with the manufacturer or supplier.
When specifying fire-resistant glazing assemblies, for instance, curtain walls or fire-rated glass floor systems, here too it is imperative to confirm with the manufacturer or supplier that the performance of the glass and frame systems match, ensuring that they have been tested and listed to work together as an assembly. As a way to simplify this process, some manufacturers offer complete systems from a single source, where all the components are designed and tested in the same assembly, thereby removing any concerns about inconsistent fire ratings diminishing effectiveness and failure to meet required fire safety standards.
Proper Use
As with any complex system, advanced fire-rated glass systems must use the specific supplied components (e.g., glass, framing, exterior caps, back framing members, seals, firesafing, etc.) in order to work properly and maximize benefits. A change to any part of the assembly, whether to achieve a different aesthetic or to cut costs, creates a higher probability of compromising the system’s ability to provide the required level of fire protection and meet overall safety standards.
If the design professional truly needs to find a more custom solution than what is specified in the manufacturer’s guidelines, it is wise to contact the manufacturer or supplier during the design process. Some manufacturers, in fact, will provide design assistance and consult in the development and testing of custom fire-rated systems.
Conclusion
The unfortunate truth is that thousands of commercial building fires occur each year in the United States. However, with incredible innovations abounding in the fire-resistive product market and the embrace of advanced materials as we’ve discussed, providing code-compliant fire and life safety for these structures does not have to mean compromising on aesthetic or daylighting goals. One final thought: It is always good practice to contact manufacturers for the latest specifications and uses. With the continued evolution of fire safety solutions, new technologies are constantly moving the needle in the direction in which these products and systems can add value, beauty, and safety to commercial and institutional buildings.
![]() |
Technical Glass Products (TGP) is a recognized leader in the fire-rated glass and framing field, offering the FireLite® family of ceramic glazing, Pilkington Pyrostop® transparent wall panels, and Fireframes® fire-rated framing. The company provides AIA-registered continuing education, project consultation, product specifications, BIM models, CAD drawings, and rapid-response quoting.
|