Designing with Metal Ceilings
Creating functional and sustainable metal ceiling designs for commercial spaces involves thoughtful product selection and installation
Continuing Education
Use the following learning objectives to focus your study while reading this month’s Continuing Education article.
Learning Objectives - After reading this article, you will be able to:
- Identify metal ceiling systems’ typical components and configurations.
- Explain design considerations when selecting metal ceiling systems.
- Describe multiple performance, durability, safety, and sustainability attributes of metal ceiling systems.
- Recognize best practices in installing and maintaining metal ceiling systems.
Architects and designers enjoy the creative potential and customization of metal ceiling designs in commercial buildings. Not only do these ceiling systems conceal, but they also attract attention with dramatic designs and decorative flourishes.
These systems can be specified for both interior and exterior applications and incorporated into all projects from airport terminals and train stations, to shopping malls and casino floors, to office lobbies and hospital corridors, to school classrooms and college stadiums.
Metal ceiling systems meet rigorous performance requirements for acoustics, wind loads, humidity, fire, earthquakes and sustainability, as well as provide mechanical systems’ accessibility and low-maintenance reliability.
Contractors also appreciate these cost-competitive ceiling systems and their ease of installation, contributing to labor savings and on-time completion. The challenge can be in balancing all of the features and benefits to determine the optimal metal ceiling system for the project application.
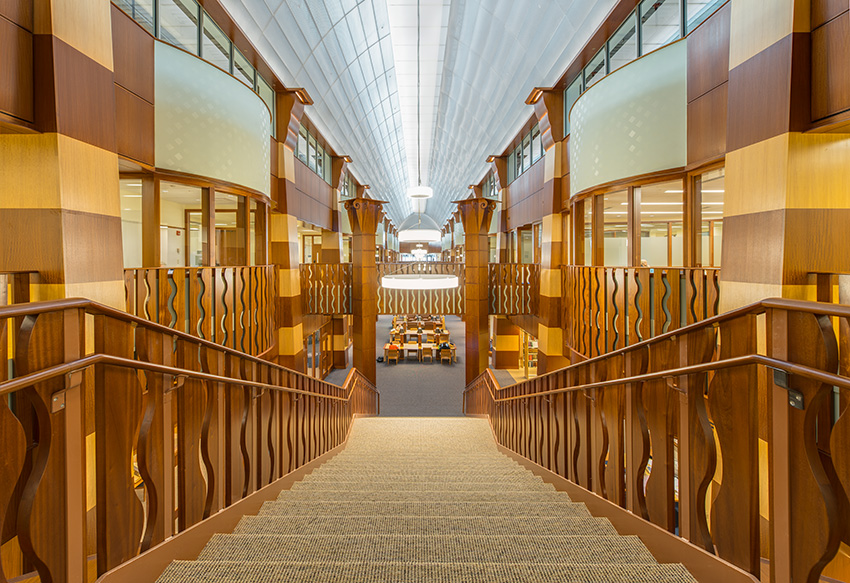
Photo courtesy of ROCKFON/Nathaniel Riley Photography
Quinnipiac School of Law features a torsion spring concealed metal panel ceiling system with Satin Silver finishes and increased acoustical performance.
Suspended Ceilings Components and Configurations
Designers in the 1950s were inspired to use “drop” ceilings in the large, open floor plans of the era. This became the preferred method for concealing HVAC, power and signal distribution equipment. The commonly called drop ceiling is better described in the commercial marketplace as a suspended ceiling. It hangs below the structural ceiling and is characterized by a suspension system of metal main runners and cross “tees” with panels placed within the system modules. The end result can resemble a tiled grid, which is why more casual references may call the suspension system a “grid” and panels “tiles.”
The main runners of the ceiling suspension system also provide direct support for the cross tees, air diffusers, lights and other devices, as well as the panels. The plenum is the space above the ceiling panels that conceals the HVAC air return, piping, wiring and/or ductwork.
Material Composition
Today’s commercial spaces feature suspended ceilings made from aluminum or steel with panels from a wide range of materials. Steel was the original material for modern suspension systems and continues to prove reliable for heavy-duty applications. Aluminum’s inherent corrosion resistance is suitable for both interior and exterior installations. Compared to steel, aluminum’s lighter weight also makes it the preference for many contractors.
Soft panel ceilings for interior applications commonly include gypsum, mineral fiber, fiberglass and stone wool. Gypsum is a soft sulfate mineral used in plaster, which can be shaped into panels. Mineral fiber is a mixture of fibers that may contain cellulose, paper and clay, which are shaped into panels using either a wet felt or cast process. Fiberglass is spun glass fibers, which are shaped into ceiling panels and given a decorative surface with a different material such as vinyl. Stone wool is primarily basalt, an abundantly available volcanic rock.
Hard ceiling panels, such as those made from wood and metal, are more durable than the soft options. Metal offers superior performance attributes and does not have the humidity and acclimatization requirements of wood. Tin and copper ceilings were the first metal ceilings introduced in the late 19th century. Compared with the elaborately decorated plaster ceilings of the 16th century, these pressed metal ceilings could be mass-produced at a fraction of the cost, and installed in a fraction of the time. Many historic tin ceiling patterns are still available today.
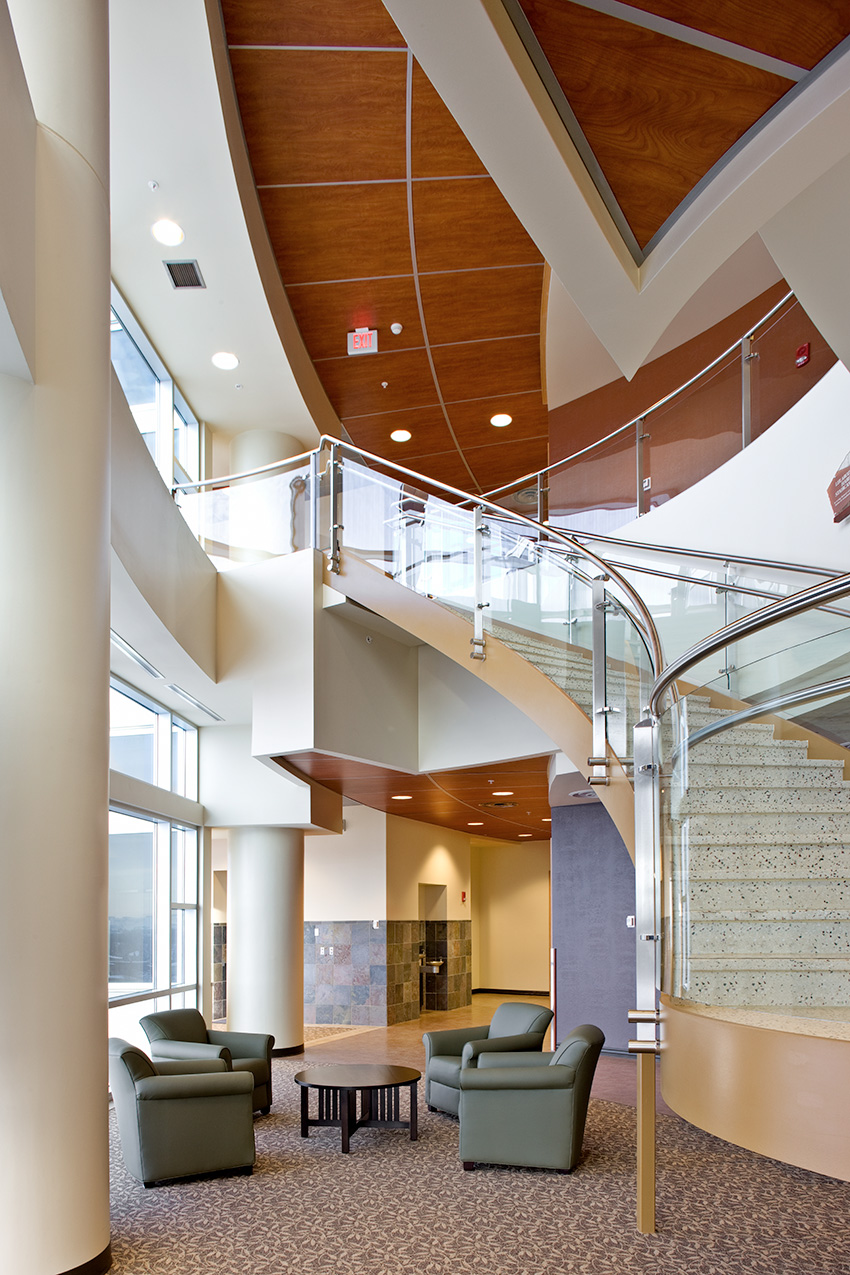
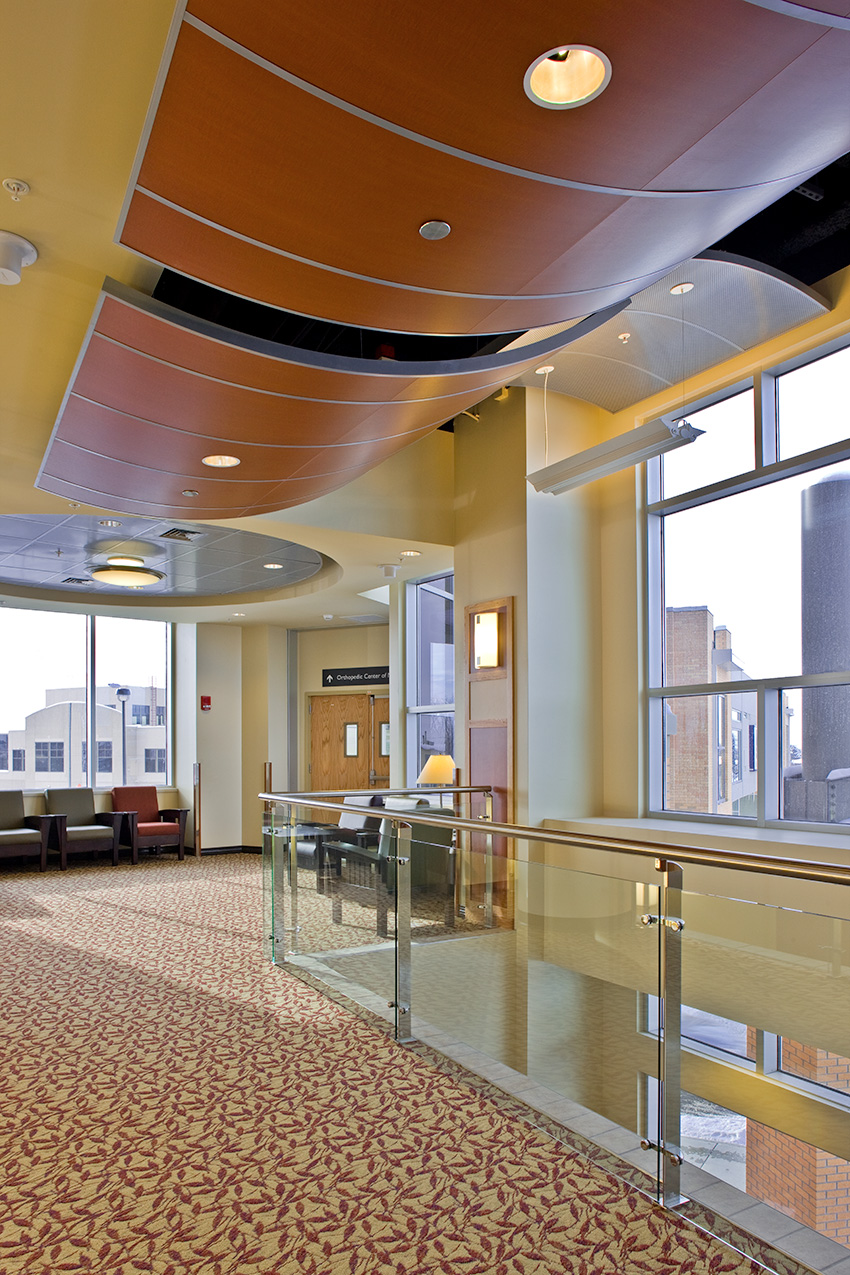
Photos courtesy of ROCKFON/J.K. Lawrence Photography
Benefis Health System’s snap-in metal plank and curved metal ceiling systems are finished to achieve the look of wood for a warm, comforting space, without the demanding maintenance of real wood.
The original pressed metal ceilings were the “nail-up” variety, meaning they were installed with nails over wooden furring strips. This method is still used today, and a “lay-in” metal panel style also was developed in the 1950s to interface with ceiling suspension systems.
From the mid-20th century to current times, metal ceiling panels are manufactured from durable steel and aluminum. A modern variation to the lay-in system is the “snap-up” system. This system hides the suspension grid, provides very tight joints, and can be specified to provide additional security.
Panels and Planks
Clip-in metal ceiling panels are easily removed and replaced into standard suspension systems, which can be helpful for spaces that must quickly adapt to changing décor and tenant needs. All clip-in panels are installed over a new or existing ceiling grid.
Hook-in and hook-on metal ceiling panels, as their names describe, are installed by hooking into specialty drywall suspension systems. Panels can be removed or replaced easily without tools to achieve downward access to the plenum.
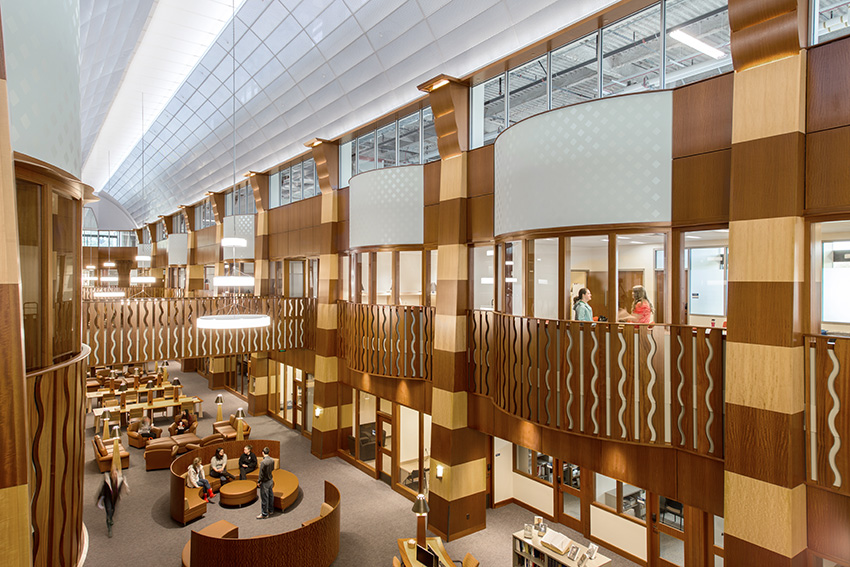
Photo courtesy of ROCKFON/Nathaniel Riley Photography
Torsion spring metal panels integrate seamlessly with factory-slotted suspension systems to provide a clean-monolithic concealed ceiling solution with ease of accessibility for Quinnipiac School of Law.
Also ideal for frequently accessed plenum areas, torsion spring panels allow maintenance staff access without taking the panel completely out of the ceiling. Torsion spring panels can be specified for flat or curved installations. Because of the strength of the connection to the grid system, this type of system can be effective in areas concerned with seismic activity.
Clip-in, hook-in, hook-on and torsion spring panels generally are fully accessible systems, where the plenum can be accessed at any point. This is almost always preferable to a point-accessible system where the plenum can be accessed only at specific locations, or to a progressive accessible system where panels and components must be removed in sequence until the desired point of access is reached.
Metal ceiling panels that have a length that is greater than two times their width, are called planks. They are used as design elements to cover large areas and provide accessibility. The decision of attachment styles is based largely on the frequency of access to the plenum. Ideal for large public spaces and as design features in offices, planks can be formed into custom shapes.
Linear Systems
To add design elements to commercial spaces’ ceilings, linear metal systems were developed in the 1960s. They typically are flat, but can be curved by using different suspension methods. The width is an aesthetic choice. Length is usually the main focus. Commonly, they are specified for long (linear) building applications, such as airport terminals and corridors. They may be used inside or outside, and can extend from the interior through to the exterior soffits. Many designers like the continuity this provides, particularly in highly transparent buildings with large glass openings.
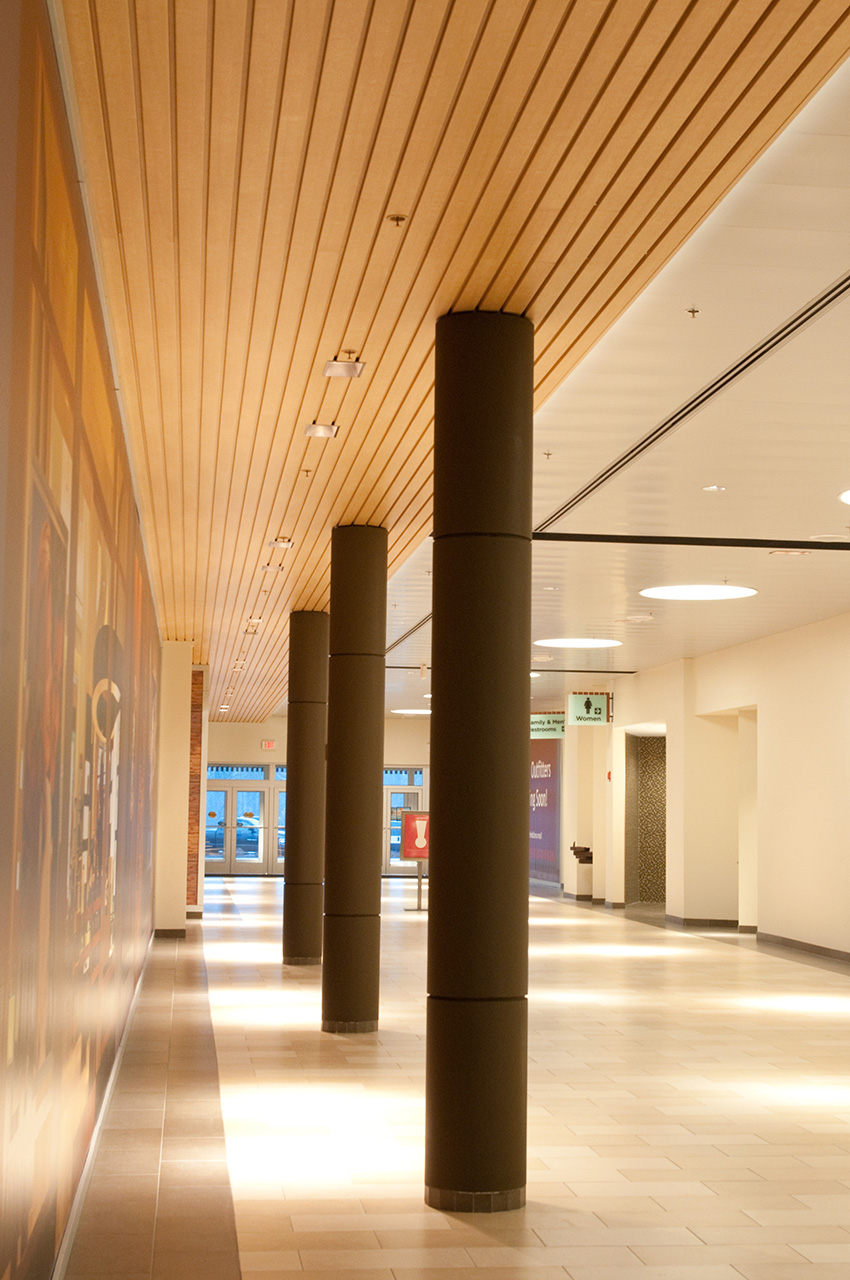
Photo courtesy of ROCKFON
Christiana Mall’s corridors showcase linear metal ceiling with wood-look painted finishes.
The spacing between the linear panels may be determined by numerous factors, balancing both form and function. If the space between the linear panels is to be closed, consider whether the “filler” should be integral to the panel or installed as an applied accessory item.
Open Plenum Systems
As the names suggests, open plenum refers to an application where the occupied space is not separated from the space above by a continuous ceiling. These include beam systems, open cell systems, plenum masks and baffle systems.
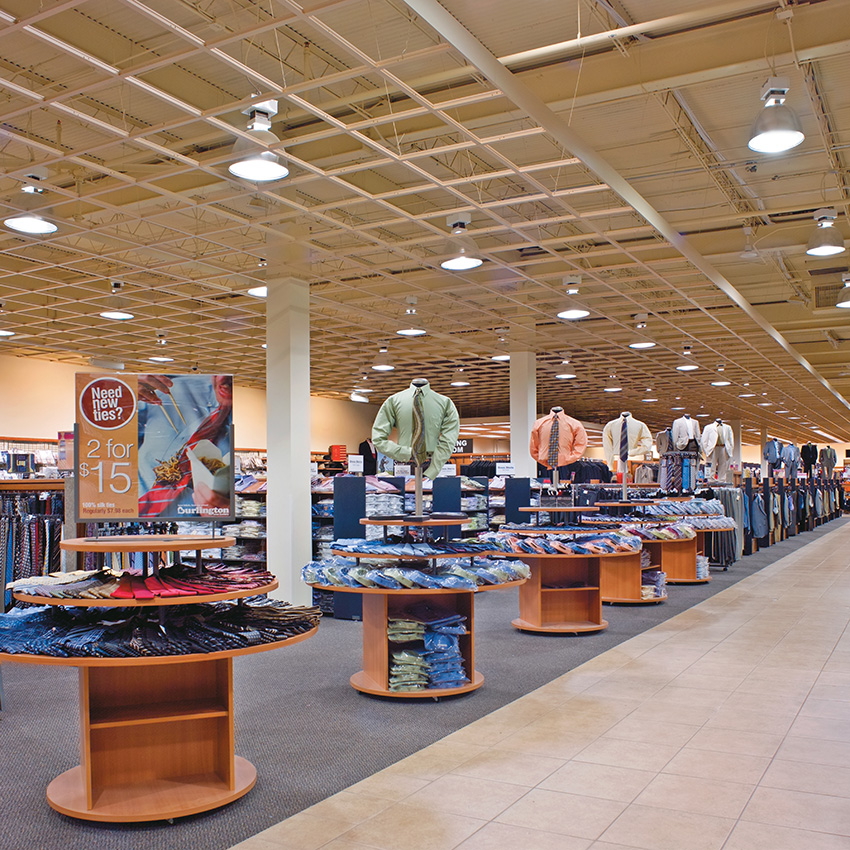
Photo courtesy of ROCKFON
Burlington shopping mall’s metal ceiling system presents a continuous, cubed, open cell appearance, and the ease of accessibility to the plenum for frequent changes in retail lighting.
Beam systems use deep sections to create large, open modules that allow completely free circulation of air and the creative placement of light fixtures and other features. They are effective in defining a ceiling plane without a solid ceiling, and letting displays define the space, such as in a retail center or showroom.
As subset of beam systems, open cell systems offer an inexpensive way to add a design element to open areas. These systems are created with standard ceiling suspension finished on all sides.
Plenum masks are used to provide an attractive way to block the view of the structure and mechanical systems above the ceiling from a casual viewing angle without impeding the movement of air. Depending on the ceiling height, the view is usually obstructed at a 45-degree viewing angle. For an industrial look, plenum masks with woven wire and expanded metal can be selected in carbon steel or stainless steel, unfinished or painted, and in a breadth of styles.
Plenum mask cell ceilings involve a grid suspension system with vertical-slat covers installed over the web of the grid to give a solid appearance. Once the web covers and cells are installed, the openings are much smaller. This provides the desired plenum masking while still allowing for the installation of standard services such as air and light diffusers, and security devices.
Another type of plenum mask is the baffle system, used to partially hide the structure above with a linear design element. Baffles give a space a very different look when viewed from different angles.
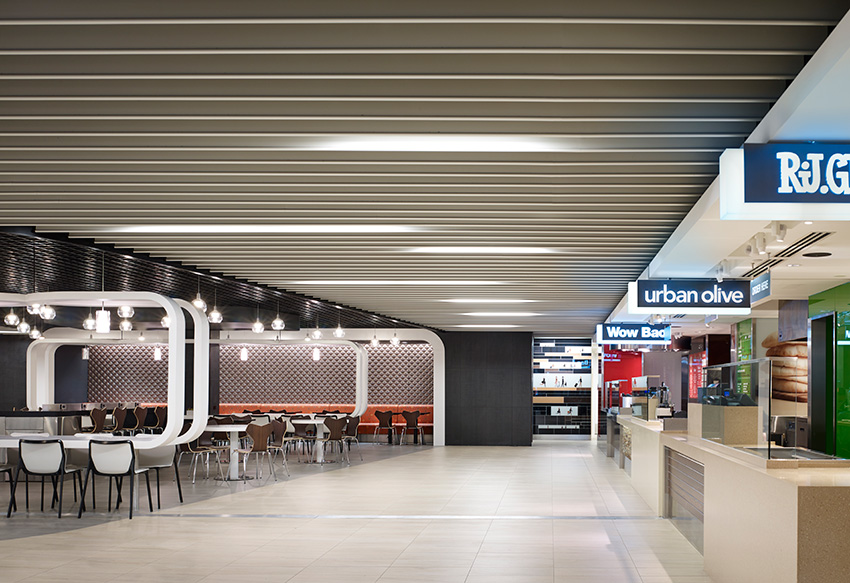
Photo courtesy of ROCKFON/Hedrich Blessing, courtesy of Epstein
O’Hare International Airport Terminal 5 in Chicago uses round base metal baffles to conceal the plenum, provide visual interest and enhance acoustics.
Curves and Clouds
Curved metal ceiling systems are most often used in open plenum ceiling applications. While several metal ceiling systems can be installed on a single dimension radius, other systems are specifically designed for curves. These are categorized as one- or two-directional curved systems and concealed curved systems. A two-directional system refers to a ceiling system that uses exposed curved main tees and cross-tees. A one-directional system uses exposed curved main tees, and concealed systems hide the suspension from view. Each curved system forms undulating ribbons. The peaks of the ribbon’s curvatures are commonly called vaults and the dips are called valleys.
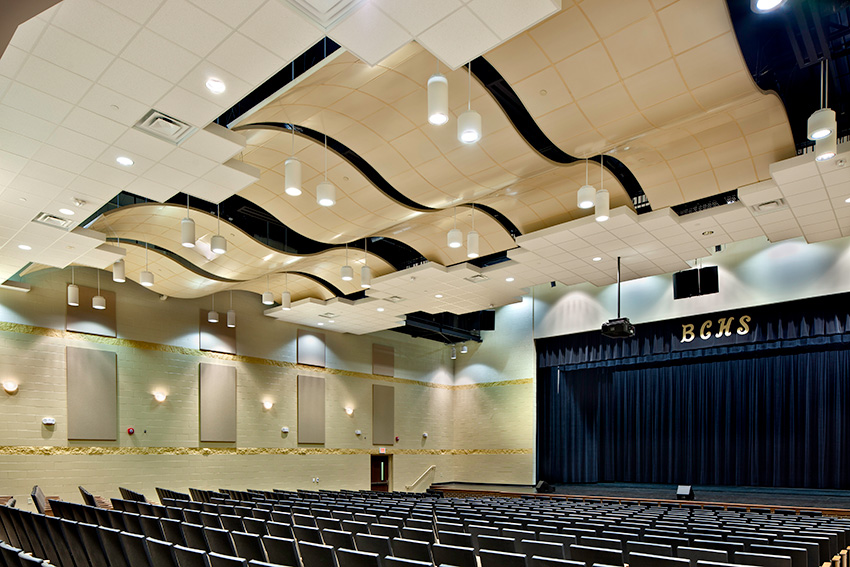
Photo courtesy of ROCKFON/Pepple Photography
Enhancing both acoustics and aesthetics, Bradley Central High School Fine Arts Center’s ceiling is composed of curved two-dimensional metal ceiling system with metal perimeter trim and suspension systems.
Creating a cloud-like design feature, ceiling suspension and panels can be assembled with perimeter trim into free-floating islands, suspended pods and other layouts. These clouds may be installed in combination with a traditional suspended ceiling system or as a separate element to provide acoustic performance enhancements or visual accents.
Design Considerations
From monolithic uniformity to dramatic accents, metal ceiling systems present a nearly unlimited menu of possibilities. Creative flexibility is found in understanding the choices available in suspension systems, sizes, shapes, perforations and finish options. Blending multiple systems and finishes can generate one-of-a-kind spaces that reflect the occupants’ brand and personal tastes.
Sizes and Edges
A ceiling’s visible grid can be minimized with a concealed suspension system, accentuated with an exposed wide-face system or recessed for a shadow effect using bolt-slot suspension with a center regress. The industry standard sizes for ceiling suspension systems have an exposed or concealed face of 9/16-inch, 15/16-inch or 13/8-inch. The wider the face, the bolder the expression of the ceiling grid modules appears. For high ceiling designs, a narrow face may appear seamless from the floor while a wider face will be more easily seen as a grid.
In open plenum ceiling systems, masking systems may be created using the standard 15/16-inch suspension to create 2-by-2-foot or 4-by-4-foot modules for a continuous, open cell ceiling. To convey the intimacy of a lowered ceiling that maintains openness, standard beam systems range from 1 to 6 inches wide by 1 to 8 inches high to create modules in sizes 1-by-1-foot to 4-by-4 feet.
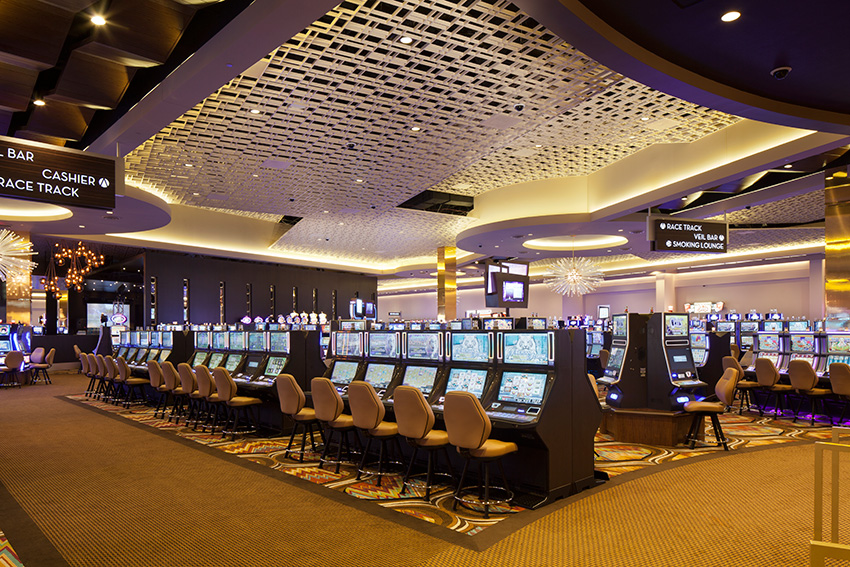
Photo courtesy of ROCKFON/Feinknopf Photography
Scioto Downs Casino selected open plenum metal ceiling to mask the lighting, HVAC and security systems, and a custom pattern design to accentuate the gaming area.
When ceiling designs conceal the plenum using panels, the most common and least expensive metal panel sizes are 2-by-2 feet and 2-by-4 feet in either flat or curved formats. Standard plank sizes are 2-by-6 or 4-by-6 feet. The panels and planks may be specified as square or reveal edge. Reveal panels expose the suspension in a recess detail. For curved panels, the radius of the vaults and valleys will need to be defined and usually conform to a minimum of 21/2 feet.
Continuous, long lines are the aesthetic emphasis with linear ceilings. To generate this desired look, most linear metal ceiling components are provided in up to 12-foot lengths with face widths of 2 to 8 inches. Multiple sizes can be used in the same ceiling for a more dramatic effect. Edges may be square, reveal or round. The edges will be more distinguishable the more space there is between the linear panels.
Metal baffles also can be installed side-by-side to provide a continuous linear appearance with spacing chosen to match the desired view of the exposed plenum. The spacing between baffles typically is equal to or greater than the baffle’s depth. For example, 4-inch-deep baffles usually are installed 4 or 6 inches apart. Round and v-shaped baffle bases are the standard choice.
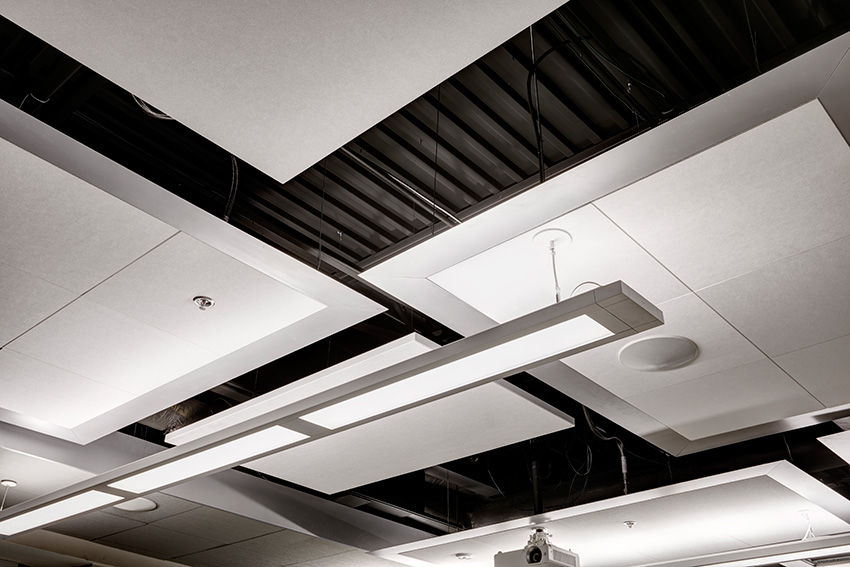
Photo courtesy of ROCKFON/Bochsler Creative Photography
Metal perimeter trim provides a neat, clean edge for the ceiling clouds suspended within a LEED Gold-certified office in Ontario, Canada.
In addition to the base of a baffle or the edge of a panel, metal perimeter trim provides an attractive, smooth, distortion-free enclosure that integrates with standard suspension systems. Perimeter trim offers a neat, clean edge for ceiling clouds, projected accents, light coves and dramatic transitions between ceiling heights. Available straight or factory-curved to project requirements, metal perimeter trim comes in 1-foot standard lengths and in a choice of edges that include concealed, razor or revealed designs. Paired bracket perimeter trim can be installed back-to-back for visual details including double-sided circles, snakes and arcs.
Perforations
Enhancing ceiling designs, metal panels and planks can be specified as solid surface or with perforations. With perforation, the diameter of the holes can be so small as to appear solid to more than 0.6 inches. The holes can be round, rectangular, or square, and placed tightly together or far apart. They can have lineal, diagonal or staggered patterns.
Most manufacturers have standard and custom perforation options. Some ceiling manufacturers offer graduated designs where the holes increase in dimension and decrease in spacing. Detailed, custom patterns also can be created for corporate logos, university mascots and other graphic reproductions. Keep in mind that custom perforation choices can increase cost, as well as lead time.
When using perforations, it is advisable to keep a solid border around the perforations. This prevents bending the panel edge where a row of perforations occurs.
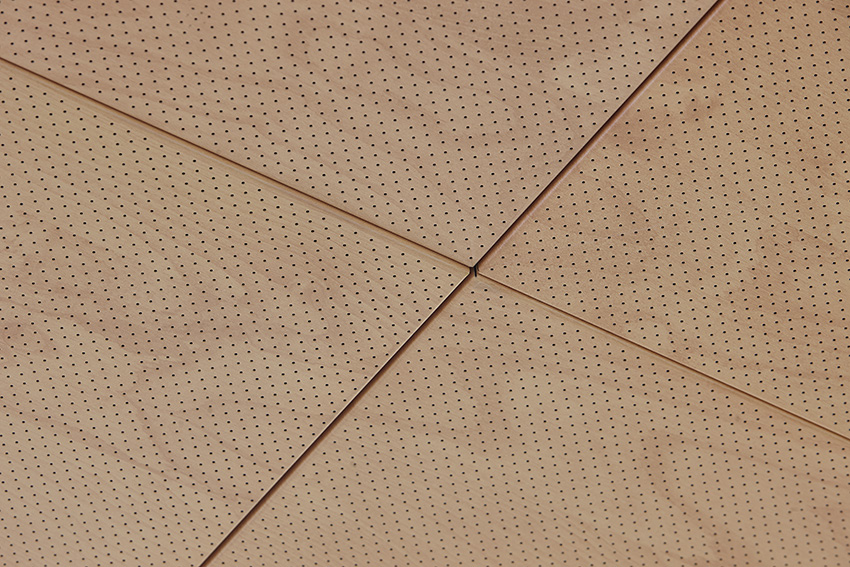
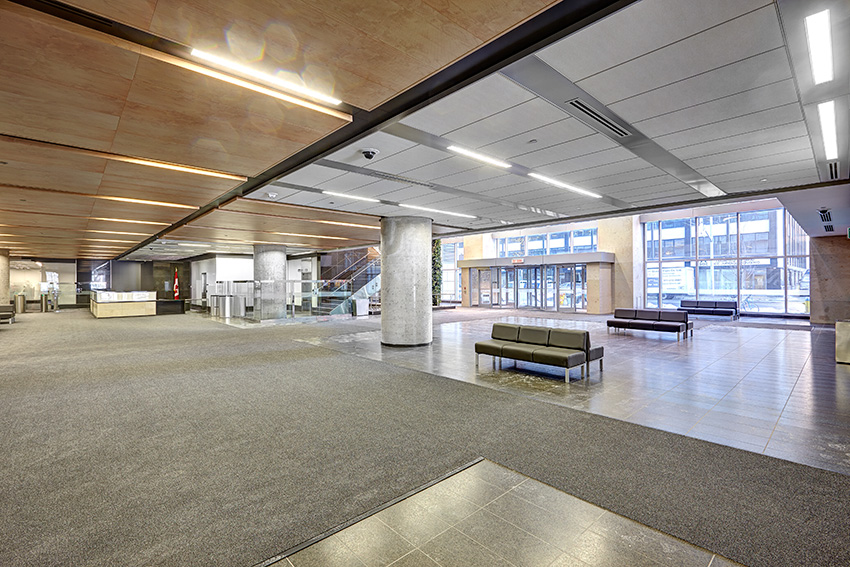
Photos courtesy of ROCKFON/Bochsler Creative Photography
The lobby of John Michael Flaherty Building in Ottawa, Canada. Plank hook-on metal panels have an acoustic backer and closely spaced perforations to optimize acoustics, while mimicking the look of natural wood with painted finishes.
Finish and Color
Metal ceiling systems’ components can be finished with different techniques and hues that bring the design from an imaginative concept to a colorful reality. The suspension systems’ exposed metal face can be finished to either match or contrast with the panels. White, silver and black are specified most frequently. For bolder designs, most ceiling system manufacturers offer a nearly unlimited choice of painted, metallic and specialty finishes.
Anodized finishes are an electro-chemical process for aluminum ceiling components, where the coating becomes integral to the panel or component. It is a very durable finish, suitable for both interior and exterior use, and for highlighting the metallic appearance. As the finish is integrated with the metal itself, the color ranges are limited and most commonly specified in clear, black or bronze.
Painted finish techniques for metal ceiling systems include coil coating, powder coating and baked enamel.
- Pre-painted coil coating finishes the metal before it is formed into ceiling components. Under factory-controlled conditions, the metal coils are unwound, cleaned, treated, dried, primed, coated with liquid paint, oven-cured, inspected and rewound. To meet stringent specifications, multiple coats may be applied.
- Baked enamel finishes are generally a one-coat system as no primer is required. These are applied after the metal has been formed into the ceiling panel or part, and typically used only for interior applications.
- Powder coatings also are applied after the metal is formed into a ceiling component. This is a dry film process where finely ground particles are electrostatically charged and sprayed onto the electrically grounded formed metal parts. The charged powder adheres to the metal and is oven-cured into a uniform finish.
Regardless of the technique, to ensure the desired look, give attention to matching the finished panels with trims, suspensions and accessory items. This is especially true when systems are to be curved or custom panels and trims are being created. Choosing a single-source supplier for metal suspension systems and panels provides consistency in finish and color selection.
While white and neutral tones are the most popular color choices for ceiling systems, finishes can be selected in nearly any color including metallics and simulated wood grain patterns. Colors evoke physical and psychological reactions. Brightness or color temperature creates different moods and ambiance. A viewer’s perception of a color also changes depending on whether it stands alone, is dominating a space or if it exists in combination with other colors. Warm colors, such as red, orange and yellow, are considered stimulating. Cool colors, like blue, purple and light green, generally have a calming effect.
Spatial perception also is affected by color. Lighter colors tend to make spaces seem bigger, while darker ones make spaces feel intimate. A dark ceiling will seem lower than it really is, or when installed high enough, seems to simply disappear.
Color schemes also can indicate the purpose and usage of space through the creation of boundaries and transitions. Consideration should be given to how the visual stimulation in a space will be perceived by the brain to evoke a desired response. This is of utmost importance in environments where varied spaces have different tasks and functions, to avoid any confusion that can cause stress in the occupants.
Function and Specification
Contributing to occupants’ wellness and safety, metal ceiling designs may be specified to meet rigorous performance requirements for acoustics, wind loads, humidity, fire, earthquakes and sustainability.
Optimized Acoustics
Metal ceiling panels with perforations can provide a moderate to high level of sound absorption. Generally, a perforated panel supplied by the manufacturer with only a non-woven, black fabric on the back will absorb 70 percent of the sound that strikes it. This can be expressed as a Noise Reduction Coefficient (NRC) of 0.70. That same perforated panel with a fibrous batt on top of it could absorb 90 percent of the sound that strikes it, or NRC 0.90. The percent of open area resulting from the selected perforation pattern, and the presence or absence of the fibrous batt, are the biggest factors in determining how much sound is absorbed.
When NRC values are included in building standards and guidelines, they usually apply to ceilings in conference rooms and open offices, and are in the mid to high range of 0.80 to 0.90 NRC. The other common acoustic metric in the standards and guidelines is reverberation time, or the time it takes reflected sound to decrease 60 dB. Metal ceilings can help to decrease reverberation as well. The sound passes through the perforations in the metal and is absorbed. Suspended ceilings are used primarily, and most effectively, for achieving sound absorption. Using acoustic islands and baffles also may yield the same acoustic performance with less material than standard suspended ceiling systems.
Additional absorption on the walls and floor may only be required if the ceiling does not provide enough sound absorption; for example, when the NRC is less than 0.70 or when parts of the ceiling are intentionally left sound reflective to project sound, such as above a presentation podium.
To further optimize acoustics, noise transfer also must be minimized between rooms through sound-blocking elements. Most ceiling systems are not massive enough to block sound and are penetrated by lights, air grilles, speakers and other potential elements where sound can leak. Likewise, this can happen via gaps between the ceiling panels and the suspension system. Where room-to-room sound blocking is needed, use walls or plenum barriers to successfully block sound.
There now are stringent acoustic criteria in standards, guidelines, and building rating systems. Both the U.S. Green Building Council’s LEED version 4 and the WELL Building Standard require minimum performance levels of sound absorption in office buildings. Optimization Features for WELL Certification of New and Existing Interiors include:
- Feature 78, which calls for maximum Reverberation Times (RT60) to decrease stress and maintain comfortable sound levels through the use of sound-absorbing materials.
- Feature 80, which requires spaces to incorporate absorptive surfaces to help with reverberation management and to improve privacy and acoustic comfort. It refers to using ceilings with high NRC values to achieve this. Open office spaces need ceilings with a minimum NRC 0.90 for 100 percent of the ceiling. Conference and teleconference rooms need ceilings with a minimum NRC 0.80 for at least 50 percent of the ceiling.
- Feature 81 addresses noise from adjacent spaces using sound barriers to reduce transmission. Noise Isolation Class (NIC) is the field measurement of total sound isolation between two rooms, specified by WELL as: NIC 40 for enclosed offices without sound masking; and NIC 53 for conference and teleconference rooms, or for private offices with adjoining walls. NIC is similar to Sound Transmission Class (STC), the former being an in-field test of how much sound transfers between two actual rooms and the latter being a laboratory measurement of the wall construction alone. WELL also notes that all interior walls enclosing regularly occupied spaces be sealed properly along the top and bottom tracks. This commonly would be interpreted as using full-height walls and preventing noise leaks to isolate sound between adjacent spaces.
As these guidelines and standards are revised during the coming years, levels are likely to be set even higher, as has happened for other types of buildings including schools and healthcare facilities.
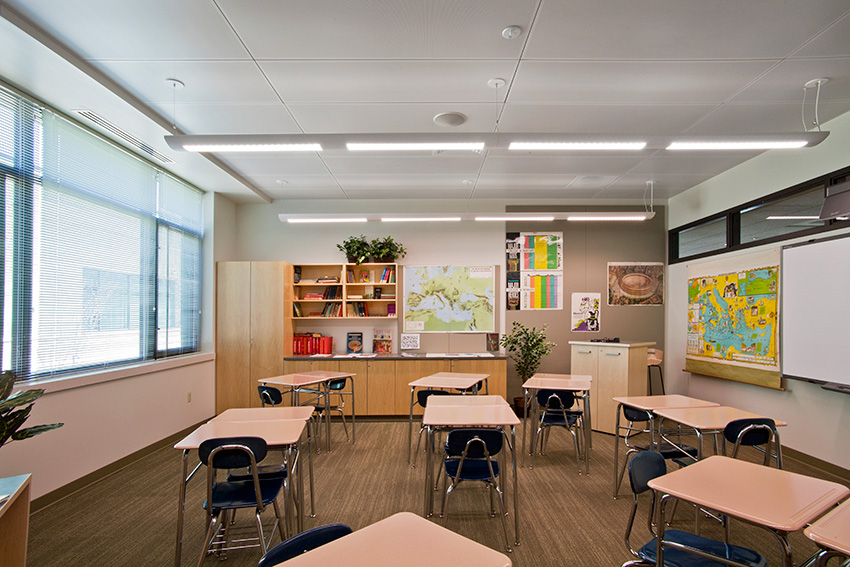
Photo courtesy of ROCKFON/Saari Photography
Cranbrook Kingswood Middle School for Girls relies on metal panel ceiling system with increased acoustic performance for an optimized learning environment.
“It is recommended that ceiling systems be used to optimize sound absorption and, where needed, walls or plenum barriers be used to effectively block sound between rooms,” says Gary Madaras, PhD, acoustics specialist at the ROCKFON Group leading its Optimized Acoustics program.
Wellness and Sustainability
In healthcare facilities, kitchens, laboratories and other places where wellness and cleanliness are essential, humidity-resistance can be critical. Ceiling panels that absorb water may lead to the growth of unwanted mold and mildew, a factor in “sick building syndrome.” In some regions where high humidity is unavoidable, excess moisture may lead to sagging, or even irreparable damage, in mineral fiber panels and wood panels.
Metal ceiling systems do not absorb water and do not contain organic compounds that would support mold or microbial growth. No volatile organic compounds (VOCs) are associated with metal ceiling systems. These attributes further contribute to indoor air quality and occupant health.
Light can also impact performance, wellbeing and mood. Too much light can cause eyestrain and make it hard to focus, but too little can lead to headaches, difficulty focusing and drowsiness. Ceiling panels finished with light-reflecting surfaces can maximize the use of natural light, reduce the number of electric light fixtures required, and lower the associated loads, costs and emissions.
The durability of metal ceiling systems also assists in reducing waste to landfills. Metal ceiling systems can approach 100 percent recycled material content and are 100 percent recyclable at the end of their useful life as a ceiling. With minimal maintenance, these systems have shown to deliver reliable performance for more than 25 years with some lasting 50 years and more. It is estimated that more than 90 percent of aluminum used in buildings is recycled after service, making it one of the most recycled building materials in the world.
Safety and Security
International and local building code requirements are in place to protect occupants’ safety and security. Relevant to ceiling systems, these include fire, seismic, wind load and corrosion resistance needs tuned to the climate, geology and functionality of the project.
A fire performance rating for a ceiling system evaluates flame spread and smoke development. The industry testing procedures for this rating is described in ASTM E-84 Standard Test Method for Surface Burning Characteristics of Building Materials. The International Building Code (IBC) classifies ceilings as Class A-C, with Class A being the most stringent and a requirement when ceilings form part of a return air plenum. When fire-suppressing sprinklers are used, a fire protection engineer should be consulted to ensure proper compliance and performance.
In addition to fire-rated ceiling products that are tested to ensure they meet or exceed code requirements, seismic-rated suspension may be necessary in critical care facilities including hospitals and in areas prone to earthquakes. The IBC outlines six Seismic Design Categories—A-F, ranging from the least to the most stringent—that every construction project must meet regardless of geography. However, ceiling panel performance and some suspension systems are not well defined in the IBC requirements. A few ceiling manufacturers have taken the additional step of having an independent, structural engineering firm test their systems to meet ASTM E580/E580M Standard Practice for Installation of Ceiling Systems for Acoustical Tile and Lay-in Panels in Areas Subject to Earthquake Ground Motions.
When ceiling systems are used outside of the building, such as in a soffit or above an entrance, it is highly recommend that a wind load test report be requested. Exterior wind load requirements are dictated by local codes. Many ceiling manufacturers have data available for positive wind load testing, but to truly evaluate the ceiling system’s performance, request the manufacturer’s proprietary test data that provides both positive and negative wind loads. This will reveal how the product performs in sustained and reoccurring winds, such as in coastal regions or mountain ranges. These same considerations must be given to certain other applications, such as subway stations, tunnels and passageways between buildings.
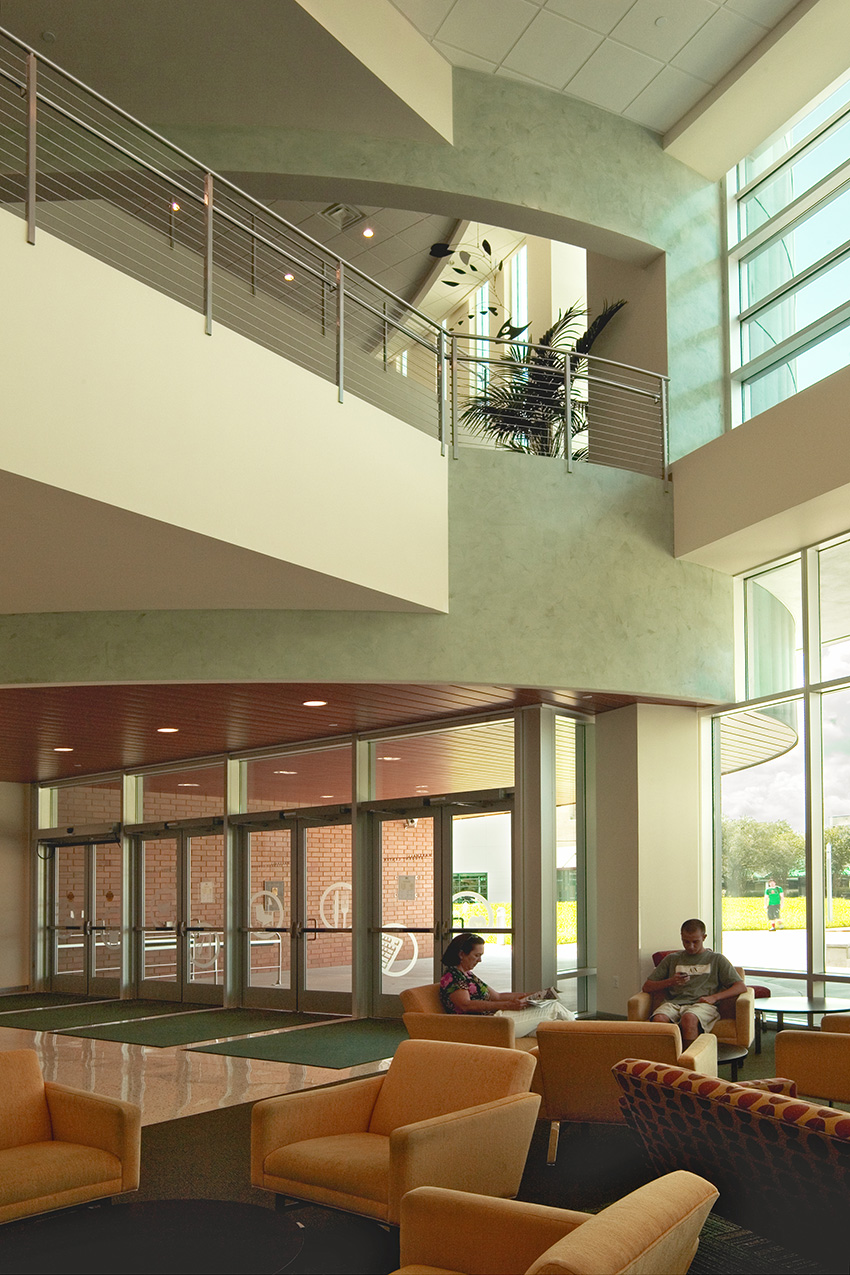
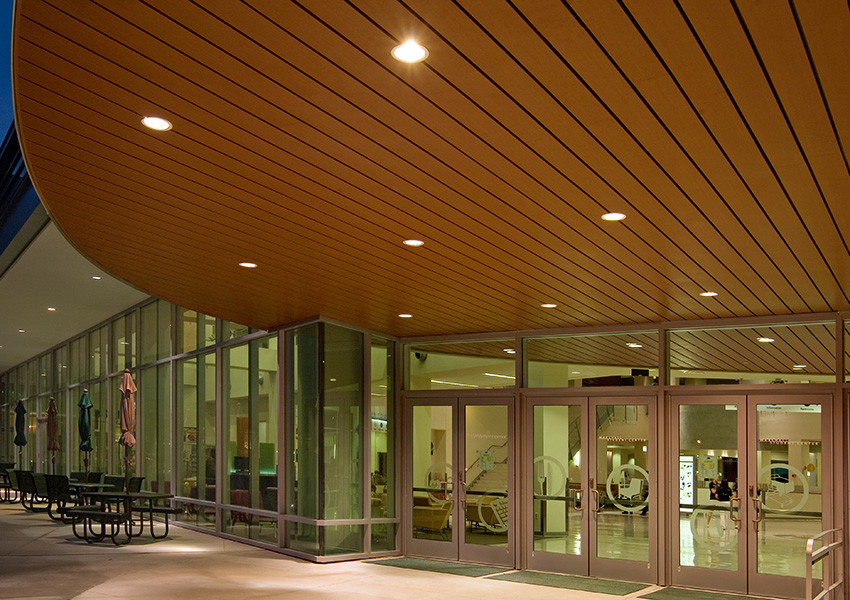
Photos courtesy of ROCKFON
The University of South Florida Marshall Student Center’s ceiling design unifies and connects the interior and exterior spaces with linear metal planks.
Like wind load, corrosion considerations for a metal ceiling are specific to location and climate with respect to the material composition. To provide corrosion-resistance, steel must be finished after the metal is formed into the ceiling component. Aluminum inherently resists corrosion, and most finishes enhance its durability. Regardless of the material, the finishing provider should apply the painted coating or anodize under factory-controlled conditions to ensure the specified performance for color and gloss retention, salt spray resistance, weathering and wear.
The strength and longevity of metal ceilings also makes them highly compatible with specialized security and sanitary applications.
- Medium-security facilities may specify a heavy-duty suspension system and steel panels that fit securely into the grid and resist removal after installation. High-security areas require steel planks that are held in place by heavy steel channels and tamper-proof screws. When specifying a metal ceiling for a secure area, remember to take into consideration the desired level of security; and the interfaces with HVAC, lighting and structure.
- For cleanroom applications, metal panels can be used with a variety of suspension systems, including stainless and gasketed, to accommodate low particulate air emissions. These systems can be used in rooms where the air cleanliness can be as stringent as Class 3, based on clean room classifications from ISO 14644-1. As with other specialized applications, be careful to consider the HVAC, lighting, structure and interfaces.
Installation and Maintenance
Properly installed and maintained, a metal ceiling system can last beyond its warranty for many years—even decades.
Installation
The Ceilings & Interiors Systems Construction Association’s (CISCA’s) Metal Ceilings Technical Guidelines was developed by industry manufacturers and contractors in 2007 and was the first industry technical publication of its kind. Updated in 2015, it remains an industry standard for best practices in manufacturing, installing and maintaining metal ceiling systems.
Common quality issues noted by the guidelines are:
- Cupping, the upward deformation across the face of the panel.
- Sagging or pillowing, the downward deformation across the face of the panel.
- Oil canning or rippling, the visible deformation in the face of the panel along its length.
- Bowing, the permanent deviation from the vertical plane without any live or dead loads.
- Stepping, the vertical distance between the two adjacent panel edges as installed.
- Gapping, the horizontal distance between the two adjacent panel edges as installed.
- Cambering, the permanent deviation from the horizontal plane.
- Angularity, the permanent out-of-squareness of the long edge in relation to the short edge of a panel.
- Twisting, the permanent rotation along the length of a component.
Helping minimize these issues, CISCA’s technical guidelines reference ASTM C-636 Standard Practice for Installation of Metal Ceiling Suspension Systems for Acoustical Tile and Lay-In Panels. ASTM C-636 was updated most recently in 2013 and should be the current version reflected in ceiling manufacturers’ and installations documentation.
Metal ceiling systems are cost competitive and easy to install, which contribute to labor savings and on-time completion rates. Some of the most common areas where costs increase for metal ceiling panels include perforations for aesthetics and acoustic performance, custom and specialty finishes, and large sizes.
For custom and complex ceiling designs, consult with the installer and manufacturer to request samples and assistance, and allow for adequate installation time in the construction schedule. When on-site coordination and timelines are a top concern, consider full-scale mock-ups to minimize confusion. Mock-ups help ensure that the ceiling system meets the desired look and specified performance, accommodates the lighting and integrates mechanical equipment components, and maximizes the likelihood of a successful installation.
Maintenance
Metal ceiling systems need very little maintenance. They are easy to clean in place. If a ceiling panel requires more rigorous cleaning, repair or replacement, most suspension systems make it simple to remove the single panel or section.
Because ceiling components feature numerous finishes varying in color, texture, gloss level and method of application, the effect of cleaning agents upon them also can have different reactions. For instance, a cleaning solution that proves effective for one type of finish may also clean another type of finish, but, in doing so, alter its color or gloss level.
Always follow the ceiling manufacturer’s instructions. When in doubt, test the selected cleaning solution on a small, inconspicuous area of the component’s finish. Such precautions will allow for adjustments to the cleaning solution, applicator or application effort without risking damage to highly visible areas.
Conclusion
The most successful projects involve close coordination between the designer, specifier, manufacturer and the installing contractor. The earlier the manufacturer is involved in the design discussion, the more easily they can help bring the vision to reality within the project’s scope. Understanding the essential aesthetic, functional and installation considerations for metal suspension systems, panels and accessories will ensure the desired, lasting appearance and performance for inspired ceiling designs.
Mark Taylor is the ceiling systems’ market manager at ROCKFON focused on helping optimize commercial ceiling designs for form, fit, finish and function. He can be reached at mark.taylor@rockfon.com.
![]() |
ROCKFON complete ceiling systems combine acoustic stone wool and specialty metal ceiling panels with suspension systems. A fast, simple way to create beautiful, comfortable spaces, they protect people from noise and the spread of fire, while contributing to a sustainable future. www.rockfon.com |