Enhancing the Stone
Stone veneer panels on aluminum honeycomb combine the beauty of natural stone with the design freedom, strength, and lightness of metal panels
Continuing Education
Use the following learning objectives to focus your study while reading this month’s Continuing Education article.
Learning Objectives - After reading this article, you will be able to:
- List the benefits of using natural thin stone veneer on aluminum honeycomb panels in a variety of applications.
- Compare the design freedom, aesthetics, cost, service life, safety, and durability provided by stone veneer on aluminum honeycomb panels against traditional stone cladding.
- List the varieties of stone available in thin natural stone veneer on aluminum honeycomb panels.
- Discuss how the characteristics of stone veneer on aluminum honeycomb panels can lead to achieving a project’s green building goals.
For thousands of years, stone has been a much-lauded ingredient in building design and construction. And with good reason. Stone has many appealing qualities. Not only is it durable, but there is an unmatched aesthetic to stone that comes not only from its natural beauty, but its ubiquity throughout history as the choice construction material of mankind. Design choices know no bounds with stone’s wide-ranging variety of colors, types, patterns, and textures. Used over the centuries for everything from mighty ancient Greek and Roman structures, the Egyptian pyramids, and graceful churches and temples around the globe, stone has stood the test of time as a premier material choice.
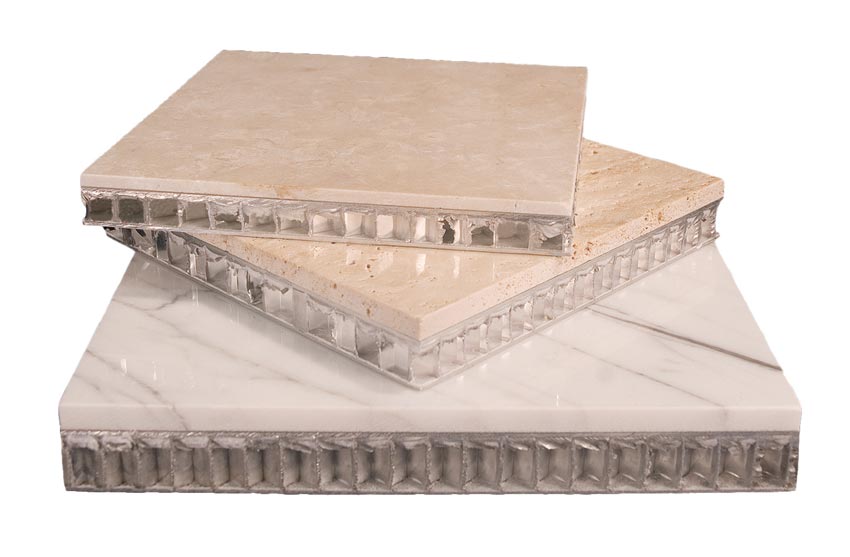
Image courtesy of StonePly
Stone veneer panels on aluminum honeycomb provide an innovative alternative to traditional stone cladding.
Traditional, heavy stone masonry is rarely used in modern buildings; its main drawbacks have been its unwieldy weight, high labor costs, and quarry, cut, and transport challenges in getting stone from point A to point B. Today however, architects looking for innovative ways to incorporate stone's many benefits into their current projects no longer need to dismiss stone as an option. A lighter, cost-effective, sustainable, and proven product is available: lightweight aluminum honeycomb-backed stone panels.
The Basics of Thin stone on Aluminum Honeycomb Backing
Natural stone veneer on aluminum honeycomb panels are composite panels consisting of a thin layer of natural stone (such as granite, marble, travertine, or limestone), typically 1/4 inch thick, bonded with high-strength epoxy to a lightweight, yet extremely durable aluminum honeycomb backing. The total panel thickness including stone and aluminum honeycomb is typically either 3/4 inch or 1 inch combined with the increased strength and light weight of aluminum. The panels are typically custom made to the size and shape required for the specific project. Corners, sills, and special shapes can be factory fabricated.
Natural stone is attached to the aluminum honeycomb backing with an extremely durable aerospace-grade epoxy.
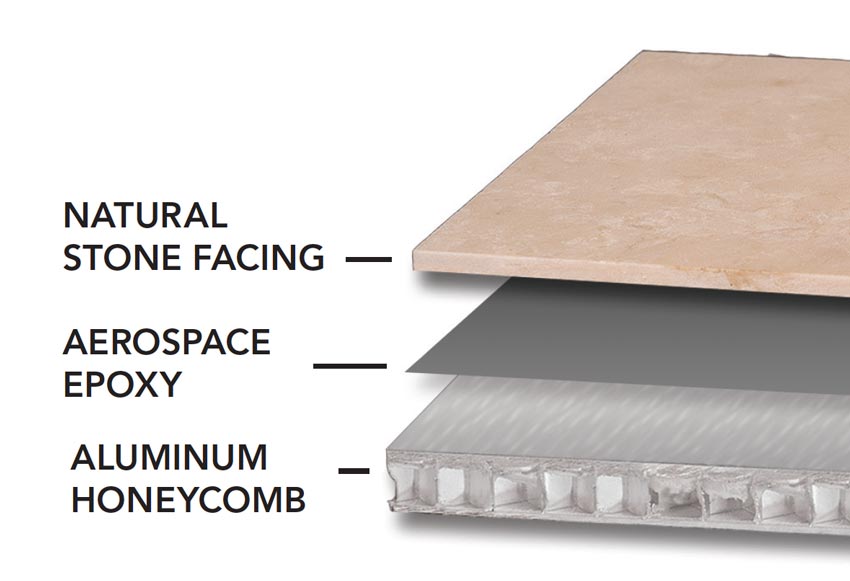
The Process: How Does It Work?
The panels are custom fabricated in the stone type, color, finish, size, and shape selected by the designer. The first steps involve providing stone samples and shop drawings to ensure the designer’s vision is being expressed. Once shop drawings and submittals are approved, the manufacturing process begins.
The manufacturing process starts at the stone quarry, where large blocks of stone are extracted. The blocks are then taken to giant saws where they are cut into slabs, typically 11/4 inches thick. The aluminum honeycomb panels are prefabricated with high-quality aluminum, which are then bonded with aerospace-strength epoxy to each face of the stone slab. The aluminum backing increases the strength and impact resistance of the stone and makes installation much easier and more secure than with traditional veneers. Panels weigh just 3.5 pounds per square foot but offer impact resistance up to 60 times greater than stone slabs.
At this point, the panel is a sandwich of aluminum honeycomb on both faces with the stone in the middle. The panel is then sawn down the middle of the stone slab to produce two panels with stone veneers roughly 5/8 inch thick before the finish is done. Next, the panels go to the finishing process where they receive a final finish and texture, decreasing the thickness of the stone to about 1/4 inch. Depending on the project and the designer’s preference, the finish can be polished, honed, flamed, sandblasted, or tooled. Other options include carving or laser engraving. The panels then go to the fabrication area, where they are cut to the specific dimensions required for the project and corner pieces and any special shapes are custom fabricated. Finally, the panels are packaged along with installation drawings and instructions and shipped to the jobsite.
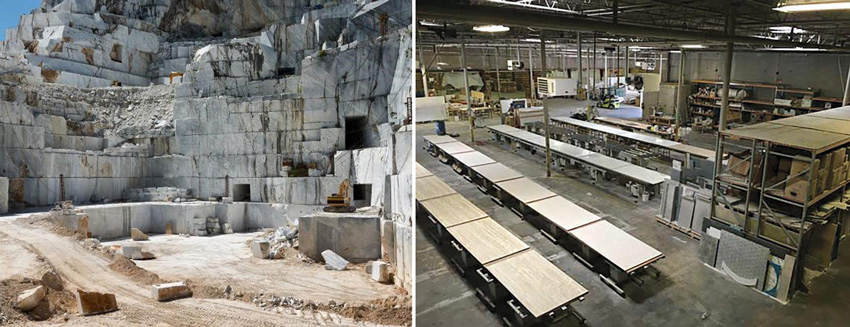
Pictured here, the process of how the stone panel is cut, ground, and polished.
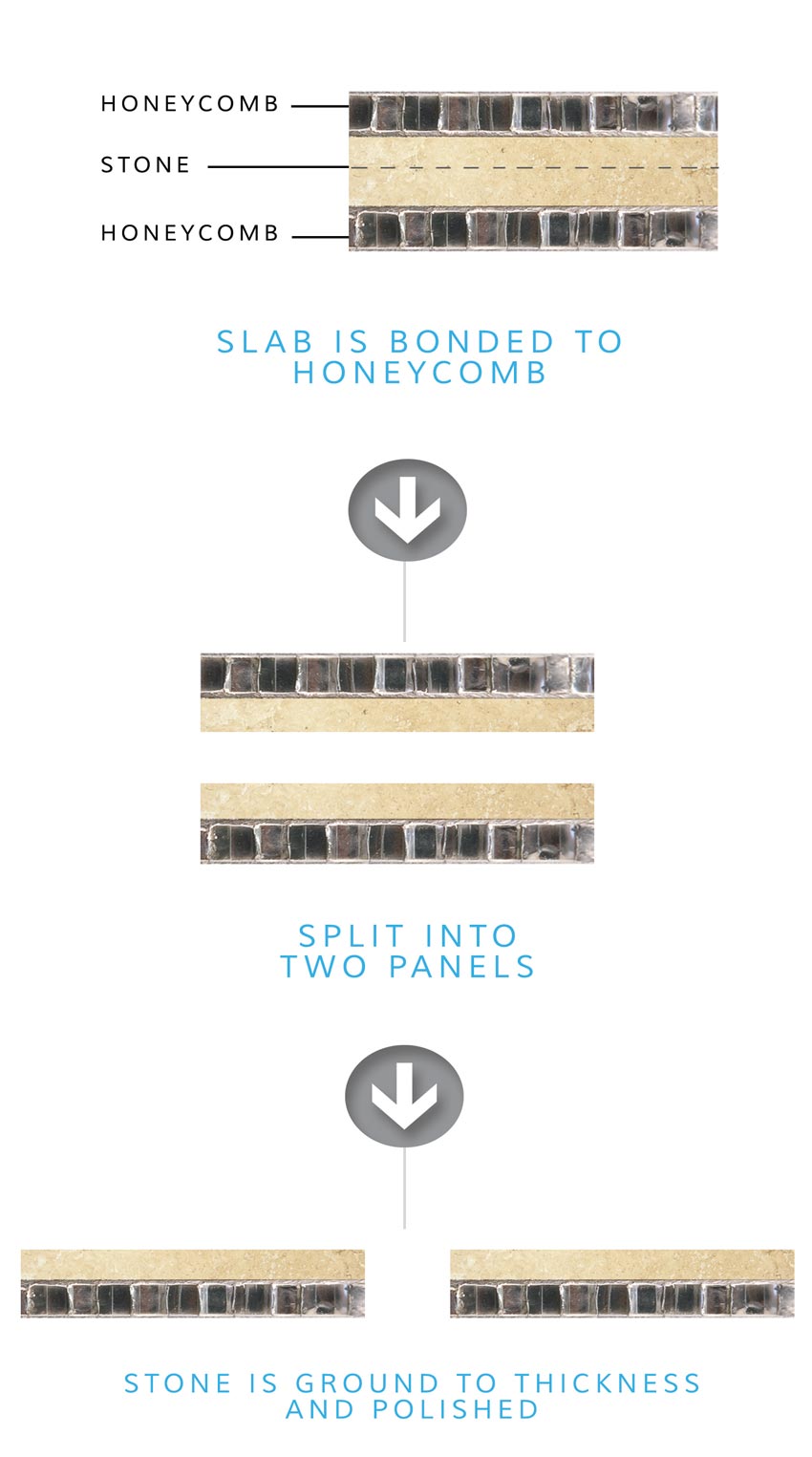
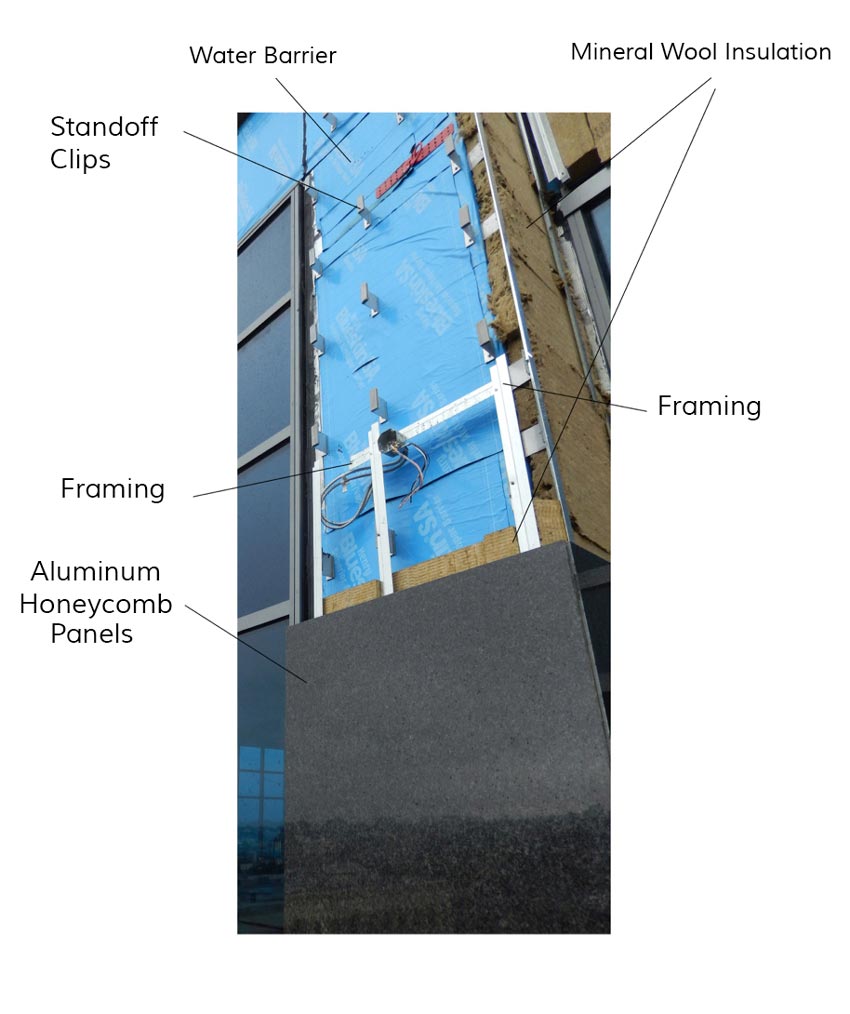
Finally, the panels go to the jobsite for installation.
Corners & Finished Edges
The panels are custom fabricated in the stone type, color, finish, size, and shape selected by the designer. The first steps involve providing stone samples and shop drawings to ensure the designer’s vision is being expressed. Once shop drawings and submittals are approved, the manufacturing process begins.
Types of Corners:
In the images above, you are able to see the different types of corners that can be made.
Quirk Miter Edges & Corners:
- An external corner formed by two stone panels at an angle, with meeting edges mitered and with visible portions finished.
Factory Bonded Corners & Finished Edges:
- Factory bonded corners and finished edges give you the appearance of solid stone without the added weight.
- These corners save time and cost with an easier onsite installation.
- Factory bonded corners and finished edges help to eliminate some of the additional onsite work.
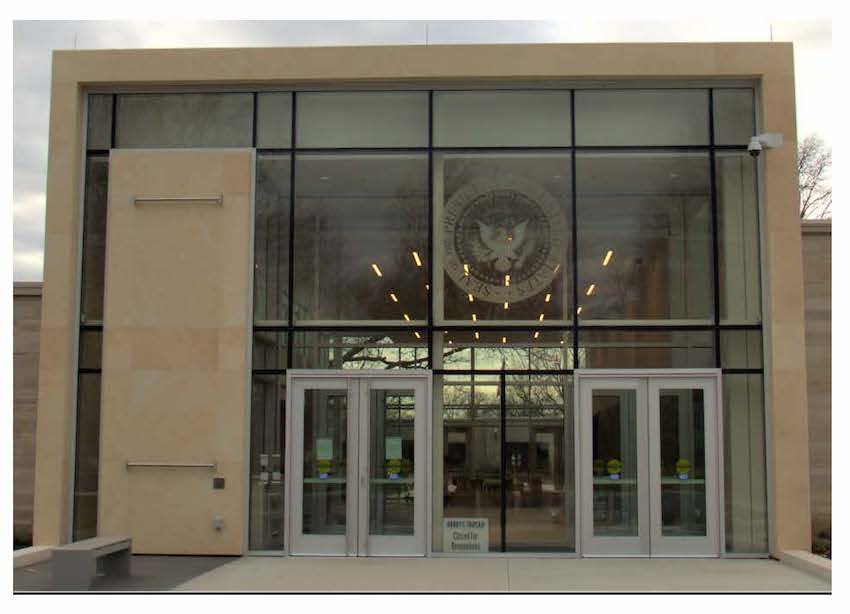
Truman Library – Front Entrance & Banner Wall
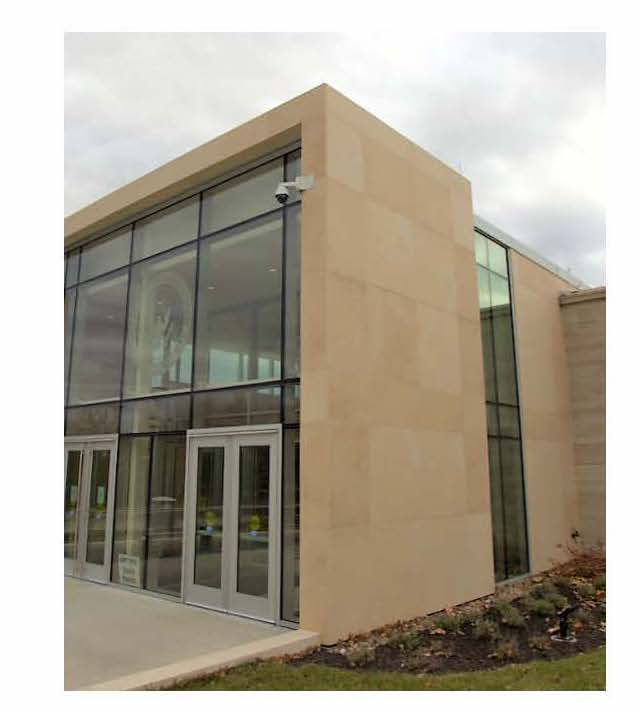
Feature Wall Drawings – Truman Library
How Stone Veneer on Aluminum Honeycomb Panels Enhance the Project—Inside and Out
Stone veneer on aluminum honeycomb panels offer designers and owners the beauty, low maintenance, and quality look and feel of natural marble, granite, travertine, or limestone. But unlike heavy and fragile stone slabs, stone on aluminum honeycomb panels are lightweight, strong, and easy to install, offering design freedom to use them in ways heavy slabs cannot be used.
According to a project manager for StonePly, a manufacturer of natural stone veneer panels, “Honeycomb-backed stone panels are an innovative solution to natural stone. The lightweight panels cut installation cost and time without sacrificing the beauty of having natural stone on your project. With the reinforced honeycomb backing, you also gain strength and durability, eliminating many of the problems faced with solid stone slabs.”
Stone on Aluminum Honeycomb Panels vs. Traditional Stone Cladding
There are several important advantages of stone on aluminum honeycomb panels:
- Traditional stone panels weigh approximately 27 pounds per square foot. Stone veneer on aluminum honeycomb panels weigh between just 3 to 4 pounds per square foot.
- Traditional stone panels are prone to bowing because of thermal hysteresis. The outside facing surface of the stone panel expands and contracts as it is exposed to warmer then cooler temperatures. In some cases, the panel does not contract fully, which is what leads to bowing. A greater load is placed on the stone anchors as a result.
- With stone veneer on aluminum honeycomb panels, the entire surface of the stone is attached to an aluminum honeycomb backing using epoxy. This eliminates weak spots and gives the marble cladding superior rigidity and flexural strength.
- Stone veneer on aluminum honeycomb panels are more cost effective since they’re lighter and faster to install.
- The honeycomb core has thin aluminum-walled cells. It is similar to the vertical element (the web) of an I-beam separating the reinforced skin on the stone side from the skin on the backside. This, along with the attachment system, increases the panel’s stability after installation.
Let’s take a closer look at some of the cost savings associated with stone veneer on aluminum honeycomb panels.
Cost advantages. There are several cost advantages of using lightweight stone on aluminum honeycomb panels. A major cost reduction can result from the speed of installation. Since the panels weigh about 80 percent less than solid dimensional stone, they can be lifted and installed by hand or light boom lifts. Since the need for extra manpower and specialized equipment is eliminated, installation can be as fast as up to 15 times that of traditional slab stone.
Another cost advantage is in the reduced structural support needed. Since the panels are considerably lighter than solid slabs, the load on the building's structure is greatly reduced. On larger projects, this can amount to millions of pounds of reduced weight. Savings on structural steel and concrete alone are often more than the price of both the panels and the installation. Additional savings come from reduced shipping and logistics.
Labor costs, too, are reduced not just by the reduced weight and speed, but by the simplicity of the system. Since these stone and aluminum panels can be installed by carpenters, more readily available trades can be used to get the job done.
Applications
Stone on aluminum honeycomb panels are used in commercial, hospitality, financial, government, retail, educational, and mixed-use construction projects throughout the world. Designers can use the panels on everything from high-rise facades, ceilings, and soffits to specialty elevator cab interiors, toilet partitions, and other areas where slab stone is too heavy or too weak to use. The lightweight panels are quick and easy to install, making them ideal for fast-track projects.
The panels allow designers the durability, beauty, and high-end appearance of stone in a lightweight panel. Thanks to the low weight of the panels, the load on the building’s structure is minimized. The panels offer speed of installation, hurricane resistance, and seismic resistance.
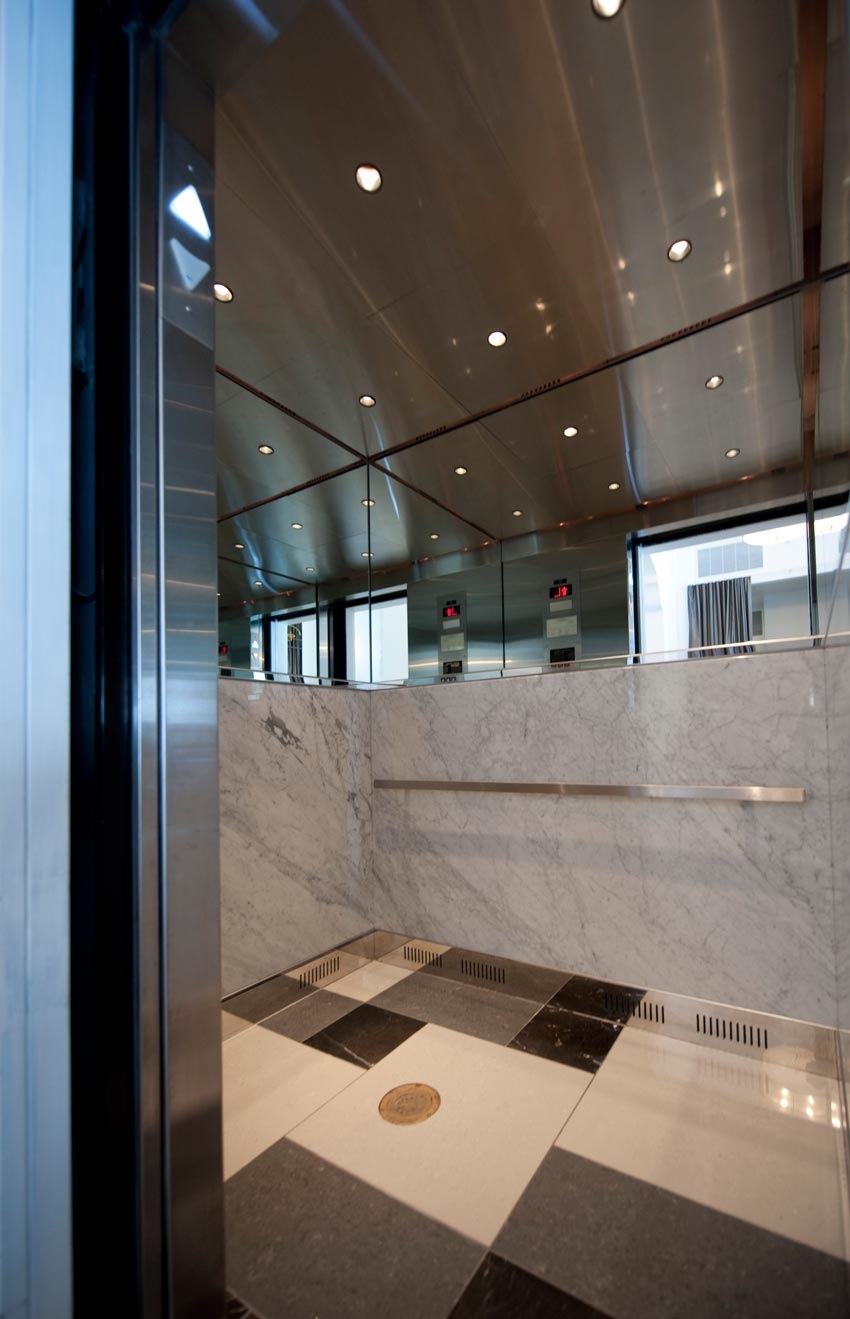
The lightweight properties of stone on aluminum honeycomb allow its use in areas where weight is a concern, such as here on the elevator cab walls at the Padre Hotel in Bakersfield, California.
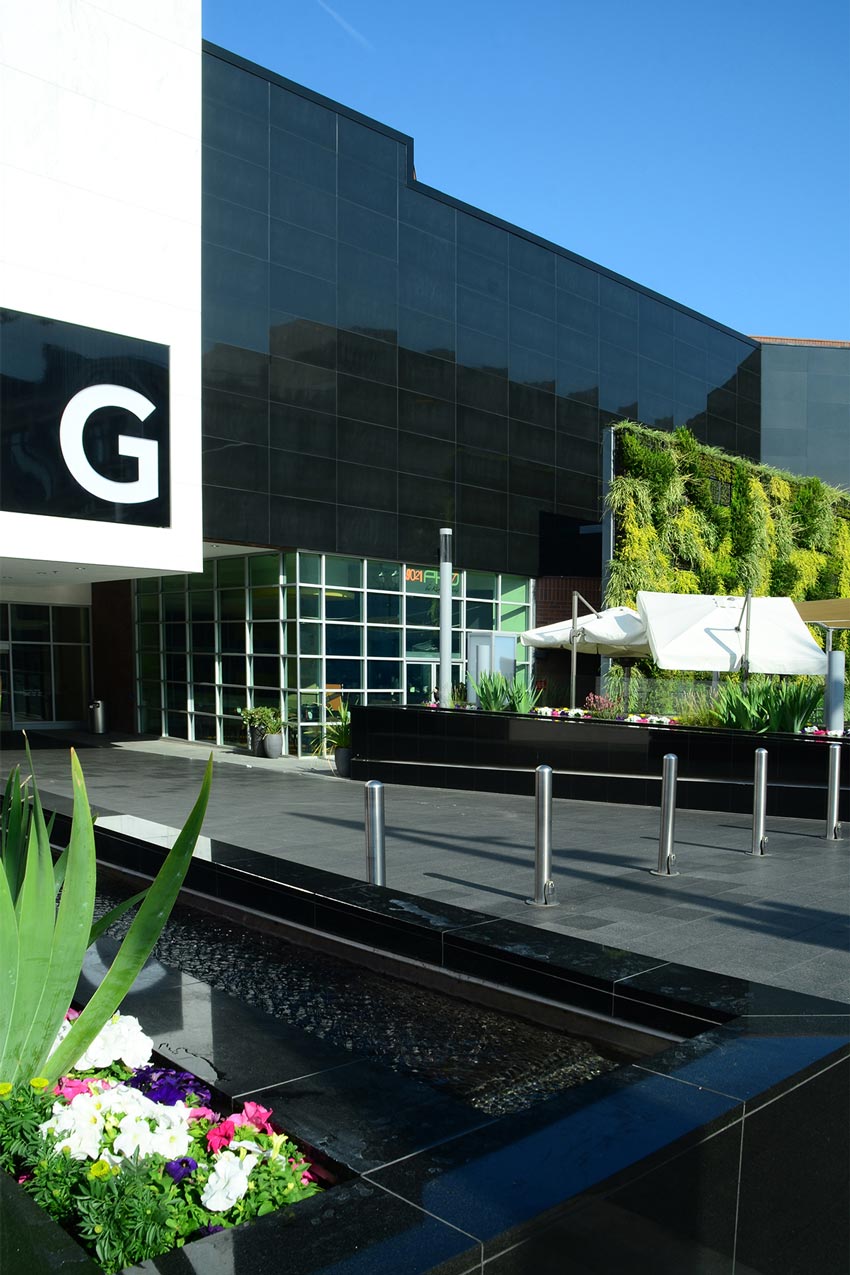
The exterior facade of Glendale Galleria in Los Angeles showcases stone on aluminum honeycomb panels.
There are many beautiful options for both exterior and interior panels. All of these applications give the look of full thickness stone without the added weight, allowing customers to have the beauty of natural stone for their projects. Here are some additional examples:
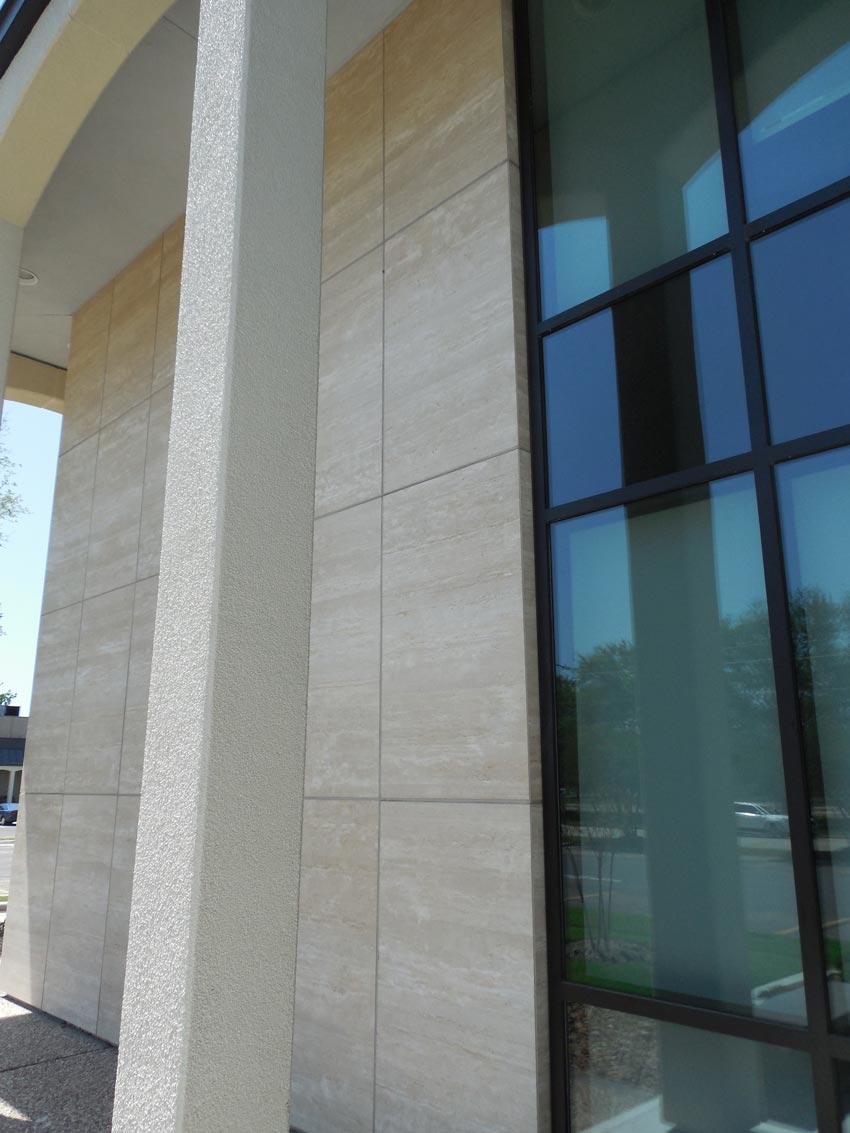
League City wall panels (travertine)
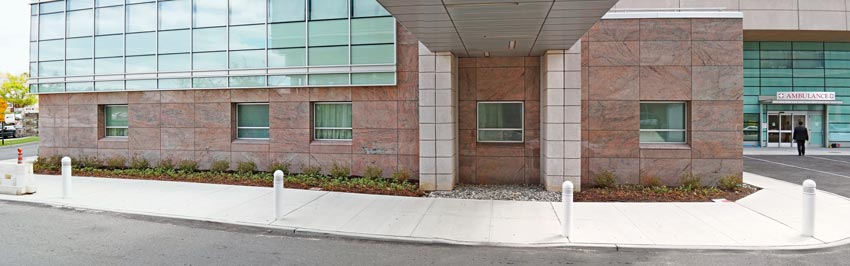
Queens Hospital wall panels
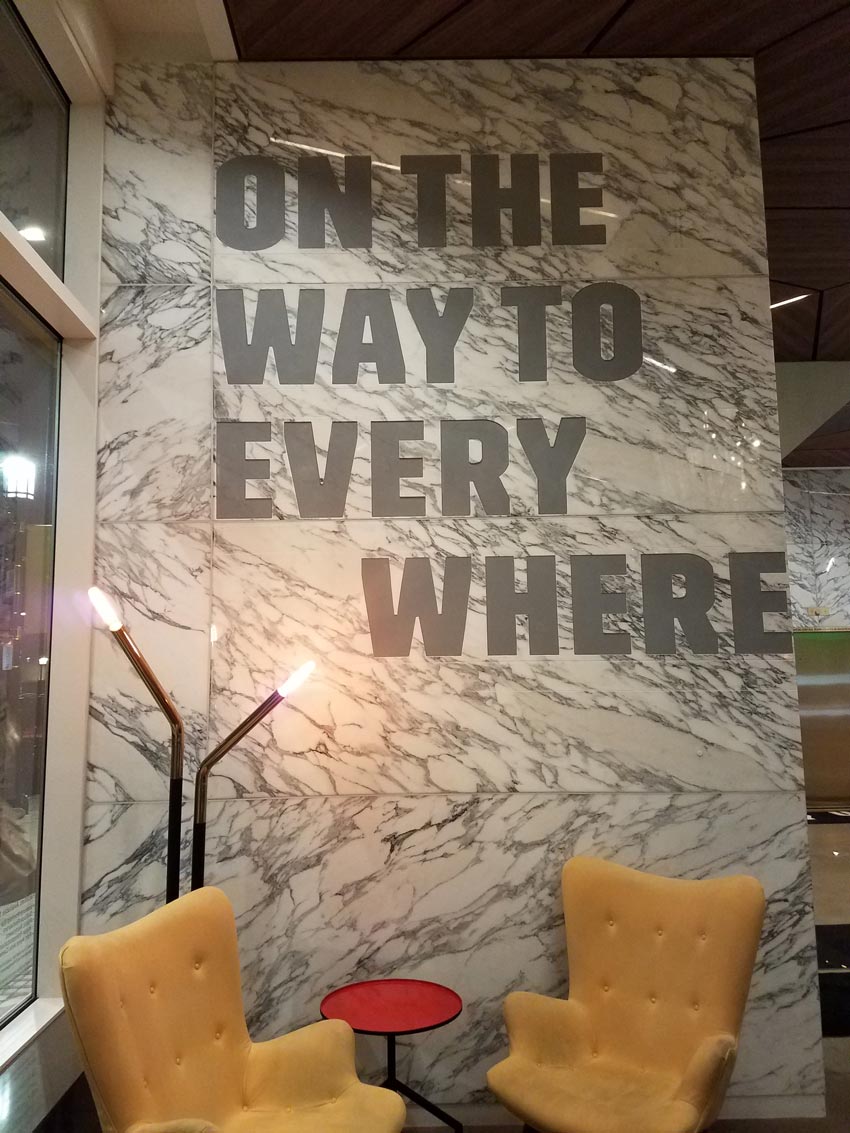
Envoy Hotel interior wall panels
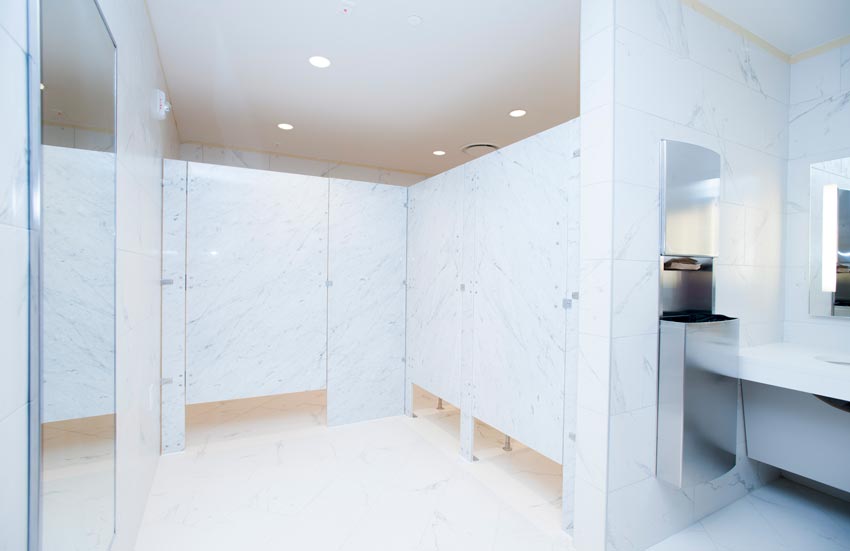
Texan Theater toilet partitions
Design Options
Panels are available in almost any stone and a variety of finishes to suit practically any design need. Most building stone is available on aluminum honeycomb panel backing, which are typically 1/2 inch or 3/4 inch thick. (Note: Stone selection may vary by manufacturer.) Let’s take a look at some of the options.
Natural Stone Types. Stone types include granites, marbles, limestone, and travertine.
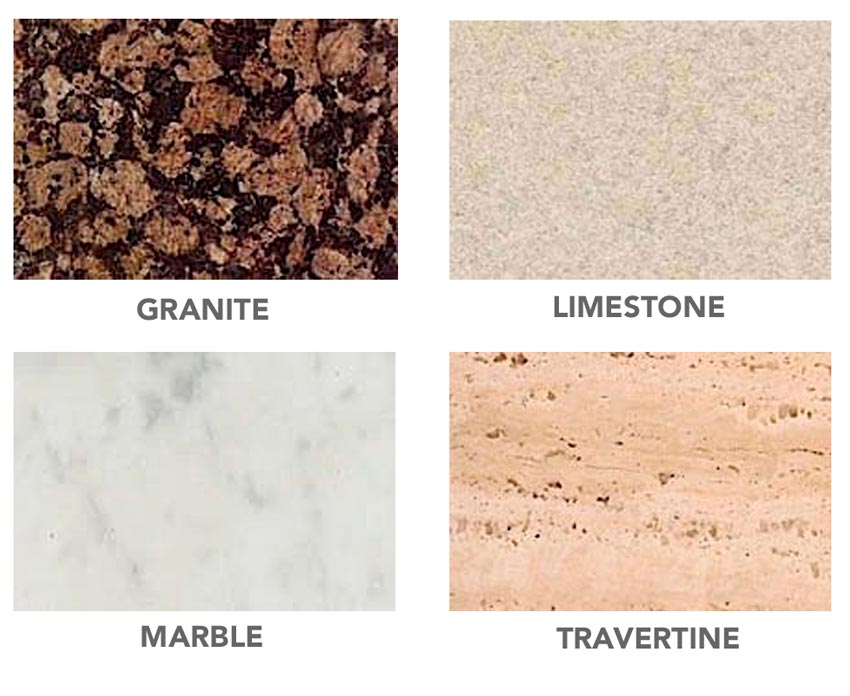
Sample of different stone types
- Granite. The hardest and most durable of stones. Granite is formed far beneath the earth’s surface as molten rock slowly cools and crystalizes.
- Marble. Used in fine architecture since ancient times, marble was originally formed from limestone that had been compacted and transformed by heat and pressure.
- Limestone. A calcium-based stone that is widely used in architecture. Formed in ancient seas from the calcium precipitate and from the shells and structures of tiny sea creatures that have been compressed and cemented over centuries.
- Travertine. The stone of the Roman Colosseum. Recognizable for its pitted surface, travertine is a calcium-rich stone formed in natural springs.
Stone finishes and colors. Stone finishes include polished, honed, flamed, sandblasted, and tooled, each providing its own unique aesthetic. How a stone appears depends upon color, pattern, and reflectivity.
- Polished. Diamond-faced pads wet polish the stone to a brilliant shine and a reflective finish. Polishing is available in marble and granite, but is not available in most limestones or sandstones.
- Honed. The stone receives a smooth mat sanded finish. The surface is smooth but not reflective.
- Flamed. The surface of the stone is super heated with a torch and then rapidly quenched to pop the crystals. This produces a rough textured finish.
- Sandblasted. The surface is blasted with an abrasive sand to create a finish slightly rougher than honed.
- Tooled. Tooled finishes include bush hammered, carved and engraved. Names, emblems, logos, signs, and other custom designs can be sandblasted or etched into panels to create unique accents and elements.
Stone runs the gamut from light to dark and all colors in between. Color is made up of reflected light, and the texture of the stone’s surface affects that. Polished stone tends to be darker, while sandblasted or flamed stone appears lighter. A black granite may appear deep black when polished, light gray when honed, and an even paler shade of gray when flamed.
Keep in mind that dark black stone can get very hot to the touch in full sun. In areas where people can touch the stone, a black or dark brown stone may not be the best choice. Instead, you may want to choose a white or lighter color stone.
Bottom line, when selecting cladding stone, make sure you see both the stone and the finish before you decide.
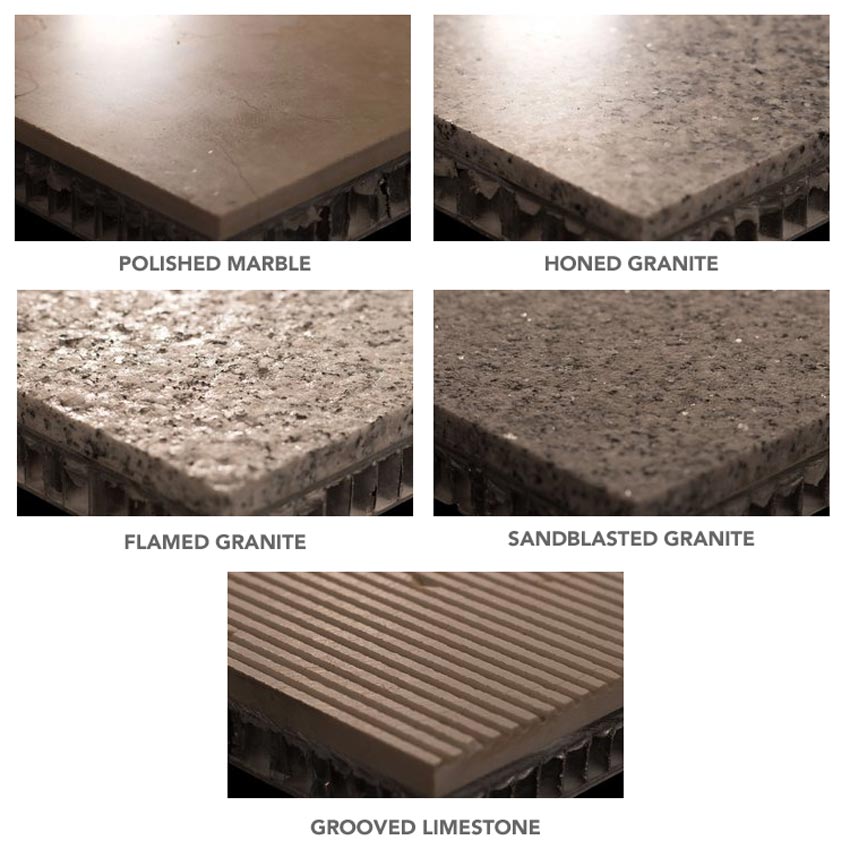
Examples of different stone finishes
Backing Options
The designer can also select from various backing options. Depending on the manufacturer, these can include aluminum honeycomb, aluminum composite material (ACM), and even glass.
Aluminum honeycomb backing (which we are focusing on in this article), typically ranges from 1/2 inch to 3/4 inch thick. This is the most common type for exterior cladding, bathroom partitions, or areas where high strength is needed.
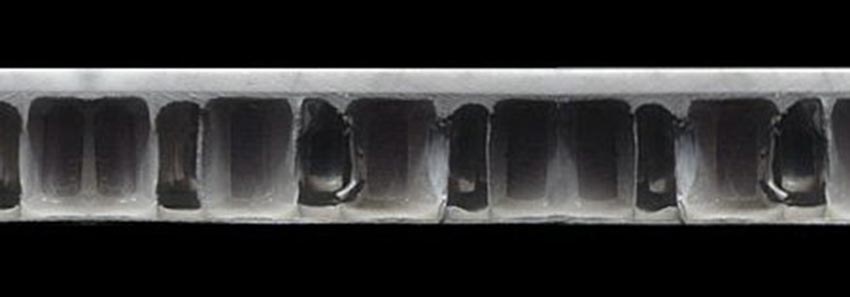
Honeycomb backing on stone
Another backing option is aluminum composite material (ACM), which is typically used on flooring or areas where a thinner material is required. The backing is just 5/16 inch thick. An ACM-backed stone panel is applied directly to a smooth surface with adhesive, and relies on the substrate for support.
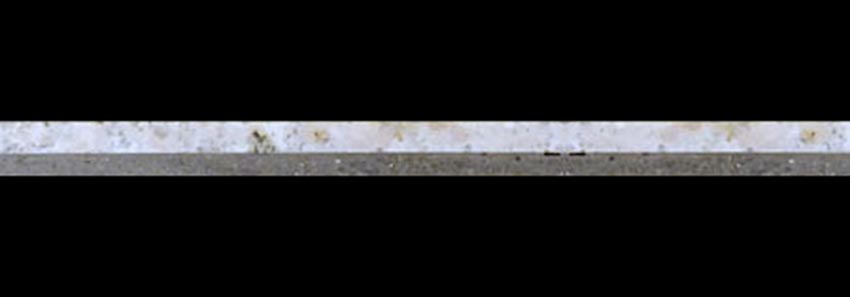
ACM backing
Translucent backing is a glass panel. This is used with certain translucent marbles and onyx; it is generally used for lighted bars, backlit walls, or feature panels and ranges from 1/4 inch to 3/4 inch thick.
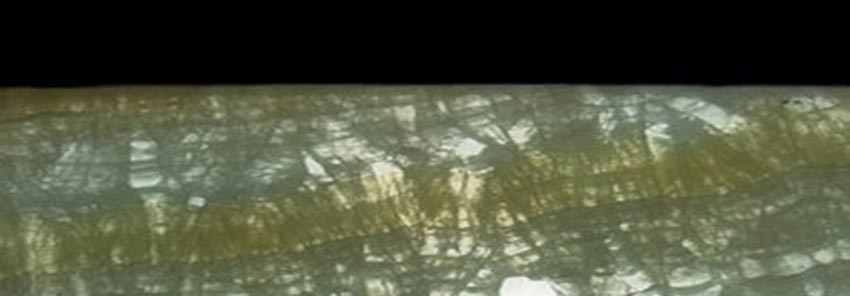
Translucent backing
Installation
For most applications, the panels attach with Z-clips, interlocking aluminum channels, or a concealed screw. The Z-clip or channel is attached to the wall, and a matching Z-clip or channel is on the back of the panel. The panels are then simply hung. Joints can be either caulked with a selected sealant or left open in an open-joint rainscreen. Thanks to the lightness of the panels, they can be installed from a variety of platforms, including scaffolding, boom lifts, scissor lifts, or swing stage scaffolding.
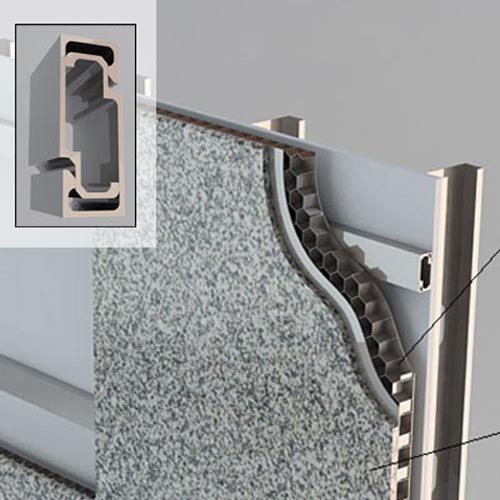
Interlocking channel attachment, used to attach panels to the substrate
Technical Specifications and Performance
When choosing a stone veneer on aluminum honeycomb panel, specifiers should look for a product that has been ASTM tested and where the panels meet or exceed the testing.
Panel installation techniques are designed to improve the safety, durability, and long-term performance. As noted, typical installation for these types of panels is usually with a Z-clip, interlocking channel, or concealed screw. With the Z-clips, they lock into place on a substrate, which locks them into place easily. With the concealed screw, they are screwed to the substrate.
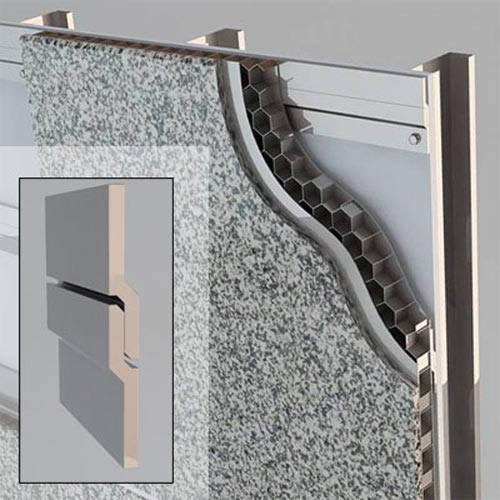
Z-clip attachment, used to attach panels to the substrate
Durability and Severe Weather
As the strength of stone on aluminum panels varies by manufacturer, it is important to verify the testing that a manufacturer has completed and the projects they have completed. Some manufacturers’ panels have been tested for large missile impact, freeze-thaw cycles, and high-wind events. An example of real-world testing includes the Atlantis Resort in the Bahamas, where the stone on aluminum honeycomb panels have been through several hurricanes, some of which were Category 5, without damage.
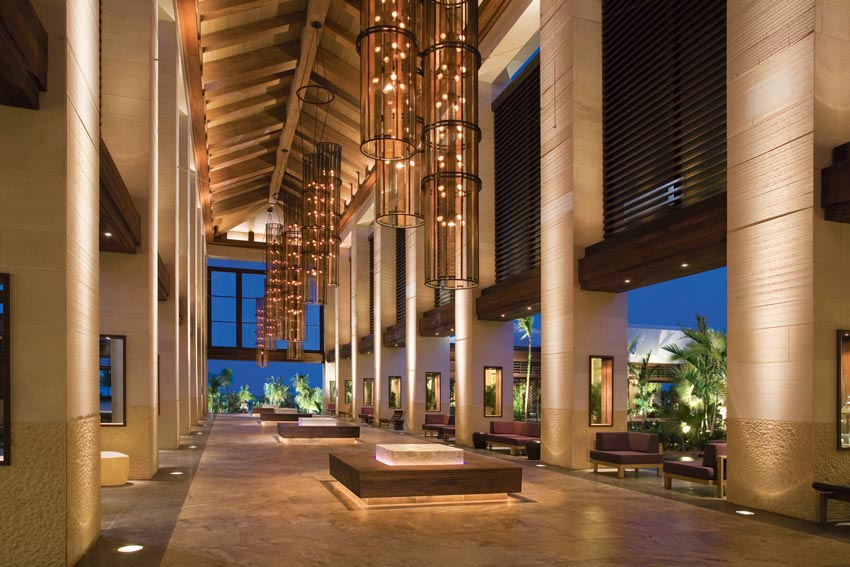
Stone veneer on aluminum honeycomb panels can be used in either a rainscreen or barrier-type wall system. The aluminum layer makes the panels impervious to water or air infiltration. Pictured here is the Cove at Atlantis Resort in the Bahamas.
Performance and Testing Methods
The following tables show typical testing methods.
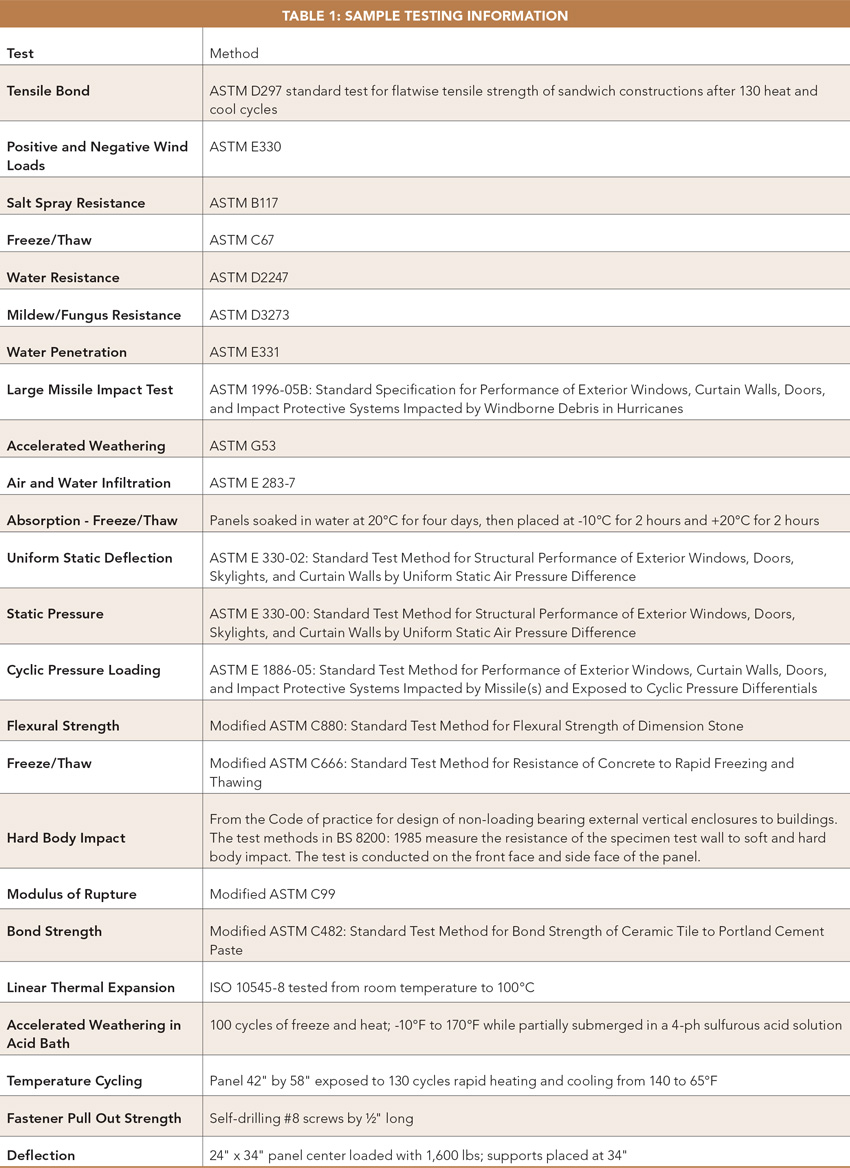
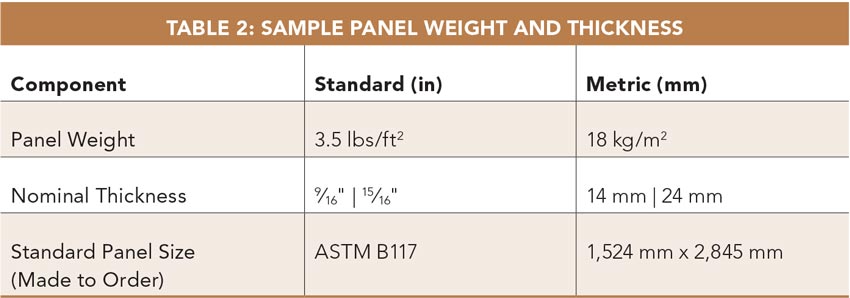

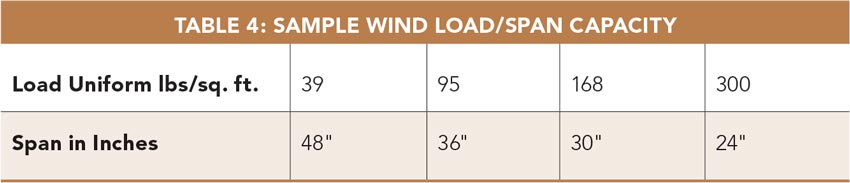
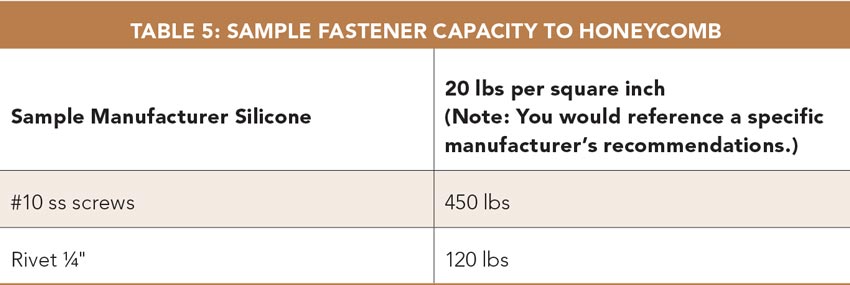
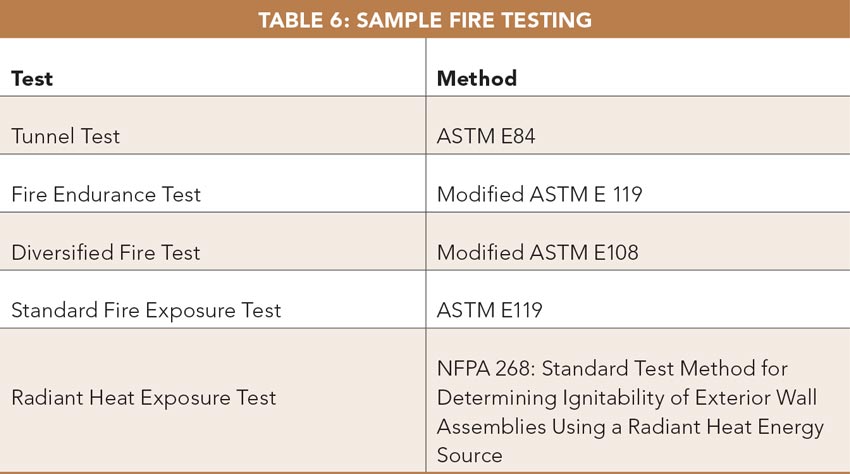
Safety
When used on the exterior, due to their lightweight, stone veneer on aluminum honeycomb panels can reduce field injury. Unlike heavy, full-thickness stone, it can be installed more easily and with less risk.
When the common stone cladding system (13/4-inch to 3-inch-thick slabs or panels of granite or marble with stainless steel anchors) is used for high-rise buildings, the stone wall system can pose a safety hazard if fire breeches the building’s exterior envelope. While the stone panels will not burn, the unreinforced stone can shatter or crack when exposed to the intense heat from a fire. This is compounded by thermal shock when firefighters spray cool water on the super-heated stone and it shatters. Since the attachment is only at the stone kerfs, the cracked stone can fall from the building, threatening the lives of people caught in the path of the heavy, falling stone.
Stone veneer on aluminum honeycomb panels are noncombustible. In the case of a fire, the panels are less likely to shatter. Instead, the stone flakes away only as small stone chips. This is much safer for emergency personnel as well as civilians around the area.
Sustainability and Energy Use Reduction with Stone Veneer on Aluminum Honeycomb Panels
The unique characteristics of stone veneer on aluminum honeycomb panels can help architects meet green building goals in a number of ways. Depending on the manufacturer, the product may help your project reduce energy usage and qualify for Leadership in Energy and Environmental Design (LEED) credits. Following is a brief summary of potential benefits.
LEED and Sustainability
Generally speaking, stone veneer on aluminum honeycomb panels:
- Reduce the amount of natural stone required
- May contain recycled aluminum content
- Improve resistance to thermal transfer
Contributions to LEED points and sustainable building design. Stone veneer on aluminum honeycomb panels can play a role in attaining LEED certification, offering durability, reduced energy use, better insulation of wall systems, space savings, an opportunity to provide healthy, comfortable, and attractive spaces, as well as savings of transportation costs when compared with traditional stone cladding systems and when compared to other building materials.
These desirable characteristics meet many of the requirements and goals of sustainable building design, including contribution to points in a number of LEED categories, including Energy & Atmosphere, Materials & Resources, Indoor Environmental Quality, and Innovation & Design.
Conclusion
As we’ve seen, stone veneer on aluminum honeycomb panel is a unique product in the architectural wall cladding industry. Proven to perform by major U.S. and international testing agencies, this product provides the beauty of authentic natural stone, such as granite, marble, travertine, and limestone, with lightweight aircraft-quality epoxy honeycomb reinforcing. The result is a product that in many ways is superior to solid dimensional stone in terms of weight, stability, impermeability to water penetration, and flexural bending and impact resistance.
Robyn M. Feller is a freelance writer and editor specializing in the architecture, design, and construction industry. www.linkedin.com/in/robynfeller
![]() |
StonePly has more than 25 years of experience in stone facades all over the world. We are the oldest and most experienced producer of stone on aluminum honeycomb still under original ownership. We offer the finest quality stone and manufacturing. From our engineers to our craftsmen, and from quarry to finished installation, we care for the product and build in quality at each step. www.stoneply.com |