Masonry Wall Systems Well Positioned to Meet Evolving Codes
New technology ups masonry’s high-performance quotient
Continuing Education
Use the following learning objectives to focus your study while reading this month’s Continuing Education article.
Learning Objectives - After reading this article, you will be able to:
- Explain why energy codes are important to the building industry and how they have affected the built environment over time.
- Discuss the prevailing energy codes and how they work together to achieve increasingly stringent energy objectives.
- Identify the characteristics of a code-compliant, high-performance wall.
- Describe the ways in which masonry wall systems can work to meet code and result in other efficiencies.
A wall is a complicated thing. It can keep a structure warm or not; let moisture in or not; improve occupant comfort or not; serve as an effective structural element or not; and be efficiently constructed and installed or not. A wall combines all of these features to play a major part in determining the energy efficiency and ultimate performance of a structure. Designers have numerous options in creating effective walls, and the government along with industry organizations have set guidelines to improve wall design practices to help reduce impacts of the built environment.
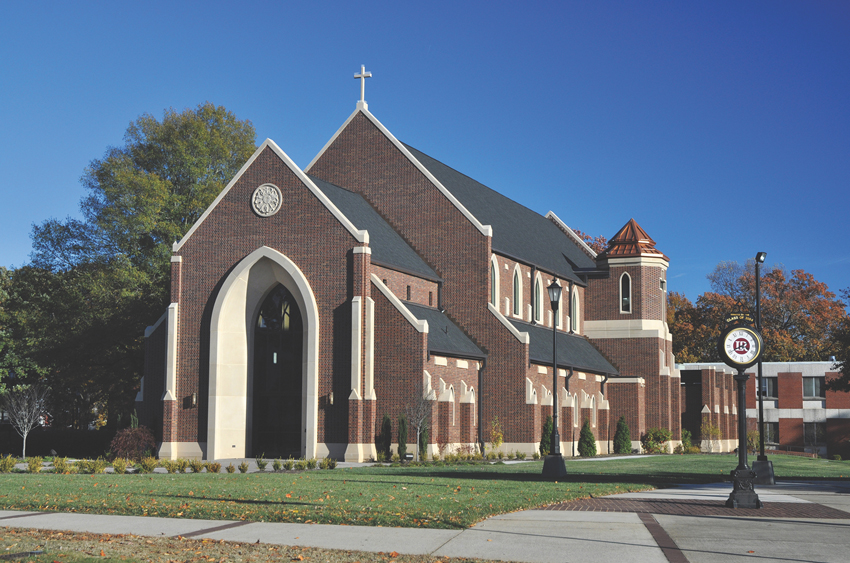
Photo courtesy of Echelon Masonry
High-performance masonry wall systems are engineered to meet and exceed codes.
A worthy goal to be sure. Widely publicized and accepted statistics point toward the impact of buildings on energy use and the environment. The World Business Council for Sustainable Develoment (WBCSD) maintains that buildings account for 40 percent of the world’s energy use.1 Besides using more energy than any other sector of the U.S. economy, in the United States, buildings account for approximately 70 percent of electricity consumption, 40 percent of CO2 emissions, and 14 percent of potable water consumption.2
Accordingly, greener targets, codes, and regulations have evolved. Energy codes are regarded as one of the quickest, most economical and cleanest ways to reduce energy use in the built environment and help ensure a sustainable future. Not only do energy codes reduce needless energy consumption and help protect the environment, they provide common benchmarks that drive new designs and technologies.
Among the most promising of these new technologies from an energy-efficiency perspective are preassembled masonry wall systems. Of course, the history of masonry is as old as the history of architecture itself. The pyramids, the Colosseum, and Notre Dame are all iconic masonry structures that have endured for centuries. Historically, masonry has been used for its longevity and low life-cycle cost, its permanence and quality, and its aesthetic value. But what’s new here are today’s masonry wall systems, which incorporate the inherent characteristics of masonry along with improved quality control, more advanced construction methods, a better understanding of masonry’s properties, and more sophisticated design. This course will review relevant code considerations, focusing on these new masonry wall systems, and how they’ve become a game changer in meeting and exceeding prevailing energy targets.
Evolving Energy Targets: The Basics
There are a plethora of energy codes and rating systems today, and making sense of them can be a labyrinthine and time-consuming undertaking. The critical theme, however, is that all of the codes are moving toward more stringent energy targets and higher R-values. A few of the major initiatives and code families are discussed next.
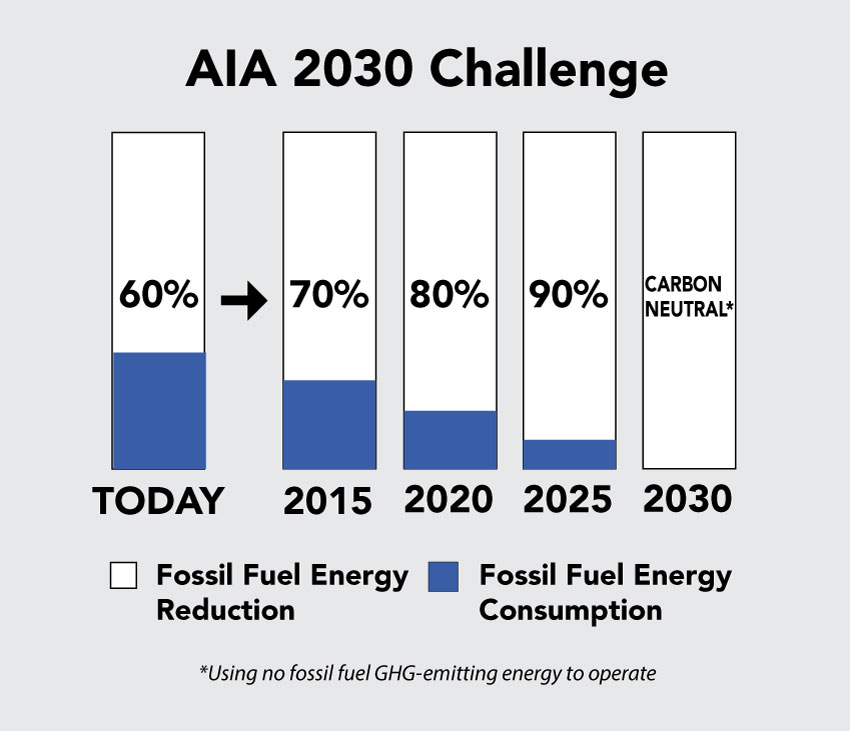
Source: © 2010 2030 Inc./Architecture 2030
The 2030 Challenge sets achievable and affordable targets to dramatically reduce the energy consumption of the Building Sector by 2040 and beyond.
Architecture 2030
Composed of several industry groups including the AIA, Architecture 2030 issued The 2030 Challenge, calling for a dramatic reduction in greenhouse gas (GHG) emissions by changing the way buildings and developments are planned, designed, and constructed. The ultimate objective: carbon-neutral buildings by the year 2030. Interim goals are also targeted: fossil fuel reduction for all new buildings and major renovations, which was increased to 70 percent in 2015, 80 percent in 2020, and 90 percent in 2025.
These goals far exceed those of the current energy codes. Architecture 2030 suggests that targets may be accomplished by implementing innovative sustainable design strategies, generating on-site renewable power, and/or purchasing (20 percent maximum) renewable energy. Of these three approaches, sustainable design strategies are by far the most important. While manufacturers can help with new and better products, the bigger opportunity falls to architects, who can employ such design strategies as building size—volume and floor space—orientation, air tightness, higher R-values, thermal mass, and continuous insulation to reduce energy costs.
ASHRAE 90.1
Rather than develop actual building codes, ASHRAE sets standards that are typically followed by such organizations as the International Code Council (ICC), the association of construction industry members that develop I-codes, which are used in the design, build, and compliance process to ensure safe, sustainable, and affordable construction. The ASHRAE standard provides minimum requirements for energy-efficient designs for buildings except low-rise residential buildings. Originally published in 1975, ASHRAE 90 has undergone multiple editions due to the rapid change in technology and energy objectives. It was updated many times, and its name was changed to the ASHRAE 90.1 standard in 2001. Many states apply the standard or equivalent standards for all commercial buildings, while others do so for all government buildings. The most recent AHSRAE update occurred in 2013.
International Energy Conservation Code (IECC)
The IECC is published by the ICC. The IECC, which references ASHRAE standards, is an I-code, a model code adopted by many state and municipal governments to establish minimum design and construction requirements for energy efficiency. Introduced in 1998, the IECC addresses energy efficiency on several fronts, including cost savings, reduced energy usage, conservation of natural resources, and the impact of energy usage on the environment. The IECC 2009 was updated in 2012 and then again in 2015, with proposals for 2018 already being considered. Each revision of the IECC ratchets up energy-performance requirements.
IECC does not mandate across-the-board changes, and its changes are only enforceable when they are adopted at the state or local level, where they may include the core provisions combined with the objectives of the adopting jurisdictions—a situation which makes it imperative that architects build to the applicable code for the jurisdiction where the project is located.
While most states have adopted some form of the IECC, many jurisdictions do not adopt new versions of the code immediately after publication. As of August 2012, the commercial code status is as follows. As of July 2016, most states and U.S. territories—43 out of 56—require ASHRAE 90.1-2007/IECC 2009 equivalent or more. Seven jurisdictions have adopted the latest codes and require ASHRAE 90.1-2013/2015 equivalent or more, and 10 have either no statewide energy code or less-efficient standards than ASHRAE 90.1-2007/IECC 2009. See the State Energy Code Adoption map for the status of state adoption of energy codes.
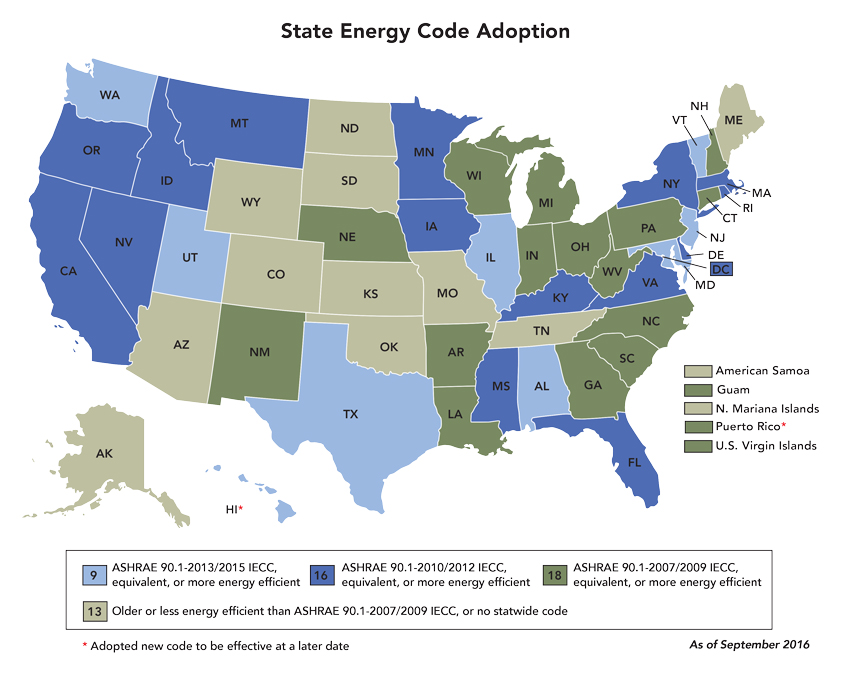
Source: EnergyCodes.gov
The U.S. Department of Energy (DOE), through its Building Energy Codes Program (BECP), has worked to enable 70 percent of states to adopt either the 2009 IECC, the ASHRAE Standard 90.1-2007 or better by 2015—a goal which has been met—and 90 percent of states to adopt these codes or better by 2017.
With the plethora of codes—ASHRAE, IECC, IBC, and state and local versions thereof—and the fact that codes frequently reference each other, it is critical that all design professional are on the same page concerning which code to follow at the beginning of the project.
IECC Iterations
The constant in all of the iterations of the IECC code is that greater energy efficiency is required. The 2012 code called for buildings that use 30 percent less energy than that required by the 2006 IECC edition. The 2015 targets of the IECC, in turn, are 20 percent above the 2012 edition.
Most of the changes in the 2015 IECC code involve HVAC, lighting, and other systems. In terms of wall design, the changes are primarily directed toward steel stud and wood-framed walls. The IECC 2015 made only minor changes regarding above-grade walls in the cavity insulation or continuous insulation requirements on prescriptive table. Masonry walls were essentially left alone, with no mandated R-value increases. This may reflect the inherent thermal value of masonry’s mass wall. The benefit of thermal mass, which is a measure of a material’s capacity to store heat for future distribution, is that its slow rate of heat transfer keeps interiors warm in winters and cool in summers. When used with complementary products or systems, concrete masonry units (CMUs) are particularly energy efficient. Mass walls can also prevent easy sound transmission, reducing noise pollution, a feature much sought after in public buildings with numerous users.
Mass walls make sense in light of the fact that ever more insulation is required as each three-year code adjustment is made. If the AIA 2030 Challenge is the timeline, the resulting template will require ever thicker amounts of insulation. Thicker insulation takes inches away from “living space,” which can be undesirable from an economic and user standpoint. In view of these constraints, mass walls present a compelling alternative to meeting increasing R-value requirements.
Compliance
Complying with R-Value requirements for building envelope components is determined by climate zone and is also impacted by building occupancy types, wall types, and the compliance path chosen.
Climate Zone: It is first necessary to determine in what climate zone the project is located. Today, there are eight climate zones for the entire United States, a vast improvement over 1989 when there were 38.
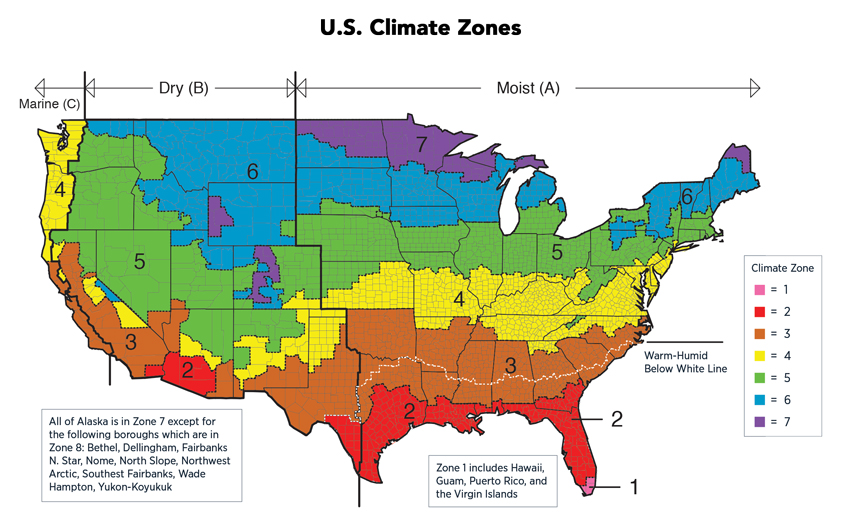
Source: U.S. Department of Energy
Building Type: The code contains one set of provisions for commercial buildings and one for residential buildings. The commercial provisions apply to all buildings with the exception of residential structures of three stories or less.
Wall Type: While the IECC has reduced the number of climate zones, R-value tables have become more complex. The commercial table lists multiple variations within each envelope component, except for walls below grade, where only one type is listed.
Compliance Path: The main compliance paths are the prescriptive and performance paths. In the 2015 IECC, there were no important changes in the prescriptive requirements. A new performance method was the Energy Rating Index, which allows builders the option of meeting a target ERI score via several performance options. This compliance method is for the residential market only, however.
Building size and complexity may determine which path to use. Smaller commercial buildings with one HVAC, hot water, and lighting system lend themselves more to a prescriptive approach, while larger commercial buildings with multiple systems, uses, and loads are more suitable to the tradeoffs found in a performance-based code.
In the prescriptive path, building design and components must meet R-values listed in the tables. Minimum mandatory requirements must be met for mechanical equipment, including lighting, HVAC, water heating systems, and electrical power systems.
While architects have traditionally used the prescriptive path, it has recently fallen out of favor because of the tedious use of tables and lack of tradeoffs. It can curtail design freedom and reflect the notion that the building is composed of separate, unrelated systems.
Prescriptive building envelope paths include R-Value and U-Factor options. Historically, every material is R-value rated. In order to meet the prescriptive requirements using the R-value method (table C402.1.3 of 2015 IECC), every wall type (mass wall, wood framing, metal framing, and metal building) is described. This prescriptive option specifies the minimum continuous insulation to be added at each assembly to meet the code.
The second, the U-factor method, allows the designer to configure the wall so that the wall assembly configured is permissible, provided its overall thermal transmittance (U-factor) is less than that specified in the code (Table C402.1.4 of 2015 IECC). Values used in the calculation of the overall U-factor are provided by the ASHRAE 90.1.
Both options aim at the same total heat loss target, but the second option (U-factor method) is less restrictive. This approach is more flexible than the R-value method.
In the IECC 2015, compliance with the first path requires compliance with ASHRAE Standard 90.1-2013, which is more stringent than ASHRAE 2010.3
Designers can use COMcheck software to see how to comply and to demonstrate compliance with ASHRAE 2007 and 2010, where allowed by the jurisdiction. It is applicable for demonstrating compliance with the three prescriptive options. Inputs include compliance the project is seeking, as well as details on the building envelope and various systems, including HVAC and lighting. A distinct advantage of using this software is that it produces not only a project summary but a certificate of code compliance for the specified code. Because of its clarity in defining a project, many states now require the use of COMcheck. The program is available for free download at www.energycodes.gov/comcheck.
The performance path offers more flexibility but involves more complex energy simulations and tradeoffs between systems; COMcheck is insufficient here for compliance. It is necessary to use ASHRAE 90.1 Section 11: Energy Modeling, which is much like LEED-required energy modeling, and takes into account actual environmental conditions and includes input on all major building systems, with mechanical and lighting systems factored into the building envelope equation.
Characteristics of a High-Performance, Code-Compliant Wall
High-performance walls have a great many elements in common. They are energy efficient, with a high R-value, high air tightness, and little or no thermal bridging. They also score high marks in moisture management, with no leaks, the ability to control condensation, and the ability to dry should moisture infiltrate the wall cavity. Other qualities include sound and fire resistance.
To promote these characteristics, a variety of code-compliant components have been developed.
Continuous Insulation
ASHRAE has required continuous insulation (CI) for many years. CI is defined as insulation that is continuous across all structural members without thermal bridges other than fasteners and service openings. The amount of insulation is climate-zone dependent and listed by ASHRAE in its 2004, 2007, 2010, and 2013 editions. There are prescriptive insulation requirements for wood-framed walls, steel-framed walls, and mass (concrete, stone, or CMU) walls for each of the eight United States climate zones.
Code requires a layer of CI in most U.S. climate zones for the purpose of limiting or eliminating thermal bridges that compromise a wall’s energy efficiency. Exterior continuous insulation has a variety of benefits. First, it reduces the condensation in the wall frame and inside the building, and the dew point of the wall is displaced toward the exterior where condensation will not cause damage.
Moisture management is critical to a successful wall and, in addition to creating a high-performance building, can head off the potential for health, legal, and financial concerns. Some moisture is likely to infiltrate even the best constructed walls, whether it is in the form of bulk moisture, capillary action, water vapor, or groundwater. Walls that control any water that has breached the cavity and enable it to drain quickly and the wall assembly to dry are the ideal.
It is important to mention that exterior CI also contributes to reducing the air leakage through the wall. For example, a rigid EPS foam continuously covering an exterior opaque wall is a contributor for reducing air leakage through the wall. It seals tears and other accidental defects occurred in the weather-resistive barrier (WRB).
Due to its mass, a masonry wall is a barrier against sound transmission. Moreover, a multilayer concrete wall like a CMU wall in addition to a veneer with insulation in the cavity gives excellent result.
The 2015 IECC, Section 402.2.1 adds language regarding multiple layers of continuous insulation and describes the installation methods for multiple CI layers, effectively upping the stringency of the 2012 IECC.3
Air Barriers
Of prime importance to designers of masonry systems are the air-barrier requirements. Air-barrier systems are comprised of a number of materials that are assembled together to provide a complete barrier to air leakage through the building enclosure. They control the unintended movement of air into and out of a building enclosure—an important consideration in reducing energy costs, as air leakage from a building can result in an increased use in energy costs of up to 30–40 percent in heating climates and 10–15 percent in cooling costs.
The 2012 version of the IECC required air barriers in both commercial and residential construction, and the directive has remained essentially the same in 2015.
According to the U.S. DOE, in the 2015 IECC, “Continuous air barriers are required except in Climate Zone 2B:
- Air barrier placement allowed inside of building envelope, outside of building envelope, located within assemblies composing envelope, or any combination thereof
- Continuous for all assemblies that are part of the thermal envelope and across joints and assemblies
- Joints and seams sealed, including sealing transitions in places and changes in materials, securely installed in or on the joint for its entire length to not dislodge, loosen or otherwise impair its ability to resist positive and negative pressure from wind, stack effect, and mechanical ventilation.”
There are two ways to comply with air- barrier requirements: Materials – C402.5.1.2.1 or Assemblies – C402.5.1.2.2.4
Fire Safety
In multistory projects where the wall assembly contains a combustible material, the IBC code requires NFPA 285 test compliancy to verify vertical and lateral fire propagation. The IBC also establishes minimum requirements for hourly fire rating based on building types, fire separation distance, and occupancy group. The fire rating of a specific wall configuration is evaluated using ASTM E119 test method.
Why Systems Make Sense
Many maintain that the best way to comply with the IEEC and other codes is a systems approach. To meet more ambitious energy targets, manufacturers have developed innovative masonry wall systems that are single solutions for thermal performance, water management, sound transmission, fire resistance and aesthetic benefits. Targeted to meeting AIA 2030 and DOE goals, these systems approaches are gaining traction in the construction industry. Further, newer systems usually have thinner and/or lighter units and often employ different anchoring techniques and CI, and have been engineered to control thermal transfer, reduce or eliminate thermal bridging, and offer air leakage and moisture control, all of which make sense from an energy-efficiency standpoint.
Systems can be tested and verified for many of these parameters. “The beauty of a wall system is that it has been designed to meet or exceed code, and can be relied upon to do so in a single efficient installation, rather than depend on a host of disparate components that may or may not work together to meet desired energy and performance targets,” says Nader Assad, masonry group manager, research and development, Oldcastle. “Often, pre-engineered systems can take the headache out of the compliance process, while reducing design and installation time and cost, and boosting efficiency and overall building performance. They can be a valuable alternative to the traditional stud framing and cavity insulation.”
Proper installation is vital to the effective functioning of any wall assembly, and installing wall assemblies with numerous elements can be time-consuming, costly, and prone to error. As a single-pass installation, these all-in-one products simplify the process, eliminating the need for adding insulation, moisture management, and finishing materials, saving associated labor costs and improving accuracy.
Masonry Foam Panel Systems
Masonry foam panel systems have the advantage of exceeding code and enabling compliance with increasingly stringent R-Value requirements, without having to add additional exterior insulation or build larger wall cavities.
Relatively new to the market, they consist of polystyrene foam panels, stainless steel screws, and specially designed stainless steel anchors that affix the masonry system solidly to the wood, steel, or concrete base wall of a building. Other elements include mortar. The type of mortar used is a key consideration and some manufacturers offer a preblended, proprietary mortar that complies with ASTM C270 and enhances pumpability, bond strength, flexibility, and dimensional stability.
To meet aesthetic goals, a variety of masonry units are available, including durable stone, clay, and concrete brick with others under development. Masonry units are friction fit in the foam, with different types of units having different foam panels. Press fit is only temporary until the mason finally points the mortar at the joints of the veneers. The veneers will be mechanically linked to the base wall through the anchors that are embedded in the mortar as per typical anchored masonry installation.
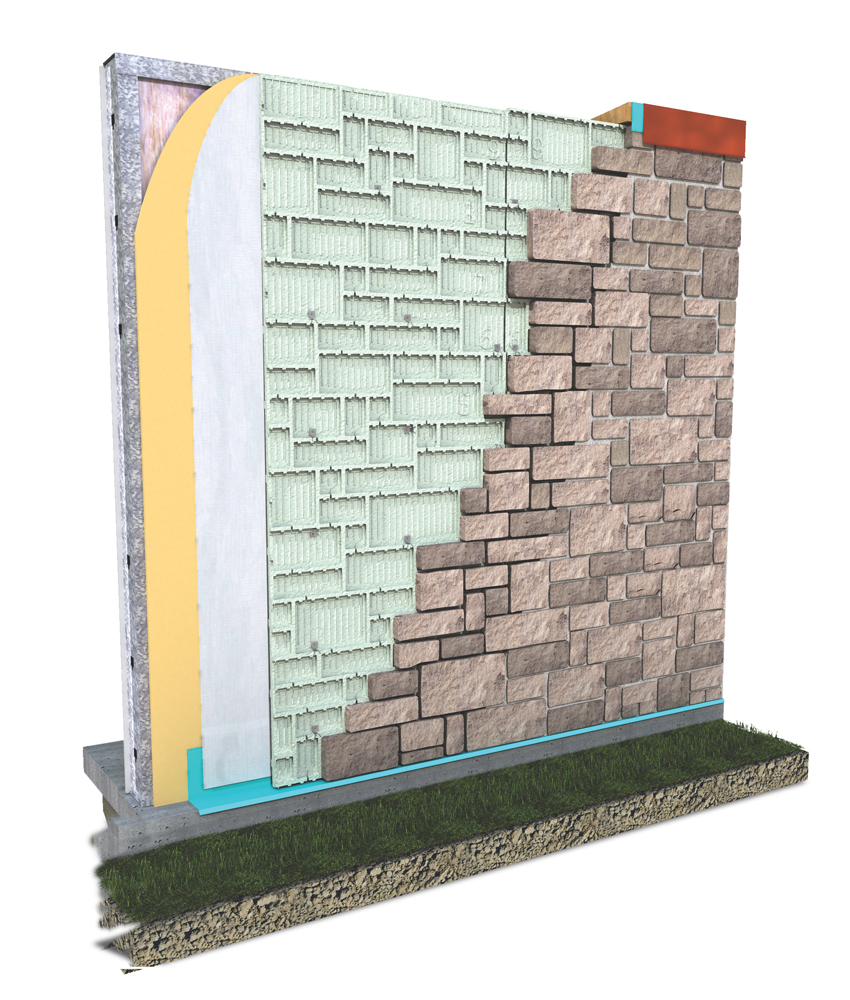
Photo courtesy of Oldcastle Architectural
Masonry veneer foam panel wall system
The foam itself is critical to the performance of the system. The engineered drainage channels on both sides of the insulation panel evacuate any water that may infiltrate the wall and protects the structure from damages over a lifetime of moisture exposure. Masonry units insert easily into the designed cells of the foam panels for quick installation, with stone, clay, and concrete brick options offering aesthetically pleasing designs.
Foam panels can provide high R-values, 9.2 steady state, and include CI. They also afford acoustical comfort with an STC rating of 61 on steel stud framing, which signifies that most sounds are inaudible, a superior soundproofing.
Foam systems have been proven to resist wind speeds up to 130 miles per hour (depending on building parameters) according to ASTM E330, with no lasting deformation. This characteristic virtually eliminates the risk of structural damage. Fire-resistance criteria, notably NFPA 285 and ASTM E119, assures that tested foam walls have successfully withstood 1 hour of exposure to temperatures of more than 1,700 degrees Fahrenheit. Foam panel systems may be used over any exterior fire-resistance-rated assembly without changing the assigned hourly rating up to 2 hours. Some of these systems may also be installed in seismic zones A to D. Regarding thermal requirements, foam panel systems can be installed on metal-frame or wood-frame buildings up to climate zone 6. Zones 7 and 8 may also be addressed by evaluating the building characteristics and installation details.
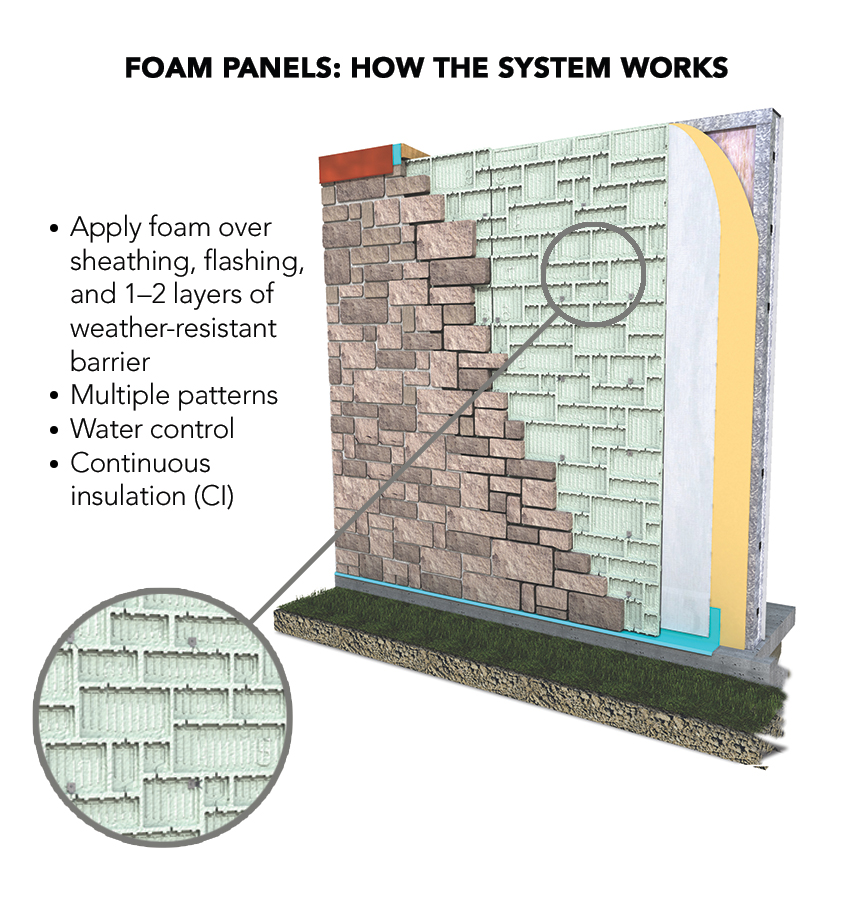
Photo courtesy of Oldcastle Architectural
Architects interested in specifying foam panel systems should make sure the product meets the above mentioned criteria. In fact, it is advisable to look to those manufacturers that have obtained third-party testing and evaluation of their products. An Evaluation Service Report (ESR) given by an accredited certification agency will provide a summary report of structural performance and durability of the system.
Insulated Concrete Masonry Systems (ICMS)
A complete insulated concrete masonry system (ICMS) consists of a pre-assembled structural masonry unit, an insulation insert, and a thin veneer face. Furthermore, the system consists of all necessary components to address every aspect of the building, including the inside and outside corners, the window and door openings, and services, maintaining a fully thermally broken envelope. The most advanced assembly includes a high-performance expanded polystyrene (EPS) molded insulation insert, giving the assembled unit a total effective R-value of 16.2 at 75 degrees Fahrenheit.
The Engineered EPS inserts are designed with a vertical shiplap, and the system also includes a closed-cell foam gasket installed on the horizontal joint. These features ensure no air leakages, while maintaining a continuous insulation.
At their best, ICMS meet IECC Energy code requirements from zones 1 through 7. Without any other layer, just a coat of paint on the inside, some of these systems can cover up to zone 6. With the addition of lath and gypsum layer in the inside the wall, many systems can address all climate zones.
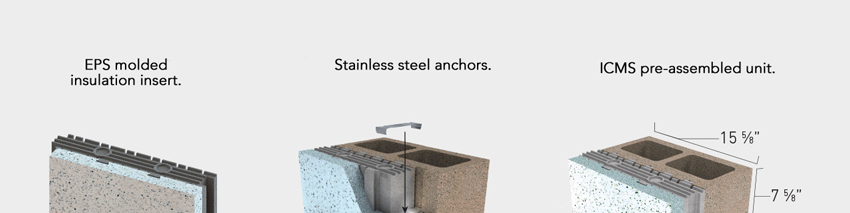
Image courtesy of Oldcastle Architectural
Insulated concrete masonry systems are a single solution for energy efficiency and water management.
Those systems with stainless steel metal anchors molded into the EPS inserts enjoy superior structural stability and ensure a safety connection to the back wall during windloading and for fire safety. With the veneer and anchors, the wall system can withstand up to 200 miles per hour of wind speed.
Because it does not readily corrode, rust, or stain with water as does ordinary steel, stainless steel anchors can be effective in salt water or coastal environments. Some systems include two additional drainage planes at each side of the continuous insulation for more effective moisture management which is particularly useful as the building ages and water infiltrates cracks in the mortar. These drainage planes eliminate the likelihood of mold and mildew.
A typical finished size is 12 inches by 8 inches by 16 inches. These insulated systems are also fairly adaptable in size, shape, and density, which eliminates the need to glue together multiple boards to achieve the desired insulation thickness—a characteristic that enables designers to achieve R-value targets in a thickness-constrained application. In the face of increasing R-value targets, these insulated systems are considered perhaps the best opportunity to easily adapt as a slight increase in insulation thickness can provide the necessary thermal performance.
Masonry Wall Systems Make Sense for Evolving Energy Targets
Energy-efficiency targets have been steadily becoming more rigorous, and the future promises more of the same. Masonry wall systems take advantage of the inherent value of masonry—thermal mass, durability, low life-cycle cost—in an all-in-one cladding solution to meet and exceed code. With the ability to be tested and verified as a single component, wall systems have gained favor over alternate methods with disparate components that may or may not work together to achieve the parameters of wall performance—energy efficiency, moisture management, air tightness, sound insulation, and fire protection.
End Notes
- “Transforming the Market: Energy Efficiency in Buildings.” The World Business Council for Sustainable Development (WBCSD). Web. 7 October 2016. www.wbcsd.org/transformingthemarketeeb.aspx.
- Benefits of Green Building.” U.S. Green Building Council (USGBC). 1 April 2016. Web. 7 October 2016. www.usgbc.org/articles/green-building-facts.
- Mukhopadhyay, Jaya et al. “Comparing The Commercial Provisions of the 2015 IECC with the Corresponding Provisions in the 2012 IECC for Commercial Construction in Texas.” November 2014. Web. 7 October 2016. esl.tamu.edu/docs/terp/2014/ESL-TR-14-11-04.pdf.
- 2015 IECC Commercial Scope and Envelope Requirements.” Building Energy Codes Program, U.S. Department of Energy. Web. 7 October 2016. www.energycodes.gov/sites/default/files/becu/2015_IECC_commercial_requirements_envelope.pdf.
- Straube, John. “BSD-163: Controlling Cold-Weather Condensation Using Insulation.’’ Building Science Digests. Building Science Corporation. 15 November 2011. Web. 7 October 2016. buildingscience.com/documents/digests/bsd-controlling-cold-weather-condensation-using-insulation.
![]() |
Echelon is the consolidated brand for all masonry products and services of Oldcastle Architectural including Trenwyth® Architectural Masonry, Artisan Masonry Stone Veneers®, Quik-Brik® Concrete Masonry Units, Amerimix® Bagged Goods and a complete portfolio of Performance Upgrades. As a single source masonry portfolio solution, Echelon delivers consistent, reliable product manufactured locally at more than 170 locations and delivered by an unrivaled logistics network. For more information, call (844) 495-8211 or visit EchelonMasonry.com |