Sustainable Envelopes with Structural Engineered Bamboo
Engineered Bamboo Products (EBPs) deliver structural, and renewable, bio-based solutions for high-performance building enclosure systems
Continuing Education
Use the following learning objectives to focus your study while reading this month’s Continuing Education article.
Learning Objectives - After reading this article, you will be able to:
- Describe engineered bamboo and LVB as high-performance, bio-based, and rapidly renewable green building materials and related building methods.
- Discuss typical applications of structural bamboo products to building envelopes and structures that increase the use of rapidly renewable materials.
- Identify general criteria for designing building envelope systems with engineered bamboo and LVB, including codes and standards, for greater use of rapidly renewable bamboo.
- Explain how recent developments in structural bamboo products and LVB construction products apply to various envelope options and performance needs for high-performance green building.
Bio-based material technology companies are developing a range of new products that improve both building sustainability and performance. In some cases, these architectural materials and systems also increase efficiencies in design and construction. One prominent example has emerged over the past decade with the introduction of dimensional, prefabricated components of performance-grade engineered bamboo. The benefits of the bamboo structural products are especially evident in the design of building envelopes and enclosures, from curtain walls to windows to rainscreens.
Employed for building structures and other architectural and original equipment manufacturer (OEM) applications, the bamboo-based panels, dimensional components, and hybrid systems offer warm, natural aesthetics. Yet engineered bamboo products (EBPs) can replace timber and engineered wood in architectural works where higher performance is desired, both in terms of sustainability and dimensional stability. Architects are beginning to find that structural engineered bamboo can serve well in contexts where metal, steel, or extruded aluminum assemblies are the norm. Hybrid solutions are also more common in recent years, a design approach pairing bamboo with steel, concrete, and other structural materials.
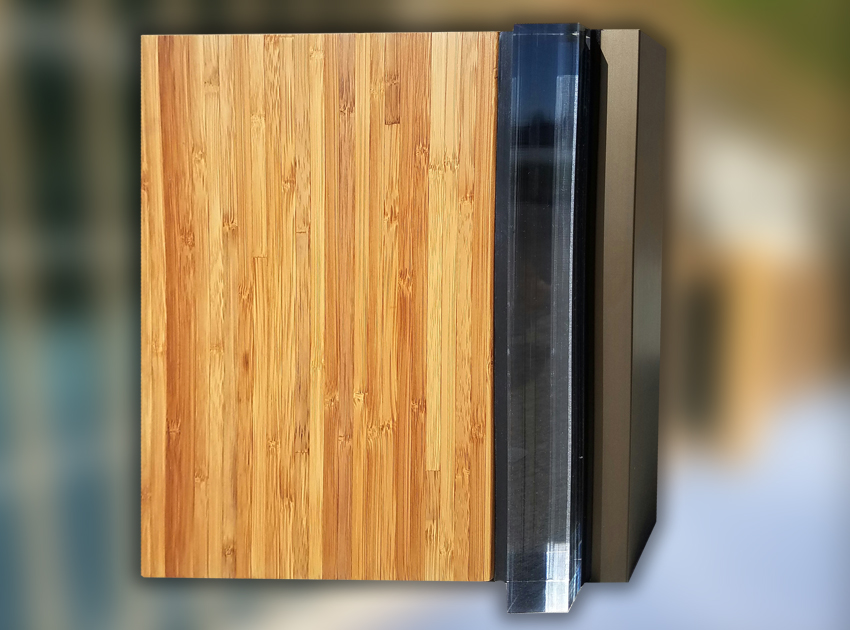
All photos courtesy of Lamboo Technologies
Modular, prefabricated components of performance-grade engineered bamboo are used for building enclosures to provide high performance, sustainability, and dimensional stability.
Part of the benefit is for increasing the use of rapidly renewable materials—bamboo-based materials—in green building construction to include structural components that are typically made with wood, plastic, metal, or concrete. With increased use of engineered bamboo, building projects may qualify for several credits toward LEED v.4 certification, including:
- EAc2: Optimize Energy Performance
- MRc3: Sourcing of Raw Materials
- MRc4: Material Ingredients
- EQc2: Low-Emitting Materials
- Inc1: Innovation
Behind the scenes, manufacturers are discovering ways to boost the performance of engineered bamboo to achieve greater sustainability as well as improved durability, uniformity, and strength. This means that architects and end users can rely on structural engineered bamboo for longer spans, larger loads, and more extreme conditions. Facilitating these advancements are manufacturing enhancements to make stronger and more durable glulam beams and common dimensional components, as well as hybrid structural solutions and complete systems. In addition, more options are available to project teams needing assistance in using EBPs. For architects, today’s manufacturers of EBPs offer EBP consulting, shop drawings, detailed structural system analysis, engineering, custom three-part specifications, fabrication, and installation advice as needed for their projects.
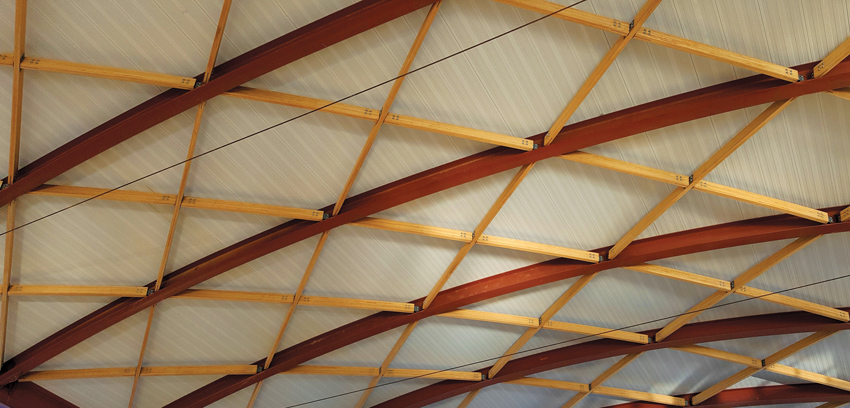
Williamson County Regional Airport terminal project in Marion, Illinois, the A/E firm RS&H has designed a domed roof structure with hybrid steel-and-bamboo cross bracing.
For these reasons, EBPs, as well as laminated veneer bamboo (LVB) materials are increasingly used for building exteriors and as exposed, load-bearing members. For sustainable buildings and LEED-certified projects, EBPs are used for facades, cladding, curtain walls, structural glazing, as well as a range of window and door solutions.
The use of engineered bamboo for structural systems have been well established. What is changing is the variety and creativity of uses in recent building designs. An example of this is the Williamson County Regional Airport terminal project in Marion, Illinois, designed by the architecture and engineering firm RS&H. As seen in the above picture, it has a novel domed roof structure with hybrid steel-and-bamboo cross bracing for a central atrium. The structural bamboo beams are visible in the ceiling within the terminal and provide a unique design feature to this project.
Other examples include an entry for the U.S. Department of Energy’s Solar Decathlon by the University of Illinois at Urbana-Champaign, using engineered laminated bamboo for structural elements and reclaimed barn wood cladding. Certified by the U.S. Passive House Institute, the innovative project called Gable Home uses 90 percent less energy than typical construction.
According to the university’s assistant professor Mark Taylor, “Using laminated veneered bamboo helped our team become the first competitors in the DOE’s Solar Decathlon competition to achieve Passive House Certification, both at the competition site and back in Illinois, where the house returned after competing in the 2009 event.”
Engineered Bamboo: Context and Background
Considered an alternative material technology, engineered bamboo takes advantage of “a rapidly renewable material that has many applications in construction,” according to Dr. Bhavna Sharma, a structural bamboo expert and lecturer at the University of Bath’s Department of Architecture & Civil Engineering. “Engineered bamboo products result from processing the raw bamboo culm into a laminated composite, similar to glue-laminated timber products.” Dr. Sharma continues by stating, "This bio-based resource also resembles wood in its mechanical properties, yet it has a faster growth rate and harvest cycle."1 In addition, bamboo is found in many places where softwoods and hardwoods are limited.
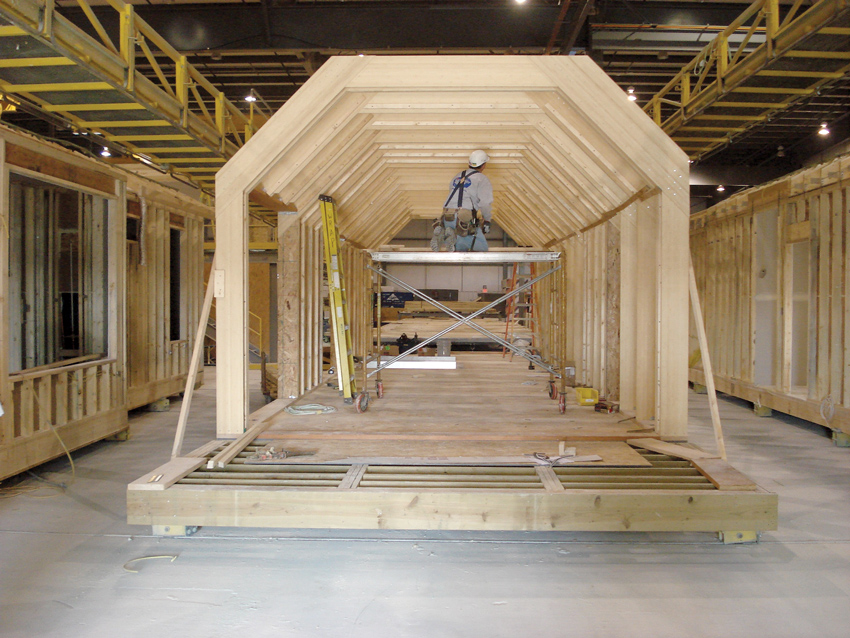
Gable Home – Solar Decathlon entry by the University of Illinois at Urbana-Champaign utilizing engineered laminated bamboo for the structural elements
Essentially a giant grass, the bamboo plant comprises a hollow, tapering culm (stalk) of longitudinally oriented fibers divided by nodes. From the interior to the exterior, the bamboo fibers increase in density. These fibers are essential to creating structural-grade engineered bamboo. One manufacturing method produces strand-woven or parallel-strand bamboo, made from crushed fiber bundles soaked in resin and treated under pressure to create solid, dense slabs. A second method, known as laminated bamboo, also maintains the longitudinal fibers as the parallel-strand process does, but it also takes advantage of the natural culm matrix. The bamboo stalks are cut and planed, and then processed as desired prior to the lamination and compression in board form. This process typically utilizes less adhesive and tends to provide higher strength-to-weight values.
Today, attention has shifted to applications by architects, engineers, and OEMs for interiors, exteriors, and structures. The strength and efficiency of EBPs and SBPs—along with the positive carbon footprint of rapidly renewable bamboo—make it a suitable choice for high-performance buildings. Yet, adherents within the industry and the construction community have focused on how to design with structural bamboo products. The findings have included innovative architecture on the one hand, and on the other hand a raft of innovations in modularity, system integration capabilities, and installation techniques. The products are also engineered for a high degree of uniformity and consistency, ensuring tolerances within those required for building enclosures and structures.
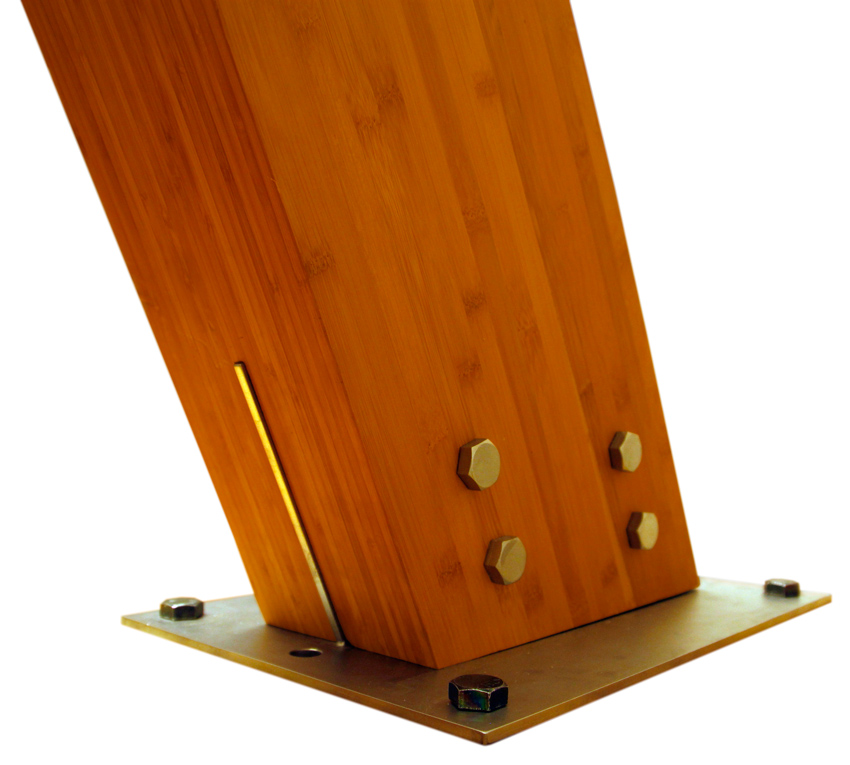
Engineered glulam beam made of laminated veneer bamboo (LVB) incorporating stainless steel plating and hardware
Engineered bamboo products are engineered for uniformity, consistency, and typical construction tolerances so they can be used just as readily as steel, aluminum, or plastic components. As a result, structural bamboo can now be incorporated into an architectural project’s envelope just as readily as its steel, aluminum, or plastic counterparts. In some cases, as is outlined in this course, there are advantages to using bio-based materials over traditional metals and other structural systems.
Enclosure Systems and Structural Bamboo
For such varied enclosure systems as fenestration, curtain walls, and rainscreens made with engineered bamboo products offer a few inherent advantages. While the engineered bamboo functions in ways similar to hardwoods and can be worked with standard carpentry tools, it can be more sustainably sourced, and it tends to have very minimal shrinkage and better dimensional stability. Engineered bamboo products have natural antimicrobial properties so they resist moisture build-up and through unique processing methods can help prevent decay or rot from the core of the materials. Bamboo's high silica content acts as a natural insect deterrent. Engineered bamboo tends to have a slightly higher density than common hardwoods, which increases its capacity to be used in applications where traditional hardwoods would perform poorly.
These products also offer aesthetic attributes where other materials used in these applications need to be covered up by additional building materials to achieve a certain look wanted by the architect and designer. Bamboo provides a unique aesthetic that can be admired by the end user. The unique look of engineered laminated bamboo is becoming more accepted and appreciated by today’s architects and designers looking for a natural product that does not need to be covered up by additional building materials which help reduce overall cost of time and labor in projects.
In summary, SBPs can be described as similar to wood glulams but with more functional consistency and better dimensional stability, all things being equal. SBPs also can provide reduction in overall cost for projects by reducing the need to utilize additional building materials to cover up the exposed engineered bamboo materials.
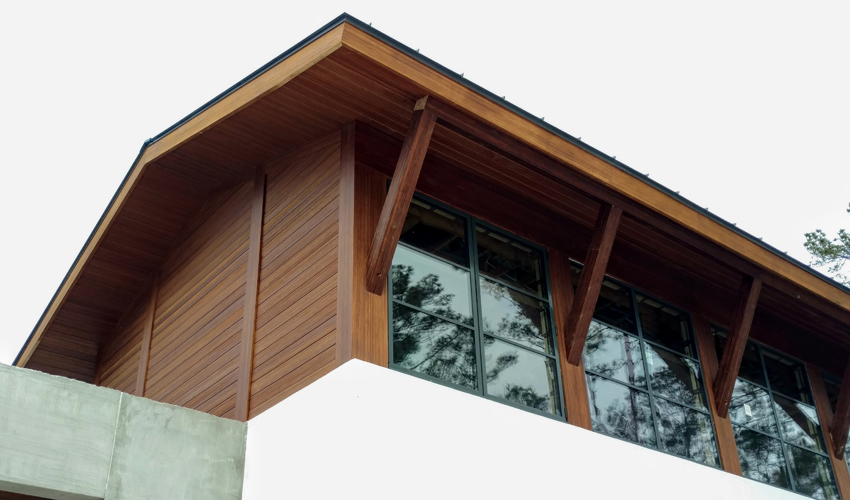
Engineered bamboo products used as rainscreen and structural supports for the overhang
Studies conducted by the University of Bath’s Dr. Bhavna, using common wood standards to allow comparison with engineered timber products, have shown that engineered bamboo boards or “scrimber” and laminated bamboo have properties that compare with or surpass those of timber.1 Other testing results by industry groups, such as PFS, Inc., show that high-performance engineered laminated bamboo members, tested parallel to the grain, have compressive strengths exceeding 8,300 psi per ASTM 3501-86A and tensile strengths of between 8,700-9,000 psi. The dimensional stability, tested per ASTM D 1037, shows the products to be more stable in varied environmental conditions. Summarizing the results, engineered SBPs:
- have mechanical properties comparable to hardwoods.
- exhibit compressive strengths greater than softwoods.
- have tensile strengths greater than other wood species.
- are more dimensional stable in moisture and temperature changes when compared to timber-based product (dependent on wood species).
In order to allow for system modularity, which translates into efficient architectural integration, SBPs are available as standard shapes, including beams, glue-laminated (glulam) members, exposed trusses and members, as well as hybrid assemblies in combination with cold-formed steel joists. Similar to timber glulams, engineered bamboo products are available through catalogs of modular structural components, which can be pre-assembled and serve as elements of pre-engineered construction systems. To include wood joinery techniques and structural connections, these members are fitted with steel plates and clips as well as pre-drilled to allow for efficient jobsite connection.
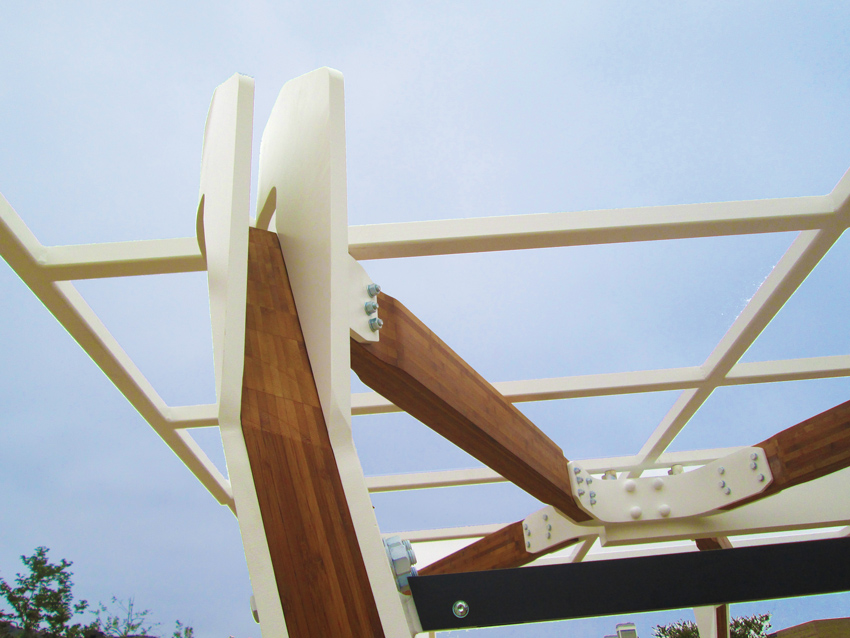
Structural bamboo products (SBPs) custom fabricated and used in conjunction with powder coated steel and dipped hardware
In other cases, some building companies are adopting modular construction approaches using engineered bamboo. In these project delivery methods, the buildings (or elements of the building) are constructed off-site under controlled fabrication conditions to meet all design needs and prevailing codes and standards. Produced in modules, the resulting structures can be assembled and put in place typically in less time than conventional, site-built facilities, according to the Modular Building Institute.2
Applications of engineered bamboo for modular or conventionally constructed high-performance enclosures and exterior structures include curtain walls, sunshade systems, canopies, and trellis components. In addition, architects can specify modular and prefabricated solar structures or design any exposed post-and-beam assemblies using pre-engineered bamboo members. Laminated veneer bamboo (LVB) can also be used as rainscreen cladding on SBP substructures. Engineered bamboo is also used for roof beams, curved beams, rafters, and columns, as well as intermediate purlins or substructures. Products for structural and enclosure applications most prevalent on the market today include:
- Structural glazing: This comes in the form of curtain wall members, storefront system components, and system and installation integrated as a thermally high-performance hybrid aluminum/SBP.
- Structural bamboo products (SBPs):These include fabricated common dimensional components, glulam beams, and hybrid structural applications. Manufacturers and glu-lam fabricators can offer consulting, shop drawings, structural system analysis, engineering, and installation support for architects working with engineered bamboo.
- Enclosure and exterior products:These include window and door components that are integrated into glazing solutions to provide efficiency and continuity within turnkey glazing systems. Rainscreen systems include exterior wall/ceiling cladding and siding solutions, soffit, fascia, exterior products, including awnings, site furnishings, and playground equipment, bollards, trellises, and more.
- High-performance, sustainable buildings: In these structural and nonstructural applications, SBPs may contribute to as many as five LEED credits, depending on the application and project details.
Applications For Structures and Enclosures
For these and other typical bamboo construction applications, SBPs and EBPs are available in two grades: exterior grade and structural grade. Solid exterior grade EBP may be specified in 07, such as 07412 (wall panels) of the Construction Specifications Institute (CSI) Manual of Practice and MasterFormat. For structural grade SBPs, the specification is typically within division 06, the section that also accommodates parallel-strand lumber, glue-laminated beams, engineered wood products and structural timber, and rough carpentry, among others.
Several ASTM International standards may be referenced for the structural grades of engineered bamboo. Most relevant is the ASTM D5456: Standard Specification for Evaluation of Structural Composite Lumber. This standard, developed with the ASTM Technical Subcommittee D07.02.03 on Structural Composite Lumber, may apply to cellulosic materials used for structures and veneers. For that reason, engineered bamboo falls under the auspices of the Technical Committee (TC) D07, which interfaces with various TCs, including E06 (Performance of Buildings), E05 (Fire Standards), D14 (Adhesives), and C16 (Thermal Insulation). In addition to standard D5456, architects may also reference other standards in project construction documents, which among others may include:
- D1037: Standard Test Methods for Evaluating Properties of Wood-Base Fiber and Particle Panel Materials
- D1761: Standard Test Methods for Mechanical Fasteners in Wood
- D5055: Standard Specification for Establishing and Monitoring Structural Capacities of Prefabricated Wood I-Joists
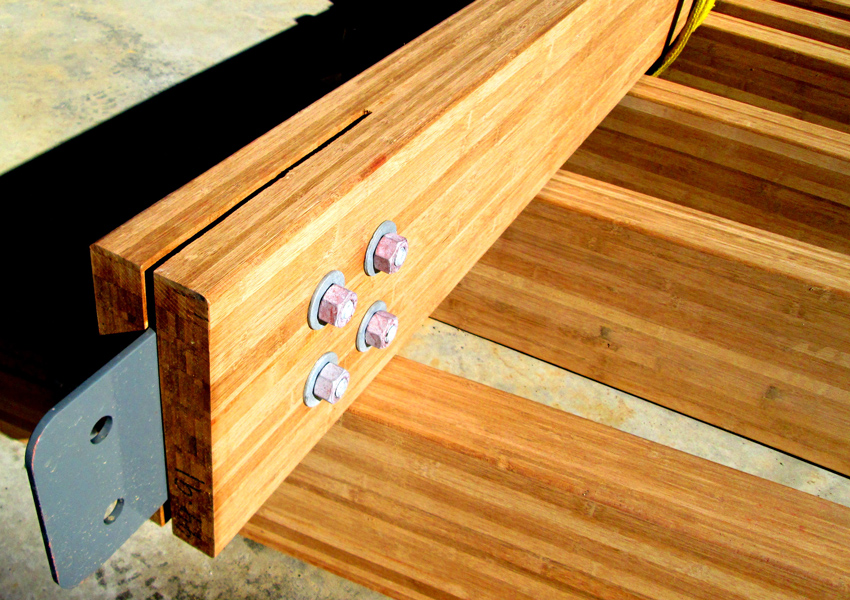
Standards, such as ASTM sD5456: Standard Specification for Evaluation of Structural Composite Lumber, apply to cellulosic materials used for structures, including engineered bamboo, such as for these structural beams used at an Illinois airport.
Though the products had been in use previously, in 2010, a watershed moment arrived for the structural application of engineered bamboo. For SBPs and the structural grades of manufactured bamboo products, that year ASTM announced an imminent revision to D5456 that “would add bamboo as a fiber material that can be used in the manufacture of products covered in the standard,” said the group. According to ASTM staff member Kevin Shanahan, director of standards development, “D5456 was originally approved in 1993 and specifies the procedures necessary for a group of engineered wood composite products to be evaluated for all structural design properties that would allow them to be used as substitutes for solid sawn lumber and glue-laminated timbers in residential and commercial building construction.”
Today, instead of referencing only traditional wood species used for solid sawn lumber, D5456 has been revised to include bamboo as another lignocellulosic fiber material—in other words, biomass—that can be used in the manufacture of these products.
The historic addition of bamboo to the standard came in the 2012 edition of the Annual Book of ASTM Standards, listing LVB as a certified product for structural applications under ASTM 11a 5456, with the heading “Evaluation of Structural Composite Lumber Products.” At the time, the broadening of the standard was hailed by some sustainability advocates and others interested in increased use of rapidly renewable resources, such as bamboo. In fact, it was the first addition in more than three decades of a bio-based structural material to the ASTM annual compendium.
While the ASTM standards added to the appeal of EBPs, the International Code Council (ICC) had already intoned on use of engineered bamboo for structural applications. In a 2009 meeting in Birmingham, Alabama, a vote passed to make LVB a newly ICC accredited product for the following year. Engineered bamboo had been used for years as a finish product, including widespread adoption for wood-look flooring.
Prior to that, the product category had its own criteria, AC162: Structural Bamboo, released in March 2000 with test methods, allowable design stress criteria, and other design considerations. This was the first codes document to recommend ASTM D5456 as a quality-control standard. It also provides reference to the International Network for Bamboo and Rattan (INBAR) Standard for Determination of Physical and Mechanical Properties of Bamboo.
It is valuable to note that the novel engineered structural component products made with bamboo culm do not perform identically to those made from traditional wood species. The bamboo-based products tend to have better dimensional stability than engineered wood, while their greater density also increases thermal transfer slightly over their wood-based cousins.
Sustainable Facades and Cladding
With bamboo-based structural elements readily employed as glulams, LVL, and structural composite lumber, architects and project teams have increasingly designed facade systems, such as cladding, storefronts, and curtain walls, using SBPs. Among the most promising approaches for storefronts and curtain walls is a thermally high-performance hybrid of extruded aluminum framing attached to SBP members for vertical members, mullions, muntins, and horizontal rails. Although non-load bearing as with all curtain walls, as a backup system, these hybrid members support the weight of the glass framing, effectively transferring that weight back to the structure. The engineered bamboo members are generally left exposed, which is ideal for the aesthetic characteristics of the materials. A variety of companies have begun utilizing SBP members into their product offerings to the glazing market.
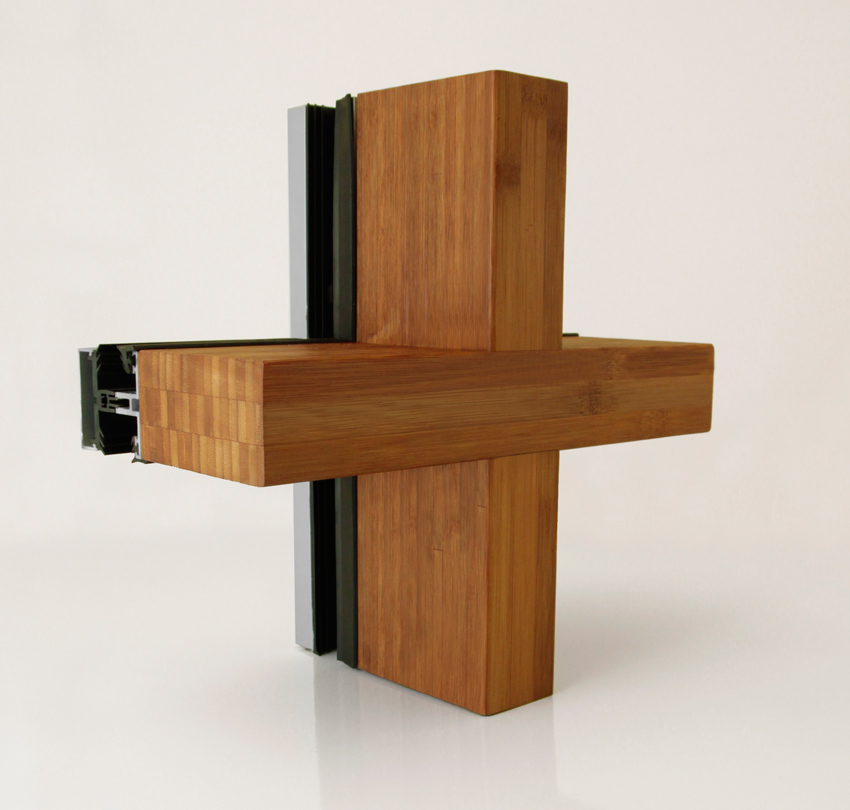
In curtain wall systems, glazing can be secured to hybrid aluminum and EBP backup systems using a captured glazing, structural silicone, and point-support systems. Mullion caps of profiled aluminum or engineered bamboo provide a finished look.
In these curtain wall systems, the glazing can be secured to the hybrid aluminum and SBP backup systems using a variety of typical approaches, including captured glazing, structural silicone, and point-support systems. Mullion caps of profiled aluminum or engineered bamboo provide a finished look, inside and out. In fact, the bamboo members replace a large portion of the aluminum typically associated with window walls, storefronts, and curtain wall systems—and they can replace the backup supports as well. The result is a wood-hued bamboo grid, with its pleasing texture and warmth.
Recent projects have included a split-mullion design by one architect, adding a unique and complex look to the SBP members in the curtain wall grid. Instead of a solid mullion, the vertical members appear as two side-by-side lengths of engineered bamboo separated by a 1-inch or 2-inch gap. Door details by some millwork and window makers have also been tailored to complement the clean sightlines of recent curtain wall designs.
Expanding this design language with a more consistent materials palette, some architects have used matching sunscreens and shading devices of engineered bamboo to complement the storefronts and curtain walls. Others have added trellises, pergolas, and other matching EBP structures and finishes. In some cases, the curtain wall and storefront systems are matched with load-bearing columns of structural bamboo in front of or behind the facade. High-performance laminated bamboo is applied to beams, glulam members, exposed trusses, and hybrid steel/SBP assemblies.
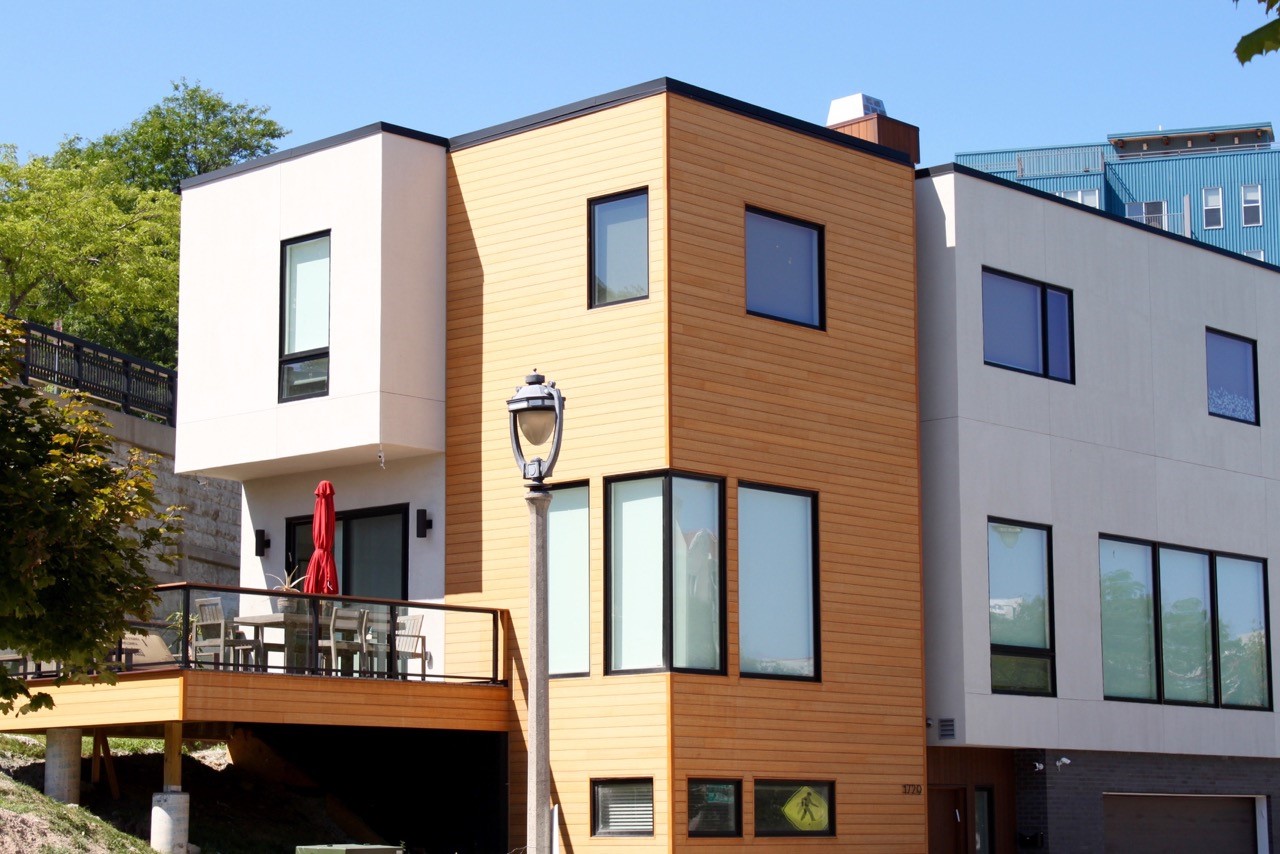
Engineered bamboo facades can be matched with sunscreens and shading devices of the same materials, as well as load-bearing columns, beams, glulam members, exposed trusses, and hybrid steel/SBP assemblies.
In general, these structural elements compare favorably with lumber, plywood, and wood composite products. SBPs have comparable strength properties to other hardwoods but offer better dimensional stability as well as contemporary aesthetics and sustainable characteristics not found in traditional or exotic woods and other engineered products. With further developments in exterior treatments as well as adhesives and binders, SBPs are expanding in areas well beyond where traditional soft and hard woods can be utilized. In terms of pest resistance, testing has indicated that bamboo processed with borate pressure treating prior to lamination records 100 percent termite mortality. Durability against wood-destroying fungi is very high due to the inherent antimicrobial properties of bamboo, with some variation expected based on proprietary treatment and curing processes employed. Many of the EBPs and SBPs are indigestible to insects and microorganisms, helping improve their durability and resiliency.
Due to the aesthetic characteristics of the materials, engineered bamboo is best utilized in situations where it is left exposed. This is a key advantage in regard to cost associated with additional labor and materials now not needed to cover up the exposed materials as done with typical wood glulam beams or structural members. SBPs have already appeared in the window and door industry, where structural stability is a must. This allows window and door manufacturers the capability of producing dimensionally stable members that meet a broad range of project needs. With these offerings, EBP and SBP have found a following among architects working in both residential and commercial building types.
For Rainscreens and Exterior Wall Panels
For cladding uses, exterior grades of engineered bamboo include SBPs and LVB, which are available in several color and grain options. Solid LVB can be used as single-skin panels and related cladding components for various types of envelope construction, including rainscreens, soffit panels, siding, fascia, and hybrid systems with other materials. Typically, the products must be specified to meet reference standards, including ASTM E84: Test Method for Surface Burning Characteristics of Building Materials; the European National Standards’ EN 438-2: Decorative Panels/Engineered Panels; or the corresponding DIN standard by the German Standards Institute.
To design exterior systems with solid LVB, architects can select from a variety of standard components from 8 feet to 16 feet in length. Standard products include 4-foot by 8-foot panels in thicknesses of 1/2 inch, 3/4 inch, and 1 inch. The SBP and LVB products are then complemented with attachment hardware. This hardware can be based on a variety of steel and aluminum clipping systems. The SBP and/or LVB can also be applied directly to the exterior or interior substrate of the building with stainless steel fasteners.
For rainscreens, systems available from fabricators include standard dimensional lumber size slats with pre-engineered corner details and window trim. Detailed similar to other rainscreen systems, the LVB panels are hung with clips on predrilled furring strips leaving an air space between the panels and the sheathing behind, which is usually faced with an air/moisture barrier. Other clipping systems can be used that do not use furring strips as well.
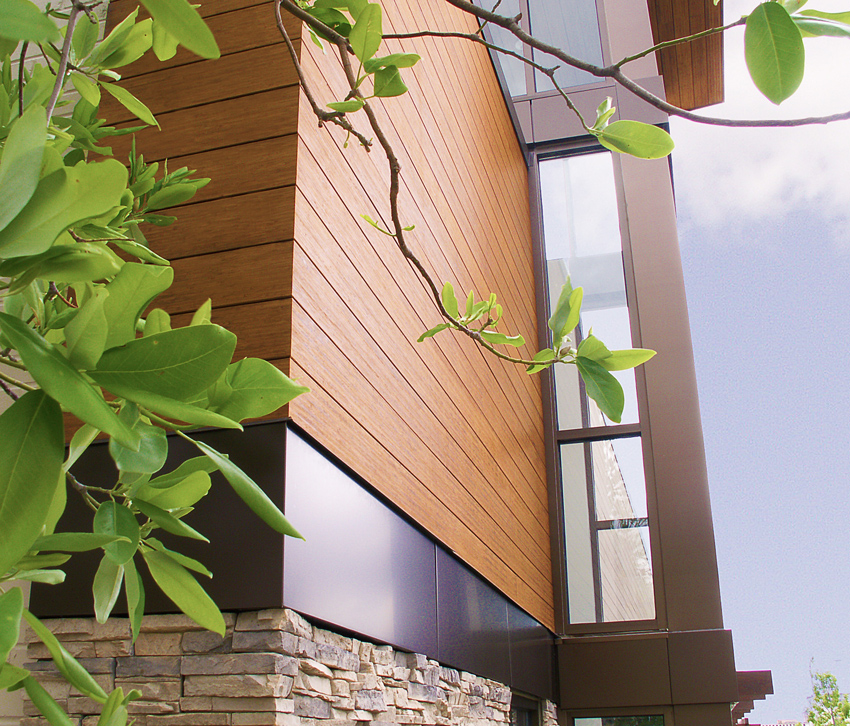
For rainscreens, systems available from fabricators include standard dimensional lumber size slats with pre-engineered corner details and window trim. The LVB panels are hung with clips on predrilled furring strips, with an air space and air/moisture barriers.
Mechanical properties for the LVB rainscreen panels are similar to those for engineered bamboo products used for structural and glazing systems. They exhibit high tensile strength parallel to grain and higher dimensional stability than wood-based counterparts. The fire rating for typical LVB panels are rated Class B per ASTM E84. Manufacturers are continuing the research for topical and premixed stain applications, which will help LVB achieve a Class A fire rating.
In terms of rainscreen design options, LVB panels are finished in standard colors created by various kinds of thermal treatment. The coloration visible from the exterior carries throughout the entire material. A variety of stains are also available, should a project require a specific tone. A variety of stain and finish systems are currently available on the market that can be used to coat LVB products. It has been found through testing that most water-based systems do not work well with LVB products. With the new stain and finishing advancements in nano-technology and water-borne systems, sustainable coating options are becoming available to complement the sustainable nature of LVB products.
Any visible structural bamboo can be similarly treated to match the rainscreens. This includes beams, columns, and trusses, as well as prefabricated layups and curtain wall systems. With these products, virtually all of the structural needs for a given building projects can be addressed using LVB and SBP components.
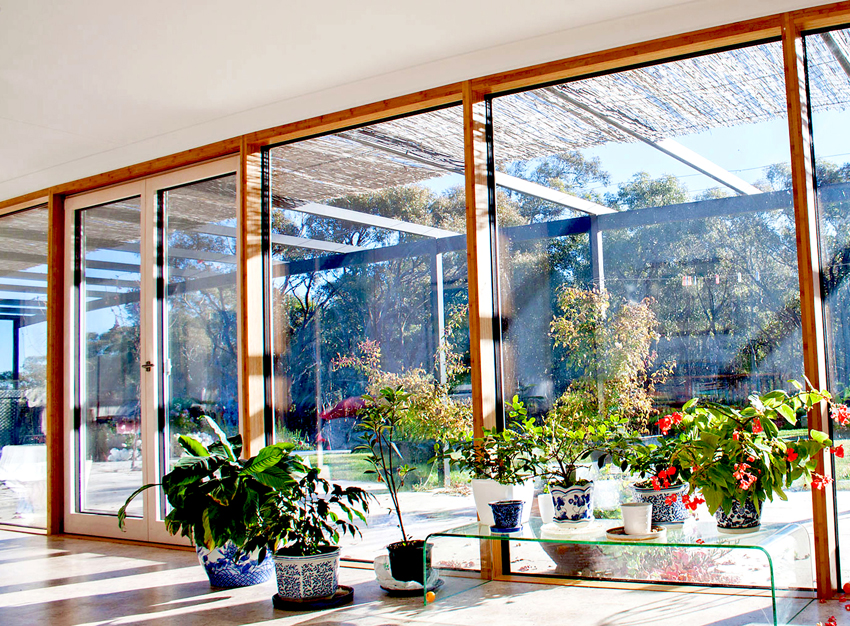
Virtually all of the structural needs for a given building projects can be addressed using modular, pre-engineered LVB and SBP components.
Windows and Doors, Engineered With Bamboo
Fenestration components made with LVB and other EBPs are now on the market designed for efficient integration into glazing systems and engineered bamboo structures. The components are specifically designed for insulated glazing units (IGUs), window, and door thermal performance as well as strength, rigidity, and water-resistant attributes. This makes them an effective choice for sustainable design challenges.
One of the benefits is that the engineered bamboo materials have tested to be more stable in climate and temperature changes than engineered woods. Engineered bamboo materials present better mechanical properties over typical natural wood materials, which means they are ideal for window and door products and assemblies. LVB functions similarly to hardwoods; however, LVB has a much better dimensional stability and as a building product can be more sustainably sourced. Some project teams and end users see LVB’s antimicrobial properties as a benefit since the resulting windows and doors resist moisture buildup. Silica content within the material acts as a natural insect deterrent as well.
For high-performance facades, the windows are higher in density than hardwoods, which allows for more resilient and durable fenestration structures—which are often relative weak points in the enclosure. The density also means moderate thermal bridging as compared to softwoods, but this is offset by other performance advantages, says Schuette. For operable units, the material’s stability also allows for more uniform and smooth operation throughout the building’s use phase.
In comparing density, typical softwoods used in light residential windows weigh about 36 pounds per cubic foot. LVB is much denser with a density of about 44 pounds per cubic foot, making LVB a more dimensionally stable and efficient material over typical softwoods. Since window and door applications are more susceptible to the changes in temperature and moisture, it is key to integrate a material that can withstand extreme changes in both temperature and moisture.
LVB materials and components, whether standard dimensional or custom, can be used for commercial entries, operable windows, movable wall systems, lift and slide systems, garage doors/openings, and skylights, as well as storefront and curtain wall assemblies. The product can be milled with the same tools as hardwoods, making production easier for fabricators and manufacturers of fenestration products. In today's market, full system and installation services for products integrated as thermally high-performance hybrids of aluminum/LVB, a solution offered by a number of manufactures, installers, and glaziers internationally.
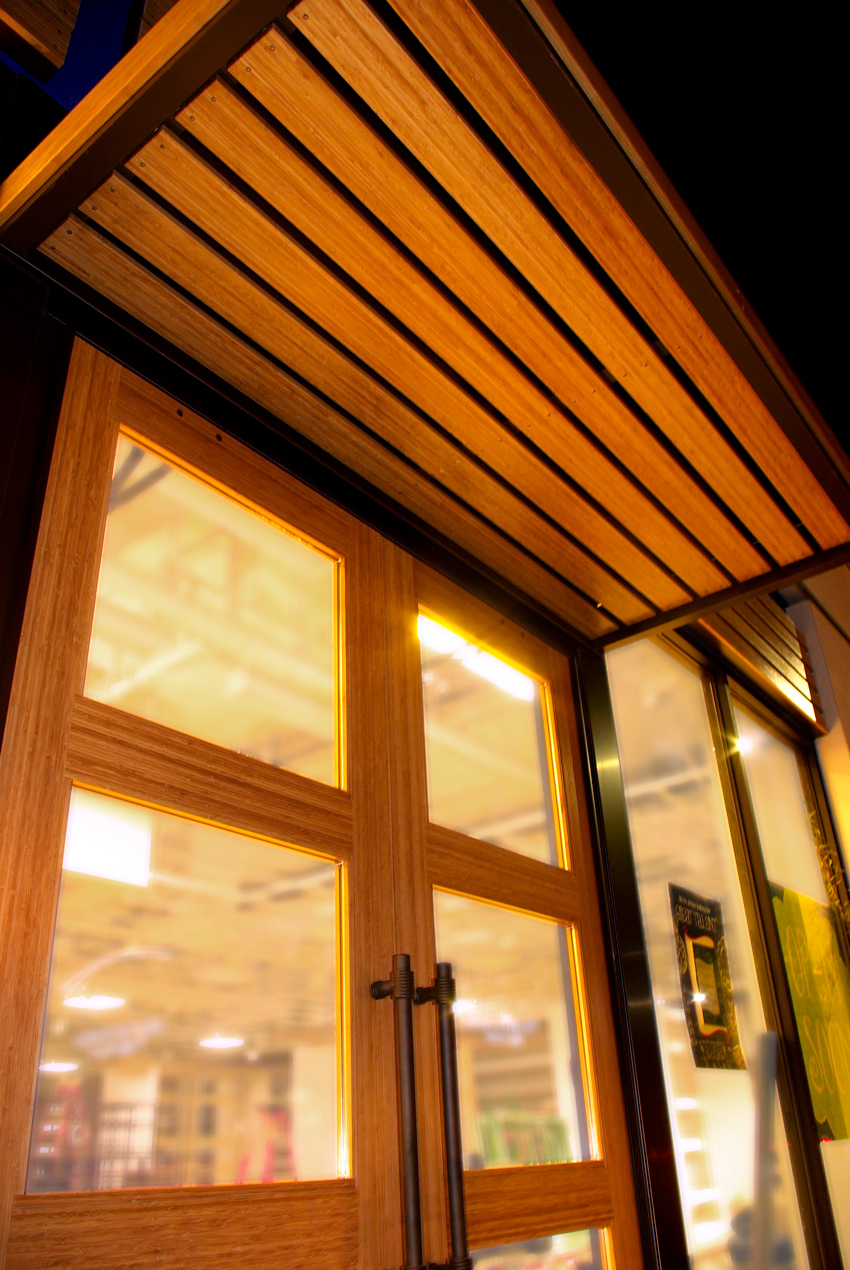
LVB materials and components, whether modular or custom, can be used for commercial entries, operable windows, movable wall systems, lift and slide systems, garage doors/openings, and skylights, as well as storefront and curtain wall assemblies.
One of the key trends in enclosure design has been the adoption of performance standards in the U.S. Green Building Council’s LEED certifications and even more so with the super-efficient Passive House standards. These programs require architects and their teams to demonstrate a specific level of energy efficiency in order to be certified. According to the Passive House Institute US, the standards and passive design in general are defined based on five building science principles: continuous insulation throughout the entire envelope without thermal bridging, an airtight envelope, heat-recovery and moisture-recovery ventilation, controlled solar gain, and high-performance windows and doors. The windows are frequently triple-paned and may include a fill, such as argon. High-performance window and doors of this type using LVB have been used successfully in Certified Passive House structures.
Among the recent advances in window design is a LVB European-designed window with hardware that revolves the window 180 degrees for cleaning and maintenance without encroaching into the building interior spaces. Another is a storefront system offered with various window hardware types as well as folding, sliding, entry, and lift-and-slide doors. The manufacturers have adopted engineered bamboo because of its mechanical properties and natural aesthetics. Some manufacturers have also introduced operable and motorized fenestration systems in the last three to five years. The operable inserts can be placed in any part of the enclosure layout and include inswing and outswing venting lights in both manually operated and fully automatic motorized systems.
High-Performance Bamboo: Case Studies
Some recent projects show how EBPs have been used in adding value to creative projects. In as well-publicized and carefully tested application, engineered bamboo took center stage at the 2009 Solar Decathlon applied to a residential project with traditional looks and materials as well as some cutting-edge energy technologies. Created by the architecture program at the University of Illinois at Urbana-Champaign, the solution includes 100-year-old barn wood and high-efficiency solar panels arranged with a gable roof profile. “Inside, the newest structural bamboo and optimized windows, insulation, and appliances mean it can be heated with a single hair dryer,” according to the design team.
The structural bamboo material was chosen for its renewable characteristics and superior structural performance. Suggesting Midwestern agricultural vernacular, the simple form employs barn wood siding, a barn door-like sliding shade structure, and decking made of reclaimed wood from a grain elevator.
Called Gable Home, the project was designed for certification by the U.S. Passive House Institute in Urbana, Illinois, using 90 percent less energy than typical construction. “Laminated bamboo for structural elements is stronger than wood and more rapidly renewable,” according to the team’s DOE page. It also benefits from a “laminated bamboo structure that minimizes thermal bridges.” Other key performance-driven selections include about 12 inches of wall, roof, and floor insulation, a high-efficiency, small-air-volume HVAC system, and a solar array generating about 9.1 kW of DC power.
In a very different application, the durability and beauty of structural laminated bamboo are already on display at the new 23,000-square-foot replacement terminal for the Williamson County Regional Airport in Marion, Illinois. Utilizing a pre-engineered hybrid dome of structural steel and engineered bamboo cross beams, the architects of RS&H created a soaring display of exposed structure visible overhead in the terminal’s central court.
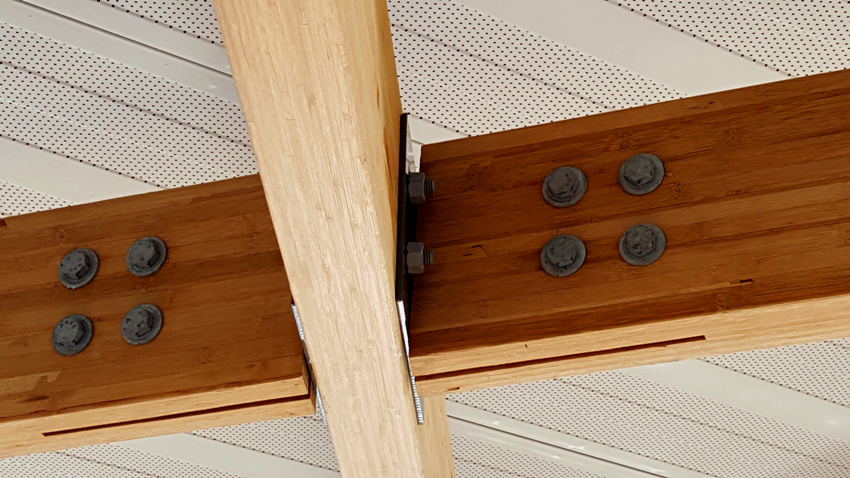
Structural laminated bamboo is on display at the new 23,000-square-foot replacement terminal for the Williamson County Regional Airport in Marion, Illinois, with its pre-engineered hybrid dome of structural steel and engineered bamboo cross beams, designed by the architecture and engineering firm RS&H.
Faculty and masters of architecture students from nearby Southern Illinois University, Carbondale visited the project site to witness the exposed gridwork and framing before the roof assembly was set by the contractor. Sixteen-foot curved EBP beams attaching to 64-foot arcs of curved steel. Created as a showcase of sustainability and innovation, the new terminal marks the first airport in the United States to have an entire roof structure made of structural engineered bamboo, according to the Williamson County Airport officials, when it opened in the fall of 2016.
Remarking on the project, the project supplier noted that inherently as a raw material, as a bio-based material, the dimensional bamboo is stronger than timbers on average. In tensile strength, it’s more than two times stronger when you compare it to other timber products relative in size and density. In addition, the roof grid is visible to travelers below in the innovative, sustainable design by RS&H, an integrated architecture and engineering firm.
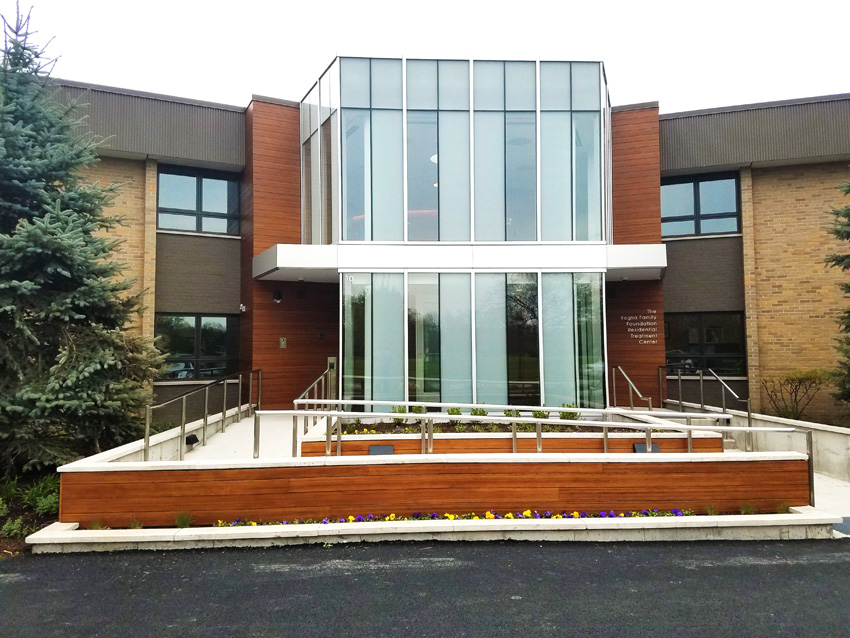
Other projects have expanded the use of engineered bamboo into civic facilities, institutional projects, commercial buildings, and more. The picture above provides another example of EBP’s used in an exterior cladding application. The customer was interested in a natural based product that promotes beauty and warmth and can be used in exterior applications. With EBP’s presenting performance, attractive aesthetic, and stability for interior and exterior applications, the customer received exactly what they were looking for in EBPs. Many architects still visualize the exposed stems and culms of unprocessed bamboo in structures both traditional and modern throughout South Asia, Southeast Asia, and East Asia. Yet, the significant benefits of LVB and other EBPs are changing their perceptions. Engineered bamboo and LVB is becoming shorthand for sustainable, high-performance structural materials that improve building operations, enclosure performance, and overall look of the final project.
Application Benefits
Some of the fastest-growing plants in the world are bamboo species, due to a unique rhizome-dependent system that lets them grow up to 10 centimeters per day.3 In about three to five years, the plants reach maturity, as compared to 20 years or more for traditional timber. Bamboo also produces 30 percent more oxygen in comparison to similar-size timber forest area, according to a Santa Clara University study, and sequesters 35 percent more carbon.4 Its unique root structure eliminates the need to replant. Bamboo is used widely as a building material, a food source, and as a versatile raw product. As noted in a Discover magazine report over two decades ago, bamboo’s tensile strength rivals that for steel and it compressive strength is greater than that for concrete, brick, or wood.5
The use of rapidly renewable bamboo-based engineered materials in green building construction can now include structural components that are typically made with wood, plastic, metal, or concrete. With increased use of engineered bamboo, building projects may qualify for several credits toward LEED certification. The demand to use sustainable building material is becoming more relevant due to the increase in sustainable building practices and the reduction of using petroleum-based building products. LVB is a perfect solution to complement the requirements for sustainable building materials.
Another key feature to EBPs, SBPs, and LVB is their unique aesthetic look. These materials are now options to be used in fully exposed applications without the need to “cover it up” with other building materials like dry-wall or paint. The natural beauty of the material can be appreciated by the building owner. Since these products are also available in interior and exterior applications, continuity can easily be achieved and allow architects and designers the availability of using one material throughout an entire project. This benefit not only helps satisfy a visual requirement, but it also can help with the overall cost reduction of not using additional materials to achieve a look the customer is requiring or looking for.
The compressive strengths of LVB and other engineered bamboo elements exceed 8,800 psi (parallel to grain), which is greater than most softwoods. The tensile strengths of the products also provide a key advantage over traditional and engineered wood products. Since LVB provides higher dimensional stability over its wood counterparts, this is a key advantage point to architects to design projects with longer spans and know their design will hold true. Lastly, the silica content and arrangement within the material help the bamboo-based products resist termite and other pests.6 Rigorous uniformity and consistency across the supply chains for EBPs adds to these good marks for basic material performance.
In summary, EBP, SBP, and LVB products are now being recognized in the architectural and building markets where manufacturers have dedicated their time and resources to enable access to this great building material to architects, engineers, interior designers, product specifiers, building owners, and other decision makers that focus on sustainable building practices. Through continued advancements in technology and engineering practices, EBP, SBP, and LVB products will become better and more available and allow for further expansion of utilizing these products through all facets of design. The architectural and building community can now rely on a sustainable building solution without the worries of deforesting our precious planet and continue the development of design solutions with a sustainable solution.
End Notes
1Sharma, B., Gatóo, A., Bock, M., and Ramage, M. “Engineered bamboo for structural applications.” Construction and Building Materials, Volume 81, 15 Apr. 2015. Web. 26 March 2016. http://www.sciencedirect.com/science/article/pii/S0950061815001117.
2Modular Building Institute. “Why Build Modular?” Modular Building Institute. Web. 26 March 2016. http://www.modular.org/htmlPage.aspx?name=why_modular.
3Farrelly, David. The Book of Bamboo. Sierra Club Books. ISBN 0-87156-825-X, 1984. Web. 26 March 2016.
4“Bamboo.” Santa Clara University, 2013. Web. 26 March 2016. https://www.scu.edu/media/ethics-center/environmental-ethics/Bamboo.pdf.
5Roach, Mary. “The Bamboo Solution: Tough as steel, sturdier than concrete, full-size in a year.” Discover magazine. 1 June 1996. Retrieved 7 Dec. 2013. Web. 26 March 2016.
6St. Louis Testing Laboratories Inc. “Resistance of Two Bamboo Species Treated with Borates to Formosan Subterranean Termites (Coptotermes Formosanus) in a No-Choice Test.” 2 Dec. 2004. Web. 26 March 2016.
C.C. Sullivan is former chief editor of Architecture magazine and principal of C.C. Sullivan, a marketing consultancy focused on architecture, construction, and other industries. He has authored or produced more than 100 continuing education units as part of his global practice. www.ccsullivan.com
![]() |
Lamboo® Technologies is the world’s leading bio-based materials company specializing in performance-grade, engineered bamboo for structural, architectural, and OEM applications. Lamboo’s product solutions for high-performance building applications achieve unmatched performance, aesthetics, and sustainability. www.lamboo.us |