Designing with Texas Limestone
A cost-effective natural product with high durability and many design opportunities
Continuing Education
Use the following learning objectives to focus your study while reading this month’s Continuing Education article.
Learning Objectives - After reading this article, you will be able to:
- Identify the natural characteristics and beneficial design opportunities, including the variety of textures, colors, and size options, for different type of Texas limestone.
- Investigate the manufacturing process of Texas limestone and its suitability for both interior and exterior building applications.
- Assess the different methods of securing different types and thicknesses of limestone onto buildings using conventional means and metal frame systems.
- Specify and describe safe and durable installation, anchoring, and sealing practices for Texas limestone on residential, commercial, and institutional building facades.
The tradition of using cut stone for buildings has been common since the time of the Greek and Roman Empires and used even earlier in Egypt, England, Ireland, and elsewhere. Some of those ancient buildings and monuments still exist today and are intact in part because of the stone material used but also because of the ways it was designed, handled, and crafted into the buildings. Today, the same is true. Cut stone of different types is still used in buildings that seek to convey a sense of permanence, a particular style, or a connectivity to the environment by using natural materials. Limestone in particular has been used as a material of choice for building facades for centuries. It is available in many parts of the world, is fairly easy to cut and carve, and has proven itself over time—in fact, the Great Pyramids in Egypt are constructed largely of limestone. A little closer to home, limestone from Texas has some specific characteristics and varieties that make it distinct and even unique compared to other limestone around the world. For building designs that need to rely on great aesthetics, long-term durability, and a range of design options, it is worthwhile learning more about Texas limestone.
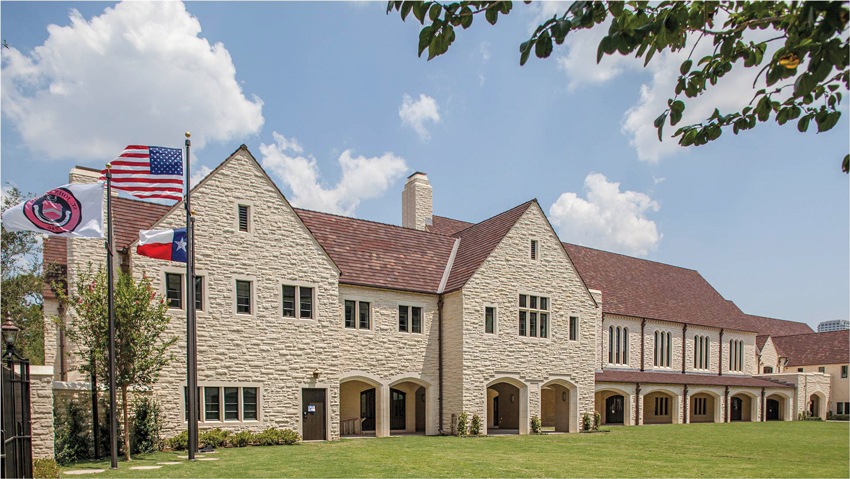
All images courtesy of Texas Quarries – An Acme Brick Company
Texas limestone is used for its appearance and durability in commercial, institutional, and residential buildings, including St. John’s school in Houston, Texas.
TEXAS LIMESTONE OVERVIEW
In geological terms, limestone in general is considered a common mineral. It is made up mostly of calcium carbonate (CaCO3) and forms primarily in shallow sea water from marine life, such as clams, scallops, or coral, which use calcium and bicarbonate in the water to form their protective shells. Over time, as the organisms die and the shells are left behind, they fall to the bottom and accumulate in layers, where they combine together to form what we know as the sedimentary rock called limestone. Its abundance on land around the world reveals the places where vast oceans previously existed millions of years ago. The variety of different types of limestone in different locations also speaks to the variety of conditions and marine life that likely existed in different places and at different times.
Some limestone is of a mixed makeup and is treated as a commodity. This is the type that is commonly used for gravel or stone in some places in the United States. It can also be used for industrial purposes, like the creation of Portland cement, lime fertilizer, or as an additive in products like paints, roofing, and even paper. But sometimes a vein of limestone is discovered that is rather pure and consistent in its makeup. Pure limestone is almost totally white, but the presence of some other substances can give limestone different colors. This type is suitable for specialized purposes where appearance and durability are important, such as building facades or interior walls.
Texas limestone exhibits all of these overall properties and characteristics of limestone. What makes it a bit more unique is the ready availability of a large quantity of high-quality, pure limestone, and the range of colors and textures available. Some Texas limestone quarries, for example, have been providing high-quality material to building projects across the country and overseas since the 1920s, and there is still plenty available. The range of colors includes not only white, but creamy beiges, some light grays, and some with hues of reds and browns.
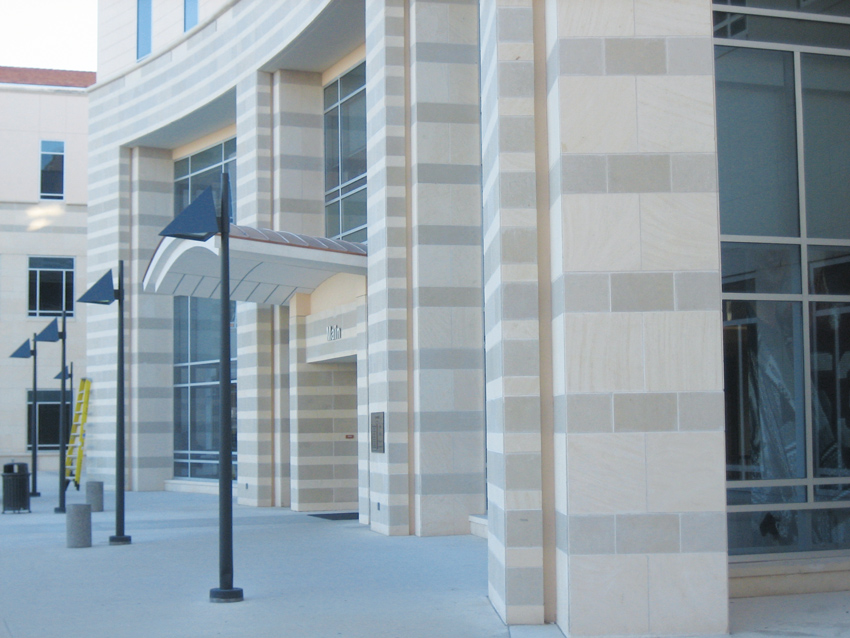
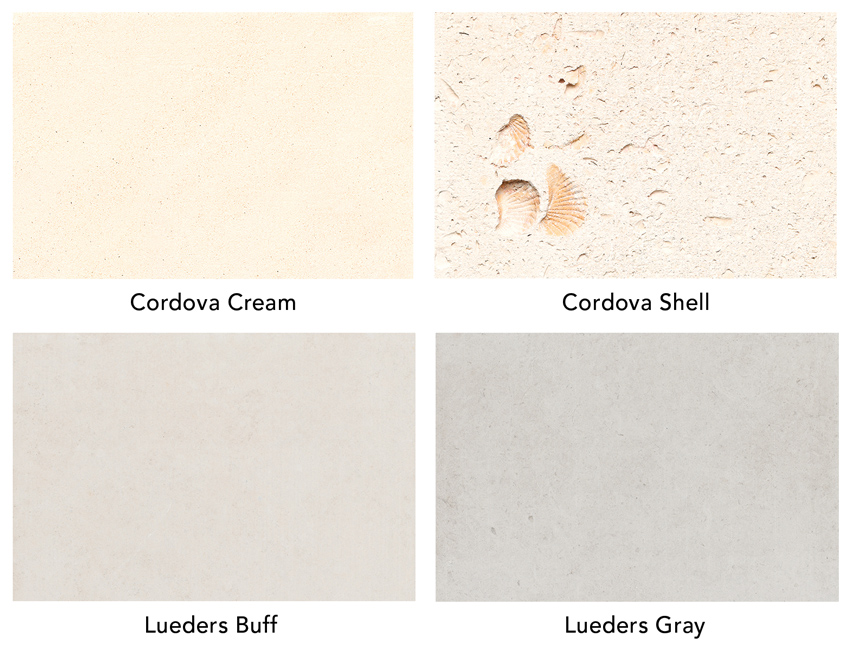
The variety of colors of Texas limestone allows for different patterns and design capabilities as shown here in Academic Building III at the University of Texas, San Antonio.
Texas limestone is typically used for interior and exterior wall surfaces. On interiors, the variety of color and texture can allow for an appropriate palette to create many different design schemes that work well with other materials. On the outside, the stone can provide the weathering surface of the building as an integral part of an overall facade or wall assembly design. Used in vertical surfaces this way, the material should hold up quite well over time as a very durable and elegant design solution. On horizontal surfaces, such as outdoor pavers, limestone can work well in low-traffic areas, but the details of installation should be reviewed with the supplier. Checking with the quarry about the suitability of a particular type of limestone to be used in a horizontal application is also advisable since different types of limestone or simply different quarries may produce stone that is better suited to horizontal applications than others.
Of course, Texas limestone, like all limestone, has a few things to keep in mind when considering its use. First, as a sedimentary rock, it is a very porous material. In order to avoid any possible degradation over time from water penetration, this can be addressed by sealing the surface of the stone or using it in locations where the porosity is not a concern. Similarly, it is a chemical mineral, and as such can react with other chemicals, including acid-based cleaners. That can be avoided with the use of neutral or mild alkaline-based cleaners when needed. In terms of the size and detailing of the stone, those factors will be very dependent on the quarry and fabricator, which may be the same company. The raw block size from the quarry will determine the maximum size of a piece of cut stone or the best smaller sizes to avoid waste from a single slab. There are many fabrication possibilities, but checking with the actual fabricator ahead of time will avoid any unwanted surprises later on.
MANUFACTURING PROCESS
As a natural material, the first step in using Texas limestone is for a quarry operation to extract the stone from the earth. All quarries are not operated equally of course, and it is worthwhile to check out how environmentally responsible a particular quarry might be.
Quarry Operation
Most quarries operate at the surface by removing any vegetation and topsoil and digging downward. At some point, a particular quarry stops being economical either because the limestone becomes more difficult to extract the quality changes, or the supply is simply depleted. There are certainly cases where the quarry operation simply stopped and left, leaving an open hole in the earth with little chance of any productive or environmentally beneficial use for many, many years. In some cases, this condition was harmful to the environment or dangerous to people. Fortunately, more and more quarries have accepted the responsibility of reclaiming and restoring the land when the stone extraction process is complete. This is done by filling in some or all of the hole left in the ground with natural materials—sometimes returning stone waste and scrap from the quarry operations itself. It can also be done using natural material from excavations in the area and covering the top with stored topsoil or similar material to allow natural vegetation to return. There may also be the opportunity to create a water feature, such as a pond or small lake, in some cases. Either way, the responsible end result is for the land to be fully restored so it can take on a new life being functional and part of the surrounding environment again.
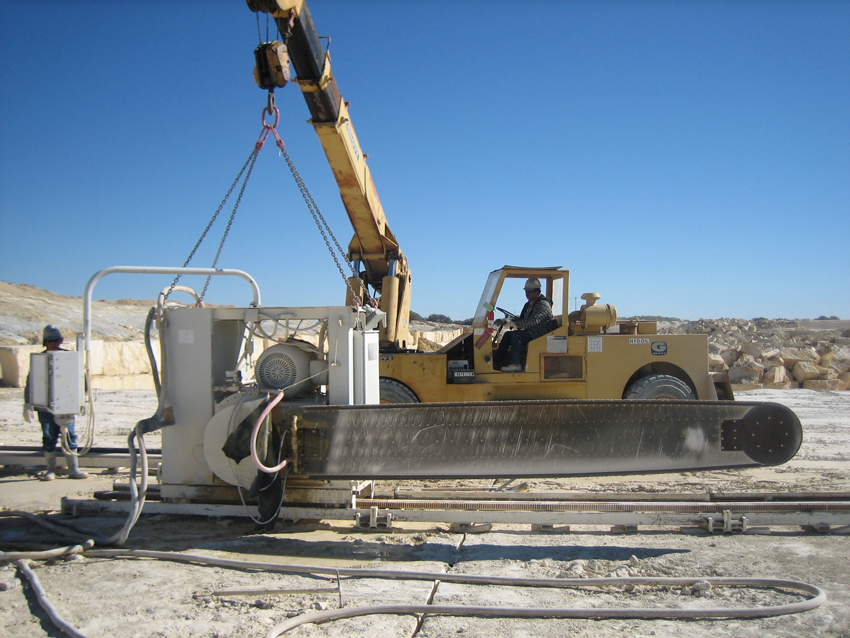
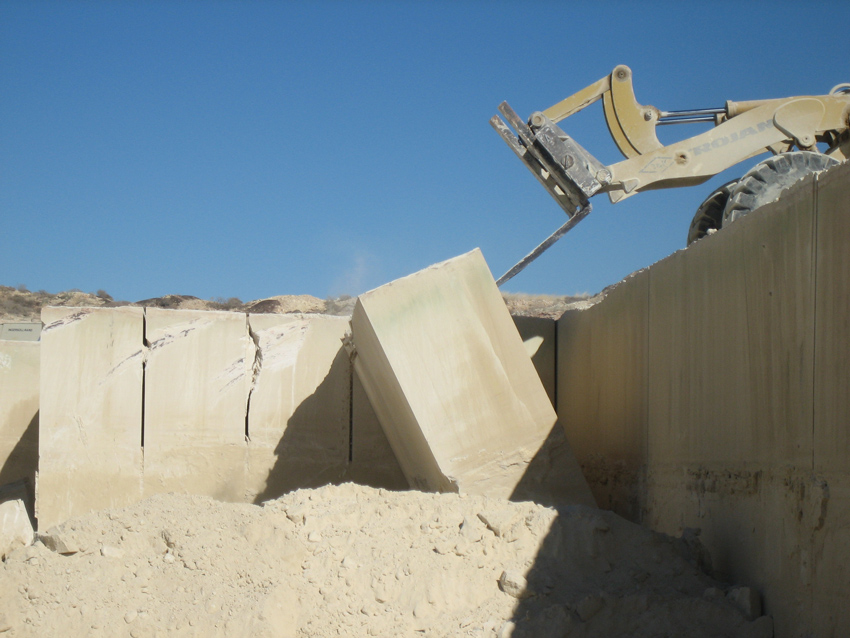
Quarry operations of limestone involve cutting large blocks and then tipping or leaning them onto their side to be carried to the mill.
In the context of responsible extraction, then, Texas limestone is quarried comparable to most other stone extraction. The surface of the exposed limestone is cut or sliced from the top down into large sections, commonly using portable stone-cutting equipment. One vertical side of those sections is commonly exposed so that hydraulic equipment can then separate the sections, or ledges, by pushing them to turn onto their side. The resulting blocks are commonly on the order of 4 feet wide by 8 feet tall by 4 feet thick. Additional equipment is then used to pick up and move these blocks to a staging area ready for next steps.
Stone Fabrication
While some quarries only provide the rough blocks, others provide further cutting and shaping through mill fabrication capabilities, thus offering a single-source responsibility for all aspects of the stone. In the mill operation, the block is sliced into slabs that can vary between 1¼ inches to 6 inches or more in thickness. Generally, the larger the size of the final panel, the thicker it needs to be in order to maintain inherent structural integrity. For example, if a final panel size of 1 foot by 2 feet is needed, then a thickness of 1¼ inches would be appropriate, thus producing a thin veneer product. If a panel size up to 3 feet by 5 feet is required, then a corresponding thickness of approximately 2¼ inches would be needed. If a full-sized panel up to 4 feet by 8 feet is desired, then the thickness would need to be on the order of 3 to 4 inches. The thicker the panel, the heavier it is, so the weight will increase at a higher rate than just the increase of surface size.
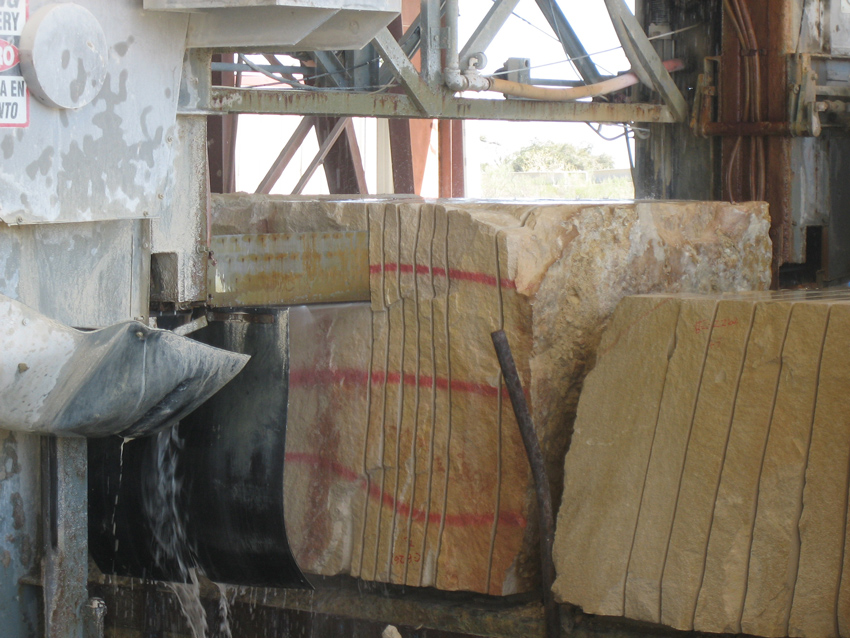
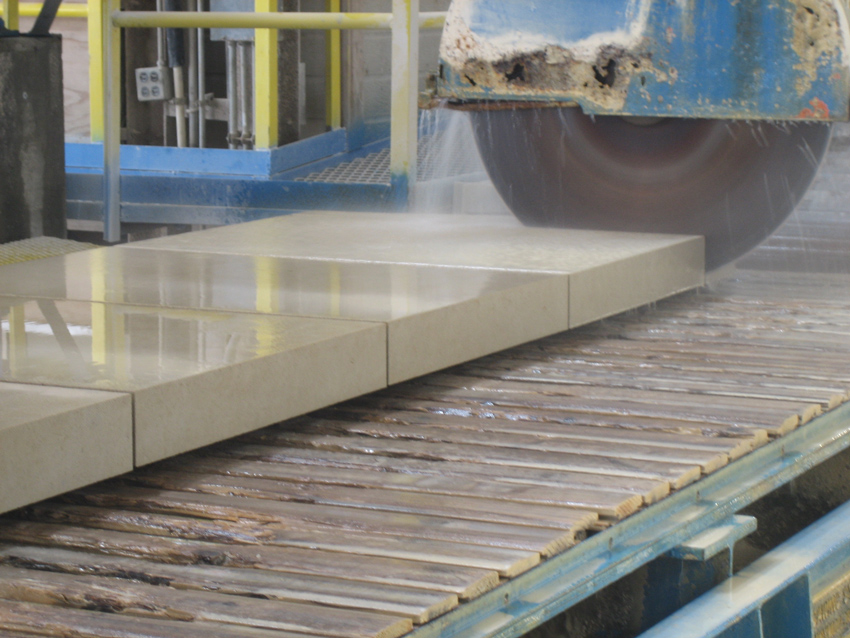
Fabrication of Texas limestone includes addressing the thickness as well as the edges of the final pieces dimensioned to the needed sizes.
Once the panels are cut to the appropriate size and thickness, they are ready for further fabrication. One of the first considerations is the type of face treatment or texture that is desired since there are many options. The blocks can be chopped or split to create an intentionally rough surface and exposing a natural inner texture. If the intent is to create rounded or smooth edges that can make the stone blocks look aged or older, then they can be pitched or tumbled to create that affect. Alternatively, they can keep more defined corners and receive a “roughback” surface that carries a more controlled rough texture. A more subtle texture can be achieved using a bush hammer or other equipment to create varying degrees of more subtle texture.
If rough or rustic isn’t the appearance being sought, then it is also possible to achieve a fairly smooth and precise look in limestone. This is done by honing the surface to the desired smoothness to create a more uniform look and appearance. Automated machinery can be used to cut honed slabs to more precise final sizes. The edges can be processed to obtain a square, chamfered, rounded, or other edge profile, as may be desired. If desired, different profiles, miters, or other detailing can also be performed according to architectural design and specifications. Either way, once the individual pieces receive the proper surface texture and are dimensioned to the proper sizes, they are ready to be crated and shipped to the project site.
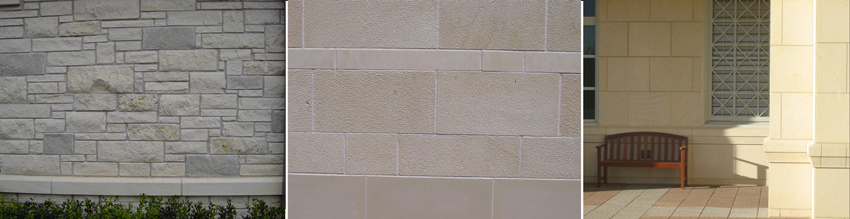
Texas limestone is available in a variety of surface textures such as the fairly rough split block (left), a more subtle rustic finish (center), or honed smooth (right).
Hand Carving
In some cases, unique limestone details are sought for either new or renovated buildings. Those details might call for some specific three-dimensional shapes, forms, or patterns to create a feature item consistent with the rest of the building. In this case, custom hand-carved pieces or panels are possible, which can create dramatic and very artistic results.
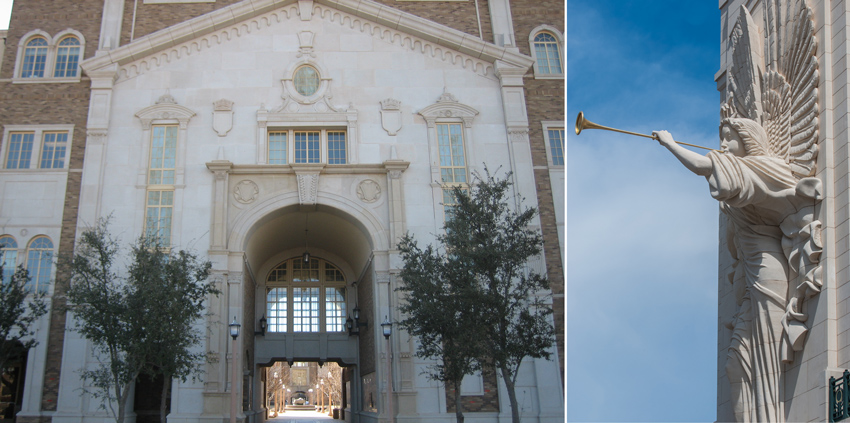
Custom hand-carved limestone is available to produce unique, three-dimensional elements that are permanent parts of an overall building, such as the Texas Tech English and Philosophy Building.
Of course, doing this type of carving work requires the availability of artisans with the skills and experience to execute it. Those capabilities may be found at some quarry/fabricators but certainly not all. It is worth investigating this ahead of time and asking to see examples of prior work, either physically or photographically. These skills are important for single, stand-alone carvings, such as statuary, but they will also be important for repeated items along a building frieze or ornamental treatments at windows, doors, etc. In this case, first creating a template that can be reviewed and approved will be important. That template can then be the basis for replicating multiple identical pieces of hand-carved limestone.
Cutting and Setting Drawings
One of the key coordination tools in the process of incorporating cut stone into a building is the use of shop drawings that depict the details of cutting and setting the stone in place. The cut stone supplier typically prepares and submits to the architect, for approval, complete cutting and setting drawings for all of the limestone work under any particular contract. Such drawings necessarily show in detail the sizes, sections, and dimensions of stone, the arrangement of joints and bonding, anchoring, and other necessary details. In short, they form the full, detailed description of the stonework cutting, fabrication, and installation based on the architectural design for the building.
In order to be sure that the building design and the stone-cutting design are working together, one or more meetings between the architect and the supplier during the design phase can definitely help. It is counter-productive for the architectural drawings to show extensive detailing that is contrary to the best practices or capabilities of limestone. It is also not appropriate to provide too little detail, leaving uncertainty or creating surprises when the stone is installed. Rather, in the spirit of an integrated project delivery process, an early discussion can help inform all parties of the best ways to communicate the design intent and the construction details. In cases where the architectural firm is using building information modeling (BIM), it may be possible to incorporate the shop drawing information from the supplier directly into the computer model as well, thus fostering full coordination with the overall design.
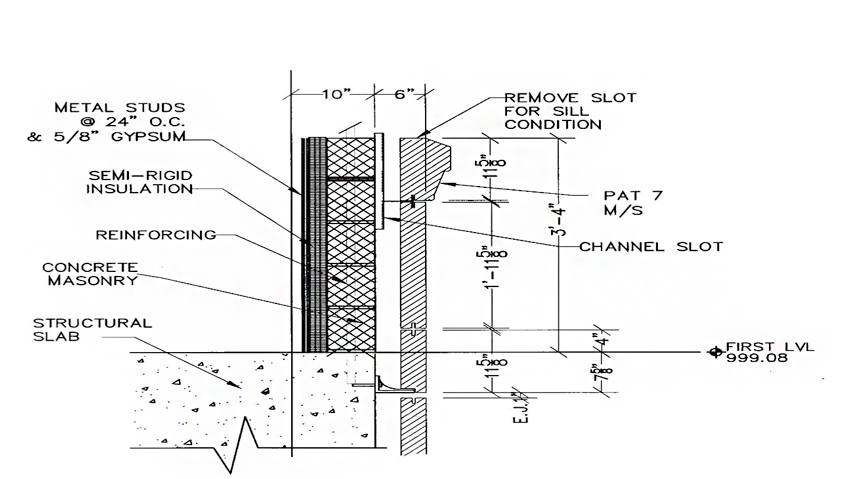
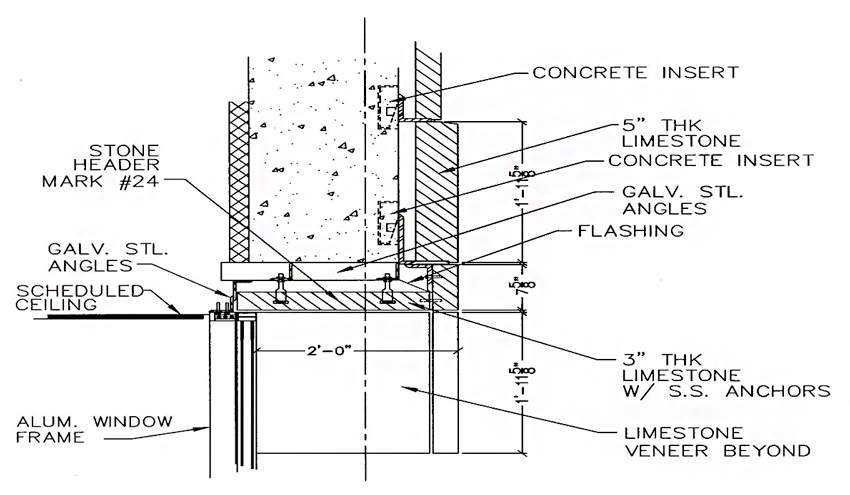
Stone cutting and setting shop drawings need to be coordinated with architectural construction drawings to allow all aspects of the stonework to be appropriately detailed.
The role of each party also needs to be understood and respected in the process. For example, the architect is still responsible for the overall design of the building and the creation of needed stone details to scale or drawn full size. If the contract drawings do not show the intent of the jointing, it will be the stone fabricator’s responsibility to establish the jointing in accordance with industry standards. Each stone indicated on these drawings shall bear the corresponding number marked on an unexposed surface with a non-staining paint. The contractor who is constructing the building that the stone will be placed on is typically responsible for furnishing all field dimensions necessary for fabrication.
DESIGN OPTIONS AND OPPORTUNITIES
When designing with Texas limestone, a common approach is to seek to match the design vision of the building with the appropriate technical capabilities of the limestone. Of course, all of that needs to be accomplished in a manner that stays within the project budget. While it is easy to think that achieving all of that is difficult, the reality is that there are enough options and choices available that architects can find it easier than anticipated. The key is to talk with suppliers and fabricators ahead of time to understand the different types of limestone available and the different aspects that can drive or control the cost. In this way, informed design decisions can be made to achieve the desired appearance, assure proper long term performance, and stay within budget parameters.
One option to consider, in cases where lighter weight and cost control are important, is the use of thin veneer limestone. Thin stone units are approximately 1¼ inches thick, and their overall face size is comparatively small to make them easy to install. Their relative light weight, roughly 15 pounds or less per square foot, allows them to be laid much like wall tile. They are very versatile in how they can be used since they can be installed over a variety of different types of substrate surfaces. Any masonry, such as brick, block, or concrete, works well for the thin stone veneer to be applied directly to the surface. In framed wall assemblies, 18-gauge metal framing is typically recommended, but all other wall details are typical. There is no need for any additional structural support like there might be for full-depth stone pieces. For existing walls that are painted, it is advisable to remove the paint using conventional paint stripping or sand blasting to assure that the stone remains secured to the surface.
The surface texture and color of thin veneer limestone can be varied just like full-thickness stone panels. Split face texture is standard among some suppliers, but it can be ordered in sawn or honed textures as well. Corner pieces are available with 90-degree returns to replicate the corner conditions of full-depth stone. This allows for the appearance of thicker stone being used, just for notably less cost. Thin veneer limestone can also be ordered in all of the same colors as full-thickness limestone. Overall, it is reasonable option to consider for many different types of buildings, both on the interior and exterior.
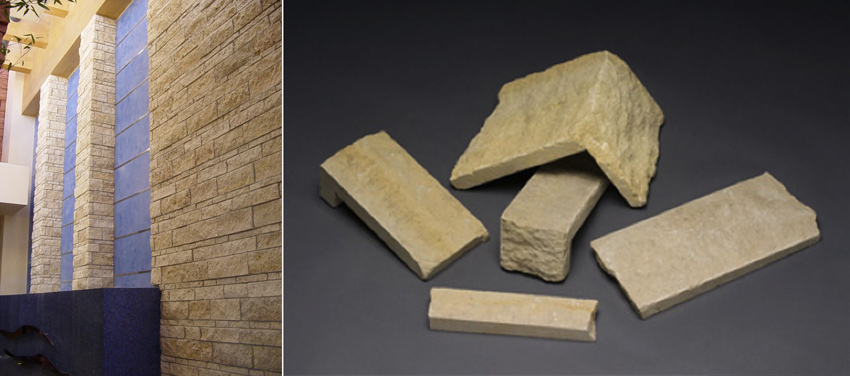
Thin stone veneer is available that reduces the weight and cost of the stone, while still maintaining the appearance and natural qualities for a building design, as shown here in the Red Rock Casino in Las Vegas, Nevada.
Commercial and Institutional Buildings
Texas limestone has found a home in many commercial and institutional buildings in a variety of locations. Typically, stone products are most economically installed when they don’t need to be shipped long distances. However, some quarries have supplied stone to projects around the world by working with the building designers to find appropriate uses and applications of limestone that can absorb the shipping costs. Sometimes this means using limestone in limited parts of a building, or it may mean finding cost-effective fabricating and finishing, which can make up for added transportation costs. It may also mean using thin veneer to reduce the weight and cut down on shipping costs accordingly.
Texas limestone of all types and sizes can be used for both exterior and interior applications in commercial and institutional buildings. This is true for stand-alone buildings, such as government or private offices or K-12 schools. Some building types with multiple locations, such as bank branches or libraries, are great candidates for Texas limestone since it can create a consistent, identifying appearance for these facilities. It can also be particularly appropriate to use it on higher-education campuses or other multi-building settings where a consistent use of building materials is sought for a unified look and coordinated facilities programs.
Residential Buildings
Texas limestone has been used on homes that seek distinguishing design features and the beauty of natural architectural stone work. Residences often incorporate chopped stone and favor thin veneer installations for both exterior and interior walls to create texture and color, while remaining within budget. However, some details can also be created that might be very ornate, such as custom entry surrounds and fireplaces. This is another case where the options and choices available can allow for the creation of a distinctive design but still keep within the overall project budget.
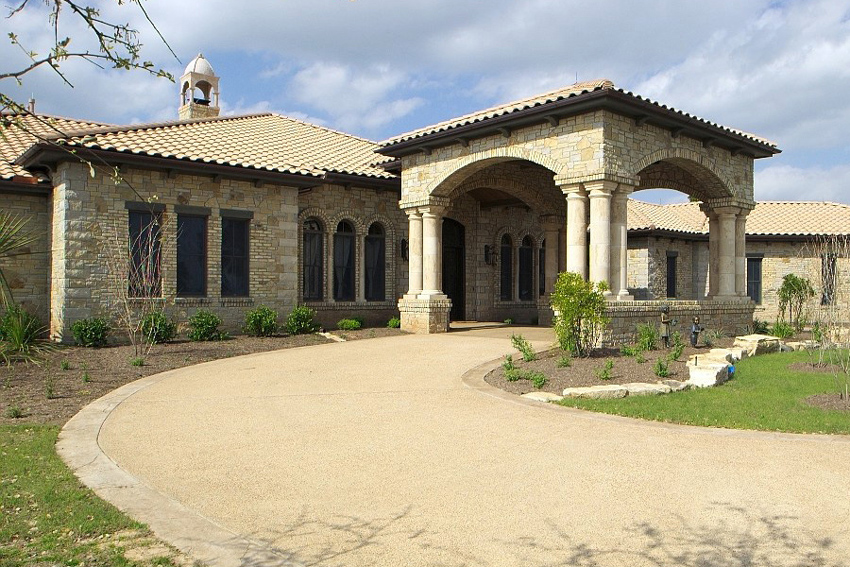
Texas limestone has been used successfully not only on commercial buildings but on custom residential projects as well.
Full-thickness units can also be used on the exterior that are the depth of brick veneer, 3¼ to 4 inches. This can allow them to be easily used in conjunction with brick or on their own with standard detailing. The full range of colors and textures is available for residences so designers can find equally creative and appropriate solutions as for commercial applications. In some cases, a distinctive rough back finish, which uses the natural edge of the limestone deposit, is available. Since the limestone edge is in contact with other materials, it offers a deeper variety of colors, including rich buffs, golds, oranges, and browns, which are sometimes popular in residential design.
INSTALLATION PROCESSES
The nature of cut stonework is such that most, if not all, of the cutting and finishing of the stone should be done at the stone-cutting plant, not in the field. There may be some minor exceptions, such as drilling holes for mechanical or electrical penetrations, that could not be anticipated ahead of time on shop drawings and fabrication. Aside from that, the architect, contractors, and stone supplier/fabricator should all anticipate a fully coordinated effort to provide the cut and finished stone in a condition where it is ready to be installed directly into the building. This is commonly facilitated by detailed shop drawings that identify and number each piece of cut stone that needs to fit on the building. The actual stone is then marked and identified with the same numbering system, making it possible to have the stone panels shipped to match the sequence of construction that is coordinated ahead of time.
The actual installation should follow the recommendations of the stone supplier for specific applications and of course be coordinated with other construction work. While stone is durable in place, it is important to realize that it can damaged, stained, or discolored during installation so it is very important that everyone is aware of proper handling for the safety of both the stone and those handling it. Those working in a stone-cutting plant will no doubt be quite well-versed in these techniques and can be a very valuable resource. They will be the ones making sure that the stone is packaged properly for safe shipment to the building where it will be installed. However, it is critically important that those receiving the stone understand that it must be moved, stored, and protected with care. Limestone should be unloaded following the instructions of the stone plant. It should be stored clear of the ground on non-staining skids, which also means that chemically treated wood should not be used. It should also be covered and protected from weather until it is installed on the building to avoid any possible discoloration.
Anchoring
Full-size stone panels need to be anchored to the building structure to be securely held in place, whether for interior or exterior installations. This is comparable to brick and masonry ties or anchors, which allow the outer surface to act as a non-structural veneer, holding only its own vertical weight, and using the anchors to transfer any lateral loads to the building structure. Such anchors for limestone are similarly designed and intended to secure the panels in place, keeping at least a 1-inch air/drainage gap between the stone and the rest of the wall, but not to incur any notable structural loads. Because of the chemical makeup of limestone, the anchors need to be made of stainless steel in order to hold up over time. Galvanized steel is generally not recommended except for relief angles.
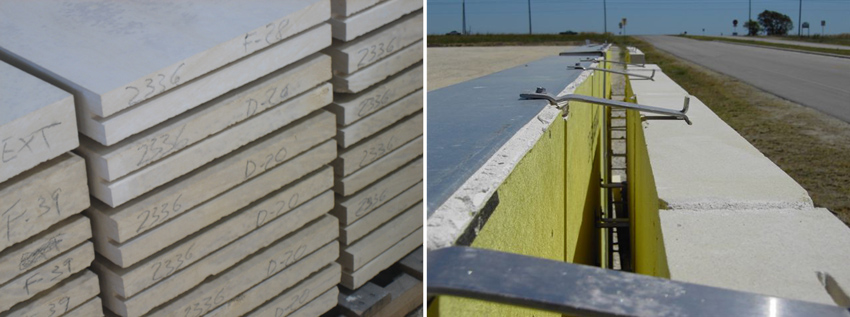
Full-depth limestone needs to be anchored to the building structure by means of a groove cut in the middle of a stone panel that receives a stainless steel anchor, as shown in the example above.
Anchors for stone can come in a variety of shapes and sizes, but they are generally designed to fit into a horizontal groove in the center of the stone panels that is not visible when installation is complete. Generally, each panel will have multiple anchors with a leg that turns up or down into the prepared groove as the stone is set in place. Mortar will be set onto the stone or base below and will help secure limestone panels in place. The process continues until the entire wall is complete.
As mentioned earlier, the architect and the stone supplier need to work together to coordinate details between construction drawings and shop drawings, and this is particularly true for anchoring details. All of the specific anchoring details that need to be coordinated for a proper installation should appear on the stone cutting and setting drawings with review and approval of the architect. For example, projecting courses typically need to have beds in the wall at least 1 inch greater in depth than the projection, or else be specially anchored to the structure, and should be detailed on the stone cutting and setting drawings. These drawings should also detail all provisions for the proper anchoring, dowelling, and cramping of work in keeping with standard practices. If any stone needs to be supported by shelf angles, loose steel, etc., it should also be clearly indicated on the setting drawings. The overall result of proper detailing is a wall surface that meets the design requirements and is securely and permanently installed.
Metal Track System
An emerging alternative trend to the traditional stacking and anchoring type of installation is to use panels that will fit into a metal track system secured to the building structure. The metal tracks are comprised of vertical members that connect to the building structure and horizontal members that receive the cut stone panels. Unlike conventional stone-veneer systems, metal track systems attach to and hang on the wall structure, thus not requiring a concrete footing to support the weight of the masonry above. This feature alone can yield considerable cost savings. Further, since metal track systems like this can weigh as little as 14 pounds per square foot when using thin veneer stone, it can be easily designed into new or existing building projects using conventional construction techniques and existing wall studs. The track also removes the need for separate anchors and allows for the stone to be set in place based on coordinating the track geometry with the cut limestone geometry. This method allows for a much easier installation of the stone to begin with and the opportunity to make changes to the building facade in the future.
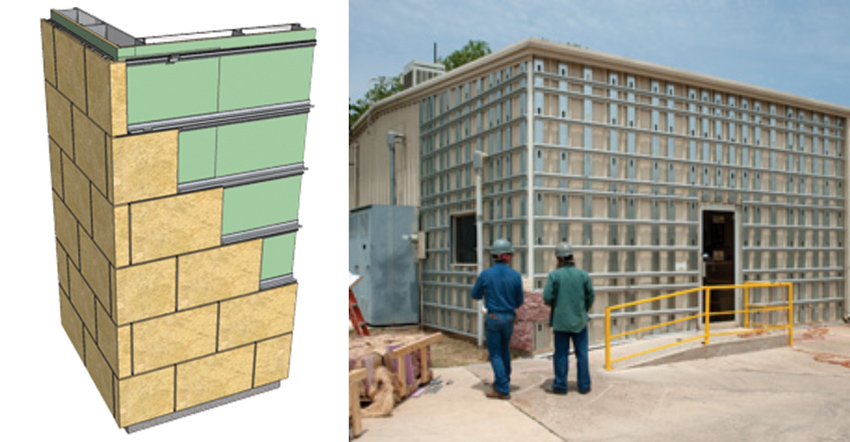
An alternative to traditional anchoring systems is to use a metal frame system that is designed to accept standard-size panels of cut stone, thus expediting installation and helping to control costs.
Installation systems based on using metal tracks are commonly based on standardized shapes to make things easier to coordinate. Standard nominal sizes for stone panels using these systems are 16 inches by 24 inches and 8 inches by 24 inches. Custom sizes may be available by special order so it is advisable to talk with a supplier to verify the size options. The use of these systems can also help achieve sustainable building design objectives. Aluminum channels and clips typically have at least 25 percent post-consumer recycled content, thus reducing the need for virgin material to be created. Further, the entire system can be dismantled and repurposed as the usage or occupancy of the building may change over its life cycle. Unused material can be fully recycled.
Sealing Limestone
Once the limestone is installed, it may be appropriate to seal it to protect the surface over time. Limestone has routinely been sealed for a number of reasons, the most common of which is to partially fill the pores in the stone and deter oil or water from penetrating through it. The most appropriate sealer to use is one that is siloxane based. That means it is comprised of silicon, oxygen, and alkane, which does not react unfavorably with the calcium carbonate makeup of the limestone. It also allows some transmission of air and vapor through the limestone so that any trapped moisture can escape rather than remain in the wall and cause damage.
The proper use of a sealer can yield other benefits, too. Specified and used correctly, it does not change color of newly cut stone, although it is always advisable to test a small area first to verify that. Existing limestone on a building may be affected by a sealer, but in this case it may actually help restore the stone to its original color and enhance its beauty. Either way, the sealer will allow the installed limestone to resist permanent staining from environmental or human sources. With less likelihood of stains and with a surface that can be easier to clean in general, that will help reduce long-term maintenance costs.
CONCLUSION
Peter J. Arsenault, FAIA, NCARB, LEED AP, is an architect and green building consultant who has authored more than 125 continuing education and technical publications as part of a nationwide practice. www.linkedin.com/in/pjaarch
![]() |
Since 1929, Texas Quarries limestone has been the primary building material for many state and national monuments, public buildings and commercial structures. We quarry and finish Texas limestone in Cordova Cream, distinctive Cordova Shell, Lueders Gray, and Lueders Buff limestone. Our large staff of artisans can render any design. http://www.texasquarries.com |