Designing for Extreme Environments
Incorporating resiliency into buildings that are subjected to harsh or damaging conditions
Continuing Education
Use the following learning objectives to focus your study while reading this month’s Continuing Education article.
Learning Objectives - After reading this article, you will be able to:
- Define the building codes and federal standards that identify requirements for structures that are resistant to extreme weather.
- Discuss the design issues related to creating buildings that can withstand a flooding event.
- Assess design strategies related to wind and projectile resistance during hurricanes and tornadoes.
- Specify and design effective, required signage that is durable and long lasting in buildings subject to extreme conditions.
The weather is always a popular topic of conversation, but it is also an important focus of researchers and government agencies. The National Weather Service (NWS), which is part of the National Oceanic and Atmospheric Administration (NOAA), has kept records for decades on weather events across the United States. In particular, it has tracked severe weather events, such as tornados, hurricanes, floods, storms of all sorts, and other things we commonly refer to as natural disasters. Its records seem to indicate a disturbing trend of an increase in severe weather events over the past several decades.1 Further, the impacts from these events related to the cost of damage or losses seems to be increasing. A report titled U.S. Billion-Dollar Weather and Climate Disasters: Data Sources, Trends, Accuracy and Biases by Adam B. Smith of the NOAA National Climatic Data Center and Richard W. Katz of the National Center for Atmospheric Research is quite telling.2 They have found that “an increasing trend in annual aggregate losses is shown to be primarily attributable to a statistically significant increasing trend of about 5 percent per year in the frequency of billion-dollar disasters.” They further indicate that inherent uncertainties and biases in the data collection suggests an underestimation of average loss of roughly 10 to 15 percent, meaning the actual loss due to weather-related damage is likely 10 to 15 percent more than reported. Fortunately, there is one positive statistic from the National Weather Service: the number of fatalities from severe weather appears to be decreasing, suggesting that we are getting better at protecting people, if not property. That is likely attributable to better communication and buildings designed to provide safer environments for people who can experience any number of these natural disasters.
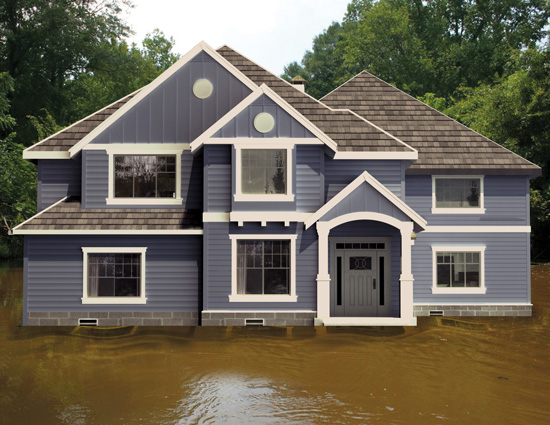
Image courtesy of Smart Vent Products, Inc.
Extreme weather conditions, such as flooding, can cause significant problems for buildings unless they are designed and constructed to withstand them.
Standards of Design for Safety
Building codes establish a baseline for safety in buildings covering a variety of issues, including weather resistance. In areas that have been identified as being prone to a higher risk of such things as tornadoes, floods, or hurricanes, there are often localized requirements that are more stringent than national codes. Miami Dade County in Florida, for example, is well known for establishing and enforcing higher standards to protect people and property in the event of hurricanes, wind, and flooding.
In some cases, a proactive approach to providing safe shelter has been adopted. Specifically, ICC 500-2014: ICC/NSSA Standard for the Design and Construction of Storm Shelters, published jointly by the International Code Council (ICC) and the National Storm Shelter Association (NSSA), has been developed. This standard is referenced in the newest building safety codes and provides minimum design and construction requirements for shelters to provide a safe refuge from storms that produce high winds, hurricanes, and tornadoes. The premise here is that the magnitude of wind speeds associated with these events require occupants of standard buildings to evacuate the area or seek protection in a shelter designed for resistance to extraordinary wind loads and flying debris. This approach isn’t limited to stand-alone shelters either since the latest ICC Codes now require storm shelters in educational occupancies and critical emergency operation centers located in areas prone to extreme tornadoes. That means such shelters, or rooms and facilities that can serve as those shelters, must be included in the design and renovation of many buildings. The ICC-500 standard provides architects and other design professionals with minimum code requirements for the main wind-resisting structural system, openings, and cladding of these shelters. It also provides basic occupant life-safety and health requirements for shelters, including means of egress, lighting, sanitation, ventilation, fire safety, and minimum required floor space for occupants.
Beyond codes, the federal government can influence local building design and construction too, particularly through programs and requirements of the Federal Emergency Management Agency (FEMA). It also issues standards for keeping people safe and sheltered in severe storms, and it relies on those standards to establish rates for things like flood insurance and other programs. In particular, FEMA P-361, Safe Rooms for Tornadoes and Hurricanes: Guidance for Community and Residential Safe Rooms (Third Edition, 2015) addresses many of the same things that ICC-500 does, but it is more stringent in some cases. A companion publication, FEMA P-320 titled Taking Shelter from the Storm, Building a Safe Room For Your Home or Small Business now in its fourth edition, helps designers, homeowners, or small business owners assess their risk and determine the best type of safe room for their needs. FEMA P-320 also includes safe room design drawings with details geared to both FEMA P-361 and ICC-500. Design options include safe rooms located inside or outside of a home or small business. For safe rooms intended for more than 16 occupants, additional requirements kick in for the design.
Like ICC-500, FEMA P-361 presents important information about the design and construction of community and residential safe rooms to provide protection during tornado and hurricane events. FEMA defines “safe rooms” as buildings or portions thereof that comply with the criteria described in P-361. ICC 500 defines “storm shelters” as buildings or portions thereof that comply with ICC 500. Though similar, there are important differences. All safe room criteria in FEMA P-361 meet the storm shelter requirements of the ICC 500, but FEMA P-361 includes a few design and performance criteria that are more conservative than those in the ICC 500. In particular, FEMA requires safe rooms that are designed specifically to provide near-absolute protection per FEMA P-361 criteria, including operational and emergency planning criteria.3
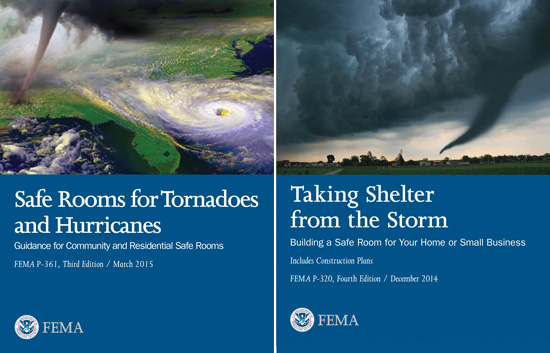
Images courtesy of FEMA
FEMA Publications P-361 and P-320 provide detailed requirements for safe rooms and shelters to withstand tornadoes, hurricanes, and flooding—some more stringent than the ICC-500 code.
While tornados and hurricanes may grab the most media attention, flooding is actually more prevalent and more of a problem in the United States. Buildings that are designed and constructed in a known flood zone need to rely on the latest available information and standards in order to remain safe and be structurally sound. The best source of such information is a FEMA Flood Map Service Center, where the flood insurance rate map (FIRM) for a municipality can be found. This is typically the map used by municipalities to enforce their local floodplain management regulations, but it’s also used by the FEMA-administered National Flood Insurance Program (NFIP) for flood insurance rating purposes. The identified flood zone of the building along with other factors play directly into the ultimate cost of flood insurance.
In addition to FEMA, The American Society of Civil Engineers (ASCE) has published Flood Resistant Design and Construction (ASCE 24-14). This standard, which is also adopted by reference in the model building codes, provides minimum requirements for the design and construction of structures located in flood hazard areas. It applies to new structures, including subsequent work, and to work classified as substantial improvement of existing structures that are not historic. As a professional resource, it provides essential guidance on design and construction to structural engineers, design professionals, code officials, floodplain managers, and building owners.
Common Design Considerations
All extreme weather conditions have the potential to create damage to buildings, increase risk to people, or both. Not all do it in the same way, however, nor do they all pose the same types of threats. The key, from a design standpoint, is to understand the differences between various weather conditions and the ways to help assess, quantify, and address the potential concerns.
Flooding
As mentioned, flooding is one of the most frequent and potentially most damaging events related to extreme weather that people and buildings need protection from. The National Flood Insurance Program (NFIP) managed by FEMA is the only place that most properties can get flood insurance, therefore, it is a significant source of information and data on flood events. Of particular interest to NFIP are the specific costs of flooding which can help to identify where to focus ways to reduce damage and hence cost. One of the best known recent flooding events occurred when Hurricane Sandy battered the northeastern United States in October of 2012. Statistics have shown that NFIP claims filed within the four months following that storm were 93 percent for building damage as opposed to 7 percent for contents damage. That may be different from what a lot of people think when they see streets piled with ruined furniture, refrigerators, etc. after a flood. The reality is that building and structural damage claims were the predominant issue in Hurricane Sandy, with claims in the range of $10,000–$100,000 each. The bottom line is that such structural damage from flooding can add up quickly, making it extremely worthwhile to design for reducing building damage in known flood zone areas.
Designing to mitigate flood damage starts by consulting the FEMA Floodplain Maps for the location where a building is sited. There you can determine the Base Flood Elevation (BFE), which is the calculated level that floodwaters will rise to during a base flood event. The maps may also show Special Flood Hazard Areas (SFHA), which are high-risk floodplain areas. If the building site is located in any area on the map that shows a BFE or a SFHA then building designs need to meet local, state, and federal floodplain construction requirements. The degree of flood mitigation required may depend on identified zones in SFHAs. Type A zones (AE and A1-30 zones) are areas with established BFEs and a perceived low impact from waves. For example, in a coastal area, these zones are typically found about two to three blocks inland from the coastline. Type V zones (VE and V1-30 zones) have a greater risk due to impact from storm-induced waves. Typically, these zones are right along the coastline as in “beachfront property.”
Using the maps to determine the BFE and zoned degree of risk, the first mitigation step is to focus on keeping occupied space above the flood level. The term used to describe this is “freeboard,” which is defined as the elevation of a building’s lowest occupied floor above the base flood elevation. Many municipalities may have freeboard provisions already incorporated into their floodplain management ordinance, indicating, for example, +1 or +2 or +3, meaning that the lowest occupied floor for a home or building must be 1 foot, 2 feet or 3 feet higher than the established base flood elevation on the map. This approach does two things. First, it provides a bit of a safety factor, allowing for the underside of the structure of the lowest floor to remain above floodwaters or to guard against occasions when floodwaters may exceed the calculated BFE. Secondly, the actual floor elevation compared to the freeboard elevation is used as a basis to calculate flood insurance premiums. If the built floor elevation is at or above the freeboard elevation, then damage is expected to be less, meaning flood insurance premiums can be less. If the floor is below the freeboard elevation, then damage can be expected to be higher and premiums can go up drastically as a result.
This freeboard approach is good and certainly helps protect building contents and the building structure from the floor up, but we all know that something has to hold up that lowest occupied floor. In some cases it is a crawl space, while in others it could be a full-height car port or other non-habitable space under the building. The available height between grade and the first floor level will certainly influence how that space is used, but so will the building type. A residential building will create different opportunities and limitations compared to a commercial (non-residential) building. One thing that is similar, however, is the need to protect the structure in all cases from the forces of floodwater. Damage to the lower or foundation level is never good for any building since it can telegraph upward and impact the entire building above it. Hence, proper mitigation of the effects of flooding at the lowest level is critically needed.
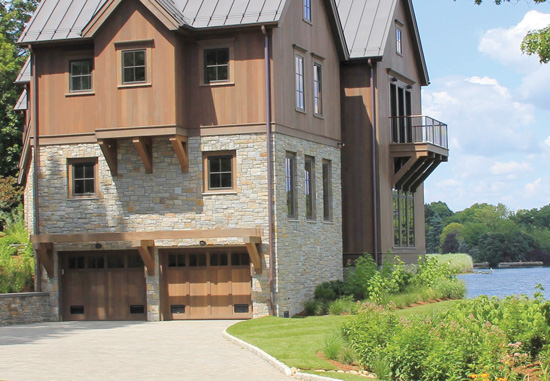
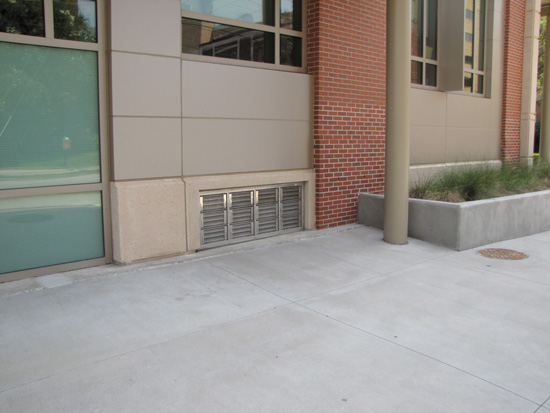
Photos courtesy of Smart Vent Products, Inc.
Commercial and residential buildings located in flood plains need to have proper flood mitigation as part of their design, such as the flood vents shown at the base of each of these buildings.
Tornadoes and Hurricanes
Residential and commercial buildings that incorporate safe rooms or shelters following ICC-500 or FEMA guidelines are becoming more popular, particularly among increasing urban populations seeking protection from violent tornadoes or hurricanes. The engineered construction of the walls, roof, and floor are fairly straightforward in terms of using substantial, reinforced materials (i.e. concrete, CMU, etc.) following the standards. However, the room or building will only be as strong as its weakest part, which in some cases has proven to be the door leading into it. Just as the walls and roof of a safe room are designed and built to protect against extreme winds and wind-borne debris, so too, the whole door assembly (door, frame, and hardware) must be designed together to do the same. When careful selection and installation of the safe room door assembly is not part of the overall design, then the safe room door opening can leave occupants at great risk of injury or even death during high-wind events.
Contrary to some perceptions, ordinary steel doors used in residential and commercial construction are not appropriate for safe rooms. There is a common misconception that a steel door marketed for storm protection with three locks and three hinges can provide the needed protection in tornadoes, but testing has demonstrated that they cannot. While they might remain in place and closed in some high-wind conditions, they cannot withstand the impact of the wind-borne debris, or “missiles,” that a tornado can propel. Dramatic failures have occurred when such wind-borne debris (wood studs, metal posts, sign supports, etc.) have struck steel doors. In some cases, the missile-like projectile can hit the door, penetrate all the way through, and either harm people inside or allow high winds to enter. In other cases, the hardware can be damaged and fail, allowing the door to swing open and/or shut in the wind and bringing the unwanted weather inside the safe room.
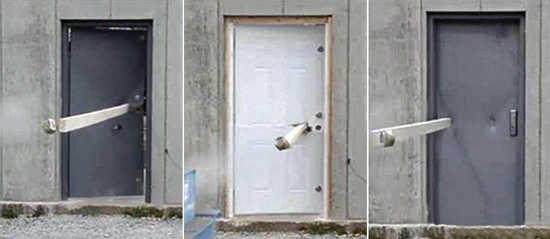
Photos courtesy of FEMA Federal Insurance and Mitigation Administration Fact Sheet, September 2014
Impact test results on safe room doors show failure at the latch/lock (left), failure by full penetration (center), and a passing condition that withstood both penetration and latch/lock failure (right).
FEMA points out that only door assemblies designed and tested to resist tornadoes can provide the needed life-safety protection for a safe room or shelter. In this case, the door assembly includes the door, hardware (locks and hinges), frame, and attachment devices used to anchor the door frame to the surrounding safe room wall. When selecting and specifying such assemblies, architects need to be sure that components have been tested together specifically for a tornado safe room. FEMA is not the entity that tests and certifies products, rather, the manufacturers of safe room door assemblies must obtain independent certification. The commonly accepted practice is through labeling by third parties, such as Underwriters Laboratories (UL), Intertek Testing Services (ITS), or others. Such labels specified for occupant protection should be issued by the agency that approved them to show basic information, including the name of the manufacturer plus performance characteristics, such as the test missile size and speed or test pressure.
Recognizing this testing and labeling, specifications can request documentation certifying that the door assembly is compliant with the most current versions of FEMA’s safe room publications (FEMA P-361 and FEMA P-320) or ICC-500 for a tornado wind speed of 250 mph. The entire safe room door assembly must have passed the required testing exactly as it is to be installed in the safe room to make sure it will withstand the required tornado wind pressures and debris impacts. This includes the door frame, the anchoring method, the door itself, and the hardware. Note that some suppliers may offer the door and frame without the tested hardware; if substitutions are made, the door may fail during a tornado. Installation instructions, whether in the specifications or from a manufacturer, should be specific to the actual safe room wall type of the building (e.g. wood frame, concrete masonry units (CMUs), etc.).
The significance of this total testing and certification cannot be overstated since there are plenty of non-tested “storm door” assemblies on the market promoted for use in safe rooms that may not perform as intended. In reality, there is no substitute for a tested and certified/labeled tornado safe room door assembly.
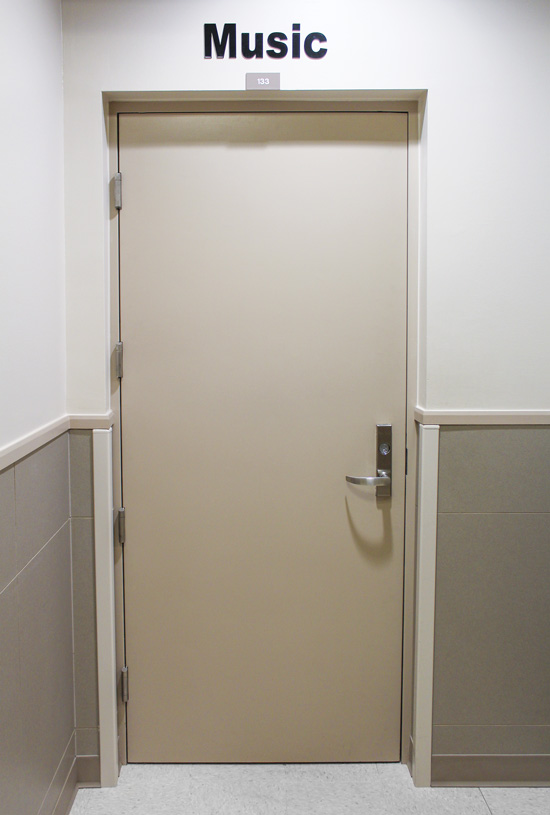
Photo courtesy of AMBICO Limited and Securitech Group, Inc.
Tornado safe room doors need to be tested and certified based on the specific assembly of the door panel, the door frame, and the hardware used, even when used in rooms that double for other uses.
Communication
During any extreme weather or emergency condition, effective communication between people is critically important. The FEMA and ICC-500 standards recognize this importance and include requirements for signage for Community Safe Rooms in particular (ICC 500 Sec 504). These requirements include a sign at every entrance to the safe room, indicating “Tornado Safe Room” or “Hurricane Safe Room,” plus the name of the manufacturer or builder of the safe room, its purpose (i.e. the storm type: tornado or hurricane), and the design wind speed. This information lets people know first of all that the room exists, and secondly what it is designed and constructed to withstand. Additionally, ICC-500 goes on to require an identifying sign, different from the entrance sign, depicting the general location of the safe room(s) and access ways. Such identifying signs should be posted in prominent locations 60 inches above the finished floor to the centerline of the sign. An identifying sign is required adjacent to access doors on the inside of the safe room, in the office of the facility manager, if present, and in the designated safe room manager’s area within the safe room, if present.
Where community safe rooms are located, the community should alert its citizens to their presence and indicate that they are open to the public by installing signs and publishing building manager contact information. The interior or exterior of the community safe room should have a sign that clearly identifies the building as a community safe room, indicating whether it is a tornado, hurricane, or combined community safe room. These information signs need to be placed in clearly visible locations, indoors or outdoors, to alert communities to the presence of the safe room, the intended occupants, the maximum number of occupants, the travel routes to the safe room, the location of the safe room entrance door, and other pertinent details. Depending on the population served, it may be necessary to include signs in languages other than English. Because of the nature of the facilities, all signage used needs to be durable, long lasting, and resistant to things like UV radiation from the sun, temperature, and weather.
During an extreme weather event, it is also imperative that people are able to reach community safe rooms quickly and without chaos. Starting at the larger scale, signs can also identify the area of the community the safe room is intended to serve and can be posted to show the best travel routes to the safe room location. Signs can also inform the residents of the neighborhood served by a safe room about the occupancy limitations during any given event. Wayfinding signage is critical for occupants to be able to readily find and enter the safe room, especially when a safe room is inside a larger building. Signage for safe rooms at schools and places of work should be clearly posted and should direct occupants through the building or from building to building. Main pathways should be marked to direct users to the community safe room. All signage should conform to the requirements of ICC A117.1, Accessible and Usable Buildings and Facilities.
Note that if the safe room is not open to the public, no signage should be placed on the exterior of the building. A safe room sign on the exterior of a non-public safe room is misleading and may result in an undesired response from the public. This unintentional miscommunication may be mitigated through community outreach and carefully placed and specifically worded safe room signage.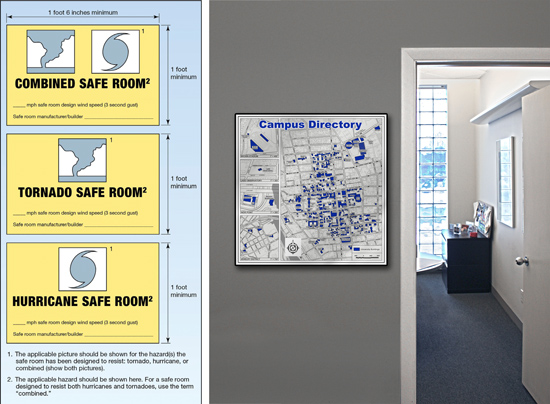
Images courtesy of FEMA and Metalphoto® Photosensitive Anodized Aluminum
FEMA and ICC-500 require very specific signage inside and outside of buildings that needs to be durable and clear.
Design Solutions
With an understanding of some of the design issues and standards surrounding tornadoes, hurricanes, and flooding, we can turn our attention to some ways to deal with those issues in buildings. The intent is to find ways to appropriately mitigate the effects of the severe weather on buildings and in doing so protect the occupants.
Floodproofing
The primary structural stresses responsible for flood damage on buildings comes from horizontal hydrostatic pressure that builds up on the outside of enclosure walls, thus pushing the walls inward. There may also be some vertical buoyancy forces on the foundation or first floor seeking to lift or float the building. This is compounded in buildings with enclosed sub-grade space, such as a finished basement, where saturated soil hydrostatic pressures and greater buoyancy forces under the basement floor can cause both lifting and collapse of a building. There are certainly some existing buildings that have this problem, but new construction or renovation that avoids any finished or habitable space below the base flood level will help avoid some of the effects of these lateral and vertical hydrostatic forces. Those that don’t address these forces typically find that as water rises up around a foundation, the wall cannot withstand the hydrostatic load and can crack, give way, or collapse inward.
Recognizing the significance of these hydrostatic forces, codes and regulations require mitigation efforts in the design and construction of buildings in flood zones. Specifically, all new construction and substantial improvements of fully enclosed areas (including crawl spaces and garages) below the lowest floor that are subject to flooding must be designed to automatically equalize hydrostatic flood forces on exterior walls by allowing for both the entry and exit of floodwaters. This means that the walls should not be designed to resist the hydrostatic pressure, but to offset it by allowing water to flow into the enclosed space and create equalized pressure on both sides. This is true whether the space is used for parking of vehicles, building access, storage, or any other function. Taken to the extreme, this approach would provide no walls at all, just “stilts” or piers that support the building and allow the water to fully pass under the first floor and around the supporting structure. While that may be appropriate for some design situations, it isn’t for all.
For foundations where perimeter foundation walls are required or desired, a technique known as “wet flood proofing” is common. This approach relies on achieving an equalized water pressure by using permanent openings in the wall with their size and placement calculated to allow the water to flow in and out quickly and evenly. If an equal depth of water exists on both sides of the wall, then the hydrostatic pressure is equalized on both sides, keeping the wall intact. This is regarded as the smart approach to floodproofing a building since it maintains flood storage capacity under a structure and allows the floodwater to take its natural path. Keep in mind that water from a flood could come quickly in multiple directions or slowly in one direction toward a building. Proper flood openings, also called flood vents, need to allow for the automatic entry and exit of floodwater regardless of the direction of flow of that floodwater. In the case of water entering slowly, that flow into an enclosure can cause outward pressure on an opposite or adjacent wall, so water needs to flow out as easily as it flows in. Further, debris is a fact of floods, and it’s something that the design of a flood opening needs to address so the debris passes through the opening and doesn’t clog it.
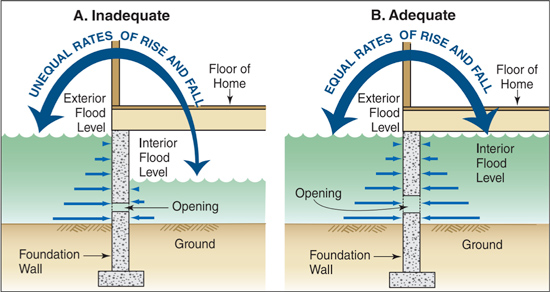
Image courtesy of Smart Vent Products, Inc.
Floodwater pushing against an enclosure wall needs to be equal in height on both sides in order to equalize the pressure on both sides of the wall.
The most critical criterion of a wet flood proofing design is keeping the buildup of head pressure within 1 foot on both sides of the wall. More than 1 foot of head differential on either side of the wall at any time during a flood event is considered a failed flood opening with the potential of the wall itself incurring significant structural damage or collapse. To prevent that from happening, engineered openings are certified to meet all of the codes and standards. ICC-ES Certified Engineered Openings provide passively operated, mechanical devices that float open to create an unobstructed area for floodwaters to travel through without the need for human intervention. In addition, they provide about five times more coverage than a non-engineered opening, which can be things like crawl space air vents or other products intended for other purposes. Non-engineered openings characteristically create unwanted obstructions to water flow and are notorious for collecting debris since they are usually fixed opening products with insect screening of some type. Hence, engineered openings are the only reliable solution.
To be fully effective, flood vents must be installed in at least two different walls. Further, the bottom of all openings must be within 12 inches of the highest adjacent grade directly below the opening to allow no more than 1 foot of head. When using ICC-ES certified flood vents, keep in mind that they must have an unobstructed, 3-inch-diameter opening or larger, and must pass a debris flow test. All flood openings must be passive, and they also must be bi-directional. In addition, designs must comply with the local floodplain management ordinances, as they sometimes go above and beyond the minimum NFIP requirements. As a design assistance resource, manufacturers of flood vent devices can provide a service to review architectural plans and calculate the quantity, placement, and type of flood vent devices for a particular building. They can help to ensure that designs are compliant with FEMA, NFIP, and construction codes, and may have CAD and BIM design files available to be easily implemented into floodplain building designs. Working together, the overall health, safety, and welfare of the occupants within that building or home remain the primary focus by assuring the integrity of the building structure during a flood.
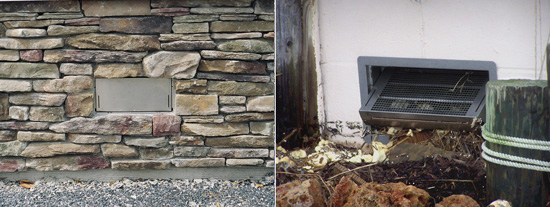
Photos courtesy of Smart Vent Products, Inc.
Insulated flood vents, when not activated, can blend into construction of a perimeter wall (left). Shown on the right, a dual-function flood vent, activated in the open position during a flood event, allows water and debris to flow freely into or out of the enclosed space.
Tornado Resistance
Resistance to both high winds and air-borne debris or “missiles” blown through the air have been shown to be critical in the design and construction of tornado safe rooms. The room construction, including all doors assemblies, needs to meet or exceed the requirements of ICC-500 and FEMA P-361 or P-320 as appropriate. The good news is these door assemblies are readily available from manufacturers who offer products with superior life-safety protection, while still allowing architects a good bit of freedom in design. Certified tornado resistant door assemblies are available in single opening sizes up to 4 feet by 8 feet and in paired openings up to 8 feet by 8 feet. Tornado shutters are also available in sizes as small as 2 feet 6 inches by 3 feet and go up from there. All of the above are available to be either in-swinging or out-swinging. Since these tornado-resistant safe rooms can also serve a dual purpose as community room, gymnasium, classroom, or assembly space, other door criteria may need to be specified, such as fire resistance and handicapped accessibility, which manufacturers can provide. Further, tornado doors, frames, and hardware can in some instances also provide blast-resistant openings, meet the acoustic requirements of LEED for Schools or the Collaborative for High Performance Schools (CHPS), or even meet the Department of Defense UFC 4-010-01 Minimum Antiterrorism Standards for Buildings.
When specifying tornado-resistant door assemblies, the first thing to look for is a single source for a complete package solution, including the frame, door(s), and hardware. This helps with quality control and the coordination of all elements working together toward the desired end of total safety meeting or exceeding the FEMA and ICC-500 requirements. Some manufacturers offer the option of factory installation of multipoint deadbolt systems to further enhance quality control. Such deadbolts can be critical components to the successful performance of the door and can come in a variety of types or styles consistent with other door hardware. Internal or concealed vertical deadbolts travel within the door and are typically reinforced by stainless steel guides. Surface-mounted bolts are also an option in traditional style or can tie directly into surface-mounted lock bodies for doors without mortise openings or pairs of doors without a mullion. Another option, to avoid using vertical bolts that secure the bottom of the door to the floor, is to utilize horizontal bottom bolts that project from the side door edge into the frame about 12 inches off the floor. This avoids costly maintenance efforts, and enhances reliability and aesthetics of the opening. When these doors are used for other room uses in buildings there is also hardware available that allows control of the deadbolts going from a single-point lock during regular use and becoming a multi-point lock during emergency conditions.
Installation of the door assembly in the field is the final but important step in having a tornado-resistant door become part of a safe room or shelter. Some manufacturers offer certified installation courses to contractors because they recognize that the field installation is critical to life safety. With such a certification course, architects and owners can have some peace of mind that once installed in the field, the door assembly performs the same way it does in the testing lab. To streamline field installation, some manufacturers also offer factory installation of the multi-bolt security hardware in the door. When specified by the architect, this ensures proper installation and function of the hardware so that all life safety and functionality is maintained. This option can offer a net savings to the project, as the manufacturer can normally install the device more efficiently in the factory environment than can be accomplished in the field.
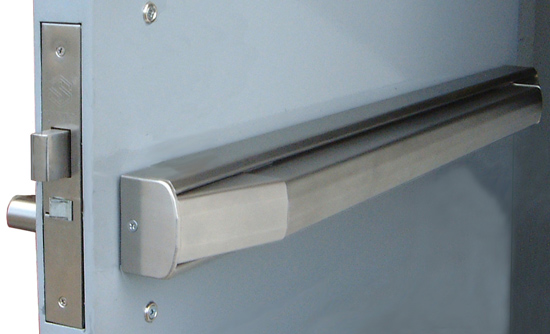
Photo courtesy of AMBICO Limited and Securitech Group, Inc.
Certified and labeled door assemblies include heavy-duty latch/lock hardware and deadbolts in either horizontal or vertical locations, or both.
Durable Communication
Designing the needed signage in safe rooms or FEMA Shelters is fairly straightforward. Picking the best material and signage system so that it remains intact and readable for years or decades to come during both normal and extreme weather use requires some attention to detail. First, it is necessary to understand the potential conditions that the signage will encounter. Any exterior signage needs to handle weather of all types, such that it holds up against precipitation, heat, freezing, condensation, wind, and all related conditions. It must also be able to remain clear without clouding or fading from bright sunlight, which carries color damaging ultraviolet (UV) radiation. In public places, whether the signage is placed indoors or out, it must be vandal resistant and easily cleaned in the event of any markings from people, graffiti, etc. In all, the signage needs to be as tough as the safe rooms and shelters that they are directing people to.
There are certainly a number of choices of materials to consider, but one that is particularly noteworthy is photosensitive anodized aluminum. This is a specialized type of anodized aluminum used to make durable, high-resolution signage. The material was first developed in 1950 for the U.S. Navy and has been reliably used since then by many engineers, designers, and architects for permanent identification of items installed in harsh environments. Some noteworthy applications include things like international space station labels, off-shore crane nameplates, labels, and control panels, along with signage and labels on army tanks and aircraft carriers. The material has held up for decades despite these unusually harsh environments, which include extreme temperature swings, intense UV exposure, corrosive salt-spray, and sand abrasion. In 2011, the U.S. Navy conducted an evaluation of 73 materials used for these type of identification and communication purposes. That test found photosensitive anodized aluminum earned more high scores than any other material evaluated.4
The manufacturing process to make this aluminum signage is essentially a photographic process using a silver-halide-based image that is sealed inside of the anodic layer of anodized aluminum. Hence, it becomes part of the aluminum base, not something that is applied on top and not something that is etched. As such, it is as durable as any anodized aluminum finish and just as resistant to fading or abuse. As a photographic medium, the graphic image capabilities are practically limitless. Architects and designers can use it to reproduce and display detailed drawings or photographs as well as signage. The other advantage of the photographic nature is that it can easily create variable data—producing hundreds or thousands of unique signs with different information, QR codes that link to websites, or other variable, custom-designed information.
Photosensitive anodized aluminum typically produces a black and silver photographic image. Color can be added but is not recommended for long-term outdoor usage unless it is protected with a laminate. Either way, the material allows designers to capture rich, photographic-quality images inside of the metal itself, thus providing its notable longevity and durability all in the contemporary look of anodized aluminum. The material is generally available in four finishes including matte, #4 heavy grain, gloss, and satin/mill. It can be specified in thicknesses as thin as three thousandths of an inch up to an eighth of an inch, depending on project needs and mounting conditions. While it will not need to be replaced as often as other signage, if replacement is desired, this all-aluminum product is 100 percent recyclable.
The cost of this type of signage will vary by size and thickness of the plates desired. When architects can work directly with the manufacturer, prices tend to be below market rates for other types of architectural signage. That means it may also make sense to coordinate it with other signage used in a building project. That could include address signage, general wayfinding, donor recognition, custom facade treatments, educational signage, and even building certification plaques, such as LEED recognition plaques.
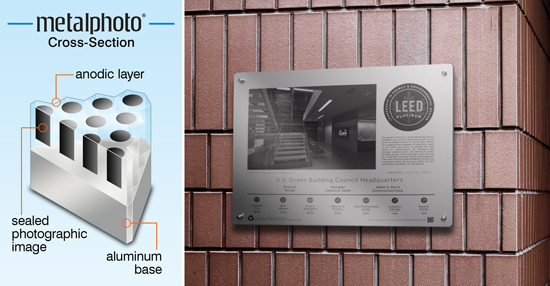
Images courtesy of Metalphoto® Photosensitive Anodized Aluminum
Photosensitive anodized aluminum signage creates photographic imagery embedded inside the anodic layer, contributing to long-lasting, durable, and fade-resistant communication.
Conclusion
Severe weather is increasingly becoming a design concern for many buildings. This is true for a number of weather types, but particularly for flooding, tornadoes, and hurricanes. Understanding the design issues, code requirements, and standards for performance allows architects and other design professionals to incorporate mitigation measures into new and renovation building projects. Successfully doing so will allow buildings to be resilient enough to survive these severe weather events, but more importantly help people to survive.
Peter J. Arsenault, FAIA, NCARB, LEED AP is an architect and green building consultant who has authored more than 120 continuing education and technical publications as part of a nationwide practice. www.linkedin.com/in/pjaarch
Endnotes
- Storm Events Database. National Oceanic and Atmospheric Administration. Sept. 2015. Web. 22 Jan. 2016. www.ncdc.noaa.gov/stormevents.
- Katz, Richard and Smith, Adam. U.S. Billion-Dollar Weather and Climate Disasters: Data Sources, Trends, Accuracy and Biases. Natural Hazards, 3 Feb. 2013. Web. 22 Jan. 2016. http://link.springer.com/article/10.1007/s11069-013-0566-5.
- FEMA P-361: Safe Rooms for Tornadoes and Hurricanes: Guidance for Community and Residential Safe Rooms. Third Edition, March 2015, 28 Dec. 2015. Web. 22 Jan. 2016. www.fema.gov/fema-p-361-safe-rooms-tornadoes-and-hurricanes-guidance-community-and-residential-safe-rooms.
- Item Unique Identification (IUID) Environmental Survivability Testing Report: Independent Assessment of Vendor-Supplied Materials. Rep. Vol. 1.0. Corona Division Item Unique Identification (IUID) Center: Naval Surface Warfare Center, Aug. 2011. Web. 22 Jan. 2016. http://www.acq.osd.mil/dpap/pdi/uid/docs/IUID_Environmental_Survivability_Testing_Report.pdf.
![]() |
|
![]() |