Creating Safer Spaces in Healthcare
Impacts, performance, and outcomes of rubber flooring
Continuing Education
Use the following learning objectives to focus your study while reading this month’s Continuing Education article.
Learning Objectives - After reading this article, you will be able to:
- Explain how the use of rubber flooring in healthcare environments addresses outcomes associated with Pay-for Performance (P4P), Value-Based Purchasing (VBP), HCAHPS, and Hospital-Acquired Conditions (HAC).
- Discuss the value attributes of rubber flooring, and how informed product decisions drive product selection in support of: clinical efficiency, operational outcomes, and patient experience.
- Review the available “Tools and Resources” developed for managing risk and improving outcomes in the healing environment such as: The FGI Safety Risk Assessment (SRA), The Joint Commission (TJC) Targeted Solutions Tool (TST), The Center for Health Design, and related organizations and initiatives.
- Evaluate goals in flooring selection and design as they relate to evidence-based performance characteristics of cleanliness and quietness of the healing environment, safety, patient experience, staff fatigue, infection control, and ROI.
As we transition from volume-based to value-based, patient-centered care. Health systems must improve the quality of care and deliver it at a lower cost by operating more efficiently, improving patient outcomes, and increasing patient satisfaction.
Healthcare leaders in the C-suite are faced with cultural, operational, and organizational changes that profoundly affect their business models. The reimbursement drivers and domains are focused on patient-centered care, outcomes, and the ability to improve the quality and reduce the cost of care in the healing environment. In this course, we will address how Pay-for Performance, Value-Based Purchasing, HCAHPS, Readmission Reduction Program, and Hospital-Acquired Conditions specifically relate to flooring selection, specification, safety, outcomes, and maintenance in the built-environment.
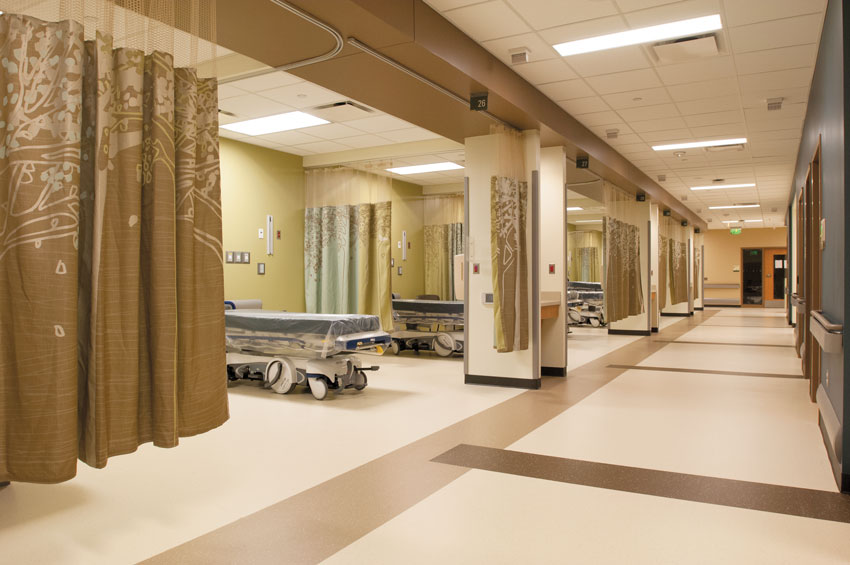
Photo courtesy of nora systems, Inc.
New Parkland/Parkland Health & Hospital System, Dallas, Texas
“Rubber is a great fit for healthcare, as it doesn’t require the same kind of maintenance that you have for some of the vinyl products; it is wax-free,” says Robyn Roleofs, senior interior designer at HDR+Corgan. “It is also naturally antimicrobial and is quieter than a lot of our other floors. Acoustic control and sound transmission are hugely important to help patients heal faster.”
In healthcare, we have choices. First impressions drive emotional response. As individuals, we want to feel safe in our physical environment, as a patient, caregiver, employee, or family member.
This course focuses on how the Pay-for Performance (P4P) domains affect patient-experience, clinical outcomes, operational efficiency, clinical process of care, and safety—the fundamental drivers for reimbursement. As the foundation of the healing environment, flooring encompasses every square inch of the healing environment.
All rubber flooring is not created equal. The materials and production variables produce floors that can and do differ significantly in terms of durability, stain resistance, maintenance, and reparability. Nine widely available commercial rubber floor coverings were selected and put through a series of tests. It was evident that production variables can alter the value attributes for reducing noise, increasing cleanliness, and controlling infection, eliminating exposure to cleaning chemicals, reducing time and expense needed for maintenance, and enhancing both the caregiver and patient-experience.
Investments in the safety and performance of flooring must consider health, safety, and welfare as they pertain to the business decisions healthcare facilities are facing today. The design community—architects, interior designers, and key stakeholders in healthcare—need a clear understanding of the terminology, operational drivers, and tools surrounding value-based patient-centered care.
In collaboration, manufacturer partners need to create products that support outcomes based on performance characteristics of rubber flooring products, which vary significantly, even within the same general material category.
Navigating the Acronyms
The following is a brief overview of the key abbreviations, and the operational domains and drivers as defined by reimbursement drivers, as the basis for understanding how they relate to creating safer spaces and the value attributes of rubber flooring products. The programs and concepts are discussed in more detail throughout this course.
CMS: Centers for Medicare and Medicaid Services is the government organization within the Department of Health and Human Services (DHS) that manages Medicare and Medicaid and administers Health Insurance Portability and Accountability Act (HIPAA).
HAC: Hospital-Acquired Conditions are illnesses or complications that patients contract during their hospital stays and that are considered highly avoidable. Since 2008, Medicare has not reimbursed hospitals for additional costs for care related to these conditions. As is relates to flooring, falls and trauma, and materials that passively fight infection are in demand.
HCAHPS: The Hospital Consumer Assessment of Healthcare Providers and Systems survey results produce data about Patient Experience of Care that allows for objective and meaningful comparisons of hospitals. It encompasses eight domains of hospital quality associated with overall patient satisfaction.
1. Communication with nurses
2. Communication with doctors
3. Responsiveness of hospital staff
4. Pain management
5. Cleanliness and quietness of hospital environment
6. Communication about medicines
7. Discharge information
8. Overall rating of hospital
The list of domains is available at https://www.medicare.gov/HospitalCompare/Data/Patient-Experience-Domain.html. Survey results are available at www.medicare.gov/hospitalcompare/search.html.
P4P: Pay-for Performance rewards quality, not volume. It is not a single form of reimbursement, but bases payments on measures of clinical quality, safety, efficiency, and patient satisfaction.
RRP: Readmissions Reduction Program penalizes hospitals for having a high rate of discharged patients readmitted to a hospital within 30 days of a prior acute care stay.
VBP: Value-Based Purchasing is a national program for acute-care hospitals. The VBP adjusts Medicare reimbursement up or down, withholding a portion that can be earned back by performing well on a set of five quality metrics: Process of Care, Patient-Experience, Outcomes, Efficiency, and Safety. HCAHPS is a component of VBP.
TPS: Total Performance Score is scored out of a possible 100 points on CMS Core Quality Measures, a very wide range of process, procedure, and outcome metrics; and 25 percent based on survey results from the HCAHPS, which drives payment redistribution. (See Figure 1 below.)

Image courtesy of nora systems, Inc.
CHD: The Center for Health Design is a non-profit organization dedicated to improving the quality of healthcare through design of the built-environment. CHD is a source of extensive research on the value of design to improving health outcomes, patient experience of care, and provider/staff satisfaction and performance.
EBD: Evidence-Based Design is the process of basing decisions about the built-environment on credible research to achieve the best possible outcomes.
FGI: The Facility Guidelines Institute enhances the content and format of Guidelines publications that encourage and improve their application and use. It published the 2014 consensus-based and evidence-based revision to the Guidelines for Design and Construction of Hospitals and Outpatient Facilities.
Hospital Safety Score: A letter grade scoring system for consumers, which uses national performance measures from the Leapfrog Hospital Survey that grades hospitals on how safe they keep patients from errors, injuries, accidents, and infections. Searchable hospital scores can be found at www.hospitalsafetyscore.org.
SRA: The new Safety Risk Assessment (SRA) Toolkit for Health Care Facility Environments is a resource created to support the 2014 FGI Guidelines. The SRA was created through extensive review of research, consensus building with industry experts, and pilot testing. Its aim is to help healthcare design teams proactively identify and mitigate built-environment conditions that may impact patient and worker safety in healthcare environments. (A PDF version of the Toolkit is available at https://www.healthdesign.org/insights-solutions/safety-risk-assessment-toolkit-pdf-version#sthash.ZNEk4uPD.dpuf.)
There are six safety issues included in the SRA Toolkit: infection control, patient handling, falls, medication safety, behavioral health, and security. The attributes of rubber flooring can be actionable as it relates to infection control, acoustics, and falls.
TJC: The Joint Commission. Created in 2008, TJC Center for Transforming Healthcare aims to solve healthcare’s most critical safety and quality problems. In July of 2014, the Targeted Solutions Tool (TST)® became available as an innovative application that guides healthcare organizations to accurately measure their organization’s actual performance, identify barriers to excellent performance, and direct them to proven solutions.
Connecting P4P Drivers and Rubber Flooring Attributes
Flooring affects all aspects of health, safety, and well-being in the healthcare setting. The floor is the most visible component of the space and provides the surface for all activity.
In 2012, CHD, with a number of partners, sponsored the creation of a report and checklist, “Achieving Evidence-Based Design Goals through Flooring Selection and Design,” which will be referenced in this course.i
It explored industry standards and best practices related to flooring. Flooring surfaces were examined using an Evidence-Based Design approach to define how flooring can contribute to the following performance-improvement goals:
1. Reduce slips, trips, and falls
2. Reduce patient and staff injuries associated with falls
3. Reduce noise levels
4. Reduce staff fatigue
5. Reduce surface contamination and potential risk of HAIs
6. Improve indoor air quality (IAQ)
7. Improve patient and family satisfaction
8. Represent the best return on investment
Evidence-Based Design is an approach to environmental design (architectural, interior, and landscape) that aspires to base design decisions on documented research and well-established best practices, with the aim of improving outcomes. Evidence-Based Design is increasingly common in the design of healthcare facilities, where the approach has found support among healthcare administrators, many of who are familiar with the conceptually comparable notion of evidence-based medicine. Healthcare environments designed on the basis of solid research evidence are intended to improve patient safety, reduce stress, increase care delivery effectiveness, and enhance quality of care—objectives that contribute to the overarching goals of improved patient, staff, and organizational outcomes.ii
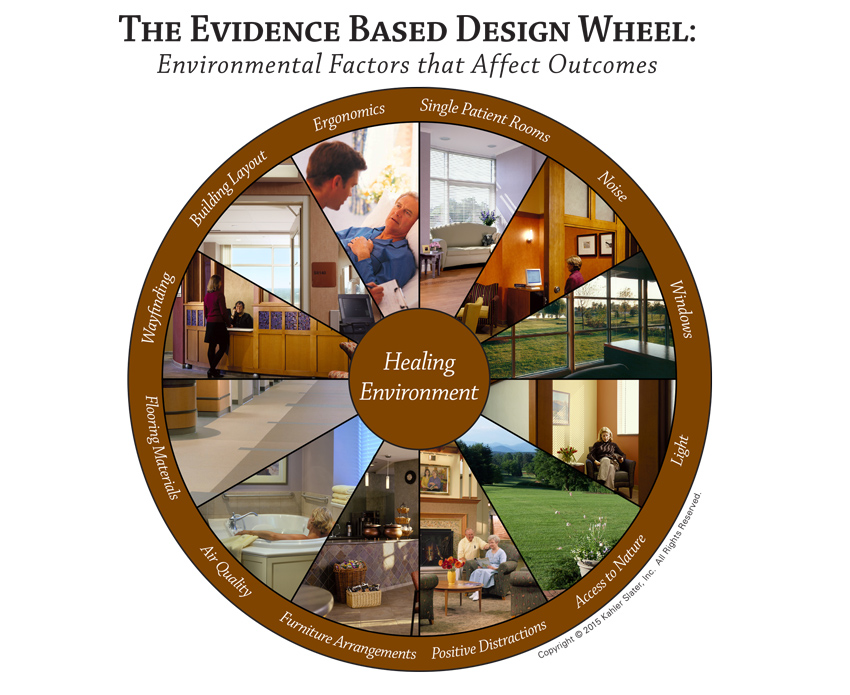
Image courtesy of Kahler Slater Architects Inc. ©2015
The product attributes of specific rubber flooring products offer actionable solutions to P4P drivers in each of these areas as discussed above. In a study conducted by the Florida Hospital - Office of Design, on the perceptions and experiences of users, specifiers, and installers of various common types of healthcare flooring, found that those interviewed for the case studies had “positive experiences to report about rubber flooring, and some of the clinical and maintenance staff had glowing praise for rubber flooring.”
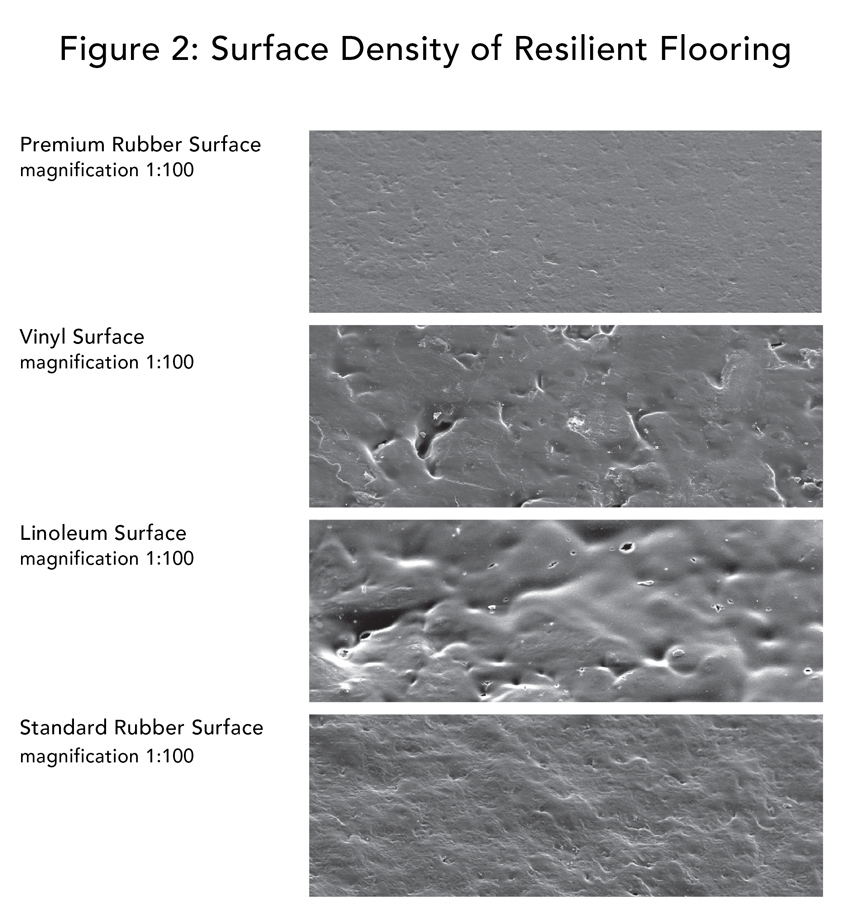
Image courtesy of nora systems, Inc.
As a performance example, if a patient room has to be turned over rapidly between patients, there may only be time to mop the floor, which is not sufficient disinfection protocol for terminal cleaning. There are specific rubber floor products where the entire patient room can be steam cleaned and dry in less than 15 minutes. Thus, making an actionable impact on clinical efficiency and patient perception as it relates to HCAHPS.
There are significant differences among rubber flooring products. The highest-quality rubber floorings have extremely dense, closed surfaces (see Figure 2 above) and are inherently dirt-repellent due to a special production process that ensures optimum material cross-linking. The advantages include reduced susceptibility to soiling, improved hygiene properties, and lower outlay for care with no need for cleaning chemicals exposed to patients and caregivers.
Surface density also has an impact on slip/trip/falls, on transportation over the surface, for example of rolling loads related to moving equipment, and on ergonomics directly related to the comfort of caregivers, staff fatigue, patient comfort and safety, and their positive perception of the environment.
There are differences in maintenance needs, as well. A common perception is that no rubber floor needs to be waxed, but some manufacturers actually require it as part of the regular maintenance cycle. Maintenance on premium rubber flooring products is to simply clean with water as there is no factory-applied finish to maintain.
As noted in the CHD Evidence-Based Design study above: “Rather than using a generalized flooring category, the design team must evaluate individual products based on their performance against each EBD goal before deciding on the right flooring material and design for a particular area. Consider the trade-offs for each product.” Operational optimization, clinical efficiency, indoor air quality, and patient satisfaction are all impacted by flooring selection and de-selection.
The next sections examine specific attributes of rubber flooring products with impact on noise reduction, infection control, safety, and efficiency during operation and maintenance. Each of these drivers are key considerations when it comes to creating safer spaces in the healing environment with products that provide actionable solutions to the financial drivers surrounding P4P.
Working Through the Noise
A patient being rolled through a corridor, equipment alarms, caregiver conversations, or environmental services doing routine floor maintenance are all significant contributing factors to sound levels in the healing environment.
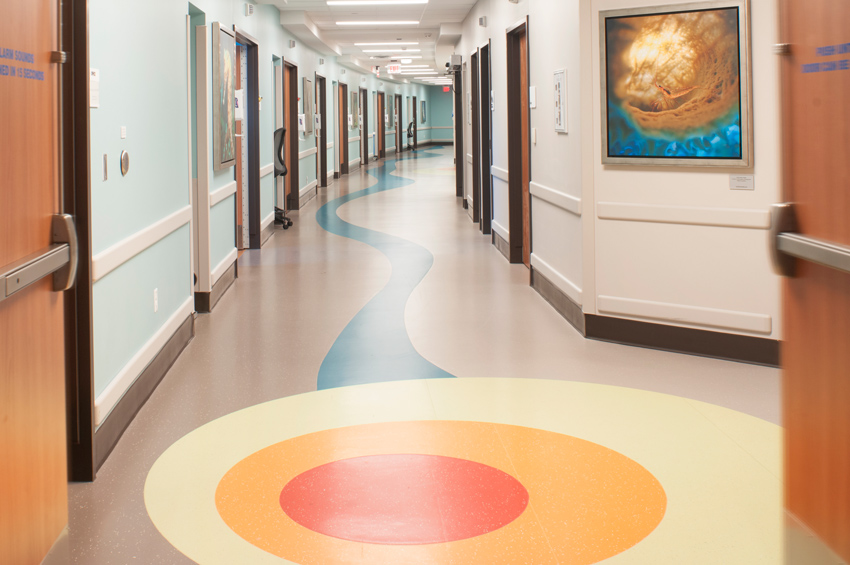
Photo courtesy of nora systems, Inc.
Children’s of Alabama, Birmingham, Alabama
“The flooring helps with the noise, as it absorbs sound better, which gives the patients the quiet they need,” says Denise Dexter, facilities design director at Children’s of Alabama.
Noise levels in hospitals have long been a source of complaints. Evidence-based research studies have shown noise also has a direct, measurable negative impact on healing. For example, noise is an error-provoking condition that causes sleep disruption that affects wound healing, and increases the need for medication and the length of the stay.
Noise also has been associated with undue stressors, having negative impacts on caregivers, and can be an error-provoking condition. It is strongly related to stress and annoyance among nurses, increased fatigue, emotional exhaustion and burnout, and difficulty in communication possibly leading to medication errors.
Contributing to the overall Patient Experience of Care domain score, where flooring can be attributed to the score, HCAHPS survey question #9 asks, “During this hospital stay, how often was the area around your room quiet at night?” This question consistently receives the lowest patient scores.
The FGI Guidelines recognize that the built-environment has a profound effect on health, productivity, and the natural environment, and requires a minimum standard that healthcare facilities be designed within a framework that recognizes the primary mission of healthcare.
The 2014 FGI Planning and Design Criteria for Acoustic Design:
1. Site Exterior Noise
2. Acoustic Surfaces
3. Room Noise Levels
4. Interior Wall and Floor/Ceiling Construction
5. Speech Privacy
6. Building Vibrationiii
Clearly, noise is affected by more than the floor. Interior finish selections have a direct correlation to patient well-being, satisfaction, HCAHPS scores, and caregiver retention. Acoustics are related to the noise reduction coefficient (NRC), sound transmission class rating (STC), and ceiling attenuation class (CAC) of ceiling tiles in partnership with the flooring attributes and wall surface finish. There is currently no evidence that links any flooring to a significant reduction of airborne sounds like speech within the same room when measured by STC.
ASTM E2179: Standard Test Method for Laboratory Measurement of the Effectiveness of Floor Coverings in Reducing Impact Sound Transmission through Concrete Floors is the standard test method used by resilient flooring manufacturers to market their floorings acoustic performance. The values are calculated in accordance with ASTM E989: Standard Classification for Determination of Impact Insulation Class (IIC). However, these results are only relevant if noise is a concern from either the room above or below, a situation which rarely exists in healthcare settings, as the entire ceiling and subfloor assembly on its own will typically reduce the sound transmission sufficiently.
The test method requires measurement of the entire ceiling and subfloor assembly, and the different testing facilities will vary considerably. That is why they must test both with and without the flooring installed so the facilities ceiling and subfloor assembly can be calculated out and the resulting value is for the flooring only. That value is stated as a Δ (delta) IIC value, without the entire ceiling and subfloor assembly. Higher values represent better sound absorbency level so at first glance flooring with a Δ IIC value of 14 does not compare well with an IIC value of 34. However, if the flooring assembly has an IIC of 28 then the true Δ IIC value of that flooring would only be 6. To make informed decisions, verify the values are stated in Δ IIC for comparative analysis.
Many product manufacturers represent their information in the European Union (E.U.) utilizing the ISO 140 test method, which is very similar to ASTM E2179. The calculated improvement in impact sound insulation value of the flooring is reported as a Δ Lw = value dB. This is simply a different measuring system like comparing metric and U.S. customary units. Similar to the IIC, the results for comparative analysis must be Δ Lw dB.
As the foundation of the built-environment, flooring plays a primary role in noise generation. Everything from chair casters, cleaning equipment (steam cleaning of rubber floors is much quieter), and hospital alarms to rolling equipment and walking with hard-soled shoes are all significant contributing factors to sound levels.
Another independent study has shown that rubber produced the least impact noise when installed directly on a concrete subfloor. The following information provides the results of comparative noise generation testing performed on seven different floor coverings. In this study, a repeatable test method was conducted on each of the floor coverings installed on a concrete subfloor and in the center of the same hemi-anechoic chamber (sound-absorbing room). A loud tapping machine was placed in four standard positions at the center of the room in accordance with ASTM E492: Standard Test Method for Laboratory Measure of Impact Sound Transmission Through Floor-Ceiling Assemblies. Using the same tapping machine, measurements were taken one meter away from the tapping machine at a height of 5 feet, to simulate an operator’s ear position.
In the test results shown in Table 1, the lower the value, the quieter the facility. The results indicate that, when tested under identical conditions, there is a significant difference amongst the most widely available commercial floor coverings.
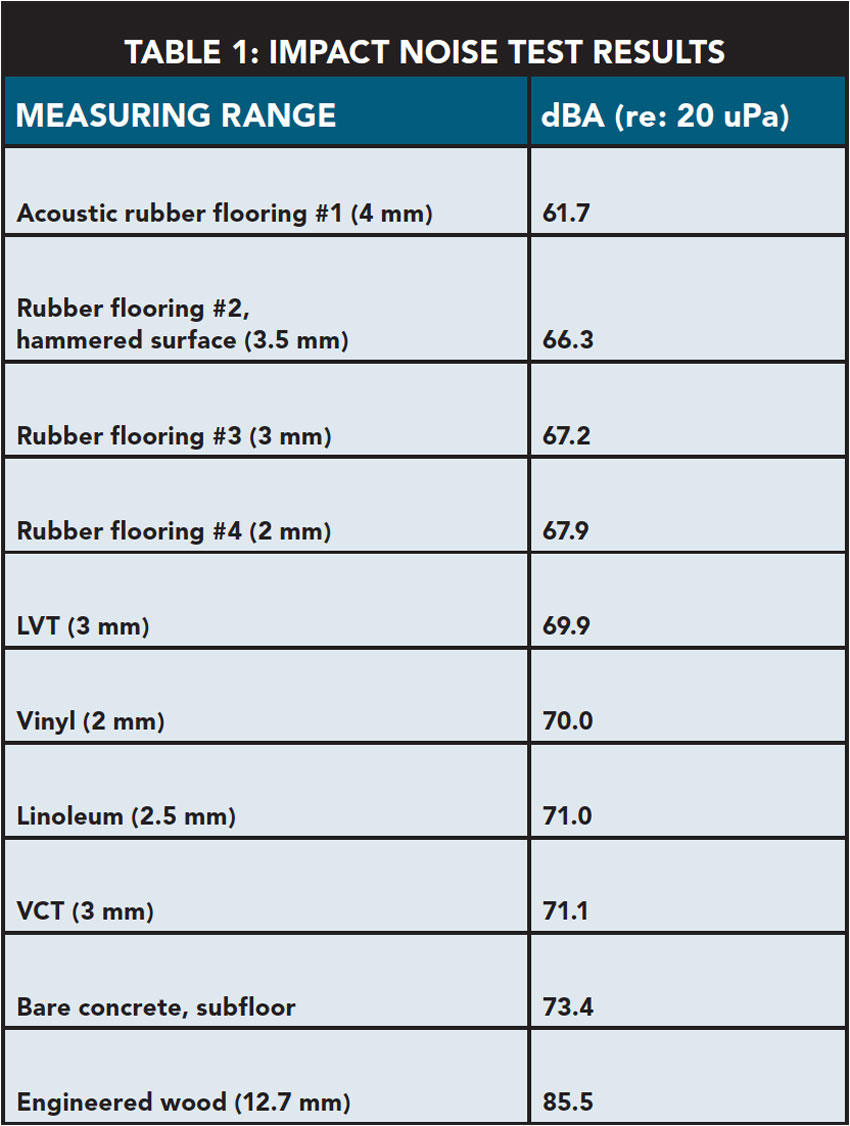
Image courtesy of nora systems, Inc.
Lower values mean less noise in the environment as represented by the loud tapping machine.
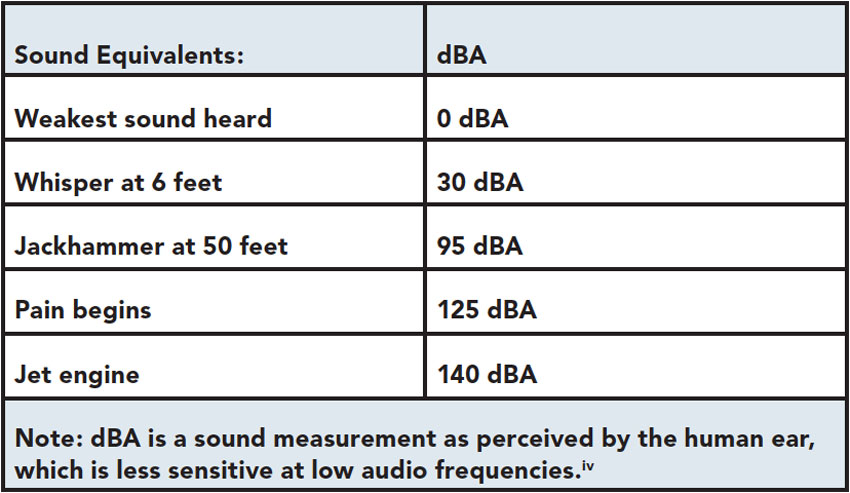
Image courtesy of nora systems, Inc.
The World Health Organization (WHO) guideline values for continuous background noise in hospital patient rooms at 35 dBA during the day and 30 dBA at night, with night time peaks to not exceed 40 dBA. The sound of 30 dBA corresponds to a whisper at a distance of 6 feet.v
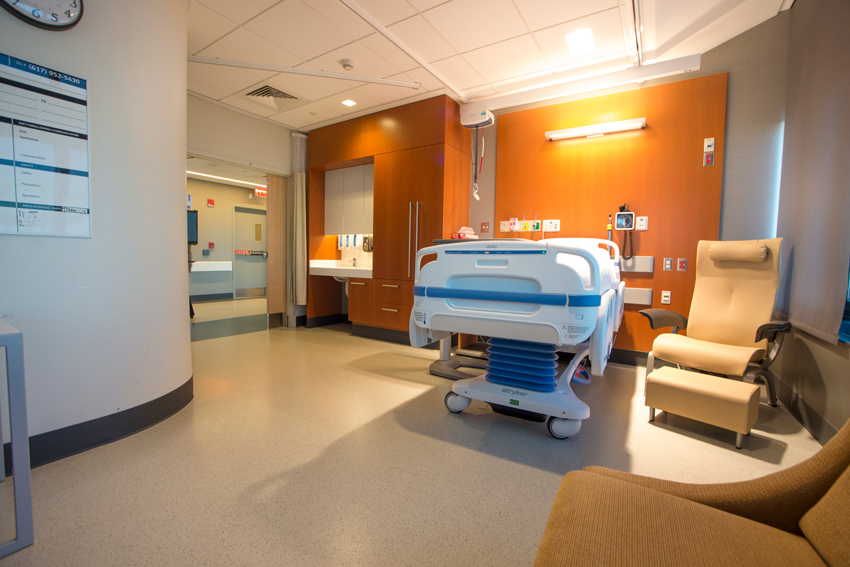
Photo courtesy of nora systems, Inc.
Spaulding Rehabilitation Hospital, Partners Healthcare, Boston, Massachusetts
“It was important to find a floor that ensures the safety and comfort of patients using canes, wheelchairs, and crutches,” says Betsy Pillsbury, disability resources coordinator. “The floors in this building are very smooth and not slippery,” says Pillsbury. “One of the differences we noted from patient satisfaction surveys is that the noise level here is much enhanced,” adds Paula Hereau, vice president of operations.
Patient Perception, HCAHPS, and TPS
In the HCAHPS survey, question #8 asks, “During the hospital stay, how often was your room and bathroom kept clean?” The patient’s perception of cleanliness has an important impact on a facility’s TPS, and thus on payments.
The dimensional stability and resilience of rubber does not trap dirt or bacteria in specific rubber products. Rubber has an inherent resistance to bacteria and fungi without any chemicals or additives. Rubber allows for non-welded seams, as they contribute to a more hygienic environment, with the exception of the OR. The Centers for Disease Control (CDC) survey, based on a large sample of U.S. acute-care hospitals, found that one in 25 hospital patients had at least one HAI. There were an estimated 722,000 HAIs in the United States in 2011. About 75,000 hospital patients with HAIs died during their hospitalizations. A separate CDC study of medical costs estimates that the overall annual direct medical costs of HAI to U.S. hospitals ranges from $35.7 billion to $45 billion.vi
HAIs, along with falls and 30-day readmit, are non-reimbursable “never events” (also called “sentinel events”): events that should never happen. Their occurrence has direct impact on the facility’s bottom line. Although there is no existing evidence that links flooring to HAIs, the use of carpet in patient areas is perhaps its most controversial consideration. A number of studies establish the role of carpet as a reservoir for fungi and bacteria.vii One study proposes that new carpeting becomes contaminated very quickly, and the effect of cleaning carpet is transient—bacterial levels soon return to pre-cleaning levels.viii Moreover, bacterial contamination increases with higher levels of activity, and soiled carpet that is damp or wet provides the ideal setting for bacteria to proliferate. Wet carpets are a slip/trip/fall hazard and can propagate microorganism growth.ix
Regarding infection control, the FGI SRA recommendations on infection prevention include: “Select interior finish materials for patient care areas, especially high touch surfaces (e.g., floor, wall, ceiling, furniture covering, door handles) that are easy to clean, disinfect, and maintain or contain antibacterial characteristics in order to minimize the risk of surface contamination. Research shows that the contamination of environmental surfaces may serve as a link in the chain of infection transmission. Certain surface materials have been reported to be easier to clean, disinfect, and maintain and are associated with lower risk of contamination.”x
As noted above, there are specific rubber flooring products that do not act as media to micro-organisms, meaning these products do not encourage or produce bacteria. Relevant standards include:
• ASTM E 2180: Standard Test Method for Determining the Activity of Incorporated Antimicrobial Agent(s) in Polymeric or Hydrophobic Materials
• ASTM G 21: Standard Practice for Determining Resistance of Synthetic Polymeric Material to Fungi
Rubber flooring products should not contain any of the 15 antimicrobial chemicals and elements as additives that leading healthcare organization Kaiser Permanente has recently banned as additives to fabrics, furnishings, and finishes in its building projectsxi:
• Benzisothiazolin 3-one
• Didecyldimethylammonium chloride (DDAC)
• Diiodomethyl p-tolyl sulfone
• Hexamethylenetetramine
• Kathon 886 (CIT/MIT mixture)
• Methylchloroisothiazolinone (CIT, CMIT)
• Methylisothiazolinone (MIT)
• N-octadecyldimethyl [3-(trimethyoxsilyl) propyl] ammonium chloride
• Silver (nano)
• Silver sodium hydrogen zirconium phosphate
• Silver zinc zeolites
• Triclosan
• Zinc pyrithione
• 4,4-dimethyloxazolodine
• Quaternary ammonium compounds, benzyl-C8-16-alkyldimethyl, chlorides
Creating Safer Spaces
Falls have been identified by CMS as an event that is preventable and should never occur. Yet falls are the most common adverse event reported in hospitals. Reviews of observational studies in acute care hospitals show that fall rates range from 1.3 to 8.9 falls per 1,000 patient days. Between 30 to 35 percent of patients who fall sustain an injury. Each of these injuries, on average, adds on 6.3 days to the hospital stay, and the cost for a fall with injury is about $14,056. (Joint Commission Prevent Falls Project). A single nurse fall is estimated to cost a hospital approximately $33,000. Rubber flooring cannot provide a measurable effect, but it can have an actionable impact on slips/trips/falls (STF).
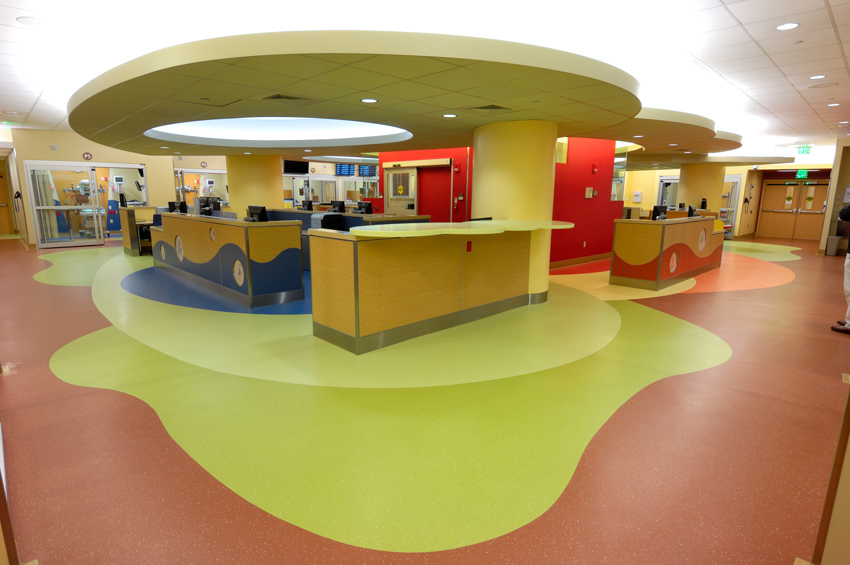
Photo courtesy of nora systems, Inc.
Baystate Medical Center/Baystate Health, Springfield, Massachusetts
“Staff members really like the flooring because it has a little bit of cushion to it,” says Stanley Hunter, project executive at Baystate Medical Center.
Falls in healthcare have far-reaching negative impacts on the patient’s recovery and quality of life, but also on the bottom line of the hospital, and because costs associated with the treatment of a fall are no longer reimbursable. CMS has identified 14 categories for HACs (the complete list is available at https://www.cms.gov/medicare/medicare-fee-for-service-payment/hospitalacqcond/hospital-acquired_conditions.html). “Falls and trauma” is the category on the list that can be directly attributed to flooring.
Flooring-Related Issues Impacting Fall Protection
For healthcare applications, the following issues are paramount to understand when evaluating specific flooring products to create safer spaces; these include the floor material, the floor finish, type of maintenance, and the coefficient of friction. Other factors include the ageing eye, change in height due to floor transitions, and floor pattern (color value, light reflectance value, glare, and the texture of the surface). Flooring selection must weigh these factors of fall prevention against closely related priorities, such as preventing staff fatigue (which has been shown to contribute to slips, trips, and falls) and enabling heavy equipment to be moved safely and efficiently.
Slip Resistance
Coefficient of Friction (COF) is the ratio between the tangential force needed to start or maintain uniform relative motion between two contacting surfaces and the perpendicular force holding them in contact. COF is often considered the only relevant component of slip resistance, but multiple factors contribute to the slip resistance of a floor, and even COF can be complicated to measure effectively.
The option considered most useful for comparing the COF of resilient flooring is to test using a modified version of ASTM D2047 without polish (unless the flooring requires it) and using a dry neolite (material of most of today’s shoe soles) sensor. This test method is currently being developed by the ASTM F06 committee. Most resilient flooring manufacturers already use this method and publish the values. The flooring manufacturer should provide testing reports, including the test method and the machine and sensors used, and if possible testing information on pre-aged samples of the product that will indicate long-term performance.
Glare
The average age of the typical inpatient population is 65; a caregiver’s average age is 55. Glare can alter cognitive perception, and visual acuity with the ageing eye can be a trip hazard. “Shiny” does not equal clean. By correcting this frequent misperception, a non-glare, finish-free product installation will impact HCAHPS scores not only for noise, indoor air quality, and cleanability, but also for safety related to mobility. The SRA recommendation to “Design to minimize glare on floor (e.g., flooring material, lighting, windows)” cites research demonstrating a number of reasons why shiny floors contribute to falls. When a surface is perceived as slippery, patients may change their step length, walking speed, or the surface contact.xii
Light Reflectance Value
Light reflectance value (LRV) has variables as it relates to lighting, daylighting, and flooring color. Gloss Value is measured by an instrument at different angles and is not related to color. If a flooring material requires a finish, this often results in high gloss due to layers of wax, and impairment and visual acuity become a concern.xiii
Clinical Efficiency and Operational Optimization
Flooring that can be efficiently cleaned and disinfected is a fundamental requirement in a healthcare setting when it comes to creating safer spaces. Facilities and environmental service (EVS) teams are tasked to demonstrate value and improve the health, safety, environmental, and operational aspects of the built-environment as it pertains to Cost Quality Outcomes (the CQO Movement is an initiative of the Association for Healthcare Resource and Materials Management: www.ahrmm.org/ahrmm/resources_and_tools/cost_quality_outcomes/index.shtml) .
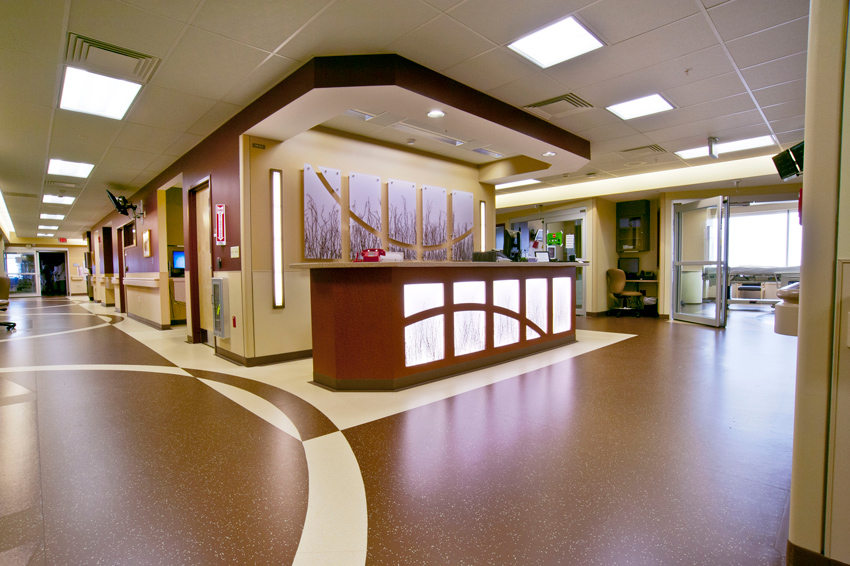
Photo courtesy of nora systems, Inc.
Roswell Park Cancer Institute, Buffalo, New York
“We wanted to make the ICU as comforting as possible by using materials that limit noise and are softer underfoot,” says Laura Shoemaker, senior planner at Roswell Park Cancer Institute.
Performance in this key area should be evaluated carefully, in order to select rubber flooring products that can be easily and quickly cleaned, require no chemicals and resist soiling, staining, and bacteria. These products contribute to clinical efficiency, the ability to control HAIs, healthy IAQ, and a patient’s perception of a “clean room,” especially when steam cleaned.
In healthcare organizations, flooring represents a significant investment over the life-cycle of the facility, literally underpinning all healthcare delivery activities. To make informed decisions, a comprehensive analysis of both first time and life-cycle costs is necessary. An analysis of VCT, vinyl, carpet, rubber, and linoleum flooring conducted by the Florida Hospital, Office of Design studied the life-cycle costs of those materials over a 15-year period. They found that while VCT is typically the least expensive “first-cost” material, the maintenance costs can be nine to 15 times the installation cost because of the requirement to apply a finish and the associated man-hours to maintain the product. The same study found that rubber flooring had the lowest cost per square foot over the 15 years. Specific rubber flooring products in healthcare do not have a factory applied finish, thus they do not require tedious man hours for waxing and stripping. A cost benefits analysis can carefully evaluate the intrinsic value and support safety and outcomes.
Maintenance is another area where proper product specification improves clinical and operational optimization. An automatic scrubber can clean and buff rubber floors rapidly by applying water to the floor via a scrubbing pad and then squeegeeing the water off the floor, leaving a clean, dry floor in about the same amount of time it takes to mop. This process improves IAQ and eliminates the need for chemicals in cleaning. A leading rubber flooring manufacturer will be introducing a steam cleaning system in early 2016. To clean the floor while an area is occupied gives increased flexibility, reduces disruption to clinical work, improves patient perception, and has a direct impact on HCAHPS scores.
The density, compound composition, and other physical characteristics of some rubber flooring products provides for superior resistance to staining from substances used in healthcare settings. These chemicals can cause permanent, unsightly staining to most other types of flooring, even some rubber flooring products.
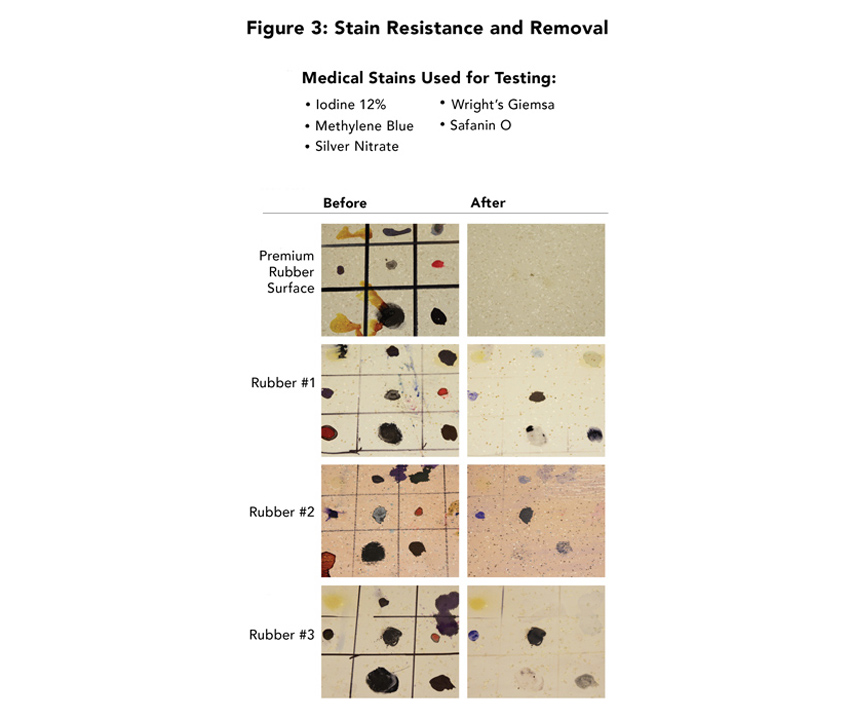
Image courtesy of nora systems, Inc.
“We selected a premium rubber flooring product because it was performing so well in the OR. It was even resisting betadine, which is unheard of,” says Aimee Davies, associate at RTKL Associates Inc., about the flooring used at the Texas Heart Institute in Houston, Texas. In the test discussed here, each resilient floor covering received multiple applications, for an extended period of time (exceeding ASTM standards), of chemicals commonly used in medical facilities. Samples were left to set for seven days before being removed, according to the manufacturer’s published recommendation.
One rubber flooring product designed specifically for applications in healthcare was tested and found that it resisted staining to the point that no permanent staining was created from the following medical products (see Figure 3):
• Methylene Blue
• Cristal violet
• Wright giemsa
• Iodine 10 percent
• 3M Dura Prep Surgical Solution and 3M One-Step Patient Prep (0.75 percent iodine)
• Silver nitrate
The staining agent could be easily removed with water and soft abrasion.
Sustainability, IAQ, and Evidence-Based Design
Beyond those already discussed, there are a number of other central topics related to selection, specification, and procurement of rubber flooring product for healthcare. For example, the environmental impact and life-cycle sustainability of flooring are imperative. With limited capital dollars, ROI is a priority. The product material should be completely free of PVC, phthalates, halogens, chlorine, formaldehyde, and carcinogens.
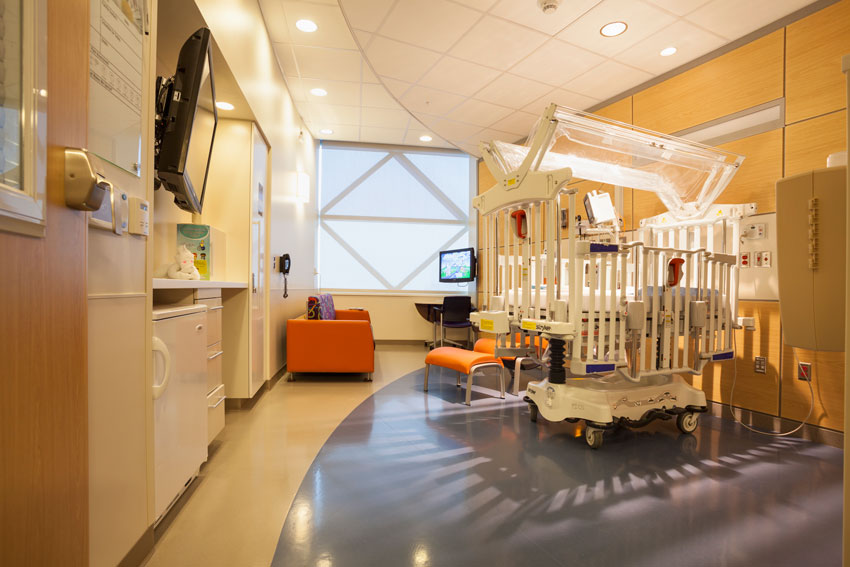
Photo courtesy of nora systems, Inc.
Nemours/Alfred I. duPont Hospital for Children, Wilmington, Delaware
Premium rubber flooring was selected to cover all clinical areas, patient rooms, and corridors in a recent 450,000-square-foot expansion. “I believe the environment really matters to a family because a hospital room represents their home,” says Kay Holbrook, associate administrator at Nemours. “Our patient satisfaction scores have gone up as a result of our new environment. When you walk in the door, you can feel the difference. The flooring has been part of that.”
Some flooring products are manufactured to be more sustainable than others, but rubber flooring in general has environmental advantages over other types of resilient flooring.xiv
Highly durable products with an extended life-cycle and products that have low maintenance requirements to reduce water use, waste water and cleaning chemical use, are preferable.
Indoor air quality is another factor of the built-environment with direct impact on a health and wellness. Flooring selected for healthcare facilities should meet stringent standards for low-VOC emission, including GREENGUARD Gold certification. The minimum requirement should be that the product has been tested and determined compliant with CA 01350; this is the standard used by major green rating systems, including LEED v4. Verification of compliance should come in the form of third-party certification. Both FloorScore and GREENGUARD Gold utilize CA 01350 protocol and are accepted by the major green rating systems.
GREENGUARD Gold certification is a higher-level certification than required by CA 01350 or the major green rating systems. In addition to the 35 chemicals required by CA 01350, it tests for an additional 330 chemicals and includes a TVOC (Total Volatile Organic Compound) measurement.
A study by Perkins+Will compared flooring materials based on environmental and economic costs to understand benefits and drawbacks of choosing certain products.xv Material selection is a crucial component of sustainable design and sustainable selection, where specification decisions are based upon numerous factors. Among a few are material properties, production, cost, and effects on indoor air quality. Prioritizing materials based on their environmental impact is becoming a common practice, with the objective to minimize negative environmental impacts. In order to understand environmental performance of several flooring materials in relation to economic factors, life-cycle assessment (LCA) was conducted for linoleum, vinyl composition tile, nylon carpet tile, composite marble tile, ceramic tile, terrazzo, cork, and rubber flooring.
The study evidenced that there is no single flooring material that has the best environmental performance across all selection criteria. Selection of flooring materials should be based on overall environmental impact, expected lifetime of the material, considerations for maintenance and repair, as well as performance for the particular functional application. Results of the life-cycle assessment indicate that cork, linoleum, and rubber flooring materials perform better than VCT for the majority of environmental impact categories. Although VCT is the least expensive choice, environmental performance should be taken into account as well as its impact on indoor air quality. It is evident that cork, linoleum, and rubber flooring materials should be selected when environmental factors are the primary concern and when both environmental and economic factors are equally weighted. When environmental performance is the driving factor, cork, linoleum, rubber flooring, and terrazzo are comparable.
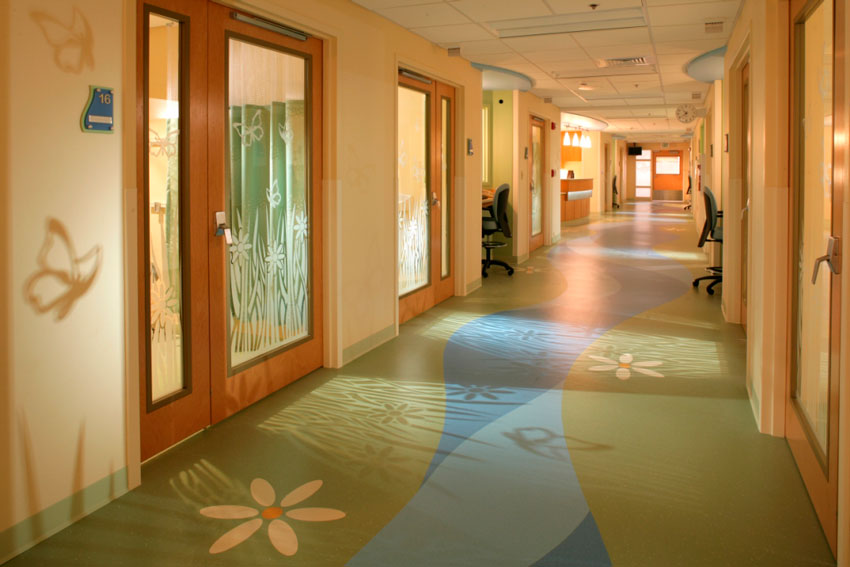
Photo courtesy of nora systems, Inc.
University of Tennessee Medical Center, Tom and Katherine Black Neonatal Intensive Care Unit, Knoxville, Tennessee
“Noise was such a problem for babies in our previous space,” says Heather King, interior designer of the University of Tennessee Medical Center. “Now, the staff can move around with a low level of noise.”
In Summary
The built-environment in healthcare defines the patient satisfaction, delivery of care, and operational outcomes. Evidence-Based Design is the process of basing decisions about the built-environment on credible research to achieve the best possible outcomes. EBD findings inform decision making. In a CHD research study, industry standards and best practices related to floorcoverings were explored. Credible product selection is based on evidence, as defined by the stakeholder goal. Evidence and outcomes define the performance attributes of rubber flooring as it relates to creating safer spaces for infection control, safety, and patient-experience.
In this study, also noted above, flooring surfaces were examined using an EBD approach, to define how flooring/floor coverings can contribute to the following performance improvement goals:
1. Reduce slips, trips, and falls
2. Reduce patient and staff injuries associated with falls
3. Reduce noise levels
4. Reduce staff fatigue
5. Reduce surface contamination and potential risk of HAIs
6. Improve indoor air quality (IAQ)
7. Improve patient and family satisfaction
8. Represent the best return on investmentxvi
Evidence-based studies have shown that flooring attributes have an actionable impact on the two major HCAHPS questions about quietness and cleanliness: “During your stay, how often was your room and bathroom kept clean?” and “How often was the area around your room quiet at night?” Flooring is also related to improving verbal communication and to pain management by reducing noise. Though RRP is a post-discharge measure, Evidence-Based Design studies have shown the impact of noise levels on the patient and how they can affect higher incidents of readmission.
The healthcare payment and delivery system has shifted from volume-driven to value-based care along with process innovation of care and facility standards are the drivers and framework of healthcare reform. The “new normal” has transformed what key stakeholders demand from flooring products that are a component of and align with an integrated approach to Cost-Quality-Outcomes (CQO). The value attributes of rubber flooring as defined by this course showcase the holistic approach to safety in the healing environment from the floor-up.
With a focus on healthcare outcomes, this course content will support architects and interior designers to address many of the pain points and challenges faced in healthcare. Rubber flooring and its inherent product attributes provide a sound focus on operational optimization, clinical efficiency, and patient/caregiver outcomes with actionable impact on outcomes and reimbursables.
Healthcare systems are streamlining product selection in support of branding, improved maintenance, and to reduce overall costs. The benefits of product standardization are to increase the ability to create safer spaces, and to have an aligned partnership in support of maintaining clinical efficiency and operational optimization.
The resilient flooring industry has many product options to choose from; a true evaluation as it pertains to product selection and de-selection must be undertaken to define product attributes as they relate to the outcomes and drivers discussed in this course for operational optimization, clinical efficiency, patient experience, and safety.
Endnotes
- iNanda, U., Malone, E., and Joseph, A. (2012) wrote Achieving EBD Goals through Flooring Selection & Design. Concord, CA: The Center for Health Design.
- ii(Hamilton K. The four levels of evidence-based practice. Healthcare Design, November 2003:18-26) (Ulrich R. Evidence-based design to enhance patient safety. In The environment for care: An NHS estates symposium. London:The Stationary Office, 2004) (Ulrich R, Zimring C, Joseph A, Quan X, Choudhary R. The role of the physical environment in the hospital of the 21st century: A once-in-alifetime opportunity. Center for Health Design: Concord CA, 2004).
- iiihttp://fgiguidelines.org/pdfs/FGI_Update_AcousticCriteria_140929.pdf, http://www.bdcnetwork.com/hospital-constructionrenovation-guidelines-promote-sound-control,http://www.ajicjournal.org/article/SO196-6533(10)00407-41.pdf
- ivJoint Subcommittee on Speech Privacy of the Acoustical Society of America, Technical Committees for Architectural Acoustics and Noise; Institute of Noise Control Engineering; and National Council of Acoustical Consultants 2006), Sound Control for Improved Outcomes in Healthcare Settings, Anjali Joseph, Ph.D., Director of Research, The Center for Health Design and Roger Ulrich, Ph.D., Professor, Center for Health Systems and Design, Texas A&M
- v(Berglund et. Al. 1999)
- vihttp://www.cdc.gov/HAI/surveillance/, http://www.cdc.gov/HAI/pdfs/hai/Scott_CostPaper.pdf
- viiBeyer& Belsito (2000), Gerson et al. (1994), and Skoutelis, et al. (1994).
- viiiJoseph (2006)
- ixhttps://www.healthdesign.org/sites/default/files/ chd_achieving_ebd_goals_through_flooring__design_final.pdf
- x(Anderson, Mackel, Stoler, & Mallison, 1982; Harris, Pacheco, & Lindner, 2010; Lankford et al., 2006; Noskin, Bednarz, Suriano, Reiner, & Peterson, 2000)
- xihttps://share.kaiserpermanente.org/article/kaiser-permanente-rejects-antimicrobials-for-infection-control/
- xii(Joh, Adolph, Campbell & Eppler, 2006).
- xiiiContribution of the Designed Environment to Fall Risk in Hospitals
- xivSustainable Resilient Flooring Choices for Hospitals: Perceptions and Experiences of Users, Specifiers and Installers December 2010, Healthcare Research Collaborative and Georgia Institute of Technology
- xvComparative Analysis of Flooring Materials: Environmental and Economic Performance, Ajla Aksamija, Ph.D., LEED® AP BD+C, CDT
- xvihttps://www.healthdesign.org/sites/default/files/ chd_achieving_ebd_goals_through_flooring__design_final.pdf
Sandra Soraci, EDAC, LEED AP, NCIDQ, IIDA As marketing leader, health care solutions, Sandra supports nora systems, Inc.’s healthcare partners by providing flooring solutions through an informed decision-making process in support of operational optimization, clinical efficiency, patient safety, and cost of ownership.