Doorway to Distinctive Design
Wood veneers and laminates give architects an edge in aesthetics and performance
Continuing Education
Use the following learning objectives to focus your study while reading this month’s Continuing Education article.
Learning Objectives - After reading this article, you will be able to:
- Identify common wood door species and wood veneer cuts, matching, and patterns that provide a basic understanding of wood veneer for architectural doors.
- Properly specify complete veneer requirements.
- Discuss high-pressure decorative laminates from an aesthetic and performance viewpoint, identifying design considerations for a choice that is cost effective and contributes to a healthy, durable, and pleasing interior environment.
- Describe how wood veneer and laminates contribute to sustainability and are consistent with green building goals.
Throughout history, the door has been a compelling design element…the arch top doors of the Romans…medieval doors wrought in bronze…the elaborately carved doors of the Renaissance, the plain doors of the Shakers—all different, all distinctive. No matter what their time period, designers throughout the centuries would no doubt recognize the door as an opportunity to make an aesthetic statement. This is no less true today, as architects choose from an unprecedented array of styles to specify a door consistent with their vision, quality goals, and performance requirements.
In terms of materials, the natural warmth and beauty of wood veneer remains a classic choice for interior doors, complete with the unique physical characteristics that give it depth and interest. Also widely used today are high-pressure decorative laminate (HPDL) doors, which are available in a full range of colors, patterns, wood grains, and custom solutions. This article will discuss the characteristics and design considerations pertaining to wood veneers and HPDL as appropriate for interior applications and available for architectural door product specification.
Wood Veneer: What is it?
Veneer is a thin sheet of wood that is rotary cut, sliced, or sawn from a log. The slice can be ultra thin—industry standard is 1/42 inch, and the minimum is 1/50 inch after sanding. Face veneer, the outermost exposed wood veneer surface of a veneered wood door, is generally made from the most beautiful wood and affixed to an engineered wood substrate. Veneers are a time-honored art form, dating back to Egyptian times and used extensively throughout history.
By its very nature, using veneer is a sustainable practice. The best logs are typically reserved for veneers because the resource can be extended and a single log can be sliced into veneer for multiple projects. Defects in the wood are eliminated during the manufacturing process. Wood veneers are available in multiple grades, matches, and assemblies to meet design requirements, with natural variations of the veneer and different cuts creating unique textures, grains, figure, and color for each veneer piece. Consult the sidebar on the following page for basic definitions of terms and processes related to the manufacture of wood veneer.
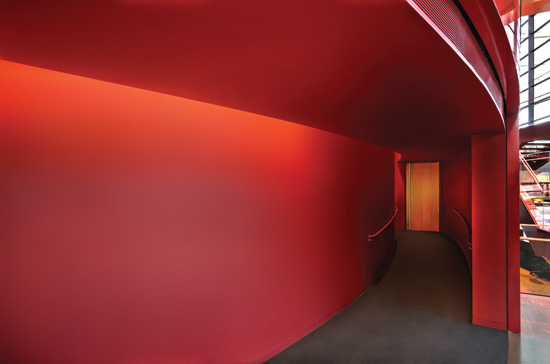
Photo courtesy of VT Industries, Inc.
Wood veneer, along with high-pressure decorative laminates, are aesthetic, economical, and environmentally sound choices for facing architectural quality doors.
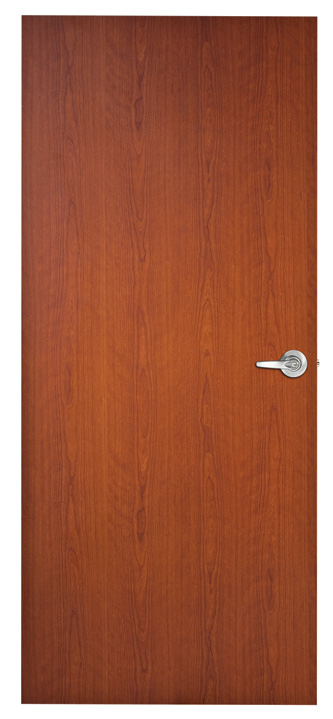
By its very nature, veneer is a sustainable practice, and the resource can be extended to many projects for maximum visual appeal.
Veneer Slicing
As mentioned previously, veneer is cut from the best trees with the fewest defects. The process involves several steps. Essentially, the cutting method for each log is determined first. The logs are then soaked and drained, and afterwards they are ready to be cut. After cutting, the slices of veneer are dried and bundled. The way in which the log is cut dictates the grain and appearance of the veneer. More specifically, the cutting method involves slicing through a tree's growth rings, and the angle at which the wood is cut produces a distinctive grain. Plain sliced or flat cut, quarter sliced, rift cut, and rotary are common veneer cutting methods.
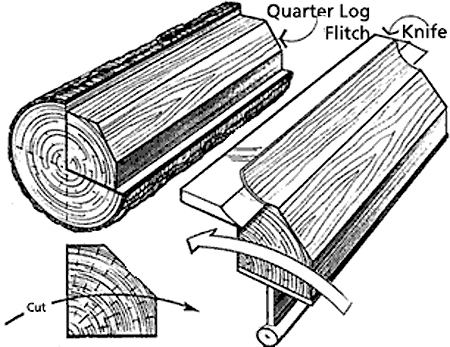
Plain sliced or flat cut veneer. The half log, or flitch, is mounted with the heart side against the guide plate of the slicer. Cuts are made parallel to a line through the center of the log, producing a distinct figure. The leaf width depends on log size and its placement in the flitch. By keeping the veneer leaves in the same order in which they are cut, the leaves can be reassembled with only a very gradual grain figure transition from one panel to another. Half round, a somewhat similar pattern, is achieved by turning a half log flitch on a lathe.
Quarter cut. A quarter log, or flitch, is mounted so that the slicer cuts the log at a 45° angle to the axis lines of the log, creating a striped or straight grain effect. A flake effect is produced in oak veneers using this method.
Rift cut. This method is generally restricted to red and white oak. A quarter log is mounted off center and cut slightly across the medullary rays common to oak, resulting in a straight grain without the flake effect of quarter sliced oak. To minimize this ray, or flake, effect, the angle of the cut is 15 degrees to the radial. The characteristic very tight and straight grain produced by the rift cut is known as the comb grain.
Rotary cut. This is a method of cutting in which the log is placed on a large lathe and turned against a fixed blade, so that a continuous cut is made round and round the log, more or less parallel at all times to the growth ring. The result is a wild, varied grain effect. Since the grain pattern is non-repetitive, it cannot be used for sequence matching. Component widths can vary from 4 inches to 12 inches. This type of cut may cause difficulty in staining some species, particularly red and white oak.
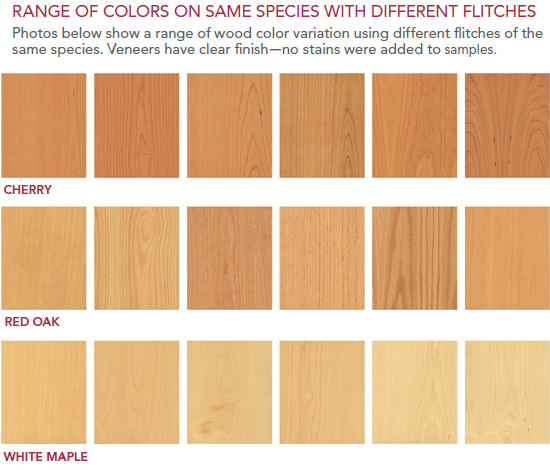
As a product of nature, wood will vary in color and grain from tree to tree, or even within the same tree.
Veneer Assembly Methods
Once the decorative veneer cutting method is specified, the type of match at the joint line must be determined. The way in which the individual cuts are matched or placed next to each other affects the appearance of the doors. Leaf matching and assembly matching are the most common types.
Leaf matching involves matching pairs of veneer cuts. Common types are book and slip matches. Book match is the most commonly used in the industry. Every other piece of veneer is turned over so adjacent pieces are opened like two adjacent pages in a book. The veneer joints match and create a mirrored image pattern at the joint line, yielding a maximum continuity of grain. Book matching is used with plain sliced, and less often with other cuts of veneer. Because the “tight” and “loose” faces alternate in adjacent pieces of veneer, they may accept stain or reflect light differently, resulting in a noticeable color variation, often called “barber pole.” These variations are not considered a manufacturing defect.
Slip matching refers to the adjoining of veneer components in sequence without turning over every other piece. The grain figure repeats, but joints will not show a mirrored effect. Slip matching is often used in quarter cut, rift cut, and comb grain veneers to minimize the barber pole effect. It may cause a leaning effect.
As the slicing advances, the leaves of veneer within a flitch will get wider or narrower, changing in appearance. To obtain a desired appearance in a door, how the individual leaves are configured requires specification. This is called an assembly match, and the most common arrangements are a running match, a balance match, and a center match. The running match is non-symmetrical in appearance on any single door face. Veneer pieces of unequal width are typical in this matching style, and each face is assembled from as many veneer pieces as necessary. It is the most common type of match. A balance match produces a more symmetrical appearance. Each face is assembled from an even or odd number of pieces of uniform width before trimming. This match reduces veneer yield. Center and balance matches also produce an asymmetrical appearance. Each face is assembled from an even number of veneer pieces of uniform width before trimming, and there is a veneer joint in the center of the panel. This match further reduces veneer yield.
Other assembly options include a pair match and a set match, which are specified for double doors. A pair match describes the way in which leaves of veneer are assembled for a pair of doors or a series of door pairs in the immediate vicinity. Doors may be, and in some grades must be, specified as pair matched where appropriate. A set match describes the way in which the leaves of veneer are assembled for sets of doors hung adjacently. Here again, doors hung in adjacent openings may be, and in some grades must be, specified as set matched.
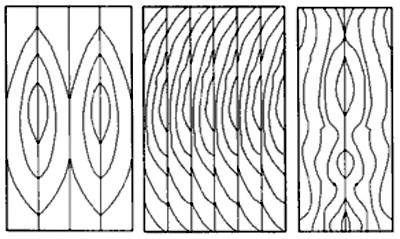
Reprinted with permission of AWI
Variations on the center and balance match include a book match (l), a slip match (c), and another take on a book match (r).
Standards
Architects should become familiar with standards set forth by the architectural flush wood door industry and assure that their veneer selection is consistent with or exceeds the established requirements. The primary quality standards are the Window and Door Manufacturers Association (WDMA I.S. 1-A) and the Architectural Woodwork Standards (AWS) Quality Standards, sections 5 and 9. WDMA is the industry standard for door manufacturers. The Architectural Woodwork Standards (AWS) are typically used in installations where the doors are blueprint matched with wall paneling and/or the doors are adjacent to millwork, requiring that the doors be consistent with the surrounding millwork. Most architectural and commercial doors are not directly associated with panels and/or millwork, and thus the WDMA requirements are more than adequate to assure consistent appearance among doors.
Both WMDA and AWS set two aesthetic grades for architectural wood doors: custom and premium. The custom grade provides a well-defined degree of control over the workmanship, materials, and installation of a project, and is typically specified for and adequately covers most high-quality interior architectural woodwork. Premium grade is reserved for special projects or featured areas within a project. Premium doors are specified when the highest degree of control is required. The difference between the two grades, custom and premium, is the veneer grade, adopted from panel and veneer grading tables established by the Hardwood Plywood and Veneer Association (HPVA), which is an ANSI-accredited standards developer, and from veneer assembly. The accompanying table (see article online) provides a quick reference. In both WDMA and AWS, Grade A face veneer is standard, with WDMA also stipulating book match and running match as standard. It should be noted that AA grade veneer also requires wider minimums for face components with plain sliced and rotary sliced flitches. Naturally, premium doors have a higher cost, and availability may be limited because of the AA grade veneer, center balance, and wider flitch requirements. Further, it is necessary to understand that if an aesthetic grade is not specified, custom grade is the default grade to be furnished. There is no difference in performance duty requirements for custom and premium doors.
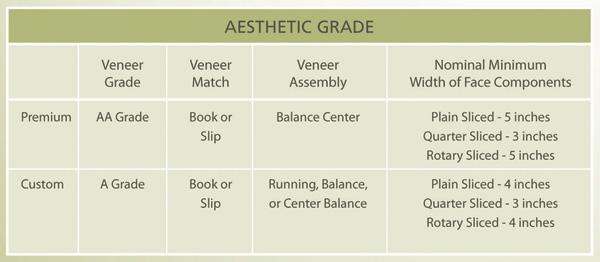
Species
While there are many species of wood veneer available, ranging from domestic to exotics, common door veneer species are generally considered to be birch, maple, oak, cherry, and African mahogany.
To ascertain the differences among species, it is important to understand sapwood and heartwood. Sapwood is the living, outermost portion of the branch, and heartwood is the center, mature portion of the tree, which makes up most of the cross section of a log. Generally, sapwood is a lighter color than heartwood. Certain wood species, particularly natural maple and birch, can vary widely in color range, which is why in many cases “select white” is specified so that the sapwood can be accumulated and spliced together to create a consistent color. When specifying “natural” maple and birch, the veneer will contain unlimited amounts of the lighter colored sapwood and/or the darker heartwood unselected for color as well as color streaks, spots, and color variation from almost white to very dark. If a light-colored veneer is preferred, architects should specify all-sapwood maple or birch. If a dark-colored veneer is preferred, specify all heartwood. Veneers, such as maple and birch, may contain sapwood/ heartwood combinations.
Each species has its own inherent characteristics. Red oak, for example, has a coarse, open grain pattern and is more uniform in color with less flake than white oak. By contrast, maple is known for its straight, moderately close grain pattern; it contains both heartwood and sapwood. Birch has a close grain pattern and, like maple, contains heartwood and sapwood. Cherry has a light reddish-brown color and a straight, satiny grain, and mahogany offers a distinct, pleasing grain pattern and has light pink to reddish and tannish-brown colors.
Natural Variation
Wood is a product of nature and, as such, can enhance a project design and aesthetic goals when used in its purest or natural state. However, each wood species will vary in color and grain from tree to tree, or even within the same tree. Environmental factors, such as climate and soil content, can cause each veneer species to exhibit a range of colors and textures. In addition, each wood species has its own particular and industry-acceptable characteristics, and it is precisely these naturally occurring variations that provide such richness and uniqueness to each project. Light and oxidation also contribute effects and can change a face veneer color.
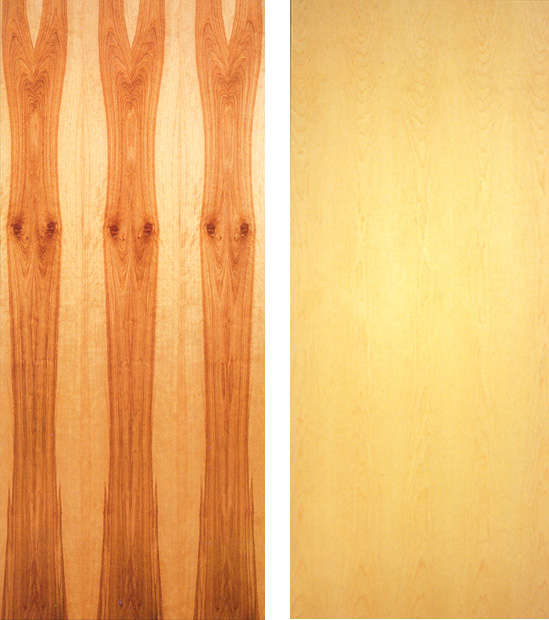
Image courtesy of VT Industries, Inc.
The accompanying image showcases differences between a select white veneer vs. a natural veneer.
Finish Options
Architects can usually consult factory finish samples to confirm the basic color, grain fill, and gloss level of the various finish systems. Most manufacturers also offer a custom finish—providing a small swatch of the desired finish color is typically all that is needed for a quality manufacturer to provide custom matching services.
Factory Finish—Controlled Conditions
The factory conditions of a manufacturer can make a difference in the quality of a finished veneer door. A clean, well-lit plant with automated sanding and staining functions stands in sharp contrast to poor jobsite conditions in the field where dust, poor lighting, and hand sanding and staining may potentially lead to inconsistency in the finish and unacceptable overall results.
That is not to say, however, that all manufacturing plants are created equal. These advanced capabilities enable manufacturers to produce consistent and durable results. In state-of-the-art facilities, doors with veneer faces are first sanded using coarse sand paper, followed by fine sand paper to remove any raised wood fibers. The finish process begins when a water-based stain coat is rolled and brushed into the veneer and dried under heat. Brushing the stain ensures the stain penetrates the veneer grain; this is important for veneers with open grains. Multiple sealer coats are applied next, sealing the stain and achieving the desired gloss to the finish. The seal coats are now finely sanded to remove any wood fibers that may have raised. Finally, top coats are applied and UV treated, ensuring a hardened finish that cures and encapsulates any VOC emissions.
High-Pressure Decorative Laminate—What is it?
The primary difference between laminate-clad wood doors and wood veneer-faced doors is simply the face material. With technological improvements in manufacturing and materials, today's high-pressure decorative laminates (HPDL) are becoming an increasingly popular door surface application. These doors offer myriad design choices, cost benefits, performance achievements, and environmental attributes. Compared to laminate doors from earlier times, today's versions feature improvements in virtually every element and process, with the results including more detailed patterns, smoother surfaces, stronger bonds to substrates, advanced resin surface chemistry for easier maintenance, manufacturing processes that prevent delamination of edges, and increased recycled content.
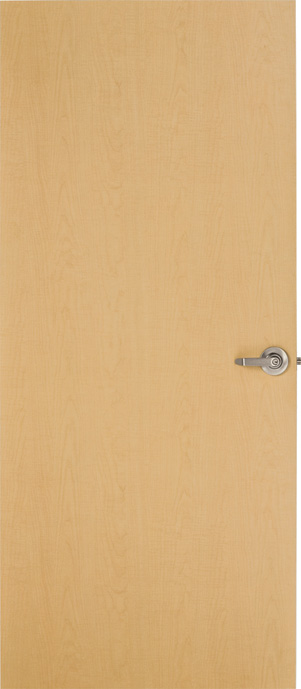
With technological improvements in manufacturing and materials, today’s high-pressure decorative laminates are becoming an increasingly popular door surface application.
Laminate-clad wood doors are available in high- and low-pressure versions. High-pressure decorative laminate (HPDL) is comprised of several layers of brown kraft paper filled with phenolic resin for flexibility and a high-quality decorative print paper impregnated with melamine resin or an overlay dipped in melamine for strength and durability. They are compressed under high pressure and heat for an extended period of time, approximately 1400 psi at 300° F for up to 40 minutes. The number of kraft/phenolic layers in each sheet of HPDL determines its thickness. In the actual process, the raw paper is first dipped in a resin bath and dried, and the laminate is then assembled with kraft paper and melamine-treated decorative paper or overlay; a textured metal plate then determines the finish properties. The bottom layer of kraft paper is sanded to provide proper adhesion between the laminate and a substrate material. For best results, door edges, which are usually finished with the same laminate as the face, must be applied first to reduce the potential for chips and to hide the seams. When designers opt to have the edges painted or stained, factory finishing almost always provides the best outcome for a look that is both polished and consistent.
HPDL Standards
Performance standards for HPDL are established by the American National Standards Institute/National Electrical Manufacturers Association (ANSI/NEMA), and HPDL must meet Standard LD3, which is the latest edition. All major laminate manufacturers meet the above referenced standard.
The WDMA standard allows low-pressure decorative laminate (LPDL) as an alternative face material. LPDL consists of a single thin sheet of decorative paper that is saturated and compressed under low pressure and heat for a short period of time, approximately 600psi at 392 degrees Fahrenheit for 20 minutes and then fused directly to a wood substrate or single-wear layer. Because the single decorative wear layer results in lower wear and impact resistance, LPL is not recommended by manufacturers for wood door use.
LPL must meet the standards of the Laminating Materials Association, Inc.'s (LMA) latest edition entitled Voluntary Product Standards and Typical Physical Properties of Decorative Overlays. In its second edition, Section 9, the AWS sets standards for face material; HPDL is recognized as a quality standard, but LPL is not recognized as such.
Design Considerations
Traditionally, decorative laminate doors have been considered primarily for their durability and standardization of appearance. Today's decorative laminate doors, however, are increasingly specified for their overall value in terms of cost, low degree of maintenance and decorative possibilities, with hundreds of colors, patterns, wood grains, and graphic images ranging from subtle to bold available from leading laminate manufacturers. Colors and patterns are available in most standard finishes. Wood grain patterns are often specified in door applications, with popular options ranging from cherry and maple to anigre and zebrawood. When used on architectural wood doors, the appearance is similar to wood veneer face material; edges can also be surfaced with laminate for a complete wood grain appearance. Custom laminates can be produced from images, and, in fact, when “picture perfect” is the expectation, a graphic process in which a full-color photographic image or original artwork is scanned into a computer and then transferred onto decorative paper often works best. Leading industry manufacturers have the capacity to print virtually any type of design, including pictorial elements, abstract figures, natural scenes, murals, logos, room numbers and other graphics in laminate form to enhance the door face. As knowledge grows about the influence of color and design on human behavior, performance and motivation, custom HPDL doors are being increasingly used in commercial, school, hospitality, and hospital and medical facilities to create engaging environments, raise morale, and reinforce overall design objectives.
In addition to the laminate designs, a host of other finish options are available on laminate doors. The most common is a matte finish, which offers the benefits of long-term durability. A matte finish, which essentially reproduces the sheen associated with waxed wood furniture, will minimize smudges and fingerprints and enhance reflective qualities. Premium finishes are also available to achieve different effects. Natural wood grain finishes are popular when paired with wood grain laminates, further enhancing the look and feel of laminate. A sparkle/crystal finish is a small-scaled texture that produces a brighter and more durable finish. Architects can also choose from a honed finish that creates the look and feel of a tumbled tile, a softly polished and etched surface, or a mirco-dot finish in which tiny circle impressions line the surface, among others. A gloss, mirror-like finish is also available, though it is not recommended for door construction.
These premium surface textures do double duty: They provide an ultra-realistic 3D depth—wood grains can be so realistic they can fool even a practiced eye—and they confer maintenance benefits, helping the face material resist stains, scratches, handprints, and smudges.
Advantages
Due to their durability and uniformity of appearance, HPDL doors have considerable appeal where consistency is desirable, such as in offices and hotels, restaurants, and other locations where design requirements should remain constant across regional or nationwide franchises.
Today, laminate doors are also recognized for their easy maintenance. HPDL doors are fingerprint resistant, which is a time- and cost-saving benefit, particularly in such facilities as commercial kitchens, school cafeterias and restaurant settings where food-stained handprints can leave grime that will eventually lead to the need to refinish or even replace the door. Laminate doors can tolerate the general purpose cleansers and disinfectants used to remove the inevitable handprints and smudges that occur on doors in high-use facilities, including schools and hospitals, as well as the stronger solvents required to remove ink stains, and the industrial-strength cleansers that will eliminate paint and graffiti marks.
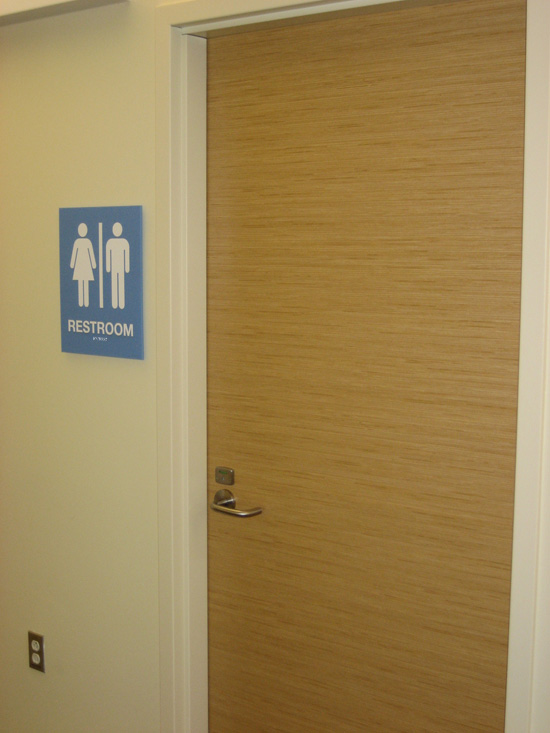
Photo courtesy of VT Industries, Inc
HPDL doors are a good choice when uniformity across an organization or a franchise is a key consideration.
Regardless of wood grain or pattern, laminates offer more constant pricing and are not subject to the vicissitudes that often come with the cost of various species of wood veneer. Decorative laminate doors are cost-effective, do not require on-site finishing, and typically arrive at the jobsite complete and ready to hang, saving considerable installation time and expense.
In addition, many of the attributes of HPDL meet today's preference for sustainable building designs and materials. Most HPDL, for example, is available as FSC certified; further, HPDL frequently includes recycled content and other GREENGUARD Certification attributes that can be considered intrinsically sustainable and that help architects to earn LEED points. The use of laminates can also be viewed as a boon to resource conservation since they can recreate the aesthetic of common and exotic wood grains without putting pressure on or depleting the world's invaluable forests.
Wood Veneer and HPDL: Two Solid Choices in Door Construction
Throughout history, the door has held special significance in architecture, and have often been given considerable aesthetic attention. Architects are faced with a staggering array of choices in designing interior doors for today's structures. Two popular contemporary options, both of which represent sound choices, are architectural wood doors faced with wood veneer and HPDL. Within these product categories, architects have a myriad of options from which to choose to meet the design objectives, performance and budget requirements, and sustainability considerations of all types of commercial projects.
Headquartered in Holstein, Iowa, VT Industries, Inc., is North America's leading manufacturer of architectural wood doors, VT Dimensions countertops, and VT GeoScapes and TruQuartz stone surfaces. The company's three divisions serve customers from nine manufacturing facilities strategically located throughout the U.S. and Canada. For more information visit the company's website at www.vtindustries.com |