Advances in Manufactured Masonry Thin Veneers
New products look, adhere, and weather better
Continuing Education
Use the following learning objectives to focus your study while reading this month’s Continuing Education article.
Learning Objectives - After reading this article, you will be able to:
- Discuss the characteristics of manufactured stone veneer in terms of green building goals.
- Compare natural stone veneer, full-profile stone, and manufactured stone veneer in terms of aesthetics, cost, environmental soundness, and durability.
- Describe the recent advances in manufactured stone veneer and how the product has advanced in terms of aesthetics, adherence, energy efficiency, and moisture control.
- Explain the various types of installation systems and how they reflect advances in design to achieve consistency with the building code and sustainability goals.
Manufactured masonry thin veneer has hit its stride. Popularity in the product has grown dramatically over the past decade and recent years have seen further innovation that seeks to refine its visual appeal and other benefits. While full-depth veneer options have expanded, the market has also seen an increase in lightweight or thin veneers used both in commercial and residential construction, with today's products engineered to look better, adhere better, and weather better than their traditional counterparts. This article will explore manufactured masonry thin veneers with respect to their aesthetic appeal, durability, and economical advantages. Also discussed will be options in installation systems that have been designed to facilitate energy efficiency and moisture control.
Manufactured Masonry Thin Veneer—What is it?
Thin veneers are any lightweight, flat-backed, thin surface product that is applied directly to a solid facing. Thin veneers average in thickness from 1 to 2 inches and per International Code Council regulations must weigh 15 pounds or less per square foot.
Manufactured masonry thin veneer is typically fabricated by pouring a lightweight concrete mix into rubber forms. The trend started with emulating the look of natural stone but has gone beyond that—thin veneers can be manufactured in a wide range of looks and options. Glazing the face can change the appearance of the veneer unit to resemble other materials such as tile, for example, and pictorial elements can even be added for visual effect.
In the recent past, advances in the molds themselves as well as in finishing techniques, mortar, and substrates have enabled manufactured masonry thin veneers to offer not only more visual effects and the ability to match an increased number of colors, shapes, and textures, but greater economic and environmental advantages as well as ease of maintenance. Today's products are machine made with quality aggregates and admixtures to make them very dense and water repellent to facilitate moisture control so that they can be used at grade and to withstand over 60 mph wind-driven rain. Additionally, veneers may be manufactured to be mold and mildew resistant. Many thin veneer products are either naturally colored or have integrated pigment for color fastness. After they are produced, some thin veneers are cut to the desired thickness and shaped to the customer's specifications. With a new understanding of the thin veneer products, manufacturers have made some adjustments to their sawing equipment to be able to cut these thin veneer products more precisely. But not all thin veneers are produced by being cut, some are manufactured at the desired depth and are ready to install without cutting. Advances in packaging materials assure safe shipment of these products nationwide while maintaining product integrity and quality.
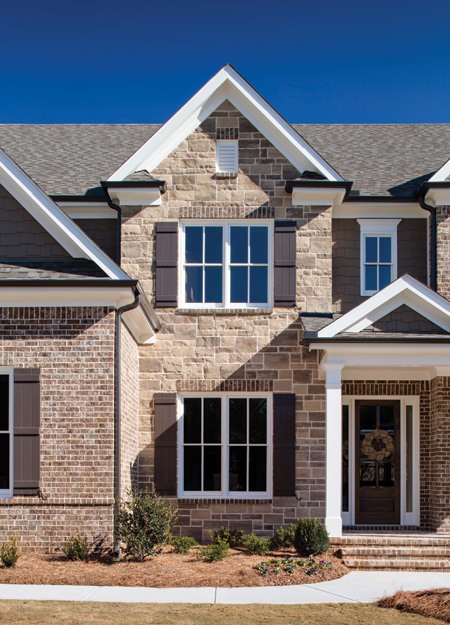
Photo courtesy of Oldcastle® Architectural and Artisan Masonry Stone Veneers®
Manufactured masonry veneers have evolved, with today’s versions offering a host of visual styles for interior and exterior applications.
Because it is made with concrete, manufactured masonry thin veneer provides a number of benefits. By its very nature, thin veneer is light in weight, making it generally more economical than full-depth veneer. Thin veneer also tends to install faster, saving money and the all-important resource of time. Further, thin veneers may be used for non-load bearing applications and do not require a footing, further eliminating costs because of the reduction of structural reinforcements required. They offer flexibility in customizing sills, arches, coping units, and larger-size units, and can be easily cut and shaped in the field. While most commercial applications have used a thin veneer stone from time to time, they have been increasingly utilized over the past few years due to several reasons, including the need for a lighter veneer due to an application or particular location on the building, and installations on projects with other thin veneer systems such as metal panels or glass curtain walls.
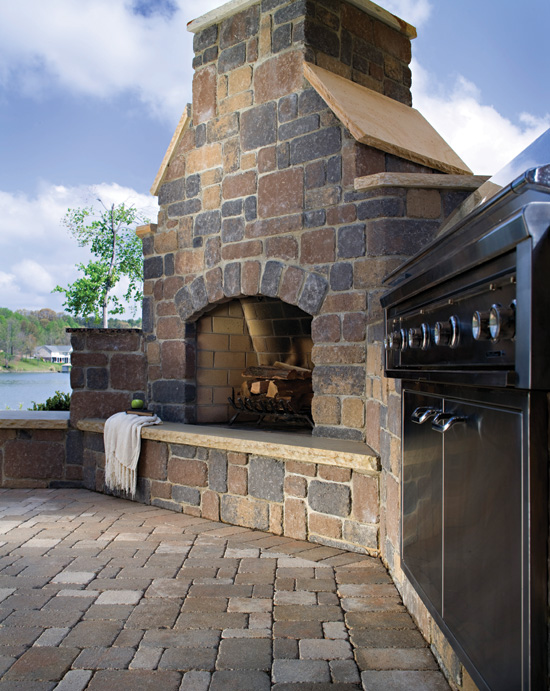
Photo courtesy of Oldcastle® Architectural
Manufactured masonry veneer in thin and full-profile styles creates distinctive outdoor spaces.
Manufactured vs. Natural Stone
Many applications call for the look of stone and, in use since the 1950s, manufactured stone is a frequent lightweight alternative to natural stone. Particularly with wood frame walls, building codes may stipulate that when natural stone cladding is used, more wall support, footings, and expansion joints may be required. Over the years, manufacturers have solved a number of problems present in early versions of manufactured stone, particularly its sometimes unauthentic look and texture, and manufacturing innovation in finishes and installation methods has generated an uptick in face and size options. With the actual material costs of manufactured stone and natural stone veneers running neck and neck1, due to its lighter weight—roughly one third the weight of natural stone—manufactured stone is a less expensive alternative in terms of fabrication, shipping, lifting, and installation, and a more economical and environmentally sound option in areas without natural quarries. Manufactured stone may also have an edge over natural stone in color options—while natural stone is confined to the palette that Mother Nature has presented, manufactured stone products are available in almost limitless colors and textures.
Market Conditions
Manufactured masonry thin veneer usage is on the rise, with the North American market for general masonry veneer in residential and commercial applications reaching more than 160 million square feet valued at nearly $700 million in 2010, according to a study by business consulting firm Principia Partners entitled Masonry Veneer 20102. The firm maintains that the residential market for masonry veneer will be the primary driver of new growth between 2010 and 2012, contributing over $150 million in new demand.
According to the study, masonry veneer including manufactured stone, thin veneer stone, thin brick, and masonry panels, simulates stone or brick appearance at an installed cost of 50 to 60 percent that of full-dimensional masonry—a figure made even higher with the shortage of skilled masons to install full-dimensional masonry.
Ken Jacobson, partner at Principia Partners, says, “Property owners are increasingly using masonry veneer products because they are significantly more affordable than natural stone and full-dimensional brick.” Jacobson continues, “According to our extensive research, property owners continue to seek products that are aesthetically pleasing, offer a wide range of design options in color, form, and texture, and can be easily installed. Masonry veneer products install easier than full-dimension masonry. More product can be moved and installed per man hour. Due to masonry veneer's lower volume and weight, more product can be shipped per truckload than traditional masonry, and with no load-bearing foundations required, thin masonry veneers are easier and less expensive to install than their full-dimension equivalents.”
Applications
Thin veneers have wide applicability in settings from residential single-family homes to multi-story commercial buildings, and are used extensively not only in façades and foundation facings but in many interior settings as well, creating striking effects. Archways, entrance pillars, courtyards as well as accent walls, alcoves, stairwells, chimneys, mantels, and fire pits are all popular candidates for thin veneer installations. Further, thin veneer can be an effective solution in both new construction and renovations, and can be fabricated to replicate a natural or specified material.
Interior. Considered a premium aesthetic as both a full application or as an accent, manufactured thin veneer is widely used in interior settings, as the 1-inch depth of a typical unit leaves more space than the full 4-inch profile. Accenting one part of a wall in a living or dining room can add visual interest and high drama at a relatively low cost. In the kitchen, stone veneer backsplashes, islands, walls, and entry arches can enhance the appearance of the room, adding a rustic feel, or emphasizing a natural aesthetic. Thin veneer is appropriate for fireplace upgrades, changing or reinforcing the design sensibility of the space—a rugged surface around the fireplace, for example, may add warmth and texture to a modern room. Door and window surrounds as well as transitional walls or arches are also prime spots for manufactured thin veneer stone treatments and can bring the dramatic richness and warmth of natural stone without the drawbacks. Options in manufactured veneers range from rough edged to natural cut, irregularly shaped field stone and the rounded smoothness of river rock.
Exterior. Manufactured thin veneer can be used to striking effect in both complete coverage or as an accent to the exterior of a structure, with a combination of different surfaces and textures adding interest and depth. Appropriately colored and textured units can help the structure blend in to its natural surroundings, be they marked by stone outcroppings or deep woods or other types of landscape. Simple or multidimensional designs for outdoor living can also be created with a combination of thin veneer products. Popular trends include built-in seating, definition of an outdoor room with seat walls, and customization of water or fire features and an outdoor kitchen. Architects can also use thin veneer walls to pleasing and practical effect in outdoor living settings to define spaces, wrap columns, control erosion, build seat walls and raised gardens, and create multidimensional poolscapes and patios.
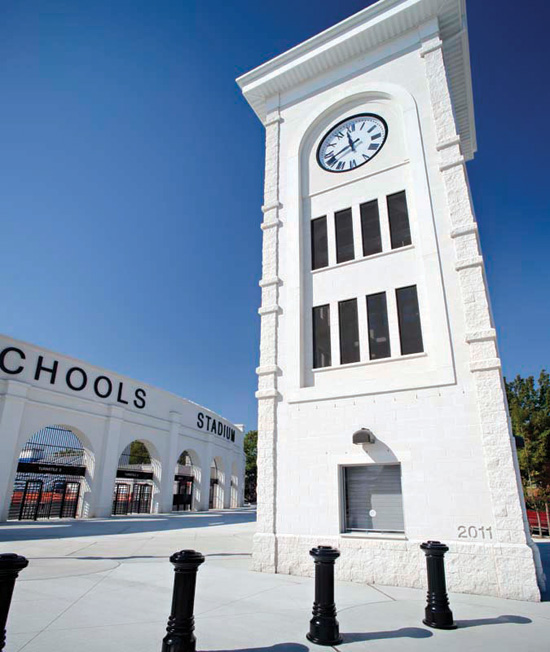
Photo courtesy of Oldcastle® Architectural
A popular option in full-profile veneer is a monument white exterior look, achieved by a mixture of white Portland cement combined with fine aggregates.
The diversity of face alternatives of manufactured full-dimension stone veneer, including color, texture, and size options, can also offer architects a versatile palette. Exterior veneer, for example, can have the look and feel of natural limestone or cast stone, creating the unique appearance of old stone with a slightly embossed, antique finish to achieve an air of softness and warmth. In some instances, a choice of two types of joints is available in order to create two very different looks within the façade, and many product lines include various proportions of large stones and accessories to create interesting architectural details that require few or no cuts. Angular and surround stones offer a variety of design possibilities, as do thin veneer units with rounded contours, and modular shapes.
Another popular option is a monument white exterior look, achieved by a mixture of white Portland cement combined with fine aggregates that can result in a highly dense product with clean lines, or a bold chiseled finish. For those who prefer a stacked stone look, manufacturers offer multi-length units that can be used on the entire façade or as accents on architectural elements such as wall sections or skirting. A product that has a single height but differing lengths makes for a stacked stone appearance with an easy installation process. Innovative manufacturing processes even enable units that possess the look of natural slate, or large stonework highly sought after in urban settings.
The manufacturing process is engineered to create in random fashion, a number of distinct textures with marked edges. Using color ranges and blends, as well as varying types of joints—concave, half recessed, recessed, and flush—and various ratios of large to smaller stones make for a façade or interior application with depth and intricacy.
Specification Considerations
When choosing a manufactured masonry thin veneer, several factors should be considered.
Depending on manufacturing process, many concrete masonry thin veneers integrate the color throughout the unit. As opposed to surface finishes, aggregate coloring creates a product that is more visually appealing and durable. Units that were surface colored, as was the case almost universally in earlier times, were subject to chips and scratches, often rendering them unusable. Specifiers should also look for products with an increased freeze thaw resistance and a low water absorption rate. Naturally, a product that is designed to fit the adherence system will quicken time and lessen the difficulty of the installation process, making for a more pleasing aesthetic effect; equally important is selecting a product that is dimensionally tolerant and does not have unwanted flanges on the back of the stone. Other desirable attributes of manufactured thin veneers are resistance to salt damage and ease of cleaning, with those that can be easily wiped without the color rubbing off being the preferable choice. In addition, some products are manufactured with an integral water repellent limiting moisture penetration and increasing the service life of the structure.
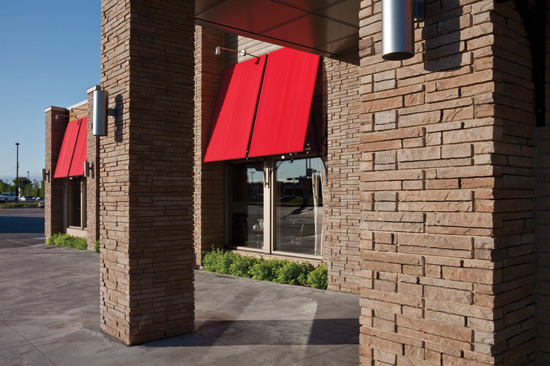
Photo courtesy of Oldcastle® Architectural Products and Artisan Masonry Stone Veneers®
Varying types of joints and ratios of larger to smaller stone create façades with depth and intricacy.
Manufactured thin veneer is sold by the square foot. Estimating the quantity of material needed involves calculating the total area to be covered minus any openings for windows, doors, fireplaces, etc. It should be noted that thin veneer does not require special corner pieces—corners are constructed by overlapping standard pieces in a woven pattern.
Installation Options
While the most common installation method used today is to anchor veneers to wood stud, metal stud, or concrete masonry backup systems, thin veneers have allowed for new, innovative methods and systems. Several of these are discussed below.
Adhered Veneers
Over the past decade and a half, adhered veneers have become quite popular. Adhered veneer is veneer set in a bed of mortar, that is “secured to and supported by the backing through adhesion.” According to the Masonry Advisory Council, the backing system of the exterior veneer must withstand water intrusion, with the flashing properly detailed.3 The council offers the following model for an adhered exterior veneer in order to provide adequate moisture control, maintaining that the general design requires the veneer's backing system must resist water penetration and that flashing must be properly detailed complete with weep holes to redirect water to the outside of the structure. Oriented Strand Board (OSB) is installed as sheathing on the outer face of the studs, followed by two layers of building paper, and then a drainage mat is installed to drain any water that has penetrated to the flashing which in turn sends it to the building exterior via the weepholes. Atop the drainage mat, a galvanized expanded metal lath, or diamond mesh, should be attached as it will hold the veneer to the studs. A parging backing, which is a thin coat of mortar that provides a smooth surface for masonry and seals it against moisture, should be applied onto the mesh. Mortar is applied to the back of the thin veneer and pressed on to the parged surface. The council cautions that drainage is often the key missing element in adhered veneer systems, and that it is the designer's responsibility to assure that an adequate drainage system with proper flashing and correct spacing of nails is included.
For design and construction requirements for adhered veneer, designers can consult the 2012 International Building Code and the TMS 402 Code. Residential application requirements are contained in the International Residential Code and applicable local building codes.
Mounting Systems
Another option for affixing masonry veneers is a lightweight system that works in conjunction with traditional mortar to secure the veneer, while reducing footing and lintel requirements, and labor and installation costs. This type of system offers a mechanical support and spacing panel in which each unit is supported by ties that mechanically interlock the masonry veneer to the panel which is anchored to the wall. Multiple support tie face heights are available, and the support tie configuration is placed at an acute angle, allowing the mortar to surround the support tie, which results in a positive masonry lock between the brick mortar and panel. Systems made of galvanized steel with a thermal set coating will prevent rust and, due to a light color, will help to evenly distribute heat. An embossed texture effectively provides a built-in weep system on both sides of the panel for moisture control, while creating greater surface area for maximum adhesion between veneer and panel. Systems made of high-grade architectural steel are of lightweight design, while still providing a similar coefficient of thermal expansion as thin veneer and mortar, and having the strength for panel support and bracing the wall so as to minimize wall racking. For more complicated applications, manufacturers also offer an enhanced version of this system that incorporates rainscreen technology for superior drainage, ventilation, pressure equalization, and bond strength.
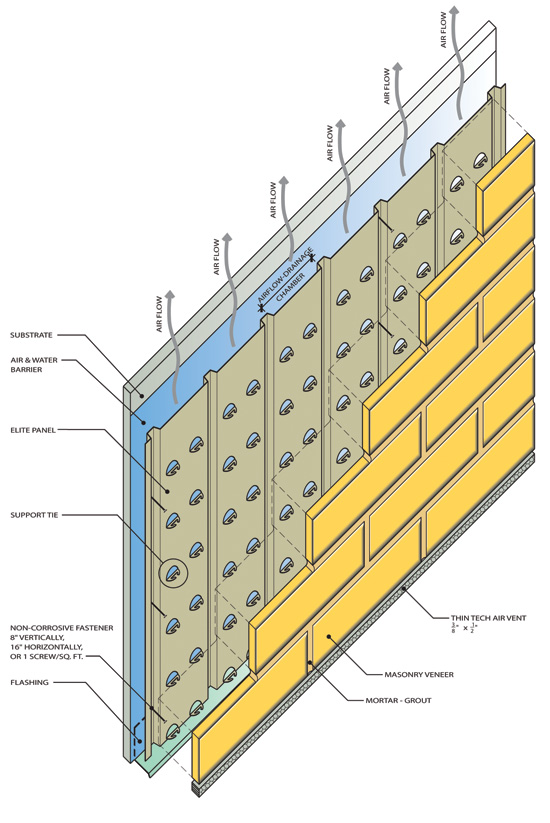
Image courtesy of Glen-Gery Brick
This system offers a mechanical support and spacing panel in which each unit is supported by ties that mechanically interlock the masonry veneer to the panel.
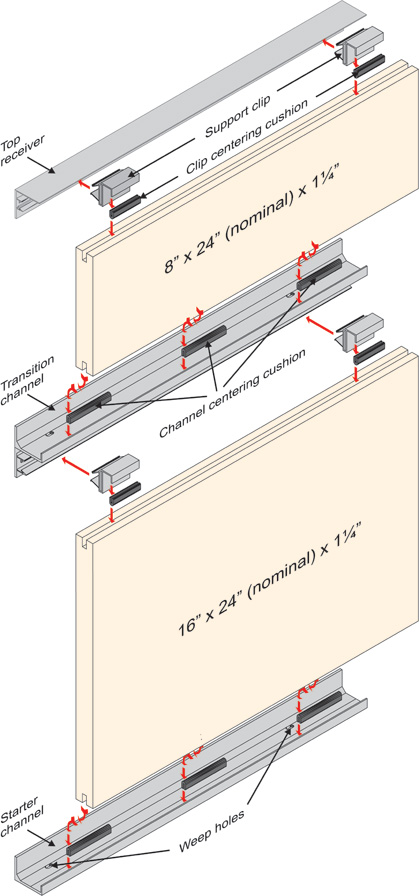
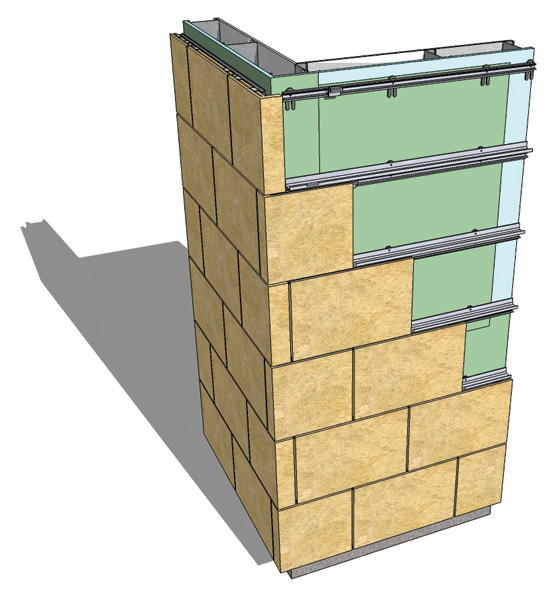
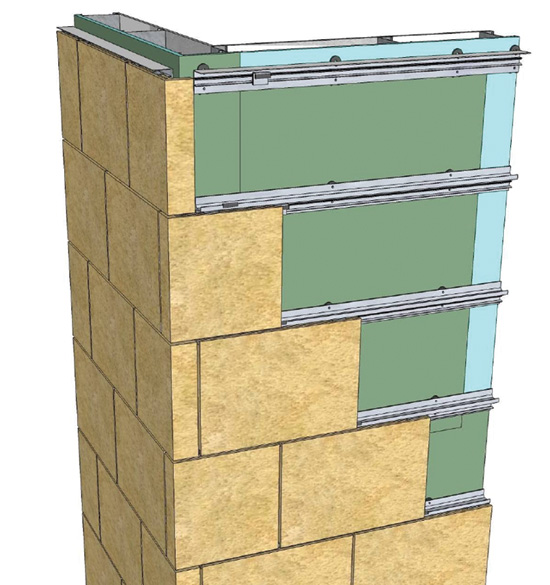
Images courtesy of Acme Brick Company
Track systems are used to hang thin veneer in either vertical or horizontal applications.
Track Systems
Track systems, typically consisting of aluminum shelf brackets, fastening clips, and 1 ¼-inch-minimum-thick masonry panels, are used to hang thin veneer from either a vertical or horizontal application in situations without a conventional perimeter concrete footing to support the weight of the veneer used. Brackets are mounted onto walls, either exterior or interior, as support for masonry panels. Kerfs are sawn in the panels' top and bottom edges so they can be held in place by a railing lip on the brackets and by the fastening clips. Brackets are installed according to a desired coursing design. Next, panels are set in place by fitting their bottom grooves over a length of bracket lip, fitting support clips into the top grooves of the panels, and then tilting them towards the wall to engage the prongs of the fastening clips with the prongs of the support bracket installed above. The installation is completed by inserting backer rod into the panel joints and applying caulk over the backer rod to seal between the panel joint edges.
Prior to installing the bracket system, it is important to assure that the backing wall surfaces are smooth, flat, clean, and free of all debris. Furring may be necessary where the backing wall is not acceptable for direct attachment of the bracket system, and it is the engineer's responsibility to determine the backing wall's structural integrity based on the load imposed by the system panels and other applicable material, live, seismic, snow, and wind-loading conditions. It is important to evaluate not only the structural integrity of the backing wall, but also its capability to resist and drain moisture. Building wrap or other sheathing materials should be properly installed to the wall surface as needed to assure an adequate moisture barrier.
Shims should be used to separate the brackets from the backing wall in order to create a drainage plane for moisture control and to insulate the aluminum of the track from corrosive contact with backing wall materials. While shims may be sized variously to plumb the brackets, it is advisable to assure that the backing wall is as level as possible before the system components are attached.
Insulated Wall System
Another option that is rapidly gaining ground is the foam masonry panel system. These total cladding systems are designed to provide better insulation and consist of foam panels, stainless steel screws or anchors, and mortar, with the foam panel systems able to accommodate a variety of masonry units, including durable stone, clay, and concrete brick with others under development, ranging from larger stone units, stacked stone, and thin brick applications.
These systems take advantage of rigid foam, which has been a key element in energy-efficient buildings over the years as it increases the R-values of the walls with minimal thickness. Because the foam covers the framing elements, and if properly sealed and taped at the seams, the thermal bridging of cavity insulation is often eliminated. As a result, a layer of continuous insulation is provided outside the framing, achieving R-values as high as R-13 and achieving integrated moisture management. Continuous insulation is important because whenever a layer of insulation is interrupted, its effective R-value is reduced.
The foam is the key to the efficiency of the unit and, in addition to its insulation advantage, an effective foam panel will have drainage on both sides to divert any water that may penetrate the wall cavity in order to protect the structure from damage. Recesses in the outside face of the foam form the installation pattern for the masonry units, making for a fast install. Masonry units are friction fit into the pockets and mortar is applied in an injection gun. Some systems use a modified Type S mortar that has been engineered for superior bond strength, adhesion, flexibility, and stability for a long service life.
Foam systems have been proven to resist wind speeds exceeding 110 mph, and placed beneath the masonry surface, foam panels give the wall system an STC rating of 51, which is desirable particularly in multifamily structures as loud sounds will only be faintly heard, leaving occupants with a quiet dwelling. In rigorous testing per NFPA 285 and ASTM E119 standards, these systems have withstood hour-long exposure to temperatures exceeding 1,700°F.
Foam panel systems are essentially an easy install. Door and window openings should first be properly sealed and flashed to ensure thermal and water resistance. After a stable substrate has been achieved, the premolded insulation panels are attached to wood studs or other framing material; best practice is to use manufacturer-provided or approved stainless steel anchors and fasteners. The modular stone or brick masonry units are then installed into place within the insulation panel. The mortar is mixed and applied with a gun or pump. When the mortar is thumbprint hard, it should be tooled with a metal, wooden, or plastic striking tool. Excess mortar should be brushed away.
A Valuable Resource
As advances in every aspect of manufactured masonry thin veneer—from fabrication to shipping to installation—have led to improved products, usage has increased significantly. With a range of striking visual effects, as well as economic and environmental benefits, and ease of maintenance, these products offer architects a valuable resource for interior and exterior applications in structures of all types.
Endnotes
- 1. http://www.businesswire.com/news/home/20110208006008/en/Masonry-Veneer-Products-Experience-Substantial-Growth-2012#.VP4bEfnF-id
- 2. http://www.landscapingnetwork.com/stone-veneer/real-vs-manufactured.html
- 3. http://www.maconline.org/tech/materials/adheredveneer/adheredveneer.html
![]() |
Echelon is the consolidated brand for all masonry products and services of Oldcastle Architectural including Trenwyth® Architectural Masonry, Artisan Masonry Stone Veneers®, Quik-Brik® Concrete Masonry Units, Amerimix® Bagged Goods and a complete portfolio of Performance Upgrades. As a single source masonry portfolio solution, Echelon delivers consistent, reliable product manufactured locally at more than 170 locations and delivered by an unrivaled logistics network. For more information, call (844) 495-8211 or visit EchelonMasonry.com |