Concrete Overlays: Success With a Systems Approach
Continuing Education
Use the following learning objectives to focus your study while reading this month’s Continuing Education article.
Learning Objectives - After reading this article, you will be able to:
- Discuss the features and benefits of concrete overlay systems.
- Describe the importance of a systems approach to concrete overlays to avoid common mistakes.
- List the green attributes of concrete overlay systems.
- Discuss the specification of concrete overlay systems and the steps to install.
- Describe aesthetic and functional case studies of concrete overlay systems.
Concrete ranks amongst the strongest, most versatile building materials on earth, and is certainly the most widely used. But there is a challenge: Its use contributes 5 percent of all global CO2 productioni , which contributes to global warming and climate change. When faced with a concrete slab or structure that needs an upgrade, the architect and owner must decide: remove or improve? In many cases, a concrete overlay system is the best solution for the planet, the budget, the schedule and other major factors.
Before the features and benefits of concrete overlay systems can be discussed, it’s helpful to know exactly what such systems are. Concrete overlay systems are designed to improve the quality and sometimes radically change the appearance of existing concrete slabs and structures. Following concrete preparation, the system proceeds with three main phases: 1) polymer modified cements applied at various depths, 2) coloring products added, and 3) protective sealers added.
In this article we’ll discuss why a concrete overlay system may be the best specification for a project, and in particular why a systems approach, which means using products made by the same manufacturer for all stages, will ensure the greatest opportunity for success and the least risk of failure.
Why Choose a Concrete Overlay System?
Imagine this: As part of a renovation or retrofit, your project includes an existing concrete structure or slab that needs help. It may be cracked, or have suffered freeze-thaw or salt damage. Cracking occurs for many reasons, such as unstable soil, chloride ion penetration that attacks the reinforcing steel or insufficient placement or existence of expansion joints. Cracking could be from high heat and windy conditions during the initial installation, which prevented proper curing.
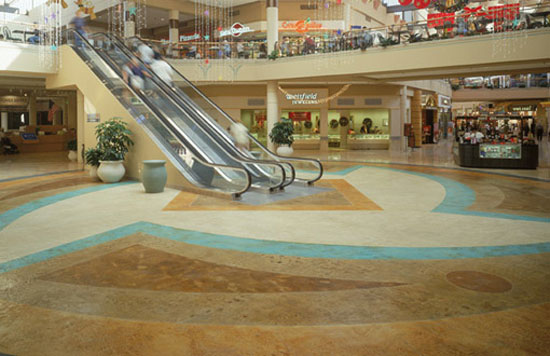
Photo courtesy of Super-Krete Products
Concrete overlay systems are often driven by a failed concrete slab. In this case, at Superstition Mall in Mesa, Arizona, the owners chose a concrete overlay system for an aesthetically dramatic upgrade.
As the architect or owner, you have two choices: Replace it or fix it.
For many reasons, the latter option can make the most sense—for financial, convenience and sustainability-focused reasons.
Typically, upgrading an aged or defective concrete slab with a concrete overlay is driven by money. The labor and material costs to tear out an existing slab and create a new one can be exorbitant. The choice depends on the substrate condition and whether or not it can indeed be retrofitted.
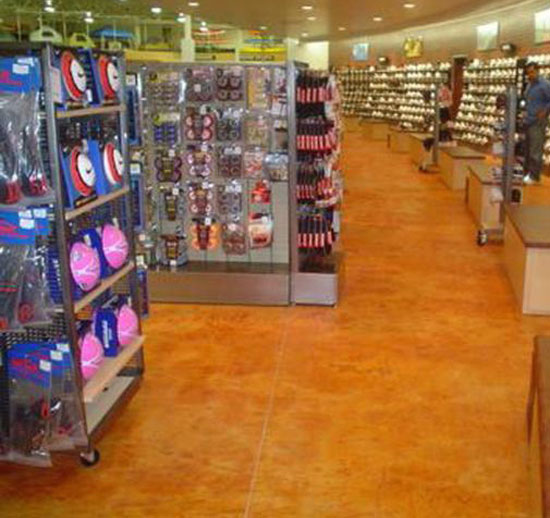
Photo courtesy of Super-Krete Products
Sports Chalet, Sacramento, California, with a concrete overlay system.
Aesthetics also play a part when the slab is simply not up to the look desired by the owner. Concrete overlays provide an opportunity for striking colors and patterns to complement a corporate brand, perhaps, or to convey sophistication and newness.
Overlay systems are sometimes specified to provide anti-skid qualities, both indoors and outdoors. This could be around a pool area, or the lobby of a municipal theater, or a retail location, a health care facility, or anywhere else where safety and slip prevention are high priorities. The need for ramps, skid resistance and working on slopes will determine design elements.
The location of the project can determine the specification of an overlay system rather than demolition and replacement. The disruption and large machines required for such an endeavor may not even be an option.
Whatever the drivers toward an overlay system and away from demolition and replacement, there are benefits to making that choice. An overlay system can hide defects and correct imperfections that may have been there for years or decades since the initial concrete placement.
An overlay system can create a seamless look throughout an entire area where concrete placement happened at different times, even different decades. The system can simply beautify the area, or correct bad pours. With color mixing and stamping, a total custom aesthetic can be achieved.
And perhaps most importantly for some owners, an overlay system process accommodates time restrictions and satisfies the need for near uninterrupted use of the property when demolition and installation of new concrete would prove prohibitive.
Common Causes of Concrete Failures
As concrete failure is typically a driver for an overlay system, let’s first look at ways in which concrete fails.
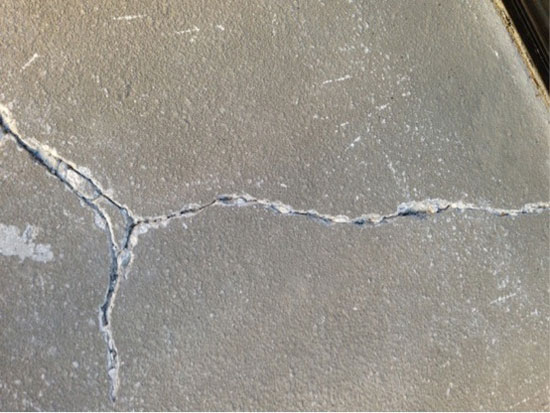
Photo courtesy of Super-Krete Products
Concrete cracks for a number of reasons. The causes need to be fixed or eliminated in order for an overlay system to be successful.
Cracking
Cracking can take place in concrete for many reasons such as unstable soil, chloride ion penetration that attacks the reinforcing steel, and simply due to high heat and windy conditions during the initial installation. Micro circular cracking is normally caused by over troweling the concrete, which traps the chemicals from the cement and prevents them from escaping. With new concrete, the issues can normally be resolved by adding densifiers to the initial concrete pour. Or, the use of spray-applied densifiers can help stop deterioration of concrete, regardless of the age, if the pH is not beyond stabilization. Cracks in existing concrete can be repaired using epoxies and other high-strength fillers, but the cause of the cracking should be addressed. Concrete requires saw cuts at various sections of the concrete to allow sections to move independently of each other. Many concrete workers simply cut joints to a depth of the tool being used. This is an incorrect procedure. Saw cuts should be full depth separating the slabs to allow for movement or allow a cracked section to be removed without disturbing the adjacent concrete. If no saw cuts are made full depth, the cracks will travel throughout the concrete. Saw cutting full depth is recommended followed by caulking of the joint.
Freeze-thaw and Salt Damage
In climates where freezing temperatures take place and salt is applied to melt snow and ice, the concrete will deteriorate much faster. That’s because the concrete has pores or capillaries and the capillaries hold water absorbed by ground water, moisture vapor transmissions or from just the atmosphere. When the weather changes rapidly below freezing the water in the capillaries turns to ice and expands, creating concrete surface chipping or complete deterioration of the concrete. Again, densifiers will normally protect against freeze-thaw by prefilling the pores with a glass-like substance that will eventually turn into impervious concrete. Salt either applied over the surface for snow melting or simply tire traffic carrying salt from the road over any adjacent concrete will also create damage. It should be understood that concrete is like a magnet to moisture. Concrete absorbs moisture from any source available.
Coating Failures
There are many excellent coatings in the market today for the repair, resurfacing and decorating of concrete substrates. Some have better bond strength and wearability than others. However, most coating failures are due to the trapping of moisture vapor transmissions and the chemicals forced to the surface in the form normally referred to as efflorescence. Some manufacturers recommend a bonding agent be applied, such as a polymer or epoxy, to both bond the coating and hopefully keep the moisture and chemicals from delaminating the topical coating system. Experience has proven that moisture vapor transmissions alone will not delaminate a well-bonded topical coating system. The chemicals forced to the surface by the moisture vapor transmissions become trapped beneath the coating system and eventually disintegrate the top layer of the concrete supporting the coating. This is evident when the failed coating is removed and either efflorescence or moisture is discovered to be present. It should be noted that manufacturers do not warranty their coating system be applied over concrete that has in excess of (3 lb) of moisture vapor transmissions per 1,000 square feet of surface area.
Avoiding Common Overlay Mistakes
Once any cause of concrete failure is understood and addressed, the concrete overlay system can be considered.
For all the benefits of concrete overlays, things can go horribly wrong if the process is not approached as a system. As in any system, the many parts must be compatible for best results. The key to a compatible overlay system is to make sure all products used in each phase (to be discussed later) are from the same manufacturer.
What can go wrong with combining products from different manufacturers?
It’s hard to say because when products are combined, and something does go wrong, each manufacturer will likely point the finger at the “other” products. In fact, no one will really know why delamination or flaking or efflorescence happened.
Common problems when mixing product lines include:
• Whitening of sealers.
• Ambient and surface temperature requirements and tolerances may vary.
• Chemistry incompatibilities lead to failure.
• Different surface preparation methods are typically required for overlays. Always work with the manufacturer’s recommended surface prep methods.
• Chemical encapsulation / coating failure can occur if moisture vapor transmission is not treated.
• Acid stains may have an adverse reaction and not turn out with polymers in concrete or contaminants in concrete.
• Products may not bond well to each other, which defeats the purpose of a “systems” approach.
• VOC compliance issues.
• No warranty/no guarantee when not applied as a system.
At least one concrete coating manufacturer emphasizes the use of the concrete treatment to treat the concrete internally, instead of a primer type material topically applied to concrete surface. Be sure to ascertain which type of treatment the manufacturer suggests.
Lack of Standards for Overlay Systems
One part of the problem is that there are not yet any standards for overlay systems. So it’s impossible to follow standards to ensure compatibility.
Systems components from the same manufacturer are guaranteed to be compatible. However, it’s important to reiterate, when mixing product lines, there are no warranties. Compatibility is not guaranteed and finger pointing can be expected. The sealer manufacturer will say the pretreatment caused the problem, or the other way around, or both will say the sealer was the culprit. Likely there will be no source of liability or technical support. In fact, it’s likely to be a negative outcome for all involved.
Using one system minimizes phone calls and problems, minimizes labor-oriented failures and provides value to clients.
Green Attributes of Concrete Overlay Systems
Concrete overlay systems provide enormous green attributes when compared to the process of concrete removal and replacement. The most obvious benefit is diverting demoed concrete from landfills. Not only is demolition and replacement expensive and disruptive, it’s also the option with the greatest embodied energy. As green building proponents like to say, the greenest building is the one that’s already built. This goes for concrete as well.
A concrete overlay system reduces the need for more key resources such as concrete, steel and rebar, and makes best use of what is already there. There is minimum site disturbance and earthwork required. That means no special heavy equipment hauling materials across town or across the country, both to remove the demoed material and to bring in the new materials. Improving what’s already there requires minimal interference with existing vegetation. This is one of the truest examples of having a small footprint, or of sustainability.
Cost to Remove Concrete Slab
According to one company that removes concrete slabs, here is a possible cost breakdownii
Zip Code | 47474 |
Size | 100 sq ft |
Labor | Direct labor expenses to remove concrete slab: 10.3 hours |
Slab Debris Disposal Costs | Costs to load and haul away old materials and installation waste |
Slab Equipment Allowance | Job related costs of specialty equipment used for job quality and efficiency, including: 115v, 15-amp electric jackhammer, 1000+ blows/minute. |
Average Cost to Remove | Low: $6.66/sf. High $7.73/sf. |
Cost for Basic Decorative Concrete Resurfacing with Sealer/Protection
Here are some basic costs for concrete resurfacing products:
Product | Approx. gallon cost | Sq Ft Coverage | Total Cost / sq ft | |
---|---|---|---|---|
Etch & Clean | $87.77 |
300 |
$0.29 |
|
Penetrating coat | $41.89 |
300 |
$0.14 |
|
Bonding coat | $46.14 |
300 |
$0.15 |
2 coats generally needed |
Color Stain | $43.26 |
300 |
$0.14 |
2 coats generally needed |
Sealer | $35.91 |
300 |
$0.12 |
2 coats generally needed |
Total cost/sq ft |
Less than $1.50 |
As these charts indicate, the cost to resurface is less than the cost just to remove the existing concrete, let alone replace it with a new concrete slab.
Contributes to Sustainability Goals
When it’s all said and done, properly applied concrete overlay system extends the life of concrete structures and slabs.
And, the process can help you qualify for LEED points in these areas:
Reduce Heat Island Effect. Darker colors (including black asphalt and dark-colored pavements) absorb more heat, raise pollution levels and increase need for air conditioning or cooling methods. On the contrary, light color selections allow solar energy to be reflected rather than absorbed, keeping the concrete cooler.
Improved Air Quality. Concrete overlay systems produce low to no volatile organic compounds. Sealers provide simple cleaning and maintenance, further reducing the need for labor and products far into the life of the product. And overlaid and sealed concrete does not harbor allergens or dust mites. Note that overlay systems are comprised mainly of local sand, cement and water.
Use of Recycled Materials. An overlay system can incorporate recycled glass, bottles, and other types of post-consumer recycled content. Plus, pigments may be made from up to 99 percent recycled material. This may help you achieve LEED credits under the recycled content category of Materials and Resources.
Other benefits include:
Improved Local Comfort. Can significantly improve the look and feel of any space. It improves areas where people congregate, such as schools, play areas and parking lots, making them more comfortable.
Better Nighttime Visibility. Color selection can enhance visibility and decrease lighting requirements. At least one manufacturer offers a glow-in-the dark concrete overlay. The light-storing material is applied up to 1/8 inch and is charged by natural sunlight. It glows for up to 12 hours, in some cases eliminating the need for electrical lighting. It provided an ambient glow anywhere that is desired, and makes areas safer, helping preventing tripping and falling.
Fire Resistance. Fire resistant materials keep toxins from being release in case of fires. And the overlaid concrete surface is unaffected by radiant floor heating.
The Specification of Concrete Overlay Systems
To specify a concrete overlay system, a step-by-step process will ensure success. Here are the recommended steps:
1. Selection – What is the condition of the existing surface? What environmental and traffic conditions will the overlay be exposed to? What maintenance is required? What is the desired look?
2. Design Development – Sufficient thickness, sufficient protection.
3. Colors – Many systems are available in dozens of standard colors and those colors can generally be mixed to create custom colors.
4. Patterns – The pattern should be chosen based on both function and aesthetics.
5. Installer qualifications – Installers should be experienced with similar products and have an appropriate sized crew for the size of the project. Prior to application for manufacturer warranty, all installers should ideally apply and file with manufacturer a copy of the project specifications, applicator certificate and required products list, tools and equipment to be used on the project.
6. Samples and mock-ups – A 12-inch-square sample of the proposed system should be provided by the installer for approval. Color, texture and finish should be representative of overall appearance of finished system.
7. On-site inspection and monitoring – The installer should test the pH, moisture vapor transmission rate, air temperature and dew point before and during installation.
Steps for Concrete Overlay System Installation
Surface preparation is key for a successful, durable project. The purpose of surface preparation is to provide a sound, clean and roughened surface for the overlay system to sufficiently bond and gain traction. Toward that goal, existing coatings, paints, sealers and waxes must removed, preferably by shot blast and/or scarifying. The surface should be clean and porous and moisture issues must be addressed.
Surface Preparation
For surface preparation, a range of methods can be considered. Which one is used depends on the repairs needed and the requirements of the protective system. The type of preparation depends on the Concrete Surface Profile, or CSP, that is needed for the products to be used. A technical guideline by the International Concrete Repair Institute (ICRI) provides a chartiii showing which methods will result in which profiles. For instance, the surface preparation method of “detergent scrubbing” will result in a CSP of 1. On the other end of the spectrum, machine rotomilling will result in a CSP of 6 to 9. In between are such methods as low-pressure water cleaning, grinding, shotblasting and others. Determining the CSP required will then indicate which surface preparation method is needed.
Moisture is a serious issue for concrete overlay success. Moisture emissions can’t always be seen. For best results in interior applications, moisture level should not exceed 3 psi. A dome test every 1,000 sf creates a snapshot in time. If applicable, treat it with concrete treatment from the same manufacturer as the concrete overlay.
According to George Donnelly Testing & Inspections, “If the architectural, design and construction communities will embrace the test standards as written, it is our opinion that there will be far fewer moisture-related floor covering failures. Proper testing, performed under proper conditions, reported directly to the owner should encourage pro-active remedial treatment of non-compliant slabs, before the flooring is installed.”iv
Concrete moisture treatments can reduce moisture vapor emissions to an acceptable level, and can increase compressive strength of concrete more than 20 percent. It increases freeze/thaw resistance, encapsulates chemicals, reduces efflorescence, prevents molds and mildew, prolongs coating life and prevents delamination. In some cases, it penetrates the concrete more than 8 inches.
The pH level of the concrete surface should not exceed 9 in a pH pencil test. The result must be neutral.
Plus, the concrete must be structurally sound. In some cases, the substrate needs a rehabilitation process. That could include patching, leveling and treating cracks. Oftentimes, the cracks are discovered after the cleaning process. Even when cracks are treated, however, many are likely to return. In fact, not all concrete can be coated, and an assessment by a concrete expert or manufacturer’s representative should be done before proceeding.
Cracks in concrete can be treated with a system including fiber mesh matting and high bond-strength polymer technology. However, this type of crack treatment system is not intended for structural repairs. Expansion joints must be honored, and may need to be cut. In some cases, cracks and joints can be incorporated into a decorative pattern.
Densifying
Densifying is accomplished with a non-hazardous penetrating sealer for use on all concrete and masonry substrates. The integral concrete sealer reacts with alkali and free lime in common cement and creates an internal crystal-like shield, increasing the strength of new and existing concrete and masonry, and reducing moisture vapor transmission. It provides chemical encapsulation by forcing excess chemicals to the surface for removal. It protects surfaces from freeze/thaw damage, reduces dusting of concrete, and can increase coating life by as much as 300 percent.
Resurfacing
The next step in the process, once the substrate is prepared, is resurfacing with the desired texture. After what can be a lengthy preparation process, this step will often make the biggest visual improvement, and can make surfaces look like newly placed and cured concrete.
A number of textures are possible, including trowel applied (interior and exterior), smooth and polished (interior), spray textures (walkways, pool decks), brush or broom finish (sidewalks, walkways) or stamp overlays (interior and exterior).
A stamped overlay of 1/8-inch or ¼-inch creates the look of natural stone, tile, brick, wood, slate and other natural surfaces. In fact, there are hundreds of options to choose from and the process is highly customizable for clients who want a truly custom specification. For overlays, color options include integral and topical options, with both acidic and water-based options. It’s important to note that acids react with concrete internally, and different slabs may react differently and they will vary. Prior testing is a must.
Color
Adding the color stain could be the most exciting step from the perspective of the architect, specifier and owner. Most color stains for concrete are water-based, which means they are non-acid, non-toxic and non-reactive. There is typically a standard color stain palette of 20 colors, which can be blended to make new colors.
Many varieties are available, including integral colors, water-based stains, acid stains, dyes, paints and metallic powders. Each manufacturer has their recommended coloring systems and the architect or specifier should stick with the same manufacturer. Pay special attention to system recommendations for the job at hand. For example, a dye is not always UV stable so should not be applied outdoors or for exterior applications. Acid stains are not favorable if color consistency is desired outcome, and so on.
For best results and to protect against liability and compatibility issues, the texture and color products should come from the same manufacturer. If the decision is made to mix products from various manufacturers under the guise of price or convenience considerations, there will be little if any recourse if there is product failure. You can be sure that each manufacturer will place the fault with the other, with you and your client left in the middle.
Sealing
The final step in the process is sealing the concrete for protection. Specification of a particular sealer depends on the traffic anticipated and the type of project. Industrial sealers will be chemical resistant while residential sealers will be FDA-compliant for use on concrete countertops or other surfaces used for food preparation. Further aesthetic customization can happen here with a gloss, semi-gloss or natural look. Needs may also include UV resistance, fade resistance and chemical resistance. As with the other steps in the process, sealing should be done only with a product made by the same manufacturer as the topcoat and color stain. When in doubt about which sealer to use within a manufacturer’s offerings, the selection of a sealer should be discussed with a manufacturers representative or through the technical support line.
VOC regulations vary significantly across the country and will make a difference in what is legal and available in specific markets. Refer to the South Coast Air Quality Management District for all compliant coatings.v
Maintenance of a properly specified concrete overlay system will be fairly straightforward, typically requiring only power washing or waxing. Over time, re-staining and resealing are options typically every three to five years.
Case Studies of Concrete Overlay Systems
Conclusion
While concrete is one of the heavyweight champions of the built environment, it should not be demolished and replaced without great consideration. The most cost-effective, time-sensitive and ecological option could be a concrete repair and overlay system. However, if the overlay is accomplished with products from various manufacturers, and problems occur in the future, the installer and owner will have little recourse. Only by using a compatible system of products, applied according to the manufacturer’s guidelines, can the specifier, installer and owner be protected from unnecessary calls, confusion and finger pointing in the case of issues.
When a compatible system is used for a concrete overlay project, the benefits are multifaceted, from aesthetic to functional, and from standard to customized. Using a system, and doing it right, is the key to a successful project.
Kathy Price-Robinson is a nationally known home and construction writer and continuing education developer. Her series on remodeling “Pardon Our Dust” ran 13 years in the www.linkedin.com/in/kathypricerobinson
Endnotes
i http://www.rsc.org/images/Construction_tcm18-114530.pdf
ii http://www.homewyse.com/services/cost_to_remove_concrete_slab.html
iii http://www.icri.org/publications/2014/PDFs/mayjune14/CRBMayJun14_WInkler.pdf
iv http://www.moisturetesting.com/calcium_chloride_vs__in-situ_relative_humidity.htm
v http://www.aqmd.gov/docs/default-source/rule-book/reg-xi/r1113.pdf
![]() |
SUPER-KRETE® provides cost effective solutions and alternatives to the tear out, removal and replacement of concrete through resurfacing and restoration. We focus on sustainable, green, environmentally friendly products and solutions while providing a customizable pallet of colors and textures. For over 25 years, Super-Krete products have been waterproofing, enhancing, protecting and restoring concrete installations worldwide. www.super-krete.com |