Structural Steel Cast Connections
An elegant solution for architecturally exposed structural steel that can also provide cost savings
Continuing Education
Use the following learning objectives to focus your study while reading this month’s Continuing Education article.
Learning Objectives - After reading this article, you will be able to:
- Investigate the design potential and innovative opportunities that steel castings can contribute to architecturally exposed structural steel (AESS) applications.
- Identify and recognize the various steps involved in the casting manufacturing process including industrial design, detailing, tooling, casting, and machining, and to understand and accommodate the lead times associated with custom castings.
- Differentiate between the various common types of cast steel connections and their appropriate uses in different settings.
- Assess through case studies how steel castings have been used in structural design to maximize architectural benefits, simplify fabrication, and speed erection.
Structural steel has been a material of choice for a wide variety of building projects for over 100 years due to its comparatively light weight and excellent structural capabilities. The industry surrounding the production of structural steel sections and the fabrication and erection of steel buildings has evolved in this time and created a fairly sophisticated and easily accessed network of companies, organizations, and individuals. Architects have embraced the benefits of this material and its industry since it allows a certain amount of design flexibility and freedom while often helping construction budgets. This has led to an increasing trend in building design to use structural steel as an exposed design element. Such a design approach requires special attention to make the steel look acceptable not only along the body of the exposed members, but particularly at the connection points. Those connections can often be characterized by an array of bolts, stiffener plates, welds, and other structurally necessary elements which produces an aesthetic that, if left unspecified, is more utilitarian than artistic. Happily, that is no longer the case when the decision is made to use cast steel components. Standardized or custom cast connectors are readily available which provide dramatic geometric freedom in structural steel shapes, thereby enabling artistic designs to be realized.
The Metal Casting Process
Casting molten metal into a form is a common process that has been used historically for many metals including bronze, copper, and steel. In fact, all structural steel starts its life being cast into an ingot or other industrial shape. That steel is then hot rolled or cold formed into the final shape of the structural steel members we are more familiar with such as wide flange sections, angles, channels, hollow structural sections, etc. This rolling/forming process works well for continuous or linear shapes, but not for other, non-linear, custom shapes. Hence, the creation of such specialty steel components relies on using a mold to pour molten metal into thus forming the desired shape without rolling or forming.
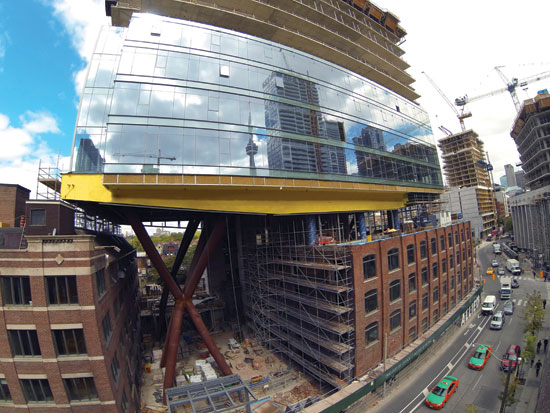
Photo courtesy of CAST CONNEX
Architecturally exposed structural steel used on buildings of all types can now also be true design statements due to the availability of cast steel connectors in the U.S. and Canada.
A common misconception regarding steel castings is that they are brittle because they are sometimes confused with cast iron. This is not the case in cast steel products which are just as ductile as rolled structural steel products, if not more so. The main difference between standard rolled structural steel shapes and steel castings is the production process which results in their final yield strength. Hot-rolled or cold-formed products attain their yield strength through the rolling or forming processes, whereas steel castings are heat treated after they are cast to attain the desired mechanical properties. In a normalized condition, low alloy steel castings can be readily produced with yield strengths in the range of 30 to 40 kips per square inch (ksi). By introducing quenching and tempering processes, yield strengths of 50 ksi and greater can be attained. In Europe, a process called secondary heat-treatment is now being used to attain yield strengths as high as 150 ksi in castings to be used in special structural applications.
The typical process for the creation of all cast steel products occurs at a metal foundry and is essentially the same regardless of the size or complexity of the casting. The process starts once a particular shape is designed and analyzed for structural integrity. Then a full-size, three-dimensional rigid replica or pattern is made of the component out of cut wood, plastic, or similar material using a computer numerical control (CNC) process. Next, chemically treated sand is placed around the finished pattern in two halves. When the sand has cured and stiffened, the pattern is removed by opening and then re-closing the halves, thus leaving a hollow, stiff sand mold that replicates the pattern exactly. In preparation for casting, the surfaces of the sand mold are treated with a ceramic-based coating. The sand and ceramic coatings are selected by the foundry for their ability to withstand the high temperatures of molten metal.
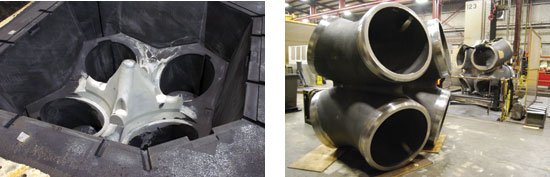
Photos courtesy of CAST CONNEX
Cast steel is formed in a hollow sand mold which receives the molten steel and then is removed to reveal the finished steel product.
With the mold readied and secured in place, the specified metal is heated in a blast furnace until it reaches its molten state. It is then carefully poured into the sand mold and allowed to cool until it solidifies into shape. After the cooling is complete, the casting is removed from the sand mold by breaking away the sand. This means that the mold is destroyed in the process but the original pattern remains which can be reused to make multiple identical molds. Hence the process can be repeated as often as needed to make as many identical products as desired.
Using this common and time proven process, cast metal products are readily produced in virtually any size from very small to very large. Further, the shape and complexity is limited only by the imagination of the designer and the limits of the materials being used. There are of course certain design parameters that make for a better casting than others, but those are fairly well known and understood within the industry. Small, simple cast steel products include things like small cable connectors or cast hardware or decorative elements. Large, complex ones include multi-angle, multi-force custom structural elements for buildings.
Cast Steel Structural Connections
Cast steel has been in use for quite some time in a variety of applications. Railroads use cast steel couplers for connecting freight cars to locomotives. Industrial equipment such as mining trucks use steel castings to make different parts including the entire load bearing frame for improved durability and resistance to impact loads. When it comes to buildings, steel castings have been commonly used for valves and fittings.
The use of cast steel as part of a structural system first occurred in the late 1970s in the construction of offshore oil platforms. These platforms consist of a complex framework of tubular steel members that commonly used welded connections. Problems arise, however, since the structures and their welded member connections are subjected to strong wind and wave action at sea. Given the constant loading and the complexity of the welded joints between the members (anywhere from two to eight members intersect and must be connected to transfer forces) these connections are susceptible to fatigue failure. In response, the concept of a rigid “cast steel node” was developed. This alternative employed casting manufacturing to handle the complex geometry of the junction point thereby smoothing out the stress concentrations in the connection and moving the welded joint away from the region of geometric complexity. Further, the geometric freedom afforded through casting enables thickening the metal where necessary, as opposed to welded fabrication whereby connections are built up from plates. The use of cast steel nodes in this way improves the high-cycle fatigue performance of these connections by more than an order of magnitude. Although these nodes are purely functional, the smooth, more organic, and sweeping appearance of these junctions made them a prime candidate to eventually be applied in architectural construction on land.
One of the first architects to make substantial use of steel castings in the design and construction of an onshore building structure was the firm of Renzo Piano and Richard Rogers. In the mid 1970s they designed the Centre Pompidou in the Beaubourg area of Paris, France. The intentionally exposed structure created a post-modern, high-tech design style with structural steel cast elements used to tie different structural elements and portions together. These castings were used as much for the structural integrity of the building as they were for the desired aesthetic. Since then, cast steel structural connections have become common in architecturally exposed structural steel (AESS) designs throughout Europe. In North America, however, their use has lagged behind primarily due to the historical focus of U.S.-based steel foundries on mass production rather than “jobbing” customized production. However, the recent advent of various standardized cast steel components meant for use in building construction has led to an interest by the U.S. foundry industry to support the architectural community in providing both standardized and custom designed steel castings.
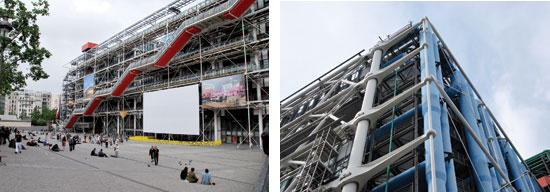
Photos courtesy of Terri Meyer Boake
The Pompideau Centre in Paris, France, was one of the first buildings in Europe to use architecturally exposed structural steel incorporating cast steel components.
Some of the beneficial characteristics of cast steel connections that have been realized in buildings include a dramatic increase in geometric and aesthetic freedom compared to conventionally fabricated connections. Structurally, they provide improved connection stiffness, strength, and fatigue resistance. During construction, they provide simplified fit up, fabrication, and erection. Given all of this, when does it make sense to consider cast steel connections in a building design? Their characteristics make them a preferred choice whenever architecturally exposed structural steel (AESS) is part of the design, particularly if round Hollow Structural Section (HSS) members are the primary structural members being used. They also work quite well for connections in exposed timber frame construction. There are several other building design conditions that also make cast steel connections a preferred choice to solve and simplify loading and connection issues, such as:
• When the building design requires complex connections due to complex geometry (i.e. many members framing together at a single location and/or at sharp angles where weld access would be an issue)
• For heavily loaded connections or when increased connection stiffness is needed
• When material fatigue is a critical connection criterion
• When the connection has to satisfy a special performance requirement, like blast or seismic resistance
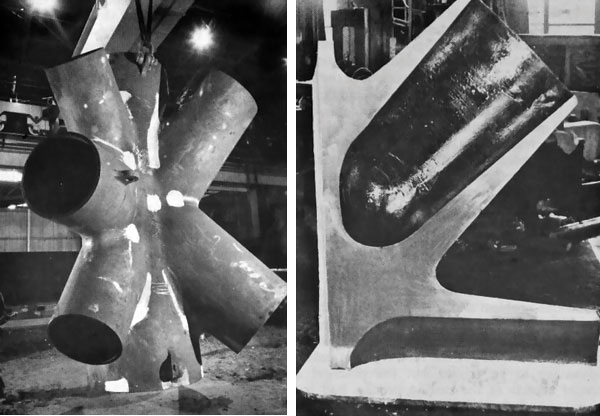
Photos courtesy of CAST CONNEX
The proper design of cast components allows for metal to be thicker or thinner within the piece as structural loading may require.
The analysis and decision on whether or not to use steel castings are best incorporated early on in the design process. Standardized cast connections can be reviewed in consultations between the architect, structural engineer, and a manufacturer's representative. Sizing and selection can often be made from available online or printed literature much the same way as other steel products. However, the building design may give rise to the need for a custom casting if standard ones are not appropriate. Given the specialty nature of such a custom casting design, they are often procured as a design-build item with all parties involved in the process. In this case, specialty casting engineers work directly with the building design team to fully integrate the building design needs with the best practices of casting fabrication. In this way all casting requirements and building design parameters can be properly assessed and accounted for. Such well integrated casting designs not only enable highly unique architecture and connection detailing, but they can also simplify fabrication, improve construction tolerances, ease erection, and thereby lower the overall cost of the installed steel structure.
In the process of reviewing how the cast connections join with the main structural elements, it is important to avoid the misconception that steel castings are not weldable. Again, this comes from incorrectly drawn parallels to cast iron. The reality is that cast steel grades can be selected for any number of mechanical properties, including weldability. In fact, welding is the primary and most common means for joining a cast connection piece to an AESS element since the joint can be ground smooth and finished to appear as a continuous member. In particular, The American Institute of Steel Construction (AISC) publishes standards and guidelines such as AISC 360-10 which lists ASTM A216 Grade WCB as a cast steel grade useful for steel structures. However, there are currently no cast steel grades listed as prequalified base metals in standard welding guidelines so welding procedure specifications must be qualified accordingly. In particular, preheating is required for welding very thick castings and common good welding practices should be exercised.
Types of Cast Steel Connections
While all cast steel connections will share the attributes and production process already discussed, different types of connectors are made for different building design conditions. The four most common types are universal pin connectors, architectural tapers, high-strength connectors, and custom cast connectors.
Universal Pin Connectors (UPC)
In many cases, the ideal structural connection from an architectural perspective is not a welded or bolted plate, rather it is a “true-pin” connection. While that ideal shape is difficult to achieve with flat or rolled steel, it is easily achieved with cast steel. Hence, universal pin connectors (UPCs) have become readily available in many sizes as standard, off-the-shelf cast connectors for AESS. They have become popular in a number of design schemes because they allow for a final appearance that provides elegance, simplicity, and consistency.
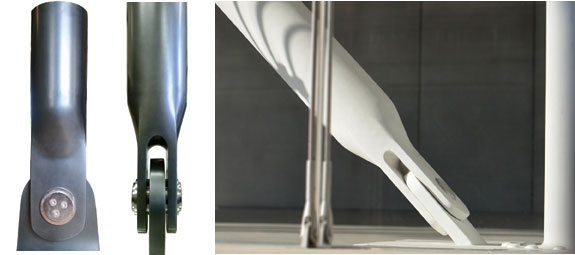
Photos courtesy of CAST CONNEX and Terri Meyer Boake
Universal pin connectors are standardized cast products that are welded to the end of a hollow structural section (HSS).
The primary benefit of a true pin connection is that it allows for any geometric angle of connection which is particularly useful in cross bracing or other angular structure situations. And since the pin rotates freely until secured in place, field adjustment of the pin and angle is easily accommodated. On a broader basis, UPCs are readily used at the ends of any structural element carrying tension and/or compression, meaning that they are suitable for use at the ends of columns, braces, struts, ties, or any other common structural element where a true pin load connection is desired. They have often been used as part of the overall structural system for entrance canopies, to connect web members of large trusses, as support connectors in specialty stairs, and at the ends of exposed braces that are part of the building's primary lateral force resistance system.
Cast UPCs are commonly sleek, clevis-type standardized fittings designed to connect to hollow structural section (HSS) elements. The connectors are generally carefully sculpted to provide a smooth transitional geometry that reflects the natural idealized flow of structural forces. The use of cast UPCs welded to HSS elements allows for a true pin connection and overcomes the inherent difficulty of trying to do so directly within the HSS element alone. Where aesthetics are a particular concern, the use of UPCs greatly simplifies the design, detailing, and fabrication of architecturally exposed structural connections while significantly improving the aesthetic appearance of the finished assembly. A complete UPC connection will require some additional hardware beyond just the cast portion. Specifically, they will need the associated carbon steel or stainless steel pins that insert through the connector and a base element. To work properly and hold the pin in place, stainless steel washers, cap plates, and cap screws are all generally required as well. Manufacturers have recognized this need and commonly supply all of this related hardware for a complete connection.
Some of the advantages of using UPCs include an aesthetic that provides elegant, smooth, curving transitions from every viewpoint. Properly designed, they can provide eye-catching end connections with a known cost, unlike traditional AESS connections which have been known to escalate in cost, even after the bid is awarded. Part of the cost improvement comes from dramatically simplified fabrication and a fraction of the grinding that typically accompanies AESS. Whether standard or custom UPCs are used, the casting process yields duplicate identical pieces to provide a consistent and reliable architectural appearance. And to make structural calculations and sizing easier, common connection details have been analyzed by manufacturers who can provide tabulated connection capacities.
Cast Architectural Tapers
Cast architectural tapers are conical, hollowed, cast structural steel members that are tapered in shape. They are designed to connect to the end of round HSS members, typically those acting in compression, for use in architecturally exposed structural steel applications. Cast architectural tapers can be used, for example, at the ends of exposed steel columns in a building's atrium. By combining universal pin connectors with architectural tapers, an aesthetic can be realized where the overall HSS member appears more slender. The smaller end condition also allows for a smaller UPC to be used.
Conventional fabrication of hollow conical steel tapers is difficult at best since it involves cold or hot forming/bending flat plate into a conical shape. Often steel fabricators and contractors will shy away from projects calling for such details if they don't feel comfortable carrying out the fabrication. By contrast, cast architectural tapers are easily welded to the end of round HSS tubes by steel fabricators and installers. Once assembled and welded, the joints can be ground smooth to create an elegant finished structural element. Due to the relative ease of fabrication and installation, cast architectural tapers have become readily available and cost effective. They are typically consistent in appearance and quality by virtue of the casting of standardized pieces.
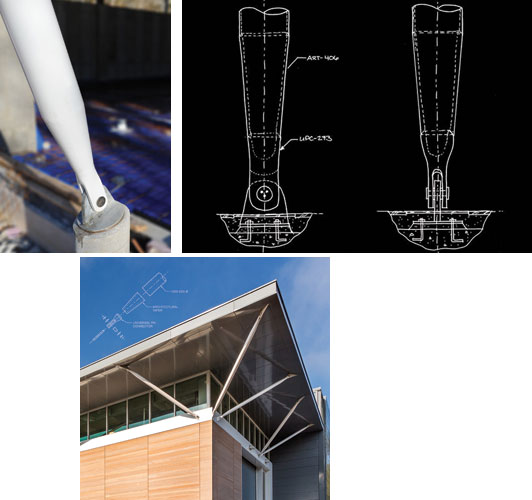
Images courtesy of CAST CONNEX and Ellenzweig
Architectural taper transitioning between a universal pin connector and a hollow structural section (HSS) tube.
High-Strength Connectors (HSC)
Not all structural loading conditions call for the use of pin connections. Some require a fully rigid connection that is tolerant of a variety of forces which may include seismic, particularly in concentric braced structural frames. The conventional manner of addressing this need is to engineer detailed connections that often require connection reinforcement and the field welding of cross bracing to gusset plates which have been fabricated onto steel beams and columns. Such field welding requires skilled labor and an independent special inspection of the completed welds. All of this makes such conventionally fabricated connections rather complex and costly. By comparison, cast steel connection products have been developed that are simpler, work better, and create a lower cost connection overall.
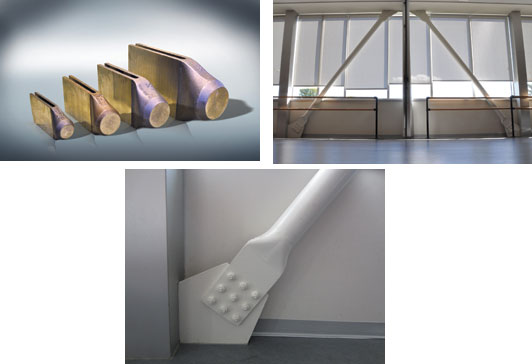
Images courtesy of CAST CONNEX
High-strength connectors provide a rigid bolted connector that is suitable for addressing seismic and other loading conditions.
Cast steel high-strength connectors are standardized brace end connectors that accommodate a bolted double-shear connection between round HSS braces and a typical corner gusset plate. They are available in different standard sizes and capacities to suit a range of loading conditions. The modular design of these connectors minimizes detailing and accelerates fabrication of the steel structure. They are available as pre-designed and detailed connections which dramatically reduces engineering time and effort. During construction, the cast HSCs eliminate the need to field weld braces to the frame, hence they significantly speed erection and reduce the cost of special inspections. Because they are fully engineered connections, they can readily demonstrate conformance to code-listed connections that meet all of the requirements of AISC standards and guidelines to provide high-strength, functional connections for earthquake-resistant braced frame buildings.
Perhaps most significantly, cast HSCs are typically designed to eliminate shear lag in the connection. The AISC defines shear lag as behavior at an end connection of a tension member where some but not all of the cross-sectional elements are connected. This can mean that the actual effective area of the connection that is tension-resisting may be less than the full calculated net area. Cast HSCs are intended to have a full penetration shop-welded joint between the connector and tubular brace member which thus assures that the full cross-sectional area is available to resist all forces, thus eliminating the shear lag effect. This means that no connection reinforcement is required and the common iterative design process for determining reinforcement plates is eliminated. Overall the final joint provides improved reliability and a simplified connection design using standardized, pre-engineered cast steel pieces.
Although intended to be functional, cast HSCs also offer a unique aesthetic, which can be suitable for use in some AESS applications. Although the bolted connection is visible, it is an effective, compact connection which is consistent with a high-tech or utilitarian aesthetic without all of the visual clutter or variations found in conventional connections. HSCs also provide a compact gusset connection which reduces the likelihood of interferences with non-structural elements of the building.
Custom Castings
Thus far we have reviewed mostly standard types of cast connections that are commonly available. As design teams are faced with bigger challenges or simply choose to get more creative about exposed structures, it is important to know that it is entirely possible to create completely custom steel cast connections that allow the realization of a design vision in freeform architecturally exposed structural steel. In some cases, the custom castings may be variations on the UPCs or HSCs already discussed. In others, design conditions may suggest completely custom castings, giving designers the ability to create unique and even iconic structures. Custom castings are appropriately considered for architecturally exposed connections, particularly for connecting HSS elements or to mate between various materials (i.e. steel to timber). They are also the best solution for complex connections subjected to heavy loading from a variety of structural members aligned in different directions. Structurally, they can be excellent solutions where increased connection stiffness is required, where fatigue critical connections are involved, or where advanced components provide specific performance or function (i.e. rockers, couplers, dissipaters, etc.).
If it is determined that custom castings offer the best design solution, then it will be critically important to work throughout the design process with a firm or manufacturer that can provide complete design or design-build services for custom cast steel components. Such a company will need to provide services that are not commonly performed by conventional architecture and engineering firms, namely, three-dimensional industrial design and modeling of cast elements, finite element stress analysis for the components, steel connection design, casting detailing, non-destructive examination specification writing, and in some cases, even destructive structural testing of full-scale components and assemblages. It will also be important that they are able to provide cast steel production and assessment with a full understanding of steel casting technologies. Foundries don't typically have the people on staff to undertake structural engineering and design work, since they are mostly staffed with process engineers and metallurgists who understand how to make the castings but not how to design buildings that use them. Instead, a company needs to be chosen that can work as part of the design team for custom cast steel components to ensure that they provide the desired aesthetic appearance, carry loads safely and efficiently, integrate with the structural steel framing of the building, are capable of being cast using best practices, and remain economical.
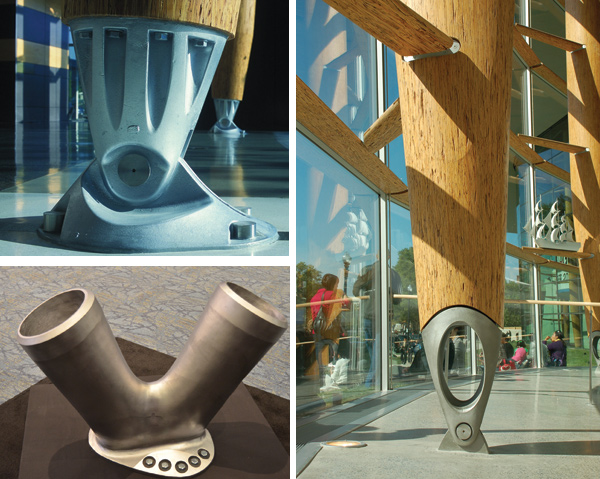
Photos courtesy of CAST CONNEX and Fast+Epp
Custom cast connectors are suitable for connecting to steel structural members or to other structural materials such as structural timber.
The first step in the process is to properly identify and understand the structural loading and flow of forces through the structural members in order to create structurally appropriate cast connections. This is where the three-dimensional computer modeling and structural analysis becomes important. By assessing the forces and capabilities of the steel, the shape and thicknesses of the castings can be optimized by reviewing alternatives that meet all of the design requirements of the project. This process also allows for elegant and sweeping forms that follow the natural flow of forces. As an alternative, the connection can be sculpted in different ways purely for aesthetic reasons while still being assessed for proper structural performance. Either way, the end result will be a designed connection that cleanly and smoothly carries the imposed loads while allowing full control of the final appearance.
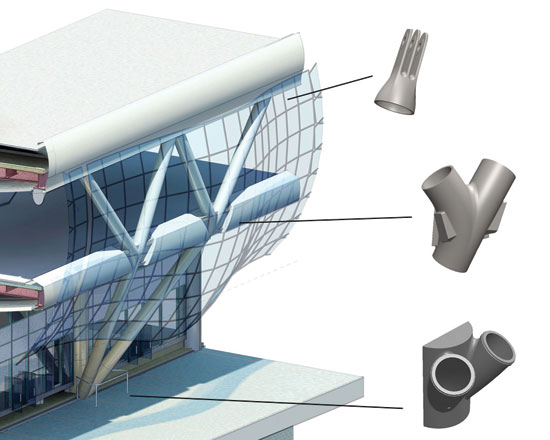
Photo courtesy of CAST CONNEX
Any given project may have a variety of custom cast connectors that need to be modeled and designed by a qualified casting engineer.
Once the preferred connection shape and size are finalized, the full industrial design and detailed engineering of the custom casting will need to be undertaken. The actual casting may include features that are needed for the casting or installation process such as fins or lifting lugs that are ultimately removed after the full structure is in place. This will tie directly into the engineering that goes on in the foundry to create the patterns and molds that will be used for the custom casting. Once all of those details are worked out, a cast of the “first article” needs to be undertaken to determine its full suitability and quality. First article castings are subjected to rigorous non-destructive (and sometimes even destructive) examination to prove out the production process. If anything is not up to par, then changes can be made to the pattern or the feeding and gating system for the casting to produce a casting that passes muster. If the first article is found to adequately meet specifications, then the original pattern becomes the basis for all subsequent castings.
By now it should be clear that there is some necessary lead time that needs to be built in to a design and construction schedule to allow for the full engineering, molding, and first article testing of custom cast products. Further, there will be some time needed to produce the quantity of custom castings that are ultimately needed for a particular design project. That means any given project needs to work within the overall production schedule of the selected foundry that will be providing the cast products. The overall actual production time will vary of course based on things like the size and complexity of the castings, the quantity needed, and the other schedule commitments of the foundry. Hence, all the more reason to engage with casting professionals earlier rather than later to assure that the connections can be made and shipped to the construction site when needed. In the end, the results will likely be very worthwhile, but proper planning and time scheduling will keep expectations in line and help maintain positive relationships between all parties.
Specifying Cast Steel Connections
Based on everything that we have covered thus far, you may have decided to use cast steel connections on a project because of an appreciation that standard steel fabrication may not or cannot achieve what casting can. You also understand that custom castings generally require a longer lead time than conventional fabrication and have allowed for that in the project schedule. While you may know all of this, you also need everyone working on the project to know it too. As a designer, the principal tool for communicating with the contractors and fabricators are the contract documents prepared by your firm. Drawings which show the castings with some general, overall dimensions and maybe some 3D images are appropriate to convey intent and make it clear to bidders that castings are required. But beyond that, the specifications will generally dictate the details of casting requirements.
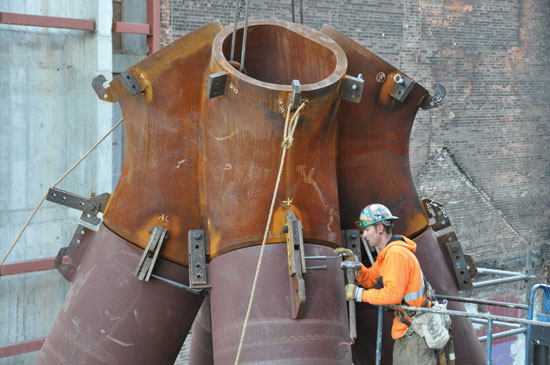
Photo courtesy of CAST CONNEX
Performance specifications are the primary means to communicate the design, fabrication, and installation requirements of cast connections to the construction team.
Since most architectural and general structural engineering offices don't have direct experience in casting design and production, either a specialized casting designer is added to the design team as discussed above, or performance specifications are used that delegate appropriate responsibilities to a suitably experienced party. Such specifications spell out the key architectural features and governing load-cases (i.e. the performance criteria) which must be met such that the casting designer can satisfy architectural, structural, and castability requirements, simultaneously. Including these items within the performance specification can help ensure that the design team and ultimately the client gets what is intended. It will allow the casting designer the flexibility (even creativity) in satisfying the architectural and structural requirements, but promote productive communication between all parties. Requirements for deliverables including a casting design report, shop drawing submittals, and production documentation (chemical and physical test reports for each cast heat and non-destructive examination reports for each casting produced) are also typically included in the performance specification. The goal of having these deliverables is to allow the casting designer the freedom to develop an economical casting design but to still allow the project architect and engineer to retain control over design intent.
The casting designer will thus be required to engineer the castings to meet these performance requirements and will prepare the required detailed casting specifications and shop drawings for review by the architect and structural engineer. An experienced casting designer typically assumes full engineering responsibility for the castings and may even procure the castings. Remember that foundries obviously have casting expertise but most will not assume design responsibility or assess whether a component they produce is fit for any specific purpose or use. Most foundries won't assist in the production of three-dimensional models or shop drawings, either.
A detailed casting specification prepared by an experienced casting design firm typically covers a number of key items including:
• Foundry qualifications in terms of capability and capacity to produce the type and size of castings being specified
• Quality control and assurance standards for production
• Metal material grade based on industry standards
• Non-destructive examination (NDE) requirements for both the first article and all subsequent production components
• Surface finish quality requirements
• Dimensional tolerances
• Machining requirements (if any) for the finished cast pieces
• Notes on handling and integration of the cast steel elements into the structural steel framing
Conclusion
Architects and engineers have the opportunity and freedom to create architecturally exposed steel structures that yield new aesthetics, exceptional performance, and economical buildings. Cast steel connections provide an exciting outlet for creativity in design and can be a key to achieving successful end results by helping to produce designs that are structurally adequate, architecturally appropriate, and readily constructed. By working with professionals in this field preferably in the design process but certainly in the construction process, choices can be made that result in economical yet elegant casting designs that enhance the full building.
Peter J. Arsenault, FAIA, NCARB, LEED AP, is a nationally known architect, sustainability consultant, technical writer, and continuing education presenter. www.linkedin.com/in/pjaarch
![]() |
CAST CONNEX is the leading supplier of cast steel components for use in buildings and bridges. Their components simplify the design and enhance the performance of structures. They take pride in collaborating in the creation of safer, innovative, and more beautiful built environments. www.castconnex.com |