Insulation Gets More Effective
Continuous insulation and the next generation of high-performance masonry walls
Continuing Education
Use the following learning objectives to focus your study while reading this month’s Continuing Education article.
Learning Objectives - After reading this article, you will be able to:
- Discuss the prevailing energy codes and how they treat insulation as a means of achieving energy efficiency in order to improve the integrity of a building.
- Explain the differences between cavity insulation and continuous insulation in terms of thermal bridging and contributing to overall energy conservation of a building.
- Describe the goals of an insulation material with regard to R-value, moisture management, air tightness, wind and fire resistance, aesthetic versatility, and other characteristics that protect the building users.
- Compare the characteristics of foam panel and insulated concrete masonry block systems and their ability to meet R-value targets and other aspects of an energy-efficient building envelope.
As a material or combination of materials, insulation of the building envelope helps keep cold air out and heat in during the winter, while keeping warm air out and cool air in during the summer to improve comfort and save energy. Insulation is widely considered the most effective way to improve the energy efficiency of a building, and can save significantly on heating and cooling costs. However, any time the insulating layer is interrupted, the effective R-value, or efficiency of the insulation, decreases. In view of this, national energy codes have moved beyond cavity insulation, encouraging the use of continuous insulation (CI) systems, which provide an uninterrupted insulation layer over an entire wall, not just in the wall cavities. Faced with code compliance and the pressing need to design for green building goals and save on energy costs, architects are turning to CI as an effective approach to eliminating segmented insulation with open gaps, blocking thermal bridging, and helping to improve thermal performance of the wall assembly. This article will discuss the requirements of the prevailing energy code in terms of continuous insulation and offer a comparative discussion on various options for achieving it in masonry construction.
Energy Codes—Where We Stand Now
According to the U.S. Energy Information Administration, the amount of energy used by buildings is nearly 40 percent of the total U.S. energy consumption, totaling some 40 quadrillion BTUs. In response to these numbers, the building industry has been adopting sustainable, resource-efficient practices that can drive more energy-efficient structures. In addition, various codes have emerged in an effort to decrease these energy usage figures, requiring designers to reconsider traditional systems and examine new approaches for their ability to meet ever-increasing energy performance goals.
The primary baseline energy code for private sector building is the International Energy Conservation Code (IECC). The primary energy-efficiency standard for buildings other than low-rise residential is ANSI/ASHRAE/IESNA Standard 90.1. The IECC is written by the International Code Council, a member-focused association dedicated to helping the building safety community and construction industry provide safe, sustainable, and affordable construction through the development of codes and standards used in the design, build, and compliance process. Most U.S. communities and many global markets choose the International Codes. The International Codes, or I-Codes, published by ICC, provide minimum safeguards for people at home, at school, and in the workplace and constitute a complete set of comprehensive, coordinated building safety and fire prevention codes. The IECC references several ASHRAE Standards, in particular the ASHRAE 90.1 for commercial building construction.
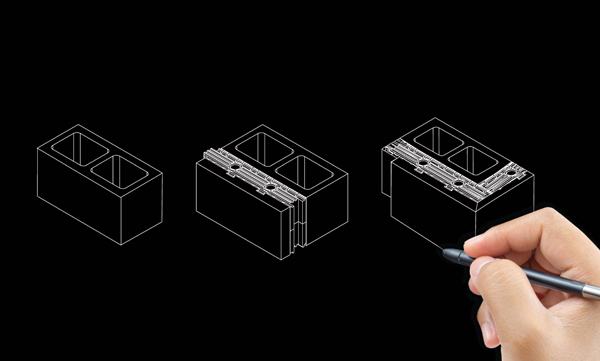
Image courtesy of Oldcastle® Architectural
Next-generation insulation systems are completely thermally broken, meeting or exceeding current energy codes.
The IECC may be only a model energy code, but it is written in mandatory, enforceable language, so that state and local jurisdictions can easily adopt it. When adopting and enforcing the code, states and local governments often make changes to reflect regional building practices, or state-specific energy-efficiency goals. This is important to consider as IECC codes and changes to the code are only enforceable when they are adopted at the state or local level. That is not to say that all states and localities adopt the codes immediately. As of 2014, the ICC reports that the IECC 2012 is in use or adopted in 47 states, the District of Columbia, the U.S. Virgin Islands, NYC, and Puerto Rico.
Every three years, the ICC publishes a new version of the IECC, upping the required energy efficiency of buildings by a substantial percentage, and heading toward a pronounced emphasis on building insulation and building envelope construction. In terms of meeting the IECC, there are three methods: the Prescriptive, Trade-off or System Performance, and Total Building Performance, with each subsequent method offering increased design flexibility and complexity. The prescriptive path, which requires building components to meet R-values listed in the tables, offers little flexibility. The performance path uses established software to measure compliance, providing less stringent requirements and more flexibility to trade off requirements. The whole building path requires even more complex software, allowing tradeoffs among envelope components, HVAC systems, and lighting. As this path analyzes a building's total energy use as opposed to requiring code-complaint individual components, it may become the most popular method as time goes on.
Continuous Insulation
Though not currently defined specifically in the ICC family of International Building Codes, CI is defined in ASHRAE 90.1 as: “Insulation that is continuous across all structural members without thermal bridges other than fasteners and service openings.”
The definition of fasteners is meant to include screws, bolts, nails, etc. Furring strips, clip angles, lintels, and other large connection details are excluded from the term “fasteners.” Many designers, contractors, and building officials are still not informed about this important aspect of CI. For example, masonry veneer wall construction typically employs steel relieving angles and steel lintels at window and door heads. These steel angles are usually fastened directly to the building structure, providing a significant thermal bridge from the interior of the building to the exterior. There are a number of solutions to this issue including welding the angles to standoffs at +/-4-feet-0-inch centers, which allows the CI to be installed behind the angles to minimize the effects of thermal bridging. There are also proprietary clip systems being marketed to perform this same function.
CI is found in various places in the 2012 IECC. Table C 402.2, for example, is a prescriptive table that lists all opaque (non-window) wall R-value requirements. Where CI is listed in this table, it is mandatory.
Why CI—CI vs. Cavity Insulation
The main purpose of insulation is to minimize the amount of heat which escapes or enters a building, a goal that is ever more important in the face of today's spiraling energy costs. Before discussing the comparative benefits of insulation, it is important to understand R-value. Generally, R-value, or resistance value, means the ability to withstand heat flow, and the higher the R-value, the more effective the insulation. For illustrative purposes, consider the fact that heat flows through an R-10 insulation twice as fast as that of an R-20 material. However, these are nominal R-values, the rated/labeled values of insulation products determined in laboratory testing. The R-value standard was developed exclusively to test small samples of insulation materials, and it constitutes insufficient information to rate the thermal performance of a wall, the reason being that these values do not take into account the effectiveness of the insulation in conjunction with framing members and other parts of the wall.
Effective R-values, on the other hand, represent the total resistance of the entire wall assembly—and the difference between nominal and effective R-values can be surprising. The discrepancy is due to the fact that R-value doesn't measure thermal bridges in the structural elements, which virtually channel heat flow through the wall; nor does it measure air movement, thermal mass, or moisture content, all of which can drive thermal performance. Thermal bridging is a particularly important factor in the equation. Beyond the potentially significant heat loss/heat gain that can occur, thermal bridging may also create condensation problems that jeopardize the wall assembly not only by reducing the R-value, but by permitting mold and compromising the service life of the entire wall assembly.
As can be seen in the illustration below, a typical insulated cavity wall may have the following elements: an interior gypsum wallboard, metal furring, concrete masonry backup, rigid insulation, and architectural concrete masonry veneer.
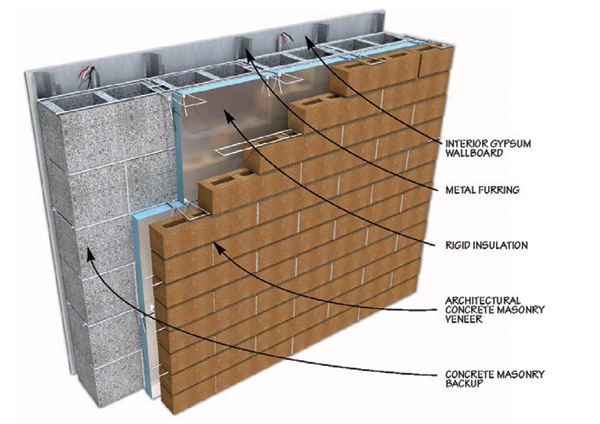
Image courtesy of Oldcastle® Architectural
Insulated cavity wall
But because the cavity insulation is installed between the studs, there will be gaps in the insulation that result in thermal bridges and potential moisture condensation. Many building experts have long considered cavity wall insulation to be inefficient. Limiting the thermal bridging will improve the thermal performance picture. A 1-inch sheet of rigid foam sheathing, for example, can nearly double the wall's effective R-value, improving thermal performance and decreasing associated heating costs.
That is the premise of CI, which runs continuously over structural members and is free of significant thermal bridging. It can be installed on the interior, exterior, or integral to any opaque surface of the building envelope. CI provides one of the most effective—some say, the only—way to comply with increasingly stringent energy codes, as it is able to block thermal bridging. Wrapping the exterior wall in a continuous layer of rigid foam improves high R-value in several ways. To begin with, it reduces the difference in temperature between the cavity and the stud, cutting heat loss and increasing the wall system's effective R-value. Further, CI has the effect of moving the dew point from the inner cavity to the outside wall, decreasing the potential of mold and mildew to grow inside the wall. If a drainage plain and a moisture barrier are added, CI can better forestall moisture intrusion and keep the wall system effective over a longer service life.
Insulation Options in a Wall Assembly
In addition to continuous thermal insulation, an effective wall assembly will provide moisture vapor control, water-resistive barrier, and air barrier, and be resistant to fire and extreme wind conditions. Insulation can play a role in all these characteristics. From interior furring and insulated cavities to foamed panel systems and next-generation insulated concrete masonry block systems, masonry construction offers diverse insulation options for energy-efficient wall systems. The relative performance of each insulation system should be examined not only in terms of its R-value, but in relation to the aforementioned goals of efficient wall assemblies as well as its potential for aesthetic effect, and the specific needs of the project.
Single Wythe Walls
A single wythe wall is a stone, brick, or concrete wall that is one masonry unit thick. Considered the most economical wall type, the single layer provides the structure, exterior surface finish, and, in some designs, interior surface finish. Single wythe walls are durable and inherently fire-proof with fire ratings up to 4 hours. Although the thermal mass and inherent R-values may be sufficient to meet code requirements, particularly in warmer climates, additional insulation may still be required. Rigid insulation inserts, foamed-in-place or loose-fill insulation can be applied to the interior or exterior of the unit. Furring strips can be added to the interior and allow for the addition of a finish material and accommodate additional insulation.
Alternatively, an exterior insulation and finishing system (EIF) can be added to the exterior. According to the definitions of the International Building Code and ASTM International, an EIFS is a non-load-bearing, exterior wall cladding system that consists of an insulation board attached either adhesively or mechanically, or both, to the substrate; an integrally reinforced base coat; and a textured protective finish coat. According to Building Science Digests BSD-146: EIFS, EIFS became very popular in the 1980s and experienced a significant number of serious failures, almost all related to rain penetration.
Early EIFS used a face-sealed approach. Drained EIFS are significantly different from face-sealed systems in that, by definition, they have a provision for drainage. Unlike face-sealed perfect barrier systems, such systems can be successfully used as an exterior cladding system in essentially all climates and exposures. Drainable EIFS are not subject to the same limitations of use as face-sealed or barrier systems. In fact, drainable EIFS are among the most robust and advanced moisture control assemblies available. EIFs comply with building codes that reference energy conservation through the CI.
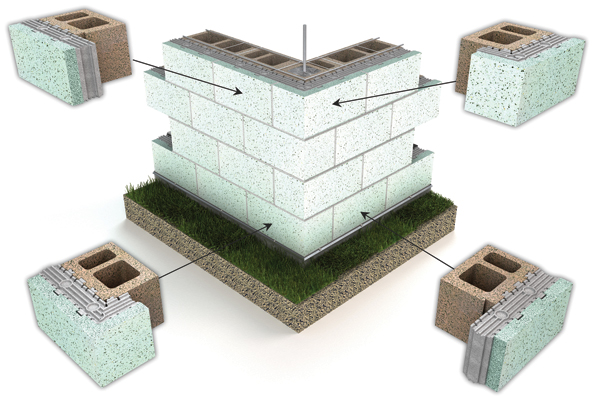
Image courtesy of Oldcastle® Architectural
An effective insulation option consists of a pre-assembled structural masonry unit, molded EPS insulation insert, and thin veneer face that is installed as a complete assembly.
In single wythe walls, R-values will depend on the density of the concrete, the number and height of the of webs, the depth of CMU as well as the type of insulation calculation method used. With the variety of concrete masonry units and insulation types and thicknesses, R-values from 5 to over 20 are possible. Rigid foam inserts will yield an R-value of 3 to 10, and injected foam or loose fill will boost the R-value from 4 to 20.
While single wythe walls can be a cost-effective solution when building goals include permanence and economy, it is important to note that single wythe walls do not have the redundancy of a traditional cavity wall, and water penetration is sometimes a concern. To achieve the weather resistance of a cavity wall, the single wythe wall must be very carefully detailed and built, with particular attention paid to flashing, base condition, joints, and coatings.
Foam Panel Systems
Far preferable in a number of respects are foam panel wall systems. Rigid foam has been a key driver of energy-efficient construction over the last few decades as it gives a significant boost to R-values of walls and roofs with minimal increases in thickness. Further, it covers the framing elements, decreasing and sometimes eliminating the thermal bridging that is characteristic of cavity insulation. Rigid foam insulation can be airtight if properly sealed and taped at seams; air can go around but not through this insulation.
Types of Foam
Code- and ASTM-compliant foam plastic CI sheathing materials are available with various characteristics and profiles, to meet specific project requirements, the main types being expanded polystyrene (EPS), extruded polystyrene (XPS), and polyisocyanurate (polyiso) foam, all produced under various trade names. Each type of product has different thermal properties and associated influence on required thickness and costs.
Expanded polystyrene (EPS) ASTM C578 is the most economical type of rigid foam and has an R-value of about R-4.0 per inch. Similar to the foam used for impact protective packaging, soil subgrade load-bearing blocks, and floation augmentation for boating and floating, EPS is one of the most widely used types of rigid foam. In successful use for many years in areas where moisture is a concern, EPS “breathes” so that moisture is diffused. It has been found to resist the growth of fungi and bacteria, and to maintain performance properties when exposed to moisture and/or water. EPS insulation is available in a variety of densities to suit project needs, and is frequently used in commercial buildings for roof and wall panel insulation. ASTM C578 provides performance properties on this type of foam insulation.
Extruded polystyrene (XPS) rigid foam is usually blue or pink in color, with a smooth plastic surface, and available in a wide range of thicknesses and edge profiles. The R-value is about 5 per inch. Used widely in residential construction, this type of rigid foam will not absorb water like polyiso and is stronger and more durable than expanded polystyrene, making it a versatile type of rigid foam. XPS falls between polyiso and expanded polystyrene in price.
Polyisocyanurate, or polyiso, foam has the highest R-value per inch (R-6.5 to R-6.8) of any rigid insulation, and is the most expensive. This type of rigid foam usually comes with a reflective foil facing on both sides, so it can also serve as a radiant barrier in some applications. It is used widely in commercial applications and increasingly in residential structures.
Foams themselves can be one of two types: open- or closed-cell. In general, the key difference between the two types is density, which has implications when used in insulation. As closed-cell foam is the denser of the two materials, it offers increased R-value per volume, increased resistance of water vapor transmission, and increased rigidity, providing superior structural integrity. A 1-inch layer of closed-cell foam provides roughly the equivalent insulation factor as a 2-inch layer of open-cell foam, making the former particularly advantageous in tight spaces as thinner layers of insulation can be used. Closed-cell foams are superior insulators: They are strong and act as structural reinforcement for the insulated surface whereas open-cell foams have little structural strength. Open-cell foams typically have R-values of 3 to 4 per inch vs. closed-cell foams' R-values of 5 to 8 per inch. Another key difference is porosity. Open-cell foam is porous, which means moisture, both water vapor and liquid water, can penetrate the insulation. Closed-cell foam, on the other hand, is non-porous, and thus not moisture-penetrable.
Foam Masonry Panel System
Relatively new to the market, the foam masonry panel systems provide CI; they consist of foam panels, stainless steel screws or anchors, masonry units, and mortar. Type S mortar can be used, which has the advantage of additives to achieve easier pumping, better bonding, flexibility, and dimensional stability. A variety of masonry units are available including durable stone, clay, and concrete brick with others under development. Masonry units are friction fit in the foam, with different types of units having different foam panels.
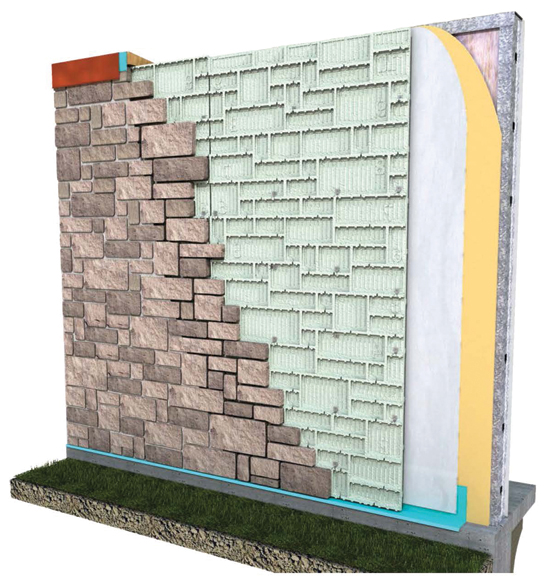
Image courtesy of Oldcastle® Architectural
In a foam panel system, foam is applied over sheathing, flashing, and one to two layers of a weather-resistant barrier. Foam panels offer the advantage of CI, water control, and multiple patterns of face material.
The foam is the key to the efficacy of the unit, adding good water management with drainage on both sides to take away any water that may infiltrate the wall and protect the structure from damage over its service life of high moisture exposure. R-values are high as well—9.1 Steady State and 13.6 including Thermal Mass. An STC of 51 and an NCMA TEK 13-1B sound transmission rating for concrete masonry walls means loud sounds are only faintly heard and occupants can enjoy their space in peace and quiet. Some foam systems have been proven to resist wind speeds of more than 110 mph according to ASTM E330 with no lasting deformation, which essentially eliminates the structural risk of damage experienced with lighter-weight veneers. Fire resistance criteria notably NFPA 285 and ASTM E119 assures that tested foam walls have successfully withstood one hour of exposure to temperatures of more than 1,700°F. Foam panel systems should meet the aforementioned criteria.
To install the panels, foam is applied over sheathing, flashing, and one to two layers of a weather-resistant barrier. Stainless steel anchors are used for wood, steel, or concrete structures. Screws are used for wood studs, self-tapping screws for metal studs, and tapcons for concrete or CMUs. Protrusions along the top of the panel help stones to fit snugly into the foam. Some patterns have 10 different stone types. Concrete brick generally comes in 4-inch by 5-inch lengths, with +/- 3.25 bricks per square foot. Some manufacturers enable installation via an easy “paint by numbers” template. Mortar is then applied via an injection gun. Architects should be aware that manufacturers are constantly coming out with new masonry units and improved features for the foam wall panels. New options include 40 percent larger stone units; stacked stone; thin brick applications in 4 x 8 x 16; larger units up to 12 by 24 inches; larger foam panels up to 4 by 4; and redesigned anchors.
Foam systems have achieved energy efficient results. In Beaver Dam, Wisconsin, a foam system was used for an apartment complex rehabilitation that required both aesthetic improvements and enhanced energy efficiency. The level of energy efficiency achieved qualified the project for funding from the U.S. Housing and Urban Development (HUD) Green Retrofit Program. After installation, engineers working for Wisconsin's Focus on Energy program discovered that a 20 percent reduction in air infiltration had occurred compared to previous measurements. The foam panel system was also used in the ReVISION House Orlando 2011. Before renovations, the ReVISION House was a typical Florida concrete block-style home; while it had a durable wall system able to withstand termites and hurricanes, the structure lacked quality insulation. Prior to renovation, the R-2.5 walls were a major contributor to both heating and cooling loads. The “before” walls led to loads of 6.8 MBTU to heating and 14 MBTU to cooling on an annual basis. After renovating, annual loads dropped to 1.9 MBTUH for heating, and 2.5 MBTUH for cooling: a reduction of nearly 80 percent.
It should be noted, however, that these foam systems are not traditional masonry units. Rather, they are an insulated panel system that can be anchored to the exterior of different building sub-structures. The insulated panels have drainage planes built into both the front and rear as well as molded pockets or profiles that allow the veneer units to be held in place while the joints are mortared and struck and so is able to offer the aesthetics of traditional masonry.
Insulated Concrete Masonry Block Systems
Another, more recently developed option is the insulated concrete masonry block system (ICMS). Unlike the aforementioned options, the ICMS is a masonry system that consists of a pre-assembled structural masonry unit, molded EPS insulation insert and thin veneer face that is installed as a complete assembly. In other words the ICMS is the wall itself, and it is 100 percent thermally broken, providing true thermal protection, rather than that expressed by a nominal R-value. The units typically have a load-bearing capability of an 8-inch structural block. Blocks and thin veneer face units produced with keyway profiles add stability to the assembly.
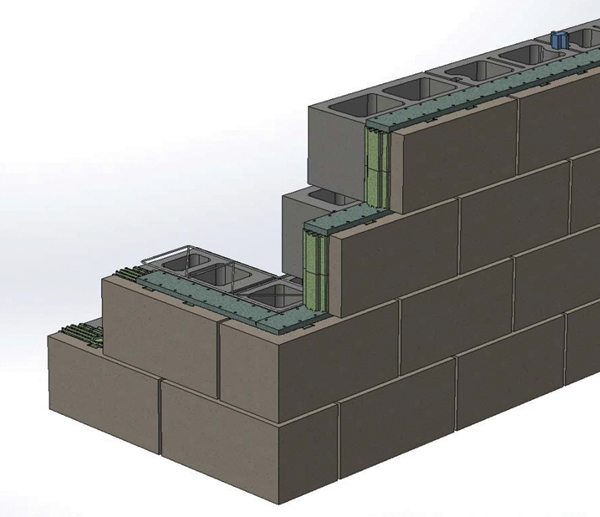
Image courtesy of Oldcastle® Architectural
Insulated masonry block systems form the wall, and were specifically designed to be code compliant and energy efficient.
The all-in-one systems were designed specifically to be code compliant and, as such, reinforce the appeal of masonry on a number of levels. More advanced ICMS offer continuous insulation at R-15, thus meeting or exceeding 2012 IECC requirements for Climate Zones 1 through Zones 7, which covers the continental U.S. This level of code compliance is essentially achieved by the type of insulation that is incorporated into the system. Some ICMS utilize proprietary EPS foam insulation material that is made with high-purity graphite integrated into the polymer matrix—a formula that has shown superior insulation performance when compared to conventional EPS. In this mix, small black beads of EPS containing particles of graphite and a blowing agent, which makes it expandable. Because graphite reflects and absorbs radiant energy, the material's thermal conductivity is reduced and its R-value increased. This type of foam insulation has shown a long-term stable R-value ranging from 4.5 – 4.9 per inch at 75°F, depending on density.
Compared to other polystyrene-based rigid foams and to polyisocyanurate rigid foam, this substance maintains more of its R-value when temperatures drop. As the temperatures decrease, the high-purity graphite integrated into the polymer matrix of the substance contributes more to slowing the flow of heat through the material. This type of foam is GreenGuard certified for Indoor Air Quality and is produced without fluorocarbons (CFC, HFC, HCFC) as an expansion agent, materials that can be harmful to the environment and have a negative effect on a structure's carbon footprint. Instead, an alternate substance known as pentane, a hydrocarbon of the methane series, is used during the manufacturing process as an expansion agent, with no ozone depletion potential and low global warming potential. It can be reclaimed for use in energy production for the manufacturing process.
This type of insulation provides the designer with flexibility as it is adaptable in size, shape and density, which eliminates the need to glue together multiple boards to achieve the desired insulation thickness—a characteristic that enables designers to achieve R-value targets in a thickness-constrained application. Monolithic 'boards' can be produced in thicknesses up to 48 inches and can be shape molded with corners and interlocking features. As codes evolve and R-value targets become ever more stringent, ICMS perhaps offer the best chance of easily adapting as a slight increase in insulation thickness can provide the necessary thermal performance. Many color and texture options are available. The thin face veneers are pre-assembled with the insulation insert and structural block, and architects can specify specific veneers to meet the desired aesthetic goals. Interior and exterior appearances can vary with, say, the inside wall being a gray tone and the exterior wall brown, or any other variation in color.
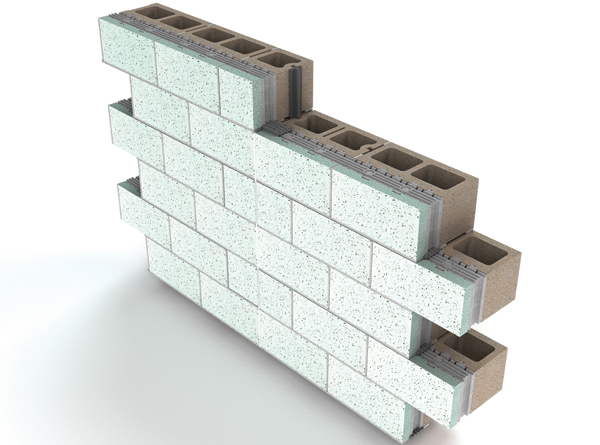
Image courtesy of Oldcastle® Architectural
The thin face veneers are pre-assembled with the insulation insert and structural block, and architects can specify specific veneers to meet the desired aesthetic goals.
ICMS with stainless steel ties offer protection in various extreme situations. Because it does not readily corrode, rust or stain with water as does ordinary steel, stainless steel anchors can be effective in salt water or coastal environments. In the event of a fire, the wall system's integrity is preserved by stainless steel ties that secure the thin veneer to the structural block. The latest EPS technologies incorporate fire retarders so that the ICMS does not contribute to flame spread. The stainless steel ties further provide wind-load resistance and protection against wind shear.
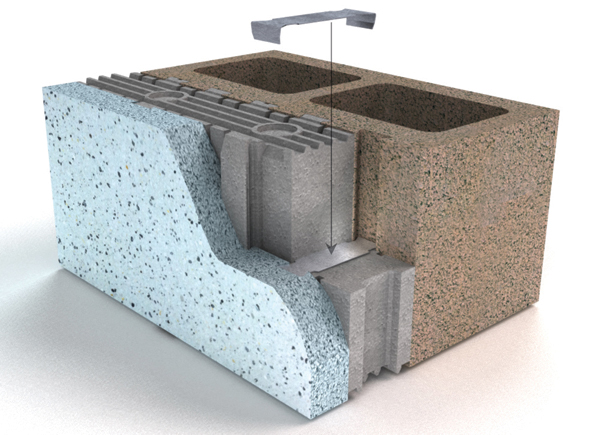
Image courtesy of Oldcastle® Architectural
In the event of a fire, the wall system’s integrity is preserved by stainless steel ties that secure the thin veneer to the structural block.
In terms of moisture management, some closed cell foams have a Class III Vapor Permeability rating of between 2.5 and 5.5 perms depending on thickness and density, meaning that this type of continuous insulation can more easily transport water vapor, reducing the likelihood of mold, mildew and structural damage. Architects should investigate the water absorption rate of the material relative to traditional insulation materials.
One critical area where ICMS have an advantage over other systems is installation. Proper installation is vital to the effective functioning of any wall assembly, and installing wall assemblies with numerous elements can be time-consuming, costly, and prone to error. As a single pass system, the ICMS affords simplified installation, eliminating the need for adding insulation and finishing materials, saving associated labor costs and improving accuracy.
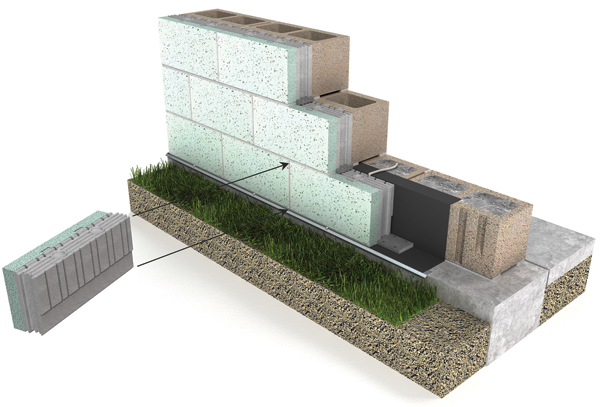
Image courtesy of Oldcastle® Architectural
Flashing detail of insulated concrete block masonry system
Insulation Gets More Effective
It goes without saying that energy codes and green building programs will continue their evolution prescribing ever stricter and more complete energy targets. R-values will increase, as will the demands of insulation within the wall system. Architects are in a position to further green building goals through the specification of effective insulation systems that decrease thermal loss and enable the building envelope to retard moisture intrusion and withstand fire and extreme wind conditions, while permitting a full range of aesthetic options and ease of installation. New all-in-one, or single pass systems, help meet all these goals, and represent a valuable addition to the designer's toolbox.
![]() |
Echelon is the consolidated brand for all masonry products and services of Oldcastle Architectural including Trenwyth® Architectural Masonry, Artisan Masonry Stone Veneers®, Quik-Brik® Concrete Masonry Units, Amerimix® Bagged Goods and a complete portfolio of Performance Upgrades. As a single source masonry portfolio solution, Echelon delivers consistent, reliable product manufactured locally at more than 170 locations and delivered by an unrivaled logistics network. For more information, call (844) 495-8211 or visit EchelonMasonry.com |