Specifying a Safe Dock Lift
A correctly specified dock lift helps ensure safe, efficient and economical loading and unloading of goods
Continuing Education
Use the following learning objectives to focus your study while reading this month’s Continuing Education article.
Learning Objectives - After reading this article, you will be able to:
- Identify the comparative advantages of using a dock lift to move goods from one level to another.
- Describe the different factors to be considered when specifying a dock lift.
- Explain how undersizing a dock lift creates a potentially dangerous situation.
- Evaluate different types of dock lifts on the market in terms of how they meet a building’s loading and unloading requirements.
Specifying an appropriate dock lift is not going to earn a design award. But specifying the wrong dock lift may add thousands of dollars in reconstruction costs, create injury-prone situations and result in a painful round of embarrassed finger pointing that will ultimately reflect on the design firm’s credibility. One instance, where a new dock lift for a museum was too small to unload large artwork, did just that.
As one of the last details to be attended to, some designers when pressed for time, might simply reach for the most recent job that needed a dock lift and copy specifications without checking the requirements of the current project or consulting with a dock lift manufacturer. This can result in oversized, more expensive or, more usually, undersized dangerous equipment. Writing correct specifications for the right dock lift is therefore critical, as is remembering to include dock and loading facilities in the first place. (One university art gallery on the East Coast is unable to exhibit large sculptures because the design team neglected both dock and access service doors.)
What Are Dock Lifts?
Dock lifts are a type of scissors lift with a large platform. They are used primarily to unload material from trucks and transfer it to a dock or to the ground. Their vertical range of travel is generally just under 5 ft. Dock lifts are used for any loading dock situation. They are installed outside a building, inside a building, in basements and even in upper floors. They are used in healthcare facilities, hospitals, office buildings, postal facilities, retail stores, schools, restaurants, supermarkets, manufacturing plants, museums, high-rise apartment buildings and anywhere that trucks arrive to be loaded or unloaded. A dock lift is needed if a building has no dock, or if the dock is too high or too low for material to be wheeled directly into a building. They are the only type of equipment that can reach from ground level to all sizes of trucks ranging from low-step vans to large refrigerated trucks. There is no vehicle size that dock lifts cannot service.
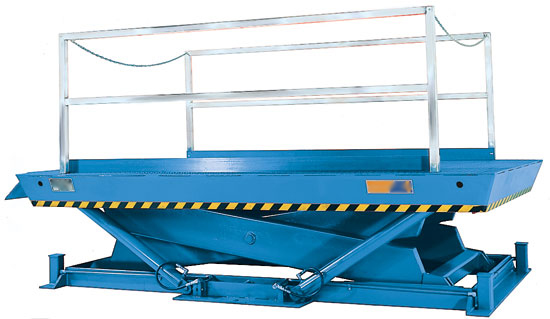
Photo courtesy of Advance Lifts®
A large-size dock lift can service any height of vehicle and is sized to handle any mobile material handling equipment.
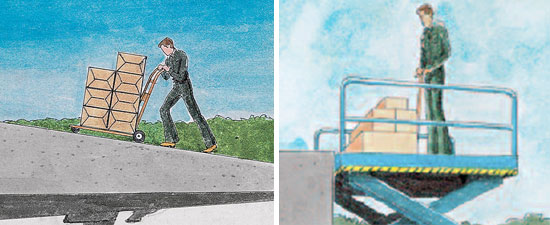
Drawings courtesy of Advance Lifts®
Concrete ramps used for unloading goods take up valuable real estate, are often steep and have safety issues (left). A dock lift (right) allows goods to be moved on the level.
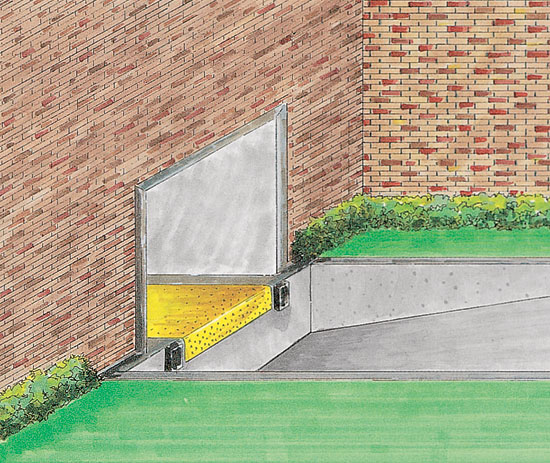
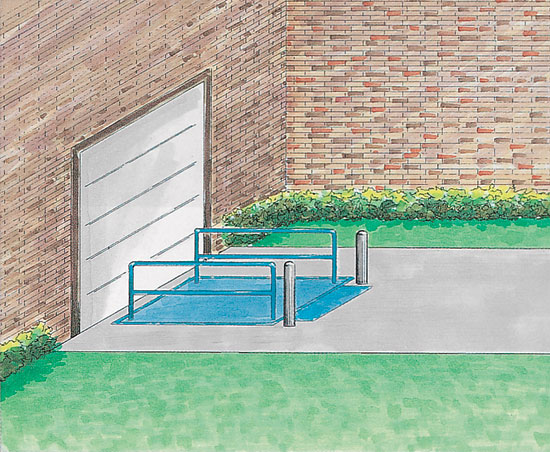
Drawings courtesy of Advance Lifts®
Truck wells (top) accumulate snow, water and trash, are expensive to install and serve only a single height truck. A dock lift (bottom) “disappears” when closed.
Dock Lift Alternatives
There are other ways of moving goods from one level to another.
Truck and dock levelers. A truck leveler installed in a pit will raise a truck to match the height of the dock. A truck leveler on the ground will do the same thing. Their drawbacks are that truck levelers have a limited range up to 36 in. and that they require a dock.
A dock leveler is mounted in a dock and is typically capable of a working range of 8 in. for a total of distance, up and down, of 16 in. But a dock leveler is unsafe at its maximum range of 16 in., which means that its useful range is a total of 8 in. (4 in. up and 4 in. down). A dock leveler installed in a 48-in. dock can therefore usefully service only a limited range of trucks.
Truck well. A truck well that effectively lowers the truck level is another option. But a truck well serves only a single truck height, will accumulate snow, water and trash, and is expensive to install.
Concrete ramp. Another solution is placing a concrete ramp between the truck and the dock or ground. This can create safety issues, especially if the ramp is steep.
Advantages of Dock Lifts
To summarize the advantages of dock lifts:
* With its typical 58 to 60-in. travel range, a dock lift can service all trucks whose bed heights vary from 21 in. to 58 in. Dock levelers or ramps cannot handle this wide range of vehicles.
* Level unloading from the bed of a truck is safer than any other loading or unloading alternative such as a concrete ramp.
* They replace expensive-to-install truck wells that hold snow, water and trash.
* They are the only type of equipment to reach from the ground level to all truck bed heights of vehicles ranging from vans and pick-ups to city delivery trucks and semi trailer trucks. Levelers have a limited vertical range.
* They guarantee that all vehicles can be accommodated at the dock.
* For retailers: A dock lift can save one or two hours of slow hand unloading. In addition to the obvious labor savings, the capital savings from better truck turnaround times can yield two to three-year paybacks on the cost of the dock lift.
* For warehouses and manufacturing buildings: Bottlenecks are compounded because everything passes over the docks twice, when they are received and when they are shipped. Although most of the traffic is concentrated in semi trailer trucks, vehicles of lower loading heights will show up often. In those cases a dock lift becomes very valuable.
* For hospitals, office buildings and institutional buildings: The widest range of delivery vehicles visit these sites. Therefore the universal service range of dock lift makes a logical choice.
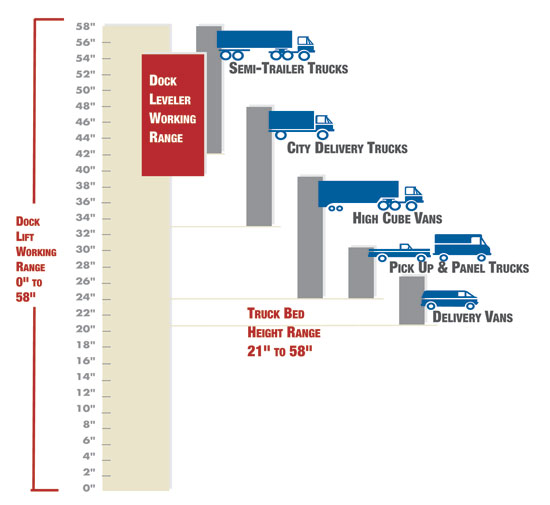
Image courtesy of Advance Lifts®
A typical dock lift working range is from zero to 60 in. and can service a truck bed height range of 21 in. to 58 in. (the maximum truck bed height). A dock leveler installed at a 48-in. dock can only service a limited range of trucks.
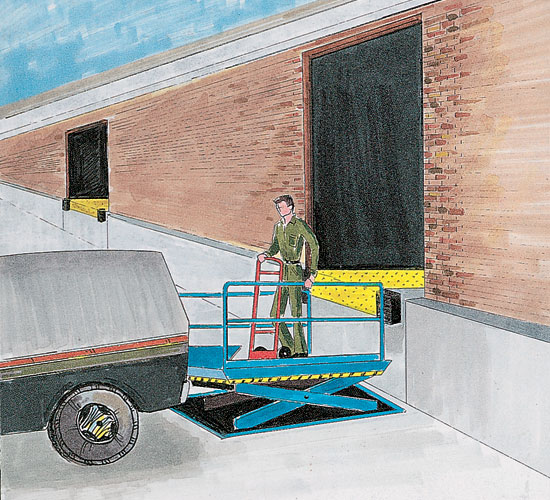
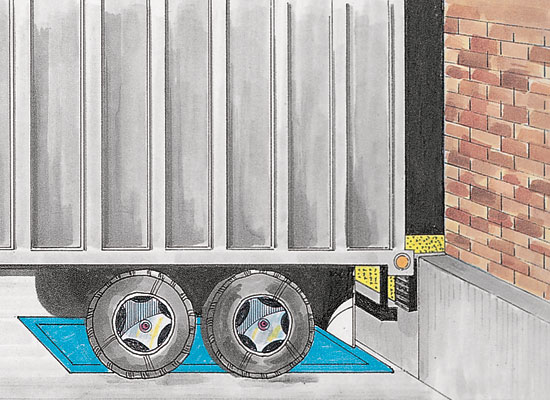
Use of dock lift at a raised concrete dock.
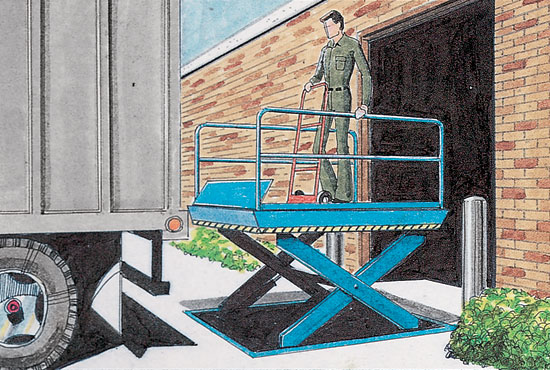
Drawings courtesy of Advance Lifts®
Uses of dock lift at a ground-level building.
Selecting a Dock Lift
A number of factors must be considered when selecting an appropriate dock lift. These considerations include whether the equipment should be on top of the ground or a pit-mounted recessed lift; the appropriate platform size; lifting and axle rating capacities; power units and controls; bridges; and other options. All factors are important, but platform size and capacities are particularly critical because they directly impact the safety of operating the dock.
Top of the Ground Lifts
These units can be mounted on any flat concrete slab and require no pit work. If mounted on blacktop, they will sink during the summer. These models cannot be installed in pits because their lowered height does not permit the addition of the 8-in. bevel toe guards required by ANSI for pit-mounted lifts.
The advantages of not installing a pit include cost savings and avoiding drainage issues and potential interference with underground utilities. In addition, if the unit needs to be moved later, it is an easy matter to unbolt the unit and move it with no pit to fill in. Some units have been in continuous service for 35 years.
Top of ground units have ramps that transition loads from the platform to ground level which is no effort for off-loading operations, but can be tiring if heavy loads must be pushed up a ramp for loading onto a truck. Top of the ground units can offer easy dock to ground access if the approach ramps are shortened and the units mounted immediately adjacent to the dock.
For typical models, capacities range from 4,000 lb up to 15,000 lb and platform sizes range from 6 ft x 6 ft up to 8 ft x 12 ft.
The cost of top of ground units is always higher than recessed units. However, if the cost of pit construction is added to the equipment prices, top of ground units can be competitive.
Recessed or Pit-Mounted Lifts
Pit-mounted dock lifts are installed in a concrete pit in the ground or a pit on top of a raised concrete dock. They can also be installed on top of the ground, but they require a long approach ramp. Equipment costs are less expensive than top of ground lifts.
Their biggest advantage is that these units are mounted flush with surrounding surfaces so they do not present an obstacle to drive-over traffic. This is especially important if the unit is being mounted in a doorway. Recessed units offer level loading both at ground level and at truck height. If recessed units are mounted within the face of a dock, they can provide easy dock to ground access. As noted above, if the approach ramps are shortened and units are mounted immediately adjacent to the dock, top of the ground units can offer the same easy dock to ground access.
Standard capacities for typical models of recessed units range up to 20,000 lb. The general rule of thumb for estimating the cost to install a pit-mounted dock lift is to add 50 percent to the price of the lift. This covers the cost of the pit, electrical work, mechanical installation, freight and taxes. If a lift costs $10,000.00, the total cost for everything would be about $15,000.00, including the lift.
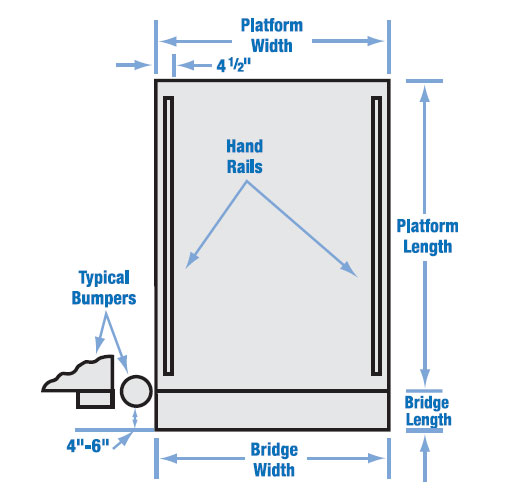
Drawing courtesy of Advance Lifts®
Anatomy of a dock lift.
Platform Size
The platform size is primarily determined by the type of transport equipment that will be used to load or unload trucks. Undersized platforms with not enough space for the operator can create an unsafe situation.
Platform width: Equals the width of the widest load plus 12 in. minimum for operating clearance including hand rails.
* The minimum suggested platform width is 6 ft.
* Guardrails use about 8 in. of useable platform width on most models.
* There should be at least 4 in. of clearance on each side of the widest load, such as a 48-in.-wide pallet, for ease of maneuvering.
* In some cases the loads may be wider and some users prefer to unload two pallets side by side (the most popular wooden pallet is 40 in. wide so that two can be put in a truck side by side). In these cases, 7-ft and 8-ft-wide platforms should be specified.
* Cushion tire fork trucks to 8,000-lb capacity are generally less than 48 in. wide.
* Pneumatic tire fork trucks to 8,000-lb capacity are generally less than 60 in. wide.
Platform length: Equals the length of the longest load plus the length of any material handling equipment which may project beyond the load plus room for the operator, if one is required.
*If the loads are four-wheeled carts or baskets, or the loading equipment is limited to two-wheeled hand carts, a 6-ft platform length is sufficient.
• Although a 7-ft-long platform is the minimum requirement for loads transferred via manual pallet jacks, an 8-ft-long platform is highly recommended and is the industry standard.
• Powered pallet jacks work best with 10-ft lengths in order to comfortably fit the load, powered pallet jacks and operator all in line.
• A 12-ft length should be used for loads transferred via sit-down rider fork trucks since they are much longer.
• Powered pallet jacks, or straddle stackers, that are powered by battery or electric motor also fit well on 10-ft-long platforms.
The sizes mentioned above cover almost all applications and are mostly available as typical standard offerings in both top of ground and recessed styles of lifts. Unusual loads may require custom designed units with platform widths of 10 ft or 12 ft and platform lengths of up to 65 ft. Examples of unusual loads include large-sized artwork for museums and air cargo containers. If a client has special requirements, design professionals are advised to consult with a full-service supplier.
Bridges
The size of the bridge is dictated by the gap from the lift to the back of the truck bed. This is determined by the location of the bumpers or bollards that are used to stop the truck’s rearward progress toward the lift. When lifts are located inside of buildings with a wall between the lift and the truck, the bridge can rest against a wear strip on the wall and automatically reach into the truck as the lift is elevated and retract as the lift is lowered. These bridges are typically very long, but because no one needs to handle them, the extra weight is not a concern.
Bridge width: 72 in. is the maximum recommended width. The reason for the 72 in. is that trucks rarely back up perfectly centered on the dock. If the truck has a roll-up door and the bridge is wider than 72 in., the bridge can hit the framework on the trailer and prevent access to the truck.
Bridge length: The bridge should be long enough to project 4-6 in. beyond any truck bumpers to provide adequate purchase on the truck bed. 12 in. is generally the minimum recommended length.
Bridge weight: This is dependent on both length and capacity. Generally, manually operated bridge weight is a concern when bridges reach 24 in. or longer. Options to mitigate bridge weight include splitting the bridges into two sections, aluminum bridge plates and hydraulically operated bridges with push button controls.
Capacities
Capacities relating to dock lifts include lifting capacity, axle rating capacity and roll over capacity. See sidebar Calculating Lift and Axle Capacities.
Lifting capacity. Once a platform size has been determined, the following weights are added together to derive the lifting capacity: the maximum weight of goods being transferred, the weight of the transport equipment and the weight of an operator.
Axle rating capacity. While lifting capacity is the more significant specification, it is useful to understand the purpose behind manufacturers citing of axle rating capacities.
The axle capacity is the amount of weight placed on a lift as the load, transport vehicle and operator enter the lift. Because most transport equipment have four wheels and two axles (an exception is a hand cart with a single set of wheels), it would be reasonable to assume that the load pressure on the lift is evenly distributed when the transport equipment moves onto the lift. But the payload weight of most powered transport equipment is not evenly distributed (see “X” chart in sidebar Calculating Lifting and Axle Capacities).
This results in higher edge loading over the ends of the lift when the axle with the heavier load is rolling on and off. Dock lifts therefore have to have axle ratings that serve the heavier axle load.
The axle loads on manually propelled carts and pallet jacks are too light to be of concern. Manual pallet jacks divide payload weight evenly between two axles. But powered pallet jacks and straddle stackers, which can move heavier loads than manual equipment, often concentrate 60 percent of the combined payload and equipment weight on their rear axles. Fork trucks usually concentrate 80 percent of the maximum payload plus fork truck weight on the front axle; but some unusual trucks may run as high as 90 percent concentration on the front axle.
Most manufacturers have appropriate end load axle ratings for corresponding maximum lifting capacities. But specifiers should be aware that such ratings can be marginal if unusual equipment is used and/or if an application requires traveling over the side of the lift in any position other than the fully lowered position. It is wise to compare the axle loads produced by the actual equipment specified—particularly small fork trucks, see below—versus the rating of the dock lifts.
Roll over capacity. Roll over (or drive over) capacity applies only to recessed units. It refers to the maximum axle load allowable for vehicles driving over a fully lowered lift. Most recessed dock lifts are rated for 10,000-lb axle load slow speed drive over. This is usually more than adequate because of state mandated limits on truck axle loads. However, large specialty vehicles and high-capacity fork trucks with small hard wheels can exceed these limits. In these cases, the lift manufacturer should be notified so the lifts can be modified to accommodate larger loads by installing thicker deck plates and other forms of reinforcement. An example of an extra-large load is a truck that picks up and drops off dumpsters. A large full dumpster can weigh 30-40,000 lb and has two sets of very small steel wheels; these wheels present very high compact axle loads.
Power Units and Controls
The up/down controls must be controlled by the operator riding on the lift. Any other scenario is a sure recipe for an accident. Standard controls for most companies are National Electrical Manufacturers Association, NEMA 4 pushbuttons. (NEMA 4 enclosures, used in many applications where an occasional washdown occurs, are gasketed and the door is clamped for maximum sealing.) These are usually mounted on straight cords or coil cords. For security options the cords may be made longer so that they can be connected to boxes inside of a secure building or mounted with twist lock plugs so they may be stored in secure areas until needed.
In other instances the hand-held controls are replaced with key lock pushbuttons that are mounted on the platforms. Some retail chains specify that all the keys in their system are the same. Limit switches may be added to cause the lift to stop at fixed dock heights. Power units on top of ground units are usually mounted on the lifts and covered with weather protection. Recessed lifts typically have remote power units that are mounted on the inside of buildings; weather covers can be ordered for outdoor mounting. Oil immersion heaters are an important option for power units that will be exposed to cold winter outdoor temperatures.
Other Options
Half a dozen standard colors are typically available at no extra charge. Additional options can include special paint finishes, special platform surfaces, wheel chocks, gates and so forth.
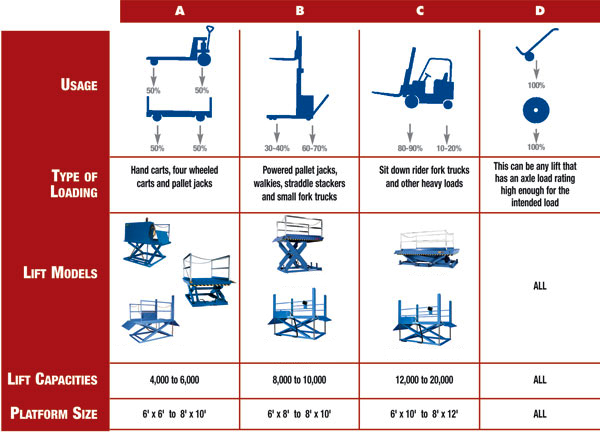
Chart courtesy of Advance Lifts®
Different types of loading equipment and their lift capacities determine which dock lift model is most suitable.
Lift Models
There are a number of dock lift models on the market that will handle lifting equipment in categories A though D.
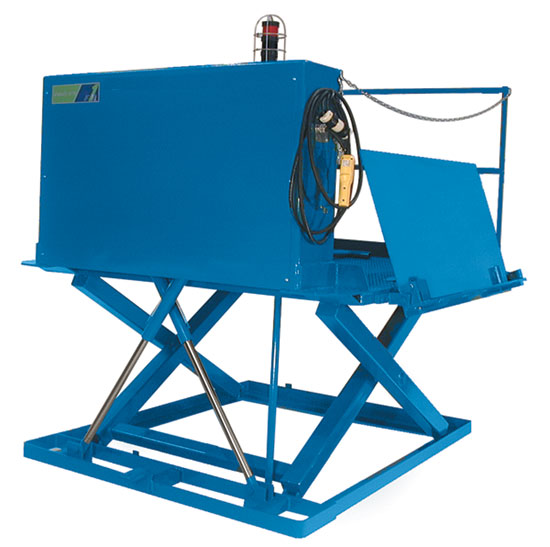
Photo courtesy of Advance Lifts®
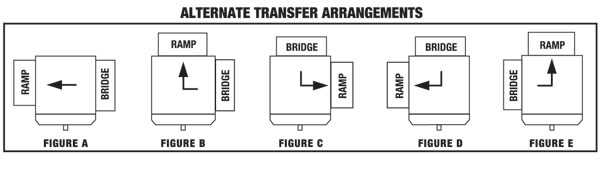
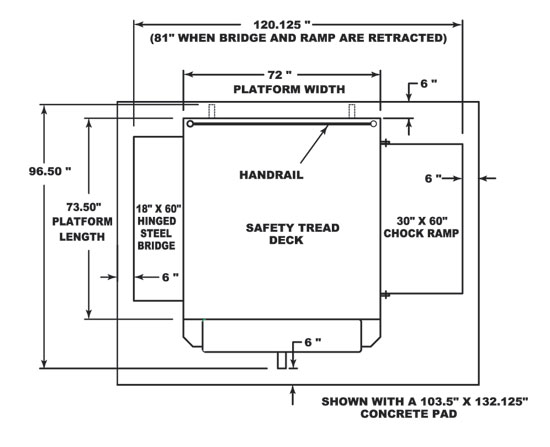
Images courtesy of Advance Lifts®
Basic instant dock: plan view and alternate configurations of the bridge and ramp.
Top of Ground Instant Dock Lift Models for Category A Lifting Equipment
Instant dock lifts are designed for the use of Category A light equipment such as hand carts, four-wheeled carts and pallet jacks. They simply require positioning and plugging into a power receptacle. When the units are raised, the ramps become wheel chocks that prevent carts from rolling off of the platforms.
The pull back chain on the hinged bridge allows the operator to pull the bridge back and secure it while the unit is being lowered, without stepping around the load. Wheel and dolly transport sets are typically standard on 5,000-lb and under units and allow limited portability on smooth concrete.
Lift capacities range from 4,000 to 6,000 lb. The dock lift platform size should be 6 ft x 6 ft to 8 ft x 10 ft.
* Typically all models are equipped with a hinged bridge that has a pull back chain.
* All models have a combination approach ramp, wheel chock.

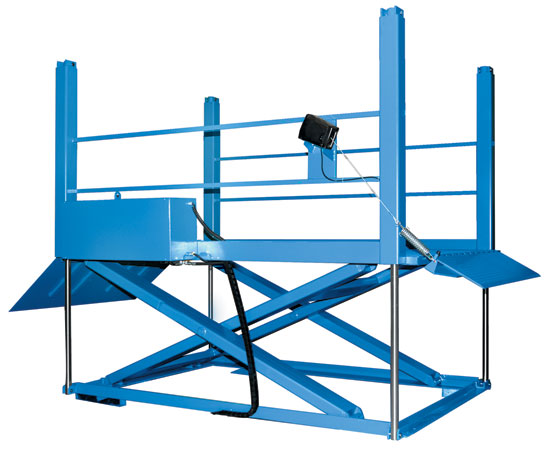
Photos courtesy of Advance Lifts®
Top of ground instant dock lift for heavier Category B lifting equipment is set on concrete pad.
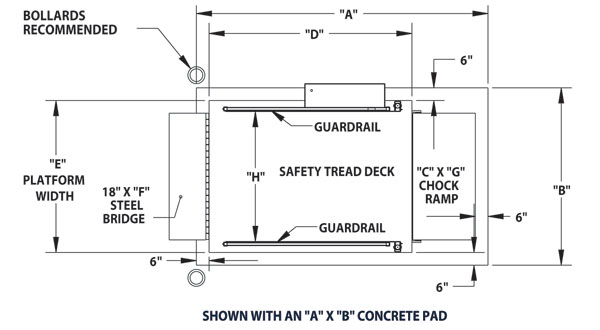
Diagram courtesy of Advance Lifts®
Bollards are recommended for the typical installation of dock lifts on a concrete pad.
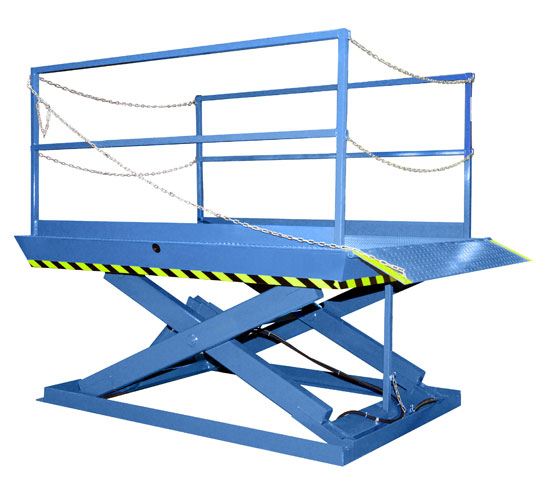
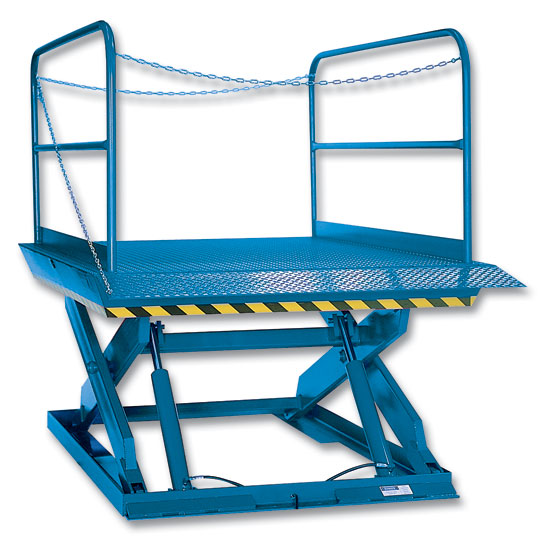
Photos courtesy of Advance Lifts®
Examples of disappearing dock lifts that are set into a pit.
Disappearing Dock Lift
Disappearing dock lifts offer numerous advantages and come in several sizes.
Smaller size. Set into a pit and suited to handle pallet jacks, four-wheel carts and dolly trucks, smaller-sized disappearing dock lifts are the most in demand. They are also used for dock to ground access. They are typically equipped with a hinged bridge with a pull back chain.
For decades, the most popular disappearing dock fitted a 10-in. pit, which was easy to build and afforded crush space between the bottom of the bevel toe guard and the bottom of the pit for any debris that may fall into the pit. Now there is an overall industry trend for 8-in. pits—one reason being the avoidance of shallow run utilities.
Medium size. Medium-sized disappearing dock lifts handle pallet jacks, powered pallet jacks, straddle stackers and small fork trucks. They too may be used for dock to ground access.
If the intended use of this equipment includes small fork trucks, specifiers are advised to calculate the axle loading of the fork truck and compare it to the axle load limits provided by the manufacturer.
Largest size. Largest-sized disappearing dock lifts are sized to handle sit-down rider fork trucks and any mobile material. They also provide dock to ground access.
One model has cylinders in direct thrust to all four platform corners, which provides maximum rigidity. This design approach for heavy fork truck applications eliminates the spring board effect of platform overhang on lifting scissors in the raised position. When watching a fork truck pass onto the lift from a semi trailer, an observer will notice an inch or more of vertical movement of the trailer and no discernable movement of the lift. The units are plumbed for anti-interflow between cylinders when the unit is at rest.
Specifying the Dock Lift
One useful first step is for design professionals to consult with a dock lift manufacturer to discuss the particular needs of the project and specification details. Specifications required include:
• Model Number
• Rated Capacity: Provide lifting capacity of not less than ______ lb with ______ lb axle load at the ends and ______ lb axle load at the sides.
• Travel Speed: Provide a nominal raising speed of _____ fpm.
• Platform Size: ______inches wide by ______ inches long.
Conformance to ANSI, IBC and UL
ANSI. Safety requirements for industrial scissors lifts are covered by ANSI MH29.1-2012. Specifiers should note that the dock lift manufacturers cite this ANSI number and not ANSI MH30, which covers levelers.
IBC. The International Building Code now recognizes the ANSI MH29.1-2012 code and will be included in the 2015 version of IBC.
UL. Specifiers should note if the entire controller assembly is covered with a UL label, or if UL approval is for electrical components only.
Manufacturer Support
Clients are better served if the manufacturer has nationwide distribution, installation and service systems. If the production facilities use U.S.-made components and are vertically integrated, there is the added benefit of no long wait for part replacements.
Warranty
A typical warranty is two years of free replacement or repair of any defective parts, material or workmanship on new equipment, including electrical and hydraulic components. Defective structure may be replaced or repaired free for a period of 10 years.
Conclusion
A correctly sized building dock lift is critical to the efficient and safe loading and unloading of materials. An incorrectly sized dock lift can create injury-prone situations and cost many thousands of dollars for reconstruction. With a vertical range of travel that is generally under 5 ft, dock lifts are the only type of equipment that can reach from ground level to all sizes of trucks. Design professionals have the choice of several types and sizes of lifts depending upon load and lifting capacities required. In addition to becoming familiar with the different factors to be considered when specifying a dock lift, it is suggested that they consult a lift manufacturer regarding particular installations.
![]() |
Advance Lifts® was founded in 1974 and quickly became the leading dock lift manufacturer in the country. We have maintained this position through innovative design, quick deliveries and superior service. Our product lines have expanded to include production lift tables, mezzanine lifts, and work access platform lifts. www.advancelifts.com. |