Cover Boards for Low-Slope Roofing Systems
Resist fire, wind uplift, impact and hail, moisture, mold and foot traffic by specifying the best cover board for the project
Continuing Education
Use the following learning objectives to focus your study while reading this month’s Continuing Education article.
Learning Objectives - After reading this article, you will be able to:
- Discuss durability, fire resistance and energy efficiency benefits to using a cover board in the design of a low-slope roofing system.
- Assess the external factors impacting the long-term performance and energy efficiency of a commercial roof system.
- Compare the different types of cover boards available and identify which type to use on various low-slope roofing systems to prevent moisture intrusion, mold, wind uplift and other external factors.
- Explain the pros and cons of various cover boards to help prevent threats to the roof and occupant wellbeing from fire, moisture, wind, sound intrusion and foot traffic.
A well-designed building is only as durable as the roof that protects it. Without a properly designed, specified, installed and maintained roof, the building below it will suffer. The reputations of the building professionals involved will also suffer. For a relatively minor investment, roofing cover boards solve many issues that cause damage to a roof during installation and into the warranty period.
Potentially negative forces on a roof include fire, wind uplift, impact and hail, moisture, mold, sound intrusion and foot traffic.
Low-slope and flat roofs endure more additional stresses than ever before, from unpredictable weather events, to increased usage for photovoltaic, staging for large HVAC equipment and the workers who install them, to a growing trend toward “green roofs.”
“The roof is a commercial building’s first line of defense from natural hazards such as wind, rain, fire, hail, ice, snow, and extreme heat.,” states the Insurance Institute for Business & Home Safety. “It is also the most vulnerable part of your building.”i
In this article, we’ll discuss cover boards as part of a well-designed, smartly specified, properly installed low-slope roofing system. We’ll talk about where a cover board fits into the whole design, the different types of roofing systems, the different types of cover boards, and which boards perform best in which applications.
Overview of Low-slope Roofing Systems
A roof is not just one element; it is an assembly, where all components perform together.
The typical low-slope roof assembly consists of the following components:
- Structural roof deck — steel, concrete or wood.
- Thermal barrier (if applicable).
- Insulation, including such rigid foam types as polyisocyanurate (ISO), expanded polystyrene (EPS) and extruded polystyrene (XPS).
- Fasteners and/or adhesives, including mechanical fasteners, low-rise adhesives, rock ballast or concrete pavers, hot asphalt or cold-applied liquid adhesives.
- Cover Board.
- Membrane system, with types including single ply systems such as thermoplastic membranes (TPO, PVC) and thermoset membranes (EPDM). Also, there are asphalt-based systems, such as B.U.R. (built up roofing), or fluid applied, and polymer-modified bitumen. The latter are accomplished with torch (APP) or mop (SBS). Another type is spray polyurethane foam.
- Roof covering such as rock ballast, concrete pavers, coatings, etc. (if applicable).
In simplest terms, the cover board goes on top of the insulation and below the membrane.
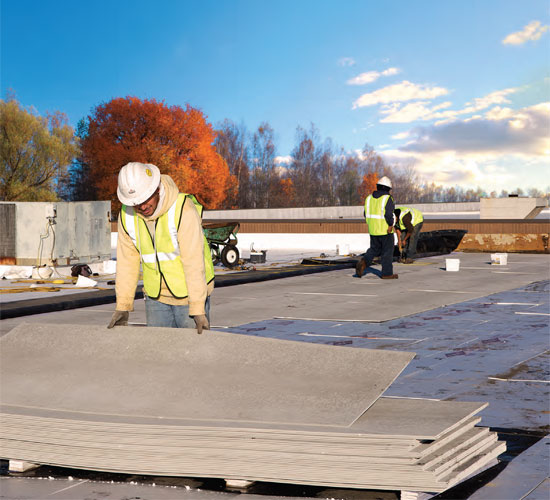
Photo courtesy of National Gypsum®
For a relatively small cost, roofing cover board protect the roofing insulation and membrane from the negative forces of fire, wind uplift, impact and hail, moisture, sound intrusion and foot traffic. Above, workers lay out 1/4" glass mat roof board over high density poly ISO. Workers in the background mechanically fasten the assembly to the roof deck with plates and long fasteners.
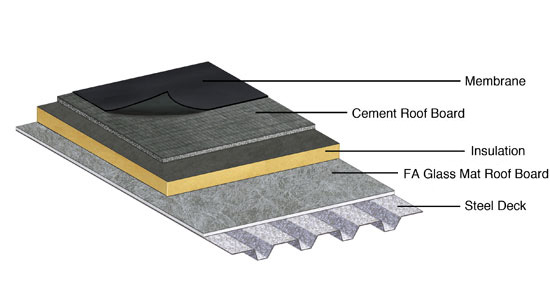
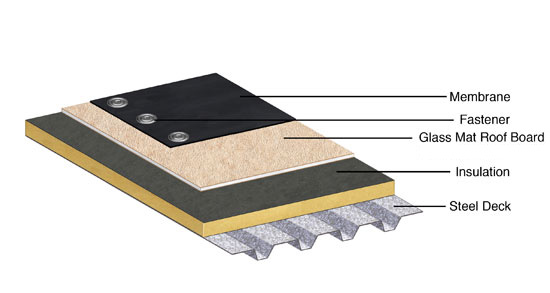
Images courtesy of National Gypsum®
A roof is not a material or a product; it is an assembly.
Why a Cover Board Matters
The advantages of including a cover board in a low-slope roofing assembly are numerous and well documented.
Cover boards provide a smooth surface on which to install a new roof membrane. Gypsum- and cement-based cover boards, in particular, can improve fire code ratings as part of the assembly. Cover boards break “cold joints” in roof systems having a single layer of insulation. Cover boards minimize damage to insulation caused by foot traffic (service) and/or damage caused during the construction of the roof system (power carts, etc.). Damage can be caused by the roofing trade or other trades working on the roof (such as HVAC crew, plumbers, carpenters, and others).
In addition, cover boards help protect against damage caused by storms or hail impact, and they eliminate most potential issues arising from polyisocyanurate insulation facer delamination. They can increase wind uplift ratings as part of the assembly. And some cover boards, such as gypsum-based cover boards, act as a thermal barrier to help prevent outside fire from transferring to the interior of the building. Two layers of gypsum (as a thermal barrier and cover board) improve performance even more.
Recommendation by the National Roof Contractors Association
Since 2000, the National Roof Contractors Association (NRCA) has recommended the use of a cover board. And since 2006, both the NRCA and the Midwest Roof Contractors Association (MRCA) have recommended the use of a noncombustible cover board such as “glass mat gypsum board.”
This was stated in a January 2006 joint MRCA/NRCA publication titled “Fire Testing of Membrane Roof Systems”:
“When using a low-slope membrane roof system, designers should include in their designs a suitable cover board that is consistent with an appropriate listing or approval from a code-approved testing agency. This recommendation is consistent with the guidelines already contained in The NRCA Roofing and Waterproofing Manual, Fifth Edition.
Furthermore, for mechanically attached single-ply membrane roof systems, designers of newly installed roof systems are now recommended to include a noncombustible cover board that is consistent with an appropriate listing or approval from a code-approved testing agency. Examples of noncombustible cover boards include glass-mat-faced gypsum boards and gypsum roof boards.”
Also, in 2000, cover boards’ impact over polyisocyanurate roof insulation was spelled out in an NRCA technical bulletin:ii
“NRCA recommends that designers specify a suitable cover board over polyisocyanurate insulation in all low-slope membrane assemblies. The use of a cover board should help reduce problems whether directly to the manufacturing process or due to other causes.”
Further, polyisocyanurate roof insulation is often specified because of its fire resistance properties. There are occasions, when the use of a cover board may be required to achieve a fire-resistance classification for a roof assembly, and the use of certain types of cover boards can generally improve the fire-resistance properties of the roof assemblies that include polyisocyanurate insulation.”
According to the NRCA, insulation cover boards should be composed of any of the following:
- Glass-faced siliconized gypsum board
- Perlite board
- Wood-fiber board
- Glass-fiber board
- Mineral-fiber board
In addition, cementitous cover board would also be acceptable.
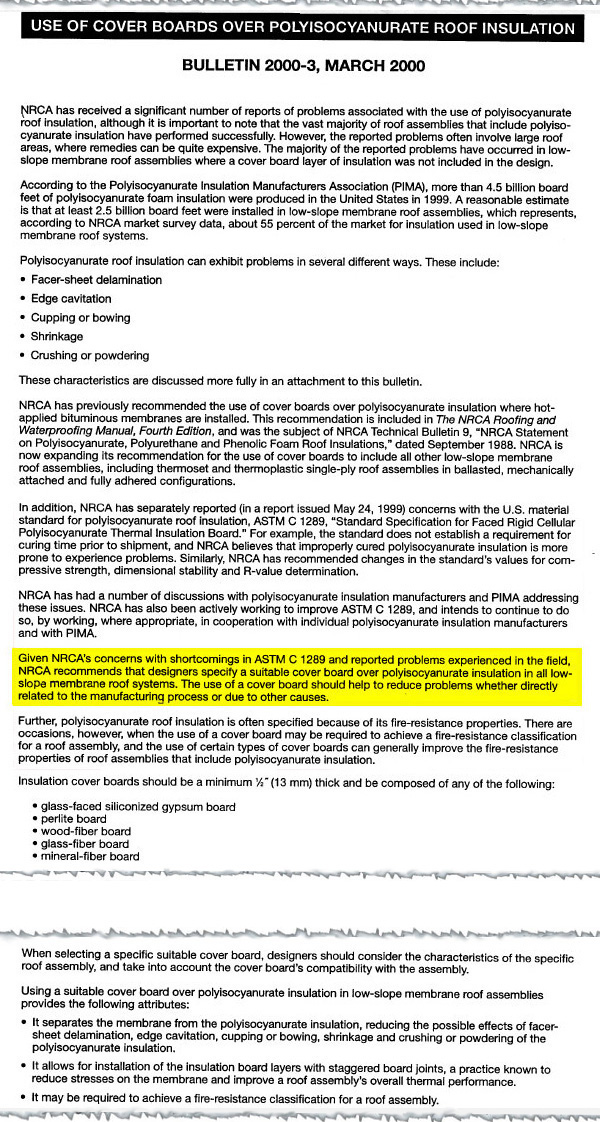
Image courtesy of National Gypsum®
Cover boards were suggested in a March, 2000, bulletin by the National Roofing Contractors Association. (Suggested presentation: show top of bulletin and bottom portion with the relevant quoted section, last two graphs on first page plus bulleted list. Use saw tooth separation technique to denote truncated copy.)
Note that while the majority of areas covered in low-slope roofs are “flat,” there may be sloped or vertical surfaces that require additional consideration. These areas include parapet walls on the exterior of the building, as well as steep-slope roof transitioning into the flat roof area, and interior walls to higher roof areas.
Of course, a specifier should make sure there is a structural deck included on any areas that might be considered walkable, which is generally considered to be a slope of 7 inches to 12 inches or less.
Factors Impacting the Long-term Performance of a Commercial Roof System
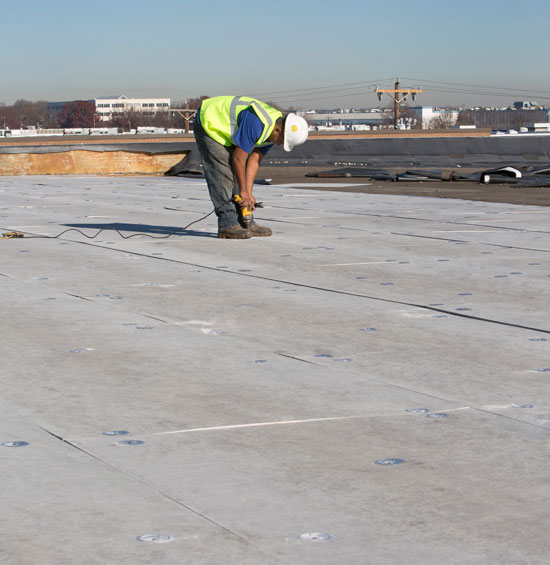
Photo courtesy of National Gypsum®
A worker is screwing the fasteners through the cover board and the insulation into the deck below the assembly.
Many outside influences affect the performance of the roofing system, and thus the durability of the building. Simulated outside forces are tested on various roofing assemblies, which are then awarded ratings to assure the specifier that the project will live up to expectations.
Here are the factors that can affect the roofing assembly and the tests and ratings that determine an assembly’s efficacy:
Fire — The fire rating for any particular low-slope roofing system is determined by the testing of the total roof assembly. There are no individual “parts” of the assembly that determine the fire rating. That means that the use of certain materials (gypsum-based cover board, cementitous-based cover board and/or thermal barrier, for instance) can positively affect the outcome of the test results.iii
The two widely accepted fire-testing agencies in the United States are Factory Mutual (FM), and Underwriters Laboratories (UL).
FM rates for combustibility from above the roof deck in these classifications: Class A, Class B and Class C. And it tests combustibility from below the roof deck with the Class 1 classification.
It’s important to understand that a Class A roof is not the same as a Class 1 roof. The achievement of a Class A roof rating is the result of one test — the external spread of flame test.
However, a Class 1 roof has been tested for a series of events, including the external spread of flame, the flame spread on the underside of the roof deck, plus wind, hail, corrosion and leakage. The test standard to achieve a Class 1 rating is much more comprehensive than the standard used to gain a Class A rating. Another way to put it is that all Class 1 roof assemblies are Class A roofs, but not all Class A roof systems meet Class 1 standards.
UL tests fire resistance according to UL 790, and rates roofs according to these standards:
- Class A roof coverings are effective against severe fire test exposures.
- Class B roof coverings are effective against moderate fire test exposures.
- Class C roof coverings are effective against light fire test exposures.
The three types of tests that UL performs to determine the fire ratings are:
- Burning Brand Test — for combustible decks only.
- Spread of Flame Test — for all combustible and noncombustible decks.
- Intermittent Flame Test — for combustible decks only
Some roof cover boards improve the fire rating of the system, while others contribute no improvement at all. We’ll discuss more fully which boards offer this added measure of protection later in the course.
Moisture/mold — The primary reason for a low-slope roof system to be installed on a building is to keep moisture out of the building. This is an on-going battle that will be waged for the 10- to 20-year life of most roofing systems.
There are any number of ways for water to get into the roof system, and then most likely into the building. The three most common ways are:
- During the installation of the roof system
- Through leaks in the roof system after it’s been installed
- By the condensation of moisture already in the building because of its use (including paper mills, buildings with indoor pools in them, food processing plants, etc.)
Mold requires a number of factors to occur in order for it to grow: heat, moisture, food, and mold spores.
Inorganic materials that are not paper-faced reduce the availability of “food” that mold spores require to grow. Fiberglass-faced or cementitious non-paper faced products reduce the availability of food that mold spores require to grow.
Note that no material can be considered “mold proof,” nor is it certain that any material will resist mold or mildew indefinitely. When used in conjunction with good design, handling and construction practices, products designed to be mold-resistant can provide increased mold resistance versus standard wallboard products. As with any building material, avoiding water exposure during handling, storage and installation, and after installation is complete, is the best way to avoid the formation of mold or mildew.
Below is a list of the roof cover boards that are manufactured to resist mold:
Glass-Mat Gypsum Board
Asphaltic Board
Extruded Polystyrene (Fanfold)
Cementitous Board
Hail and impact resistance — Including a high compressive strength cover board in the roof system design as a separation layer between the insulation and the membrane will disperse an impact load over a wider area and help protect both the membrane and underlying insulation from premature failure.
The high amount of repetitive traffic that occurs across the surface of the roof system during its installation can negatively affect the insulation below the membrane.
Wheelbarrows, power carts, and a continual stream of roofers walking and dragging materials across the rooftop can damage the roof system before the installation is even complete (crushing, facer delamination, etc.). This potential damage may or may not be noticeable during the roof system manufacturer’s warranty inspection.
Cover boards can also help prevent punctures of the roof membrane from occurring after the roof system has been installed. This can occur due to service technicians dropping tools while working on the rooftop equipment, or wind blown objects such as tree limbs falling on the roof.
Sound intrusion — While its true that excessive sound levels do not affect the long-term performance of the roof, they can definitely have a negative impact the quality of life that occurs inside of the building. This is particularly true for buildings in the immediate vicinity of airports, or located within their regular flight paths.
The inclusion of a cover board between the top layer of insulation and the roof membrane can mitigate this noise problem. And by using a layer of gypsum board on the roof deck as well, designers can create a sandwich effect that will noticeably decrease the amount of sound transmitted to the interior of the building through the roof.
Wind uplift and fastening patterns — Resistance to wind uplift is increased by the addition of certain cover boards, while other cover boards offer little or no improvement.
The main factors taken into account for wind uplift ratings are:
- Building Location
- Height of Building
- Wind Velocity
- Ground Surface/Topography
FM Global checks the roof edge requirements on all of their buildings. FM 1-90 is a standard wind rating used in the roofing industry. FM 4470 is the approval standard for single-ply, polymer-modified bitumen sheet, built-up roof (BUR) and liquid applied roof assemblies for use in Class 1 and noncombustible roof deck construction. FM 4450 is the approval standard for Class 1 insulated steel deck roofs.
UL 580 is the test standard for uplift resistance of roof assemblies. According to UL, “This test method subjects a 10 ft. x 10 ft. test sample to various static and oscillating air pressure to index performance under uplift loads imposed on roof decks.”
Cover Boards and Roof Types
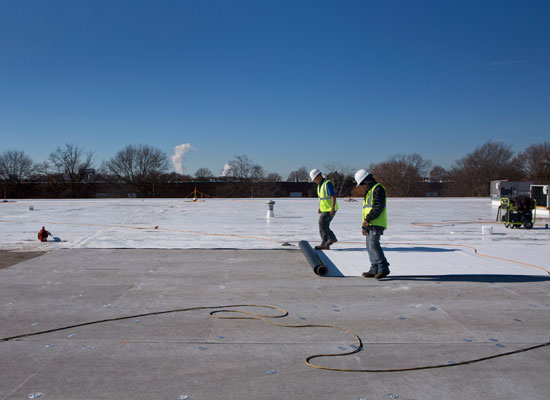
Photo courtesy of National Gypsum®
Workers roll out the white roof membrane prior to attaching it to the roof system over the cover board.
With the need for and desirability of cover boards established, the question then arises: Which cover board serves the project the best? The first issue will be determining which cover board is compatible with the specified roofing type.
Glass mat gypsum board — A water-resistant treated gypsum core with embedded fiberglass mats on both sides. Common thicknesses are 1/4 inch, 1/2 inch and 5/8 inch. It is compatible with all roofing types: single ply, built up, app mode bit, SBS modified bitumen and fluid applied roofs. (Standard: ASTM C1177)
Cement roof board — A noncombustible, water-durable, high-performance cement-based roofing cover board that is compatible with all low-slope roofing types. Common thickness is 7/16 inch. (ASTM C1325)
Fiber-reinforced gypsum board — This is a high-density gypsum reinforced with cellulose fibers. Common thicknesses are 1/4 inch, 3/8 inch, 1/2 inch and 5/8 inch. It is compatible with all roofing types: single ply, built up, APP modified bitumen, SBS modified bitumen and fluid applied roofs. (ASTM C1278)
Paper-faced gypsum board — This is a gypsum core with paper facers on both sides. It is for use as a thermal barrier. But must be Type X product. Common thicknesses are 1/2 inch and 5/8 inch. Compatible only with single-ply roofs. (ASTM C1396)
Wood fiberboard — Wood fibers or cane fibers bonded together with resins make up this product. Common thicknesses are 1/2 inch and 1 inch. It is compatible with single ply, built up, SBS modified bitumen and fluid applied roofs. (ASTM C208)
Asphaltic board — This is an asphalt core with fiberglass facers on both sides. It is 1/8 inch thick and is 4 ft. x 4 ft. (ASTM D6451)
Mineral fiberboard — Bonded fiberglass or rock wool with an adhered kraft paper face Common thicknesses are 1/2 inch to 1 inch. (ASTM C726).
Perlite board — Expanded volcanic materials combined with organic fibers and binders with an asphalt emulsion coating on the top side Common thickness is 1/2 inch. (ASTM C726).
Extruded polystyrene board (fanfold) — Extruded polystyrene beads formed into a fanfold board. It is commonly 1/4 inch thick, and comes in lengths of 4 ft. by 50 ft. (ASTM C578)
High-density polyisocyanurate board — This is composed of a polyisocyanurate foam core with fiberglass facers on both sides. It is high density with 100+ psi as compared to normal iso board with 16 psi to 20 psi. Common thickness is 1/2 inch. (ASTM C1289)
Plywood/OSB — Plywood is created by combining thin layers of wood veneer, while OSB (oriented strand board) is non-veneer panels made up of compressed layers of cross-laminated wood strands. Common thicknesses are 1/2 inch and 5/8 inch.
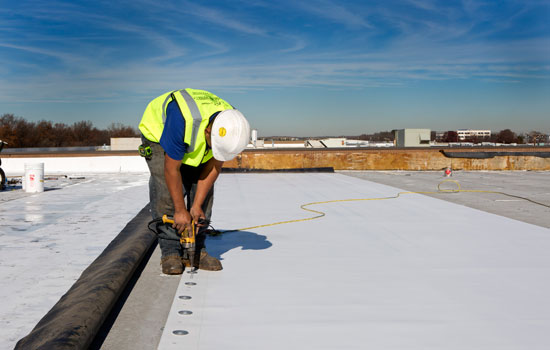
Photo courtesy of National Gypsum®
A worker is attaches the fasteners through to membrane into the roof system along the seam of the membrane. The seam of the adjacent membrane will overlap and will be adhered to the membrane below it, creating a redundancy at the seam overlaps.
Which Cover Boards to Use With Which Roof Systems
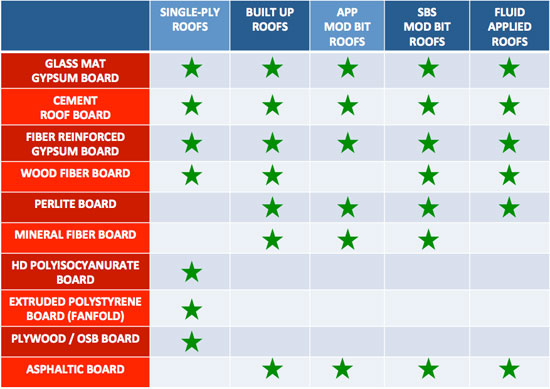
Source: National Gypsum
With so many choices, the selection of a roofing cover board could be confusing. This chart shows which boards are compatible with each type of roofing system.
- Glass mat gypsum board works with all low-slope roof systems.
- Cement roof board also works with all low-slope roof systems.
- Fiber-reinforced gypsum board works with all low-slope roof systems.
- Wood fiberboard works with all systems except APP modified. This will not stand up to torching.
- Perlite board is a good fit with asphalt-based systems.
- Mineral fiberboard works with asphalt-based systems.
- High-density polyisocyanurate board is compatible with single-ply roof systems.
- Extruded polystyrene board/sheet also works best with single-ply roof systems.
- Plywood/OSB board is used with single-ply roof systems in high-wind areas.
- Asphaltic board is best used with asphalt-based systems.
- Note: Paper-faced gypsum historically has been used as a thermal barrier on the deck, although it is not currently recommended.
Pros and Cons of Various Cover Boards
Each type of roofing cover board has characteristics that add certain performance improvements to a roofing system. Some cover board types bring more benefits than others. This section discusses each type of board and the pros and cons in specifying these materials.
Glass mat gypsum board — The water-resistant, treated core of this type of cover board provides moisture protection. It also provides good heat resistance, which can help improve the fire classification when tested within a roof system. It has high compressive strength. Quite importantly, it is mold resistant. This board has high durability and hail resistance, and it limits sound intrusion into the building. It is used in wide range of roof systems and is readily available. Note that there are designated products for fully adhered systems.
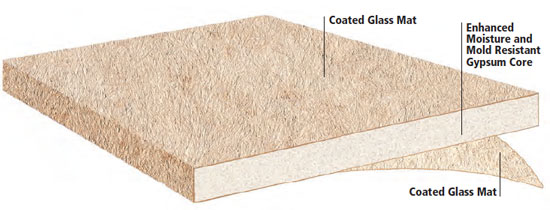
Image courtesy of National Gypsum®
The treated core of this type of cover board provides mold resistance. The board also provides good heat resistance and other benefits.
Cement roof board — This cement-based cover board has high compressive strength for protecting the roof's insulating layer. It is noncombustible and is mold resistant. It is engineered for resistance to wind uplift and has excellent compressive strength.
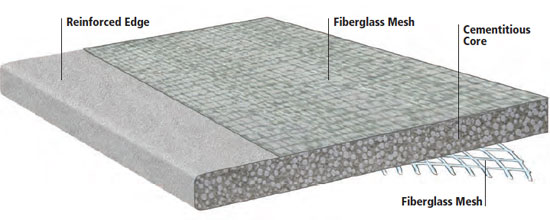
Image courtesy of National Gypsum®
Cement-based cover board is well known for having high compressive strength for protecting the roof's insulation. Plus it is mold resistant is not combustible.
Fiber reinforced gypsum board — This product’s water-resistant, treated core provides moisture protection, good heat resistance, and can upgrade fire classification when tested within a roof system. It has high compressive strength, and is mold resistant. It is hail resistant and does well with foot traffic. It limits sound intrusion and has good wind uplift characteristics.
However, fiberglass is very friable, and creates fiberglass flying around on jobsite and causes itchiness for workers. It is difficult to cut board on jobsite. And it is very heavy, which increases rooftop-loading time, and is harder on installers. It has limited R-Value. When cut, scratched or damaged, the board becomes susceptible to moisture penetration, which makes it vulnerable to causing future moisture and mold problems. While cutting to modify board length or width is not very difficult, the cutting of holes for pipes and drains is difficult. The product comes coated on six sides from the factory, so once it’s cut, the coating no longer protects the gypsum/cellulose core of the product from moisture.
Paper-faced gypsum board — Although not recommended, it can be used as a thermal barrier on a combustible deck to improve the fire rating. , It limits sound intrusion, especially when used together with a gypsum-based cover board.
Negatives include paper facers deteriorating in the presence of moisture, destabilizing the product. It is not meant for use as a cover board, but rather only as a thermal barrier on the deck. It has limited R-Value, and is typically excluded from roof manufacturers’ warranties. Only Type X gypsum can be used for this purpose. This product is relatively heavy for installers to handle. With a number of options of glass mat Type X gypsum products available, this product should not be the specifier’s first option.
Wood fiberboard — This material has a long track record of use as a cover board in the roofing industry. It is relatively lightweight with good compressive strength. It can be used with a wide range of roofing systems. It is one of the less expensive boards available on the market. Some sugarcane cellulose is made to make the board, as opposed to using just wood fibers.
On the negative side, it is highly susceptible to moisture absorption; it acts as a sponge. Loss of structural stability, rot and decay once exposed to water within the roof system. This type of board is combustible. This product readily absorbs adhesives used to attach the membrane, increasing the cost of the system installation. Used rarely in many parts of the country because of improved product alternatives.
Perlite board — This material has good heat resistance and is relatively lightweight, which the workers will appreciate.
But that comes with a cost. The structural integrity disintegrates when the board is exposed to water. It is easily breakable, and prone to corners breaking off. It cannot adhere any of the single ply or self-adhesive membrane products. It is rarely used in many parts of the country anymore due to improved product alternatives.
Mineral fiberboard — This material has good heat resistance and is dimensionally stable.
While this product does not readily absorb water, it can lose its structural integrity if wet for a long period of time. It has limited availability in the marketplace and is used rarely in many parts of the country due to improved product alternatives.
High-density polyisocyanurate board — This is a very lightweight and easy to handle material, which reduces loading time. It adds a small amount of R-Value to the roof system. Provides a firm surface for walkability.
However, it has low compressive strength relative to the more rigid products available (100 psf vs. 600 to 1,200 psf). It has fiberglass facers on both sides, which may experience the historical facer delamination issues iso has had. Polyisocyanurate insulation has had historical problems with cupping, warping, etc. Some industry observers believe this product may be too new to determine whether that will continue to occur. It has slope restrictions for fire ratings. High Density iso is 100+ psi versus ratings of 500 psi compared to 600 / 1250 psi for gypsum-based products.
Extruded polystyrene board — This material is extremely lightweight and transportable and easy to install. Workers can cover large areas fairly quickly. It is very water resistant due to its closed-cell structure.
On the other hand, this product provides no protection as a fire barrier. And it does not prevent damage from hail or foot traffic. The fanfold configuration can cause high and low points in the roof. And to top it off, it’s relative expensive compared to other roofing cover boards.
Plywood/OSB — Of course these products have very high compressive strength and good dimensional stability. They can improve wind uplift ratings when tested as part of a single ply roof assembly, according to ASTM D 3501, compression for wood-based structural panels.
Then again, these products are highly combustible, and efforts to chemically treat them for fire resistance have caused other issues. The fire-rated version of the product can experience problems with having adhesives bonding to it properly. These boards are relatively heavy and hard to work with. Most alarming, they are susceptible to absorbing moisture and will support the growth of mold when wet as they provide the food source that mold needs.
Asphaltic board — This is the thinnest board available, which could be helpful in case of height limitation during installation. Plus, it is very water resistant.
However, it does not add to fire resistance, nor does it improve fire ratings. It has low impact resistance, and very little compressive strength.
Conclusion
For a superior building that is high performing and long lasting, the roofing assembly must perform exceptionally well. A superior roofing assembly comes about by design. The addition of a roofing cover board helps insure the long-term viability of a roofing assembly, and helps avoid leaks and damage later on. We have discussed different roofing assemblies for low-slope roofing, and the standards that apply to them. We have examined the external forces that impact a roof, and how those forces are tested. Finally, we took an expansive look at the various types of roofing cover boards that you, as the designer and/or specifier, can choose from, and gave you the necessary information to choose the right roofing board for the best protection of the building.
REFERENCES
For more information on roofing cover boards, go to:
- National Roof Contractors Association (NRCA): www.nrca.net
- Roof Consultants Institute (RCI): www.rci-online.org
- Midwest Roof Contractors Association (MRCA): www.mrca.org
- Single Ply Roofing Institute (SPRI): www.spri.org
- Underwriters Laboratories (UL): www.ul.com
- Factory Mutual Global (FM): www.fmglobal.com
- Roofing Industry Committee on Weather Issues (RICOWI): www.ricowi.com
- Construction Specifications Institute (CSI): www.csinet.org
- ASTM International (formerly American Society of Testing & Materials) www.astm.org
ENDNOTES
ii.) NRCA Technical bulletin, Use of Cover Boards over Polyisocyanurate Roof Insulation, March 2000
See http://www.nationalgypsum.com/resources/fire-safety.htm for additional information regarding fire safety ratings.
iii.) See http://www.nationalgypsum.com/resources/fire-safety.htm for additional information regarding fire safety ratings.
![]() |
Known for providing innovative solutions for sustainable design and green building practices, National Gypsum is a fully integrated manufacturer of building products. Primary emphasis is on its three core brands — Gold Bond® gypsum board, including the PURPLE® family of drywall products, ProForm® drywall finishing products and PermaBase® cement board products. |