Recycled Material Innovations
Designing with sustainable natural fiber insulating products
Continuing Education
Use the following learning objectives to focus your study while reading this month’s Continuing Education article.
Learning Objectives - After reading this article, you will be able to:
- Investigate the historical development of the use of natural fiber materials for insulation products.
- Identify the green and sustainable characteristics in the types of insulation made from recycled cellulose materials.
- Assess the thermal and acoustical performance of green building insulation made from rapidly renewable and recycled cotton fiber textiles.
- Explore some of the emerging trends and market demands for the use of insulation made from recycled natural materials.
Reduce, re-use, and recycle has been a popular mantra of recent times for good reasons. The historic “cradle to grave” approach relies on extracting raw materials (the cradle), processing them, shipping them, using them for a while, and sending them to a landfill (the grave) when we are done using them. By contrast, diverting materials from a landfill and giving it new life as a new product has been the basis for an enlightened sustainable approach championed by architect William McDonough in his well-known book Cradle to Cradle.
McDonough goes beyond the realm of just buildings and looks instead at the bigger picture of how products and materials of all types can be interrelated to many other things during their total life cycle to influence design processes, manufacturing, effective performance, and lifestyles in general.
A great example of this approach is found in using recycled natural fibers from other sources for building insulation. By definition, natural fibers are those that come from natural resources such as forestry or agricultural products. In particular, building insulation that uses recycled natural fibers from trees (in the form of cellulose) or from cotton plants capture the true spirit of “cradle to cradle” by giving materials a new life instead of going to the landfill. Just as important, this sustainable type of insulation has been shown to perform exceptionally well in terms of optimizing energy performance in buildings and effectively reducing sound transmission as an acoustic control measure.
Historical Use of Natural Fibers in Buildings
European settlers arriving in this country and Canada in the 1600s and 1700s likely discovered quickly that the climate was a little different than along the Mediterranean Ocean. Seeking ways to keep homes warmer, they appear to have relied on large wood-burning fireplaces that radiated excessive amounts of heat. Some of that heat surely ended up being stored in the massive structural elements of the home such as logs or large timbers in forested areas, sod in the Midwest prairie, or directly in the massive stone and brick used in the fireplaces. There was little if any thought given to insulation as we know it today, but there certainly was thought given to keeping out drafts. It was common to find blankets made out of wool or other fabrics being used to hang down in front of doors or other openings as a means to prevent drafts from blowing into a main working/living area. The blankets would also help to contain heat around an area that had a fireplace, in effect acting as very rudimentary insulation.
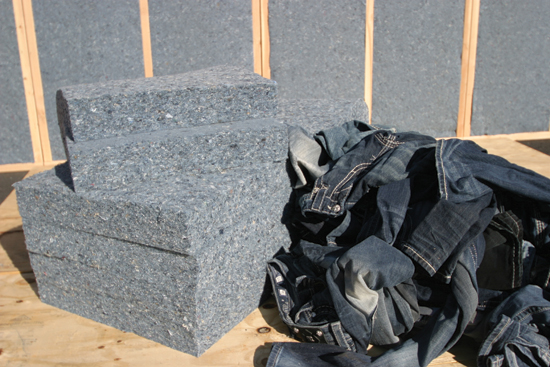
Photo courtesy of Bonded Logic, Inc.
Natural cotton fibers used in denim can be recycled, broken down, processed, and turned into effective building insulation batts to help improve thermal and acoustic performance in buildings.
During the 1800s and early 1900s, the country became more developed and heavy mass construction gave way to lighter wood-framed cavity walls with balloon framing. This meant that buildings had less mass to store heat and more need to hold in the heat that was being created in a fireplace, a stove, or a furnace. Recognizing this need, resourceful homeowners began to stuff the framing cavities with familiar and available natural materials to keep them warm the way a blanket would. Materials like newspaper, cardboard, cotton, straw, sawdust, hemp, and corncob are all believed to have been used based on findings in older buildings. There is also the suggestion that sheep's wool was used as insulation in some cases although that should not be confused with rock-wool which is literally made from stone ingredients.
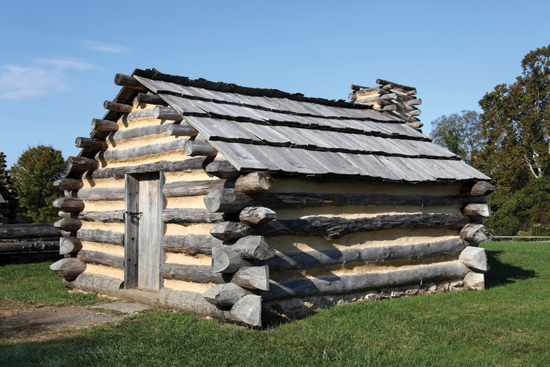
Photo courtesy of Bonded Logic, Inc.
Historically, buildings in the U.S. had more mass from heavy structural members. Insulation became more important as buildings became lighter and needed to control heat flow better.
Following World War II in the 1950s, the first manufactured natural fiber material began to become available. Some innovative companies ahead of their time began collecting recycled newspaper and put it through a grinding and dust removal machine, breaking up the fibers to create a fluffy end product. Once a fire retardant was added, it was offered as a blown-in building insulation product, although it was not widely or commonly used right away. That all changed in the 1970s when the oil embargo focused everyone's attention on energy and conservation in particular. Literally hundreds of small companies began offering blown cellulose as building insulation for existing and new buildings and its use gained significant popularity. Because of this upsurge in activity and a need for identifying standards for this product, the U.S. Consumer Products Safety Commission (CPSC) issued regulations in the late 1970s that addressed technical requirements for settled density, corrosiveness, critical radiant flux, and smoldering combustion. This was all good for the consumer because it provided some consistent quality control that could be monitored and corrected where need be. However, it was not economical for many of the smaller companies to implement all of the needed testing and quality measures which meant many decided to consolidate with others, become larger on their own, or go out of business altogether.
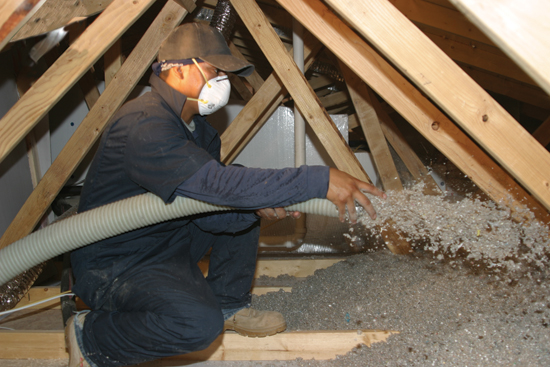
Photo courtesy of Bonded Logic, Inc.
Cellulose insulation has a post-consumer recycled content of up to 85 percent and can be more effective and economical overall than other insulations with the same R-value per inch.
Over the past 20 years or so, the current green building movement has increased the need and demand for effective and environmentally sound building insulation. Increasing awareness of the role that recycled material choices can play in green buildings has spawned new innovations, new products, and new ways to capture material otherwise headed to landfills. At the same time, a recognized premium has been placed on rapidly renewable materials that can be used to fabricate products rather than depleting a finite source of limited materials. This includes things like forestry and agricultural products that can be grown sustainably, harvested, and grown again. These motivators have meant that blown cellulose insulation has matured and developed as a product with variations and improvements to make it suitable for differing commercial and residential building applications. It has also spawned an interest in finding other recycled materials such as cotton textiles that can be captured and used to create batt type insulation products with superior characteristics for use in commercial and residential buildings of all types. Recycled cotton textiles are also being used in various ways to create very effective acoustic insulation products or being integrated into other building product systems. We will take a closer look at these insulation products and their increasing popularity in the following sections.
Cellulose Insulation
Cellulose insulation today is commonly manufactured by national companies to meet standards and regulations and then installed by local contractors. Like most large businesses, the manufacturers distribute their products throughout wide geographic areas. There is certainly not a cellulose insulation plant in every community or even every state, but cellulose insulation is readily available in every part of the U.S. Many of the manufacturers are part of a national trade association known as the Cellulose Insulation Manufacturers Association (CIMA). It was first established in 1982 as the Cellulose Industry Standards Enforcement Program (CISEP) as a voluntary program to enforce and document conformance of the CPSC regulations issued just a few years prior. They also addressed relevant ASTM testing standards for building products such as fire resistance. As the industry matured and the national companies became more established, CIMA became a full association of manufacturers in 1992.
Under the CIMA and ASTM standards, cellulose insulation is commonly made from up to 85 percent recycled content (post-consumer). The primary ingredient is still recycled newspaper that is hammer milled to break apart the pages and fibers so it can become insulation. The small remainder of additional ingredients includes additives that give the insulation some of its more desirable properties. For example, cellulose insulation is treated with fire retardants achieving a Class 1 Fire rating to meet all federal, state, and local fire safety requirements. Some manufacturers have even qualified for two- and three-hour firewall designs using cellulose insulation.
Manufacturers have further enhanced their products to create some variations being offered for different applications. Dry spray products minimize the use of water, making them well suited for retrofit into existing buildings. Wet spray products are used in new construction to make them more self-supporting, thus reducing the chance of the product settling. For deep applications in attics and roof areas, stabilized products are available that keep them from settling down on themselves. For applications where dust may be a concern either to occupants or building operations, dust controlled products are available.
All of these types of cellulose insulation have seen increased popularity due to their very “green” recycled content but also because of their effective characteristics and benefits. For example, cellulose insulation is denser than fiberglass so it reduces convection currents in framing cavities and helps slow air infiltration. R-values of cellulose insulation are R-3.6 to R-4.0 per inch, making them comparable to or better than other loose fill insulation products. Perhaps more importantly, however, cellulose easily insulates closed cavities, irregular shaped areas, or hard-to-reach spaces, meaning that it fills the framing cavity completely. From an indoor air quality standpoint, no harmful hydro-fluorocarbons of any type are used and no formaldehyde is present in the insulation, meaning there are no harmful emissions or air quality concerns. Further, cellulose insulation is very good at wicking any moisture or water out of the insulation, avoiding any buildup that could produce mold. Overall, cellulose insulation is found to be a very good, green, and cost-effective type of blown-in insulation.
While there are decades of performance statistics and supporting information on the use cellulose insulation, there are also some common misperceptions that CIMA corrects with actual information such as the following:
• Mold and mildew: Some people imagine that since cellulose is wet-spray applied that it will contribute to the growth of mold and mildew in walls. In fact, this type of application uses a small amount of added water for increased bonding to the sheathing. This added moisture, when installed correctly, dissipates quickly, typically resulting in a moisture content that is the same or less than wood framing members. Since cellulose drains and manages water very well, any trace moisture in the insulation will pass through it and then the drywall after it is installed, similar to moisture dissipation from wood wall studs. Hence, cellulose insulation is not subject to mold contamination any more than any other building material. In fact, published studies indicate that the hygroscopic or water draining nature of cellulose insulation results in superior moisture handling characteristics.
• Deforestation: It has been mistakenly said that cellulose insulation results in deforestation because it uses wood from trees. The reality is that the extremely high recycled paper content of cellulose insulation avoids the need for material from newly cut trees. Further, with almost 85 percent recycled paper content, it actually diverts almost a million tons of waste paper from landfills annually.
• R-value should govern insulation choice: R-value is always a consideration but it is only one factor to consider when choosing insulation. The performance of an insulation material is also dependent upon other factors such as reducing heat loss through air infiltration, convection, and radiation. Cellulose insulation is denser than some other choices hence it reduces air infiltration and convection better than other insulation products with the same R-Value meaning that cellulose insulation can provide superior overall performance. It should be noted that cellulose insulation does sometimes settle over time. If it is not installed correctly with the correct depth to account for this settling then there could be a potential loss in R-value. CIMA requires that manufacturers packaging identifies the correct depth of insulation after settling to achieve the desired R-value.
• Cost: Cellulose insulation is more competitive than some may think. Blown-in cellulose and blown-in fiberglass insulations are typically priced to be comparable while blown-in cellulose insulation is less expensive than spray foam insulations. Blowing cellulose insulation into wall cavities will typically be a bit more expensive than installing fiberglass batts mostly due to higher labor/installation costs. This difference however is easily overcome by the commonly greater savings on energy costs by using the denser cellulose insulation.
Armed with accurate information and an understanding of the best applications for its use, architects and other design professionals should continue to consider blown-in cellulose insulation as a viable option for both new and retrofit insulation needs.
Cotton Fiber Insulation
While cellulose insulation was succeeding as a blown-in natural fiber insulation, the need was also recognized for a high-performance, recycled natural fiber batt type of insulation product as well. That would require fibers that are denser and more capable of holding their shape when processed. Innovations learned in the production of cellulose insulation were applied to textiles to see if they would have the needed characteristics and indeed they have been successfully developed. Currently, recycled cotton batt insulation is available across the country and is being used to help create greener and more sustainable buildings.
Textile Recycling Process
The “cradle” for cotton fiber insulation is what many would consider the “grave” or the end of the line for parts of our wardrobes. Specifically it is the collection of post-consumer or pre-consumer cotton fabric such as denim, blue-jeans, or similar material. At least one manufacturer has developed an innovative and far-reaching collection program for recycling these otherwise wasted cotton textiles. The recycling division of the company diverts an impressive 300 tons per month of textile waste from the landfill and into the insulation production process. The waste material is collected through a variety of pro-active outreach methods, including public textile collection bins, partnerships with organizations like The Salvation Army and Goodwill, corporate recycling initiatives, manufacturer waste diversion, and “certified destruction” programs that deal with counterfeit merchandise. There are clearly many available sources and the beauty of the program is that it captures and collects them to everyone's benefit.
Once collected, the textiles arrive at the recycling facility and our sorted by fiber content. For example, materials with high synthetic content are segregated from materials which will ultimately become recycled cotton denim insulation. After the textiles have been sorted, they enter the first stage of “fiber opening,” which includes passing through guillotine choppers to reduce the size of the pieces. Next, any metal buttons, snaps, zippers, etc. are separated from the chopped textiles via a sophisticated system of magnets and metal detectors combined with compressed air bursts.
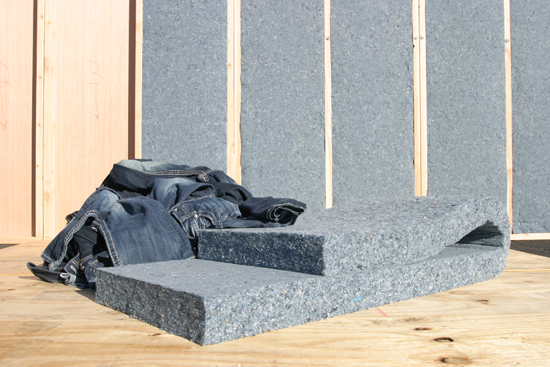
Photo courtesy of Bonded Logic, Inc.
Textiles captured from the waste stream can be recycled and reprocessed to create high-density, high-performing batt insulation.
After the metal has been removed, the chopped textiles pass through a series of six spiked cylinders spinning at a very high speed. Each cylinder has thousands of tiny “needles” that reduce the textile pieces back to their raw fiber form. In the case of denim, the result looks like blue cotton candy at the end of the opening process. The fiber is then compression baled and is ready to be used as a raw material for recycled cotton insulating products.
Cotton Thermal Insulation
Once the newly re-purposed raw material of recycled cotton fiber is ready, then it can be manufactured into a superior performing thermal insulation product that is safe for people and for the environment.
Building on decades of natural fiber insulation experience and manufacturers' own patented processes, they are able to create an insulation that provides designers, building owners, and occupants with documented thermal and safety performance. The manufactured construction of cotton batt insulation creates thousands of tiny air pockets in the insulation that maintain a strong thermal barrier even in extreme temperatures. The density of the insulation is also high so like cellulose insulation, it contributes to providing a consistent thermal performance by inhibiting air flow and convection currents in the framed cavity spaces. In order to assure a tight fitting seal and maximum filling of the cavities, cotton batts are commonly manufactured in “oversized” widths and installed with a friction fit.
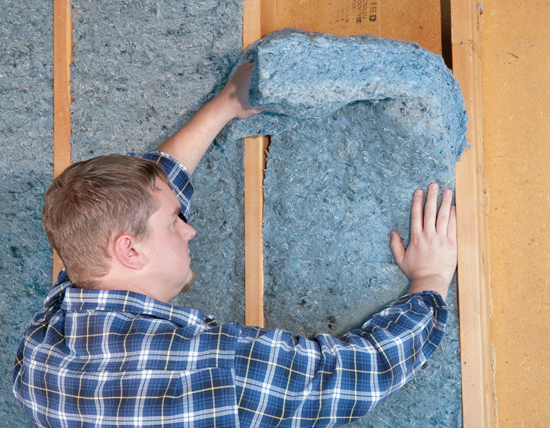
Photo courtesy of Bonded Logic, Inc.
Cotton batt insulation is typically manufactured to be snugly friction fit between framing members to fill the cavity completely and provide superior thermal performance.
The recycled denim fibers used in the manufacturing of cotton batt insulation are treated with non-toxic additives that address safety and indoor air quality. This is demonstrated with the fibers being treated in order to achieve a class-A fire rating and satisfy code and regulatory fire concerns when used in wall and roof assemblies. This is a similar process to the one used for cellulose insulation and has been tested and approved accordingly. The insulation treatment also includes a non-toxic mold and mildew inhibitor to dispel any concerns about such growth in the final constructed assemblies. The treated fibers are then “flash-dried” to ensure that quality control standards are met. The result is an effective but natural product that actively inhibits the growth of mold, mildew, bacteria, and fungi while retarding fire to achieve that Class-A Fire rating.
Recycled cotton insulation is also a fully green and sustainable product that can contribute toward earning multiple LEED credits. Cotton batt insulation contains up to 90 percent post-consumer recycled content and uses cotton, a rapidly renewable resource, as its main component. The finished product does not contain any harmful chemicals or irritants and therefore does not pose any VOC or off-gassing concerns. Using cotton batt insulation in new or retrofit building projects will likely assist in earning LEED credits while also providing building owners and occupants with a superior, healthy, and safe insulation.
When it comes to installing cotton batt insulation, most contractors find it easy to work with and very safe since they are exposed to less dust or health concerns when the materials and additives are all natural. Often the material is compressed for shipping purposes and requires a shaking out prior to installing. This will help accelerate the natural rebounding properties of the fibers. Depending upon climate and environmental conditions, full rebound may take several days. For walls, the insulation batts are installed between studs by simply fitting each batt firmly into place—most products are sized to fit between standard 16-inch O.C and 24-inch O.C. framing. If an off-size cavity is encountered, some manufacturers offer a pre-perforated batt that allows a simple tearing along the line to be able to fit it to size. Alternatively, it can be easily cut with common hand tools to fit. In either case, an extra half inch in width and in length should be allowed for to maintain the friction fit properties of the batts. The insulation can be further cut or torn to fit snugly around obstructions such as plumbing, mechanical, and electrical items with any left-over pieces used to fill small openings around windows and doors.
For exterior walls, most municipalities will require a vapor barrier to be installed although this can vary depending on the local climate and local building codes. If a vapor barrier is required, manufacturers tend to recommend the use of a permeable barrier which will allow walls to “breathe” while still stopping moisture transfer. In most northern climate situations, the vapor barrier should be applied towards the living area after insulation installation. Keep in mind that a single continuous vapor retarder is more effective than individual kraft paper faced batts and usually requires less labor.
When used in ceilings or attics, cotton fiber insulation can be layered to achieve higher total R-values. In this case, it is best to alternate the direction of the batts in each layer. If the insulation is installed before a ceiling is in place or if they need to be otherwise supported, then the batts can be secured to the ceiling joists using either wire or a mesh. In a similar manner, cotton fiber insulation can be used as an effective option for insulating floors and crawlspaces as well. The insulation should be secured to floor joists or crawl space cavities in the same manner as ceiling applications, using either a mesh or wire support system. For crawlspaces specifically, a system of vapor barriers is recommended. The bare ground should be covered with a barrier as well as applied to the cavities before the insulation is installed (facing the warm side of the subfloor).
Acoustic Insulation
Controlling sound and noise transmission through walls, ceilings, and floors can be a complex design and construction challenge. Cotton fiber insulation has been shown to offer an extremely high Noise Reduction Coefficient (NRC) to effectively reduce airborne sound transmission including traffic, airplane, radio, television, and everyday human conversation. The natural fibers in the insulation provide excellent sound absorption, while the manufacturing process produces a three-dimensional infrastructure that effectively traps, isolates, and controls sound waves. The cotton batts are installed similar to other acoustic insulation and in the same manner as thermal insulation. The result is a quiet comfortable environment between rooms, walls, and flooring.
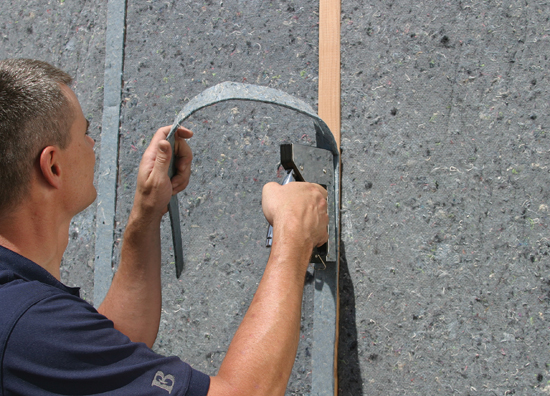
Photo courtesy of Bonded Logic, Inc.
An innovative acoustic control system combines dense cotton fiber insulation with resilient strips that allow gypsum board to float away from the studs and enhance sound ratings as a result.
At least one manufacturer has developed an enhanced acoustical insulation package that combines high-density cotton batt insulation and vibration damping strips that together allows for high STC performance with an easy to install system. There is no need to combine products with historically difficult installations to achieve above average STC ratings. The high density batt insulation is fitted into cavities in the standard installation manner. Once all the cavities have been filled, 12mm-thick by 6-inch-long strips are ready to be installed on the framing. The preferred method of attachment is by using standard spray adhesive. On a typical 8-foot or 9-foot vertical stud, it is recommended that five 6-inch strips should be installed spaced at even intervals. It is also recommended to install one 6-inch strip horizontally on both the top and bottom plates centered above and below each cavity.
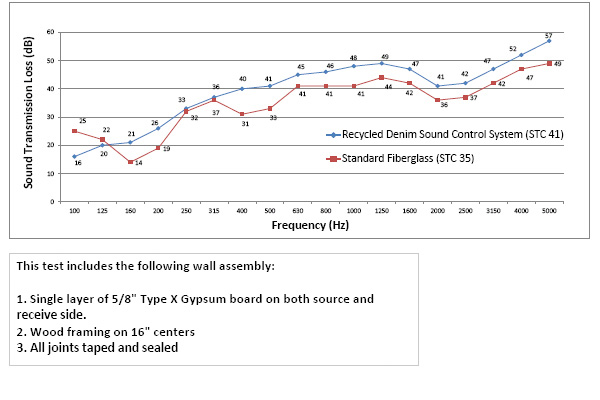
Chart courtesy of Bonded Logic, Inc.
A comparison of the performance of different wall systems in relation to acoustical frequencies.
This system allows the finish material (drywall) to float, rather than have direct contact with the framing. This greatly reduces the sound energy from transmitting through the wall. Tested STC values for typical wall assemblies are listed below based on third-party testing laboratory reports:
• STC 41 – 2x4 Wood Framing, 16-inch O.C., 5/8-inch Type X Gypsum Board on both source and receive side, cotton batt insulation + vibration damping strips
• STC 50 – 3 5/8-inch 25 Gauge Metal Framing, 24-inch O.C., Type X Gypsum Board on both source and receive side, cotton batt insulation + vibration damping strips
• STC 52 - Double Row of 2x4 Wood Framing, 1-inch Air Gap between Stud Rows, 16-inch O.C., 5/8” Type X Gypsum Board on both source and receive side, cotton batt insulation + vibration damping strips
• STC 52 - Staggered Stud 2x4 Wood Framing, 16-inch O.C., 5/8-inch Type X Gypsum Board on both source and receive side, cotton batt insulation + vibration damping strips
In applications where thermal performance is also desired, the system provides an R-13 value. The vibration strips function as a thermal break, preventing the flow of thermal energy between conductive materials.
In addition to acoustical batt insulation, recycled cotton fiber can be used to create exposed acoustic panels that dampen sound reverberation and improve acoustics in spaces where sound control is needed. The semi-rigid panels have been used in auditoriums, gymnasiums, concert halls, offices, and even residences where excessive sound and echoes needed attention. The panels are available in a range of colors and sizes making them easy to work into interior designs and complement overall design intents.
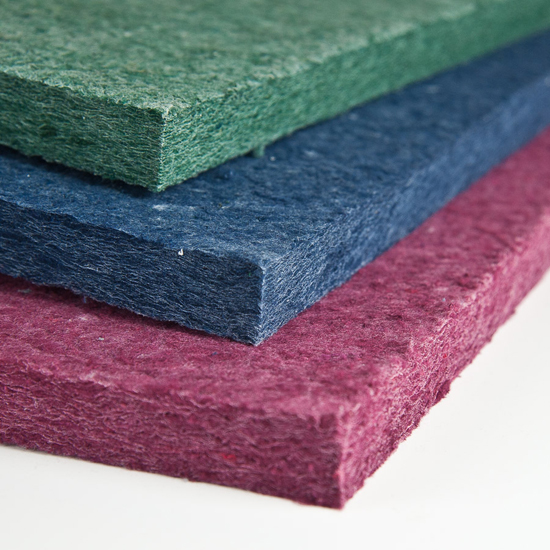
Photo courtesy of Bonded Logic, Inc.
Exposed acoustical wall panels made from recycled cotton fibers are an effective and attractive means to control sound reverberation and echoes in open spaces.
The making of these acoustic panels begins by taking the initial textile sorting process one step farther beyond just identifying material types. The acoustic panel color options come directly from the raw material source. For example, pure white acoustic panels are created from pre-consumer T-shirt and sock waste. Khaki colored acoustic panels are sourced from recycled khaki pants. Black and grey colored acoustic panels are sourced directly from sweatshirt and sweat-pant scrap. In this way, a fully functional product is created by building off of the character and color of the original fabric.
Emerging Trends
The building design and construction industry overall is moving further and further along the path of sustainable, energy-efficient buildings that use products which acknowledge the full life cycle of products and materials. This is being fueled by green building standards such as the well-known LEED® rating system which has been released in version 4 and raises the bar on energy performance and material life-cycle environmental impact. It is also being pushed along by building codes requiring better insulation practices and cleaner indoor air. Perhaps most directly, it is being influenced by building owners who are looking for reduced energy costs, better acoustic performance, and the marketing benefits of having a healthy, sustainable building. With all of these motivators, it is easy to anticipate an increase in the demand and use of natural fiber insulation.
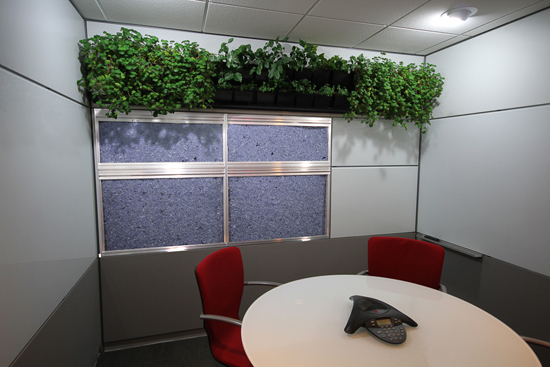
Photo courtesy of Bonded Logic, Inc. and DIRTT
Movable interior wall panels showing recycled cotton fiber acoustical insulation built into the product.
This increase in use may not be limited to exterior construction assemblies, rather it is showing up in products that are installed within a building as well. DIRTT Environmental Solutions, for example, manufactures moveable interior wall systems and has been turning to recycled denim insulation for acoustical control in their products. DIRTT, which stands for Doing It Right This Time, uses an innovative approach to manufacturing that result in faster, cleaner construction, and high levels of customization and flexibility all while significantly lowering a building's carbon footprint. In an effort to achieve total sustainability, DIRTT sought to replace fiberglass insulation with a more environmentally friendly alternative. Their investigation and research brought them to recycled cotton denim insulation.
Not only did they prefer the 80 percent post-consumer recycled content, they found that it outperformed fiberglass in acoustical properties without any off-gassing, harmful chemicals, or irritants. They have also committed to collect any insulation scraps left over from DIRTT's manufacturing process and send them back to the insulation manufacturer for reuse in new products, creating a zero-waste stream. “We tirelessly searched for a better alternative to fiberglass insulation,” says DIRTT COO Tracy Baker. “Recycled natural cotton fiber insulation was the perfect solution. Not only does it outperform traditional insulation, it is a highly sustainable product that contributes to our goal of zero-waste manufacturing.” It is cooperative efforts such as these that truly advance and make possible the “cradle to cradle” philosophy to fully take hold.
Conclusion
Natural fiber insulation has shown itself as a proven choice for building designers and owners looking to meet a variety of performance requirements and green building standards. Whether using blown-in cellulose insulation or cotton fiber batt insulation, the basis of the product is to use and process predominantly recycled natural fibers into a high-performing product. Relying on safe and non-toxic additives to meet fire and other safety standards, indoor air quality and health safety are also protected. The manufacturers and their cooperating business partners that are involved in making these sustainable and green products available are truly following the principles of cradle-to-cradle life cycles, making them easy to show compliance with LEED and other green building standards. Architects and designers who give consideration to these products will likely find they meet many design criteria and building owner requirements as well.
![]() |
Bonded Logic, Inc. is a manufacturer of thermal and acoustic insulations, sourced from recycled cotton textiles. With the flagship products lines consisting of UltraTouch Denim Insulation and Echo Eliminator Acoustic Panels, Bonded Logic provides thermal and acoustic insulating solutions with a focus on sustainable performance. www.bondedlogic.com |